RENAULT TWINGO RS 2009 2.G General Vehicle Information User Guide
Manufacturer: RENAULT, Model Year: 2009, Model line: TWINGO RS, Model: RENAULT TWINGO RS 2009 2.GPages: 46
Page 11 of 46
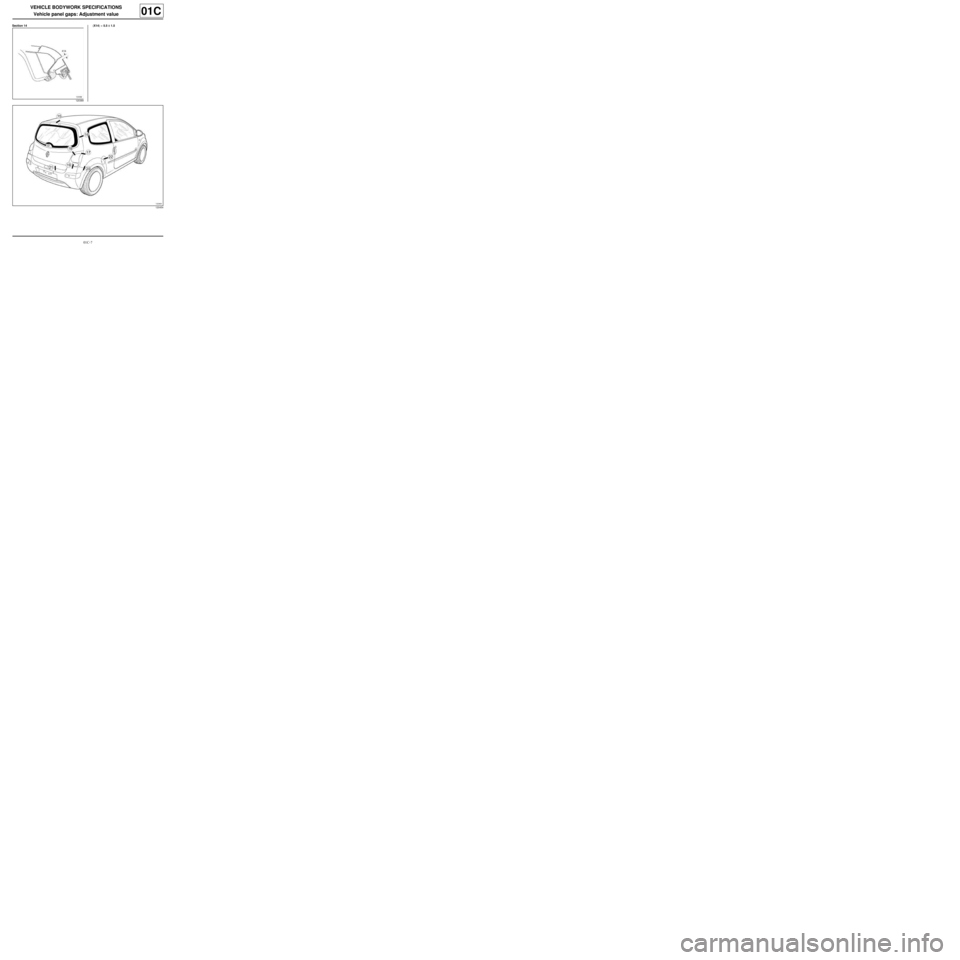
01C-7
VEHICLE BODYWORK SPECIFICATIONS
Vehicle panel gaps: Adjustment value
01C
Section 14 (X14) = 5.5 ±± ± ±
1.5
120389
120454
Page 12 of 46
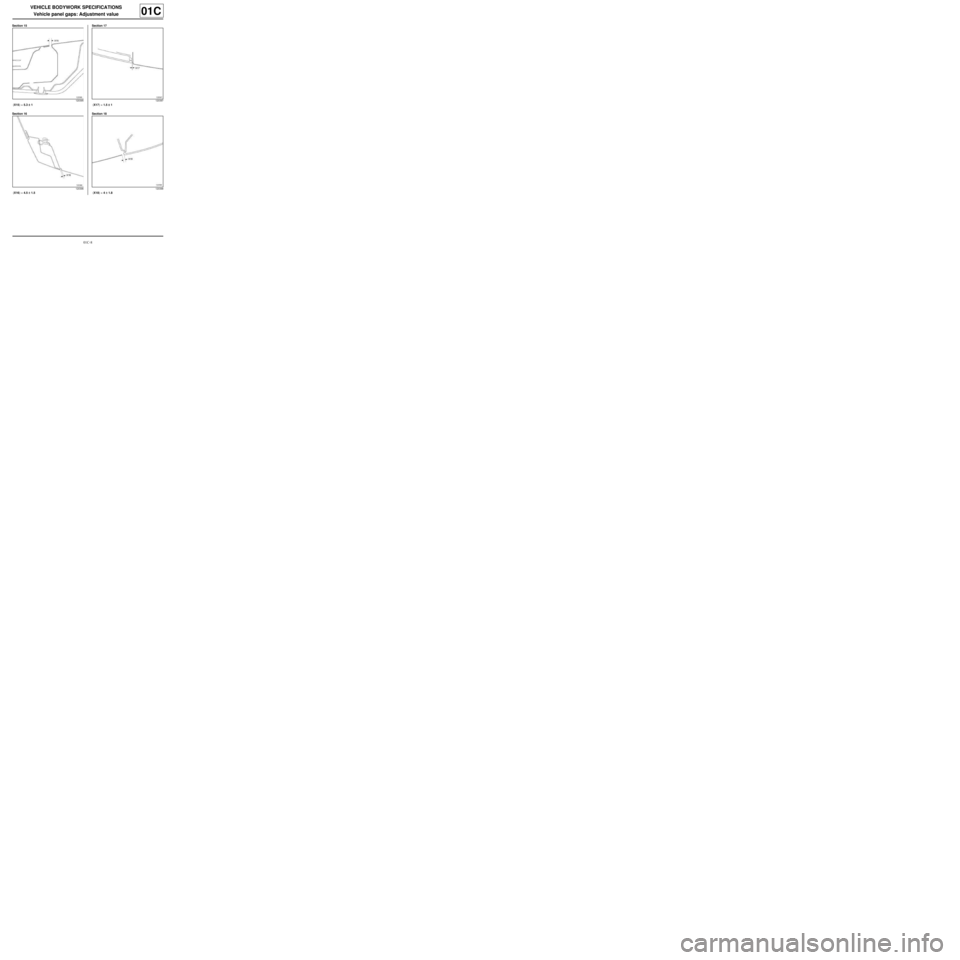
01C-8
VEHICLE BODYWORK SPECIFICATIONS
Vehicle panel gaps: Adjustment value
01C
Section 15
(X15) = 5.3 ±± ± ±
1
Section 16
(X16) = 4.5 ±± ± ±
1.5Section 17
(X17) = 1.5 ±± ± ±
1
Section 18
(X18) = 4 ±± ± ±
1.8
120395
120396120397
120398
Page 13 of 46
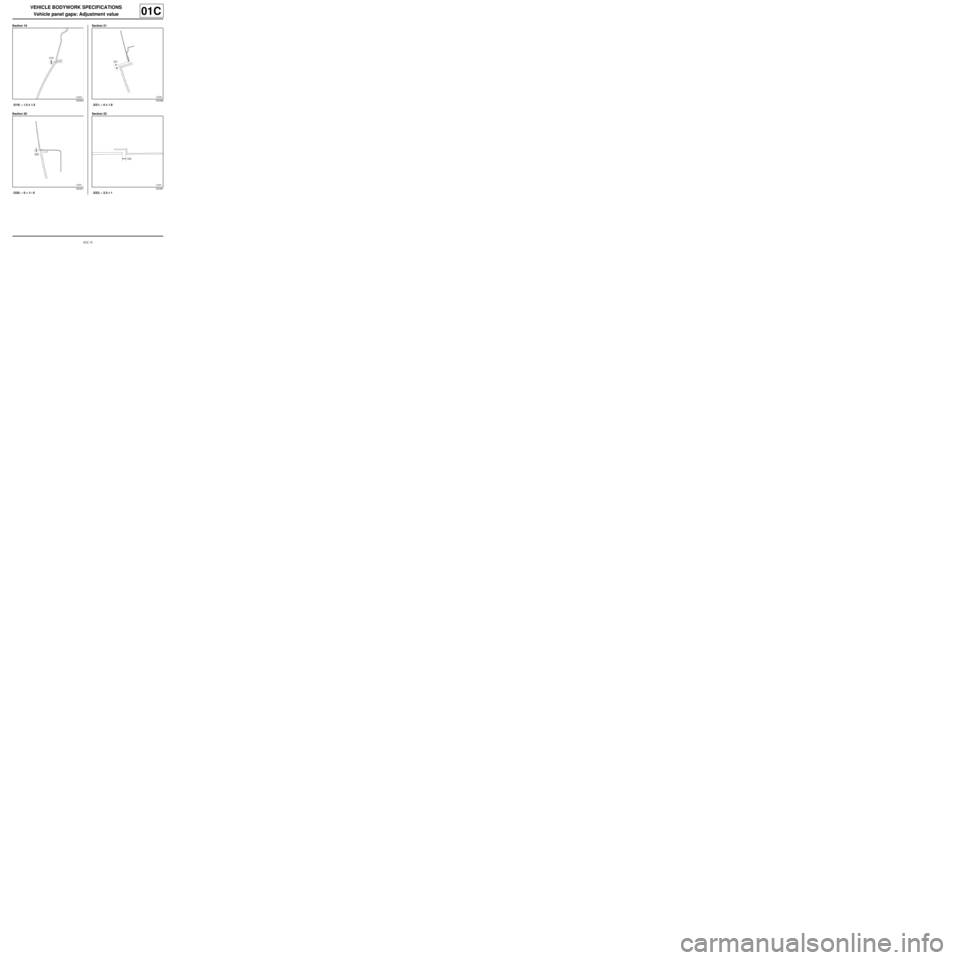
01C-9
VEHICLE BODYWORK SPECIFICATIONS
Vehicle panel gaps: Adjustment value
01C
Section 19
(X19) = 1.5 ±± ± ±
1.5
Section 20
(X20) = 0 + 1/- 0Section 21
(X21) = 6 ±± ± ±
1.8
Section 22
(X22) = 2.5 ±± ± ±
1
120400
120401120399
120391
Page 14 of 46
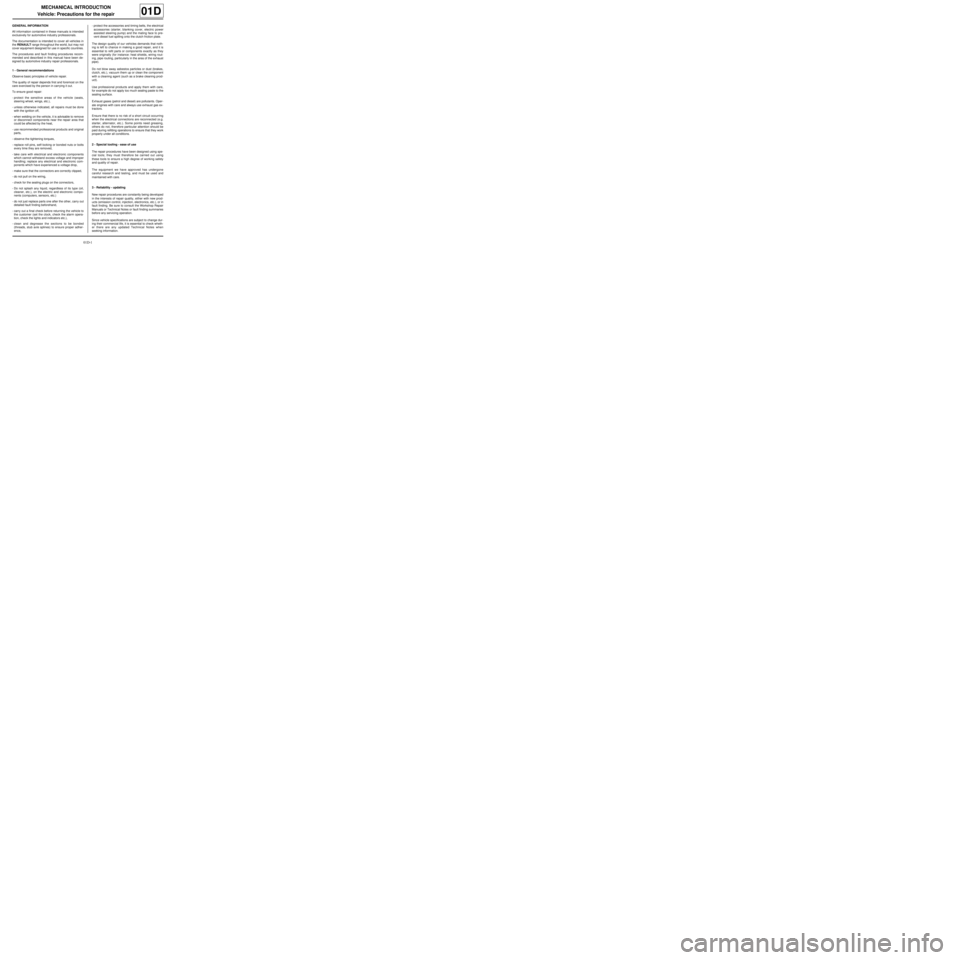
01D-1
MECHANICAL INTRODUCTION
Vehicle: Precautions for the repair
01D
GENERAL INFORMATION
All information contained in these manuals is intended
exclusively for automotive industry professionals.
The documentation is intended to cover all vehicles in
the RENAULT range throughout the world, but may not
cover equipment designed for use in specific countries.
The procedures and fault finding procedures recom-
mended and described in this manual have been de-
signed by automotive industry repair professionals.
1 - General recommendations
Observe basic principles of vehicle repair.
The quality of repair depends first and foremost on the
care exercised by the person in carrying it out.
To ensure good repair:
-protect the sensitive areas of the vehicle (seats,
steering wheel, wings, etc.),
-unless otherwise indicated, all repairs must be done
with the ignition off,
-when welding on the vehicle, it is advisable to remove
or disconnect components near the repair area that
could be affected by the heat,
-use recommended professional products and original
parts,
-observe the tightening torques,
-replace roll pins, self-locking or bonded nuts or bolts
every time they are removed,
-take care with electrical and electronic components
which cannot withstand excess voltage and improper
handling; replace any electrical and electronic com-
ponents which have experienced a voltage drop,
-make sure that the connectors are correctly clipped,
-do not pull on the wiring,
-check for the sealing plugs on the connectors,
-Do not splash any liquid, regardless of its type (oil,
cleaner, etc.), on the electric and electronic compo-
nents (computers, sensors, etc.)
-do not just replace parts one after the other, carry out
detailed fault finding beforehand,
-carry out a final check before returning the vehicle to
the customer (set the clock, check the alarm opera-
tion, check the lights and indicators etc.),
-clean and degrease the sections to be bonded
(threads, stub axle splines) to ensure proper adher-
ence,-protect the accessories and timing belts, the electrical
accessories (starter, blanking cover, electric power
assisted steering pump) and the mating face to pre-
vent diesel fuel spilling onto the clutch friction plate.
The design quality of our vehicles demands that noth-
ing is left to chance in making a good repair, and it is
essential to refit parts or components exactly as they
were originally (for instance: heat shields, wiring rout-
ing, pipe routing, particularly in the area of the exhaust
pipe).
Do not blow away asbestos particles or dust (brakes,
clutch, etc.), vacuum them up or clean the component
with a cleaning agent (such as a brake cleaning prod-
uct).
Use professional products and apply them with care,
for example do not apply too much sealing paste to the
sealing surface.
Exhaust gases (petrol and diesel) are pollutants. Oper-
ate engines with care and always use exhaust gas ex-
tractors.
Ensure that there is no risk of a short circuit occurring
when the electrical connections are reconnected (e.g.
starter, alternator, etc.). Some points need greasing,
others do not, therefore particular attention should be
paid during refitting operations to ensure that they work
properly under all conditions.
2 - Special tooling - ease of use
The repair procedures have been designed using spe-
cial tools; they must therefore be carried out using
these tools to ensure a high degree of working safety
and quality of repair.
The equipment we have approved has undergone
careful research and testing, and must be used and
maintained with care.
3 - Reliability - updating
New repair procedures are constantly being developed
in the interests of repair quality, either with new prod-
ucts (emission control, injection, electronics, etc.), or in
fault finding. Be sure to consult the Workshop Repair
Manuals or Technical Notes or fault finding summaries
before any servicing operation.
Since vehicle specifications are subject to change dur-
ing their commercial life, it is essential to check wheth-
er there are any updated Technical Notes when
seeking information.
Page 15 of 46
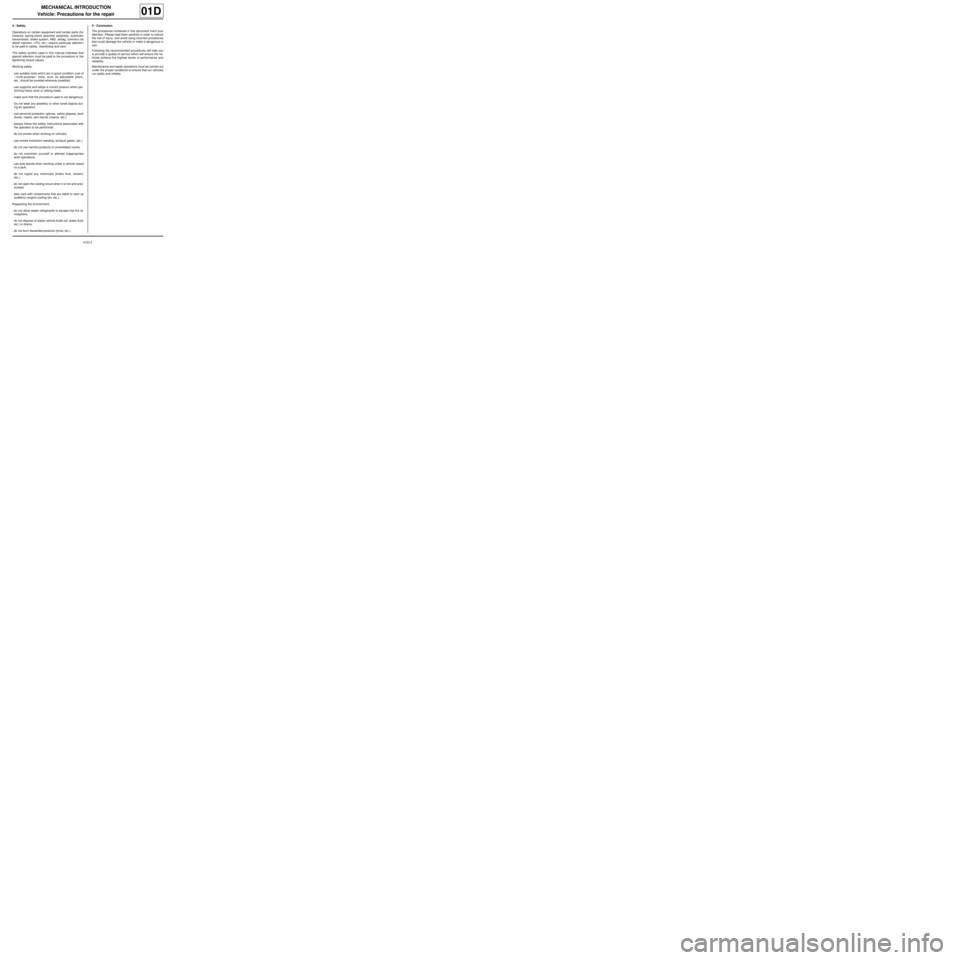
01D-2
MECHANICAL INTRODUCTION
Vehicle: Precautions for the repair
01D
4 - Safety
Operations on certain equipment and certain parts (for
instance: spring-shock absorber assembly, automatic
transmission, brake system, ABS, airbag, common rail
diesel injection, LPG, etc.) require particular attention
to be paid to safety, cleanliness and care.
The safety symbol used in this manual indicates that
special attention must be paid to the procedure or the
tightening torque values.
Working safely:
-use suitable tools which are in good condition (use of
« multi-purpose » tools, such as adjustable pliers,
etc., should be avoided wherever possible),
-use supports and adopt a correct posture when per-
forming heavy work or raising loads,
-make sure that the procedure used is not dangerous,
-Do not wear any jewellery or other small objects dur-
ing an operation,
-use personal protection (gloves, safety glasses, work
shoes, masks, skin barrier creams, etc.),
-always follow the safety instructions associated with
the operation to be performed,
-do not smoke when working on vehicles,
-use smoke extractors (welding, exhaust gases, etc.),
-do not use harmful products in unventilated rooms,
-do not overstrain yourself or attempt inappropriate
work operations,
-use axle stands when working under a vehicle raised
on a jack,
-do not ingest any chemicals (brake fluid, coolant,
etc.),
-do not open the cooling circuit when it is hot and pres-
surised,
-take care with components that are liable to start up
suddenly (engine cooling fan, etc.).
Respecting the environment:
-do not allow waste refrigerants to escape into the at-
mosphere,
-do not dispose of waste vehicle fluids (oil, brake fluid,
etc.) in drains,
-do not burn discarded products (tyres, etc.).5 - Conclusion
The procedures contained in this document merit your
attention. Please read them carefully in order to reduce
the risk of injury, and avoid using incorrect procedures
that could damage the vehicle or make it dangerous in
use.
Following the recommended procedures will help you
to provide a quality of service which will ensure the ve-
hicles achieve the highest levels of performance and
reliability.
Maintenance and repair operations must be carried out
under the proper conditions to ensure that our vehicles
run safely and reliably.
Page 16 of 46
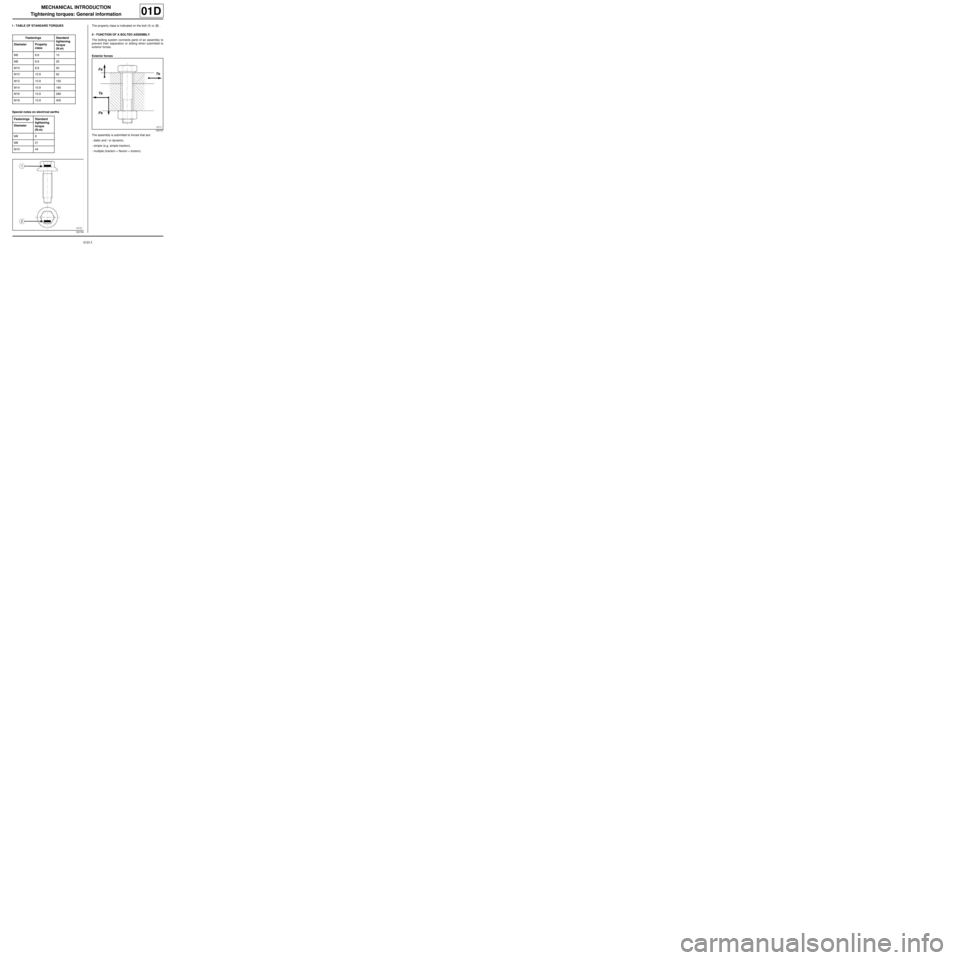
01D-3
MECHANICAL INTRODUCTION
Tightening torques: General information
01D
I - TABLE OF STANDARD TORQUES
Special notes on electrical earthsThe property class is indicated on the bolt (1) or (2) .
II - FUNCTION OF A BOLTED ASSEMBLY
The bolting system connects parts of an assembly to
prevent their separation or sliding when submitted to
exterior forces.
Exterior forces
The assembly is submitted to forces that are:
-static and / or dynamic,
-simple (e.g. simple traction),
-multiple (traction + flexion + torsion). Fastenings Standard
tightening
torque
(N.m) Diameter Property
class
M6 8.8 10
M8 8.8 25
M10 8.8 50
M10 10.9 62
M12 10.9 105
M14 10.9 180
M16 10.9 280
M18 10.9 400
Fastenings Standard
tightening
torque
(N.m) Diameter
M6 8
M8 21
M10 44
120736
120737
Page 17 of 46
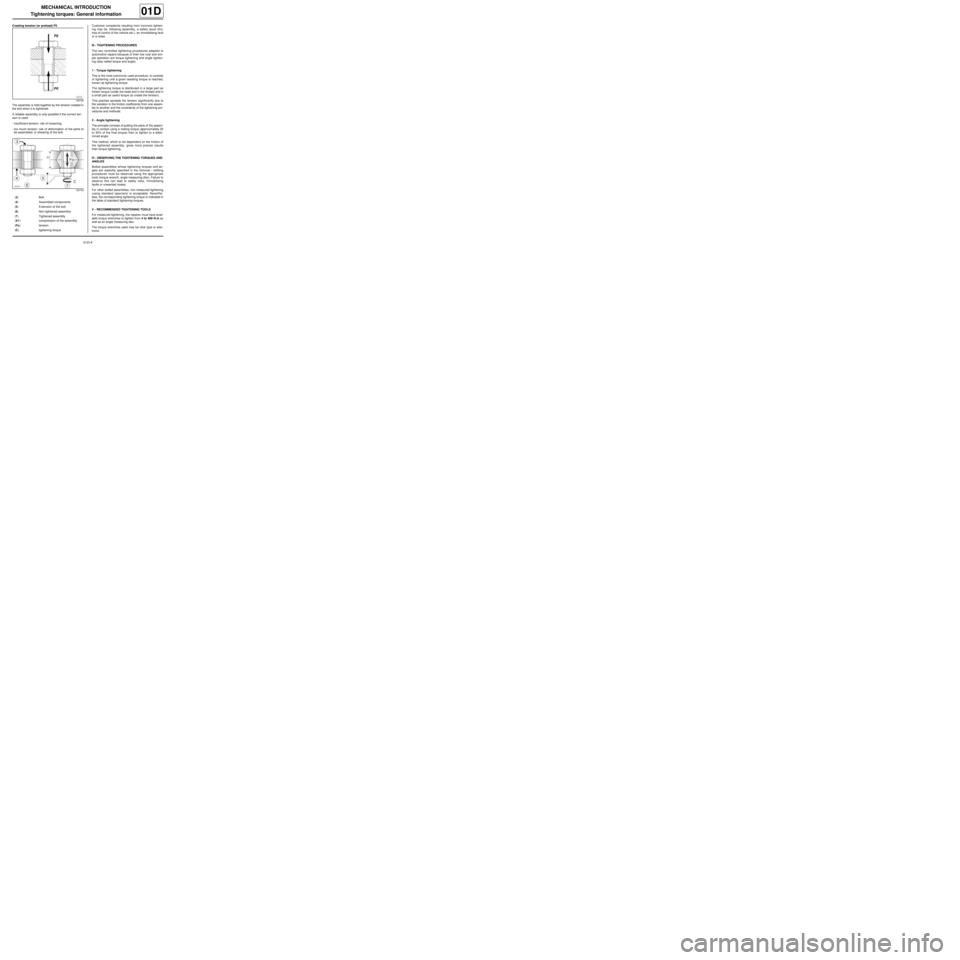
01D-4
MECHANICAL INTRODUCTION
Tightening torques: General information
01D
Creating tension (or preload) F0
The assembly is held together by the tension created in
the bolt when it is tightened.
A reliable assembly is only possible if the correct ten-
sion is used:
-insufficient tension: risk of loosening,
-too much tension: risk of deformation of the parts to
be assembled, or shearing of the bolt.Customer complaints resulting from incorrect tighten-
ing may be, following assembly, a safety issue (fire,
loss of control of the vehicle etc.), an immobilising fault
or a noise.
III - TIGHTENING PROCEDURES
The two controlled tightening procedures adapted to
automotive repairs because of their low cost and sim-
ple operation are torque tightening and angle tighten-
ing (also called torque and angle).
1 - Torque tightening
This is the most commonly used procedure. Is consists
of tightening until a given resisting torque is reached,
known as tightening torque.
The tightening torque is distributed in a large part as
friction torque (under the head and in the thread) and in
a small part as useful torque (to create the tension).
This practise spreads the tension significantly due to
the variation in the friction coefficients from one assem-
bly to another and the uncertainty of the tightening pro-
cedures and methods.
2 - Angle tightening
The principle consists of putting the parts of the assem-
bly in contact using a mating torque (approximately 25
to 30% of the final torque) then to tighten to a deter-
mined angle.
This method, which is not dependent on the friction of
the tightened assembly, gives more precise results
than torque tightening.
IV - OBSERVING THE TIGHTENING TORQUES AND
ANGLES
Bolted assemblies whose tightening torques and an-
gles are explicitly specified in the removal / refitting
procedures must be observed using the appropriate
tools (torque wrench, angle measuring disc). Failure to
observe this can lead to safety risks, immobilising
faults or unwanted noises.
For other bolted assemblies, non-measured tightening
(using standard spanners) is acceptable. Neverthe-
less, the corresponding tightening torque is indicated in
the table of standard tightening torques.
V - RECOMMENDED TIGHTENING TOOLS
For measured tightening, the repairer must have avail-
able torque wrenches to tighten from 4 to 400 N.m as
well as an angle measuring disc.
The torque wrenches used may be click type or elec-
tronic.
120738
120739
(3) Bolt
(4) Assembled components
(5) Extension of the bolt
(6) Non-tightened assembly
(7) Tightened assembly
(X1) compression of the assembly
(Fo) tension
(C) tightening torque
Page 18 of 46
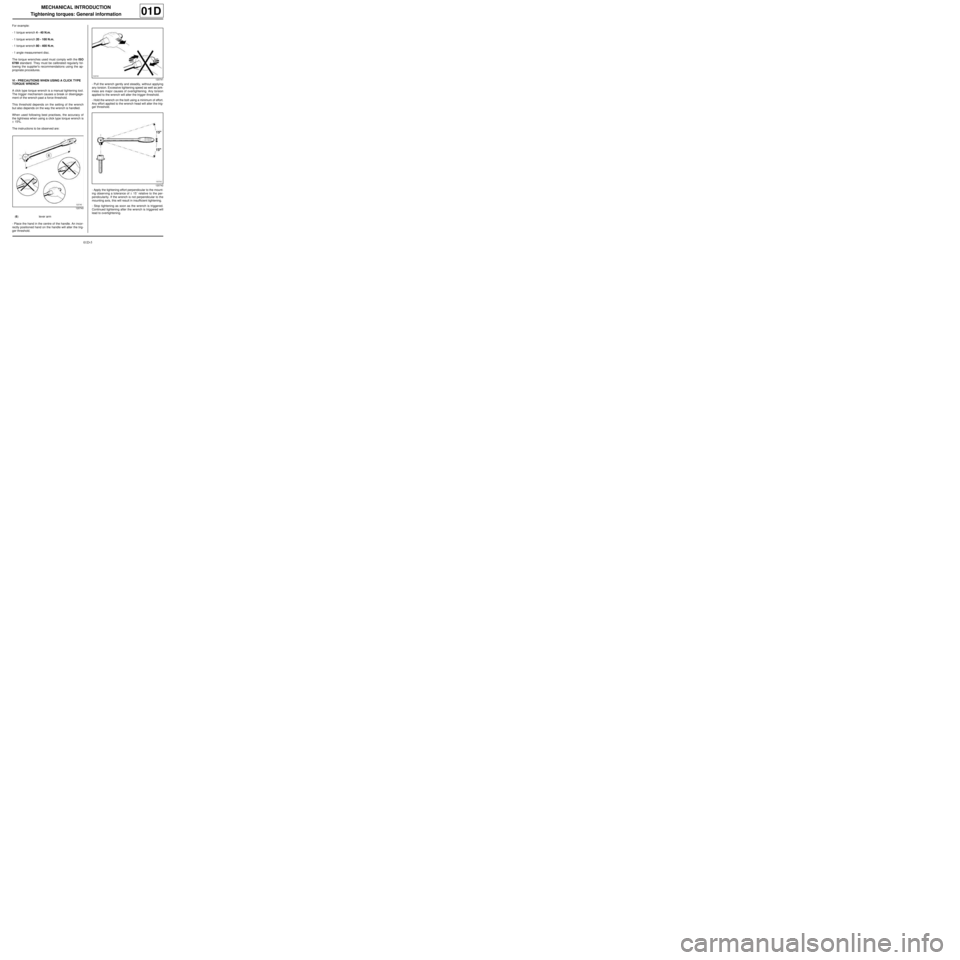
01D-5
MECHANICAL INTRODUCTION
Tightening torques: General information
01D
For example:
-1 torque wrench 4 - 40 N.m,
-1 torque wrench 20 - 100 N.m,
-1 torque wrench 80 - 400 N.m,
-1 angle measurement disc.
The torque wrenches used must comply with the ISO
6789 standard. They must be calibrated regularly fol-
lowing the supplier's recommendations using the ap-
propriate procedures.
VI - PRECAUTIONS WHEN USING A CLICK TYPE
TORQUE WRENCH
A click type torque wrench is a manual tightening tool.
The trigger mechanism causes a break or disengage-
ment of the wrench past a force threshold.
This threshold depends on the setting of the wrench
but also depends on the way the wrench is handled.
When used following best practises, the accuracy of
the tightness when using a click type torque wrench is
± 15%.
The instructions to be observed are:
- Place the hand in the centre of the handle. An incor-
rectly positioned hand on the handle will alter the trig-
ger threshold.- Pull the wrench gently and steadily, without applying
any torsion. Excessive tightening speed as well as jerk-
iness are major causes of overtightening. Any torsion
applied to the wrench will alter the trigger threshold.
- Hold the wrench on the bolt using a minimum of effort.
Any effort applied to the wrench head will alter the trig-
ger threshold.
- Apply the tightening effort perpendicular to the mount-
ing observing a tolerance of ± 15˚ relative to the per-
pendicularity. If the wrench is not perpendicular to the
mounting axis, this will result in insufficient tightening.
- Stop tightening as soon as the wrench is triggered.
Continued tightening after the wrench is triggered will
lead to overtightening.
120740
(6) lever arm
120741
120742
Page 19 of 46
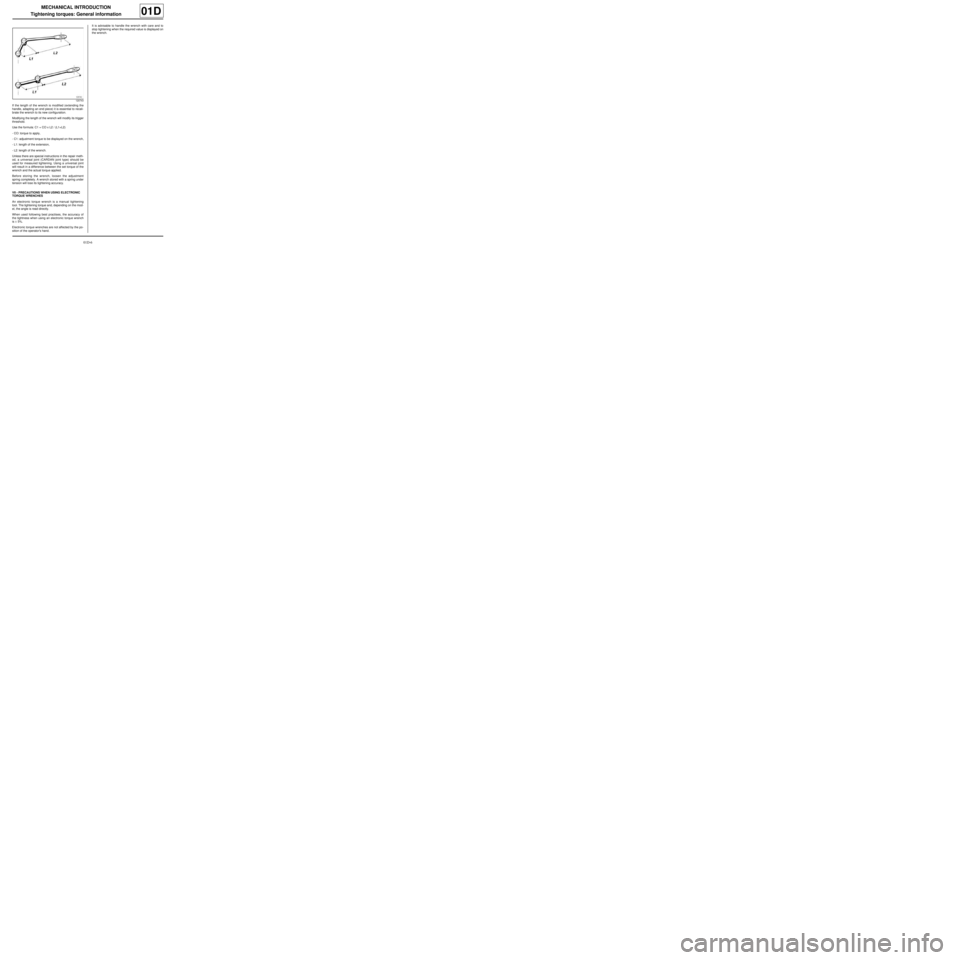
01D-6
MECHANICAL INTRODUCTION
Tightening torques: General information
01D
If the length of the wrench is modified (extending the
handle, adapting an end piece) it is essential to recali-
brate the wrench to its new configuration.
Modifying the length of the wrench will modify its trigger
threshold.
Use the formula: C1 = CO x L2 / (L1+L2)
-CO: torque to apply,
-C1: adjustment torque to be displayed on the wrench,
-L1: length of the extension,
-L2: length of the wrench.
Unless there are special instructions in the repair meth-
od, a universal joint (CARDAN joint type) should be
used for measured tightening. Using a universal joint
will result in a difference between the set torque of the
wrench and the actual torque applied.
Before storing the wrench, loosen the adjustment
spring completely. A wrench stored with a spring under
tension will lose its tightening accuracy.
VII - PRECAUTIONS WHEN USING ELECTRONIC
TORQUE WRENCHES
An electronic torque wrench is a manual tightening
tool. The tightening torque and, depending on the mod-
el, the angle is read directly.
When used following best practises, the accuracy of
the tightness when using an electronic torque wrench
is ± 5%.
Electronic torque wrenches are not affected by the po-
sition of the operator's hand.It is advisable to handle the wrench with care and to
stop tightening when the required value is displayed on
the wrench.
120743
Page 20 of 46

02A-1
LIFTING EQUIPMENT
Vehicle: Towing and lifting
02A
I - TOWING1 - Position of front attachment point
2 - Position of rear attachment point
II - LIFTING BY TROLLEY JACK Equipment required
Diagnostic tool
safety strap(s)
WARNING
See the current towing regulations in each country.
Never use the drive shafts as attachment points.
The towing points may only be used for towing on
the road.
Never use the towing points for removing the vehi-
cle from a ditch or to lift the vehicle, either directly
or indirectly.
Screw in and lock the towing ring before towing.
Vehicles fitted with automatic transmission:
-The vehicle should preferably be transported on a
platform or towed by lifting the front wheels. As an
exception, the vehicle may be towed with the
wheels on the ground but at a speed below 12
mph (20km/h) and over a maximum distance of
18 miles (30 kms) (with the gear lever in neutral).
Vehicles fitted with Renault Card:
-If the vehicle battery is flat, the steering column
remains locked. In this case, fit a new battery or
connect to an electrical source to lock the airbag
computer using the Diagnostic tool (see Airbag
and pretensioners: Precautions for the repair)
(88C, Airbag and pretensioners), which unlocks
the steering column.
-If it is not possible to lock the airbag computer, the
front of the vehicle must be lifted.
120735
120450
IMPORTANT
To prevent any accidents, the trolley jack must only
be used to lift and/or move the vehicle. The vehicle
height must be maintained with axle stands which
are strong enough to support the weight of the vehi-
cle.