lock SSANGYONG MUSSO 1998 Workshop Repair Manual
[x] Cancel search | Manufacturer: SSANGYONG, Model Year: 1998, Model line: MUSSO, Model: SSANGYONG MUSSO 1998Pages: 1463, PDF Size: 19.88 MB
Page 973 of 1463
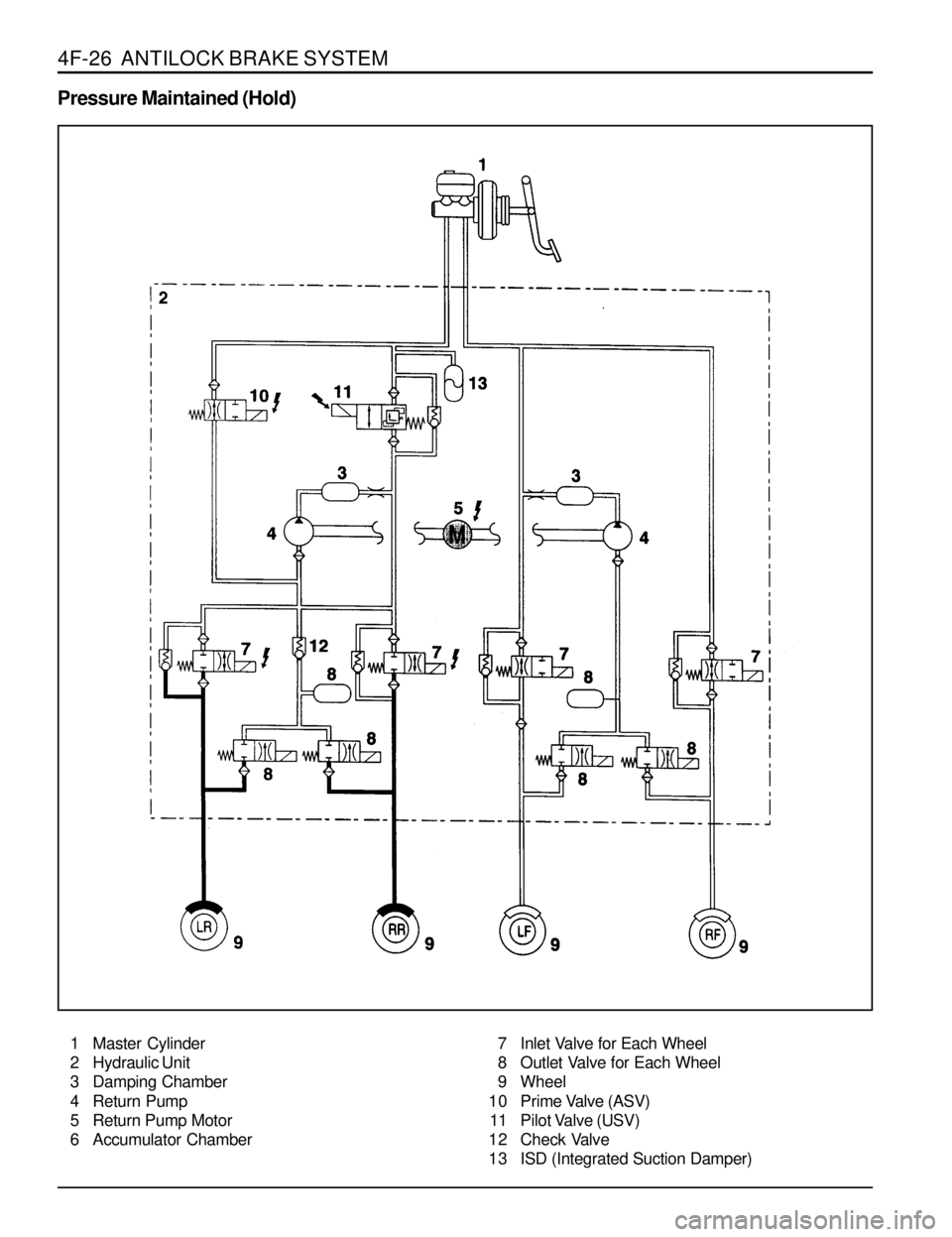
4F-26 ANTILOCK BRAKE SYSTEM
Pressure Maintained (Hold)
1 Master Cylinder
2 Hydraulic Unit
3 Damping Chamber
4 Return Pump
5 Return Pump Motor
6 Accumulator Chamber7 Inlet Valve for Each Wheel
8 Outlet Valve for Each Wheel
9 Wheel
10 Prime Valve (ASV)
11 Pilot Valve (USV)
12 Check Valve
13 ISD (Integrated Suction Damper)
Page 974 of 1463
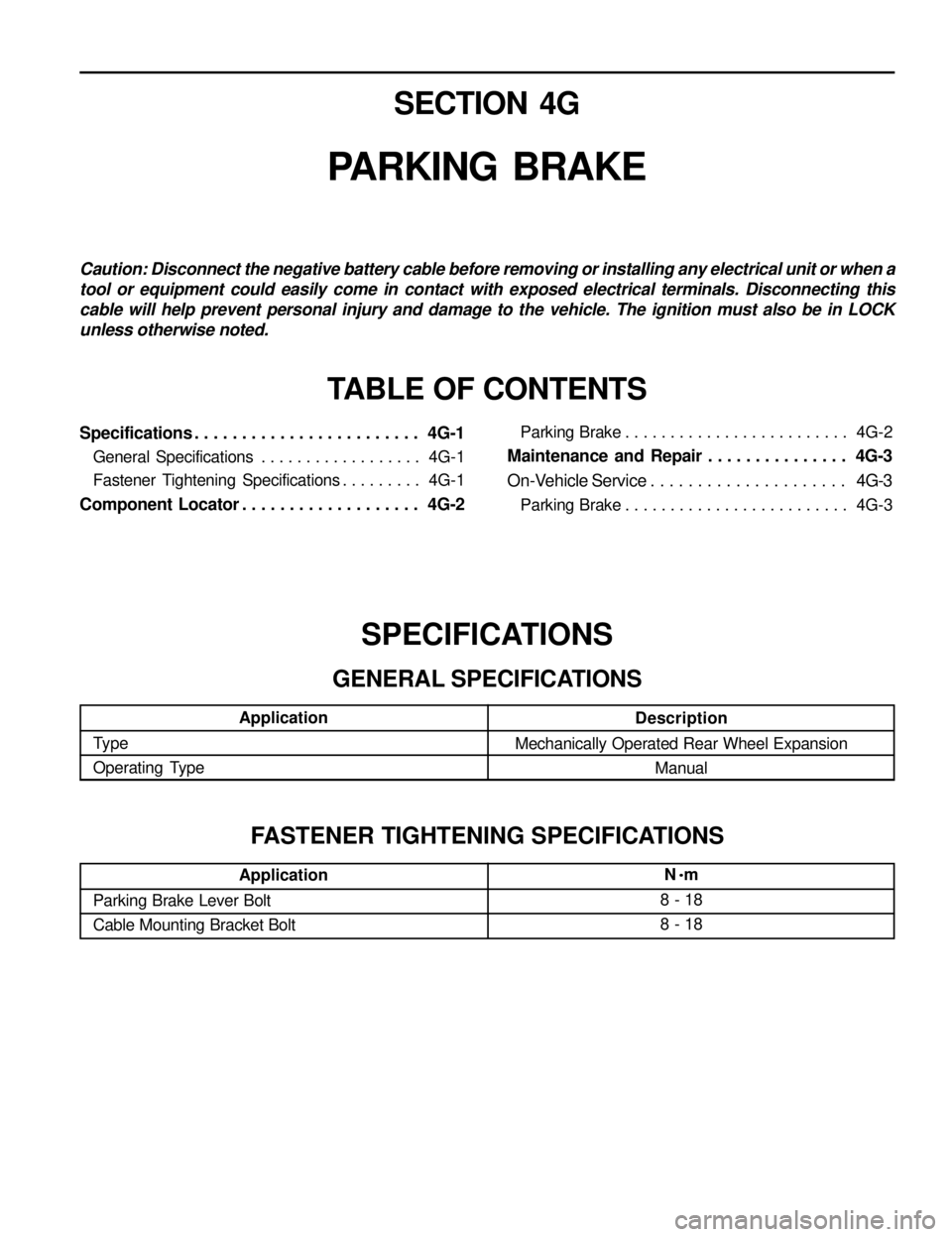
SECTION 4G
PARKING BRAKE
Specifications . . . . . . . . . . . . . . . . . . . . . . . . 4G-1
General Specifications . . . . . . . . . . . . . . . . . . 4G-1
Fastener Tightening Specifications . . . . . . . . . 4G-1
Component Locator . . . . . . . . . . . . . . . . . . . 4G-2
TABLE OF CONTENTS
Parking Brake . . . . . . . . . . . . . . . . . . . . . . . . . 4G-2
Maintenance and Repair . . . . . . . . . . . . . . . 4G-3
On-Vehicle Service . . . . . . . . . . . . . . . . . . . . . 4G-3
Parking Brake . . . . . . . . . . . . . . . . . . . . . . . . . 4G-3
Caution: Disconnect the negative battery cable before removing or installing any electrical unit or when a
tool or equipment could easily come in contact with exposed electrical terminals. Disconnecting this
cable will help prevent personal injury and damage to the vehicle. The ignition must also be in LOCK
unless otherwise noted.
SPECIFICATIONS
GENERAL SPECIFICATIONS
Application
Parking Brake Lever Bolt
Cable Mounting Bracket BoltN
· ·· ·
·m
8 - 18
8 - 18
FASTENER TIGHTENING SPECIFICATIONS
Application
Type
Operating TypeDescription
Mechanically Operated Rear Wheel Expansion
Manual
Page 978 of 1463
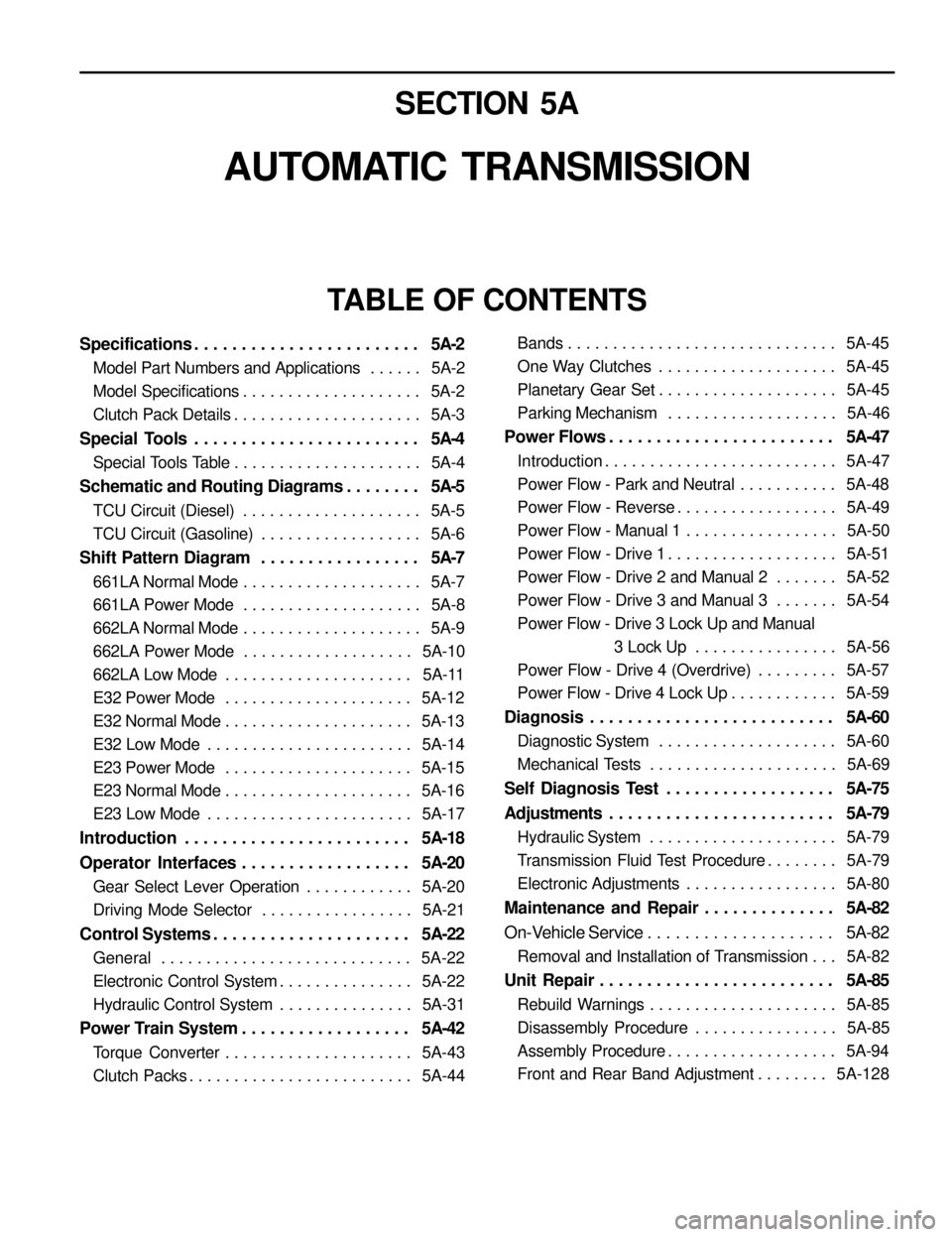
SECTION 5A
AUTOMATIC TRANSMISSION
TABLE OF CONTENTS
Specifications . . . . . . . . . . . . . . . . . . . . . . . . 5A-2
Model Part Numbers and Applications . . . . . . 5A-2
Model Specifications . . . . . . . . . . . . . . . . . . . . 5A-2
Clutch Pack Details . . . . . . . . . . . . . . . . . . . . . 5A-3
Special Tools . . . . . . . . . . . . . . . . . . . . . . . . 5A-4
Special Tools Table . . . . . . . . . . . . . . . . . . . . . 5A-4
Schematic and Routing Diagrams . . . . . . . . 5A-5
TCU Circuit (Diesel) . . . . . . . . . . . . . . . . . . . . 5A-5
TCU Circuit (Gasoline) . . . . . . . . . . . . . . . . . . 5A-6
Shift Pattern Diagram . . . . . . . . . . . . . . . . . 5A-7
661LA Normal Mode . . . . . . . . . . . . . . . . . . . . 5A-7
661LA Power Mode . . . . . . . . . . . . . . . . . . . . 5A-8
662LA Normal Mode . . . . . . . . . . . . . . . . . . . . 5A-9
662LA Power Mode . . . . . . . . . . . . . . . . . . . 5A-10
662LA Low Mode . . . . . . . . . . . . . . . . . . . . . 5A-11
E32 Power Mode . . . . . . . . . . . . . . . . . . . . . 5A-12
E32 Normal Mode . . . . . . . . . . . . . . . . . . . . . 5A-13
E32 Low Mode . . . . . . . . . . . . . . . . . . . . . . . 5A-14
E23 Power Mode . . . . . . . . . . . . . . . . . . . . . 5A-15
E23 Normal Mode . . . . . . . . . . . . . . . . . . . . . 5A-16
E23 Low Mode . . . . . . . . . . . . . . . . . . . . . . . 5A-17
Introduction . . . . . . . . . . . . . . . . . . . . . . . . 5A-18
Operator Interfaces . . . . . . . . . . . . . . . . . . 5A-20
Gear Select Lever Operation . . . . . . . . . . . . 5A-20
Driving Mode Selector . . . . . . . . . . . . . . . . . 5A-21
Control Systems . . . . . . . . . . . . . . . . . . . . . 5A-22
General . . . . . . . . . . . . . . . . . . . . . . . . . . . . 5A-22
Electronic Control System . . . . . . . . . . . . . . . 5A-22
Hydraulic Control System . . . . . . . . . . . . . . . 5A-31
Power Train System . . . . . . . . . . . . . . . . . . 5A-42
Torque Converter . . . . . . . . . . . . . . . . . . . . . 5A-43
Clutch Packs . . . . . . . . . . . . . . . . . . . . . . . . . 5A-44Bands . . . . . . . . . . . . . . . . . . . . . . . . . . . . . . 5A-45
One Way Clutches . . . . . . . . . . . . . . . . . . . . 5A-45
Planetary Gear Set . . . . . . . . . . . . . . . . . . . . 5A-45
Parking Mechanism . . . . . . . . . . . . . . . . . . . 5A-46
Power Flows . . . . . . . . . . . . . . . . . . . . . . . . 5A-47
Introduction . . . . . . . . . . . . . . . . . . . . . . . . . . 5A-47
Power Flow - Park and Neutral . . . . . . . . . . . 5A-48
Power Flow - Reverse . . . . . . . . . . . . . . . . . . 5A-49
Power Flow - Manual 1 . . . . . . . . . . . . . . . . . 5A-50
Power Flow - Drive 1 . . . . . . . . . . . . . . . . . . . 5A-51
Power Flow - Drive 2 and Manual 2 . . . . . . . 5A-52
Power Flow - Drive 3 and Manual 3 . . . . . . . 5A-54
Power Flow - Drive 3 Lock Up and Manual
3 Lock Up . . . . . . . . . . . . . . . . 5A-56
Power Flow - Drive 4 (Overdrive) . . . . . . . . . 5A-57
Power Flow - Drive 4 Lock Up . . . . . . . . . . . . 5A-59
Diagnosis . . . . . . . . . . . . . . . . . . . . . . . . . . 5A-60
Diagnostic System . . . . . . . . . . . . . . . . . . . . 5A-60
Mechanical Tests . . . . . . . . . . . . . . . . . . . . . 5A-69
Self Diagnosis Test . . . . . . . . . . . . . . . . . . 5A-75
Adjustments . . . . . . . . . . . . . . . . . . . . . . . . 5A-79
Hydraulic System . . . . . . . . . . . . . . . . . . . . . 5A-79
Transmission Fluid Test Procedure . . . . . . . . 5A-79
Electronic Adjustments . . . . . . . . . . . . . . . . . 5A-80
Maintenance and Repair . . . . . . . . . . . . . . 5A-82
On-Vehicle Service . . . . . . . . . . . . . . . . . . . . 5A-82
Removal and Installation of Transmission . . . 5A-82
Unit Repair . . . . . . . . . . . . . . . . . . . . . . . . . 5A-85
Rebuild Warnings . . . . . . . . . . . . . . . . . . . . . 5A-85
Disassembly Procedure . . . . . . . . . . . . . . . . 5A-85
Assembly Procedure . . . . . . . . . . . . . . . . . . . 5A-94
Front and Rear Band Adjustment . . . . . . . . 5A-128
Page 981 of 1463
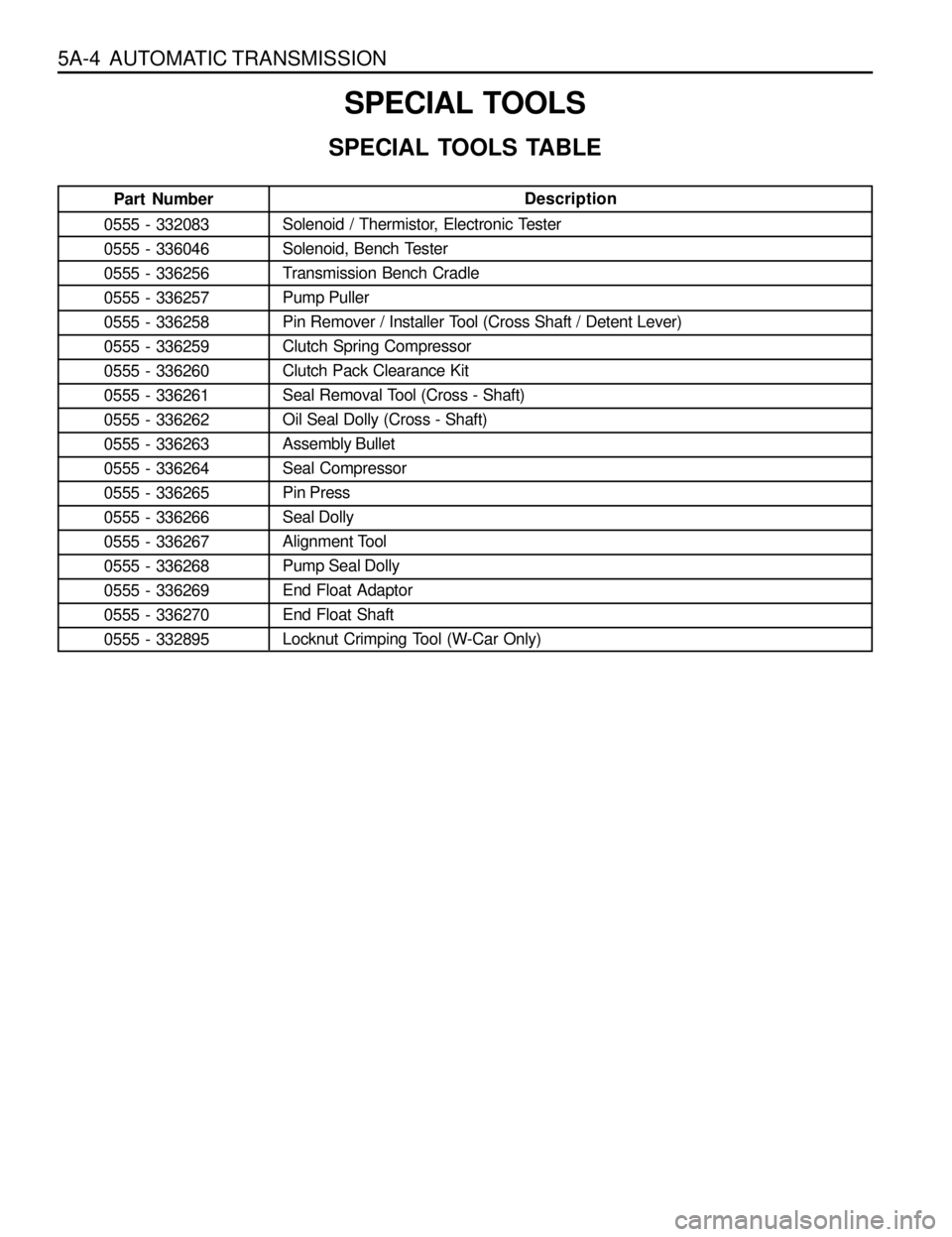
5A-4 AUTOMATIC TRANSMISSION
SPECIAL TOOLS
SPECIAL TOOLS TABLE
Part Number
0555 - 332083
0555 - 336046
0555 - 336256
0555 - 336257
0555 - 336258
0555 - 336259
0555 - 336260
0555 - 336261
0555 - 336262
0555 - 336263
0555 - 336264
0555 - 336265
0555 - 336266
0555 - 336267
0555 - 336268
0555 - 336269
0555 - 336270
0555 - 332895Description
Solenoid / Thermistor, Electronic Tester
Solenoid, Bench Tester
Transmission Bench Cradle
Pump Puller
Pin Remover / Installer Tool (Cross Shaft / Detent Lever)
Clutch Spring Compressor
Clutch Pack Clearance Kit
Seal Removal Tool (Cross - Shaft)
Oil Seal Dolly (Cross - Shaft)
Assembly Bullet
Seal Compressor
Pin Press
Seal Dolly
Alignment Tool
Pump Seal Dolly
End Float Adaptor
End Float Shaft
Locknut Crimping Tool (W-Car Only)
Page 995 of 1463
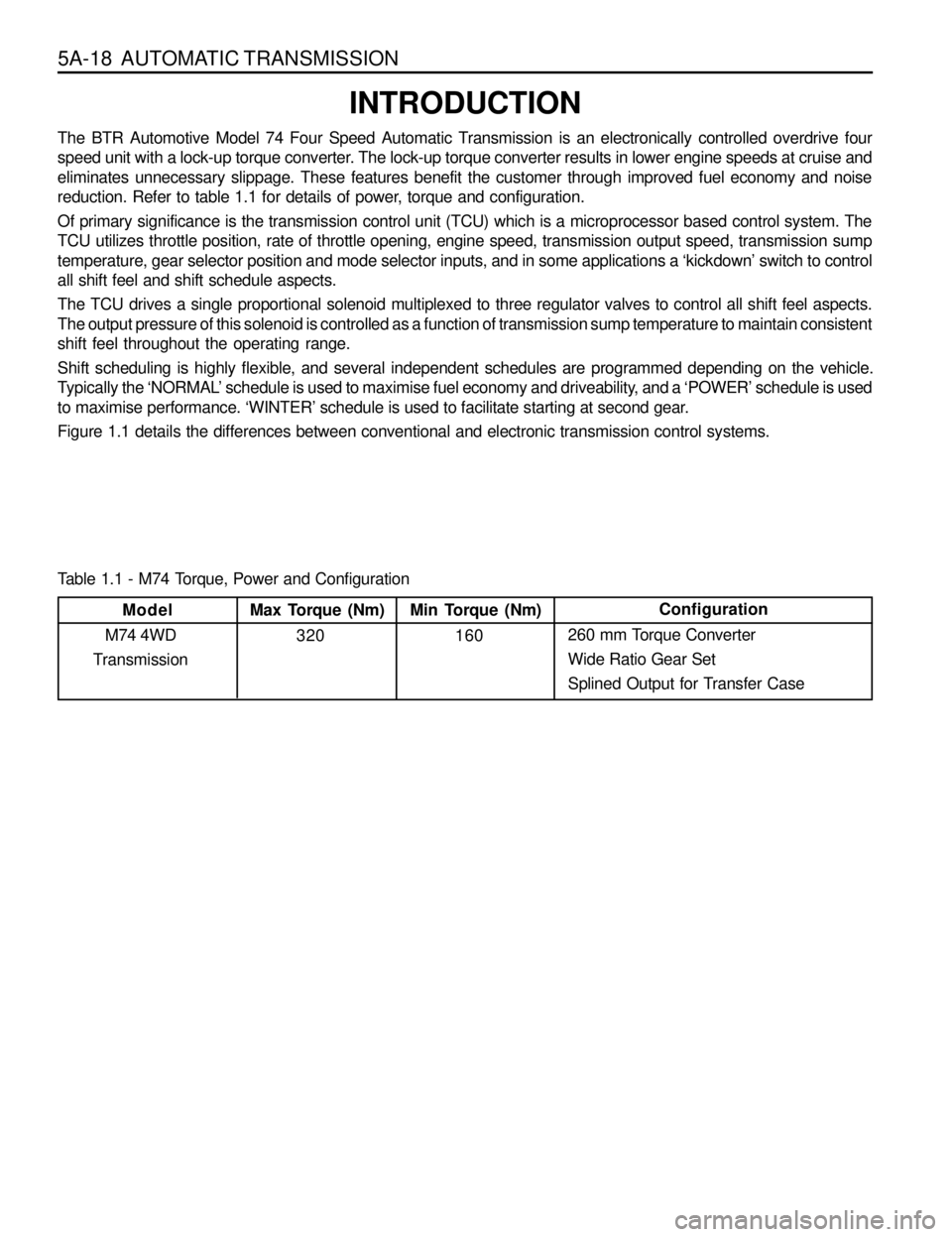
5A-18 AUTOMATIC TRANSMISSION
INTRODUCTION
The BTR Automotive Model 74 Four Speed Automatic Transmission is an electronically controlled overdrive four
speed unit with a lock-up torque converter. The lock-up torque converter results in lower engine speeds at cruise and
eliminates unnecessary slippage. These features benefit the customer through improved fuel economy and noise
reduction. Refer to table 1.1 for details of power, torque and configuration.
Of primary significance is the transmission control unit (TCU) which is a microprocessor based control system. The
TCU utilizes throttle position, rate of throttle opening, engine speed, transmission output speed, transmission sump
temperature, gear selector position and mode selector inputs, and in some applications a ‘kickdown’ switch to control
all shift feel and shift schedule aspects.
The TCU drives a single proportional solenoid multiplexed to three regulator valves to control all shift feel aspects.
The output pressure of this solenoid is controlled as a function of transmission sump temperature to maintain consistent
shift feel throughout the operating range.
Shift scheduling is highly flexible, and several independent schedules are programmed depending on the vehicle.
Typically the ‘NORMAL’ schedule is used to maximise fuel economy and driveability, and a ‘POWER’ schedule is used
to maximise performance. ‘WINTER’ schedule is used to facilitate starting at second gear.
Figure 1.1 details the differences between conventional and electronic transmission control systems.
Max Torque (Nm)
320Configuration
260 mm Torque Converter
Wide Ratio Gear Set
Splined Output for Transfer CaseMin Torque (Nm)
160 Model
M74 4WD
Transmission Table 1.1 - M74 Torque, Power and Configuration
Page 998 of 1463
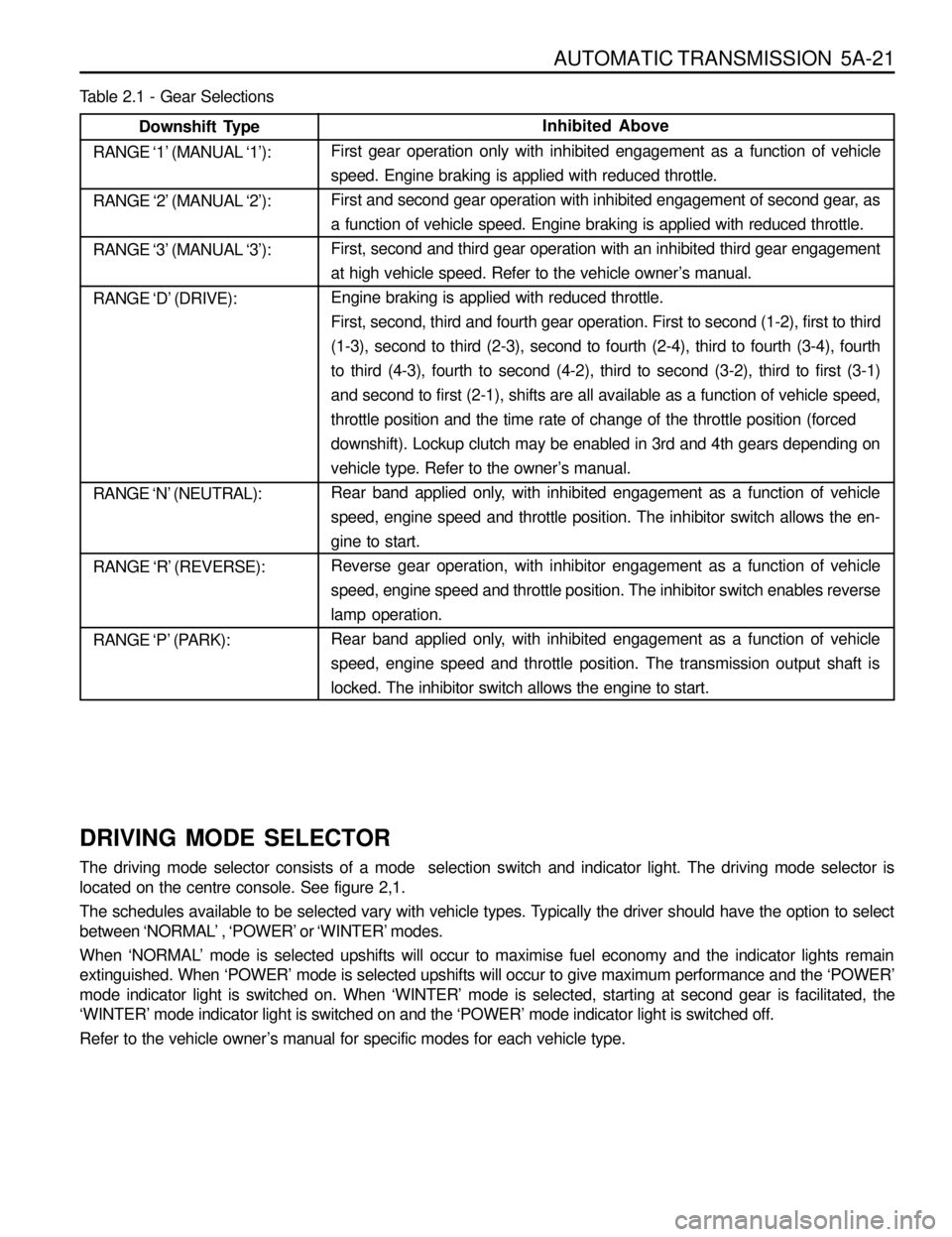
AUTOMATIC TRANSMISSION 5A-21
Downshift Type
RANGE ‘1’ (MANUAL ‘1’):
RANGE ‘2’ (MANUAL ‘2’):
RANGE ‘3’ (MANUAL ‘3’):
RANGE ‘D’ (DRIVE):
RANGE ‘N’ (NEUTRAL):
RANGE ‘R’ (REVERSE):
RANGE ‘P’ (PARK):Inhibited Above
First gear operation only with inhibited engagement as a function of vehicle
speed. Engine braking is applied with reduced throttle.
First and second gear operation with inhibited engagement of second gear, as
a function of vehicle speed. Engine braking is applied with reduced throttle.
First, second and third gear operation with an inhibited third gear engagement
at high vehicle speed. Refer to the vehicle owner’s manual.
Engine braking is applied with reduced throttle.
First, second, third and fourth gear operation. First to second (1-2), first to third
(1-3), second to third (2-3), second to fourth (2-4), third to fourth (3-4), fourth
to third (4-3), fourth to second (4-2), third to second (3-2), third to first (3-1)
and second to first (2-1), shifts are all available as a function of vehicle speed,
throttle position and the time rate of change of the throttle position (forced
downshift). Lockup clutch may be enabled in 3rd and 4th gears depending on
vehicle type. Refer to the owner’s manual.
Rear band applied only, with inhibited engagement as a function of vehicle
speed, engine speed and throttle position. The inhibitor switch allows the en-
gine to start.
Reverse gear operation, with inhibitor engagement as a function of vehicle
speed, engine speed and throttle position. The inhibitor switch enables reverse
lamp operation.
Rear band applied only, with inhibited engagement as a function of vehicle
speed, engine speed and throttle position. The transmission output shaft is
locked. The inhibitor switch allows the engine to start.
Table 2.1 - Gear Selections
DRIVING MODE SELECTOR
The driving mode selector consists of a mode selection switch and indicator light. The driving mode selector is
located on the centre console. See figure 2,1.
The schedules available to be selected vary with vehicle types. Typically the driver should have the option to select
between ‘NORMAL’ , ‘POWER’ or ‘WINTER’ modes.
When ‘NORMAL’ mode is selected upshifts will occur to maximise fuel economy and the indicator lights remain
extinguished. When ‘POWER’ mode is selected upshifts will occur to give maximum performance and the ‘POWER’
mode indicator light is switched on. When ‘WINTER’ mode is selected, starting at second gear is facilitated, the
‘WINTER’ mode indicator light is switched on and the ‘POWER’ mode indicator light is switched off.
Refer to the vehicle owner’s manual for specific modes for each vehicle type.
Page 999 of 1463
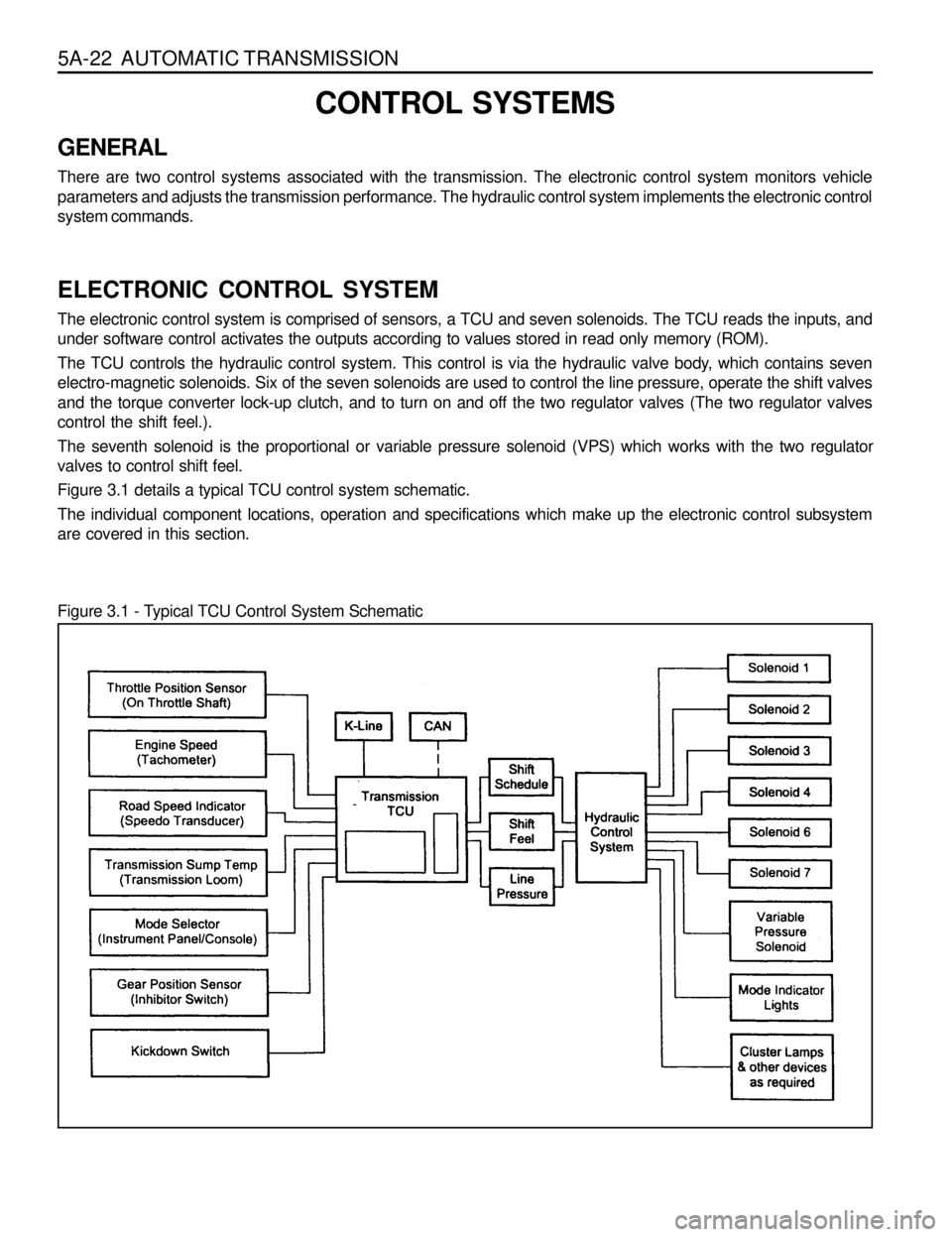
5A-22 AUTOMATIC TRANSMISSION
CONTROL SYSTEMS
GENERAL
There are two control systems associated with the transmission. The electronic control system monitors vehicle
parameters and adjusts the transmission performance. The hydraulic control system implements the electronic control
system commands.
ELECTRONIC CONTROL SYSTEM
The electronic control system is comprised of sensors, a TCU and seven solenoids. The TCU reads the inputs, and
under software control activates the outputs according to values stored in read only memory (ROM).
The TCU controls the hydraulic control system. This control is via the hydraulic valve body, which contains seven
electro-magnetic solenoids. Six of the seven solenoids are used to control the line pressure, operate the shift valves
and the torque converter lock-up clutch, and to turn on and off the two regulator valves (The two regulator valves
control the shift feel.).
The seventh solenoid is the proportional or variable pressure solenoid (VPS) which works with the two regulator
valves to control shift feel.
Figure 3.1 details a typical TCU control system schematic.
The individual component locations, operation and specifications which make up the electronic control subsystem
are covered in this section.
Figure 3.1 - Typical TCU Control System Schematic
Page 1002 of 1463
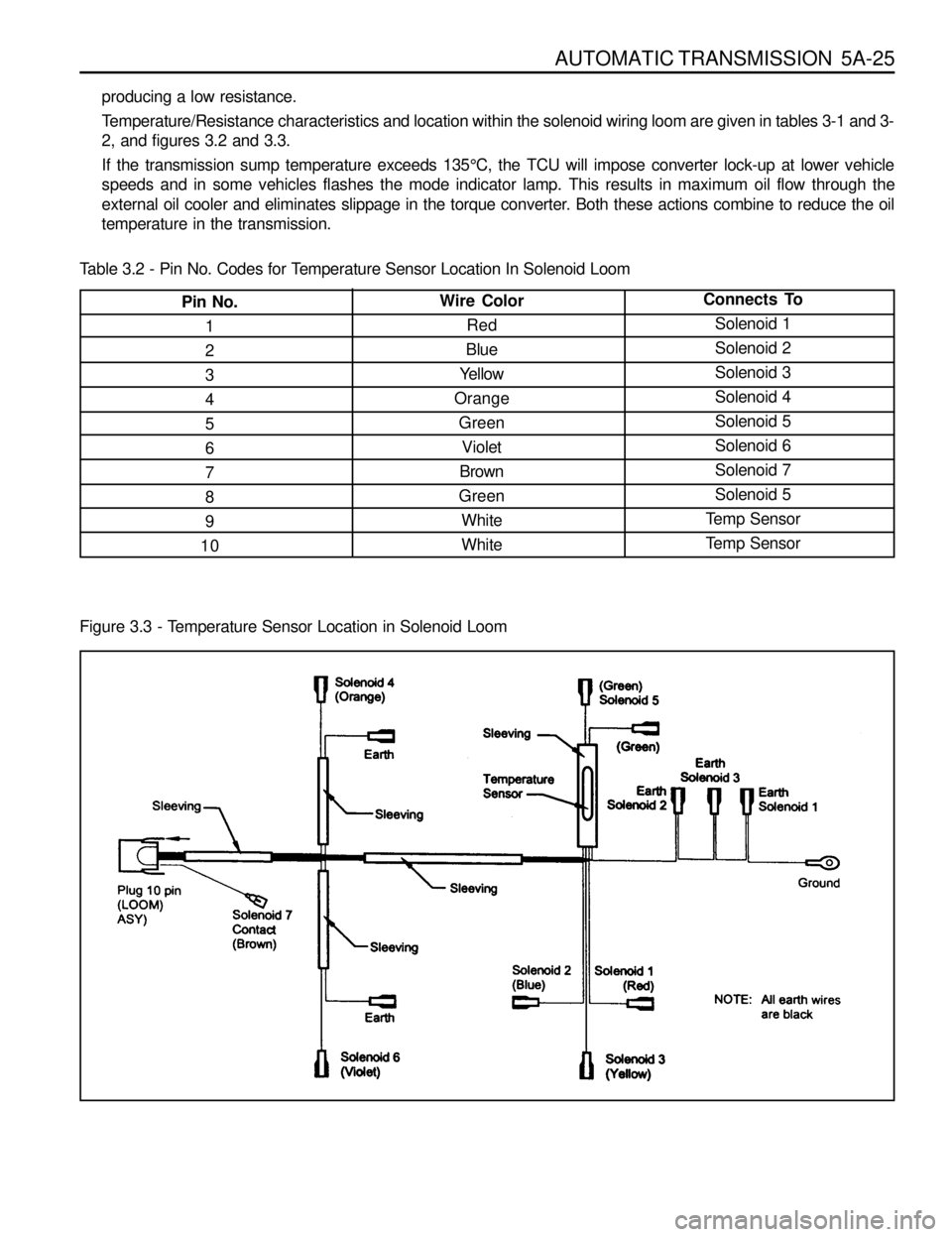
AUTOMATIC TRANSMISSION 5A-25
producing a low resistance.
Temperature/Resistance characteristics and location within the solenoid wiring loom are given in tables 3-1 and 3-
2, and figures 3.2 and 3.3.
If the transmission sump temperature exceeds 135°C, the TCU will impose converter lock-up at lower vehicle
speeds and in some vehicles flashes the mode indicator lamp. This results in maximum oil flow through the
external oil cooler and eliminates slippage in the torque converter. Both these actions combine to reduce the oil
temperature in the transmission.
Connects To
Solenoid 1
Solenoid 2
Solenoid 3
Solenoid 4
Solenoid 5
Solenoid 6
Solenoid 7
Solenoid 5
Temp Sensor
Temp SensorWire Color
Red
Blue
Yellow
Orange
Green
Violet
Brown
Green
White
WhitePin No.
1
2
3
4
5
6
7
8
9
10
Table 3.2 - Pin No. Codes for Temperature Sensor Location In Solenoid Loom
Figure 3.3 - Temperature Sensor Location in Solenoid Loom
Page 1008 of 1463
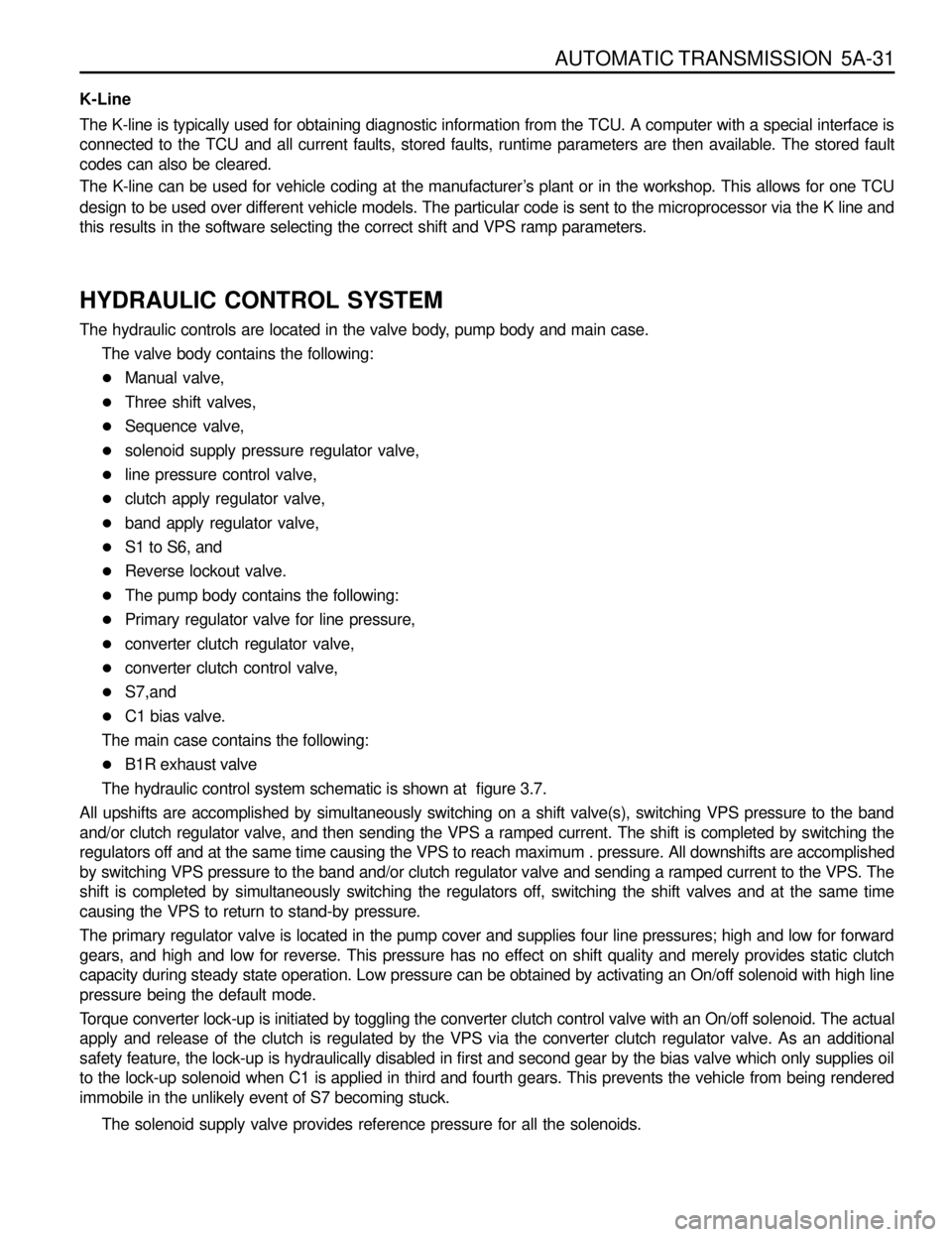
AUTOMATIC TRANSMISSION 5A-31
K-Line
The K-line is typically used for obtaining diagnostic information from the TCU. A computer with a special interface is
connected to the TCU and all current faults, stored faults, runtime parameters are then available. The stored fault
codes can also be cleared.
The K-line can be used for vehicle coding at the manufacturer’s plant or in the workshop. This allows for one TCU
design to be used over different vehicle models. The particular code is sent to the microprocessor via the K line and
this results in the software selecting the correct shift and VPS ramp parameters.
HYDRAULIC CONTROL SYSTEM
The hydraulic controls are located in the valve body, pump body and main case.
The valve body contains the following:
lManual valve,
lThree shift valves,
lSequence valve,
lsolenoid supply pressure regulator valve,
lline pressure control valve,
lclutch apply regulator valve,
lband apply regulator valve,
lS1 to S6, and
lReverse lockout valve.
lThe pump body contains the following:
lPrimary regulator valve for line pressure,
lconverter clutch regulator valve,
lconverter clutch control valve,
lS7,and
lC1 bias valve.
The main case contains the following:
lB1R exhaust valve
The hydraulic control system schematic is shown at figure 3.7.
All upshifts are accomplished by simultaneously switching on a shift valve(s), switching VPS pressure to the band
and/or clutch regulator valve, and then sending the VPS a ramped current. The shift is completed by switching the
regulators off and at the same time causing the VPS to reach maximum . pressure. All downshifts are accomplished
by switching VPS pressure to the band and/or clutch regulator valve and sending a ramped current to the VPS. The
shift is completed by simultaneously switching the regulators off, switching the shift valves and at the same time
causing the VPS to return to stand-by pressure.
The primary regulator valve is located in the pump cover and supplies four line pressures; high and low for forward
gears, and high and low for reverse. This pressure has no effect on shift quality and merely provides static clutch
capacity during steady state operation. Low pressure can be obtained by activating an On/off solenoid with high line
pressure being the default mode.
Torque converter lock-up is initiated by toggling the converter clutch control valve with an On/off solenoid. The actual
apply and release of the clutch is regulated by the VPS via the converter clutch regulator valve. As an additional
safety feature, the lock-up is hydraulically disabled in first and second gear by the bias valve which only supplies oil
to the lock-up solenoid when C1 is applied in third and fourth gears. This prevents the vehicle from being rendered
immobile in the unlikely event of S7 becoming stuck.
The solenoid supply valve provides reference pressure for all the solenoids.
Page 1015 of 1463
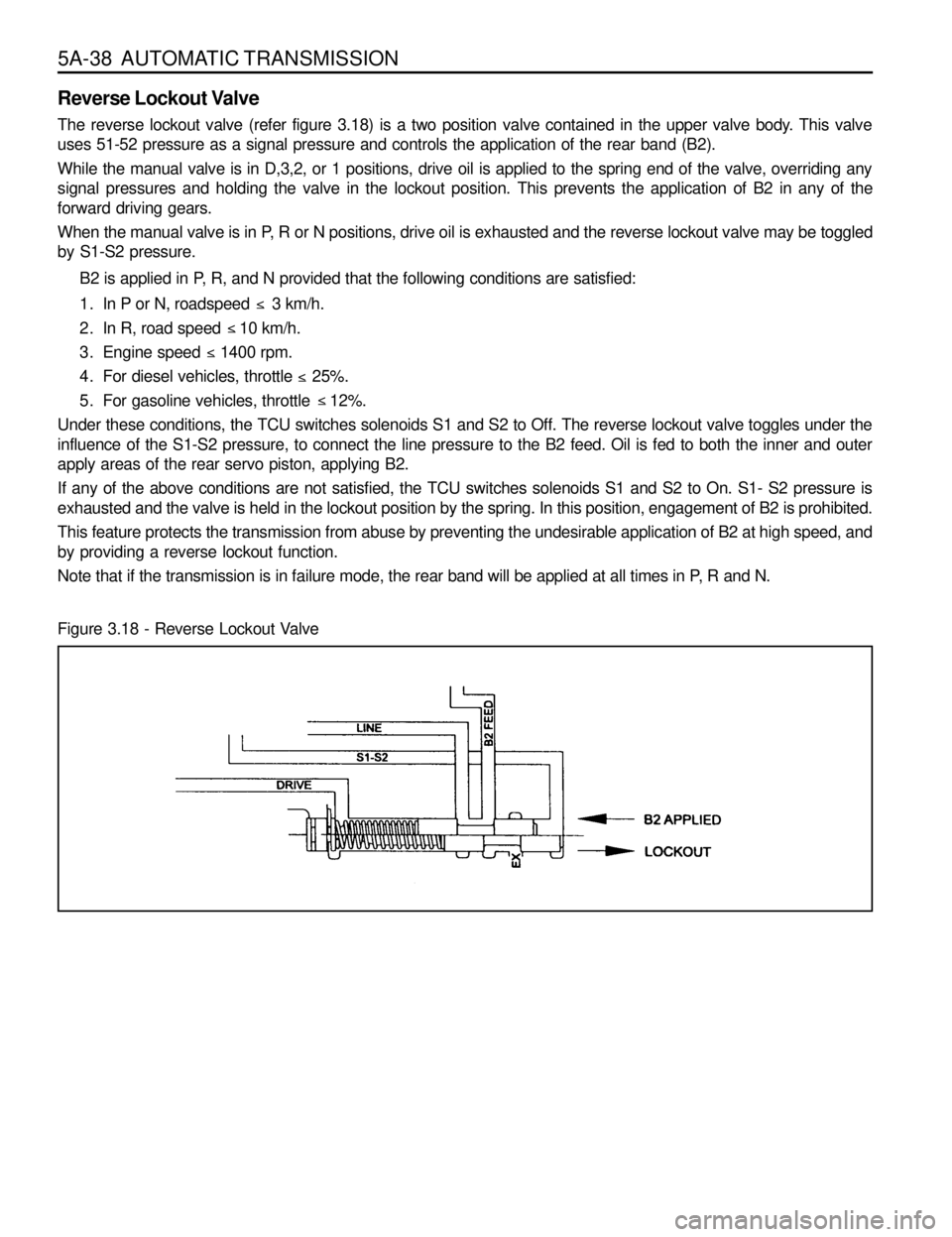
5A-38 AUTOMATIC TRANSMISSION
Reverse Lockout Valve
The reverse lockout valve (refer figure 3.18) is a two position valve contained in the upper valve body. This valve
uses 51-52 pressure as a signal pressure and controls the application of the rear band (B2).
While the manual valve is in D,3,2, or 1 positions, drive oil is applied to the spring end of the valve, overriding any
signal pressures and holding the valve in the lockout position. This prevents the application of B2 in any of the
forward driving gears.
When the manual valve is in P, R or N positions, drive oil is exhausted and the reverse lockout valve may be toggled
by S1-S2 pressure.
B2 is applied in P, R, and N provided that the following conditions are satisfied:
1. In P or N, roadspeed 3 km/h.
2. In R, road speed 10 km/h.
3. Engine speed 1400 rpm.
4. For diesel vehicles, throttle 25%.
5. For gasoline vehicles, throttle 12%.
Under these conditions, the TCU switches solenoids S1 and S2 to Off. The reverse lockout valve toggles under the
influence of the S1-S2 pressure, to connect the line pressure to the B2 feed. Oil is fed to both the inner and outer
apply areas of the rear servo piston, applying B2.
If any of the above conditions are not satisfied, the TCU switches solenoids S1 and S2 to On. S1- S2 pressure is
exhausted and the valve is held in the lockout position by the spring. In this position, engagement of B2 is prohibited.
This feature protects the transmission from abuse by preventing the undesirable application of B2 at high speed, and
by providing a reverse lockout function.
Note that if the transmission is in failure mode, the rear band will be applied at all times in P, R and N.
Figure 3.18 - Reverse Lockout Valve
<
<
<
<
<