lock SSANGYONG MUSSO 1998 Workshop Repair Manual
[x] Cancel search | Manufacturer: SSANGYONG, Model Year: 1998, Model line: MUSSO, Model: SSANGYONG MUSSO 1998Pages: 1463, PDF Size: 19.88 MB
Page 1029 of 1463
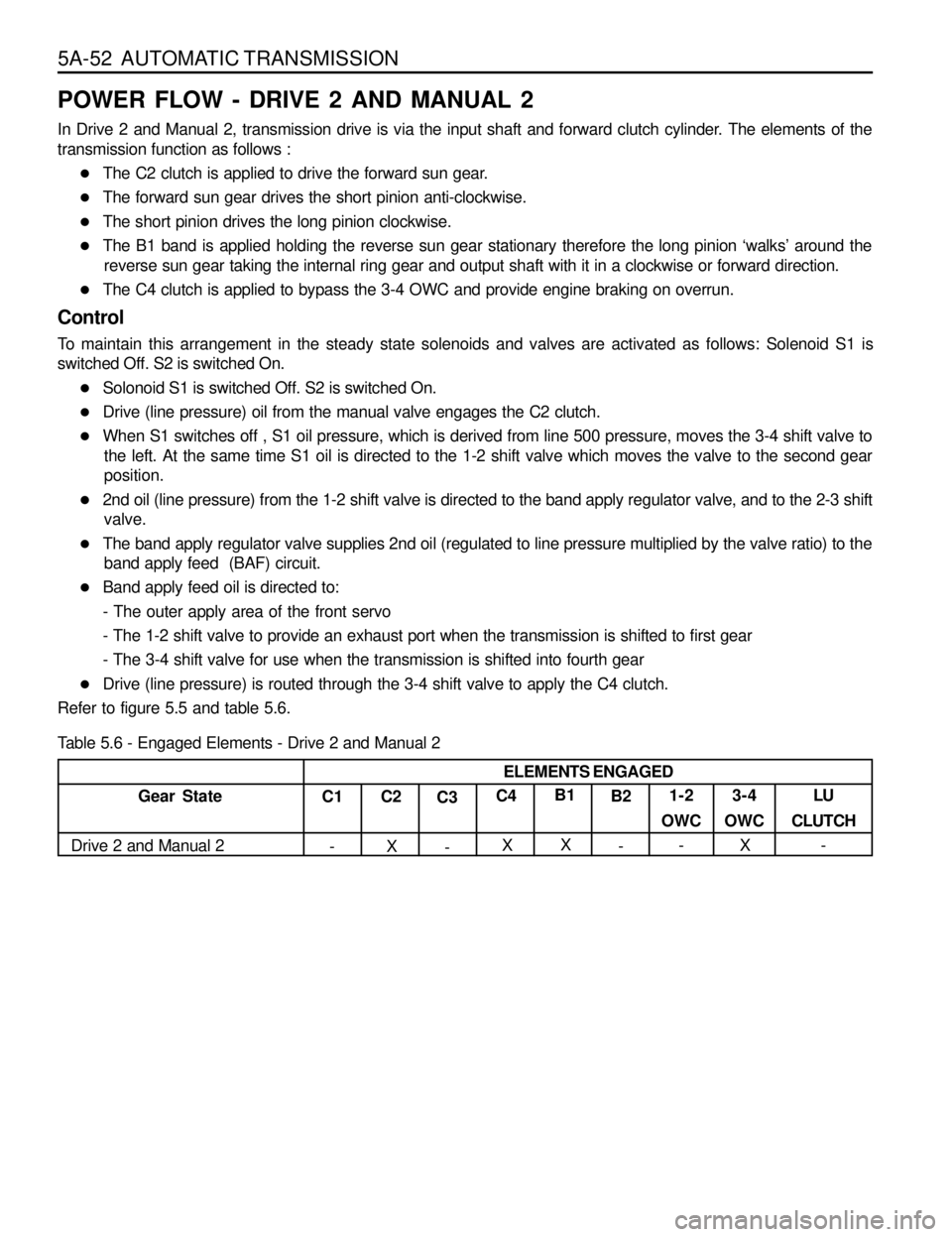
5A-52 AUTOMATIC TRANSMISSION
POWER FLOW - DRIVE 2 AND MANUAL 2
In Drive 2 and Manual 2, transmission drive is via the input shaft and forward clutch cylinder. The elements of the
transmission function as follows :
lThe C2 clutch is applied to drive the forward sun gear.
lThe forward sun gear drives the short pinion anti-clockwise.
lThe short pinion drives the long pinion clockwise.
lThe B1 band is applied holding the reverse sun gear stationary therefore the long pinion ‘walks’ around the
reverse sun gear taking the internal ring gear and output shaft with it in a clockwise or forward direction.
lThe C4 clutch is applied to bypass the 3-4 OWC and provide engine braking on overrun.
Control
To maintain this arrangement in the steady state solenoids and valves are activated as follows: Solenoid S1 is
switched Off. S2 is switched On.
lSolonoid S1 is switched Off. S2 is switched On.
lDrive (line pressure) oil from the manual valve engages the C2 clutch.
lWhen S1 switches off , S1 oil pressure, which is derived from line 500 pressure, moves the 3-4 shift valve to
the left. At the same time S1 oil is directed to the 1-2 shift valve which moves the valve to the second gear
position.
l2nd oil (line pressure) from the 1-2 shift valve is directed to the band apply regulator valve, and to the 2-3 shift
valve.
lThe band apply regulator valve supplies 2nd oil (regulated to line pressure multiplied by the valve ratio) to the
band apply feed (BAF) circuit.
lBand apply feed oil is directed to:
- The outer apply area of the front servo
- The 1-2 shift valve to provide an exhaust port when the transmission is shifted to first gear
- The 3-4 shift valve for use when the transmission is shifted into fourth gear
lDrive (line pressure) is routed through the 3-4 shift valve to apply the C4 clutch.
Refer to figure 5.5 and table 5.6.
Table 5.6 - Engaged Elements - Drive 2 and Manual 2
Gear State
Drive 2 and Manual 2C1
-C2
XC3
-C4
XB1
XB2
-1-2
OWC
-3-4
OWC
XLU
CLUTCH
- ELEMENTS ENGAGED
Page 1031 of 1463
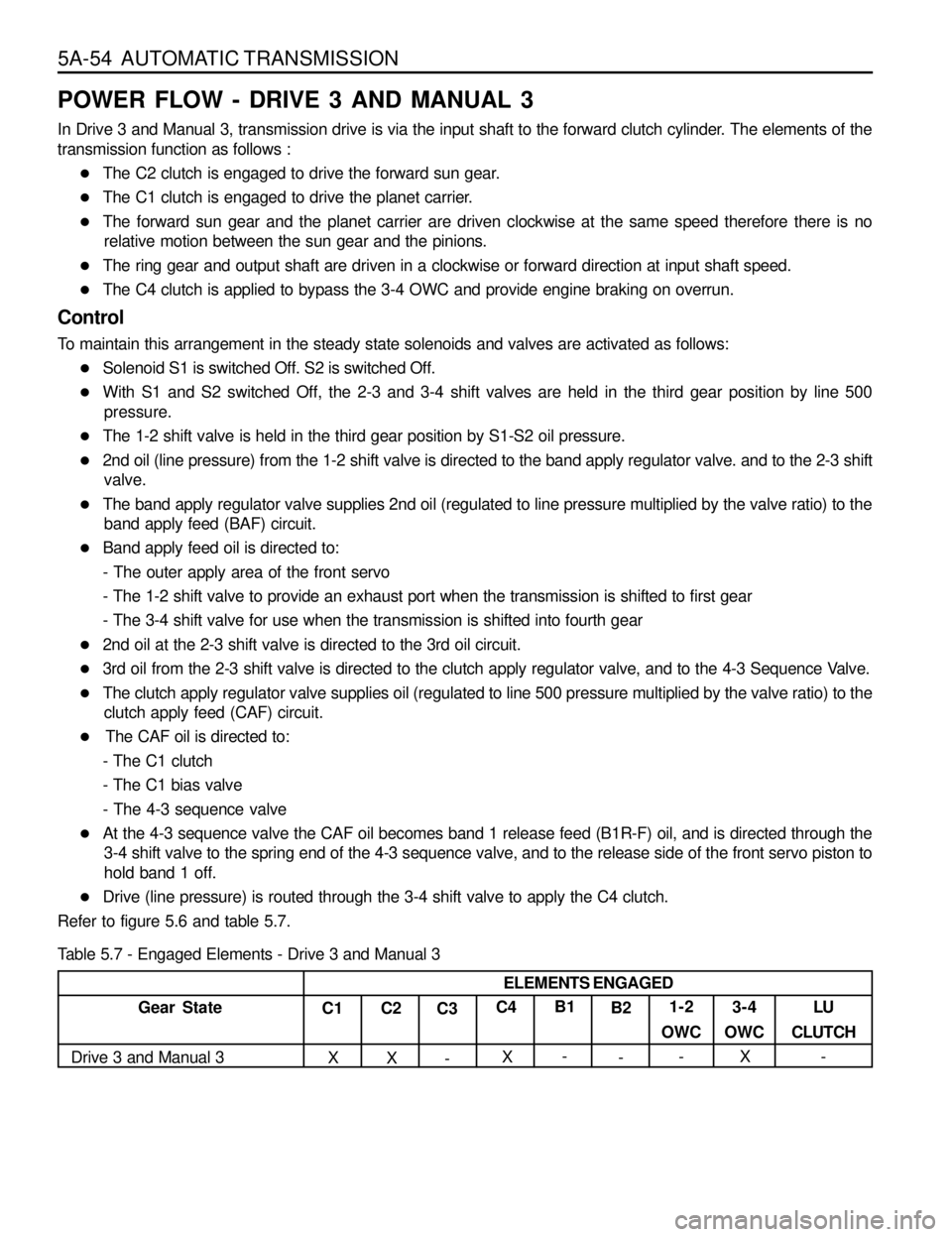
5A-54 AUTOMATIC TRANSMISSION
POWER FLOW - DRIVE 3 AND MANUAL 3
In Drive 3 and Manual 3, transmission drive is via the input shaft to the forward clutch cylinder. The elements of the
transmission function as follows :
lThe C2 clutch is engaged to drive the forward sun gear.
lThe C1 clutch is engaged to drive the planet carrier.
lThe forward sun gear and the planet carrier are driven clockwise at the same speed therefore there is no
relative motion between the sun gear and the pinions.
lThe ring gear and output shaft are driven in a clockwise or forward direction at input shaft speed.
lThe C4 clutch is applied to bypass the 3-4 OWC and provide engine braking on overrun.
Control
To maintain this arrangement in the steady state solenoids and valves are activated as follows:
lSolenoid S1 is switched Off. S2 is switched Off.
lWith S1 and S2 switched Off, the 2-3 and 3-4 shift valves are held in the third gear position by line 500
pressure.
lThe 1-2 shift valve is held in the third gear position by S1-S2 oil pressure.
l2nd oil (line pressure) from the 1-2 shift valve is directed to the band apply regulator valve. and to the 2-3 shift
valve.
lThe band apply regulator valve supplies 2nd oil (regulated to line pressure multiplied by the valve ratio) to the
band apply feed (BAF) circuit.
lBand apply feed oil is directed to:
- The outer apply area of the front servo
- The 1-2 shift valve to provide an exhaust port when the transmission is shifted to first gear
- The 3-4 shift valve for use when the transmission is shifted into fourth gear
l2nd oil at the 2-3 shift valve is directed to the 3rd oil circuit.
l3rd oil from the 2-3 shift valve is directed to the clutch apply regulator valve, and to the 4-3 Sequence Valve.
lThe clutch apply regulator valve supplies oil (regulated to line 500 pressure multiplied by the valve ratio) to the
clutch apply feed (CAF) circuit.
l The CAF oil is directed to:
- The C1 clutch
- The C1 bias valve
- The 4-3 sequence valve
lAt the 4-3 sequence valve the CAF oil becomes band 1 release feed (B1R-F) oil, and is directed through the
3-4 shift valve to the spring end of the 4-3 sequence valve, and to the release side of the front servo piston to
hold band 1 off.
lDrive (line pressure) is routed through the 3-4 shift valve to apply the C4 clutch.
Refer to figure 5.6 and table 5.7.
Table 5.7 - Engaged Elements - Drive 3 and Manual 3
Gear State
Drive 3 and Manual 3C1
XC2
XC3
-C4
XB1
-B2
-1-2
OWC
-3-4
OWC
XLU
CLUTCH
- ELEMENTS ENGAGED
Page 1033 of 1463
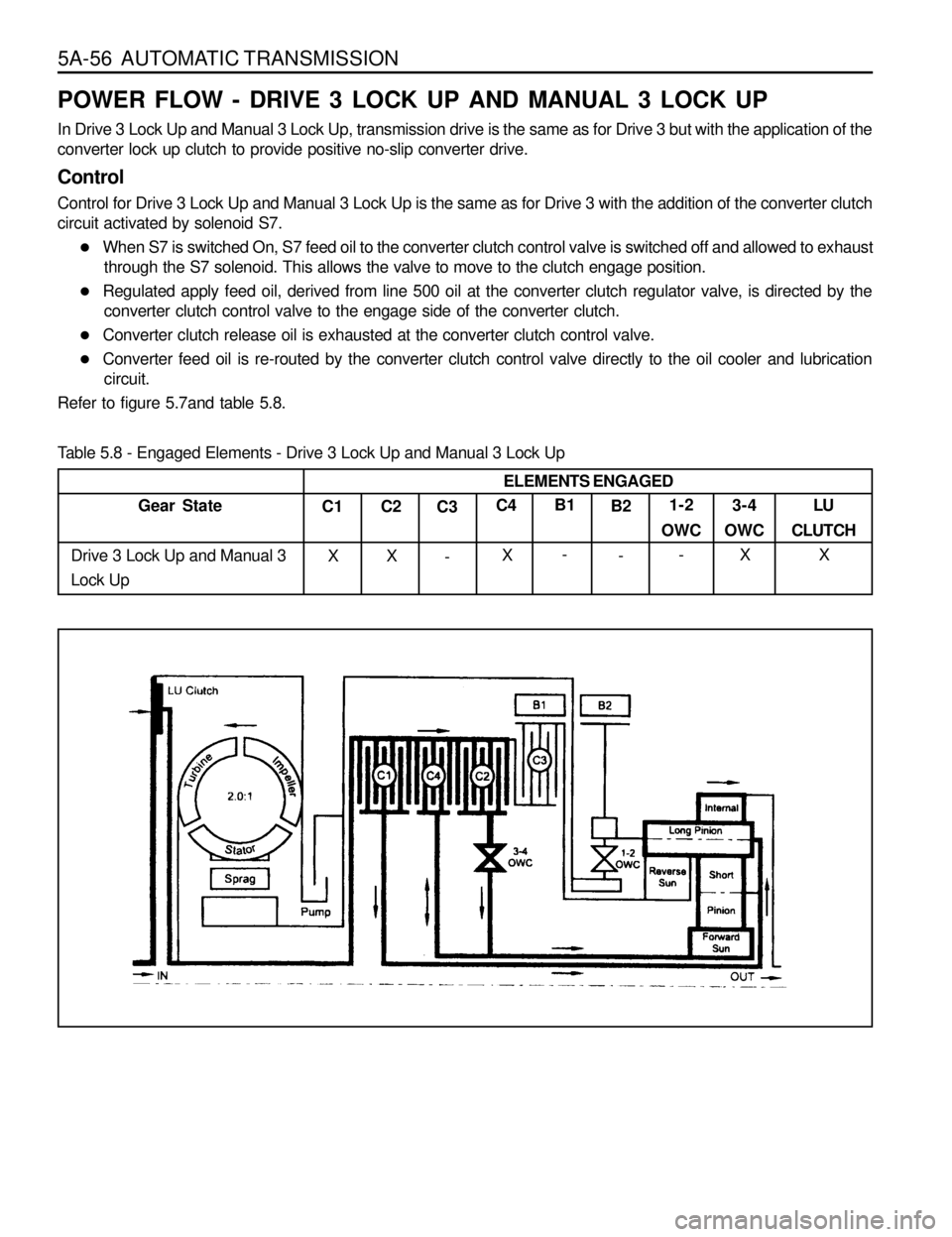
5A-56 AUTOMATIC TRANSMISSION
POWER FLOW - DRIVE 3 LOCK UP AND MANUAL 3 LOCK UP
In Drive 3 Lock Up and Manual 3 Lock Up, transmission drive is the same as for Drive 3 but with the application of the
converter lock up clutch to provide positive no-slip converter drive.
Control
Control for Drive 3 Lock Up and Manual 3 Lock Up is the same as for Drive 3 with the addition of the converter clutch
circuit activated by solenoid S7.
lWhen S7 is switched On, S7 feed oil to the converter clutch control valve is switched off and allowed to exhaust
through the S7 solenoid. This allows the valve to move to the clutch engage position.
lRegulated apply feed oil, derived from line 500 oil at the converter clutch regulator valve, is directed by the
converter clutch control valve to the engage side of the converter clutch.
lConverter clutch release oil is exhausted at the converter clutch control valve.
lConverter feed oil is re-routed by the converter clutch control valve directly to the oil cooler and lubrication
circuit.
Refer to figure 5.7and table 5.8.
Table 5.8 - Engaged Elements - Drive 3 Lock Up and Manual 3 Lock Up
Gear State
Drive 3 Lock Up and Manual 3
Lock UpC1
XC2
XC3
-C4
XB1
-B2
-1-2
OWC
-3-4
OWC
XLU
CLUTCH
X ELEMENTS ENGAGED
Page 1034 of 1463
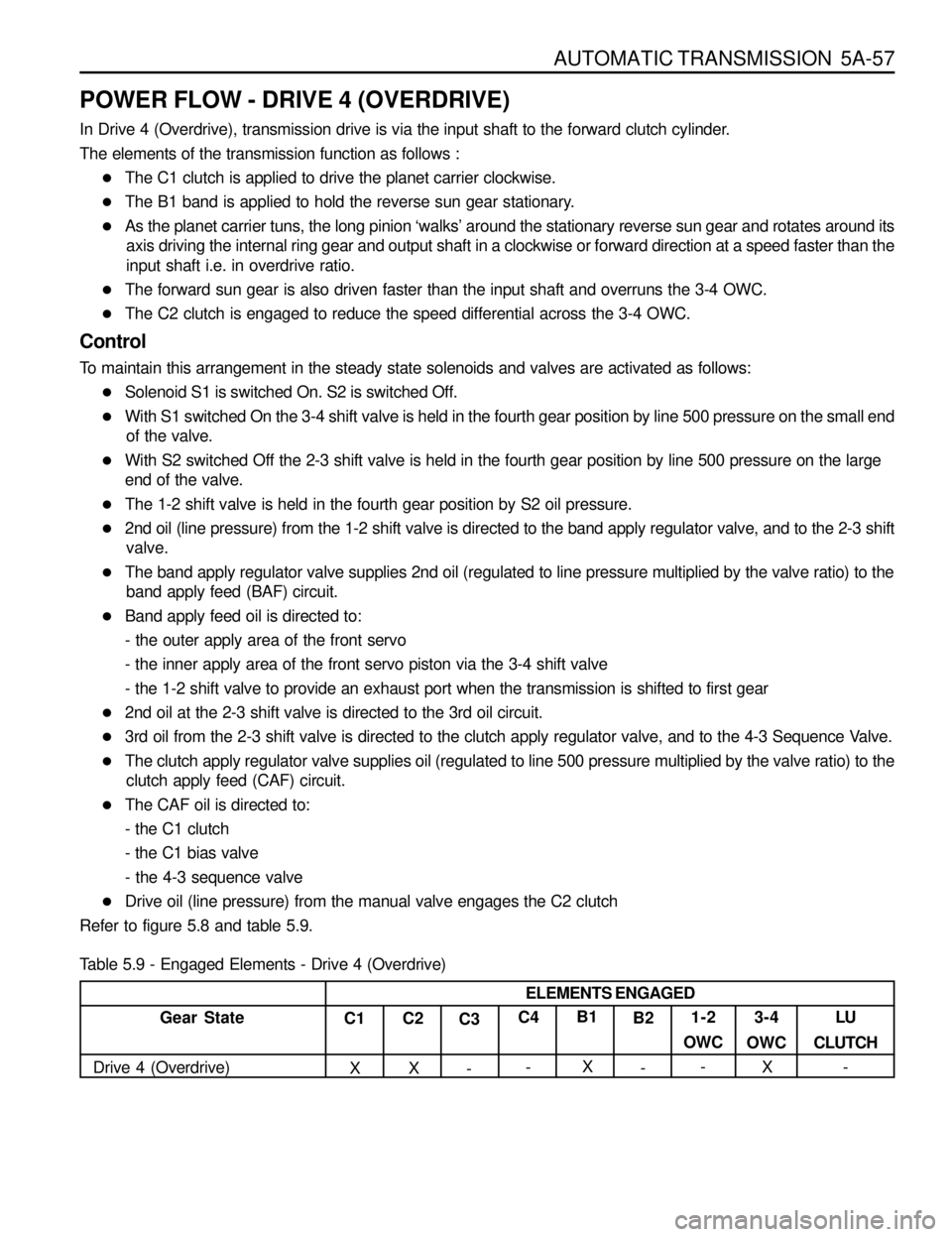
AUTOMATIC TRANSMISSION 5A-57
POWER FLOW - DRIVE 4 (OVERDRIVE)
In Drive 4 (Overdrive), transmission drive is via the input shaft to the forward clutch cylinder.
The elements of the transmission function as follows :
lThe C1 clutch is applied to drive the planet carrier clockwise.
lThe B1 band is applied to hold the reverse sun gear stationary.
lAs the planet carrier tuns, the long pinion ‘walks’ around the stationary reverse sun gear and rotates around its
axis driving the internal ring gear and output shaft in a clockwise or forward direction at a speed faster than the
input shaft i.e. in overdrive ratio.
lThe forward sun gear is also driven faster than the input shaft and overruns the 3-4 OWC.
lThe C2 clutch is engaged to reduce the speed differential across the 3-4 OWC.
Control
To maintain this arrangement in the steady state solenoids and valves are activated as follows:
lSolenoid S1 is switched On. S2 is switched Off.
lWith S1 switched On the 3-4 shift valve is held in the fourth gear position by line 500 pressure on the small end
of the valve.
lWith S2 switched Off the 2-3 shift valve is held in the fourth gear position by line 500 pressure on the large
end of the valve.
lThe 1-2 shift valve is held in the fourth gear position by S2 oil pressure.
l2nd oil (line pressure) from the 1-2 shift valve is directed to the band apply regulator valve, and to the 2-3 shift
valve.
lThe band apply regulator valve supplies 2nd oil (regulated to line pressure multiplied by the valve ratio) to the
band apply feed (BAF) circuit.
lBand apply feed oil is directed to:
- the outer apply area of the front servo
- the inner apply area of the front servo piston via the 3-4 shift valve
- the 1-2 shift valve to provide an exhaust port when the transmission is shifted to first gear
l2nd oil at the 2-3 shift valve is directed to the 3rd oil circuit.
l3rd oil from the 2-3 shift valve is directed to the clutch apply regulator valve, and to the 4-3 Sequence Valve.
lThe clutch apply regulator valve supplies oil (regulated to line 500 pressure multiplied by the valve ratio) to the
clutch apply feed (CAF) circuit.
lThe CAF oil is directed to:
- the C1 clutch
- the C1 bias valve
- the 4-3 sequence valve
lDrive oil (line pressure) from the manual valve engages the C2 clutch
Refer to figure 5.8 and table 5.9.
Table 5.9 - Engaged Elements - Drive 4 (Overdrive)
Gear State
Drive 4 (Overdrive)C1
XC2
XC3
-C4
-B1
XB2
-1-2
OWC
-3-4
OWC
XLU
CLUTCH
- ELEMENTS ENGAGED
Page 1036 of 1463
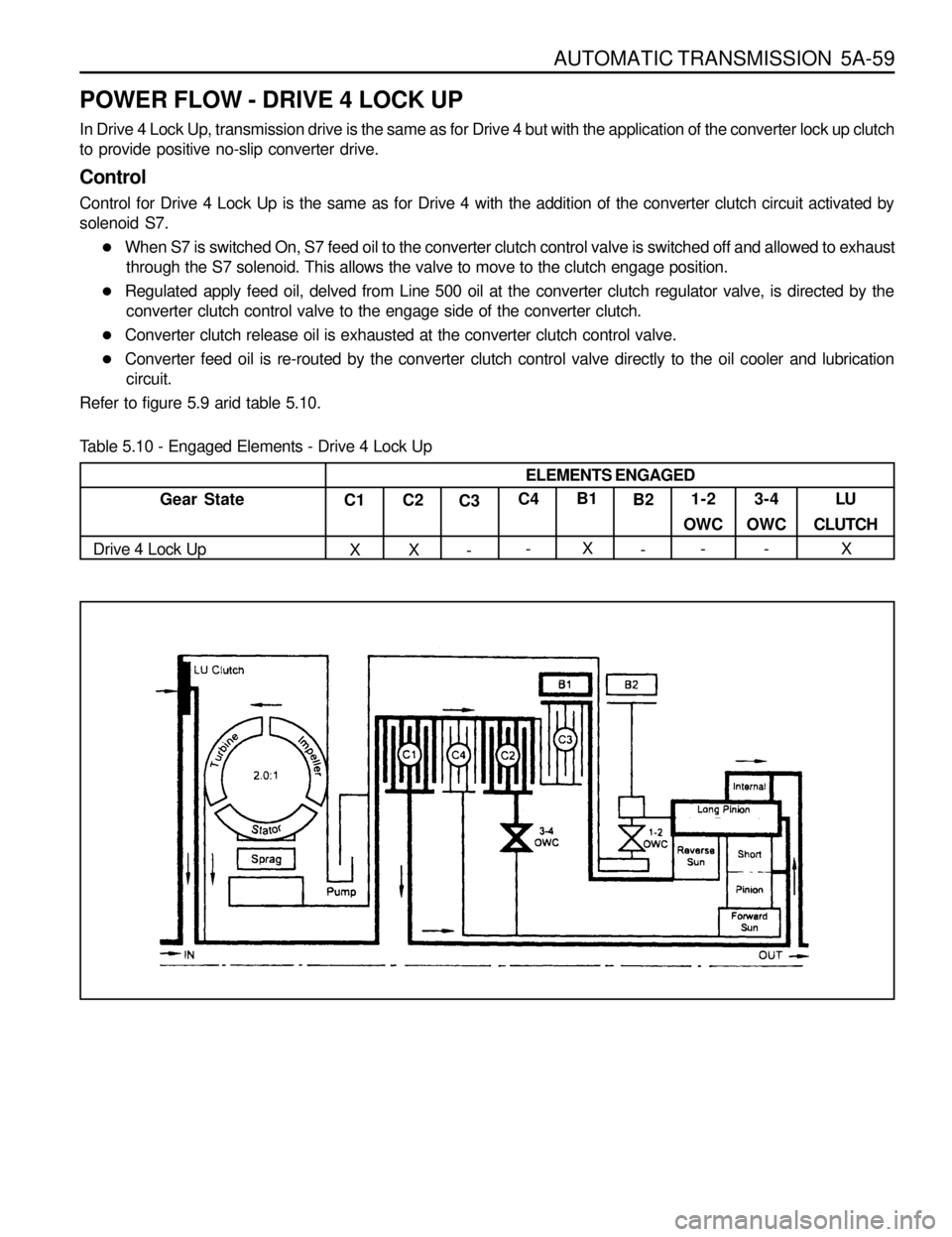
AUTOMATIC TRANSMISSION 5A-59
POWER FLOW - DRIVE 4 LOCK UP
In Drive 4 Lock Up, transmission drive is the same as for Drive 4 but with the application of the converter lock up clutch
to provide positive no-slip converter drive.
Control
Control for Drive 4 Lock Up is the same as for Drive 4 with the addition of the converter clutch circuit activated by
solenoid S7.
lWhen S7 is switched On, S7 feed oil to the converter clutch control valve is switched off and allowed to exhaust
through the S7 solenoid. This allows the valve to move to the clutch engage position.
lRegulated apply feed oil, delved from Line 500 oil at the converter clutch regulator valve, is directed by the
converter clutch control valve to the engage side of the converter clutch.
lConverter clutch release oil is exhausted at the converter clutch control valve.
lConverter feed oil is re-routed by the converter clutch control valve directly to the oil cooler and lubrication
circuit.
Refer to figure 5.9 arid table 5.10.
Table 5.10 - Engaged Elements - Drive 4 Lock Up
Gear State
Drive 4 Lock UpC1
XC2
XC3
-C4
-B1
XB2
-1-2
OWC
-3-4
OWC
-LU
CLUTCH
X ELEMENTS ENGAGED
Page 1039 of 1463
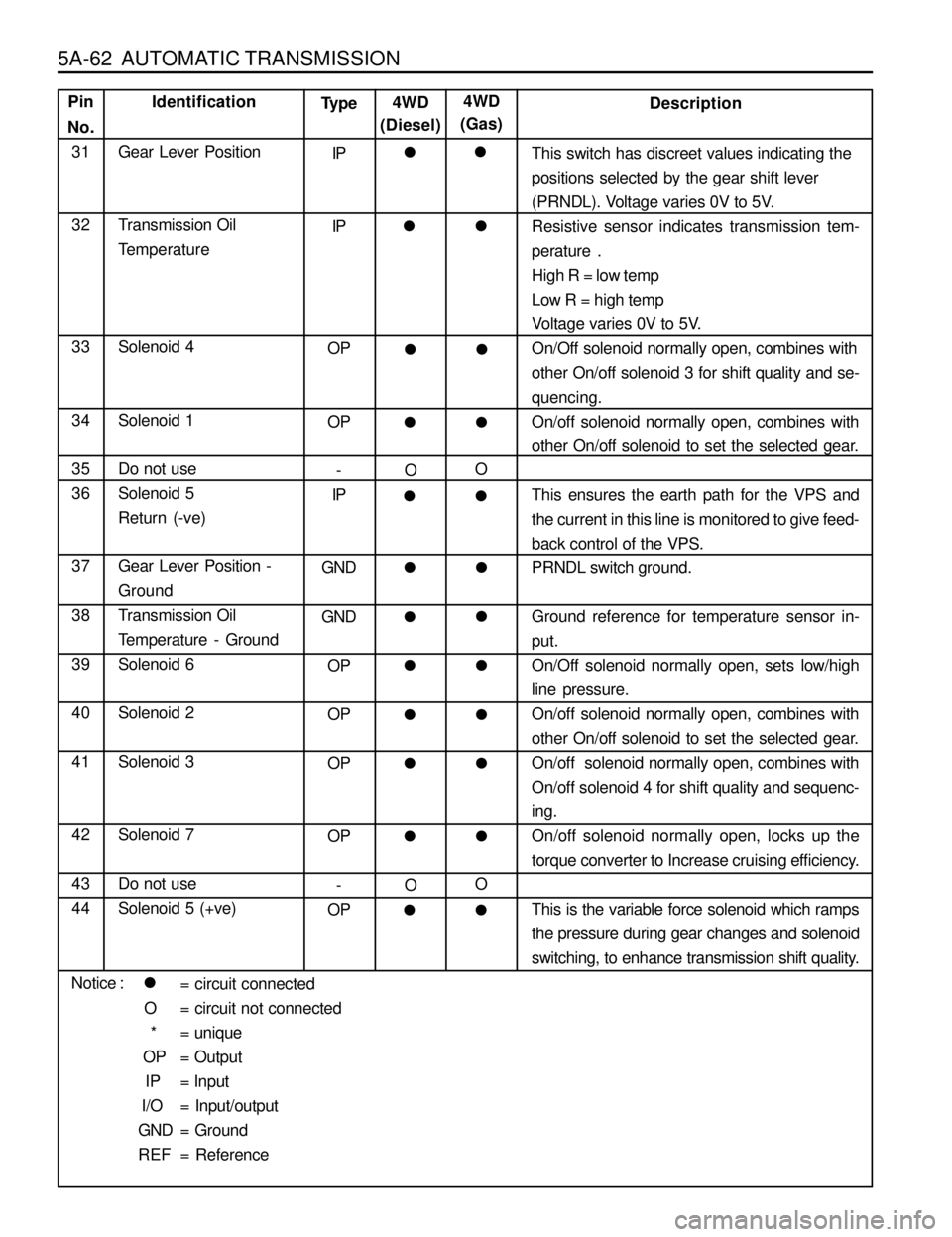
5A-62 AUTOMATIC TRANSMISSION
Identification
Gear Lever Position
Transmission Oil
Temperature
Solenoid 4
Solenoid 1
Do not use
Solenoid 5
Return (-ve)
Gear Lever Position -
Ground
Transmission Oil
Temperature - Ground
Solenoid 6
Solenoid 2
Solenoid 3
Solenoid 7
Do not use
Solenoid 5 (+ve)Type
IP
IP
OP
OP
-
IP
GND
GND
OP
OP
OP
OP
-
OPDescription
This switch has discreet values indicating the
positions selected by the gear shift lever
(PRNDL). Voltage varies 0V to 5V.
Resistive sensor indicates transmission tem-
perature .
High R = low temp
Low R = high temp
Voltage varies 0V to 5V.
On/Off solenoid normally open, combines with
other On/off solenoid 3 for shift quality and se-
quencing.
On/off solenoid normally open, combines with
other On/off solenoid to set the selected gear.
This ensures the earth path for the VPS and
the current in this line is monitored to give feed-
back control of the VPS.
PRNDL switch ground.
Ground reference for temperature sensor in-
put.
On/Off solenoid normally open, sets low/high
line pressure.
On/off solenoid normally open, combines with
other On/off solenoid to set the selected gear.
On/off solenoid normally open, combines with
On/off solenoid 4 for shift quality and sequenc-
ing.
On/off solenoid normally open, locks up the
torque converter to Increase cruising efficiency.
This is the variable force solenoid which ramps
the pressure during gear changes and solenoid
switching, to enhance transmission shift quality. 4WD
(Diesel)
O
O
l
l
4WD
(Gas)
O
O
l
l
ll
ll
ll
ll
Pin
No.
31
32
33
34
35
36
37
38
39
40
41
42
43
44
ll
ll
ll
ll
ll
ll
l= circuit connected
O = circuit not connected
* = unique
OP = Output
IP = Input
I/O = Input/output
GND = Ground
REF = Reference Notice :
Page 1041 of 1463
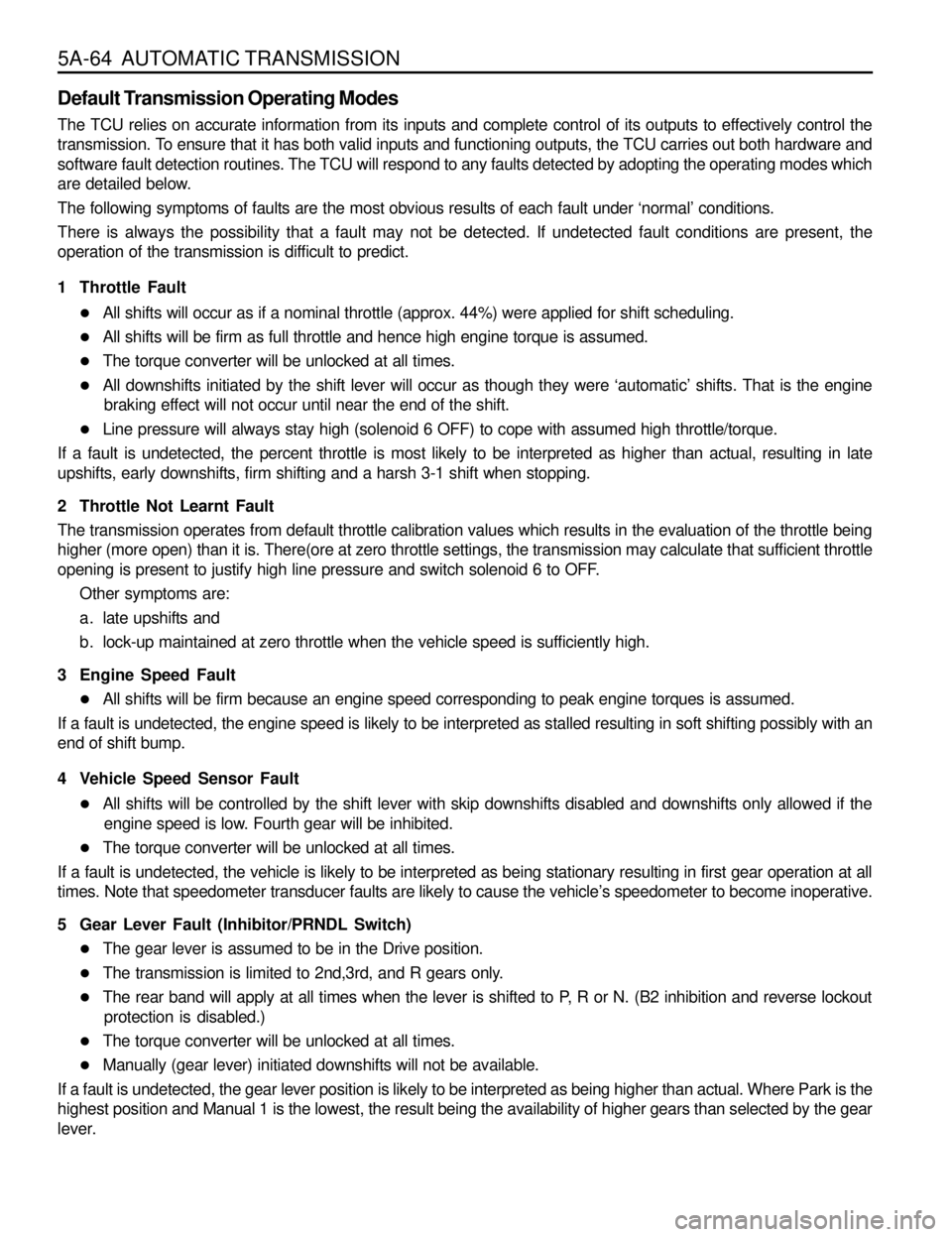
5A-64 AUTOMATIC TRANSMISSION
Default Transmission Operating Modes
The TCU relies on accurate information from its inputs and complete control of its outputs to effectively control the
transmission. To ensure that it has both valid inputs and functioning outputs, the TCU carries out both hardware and
software fault detection routines. The TCU will respond to any faults detected by adopting the operating modes which
are detailed below.
The following symptoms of faults are the most obvious results of each fault under ‘normal’ conditions.
There is always the possibility that a fault may not be detected. If undetected fault conditions are present, the
operation of the transmission is difficult to predict.
1 Throttle Fault
lAll shifts will occur as if a nominal throttle (approx. 44%) were applied for shift scheduling.
lAll shifts will be firm as full throttle and hence high engine torque is assumed.
lThe torque converter will be unlocked at all times.
lAll downshifts initiated by the shift lever will occur as though they were ‘automatic’ shifts. That is the engine
braking effect will not occur until near the end of the shift.
lLine pressure will always stay high (solenoid 6 OFF) to cope with assumed high throttle/torque.
If a fault is undetected, the percent throttle is most likely to be interpreted as higher than actual, resulting in late
upshifts, early downshifts, firm shifting and a harsh 3-1 shift when stopping.
2 Throttle Not Learnt Fault
The transmission operates from default throttle calibration values which results in the evaluation of the throttle being
higher (more open) than it is. There(ore at zero throttle settings, the transmission may calculate that sufficient throttle
opening is present to justify high line pressure and switch solenoid 6 to OFF.
Other symptoms are:
a. late upshifts and
b. lock-up maintained at zero throttle when the vehicle speed is sufficiently high.
3 Engine Speed Fault
lAll shifts will be firm because an engine speed corresponding to peak engine torques is assumed.
If a fault is undetected, the engine speed is likely to be interpreted as stalled resulting in soft shifting possibly with an
end of shift bump.
4 Vehicle Speed Sensor Fault
lAll shifts will be controlled by the shift lever with skip downshifts disabled and downshifts only allowed if the
engine speed is low. Fourth gear will be inhibited.
lThe torque converter will be unlocked at all times.
If a fault is undetected, the vehicle is likely to be interpreted as being stationary resulting in first gear operation at all
times. Note that speedometer transducer faults are likely to cause the vehicle’s speedometer to become inoperative.
5 Gear Lever Fault (Inhibitor/PRNDL Switch)
lThe gear lever is assumed to be in the Drive position.
lThe transmission is limited to 2nd,3rd, and R gears only.
lThe rear band will apply at all times when the lever is shifted to P, R or N. (B2 inhibition and reverse lockout
protection is disabled.)
lThe torque converter will be unlocked at all times.
lManually (gear lever) initiated downshifts will not be available.
If a fault is undetected, the gear lever position is likely to be interpreted as being higher than actual. Where Park is the
highest position and Manual 1 is the lowest, the result being the availability of higher gears than selected by the gear
lever.
Page 1042 of 1463
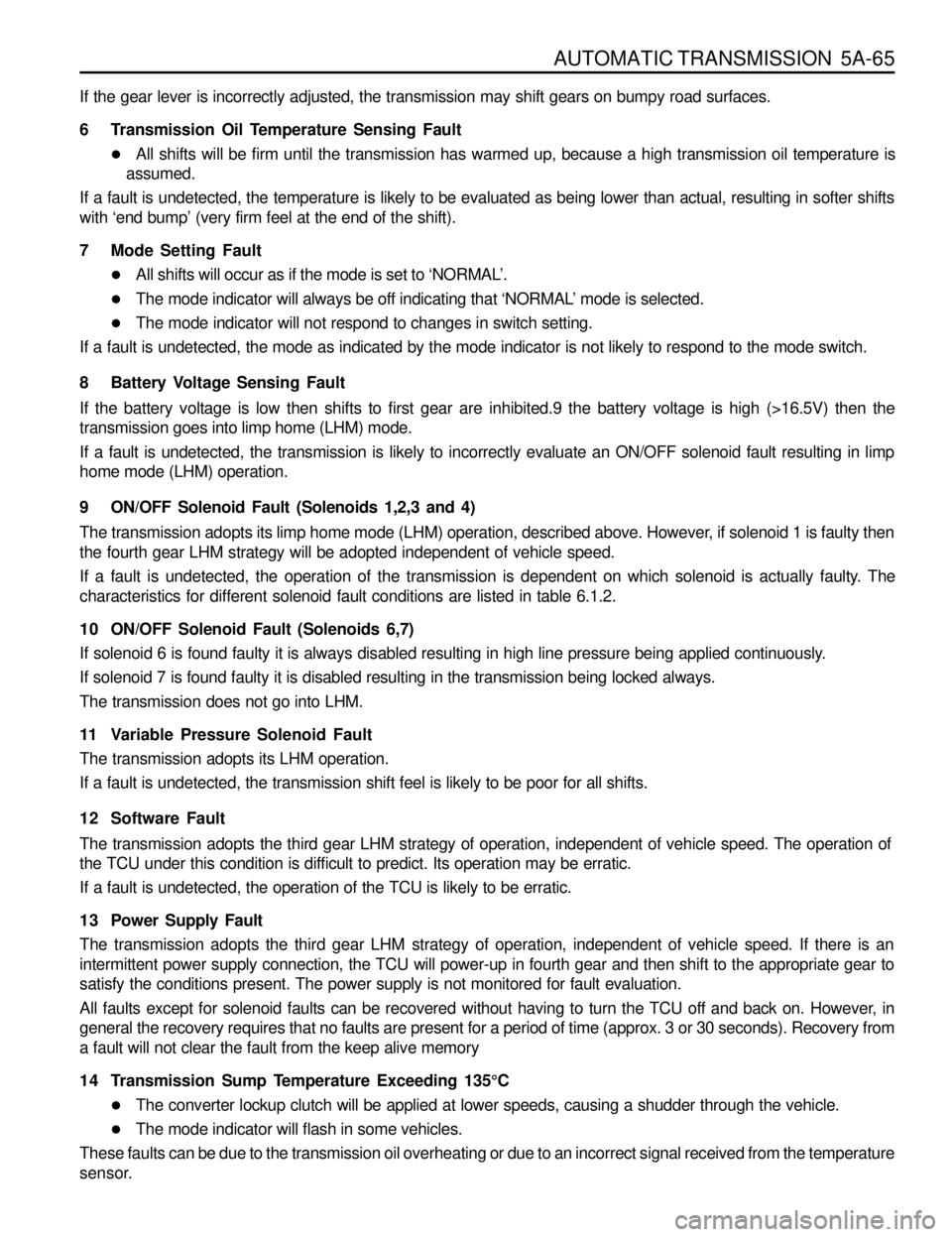
AUTOMATIC TRANSMISSION 5A-65
If the gear lever is incorrectly adjusted, the transmission may shift gears on bumpy road surfaces.
6 Transmission Oil Temperature Sensing Fault
lAll shifts will be firm until the transmission has warmed up, because a high transmission oil temperature is
assumed.
If a fault is undetected, the temperature is likely to be evaluated as being lower than actual, resulting in softer shifts
with ‘end bump’ (very firm feel at the end of the shift).
7 Mode Setting Fault
lAll shifts will occur as if the mode is set to ‘NORMAL’.
lThe mode indicator will always be off indicating that ‘NORMAL’ mode is selected.
lThe mode indicator will not respond to changes in switch setting.
If a fault is undetected, the mode as indicated by the mode indicator is not likely to respond to the mode switch.
8 Battery Voltage Sensing Fault
If the battery voltage is low then shifts to first gear are inhibited.9 the battery voltage is high (>16.5V) then the
transmission goes into limp home (LHM) mode.
If a fault is undetected, the transmission is likely to incorrectly evaluate an ON/OFF solenoid fault resulting in limp
home mode (LHM) operation.
9 ON/OFF Solenoid Fault (Solenoids 1,2,3 and 4)
The transmission adopts its limp home mode (LHM) operation, described above. However, if solenoid 1 is faulty then
the fourth gear LHM strategy will be adopted independent of vehicle speed.
If a fault is undetected, the operation of the transmission is dependent on which solenoid is actually faulty. The
characteristics for different solenoid fault conditions are listed in table 6.1.2.
10 ON/OFF Solenoid Fault (Solenoids 6,7)
If solenoid 6 is found faulty it is always disabled resulting in high line pressure being applied continuously.
If solenoid 7 is found faulty it is disabled resulting in the transmission being locked always.
The transmission does not go into LHM.
11 Variable Pressure Solenoid Fault
The transmission adopts its LHM operation.
If a fault is undetected, the transmission shift feel is likely to be poor for all shifts.
12 Software Fault
The transmission adopts the third gear LHM strategy of operation, independent of vehicle speed. The operation of
the TCU under this condition is difficult to predict. Its operation may be erratic.
If a fault is undetected, the operation of the TCU is likely to be erratic.
13 Power Supply Fault
The transmission adopts the third gear LHM strategy of operation, independent of vehicle speed. If there is an
intermittent power supply connection, the TCU will power-up in fourth gear and then shift to the appropriate gear to
satisfy the conditions present. The power supply is not monitored for fault evaluation.
All faults except for solenoid faults can be recovered without having to turn the TCU off and back on. However, in
general the recovery requires that no faults are present for a period of time (approx. 3 or 30 seconds). Recovery from
a fault will not clear the fault from the keep alive memory
14 Transmission Sump Temperature Exceeding 135°C
lThe converter lockup clutch will be applied at lower speeds, causing a shudder through the vehicle.
lThe mode indicator will flash in some vehicles.
These faults can be due to the transmission oil overheating or due to an incorrect signal received from the temperature
sensor.
Page 1043 of 1463
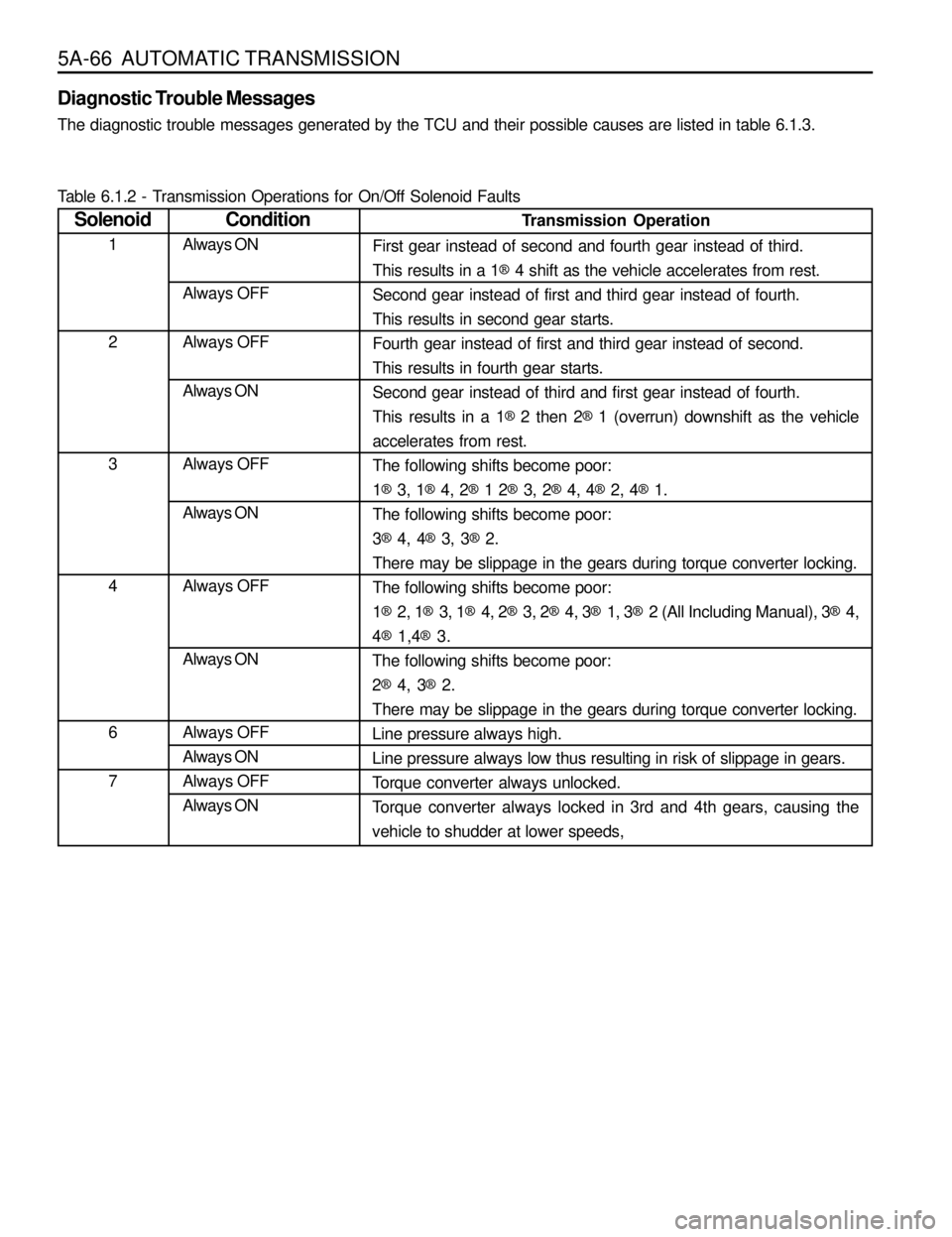
5A-66 AUTOMATIC TRANSMISSION
Diagnostic Trouble Messages
The diagnostic trouble messages generated by the TCU and their possible causes are listed in table 6.1.3.
Table 6.1.2 - Transmission Operations for On/Off Solenoid Faults
Transmission Operation
First gear instead of second and fourth gear instead of third.
This results in a 1®
4 shift as the vehicle accelerates from rest.
Second gear instead of first and third gear instead of fourth.
This results in second gear starts.
Fourth gear instead of first and third gear instead of second.
This results in fourth gear starts.
Second gear instead of third and first gear instead of fourth.
This results in a 1®
2 then 2®
1 (overrun) downshift as the vehicle
accelerates from rest.
The following shifts become poor:
1®
3, 1®
4, 2®
1 2®
3, 2®
4, 4®
2, 4®
1.
The following shifts become poor:
3®
4, 4®
3, 3®
2.
There may be slippage in the gears during torque converter locking.
The following shifts become poor:
1®
2, 1®
3, 1®
4, 2®
3, 2®
4, 3®
1, 3®
2 (All Including Manual), 3®
4,
4®
1,4®
3.
The following shifts become poor:
2®
4, 3®
2.
There may be slippage in the gears during torque converter locking.
Line pressure always high.
Line pressure always low thus resulting in risk of slippage in gears.
Torque converter always unlocked.
Torque converter always locked in 3rd and 4th gears, causing the
vehicle to shudder at lower speeds,Condition
Always ON
Always OFF
Always OFF
Always ON
Always OFF
Always ON
Always OFF
Always ON
Always OFF
Always ON
Always OFF
Always ON
Solenoid
1
2
3
4
6
7
Page 1046 of 1463
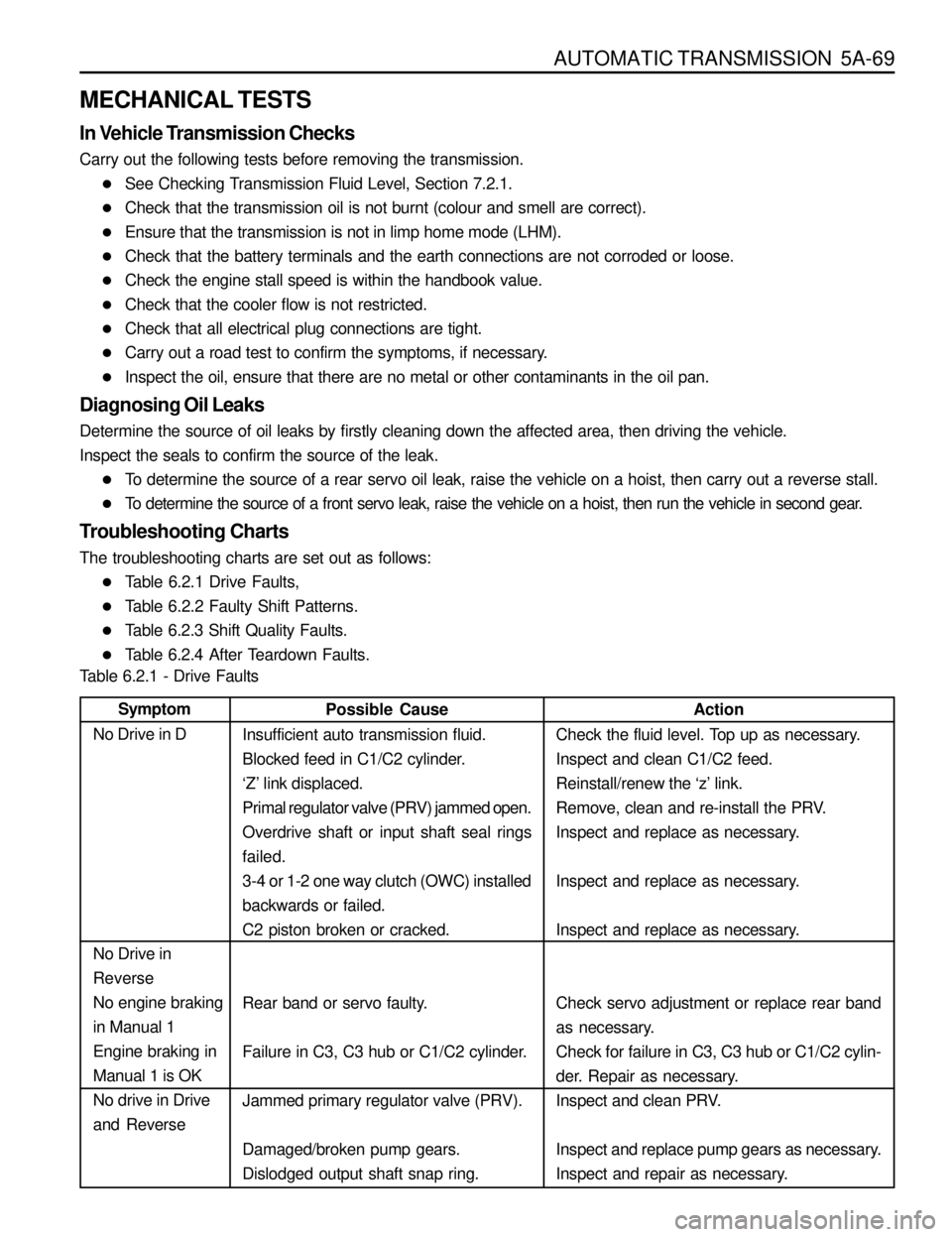
AUTOMATIC TRANSMISSION 5A-69
MECHANICAL TESTS
In Vehicle Transmission Checks
Carry out the following tests before removing the transmission.
lSee Checking Transmission Fluid Level, Section 7.2.1.
lCheck that the transmission oil is not burnt (colour and smell are correct).
lEnsure that the transmission is not in limp home mode (LHM).
lCheck that the battery terminals and the earth connections are not corroded or loose.
lCheck the engine stall speed is within the handbook value.
lCheck that the cooler flow is not restricted.
lCheck that all electrical plug connections are tight.
lCarry out a road test to confirm the symptoms, if necessary.
lInspect the oil, ensure that there are no metal or other contaminants in the oil pan.
Diagnosing Oil Leaks
Determine the source of oil leaks by firstly cleaning down the affected area, then driving the vehicle.
Inspect the seals to confirm the source of the leak.
lTo determine the source of a rear servo oil leak, raise the vehicle on a hoist, then carry out a reverse stall.
lTo determine the source of a front servo leak, raise the vehicle on a hoist, then run the vehicle in second gear.
Troubleshooting Charts
The troubleshooting charts are set out as follows:
lTable 6.2.1 Drive Faults,
lTable 6.2.2 Faulty Shift Patterns.
lTable 6.2.3 Shift Quality Faults.
lTable 6.2.4 After Teardown Faults.
Table 6.2.1 - Drive Faults
Action
Check the fluid level. Top up as necessary.
Inspect and clean C1/C2 feed.
Reinstall/renew the ‘z’ link.
Remove, clean and re-install the PRV.
Inspect and replace as necessary.
Inspect and replace as necessary.
Inspect and replace as necessary.
Check servo adjustment or replace rear band
as necessary.
Check for failure in C3, C3 hub or C1/C2 cylin-
der. Repair as necessary.
Inspect and clean PRV.
Inspect and replace pump gears as necessary.
Inspect and repair as necessary. Possible Cause
Insufficient auto transmission fluid.
Blocked feed in C1/C2 cylinder.
‘Z’ link displaced.
Primal regulator valve (PRV) jammed open.
Overdrive shaft or input shaft seal rings
failed.
3-4 or 1-2 one way clutch (OWC) installed
backwards or failed.
C2 piston broken or cracked.
Rear band or servo faulty.
Failure in C3, C3 hub or C1/C2 cylinder.
Jammed primary regulator valve (PRV).
Damaged/broken pump gears.
Dislodged output shaft snap ring.Symptom
No Drive in D
No Drive in
Reverse
No engine braking
in Manual 1
Engine braking in
Manual 1 is OK
No drive in Drive
and Reverse