lock SSANGYONG MUSSO 1998 Workshop Repair Manual
[x] Cancel search | Manufacturer: SSANGYONG, Model Year: 1998, Model line: MUSSO, Model: SSANGYONG MUSSO 1998Pages: 1463, PDF Size: 19.88 MB
Page 1051 of 1463
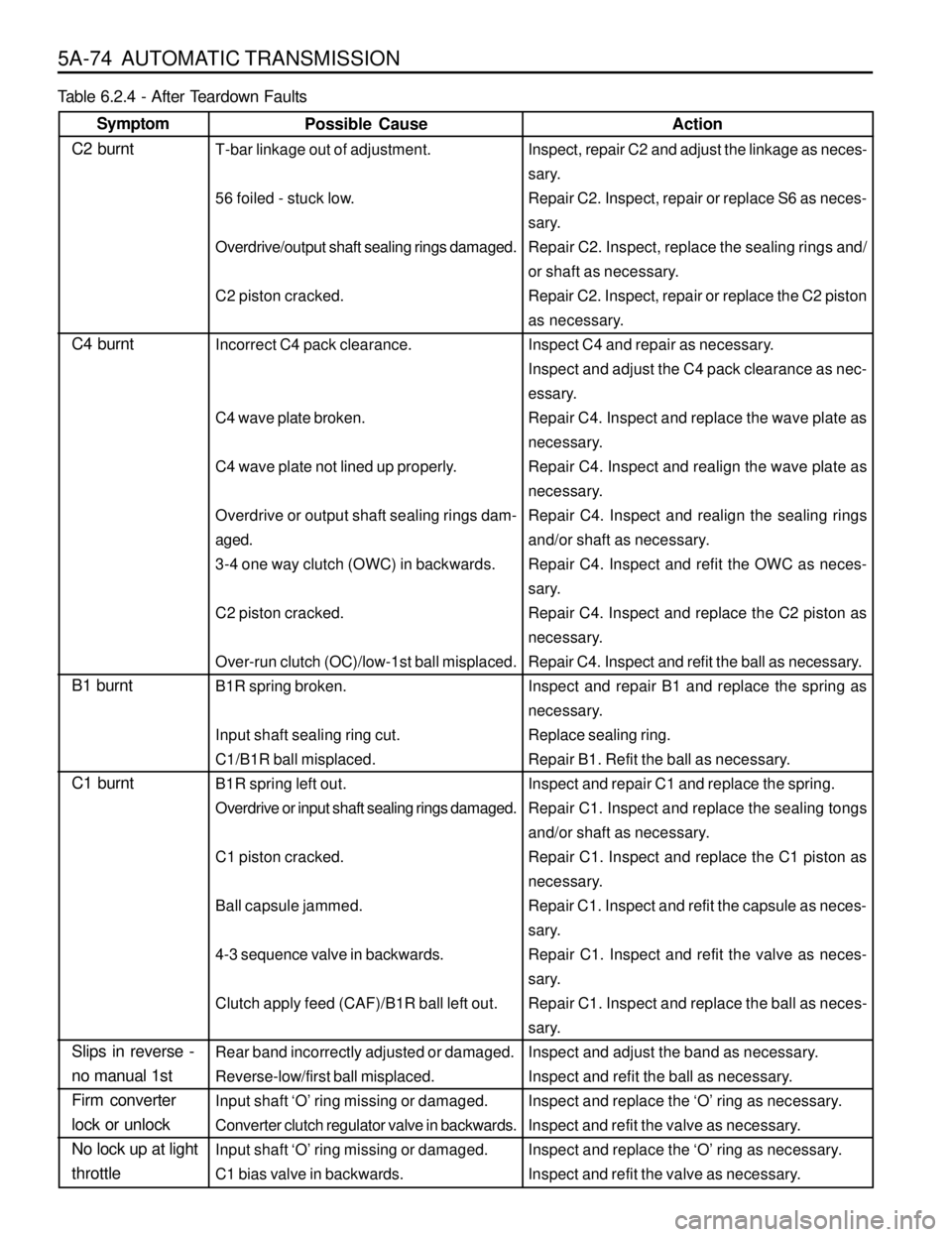
5A-74 AUTOMATIC TRANSMISSION
Action
Inspect, repair C2 and adjust the linkage as neces-
sary.
Repair C2. Inspect, repair or replace S6 as neces-
sary.
Repair C2. Inspect, replace the sealing rings and/
or shaft as necessary.
Repair C2. Inspect, repair or replace the C2 piston
as necessary.
Inspect C4 and repair as necessary.
Inspect and adjust the C4 pack clearance as nec-
essary.
Repair C4. Inspect and replace the wave plate as
necessary.
Repair C4. Inspect and realign the wave plate as
necessary.
Repair C4. Inspect and realign the sealing rings
and/or shaft as necessary.
Repair C4. Inspect and refit the OWC as neces-
sary.
Repair C4. Inspect and replace the C2 piston as
necessary.
Repair C4. Inspect and refit the ball as necessary.
Inspect and repair B1 and replace the spring as
necessary.
Replace sealing ring.
Repair B1. Refit the ball as necessary.
Inspect and repair C1 and replace the spring.
Repair C1. Inspect and replace the sealing tongs
and/or shaft as necessary.
Repair C1. Inspect and replace the C1 piston as
necessary.
Repair C1. Inspect and refit the capsule as neces-
sary.
Repair C1. Inspect and refit the valve as neces-
sary.
Repair C1. Inspect and replace the ball as neces-
sary.
Inspect and adjust the band as necessary.
Inspect and refit the ball as necessary.
Inspect and replace the ‘O’ ring as necessary.
Inspect and refit the valve as necessary.
Inspect and replace the ‘O’ ring as necessary.
Inspect and refit the valve as necessary.
Possible Cause
T-bar linkage out of adjustment.
56 foiled - stuck low.
Overdrive/output shaft sealing rings damaged.
C2 piston cracked.
Incorrect C4 pack clearance.
C4 wave plate broken.
C4 wave plate not lined up properly.
Overdrive or output shaft sealing rings dam-
aged.
3-4 one way clutch (OWC) in backwards.
C2 piston cracked.
Over-run clutch (OC)/low-1st ball misplaced.
B1R spring broken.
Input shaft sealing ring cut.
C1/B1R ball misplaced.
B1R spring left out.
Overdrive or input shaft sealing rings damaged.
C1 piston cracked.
Ball capsule jammed.
4-3 sequence valve in backwards.
Clutch apply feed (CAF)/B1R ball left out.
Rear band incorrectly adjusted or damaged.
Reverse-low/first ball misplaced.
Input shaft ‘O’ ring missing or damaged.
Converter clutch regulator valve in backwards.
Input shaft ‘O’ ring missing or damaged.
C1 bias valve in backwards.
Symptom
C2 burnt
C4 burnt
B1 burnt
C1 burnt
Slips in reverse -
no manual 1st
Firm converter
lock or unlock
No lock up at light
throttle
Table 6.2.4 - After Teardown Faults
Page 1060 of 1463
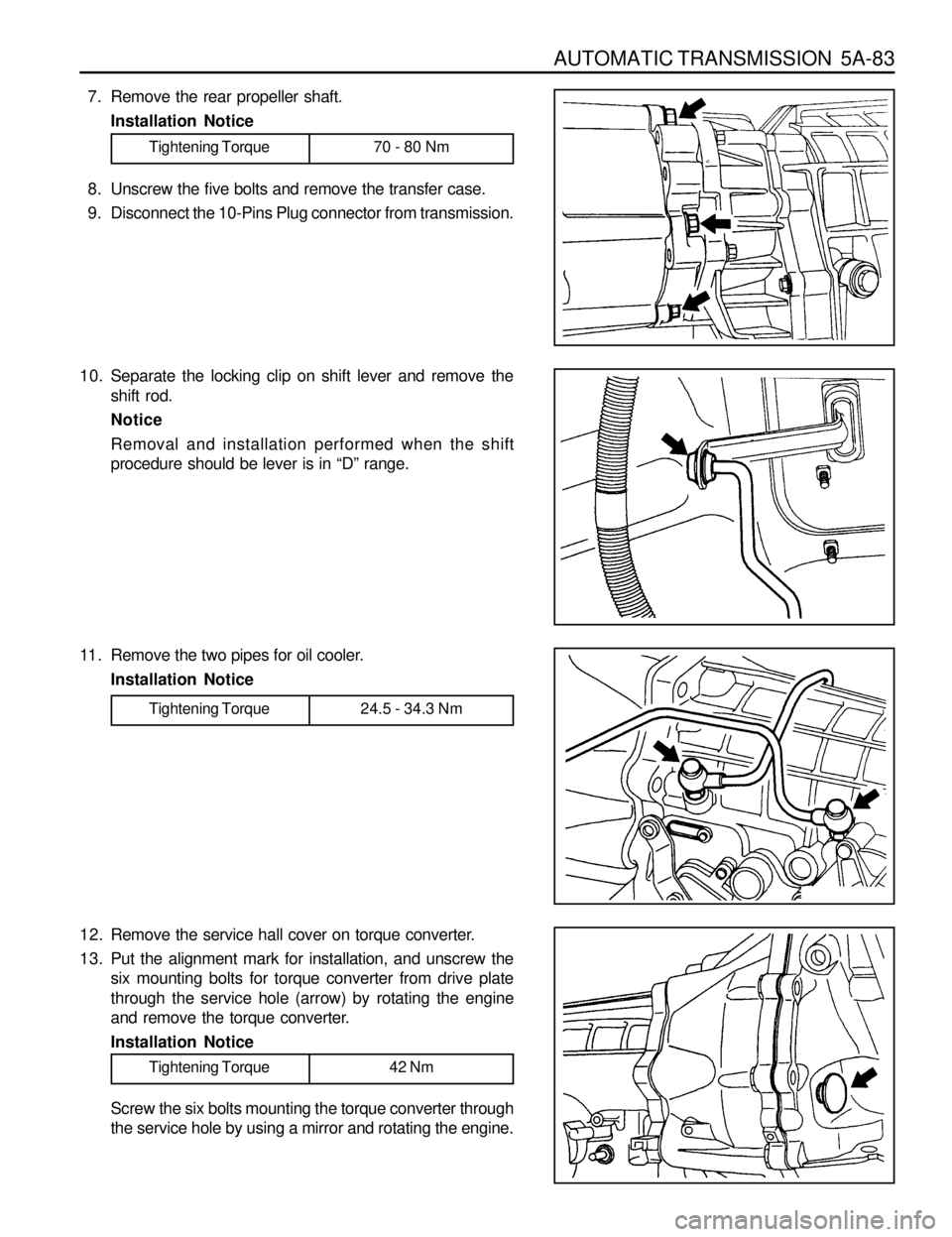
AUTOMATIC TRANSMISSION 5A-83
Tightening Torque 70 - 80 Nm
11. Remove the two pipes for oil cooler.
Installation Notice
Tightening Torque24.5 - 34.3 Nm
12. Remove the service hall cover on torque converter.
13. Put the alignment mark for installation, and unscrew the
six mounting bolts for torque converter from drive plate
through the service hole (arrow) by rotating the engine
and remove the torque converter.
Installation Notice
Tightening Torque 42 Nm
7. Remove the rear propeller shaft.
Installation Notice
8. Unscrew the five bolts and remove the transfer case.
9. Disconnect the 10-Pins Plug connector from transmission.
10. Separate the locking clip on shift lever and remove the
shift rod.
Notice
Removal and installation performed when the shift
procedure should be lever is in “D” range.
Screw the six bolts mounting the torque converter through
the service hole by using a mirror and rotating the engine.
Page 1063 of 1463
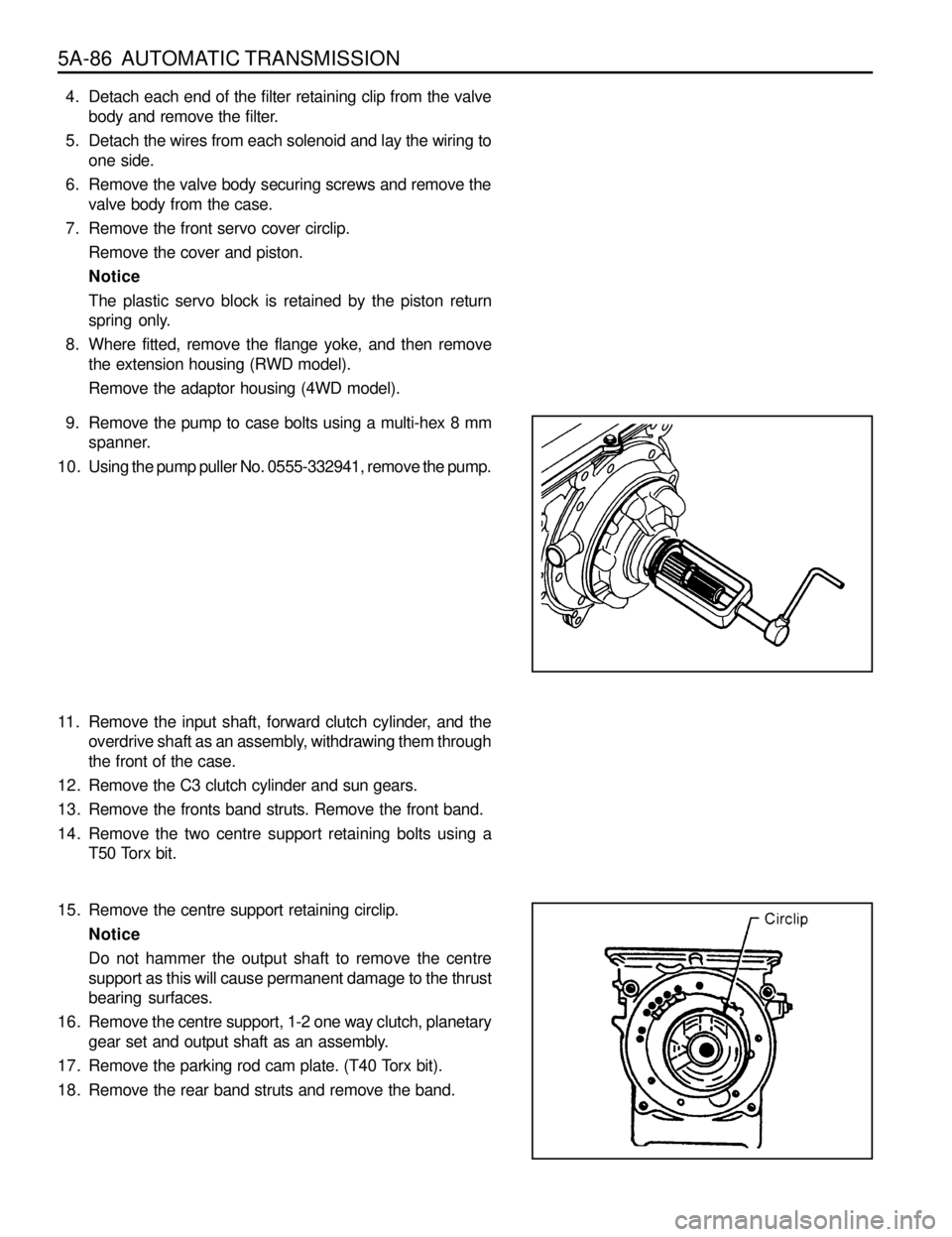
5A-86 AUTOMATIC TRANSMISSION
9. Remove the pump to case bolts using a multi-hex 8 mm
spanner.
10. Using the pump puller No. 0555-332941, remove the pump.
11. Remove the input shaft, forward clutch cylinder, and the
overdrive shaft as an assembly, withdrawing them through
the front of the case.
12. Remove the C3 clutch cylinder and sun gears.
13. Remove the fronts band struts. Remove the front band.
14. Remove the two centre support retaining bolts using a
T50 Torx bit.
15. Remove the centre support retaining circlip.
Notice
Do not hammer the output shaft to remove the centre
support as this will cause permanent damage to the thrust
bearing surfaces.
16. Remove the centre support, 1-2 one way clutch, planetary
gear set and output shaft as an assembly.
17. Remove the parking rod cam plate. (T40 Torx bit).
18. Remove the rear band struts and remove the band.4. Detach each end of the filter retaining clip from the valve
body and remove the filter.
5. Detach the wires from each solenoid and lay the wiring to
one side.
6. Remove the valve body securing screws and remove the
valve body from the case.
7. Remove the front servo cover circlip.
Remove the cover and piston.
Notice
The plastic servo block is retained by the piston return
spring only.
8. Where fitted, remove the flange yoke, and then remove
the extension housing (RWD model).
Remove the adaptor housing (4WD model).
Page 1066 of 1463
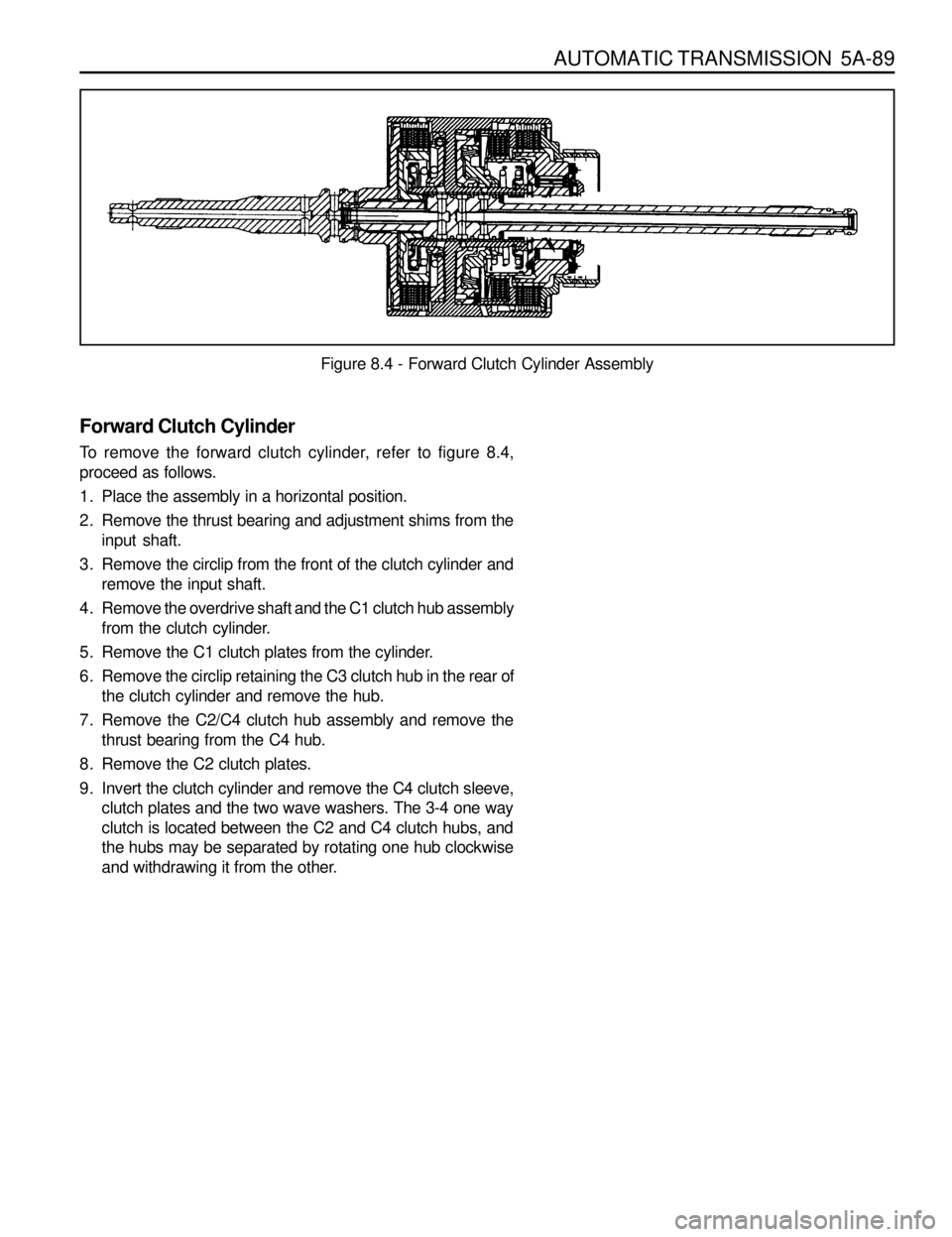
AUTOMATIC TRANSMISSION 5A-89
Forward Clutch Cylinder
To remove the forward clutch cylinder, refer to figure 8.4,
proceed as follows.
1. Place the assembly in a horizontal position.
2. Remove the thrust bearing and adjustment shims from the
input shaft.
3. Remove the circlip from the front of the clutch cylinder and
remove the input shaft.
4. Remove the overdrive shaft and the C1 clutch hub assembly
from the clutch cylinder.
5. Remove the C1 clutch plates from the cylinder.
6. Remove the circlip retaining the C3 clutch hub in the rear of
the clutch cylinder and remove the hub.
7. Remove the C2/C4 clutch hub assembly and remove the
thrust bearing from the C4 hub.
8. Remove the C2 clutch plates.
9. Invert the clutch cylinder and remove the C4 clutch sleeve,
clutch plates and the two wave washers. The 3-4 one way
clutch is located between the C2 and C4 clutch hubs, and
the hubs may be separated by rotating one hub clockwise
and withdrawing it from the other.
Figure 8.4 - Forward Clutch Cylinder Assembly
Page 1067 of 1463
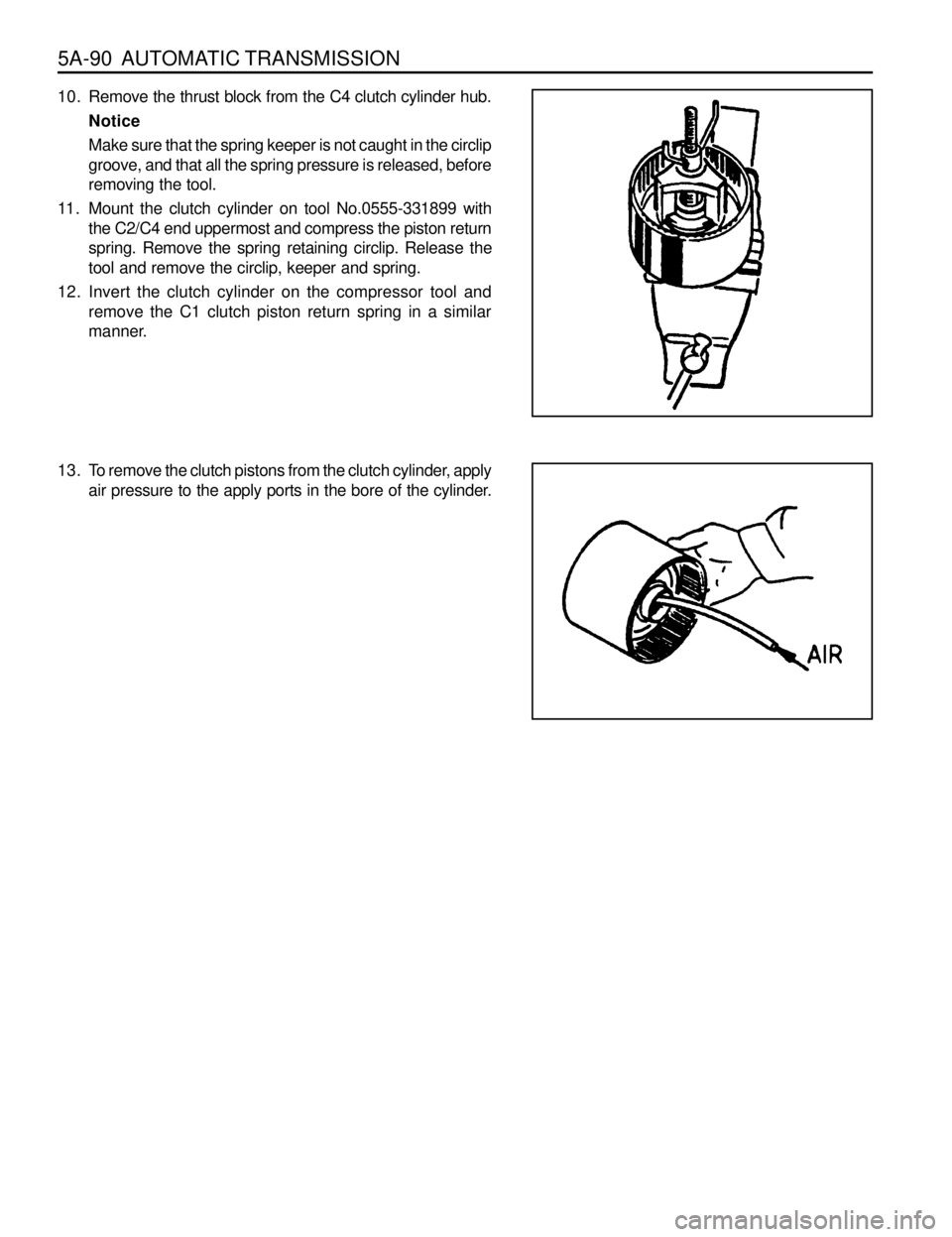
5A-90 AUTOMATIC TRANSMISSION
10. Remove the thrust block from the C4 clutch cylinder hub.
Notice
Make sure that the spring keeper is not caught in the circlip
groove, and that all the spring pressure is released, before
removing the tool.
11. Mount the clutch cylinder on tool No.0555-331899 with
the C2/C4 end uppermost and compress the piston return
spring. Remove the spring retaining circlip. Release the
tool and remove the circlip, keeper and spring.
12. Invert the clutch cylinder on the compressor tool and
remove the C1 clutch piston return spring in a similar
manner.
13. To remove the clutch pistons from the clutch cylinder, apply
air pressure to the apply ports in the bore of the cylinder.
Page 1068 of 1463
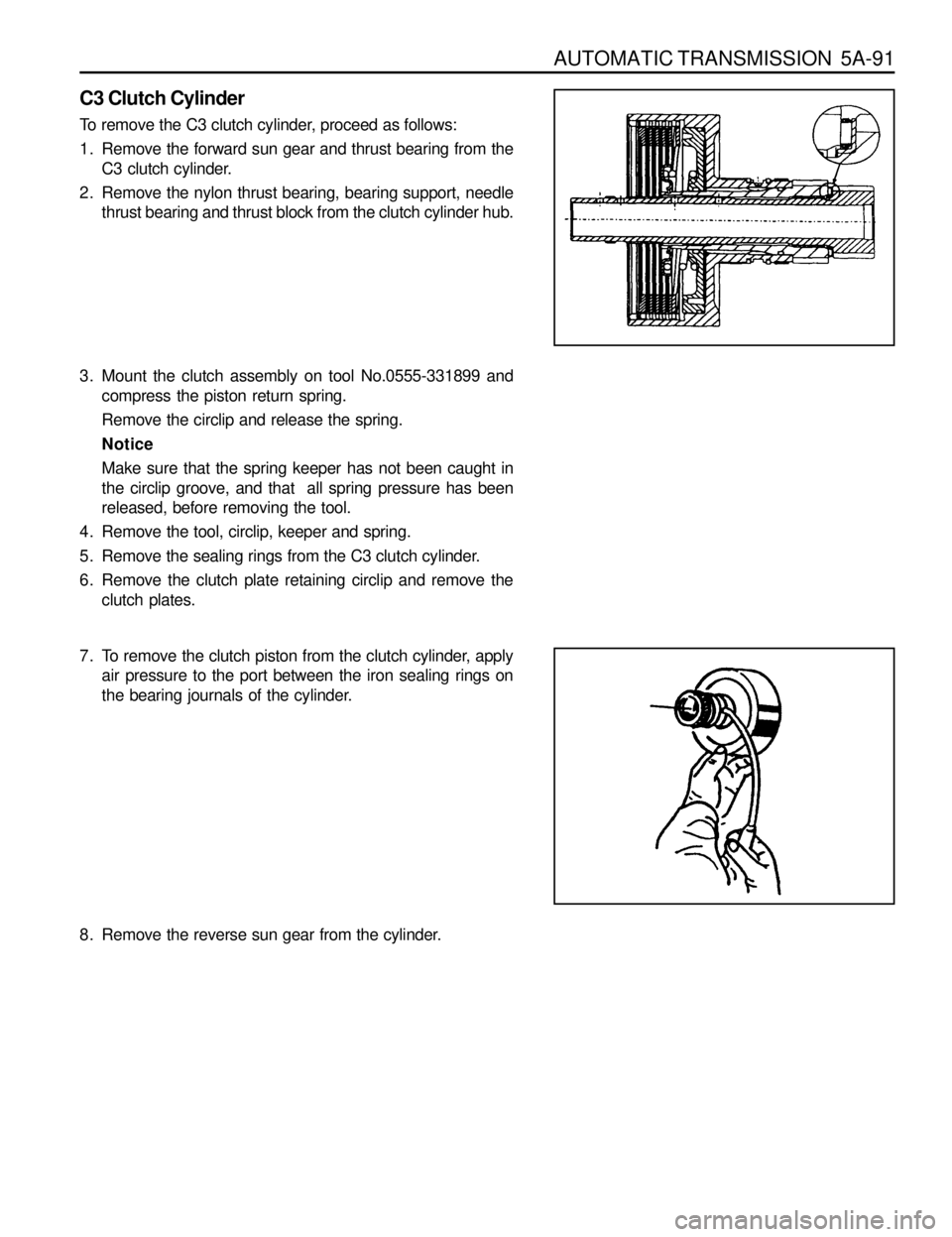
AUTOMATIC TRANSMISSION 5A-91
C3 Clutch Cylinder
To remove the C3 clutch cylinder, proceed as follows:
1. Remove the forward sun gear and thrust bearing from the
C3 clutch cylinder.
2. Remove the nylon thrust bearing, bearing support, needle
thrust bearing and thrust block from the clutch cylinder hub.
3. Mount the clutch assembly on tool No.0555-331899 and
compress the piston return spring.
Remove the circlip and release the spring.
Notice
Make sure that the spring keeper has not been caught in
the circlip groove, and that all spring pressure has been
released, before removing the tool.
4. Remove the tool, circlip, keeper and spring.
5. Remove the sealing rings from the C3 clutch cylinder.
6. Remove the clutch plate retaining circlip and remove the
clutch plates.
7. To remove the clutch piston from the clutch cylinder, apply
air pressure to the port between the iron sealing rings on
the bearing journals of the cylinder.
8. Remove the reverse sun gear from the cylinder.
Page 1069 of 1463
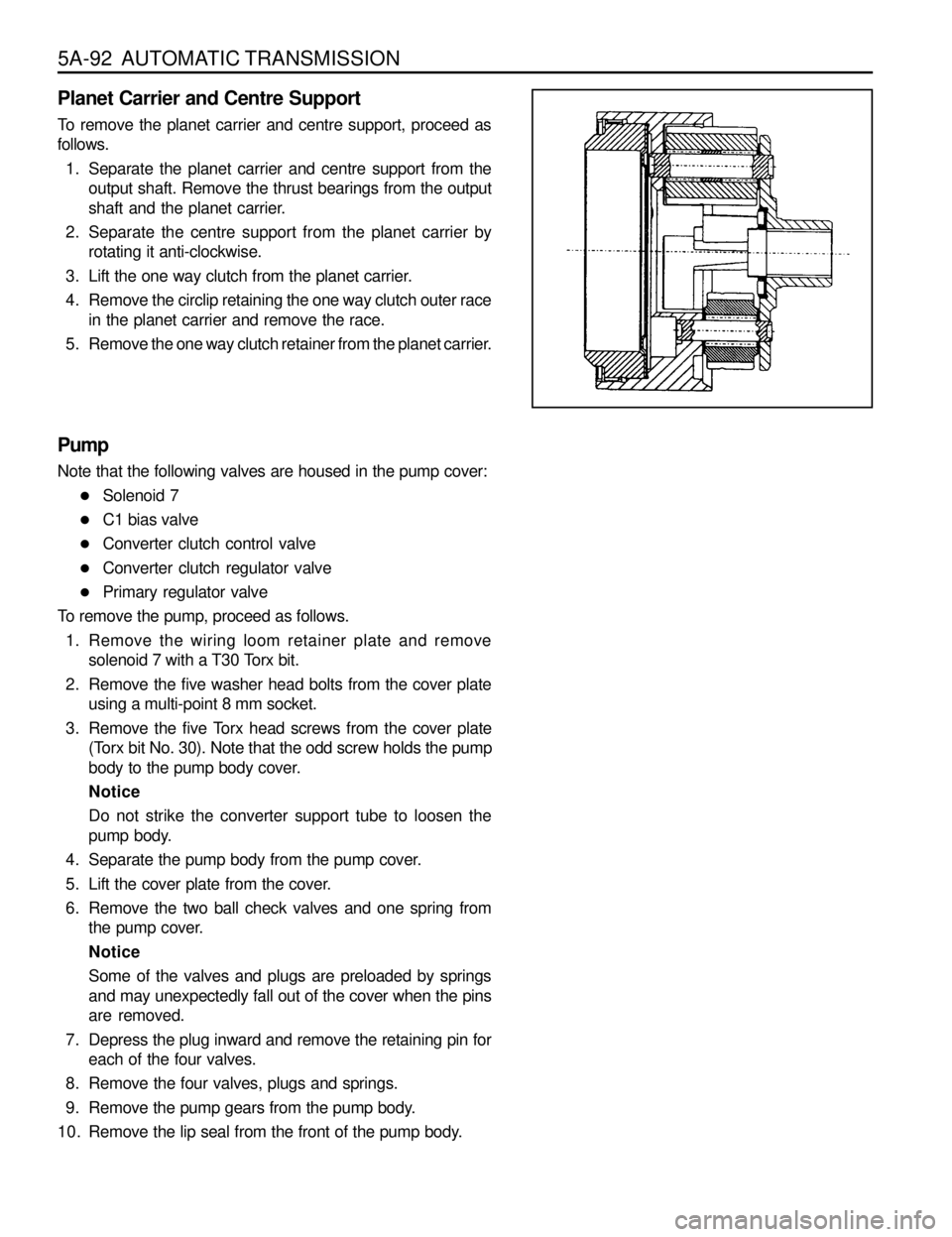
5A-92 AUTOMATIC TRANSMISSION
Planet Carrier and Centre Support
To remove the planet carrier and centre support, proceed as
follows.
1. Separate the planet carrier and centre support from the
output shaft. Remove the thrust bearings from the output
shaft and the planet carrier.
2. Separate the centre support from the planet carrier by
rotating it anti-clockwise.
3. Lift the one way clutch from the planet carrier.
4. Remove the circlip retaining the one way clutch outer race
in the planet carrier and remove the race.
5. Remove the one way clutch retainer from the planet carrier.
Pump
Note that the following valves are housed in the pump cover:
lSolenoid 7
lC1 bias valve
lConverter clutch control valve
lConverter clutch regulator valve
lPrimary regulator valve
To remove the pump, proceed as follows.
1. Remove the wiring loom retainer plate and remove
solenoid 7 with a T30 Torx bit.
2. Remove the five washer head bolts from the cover plate
using a multi-point 8 mm socket.
3. Remove the five Torx head screws from the cover plate
(Torx bit No. 30). Note that the odd screw holds the pump
body to the pump body cover.
Notice
Do not strike the converter support tube to loosen the
pump body.
4. Separate the pump body from the pump cover.
5. Lift the cover plate from the cover.
6. Remove the two ball check valves and one spring from
the pump cover.
Notice
Some of the valves and plugs are preloaded by springs
and may unexpectedly fall out of the cover when the pins
are removed.
7. Depress the plug inward and remove the retaining pin for
each of the four valves.
8. Remove the four valves, plugs and springs.
9. Remove the pump gears from the pump body.
10. Remove the lip seal from the front of the pump body.
Page 1070 of 1463
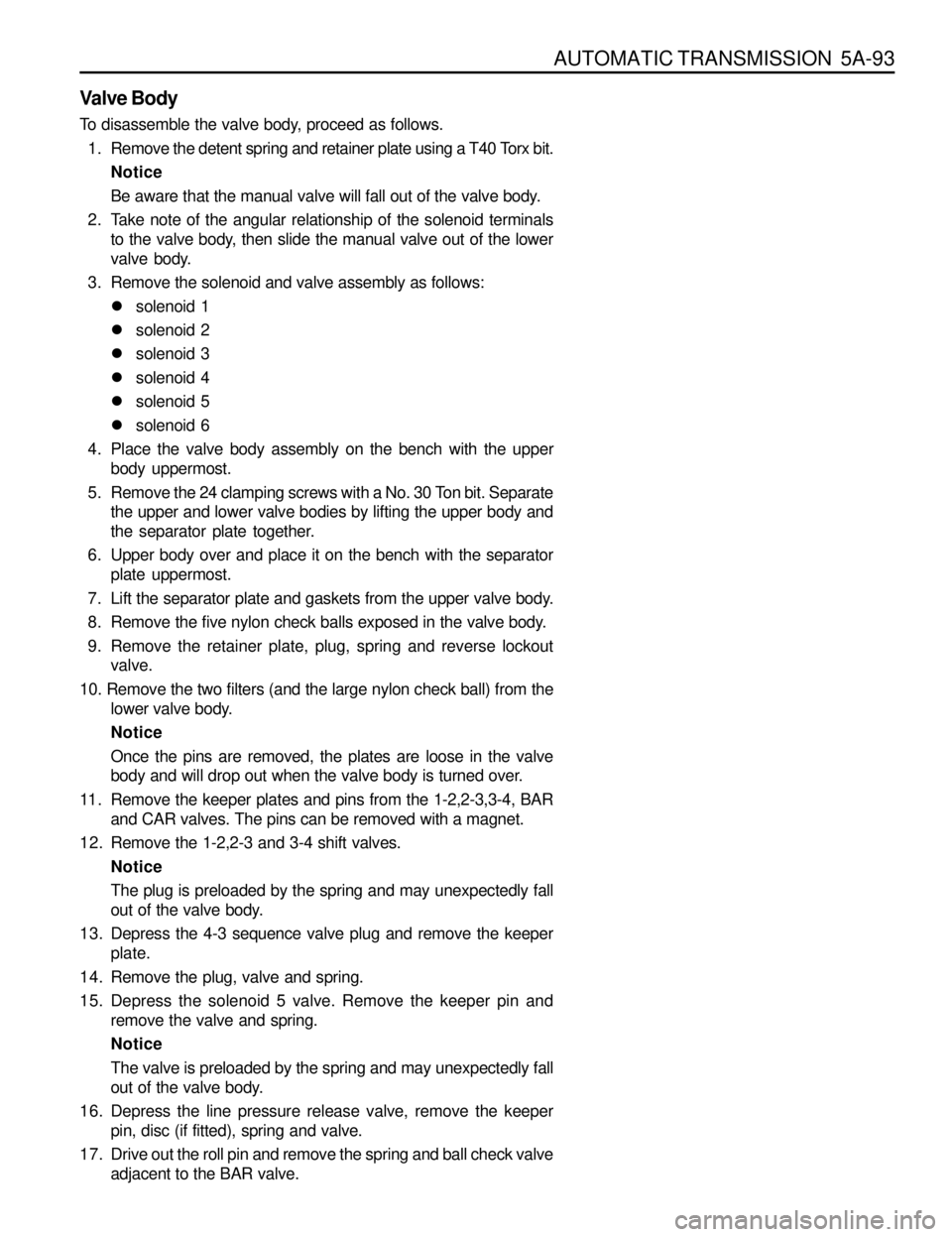
AUTOMATIC TRANSMISSION 5A-93
Valve Body
To disassemble the valve body, proceed as follows.
1. Remove the detent spring and retainer plate using a T40 Torx bit.
Notice
Be aware that the manual valve will fall out of the valve body.
2. Take note of the angular relationship of the solenoid terminals
to the valve body, then slide the manual valve out of the lower
valve body.
3. Remove the solenoid and valve assembly as follows:
lsolenoid 1
lsolenoid 2
lsolenoid 3
lsolenoid 4
lsolenoid 5
lsolenoid 6
4. Place the valve body assembly on the bench with the upper
body uppermost.
5. Remove the 24 clamping screws with a No. 30 Ton bit. Separate
the upper and lower valve bodies by lifting the upper body and
the separator plate together.
6. Upper body over and place it on the bench with the separator
plate uppermost.
7. Lift the separator plate and gaskets from the upper valve body.
8. Remove the five nylon check balls exposed in the valve body.
9. Remove the retainer plate, plug, spring and reverse lockout
valve.
10. Remove the two filters (and the large nylon check ball) from the
lower valve body.
Notice
Once the pins are removed, the plates are loose in the valve
body and will drop out when the valve body is turned over.
11. Remove the keeper plates and pins from the 1-2,2-3,3-4, BAR
and CAR valves. The pins can be removed with a magnet.
12. Remove the 1-2,2-3 and 3-4 shift valves.
Notice
The plug is preloaded by the spring and may unexpectedly fall
out of the valve body.
13. Depress the 4-3 sequence valve plug and remove the keeper
plate.
14. Remove the plug, valve and spring.
15. Depress the solenoid 5 valve. Remove the keeper pin and
remove the valve and spring.
Notice
The valve is preloaded by the spring and may unexpectedly fall
out of the valve body.
16. Depress the line pressure release valve, remove the keeper
pin, disc (if fitted), spring and valve.
17. Drive out the roll pin and remove the spring and ball check valve
adjacent to the BAR valve.
Page 1077 of 1463
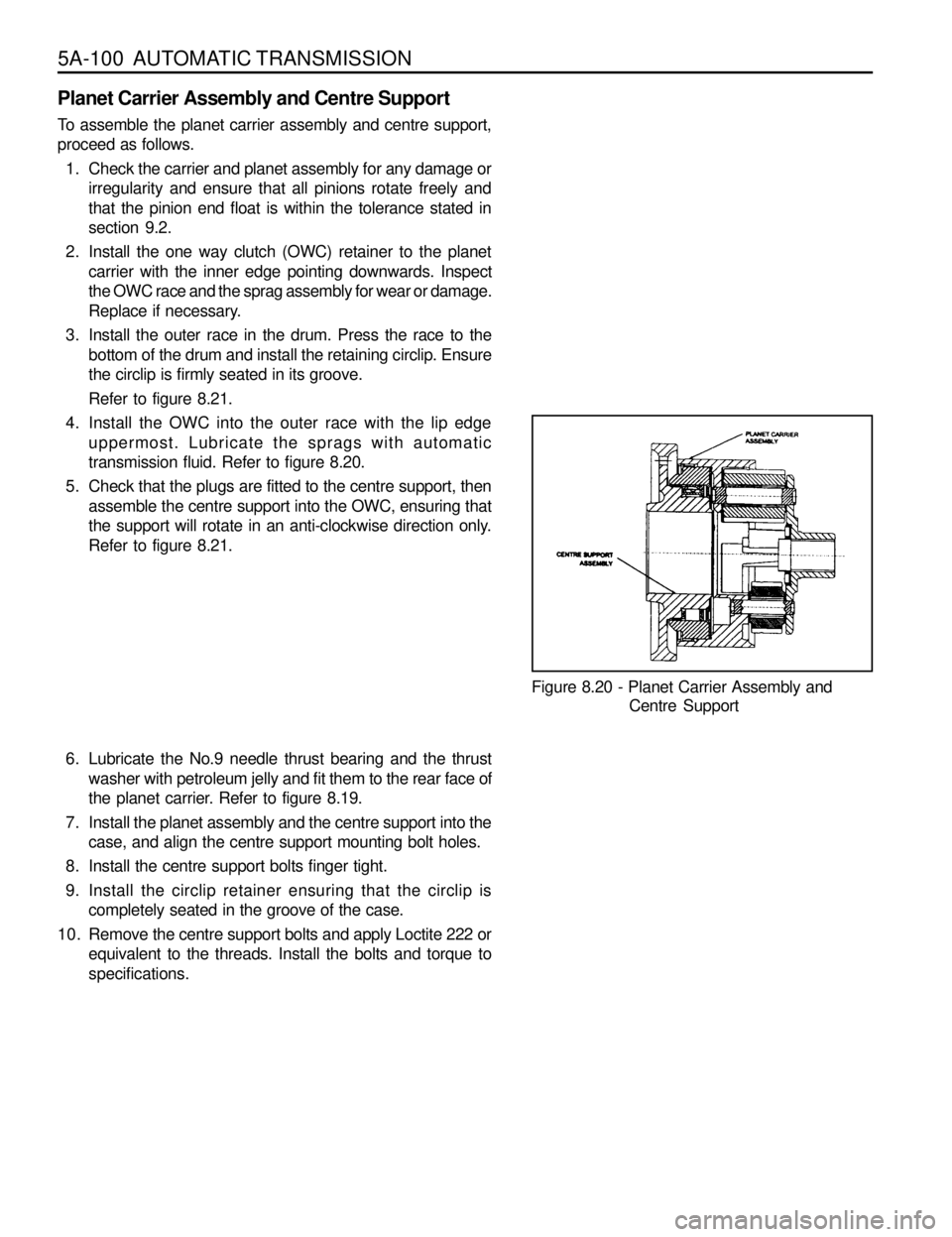
5A-100 AUTOMATIC TRANSMISSION
Planet Carrier Assembly and Centre Support
To assemble the planet carrier assembly and centre support,
proceed as follows.
1. Check the carrier and planet assembly for any damage or
irregularity and ensure that all pinions rotate freely and
that the pinion end float is within the tolerance stated in
section 9.2.
2. Install the one way clutch (OWC) retainer to the planet
carrier with the inner edge pointing downwards. Inspect
the OWC race and the sprag assembly for wear or damage.
Replace if necessary.
3. Install the outer race in the drum. Press the race to the
bottom of the drum and install the retaining circlip. Ensure
the circlip is firmly seated in its groove.
Refer to figure 8.21.
4. Install the OWC into the outer race with the lip edge
uppermost. Lubricate the sprags with automatic
transmission fluid. Refer to figure 8.20.
5. Check that the plugs are fitted to the centre support, then
assemble the centre support into the OWC, ensuring that
the support will rotate in an anti-clockwise direction only.
Refer to figure 8.21.
Figure 8.20 - Planet Carrier Assembly and
Centre Support
6. Lubricate the No.9 needle thrust bearing and the thrust
washer with petroleum jelly and fit them to the rear face of
the planet carrier. Refer to figure 8.19.
7. Install the planet assembly and the centre support into the
case, and align the centre support mounting bolt holes.
8. Install the centre support bolts finger tight.
9. Install the circlip retainer ensuring that the circlip is
completely seated in the groove of the case.
10. Remove the centre support bolts and apply Loctite 222 or
equivalent to the threads. Install the bolts and torque to
specifications.
Page 1078 of 1463
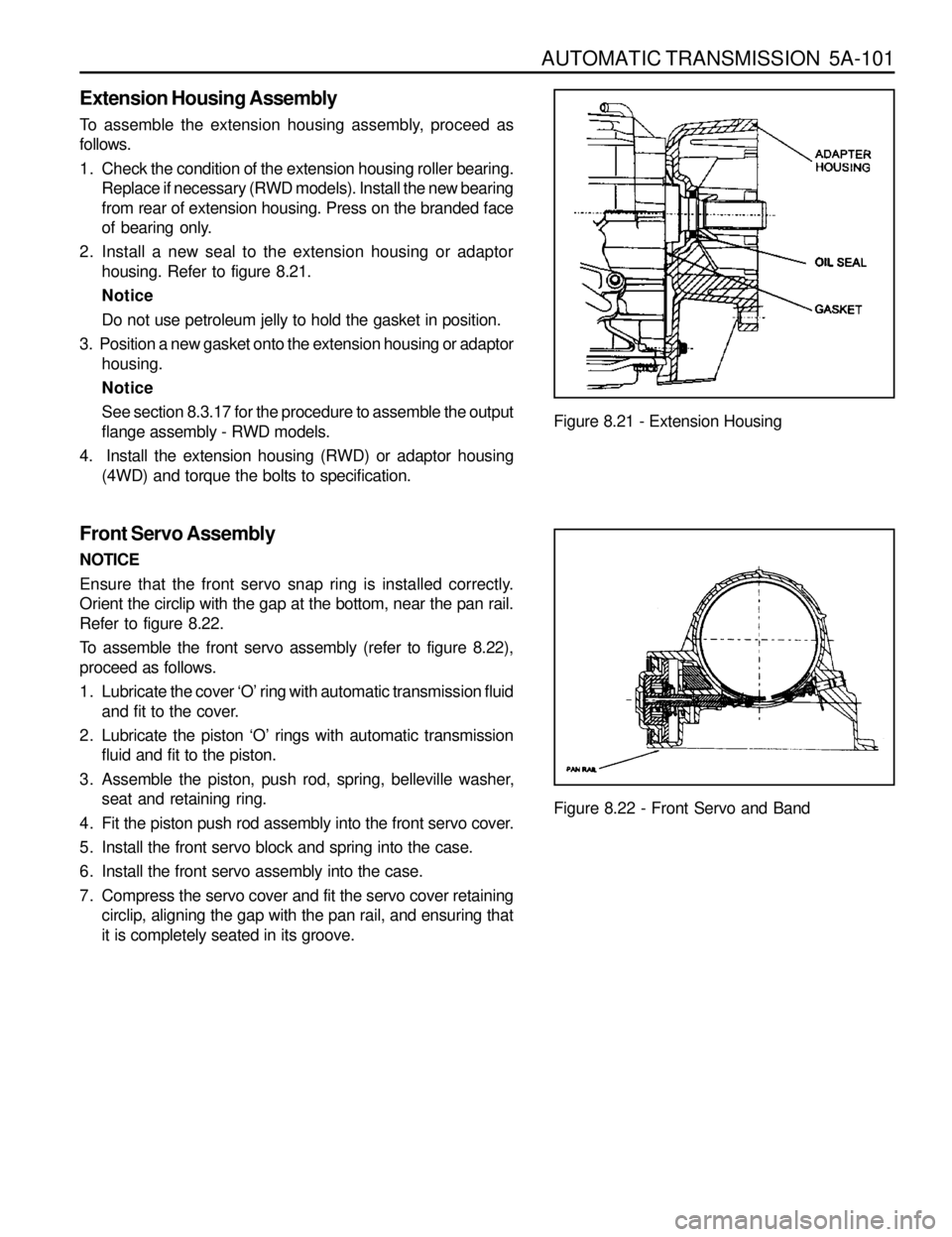
AUTOMATIC TRANSMISSION 5A-101
Extension Housing Assembly
To assemble the extension housing assembly, proceed as
follows.
1. Check the condition of the extension housing roller bearing.
Replace if necessary (RWD models). Install the new bearing
from rear of extension housing. Press on the branded face
of bearing only.
2. Install a new seal to the extension housing or adaptor
housing. Refer to figure 8.21.
Notice
Do not use petroleum jelly to hold the gasket in position.
3. Position a new gasket onto the extension housing or adaptor
housing.
Notice
See section 8.3.17 for the procedure to assemble the output
flange assembly - RWD models.
4. Install the extension housing (RWD) or adaptor housing
(4WD) and torque the bolts to specification.
Front Servo Assembly
NOTICE
Ensure that the front servo snap ring is installed correctly.
Orient the circlip with the gap at the bottom, near the pan rail.
Refer to figure 8.22.
To assemble the front servo assembly (refer to figure 8.22),
proceed as follows.
1. Lubricate the cover ‘O’ ring with automatic transmission fluid
and fit to the cover.
2. Lubricate the piston ‘O’ rings with automatic transmission
fluid and fit to the piston.
3. Assemble the piston, push rod, spring, belleville washer,
seat and retaining ring.
4. Fit the piston push rod assembly into the front servo cover.
5. Install the front servo block and spring into the case.
6. Install the front servo assembly into the case.
7. Compress the servo cover and fit the servo cover retaining
circlip, aligning the gap with the pan rail, and ensuring that
it is completely seated in its groove.
Figure 8.21 - Extension Housing
Figure 8.22 - Front Servo and Band