torque SSANGYONG MUSSO 1998 Workshop Repair Manual
[x] Cancel search | Manufacturer: SSANGYONG, Model Year: 1998, Model line: MUSSO, Model: SSANGYONG MUSSO 1998Pages: 1463, PDF Size: 19.88 MB
Page 1218 of 1463
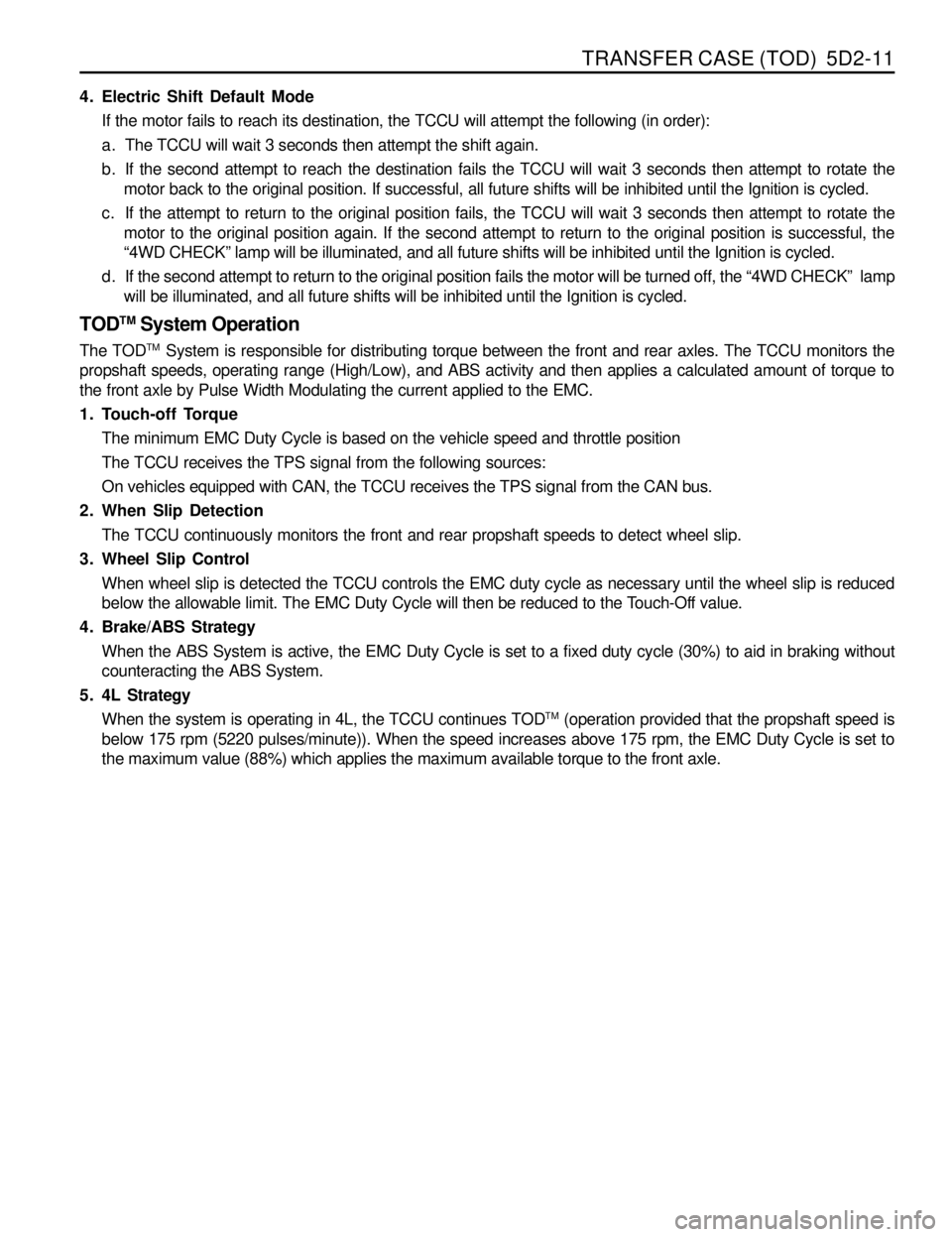
TRANSFER CASE (TOD) 5D2-11
4. Electric Shift Default Mode
If the motor fails to reach its destination, the TCCU will attempt the following (in order):
a. The TCCU will wait 3 seconds then attempt the shift again.
b. If the second attempt to reach the destination fails the TCCU will wait 3 seconds then attempt to rotate the
motor back to the original position. If successful, all future shifts will be inhibited until the Ignition is cycled.
c. If the attempt to return to the original position fails, the TCCU will wait 3 seconds then attempt to rotate the
motor to the original position again. If the second attempt to return to the original position is successful, the
“4WD CHECK” lamp will be illuminated, and all future shifts will be inhibited until the Ignition is cycled.
d. If the second attempt to return to the original position fails the motor will be turned off, the “4WD CHECK” lamp
will be illuminated, and all future shifts will be inhibited until the Ignition is cycled.
TODTM System Operation
The TODTM System is responsible for distributing torque between the front and rear axles. The TCCU monitors the
propshaft speeds, operating range (High/Low), and ABS activity and then applies a calculated amount of torque to
the front axle by Pulse Width Modulating the current applied to the EMC.
1. Touch-off Torque
The minimum EMC Duty Cycle is based on the vehicle speed and throttle position
The TCCU receives the TPS signal from the following sources:
On vehicles equipped with CAN, the TCCU receives the TPS signal from the CAN bus.
2. When Slip Detection
The TCCU continuously monitors the front and rear propshaft speeds to detect wheel slip.
3. Wheel Slip Control
When wheel slip is detected the TCCU controls the EMC duty cycle as necessary until the wheel slip is reduced
below the allowable limit. The EMC Duty Cycle will then be reduced to the Touch-Off value.
4. Brake/ABS Strategy
When the ABS System is active, the EMC Duty Cycle is set to a fixed duty cycle (30%) to aid in braking without
counteracting the ABS System.
5. 4L Strategy
When the system is operating in 4L, the TCCU continues TOD
TM (operation provided that the propshaft speed is
below 175 rpm (5220 pulses/minute)). When the speed increases above 175 rpm, the EMC Duty Cycle is set to
the maximum value (88%) which applies the maximum available torque to the front axle.
Page 1240 of 1463
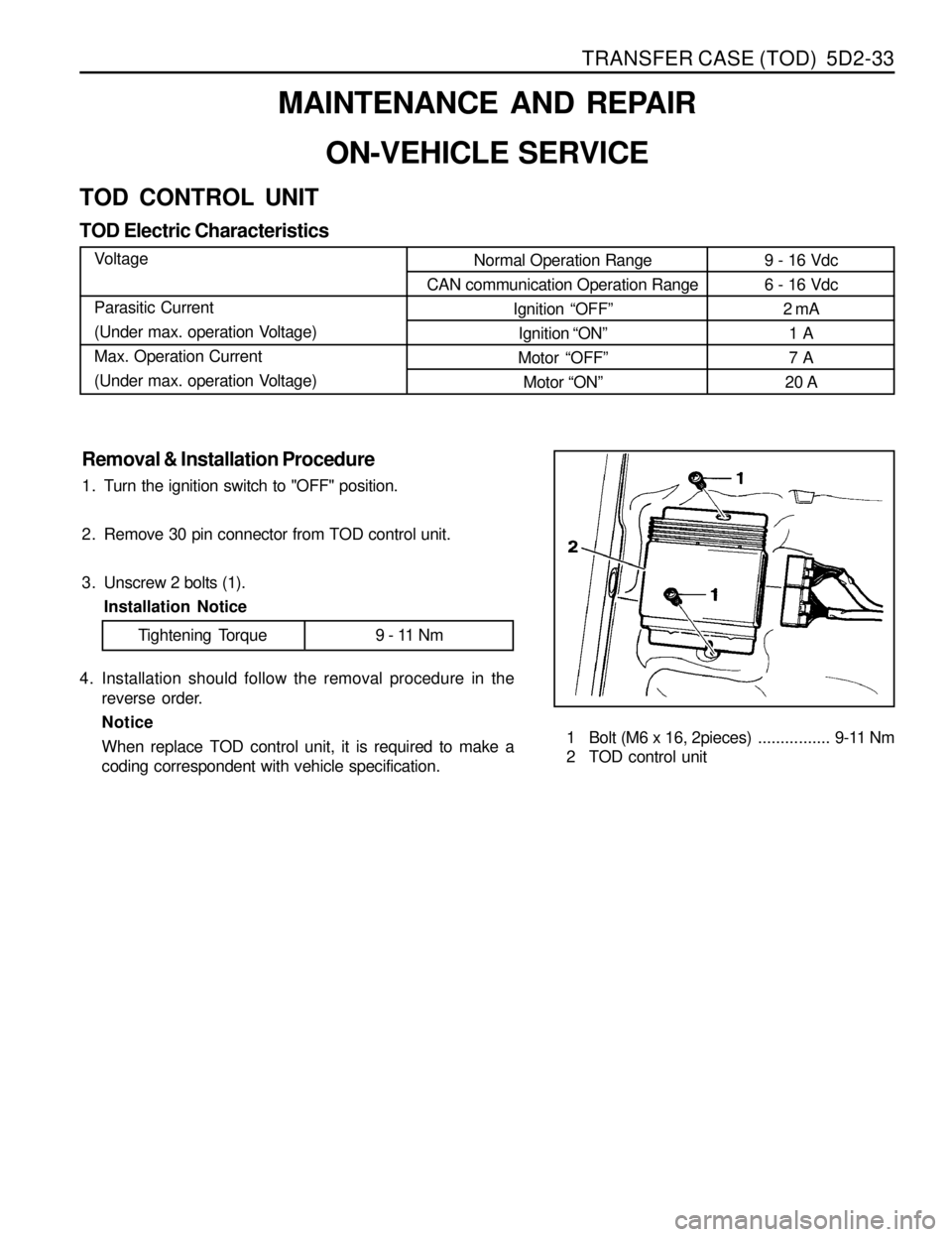
TRANSFER CASE (TOD) 5D2-33
9 - 16 Vdc
6 - 16 Vdc
2 mA
1 A
7 A
20 A
Removal & Installation Procedure
1. Turn the ignition switch to "OFF" position.
2. Remove 30 pin connector from TOD control unit.
3. Unscrew 2 bolts (1).
Installation Notice
1 Bolt (M6 x 16, 2pieces)................ 9-11 Nm
2 TOD control unit
MAINTENANCE AND REPAIR
ON-VEHICLE SERVICE
TOD CONTROL UNIT
TOD Electric Characteristics
Voltage
Parasitic Current
(Under max. operation Voltage)
Max. Operation Current
(Under max. operation Voltage)Normal Operation Range
CAN communication Operation Range
Ignition “OFF”
Ignition “ON”
Motor “OFF”
Motor “ON”
4. Installation should follow the removal procedure in the
reverse order.
Notice
When replace TOD control unit, it is required to make a
coding correspondent with vehicle specification.
Tightening Torque 9 - 11 Nm
Page 1243 of 1463
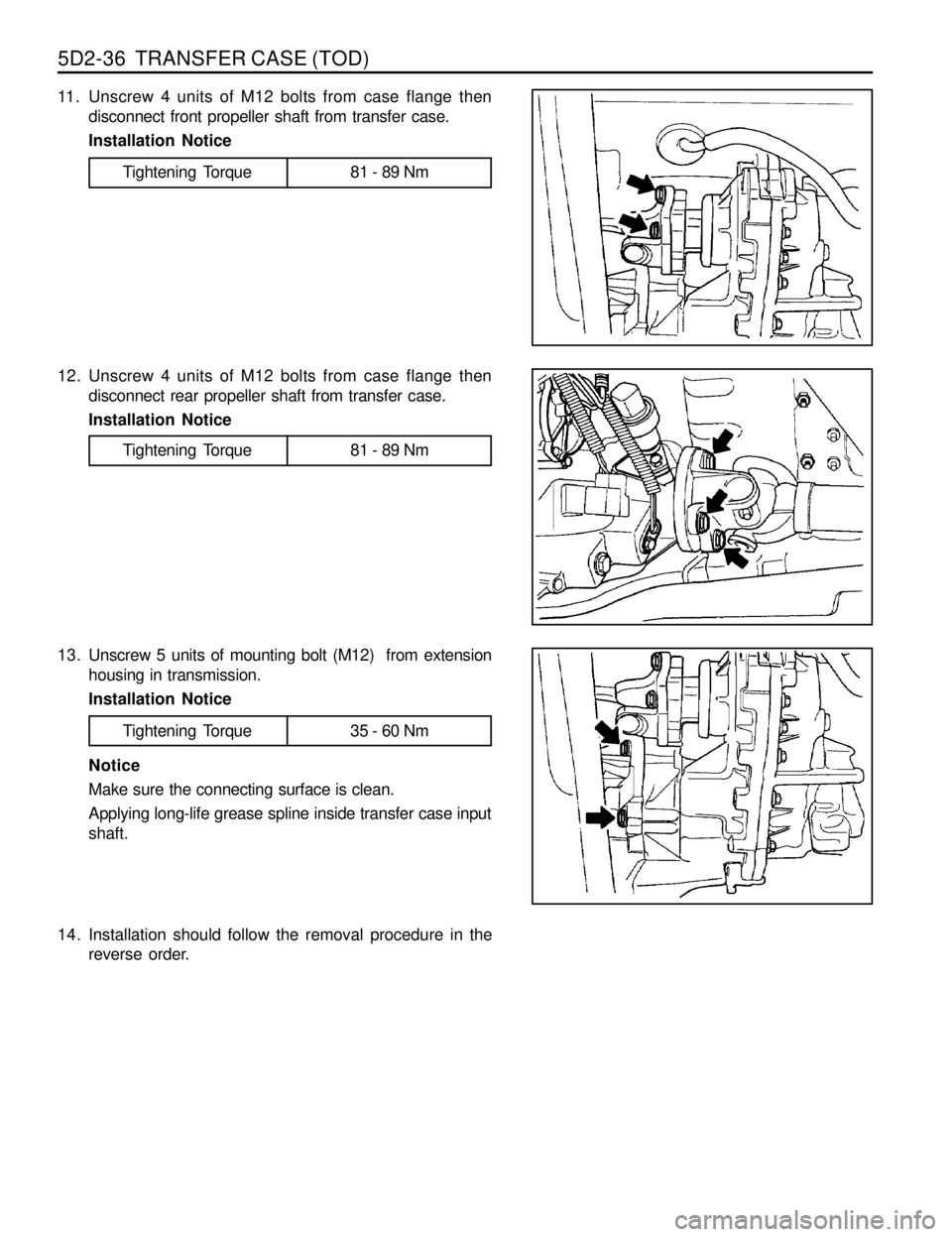
5D2-36 TRANSFER CASE (TOD)
11. Unscrew 4 units of M12 bolts from case flange then
disconnect front propeller shaft from transfer case.
Installation Notice
Tightening Torque 81 - 89 Nm
12. Unscrew 4 units of M12 bolts from case flange then
disconnect rear propeller shaft from transfer case.
Installation Notice
13. Unscrew 5 units of mounting bolt (M12) from extension
housing in transmission.
Installation Notice
Tightening Torque 81 - 89 Nm
Tightening Torque 35 - 60 Nm
Notice
Make sure the connecting surface is clean.
Applying long-life grease spline inside transfer case input
shaft.
14. Installation should follow the removal procedure in the
reverse order.
Page 1244 of 1463
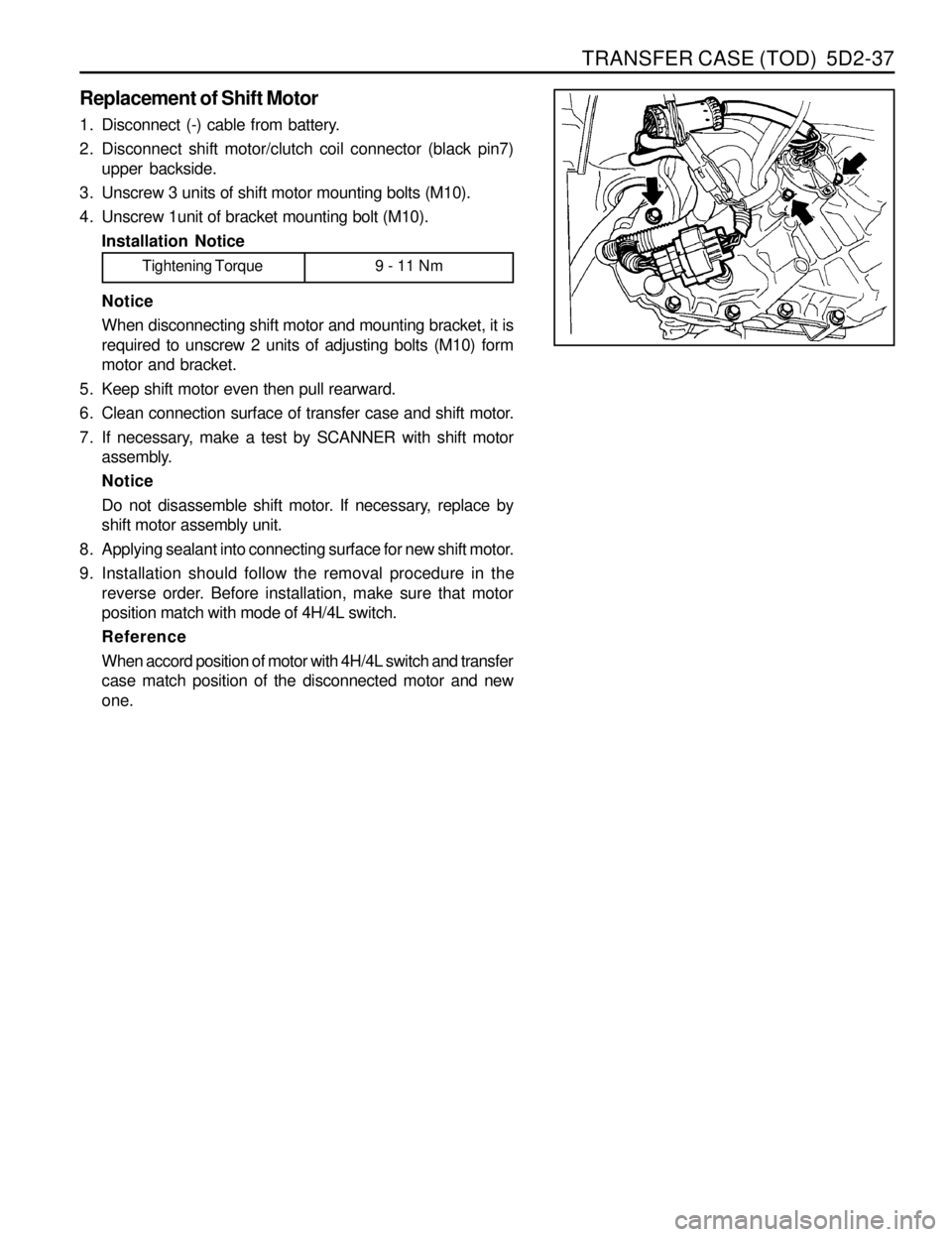
TRANSFER CASE (TOD) 5D2-37
Replacement of Shift Motor
1. Disconnect (-) cable from battery.
2. Disconnect shift motor/clutch coil connector (black pin7)
upper backside.
3. Unscrew 3 units of shift motor mounting bolts (M10).
4. Unscrew 1unit of bracket mounting bolt (M10).
Installation Notice
Tightening Torque 9 - 11 Nm
Notice
When disconnecting shift motor and mounting bracket, it is
required to unscrew 2 units of adjusting bolts (M10) form
motor and bracket.
5. Keep shift motor even then pull rearward.
6. Clean connection surface of transfer case and shift motor.
7. If necessary, make a test by SCANNER with shift motor
assembly.
Notice
Do not disassemble shift motor. If necessary, replace by
shift motor assembly unit.
8. Applying sealant into connecting surface for new shift motor.
9. Installation should follow the removal procedure in the
reverse order. Before installation, make sure that motor
position match with mode of 4H/4L switch.
Reference
When accord position of motor with 4H/4L switch and transfer
case match position of the disconnected motor and new
one.
Page 1246 of 1463
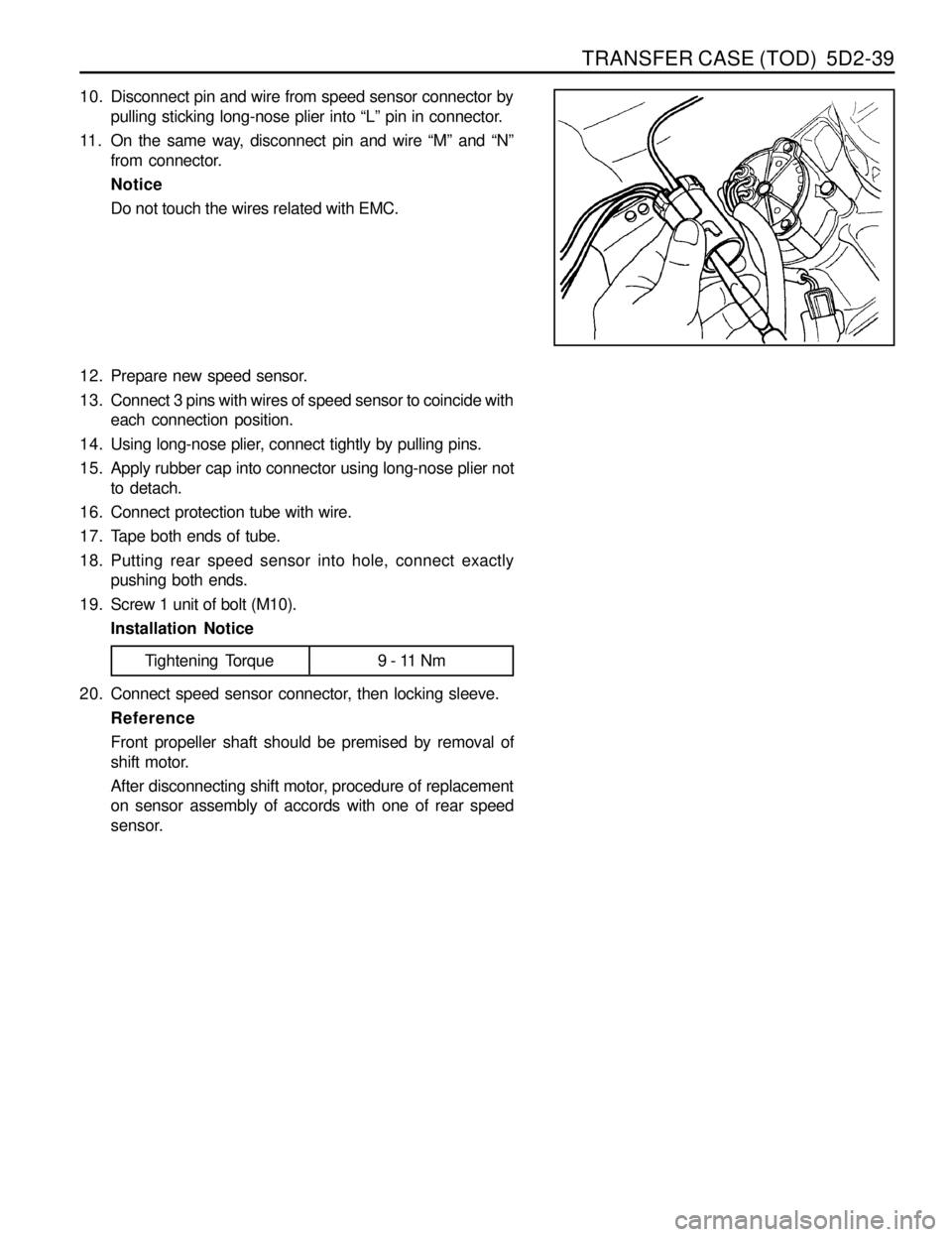
TRANSFER CASE (TOD) 5D2-39
10. Disconnect pin and wire from speed sensor connector by
pulling sticking long-nose plier into “L” pin in connector.
11. On the same way, disconnect pin and wire “M” and “N”
from connector.
Notice
Do not touch the wires related with EMC.
12. Prepare new speed sensor.
13. Connect 3 pins with wires of speed sensor to coincide with
each connection position.
14. Using long-nose plier, connect tightly by pulling pins.
15. Apply rubber cap into connector using long-nose plier not
to detach.
16. Connect protection tube with wire.
17. Tape both ends of tube.
18. Putting rear speed sensor into hole, connect exactly
pushing both ends.
19. Screw 1 unit of bolt (M10).
Installation Notice
Tightening Torque 9 - 11 Nm
20. Connect speed sensor connector, then locking sleeve.
Reference
Front propeller shaft should be premised by removal of
shift motor.
After disconnecting shift motor, procedure of replacement
on sensor assembly of accords with one of rear speed
sensor.
Page 1247 of 1463
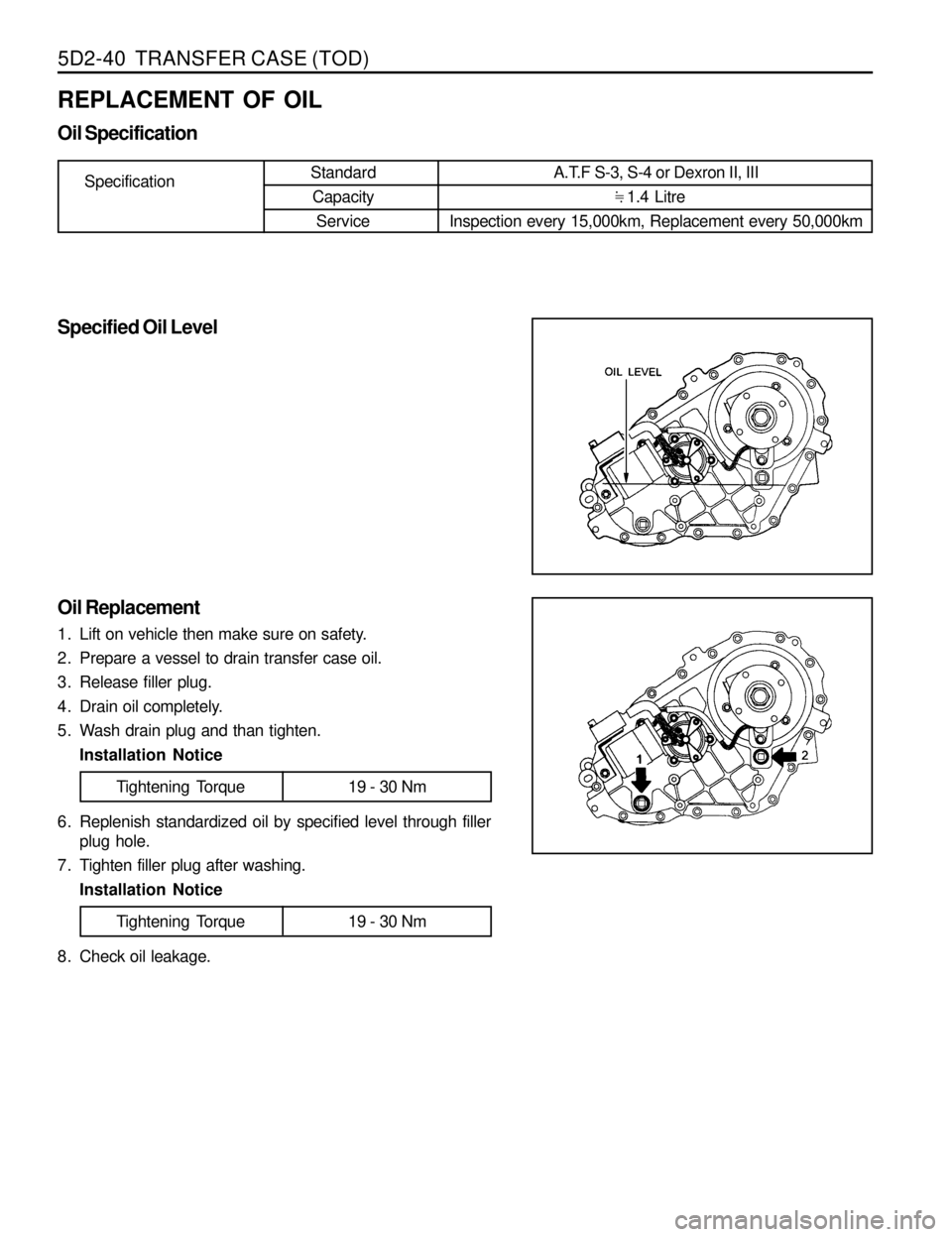
5D2-40 TRANSFER CASE (TOD)
REPLACEMENT OF OIL
Oil Specification
Specified Oil Level
SpecificationStandard
Capacity
ServiceA.T.F S-3, S-4 or Dexron II, III
1.4 Litre
Inspection every 15,000km, Replacement every 50,000km=
Oil Replacement
1. Lift on vehicle then make sure on safety.
2. Prepare a vessel to drain transfer case oil.
3. Release filler plug.
4. Drain oil completely.
5. Wash drain plug and than tighten.
Installation Notice
Tightening Torque 19 - 30 Nm
6. Replenish standardized oil by specified level through filler
plug hole.
7. Tighten filler plug after washing.
Installation Notice
8. Check oil leakage.
Tightening Torque 19 - 30 Nm
.
.
Page 1250 of 1463
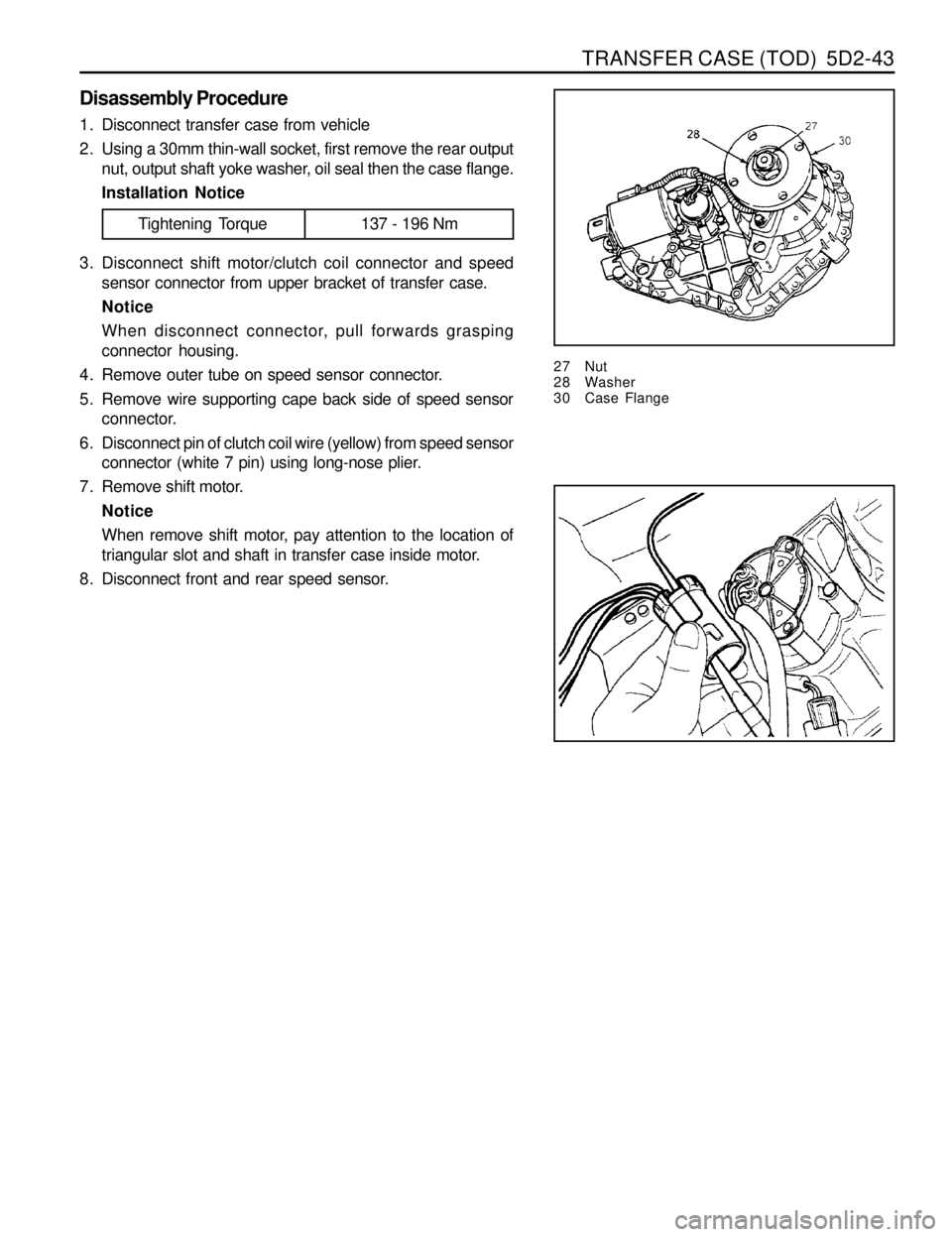
TRANSFER CASE (TOD) 5D2-43
Disassembly Procedure
1. Disconnect transfer case from vehicle
2. Using a 30mm thin-wall socket, first remove the rear output
nut, output shaft yoke washer, oil seal then the case flange.
Installation Notice
27 Nut
28 Washer
30 Case Flange
Tightening Torque 137 - 196 Nm
3. Disconnect shift motor/clutch coil connector and speed
sensor connector from upper bracket of transfer case.
Notice
When disconnect connector, pull forwards grasping
connector housing.
4. Remove outer tube on speed sensor connector.
5. Remove wire supporting cape back side of speed sensor
connector.
6. Disconnect pin of clutch coil wire (yellow) from speed sensor
connector (white 7 pin) using long-nose plier.
7. Remove shift motor.
Notice
When remove shift motor, pay attention to the location of
triangular slot and shaft in transfer case inside motor.
8. Disconnect front and rear speed sensor.
Page 1258 of 1463
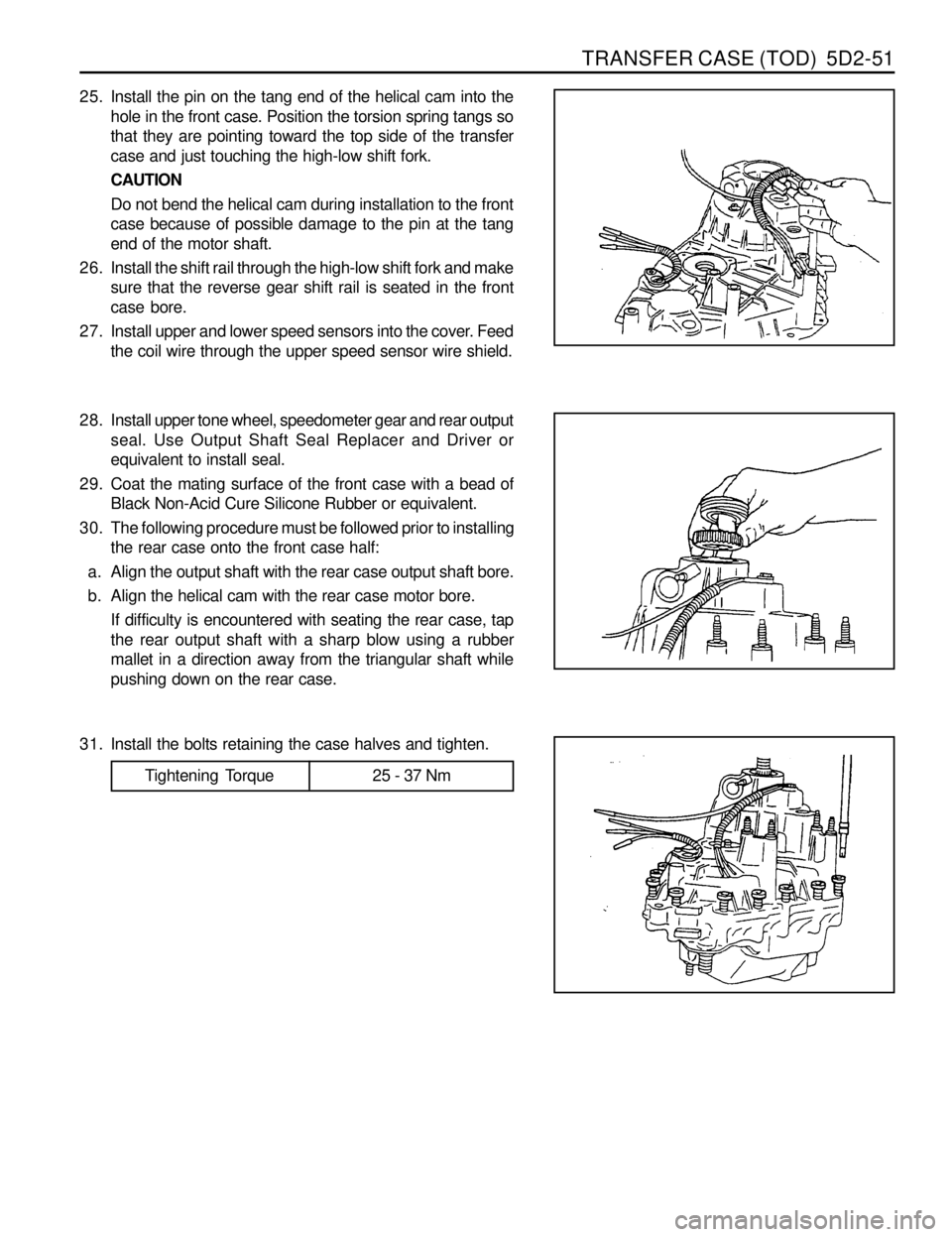
TRANSFER CASE (TOD) 5D2-51
25. Install the pin on the tang end of the helical cam into the
hole in the front case. Position the torsion spring tangs so
that they are pointing toward the top side of the transfer
case and just touching the high-low shift fork.
CAUTION
Do not bend the helical cam during installation to the front
case because of possible damage to the pin at the tang
end of the motor shaft.
26. Install the shift rail through the high-low shift fork and make
sure that the reverse gear shift rail is seated in the front
case bore.
27. Install upper and lower speed sensors into the cover. Feed
the coil wire through the upper speed sensor wire shield.
28. Install upper tone wheel, speedometer gear and rear output
seal. Use Output Shaft Seal Replacer and Driver or
equivalent to install seal.
29. Coat the mating surface of the front case with a bead of
Black Non-Acid Cure Silicone Rubber or equivalent.
30. The following procedure must be followed prior to installing
the rear case onto the front case half:
a. Align the output shaft with the rear case output shaft bore.
b. Align the helical cam with the rear case motor bore.
If difficulty is encountered with seating the rear case, tap
the rear output shaft with a sharp blow using a rubber
mallet in a direction away from the triangular shaft while
pushing down on the rear case.
Tightening Torque 25 - 37 Nm 31. Install the bolts retaining the case halves and tighten.
Page 1260 of 1463
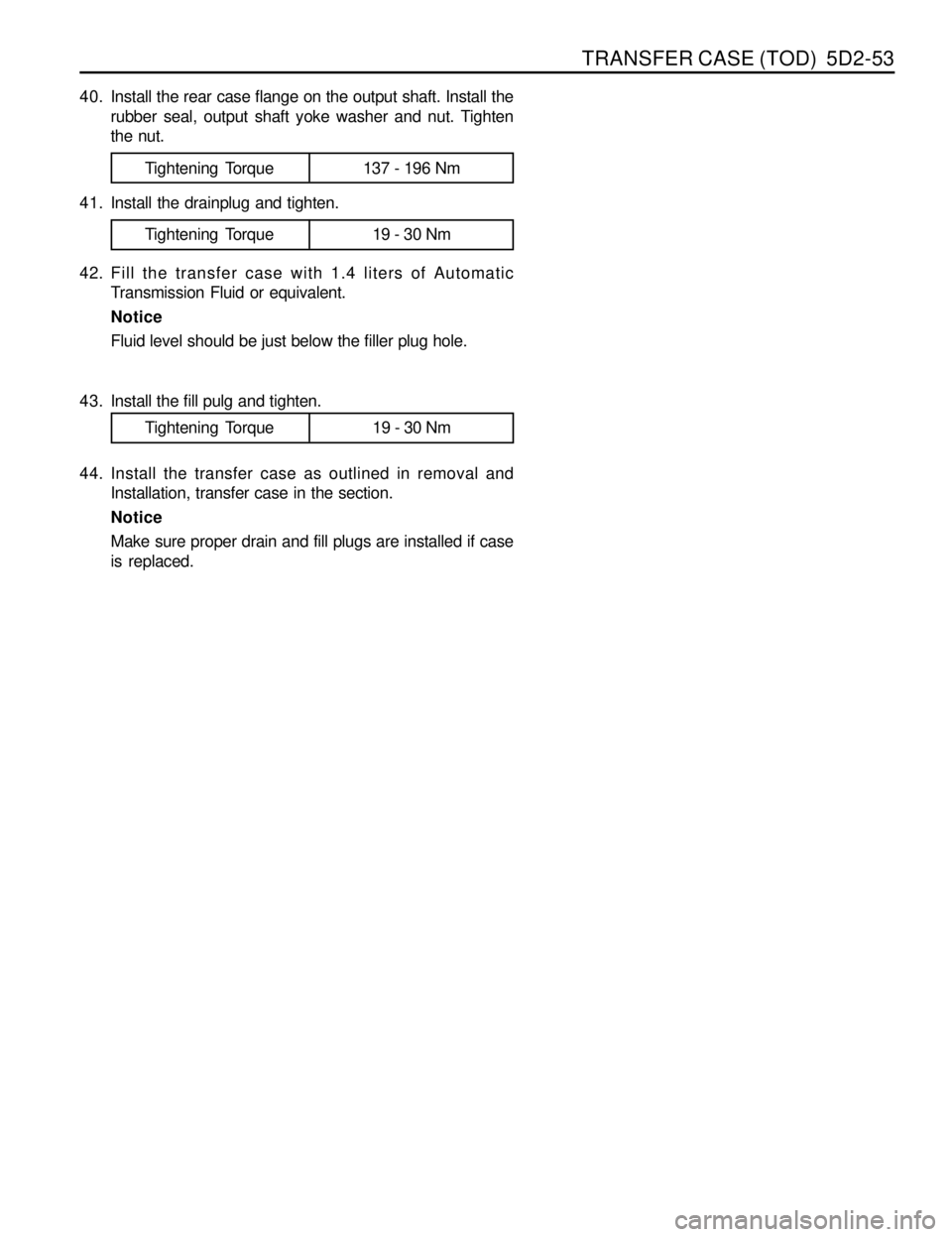
TRANSFER CASE (TOD) 5D2-53
40. Install the rear case flange on the output shaft. Install the
rubber seal, output shaft yoke washer and nut. Tighten
the nut.
Tightening Torque 137 - 196 Nm
41. Install the drainplug and tighten.
42. Fill the transfer case with 1.4 liters of Automatic
Transmission Fluid or equivalent.
Notice
Fluid level should be just below the filler plug hole.
Tightening Torque 19 - 30 Nm
Tightening Torque 19 - 30 Nm 43. Install the fill pulg and tighten.
44. Install the transfer case as outlined in removal and
Installation, transfer case in the section.
Notice
Make sure proper drain and fill plugs are installed if case
is replaced.
Page 1268 of 1463
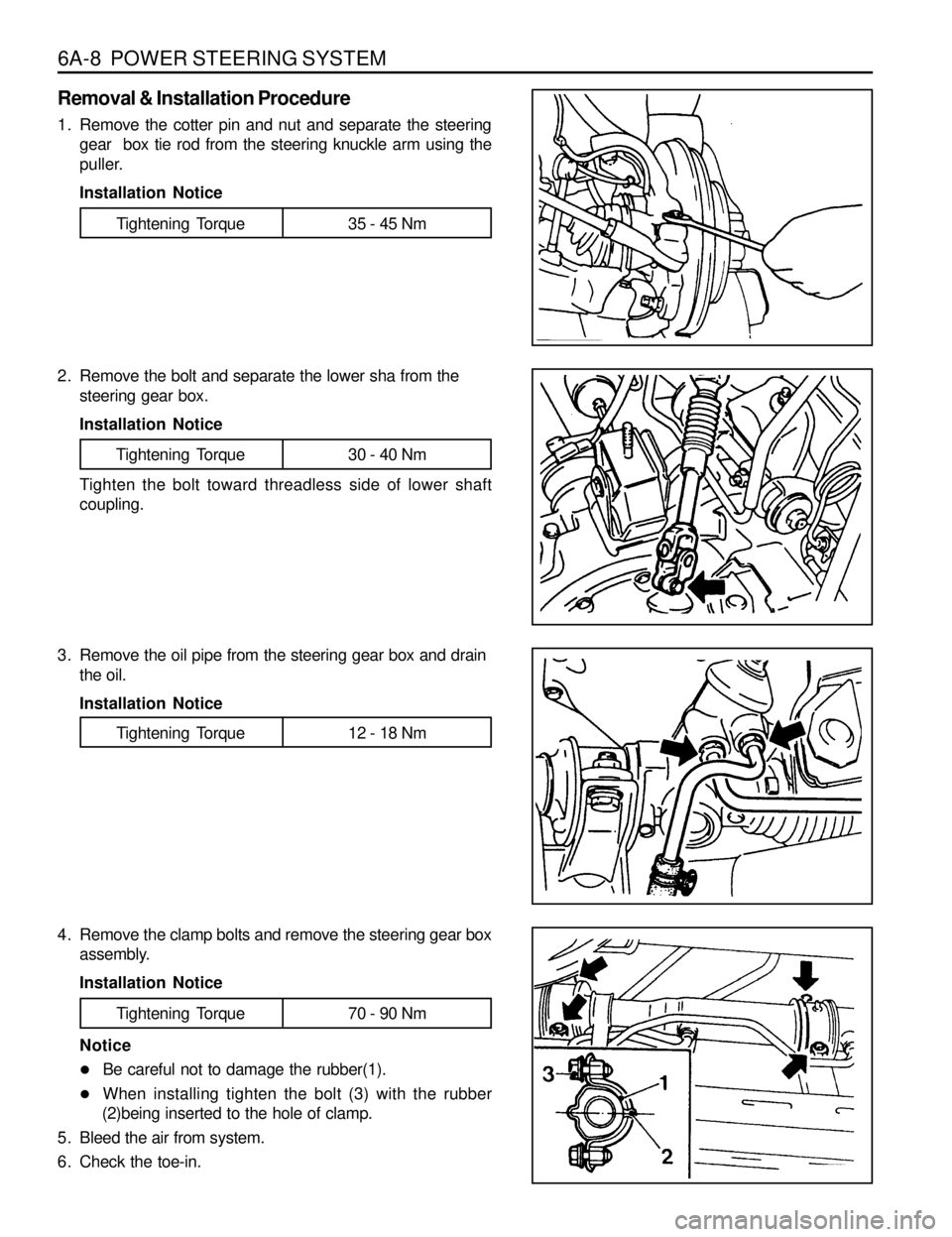
6A-8 POWER STEERING SYSTEM
Tightening Torque 35 - 45 Nm
Removal & Installation Procedure
1. Remove the cotter pin and nut and separate the steering
gear box tie rod from the steering knuckle arm using the
puller.
Installation Notice
2. Remove the bolt and separate the lower sha from the
steering gear box.
Installation Notice
Tightening Torque 30 - 40 Nm
3. Remove the oil pipe from the steering gear box and drain
the oil.
Installation Notice
4. Remove the clamp bolts and remove the steering gear box
assembly.
Installation Notice
Tightening Torque 12 - 18 Nm
Notice
lBe careful not to damage the rubber(1).
lWhen installing tighten the bolt (3) with the rubber
(2)being inserted to the hole of clamp.
5. Bleed the air from system.
6. Check the toe-in.
Tightening Torque 70 - 90 Nm Tighten the bolt toward threadless side of lower shaft
coupling.