torque SSANGYONG MUSSO 1998 Workshop Repair Manual
[x] Cancel search | Manufacturer: SSANGYONG, Model Year: 1998, Model line: MUSSO, Model: SSANGYONG MUSSO 1998Pages: 1463, PDF Size: 19.88 MB
Page 1008 of 1463
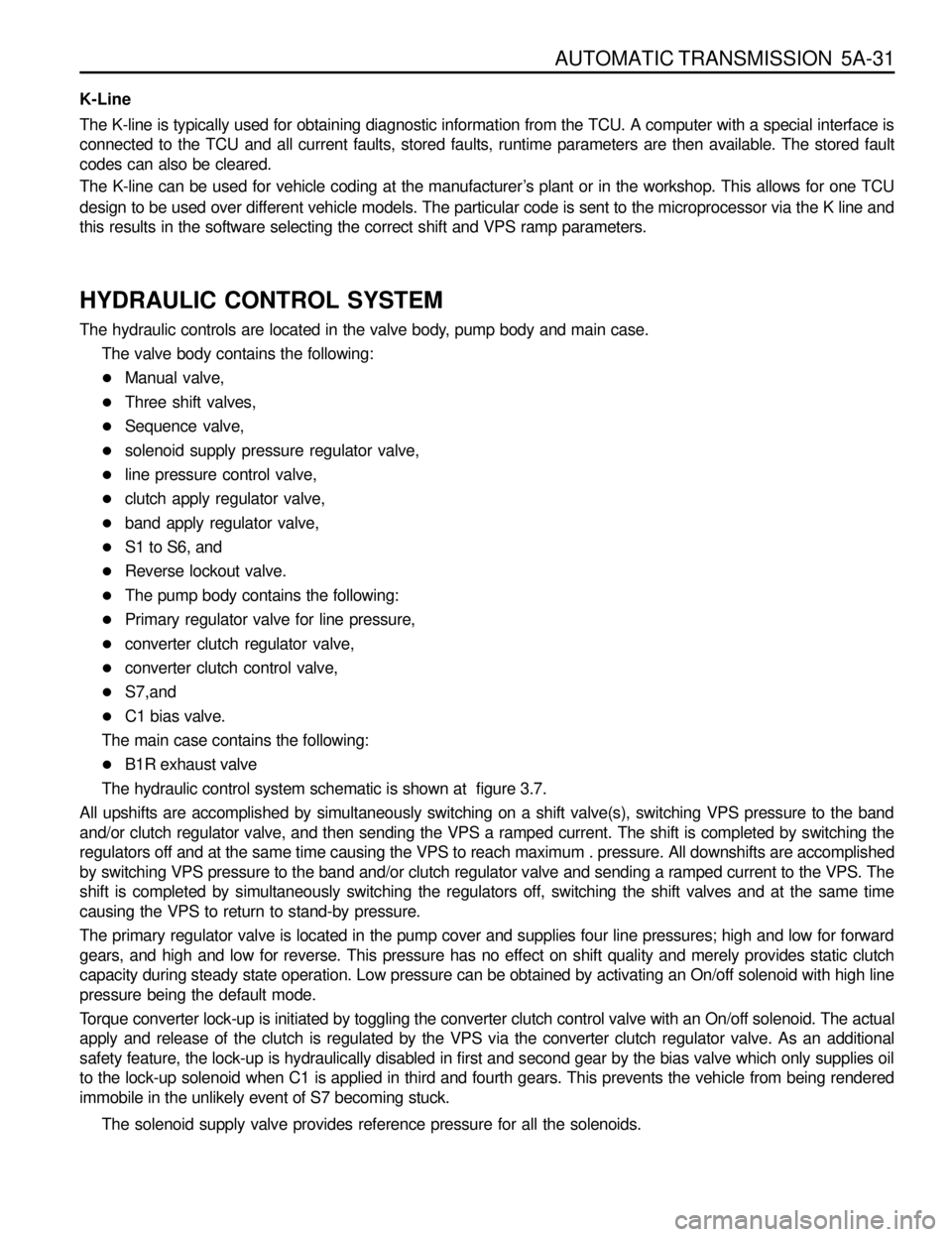
AUTOMATIC TRANSMISSION 5A-31
K-Line
The K-line is typically used for obtaining diagnostic information from the TCU. A computer with a special interface is
connected to the TCU and all current faults, stored faults, runtime parameters are then available. The stored fault
codes can also be cleared.
The K-line can be used for vehicle coding at the manufacturer’s plant or in the workshop. This allows for one TCU
design to be used over different vehicle models. The particular code is sent to the microprocessor via the K line and
this results in the software selecting the correct shift and VPS ramp parameters.
HYDRAULIC CONTROL SYSTEM
The hydraulic controls are located in the valve body, pump body and main case.
The valve body contains the following:
lManual valve,
lThree shift valves,
lSequence valve,
lsolenoid supply pressure regulator valve,
lline pressure control valve,
lclutch apply regulator valve,
lband apply regulator valve,
lS1 to S6, and
lReverse lockout valve.
lThe pump body contains the following:
lPrimary regulator valve for line pressure,
lconverter clutch regulator valve,
lconverter clutch control valve,
lS7,and
lC1 bias valve.
The main case contains the following:
lB1R exhaust valve
The hydraulic control system schematic is shown at figure 3.7.
All upshifts are accomplished by simultaneously switching on a shift valve(s), switching VPS pressure to the band
and/or clutch regulator valve, and then sending the VPS a ramped current. The shift is completed by switching the
regulators off and at the same time causing the VPS to reach maximum . pressure. All downshifts are accomplished
by switching VPS pressure to the band and/or clutch regulator valve and sending a ramped current to the VPS. The
shift is completed by simultaneously switching the regulators off, switching the shift valves and at the same time
causing the VPS to return to stand-by pressure.
The primary regulator valve is located in the pump cover and supplies four line pressures; high and low for forward
gears, and high and low for reverse. This pressure has no effect on shift quality and merely provides static clutch
capacity during steady state operation. Low pressure can be obtained by activating an On/off solenoid with high line
pressure being the default mode.
Torque converter lock-up is initiated by toggling the converter clutch control valve with an On/off solenoid. The actual
apply and release of the clutch is regulated by the VPS via the converter clutch regulator valve. As an additional
safety feature, the lock-up is hydraulically disabled in first and second gear by the bias valve which only supplies oil
to the lock-up solenoid when C1 is applied in third and fourth gears. This prevents the vehicle from being rendered
immobile in the unlikely event of S7 becoming stuck.
The solenoid supply valve provides reference pressure for all the solenoids.
Page 1019 of 1463
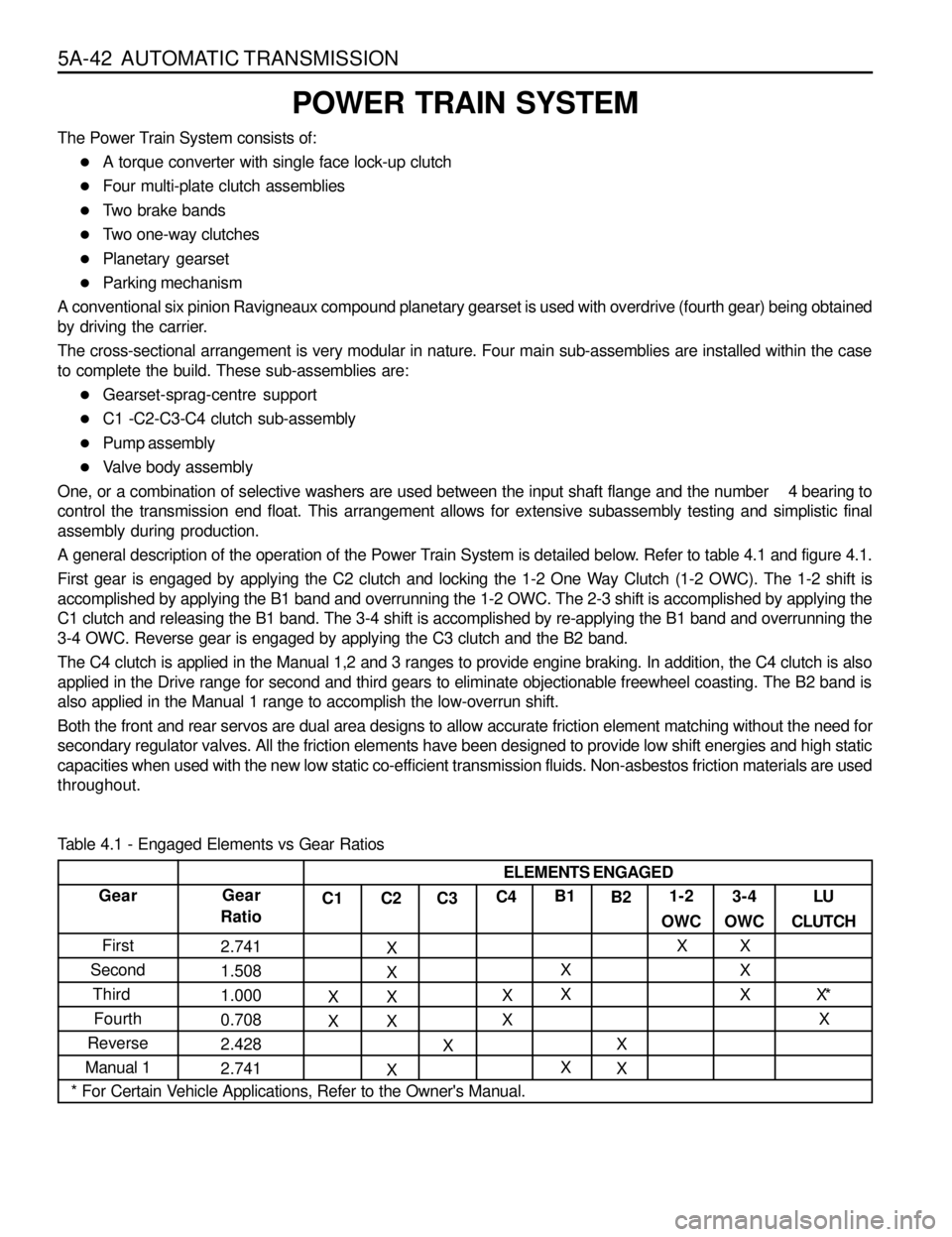
5A-42 AUTOMATIC TRANSMISSION
POWER TRAIN SYSTEM
The Power Train System consists of:
lA torque converter with single face lock-up clutch
lFour multi-plate clutch assemblies
lTwo brake bands
lTwo one-way clutches
lPlanetary gearset
lParking mechanism
A conventional six pinion Ravigneaux compound planetary gearset is used with overdrive (fourth gear) being obtained
by driving the carrier.
The cross-sectional arrangement is very modular in nature. Four main sub-assemblies are installed within the case
to complete the build. These sub-assemblies are:
lGearset-sprag-centre support
lC1 -C2-C3-C4 clutch sub-assembly
lPump assembly
lValve body assembly
One, or a combination of selective washers are used between the input shaft flange and the number 4 bearing to
control the transmission end float. This arrangement allows for extensive subassembly testing and simplistic final
assembly during production.
A general description of the operation of the Power Train System is detailed below. Refer to table 4.1 and figure 4.1.
First gear is engaged by applying the C2 clutch and locking the 1-2 One Way Clutch (1-2 OWC). The 1-2 shift is
accomplished by applying the B1 band and overrunning the 1-2 OWC. The 2-3 shift is accomplished by applying the
C1 clutch and releasing the B1 band. The 3-4 shift is accomplished by re-applying the B1 band and overrunning the
3-4 OWC. Reverse gear is engaged by applying the C3 clutch and the B2 band.
The C4 clutch is applied in the Manual 1,2 and 3 ranges to provide engine braking. In addition, the C4 clutch is also
applied in the Drive range for second and third gears to eliminate objectionable freewheel coasting. The B2 band is
also applied in the Manual 1 range to accomplish the low-overrun shift.
Both the front and rear servos are dual area designs to allow accurate friction element matching without the need for
secondary regulator valves. All the friction elements have been designed to provide low shift energies and high static
capacities when used with the new low static co-efficient transmission fluids. Non-asbestos friction materials are used
throughout.
Gear
First
Second
Third
Fourth
Reverse
Manual 1Gear
Ratio
2.741
1.508
1.000
0.708
2.428
2.741C1
X
XC2
X
X
X
X
XC3
XC4
X
XB1
X
X
XB2
X
X1-2
OWC
X3-4
OWC
X
X
XLU
CLUTCH
X*
X ELEMENTS ENGAGED
* For Certain Vehicle Applications, Refer to the Owner's Manual. Table 4.1 - Engaged Elements vs Gear Ratios
Page 1020 of 1463
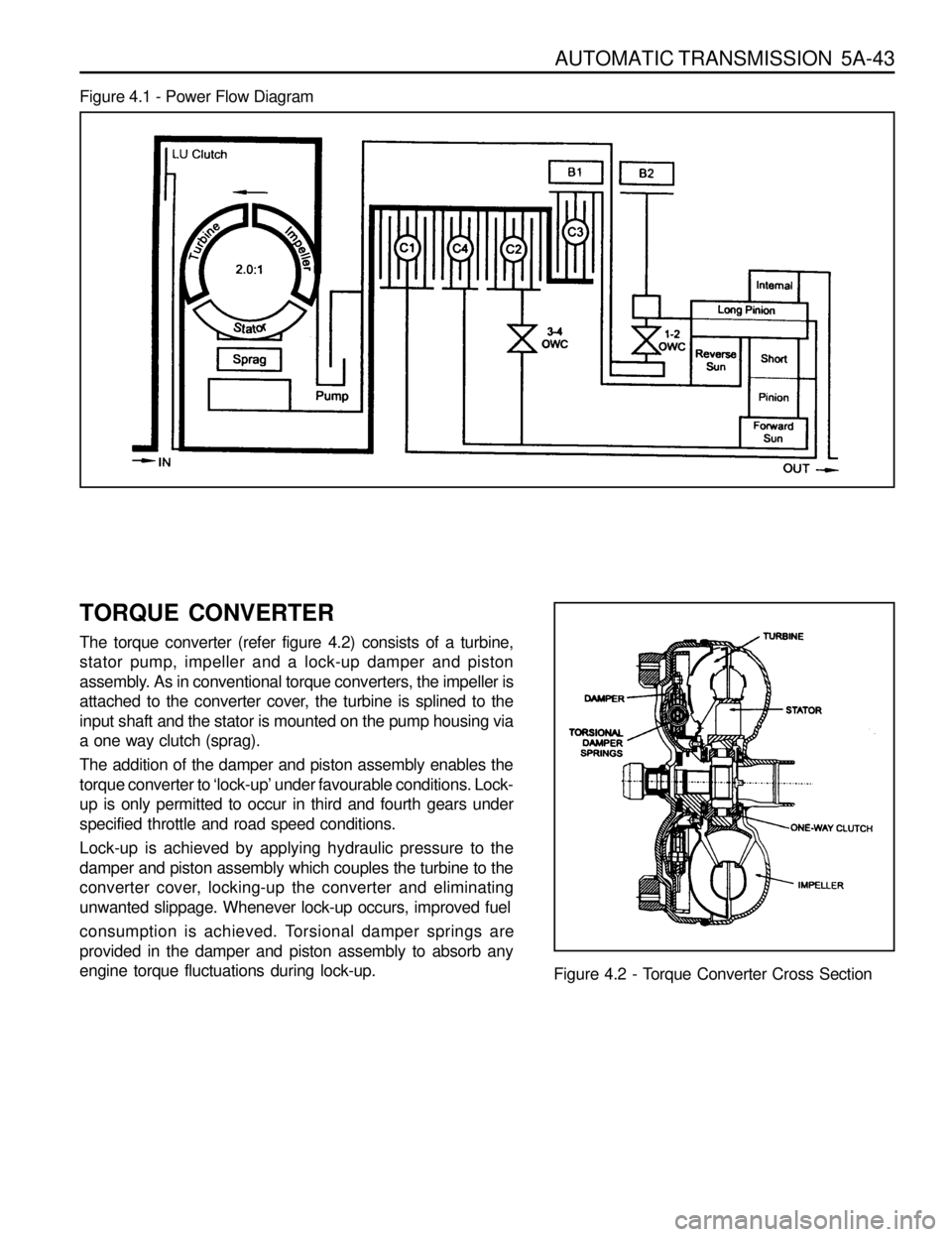
AUTOMATIC TRANSMISSION 5A-43
Figure 4.1 - Power Flow Diagram
TORQUE CONVERTER
The torque converter (refer figure 4.2) consists of a turbine,
stator pump, impeller and a lock-up damper and piston
assembly. As in conventional torque converters, the impeller is
attached to the converter cover, the turbine is splined to the
input shaft and the stator is mounted on the pump housing via
a one way clutch (sprag).
The addition of the damper and piston assembly enables the
torque converter to ‘lock-up’ under favourable conditions. Lock-
up is only permitted to occur in third and fourth gears under
specified throttle and road speed conditions.
Lock-up is achieved by applying hydraulic pressure to the
damper and piston assembly which couples the turbine to the
converter cover, locking-up the converter and eliminating
unwanted slippage. Whenever lock-up occurs, improved fuel
consumption is achieved. Torsional damper springs are
provided in the damper and piston assembly to absorb any
engine torque fluctuations during lock-up.
Figure 4.2 - Torque Converter Cross Section
Page 1022 of 1463
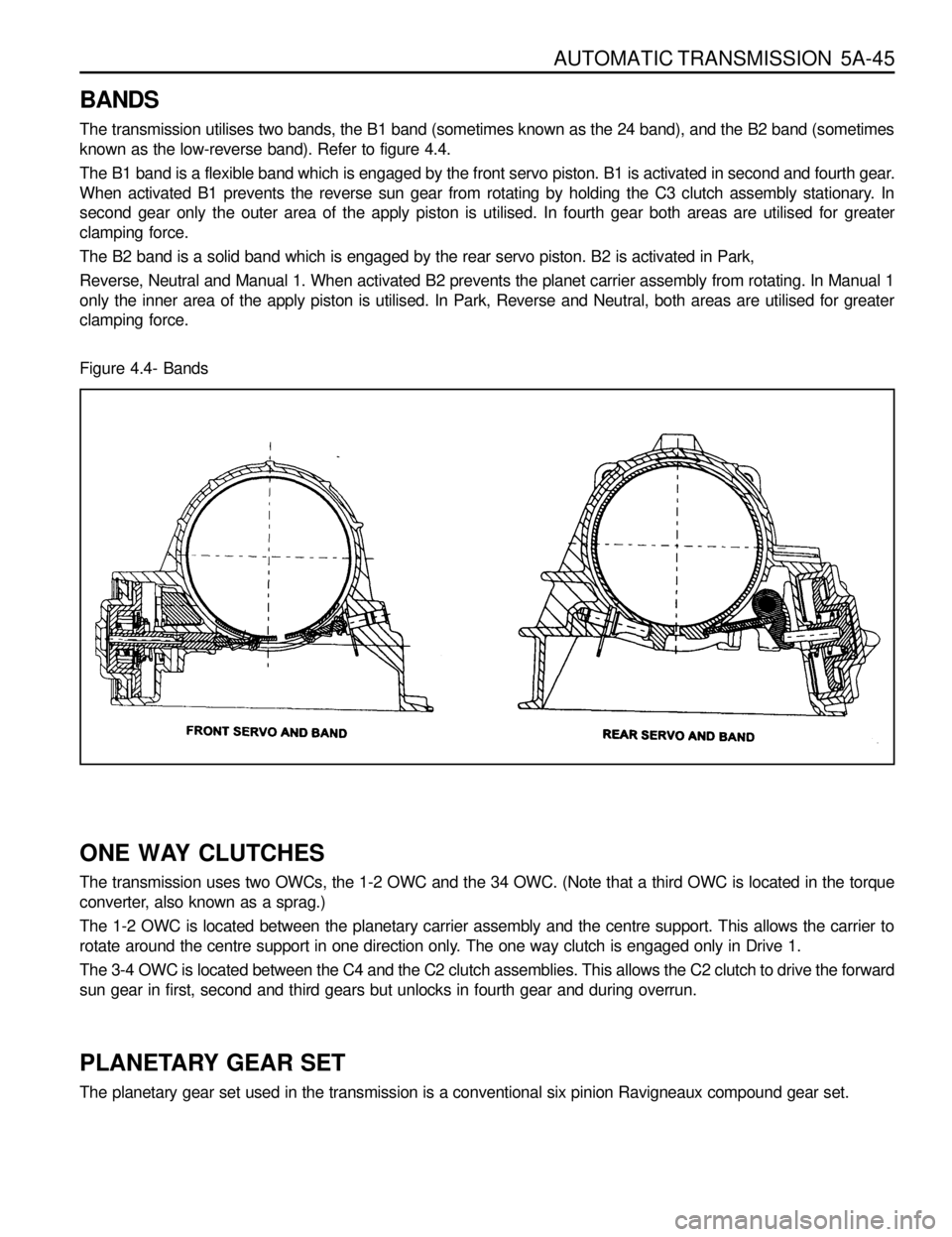
AUTOMATIC TRANSMISSION 5A-45
BANDS
The transmission utilises two bands, the B1 band (sometimes known as the 24 band), and the B2 band (sometimes
known as the low-reverse band). Refer to figure 4.4.
The B1 band is a flexible band which is engaged by the front servo piston. B1 is activated in second and fourth gear.
When activated B1 prevents the reverse sun gear from rotating by holding the C3 clutch assembly stationary. In
second gear only the outer area of the apply piston is utilised. In fourth gear both areas are utilised for greater
clamping force.
The B2 band is a solid band which is engaged by the rear servo piston. B2 is activated in Park,
Reverse, Neutral and Manual 1. When activated B2 prevents the planet carrier assembly from rotating. In Manual 1
only the inner area of the apply piston is utilised. In Park, Reverse and Neutral, both areas are utilised for greater
clamping force.
Figure 4.4- Bands
ONE WAY CLUTCHES
The transmission uses two OWCs, the 1-2 OWC and the 34 OWC. (Note that a third OWC is located in the torque
converter, also known as a sprag.)
The 1-2 OWC is located between the planetary carrier assembly and the centre support. This allows the carrier to
rotate around the centre support in one direction only. The one way clutch is engaged only in Drive 1.
The 3-4 OWC is located between the C4 and the C2 clutch assemblies. This allows the C2 clutch to drive the forward
sun gear in first, second and third gears but unlocks in fourth gear and during overrun.
PLANETARY GEAR SET
The planetary gear set used in the transmission is a conventional six pinion Ravigneaux compound gear set.
Page 1038 of 1463
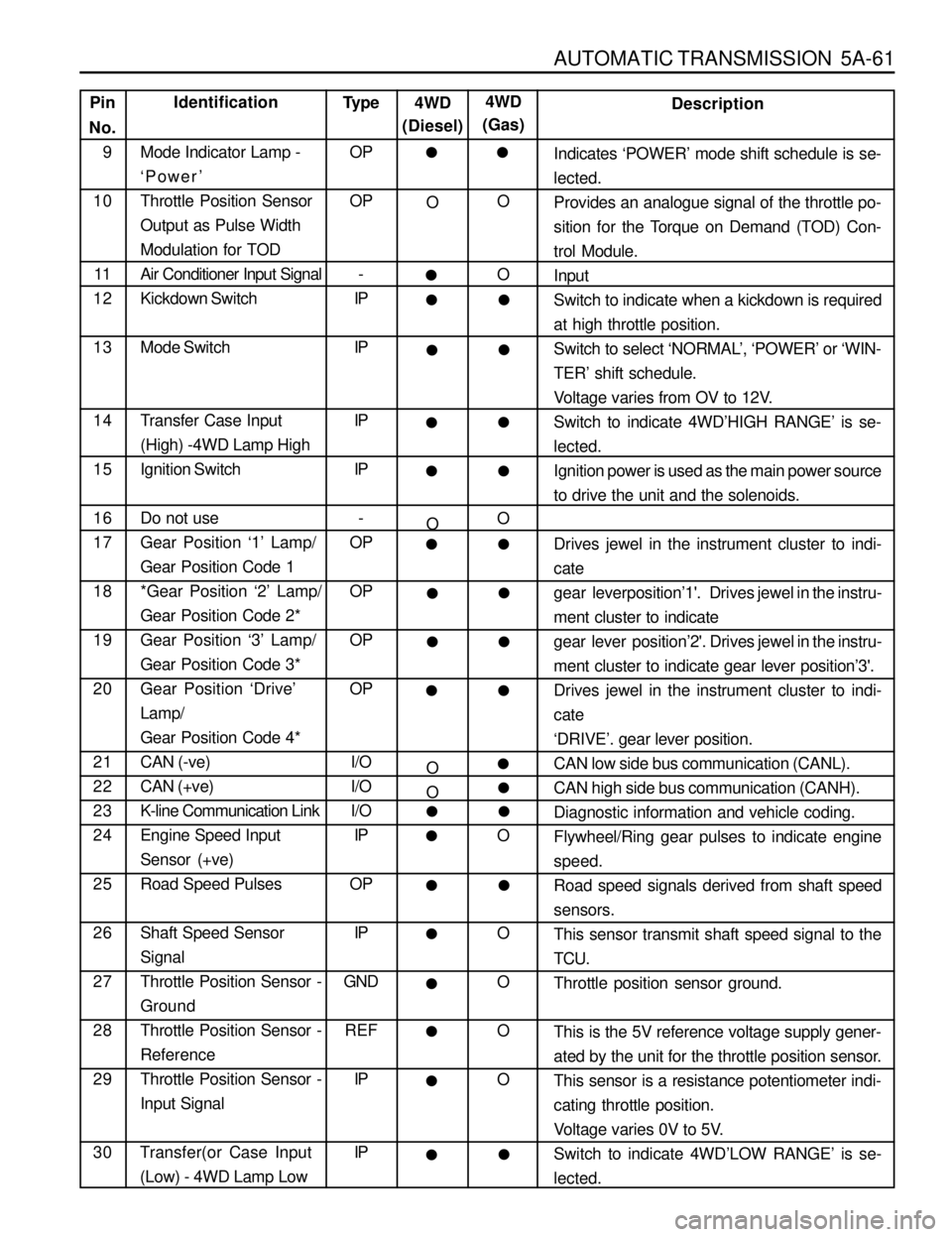
AUTOMATIC TRANSMISSION 5A-61
Pin
No.
9
10
11
12
13
14
15
16
17
18
19
20
21
22
23
24
25
26
27
28
29
30Identification
Mode Indicator Lamp -
‘Power’
Throttle Position Sensor
Output as Pulse Width
Modulation for TOD
Air Conditioner Input Signal
Kickdown Switch
Mode Switch
Transfer Case Input
(High) -4WD Lamp High
Ignition Switch
Do not use
Gear Position ‘1’ Lamp/
Gear Position Code 1
*Gear Position ‘2’ Lamp/
Gear Position Code 2*
Gear Position ‘3’ Lamp/
Gear Position Code 3*
Gear Position ‘Drive’
Lamp/
Gear Position Code 4*
CAN (-ve)
CAN (+ve)
K-line Communication Link
Engine Speed Input
Sensor (+ve)
Road Speed Pulses
Shaft Speed Sensor
Signal
Throttle Position Sensor -
Ground
Throttle Position Sensor -
Reference
Throttle Position Sensor -
Input Signal
Transfer(or Case Input
(Low) - 4WD Lamp LowType
OP
OP
-
IP
IP
IP
IP
-
OP
OP
OP
OP
I/O
I/O
I/O
IP
OP
IP
GND
REF
IP
IPDescription
Indicates ‘POWER’ mode shift schedule is se-
lected.
Provides an analogue signal of the throttle po-
sition for the Torque on Demand (TOD) Con-
trol Module.
Input
Switch to indicate when a kickdown is required
at high throttle position.
Switch to select ‘NORMAL’, ‘POWER’ or ‘WIN-
TER’ shift schedule.
Voltage varies from OV to 12V.
Switch to indicate 4WD’HIGH RANGE’ is se-
lected.
Ignition power is used as the main power source
to drive the unit and the solenoids.
Drives jewel in the instrument cluster to indi-
cate
gear leverposition’1'. Drives jewel in the instru-
ment cluster to indicate
gear lever position’2'. Drives jewel in the instru-
ment cluster to indicate gear lever position’3'.
Drives jewel in the instrument cluster to indi-
cate
‘DRIVE’. gear lever position.
CAN low side bus communication (CANL).
CAN high side bus communication (CANH).
Diagnostic information and vehicle coding.
Flywheel/Ring gear pulses to indicate engine
speed.
Road speed signals derived from shaft speed
sensors.
This sensor transmit shaft speed signal to the
TCU.
Throttle position sensor ground.
This is the 5V reference voltage supply gener-
ated by the unit for the throttle position sensor.
This sensor is a resistance potentiometer indi-
cating throttle position.
Voltage varies 0V to 5V.
Switch to indicate 4WD’LOW RANGE’ is se-
lected. 4WD
(Diesel)
O
O
O
O
l
l
l
4WD
(Gas)
O
O
O
O
O
O
O
O
l
l
l
ll
ll
ll
ll
ll
ll
l
l
ll
l
ll
l
l
l
l
ll l
Page 1039 of 1463
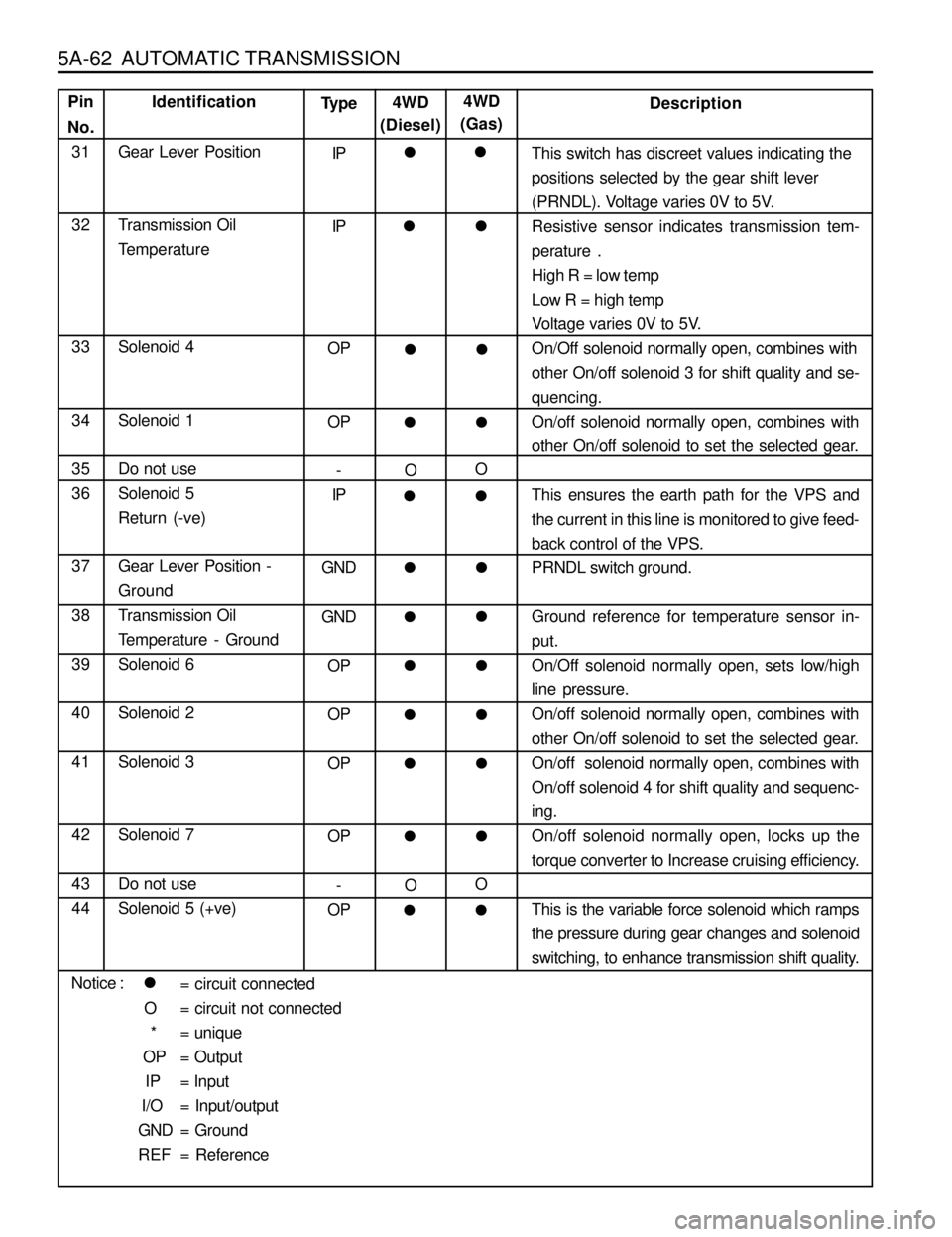
5A-62 AUTOMATIC TRANSMISSION
Identification
Gear Lever Position
Transmission Oil
Temperature
Solenoid 4
Solenoid 1
Do not use
Solenoid 5
Return (-ve)
Gear Lever Position -
Ground
Transmission Oil
Temperature - Ground
Solenoid 6
Solenoid 2
Solenoid 3
Solenoid 7
Do not use
Solenoid 5 (+ve)Type
IP
IP
OP
OP
-
IP
GND
GND
OP
OP
OP
OP
-
OPDescription
This switch has discreet values indicating the
positions selected by the gear shift lever
(PRNDL). Voltage varies 0V to 5V.
Resistive sensor indicates transmission tem-
perature .
High R = low temp
Low R = high temp
Voltage varies 0V to 5V.
On/Off solenoid normally open, combines with
other On/off solenoid 3 for shift quality and se-
quencing.
On/off solenoid normally open, combines with
other On/off solenoid to set the selected gear.
This ensures the earth path for the VPS and
the current in this line is monitored to give feed-
back control of the VPS.
PRNDL switch ground.
Ground reference for temperature sensor in-
put.
On/Off solenoid normally open, sets low/high
line pressure.
On/off solenoid normally open, combines with
other On/off solenoid to set the selected gear.
On/off solenoid normally open, combines with
On/off solenoid 4 for shift quality and sequenc-
ing.
On/off solenoid normally open, locks up the
torque converter to Increase cruising efficiency.
This is the variable force solenoid which ramps
the pressure during gear changes and solenoid
switching, to enhance transmission shift quality. 4WD
(Diesel)
O
O
l
l
4WD
(Gas)
O
O
l
l
ll
ll
ll
ll
Pin
No.
31
32
33
34
35
36
37
38
39
40
41
42
43
44
ll
ll
ll
ll
ll
ll
l= circuit connected
O = circuit not connected
* = unique
OP = Output
IP = Input
I/O = Input/output
GND = Ground
REF = Reference Notice :
Page 1041 of 1463
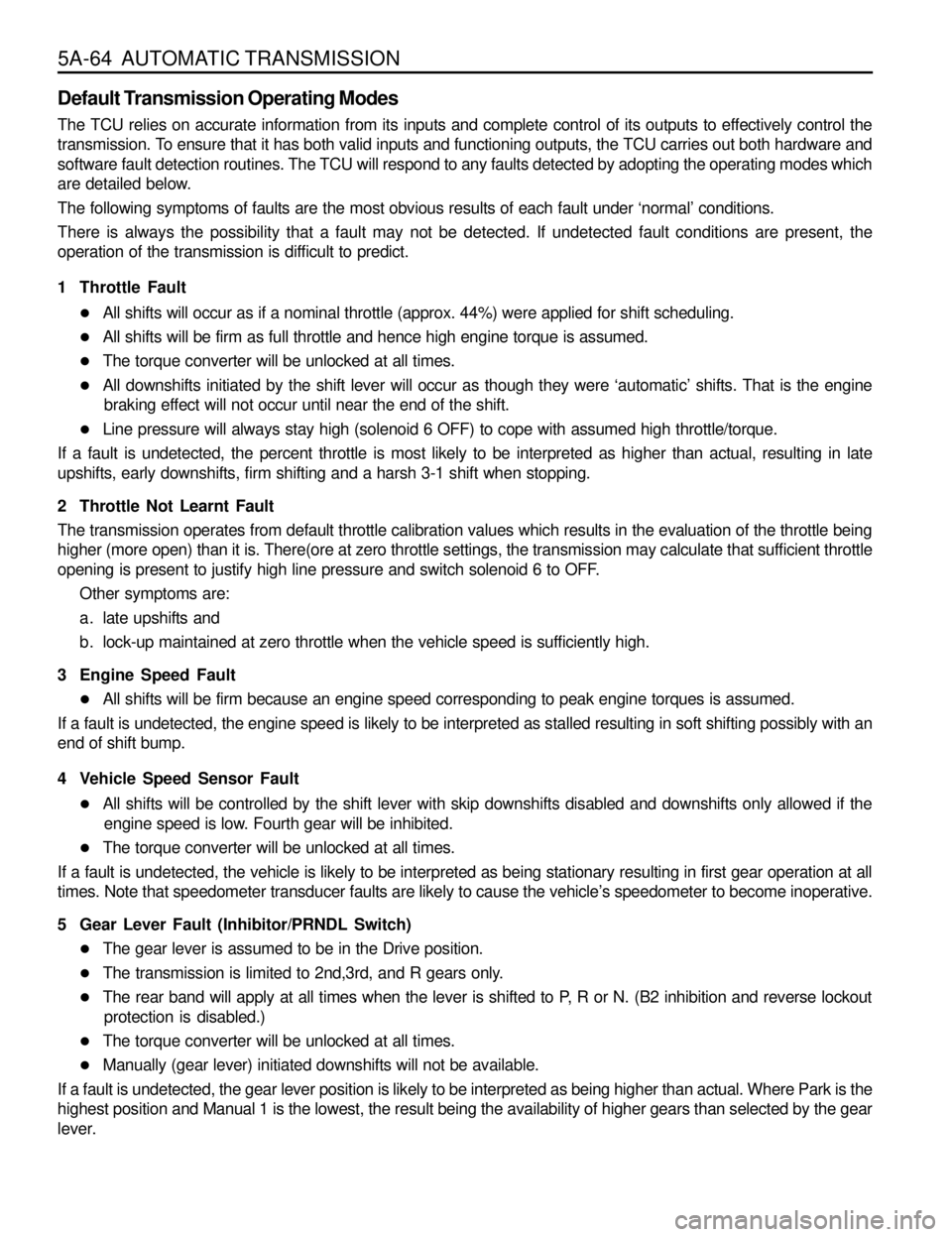
5A-64 AUTOMATIC TRANSMISSION
Default Transmission Operating Modes
The TCU relies on accurate information from its inputs and complete control of its outputs to effectively control the
transmission. To ensure that it has both valid inputs and functioning outputs, the TCU carries out both hardware and
software fault detection routines. The TCU will respond to any faults detected by adopting the operating modes which
are detailed below.
The following symptoms of faults are the most obvious results of each fault under ‘normal’ conditions.
There is always the possibility that a fault may not be detected. If undetected fault conditions are present, the
operation of the transmission is difficult to predict.
1 Throttle Fault
lAll shifts will occur as if a nominal throttle (approx. 44%) were applied for shift scheduling.
lAll shifts will be firm as full throttle and hence high engine torque is assumed.
lThe torque converter will be unlocked at all times.
lAll downshifts initiated by the shift lever will occur as though they were ‘automatic’ shifts. That is the engine
braking effect will not occur until near the end of the shift.
lLine pressure will always stay high (solenoid 6 OFF) to cope with assumed high throttle/torque.
If a fault is undetected, the percent throttle is most likely to be interpreted as higher than actual, resulting in late
upshifts, early downshifts, firm shifting and a harsh 3-1 shift when stopping.
2 Throttle Not Learnt Fault
The transmission operates from default throttle calibration values which results in the evaluation of the throttle being
higher (more open) than it is. There(ore at zero throttle settings, the transmission may calculate that sufficient throttle
opening is present to justify high line pressure and switch solenoid 6 to OFF.
Other symptoms are:
a. late upshifts and
b. lock-up maintained at zero throttle when the vehicle speed is sufficiently high.
3 Engine Speed Fault
lAll shifts will be firm because an engine speed corresponding to peak engine torques is assumed.
If a fault is undetected, the engine speed is likely to be interpreted as stalled resulting in soft shifting possibly with an
end of shift bump.
4 Vehicle Speed Sensor Fault
lAll shifts will be controlled by the shift lever with skip downshifts disabled and downshifts only allowed if the
engine speed is low. Fourth gear will be inhibited.
lThe torque converter will be unlocked at all times.
If a fault is undetected, the vehicle is likely to be interpreted as being stationary resulting in first gear operation at all
times. Note that speedometer transducer faults are likely to cause the vehicle’s speedometer to become inoperative.
5 Gear Lever Fault (Inhibitor/PRNDL Switch)
lThe gear lever is assumed to be in the Drive position.
lThe transmission is limited to 2nd,3rd, and R gears only.
lThe rear band will apply at all times when the lever is shifted to P, R or N. (B2 inhibition and reverse lockout
protection is disabled.)
lThe torque converter will be unlocked at all times.
lManually (gear lever) initiated downshifts will not be available.
If a fault is undetected, the gear lever position is likely to be interpreted as being higher than actual. Where Park is the
highest position and Manual 1 is the lowest, the result being the availability of higher gears than selected by the gear
lever.
Page 1043 of 1463
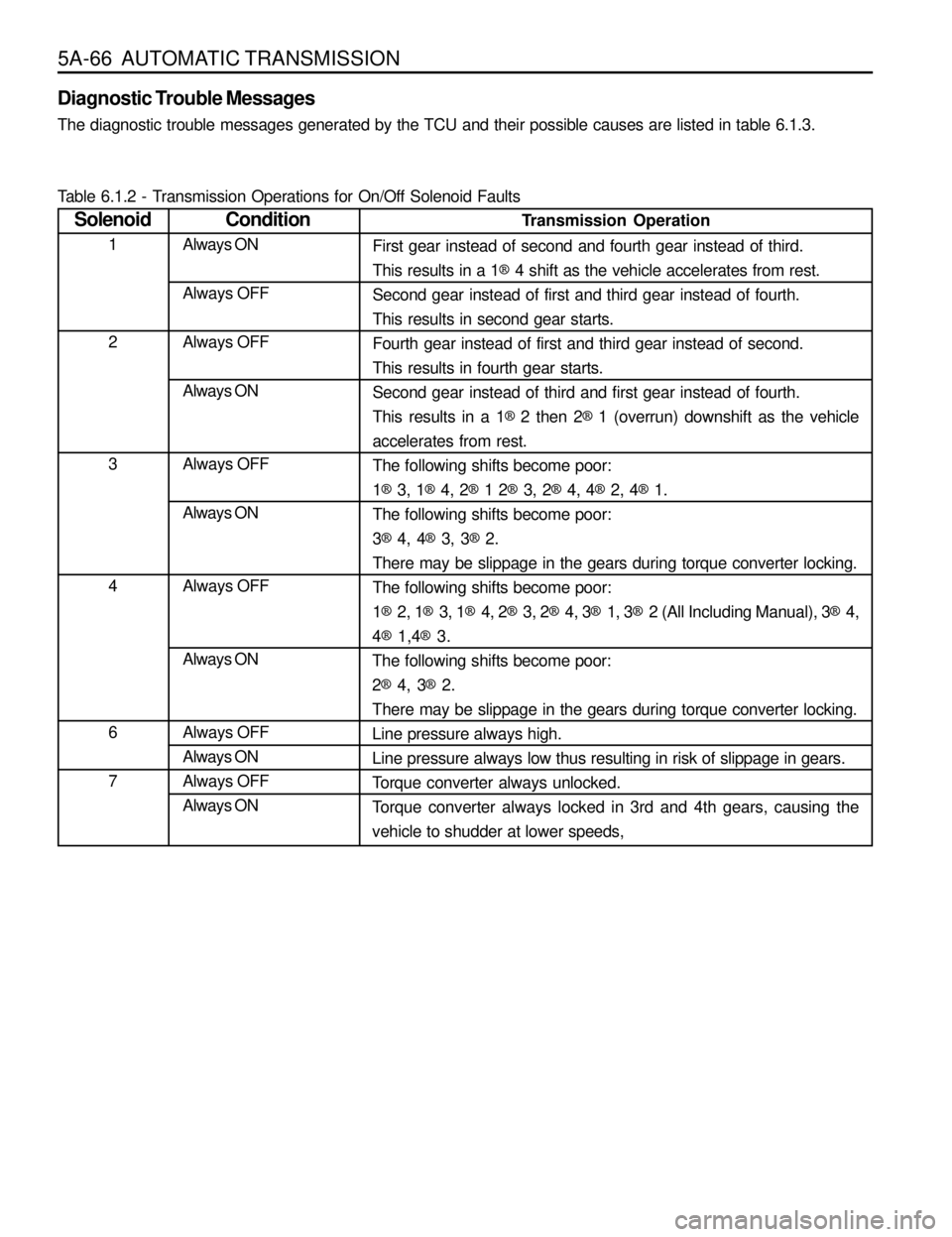
5A-66 AUTOMATIC TRANSMISSION
Diagnostic Trouble Messages
The diagnostic trouble messages generated by the TCU and their possible causes are listed in table 6.1.3.
Table 6.1.2 - Transmission Operations for On/Off Solenoid Faults
Transmission Operation
First gear instead of second and fourth gear instead of third.
This results in a 1®
4 shift as the vehicle accelerates from rest.
Second gear instead of first and third gear instead of fourth.
This results in second gear starts.
Fourth gear instead of first and third gear instead of second.
This results in fourth gear starts.
Second gear instead of third and first gear instead of fourth.
This results in a 1®
2 then 2®
1 (overrun) downshift as the vehicle
accelerates from rest.
The following shifts become poor:
1®
3, 1®
4, 2®
1 2®
3, 2®
4, 4®
2, 4®
1.
The following shifts become poor:
3®
4, 4®
3, 3®
2.
There may be slippage in the gears during torque converter locking.
The following shifts become poor:
1®
2, 1®
3, 1®
4, 2®
3, 2®
4, 3®
1, 3®
2 (All Including Manual), 3®
4,
4®
1,4®
3.
The following shifts become poor:
2®
4, 3®
2.
There may be slippage in the gears during torque converter locking.
Line pressure always high.
Line pressure always low thus resulting in risk of slippage in gears.
Torque converter always unlocked.
Torque converter always locked in 3rd and 4th gears, causing the
vehicle to shudder at lower speeds,Condition
Always ON
Always OFF
Always OFF
Always ON
Always OFF
Always ON
Always OFF
Always ON
Always OFF
Always ON
Always OFF
Always ON
Solenoid
1
2
3
4
6
7
Page 1057 of 1463
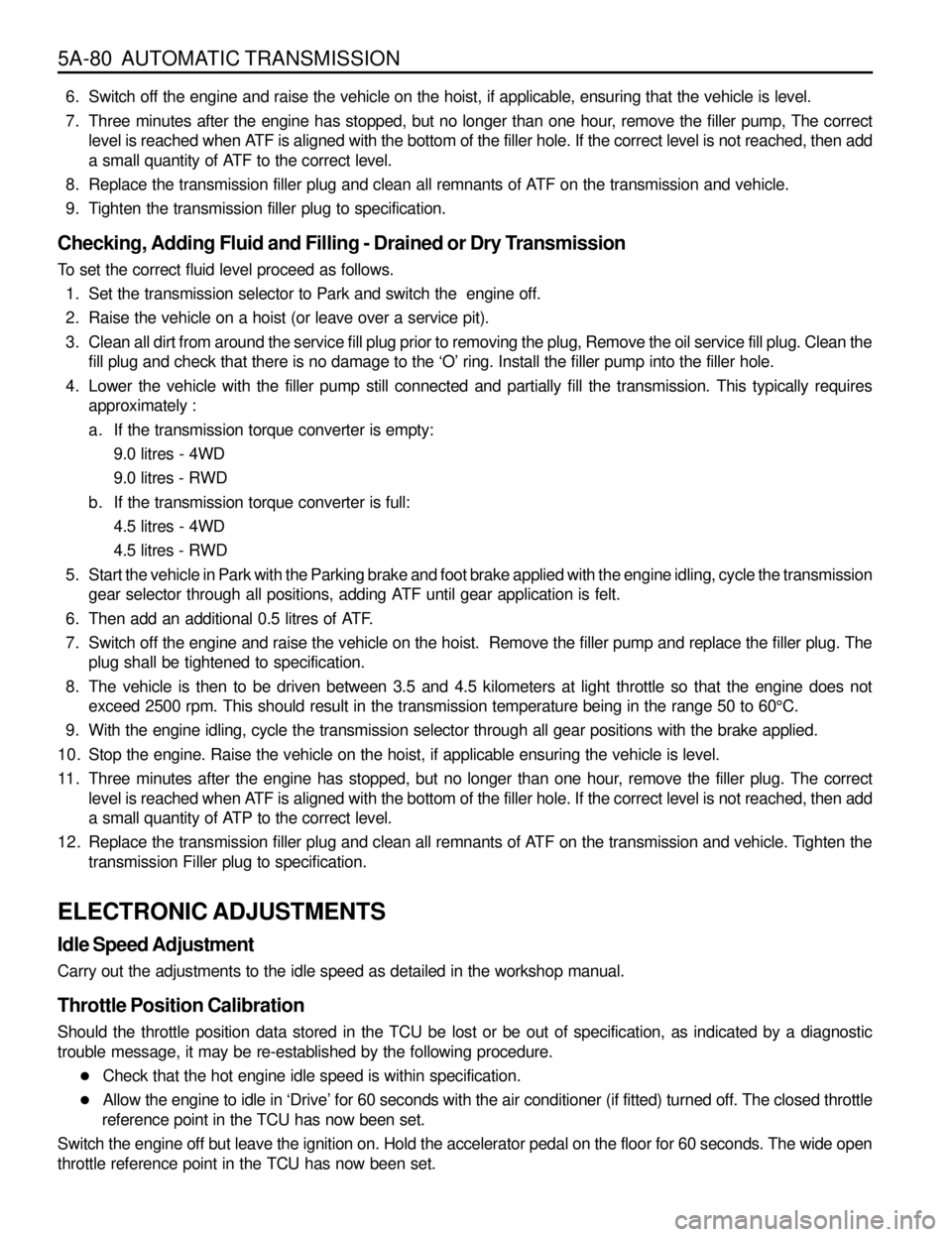
5A-80 AUTOMATIC TRANSMISSION
6. Switch off the engine and raise the vehicle on the hoist, if applicable, ensuring that the vehicle is level.
7. Three minutes after the engine has stopped, but no longer than one hour, remove the filler pump, The correct
level is reached when ATF is aligned with the bottom of the filler hole. If the correct level is not reached, then add
a small quantity of ATF to the correct level.
8. Replace the transmission filler plug and clean all remnants of ATF on the transmission and vehicle.
9. Tighten the transmission filler plug to specification.
Checking, Adding Fluid and Filling - Drained or Dry Transmission
To set the correct fluid level proceed as follows.
1. Set the transmission selector to Park and switch the engine off.
2. Raise the vehicle on a hoist (or leave over a service pit).
3. Clean all dirt from around the service fill plug prior to removing the plug, Remove the oil service fill plug. Clean the
fill plug and check that there is no damage to the ‘O’ ring. Install the filler pump into the filler hole.
4. Lower the vehicle with the filler pump still connected and partially fill the transmission. This typically requires
approximately :
a. If the transmission torque converter is empty:
9.0 litres - 4WD
9.0 litres - RWD
b. If the transmission torque converter is full:
4.5 litres - 4WD
4.5 litres - RWD
5. Start the vehicle in Park with the Parking brake and foot brake applied with the engine idling, cycle the transmission
gear selector through all positions, adding ATF until gear application is felt.
6. Then add an additional 0.5 litres of ATF.
7. Switch off the engine and raise the vehicle on the hoist. Remove the filler pump and replace the filler plug. The
plug shall be tightened to specification.
8. The vehicle is then to be driven between 3.5 and 4.5 kilometers at light throttle so that the engine does not
exceed 2500 rpm. This should result in the transmission temperature being in the range 50 to 60°C.
9. With the engine idling, cycle the transmission selector through all gear positions with the brake applied.
10. Stop the engine. Raise the vehicle on the hoist, if applicable ensuring the vehicle is level.
11. Three minutes after the engine has stopped, but no longer than one hour, remove the filler plug. The correct
level is reached when ATF is aligned with the bottom of the filler hole. If the correct level is not reached, then add
a small quantity of ATP to the correct level.
12. Replace the transmission filler plug and clean all remnants of ATF on the transmission and vehicle. Tighten the
transmission Filler plug to specification.
ELECTRONIC ADJUSTMENTS
Idle Speed Adjustment
Carry out the adjustments to the idle speed as detailed in the workshop manual.
Throttle Position Calibration
Should the throttle position data stored in the TCU be lost or be out of specification, as indicated by a diagnostic
trouble message, it may be re-established by the following procedure.
lCheck that the hot engine idle speed is within specification.
lAllow the engine to idle in ‘Drive’ for 60 seconds with the air conditioner (if fitted) turned off. The closed throttle
reference point in the TCU has now been set.
Switch the engine off but leave the ignition on. Hold the accelerator pedal on the floor for 60 seconds. The wide open
throttle reference point in the TCU has now been set.
Page 1059 of 1463
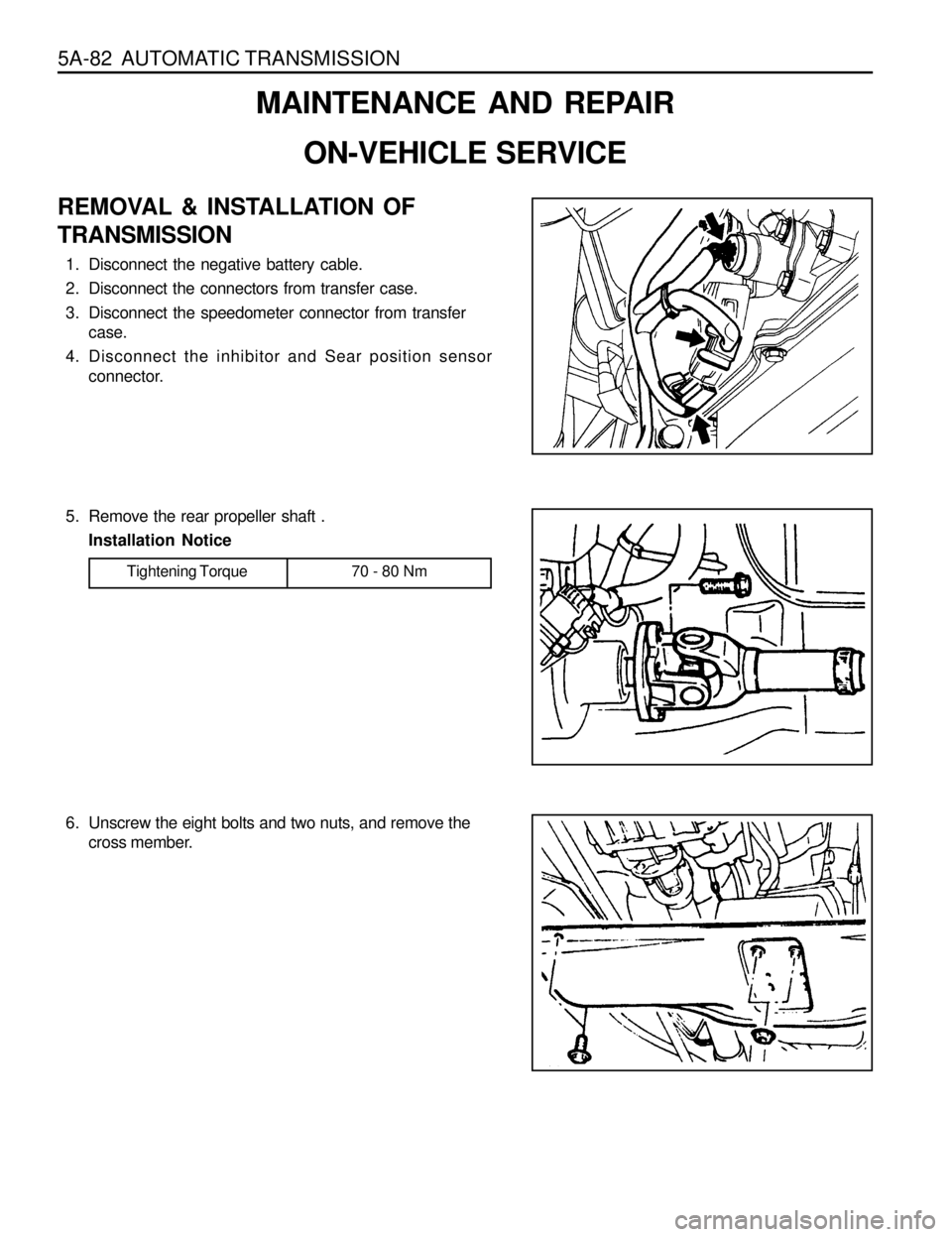
5A-82 AUTOMATIC TRANSMISSION
MAINTENANCE AND REPAIR
ON-VEHICLE SERVICE
Tightening Torque 70 - 80 Nm
5. Remove the rear propeller shaft .
Installation Notice
REMOVAL & INSTALLATION OF
TRANSMISSION
1. Disconnect the negative battery cable.
2. Disconnect the connectors from transfer case.
3. Disconnect the speedometer connector from transfer
case.
4. Disconnect the inhibitor and Sear position sensor
connector.
6. Unscrew the eight bolts and two nuts, and remove the
cross member.