air condition SSANGYONG RODIUS 2005 Service Manual
[x] Cancel search | Manufacturer: SSANGYONG, Model Year: 2005, Model line: RODIUS, Model: SSANGYONG RODIUS 2005Pages: 502, PDF Size: 70.43 MB
Page 124 of 502
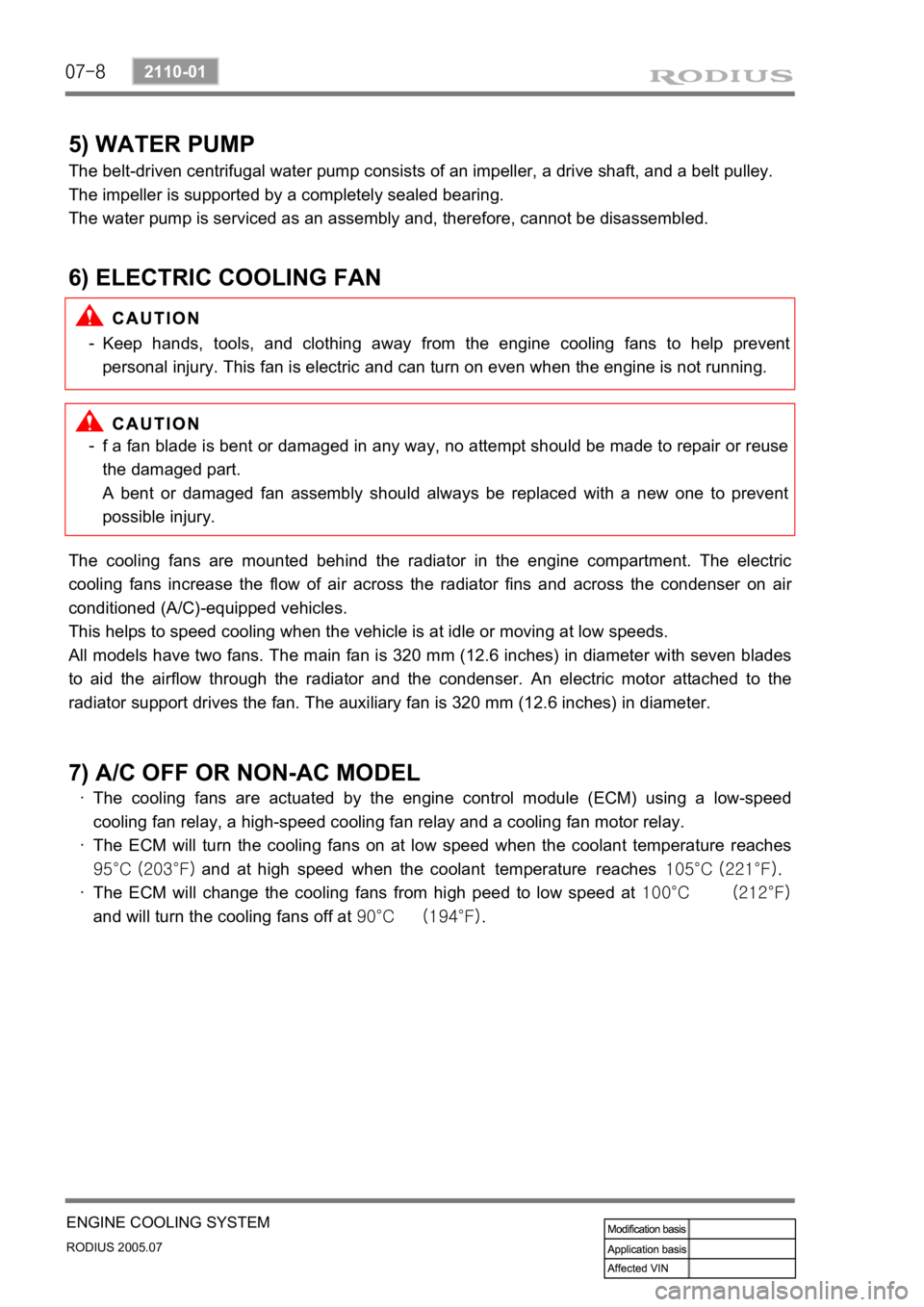
07-8
RODIUS 2005.07
2110-01
ENGINE COOLING SYSTEM
5) WATER PUMP
The belt-driven centrifugal water pump consists of an impeller, a drive shaft, and a belt pulley.
The impeller is supported by a completely sealed bearing.
The water pump is serviced as an assembly and, therefore, cannot be disassembled.
6) ELECTRIC COOLING FAN
Keep hands, tools, and clothing away from the engine cooling fans to help prevent
personal injury. This fan is electric and can turn on even when the engine is not running. -
f a fan blade is bent or damaged in any way, no attempt should be made to repair or reuse
the damaged part.
A bent or damaged fan assembly should always be replaced with a new one to prevent
possible injury. -
The cooling fans are mounted behind the radiator in the engine compartment. The electric
cooling fans increase the flow of air across the radiator fins and across the condenser on ai
r
conditioned (A/C)-equipped vehicles.
This helps to speed cooling when the vehicle is at idle or moving at low speeds.
All models have two fans. The main fan is 320 mm (12.6 inches) in diameter with seven blades
to aid the airflow through the radiator and the condenser. An electric motor attached to the
radiator support drives the fan. The auxiliary fan is 320 mm (12.6 inches) in diameter.
7) A/C OFF OR NON-AC MODEL
The cooling fans are actuated by the engine control module (ECM) using a low-speed
cooling fan relay, a high-speed cooling fan relay and a cooling fan motor relay.
The ECM will turn the cooling fans on at low speed when the coolant temperature reaches
95°C (203°F) and at high speed when the coolant temperature reaches 105°C (221°F).
The ECM will change the cooling fans from high peed to low speed at 100°C (212°F)
and will turn the cooling fans off at 90°C (194°F). ·
·
·
Page 155 of 502
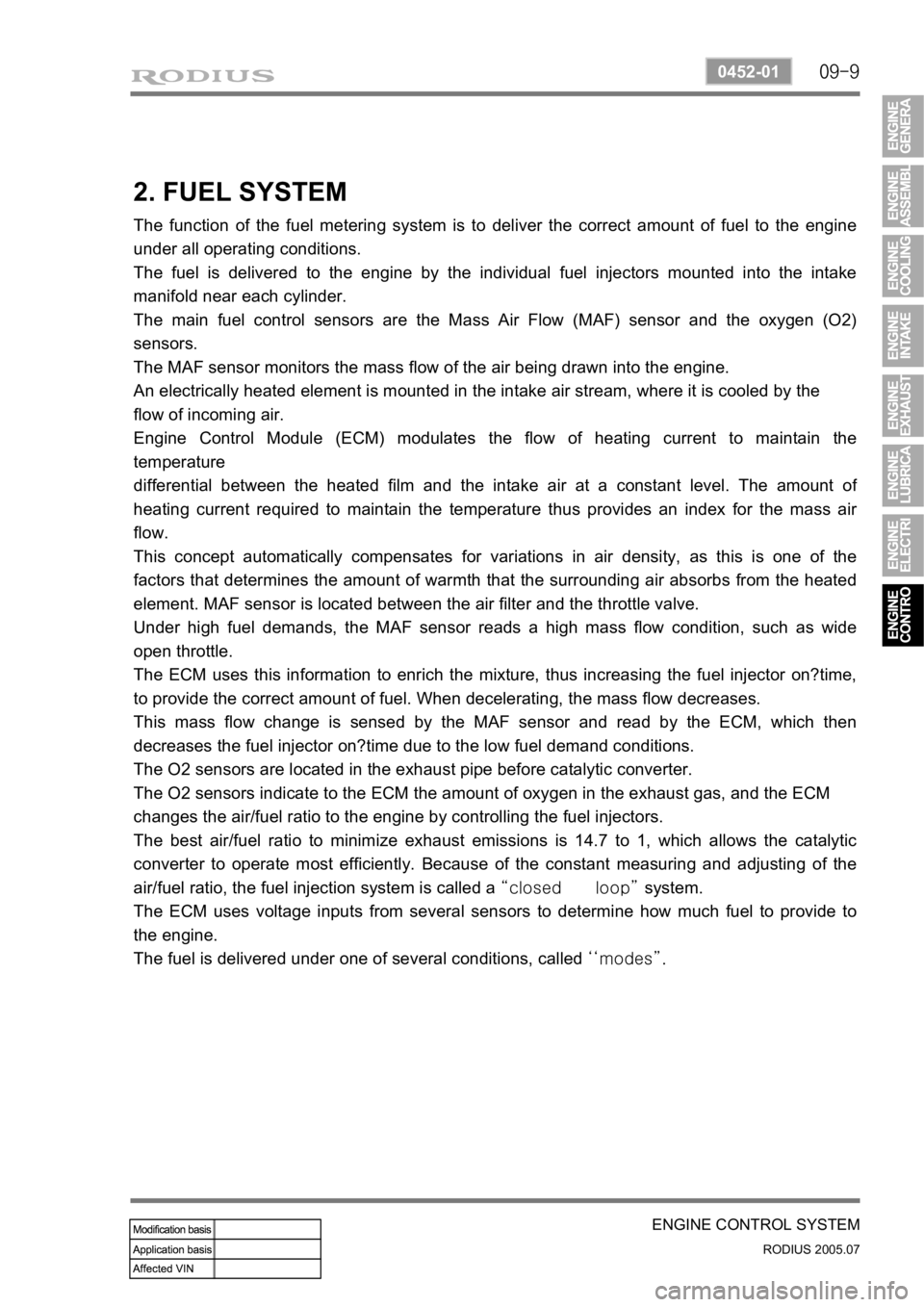
09-9
ENGINE CONTROL SYSTEM
RODIUS 2005.07
0452-01
2. FUEL SYSTEM
The function of the fuel metering system is to deliver the correct amount of fuel to the engine
under all operating conditions.
The fuel is delivered to the engine by the individual fuel injectors mounted into the intake
manifold near each cylinder.
The main fuel control sensors are the Mass Air Flow (MAF) sensor and the oxygen (O2)
sensors.
The MAF sensor monitors the mass flow of the air being drawn into the engine.
An electrically heated element is mounted in the intake air stream, where it is cooled by the
flow of incoming air.
Engine Control Module (ECM) modulates the flow of heating current to maintain the
temperature
differential between the heated film and the intake air at a constant level. The amount o
f
heating current required to maintain the temperature thus provides an index for the mass ai
r
flow.
This concept automatically compensates for variations in air density, as this is one of the
factors that determines the amount of warmth that the surrounding air absorbs from the heated
element. MAF sensor is located between the air filter and the throttle valve.
Under high fuel demands, the MAF sensor reads a high mass flow condition, such as wide
open throttle.
The ECM uses this information to enrich the mixture, thus increasing the fuel injector on?time,
to provide the correct amount of fuel. When decelerating, the mass flow decreases.
This mass flow change is sensed by the MAF sensor and read by the ECM, which then
decreases the fuel injector on?time due to the low fuel demand conditions.
The O2 sensors are located in the exhaust pipe before catalytic converter.
The O2 sensors indicate to the ECM the amount of oxygen in the exhaust gas, and the ECM
changes the air/fuel ratio to the engine by controlling the fuel injectors.
The best air/fuel ratio to minimize exhaust emissions is 14.7 to 1, which allows the catalytic
converter to operate most efficiently. Because of the constant measuring and adjusting of the
air/fuel ratio, the fuel injection system is called a “closed loop” system.
The ECM uses voltage inputs from several sensors to determine how much fuel to provide to
the engine.
The fuel is delivered under one of several conditions, called ‘‘modes”.
Page 156 of 502
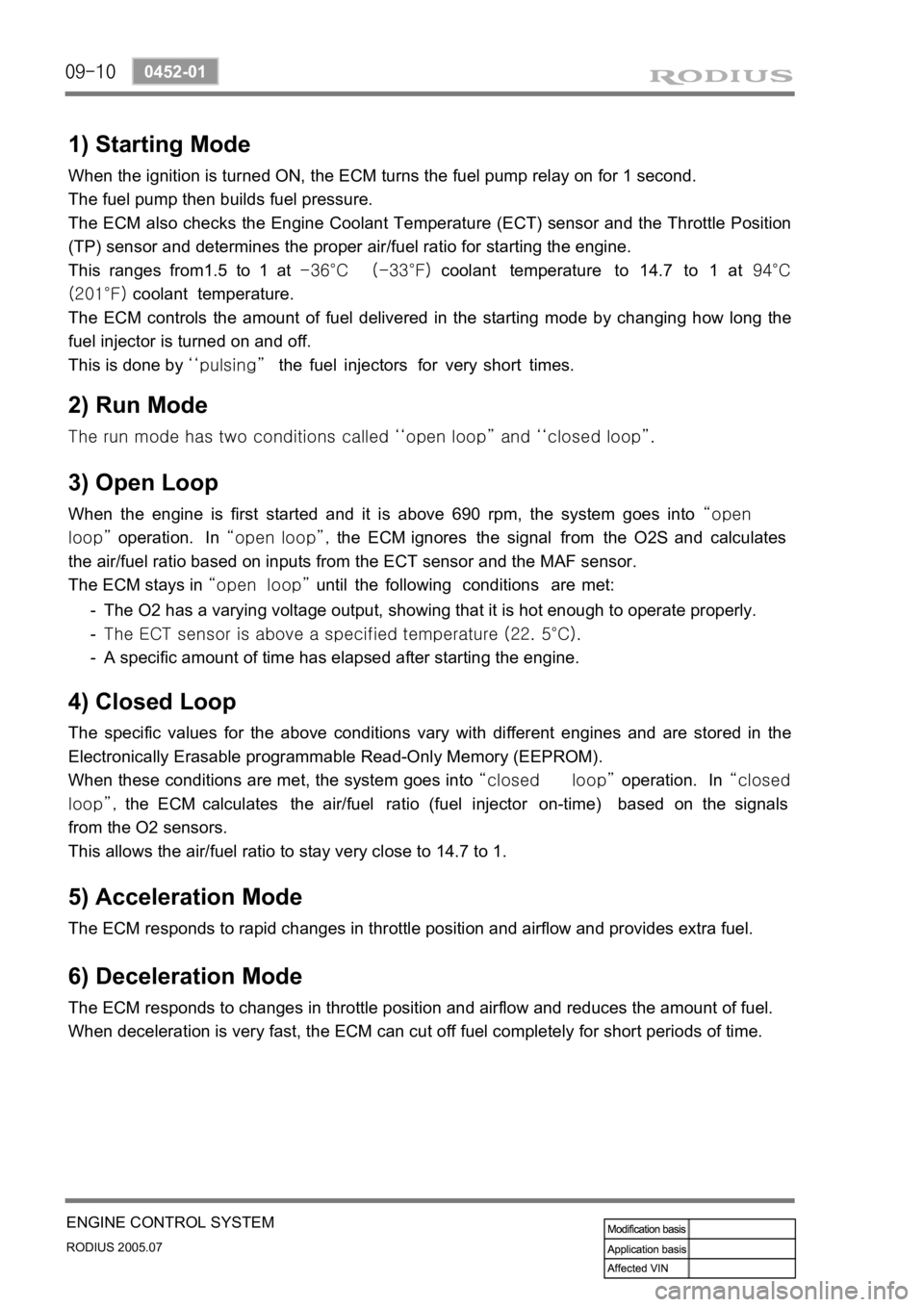
09-10
RODIUS 2005.07
0452-01
ENGINE CONTROL SYSTEM
1) Starting Mode
When the ignition is turned ON, the ECM turns the fuel pump relay on for 1 second.
The fuel pump then builds fuel pressure.
The ECM also checks the Engine Coolant Temperature (ECT) sensor and the Throttle Position
(TP) sensor and determines the proper air/fuel ratio for starting the engine.
This ranges from1.5 to 1 at -36°C (-33°F) coolant temperature to 14.7 to 1 at 94°C
(201°F) coolant temperature.
The ECM controls the amount of fuel delivered in the starting mode by changing how long the
fuel injector is turned on and off.
This is done by ‘‘pulsing” the fuel injectors for very short times.
<007b008f008c00470099009c0095004700940096008b008c0047008f0088009a0047009b009e00960047008a00960095008b0090009b009000960095009a0047008a008800930093008c008b004702c402c400960097008c00950047009300960096009702
c9004700880095008b004702c402c4008a00930096009a008c>d loop”.
2) Run Mode
3) Open Loop
When the engine is first started and it is above 690 rpm, the system goes into “open
loop” operation. In “open loop”, the ECM ignores the signal from the O2S and calculates
the air/fuel ratio based on inputs from the ECT sensor and the MAF sensor.
The ECM stays in “open loop” until the following conditions are met:
The O2 has a varying voltage output, showing that it is hot enough to operate properly.
<007b008f008c0047006c006a007b0047009a008c0095009a0096009900470090009a0047008800890096009d008c004700880047009a0097008c008a0090008d0090008c008b0047009b008c00940097008c00990088009b009c0099008c0047004f005900
5900550047005c00b6006a00500055>
A specific amount of time has elapsed after starting the engine. -
-
-
4) Closed Loop
The specific values for the above conditions vary with different engines and are stored in the
Electronically Erasable programmable Read-Only Memory (EEPROM).
When these conditions are met, the system goes into “closed loop” operation. In “closed
loop”, the ECM calculates the air/fuel ratio (fuel injector on-time) based on the signals
from the O2 sensors.
This allows the air/fuel ratio to stay very close to 14.7 to 1.
5) Acceleration Mode
The ECM responds to rapid changes in throttle position and airflow and provides extra fuel.
The ECM responds to changes in throttle position and airflow and reduces the amount of fuel.
When deceleration is very fast, the ECM can cut off fuel completely for short periods of time.
6) Deceleration Mode
Page 234 of 502
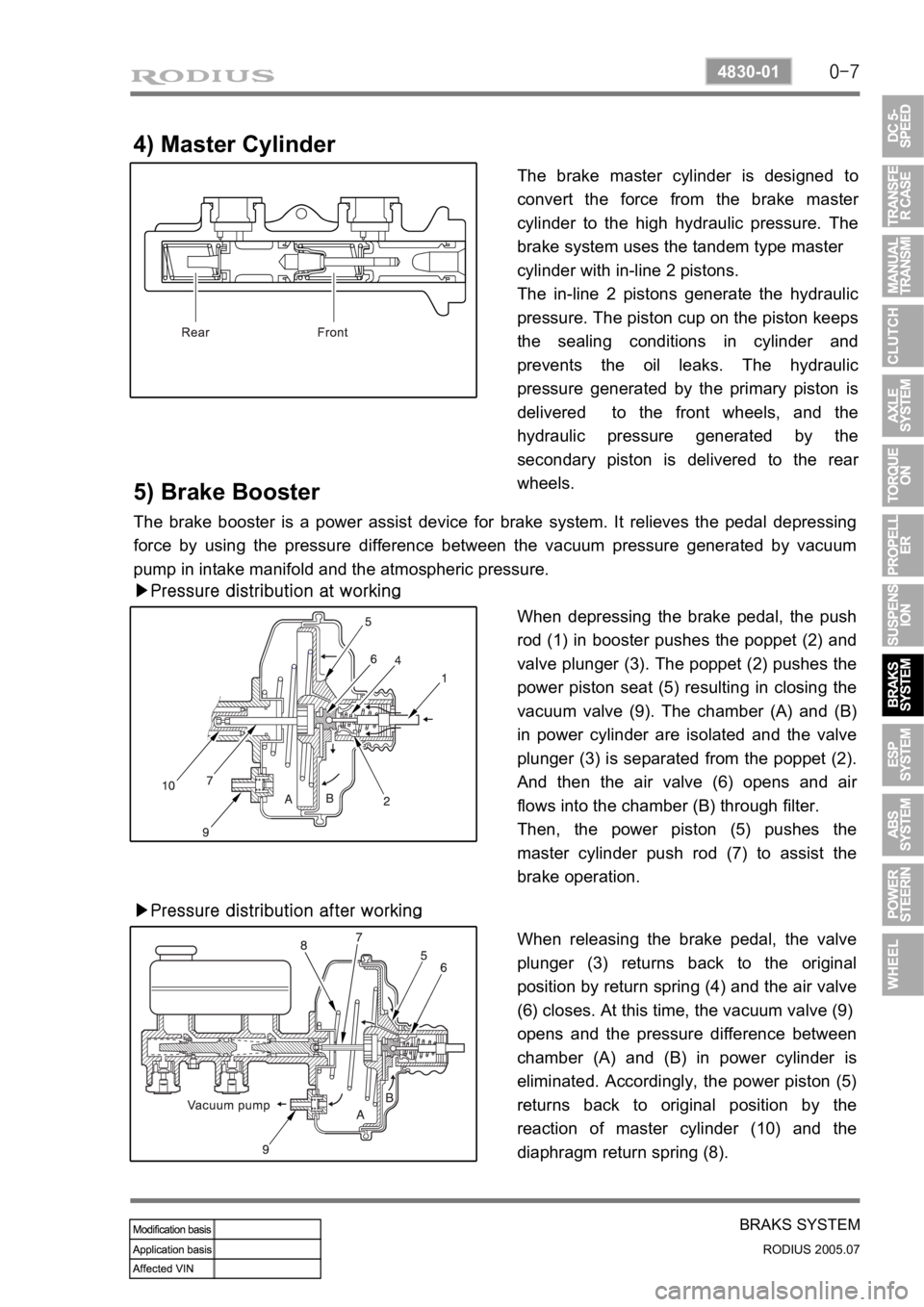
0-7
BRAKS SYSTEM
RODIUS 2005.07
4830-01
4) Master Cylinder
The brake master cylinder is designed to
convert the force from the brake maste
r
cylinder to the high hydraulic pressure. The
brake system uses the tandem type master
cylinder with in-line 2 pistons.
The in-line 2 pistons generate the hydraulic
pressure. The piston cup on the piston keeps
the sealing conditions in cylinder and
prevents the oil leaks. The hydraulic
pressure generated by the primary piston is
delivered to the front wheels, and the
hydraulic pressure generated by the
secondary piston is delivered to the rea
r
wheels.
5) Brake Booster
The brake booster is a power assist device for brake system. It relieves the pedal depressing
force by using the pressure difference between the vacuum pressure generated by vacuum
pump in intake manifold and the atmospheric pressure.
▶Pressure distribution at working
When depressing the brake pedal, the push
rod (1) in booster pushes the poppet (2) and
valve plunger (3). The poppet (2) pushes the
power piston seat (5) resulting in closing the
vacuum valve (9). The chamber (A) and (B)
in power cylinder are isolated and the valve
plunger (3) is separated from the poppet (2).
And then the air valve (6) opens and ai
r
flows into the chamber (B) through filter.
Then, the power piston (5) pushes the
master cylinder push rod (7) to assist the
brake operation.
▶Pressure distribution after working
When releasing the brake pedal, the valve
plunger (3) returns back to the original
position by return spring (4) and the air valve
(6) closes. At this time, the vacuum valve (9)
opens and the pressure difference between
chamber (A) and (B) in power cylinder is
eliminated. Accordingly, the power piston (5)
returns back to original position by the
reaction of master cylinder (10) and the
diaphragm return spring (8).
Page 399 of 502
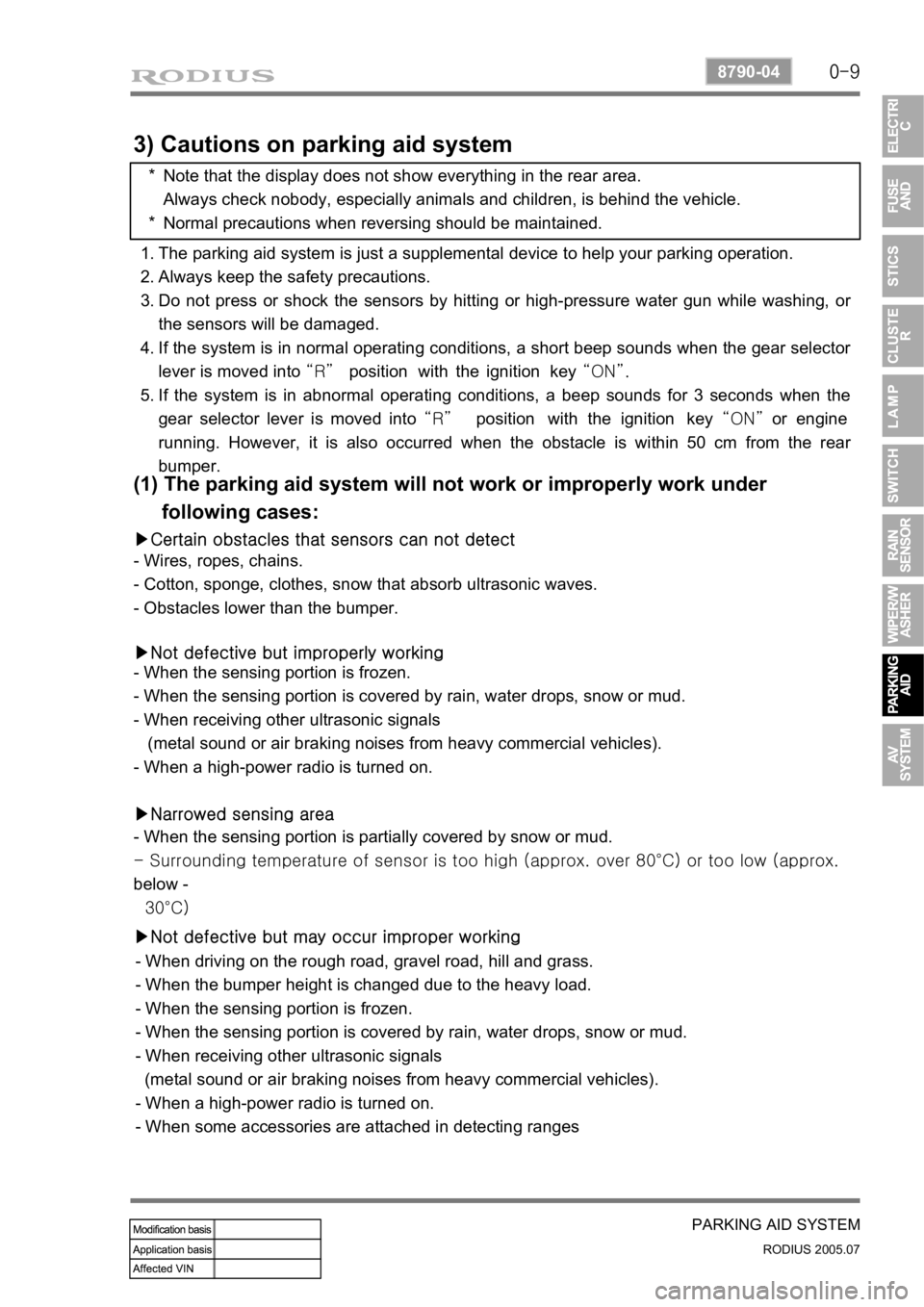
0-9
PARKING AID SYSTEM
RODIUS 2005.07
8790-04
3) Cautions on parking aid system
Note that the display does not show everything in the rear area.
Always check nobody, especially animals and children, is behind the vehicle.
Normal precautions when reversing should be maintained. *
*
The parking aid system is just a supplemental device to help your parking operation.
Always keep the safety precautions.
Do not press or shock the sensors by hitting or high-pressure water gun while washing, o
r
the sensors will be damaged.
If the system is in normal operating conditions, a short beep sounds when the gear selecto
r
lever is moved into “R” position with the ignition key “ON”.
If the system is in abnormal operating conditions, a beep sounds for 3 seconds when the
gear selector lever is moved into “R” position with the ignition key “ON” or engine
running. However, it is also occurred when the obstacle is within 50 cm from the rea
r
bumper. 1.
2.
3.
4.
5.
(1) The parking aid system will not work or improperly work under
following cases:
▶Certain obstacles that sensors can not detect
- Wires, ropes, chains.
- Cotton, sponge, clothes, snow that absorb ultrasonic waves.
- Obstacles lower than the bumper.
▶Not defective but improperly working
- When the sensing portion is frozen.
- When the sensing portion is covered by rain, water drops, snow or mud.
- When receiving other ultrasonic signals
(metal sound or air braking noises from heavy commercial vehicles).
- When a high-power radio is turned on.
▶Narrowed sensing area
- When the sensing portion is partially covered by snow or mud.
<00540047007a009c009900990096009c0095008b00900095008e0047009b008c00940097008c00990088009b009c0099008c00470096008d0047009a008c0095009a0096009900470090009a0047009b009600960047008f0090008e008f0047004f008800
97009700990096009f005500470096009d008c00990047005f>0°C) or too low (approx.
below -
30°C)
▶Not defective but may occur improper working
- When driving on the rough road, gravel road, hill and grass.
- When the bumper height is changed due to the heavy load.
- When the sensing portion is frozen.
- When the sensing portion is covered by rain, water drops, snow or mud.
- When receiving other ultrasonic signals
(metal sound or air braking noises from heavy commercial vehicles).
- When a high-power radio is turned on.
- When some accessories are attached in detecting ranges
Page 412 of 502
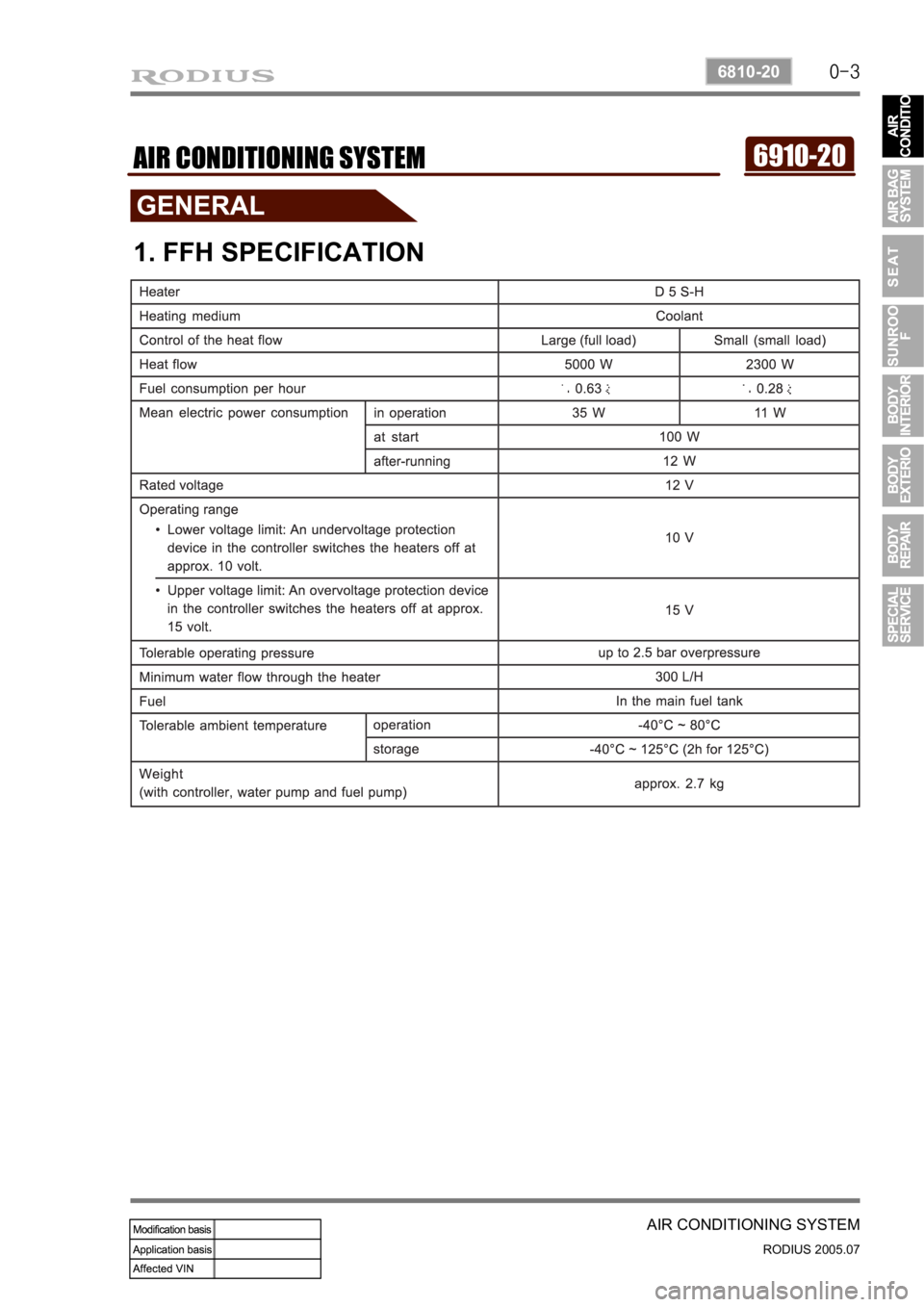
0-3
AIR CONDITIONING SYSTEM
RODIUS 2005.07
6810-20
6910-20AIR CONDITIONING SYSTEM
1. FFH SPECIFICATION
Page 413 of 502
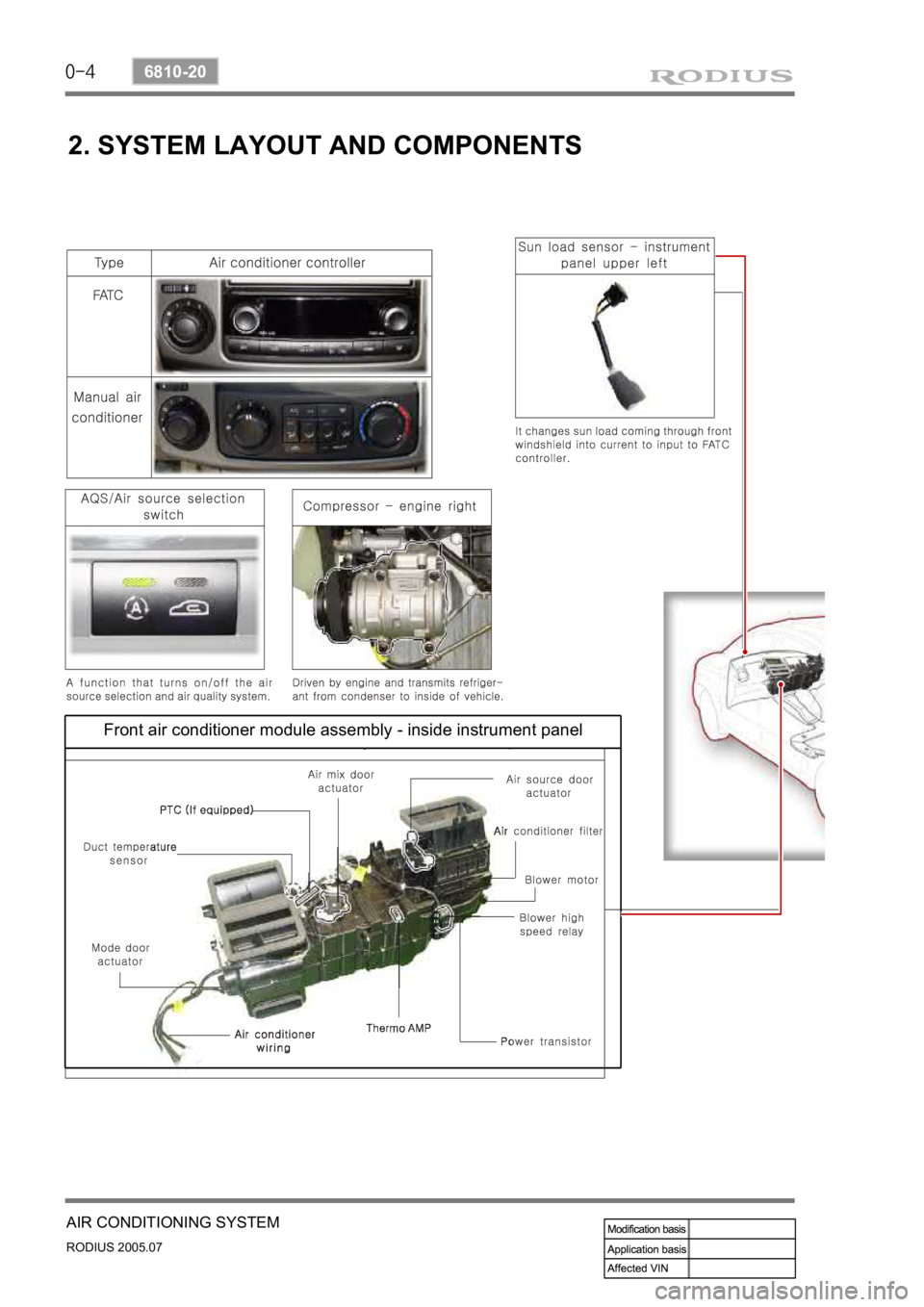
0-4
RODIUS 2005.07
6810-20
AIR CONDITIONING SYSTEM
2. SYSTEM LAYOUT AND COMPONENTS
Front air conditioner module assembly - inside instrument panel
Page 414 of 502
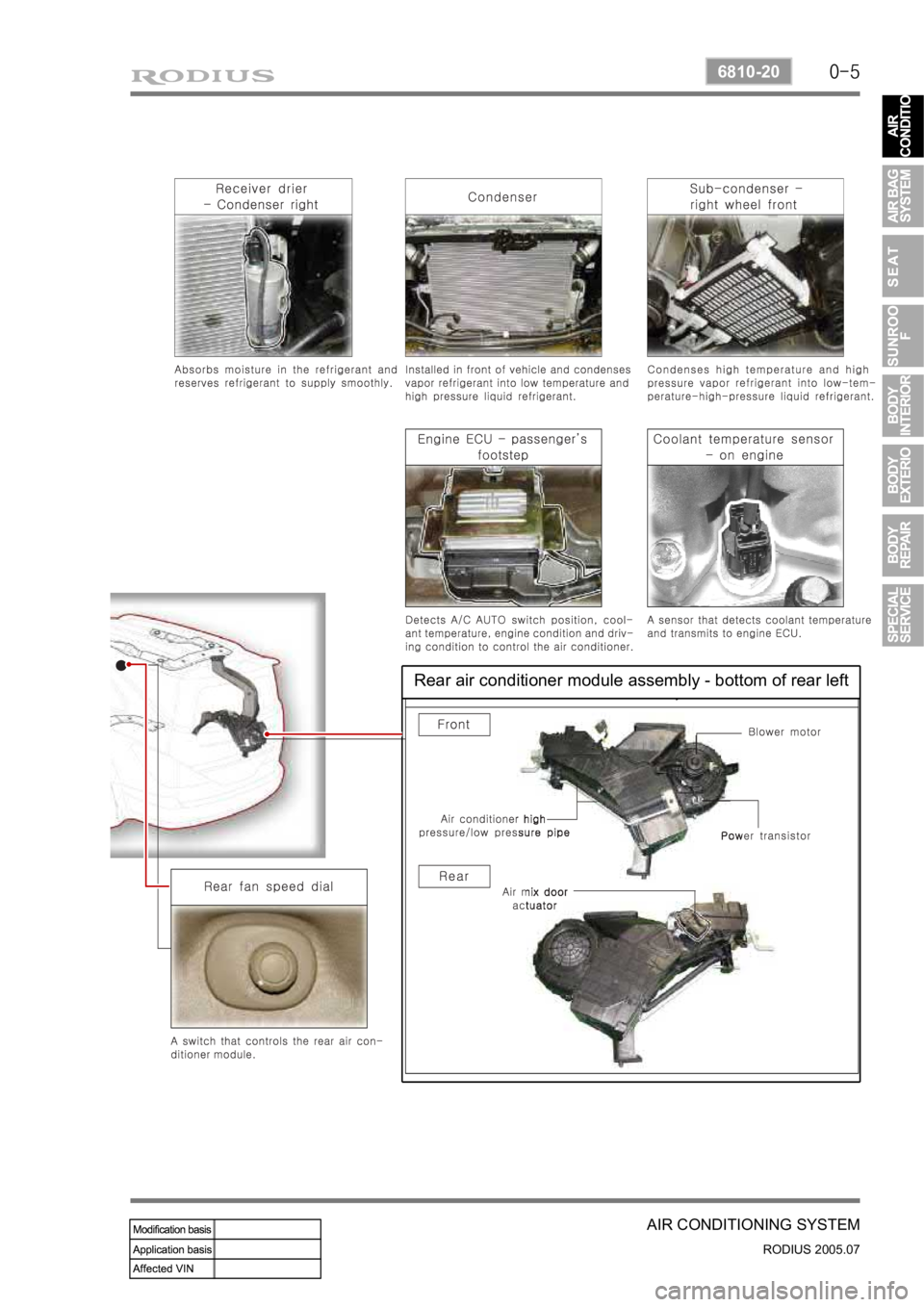
0-5
AIR CONDITIONING SYSTEM
RODIUS 2005.07
6810-20
Rear air conditioner module assembly - bottom of rear left
Page 415 of 502
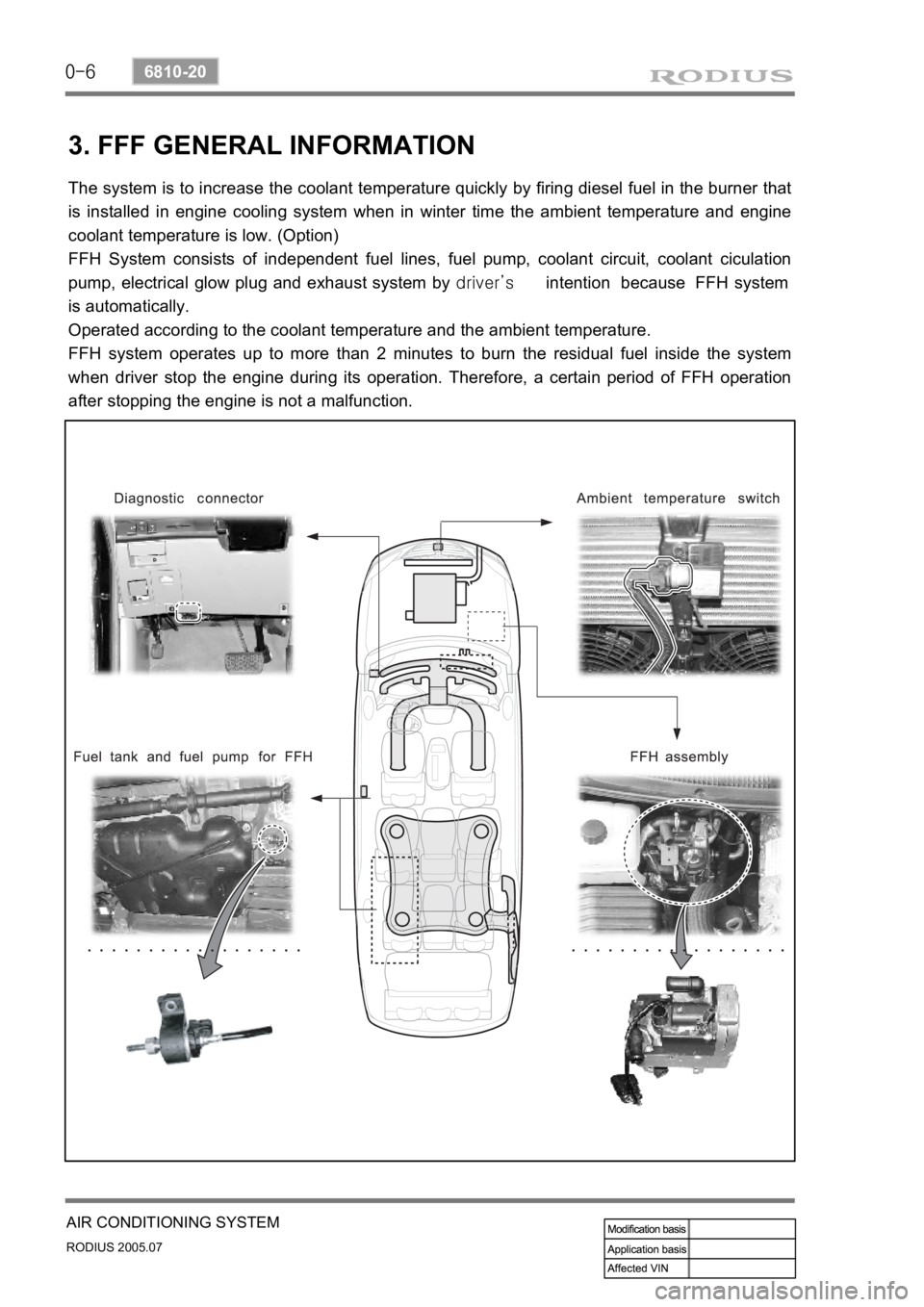
0-6
RODIUS 2005.07
6810-20
AIR CONDITIONING SYSTEM
3. FFF GENERAL INFORMATION
The system is to increase the coolant temperature quickly by firing diesel fuel in the burner that
is installed in engine cooling system when in winter time the ambient temperature and engine
coolant temperature is low. (Option)
FFH System consists of independent fuel lines, fuel pump, coolant circuit, coolant ciculation
pump, electrical glow plug and exhaust system by driver’s intention because FFH system
is automatically.
Operated according to the coolant temperature and the ambient temperature.
FFH system operates up to more than 2 minutes to burn the residual fuel inside the system
when driver stop the engine during its operation. Therefore, a certain period of FFH operation
after stopping the engine is not a malfunction.
Page 416 of 502
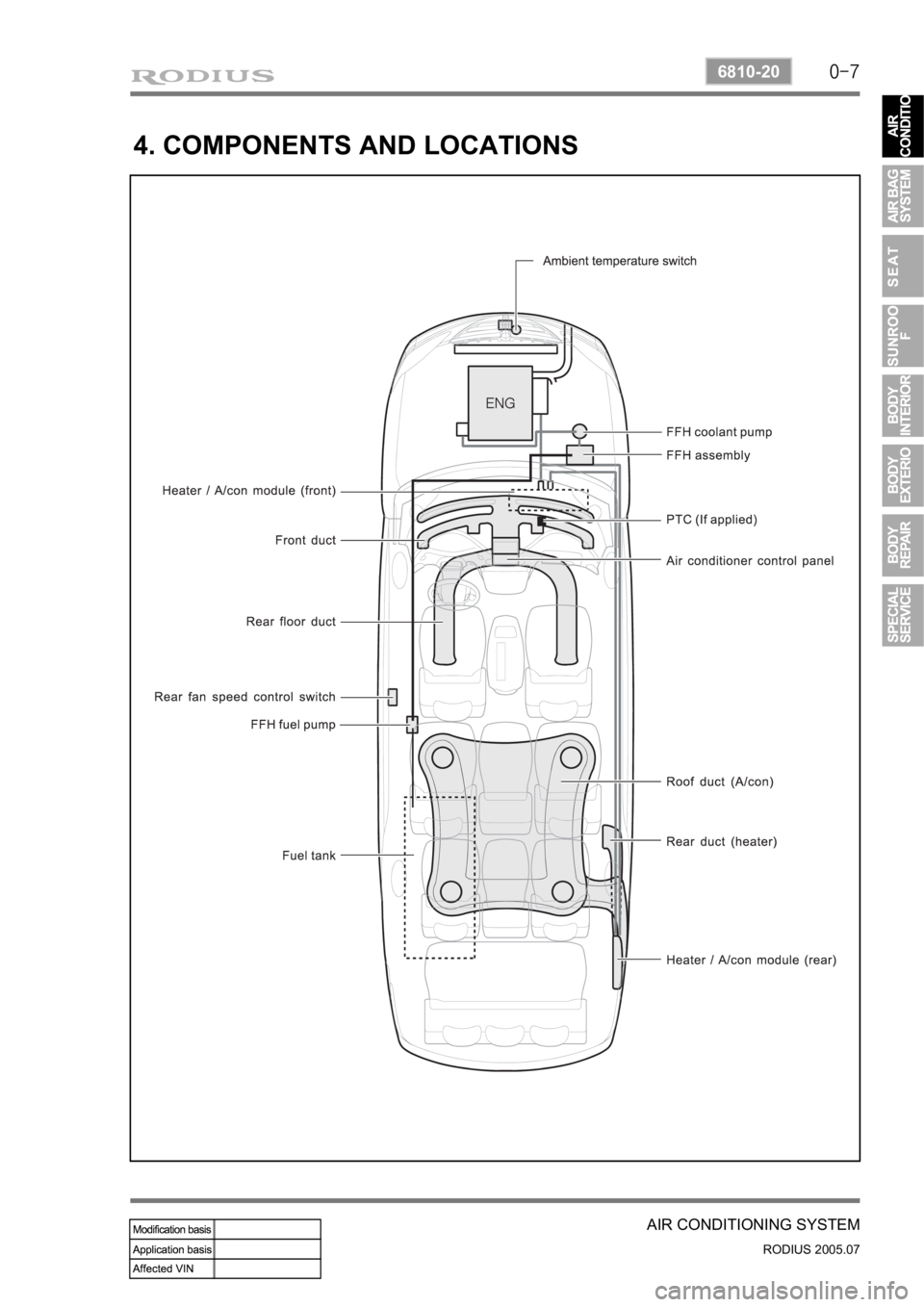
0-7
AIR CONDITIONING SYSTEM
RODIUS 2005.07
6810-20
4. COMPONENTS AND LOCATIONS