SUBARU LEGACY 1999 Service Service Manual
Manufacturer: SUBARU, Model Year: 1999, Model line: LEGACY, Model: SUBARU LEGACY 1999Pages: 1456, PDF Size: 59.93 MB
Page 41 of 1456
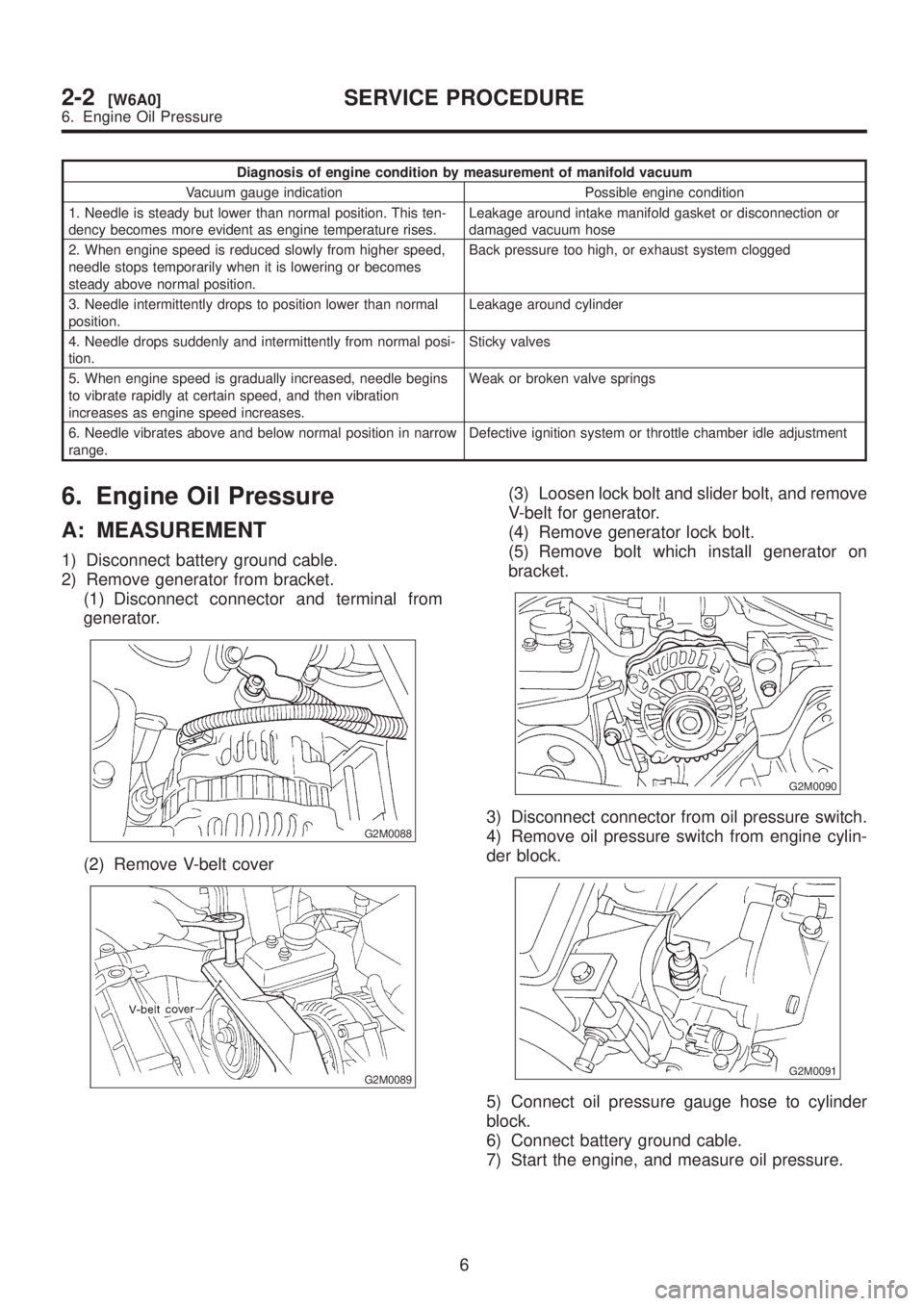
Diagnosis of engine condition by measurement of manifold vacuum
Vacuum gauge indication Possible engine condition
1. Needle is steady but lower than normal position. This ten-
dency becomes more evident as engine temperature rises.Leakage around intake manifold gasket or disconnection or
damaged vacuum hose
2. When engine speed is reduced slowly from higher speed,
needle stops temporarily when it is lowering or becomes
steady above normal position.Back pressure too high, or exhaust system clogged
3. Needle intermittently drops to position lower than normal
position.Leakage around cylinder
4. Needle drops suddenly and intermittently from normal posi-
tion.Sticky valves
5. When engine speed is gradually increased, needle begins
to vibrate rapidly at certain speed, and then vibration
increases as engine speed increases.Weak or broken valve springs
6. Needle vibrates above and below normal position in narrow
range.Defective ignition system or throttle chamber idle adjustment
6. Engine Oil Pressure
A: MEASUREMENT
1) Disconnect battery ground cable.
2) Remove generator from bracket.
(1) Disconnect connector and terminal from
generator.
G2M0088
(2) Remove V-belt cover
G2M0089
(3) Loosen lock bolt and slider bolt, and remove
V-belt for generator.
(4) Remove generator lock bolt.
(5) Remove bolt which install generator on
bracket.
G2M0090
3) Disconnect connector from oil pressure switch.
4) Remove oil pressure switch from engine cylin-
der block.
G2M0091
5) Connect oil pressure gauge hose to cylinder
block.
6) Connect battery ground cable.
7) Start the engine, and measure oil pressure.
6
2-2[W6A0]SERVICE PROCEDURE
6. Engine Oil Pressure
Page 42 of 1456
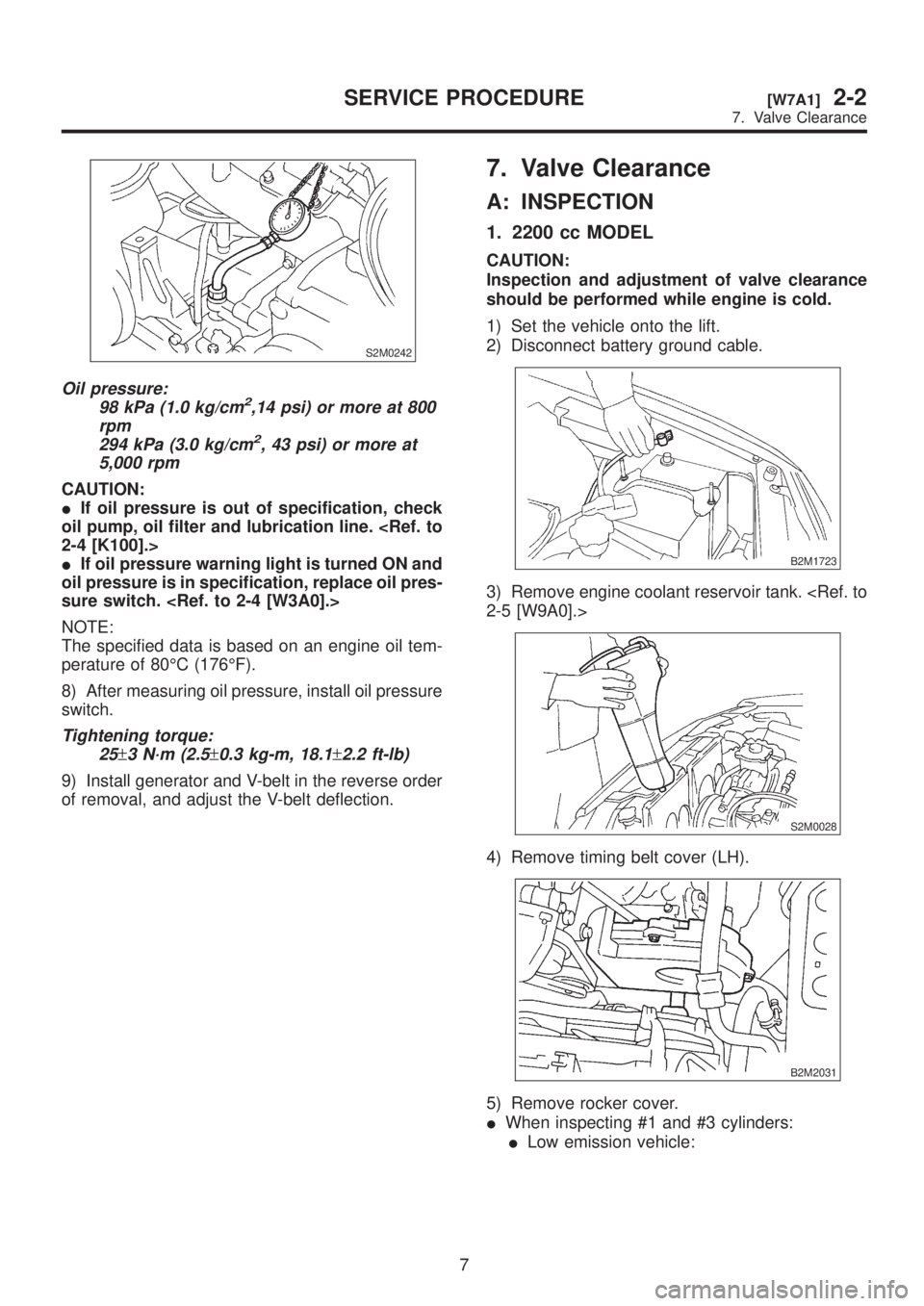
S2M0242
Oil pressure:
98 kPa (1.0 kg/cm2,14 psi) or more at 800
rpm
294 kPa (3.0 kg/cm
2, 43 psi) or more at
5,000 rpm
CAUTION:
IIf oil pressure is out of specification, check
oil pump, oil filter and lubrication line.
IIf oil pressure warning light is turned ON and
oil pressure is in specification, replace oil pres-
sure switch.
NOTE:
The specified data is based on an engine oil tem-
perature of 80ÉC (176ÉF).
8) After measuring oil pressure, install oil pressure
switch.
Tightening torque:
25
±3 N´m (2.5±0.3 kg-m, 18.1±2.2 ft-lb)
9) Install generator and V-belt in the reverse order
of removal, and adjust the V-belt deflection.
7. Valve Clearance
A: INSPECTION
1. 2200 cc MODEL
CAUTION:
Inspection and adjustment of valve clearance
should be performed while engine is cold.
1) Set the vehicle onto the lift.
2) Disconnect battery ground cable.
B2M1723
3) Remove engine coolant reservoir tank.
S2M0028
4) Remove timing belt cover (LH).
B2M2031
5) Remove rocker cover.
IWhen inspecting #1 and #3 cylinders:
ILow emission vehicle:
7
[W7A1]2-2SERVICE PROCEDURE
7. Valve Clearance
Page 43 of 1456
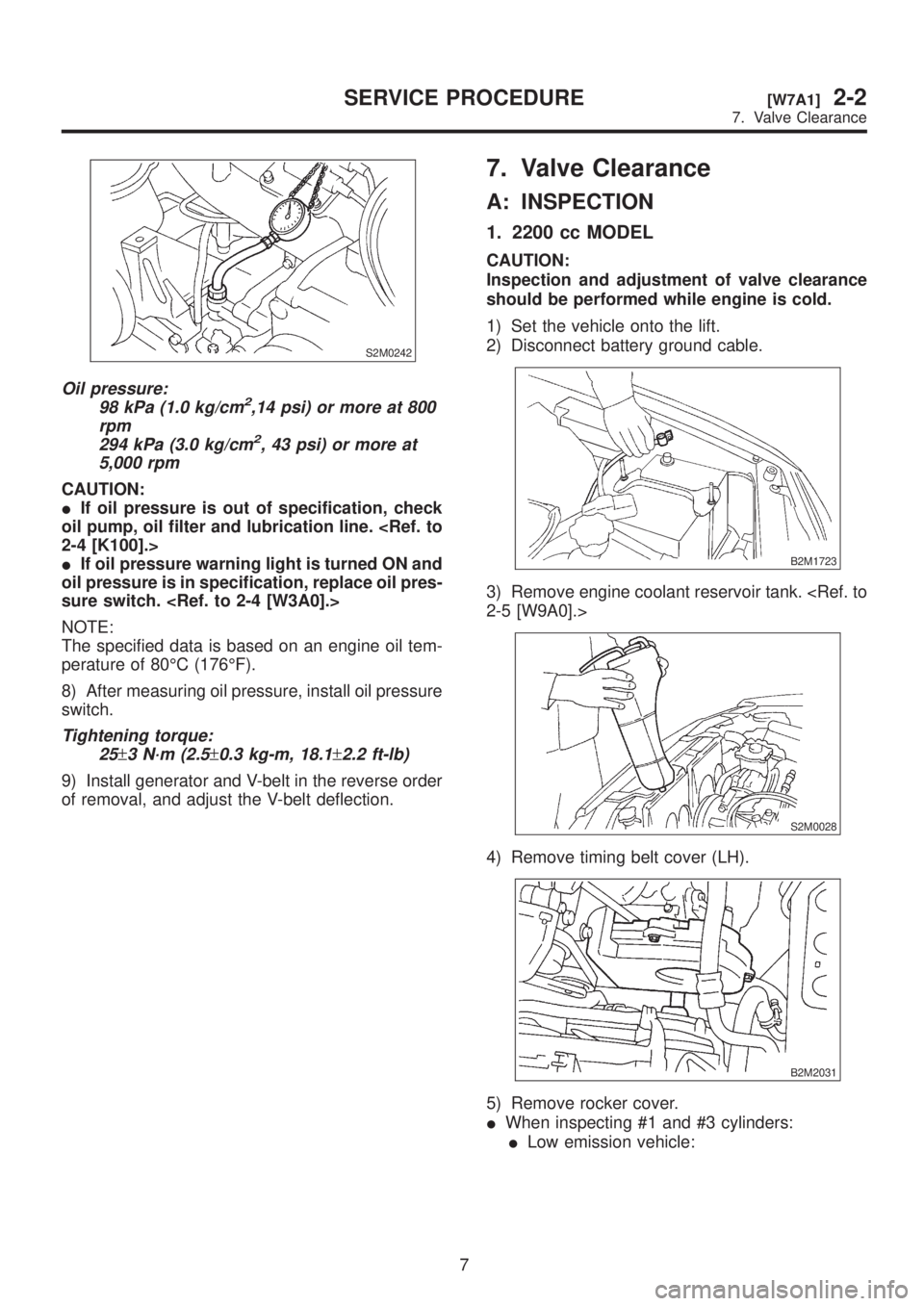
S2M0242
Oil pressure:
98 kPa (1.0 kg/cm2,14 psi) or more at 800
rpm
294 kPa (3.0 kg/cm
2, 43 psi) or more at
5,000 rpm
CAUTION:
IIf oil pressure is out of specification, check
oil pump, oil filter and lubrication line.
IIf oil pressure warning light is turned ON and
oil pressure is in specification, replace oil pres-
sure switch.
NOTE:
The specified data is based on an engine oil tem-
perature of 80ÉC (176ÉF).
8) After measuring oil pressure, install oil pressure
switch.
Tightening torque:
25
±3 N´m (2.5±0.3 kg-m, 18.1±2.2 ft-lb)
9) Install generator and V-belt in the reverse order
of removal, and adjust the V-belt deflection.
7. Valve Clearance
A: INSPECTION
1. 2200 cc MODEL
CAUTION:
Inspection and adjustment of valve clearance
should be performed while engine is cold.
1) Set the vehicle onto the lift.
2) Disconnect battery ground cable.
B2M1723
3) Remove engine coolant reservoir tank.
S2M0028
4) Remove timing belt cover (LH).
B2M2031
5) Remove rocker cover.
IWhen inspecting #1 and #3 cylinders:
ILow emission vehicle:
7
[W7A1]2-2SERVICE PROCEDURE
7. Valve Clearance
Page 44 of 1456
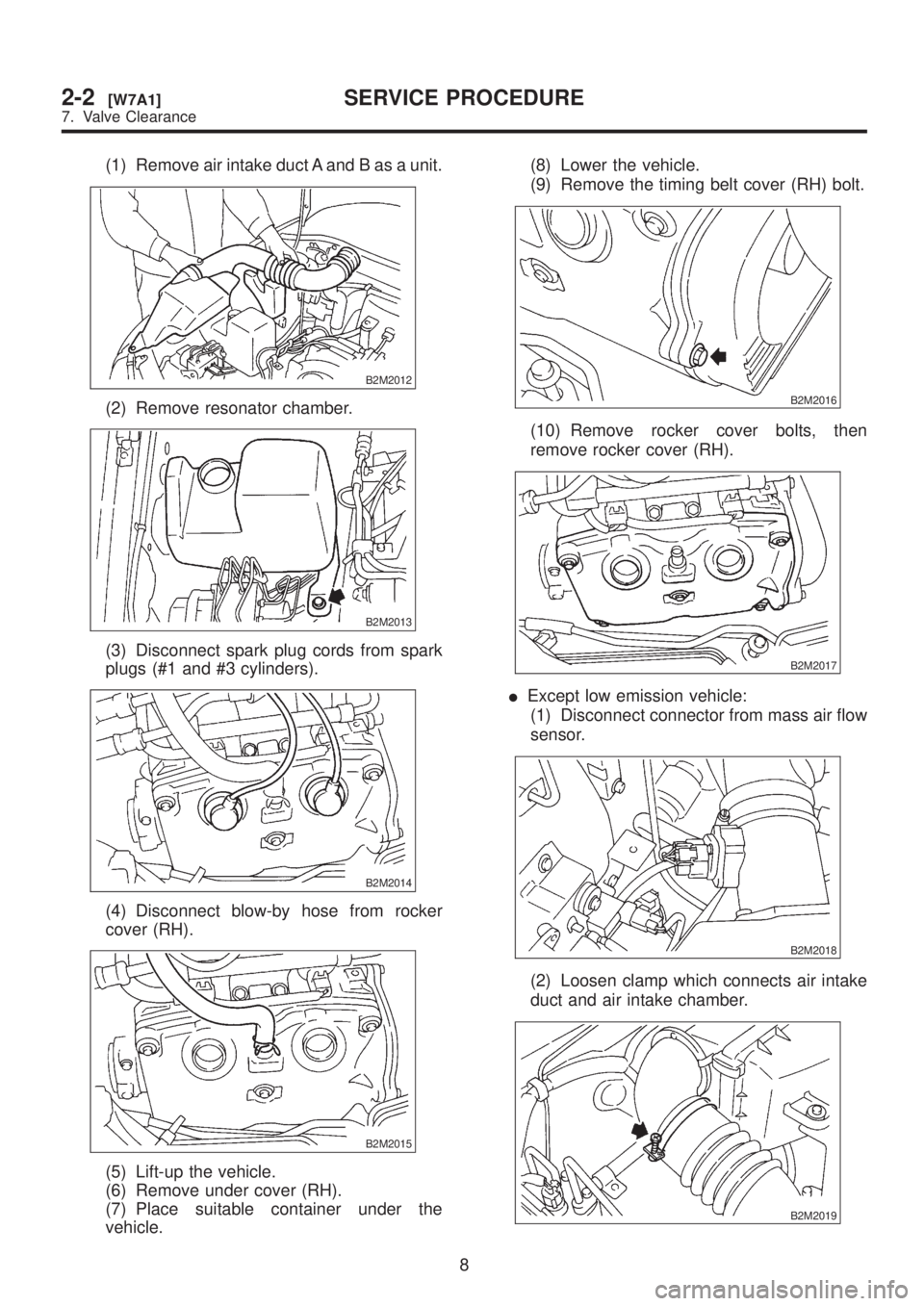
(1) Remove air intake duct A and B as a unit.
B2M2012
(2) Remove resonator chamber.
B2M2013
(3) Disconnect spark plug cords from spark
plugs (#1 and #3 cylinders).
B2M2014
(4) Disconnect blow-by hose from rocker
cover (RH).
B2M2015
(5) Lift-up the vehicle.
(6) Remove under cover (RH).
(7) Place suitable container under the
vehicle.(8) Lower the vehicle.
(9) Remove the timing belt cover (RH) bolt.
B2M2016
(10) Remove rocker cover bolts, then
remove rocker cover (RH).
B2M2017
IExcept low emission vehicle:
(1) Disconnect connector from mass air flow
sensor.
B2M2018
(2) Loosen clamp which connects air intake
duct and air intake chamber.
B2M2019
8
2-2[W7A1]SERVICE PROCEDURE
7. Valve Clearance
Page 45 of 1456
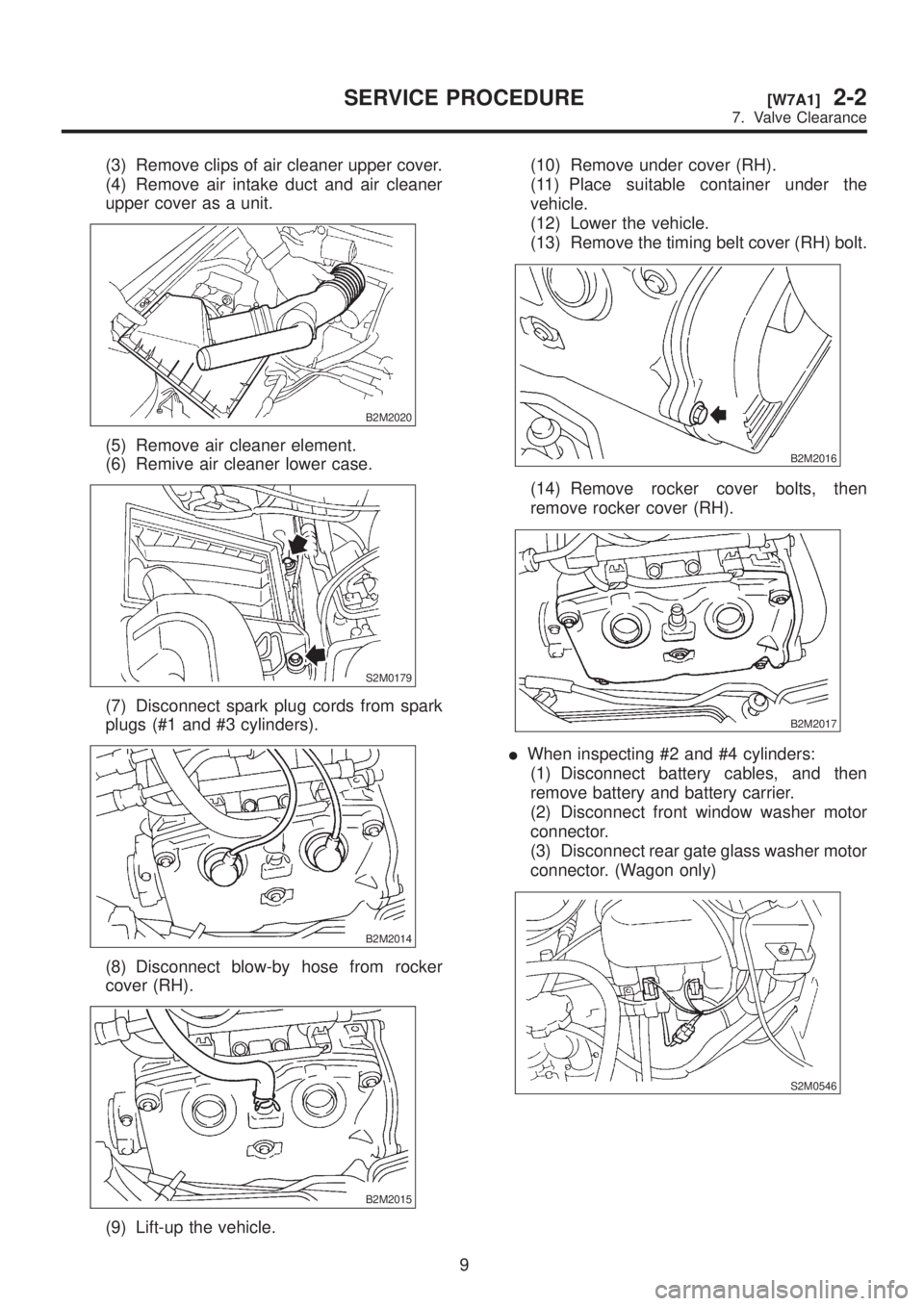
(3) Remove clips of air cleaner upper cover.
(4) Remove air intake duct and air cleaner
upper cover as a unit.
B2M2020
(5) Remove air cleaner element.
(6) Remive air cleaner lower case.
S2M0179
(7) Disconnect spark plug cords from spark
plugs (#1 and #3 cylinders).
B2M2014
(8) Disconnect blow-by hose from rocker
cover (RH).
B2M2015
(9) Lift-up the vehicle.(10) Remove under cover (RH).
(11) Place suitable container under the
vehicle.
(12) Lower the vehicle.
(13) Remove the timing belt cover (RH) bolt.
B2M2016
(14) Remove rocker cover bolts, then
remove rocker cover (RH).
B2M2017
IWhen inspecting #2 and #4 cylinders:
(1) Disconnect battery cables, and then
remove battery and battery carrier.
(2) Disconnect front window washer motor
connector.
(3) Disconnect rear gate glass washer motor
connector. (Wagon only)
S2M0546
9
[W7A1]2-2SERVICE PROCEDURE
7. Valve Clearance
Page 46 of 1456
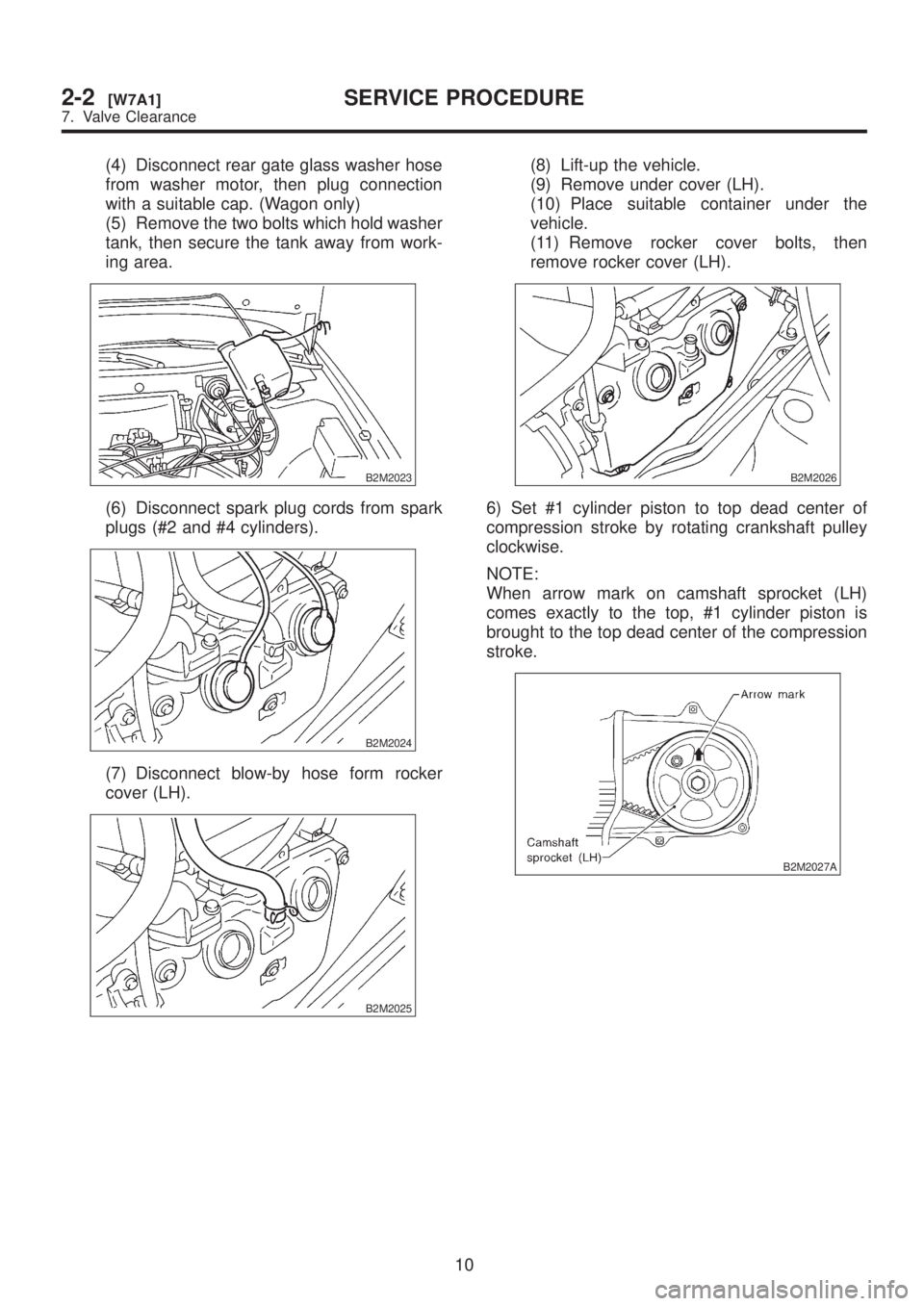
(4) Disconnect rear gate glass washer hose
from washer motor, then plug connection
with a suitable cap. (Wagon only)
(5) Remove the two bolts which hold washer
tank, then secure the tank away from work-
ing area.
B2M2023
(6) Disconnect spark plug cords from spark
plugs (#2 and #4 cylinders).
B2M2024
(7) Disconnect blow-by hose form rocker
cover (LH).
B2M2025
(8) Lift-up the vehicle.
(9) Remove under cover (LH).
(10) Place suitable container under the
vehicle.
(11) Remove rocker cover bolts, then
remove rocker cover (LH).
B2M2026
6) Set #1 cylinder piston to top dead center of
compression stroke by rotating crankshaft pulley
clockwise.
NOTE:
When arrow mark on camshaft sprocket (LH)
comes exactly to the top, #1 cylinder piston is
brought to the top dead center of the compression
stroke.
B2M2027A
10
2-2[W7A1]SERVICE PROCEDURE
7. Valve Clearance
Page 47 of 1456
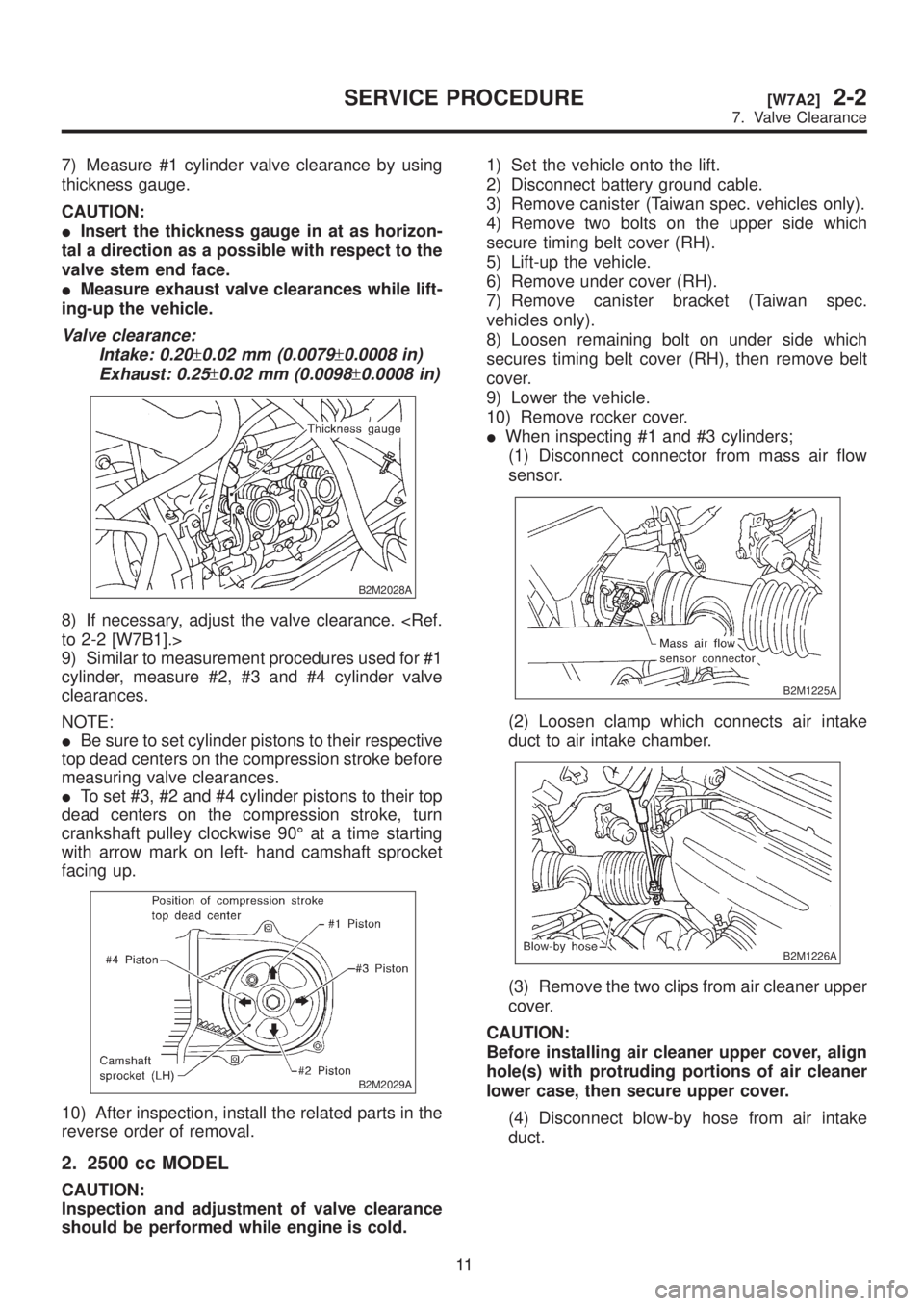
7) Measure #1 cylinder valve clearance by using
thickness gauge.
CAUTION:
IInsert the thickness gauge in at as horizon-
tal a direction as a possible with respect to the
valve stem end face.
IMeasure exhaust valve clearances while lift-
ing-up the vehicle.
Valve clearance:
Intake: 0.20
±0.02 mm (0.0079±0.0008 in)
Exhaust: 0.25
±0.02 mm (0.0098±0.0008 in)
B2M2028A
8) If necessary, adjust the valve clearance.
9) Similar to measurement procedures used for #1
cylinder, measure #2, #3 and #4 cylinder valve
clearances.
NOTE:
IBe sure to set cylinder pistons to their respective
top dead centers on the compression stroke before
measuring valve clearances.
ITo set #3, #2 and #4 cylinder pistons to their top
dead centers on the compression stroke, turn
crankshaft pulley clockwise 90É at a time starting
with arrow mark on left- hand camshaft sprocket
facing up.
B2M2029A
10) After inspection, install the related parts in the
reverse order of removal.
2. 2500 cc MODEL
CAUTION:
Inspection and adjustment of valve clearance
should be performed while engine is cold.1) Set the vehicle onto the lift.
2) Disconnect battery ground cable.
3) Remove canister (Taiwan spec. vehicles only).
4) Remove two bolts on the upper side which
secure timing belt cover (RH).
5) Lift-up the vehicle.
6) Remove under cover (RH).
7) Remove canister bracket (Taiwan spec.
vehicles only).
8) Loosen remaining bolt on under side which
secures timing belt cover (RH), then remove belt
cover.
9) Lower the vehicle.
10) Remove rocker cover.
IWhen inspecting #1 and #3 cylinders;
(1) Disconnect connector from mass air flow
sensor.
B2M1225A
(2) Loosen clamp which connects air intake
duct to air intake chamber.
B2M1226A
(3) Remove the two clips from air cleaner upper
cover.
CAUTION:
Before installing air cleaner upper cover, align
hole(s) with protruding portions of air cleaner
lower case, then secure upper cover.
(4) Disconnect blow-by hose from air intake
duct.
11
[W7A2]2-2SERVICE PROCEDURE
7. Valve Clearance
Page 48 of 1456
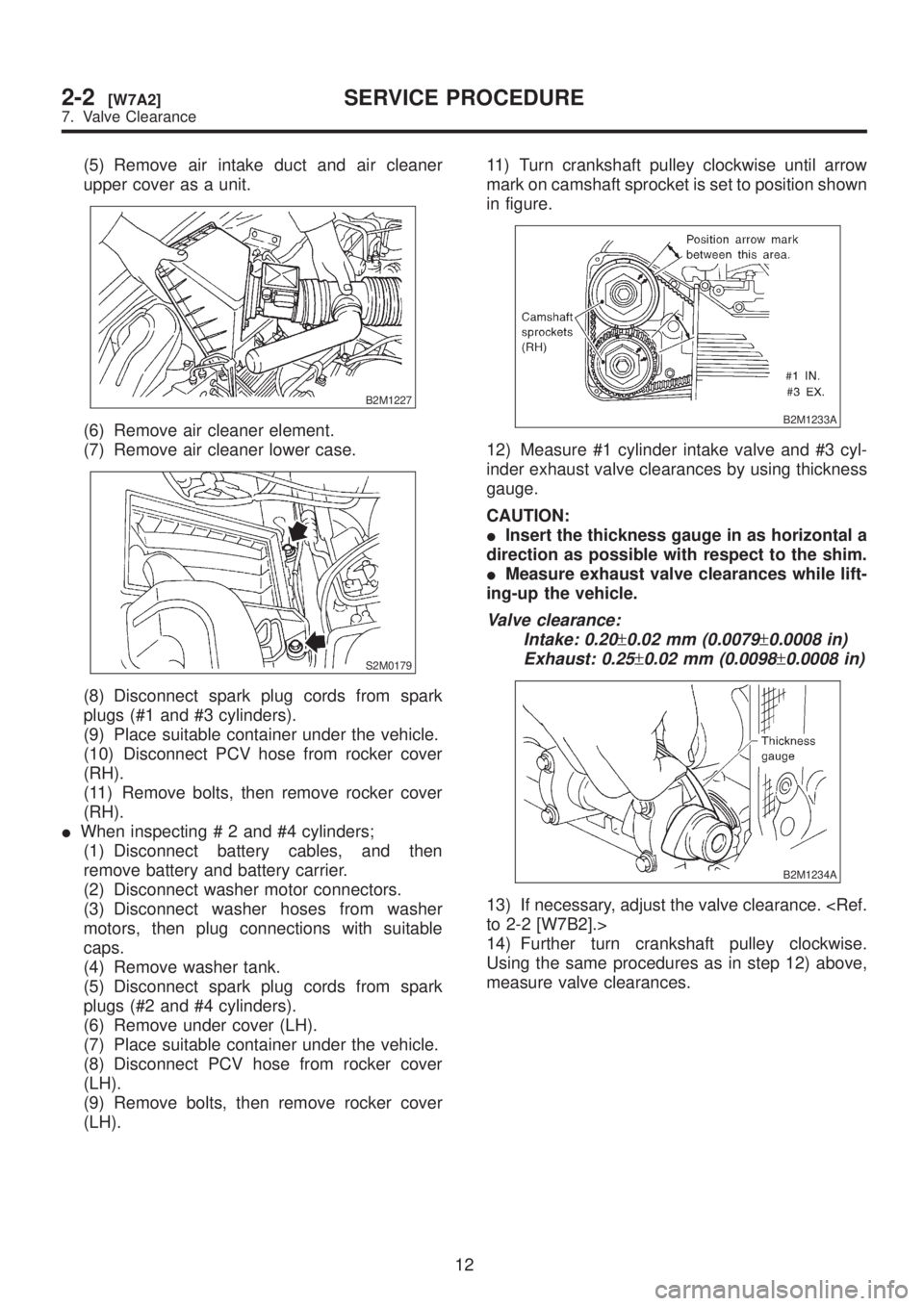
(5) Remove air intake duct and air cleaner
upper cover as a unit.
B2M1227
(6) Remove air cleaner element.
(7) Remove air cleaner lower case.
S2M0179
(8) Disconnect spark plug cords from spark
plugs (#1 and #3 cylinders).
(9) Place suitable container under the vehicle.
(10) Disconnect PCV hose from rocker cover
(RH).
(11) Remove bolts, then remove rocker cover
(RH).
IWhen inspecting # 2 and #4 cylinders;
(1) Disconnect battery cables, and then
remove battery and battery carrier.
(2) Disconnect washer motor connectors.
(3) Disconnect washer hoses from washer
motors, then plug connections with suitable
caps.
(4) Remove washer tank.
(5) Disconnect spark plug cords from spark
plugs (#2 and #4 cylinders).
(6) Remove under cover (LH).
(7) Place suitable container under the vehicle.
(8) Disconnect PCV hose from rocker cover
(LH).
(9) Remove bolts, then remove rocker cover
(LH).11) Turn crankshaft pulley clockwise until arrow
mark on camshaft sprocket is set to position shown
in figure.
B2M1233A
12) Measure #1 cylinder intake valve and #3 cyl-
inder exhaust valve clearances by using thickness
gauge.
CAUTION:
IInsert the thickness gauge in as horizontal a
direction as possible with respect to the shim.
IMeasure exhaust valve clearances while lift-
ing-up the vehicle.
Valve clearance:
Intake: 0.20
±0.02 mm (0.0079±0.0008 in)
Exhaust: 0.25
±0.02 mm (0.0098±0.0008 in)
B2M1234A
13) If necessary, adjust the valve clearance.
14) Further turn crankshaft pulley clockwise.
Using the same procedures as in step 12) above,
measure valve clearances.
12
2-2[W7A2]SERVICE PROCEDURE
7. Valve Clearance
Page 49 of 1456
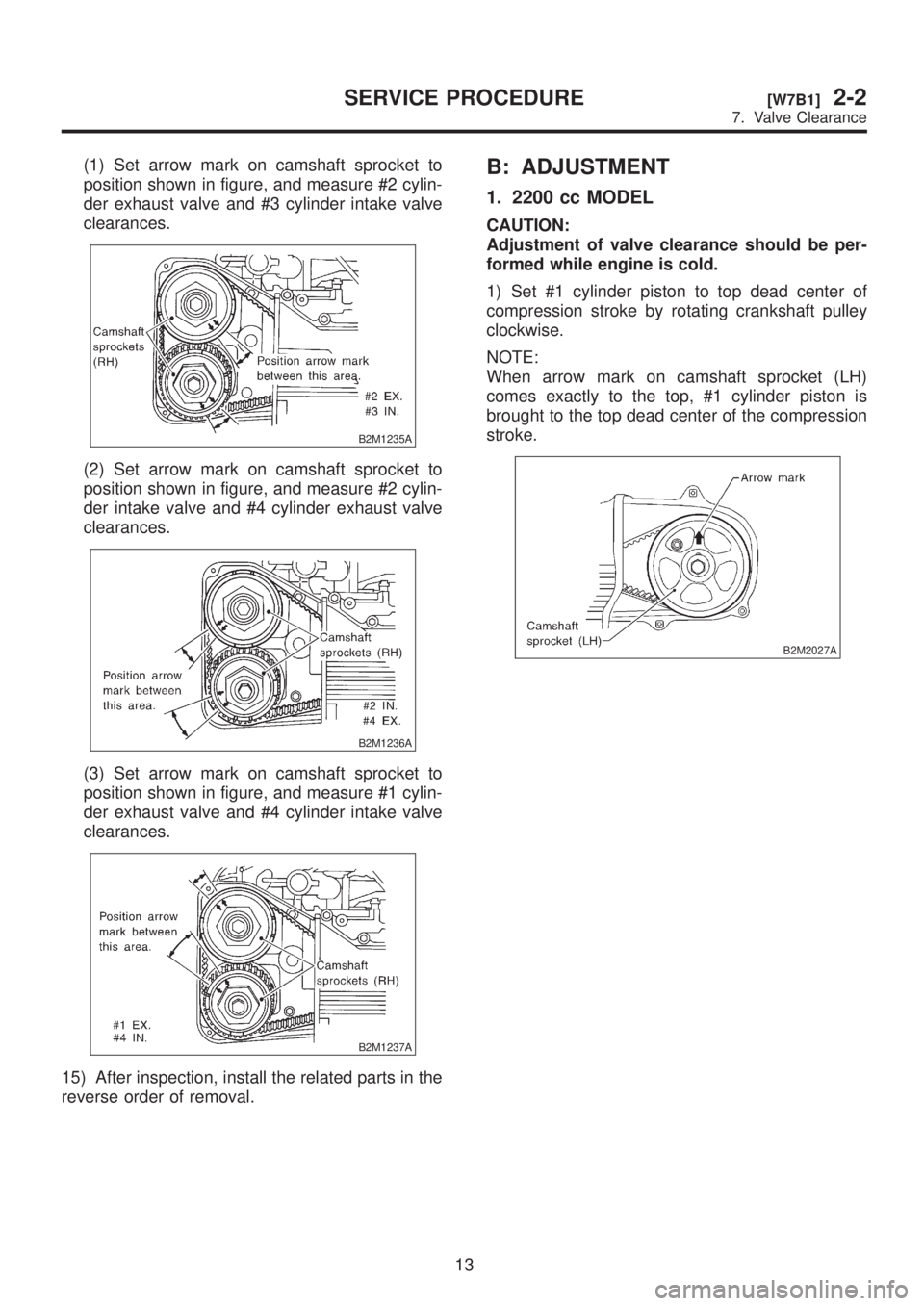
(1) Set arrow mark on camshaft sprocket to
position shown in figure, and measure #2 cylin-
der exhaust valve and #3 cylinder intake valve
clearances.
B2M1235A
(2) Set arrow mark on camshaft sprocket to
position shown in figure, and measure #2 cylin-
der intake valve and #4 cylinder exhaust valve
clearances.
B2M1236A
(3) Set arrow mark on camshaft sprocket to
position shown in figure, and measure #1 cylin-
der exhaust valve and #4 cylinder intake valve
clearances.
B2M1237A
15) After inspection, install the related parts in the
reverse order of removal.
B: ADJUSTMENT
1. 2200 cc MODEL
CAUTION:
Adjustment of valve clearance should be per-
formed while engine is cold.
1) Set #1 cylinder piston to top dead center of
compression stroke by rotating crankshaft pulley
clockwise.
NOTE:
When arrow mark on camshaft sprocket (LH)
comes exactly to the top, #1 cylinder piston is
brought to the top dead center of the compression
stroke.
B2M2027A
13
[W7B1]2-2SERVICE PROCEDURE
7. Valve Clearance
Page 50 of 1456
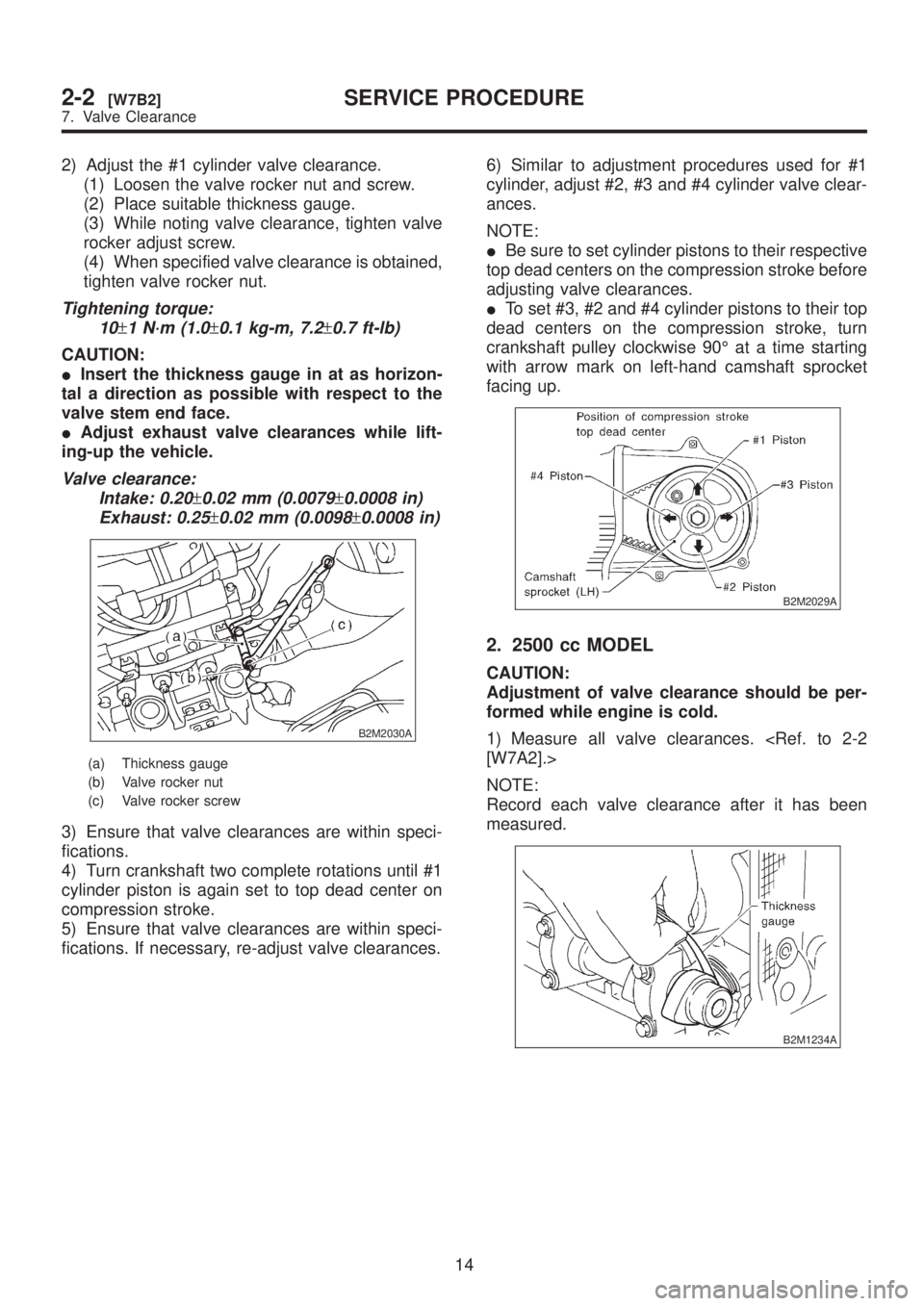
2) Adjust the #1 cylinder valve clearance.
(1) Loosen the valve rocker nut and screw.
(2) Place suitable thickness gauge.
(3) While noting valve clearance, tighten valve
rocker adjust screw.
(4) When specified valve clearance is obtained,
tighten valve rocker nut.
Tightening torque:
10
±1 N´m (1.0±0.1 kg-m, 7.2±0.7 ft-lb)
CAUTION:
IInsert the thickness gauge in at as horizon-
tal a direction as possible with respect to the
valve stem end face.
IAdjust exhaust valve clearances while lift-
ing-up the vehicle.
Valve clearance:
Intake: 0.20
±0.02 mm (0.0079±0.0008 in)
Exhaust: 0.25
±0.02 mm (0.0098±0.0008 in)
B2M2030A
(a) Thickness gauge
(b) Valve rocker nut
(c) Valve rocker screw
3) Ensure that valve clearances are within speci-
fications.
4) Turn crankshaft two complete rotations until #1
cylinder piston is again set to top dead center on
compression stroke.
5) Ensure that valve clearances are within speci-
fications. If necessary, re-adjust valve clearances.6) Similar to adjustment procedures used for #1
cylinder, adjust #2, #3 and #4 cylinder valve clear-
ances.
NOTE:
IBe sure to set cylinder pistons to their respective
top dead centers on the compression stroke before
adjusting valve clearances.
ITo set #3, #2 and #4 cylinder pistons to their top
dead centers on the compression stroke, turn
crankshaft pulley clockwise 90É at a time starting
with arrow mark on left-hand camshaft sprocket
facing up.
B2M2029A
2. 2500 cc MODEL
CAUTION:
Adjustment of valve clearance should be per-
formed while engine is cold.
1) Measure all valve clearances.
NOTE:
Record each valve clearance after it has been
measured.
B2M1234A
14
2-2[W7B2]SERVICE PROCEDURE
7. Valve Clearance