SUZUKI GRAND VITARA 1999 2.G Owners Manual
Manufacturer: SUZUKI, Model Year: 1999, Model line: GRAND VITARA, Model: SUZUKI GRAND VITARA 1999 2.GPages: 656, PDF Size: 14.31 MB
Page 121 of 656
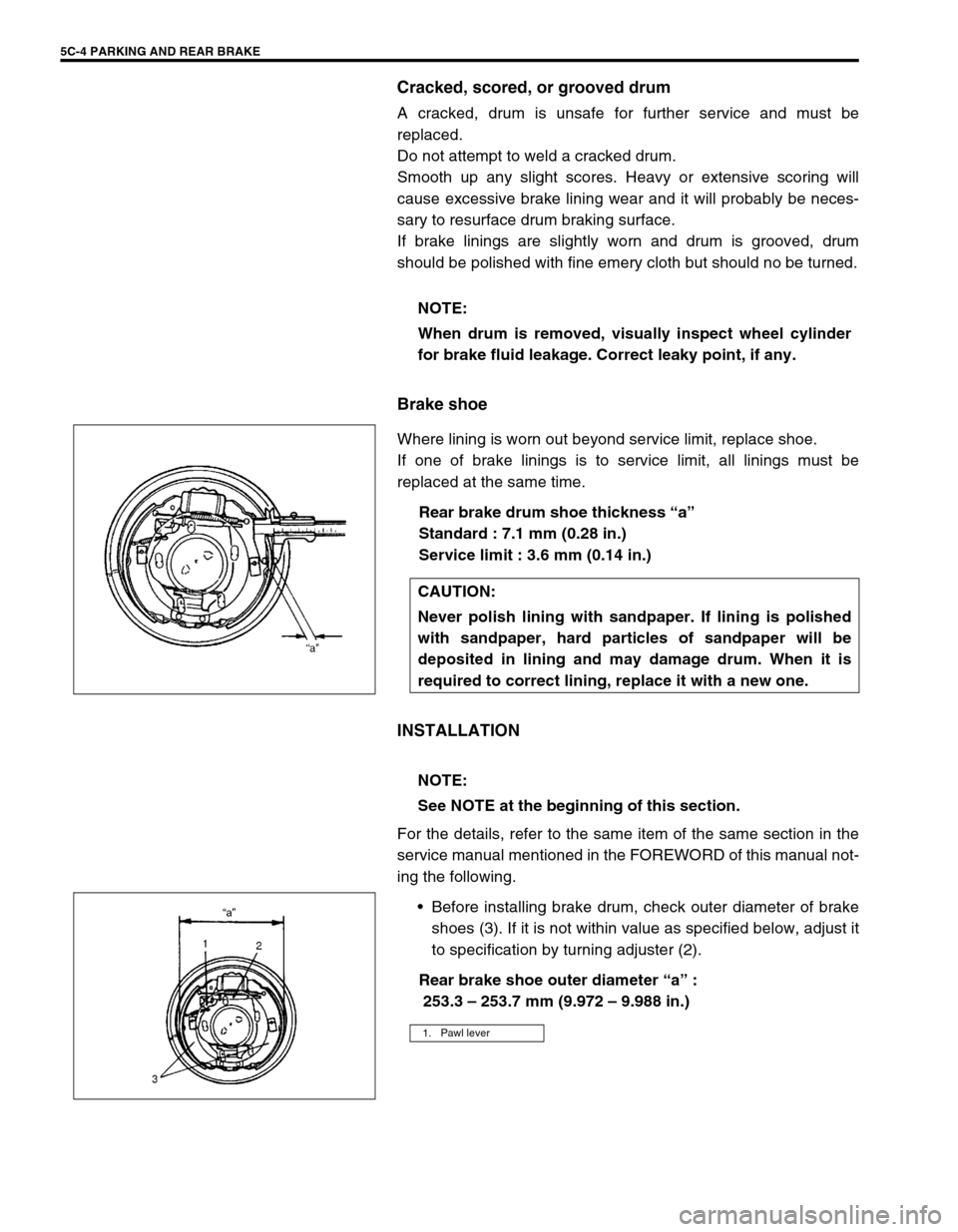
5C-4 PARKING AND REAR BRAKE
Cracked, scored, or grooved drum
A cracked, drum is unsafe for further service and must be
replaced.
Do not attempt to weld a cracked drum.
Smooth up any slight scores. Heavy or extensive scoring will
cause excessive brake lining wear and it will probably be neces-
sary to resurface drum braking surface.
If brake linings are slightly worn and drum is grooved, drum
should be polished with fine emery cloth but should no be turned.
Brake shoe
Where lining is worn out beyond service limit, replace shoe.
If one of brake linings is to service limit, all linings must be
replaced at the same time.
Rear brake drum shoe thickness “a”
Standard : 7.1 mm (0.28 in.)
Service limit : 3.6 mm (0.14 in.)
INSTALLATION
For the details, refer to the same item of the same section in the
service manual mentioned in the FOREWORD of this manual not-
ing the following.
Before installing brake drum, check outer diameter of brake
shoes (3). If it is not within value as specified below, adjust it
to specification by turning adjuster (2).
Rear brake shoe outer diameter “a” :
253.3 – 253.7 mm (9.972 – 9.988 in.) NOTE:
When drum is removed, visually inspect wheel cylinder
for brake fluid leakage. Correct leaky point, if any.
CAUTION:
Never polish lining with sandpaper. If lining is polished
with sandpaper, hard particles of sandpaper will be
deposited in lining and may damage drum. When it is
required to correct lining, replace it with a new one.
NOTE:
See NOTE at the beginning of this section.
1. Pawl lever
Page 122 of 656
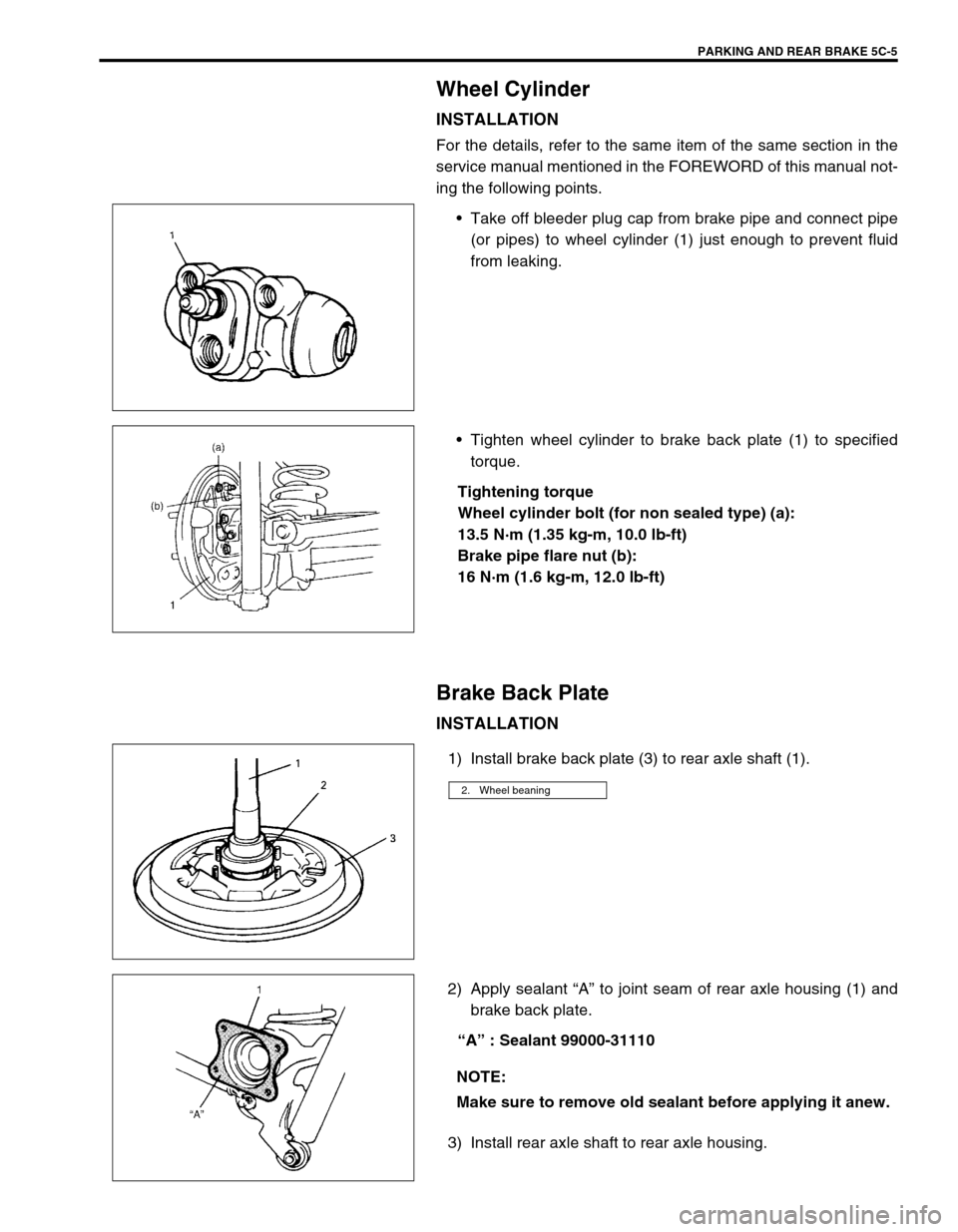
PARKING AND REAR BRAKE 5C-5
Wheel Cylinder
INSTALLATION
For the details, refer to the same item of the same section in the
service manual mentioned in the FOREWORD of this manual not-
ing the following points.
Take off bleeder plug cap from brake pipe and connect pipe
(or pipes) to wheel cylinder (1) just enough to prevent fluid
from leaking.
Tighten wheel cylinder to brake back plate (1) to specified
torque.
Tightening torque
Wheel cylinder bolt (for non sealed type) (a):
13.5 N·m (1.35 kg-m, 10.0 lb-ft)
Brake pipe flare nut (b):
16 N·m (1.6 kg-m, 12.0 lb-ft)
Brake Back Plate
INSTALLATION
1) Install brake back plate (3) to rear axle shaft (1).
2) Apply sealant “A” to joint seam of rear axle housing (1) and
brake back plate.
“A” : Sealant 99000-31110
3) Install rear axle shaft to rear axle housing.
2. Wheel beaning
NOTE:
Make sure to remove old sealant before applying it anew.
Page 123 of 656
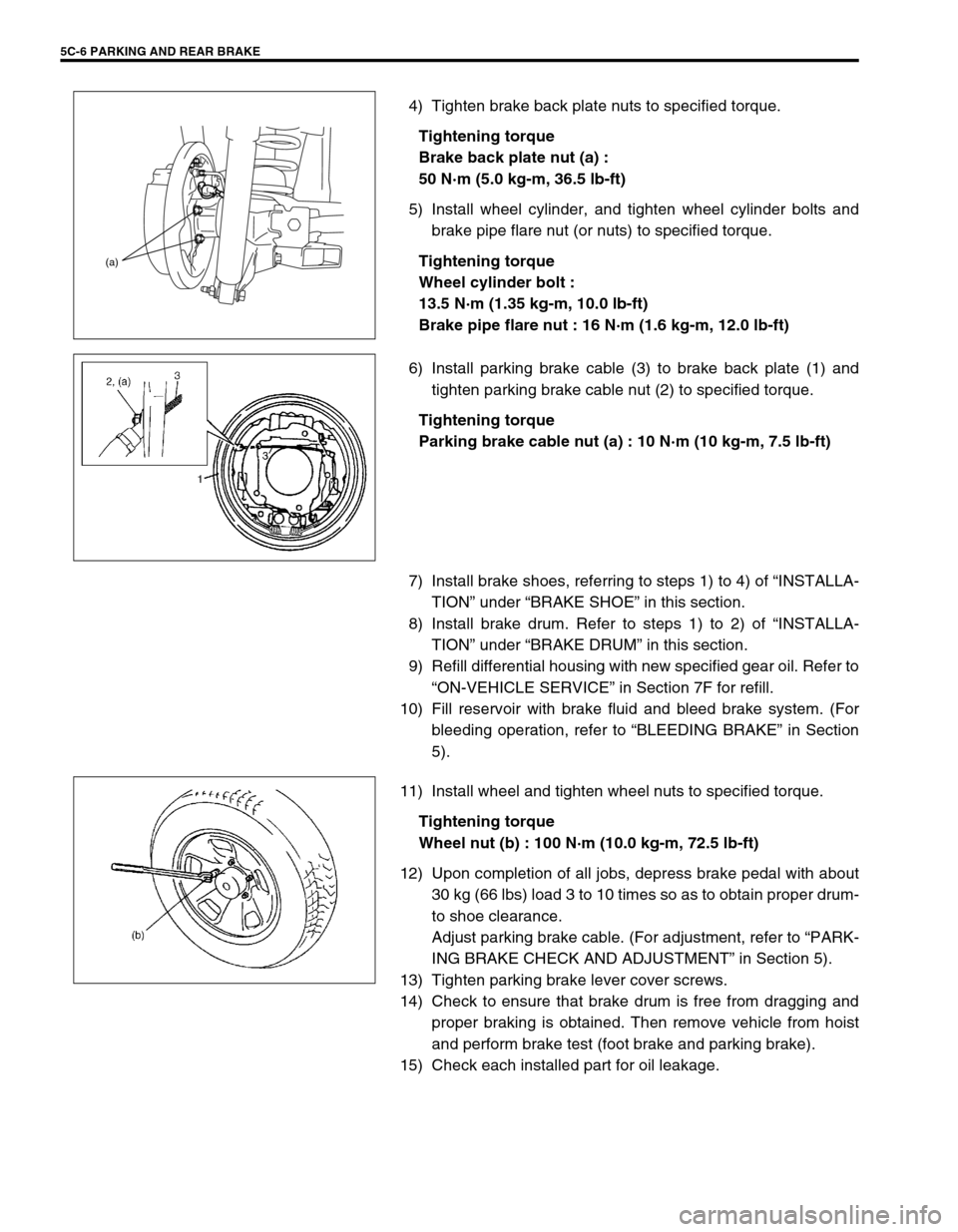
5C-6 PARKING AND REAR BRAKE
4) Tighten brake back plate nuts to specified torque.
Tightening torque
Brake back plate nut (a) :
50 N·m (5.0 kg-m, 36.5 lb-ft)
5) Install wheel cylinder, and tighten wheel cylinder bolts and
brake pipe flare nut (or nuts) to specified torque.
Tightening torque
Wheel cylinder bolt :
13.5 N·m (1.35 kg-m, 10.0 lb-ft)
Brake pipe flare nut : 16 N·m (1.6 kg-m, 12.0 lb-ft)
6) Install parking brake cable (3) to brake back plate (1) and
tighten parking brake cable nut (2) to specified torque.
Tightening torque
Parking brake cable nut (a) : 10 N·m (10 kg-m, 7.5 lb-ft)
7) Install brake shoes, referring to steps 1) to 4) of “INSTALLA-
TION” under “BRAKE SHOE” in this section.
8) Install brake drum. Refer to steps 1) to 2) of “INSTALLA-
TION” under “BRAKE DRUM” in this section.
9) Refill differential housing with new specified gear oil. Refer to
“ON-VEHICLE SERVICE” in Section 7F for refill.
10) Fill reservoir with brake fluid and bleed brake system. (For
bleeding operation, refer to “BLEEDING BRAKE” in Section
5).
11) Install wheel and tighten wheel nuts to specified torque.
Tightening torque
Wheel nut (b) : 100 N·m (10.0 kg-m, 72.5 lb-ft)
12) Upon completion of all jobs, depress brake pedal with about
30 kg (66 lbs) load 3 to 10 times so as to obtain proper drum-
to shoe clearance.
Adjust parking brake cable. (For adjustment, refer to “PARK-
ING BRAKE CHECK AND ADJUSTMENT” in Section 5).
13) Tighten parking brake lever cover screws.
14) Check to ensure that brake drum is free from dragging and
proper braking is obtained. Then remove vehicle from hoist
and perform brake test (foot brake and parking brake).
15) Check each installed part for oil leakage.
(a)
Page 124 of 656
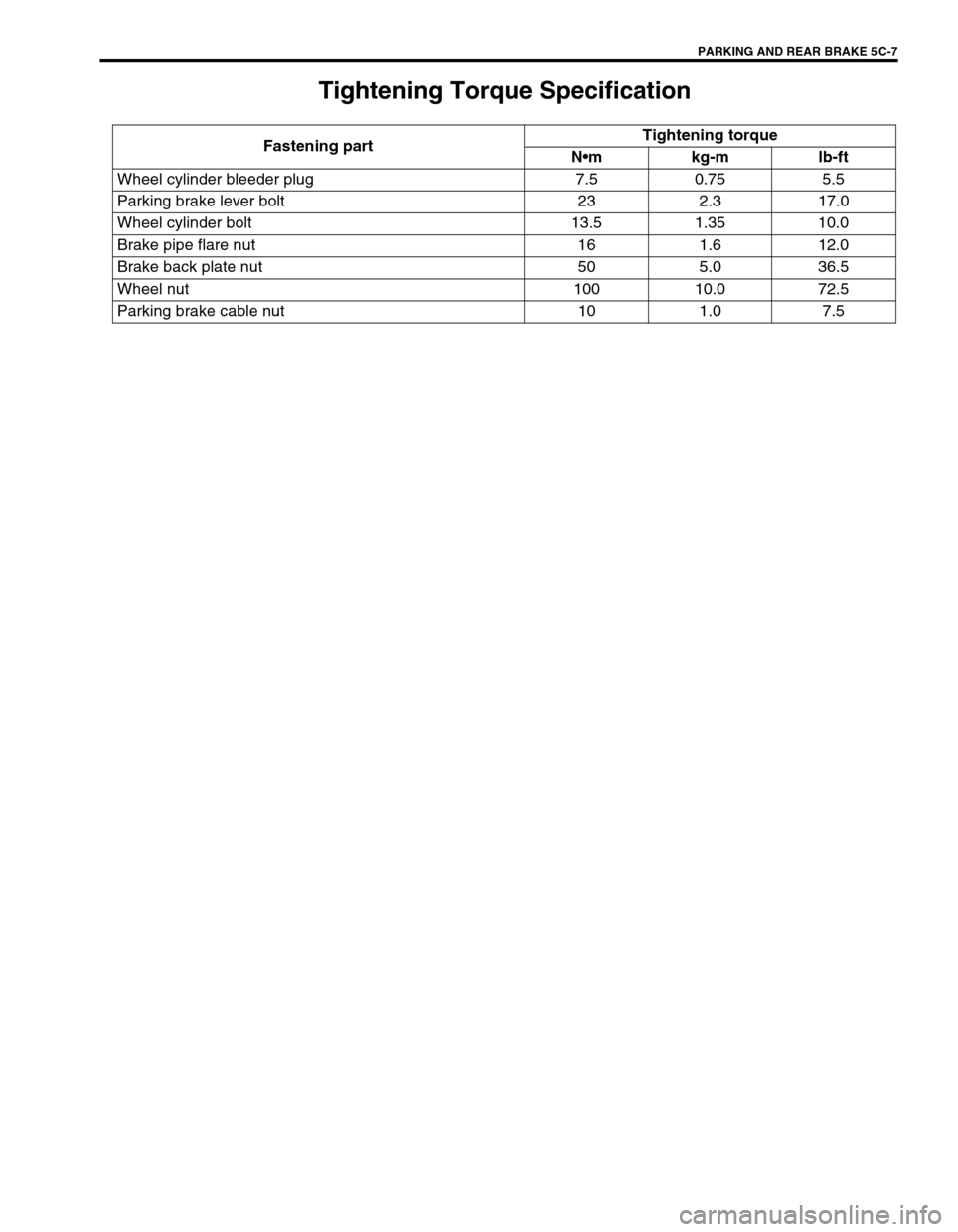
PARKING AND REAR BRAKE 5C-7
Tightening Torque Specification
Fastening partTightening torque
Nmkg-mlb-ft
Wheel cylinder bleeder plug 7.5 0.75 5.5
Parking brake lever bolt 23 2.3 17.0
Wheel cylinder bolt 13.5 1.35 10.0
Brake pipe flare nut 16 1.6 12.0
Brake back plate nut 50 5.0 36.5
Wheel nut 100 10.0 72.5
Parking brake cable nut 10 1.0 7.5
Page 125 of 656
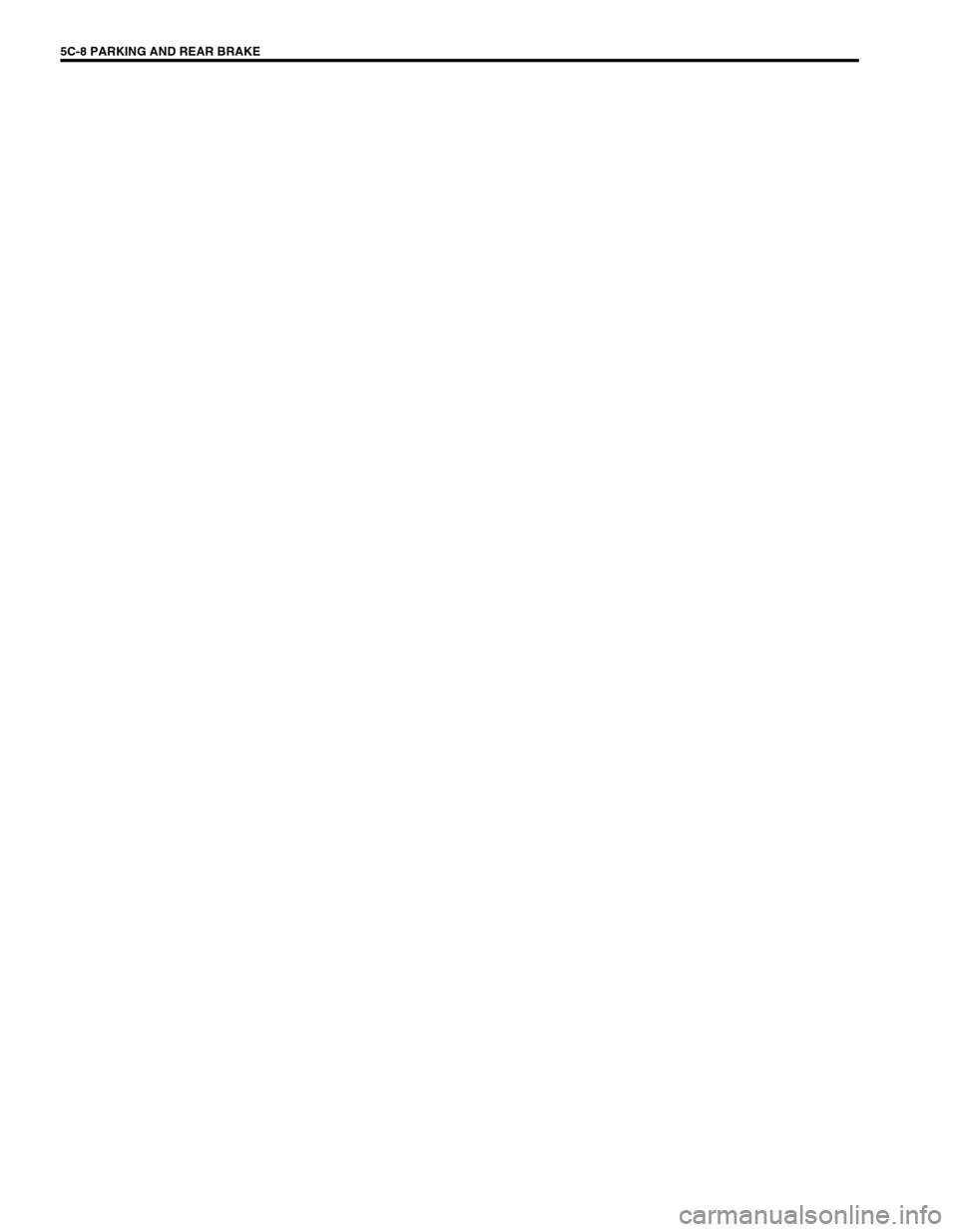
5C-8 PARKING AND REAR BRAKE
Page 126 of 656
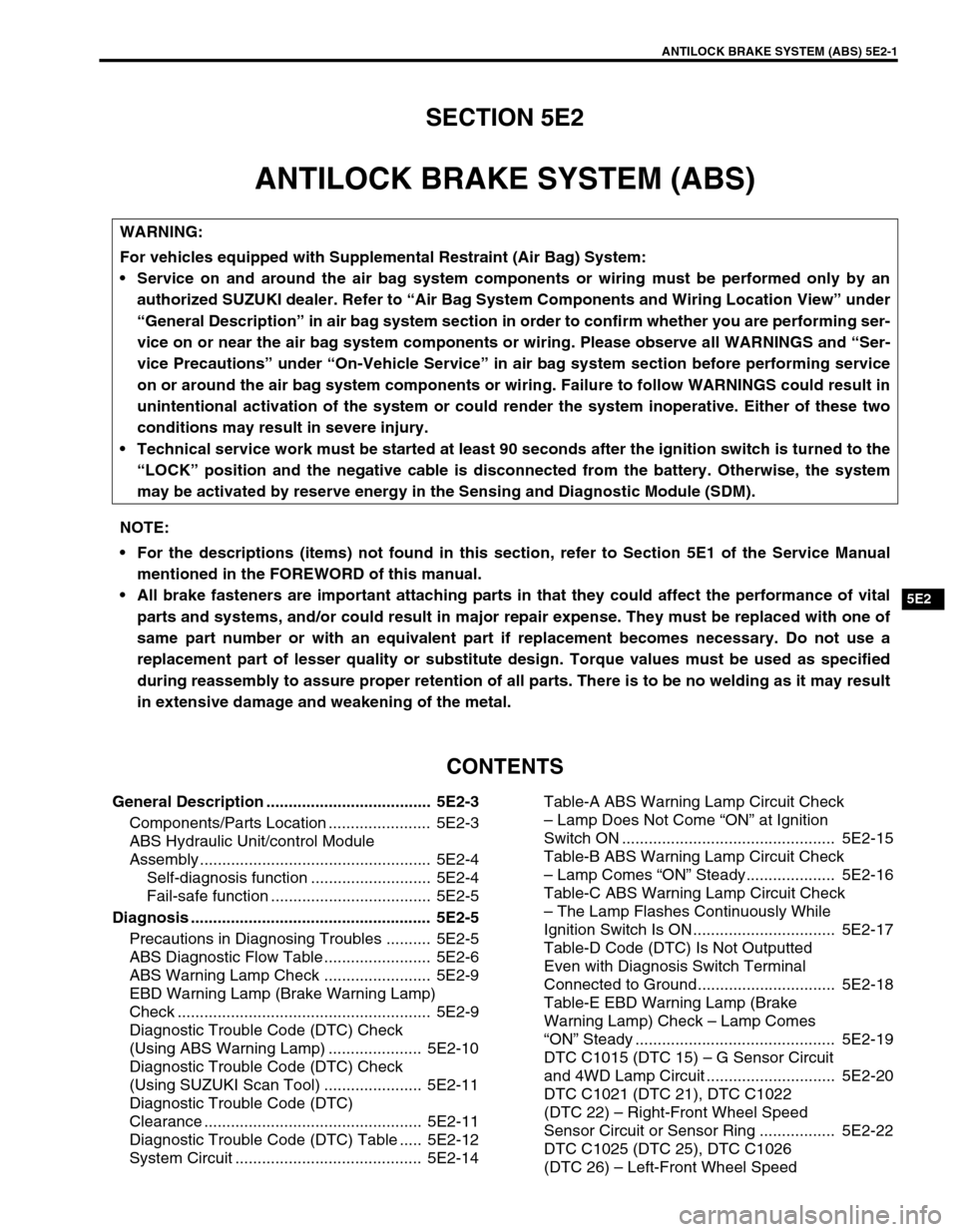
ANTILOCK BRAKE SYSTEM (ABS) 5E2-1
5E2
SECTION 5E2
ANTILOCK BRAKE SYSTEM (ABS)
CONTENTS
General Description ..................................... 5E2-3
Components/Parts Location ....................... 5E2-3
ABS Hydraulic Unit/control Module
Assembly .................................................... 5E2-4
Self-diagnosis function ........................... 5E2-4
Fail-safe function .................................... 5E2-5
Diagnosis ...................................................... 5E2-5
Precautions in Diagnosing Troubles .......... 5E2-5
ABS Diagnostic Flow Table ........................ 5E2-6
ABS Warning Lamp Check ........................ 5E2-9
EBD Warning Lamp (Brake Warning Lamp)
Check ......................................................... 5E2-9
Diagnostic Trouble Code (DTC) Check
(Using ABS Warning Lamp) ..................... 5E2-10
Diagnostic Trouble Code (DTC) Check
(Using SUZUKI Scan Tool) ...................... 5E2-11
Diagnostic Trouble Code (DTC)
Clearance ................................................. 5E2-11
Diagnostic Trouble Code (DTC) Table ..... 5E2-12
System Circuit .......................................... 5E2-14Table-A ABS Warning Lamp Circuit Check
– Lamp Does Not Come “ON” at Ignition
Switch ON ................................................ 5E2-15
Table-B ABS Warning Lamp Circuit Check
– Lamp Comes “ON” Steady.................... 5E2-16
Table-C ABS Warning Lamp Circuit Check
– The Lamp Flashes Continuously While
Ignition Switch Is ON ................................ 5E2-17
Table-D Code (DTC) Is Not Outputted
Even with Diagnosis Switch Terminal
Connected to Ground............................... 5E2-18
Table-E EBD Warning Lamp (Brake
Warning Lamp) Check – Lamp Comes
“ON” Steady ............................................. 5E2-19
DTC C1015 (DTC 15) – G Sensor Circuit
and 4WD Lamp Circuit ............................. 5E2-20
DTC C1021 (DTC 21), DTC C1022
(DTC 22) – Right-Front Wheel Speed
Sensor Circuit or Sensor Ring ................. 5E2-22
DTC C1025 (DTC 25), DTC C1026
(DTC 26) – Left-Front Wheel Speed WARNING:
For vehicles equipped with Supplemental Restraint (Air Bag) System:
Service on and around the air bag system components or wiring must be performed only by an
authorized SUZUKI dealer. Refer to “Air Bag System Components and Wiring Location View” under
“General Description” in air bag system section in order to confirm whether you are performing ser-
vice on or near the air bag system components or wiring. Please observe all WARNINGS and “Ser-
vice Precautions” under “On-Vehicle Service” in air bag system section before performing service
on or around the air bag system components or wiring. Failure to follow WARNINGS could result in
unintentional activation of the system or could render the system inoperative. Either of these two
conditions may result in severe injury.
Technical service work must be started at least 90 seconds after the ignition switch is turned to the
“LOCK” position and the negative cable is disconnected from the battery. Otherwise, the system
may be activated by reserve energy in the Sensing and Diagnostic Module (SDM).
NOTE:
For the descriptions (items) not found in this section, refer to Section 5E1 of the Service Manual
mentioned in the FOREWORD of this manual.
All brake fasteners are important attaching parts in that they could affect the performance of vital
parts and systems, and/or could result in major repair expense. They must be replaced with one of
same part number or with an equivalent part if replacement becomes necessary. Do not use a
replacement part of lesser quality or substitute design. Torque values must be used as specified
during reassembly to assure proper retention of all parts. There is to be no welding as it may result
in extensive damage and weakening of the metal.
Page 127 of 656
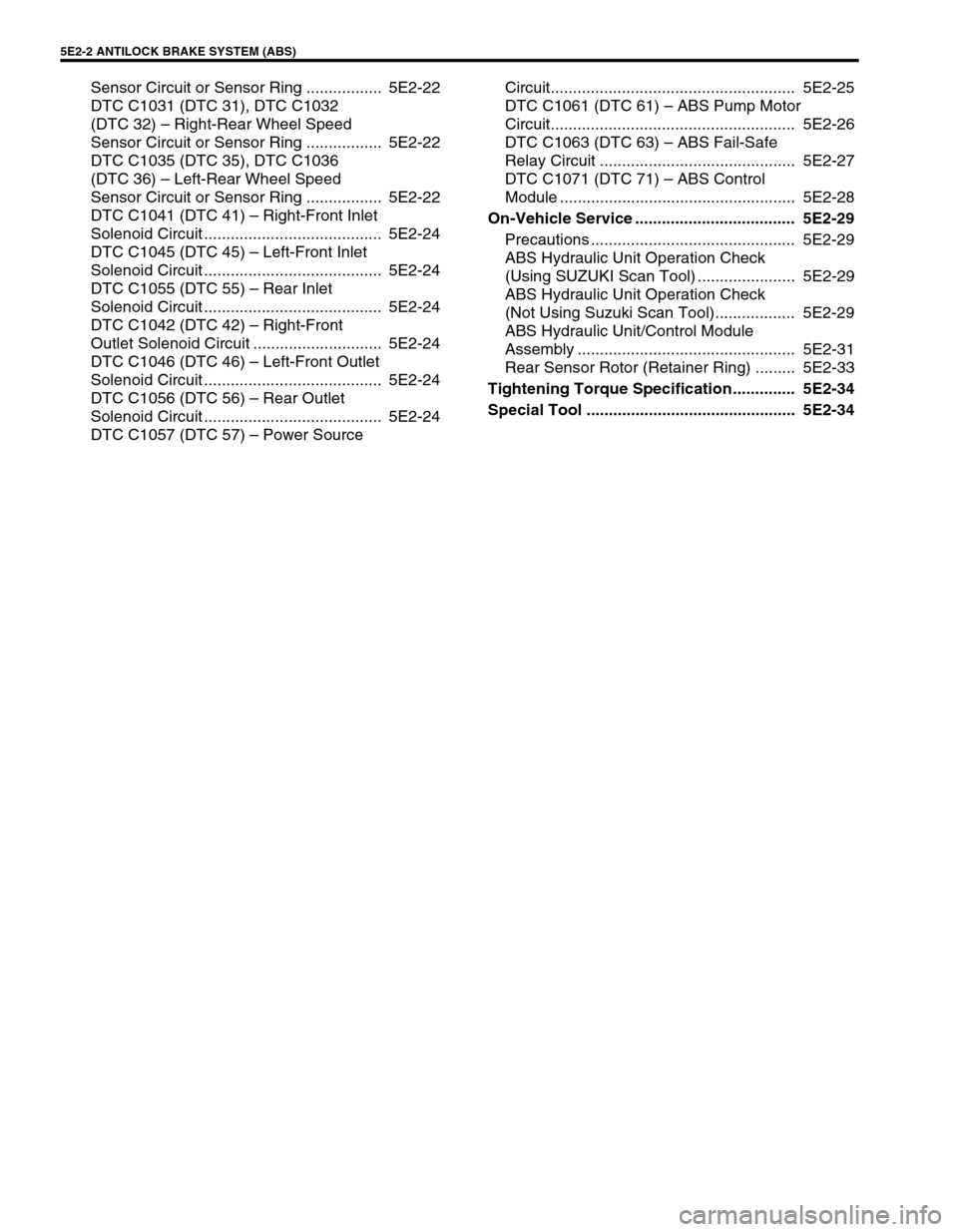
5E2-2 ANTILOCK BRAKE SYSTEM (ABS)
Sensor Circuit or Sensor Ring ................. 5E2-22
DTC C1031 (DTC 31), DTC C1032
(DTC 32) – Right-Rear Wheel Speed
Sensor Circuit or Sensor Ring ................. 5E2-22
DTC C1035 (DTC 35), DTC C1036
(DTC 36) – Left-Rear Wheel Speed
Sensor Circuit or Sensor Ring ................. 5E2-22
DTC C1041 (DTC 41) – Right-Front Inlet
Solenoid Circuit ........................................ 5E2-24
DTC C1045 (DTC 45) – Left-Front Inlet
Solenoid Circuit ........................................ 5E2-24
DTC C1055 (DTC 55) – Rear Inlet
Solenoid Circuit ........................................ 5E2-24
DTC C1042 (DTC 42) – Right-Front
Outlet Solenoid Circuit ............................. 5E2-24
DTC C1046 (DTC 46) – Left-Front Outlet
Solenoid Circuit ........................................ 5E2-24
DTC C1056 (DTC 56) – Rear Outlet
Solenoid Circuit ........................................ 5E2-24
DTC C1057 (DTC 57) – Power Source Circuit....................................................... 5E2-25
DTC C1061 (DTC 61) – ABS Pump Motor
Circuit....................................................... 5E2-26
DTC C1063 (DTC 63) – ABS Fail-Safe
Relay Circuit ............................................ 5E2-27
DTC C1071 (DTC 71) – ABS Control
Module ..................................................... 5E2-28
On-Vehicle Service .................................... 5E2-29
Precautions .............................................. 5E2-29
ABS Hydraulic Unit Operation Check
(Using SUZUKI Scan Tool) ...................... 5E2-29
ABS Hydraulic Unit Operation Check
(Not Using Suzuki Scan Tool).................. 5E2-29
ABS Hydraulic Unit/Control Module
Assembly ................................................. 5E2-31
Rear Sensor Rotor (Retainer Ring) ......... 5E2-33
Tightening Torque Specification.............. 5E2-34
Special Tool ............................................... 5E2-34
Page 128 of 656
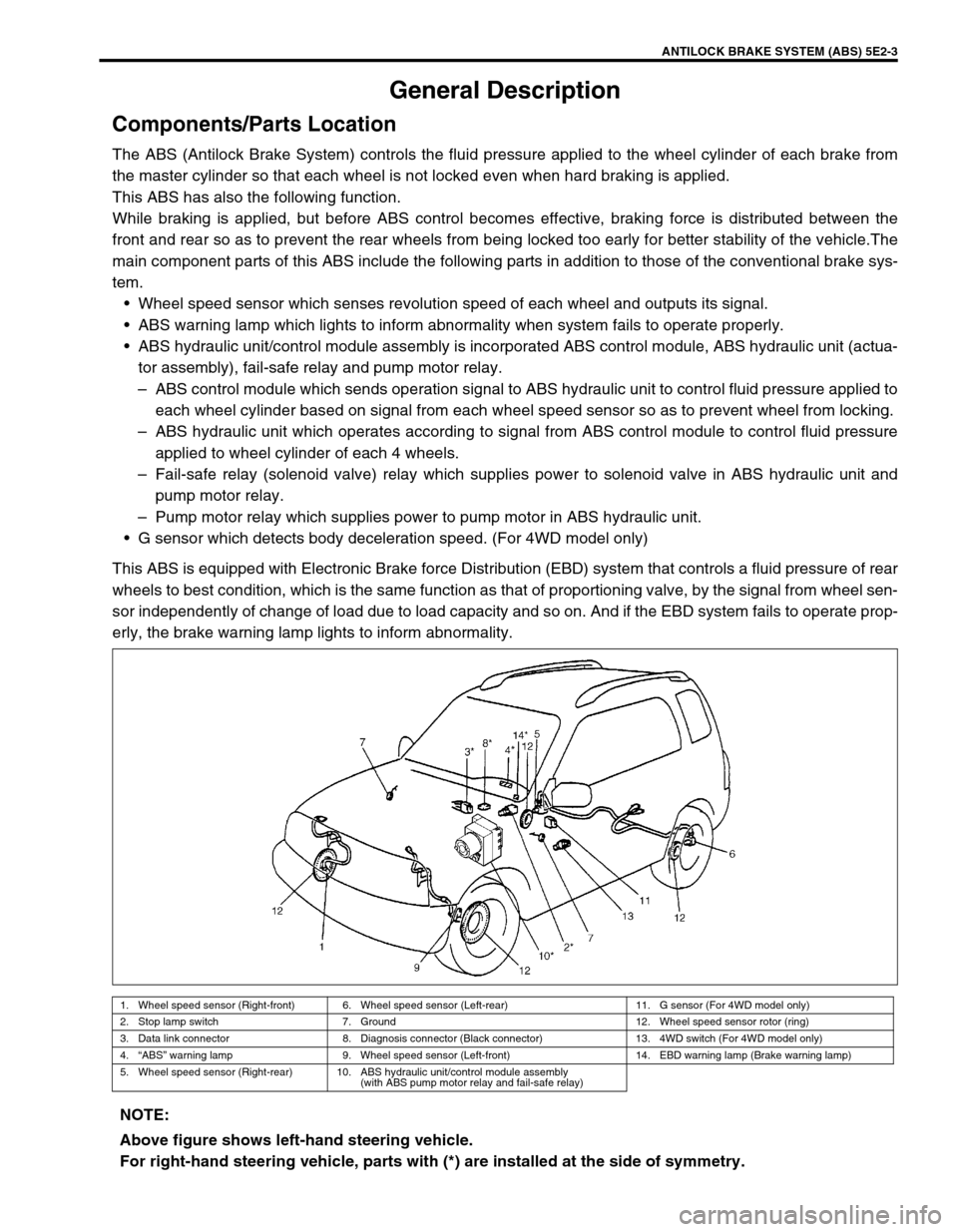
ANTILOCK BRAKE SYSTEM (ABS) 5E2-3
General Description
Components/Parts Location
The ABS (Antilock Brake System) controls the fluid pressure applied to the wheel cylinder of each brake from
the master cylinder so that each wheel is not locked even when hard braking is applied.
This ABS has also the following function.
While braking is applied, but before ABS control becomes effective, braking force is distributed between the
front and rear so as to prevent the rear wheels from being locked too early for better stability of the vehicle.The
main component parts of this ABS include the following parts in addition to those of the conventional brake sys-
tem.
Wheel speed sensor which senses revolution speed of each wheel and outputs its signal.
ABS warning lamp which lights to inform abnormality when system fails to operate properly.
ABS hydraulic unit/control module assembly is incorporated ABS control module, ABS hydraulic unit (actua-
tor assembly), fail-safe relay and pump motor relay.
–ABS control module which sends operation signal to ABS hydraulic unit to control fluid pressure applied to
each wheel cylinder based on signal from each wheel speed sensor so as to prevent wheel from locking.
–ABS hydraulic unit which operates according to signal from ABS control module to control fluid pressure
applied to wheel cylinder of each 4 wheels.
–Fail-safe relay (solenoid valve) relay which supplies power to solenoid valve in ABS hydraulic unit and
pump motor relay.
–Pump motor relay which supplies power to pump motor in ABS hydraulic unit.
G sensor which detects body deceleration speed. (For 4WD model only)
This ABS is equipped with Electronic Brake force Distribution (EBD) system that controls a fluid pressure of rear
wheels to best condition, which is the same function as that of proportioning valve, by the signal from wheel sen-
sor independently of change of load due to load capacity and so on. And if the EBD system fails to operate prop-
erly, the brake warning lamp lights to inform abnormality.
1. Wheel speed sensor (Right-front) 6. Wheel speed sensor (Left-rear) 11. G sensor (For 4WD model only)
2. Stop lamp switch 7. Ground 12. Wheel speed sensor rotor (ring)
3. Data link connector 8. Diagnosis connector (Black connector) 13. 4WD switch (For 4WD model only)
4.“ABS” warning lamp 9. Wheel speed sensor (Left-front) 14. EBD warning lamp (Brake warning lamp)
5. Wheel speed sensor (Right-rear) 10. ABS hydraulic unit/control module assembly
(with ABS pump motor relay and fail-safe relay)
NOTE:
Above figure shows left-hand steering vehicle.
For right-hand steering vehicle, parts with (*) are installed at the side of symmetry.
Page 129 of 656
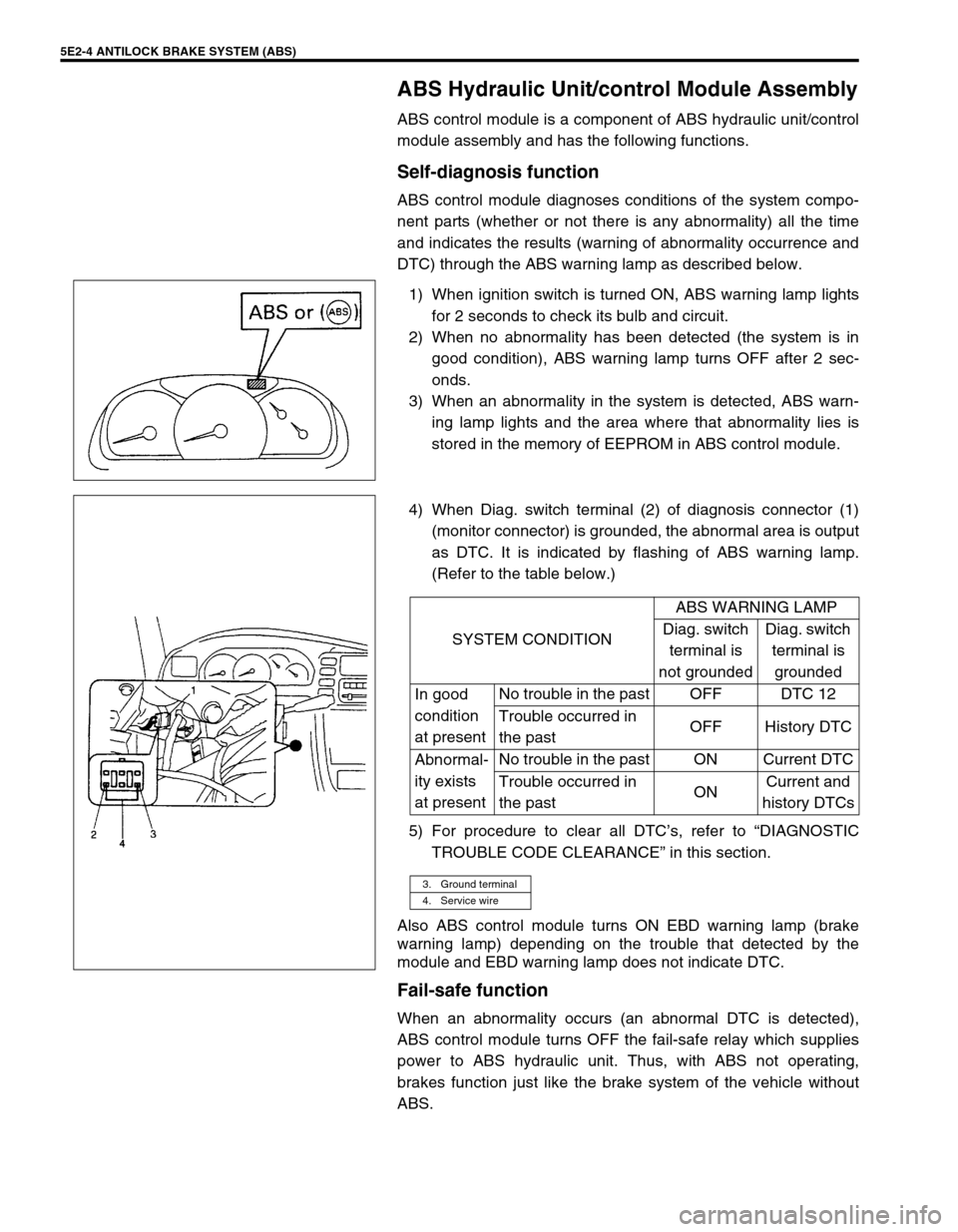
5E2-4 ANTILOCK BRAKE SYSTEM (ABS)
ABS Hydraulic Unit/control Module Assembly
ABS control module is a component of ABS hydraulic unit/control
module assembly and has the following functions.
Self-diagnosis function
ABS control module diagnoses conditions of the system compo-
nent parts (whether or not there is any abnormality) all the time
and indicates the results (warning of abnormality occurrence and
DTC) through the ABS warning lamp as described below.
1) When ignition switch is turned ON, ABS warning lamp lights
for 2 seconds to check its bulb and circuit.
2) When no abnormality has been detected (the system is in
good condition), ABS warning lamp turns OFF after 2 sec-
onds.
3) When an abnormality in the system is detected, ABS warn-
ing lamp lights and the area where that abnormality lies is
stored in the memory of EEPROM in ABS control module.
4) When Diag. switch terminal (2) of diagnosis connector (1)
(monitor connector) is grounded, the abnormal area is output
as DTC. It is indicated by flashing of ABS warning lamp.
(Refer to the table below.)
5) For procedure to clear all DTC’s, refer to “DIAGNOSTIC
TROUBLE CODE CLEARANCE” in this section.
Also ABS control module turns ON EBD warning lamp (brake
warning lamp) depending on the trouble that detected by the
module and EBD warning lamp does not indicate DTC.
Fail-safe function
When an abnormality occurs (an abnormal DTC is detected),
ABS control module turns OFF the fail-safe relay which supplies
power to ABS hydraulic unit. Thus, with ABS not operating,
brakes function just like the brake system of the vehicle without
ABS.
SYSTEM CONDITIONABS WARNING LAMP
Diag. switch
terminal is
not groundedDiag. switch
terminal is
grounded
In good
condition
at presentNo trouble in the past OFF DTC 12
Trouble occurred in
the pastOFF History DTC
Abnormal-
ity exists
at presentNo trouble in the past ON Current DTC
Trouble occurred in
the pastONCurrent and
history DTCs
3. Ground terminal
4. Service wire
Page 130 of 656
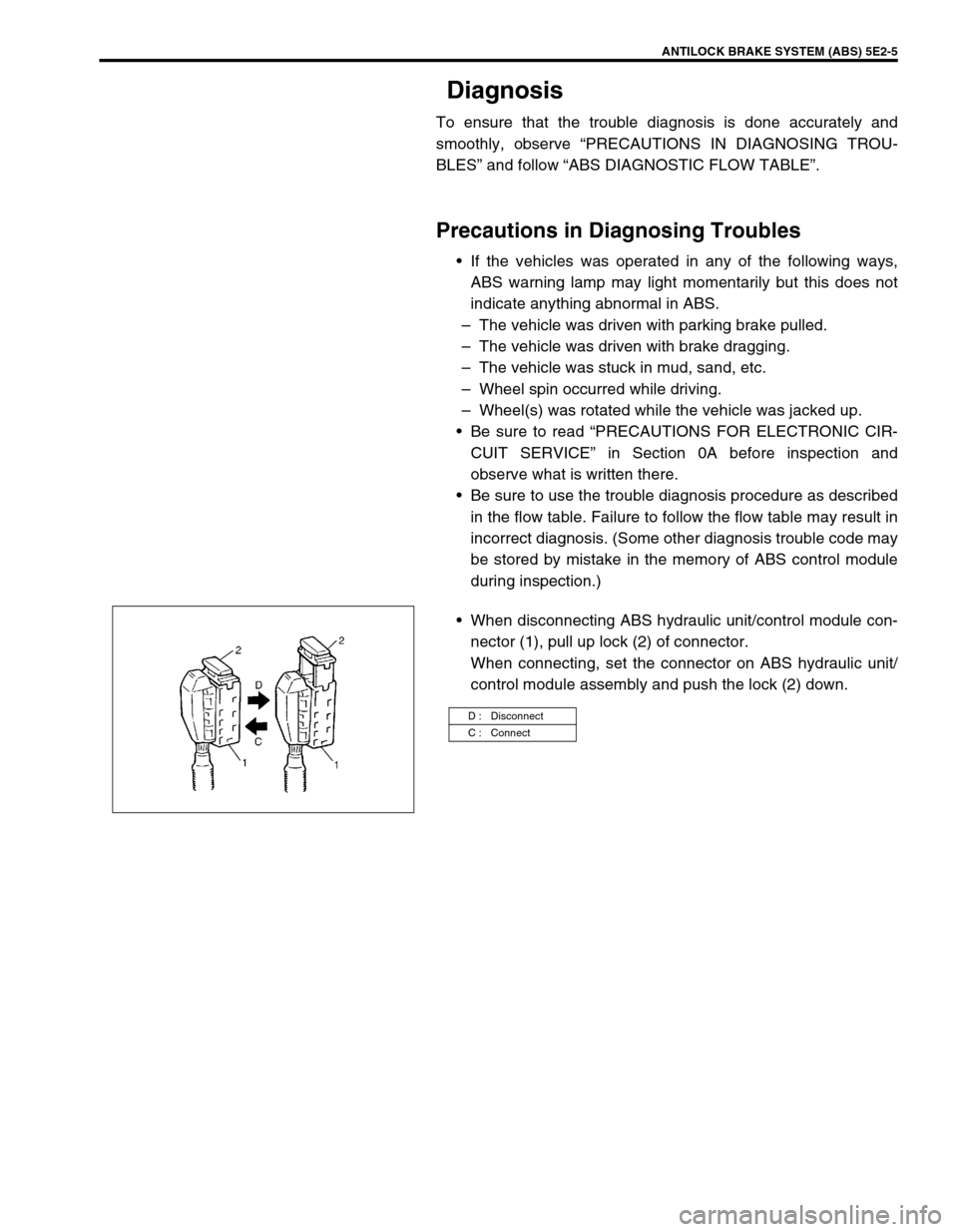
ANTILOCK BRAKE SYSTEM (ABS) 5E2-5
Diagnosis
To ensure that the trouble diagnosis is done accurately and
smoothly, observe “PRECAUTIONS IN DIAGNOSING TROU-
BLES” and follow “ABS DIAGNOSTIC FLOW TABLE”.
Precautions in Diagnosing Troubles
If the vehicles was operated in any of the following ways,
ABS warning lamp may light momentarily but this does not
indicate anything abnormal in ABS.
–The vehicle was driven with parking brake pulled.
–The vehicle was driven with brake dragging.
–The vehicle was stuck in mud, sand, etc.
–Wheel spin occurred while driving.
–Wheel(s) was rotated while the vehicle was jacked up.
Be sure to read “PRECAUTIONS FOR ELECTRONIC CIR-
CUIT SERVICE” in Section 0A before inspection and
observe what is written there.
Be sure to use the trouble diagnosis procedure as described
in the flow table. Failure to follow the flow table may result in
incorrect diagnosis. (Some other diagnosis trouble code may
be stored by mistake in the memory of ABS control module
during inspection.)
When disconnecting ABS hydraulic unit/control module con-
nector (1), pull up lock (2) of connector.
When connecting, set the connector on ABS hydraulic unit/
control module assembly and push the lock (2) down.
D : Disconnect
C : Connect