SUZUKI GRAND VITARA 1999 2.G Owners Manual
Manufacturer: SUZUKI, Model Year: 1999, Model line: GRAND VITARA, Model: SUZUKI GRAND VITARA 1999 2.GPages: 656, PDF Size: 14.31 MB
Page 101 of 656
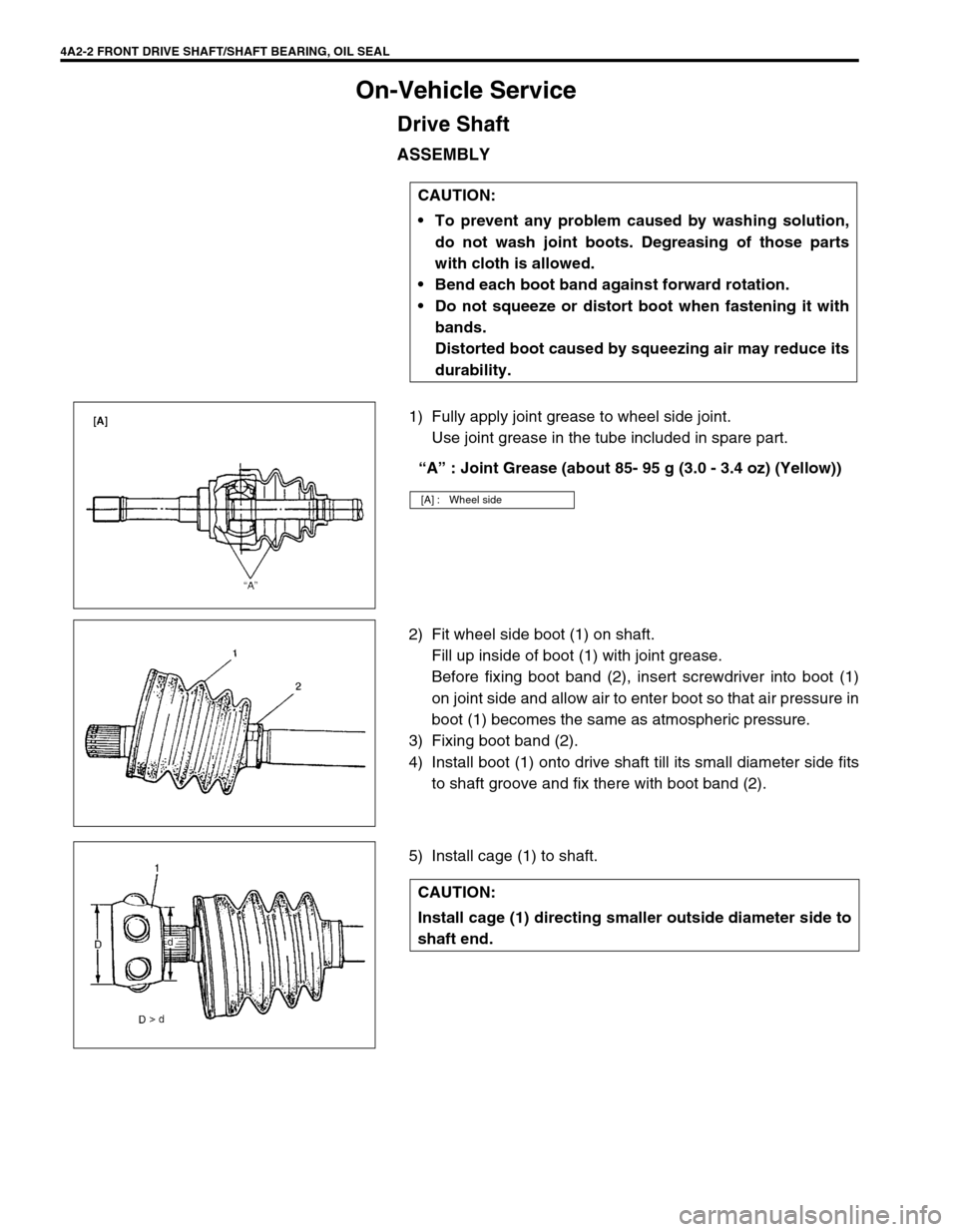
4A2-2 FRONT DRIVE SHAFT/SHAFT BEARING, OIL SEAL
On-Vehicle Service
Drive Shaft
ASSEMBLY
1) Fully apply joint grease to wheel side joint.
Use joint grease in the tube included in spare part.
“A” : Joint Grease (about 85- 95 g (3.0 - 3.4 oz) (Yellow))
2) Fit wheel side boot (1) on shaft.
Fill up inside of boot (1) with joint grease.
Before fixing boot band (2), insert screwdriver into boot (1)
on joint side and allow air to enter boot so that air pressure in
boot (1) becomes the same as atmospheric pressure.
3) Fixing boot band (2).
4) Install boot (1) onto drive shaft till its small diameter side fits
to shaft groove and fix there with boot band (2).
5) Install cage (1) to shaft.CAUTION:
To prevent any problem caused by washing solution,
do not wash joint boots. Degreasing of those parts
with cloth is allowed.
Bend each boot band against forward rotation.
Do not squeeze or distort boot when fastening it with
bands.
Distorted boot caused by squeezing air may reduce its
durability.
[A] : Wheel side
CAUTION:
Install cage (1) directing smaller outside diameter side to
shaft end.
Page 102 of 656
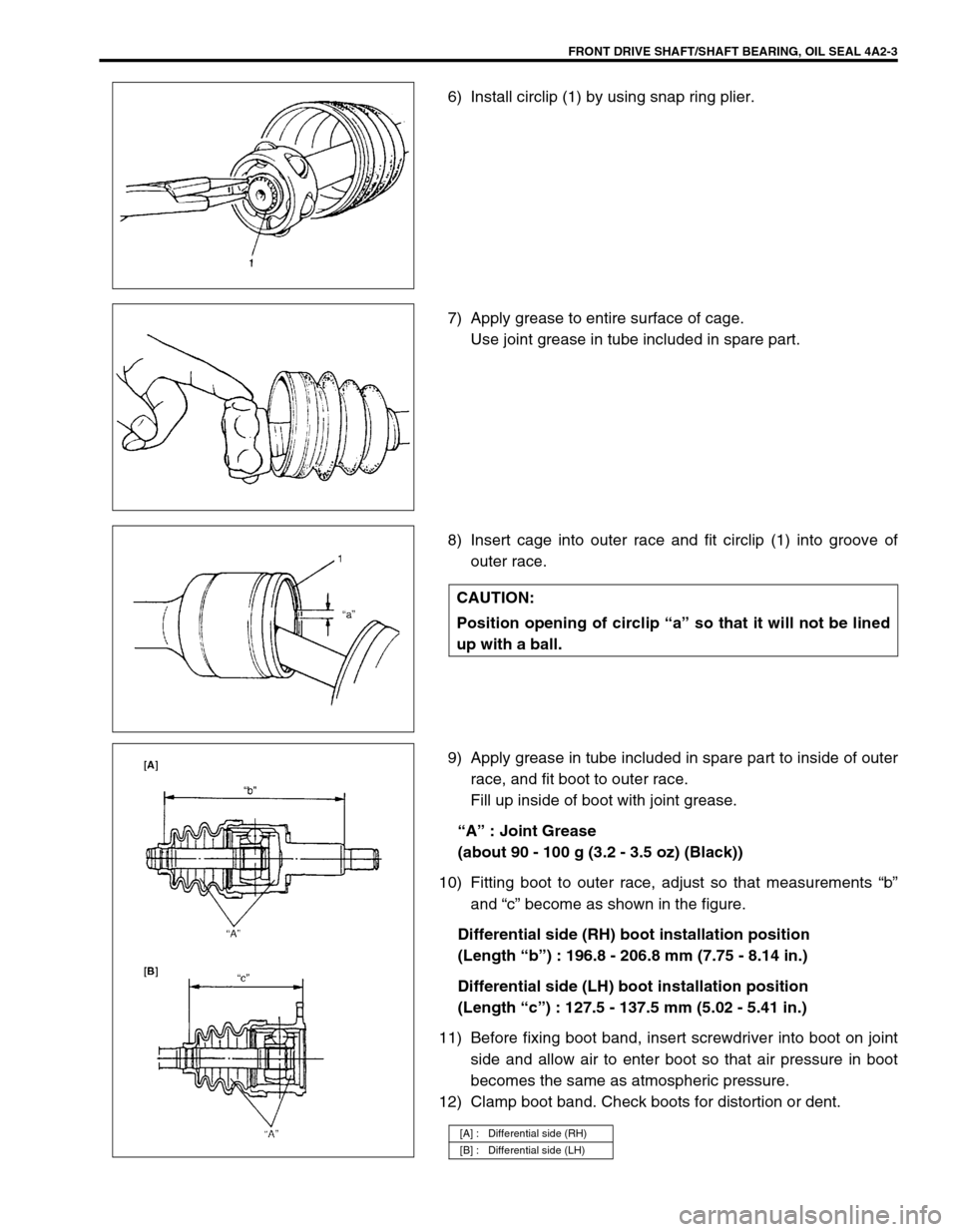
FRONT DRIVE SHAFT/SHAFT BEARING, OIL SEAL 4A2-3
6) Install circlip (1) by using snap ring plier.
7) Apply grease to entire surface of cage.
Use joint grease in tube included in spare part.
8) Insert cage into outer race and fit circlip (1) into groove of
outer race.
9) Apply grease in tube included in spare part to inside of outer
race, and fit boot to outer race.
Fill up inside of boot with joint grease.
“A” : Joint Grease
(about 90 - 100 g (3.2 - 3.5 oz) (Black))
10) Fitting boot to outer race, adjust so that measurements “b”
and “c” become as shown in the figure.
Differential side (RH) boot installation position
(Length “b”) : 196.8 - 206.8 mm (7.75 - 8.14 in.)
Differential side (LH) boot installation position
(Length “c”) : 127.5 - 137.5 mm (5.02 - 5.41 in.)
11) Before fixing boot band, insert screwdriver into boot on joint
side and allow air to enter boot so that air pressure in boot
becomes the same as atmospheric pressure.
12) Clamp boot band. Check boots for distortion or dent.
CAUTION:
Position opening of circlip “a” so that it will not be lined
up with a ball.
[A] : Differential side (RH)
[B] : Differential side (LH)
Page 103 of 656
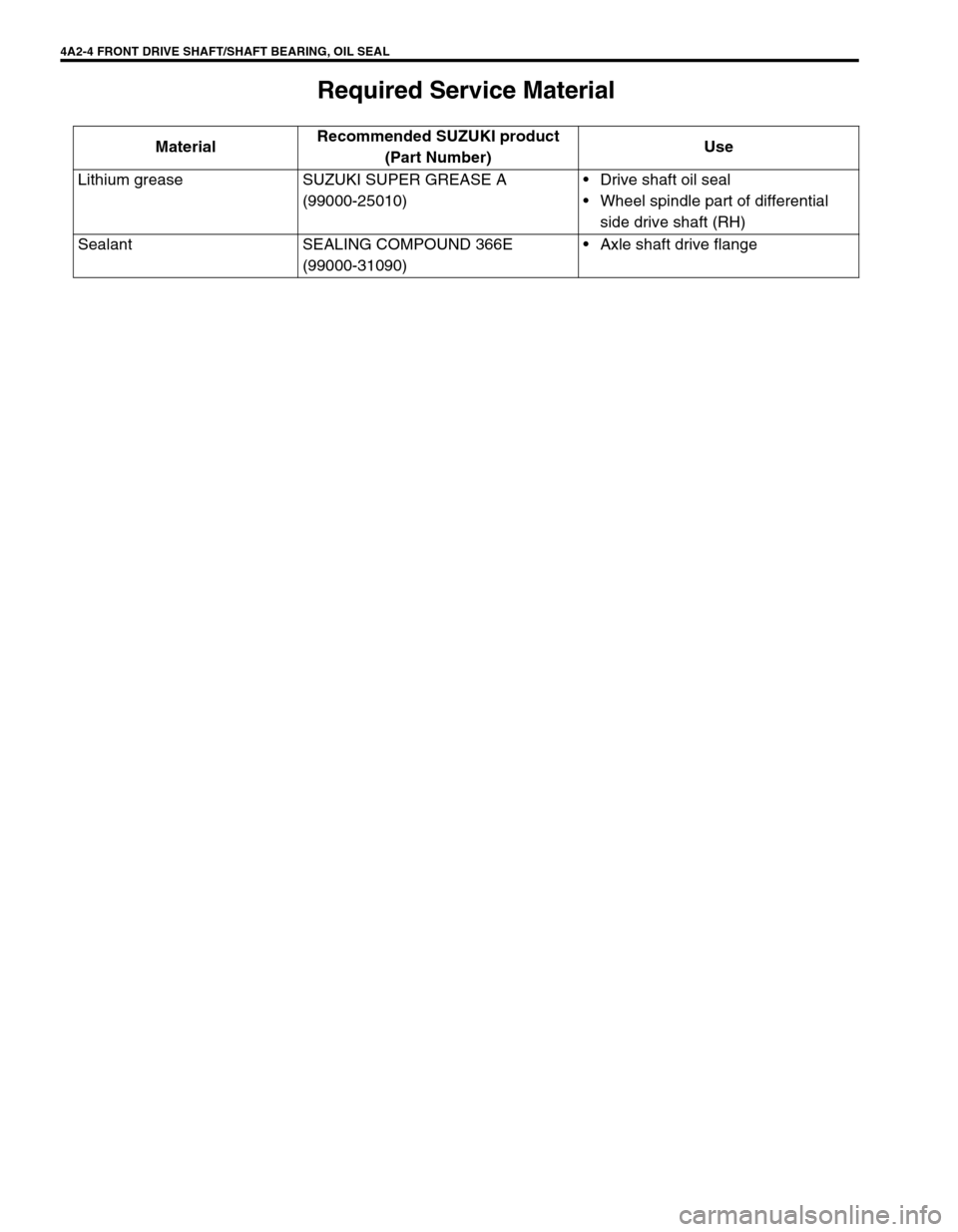
4A2-4 FRONT DRIVE SHAFT/SHAFT BEARING, OIL SEAL
Required Service Material
MaterialRecommended SUZUKI product
(Part Number)Use
Lithium grease SUZUKI SUPER GREASE A
(99000-25010)Drive shaft oil seal
Wheel spindle part of differential
side drive shaft (RH)
Sealant SEALING COMPOUND 366E
(99000-31090)Axle shaft drive flange
Page 104 of 656
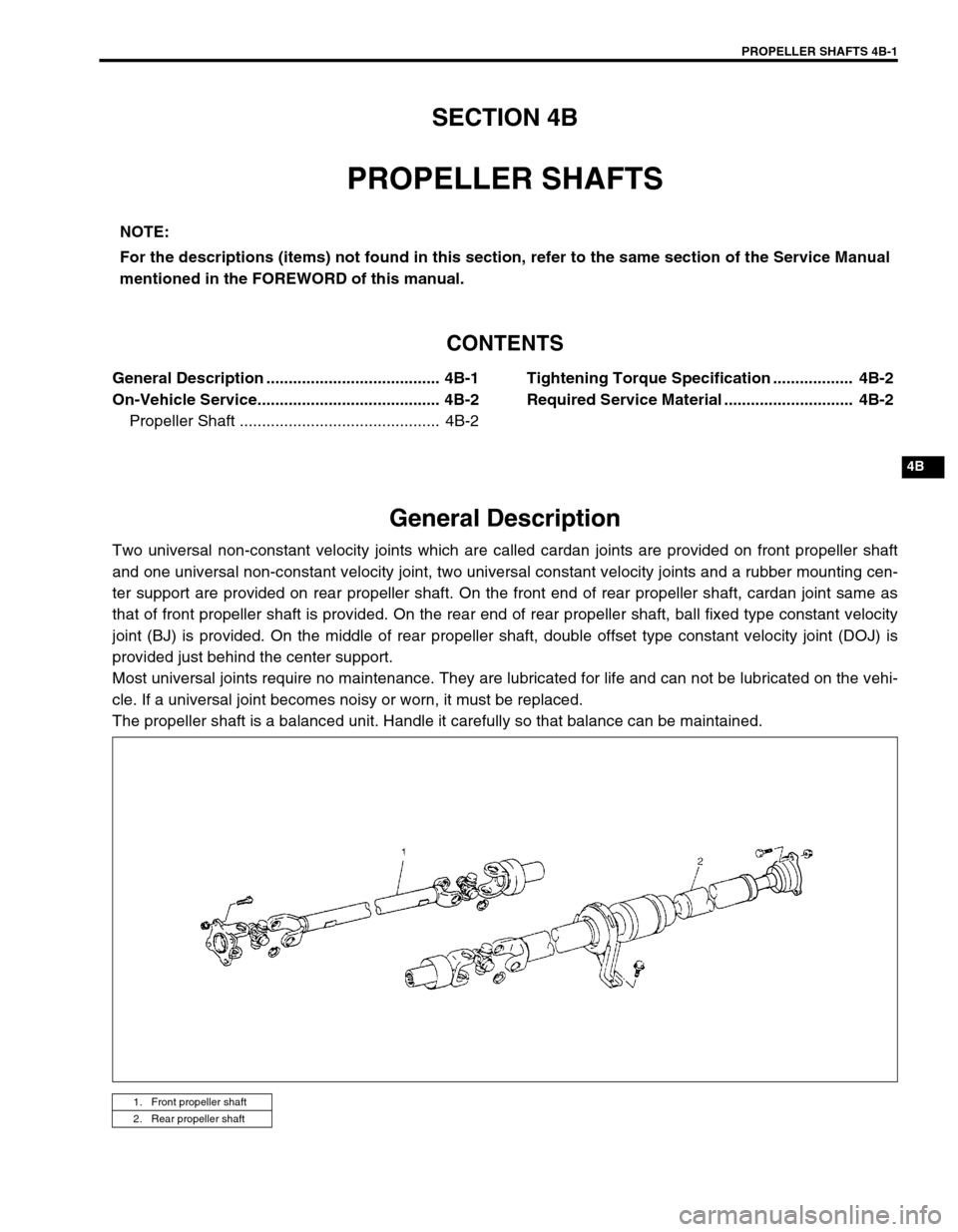
PROPELLER SHAFTS 4B-1
4B
SECTION 4B
PROPELLER SHAFTS
CONTENTS
General Description ....................................... 4B-1
On-Vehicle Service......................................... 4B-2
Propeller Shaft ............................................. 4B-2Tightening Torque Specification .................. 4B-2
Required Service Material ............................. 4B-2
General Description
Two universal non-constant velocity joints which are called cardan joints are provided on front propeller shaft
and one universal non-constant velocity joint, two universal constant velocity joints and a rubber mounting cen-
ter support are provided on rear propeller shaft. On the front end of rear propeller shaft, cardan joint same as
that of front propeller shaft is provided. On the rear end of rear propeller shaft, ball fixed type constant velocity
joint (BJ) is provided. On the middle of rear propeller shaft, double offset type constant velocity joint (DOJ) is
provided just behind the center support.
Most universal joints require no maintenance. They are lubricated for life and can not be lubricated on the vehi-
cle. If a universal joint becomes noisy or worn, it must be replaced.
The propeller shaft is a balanced unit. Handle it carefully so that balance can be maintained.NOTE:
For the descriptions (items) not found in this section, refer to the same section of the Service Manual
mentioned in the FOREWORD of this manual.
1. Front propeller shaft
2. Rear propeller shaft
Page 105 of 656
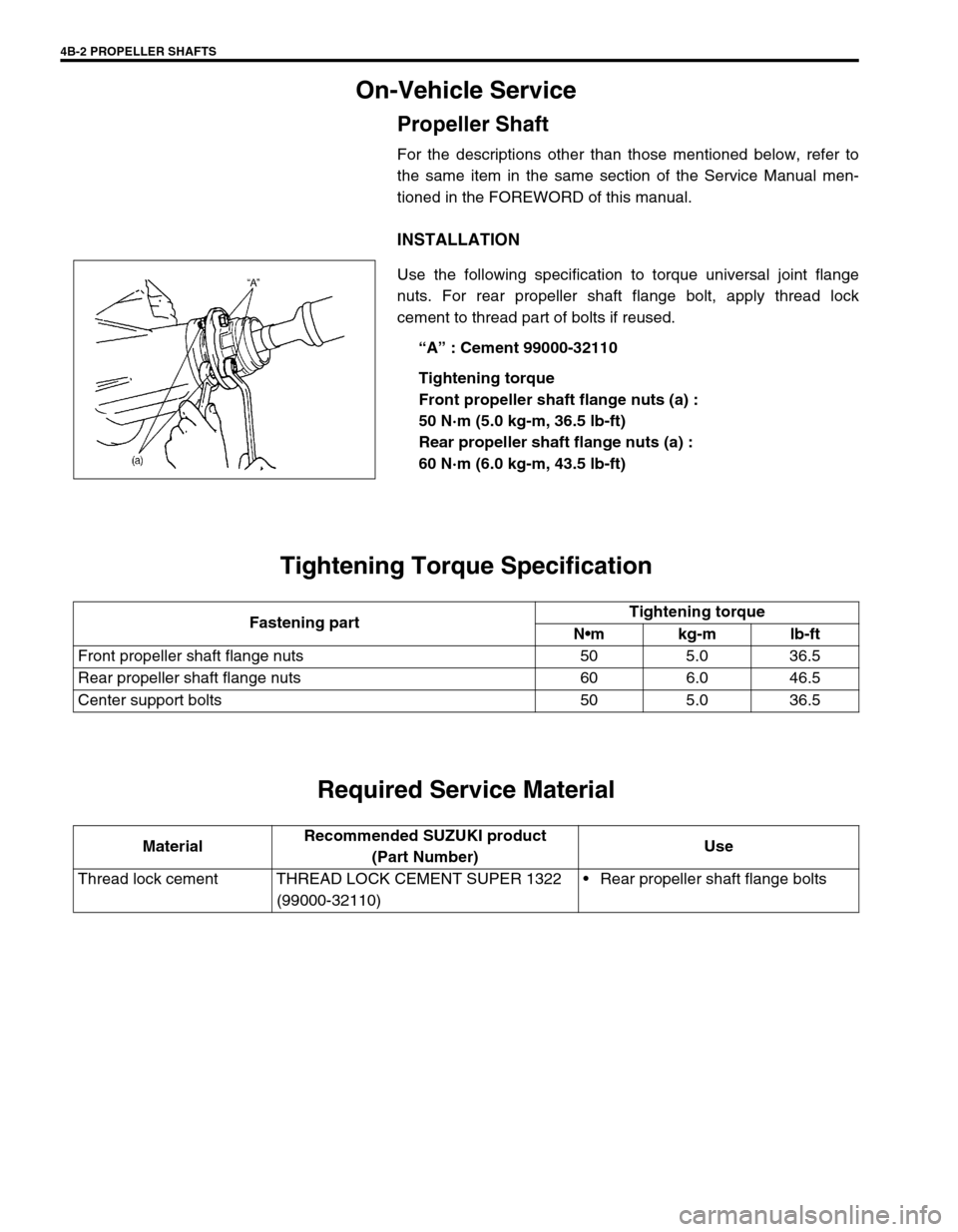
4B-2 PROPELLER SHAFTS
On-Vehicle Service
Propeller Shaft
For the descriptions other than those mentioned below, refer to
the same item in the same section of the Service Manual men-
tioned in the FOREWORD of this manual.
INSTALLATION
Use the following specification to torque universal joint flange
nuts. For rear propeller shaft flange bolt, apply thread lock
cement to thread part of bolts if reused.
“A” : Cement 99000-32110
Tightening torque
Front propeller shaft flange nuts (a) :
50 N·m (5.0 kg-m, 36.5 lb-ft)
Rear propeller shaft flange nuts (a) :
60 N·m (6.0 kg-m, 43.5 lb-ft)
Tightening Torque Specification
Required Service Material
Fastening partTightening torque
Nm kg-m lb-ft
Front propeller shaft flange nuts 50 5.0 36.5
Rear propeller shaft flange nuts 60 6.0 46.5
Center support bolts 50 5.0 36.5
MaterialRecommended SUZUKI product
(Part Number)Use
Thread lock cement THREAD LOCK CEMENT SUPER 1322
(99000-32110)Rear propeller shaft flange bolts
Page 106 of 656
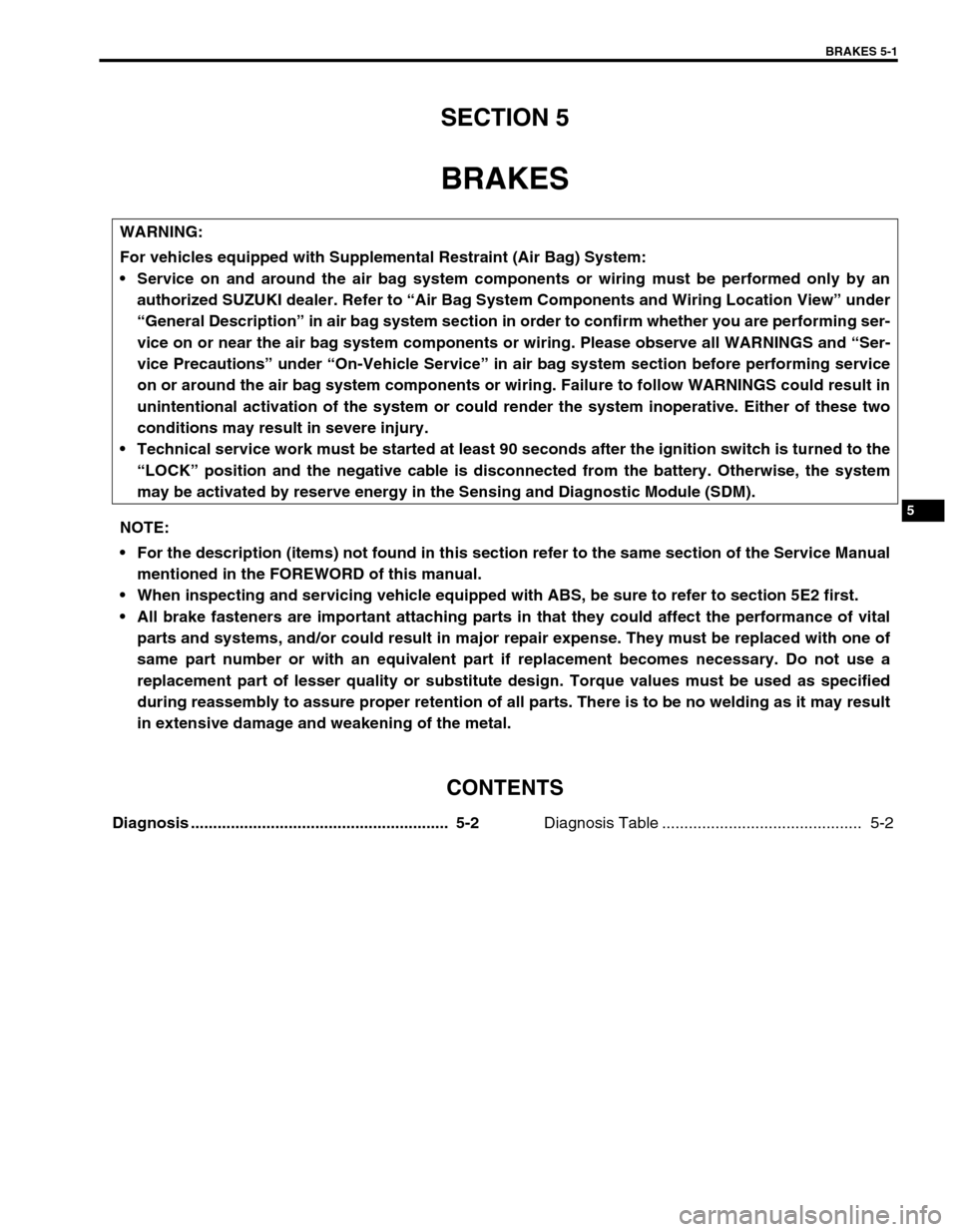
BRAKES 5-1
5
SECTION 5
BRAKES
CONTENTS
Diagnosis .......................................................... 5-2
Diagnosis Table ............................................. 5-2
WARNING:
For vehicles equipped with Supplemental Restraint (Air Bag) System:
Service on and around the air bag system components or wiring must be performed only by an
authorized SUZUKI dealer. Refer to “Air Bag System Components and Wiring Location View” under
“General Description” in air bag system section in order to confirm whether you are performing ser-
vice on or near the air bag system components or wiring. Please observe all WARNINGS and “Ser-
vice Precautions” under “On-Vehicle Service” in air bag system section before performing service
on or around the air bag system components or wiring. Failure to follow WARNINGS could result in
unintentional activation of the system or could render the system inoperative. Either of these two
conditions may result in severe injury.
Technical service work must be started at least 90 seconds after the ignition switch is turned to the
“LOCK” position and the negative cable is disconnected from the battery. Otherwise, the system
may be activated by reserve energy in the Sensing and Diagnostic Module (SDM).
NOTE:
For the description (items) not found in this section refer to the same section of the Service Manual
mentioned in the FOREWORD of this manual.
When inspecting and servicing vehicle equipped with ABS, be sure to refer to section 5E2 first.
All brake fasteners are important attaching parts in that they could affect the performance of vital
parts and systems, and/or could result in major repair expense. They must be replaced with one of
same part number or with an equivalent part if replacement becomes necessary. Do not use a
replacement part of lesser quality or substitute design. Torque values must be used as specified
during reassembly to assure proper retention of all parts. There is to be no welding as it may result
in extensive damage and weakening of the metal.
Page 107 of 656
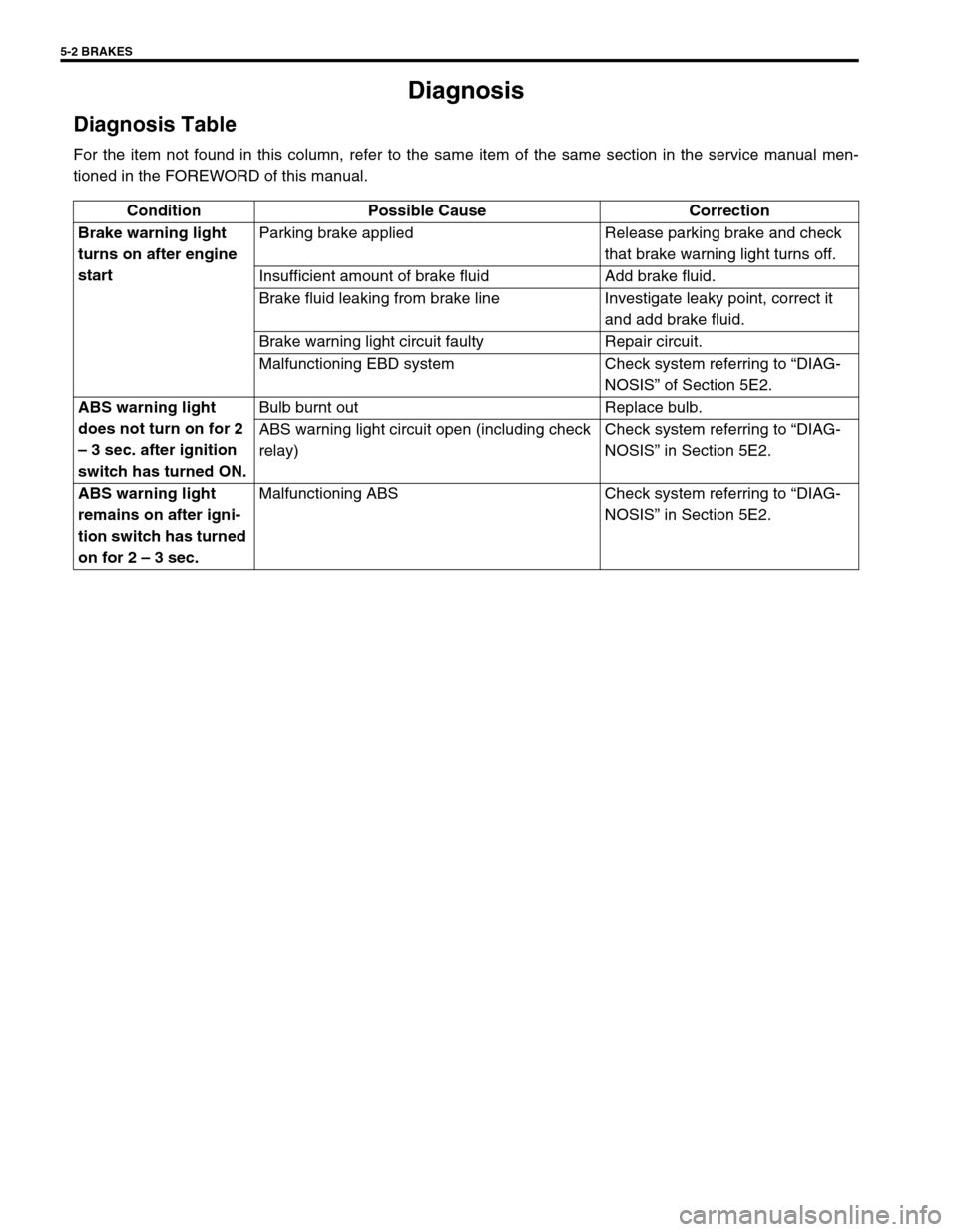
5-2 BRAKES
Diagnosis
Diagnosis Table
For the item not found in this column, refer to the same item of the same section in the service manual men-
tioned in the FOREWORD of this manual.
Condition Possible Cause Correction
Brake warning light
turns on after engine
startParking brake applied Release parking brake and check
that brake warning light turns off.
Insufficient amount of brake fluid Add brake fluid.
Brake fluid leaking from brake line Investigate leaky point, correct it
and add brake fluid.
Brake warning light circuit faulty Repair circuit.
Malfunctioning EBD system Check system referring to “DIAG-
NOSIS” of Section 5E2.
ABS warning light
does not turn on for 2
– 3 sec. after ignition
switch has turned ON.Bulb burnt out Replace bulb.
ABS warning light circuit open (including check
relay)Check system referring to “DIAG-
NOSIS” in Section 5E2.
ABS warning light
remains on after igni-
tion switch has turned
on for 2 – 3 sec.Malfunctioning ABS Check system referring to “DIAG-
NOSIS” in Section 5E2.
Page 108 of 656
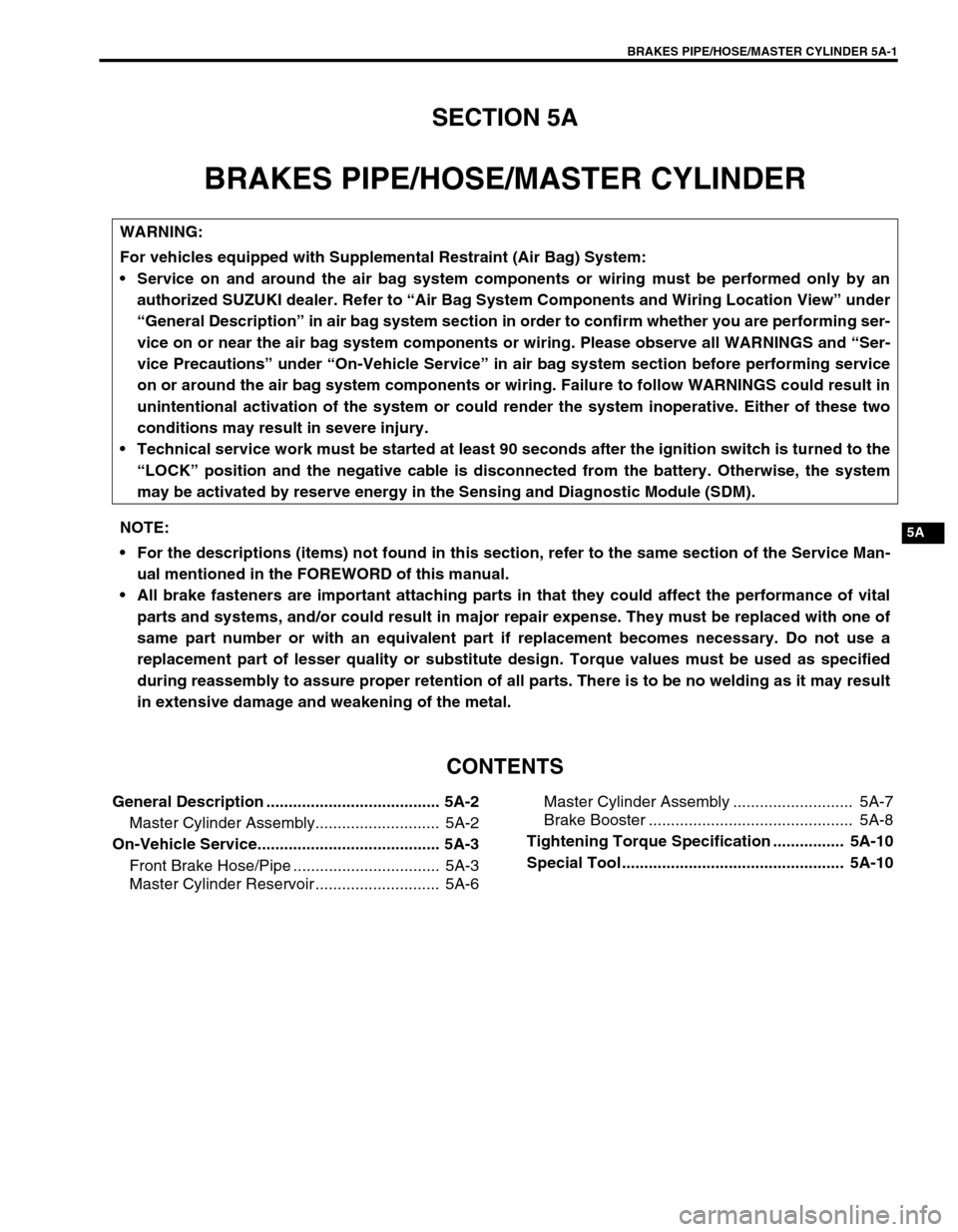
BRAKES PIPE/HOSE/MASTER CYLINDER 5A-1
5A
SECTION 5A
BRAKES PIPE/HOSE/MASTER CYLINDER
CONTENTS
General Description ....................................... 5A-2
Master Cylinder Assembly............................ 5A-2
On-Vehicle Service......................................... 5A-3
Front Brake Hose/Pipe ................................. 5A-3
Master Cylinder Reservoir ............................ 5A-6Master Cylinder Assembly ........................... 5A-7
Brake Booster .............................................. 5A-8
Tightening Torque Specification ................ 5A-10
Special Tool .................................................. 5A-10
WARNING:
For vehicles equipped with Supplemental Restraint (Air Bag) System:
Service on and around the air bag system components or wiring must be performed only by an
authorized SUZUKI dealer. Refer to “Air Bag System Components and Wiring Location View” under
“General Description” in air bag system section in order to confirm whether you are performing ser-
vice on or near the air bag system components or wiring. Please observe all WARNINGS and “Ser-
vice Precautions” under “On-Vehicle Service” in air bag system section before performing service
on or around the air bag system components or wiring. Failure to follow WARNINGS could result in
unintentional activation of the system or could render the system inoperative. Either of these two
conditions may result in severe injury.
Technical service work must be started at least 90 seconds after the ignition switch is turned to the
“LOCK” position and the negative cable is disconnected from the battery. Otherwise, the system
may be activated by reserve energy in the Sensing and Diagnostic Module (SDM).
NOTE:
For the descriptions (items) not found in this section, refer to the same section of the Service Man-
ual mentioned in the FOREWORD of this manual.
All brake fasteners are important attaching parts in that they could affect the performance of vital
parts and systems, and/or could result in major repair expense. They must be replaced with one of
same part number or with an equivalent part if replacement becomes necessary. Do not use a
replacement part of lesser quality or substitute design. Torque values must be used as specified
during reassembly to assure proper retention of all parts. There is to be no welding as it may result
in extensive damage and weakening of the metal.
Page 109 of 656
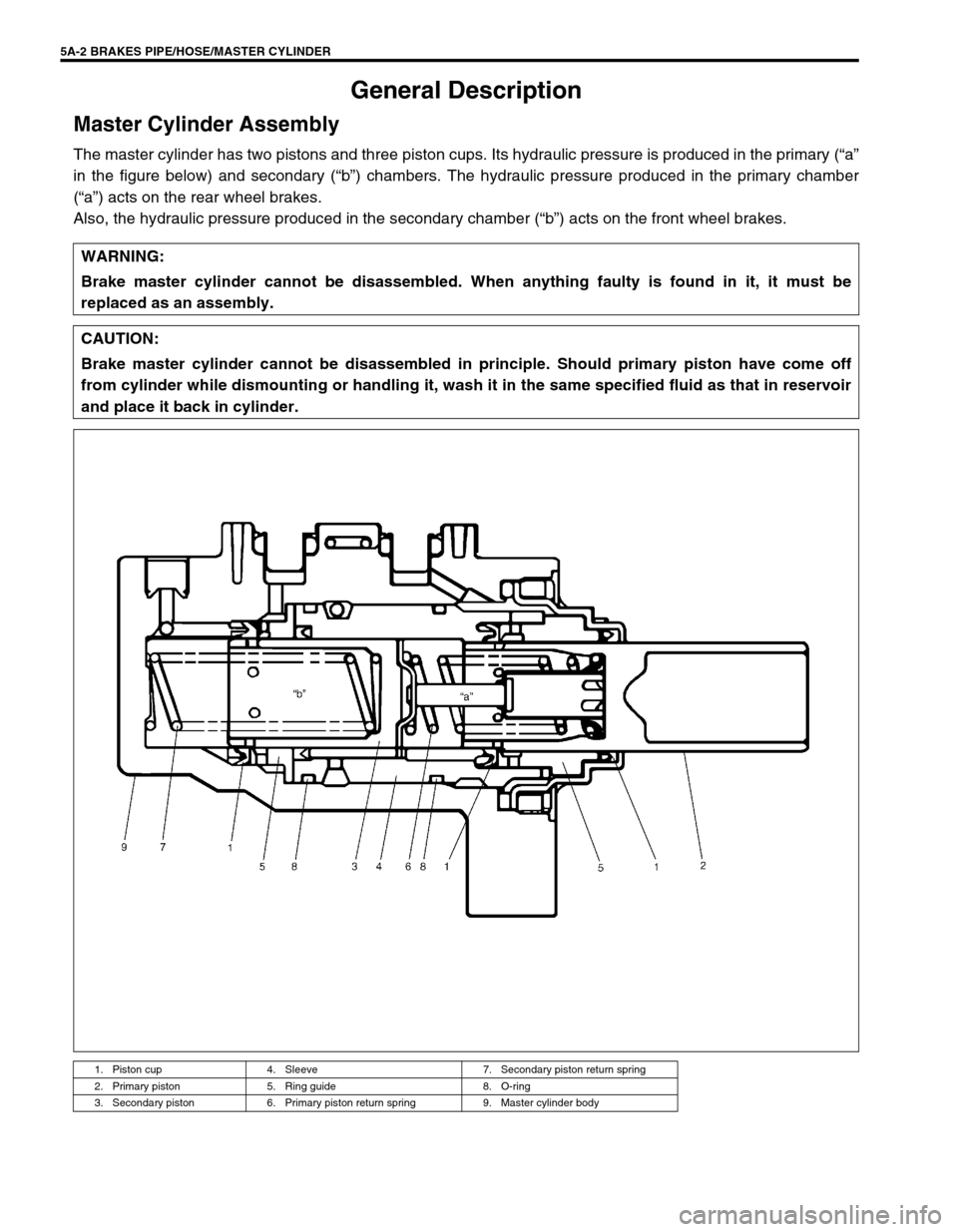
5A-2 BRAKES PIPE/HOSE/MASTER CYLINDER
General Description
Master Cylinder Assembly
The master cylinder has two pistons and three piston cups. Its hydraulic pressure is produced in the primary (“a”
in the figure below) and secondary (“b”) chambers. The hydraulic pressure produced in the primary chamber
(“a”) acts on the rear wheel brakes.
Also, the hydraulic pressure produced in the secondary chamber (“b”) acts on the front wheel brakes.
WARNING:
Brake master cylinder cannot be disassembled. When anything faulty is found in it, it must be
replaced as an assembly.
CAUTION:
Brake master cylinder cannot be disassembled in principle. Should primary piston have come off
from cylinder while dismounting or handling it, wash it in the same specified fluid as that in reservoir
and place it back in cylinder.
1. Piston cup 4. Sleeve 7. Secondary piston return spring
2. Primary piston 5. Ring guide 8. O-ring
3. Secondary piston 6. Primary piston return spring 9. Master cylinder body
Page 110 of 656
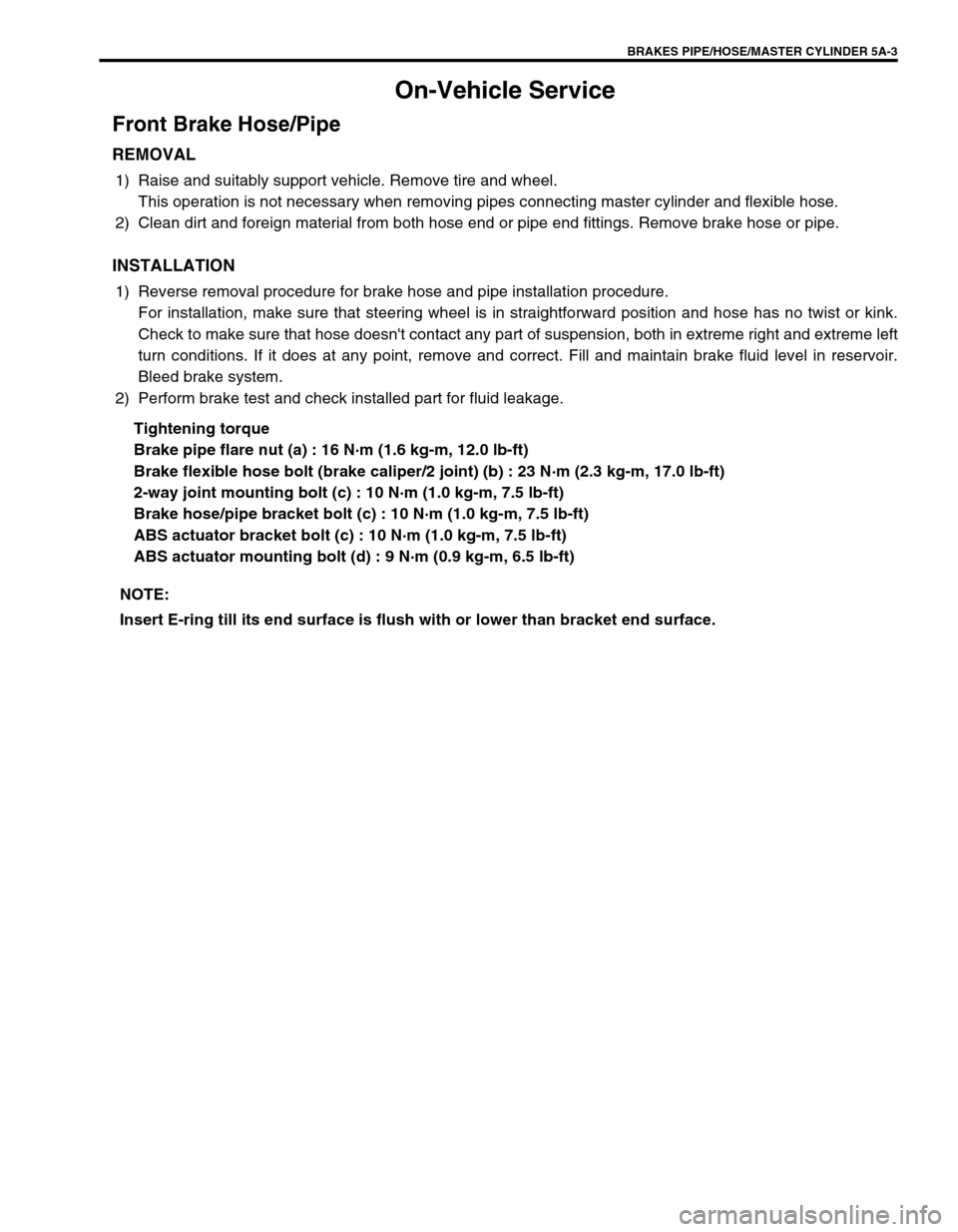
BRAKES PIPE/HOSE/MASTER CYLINDER 5A-3
On-Vehicle Service
Front Brake Hose/Pipe
REMOVAL
1) Raise and suitably support vehicle. Remove tire and wheel.
This operation is not necessary when removing pipes connecting master cylinder and flexible hose.
2) Clean dirt and foreign material from both hose end or pipe end fittings. Remove brake hose or pipe.
INSTALLATION
1) Reverse removal procedure for brake hose and pipe installation procedure.
For installation, make sure that steering wheel is in straightforward position and hose has no twist or kink.
Check to make sure that hose doesn't contact any part of suspension, both in extreme right and extreme left
turn conditions. If it does at any point, remove and correct. Fill and maintain brake fluid level in reservoir.
Bleed brake system.
2) Perform brake test and check installed part for fluid leakage.
Tightening torque
Brake pipe flare nut (a) : 16 N·m (1.6 kg-m, 12.0 lb-ft)
Brake flexible hose bolt (brake caliper/2 joint) (b) : 23 N·m (2.3 kg-m, 17.0 lb-ft)
2-way joint mounting bolt (c) : 10 N·m (1.0 kg-m, 7.5 lb-ft)
Brake hose/pipe bracket bolt (c) : 10 N·m (1.0 kg-m, 7.5 lb-ft)
ABS actuator bracket bolt (c) : 10 N·m (1.0 kg-m, 7.5 lb-ft)
ABS actuator mounting bolt (d) : 9 N·m (0.9 kg-m, 6.5 lb-ft)
NOTE:
Insert E-ring till its end surface is flush with or lower than bracket end surface.