SUZUKI GRAND VITARA 1999 2.G Owners Manual
Manufacturer: SUZUKI, Model Year: 1999, Model line: GRAND VITARA, Model: SUZUKI GRAND VITARA 1999 2.GPages: 656, PDF Size: 14.31 MB
Page 451 of 656
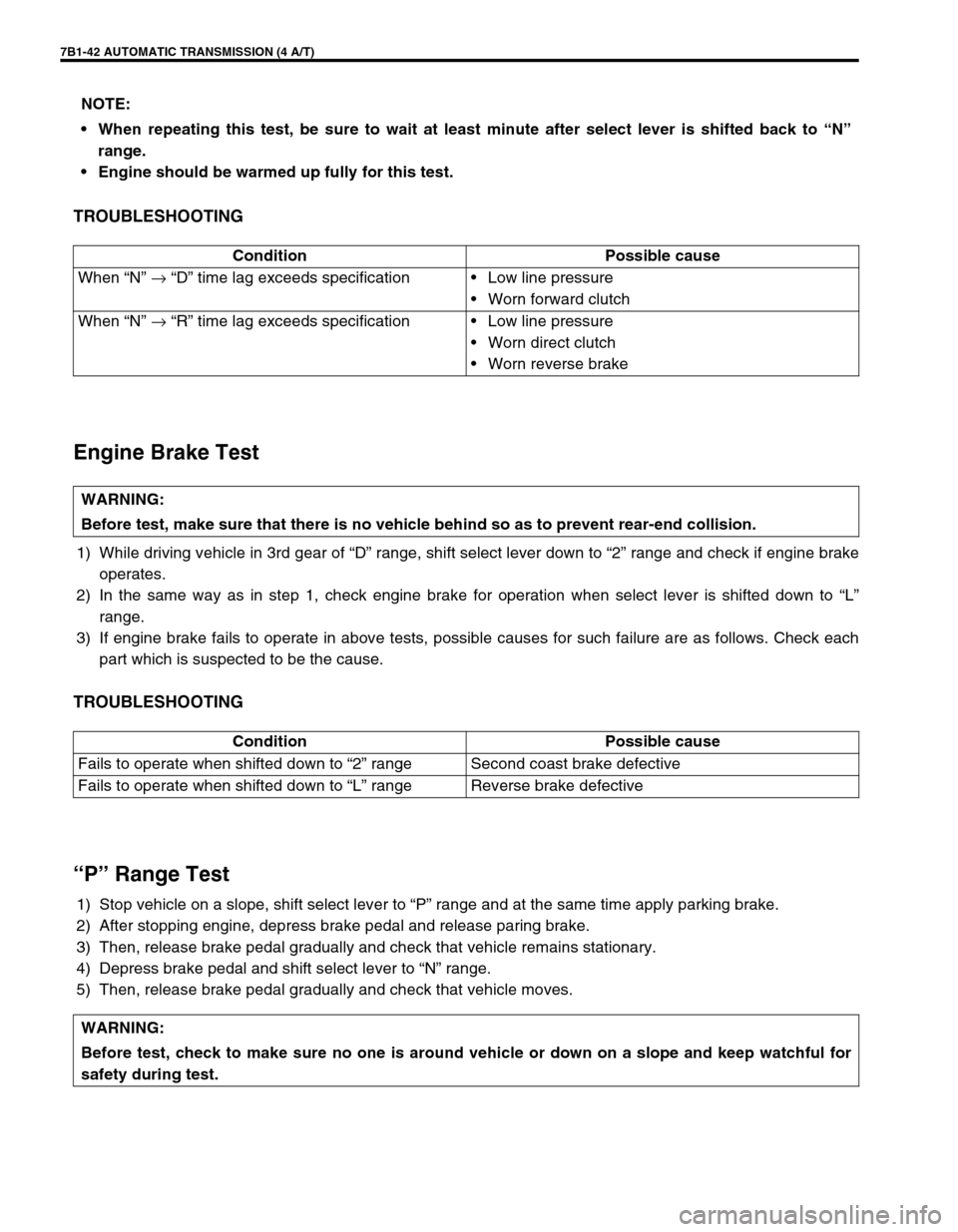
7B1-42 AUTOMATIC TRANSMISSION (4 A/T)
TROUBLESHOOTING
Engine Brake Test
1) While driving vehicle in 3rd gear of “D” range, shift select lever down to “2” range and check if engine brake
operates.
2) In the same way as in step 1, check engine brake for operation when select lever is shifted down to “L”
range.
3) If engine brake fails to operate in above tests, possible causes for such failure are as follows. Check each
part which is suspected to be the cause.
TROUBLESHOOTING
“P” Range Test
1) Stop vehicle on a slope, shift select lever to “P” range and at the same time apply parking brake.
2) After stopping engine, depress brake pedal and release paring brake.
3) Then, release brake pedal gradually and check that vehicle remains stationary.
4) Depress brake pedal and shift select lever to “N” range.
5) Then, release brake pedal gradually and check that vehicle moves.NOTE:
When repeating this test, be sure to wait at least minute after select lever is shifted back to “N”
range.
Engine should be warmed up fully for this test.
Condition Possible cause
When “N” → “D” time lag exceeds specification•Low line pressure
•Worn forward clutch
When “N” → “R” time lag exceeds specification•Low line pressure
•Worn direct clutch
•Worn reverse brake
WARNING:
Before test, make sure that there is no vehicle behind so as to prevent rear-end collision.
Condition Possible cause
Fails to operate when shifted down to “2” range Second coast brake defective
Fails to operate when shifted down to “L” range Reverse brake defective
WARNING:
Before test, check to make sure no one is around vehicle or down on a slope and keep watchful for
safety during test.
Page 452 of 656
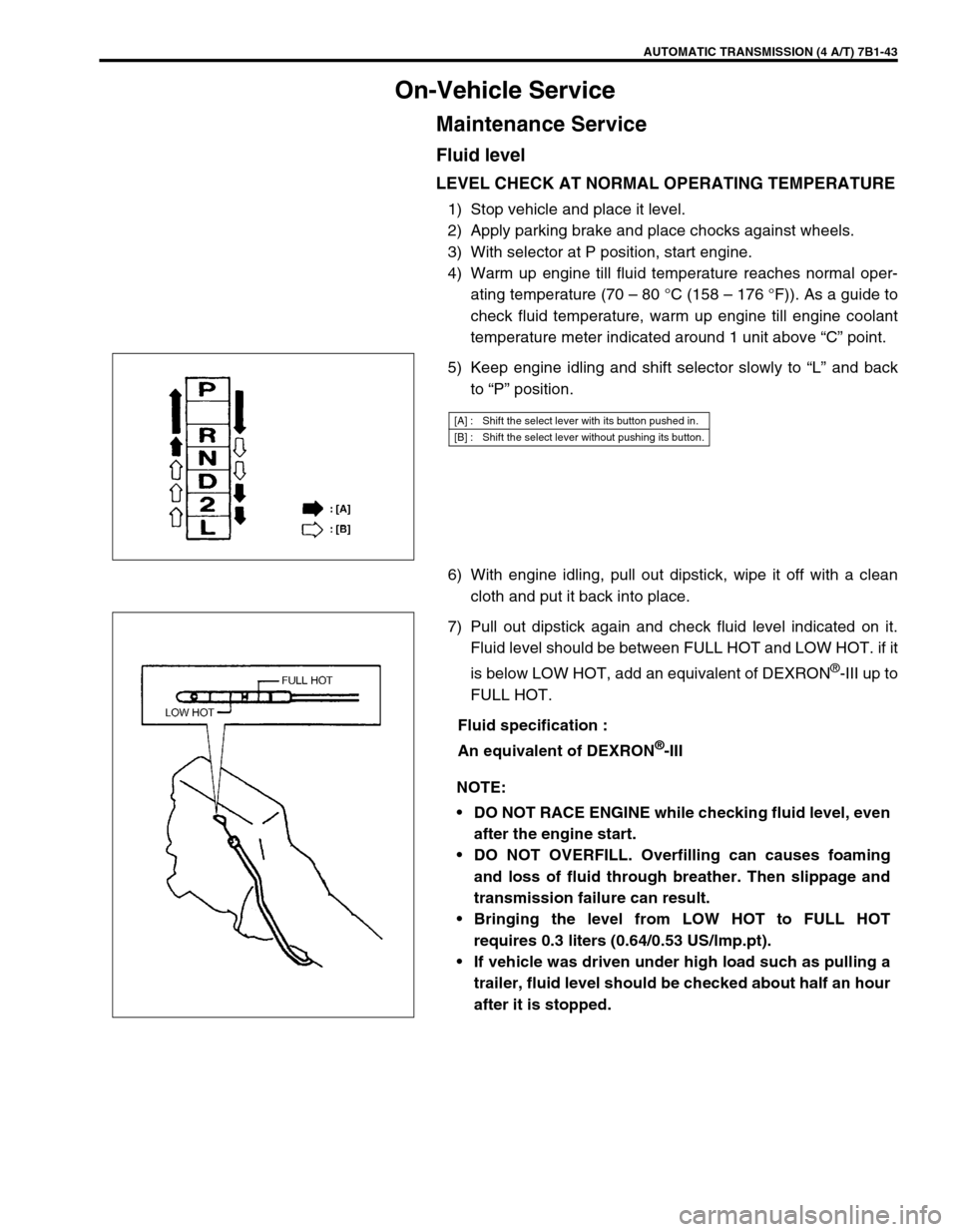
AUTOMATIC TRANSMISSION (4 A/T) 7B1-43
On-Vehicle Service
Maintenance Service
Fluid level
LEVEL CHECK AT NORMAL OPERATING TEMPERATURE
1) Stop vehicle and place it level.
2) Apply parking brake and place chocks against wheels.
3) With selector at P position, start engine.
4) Warm up engine till fluid temperature reaches normal oper-
ating temperature (70 – 80 °C (158 – 176 °F)). As a guide to
check fluid temperature, warm up engine till engine coolant
temperature meter indicated around 1 unit above “C” point.
5) Keep engine idling and shift selector slowly to “L” and back
to “P” position.
6) With engine idling, pull out dipstick, wipe it off with a clean
cloth and put it back into place.
7) Pull out dipstick again and check fluid level indicated on it.
Fluid level should be between FULL HOT and LOW HOT. if it
is below LOW HOT, add an equivalent of DEXRON
®-III up to
FULL HOT.
Fluid specification :
An equivalent of DEXRON
®-III
[A] : Shift the select lever with its button pushed in.
[B] : Shift the select lever without pushing its button.
NOTE:
DO NOT RACE ENGINE while checking fluid level, even
after the engine start.
DO NOT OVERFILL. Overfilling can causes foaming
and loss of fluid through breather. Then slippage and
transmission failure can result.
Bringing the level from LOW HOT to FULL HOT
requires 0.3 liters (0.64/0.53 US/lmp.pt).
If vehicle was driven under high load such as pulling a
trailer, fluid level should be checked about half an hour
after it is stopped.
Page 453 of 656
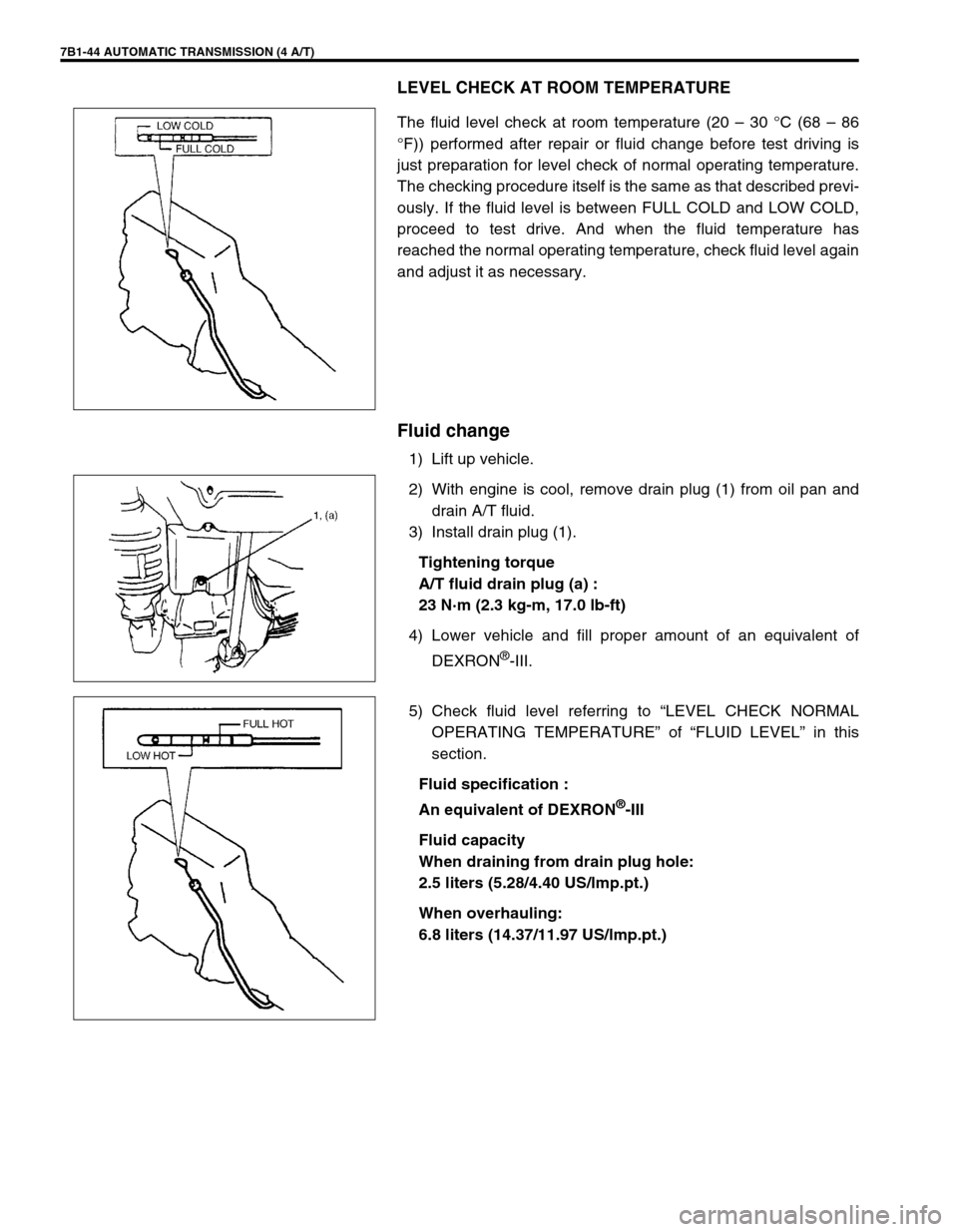
7B1-44 AUTOMATIC TRANSMISSION (4 A/T)
LEVEL CHECK AT ROOM TEMPERATURE
The fluid level check at room temperature (20 – 30 °C (68 – 86
°F)) performed after repair or fluid change before test driving is
just preparation for level check of normal operating temperature.
The checking procedure itself is the same as that described previ-
ously. If the fluid level is between FULL COLD and LOW COLD,
proceed to test drive. And when the fluid temperature has
reached the normal operating temperature, check fluid level again
and adjust it as necessary.
Fluid change
1) Lift up vehicle.
2) With engine is cool, remove drain plug (1) from oil pan and
drain A/T fluid.
3) Install drain plug (1).
Tightening torque
A/T fluid drain plug (a) :
23 N·m (2.3 kg-m, 17.0 lb-ft)
4) Lower vehicle and fill proper amount of an equivalent of
DEXRON
®-III.
5) Check fluid level referring to “LEVEL CHECK NORMAL
OPERATING TEMPERATURE” of “FLUID LEVEL” in this
section.
Fluid specification :
An equivalent of DEXRON
®-III
Fluid capacity
When draining from drain plug hole:
2.5 liters (5.28/4.40 US/lmp.pt.)
When overhauling:
6.8 liters (14.37/11.97 US/lmp.pt.)
Page 454 of 656
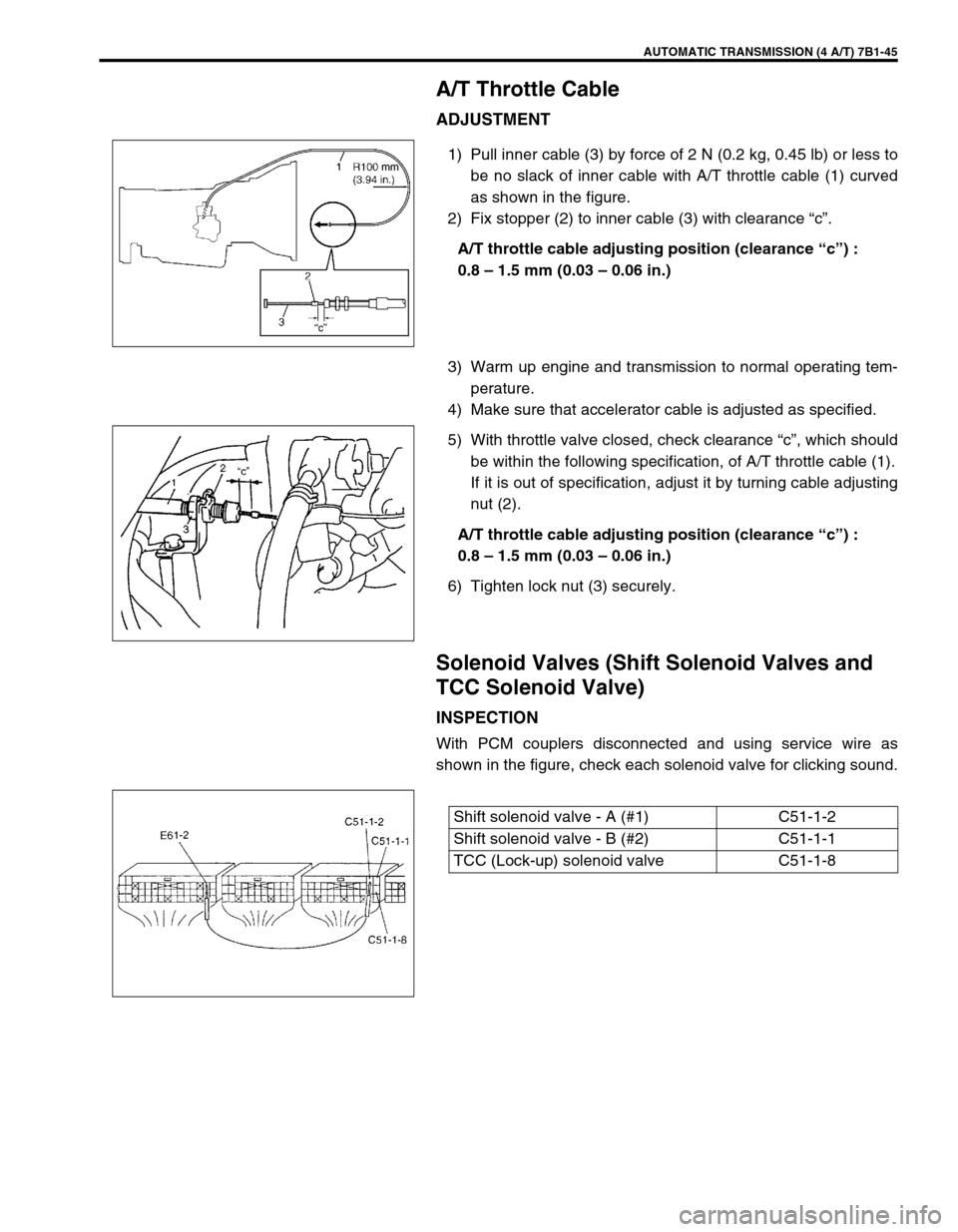
AUTOMATIC TRANSMISSION (4 A/T) 7B1-45
A/T Throttle Cable
ADJUSTMENT
1) Pull inner cable (3) by force of 2 N (0.2 kg, 0.45 lb) or less to
be no slack of inner cable with A/T throttle cable (1) curved
as shown in the figure.
2) Fix stopper (2) to inner cable (3) with clearance “c”.
A/T throttle cable adjusting position (clearance “c”) :
0.8 – 1.5 mm (0.03 – 0.06 in.)
3) Warm up engine and transmission to normal operating tem-
perature.
4) Make sure that accelerator cable is adjusted as specified.
5) With throttle valve closed, check clearance “c”, which should
be within the following specification, of A/T throttle cable (1).
If it is out of specification, adjust it by turning cable adjusting
nut (2).
A/T throttle cable adjusting position (clearance “c”) :
0.8 – 1.5 mm (0.03 – 0.06 in.)
6) Tighten lock nut (3) securely.
Solenoid Valves (Shift Solenoid Valves and
TCC Solenoid Valve)
INSPECTION
With PCM couplers disconnected and using service wire as
shown in the figure, check each solenoid valve for clicking sound.
Shift solenoid valve - A (#1) C51-1-2
Shift solenoid valve - B (#2) C51-1-1
TCC (Lock-up) solenoid valve C51-1-8
Page 455 of 656
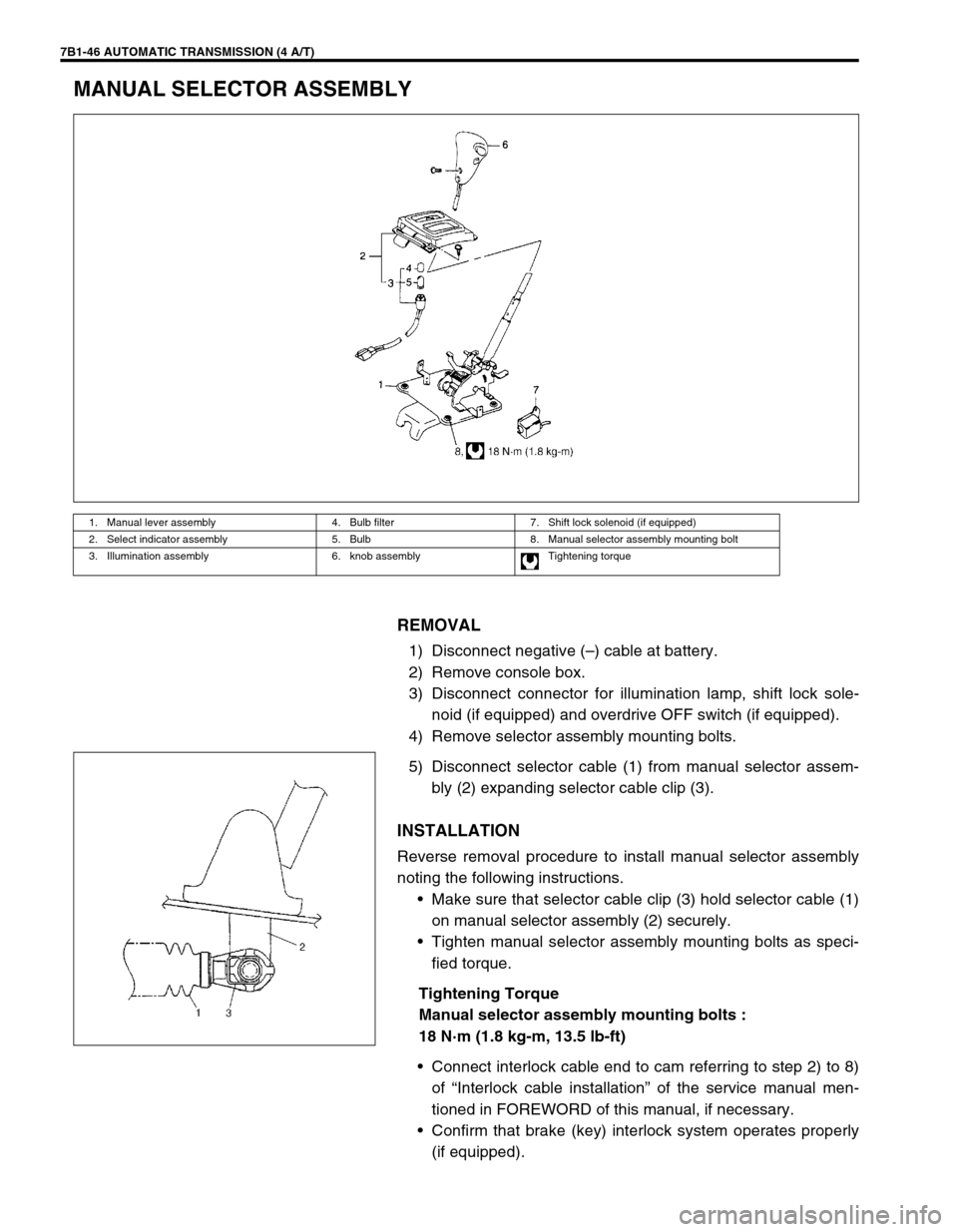
7B1-46 AUTOMATIC TRANSMISSION (4 A/T)
MANUAL SELECTOR ASSEMBLY
REMOVAL
1) Disconnect negative (–) cable at battery.
2) Remove console box.
3) Disconnect connector for illumination lamp, shift lock sole-
noid (if equipped) and overdrive OFF switch (if equipped).
4) Remove selector assembly mounting bolts.
5) Disconnect selector cable (1) from manual selector assem-
bly (2) expanding selector cable clip (3).
INSTALLATION
Reverse removal procedure to install manual selector assembly
noting the following instructions.
•Make sure that selector cable clip (3) hold selector cable (1)
on manual selector assembly (2) securely.
•Tighten manual selector assembly mounting bolts as speci-
fied torque.
Tightening Torque
Manual selector assembly mounting bolts :
18 N·m (1.8 kg-m, 13.5 lb-ft)
•Connect interlock cable end to cam referring to step 2) to 8)
of “Interlock cable installation” of the service manual men-
tioned in FOREWORD of this manual, if necessary.
•Confirm that brake (key) interlock system operates properly
(if equipped).
1. Manual lever assembly 4. Bulb filter 7. Shift lock solenoid (if equipped)
2. Select indicator assembly 5. Bulb 8. Manual selector assembly mounting bolt
3. Illumination assembly 6. knob assembly Tightening torque
Page 456 of 656
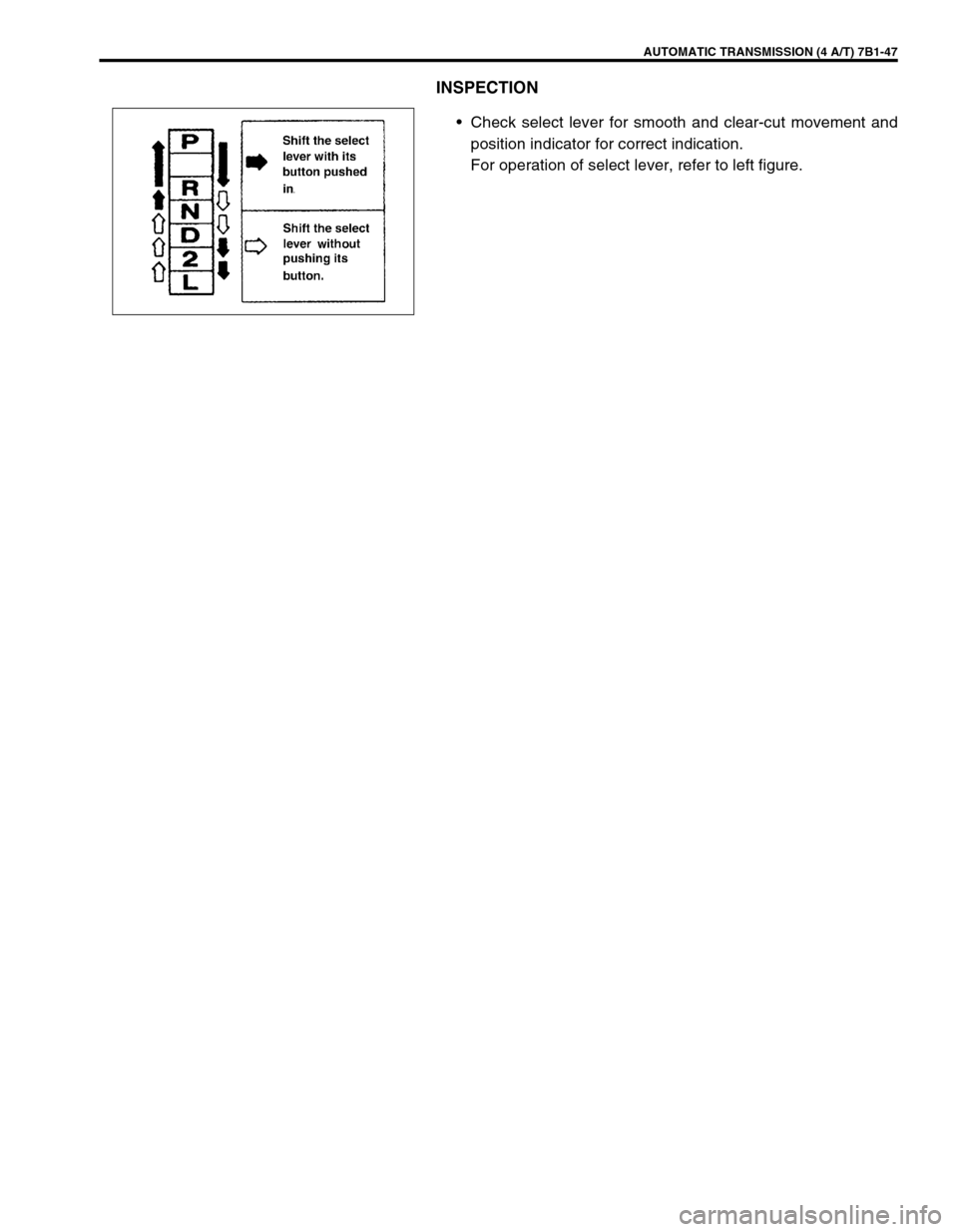
AUTOMATIC TRANSMISSION (4 A/T) 7B1-47
INSPECTION
•Check select lever for smooth and clear-cut movement and
position indicator for correct indication.
For operation of select lever, refer to left figure.
Page 457 of 656
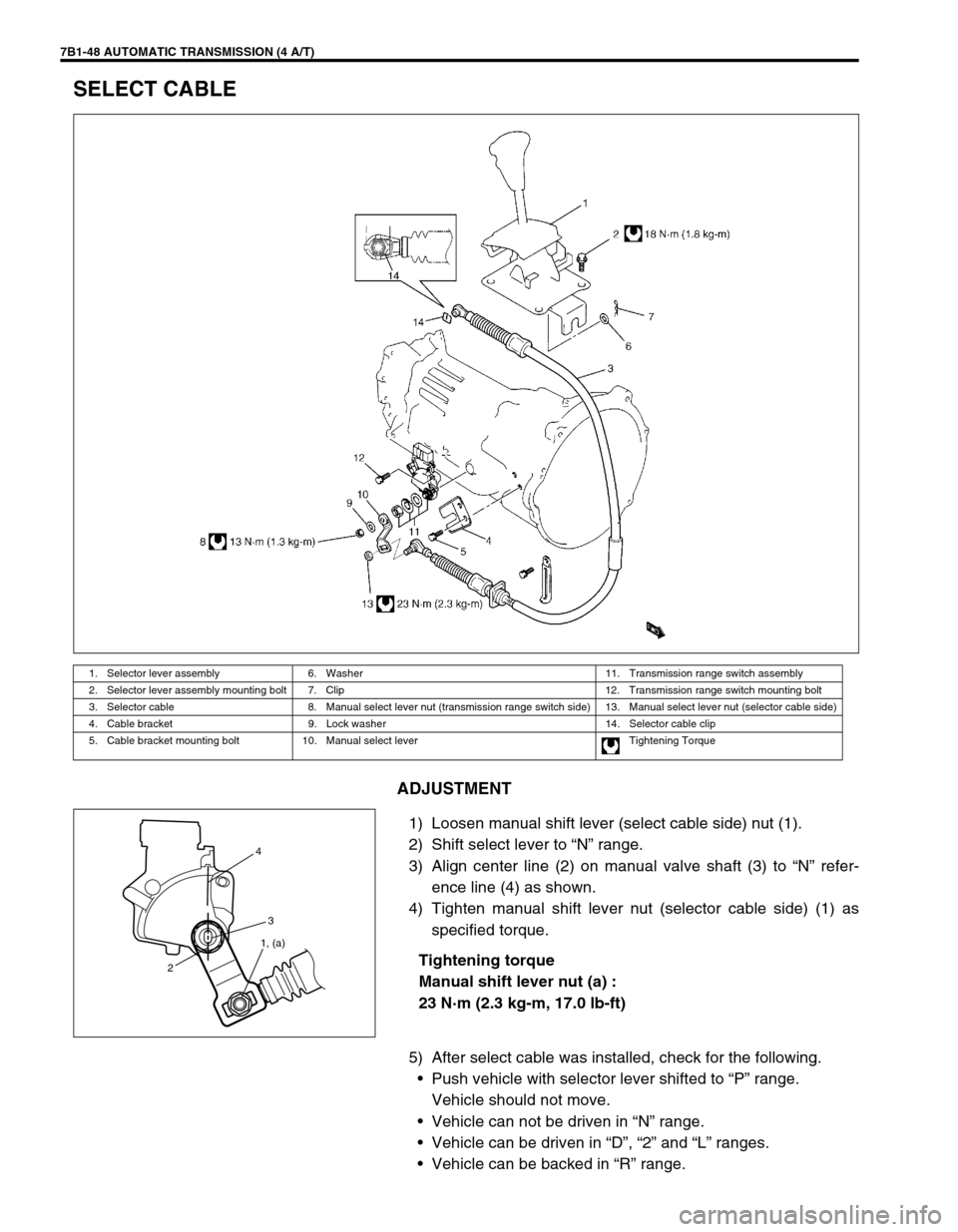
7B1-48 AUTOMATIC TRANSMISSION (4 A/T)
SELECT CABLE
ADJUSTMENT
1) Loosen manual shift lever (select cable side) nut (1).
2) Shift select lever to “N” range.
3) Align center line (2) on manual valve shaft (3) to “N” refer-
ence line (4) as shown.
4) Tighten manual shift lever nut (selector cable side) (1) as
specified torque.
Tightening torque
Manual shift lever nut (a) :
23 N·m (2.3 kg-m, 17.0 lb-ft)
5) After select cable was installed, check for the following.
•Push vehicle with selector lever shifted to “P” range.
Vehicle should not move.
•Vehicle can not be driven in “N” range.
•Vehicle can be driven in “D”, “2” and “L” ranges.
•Vehicle can be backed in “R” range.
1. Selector lever assembly 6. Washer 11. Transmission range switch assembly
2. Selector lever assembly mounting bolt 7. Clip 12. Transmission range switch mounting bolt
3. Selector cable 8. Manual select lever nut (transmission range switch side) 13. Manual select lever nut (selector cable side)
4. Cable bracket 9. Lock washer 14. Selector cable clip
5. Cable bracket mounting bolt 10. Manual select lever Tightening Torque
24
3
1, (a)
Page 458 of 656
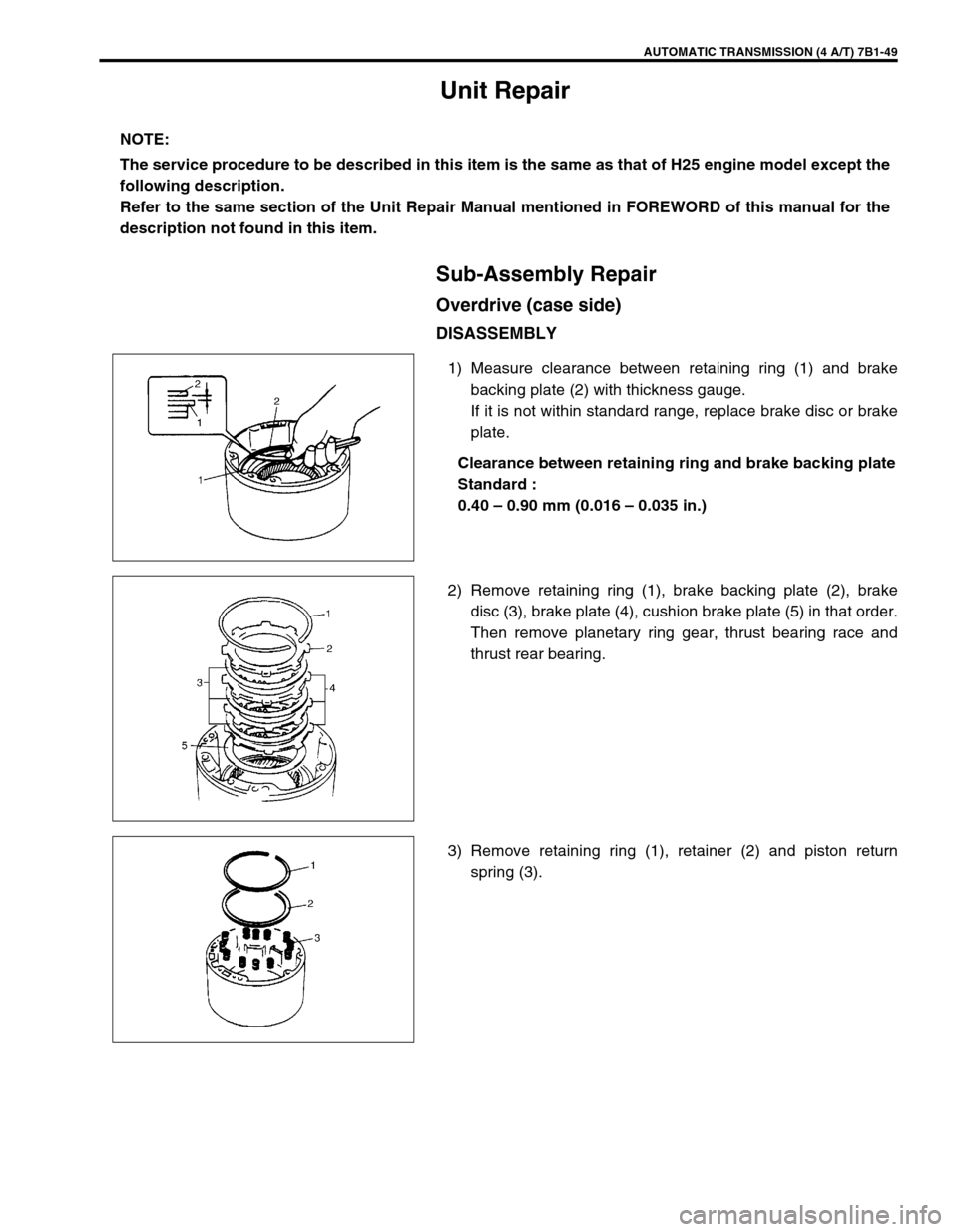
AUTOMATIC TRANSMISSION (4 A/T) 7B1-49
Unit Repair
Sub-Assembly Repair
Overdrive (case side)
DISASSEMBLY
1) Measure clearance between retaining ring (1) and brake
backing plate (2) with thickness gauge.
If it is not within standard range, replace brake disc or brake
plate.
Clearance between retaining ring and brake backing plate
Standard :
0.40 – 0.90 mm (0.016 – 0.035 in.)
2) Remove retaining ring (1), brake backing plate (2), brake
disc (3), brake plate (4), cushion brake plate (5) in that order.
Then remove planetary ring gear, thrust bearing race and
thrust rear bearing.
3) Remove retaining ring (1), retainer (2) and piston return
spring (3). NOTE:
The service procedure to be described in this item is the same as that of H25 engine model except the
following description.
Refer to the same section of the Unit Repair Manual mentioned in FOREWORD of this manual for the
description not found in this item.
Page 459 of 656
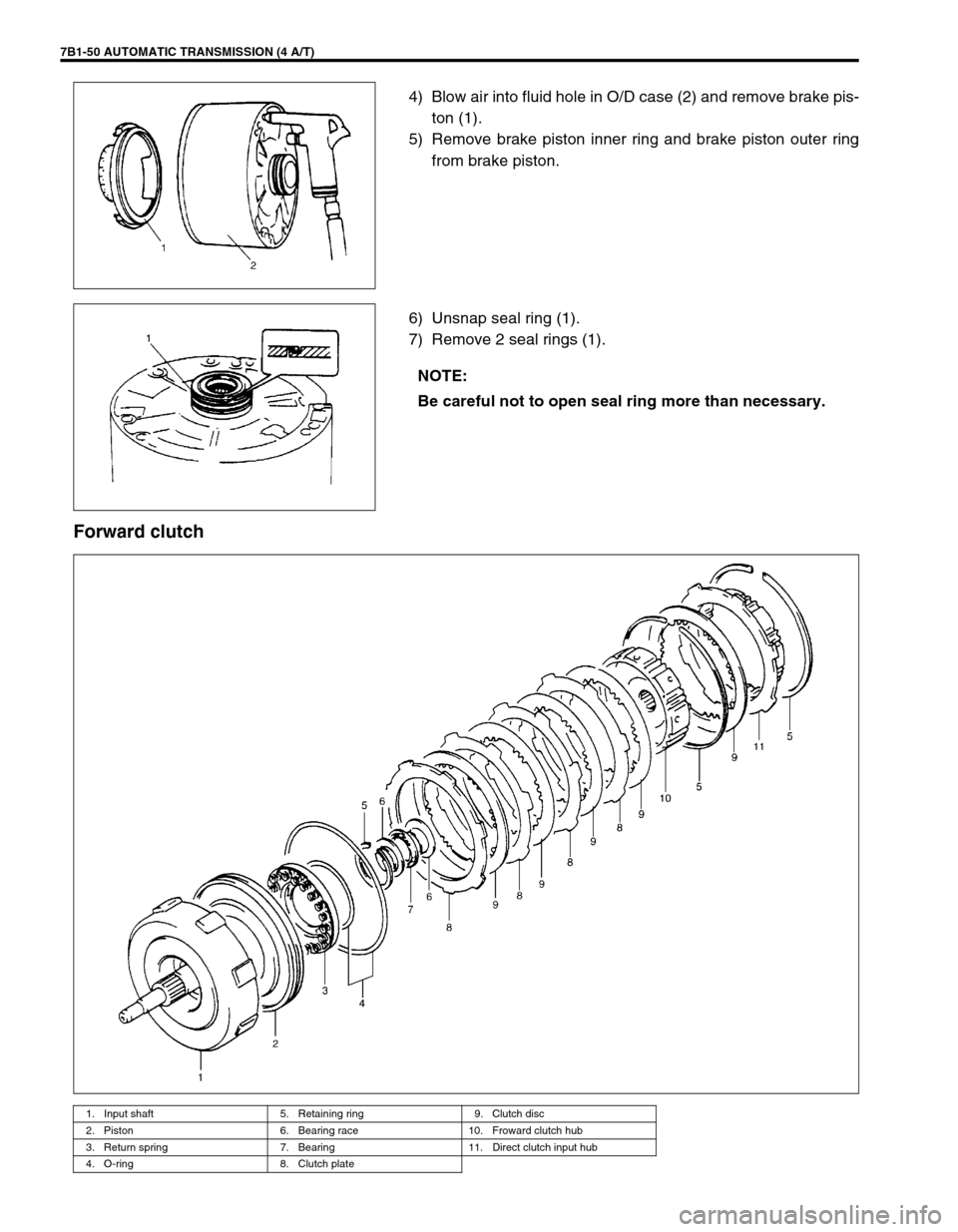
7B1-50 AUTOMATIC TRANSMISSION (4 A/T)
4) Blow air into fluid hole in O/D case (2) and remove brake pis-
ton (1).
5) Remove brake piston inner ring and brake piston outer ring
from brake piston.
6) Unsnap seal ring (1).
7) Remove 2 seal rings (1).
Forward clutch
NOTE:
Be careful not to open seal ring more than necessary.
1. Input shaft 5. Retaining ring 9. Clutch disc
2. Piston 6. Bearing race 10. Froward clutch hub
3. Return spring 7. Bearing 11. Direct clutch input hub
4. O-ring 8. Clutch plate
Page 460 of 656
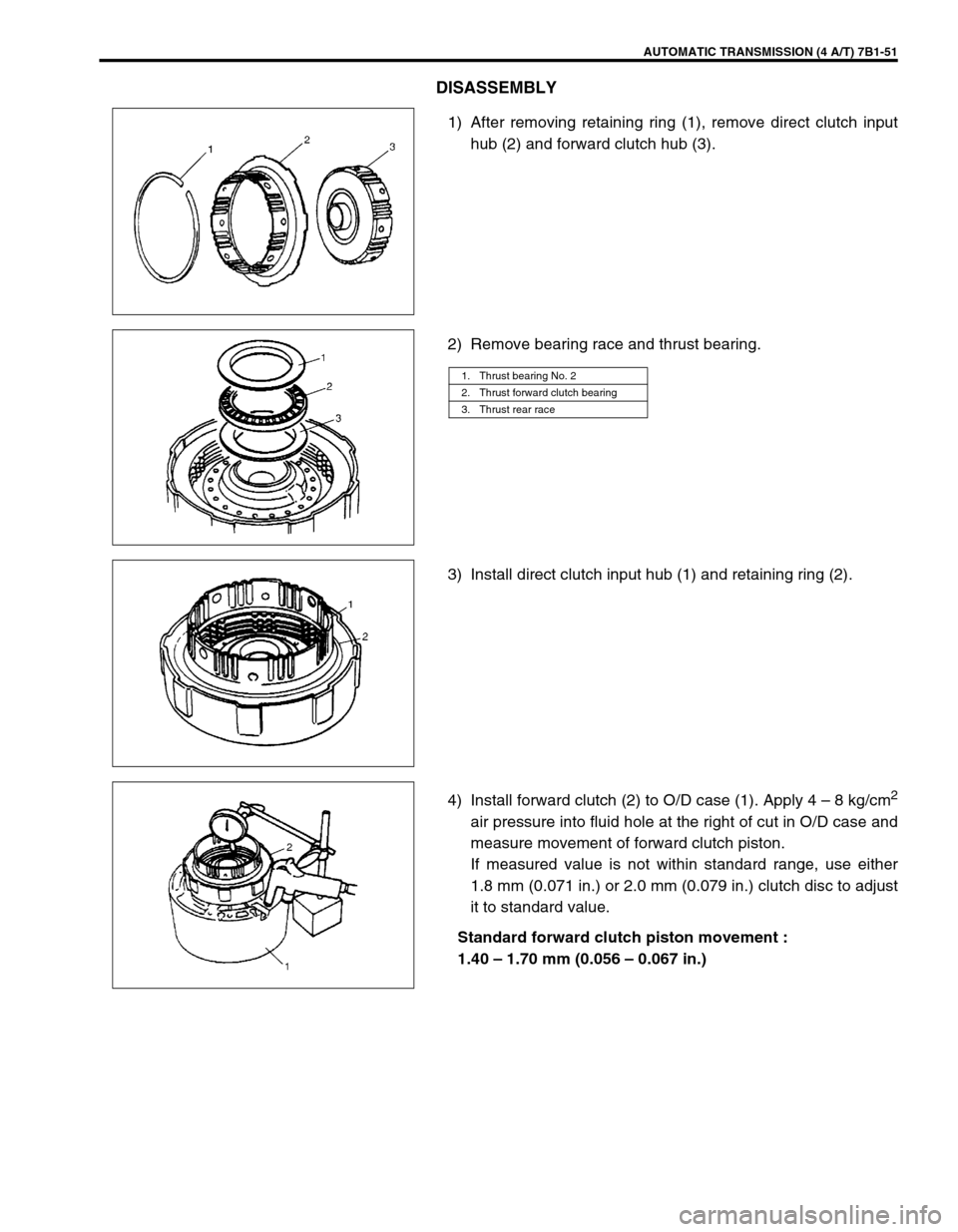
AUTOMATIC TRANSMISSION (4 A/T) 7B1-51
DISASSEMBLY
1) After removing retaining ring (1), remove direct clutch input
hub (2) and forward clutch hub (3).
2) Remove bearing race and thrust bearing.
3) Install direct clutch input hub (1) and retaining ring (2).
4) Install forward clutch (2) to O/D case (1). Apply 4 – 8 kg/cm
2
air pressure into fluid hole at the right of cut in O/D case and
measure movement of forward clutch piston.
If measured value is not within standard range, use either
1.8 mm (0.071 in.) or 2.0 mm (0.079 in.) clutch disc to adjust
it to standard value.
Standard forward clutch piston movement :
1.40 – 1.70 mm (0.056 – 0.067 in.)
1. Thrust bearing No. 2
2. Thrust forward clutch bearing
3. Thrust rear race