SUZUKI SWIFT 2000 1.G RG413 Service Workshop Manual
Manufacturer: SUZUKI, Model Year: 2000, Model line: SWIFT, Model: SUZUKI SWIFT 2000 1.GPages: 698, PDF Size: 16.01 MB
Page 191 of 698
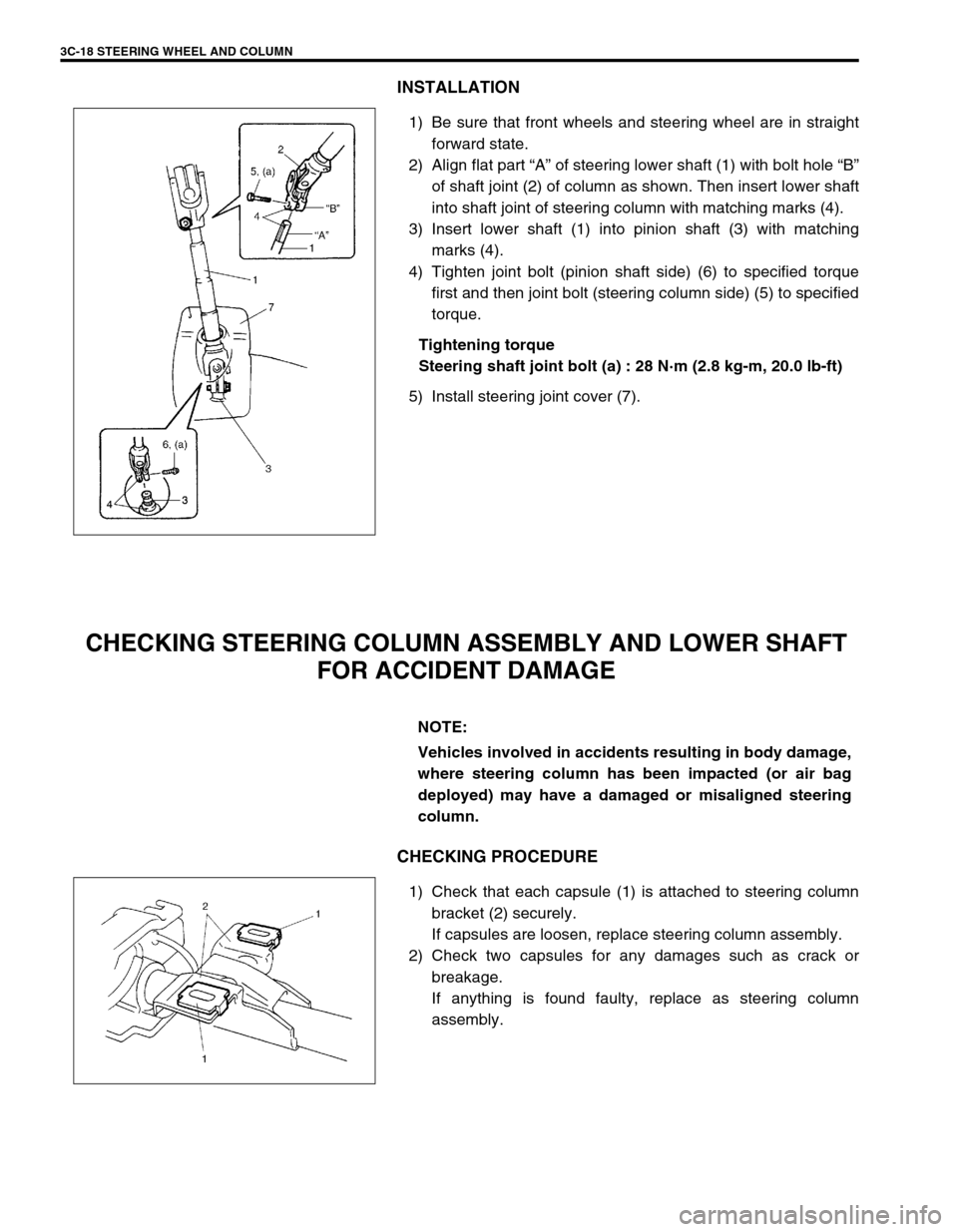
3C-18 STEERING WHEEL AND COLUMN
INSTALLATION
1) Be sure that front wheels and steering wheel are in straight
forward state.
2) Align flat part “A” of steering lower shaft (1) with bolt hole “B”
of shaft joint (2) of column as shown. Then insert lower shaft
into shaft joint of steering column with matching marks (4).
3) Insert lower shaft (1) into pinion shaft (3) with matching
marks (4).
4) Tighten joint bolt (pinion shaft side) (6) to specified torque
first and then joint bolt (steering column side) (5) to specified
torque.
Tightening torque
Steering shaft joint bolt (a) : 28 N·m (2.8 kg-m, 20.0 lb-ft)
5) Install steering joint cover (7).
CHECKING STEERING COLUMN ASSEMBLY AND LOWER SHAFT
FOR ACCIDENT DAMAGE
CHECKING PROCEDURE
1) Check that each capsule (1) is attached to steering column
bracket (2) securely.
If capsules are loosen, replace steering column assembly.
2) Check two capsules for any damages such as crack or
breakage.
If anything is found faulty, replace as steering column
assembly.
NOTE:
Vehicles involved in accidents resulting in body damage,
where steering column has been impacted (or air bag
deployed) may have a damaged or misaligned steering
column.
Page 192 of 698
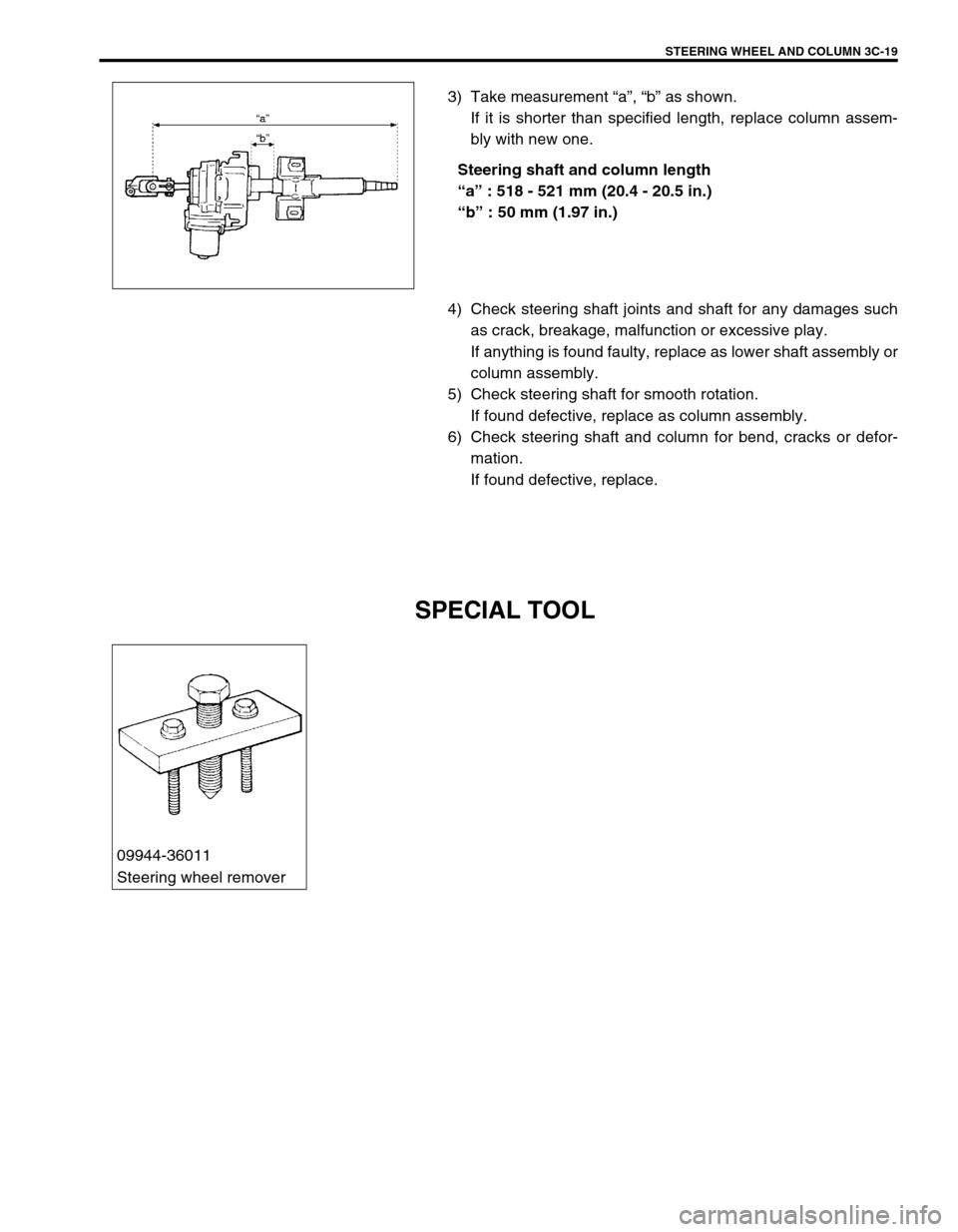
STEERING WHEEL AND COLUMN 3C-19
3) Take measurement “a”, “b” as shown.
If it is shorter than specified length, replace column assem-
bly with new one.
Steering shaft and column length
“a” : 518 - 521 mm (20.4 - 20.5 in.)
“b” : 50 mm (1.97 in.)
4) Check steering shaft joints and shaft for any damages such
as crack, breakage, malfunction or excessive play.
If anything is found faulty, replace as lower shaft assembly or
column assembly.
5) Check steering shaft for smooth rotation.
If found defective, replace as column assembly.
6) Check steering shaft and column for bend, cracks or defor-
mation.
If found defective, replace.
SPECIAL TOOL
09944-36011
Steering wheel remover
Page 193 of 698
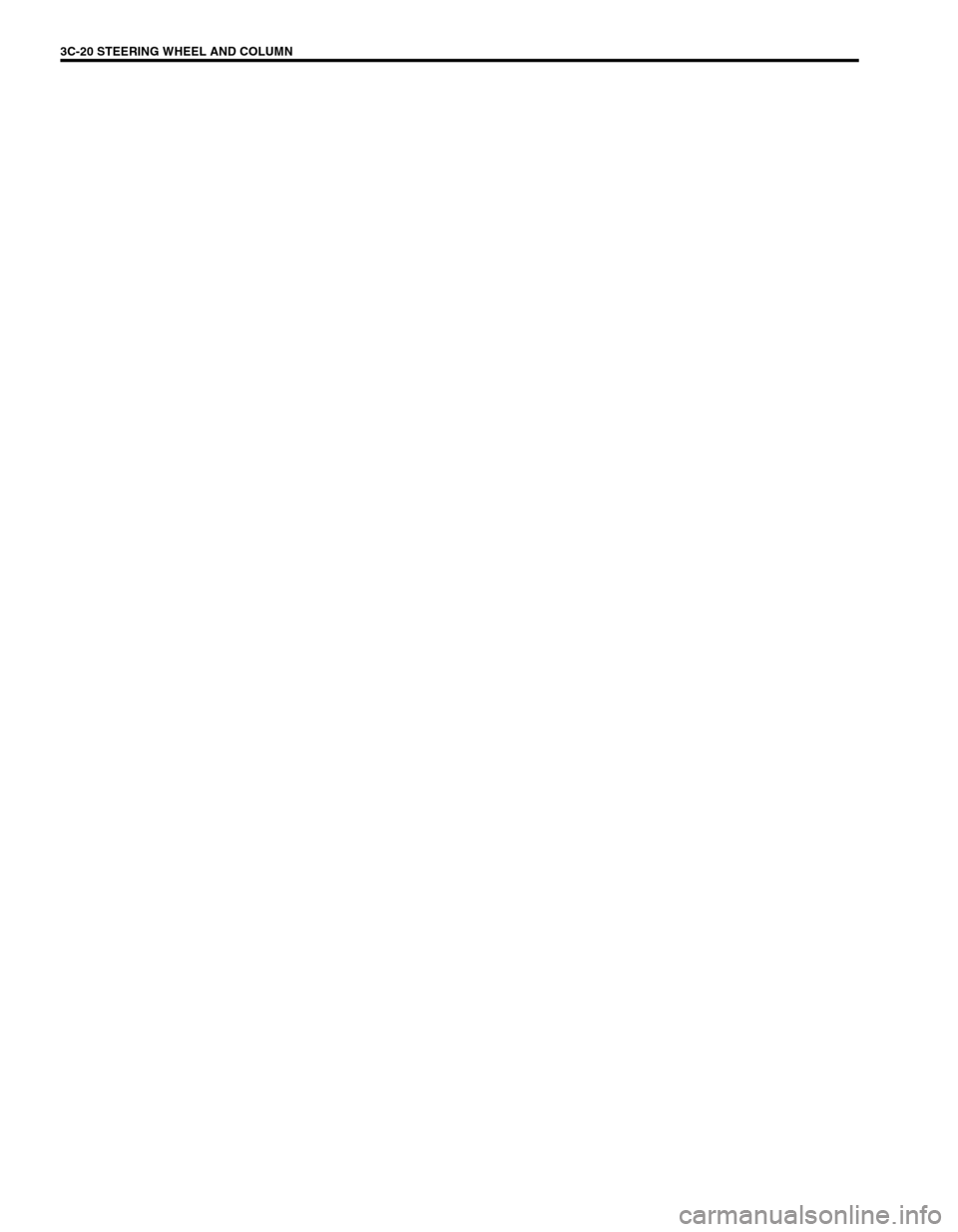
3C-20 STEERING WHEEL AND COLUMN
Page 194 of 698
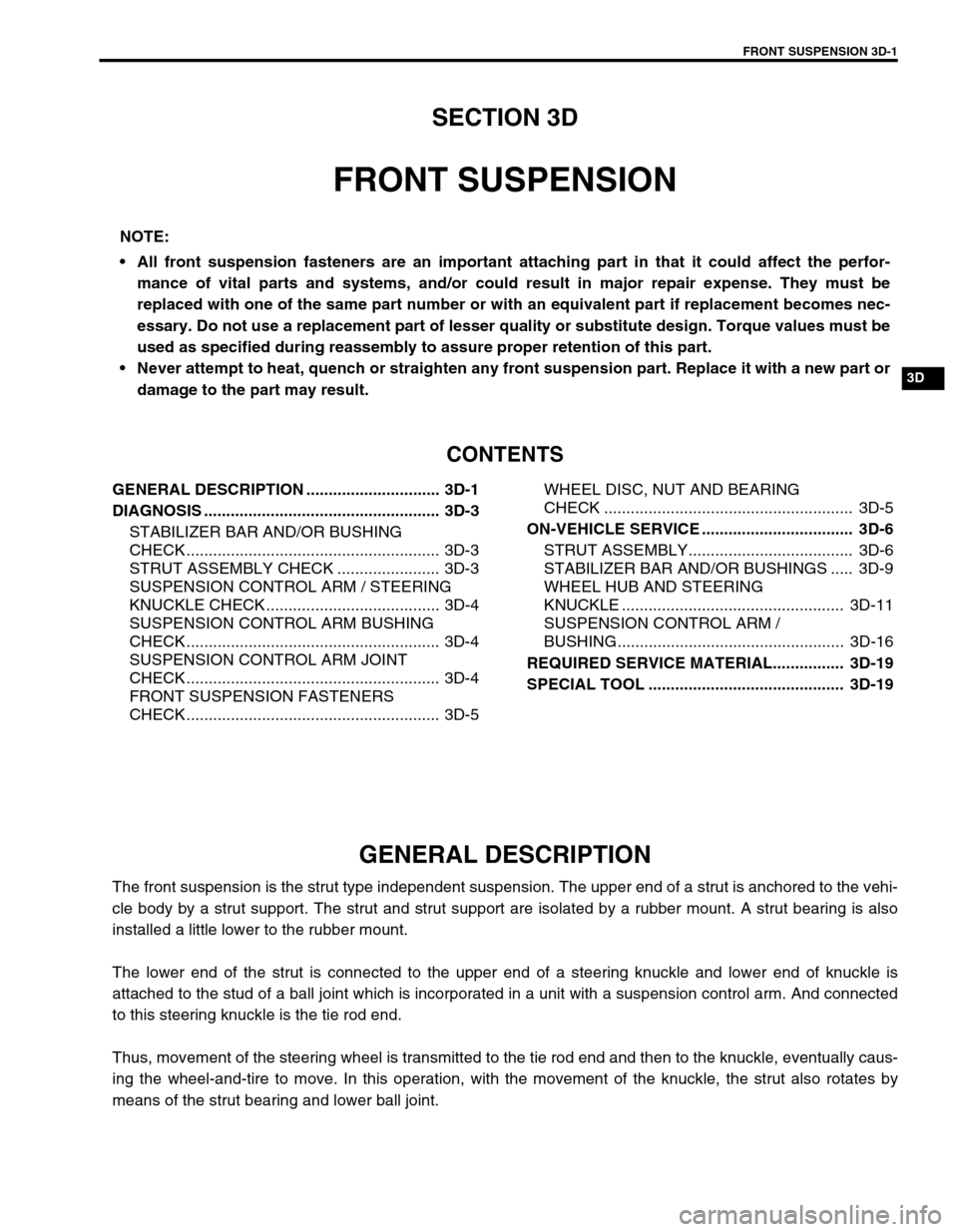
FRONT SUSPENSION 3D-1
6F1
6F2
6G
1A
6K
7A
7A1
7B1
7C1
3D
7F
8A
8B
8C
8D
8E
9
10
10A
10B
SECTION 3D
FRONT SUSPENSION
CONTENTS
GENERAL DESCRIPTION .............................. 3D-1
DIAGNOSIS ..................................................... 3D-3
STABILIZER BAR AND/OR BUSHING
CHECK ......................................................... 3D-3
STRUT ASSEMBLY CHECK ....................... 3D-3
SUSPENSION CONTROL ARM / STEERING
KNUCKLE CHECK ....................................... 3D-4
SUSPENSION CONTROL ARM BUSHING
CHECK ......................................................... 3D-4
SUSPENSION CONTROL ARM JOINT
CHECK ......................................................... 3D-4
FRONT SUSPENSION FASTENERS
CHECK ......................................................... 3D-5WHEEL DISC, NUT AND BEARING
CHECK ........................................................ 3D-5
ON-VEHICLE SERVICE .................................. 3D-6
STRUT ASSEMBLY..................................... 3D-6
STABILIZER BAR AND/OR BUSHINGS ..... 3D-9
WHEEL HUB AND STEERING
KNUCKLE .................................................. 3D-11
SUSPENSION CONTROL ARM /
BUSHING................................................... 3D-16
REQUIRED SERVICE MATERIAL................ 3D-19
SPECIAL TOOL ............................................ 3D-19
GENERAL DESCRIPTION
The front suspension is the strut type independent suspension. The upper end of a strut is anchored to the vehi-
cle body by a strut support. The strut and strut support are isolated by a rubber mount. A strut bearing is also
installed a little lower to the rubber mount.
The lower end of the strut is connected to the upper end of a steering knuckle and lower end of knuckle is
attached to the stud of a ball joint which is incorporated in a unit with a suspension control arm. And connected
to this steering knuckle is the tie rod end.
Thus, movement of the steering wheel is transmitted to the tie rod end and then to the knuckle, eventually caus-
ing the wheel-and-tire to move. In this operation, with the movement of the knuckle, the strut also rotates by
means of the strut bearing and lower ball joint.NOTE:
All front suspension fasteners are an important attaching part in that it could affect the perfor-
mance of vital parts and systems, and/or could result in major repair expense. They must be
replaced with one of the same part number or with an equivalent part if replacement becomes nec-
essary. Do not use a replacement part of lesser quality or substitute design. Torque values must be
used as specified during reassembly to assure proper retention of this part.
Never attempt to heat, quench or straighten any front suspension part. Replace it with a new part or
damage to the part may result.
Page 195 of 698
![SUZUKI SWIFT 2000 1.G RG413 Service Workshop Manual 3D-2 FRONT SUSPENSION
1. Strut assembly 4. Wheel 7. Drive shaft [A] : FORWARD
2. Stabilizer bar 5. Suspension control arm 8. Tie rod Tightening torque
3. Steering knuckle 6. Vehicle body 9. Brake disc SUZUKI SWIFT 2000 1.G RG413 Service Workshop Manual 3D-2 FRONT SUSPENSION
1. Strut assembly 4. Wheel 7. Drive shaft [A] : FORWARD
2. Stabilizer bar 5. Suspension control arm 8. Tie rod Tightening torque
3. Steering knuckle 6. Vehicle body 9. Brake disc](/img/20/7606/w960_7606-194.png)
3D-2 FRONT SUSPENSION
1. Strut assembly 4. Wheel 7. Drive shaft [A] : FORWARD
2. Stabilizer bar 5. Suspension control arm 8. Tie rod Tightening torque
3. Steering knuckle 6. Vehicle body 9. Brake disc Do not reuse.
[A]
4
92
35
8
660 N·m(6.0 kg-m) 175 N·m(17.5 kg-m)
60 N·m(6.0 kg-m)
85 N·m(8.5 kg-m)
85 N·m(8.5 kg-m)
43 N·m(4.3 kg-m)
65 N·m(6.5 kg-m)
65 N·m(6.5 kg-m)
23 N·m(2.3 kg-m)
50 N·m(5.0 kg-m)
175 N·m(17.5 kg-m)
105 N·m(10.5 kg-m)
1
8
45 N·m (4.5kg-m) 7
5
4
9
Page 196 of 698
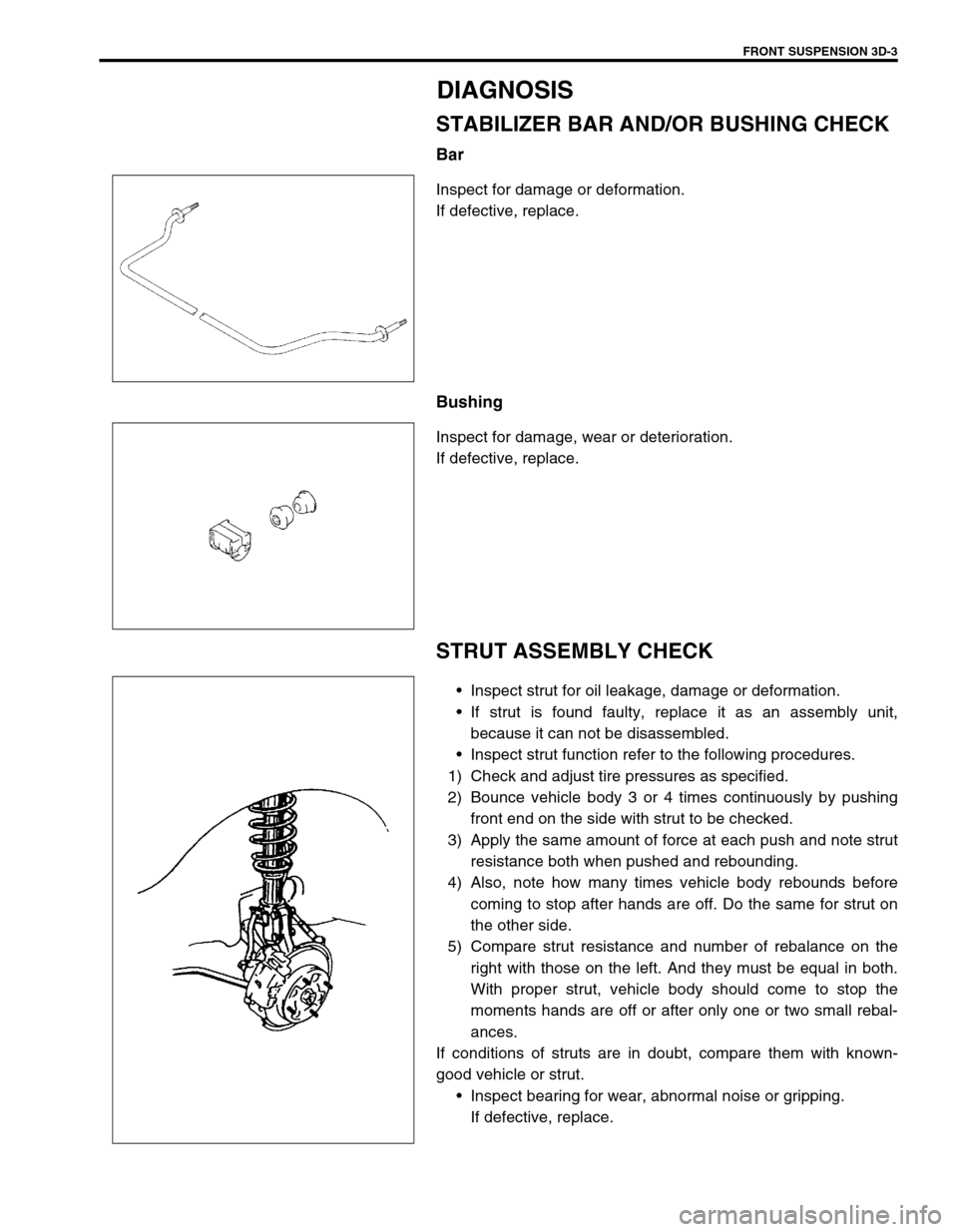
FRONT SUSPENSION 3D-3
DIAGNOSIS
STABILIZER BAR AND/OR BUSHING CHECK
Bar
Inspect for damage or deformation.
If defective, replace.
Bushing
Inspect for damage, wear or deterioration.
If defective, replace.
STRUT ASSEMBLY CHECK
Inspect strut for oil leakage, damage or deformation.
If strut is found faulty, replace it as an assembly unit,
because it can not be disassembled.
Inspect strut function refer to the following procedures.
1) Check and adjust tire pressures as specified.
2) Bounce vehicle body 3 or 4 times continuously by pushing
front end on the side with strut to be checked.
3) Apply the same amount of force at each push and note strut
resistance both when pushed and rebounding.
4) Also, note how many times vehicle body rebounds before
coming to stop after hands are off. Do the same for strut on
the other side.
5) Compare strut resistance and number of rebalance on the
right with those on the left. And they must be equal in both.
With proper strut, vehicle body should come to stop the
moments hands are off or after only one or two small rebal-
ances.
If conditions of struts are in doubt, compare them with known-
good vehicle or strut.
Inspect bearing for wear, abnormal noise or gripping.
If defective, replace.
Page 197 of 698

3D-4 FRONT SUSPENSION
Inspect spring seat for cracks or deformation.
If defective, replace.
Inspect bump stopper for deterioration.
If defective, replace.
Inspect rebound stopper and strut mount for wear, cracks or
deformation.
If defective, replace.
SUSPENSION CONTROL ARM / STEERING
KNUCKLE CHECK
Inspect for cracks, deformation or damage.
If defective, replace.
SUSPENSION CONTROL ARM BUSHING
CHECK
Inspect for damage, wear or deterioration.
If defective, replace.
SUSPENSION CONTROL ARM JOINT CHECK
Check for smooth rotation.
Inspect ball stud for damage.
Inspect dust cover for damage.
If there is any damage to either, control arm assembly must be
replaced as a complete unit.
NOTE:
Suspension control arm and arm joint cannot be sepa-
rated.
Page 198 of 698
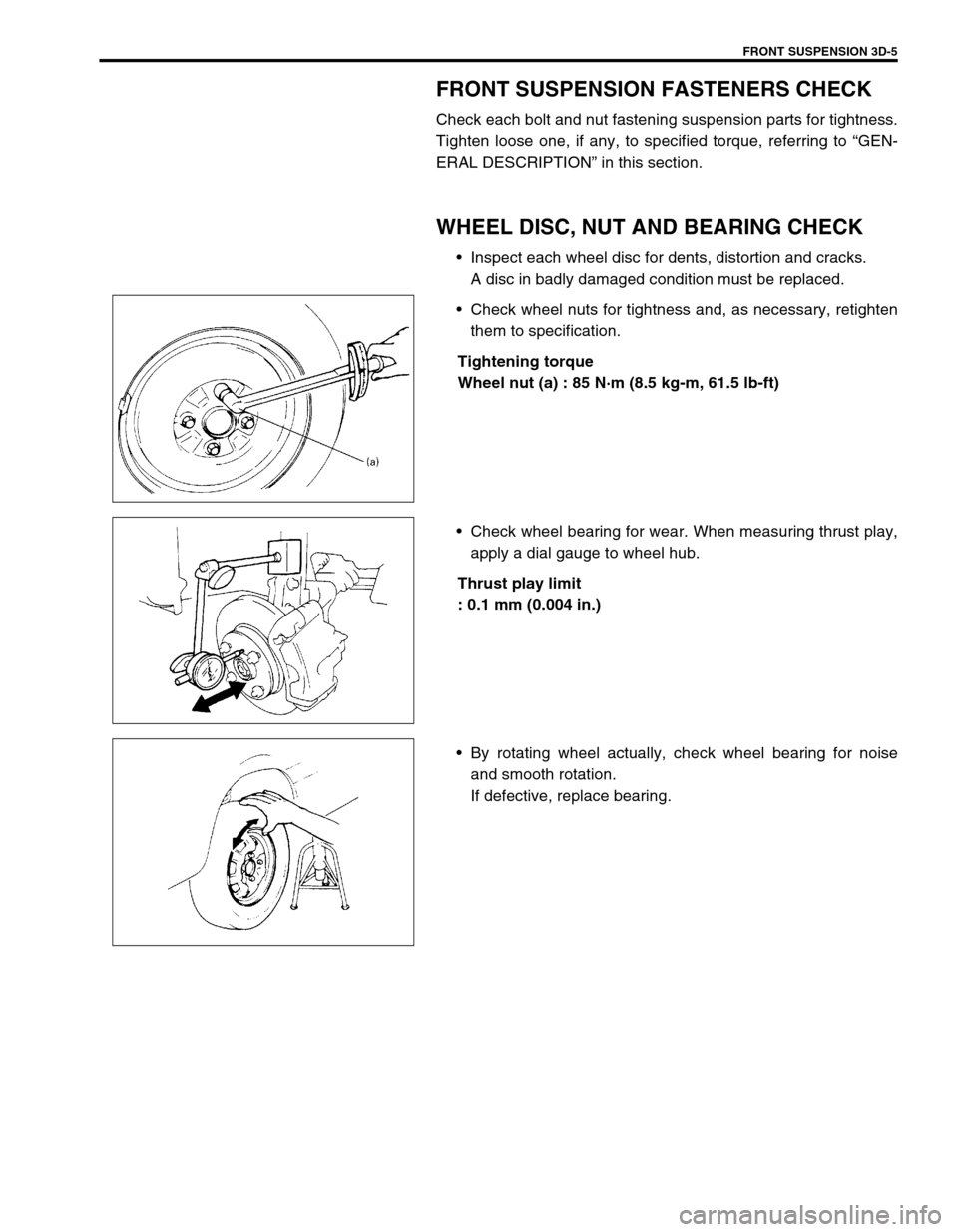
FRONT SUSPENSION 3D-5
FRONT SUSPENSION FASTENERS CHECK
Check each bolt and nut fastening suspension parts for tightness.
Tighten loose one, if any, to specified torque, referring to “GEN-
ERAL DESCRIPTION” in this section.
WHEEL DISC, NUT AND BEARING CHECK
Inspect each wheel disc for dents, distortion and cracks.
A disc in badly damaged condition must be replaced.
Check wheel nuts for tightness and, as necessary, retighten
them to specification.
Tightening torque
Wheel nut (a) : 85 N·m (8.5 kg-m, 61.5 lb-ft)
Check wheel bearing for wear. When measuring thrust play,
apply a dial gauge to wheel hub.
Thrust play limit
: 0.1 mm (0.004 in.)
By rotating wheel actually, check wheel bearing for noise
and smooth rotation.
If defective, replace bearing.
Page 199 of 698

3D-6 FRONT SUSPENSION
ON-VEHICLE SERVICE
STRUT ASSEMBLY
REMOVAL
1) Hoist vehicle, allowing front suspension to hang free.
2) Remove wheel.
3) Remove E-ring (1) securing brake hose and take brake hose
off strut bracket as shown.
4) Remove strut bracket bolts (2).
1. Strut assembly 5. Coil spring upper seat 9. Strut support nut
2. Coil spring 6. Strut bearing
: Apply grease (99000-25010) to all around bearing.10. Strut bracket bolt
: Insert from vehicle rear side.
3. Bump stopper 7. Strut support 11. Strut bracket nut
4. Coil spring lower seat 8. Strut nut Tightening torque
Page 200 of 698
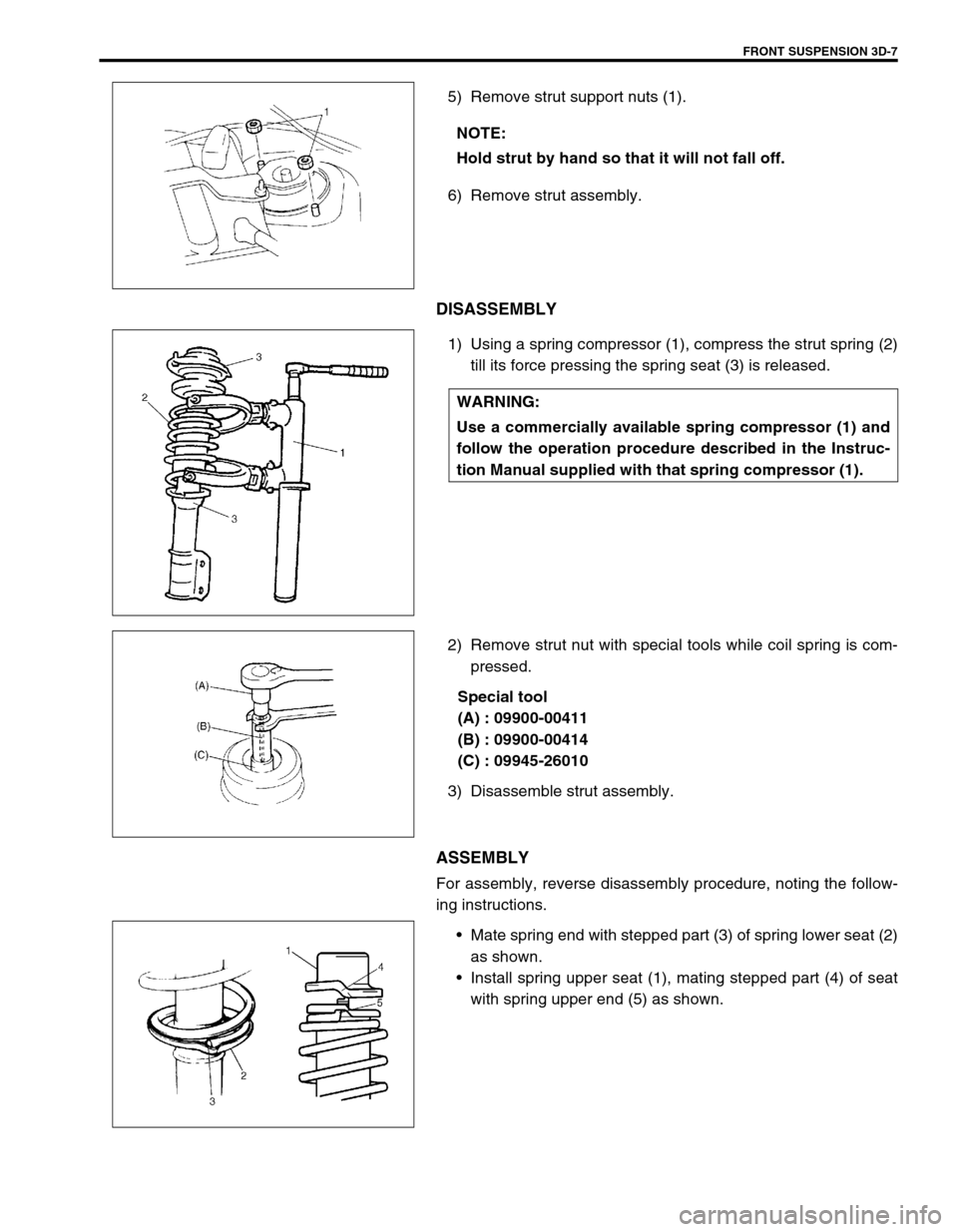
FRONT SUSPENSION 3D-7
5) Remove strut support nuts (1).
6) Remove strut assembly.
DISASSEMBLY
1) Using a spring compressor (1), compress the strut spring (2)
till its force pressing the spring seat (3) is released.
2) Remove strut nut with special tools while coil spring is com-
pressed.
Special tool
(A) : 09900-00411
(B) : 09900-00414
(C) : 09945-26010
3) Disassemble strut assembly.
ASSEMBLY
For assembly, reverse disassembly procedure, noting the follow-
ing instructions.
Mate spring end with stepped part (3) of spring lower seat (2)
as shown.
Install spring upper seat (1), mating stepped part (4) of seat
with spring upper end (5) as shown. NOTE:
Hold strut by hand so that it will not fall off.
WARNING:
Use a commercially available spring compressor (1) and
follow the operation procedure described in the Instruc-
tion Manual supplied with that spring compressor (1).