sensor SUZUKI SWIFT 2000 1.G RG413 Service Owner's Manual
[x] Cancel search | Manufacturer: SUZUKI, Model Year: 2000, Model line: SWIFT, Model: SUZUKI SWIFT 2000 1.GPages: 698, PDF Size: 16.01 MB
Page 166 of 698
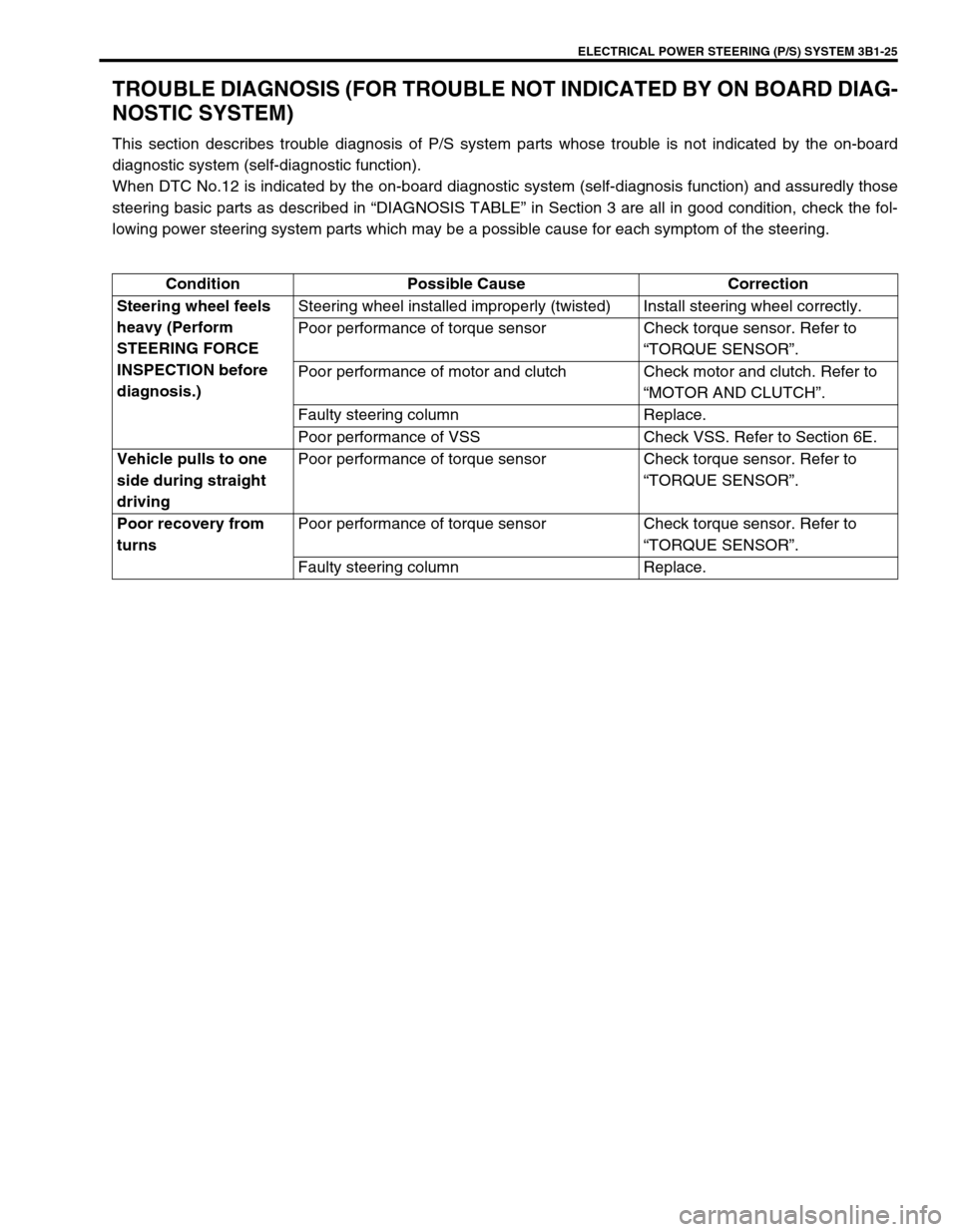
ELECTRICAL POWER STEERING (P/S) SYSTEM 3B1-25
TROUBLE DIAGNOSIS (FOR TROUBLE NOT INDICATED BY ON BOARD DIAG-
NOSTIC SYSTEM)
This section describes trouble diagnosis of P/S system parts whose trouble is not indicated by the on-board
diagnostic system (self-diagnostic function).
When DTC No.12 is indicated by the on-board diagnostic system (self-diagnosis function) and assuredly those
steering basic parts as described in “DIAGNOSIS TABLE” in Section 3 are all in good condition, check the fol-
lowing power steering system parts which may be a possible cause for each symptom of the steering.
Condition Possible Cause Correction
Steering wheel feels
heavy (Perform
STEERING FORCE
INSPECTION before
diagnosis.)Steering wheel installed improperly (twisted) Install steering wheel correctly.
Poor performance of torque sensor Check torque sensor. Refer to
“TORQUE SENSOR”.
Poor performance of motor and clutch Check motor and clutch. Refer to
“MOTOR AND CLUTCH”.
Faulty steering column Replace.
Poor performance of VSS Check VSS. Refer to Section 6E.
Vehicle pulls to one
side during straight
drivingPoor performance of torque sensor Check torque sensor. Refer to
“TORQUE SENSOR”.
Poor recovery from
turnsPoor performance of torque sensor Check torque sensor. Refer to
“TORQUE SENSOR”.
Faulty steering column Replace.
Page 168 of 698
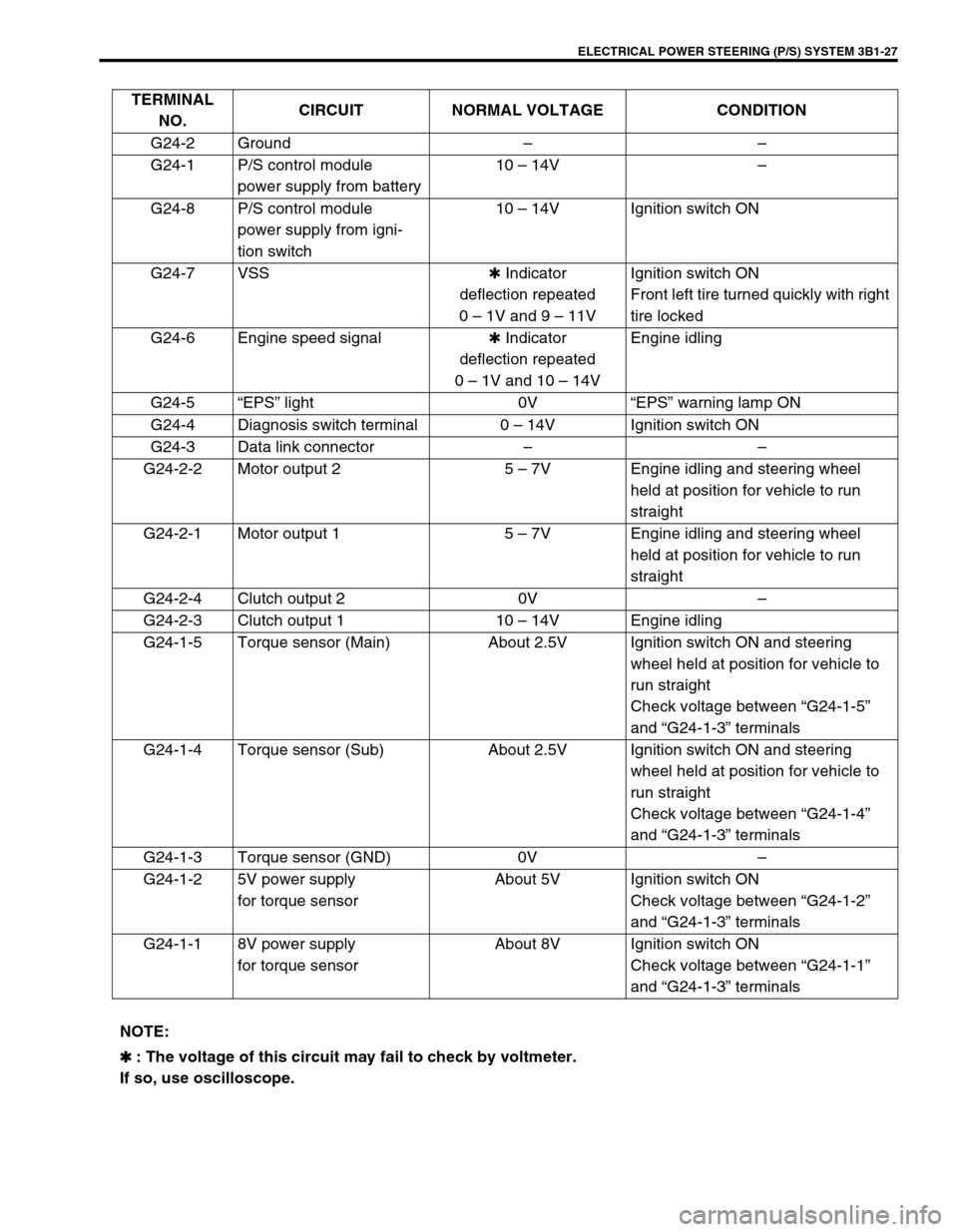
ELECTRICAL POWER STEERING (P/S) SYSTEM 3B1-27
TERMINAL
NO.CIRCUIT NORMAL VOLTAGE CONDITION
G24-2 Ground––
G24-1 P/S control module
power supply from battery10 – 14V–
G24-8 P/S control module
power supply from igni-
tion switch10 – 14V Ignition switch ON
G24-7 VSS✱ Indicator
deflection repeated
0 – 1V and 9 – 11VIgnition switch ON
Front left tire turned quickly with right
tire locked
G24-6 Engine speed signal✱ Indicator
deflection repeated
0 – 1V and 10 – 14VEngine idling
G24-5“EPS” light 0V“EPS” warning lamp ON
G24-4 Diagnosis switch terminal 0 – 14V Ignition switch ON
G24-3 Data link connector––
G24-2-2 Motor output 2 5 – 7V Engine idling and steering wheel
held at position for vehicle to run
straight
G24-2-1 Motor output 1 5 – 7V Engine idling and steering wheel
held at position for vehicle to run
straight
G24-2-4 Clutch output 2 0V–
G24-2-3 Clutch output 1 10 – 14V Engine idling
G24-1-5 Torque sensor (Main) About 2.5V Ignition switch ON and steering
wheel held at position for vehicle to
run straight
Check voltage between “G24-1-5”
and “G24-1-3” terminals
G24-1-4 Torque sensor (Sub) About 2.5V Ignition switch ON and steering
wheel held at position for vehicle to
run straight
Check voltage between “G24-1-4”
and “G24-1-3” terminals
G24-1-3 Torque sensor (GND) 0V–
G24-1-2 5V power supply
for torque sensorAbout 5V Ignition switch ON
Check voltage between “G24-1-2”
and “G24-1-3” terminals
G24-1-1 8V power supply
for torque sensorAbout 8V Ignition switch ON
Check voltage between “G24-1-1”
and “G24-1-3” terminals
NOTE:
✱
✱✱ ✱ : The voltage of this circuit may fail to check by voltmeter.
If so, use oscilloscope.
Page 170 of 698
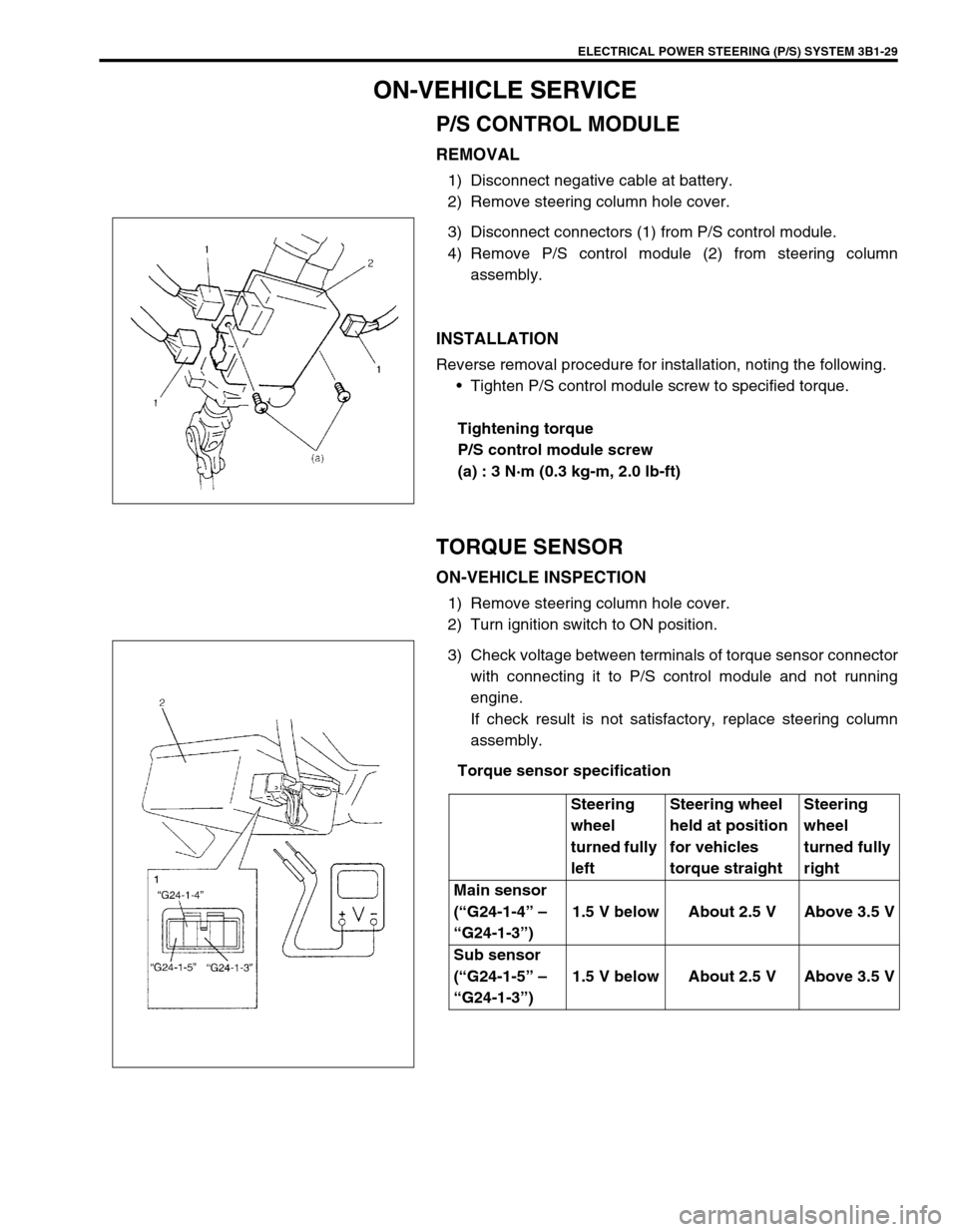
ELECTRICAL POWER STEERING (P/S) SYSTEM 3B1-29
ON-VEHICLE SERVICE
P/S CONTROL MODULE
REMOVAL
1) Disconnect negative cable at battery.
2) Remove steering column hole cover.
3) Disconnect connectors (1) from P/S control module.
4) Remove P/S control module (2) from steering column
assembly.
INSTALLATION
Reverse removal procedure for installation, noting the following.
Tighten P/S control module screw to specified torque.
Tightening torque
P/S control module screw
(a) : 3 N·m (0.3 kg-m, 2.0 lb-ft)
TORQUE SENSOR
ON-VEHICLE INSPECTION
1) Remove steering column hole cover.
2) Turn ignition switch to ON position.
3) Check voltage between terminals of torque sensor connector
with connecting it to P/S control module and not running
engine.
If check result is not satisfactory, replace steering column
assembly.
Torque sensor specification
Steering
wheel
turned fully
leftSteering wheel
held at position
for vehicles
torque straightSteering
wheel
turned fully
right
Main sensor
(“G24-1-4” –
“G24-1-3”)1.5 V below About 2.5 V Above 3.5 V
Sub sensor
(“G24-1-5” –
“G24-1-3”)1.5 V below About 2.5 V Above 3.5 V
Page 205 of 698
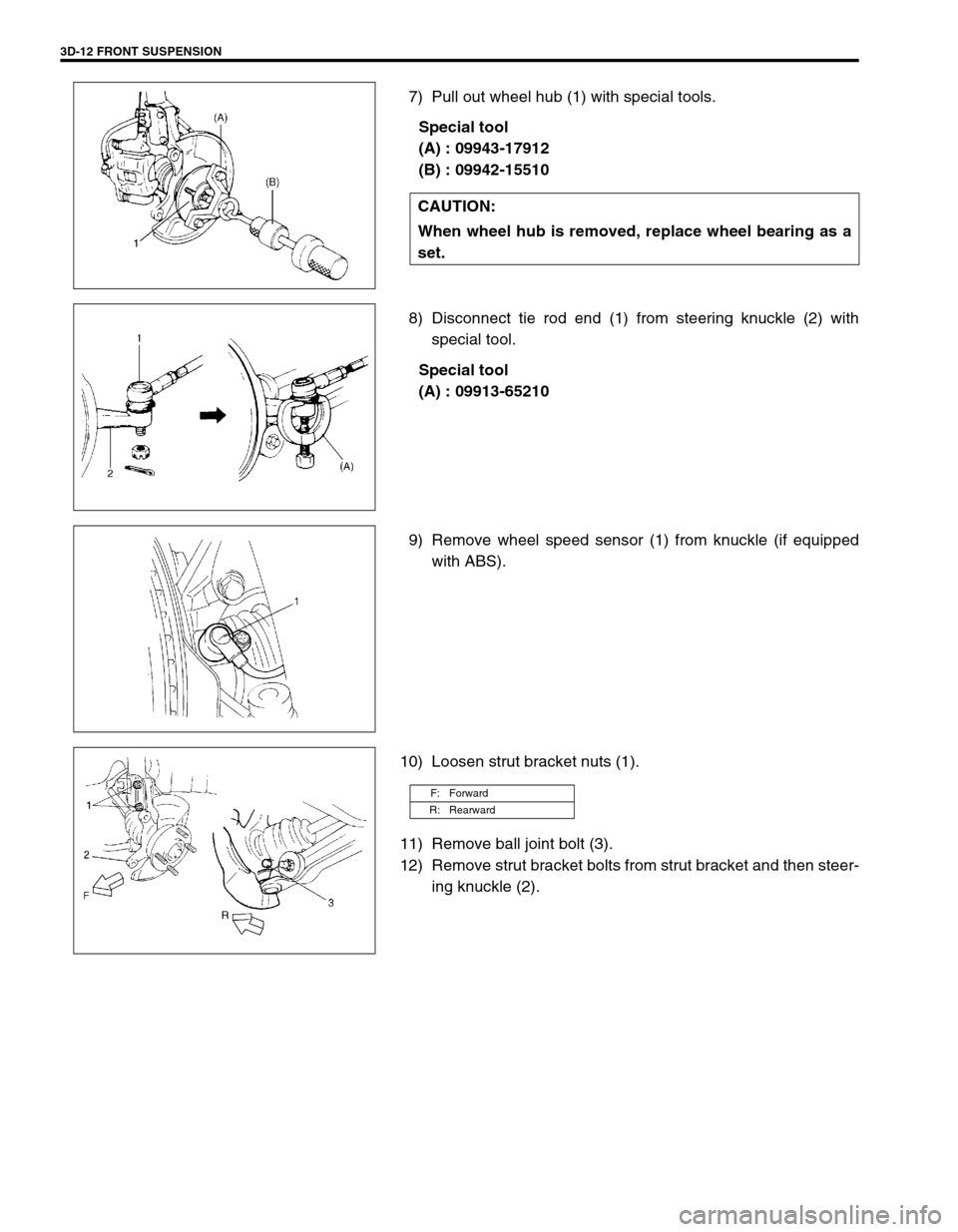
3D-12 FRONT SUSPENSION
7) Pull out wheel hub (1) with special tools.
Special tool
(A) : 09943-17912
(B) : 09942-15510
8) Disconnect tie rod end (1) from steering knuckle (2) with
special tool.
Special tool
(A) : 09913-65210
9) Remove wheel speed sensor (1) from knuckle (if equipped
with ABS).
10) Loosen strut bracket nuts (1).
11) Remove ball joint bolt (3).
12) Remove strut bracket bolts from strut bracket and then steer-
ing knuckle (2). CAUTION:
When wheel hub is removed, replace wheel bearing as a
set.
F: Forward
R: Rearward
Page 208 of 698
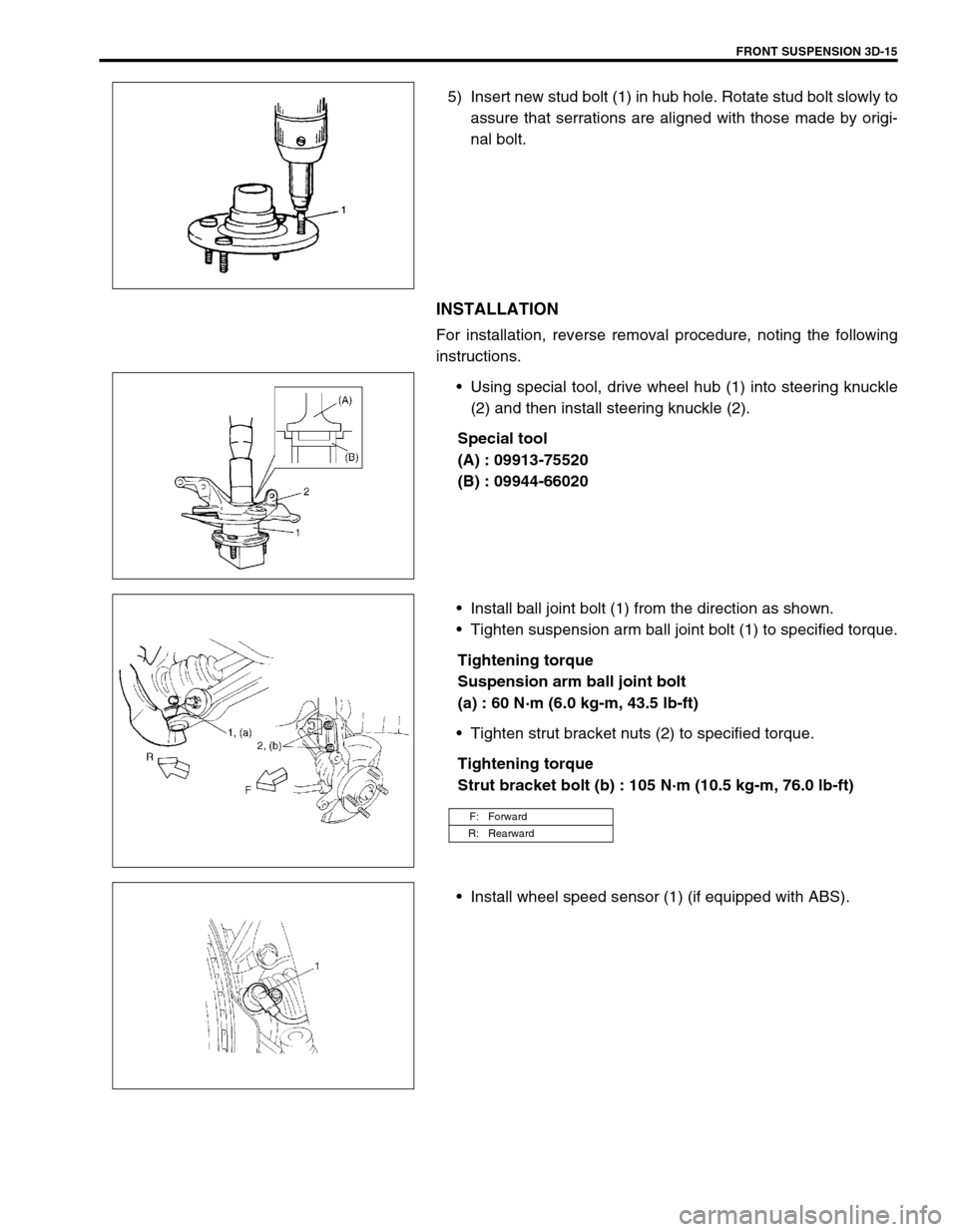
FRONT SUSPENSION 3D-15
5) Insert new stud bolt (1) in hub hole. Rotate stud bolt slowly to
assure that serrations are aligned with those made by origi-
nal bolt.
INSTALLATION
For installation, reverse removal procedure, noting the following
instructions.
Using special tool, drive wheel hub (1) into steering knuckle
(2) and then install steering knuckle (2).
Special tool
(A) : 09913-75520
(B) : 09944-66020
Install ball joint bolt (1) from the direction as shown.
Tighten suspension arm ball joint bolt (1) to specified torque.
Tightening torque
Suspension arm ball joint bolt
(a) : 60 N·m (6.0 kg-m, 43.5 lb-ft)
Tighten strut bracket nuts (2) to specified torque.
Tightening torque
Strut bracket bolt (b) : 105 N·m (10.5 kg-m, 76.0 lb-ft)
Install wheel speed sensor (1) (if equipped with ABS).
F: Forward
R: Rearward
Page 215 of 698
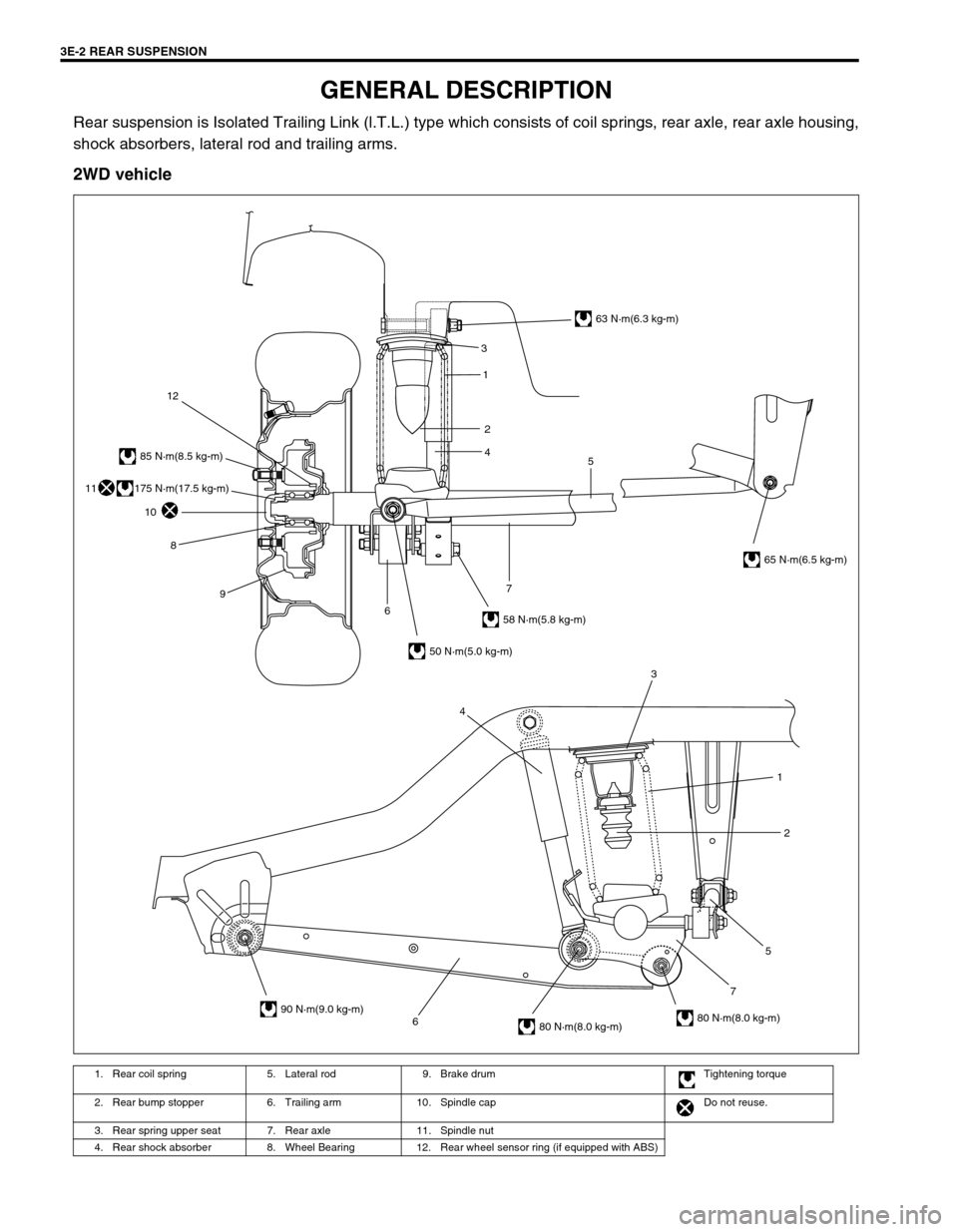
3E-2 REAR SUSPENSION
GENERAL DESCRIPTION
Rear suspension is Isolated Trailing Link (l.T.L.) type which consists of coil springs, rear axle, rear axle housing,
shock absorbers, lateral rod and trailing arms.
2WD vehicle
1. Rear coil spring 5. Lateral rod 9. Brake drum Tightening torque
2. Rear bump stopper 6. Trailing arm 10. Spindle cap Do not reuse.
3. Rear spring upper seat 7. Rear axle 11. Spindle nut
4. Rear shock absorber 8. Wheel Bearing 12. Rear wheel sensor ring (if equipped with ABS)
6752 1 3
4
3
5 1
2
4
63 N·m(6.3 kg-m)
65 N·m(6.5 kg-m)
58 N·m(5.8 kg-m)
50 N·m(5.0 kg-m)
90 N·m(9.0 kg-m)
80 N·m(8.0 kg-m)80 N·m(8.0 kg-m)
85 N·m(8.5 kg-m)
12
10
8
9
67
175 N·m(17.5 kg-m)11
Page 216 of 698
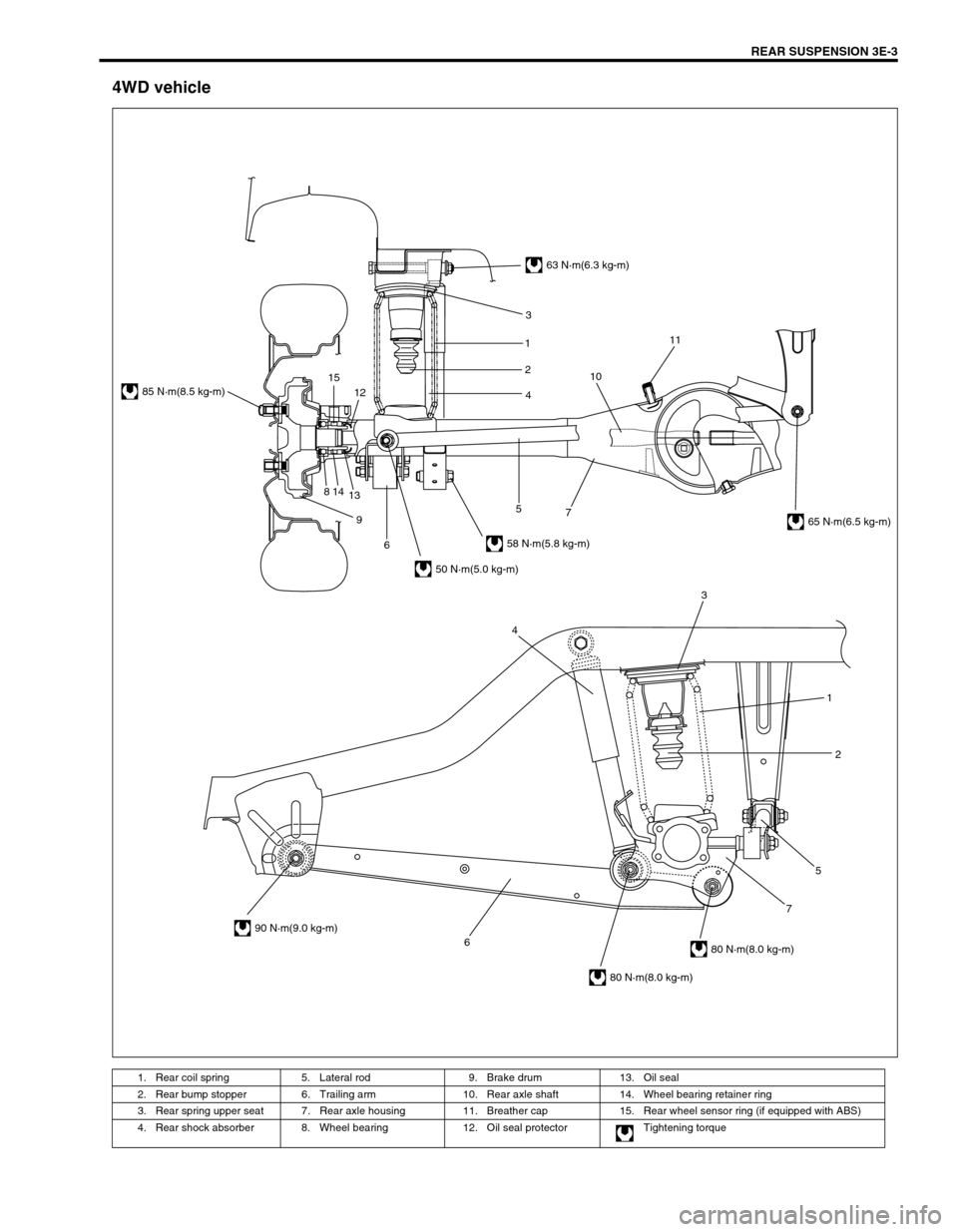
REAR SUSPENSION 3E-3
4WD vehicle
1. Rear coil spring 5. Lateral rod 9. Brake drum 13. Oil seal
2. Rear bump stopper 6. Trailing arm 10. Rear axle shaft 14. Wheel bearing retainer ring
3. Rear spring upper seat 7. Rear axle housing 11. Breather cap 15. Rear wheel sensor ring (if equipped with ABS)
4. Rear shock absorber 8. Wheel bearing 12. Oil seal protector Tightening torque
6752 1 3
4
63 N·m(6.3 kg-m)
58 N·m(5.8 kg-m)
50 N·m(5.0 kg-m)
85 N·m(8.5 kg-m)
90 N·m(9.0 kg-m)
80 N·m(8.0 kg-m)
80 N·m(8.0 kg-m)
65 N·m(6.5 kg-m) 3
1
2
4
7 5
6 9 814
1312 151011
Page 225 of 698
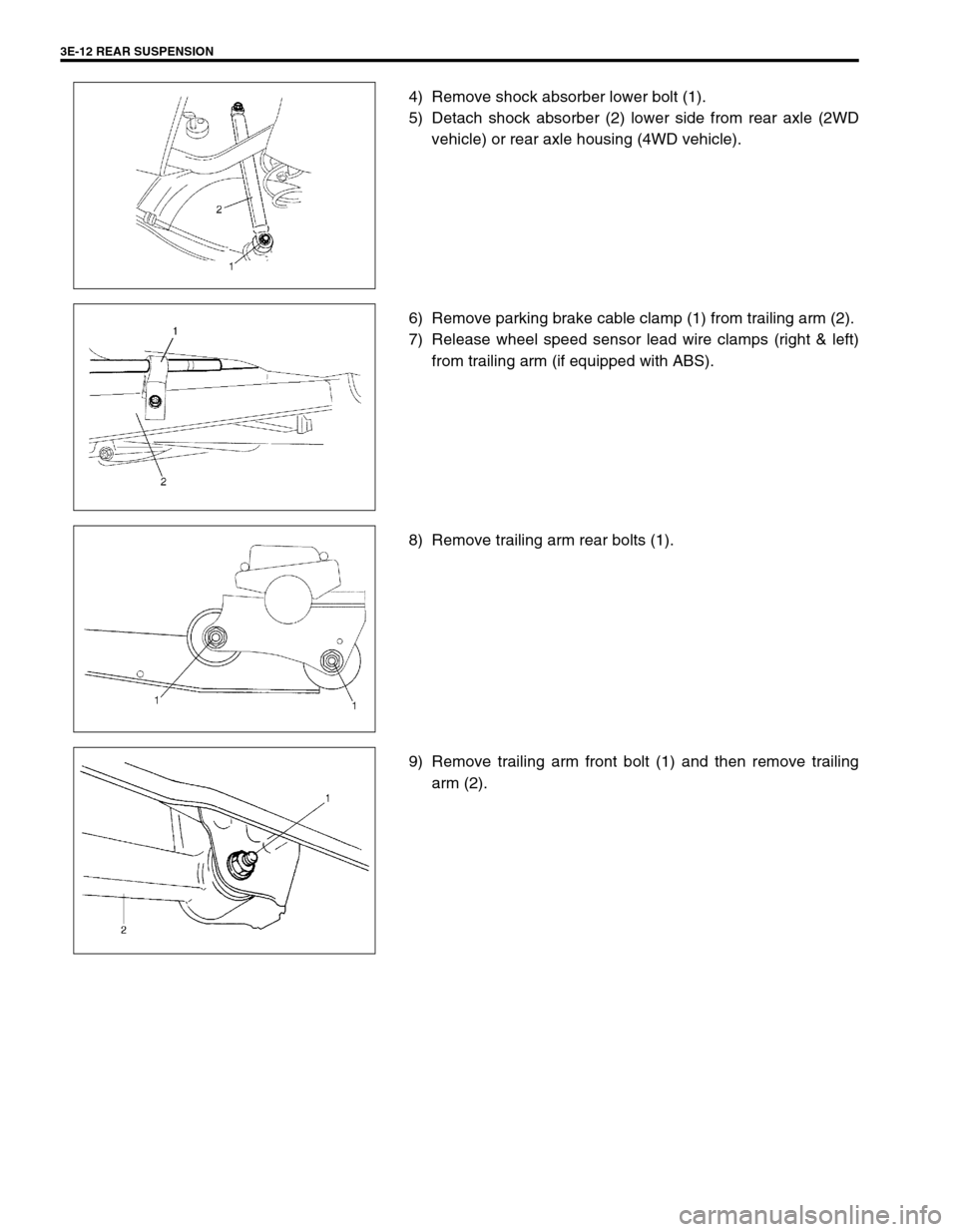
3E-12 REAR SUSPENSION
4) Remove shock absorber lower bolt (1).
5) Detach shock absorber (2) lower side from rear axle (2WD
vehicle) or rear axle housing (4WD vehicle).
6) Remove parking brake cable clamp (1) from trailing arm (2).
7) Release wheel speed sensor lead wire clamps (right & left)
from trailing arm (if equipped with ABS).
8) Remove trailing arm rear bolts (1).
9) Remove trailing arm front bolt (1) and then remove trailing
arm (2).
Page 226 of 698
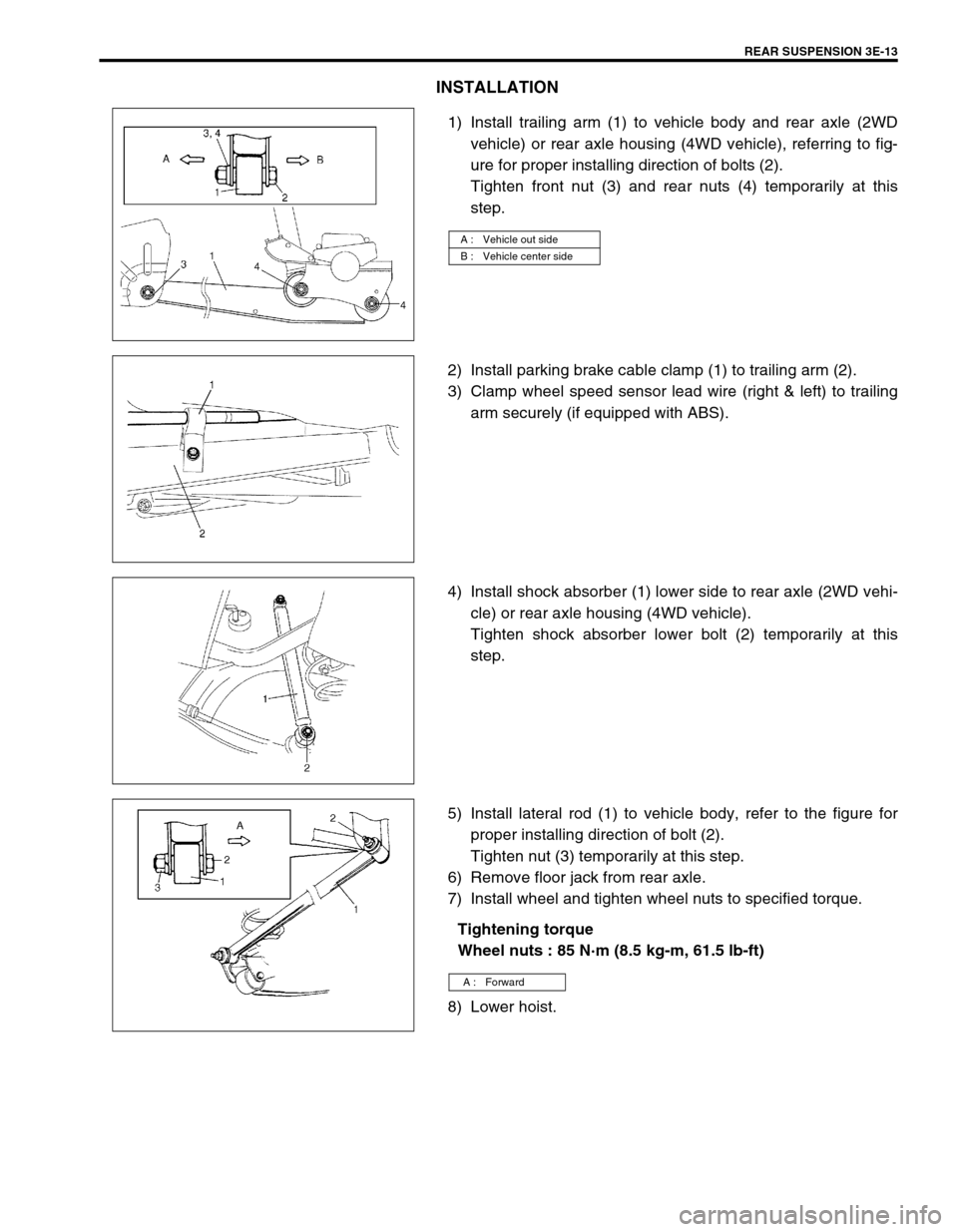
REAR SUSPENSION 3E-13
INSTALLATION
1) Install trailing arm (1) to vehicle body and rear axle (2WD
vehicle) or rear axle housing (4WD vehicle), referring to fig-
ure for proper installing direction of bolts (2).
Tighten front nut (3) and rear nuts (4) temporarily at this
step.
2) Install parking brake cable clamp (1) to trailing arm (2).
3) Clamp wheel speed sensor lead wire (right & left) to trailing
arm securely (if equipped with ABS).
4) Install shock absorber (1) lower side to rear axle (2WD vehi-
cle) or rear axle housing (4WD vehicle).
Tighten shock absorber lower bolt (2) temporarily at this
step.
5) Install lateral rod (1) to vehicle body, refer to the figure for
proper installing direction of bolt (2).
Tighten nut (3) temporarily at this step.
6) Remove floor jack from rear axle.
7) Install wheel and tighten wheel nuts to specified torque.
Tightening torque
Wheel nuts : 85 N·m (8.5 kg-m, 61.5 lb-ft)
8) Lower hoist.
A : Vehicle out side
B : Vehicle center side
A : Forward
Page 228 of 698
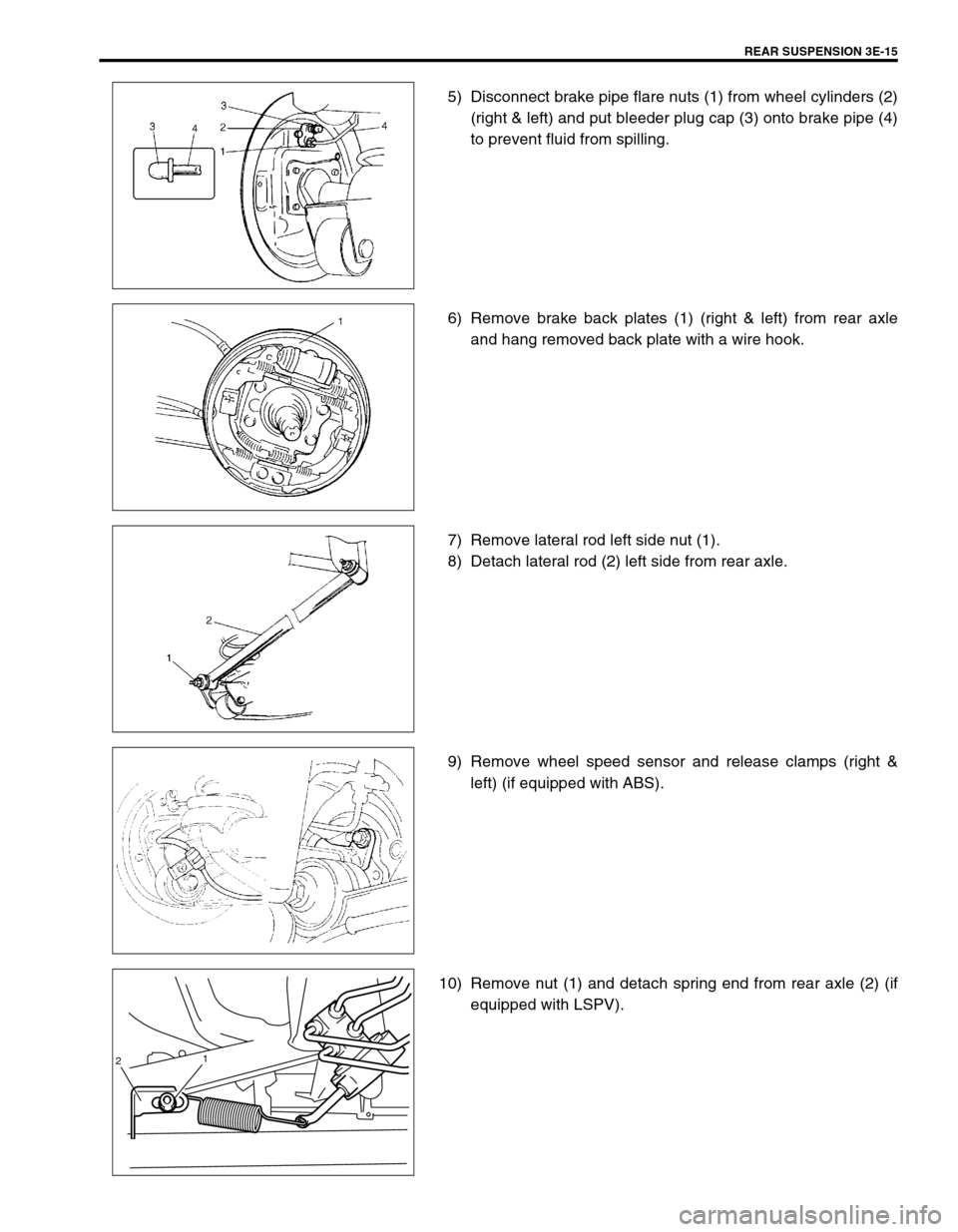
REAR SUSPENSION 3E-15
5) Disconnect brake pipe flare nuts (1) from wheel cylinders (2)
(right & left) and put bleeder plug cap (3) onto brake pipe (4)
to prevent fluid from spilling.
6) Remove brake back plates (1) (right & left) from rear axle
and hang removed back plate with a wire hook.
7) Remove lateral rod left side nut (1).
8) Detach lateral rod (2) left side from rear axle.
9) Remove wheel speed sensor and release clamps (right &
left) (if equipped with ABS).
10) Remove nut (1) and detach spring end from rear axle (2) (if
equipped with LSPV).
21