Torque SUZUKI SWIFT 2000 1.G RG413 Service Service Manual
[x] Cancel search | Manufacturer: SUZUKI, Model Year: 2000, Model line: SWIFT, Model: SUZUKI SWIFT 2000 1.GPages: 698, PDF Size: 16.01 MB
Page 170 of 698
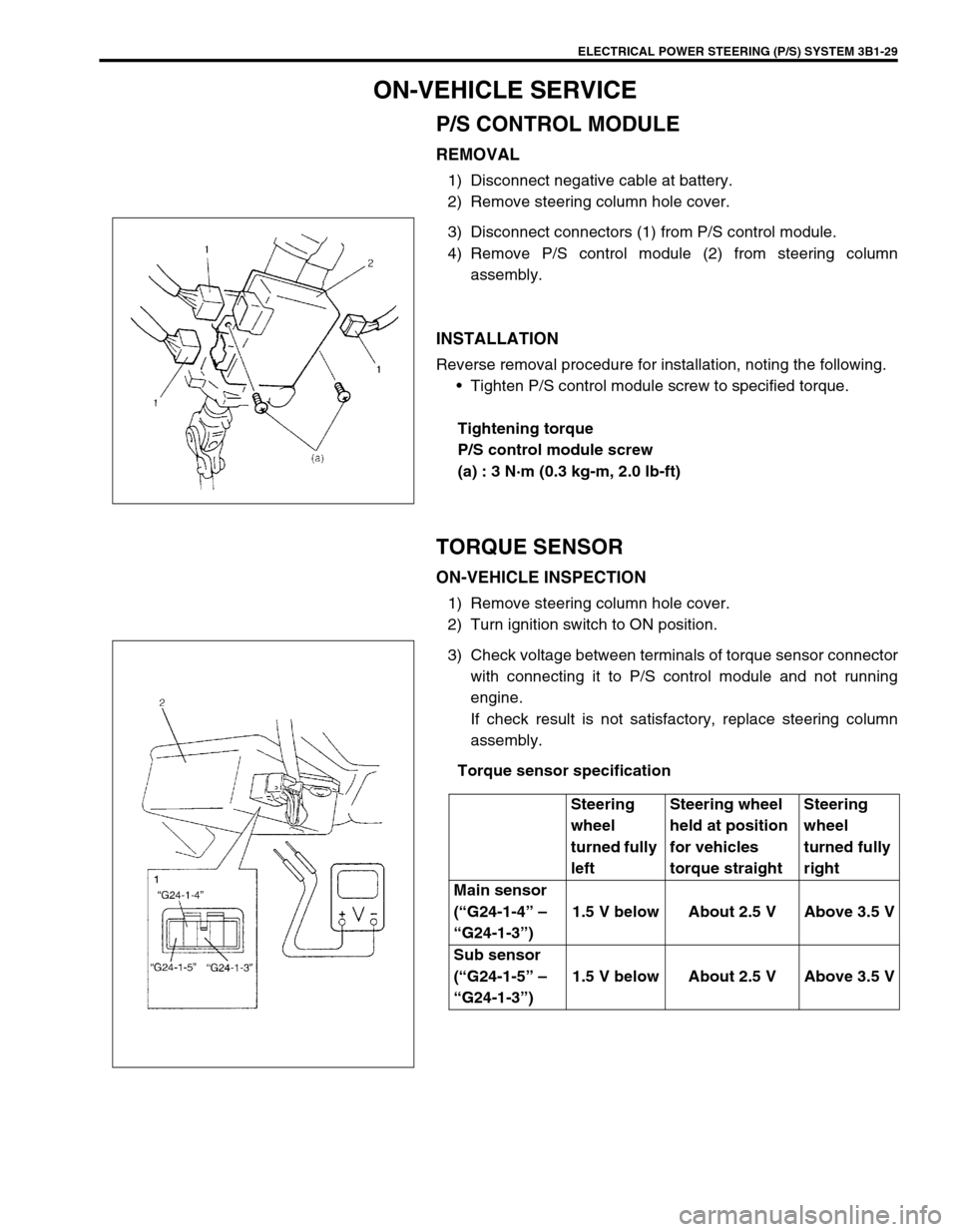
ELECTRICAL POWER STEERING (P/S) SYSTEM 3B1-29
ON-VEHICLE SERVICE
P/S CONTROL MODULE
REMOVAL
1) Disconnect negative cable at battery.
2) Remove steering column hole cover.
3) Disconnect connectors (1) from P/S control module.
4) Remove P/S control module (2) from steering column
assembly.
INSTALLATION
Reverse removal procedure for installation, noting the following.
Tighten P/S control module screw to specified torque.
Tightening torque
P/S control module screw
(a) : 3 N·m (0.3 kg-m, 2.0 lb-ft)
TORQUE SENSOR
ON-VEHICLE INSPECTION
1) Remove steering column hole cover.
2) Turn ignition switch to ON position.
3) Check voltage between terminals of torque sensor connector
with connecting it to P/S control module and not running
engine.
If check result is not satisfactory, replace steering column
assembly.
Torque sensor specification
Steering
wheel
turned fully
leftSteering wheel
held at position
for vehicles
torque straightSteering
wheel
turned fully
right
Main sensor
(“G24-1-4” –
“G24-1-3”)1.5 V below About 2.5 V Above 3.5 V
Sub sensor
(“G24-1-5” –
“G24-1-3”)1.5 V below About 2.5 V Above 3.5 V
Page 174 of 698
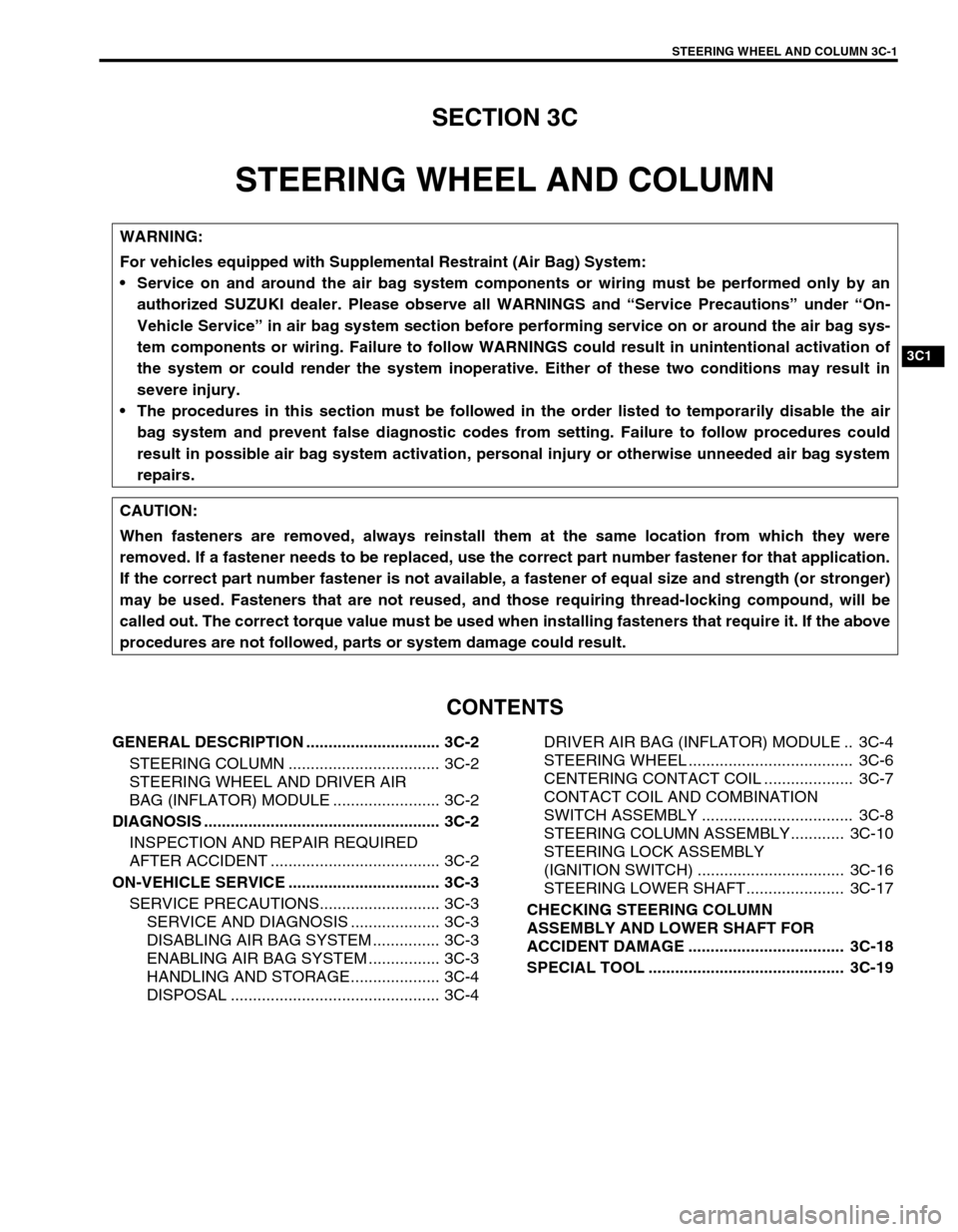
STEERING WHEEL AND COLUMN 3C-1
6F1
6F2
6G
6H
6K
7A
7A1
7B1
3C1
7E
7F
8A
8B
8C
8D
8E
9
10
10A
10B
SECTION 3C
STEERING WHEEL AND COLUMN
CONTENTS
GENERAL DESCRIPTION .............................. 3C-2
STEERING COLUMN .................................. 3C-2
STEERING WHEEL AND DRIVER AIR
BAG (INFLATOR) MODULE ........................ 3C-2
DIAGNOSIS ..................................................... 3C-2
INSPECTION AND REPAIR REQUIRED
AFTER ACCIDENT ...................................... 3C-2
ON-VEHICLE SERVICE .................................. 3C-3
SERVICE PRECAUTIONS........................... 3C-3
SERVICE AND DIAGNOSIS .................... 3C-3
DISABLING AIR BAG SYSTEM ............... 3C-3
ENABLING AIR BAG SYSTEM ................ 3C-3
HANDLING AND STORAGE.................... 3C-4
DISPOSAL ............................................... 3C-4DRIVER AIR BAG (INFLATOR) MODULE .. 3C-4
STEERING WHEEL ..................................... 3C-6
CENTERING CONTACT COIL .................... 3C-7
CONTACT COIL AND COMBINATION
SWITCH ASSEMBLY .................................. 3C-8
STEERING COLUMN ASSEMBLY............ 3C-10
STEERING LOCK ASSEMBLY
(IGNITION SWITCH) ................................. 3C-16
STEERING LOWER SHAFT...................... 3C-17
CHECKING STEERING COLUMN
ASSEMBLY AND LOWER SHAFT FOR
ACCIDENT DAMAGE ................................... 3C-18
SPECIAL TOOL ............................................ 3C-19
WARNING:
For vehicles equipped with Supplemental Restraint (Air Bag) System:
Service on and around the air bag system components or wiring must be performed only by an
authorized SUZUKI dealer. Please observe all WARNINGS and “Service Precautions” under “On-
Vehicle Service” in air bag system section before performing service on or around the air bag sys-
tem components or wiring. Failure to follow WARNINGS could result in unintentional activation of
the system or could render the system inoperative. Either of these two conditions may result in
severe injury.
The procedures in this section must be followed in the order listed to temporarily disable the air
bag system and prevent false diagnostic codes from setting. Failure to follow procedures could
result in possible air bag system activation, personal injury or otherwise unneeded air bag system
repairs.
CAUTION:
When fasteners are removed, always reinstall them at the same location from which they were
removed. If a fastener needs to be replaced, use the correct part number fastener for that application.
If the correct part number fastener is not available, a fastener of equal size and strength (or stronger)
may be used. Fasteners that are not reused, and those requiring thread-locking compound, will be
called out. The correct torque value must be used when installing fasteners that require it. If the above
procedures are not followed, parts or system damage could result.
Page 175 of 698
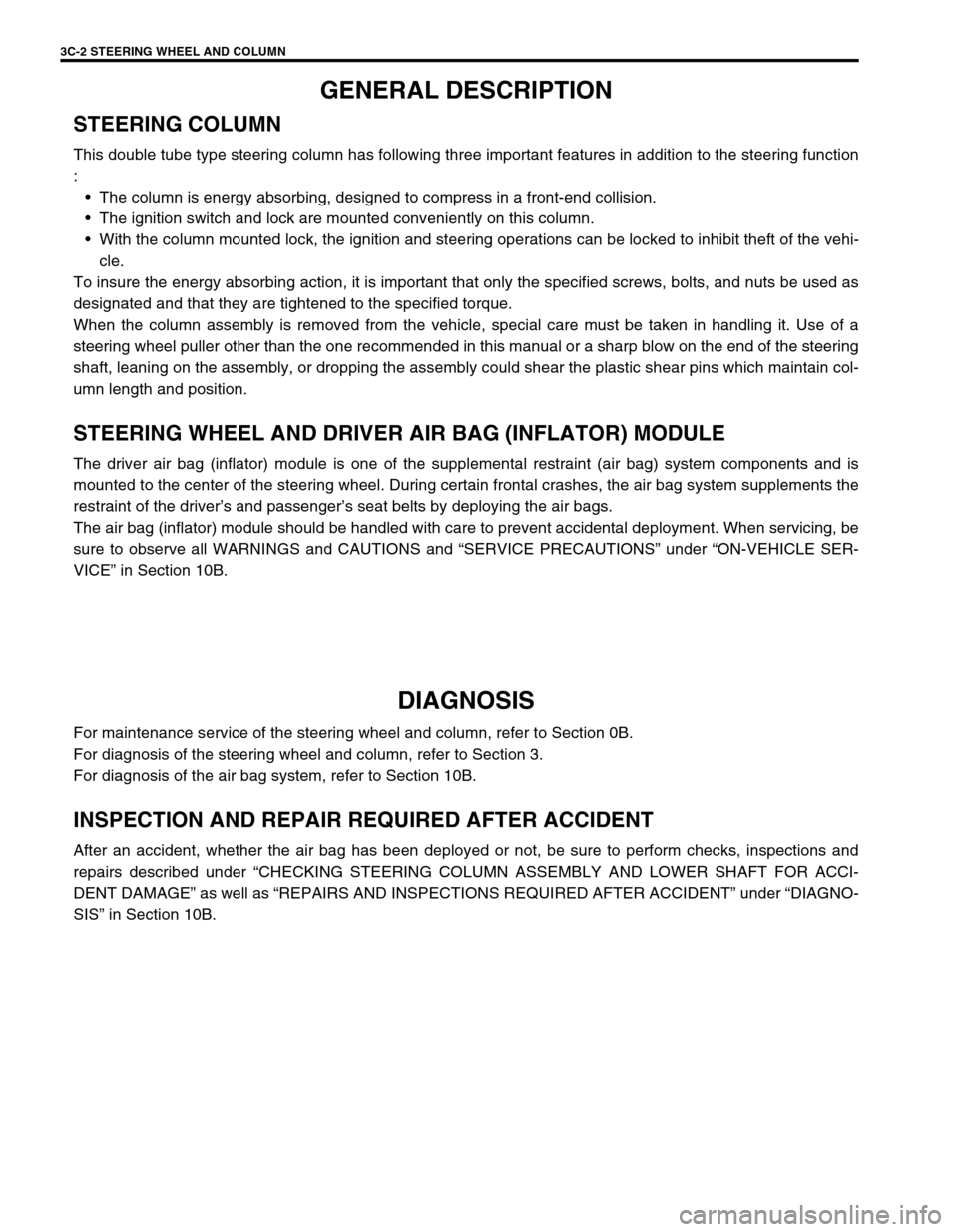
3C-2 STEERING WHEEL AND COLUMN
GENERAL DESCRIPTION
STEERING COLUMN
This double tube type steering column has following three important features in addition to the steering function
:
The column is energy absorbing, designed to compress in a front-end collision.
The ignition switch and lock are mounted conveniently on this column.
With the column mounted lock, the ignition and steering operations can be locked to inhibit theft of the vehi-
cle.
To insure the energy absorbing action, it is important that only the specified screws, bolts, and nuts be used as
designated and that they are tightened to the specified torque.
When the column assembly is removed from the vehicle, special care must be taken in handling it. Use of a
steering wheel puller other than the one recommended in this manual or a sharp blow on the end of the steering
shaft, leaning on the assembly, or dropping the assembly could shear the plastic shear pins which maintain col-
umn length and position.
STEERING WHEEL AND DRIVER AIR BAG (INFLATOR) MODULE
The driver air bag (inflator) module is one of the supplemental restraint (air bag) system components and is
mounted to the center of the steering wheel. During certain frontal crashes, the air bag system supplements the
restraint of the driver’s and passenger’s seat belts by deploying the air bags.
The air bag (inflator) module should be handled with care to prevent accidental deployment. When servicing, be
sure to observe all WARNINGS and CAUTIONS and “SERVICE PRECAUTIONS” under “ON-VEHICLE SER-
VICE” in Section 10B.
DIAGNOSIS
For maintenance service of the steering wheel and column, refer to Section 0B.
For diagnosis of the steering wheel and column, refer to Section 3.
For diagnosis of the air bag system, refer to Section 10B.
INSPECTION AND REPAIR REQUIRED AFTER ACCIDENT
After an accident, whether the air bag has been deployed or not, be sure to perform checks, inspections and
repairs described under “CHECKING STEERING COLUMN ASSEMBLY AND LOWER SHAFT FOR ACCI-
DENT DAMAGE” as well as “REPAIRS AND INSPECTIONS REQUIRED AFTER ACCIDENT” under “DIAGNO-
SIS” in Section 10B.
Page 176 of 698
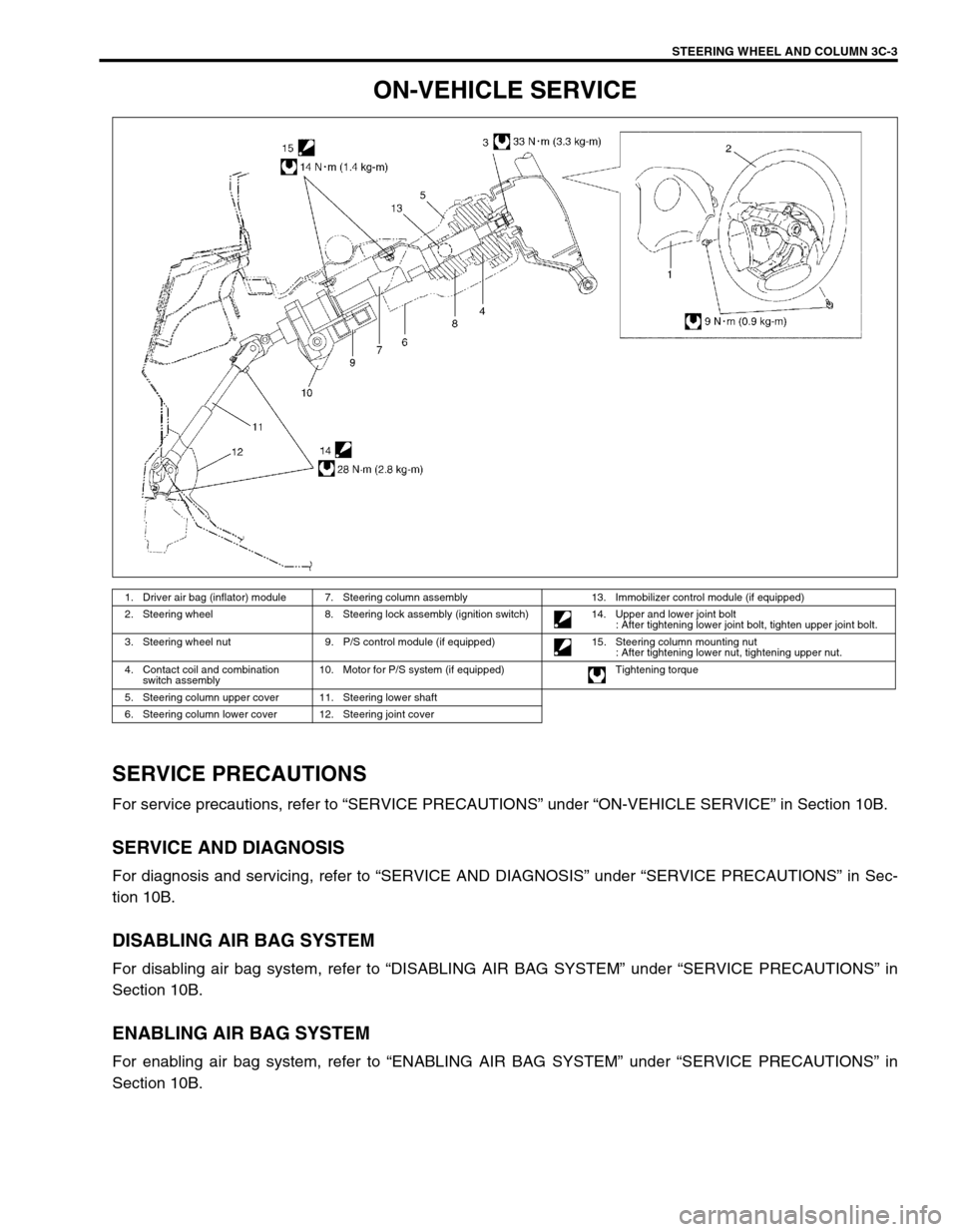
STEERING WHEEL AND COLUMN 3C-3
ON-VEHICLE SERVICE
SERVICE PRECAUTIONS
For service precautions, refer to “SERVICE PRECAUTIONS” under “ON-VEHICLE SERVICE” in Section 10B.
SERVICE AND DIAGNOSIS
For diagnosis and servicing, refer to “SERVICE AND DIAGNOSIS” under “SERVICE PRECAUTIONS” in Sec-
tion 10B.
DISABLING AIR BAG SYSTEM
For disabling air bag system, refer to “DISABLING AIR BAG SYSTEM” under “SERVICE PRECAUTIONS” in
Section 10B.
ENABLING AIR BAG SYSTEM
For enabling air bag system, refer to “ENABLING AIR BAG SYSTEM” under “SERVICE PRECAUTIONS” in
Section 10B.
1. Driver air bag (inflator) module 7. Steering column assembly 13. Immobilizer control module (if equipped)
2. Steering wheel 8. Steering lock assembly (ignition switch) 14. Upper and lower joint bolt
: After tightening lower joint bolt, tighten upper joint bolt.
3. Steering wheel nut 9. P/S control module (if equipped) 15. Steering column mounting nut
: After tightening lower nut, tightening upper nut.
4. Contact coil and combination
switch assembly10. Motor for P/S system (if equipped) Tightening torque
5. Steering column upper cover 11. Steering lower shaft
6. Steering column lower cover 12. Steering joint cover
Page 178 of 698
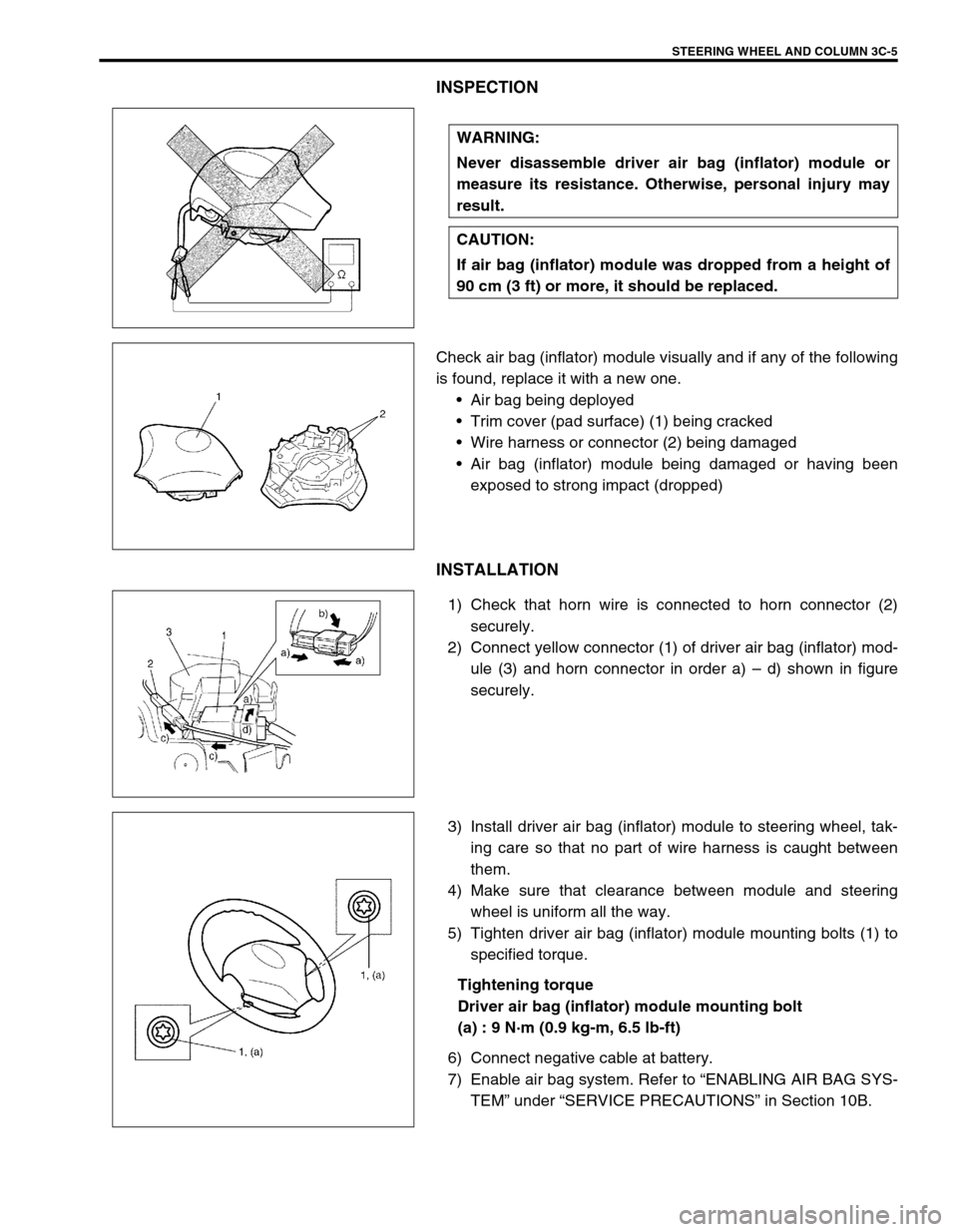
STEERING WHEEL AND COLUMN 3C-5
INSPECTION
Check air bag (inflator) module visually and if any of the following
is found, replace it with a new one.
Air bag being deployed
Trim cover (pad surface) (1) being cracked
Wire harness or connector (2) being damaged
Air bag (inflator) module being damaged or having been
exposed to strong impact (dropped)
INSTALLATION
1) Check that horn wire is connected to horn connector (2)
securely.
2) Connect yellow connector (1) of driver air bag (inflator) mod-
ule (3) and horn connector in order a) – d) shown in figure
securely.
3) Install driver air bag (inflator) module to steering wheel, tak-
ing care so that no part of wire harness is caught between
them.
4) Make sure that clearance between module and steering
wheel is uniform all the way.
5) Tighten driver air bag (inflator) module mounting bolts (1) to
specified torque.
Tightening torque
Driver air bag (inflator) module mounting bolt
(a) : 9 N·m (0.9 kg-m, 6.5 lb-ft)
6) Connect negative cable at battery.
7) Enable air bag system. Refer to “ENABLING AIR BAG SYS-
TEM” under “SERVICE PRECAUTIONS” in Section 10B. WARNING:
Never disassemble driver air bag (inflator) module or
measure its resistance. Otherwise, personal injury may
result.
CAUTION:
If air bag (inflator) module was dropped from a height of
90 cm (3 ft) or more, it should be replaced.
Page 180 of 698
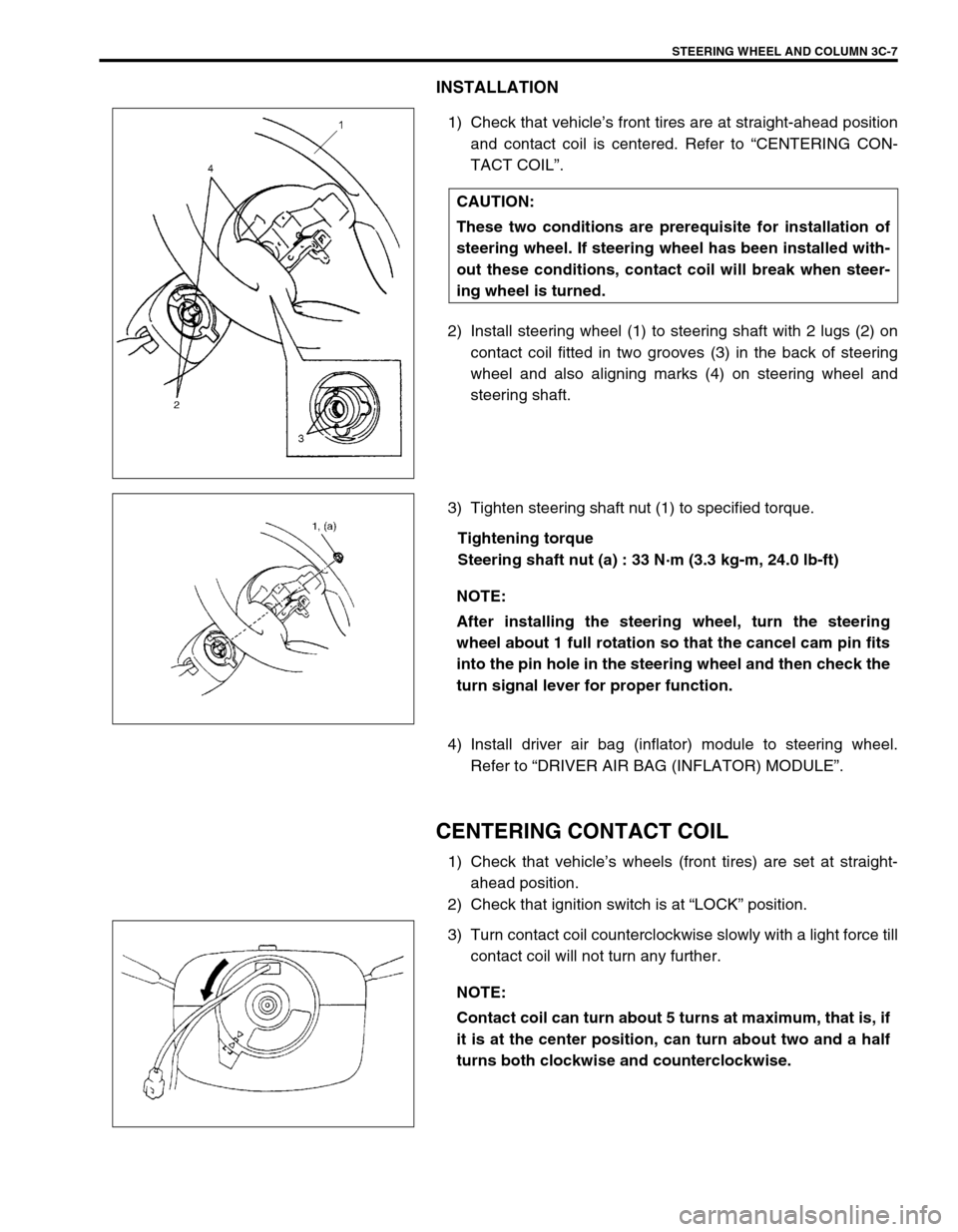
STEERING WHEEL AND COLUMN 3C-7
INSTALLATION
1) Check that vehicle’s front tires are at straight-ahead position
and contact coil is centered. Refer to “CENTERING CON-
TACT COIL”.
2) Install steering wheel (1) to steering shaft with 2 lugs (2) on
contact coil fitted in two grooves (3) in the back of steering
wheel and also aligning marks (4) on steering wheel and
steering shaft.
3) Tighten steering shaft nut (1) to specified torque.
Tightening torque
Steering shaft nut (a) : 33 N·m (3.3 kg-m, 24.0 lb-ft)
4) Install driver air bag (inflator) module to steering wheel.
Refer to “DRIVER AIR BAG (INFLATOR) MODULE”.
CENTERING CONTACT COIL
1) Check that vehicle’s wheels (front tires) are set at straight-
ahead position.
2) Check that ignition switch is at “LOCK” position.
3) Turn contact coil counterclockwise slowly with a light force till
contact coil will not turn any further. CAUTION:
These two conditions are prerequisite for installation of
steering wheel. If steering wheel has been installed with-
out these conditions, contact coil will break when steer-
ing wheel is turned.
NOTE:
After installing the steering wheel, turn the steering
wheel about 1 full rotation so that the cancel cam pin fits
into the pin hole in the steering wheel and then check the
turn signal lever for proper function.
NOTE:
Contact coil can turn about 5 turns at maximum, that is, if
it is at the center position, can turn about two and a half
turns both clockwise and counterclockwise.
Page 188 of 698
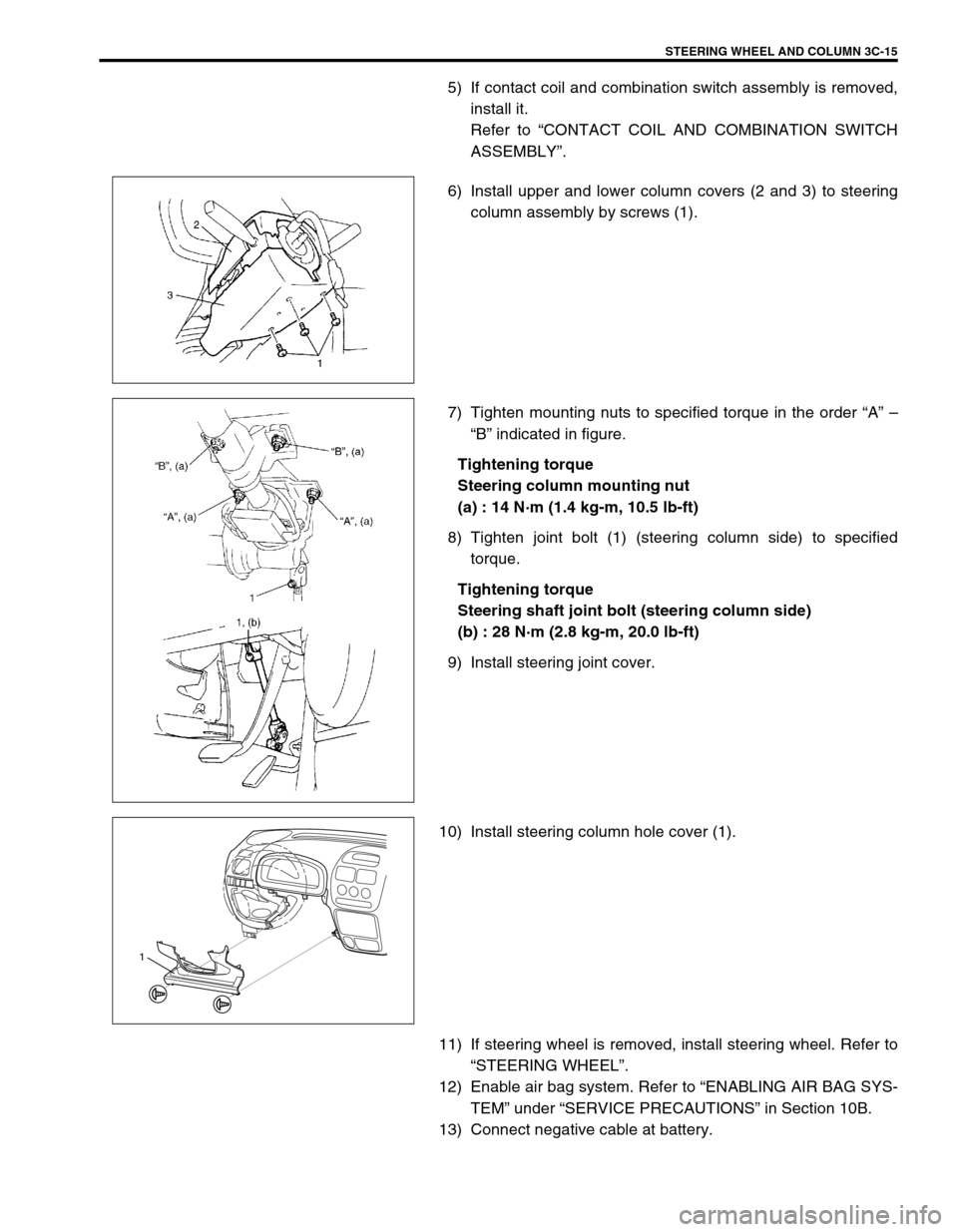
STEERING WHEEL AND COLUMN 3C-15
5) If contact coil and combination switch assembly is removed,
install it.
Refer to “CONTACT COIL AND COMBINATION SWITCH
ASSEMBLY”.
6) Install upper and lower column covers (2 and 3) to steering
column assembly by screws (1).
7) Tighten mounting nuts to specified torque in the order “A” –
“B” indicated in figure.
Tightening torque
Steering column mounting nut
(a) : 14 N·m (1.4 kg-m, 10.5 lb-ft)
8) Tighten joint bolt (1) (steering column side) to specified
torque.
Tightening torque
Steering shaft joint bolt (steering column side)
(b) : 28 N·m (2.8 kg-m, 20.0 lb-ft)
9) Install steering joint cover.
10) Install steering column hole cover (1).
11) If steering wheel is removed, install steering wheel. Refer to
“STEERING WHEEL”.
12) Enable air bag system. Refer to “ENABLING AIR BAG SYS-
TEM” under “SERVICE PRECAUTIONS” in Section 10B.
13) Connect negative cable at battery.
1
Page 191 of 698
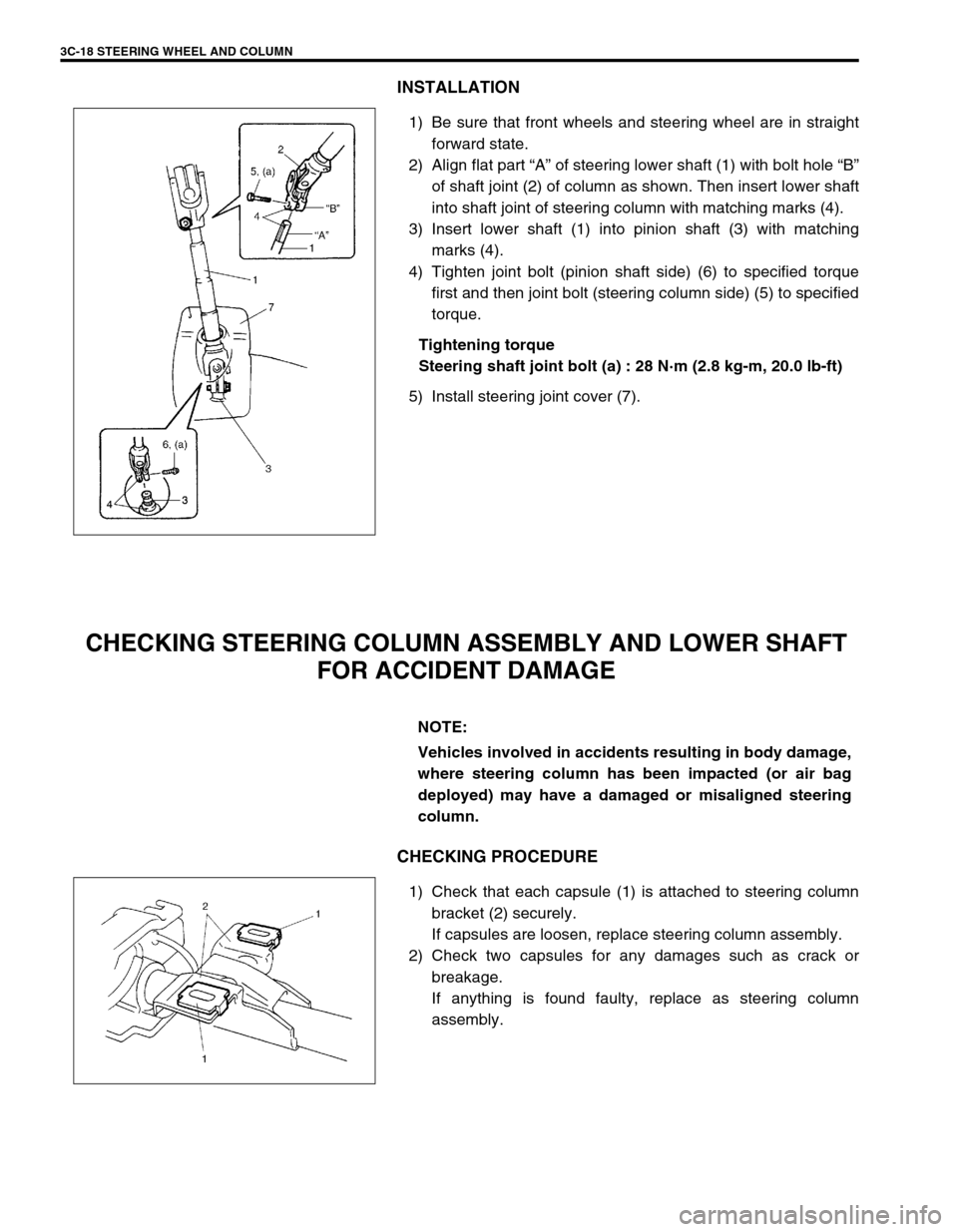
3C-18 STEERING WHEEL AND COLUMN
INSTALLATION
1) Be sure that front wheels and steering wheel are in straight
forward state.
2) Align flat part “A” of steering lower shaft (1) with bolt hole “B”
of shaft joint (2) of column as shown. Then insert lower shaft
into shaft joint of steering column with matching marks (4).
3) Insert lower shaft (1) into pinion shaft (3) with matching
marks (4).
4) Tighten joint bolt (pinion shaft side) (6) to specified torque
first and then joint bolt (steering column side) (5) to specified
torque.
Tightening torque
Steering shaft joint bolt (a) : 28 N·m (2.8 kg-m, 20.0 lb-ft)
5) Install steering joint cover (7).
CHECKING STEERING COLUMN ASSEMBLY AND LOWER SHAFT
FOR ACCIDENT DAMAGE
CHECKING PROCEDURE
1) Check that each capsule (1) is attached to steering column
bracket (2) securely.
If capsules are loosen, replace steering column assembly.
2) Check two capsules for any damages such as crack or
breakage.
If anything is found faulty, replace as steering column
assembly.
NOTE:
Vehicles involved in accidents resulting in body damage,
where steering column has been impacted (or air bag
deployed) may have a damaged or misaligned steering
column.
Page 194 of 698
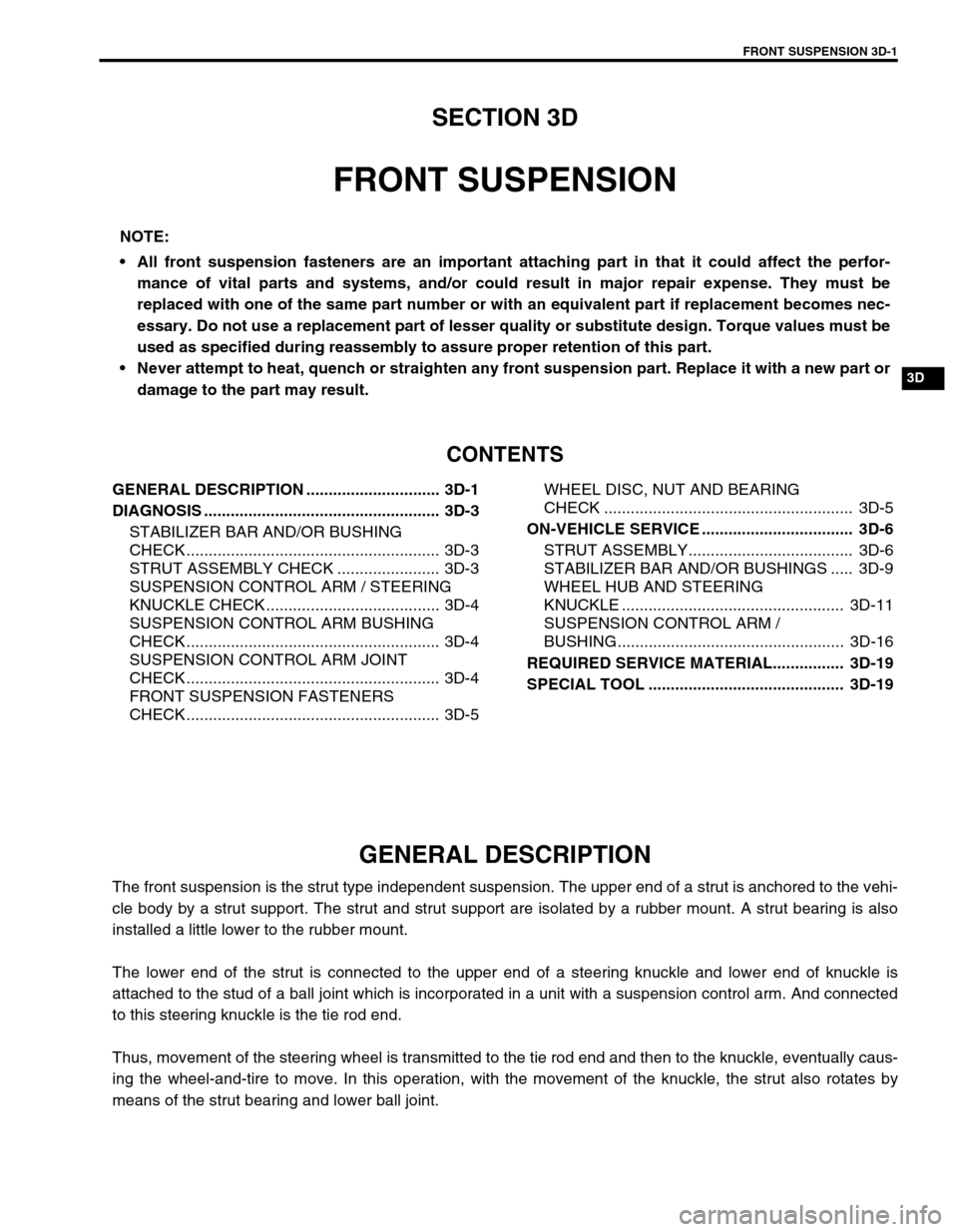
FRONT SUSPENSION 3D-1
6F1
6F2
6G
1A
6K
7A
7A1
7B1
7C1
3D
7F
8A
8B
8C
8D
8E
9
10
10A
10B
SECTION 3D
FRONT SUSPENSION
CONTENTS
GENERAL DESCRIPTION .............................. 3D-1
DIAGNOSIS ..................................................... 3D-3
STABILIZER BAR AND/OR BUSHING
CHECK ......................................................... 3D-3
STRUT ASSEMBLY CHECK ....................... 3D-3
SUSPENSION CONTROL ARM / STEERING
KNUCKLE CHECK ....................................... 3D-4
SUSPENSION CONTROL ARM BUSHING
CHECK ......................................................... 3D-4
SUSPENSION CONTROL ARM JOINT
CHECK ......................................................... 3D-4
FRONT SUSPENSION FASTENERS
CHECK ......................................................... 3D-5WHEEL DISC, NUT AND BEARING
CHECK ........................................................ 3D-5
ON-VEHICLE SERVICE .................................. 3D-6
STRUT ASSEMBLY..................................... 3D-6
STABILIZER BAR AND/OR BUSHINGS ..... 3D-9
WHEEL HUB AND STEERING
KNUCKLE .................................................. 3D-11
SUSPENSION CONTROL ARM /
BUSHING................................................... 3D-16
REQUIRED SERVICE MATERIAL................ 3D-19
SPECIAL TOOL ............................................ 3D-19
GENERAL DESCRIPTION
The front suspension is the strut type independent suspension. The upper end of a strut is anchored to the vehi-
cle body by a strut support. The strut and strut support are isolated by a rubber mount. A strut bearing is also
installed a little lower to the rubber mount.
The lower end of the strut is connected to the upper end of a steering knuckle and lower end of knuckle is
attached to the stud of a ball joint which is incorporated in a unit with a suspension control arm. And connected
to this steering knuckle is the tie rod end.
Thus, movement of the steering wheel is transmitted to the tie rod end and then to the knuckle, eventually caus-
ing the wheel-and-tire to move. In this operation, with the movement of the knuckle, the strut also rotates by
means of the strut bearing and lower ball joint.NOTE:
All front suspension fasteners are an important attaching part in that it could affect the perfor-
mance of vital parts and systems, and/or could result in major repair expense. They must be
replaced with one of the same part number or with an equivalent part if replacement becomes nec-
essary. Do not use a replacement part of lesser quality or substitute design. Torque values must be
used as specified during reassembly to assure proper retention of this part.
Never attempt to heat, quench or straighten any front suspension part. Replace it with a new part or
damage to the part may result.
Page 195 of 698
![SUZUKI SWIFT 2000 1.G RG413 Service Service Manual 3D-2 FRONT SUSPENSION
1. Strut assembly 4. Wheel 7. Drive shaft [A] : FORWARD
2. Stabilizer bar 5. Suspension control arm 8. Tie rod Tightening torque
3. Steering knuckle 6. Vehicle body 9. Brake disc SUZUKI SWIFT 2000 1.G RG413 Service Service Manual 3D-2 FRONT SUSPENSION
1. Strut assembly 4. Wheel 7. Drive shaft [A] : FORWARD
2. Stabilizer bar 5. Suspension control arm 8. Tie rod Tightening torque
3. Steering knuckle 6. Vehicle body 9. Brake disc](/img/20/7606/w960_7606-194.png)
3D-2 FRONT SUSPENSION
1. Strut assembly 4. Wheel 7. Drive shaft [A] : FORWARD
2. Stabilizer bar 5. Suspension control arm 8. Tie rod Tightening torque
3. Steering knuckle 6. Vehicle body 9. Brake disc Do not reuse.
[A]
4
92
35
8
660 N·m(6.0 kg-m) 175 N·m(17.5 kg-m)
60 N·m(6.0 kg-m)
85 N·m(8.5 kg-m)
85 N·m(8.5 kg-m)
43 N·m(4.3 kg-m)
65 N·m(6.5 kg-m)
65 N·m(6.5 kg-m)
23 N·m(2.3 kg-m)
50 N·m(5.0 kg-m)
175 N·m(17.5 kg-m)
105 N·m(10.5 kg-m)
1
8
45 N·m (4.5kg-m) 7
5
4
9