idle SUZUKI SWIFT 2000 1.G SF310 Service Manual Online
[x] Cancel search | Manufacturer: SUZUKI, Model Year: 2000, Model line: SWIFT, Model: SUZUKI SWIFT 2000 1.GPages: 557, PDF Size: 14.35 MB
Page 248 of 557
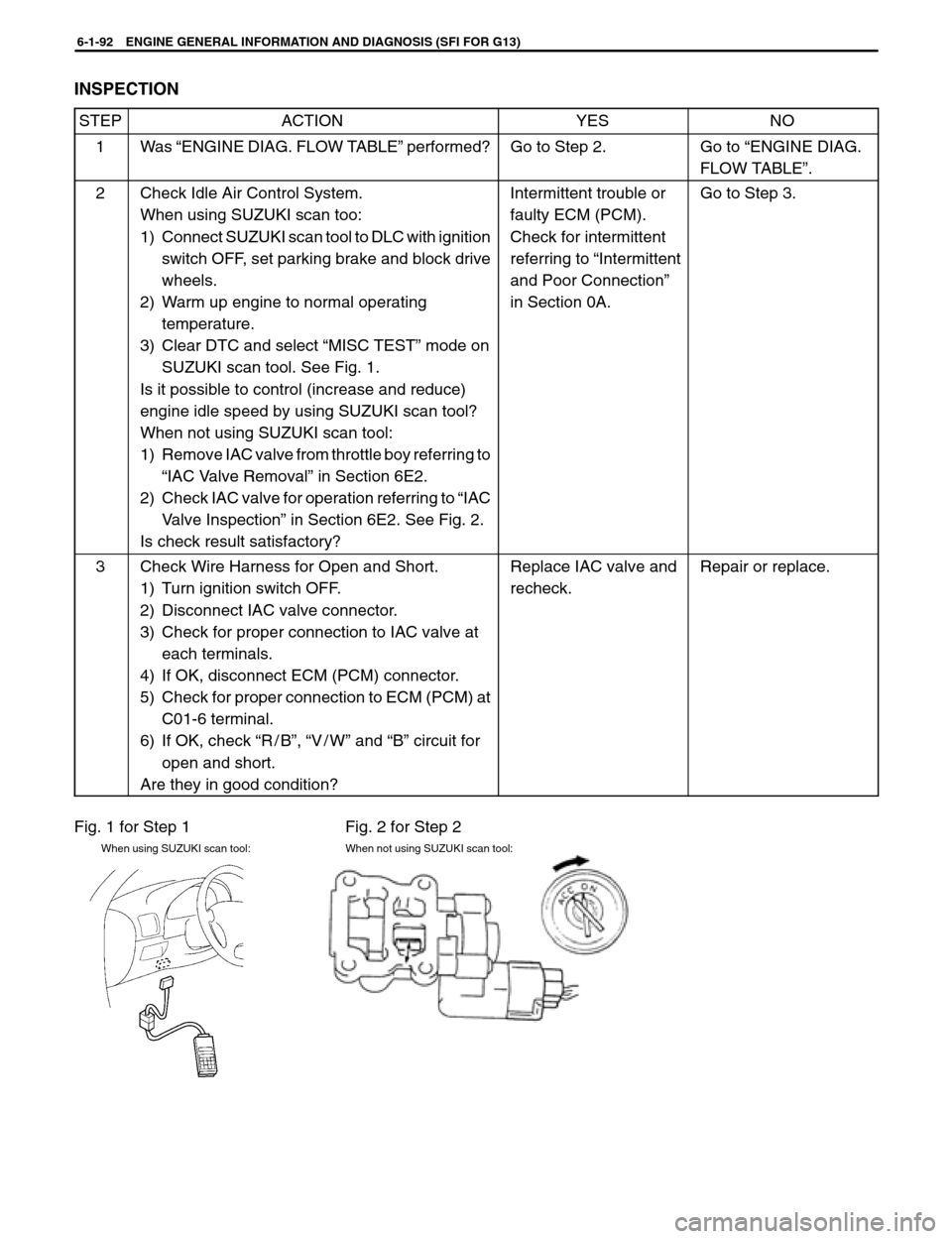
6-1-92 ENGINE GENERAL INFORMATION AND DIAGNOSIS (SFI FOR G13)
Fig. 1 for Step 1 Fig. 2 for Step 2
When using SUZUKI scan tool: When not using SUZUKI scan tool:
INSPECTION
STEPACTIONYESNO
1Was “ENGINE DIAG. FLOW TABLE” performed?Go to Step 2.Go to “ENGINE DIAG.
FLOW TABLE”.
2Check Idle Air Control System.
When using SUZUKI scan too:
1) Connect SUZUKI scan tool to DLC with ignition
switch OFF, set parking brake and block drive
wheels.
2) Warm up engine to normal operating
temperature.
3) Clear DTC and select “MISC TEST” mode on
SUZUKI scan tool. See Fig. 1.
Is it possible to control (increase and reduce)
engine idle speed by using SUZUKI scan tool?
When not using SUZUKI scan tool:
1) Remove IAC valve from throttle boy referring to
“IAC Valve Removal” in Section 6E2.
2) Check IAC valve for operation referring to “IAC
Valve Inspection” in Section 6E2. See Fig. 2.
Is check result satisfactory?Intermittent trouble or
faulty ECM (PCM).
Check for intermittent
referring to “Intermittent
and Poor Connection”
in Section 0A.Go to Step 3.
3Check Wire Harness for Open and Short.
1) Turn ignition switch OFF.
2) Disconnect IAC valve connector.
3) Check for proper connection to IAC valve at
each terminals.
4) If OK, disconnect ECM (PCM) connector.
5) Check for proper connection to ECM (PCM) at
C01-6 terminal.
6) If OK, check “R/B”, “V/W” and “B” circuit for
open and short.
Are they in good condition?Replace IAC valve and
recheck.Repair or replace.
Page 249 of 557
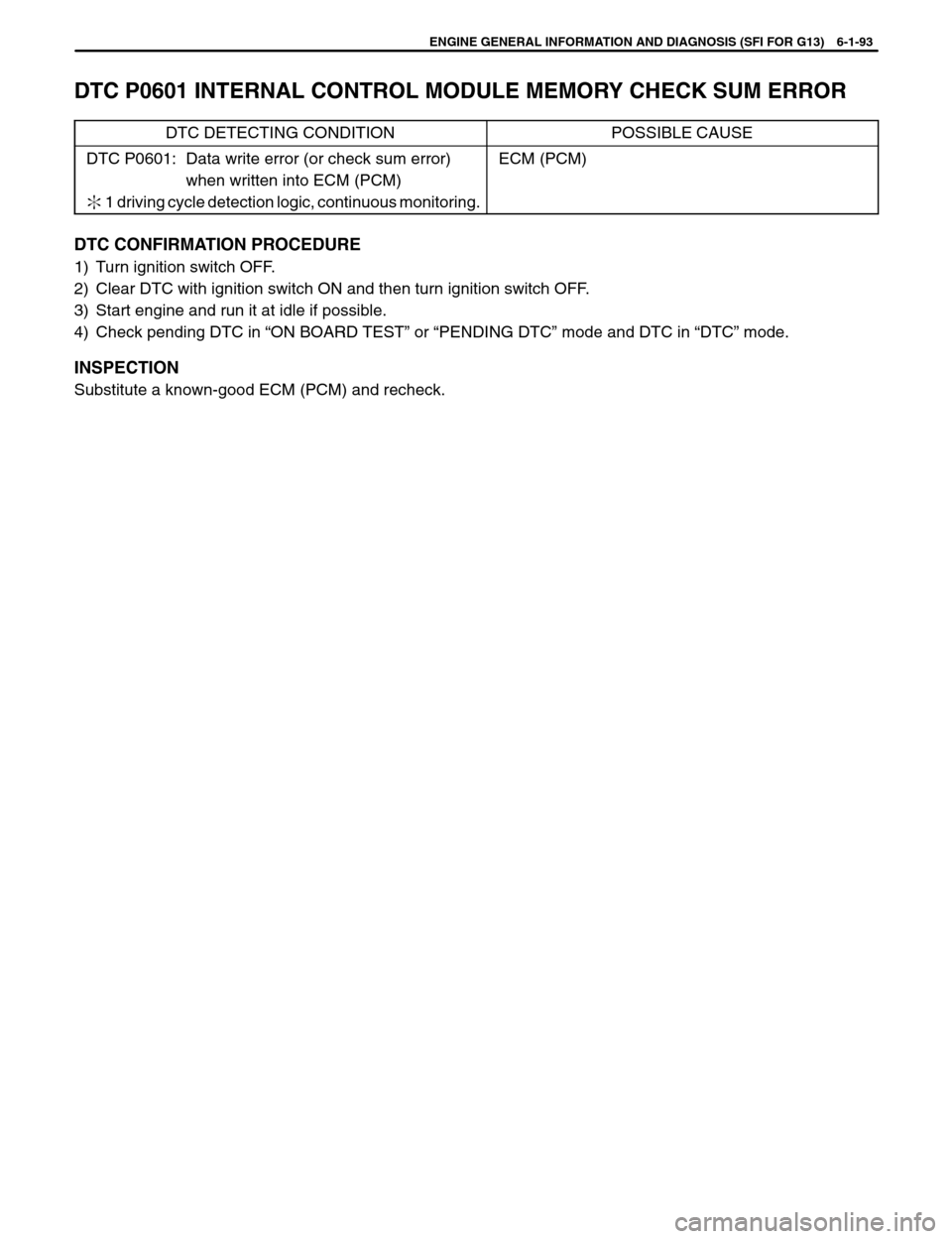
ENGINE GENERAL INFORMATION AND DIAGNOSIS (SFI FOR G13) 6-1-93
DTC P0601 INTERNAL CONTROL MODULE MEMORY CHECK SUM ERROR
DTC DETECTING CONDITIONPOSSIBLE CAUSE
DTC P0601: Data write error (or check sum error)
when written into ECM (PCM)
1 driving cycle detection logic, continuous monitoring.ECM (PCM)
DTC CONFIRMATION PROCEDURE
1) Turn ignition switch OFF.
2) Clear DTC with ignition switch ON and then turn ignition switch OFF.
3) Start engine and run it at idle if possible.
4) Check pending DTC in “ON BOARD TEST” or “PENDING DTC” mode and DTC in “DTC” mode.
INSPECTION
Substitute a known-good ECM (PCM) and recheck.
Page 250 of 557
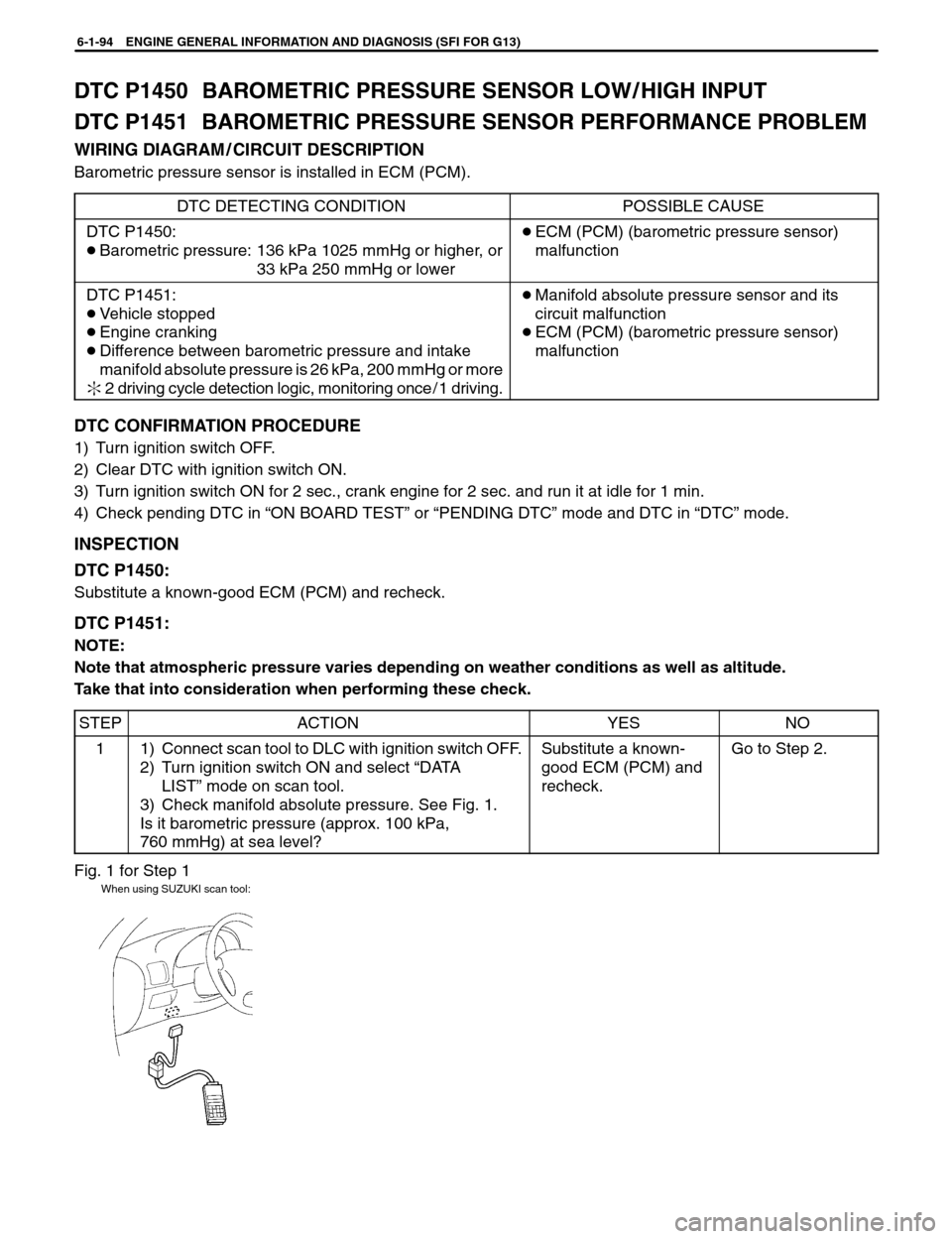
6-1-94 ENGINE GENERAL INFORMATION AND DIAGNOSIS (SFI FOR G13)
Fig. 1 for Step 1
When using SUZUKI scan tool:
DTC P1450 BAROMETRIC PRESSURE SENSOR LOW / HIGH INPUT
DTC P1451 BAROMETRIC PRESSURE SENSOR PERFORMANCE PROBLEM
WIRING DIAGRAM / CIRCUIT DESCRIPTION
Barometric pressure sensor is installed in ECM (PCM).
DTC DETECTING CONDITION
POSSIBLE CAUSE
DTC P1450:
Barometric pressure: 136 kPa 1025 mmHg or higher, or
33 kPa 250 mmHg or lowerECM (PCM) (barometric pressure sensor)
malfunction
DTC P1451:
Vehicle stopped
Engine cranking
Difference between barometric pressure and intake
manifold absolute pressure is 26 kPa, 200 mmHg or more
2 driving cycle detection logic, monitoring once / 1 driving.Manifold absolute pressure sensor and its
circuit malfunction
ECM (PCM) (barometric pressure sensor)
malfunction
DTC CONFIRMATION PROCEDURE
1) Turn ignition switch OFF.
2) Clear DTC with ignition switch ON.
3) Turn ignition switch ON for 2 sec., crank engine for 2 sec. and run it at idle for 1 min.
4) Check pending DTC in “ON BOARD TEST” or “PENDING DTC” mode and DTC in “DTC” mode.
INSPECTION
DTC P1450:
Substitute a known-good ECM (PCM) and recheck.
DTC P1451:
NOTE:
Note that atmospheric pressure varies depending on weather conditions as well as altitude.
Take that into consideration when performing these check.
STEP
ACTIONYESNO
11) Connect scan tool to DLC with ignition switch OFF.
2) Turn ignition switch ON and select “DATA
LIST” mode on scan tool.
3) Check manifold absolute pressure. See Fig. 1.
Is it barometric pressure (approx. 100 kPa,
760 mmHg) at sea level?Substitute a known-
good ECM (PCM) and
recheck.Go to Step 2.
Page 252 of 557
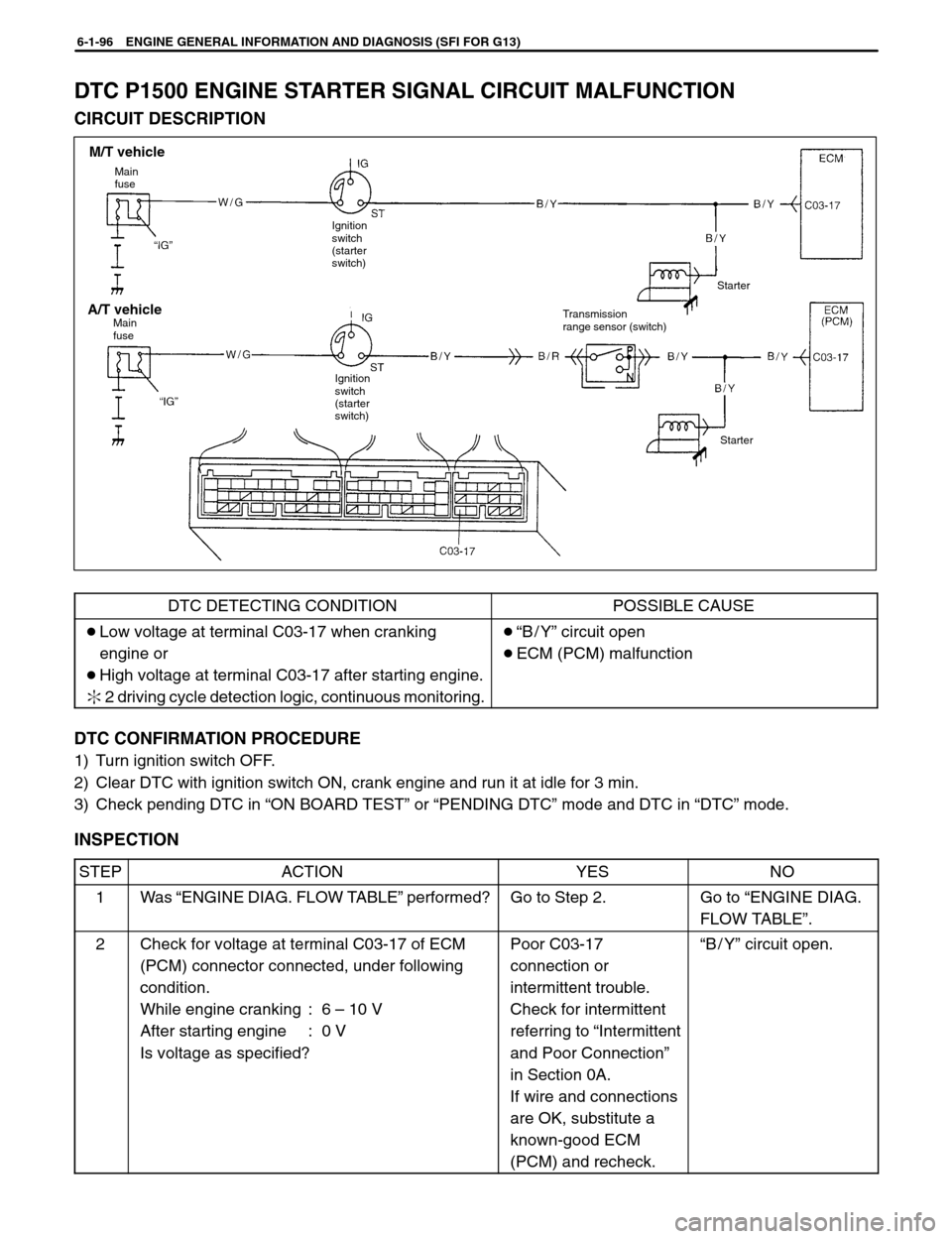
6-1-96 ENGINE GENERAL INFORMATION AND DIAGNOSIS (SFI FOR G13)
Main
fuse
M/T vehicle
A/T vehicle
Ignition
switch
(starter
switch)
Starter
Starter Transmission
range sensor (switch) Main
fuse
Ignition
switch
(starter
switch)
DTC P1500 ENGINE STARTER SIGNAL CIRCUIT MALFUNCTION
CIRCUIT DESCRIPTION
DTC DETECTING CONDITIONPOSSIBLE CAUSE
Low voltage at terminal C03-17 when cranking
engine or
High voltage at terminal C03-17 after starting engine.
2 driving cycle detection logic, continuous monitoring.“B/Y” circuit open
ECM (PCM) malfunction
DTC CONFIRMATION PROCEDURE
1) Turn ignition switch OFF.
2) Clear DTC with ignition switch ON, crank engine and run it at idle for 3 min.
3) Check pending DTC in “ON BOARD TEST” or “PENDING DTC” mode and DTC in “DTC” mode.
INSPECTION
STEPACTIONYESNO
1Was “ENGINE DIAG. FLOW TABLE” performed?Go to Step 2.Go to “ENGINE DIAG.
FLOW TABLE”.
2Check for voltage at terminal C03-17 of ECM
(PCM) connector connected, under following
condition.
While engine cranking : 6 – 10 V
After starting engine : 0 V
Is voltage as specified?Poor C03-17
connection or
intermittent trouble.
Check for intermittent
referring to “Intermittent
and Poor Connection”
in Section 0A.
If wire and connections
are OK, substitute a
known-good ECM
(PCM) and recheck.“B/Y” circuit open.
Page 253 of 557
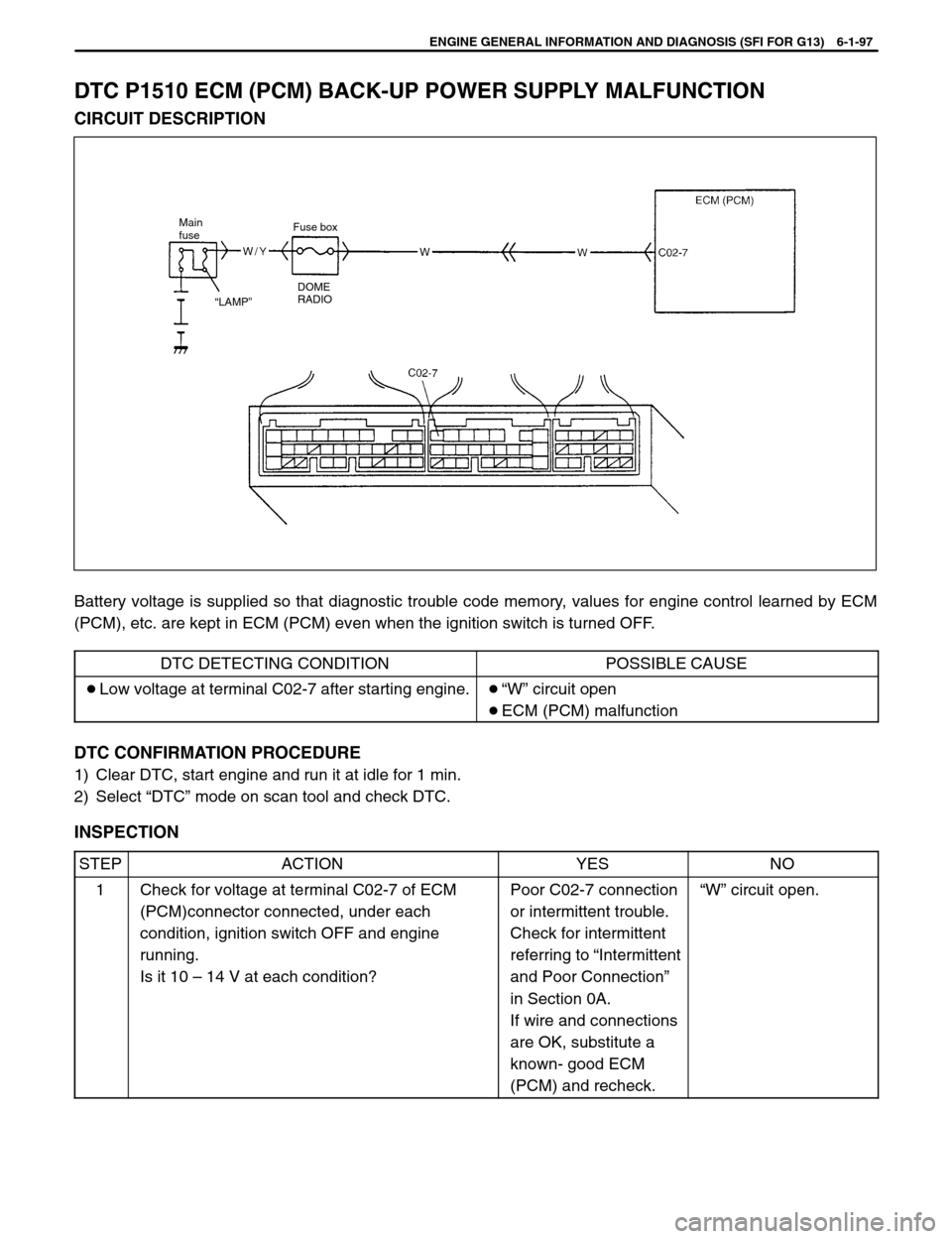
ENGINE GENERAL INFORMATION AND DIAGNOSIS (SFI FOR G13) 6-1-97
Fuse box Main
fuse
DOME
RADIO
“LAMP”
DTC P1510 ECM (PCM) BACK-UP POWER SUPPLY MALFUNCTION
CIRCUIT DESCRIPTION
Battery voltage is supplied so that diagnostic trouble code memory, values for engine control learned by ECM
(PCM), etc. are kept in ECM (PCM) even when the ignition switch is turned OFF.
DTC DETECTING CONDITION
POSSIBLE CAUSE
Low voltage at terminal C02-7 after starting engine.“W” circuit open
ECM (PCM) malfunction
DTC CONFIRMATION PROCEDURE
1) Clear DTC, start engine and run it at idle for 1 min.
2) Select “DTC” mode on scan tool and check DTC.
INSPECTION
STEPACTIONYESNO
1Check for voltage at terminal C02-7 of ECM
(PCM)connector connected, under each
condition, ignition switch OFF and engine
running.
Is it 10 – 14 V at each condition?Poor C02-7 connection
or intermittent trouble.
Check for intermittent
referring to “Intermittent
and Poor Connection”
in Section 0A.
If wire and connections
are OK, substitute a
known- good ECM
(PCM) and recheck.“W” circuit open.
Page 257 of 557

ENGINE GENERAL INFORMATION AND DIAGNOSIS (SFI FOR G13) 6-1-101
1. Fuel injector
2. Delivery pipe
3. Fuel regulator
4. Fuel filter
5. Fuel pump
Special Tool
(A) Gauge (09912-58441)
(B) Hose (09912-58431)
(C) 3-way joint (09912-58490)
TABLE B-3 FUEL PRESSURE CHECK
INSPECTION
STEPACTIONYESON
11) Release fuel pressure from fuel feed line.
2) Install fuel pressure gauge.
3) Check fuel pressure by repeating ignition switch
ON and OFF.
Is fuel pressure then 270 – 310 kPa
(2.7 – 3.1 kg / cm
2, 38.4 – 44.0 psi)?
Go to Step 2.Go to Step 5.
2Is 200 kPa (2.0 kg / cm2, 28.4 psi) or higher fuel
pressure retained for 1 minute after fuel pump is
stopped at step 1?Go to Step 3.Go to Step 4.
31) Start engine and warm it up to normal operating
temperature.
2) Keep it running at specified idle speed.
Is fuel pressure then within 200 – 240 kPa
(2.0 – 2.4 kg / cm
2, 28.4 – 34.1 psi)?
Normal fuel pressure.Clogged vacuum
passage for fuel
pressure regulator or
faulty fuel pressure
regulator.
4Is there fuel leakage from fuel feed line hose, pipe or
their joint?Fuel leakage from
hose, pipe or joint.Go to Step 10.
5Was fuel pressure higher than spec. in step 1?Go to Step 6.Go to Step 7.
61) Disconnect fuel return hose from fuel pressure
regulator and connect new return hose to it.
2) Put the other end of new return hose into approved
gasoline container.
3) Operate fuel pump.
Is specified fuel pressure obtained then?Restricted fuel return
hose or pipe.Faulty fuel pressure
regulator.
Page 259 of 557
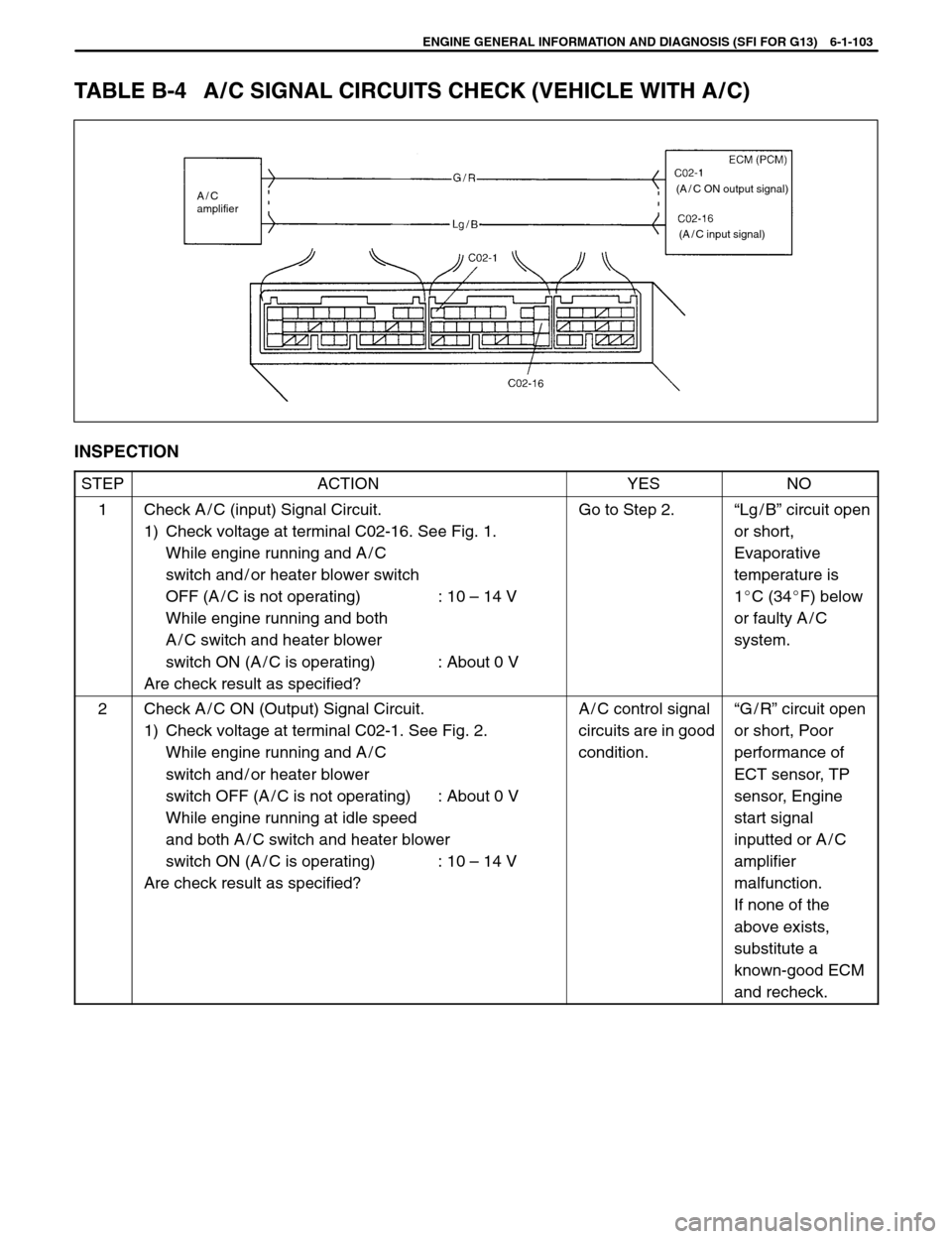
ENGINE GENERAL INFORMATION AND DIAGNOSIS (SFI FOR G13) 6-1-103
A/C
amplifier(A / C ON output signal)
(A / C input signal)
TABLE B-4 A / C SIGNAL CIRCUITS CHECK (VEHICLE WITH A / C)
INSPECTION
STEPACTIONYESNO
1Check A / C (input) Signal Circuit.
1) Check voltage at terminal C02-16. See Fig. 1.
While engine running and A / C
switch and / or heater blower switch
OFF (A / C is not operating) : 10 – 14 V
While engine running and both
A / C switch and heater blower
switch ON (A / C is operating) : About 0 V
Are check result as specified?Go to Step 2.“Lg / B” circuit open
or short,
Evaporative
temperature is
1C (34F) below
or faulty A / C
system.
2Check A / C ON (Output) Signal Circuit.
1) Check voltage at terminal C02-1. See Fig. 2.
While engine running and A / C
switch and / or heater blower
switch OFF (A / C is not operating) : About 0 V
While engine running at idle speed
and both A / C switch and heater blower
switch ON (A / C is operating) : 10 – 14 V
Are check result as specified?A / C control signal
circuits are in good
condition.“G/R” circuit open
or short, Poor
performance of
ECT sensor, TP
sensor, Engine
start signal
inputted or A / C
amplifier
malfunction.
If none of the
above exists,
substitute a
known-good ECM
and recheck.
Page 266 of 557
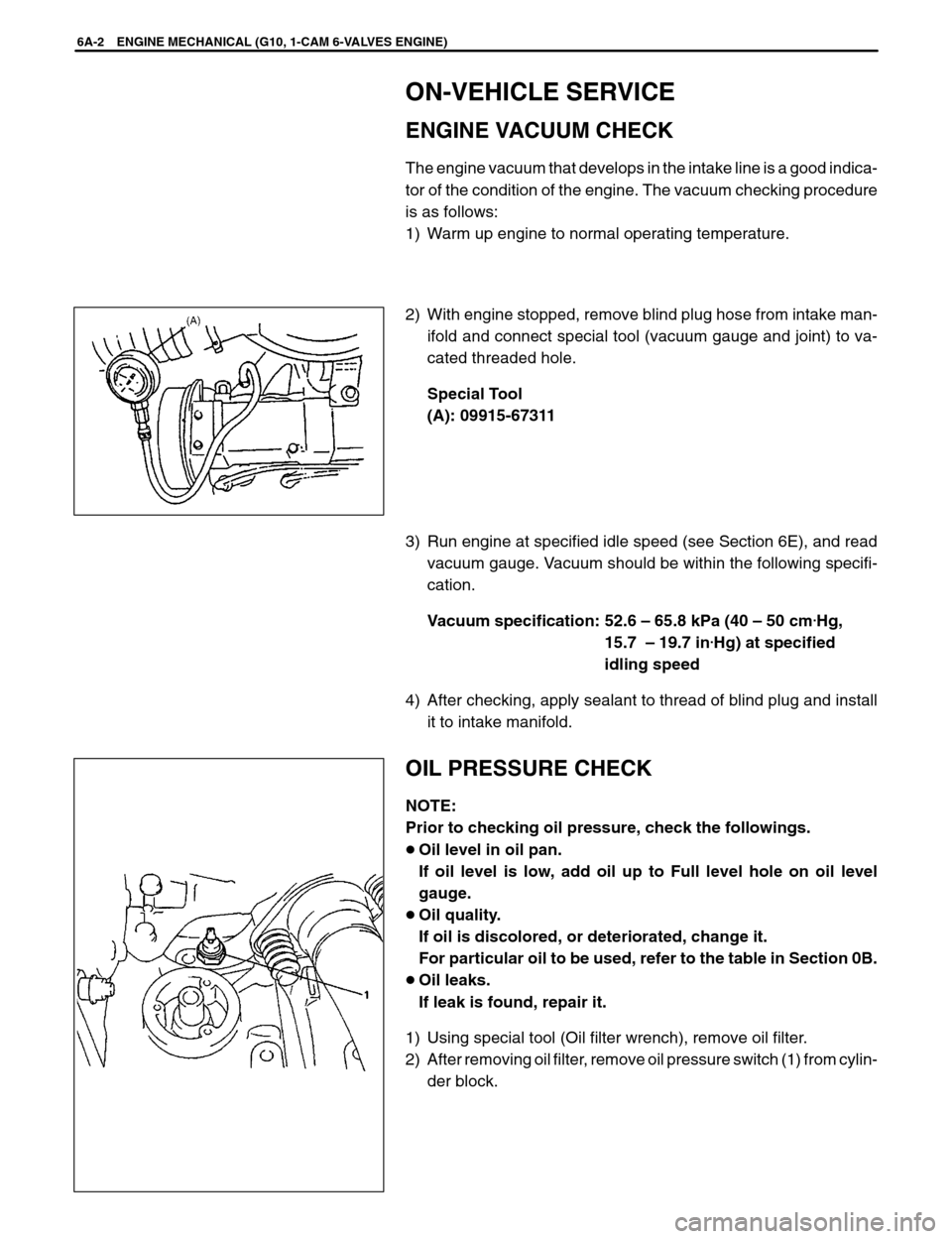
6A-2 ENGINE MECHANICAL (G10, 1-CAM 6-VALVES ENGINE)
ON-VEHICLE SERVICE
ENGINE VACUUM CHECK
The engine vacuum that develops in the intake line is a good indica-
tor of the condition of the engine. The vacuum checking procedure
is as follows:
1) Warm up engine to normal operating temperature.
2) With engine stopped, remove blind plug hose from intake man-
ifold and connect special tool (vacuum gauge and joint) to va-
cated threaded hole.
Special Tool
(A): 09915-67311
3) Run engine at specified idle speed (see Section 6E), and read
vacuum gauge. Vacuum should be within the following specifi-
cation.
Vacuum specification: 52.6 – 65.8 kPa (40 – 50 cm
.Hg,
15.7 – 19.7 in
.Hg) at specified
idling speed
4) After checking, apply sealant to thread of blind plug and install
it to intake manifold.
OIL PRESSURE CHECK
NOTE:
Prior to checking oil pressure, check the followings.
Oil level in oil pan.
If oil level is low, add oil up to Full level hole on oil level
gauge.
Oil quality.
If oil is discolored, or deteriorated, change it.
For particular oil to be used, refer to the table in Section 0B.
Oil leaks.
If leak is found, repair it.
1) Using special tool (Oil filter wrench), remove oil filter.
2) After removing oil filter, remove oil pressure switch (1) from cylin-
der block.
Page 301 of 557
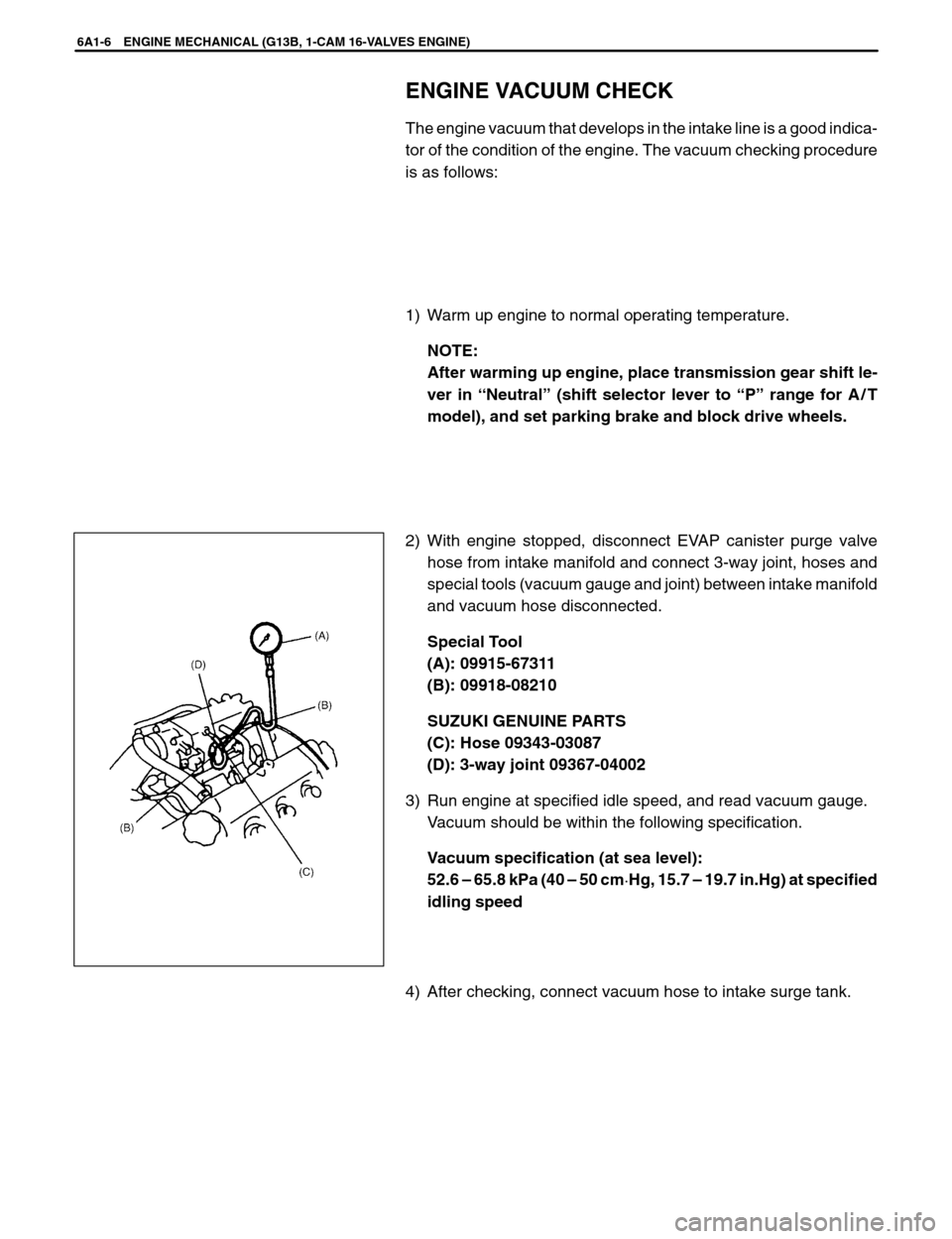
6A1-6 ENGINE MECHANICAL (G13B, 1-CAM 16-VALVES ENGINE)
ENGINE VACUUM CHECK
The engine vacuum that develops in the intake line is a good indica-
tor of the condition of the engine. The vacuum checking procedure
is as follows:
1) Warm up engine to normal operating temperature.
NOTE:
After warming up engine, place transmission gear shift le-
ver in “Neutral” (shift selector lever to “P” range for A / T
model), and set parking brake and block drive wheels.
2) With engine stopped, disconnect EVAP canister purge valve
hose from intake manifold and connect 3-way joint, hoses and
special tools (vacuum gauge and joint) between intake manifold
and vacuum hose disconnected.
Special Tool
(A): 09915-67311
(B): 09918-08210
SUZUKI GENUINE PARTS
(C): Hose 09343-03087
(D): 3-way joint 09367-04002
3) Run engine at specified idle speed, and read vacuum gauge.
Vacuum should be within the following specification.
Vacuum specification (at sea level):
52.6 – 65.8 kPa (40 – 50 cmHg, 15.7 – 19.7 in.Hg) at specified
idling speed
4) After checking, connect vacuum hose to intake surge tank.
Page 392 of 557
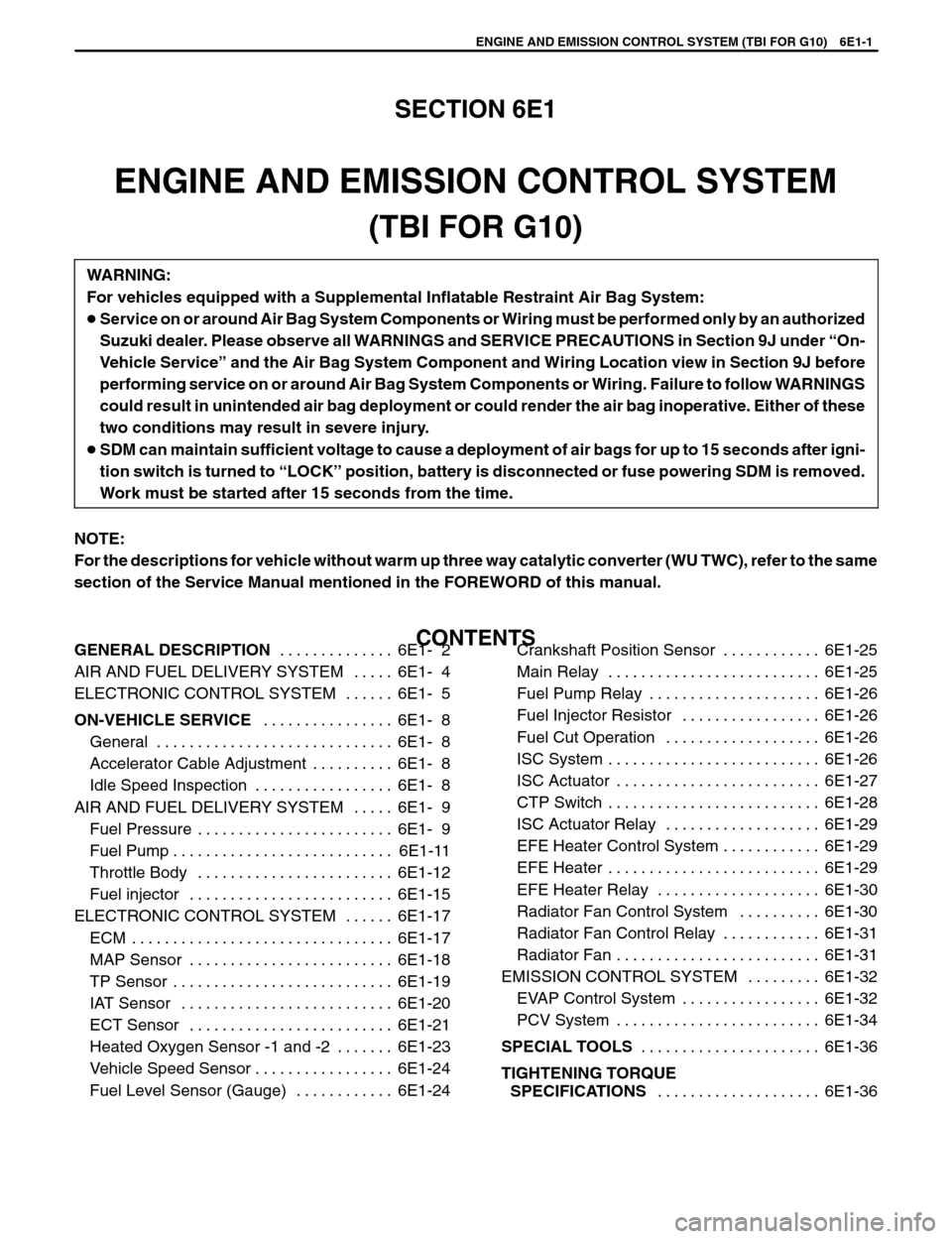
ENGINE AND EMISSION CONTROL SYSTEM (TBI FOR G10) 6E1-1
GENERAL DESCRIPTION6E1- 2 . . . . . . . . . . . . . .
AIR AND FUEL DELIVERY SYSTEM 6E1- 4. . . . .
ELECTRONIC CONTROL SYSTEM 6E1- 5. . . . . .
ON-VEHICLE SERVICE6E1- 8 . . . . . . . . . . . . . . . .
General 6E1- 8. . . . . . . . . . . . . . . . . . . . . . . . . . . . .
Accelerator Cable Adjustment 6E1- 8. . . . . . . . . .
Idle Speed Inspection 6E1- 8. . . . . . . . . . . . . . . . .
AIR AND FUEL DELIVERY SYSTEM 6E1- 9. . . . .
Fuel Pressure 6E1- 9. . . . . . . . . . . . . . . . . . . . . . . .
Fuel Pump 6E1-11. . . . . . . . . . . . . . . . . . . . . . . . . . .
Throttle Body 6E1-12. . . . . . . . . . . . . . . . . . . . . . . .
Fuel injector 6E1-15. . . . . . . . . . . . . . . . . . . . . . . . .
ELECTRONIC CONTROL SYSTEM 6E1-17. . . . . .
ECM 6E1-17. . . . . . . . . . . . . . . . . . . . . . . . . . . . . . . .
MAP Sensor 6E1-18. . . . . . . . . . . . . . . . . . . . . . . . .
TP Sensor 6E1-19. . . . . . . . . . . . . . . . . . . . . . . . . . .
IAT Sensor 6E1-20. . . . . . . . . . . . . . . . . . . . . . . . . .
ECT Sensor 6E1-21. . . . . . . . . . . . . . . . . . . . . . . . .
Heated Oxygen Sensor -1 and -2 6E1-23. . . . . . .
Vehicle Speed Sensor 6E1-24. . . . . . . . . . . . . . . . .
Fuel Level Sensor (Gauge) 6E1-24. . . . . . . . . . . . Crankshaft Position Sensor 6E1-25. . . . . . . . . . . .
Main Relay 6E1-25. . . . . . . . . . . . . . . . . . . . . . . . . .
Fuel Pump Relay 6E1-26. . . . . . . . . . . . . . . . . . . . .
Fuel Injector Resistor 6E1-26. . . . . . . . . . . . . . . . .
Fuel Cut Operation 6E1-26. . . . . . . . . . . . . . . . . . .
ISC System 6E1-26. . . . . . . . . . . . . . . . . . . . . . . . . .
ISC Actuator 6E1-27. . . . . . . . . . . . . . . . . . . . . . . . .
CTP Switch 6E1-28. . . . . . . . . . . . . . . . . . . . . . . . . .
ISC Actuator Relay 6E1-29. . . . . . . . . . . . . . . . . . .
EFE Heater Control System 6E1-29. . . . . . . . . . . .
EFE Heater 6E1-29. . . . . . . . . . . . . . . . . . . . . . . . . .
EFE Heater Relay 6E1-30. . . . . . . . . . . . . . . . . . . .
Radiator Fan Control System 6E1-30. . . . . . . . . .
Radiator Fan Control Relay 6E1-31. . . . . . . . . . . .
Radiator Fan 6E1-31. . . . . . . . . . . . . . . . . . . . . . . . .
EMISSION CONTROL SYSTEM 6E1-32. . . . . . . . .
EVAP Control System 6E1-32. . . . . . . . . . . . . . . . .
PCV System 6E1-34. . . . . . . . . . . . . . . . . . . . . . . . .
SPECIAL TOOLS6E1-36 . . . . . . . . . . . . . . . . . . . . . .
TIGHTENING TORQUE
SPECIFICATIONS6E1-36 . . . . . . . . . . . . . . . . . . . .
SECTION 6E1
ENGINE AND EMISSION CONTROL SYSTEM
(TBI FOR G10)
WARNING:
For vehicles equipped with a Supplemental Inflatable Restraint Air Bag System:
Service on or around Air Bag System Components or Wiring must be performed only by an authorized
Suzuki dealer. Please observe all WARNINGS and SERVICE PRECAUTIONS in Section 9J under “On-
Vehicle Service” and the Air Bag System Component and Wiring Location view in Section 9J before
performing service on or around Air Bag System Components or Wiring. Failure to follow WARNINGS
could result in unintended air bag deployment or could render the air bag inoperative. Either of these
two conditions may result in severe injury.
SDM can maintain sufficient voltage to cause a deployment of air bags for up to 15 seconds after igni-
tion switch is turned to “LOCK” position, battery is disconnected or fuse powering SDM is removed.
Work must be started after 15 seconds from the time.
NOTE:
For the descriptions for vehicle without warm up three way catalytic converter (WU TWC), refer to the same
section of the Service Manual mentioned in the FOREWORD of this manual.
CONTENTS