SUZUKI SX4 2006 1.G Service Workshop Manual
Manufacturer: SUZUKI, Model Year: 2006, Model line: SX4, Model: SUZUKI SX4 2006 1.GPages: 1556, PDF Size: 37.31 MB
Page 971 of 1556
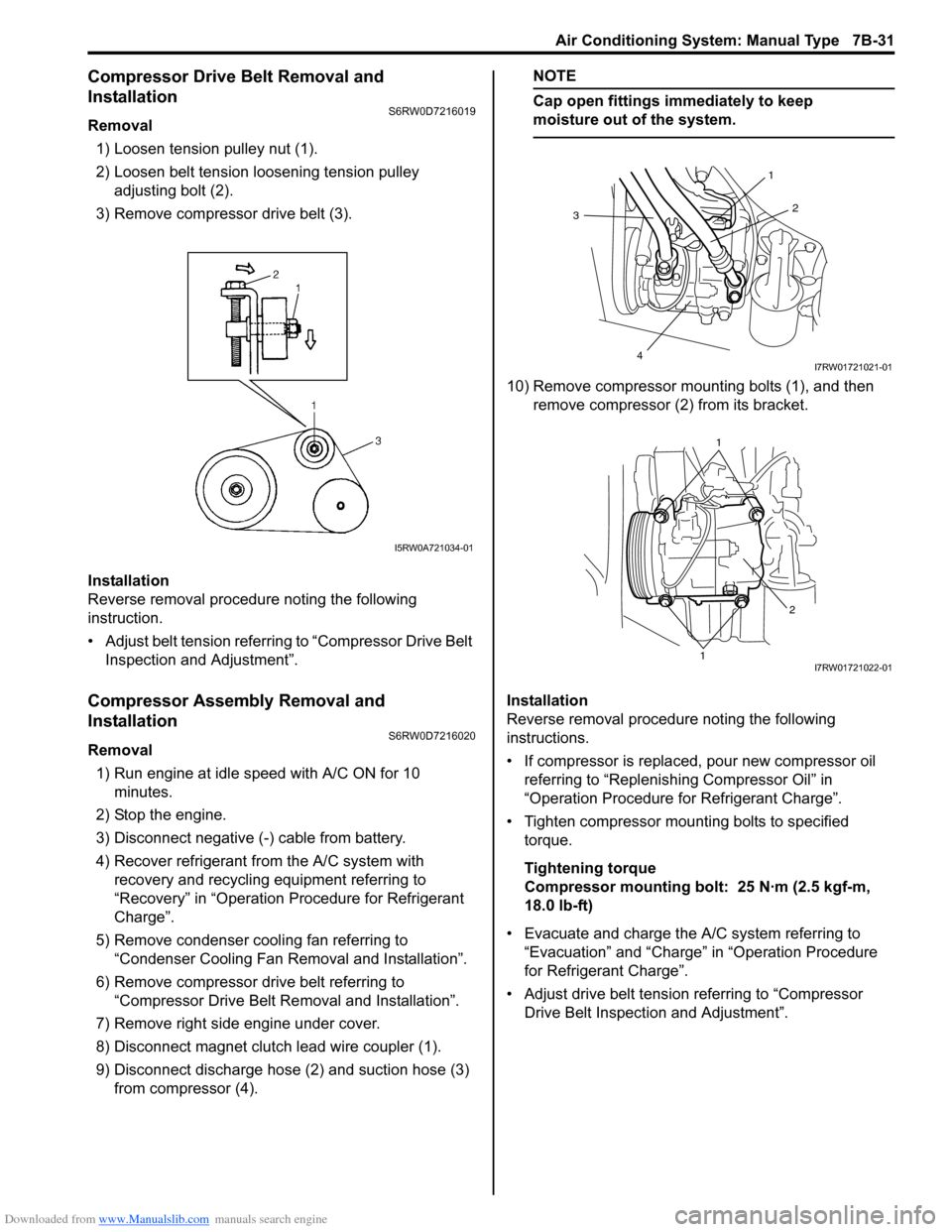
Downloaded from www.Manualslib.com manuals search engine Air Conditioning System: Manual Type 7B-31
Compressor Drive Belt Removal and
Installation
S6RW0D7216019
Removal
1) Loosen tension pulley nut (1).
2) Loosen belt tension loosening tension pulley
adjusting bolt (2).
3) Remove compressor drive belt (3).
Installation
Reverse removal procedure noting the following
instruction.
• Adjust belt tension referring to “Compressor Drive Belt
Inspection and Adjustment”.
Compressor Assembly Removal and
Installation
S6RW0D7216020
Removal
1) Run engine at idle speed with A/C ON for 10
minutes.
2) Stop the engine.
3) Disconnect negative (-) cable from battery.
4) Recover refrigerant from the A/C system with
recovery and recycling equipment referring to
“Recovery” in “Operation Procedure for Refrigerant
Charge”.
5) Remove condenser cooling fan referring to
“Condenser Cooling Fan Removal and Installation”.
6) Remove compressor drive belt referring to
“Compressor Drive Belt Removal and Installation”.
7) Remove right side engine under cover.
8) Disconnect magnet clutch lead wire coupler (1).
9) Disconnect discharge hose (2) and suction hose (3)
from compressor (4).
NOTE
Cap open fittings immediately to keep
moisture out of the system.
10) Remove compressor mounting bolts (1), and then
remove compressor (2) from its bracket.
Installation
Reverse removal procedure noting the following
instructions.
• If compressor is replaced, pour new compressor oil
referring to “Replenishing Compressor Oil” in
“Operation Procedure for Refrigerant Charge”.
• Tighten compressor mounting bolts to specified
torque.
Tightening torque
Compressor mounting bolt: 25 N·m (2.5 kgf-m,
18.0 lb-ft)
• Evacuate and charge the A/C system referring to
“Evacuation” and “Charge” in “Operation Procedure
for Refrigerant Charge”.
• Adjust drive belt tension referring to “Compressor
Drive Belt Inspection and Adjustment”.
I5RW0A721034-01
3
42 1
I7RW01721021-01
1
12
I7RW01721022-01
Page 972 of 1556
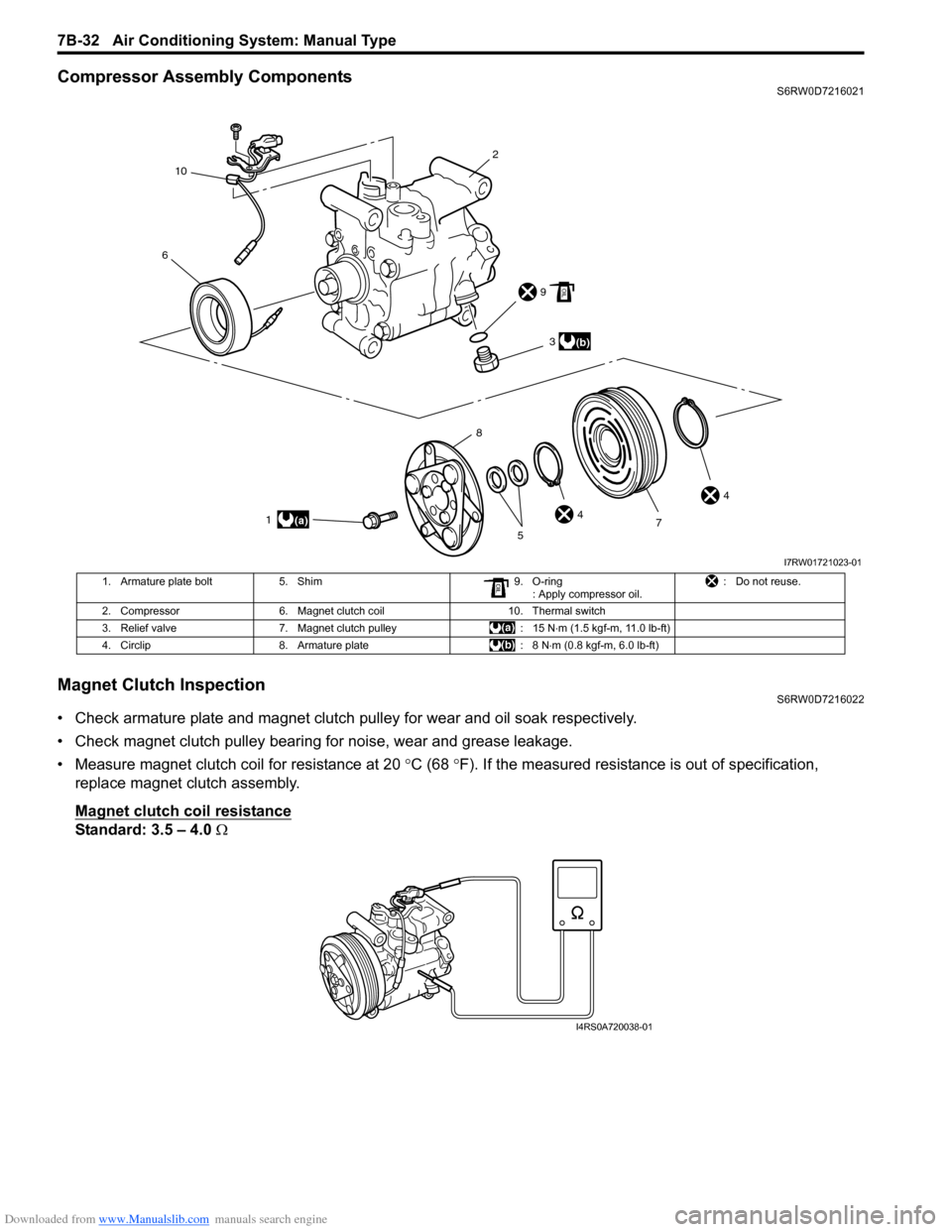
Downloaded from www.Manualslib.com manuals search engine 7B-32 Air Conditioning System: Manual Type
Compressor Assembly ComponentsS6RW0D7216021
Magnet Clutch InspectionS6RW0D7216022
• Check armature plate and magnet clutch pulley for wear and oil soak respectively.
• Check magnet clutch pulley bearing for noise, wear and grease leakage.
• Measure magnet clutch coil for resistance at 20 °C (68 °F). If the measured resistance is out of specification,
replace magnet clutch assembly.
Magnet clutch coil resistance
Standard: 3.5 – 4.0 Ω
6
2
9
4
4 3
1
7
5 8(a)
(b)
10
I7RW01721023-01
1. Armature plate bolt 5. Shim 9. O-ring
: Apply compressor oil.: Do not reuse.
2. Compressor 6. Magnet clutch coil 10. Thermal switch
3. Relief valve 7. Magnet clutch pulley : 15 N⋅m (1.5 kgf-m, 11.0 lb-ft)
4. Circlip 8. Armature plate : 8 N⋅m (0.8 kgf-m, 6.0 lb-ft)
I4RS0A720038-01
Page 973 of 1556
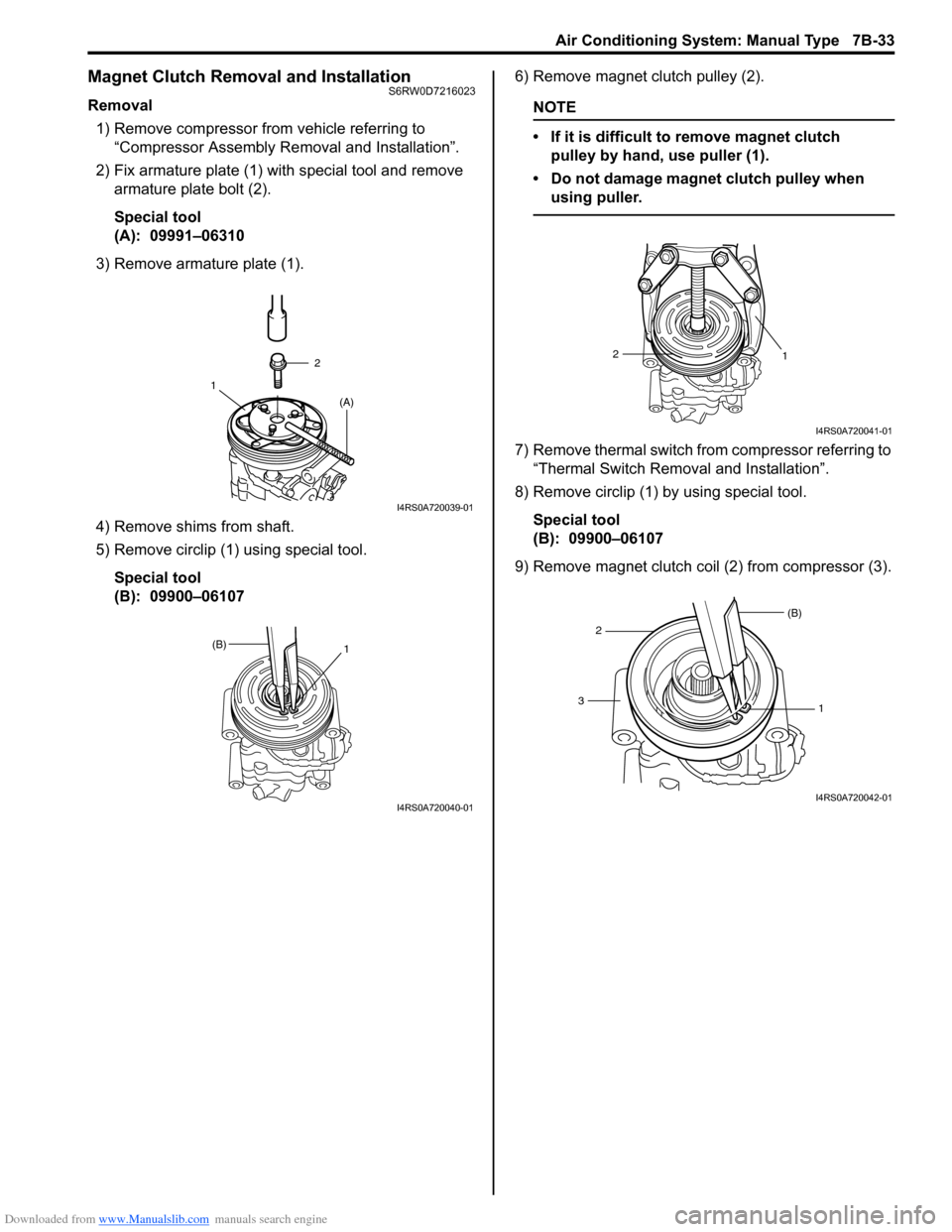
Downloaded from www.Manualslib.com manuals search engine Air Conditioning System: Manual Type 7B-33
Magnet Clutch Removal and InstallationS6RW0D7216023
Removal
1) Remove compressor from vehicle referring to
“Compressor Assembly Removal and Installation”.
2) Fix armature plate (1) with special tool and remove
armature plate bolt (2).
Special tool
(A): 09991–06310
3) Remove armature plate (1).
4) Remove shims from shaft.
5) Remove circlip (1) using special tool.
Special tool
(B): 09900–061076) Remove magnet clutch pulley (2).NOTE
• If it is difficult to remove magnet clutch
pulley by hand, use puller (1).
• Do not damage magnet clutch pulley when
using puller.
7) Remove thermal switch from compressor referring to
“Thermal Switch Removal and Installation”.
8) Remove circlip (1) by using special tool.
Special tool
(B): 09900–06107
9) Remove magnet clutch coil (2) from compressor (3).
2
1
(A)
I4RS0A720039-01
(B)
1
I4RS0A720040-01
1 2
I4RS0A720041-01
1 (B)
23
I4RS0A720042-01
Page 974 of 1556
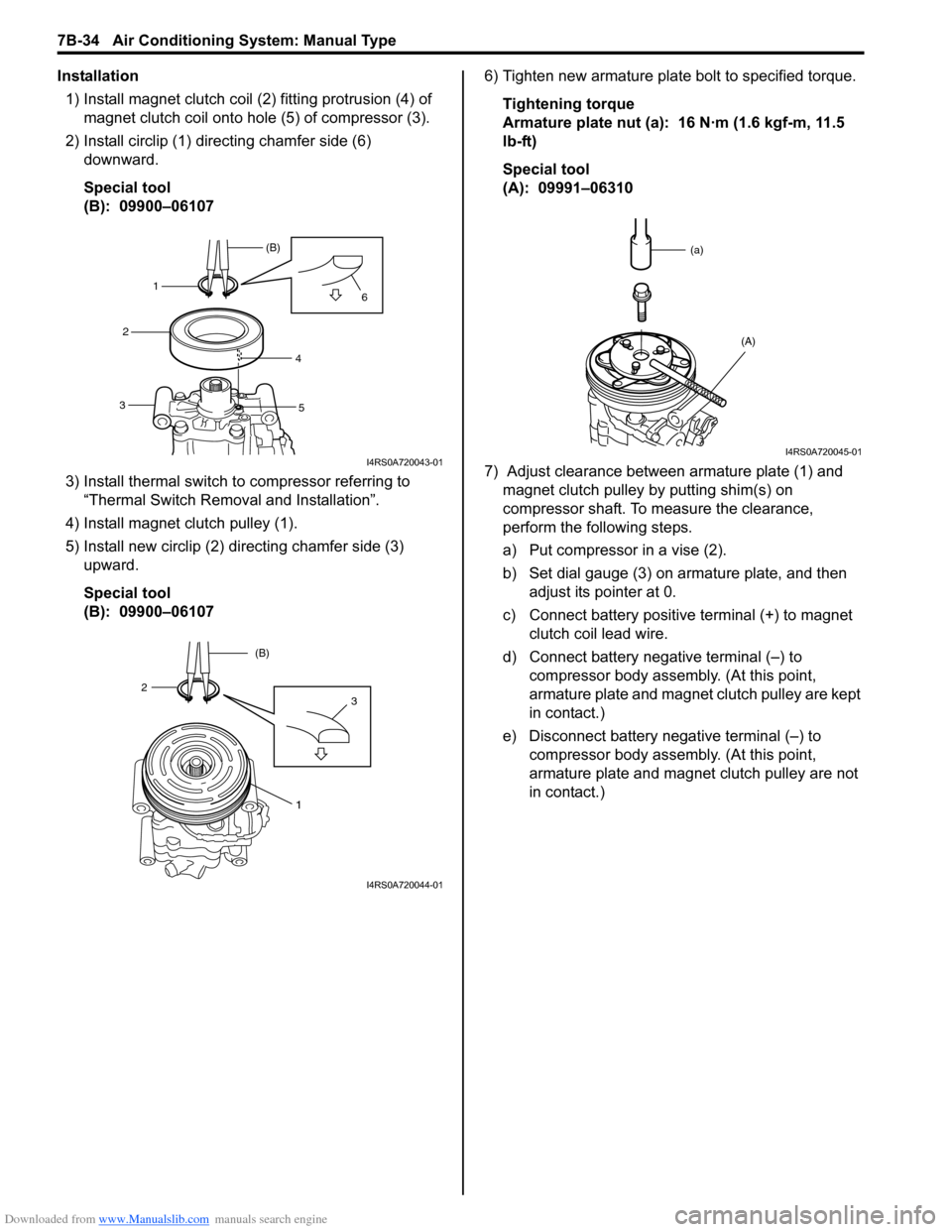
Downloaded from www.Manualslib.com manuals search engine 7B-34 Air Conditioning System: Manual Type
Installation
1) Install magnet clutch coil (2) fitting protrusion (4) of
magnet clutch coil onto hole (5) of compressor (3).
2) Install circlip (1) directing chamfer side (6)
downward.
Special tool
(B): 09900–06107
3) Install thermal switch to compressor referring to
“Thermal Switch Removal and Installation”.
4) Install magnet clutch pulley (1).
5) Install new circlip (2) directing chamfer side (3)
upward.
Special tool
(B): 09900–061076) Tighten new armature plate bolt to specified torque.
Tightening torque
Armature plate nut (a): 16 N·m (1.6 kgf-m, 11.5
lb-ft)
Special tool
(A): 09991–06310
7) Adjust clearance between armature plate (1) and
magnet clutch pulley by putting shim(s) on
compressor shaft. To measure the clearance,
perform the following steps.
a) Put compressor in a vise (2).
b) Set dial gauge (3) on armature plate, and then
adjust its pointer at 0.
c) Connect battery positive terminal (+) to magnet
clutch coil lead wire.
d) Connect battery negative terminal (–) to
compressor body assembly. (At this point,
armature plate and magnet clutch pulley are kept
in contact.)
e) Disconnect battery negative terminal (–) to
compressor body assembly. (At this point,
armature plate and magnet clutch pulley are not
in contact.)
1(B)
2
34
56
I4RS0A720043-01
1
32(B)
I4RS0A720044-01
(a)
(A)
I4RS0A720045-01
Page 975 of 1556
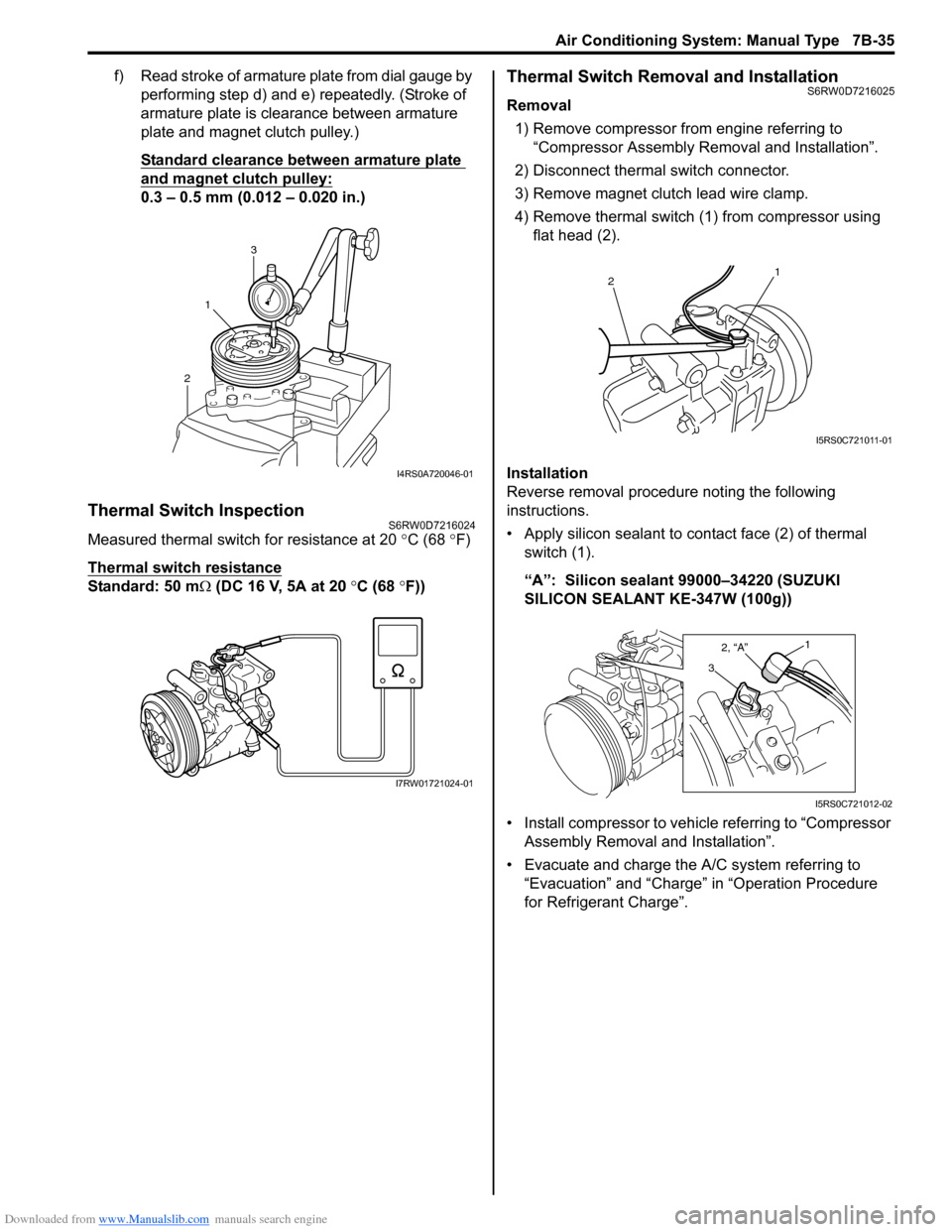
Downloaded from www.Manualslib.com manuals search engine Air Conditioning System: Manual Type 7B-35
f) Read stroke of armature plate from dial gauge by
performing step d) and e) repeatedly. (Stroke of
armature plate is clearance between armature
plate and magnet clutch pulley.)
Standard clearance between armature plate
and magnet clutch pulley:
0.3 – 0.5 mm (0.012 – 0.020 in.)
Thermal Switch InspectionS6RW0D7216024
Measured thermal switch for resistance at 20 °C (68 °F)
Thermal switch resistance
Standard: 50 mΩ (DC 16 V, 5A at 20 °C (68 °F))
Thermal Switch Removal and InstallationS6RW0D7216025
Removal
1) Remove compressor from engine referring to
“Compressor Assembly Removal and Installation”.
2) Disconnect thermal switch connector.
3) Remove magnet clutch lead wire clamp.
4) Remove thermal switch (1) from compressor using
flat head (2).
Installation
Reverse removal procedure noting the following
instructions.
• Apply silicon sealant to contact face (2) of thermal
switch (1).
“A”: Silicon sealant 99000–34220 (SUZUKI
SILICON SEALANT KE-347W (100g))
• Install compressor to vehicle referring to “Compressor
Assembly Removal and Installation”.
• Evacuate and charge the A/C system referring to
“Evacuation” and “Charge” in “Operation Procedure
for Refrigerant Charge”.
213
I4RS0A720046-01
I7RW01721024-01
21
I5RS0C721011-01
3
2, “A”1
I5RS0C721012-02
Page 976 of 1556
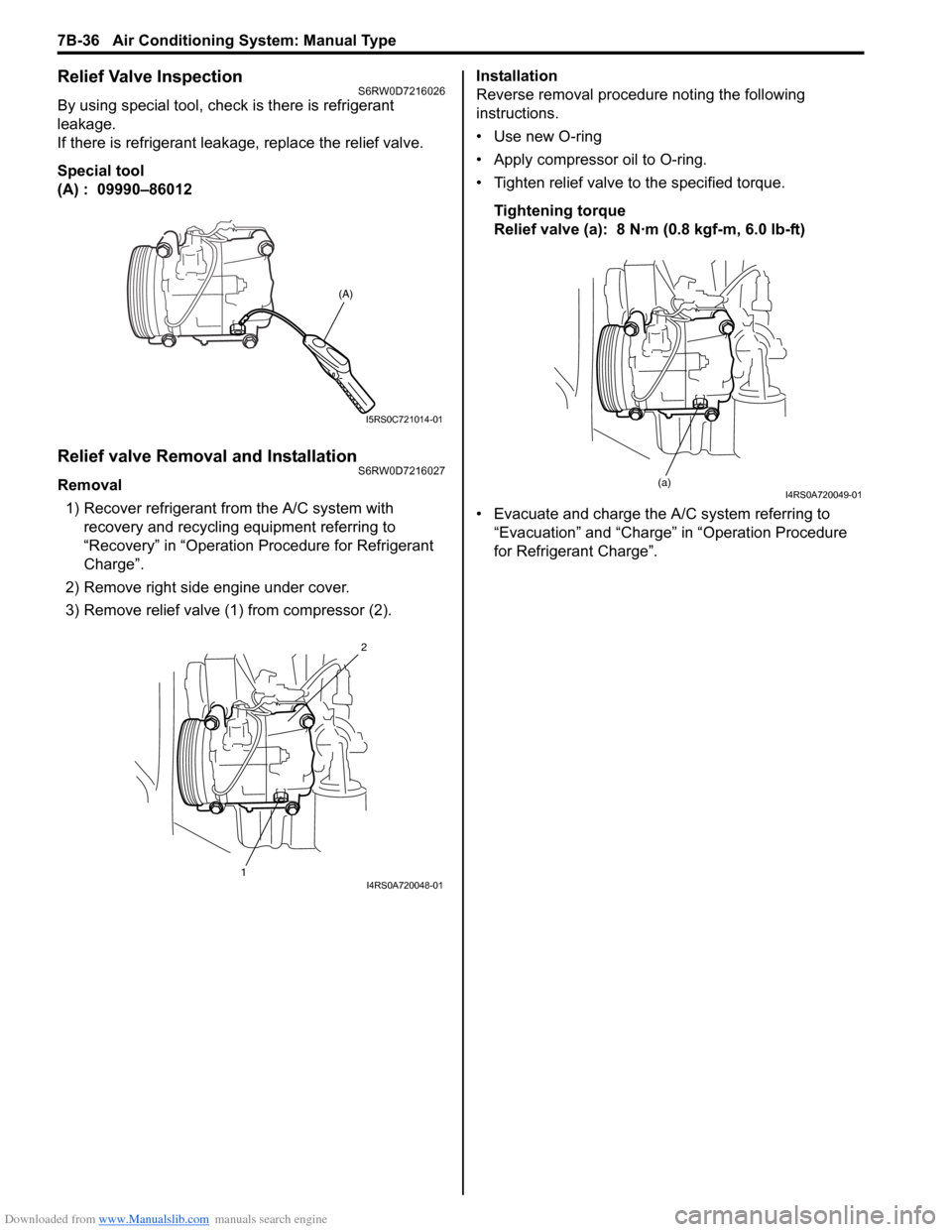
Downloaded from www.Manualslib.com manuals search engine 7B-36 Air Conditioning System: Manual Type
Relief Valve InspectionS6RW0D7216026
By using special tool, check is there is refrigerant
leakage.
If there is refrigerant leakage, replace the relief valve.
Special tool
(A) : 09990–86012
Relief valve Removal and InstallationS6RW0D7216027
Removal
1) Recover refrigerant from the A/C system with
recovery and recycling equipment referring to
“Recovery” in “Operation Procedure for Refrigerant
Charge”.
2) Remove right side engine under cover.
3) Remove relief valve (1) from compressor (2).Installation
Reverse removal procedure noting the following
instructions.
• Use new O-ring
• Apply compressor oil to O-ring.
• Tighten relief valve to the specified torque.
Tightening torque
Relief valve (a): 8 N·m (0.8 kgf-m, 6.0 lb-ft)
• Evacuate and charge the A/C system referring to
“Evacuation” and “Charge” in “Operation Procedure
for Refrigerant Charge”.
(A)
I5RS0C721014-01
12I4RS0A720048-01
(a)I4RS0A720049-01
Page 977 of 1556
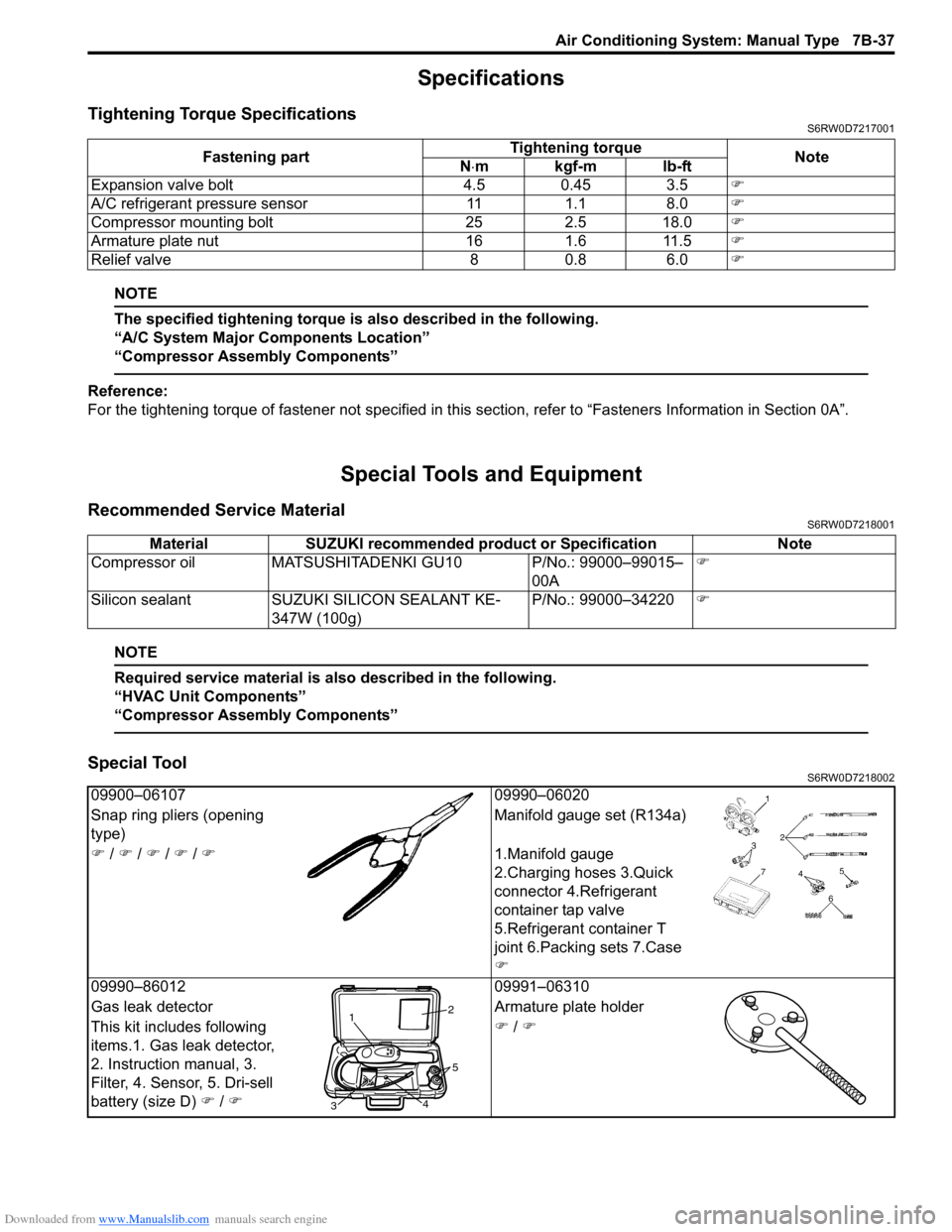
Downloaded from www.Manualslib.com manuals search engine Air Conditioning System: Manual Type 7B-37
Specifications
Tightening Torque SpecificationsS6RW0D7217001
NOTE
The specified tightening torque is also described in the following.
“A/C System Major Components Location”
“Compressor Assembly Components”
Reference:
For the tightening torque of fastener not specified in this section, refer to “Fasteners Information in Section 0A”.
Special Tools and Equipment
Recommended Service MaterialS6RW0D7218001
NOTE
Required service material is also described in the following.
“HVAC Unit Components”
“Compressor Assembly Components”
Special ToolS6RW0D7218002
Fastening partTightening torque
Note
N⋅mkgf-mlb-ft
Expansion valve bolt 4.5 0.45 3.5 )
A/C refrigerant pressure sensor 11 1.1 8.0 )
Compressor mounting bolt 25 2.5 18.0 )
Armature plate nut 16 1.6 11.5 )
Relief valve 8 0.8 6.0 )
Material SUZUKI recommended product or Specification Note
Compressor oil MATSUSHITADENKI GU10 P/No.: 99000–99015–
00A )
Silicon sealant SUZUKI SILICON SEALANT KE-
347W (100g)P/No.: 99000–34220 )
09900–06107 09990–06020
Snap ring pliers (opening
type)Manifold gauge set (R134a)
) / ) / ) / ) / )1.Manifold gauge
2.Charging hoses 3.Quick
connector 4.Refrigerant
container tap valve
5.Refrigerant container T
joint 6.Packing sets 7.Case
)
09990–86012 09991–06310
Gas leak detector Armature plate holder
This kit includes following
items.1. Gas leak detector,
2. Instruction manual, 3.
Filter, 4. Sensor, 5. Dri-sell
battery (size D) ) / ) ) / )
12
34
5
Page 978 of 1556
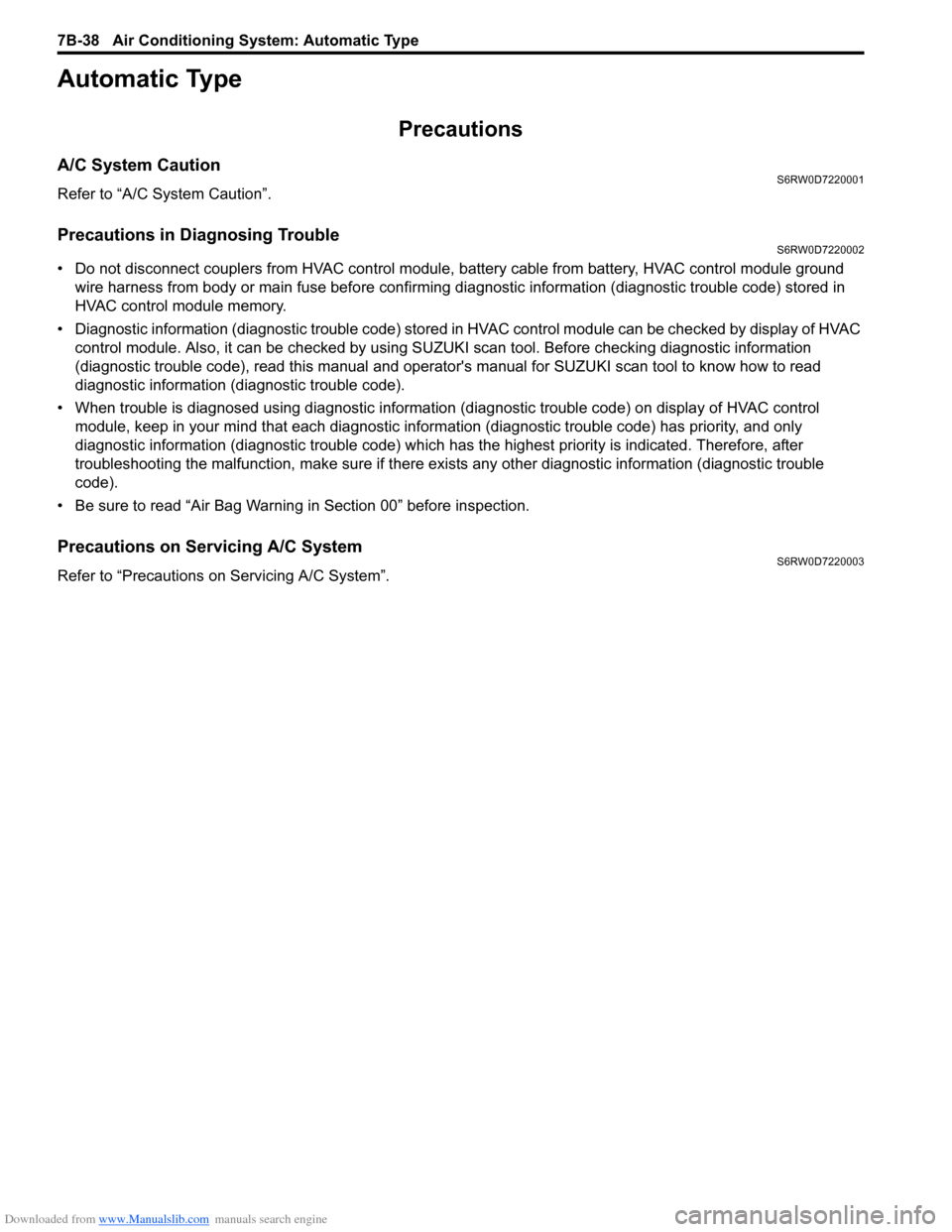
Downloaded from www.Manualslib.com manuals search engine 7B-38 Air Conditioning System: Automatic Type
Automatic Type
Precautions
A/C System CautionS6RW0D7220001
Refer to “A/C System Caution”.
Precautions in Diagnosing TroubleS6RW0D7220002
• Do not disconnect couplers from HVAC control module, battery cable from battery, HVAC control module ground
wire harness from body or main fuse before confirming diagnostic information (diagnostic trouble code) stored in
HVAC control module memory.
• Diagnostic information (diagnostic trouble code) stored in HVAC control module can be checked by display of HVAC
control module. Also, it can be checked by using SUZUKI scan tool. Before checking diagnostic information
(diagnostic trouble code), read this manual and operator's manual for SUZUKI scan tool to know how to read
diagnostic information (diagnostic trouble code).
• When trouble is diagnosed using diagnostic information (diagnostic trouble code) on display of HVAC control
module, keep in your mind that each diagnostic information (diagnostic trouble code) has priority, and only
diagnostic information (diagnostic trouble code) which has the highest priority is indicated. Therefore, after
troubleshooting the malfunction, make sure if there exists any other diagnostic information (diagnostic trouble
code).
• Be sure to read “Air Bag Warning in Section 00” before inspection.
Precautions on Servicing A/C SystemS6RW0D7220003
Refer to “Precautions on Servicing A/C System”.
Page 979 of 1556
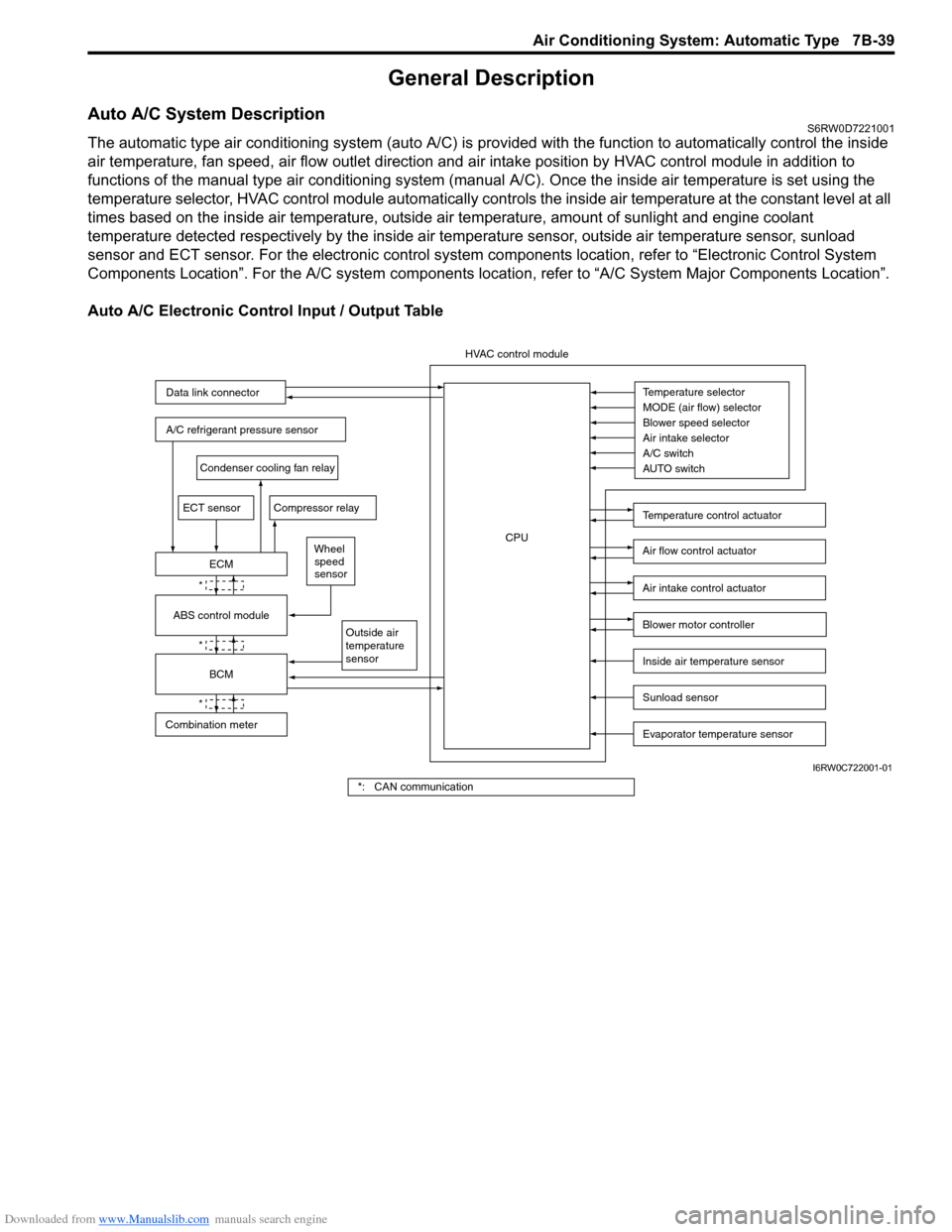
Downloaded from www.Manualslib.com manuals search engine Air Conditioning System: Automatic Type 7B-39
General Description
Auto A/C System DescriptionS6RW0D7221001
The automatic type air conditioning system (auto A/C) is provided with the function to automatically control the inside
air temperature, fan speed, air flow outlet direction and air intake position by HVAC control module in addition to
functions of the manual type air conditioning system (manual A/C). Once the inside air temperature is set using the
temperature selector, HVAC control module automatically controls the inside air temperature at the constant level at all
times based on the inside air temperature, outside air temperature, amount of sunlight and engine coolant
temperature detected respectively by the inside air temperature sensor, outside air temperature sensor, sunload
sensor and ECT sensor. For the electronic control system components location, refer to “Electronic Control System
Components Location”. For the A/C system components location, refer to “A/C System Major Components Location”.
Auto A/C Electronic Control Input / Output Table
Temperature selector
MODE (air flow) selector
Blower speed selector
Air intake selector
AUTO switch A/C switch
Outside air
temperature
sensor
A/C refrigerant pressure sensor
Compressor relay
Blower motor controller
Temperature control actuator
Air flow control actuator
Air intake control actuator
BCM
ECM
Data link connector
HVAC control module
CPU
ECT sensor
Sunload sensor
Inside air temperature sensor
Evaporator temperature sensor
Condenser cooling fan relay
Wheel
speed
sensor
*
*
*
Combination meterABS control module
I6RW0C722001-01
*: CAN communication
Page 980 of 1556
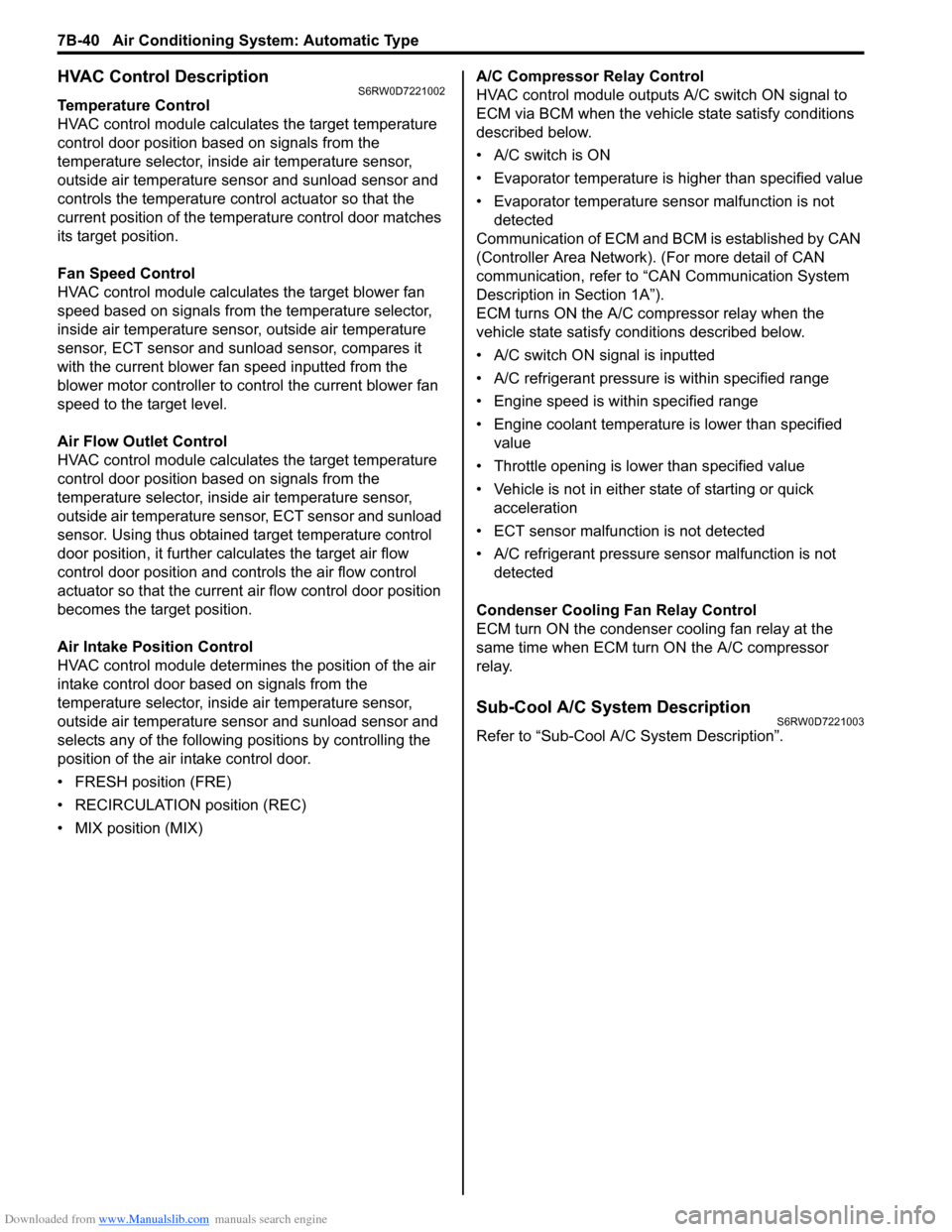
Downloaded from www.Manualslib.com manuals search engine 7B-40 Air Conditioning System: Automatic Type
HVAC Control DescriptionS6RW0D7221002
Temperature Control
HVAC control module calculates the target temperature
control door position based on signals from the
temperature selector, inside air temperature sensor,
outside air temperature sensor and sunload sensor and
controls the temperature control actuator so that the
current position of the temperature control door matches
its target position.
Fan Speed Control
HVAC control module calculates the target blower fan
speed based on signals from the temperature selector,
inside air temperature sensor, outside air temperature
sensor, ECT sensor and sunload sensor, compares it
with the current blower fan speed inputted from the
blower motor controller to control the current blower fan
speed to the target level.
Air Flow Outlet Control
HVAC control module calculates the target temperature
control door position based on signals from the
temperature selector, inside air temperature sensor,
outside air temperature sensor, ECT sensor and sunload
sensor. Using thus obtained target temperature control
door position, it further calculates the target air flow
control door position and controls the air flow control
actuator so that the current air flow control door position
becomes the target position.
Air Intake Position Control
HVAC control module determines the position of the air
intake control door based on signals from the
temperature selector, inside air temperature sensor,
outside air temperature sensor and sunload sensor and
selects any of the following positions by controlling the
position of the air intake control door.
• FRESH position (FRE)
• RECIRCULATION position (REC)
• MIX position (MIX)A/C Compressor Relay Control
HVAC control module outputs A/C switch ON signal to
ECM via BCM when the vehicle state satisfy conditions
described below.
• A/C switch is ON
• Evaporator temperature is higher than specified value
• Evaporator temperature sensor malfunction is not
detected
Communication of ECM and BCM is established by CAN
(Controller Area Network). (For more detail of CAN
communication, refer to “CAN Communication System
Description in Section 1A”).
ECM turns ON the A/C compressor relay when the
vehicle state satisfy conditions described below.
• A/C switch ON signal is inputted
• A/C refrigerant pressure is within specified range
• Engine speed is within specified range
• Engine coolant temperature is lower than specified
value
• Throttle opening is lower than specified value
• Vehicle is not in either state of starting or quick
acceleration
• ECT sensor malfunction is not detected
• A/C refrigerant pressure sensor malfunction is not
detected
Condenser Cooling Fan Relay Control
ECM turn ON the condenser cooling fan relay at the
same time when ECM turn ON the A/C compressor
relay.
Sub-Cool A/C System DescriptionS6RW0D7221003
Refer to “Sub-Cool A/C System Description”.