sensor TOYOTA CAMRY 1994 XV10 / 4.G Wiring Diagrams Service Manual
[x] Cancel search | Manufacturer: TOYOTA, Model Year: 1994, Model line: CAMRY, Model: TOYOTA CAMRY 1994 XV10 / 4.GPages: 307, PDF Size: 5.48 MB
Page 152 of 307
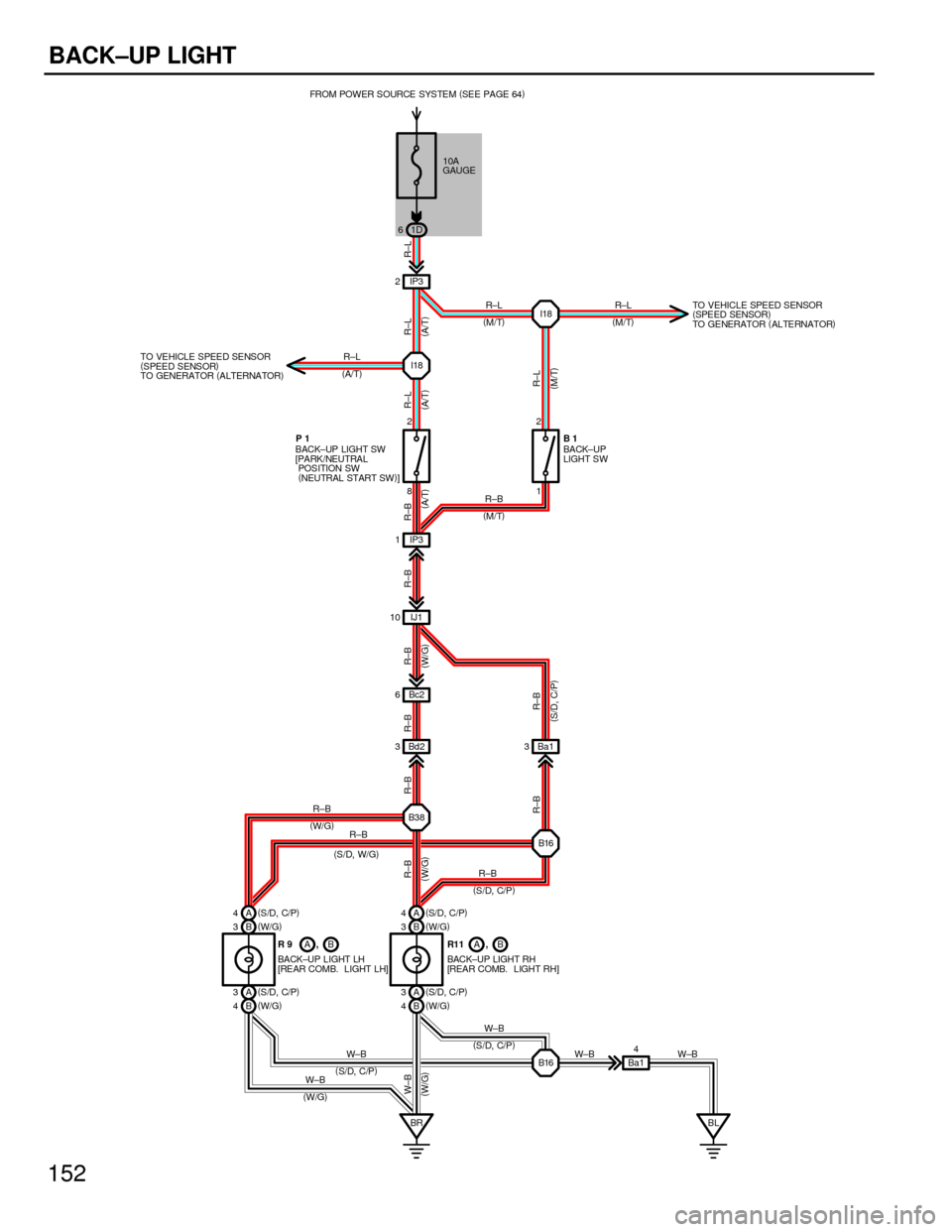
152
BACK±UP LIGHT
IP3 2
8 2
1 2
IP3 1
Bd2 3IJ1 10
B38
BR FROM POWER SOURCE SYSTEM(
SEEPAGE64)
R±L
R±B
R±B
R±L R±L R±B R±B R±B R±B R±B W±B
BACK±UP
LIGHT SW BACK±UP LIGHT SW
[PARK/NEUTRAL
POSITION SW
(
NEUTRAL START SW)
]B1 P1(
M/T)
(
A/T)
(
M/T)(
A/T)
Bc2 6
R±B
W±BBa1 3
B16
B16 Ba 14
BL W±BR±B
W±B R±B
W±B W±B
R±B R±B(
W/G)
(
S/D, C/P)
(
S /D, C/P) (
S/D, W/G) (
W/G)(
W/G)
(
S/D, C/P)
(
W/G)(
S /D, C/P)
(
W/G)R±L
(
A/T)
R±L TO VEHICLE SPEED SENSOR
(
SPEED SENSOR)
TO GENERATOR(
ALTERNATOR)TO VEHICLE SPEED SENSOR
(
SPEED SENSOR)
TO GE NERATOR(
ALTERNATOR) R±L
R±L
(
M/T)
(
A/T)
(
M/T)
I18
I18
B 3A 4
B 3A 4 (
S/D, C/P)
(
W/G)(
S/D, C/P)
(
W/G)
A 3A3
B 4 B 4(
S/D, C/P)
(
W/G) (
S/D, C/P)
(
W/G)B R9 ,A
BA CK ±UP LIGHT LH
[REAR COMB. LIGHT LH]B R11 ,A
BACK±UP LIGHT RH
[REAR COMB. LIGHT RH]
1D 610A
GAUGE
Page 174 of 307
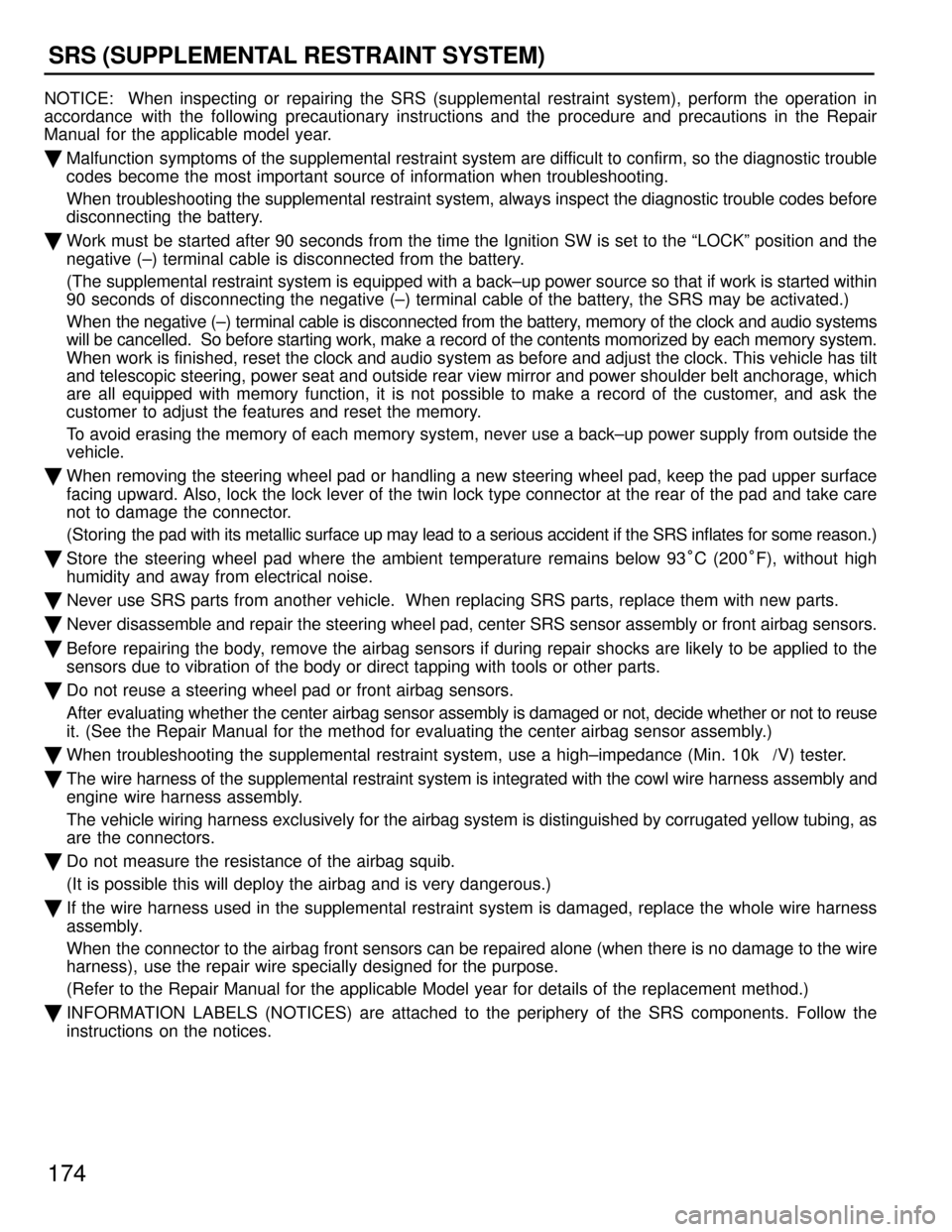
174
SRS (SUPPLEMENTAL RESTRAINT SYSTEM)
NOTICE: When inspecting or repairing the SRS (supplemental restraint system), perform the operation in
accordance with the following precautionary instructions and the procedure and precautions in the Repair
Manual for the applicable model year.
Malfunction symptoms of the supplemental restraint system are difficult to confirm, so the diagnostic trouble
codes become the most important source of information when troubleshooting.
When troubleshooting the supplemental restraint system, always inspect the diagnostic trouble codes before
disconnecting the battery.
Work must be started after 90 seconds from the time the Ignition SW is set to the ªLOCKº position and the
negative (±) terminal cable is disconnected from the battery.
(The supplemental restraint system is equipped with a back±up power source so that if work is started within
90 seconds of disconnecting the negative (±) terminal cable of the battery, the SRS may be activated.)
When the negative (±) terminal cable is disconnected from the battery, memory of the clock and audio systems
will be cancelled. So before starting work, make a record of the contents momorized by each memory system.
When work is finished, reset the clock and audio system as before and adjust the clock. This vehicle has tilt
and telescopic steering, power seat and outside rear view mirror and power shoulder belt anchorage, which
are all equipped with memory function, it is not possible to make a record of the customer, and ask the
customer to adjust the features and reset the memory.
To avoid erasing the memory of each memory system, never use a back±up power supply from outside the
vehicle.
When removing the steering wheel pad or handling a new steering wheel pad, keep the pad upper surface
facing upward. Also, lock the lock lever of the twin lock type connector at the rear of the pad and take care
not to damage the connector.
(Storing the pad with its metallic surface up may lead to a serious accident if the SRS inflates for some reason.)
Store the steering wheel pad where the ambient temperature remains below 93°C (200°F), without high
humidity and away from electrical noise.
Never use SRS parts from another vehicle. When replacing SRS parts, replace them with new parts.
Never disassemble and repair the steering wheel pad, center SRS sensor assembly or front airbag sensors.
Before repairing the body, remove the airbag sensors if during repair shocks are likely to be applied to the
sensors due to vibration of the body or direct tapping with tools or other parts.
Do not reuse a steering wheel pad or front airbag sensors.
After evaluating whether the center airbag sensor assembly is damaged or not, decide whether or not to reuse
it. (See the Repair Manual for the method for evaluating the center airbag sensor assembly.)
When troubleshooting the supplemental restraint system, use a high±impedance (Min. 10k/V) tester.
The wire harness of the supplemental restraint system is integrated with the cowl wire harness assembly and
engine wire harness assembly.
The vehicle wiring harness exclusively for the airbag system is distinguished by corrugated yellow tubing, as
are the connectors.
Do not measure the resistance of the airbag squib.
(It is possible this will deploy the airbag and is very dangerous.)
If the wire harness used in the supplemental restraint system is damaged, replace the whole wire harness
assembly.
When the connector to the airbag front sensors can be repaired alone (when there is no damage to the wire
harness), use the repair wire specially designed for the purpose.
(Refer to the Repair Manual for the applicable Model year for details of the replacement method.)
INFORMATION LABELS (NOTICES) are attached to the periphery of the SRS components. Follow the
instructions on the notices.
Page 177 of 307
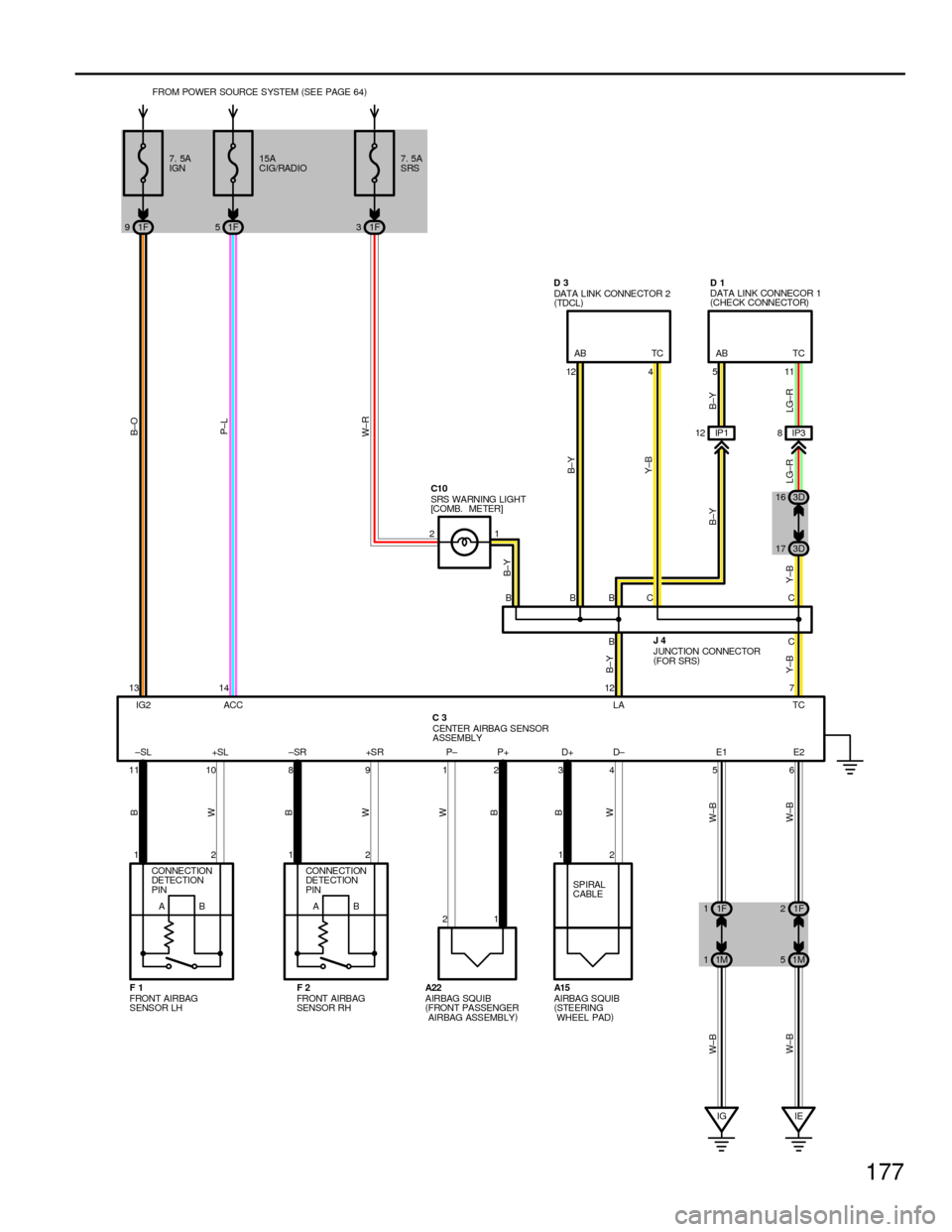
177
IP 1 12 IP38
12
FRONT AIRBAG
SENSOR LHAIRBAG SQUIB
(
STEERING
WHEEL PAD) SPIRAL
CABLE
F1A1512 4 5 11B±O
P±L
B±Y
Y±B
LG±RB±Y
W±B W±BWB WB
±SL +SLD+ D± E1 E2 IG2 ACCLA FROM POWER SOURCE SYSTEM(
SEE PAGE 64)
DATA LINK CONNE CTOR 2
(
TDCL)DATA LINK CONNECOR 1
(
CHECK CONNECTOR)
AB TC AB TC D3 D1
CENTER AIRBAG SENSOR
ASSEMBLY C3 SRS WARNING LIGHT
[COMB. METER] C10
Y±B
21
W±B W±BW±R
B±Y
Y±BB±Y
LG±R B±Y
TC
IG IEC C B B B
13 1412 7C B
11 1034 5 6JUNCTION CONNECTOR
(
FOR SRS) J4
21
AIRBAG SQUIB
(
FRONT PASSENGER
AIRBAG ASSEMBLY) A22
B W
P± P+
12
12
AB CONNE CTION
DE TECTION
PIN12
AB CONNE CTION
DE TE CTION
PIN
WB
±SR +SR
89
FRONT AI RB AG
SENSOR RH F2
1F 91F 31F7. 5A
IGN15A
CIG/RADIO7. 5A
SRS
5
3D 16
3D 17
1M 11M51F 2 1F 1
Page 178 of 307
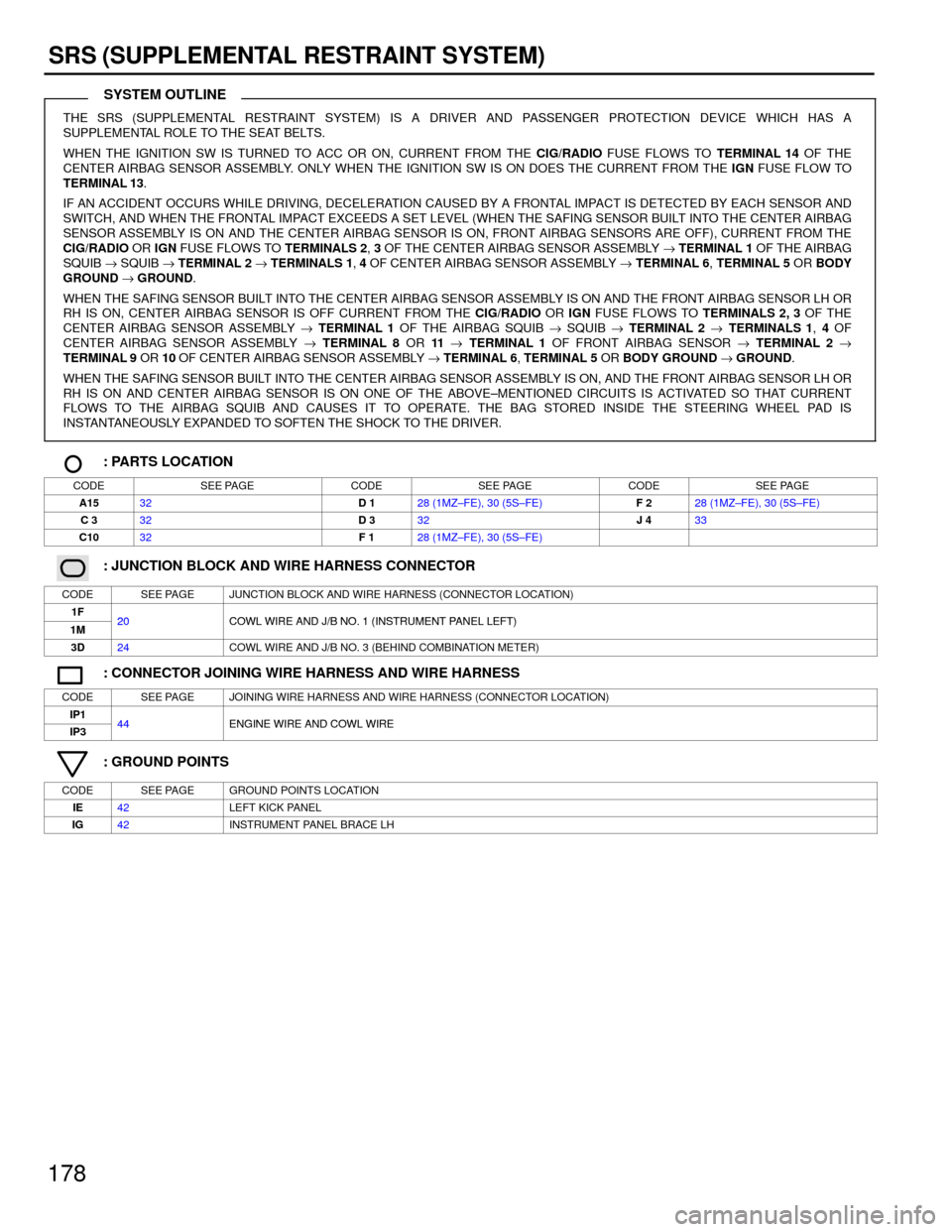
178
SRS (SUPPLEMENTAL RESTRAINT SYSTEM)
THE SRS (SUPPLEMENTAL RESTRAINT SYSTEM) IS A DRIVER AND PASSENGER PROTECTION DEVICE WHICH HAS A
SUPPLEMENTAL ROLE TO THE SEAT BELTS.
WHEN THE IGNITION SW IS TURNED TO ACC OR ON, CURRENT FROM THE CIG/RADIO FUSE FLOWS TO TERMINAL 14 OF THE
CENTER AIRBAG SENSOR ASSEMBLY. ONLY WHEN THE IGNITION SW IS ON DOES THE CURRENT FROM THE IGN FUSE FLOW TO
TERMINAL 13.
IF AN ACCIDENT OCCURS WHILE DRIVING, DECELERATION CAUSED BY A FRONTAL IMPACT IS DETECTED BY EACH SENSOR AND
SWITCH, AND WHEN THE FRONTAL IMPACT EXCEEDS A SET LEVEL (WHEN THE SAFING SENSOR BUILT INTO THE CENTER AIRBAG
SENSOR ASSEMBLY IS ON AND THE CENTER AIRBAG SENSOR IS ON, FRONT AIRBAG SENSORS ARE OFF), CURRENT FROM THE
CIG/RADIO OR IGN FUSE FLOWS TO TERMINALS 2, 3 OF THE CENTER AIRBAG SENSOR ASSEMBLY " TERMINAL 1 OF THE AIRBAG
SQUIB " SQUIB " TERMINAL 2 " TERMINALS 1, 4 OF CENTER AIRBAG SENSOR ASSEMBLY " TERMINAL 6, TERMINAL 5 OR BODY
GROUND " GROUND.
WHEN THE SAFING SENSOR BUILT INTO THE CENTER AIRBAG SENSOR ASSEMBLY IS ON AND THE FRONT AIRBAG SENSOR LH OR
RH IS ON, CENTER AIRBAG SENSOR IS OFF CURRENT FROM THE CIG/RADIO OR IGN FUSE FLOWS TO TERMINALS 2, 3 OF THE
CENTER AIRBAG SENSOR ASSEMBLY " TERMINAL 1 OF THE AIRBAG SQUIB " SQUIB " TERMINAL 2 " TERMINALS 1, 4 OF
CENTER AIRBAG SENSOR ASSEMBLY " TERMINAL 8 OR 11 " TERMINAL 1 OF FRONT AIRBAG SENSOR " TERMINAL 2 "
TERMINAL 9 OR 10 OF CENTER AIRBAG SENSOR ASSEMBLY " TERMINAL 6, TERMINAL 5 OR BODY GROUND " GROUND.
WHEN THE SAFING SENSOR BUILT INTO THE CENTER AIRBAG SENSOR ASSEMBLY IS ON, AND THE FRONT AIRBAG SENSOR LH OR
RH IS ON AND CENTER AIRBAG SENSOR IS ON ONE OF THE ABOVE±MENTIONED CIRCUITS IS ACTIVATED SO THAT CURRENT
FLOWS TO THE AIRBAG SQUIB AND CAUSES IT TO OPERATE. THE BAG STORED INSIDE THE STEERING WHEEL PAD IS
INSTANTANEOUSLY EXPANDED TO SOFTEN THE SHOCK TO THE DRIVER.
: PARTS LOCATION
CODESEE PAGECODESEE PAGECODESEE PAGE
A1532D 128 (1MZ±FE), 30 (5S±FE)F 228 (1MZ±FE), 30 (5S±FE)
C 332D 332J 433
C1032F 128 (1MZ±FE), 30 (5S±FE)
: JUNCTION BLOCK AND WIRE HARNESS CONNECTOR
CODESEE PAGEJUNCTION BLOCK AND WIRE HARNESS (CONNECTOR LOCATION)
1F20COWL WIRE AND J/B NO 1 (INSTRUMENT PANEL LEFT)1M20COWL WIRE AND J/B NO. 1 (INSTRUMENT PANEL LEFT)
3D24COWL WIRE AND J/B NO. 3 (BEHIND COMBINATION METER)
: CONNECTOR JOINING WIRE HARNESS AND WIRE HARNESS
CODESEE PAGEJOINING WIRE HARNESS AND WIRE HARNESS (CONNECTOR LOCATION)
IP144ENGINE WIRE AND COWL WIREIP344ENGINE WIRE AND COWL WIRE
: GROUND POINTS
CODESEE PAGEGROUND POINTS LOCATION
IE42LEFT KICK PANEL
IG42INSTRUMENT PANEL BRACE LH
SYSTEM OUTLINE
Page 192 of 307
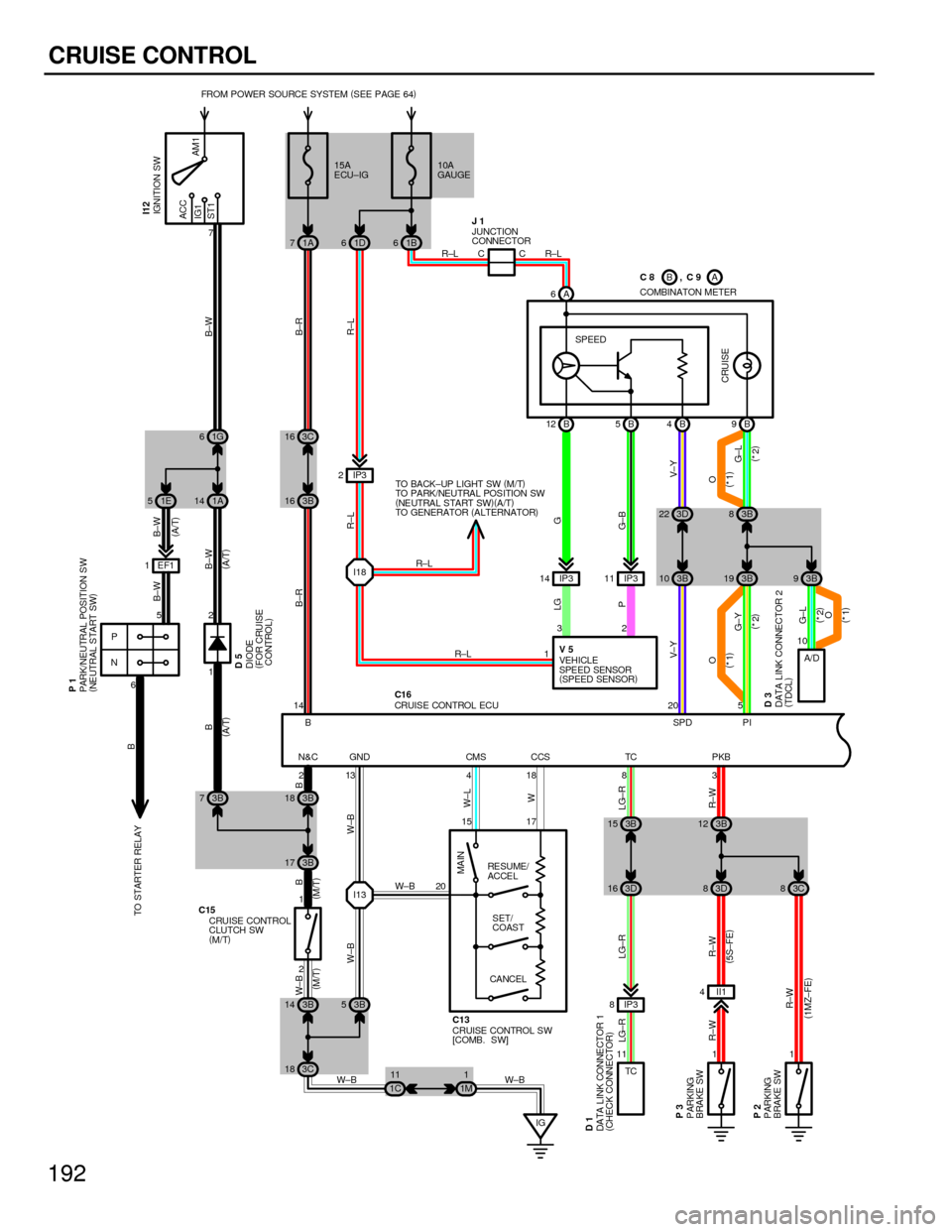
192
CRUISE CONTROL
B
ST1 IG1 ACC
AM1
7
IP3 8IP3 11
II1 4 2 1
1 1 213 41883
17 15
20 1420 510 2
13B 4 B 12 B5B9 A 6
1 2
IG CC
I13
11 R±L R±L
R±L
W±B
W±B W±B
B±R B±W
R±L B±W
B±R B
B
W±B
W±L
W
LG±R
R±W LG±R
R±W LG±R
R±W
R±WW±B
W±B
G±BG
V±Y
G±Y V±YP LG B
FROM POWER SOURCE SYSTEM(
SEEPAGE64)
10A
GAUGE
COMBINATON METER
DIODE
(
FOR CRUISE
CONTROL)VEHICLE
SPEED SENSOR
(
SPEED SENSOR)
DATA LINK CONNECTOR 2
(
TDCL)
A/D JUNCTION
CONNECTOR
CRUISE CONTROL
CLUTCH SW
(
M/T)
CRUISE CONTROL SW
[COMB. SW]
DA TA LINK CONNE CTOR 1
(
CHECK CONNECTOR)
PARKING
BRAKE SW
PARKING
BRAKE SWMAIN
CA NCELSET/
COAST RE SUME/
ACCEL N&C GND CMS CCS TC PKBBSPD PI
TC
IGNITION SW
P
N5
6EF1 1
B±W B±W
J1
P1
D5
C8 , C9
D3
V5A
PARK/NEUTRAL POSITION SW
(
NE UTRAL S TA RT SW)
(
A/T) B
TO STARTER RELAY
CRUIS E CONTROL ECU C16
C15
C13
D1
P3
P2
(
1MZ±FE)
SPEED
CRUISEI12
IP3 2
(
A/T)
(
5S±FE)IP3 14
(
A/T)
(
M/T) (
M/T)
R±L
TO BA CK ±UP LIGHT SW(
M/T)
TO PARK/NEUTRAL POSITION SW
(
NE UTRA L S TA RT SW)(
A/T)
TO GENERATOR(
ALTERNATOR)
R±L
I18
(
*2) O
(
*1)
G±L
(
*2) O
(
*1)
O
(
*1) G±L
(
*2)
1G 63C16
1A 14 3B16 1E 5
1A 71D61B6 15A
ECU±IG
3D 22 3B8
3B 10 3B19 3B9
3B 73B18
3B 17
3B 14 3B5
3C 18
1M1
1C11
3B 12
3D 83C83B 15
3D 16
Page 196 of 307
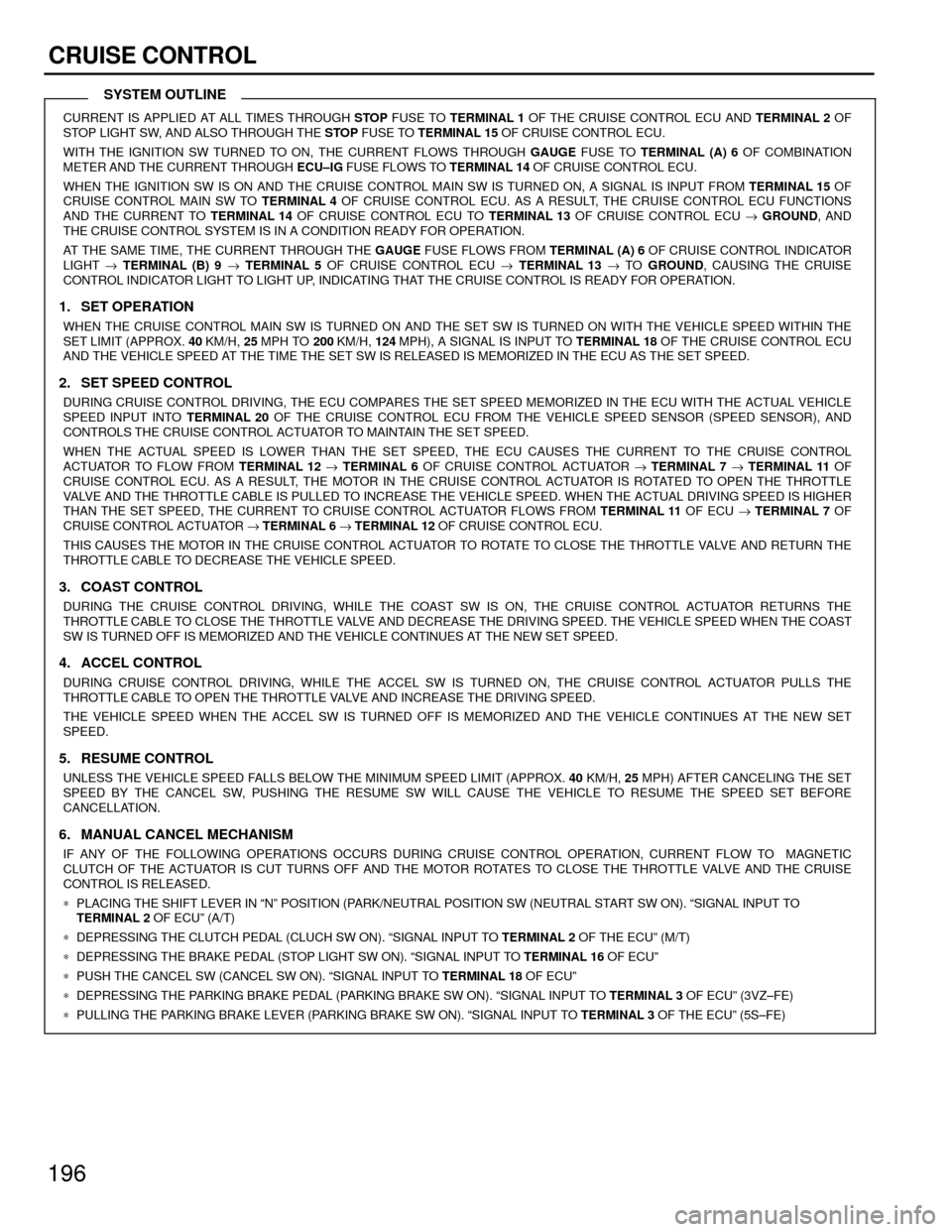
196
CRUISE CONTROL
CURRENT IS APPLIED AT ALL TIMES THROUGH STOP FUSE TO TERMINAL 1 OF THE CRUISE CONTROL ECU AND TERMINAL 2 OF
STOP LIGHT SW, AND ALSO THROUGH THE STOP FUSE TO TERMINAL 15 OF CRUISE CONTROL ECU.
WITH THE IGNITION SW TURNED TO ON, THE CURRENT FLOWS THROUGH GAUGE FUSE TO TERMINAL (A) 6 OF COMBINATION
METER AND THE CURRENT THROUGH ECU±IG FUSE FLOWS TO TERMINAL 14 OF CRUISE CONTROL ECU.
WHEN THE IGNITION SW IS ON AND THE CRUISE CONTROL MAIN SW IS TURNED ON, A SIGNAL IS INPUT FROM TERMINAL 15 OF
CRUISE CONTROL MAIN SW TO TERMINAL 4 OF CRUISE CONTROL ECU. AS A RESULT, THE CRUISE CONTROL ECU FUNCTIONS
AND THE CURRENT TO TERMINAL 14 OF CRUISE CONTROL ECU TO TERMINAL 13 OF CRUISE CONTROL ECU " GROUND, AND
THE CRUISE CONTROL SYSTEM IS IN A CONDITION READY FOR OPERATION.
AT THE SAME TIME, THE CURRENT THROUGH THE GAUGE FUSE FLOWS FROM TERMINAL (A) 6 OF CRUISE CONTROL INDICATOR
LIGHT " TERMINAL (B) 9 " TERMINAL 5 OF CRUISE CONTROL ECU " TERMINAL 13 " TO GROUND, CAUSING THE CRUISE
CONTROL INDICATOR LIGHT TO LIGHT UP, INDICATING THAT THE CRUISE CONTROL IS READY FOR OPERATION.
1. SET OPERATION
WHEN THE CRUISE CONTROL MAIN SW IS TURNED ON AND THE SET SW IS TURNED ON WITH THE VEHICLE SPEED WITHIN THE
SET LIMIT (APPROX. 40 KM/H, 25 MPH TO 200 KM/H, 124 MPH), A SIGNAL IS INPUT TO TERMINAL 18 OF THE CRUISE CONTROL ECU
AND THE VEHICLE SPEED AT THE TIME THE SET SW IS RELEASED IS MEMORIZED IN THE ECU AS THE SET SPEED.
2. SET SPEED CONTROL
DURING CRUISE CONTROL DRIVING, THE ECU COMPARES THE SET SPEED MEMORIZED IN THE ECU WITH THE ACTUAL VEHICLE
SPEED INPUT INTO TERMINAL 20 OF THE CRUISE CONTROL ECU FROM THE VEHICLE SPEED SENSOR (SPEED SENSOR), AND
CONTROLS THE CRUISE CONTROL ACTUATOR TO MAINTAIN THE SET SPEED.
WHEN THE ACTUAL SPEED IS LOWER THAN THE SET SPEED, THE ECU CAUSES THE CURRENT TO THE CRUISE CONTROL
ACTUATOR TO FLOW FROM TERMINAL 12" TERMINAL 6 OF CRUISE CONTROL ACTUATOR "TERMINAL 7 "TERMINAL 11 OF
CRUISE CONTROL ECU. AS A RESULT, THE MOTOR IN THE CRUISE CONTROL ACTUATOR IS ROTATED TO OPEN THE THROTTLE
VALVE AND THE THROTTLE CABLE IS PULLED TO INCREASE THE VEHICLE SPEED. WHEN THE ACTUAL DRIVING SPEED IS HIGHER
THAN THE SET SPEED, THE CURRENT TO CRUISE CONTROL ACTUATOR FLOWS FROM TERMINAL 11 OF ECU "TERMINAL 7 OF
CRUISE CONTROL ACTUATOR "TERMINAL 6 "TERMINAL 12 OF CRUISE CONTROL ECU.
THIS CAUSES THE MOTOR IN THE CRUISE CONTROL ACTUATOR TO ROTATE TO CLOSE THE THROTTLE VALVE AND RETURN THE
THROTTLE CABLE TO DECREASE THE VEHICLE SPEED.
3. COAST CONTROL
DURING THE CRUISE CONTROL DRIVING, WHILE THE COAST SW IS ON, THE CRUISE CONTROL ACTUATOR RETURNS THE
THROTTLE CABLE TO CLOSE THE THROTTLE VALVE AND DECREASE THE DRIVING SPEED. THE VEHICLE SPEED WHEN THE COAST
SW IS TURNED OFF IS MEMORIZED AND THE VEHICLE CONTINUES AT THE NEW SET SPEED.
4. ACCEL CONTROL
DURING CRUISE CONTROL DRIVING, WHILE THE ACCEL SW IS TURNED ON, THE CRUISE CONTROL ACTUATOR PULLS THE
THROTTLE CABLE TO OPEN THE THROTTLE VALVE AND INCREASE THE DRIVING SPEED.
THE VEHICLE SPEED WHEN THE ACCEL SW IS TURNED OFF IS MEMORIZED AND THE VEHICLE CONTINUES AT THE NEW SET
SPEED.
5. RESUME CONTROL
UNLESS THE VEHICLE SPEED FALLS BELOW THE MINIMUM SPEED LIMIT (APPROX. 40 KM/H, 25 MPH) AFTER CANCELING THE SET
SPEED BY THE CANCEL SW, PUSHING THE RESUME SW WILL CAUSE THE VEHICLE TO RESUME THE SPEED SET BEFORE
CANCELLATION.
6. MANUAL CANCEL MECHANISM
IF ANY OF THE FOLLOWING OPERATIONS OCCURS DURING CRUISE CONTROL OPERATION, CURRENT FLOW TO MAGNETIC
CLUTCH OF THE ACTUATOR IS CUT TURNS OFF AND THE MOTOR ROTATES TO CLOSE THE THROTTLE VALVE AND THE CRUISE
CONTROL IS RELEASED.
*PLACING THE SHIFT LEVER IN ªNº POSITION (PARK/NEUTRAL POSITION SW (NEUTRAL START SW ON). ªSIGNAL INPUT TO
TERMINAL 2 OF ECUº (A/T)
*DEPRESSING THE CLUTCH PEDAL (CLUCH SW ON). ªSIGNAL INPUT TO TERMINAL 2 OF THE ECUº (M/T)
*DEPRESSING THE BRAKE PEDAL (STOP LIGHT SW ON). ªSIGNAL INPUT TO TERMINAL 16 OF ECUº
*PUSH THE CANCEL SW (CANCEL SW ON). ªSIGNAL INPUT TO TERMINAL 18 OF ECUº
*DEPRESSING THE PARKING BRAKE PEDAL (PARKING BRAKE SW ON). ªSIGNAL INPUT TO TERMINAL 3 OF ECUº (3VZ±FE)
*PULLING THE PARKING BRAKE LEVER (PARKING BRAKE SW ON). ªSIGNAL INPUT TO TERMINAL 3 OF THE ECUº (5S±FE)
SYSTEM OUTLINE
Page 198 of 307
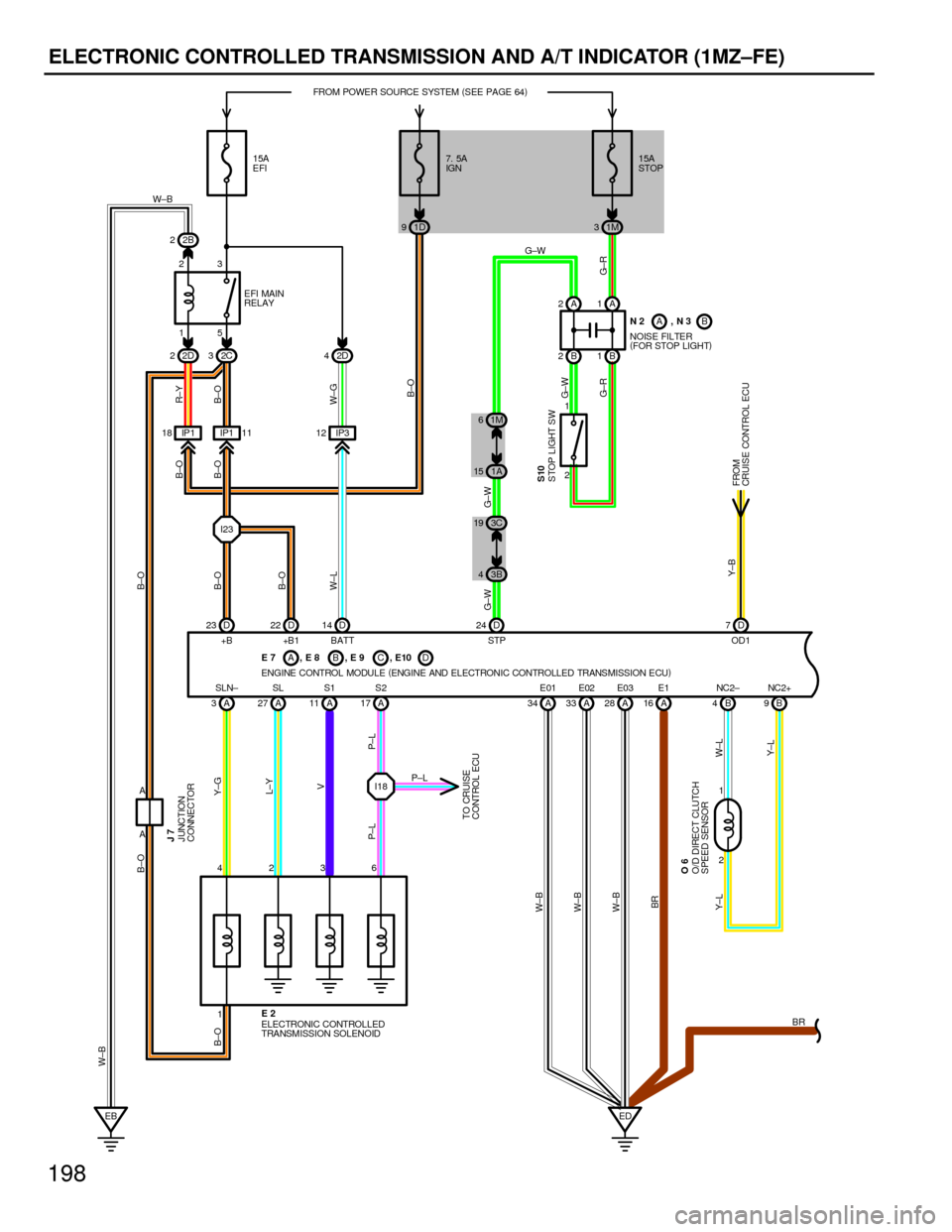
198
ELECTRONIC CONTROLLED TRANSMISSION AND A/T INDICATOR (1MZ±FE)
A
2D 22C32D4 2B 2
I23
I18
2 1
EBED IP 1 18 IP1 11 IP312
D 7 D 24 D 14 D 22 D 23
A 27 A11 A17 A33 B4
26FROM POWER SOURCE SYSTEM(
SEE PAGE 64)
P±L P±LV L±Y W±B
B±O
B±OB±O
W±L
G±W G±W
Y±BW±GB±OR±Y
W±L Y±L W±BB±O
15A
EFI
SL S1 S2 E02 NC2± +B +B1 BATT STP OD1EFI MAIN
RELAY
FROM
CRUIS E CONTROL ECU
BR P±L
TO CRUISE
CONTROL ECU
15 23
O/D DIRECT CLUTCH
SPEED SENSOR O6STOP LIGHT SW
G±R
G±W
2 1
S10
B 1 A 2
B 2B1NOISE FILTER
(
FOR STOP LIGHT) N2 ,N3 A
G±W
G±R
B E7 ,E8AC,E9
ENGINE CONTROL MODULE(
ENGINE AND ELECTRONIC CONTROLLED TRANSMISSION ECU)
B±O
D ,E10
A
3
ELECTRONIC CONTROLLED
TRANSMISSION SOLENOID E2 4 A
1
J UNCTION
CONNECTOR J7
A 3SLN±
Y±GB±O
B±OB±O
W±B
W±B
BR
A 34E01
A 28E03
A 16E1
B 9NC2+
Y±L
W±B
1D 91M3 7. 5A
IGN15A
STOP
1A 15
3B 43C 191M 6
Page 199 of 307
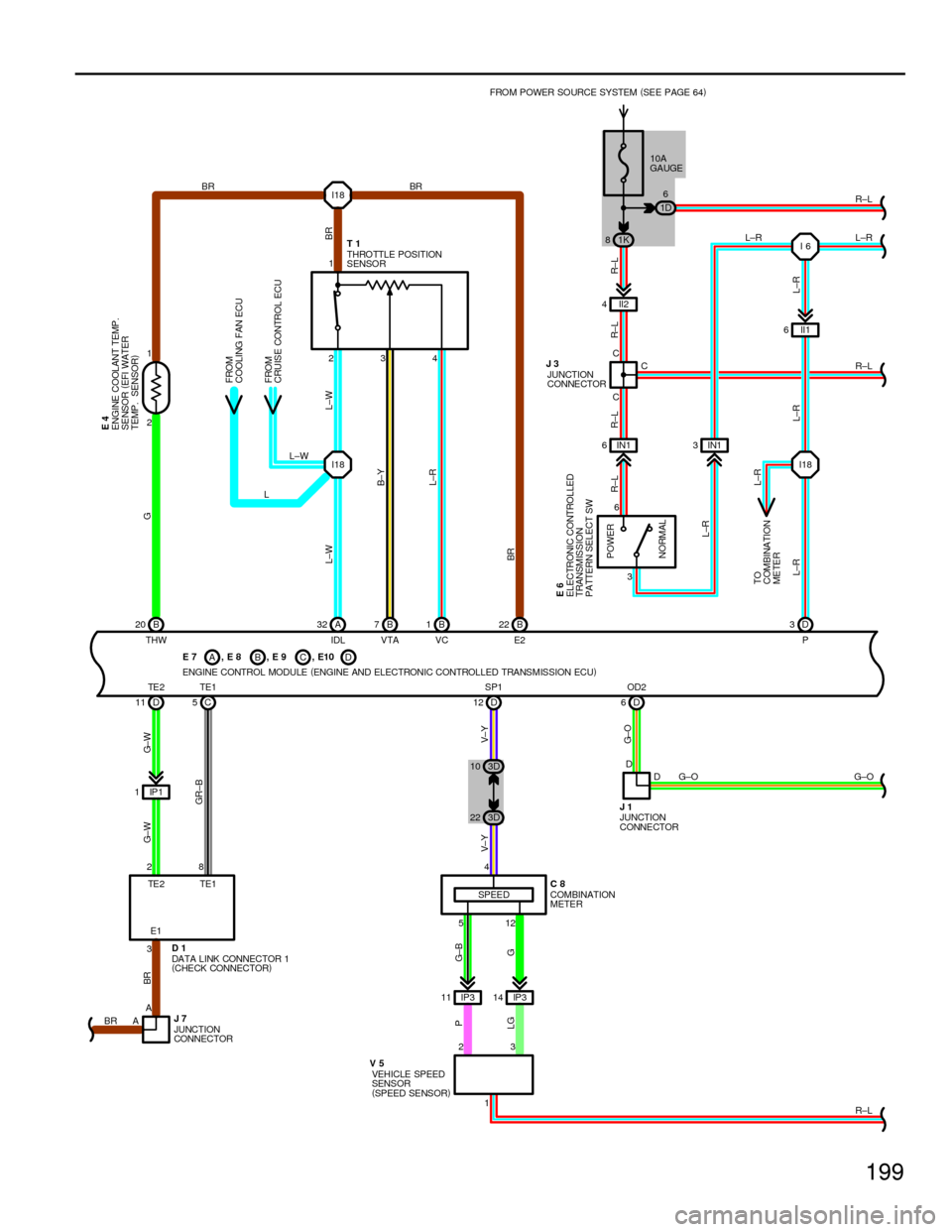
199
3
3C
28D 6 C 1
234I6
I18 I18
C
D B 20 A32 B7B1B22
C 5D 6D 3
D 112 1
BRG±OR±L L±R R±L
L±R BR BR
GR±B G±W
G± OL±R B±Y L±WG
BR
BR
R±L R±L
L±R L±RL±R
G±O THW IDL VTA VCP E2
L±W
L±WII2 4
R±L ENGINE COOLANT TEMP.
SENSOR(
EFI WATER
TEMP. SENSOR)
FROM
CRUISE CONTROL ECU
THROTTLE POSITION
SENSORFROM POWER SOURCE SYSTEM(
SEE PAGE 64)
JUNCTION
CONNECTOR
POWER
NORMAL ELECTRONIC CONTROLLED
TRANSMISSION
PATTERN SELECT SW
TE 2 TE1OD2
E1 TE 2 TE1
DA TA LINK CONNECTOR 1
(
CHECK CONNECTOR)JUNCTION
CONNECTOR D 12
SPEED
IP3 11 IP314 5124
G±B
G
23
1 VEHICLE SPEED
SENSOR
(
SPEED SENSOR)
LGP
R±L SP1
COMBINATION
METER
V5C8 T1
J3
E6E4
J1
D1I18II1 6
L±R TO
COMBINATION
METERL±R
IN1 6IN13
R±L
B E7 ,E8
AC,E9
ENGINE CONTROL MODULE(
ENGINE AND ELECTRONIC CONTROLLED TRANSMISSION ECU)
FROM
COOLING FAN ECU
L
D ,E10
IP 1 1
G± W
V±Y V±Y
AA
JUNCTION
CONNECTOR J7
BR
1K 81D6
3D 223D 10
10A
GAUGE
Page 201 of 307
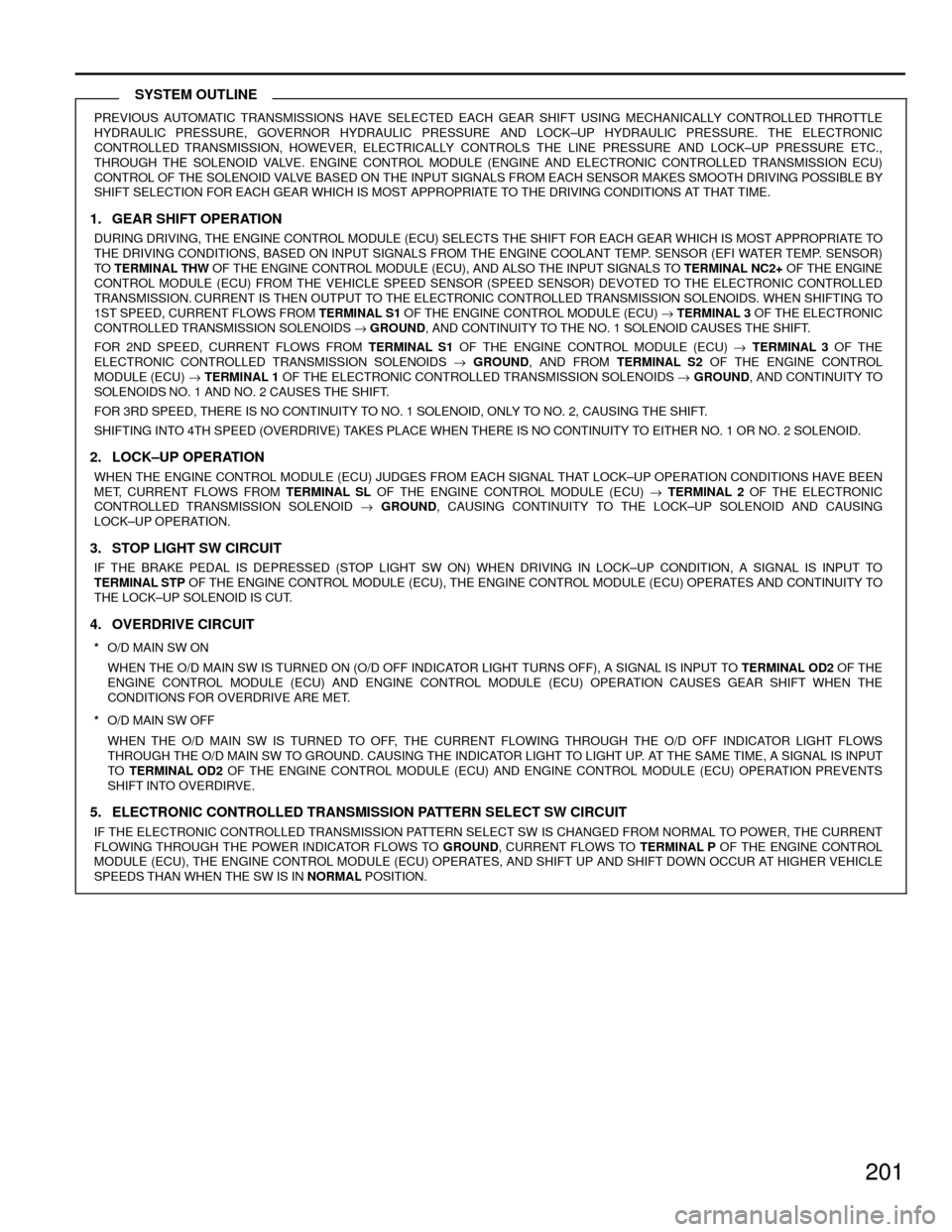
201
PREVIOUS AUTOMATIC TRANSMISSIONS HAVE SELECTED EACH GEAR SHIFT USING MECHANICALLY CONTROLLED THROTTLE
HYDRAULIC PRESSURE, GOVERNOR HYDRAULIC PRESSURE AND LOCK±UP HYDRAULIC PRESSURE. THE ELECTRONIC
CONTROLLED TRANSMISSION, HOWEVER, ELECTRICALLY CONTROLS THE LINE PRESSURE AND LOCK±UP PRESSURE ETC.,
THROUGH THE SOLENOID VALVE. ENGINE CONTROL MODULE (ENGINE AND ELECTRONIC CONTROLLED TRANSMISSION ECU)
CONTROL OF THE SOLENOID VALVE BASED ON THE INPUT SIGNALS FROM EACH SENSOR MAKES SMOOTH DRIVING POSSIBLE BY
SHIFT SELECTION FOR EACH GEAR WHICH IS MOST APPROPRIATE TO THE DRIVING CONDITIONS AT THAT TIME.
1. GEAR SHIFT OPERATION
DURING DRIVING, THE ENGINE CONTROL MODULE (ECU) SELECTS THE SHIFT FOR EACH GEAR WHICH IS MOST APPROPRIATE TO
THE DRIVING CONDITIONS, BASED ON INPUT SIGNALS FROM THE ENGINE COOLANT TEMP. SENSOR (EFI WATER TEMP. SENSOR)
TO TERMINAL THW OF THE ENGINE CONTROL MODULE (ECU), AND ALSO THE INPUT SIGNALS TO TERMINAL NC2+ OF THE ENGINE
CONTROL MODULE (ECU) FROM THE VEHICLE SPEED SENSOR (SPEED SENSOR) DEVOTED TO THE ELECTRONIC CONTROLLED
TRANSMISSION. CURRENT IS THEN OUTPUT TO THE ELECTRONIC CONTROLLED TRANSMISSION SOLENOIDS. WHEN SHIFTING TO
1ST SPEED, CURRENT FLOWS FROM TERMINAL S1 OF THE ENGINE CONTROL MODULE (ECU) " TERMINAL 3 OF THE ELECTRONIC
CONTROLLED TRANSMISSION SOLENOIDS " GROUND, AND CONTINUITY TO THE NO. 1 SOLENOID CAUSES THE SHIFT.
FOR 2ND SPEED, CURRENT FLOWS FROM TERMINAL S1 OF THE ENGINE CONTROL MODULE (ECU) " TERMINAL 3 OF THE
ELECTRONIC CONTROLLED TRANSMISSION SOLENOIDS " GROUND, AND FROM TERMINAL S2 OF THE ENGINE CONTROL
MODULE (ECU) " TERMINAL 1 OF THE ELECTRONIC CONTROLLED TRANSMISSION SOLENOIDS " GROUND, AND CONTINUITY TO
SOLENOIDS NO. 1 AND NO. 2 CAUSES THE SHIFT.
FOR 3RD SPEED, THERE IS NO CONTINUITY TO NO. 1 SOLENOID, ONLY TO NO. 2, CAUSING THE SHIFT.
SHIFTING INTO 4TH SPEED (OVERDRIVE) TAKES PLACE WHEN THERE IS NO CONTINUITY TO EITHER NO. 1 OR NO. 2 SOLENOID.
2. LOCK±UP OPERATION
WHEN THE ENGINE CONTROL MODULE (ECU) JUDGES FROM EACH SIGNAL THAT LOCK±UP OPERATION CONDITIONS HAVE BEEN
MET, CURRENT FLOWS FROM TERMINAL SL OF THE ENGINE CONTROL MODULE (ECU) " TERMINAL 2 OF THE ELECTRONIC
CONTROLLED TRANSMISSION SOLENOID " GROUND, CAUSING CONTINUITY TO THE LOCK±UP SOLENOID AND CAUSING
LOCK±UP OPERATION.
3. STOP LIGHT SW CIRCUIT
IF THE BRAKE PEDAL IS DEPRESSED (STOP LIGHT SW ON) WHEN DRIVING IN LOCK±UP CONDITION, A SIGNAL IS INPUT TO
TERMINAL STP OF THE ENGINE CONTROL MODULE (ECU), THE ENGINE CONTROL MODULE (ECU) OPERATES AND CONTINUITY TO
THE LOCK±UP SOLENOID IS CUT.
4. OVERDRIVE CIRCUIT
*O/D MAIN SW ON
WHEN THE O/D MAIN SW IS TURNED ON (O/D OFF INDICATOR LIGHT TURNS OFF), A SIGNAL IS INPUT TO TERMINAL OD2 OF THE
ENGINE CONTROL MODULE (ECU) AND ENGINE CONTROL MODULE (ECU) OPERATION CAUSES GEAR SHIFT WHEN THE
CONDITIONS FOR OVERDRIVE ARE MET.
*O/D MAIN SW OFF
WHEN THE O/D MAIN SW IS TURNED TO OFF, THE CURRENT FLOWING THROUGH THE O/D OFF INDICATOR LIGHT FLOWS
THROUGH THE O/D MAIN SW TO GROUND. CAUSING THE INDICATOR LIGHT TO LIGHT UP. AT THE SAME TIME, A SIGNAL IS INPUT
TO TERMINAL OD2 OF THE ENGINE CONTROL MODULE (ECU) AND ENGINE CONTROL MODULE (ECU) OPERATION PREVENTS
SHIFT INTO OVERDIRVE.
5. ELECTRONIC CONTROLLED TRANSMISSION PATTERN SELECT SW CIRCUIT
IF THE ELECTRONIC CONTROLLED TRANSMISSION PATTERN SELECT SW IS CHANGED FROM NORMAL TO POWER, THE CURRENT
FLOWING THROUGH THE POWER INDICATOR FLOWS TO GROUND, CURRENT FLOWS TO TERMINAL P OF THE ENGINE CONTROL
MODULE (ECU), THE ENGINE CONTROL MODULE (ECU) OPERATES, AND SHIFT UP AND SHIFT DOWN OCCUR AT HIGHER VEHICLE
SPEEDS THAN WHEN THE SW IS IN NORMAL POSITION.
SYSTEM OUTLINE
Page 204 of 307
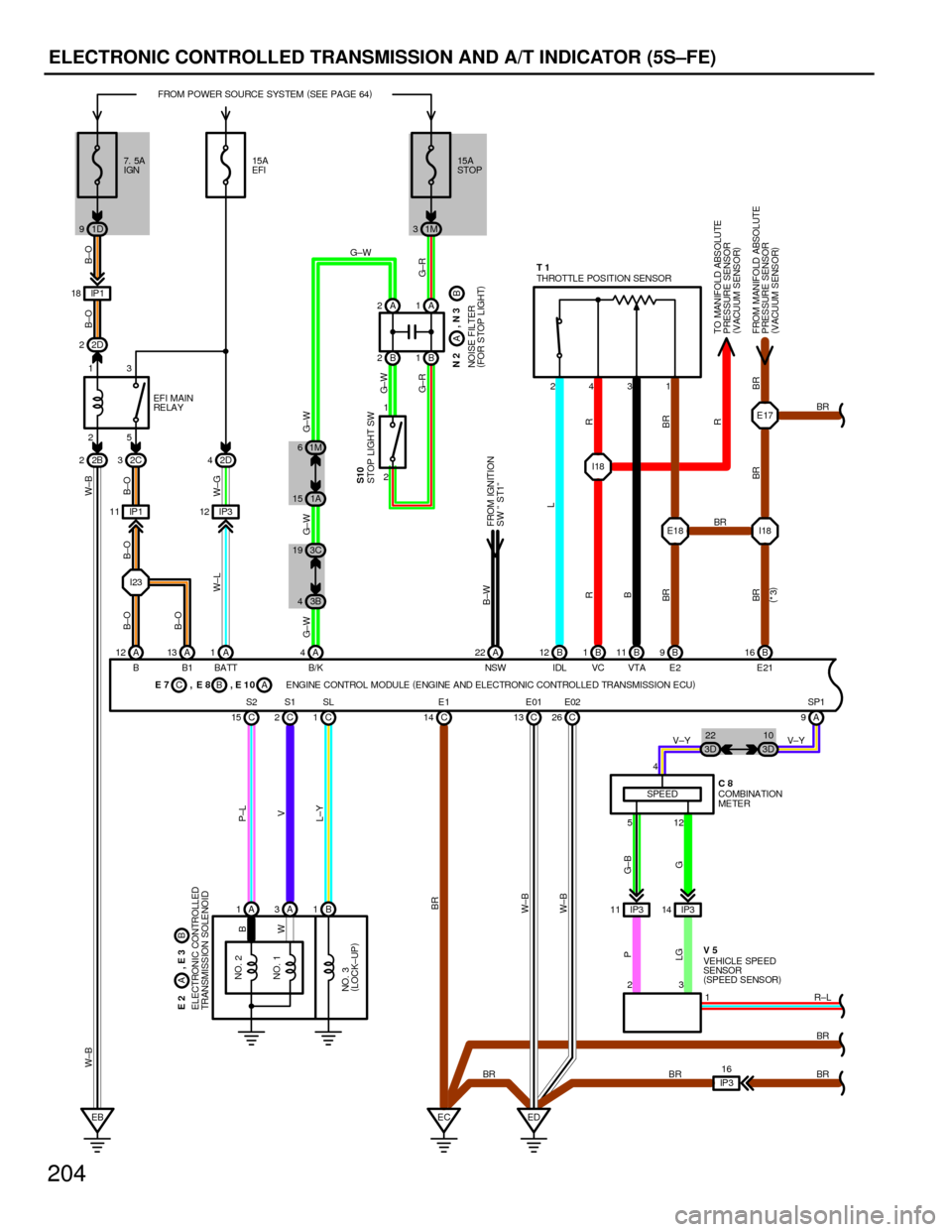
204
ELECTRONIC CONTROLLED TRANSMISSION AND A/T INDICATOR (5S±FE)
A
C,B
A2D 2
2B 22C32D4
IP 1 11 IP312 IP 1 18
I23
A 1A3B1 A 12
BA 13
B1A 1
BATTA 4
B/KA 22
NSWB 12
IDLB 1
VCB 11
VTAB 9
E2
C 15S2
C 2S1
C 1SL
C 14E1
C 13E01
C 26E02
EBEC EDE21 2431
I18
E18 I18BRBR
BR
B±O B±O
G±W
R
BR
R
BR BRR B±W G±W G±WW±B
B±O
W±G B±O B±O
B±O
W±L
V
L±Y P±L
W±B
W±BBR W±B
L
B
FROM POWER SOURCE SYSTEM(
SEE PAGE 64)
15A
EFI
EFI MAIN
RE LA YTHROTTLE POSITION SENSOR
ELECTRONIC CONTROLLED
TRANSMISSION SOLENOID
FROM IGNITION
SW º ST1º
IP 316
BR
E2 ,E3
E7 E8 ,E10T1
A
B
WB
B 16E17
25 13
A 9
SPEED
IP3 11 IP314 5124
G±B
G
23
1 VEHICLE SPEED
SENSOR
(
SPEED SENSOR)
LGP
R±L SP1
COMBINATION
METER
V5C8V±Y V±Y
BR BR FROM MANIFOLD ABSOLUTE
PRESSURE SENSOR
(
V ACUUM S ENS OR) TO MANIFOLD ABSOLUTE
PRESSURE SENSOR
(
V ACUUM S ENS OR)
BR
BR
STOP LIGHT SW
G±R
G±W
2 1
S10
B
1 A 2
B 2B1
NOISE FILTER
(
FOR S TOP L IGHT) N2 ,N3
A
G± W
G±R NO. 3
(
LOCK±UP) NO. 1 NO. 2
E NGINE CONTROL MODULE(
ENGINE AND ELECTRONIC CONTROLLED TRANSMISSION ECU)
(
*3)
1A 15
3B 43C 191M 6
1D 97. 5A
IGN1M 315A
STOP
3D22
3D10