TOYOTA SUPRA 1986 Service Repair Manual
Manufacturer: TOYOTA, Model Year: 1986, Model line: SUPRA, Model: TOYOTA SUPRA 1986Pages: 878, PDF Size: 20 MB
Page 241 of 878
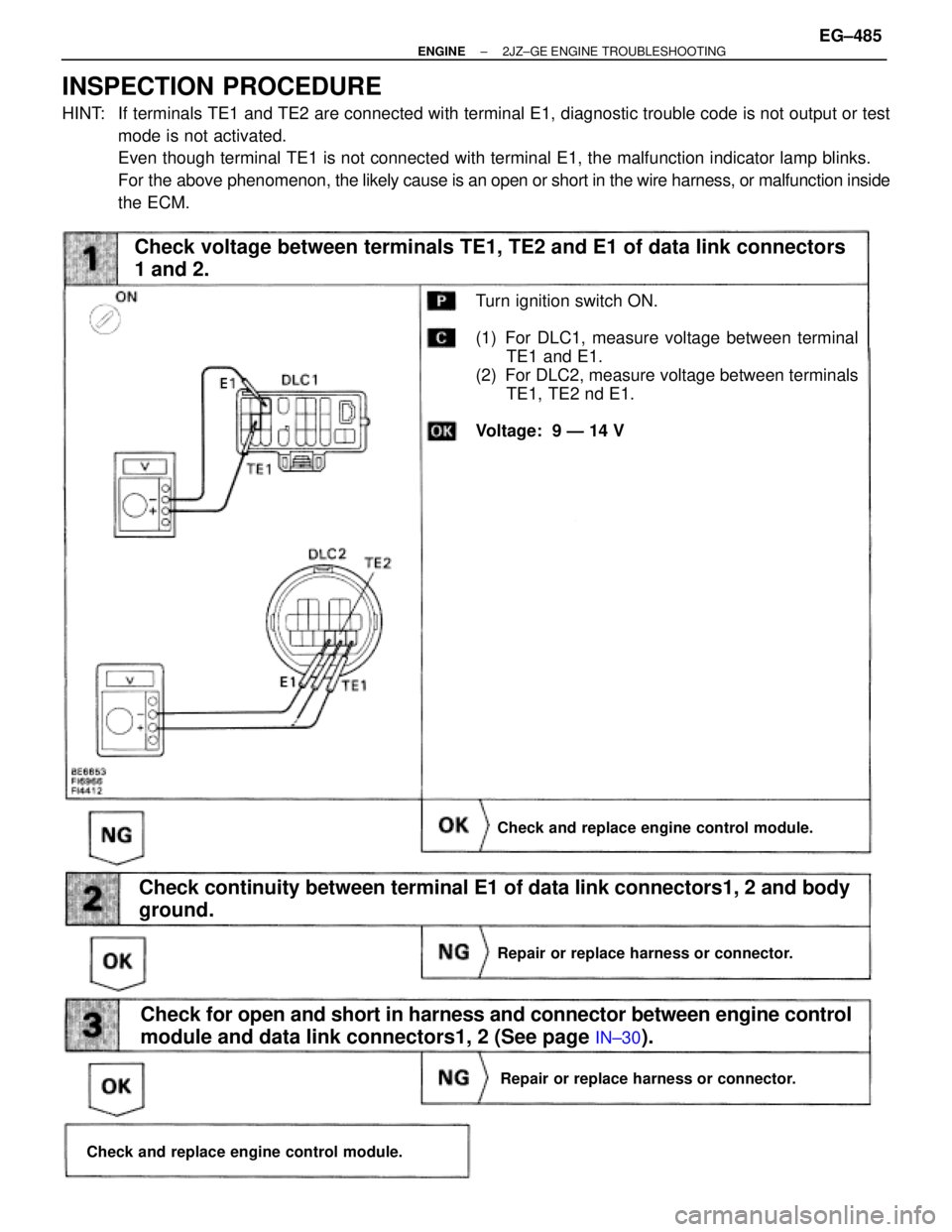
Check voltage between terminals TE1, TE2 and E1 of data link connectors
1 and 2.
Turn ignition switch ON.
(1) For DLC1, measure voltage between terminal
TE1 and E1.
(2) For DLC2, measure voltage between terminals
TE1, TE2 nd E1.
Voltage: 9 Ð 14 V
Check and replace engine control module.
Check continuity between terminal E1 of data link connectors1, 2 and body
ground.
Repair or replace harness or connector.
Check and replace engine control module.
Check for open and short in harness and connector between engine control
module and data link connectors1, 2 (See page
IN±30).
Repair or replace harness or connector.
INSPECTION PROCEDURE
HINT: If terminals TE1 and TE2 are connected with terminal E1, diagnostic trouble code is not output or test
mode is not activated.
Even though terminal TE1 is not connected with terminal E1, the malfunction indicator lamp blinks.
For the above phenomenon, the likely cause is an open or short in the wire harness, or malfunction inside
the ECM.
± ENGINE2JZ±GE ENGINE TROUBLESHOOTINGEG±485
Page 242 of 878
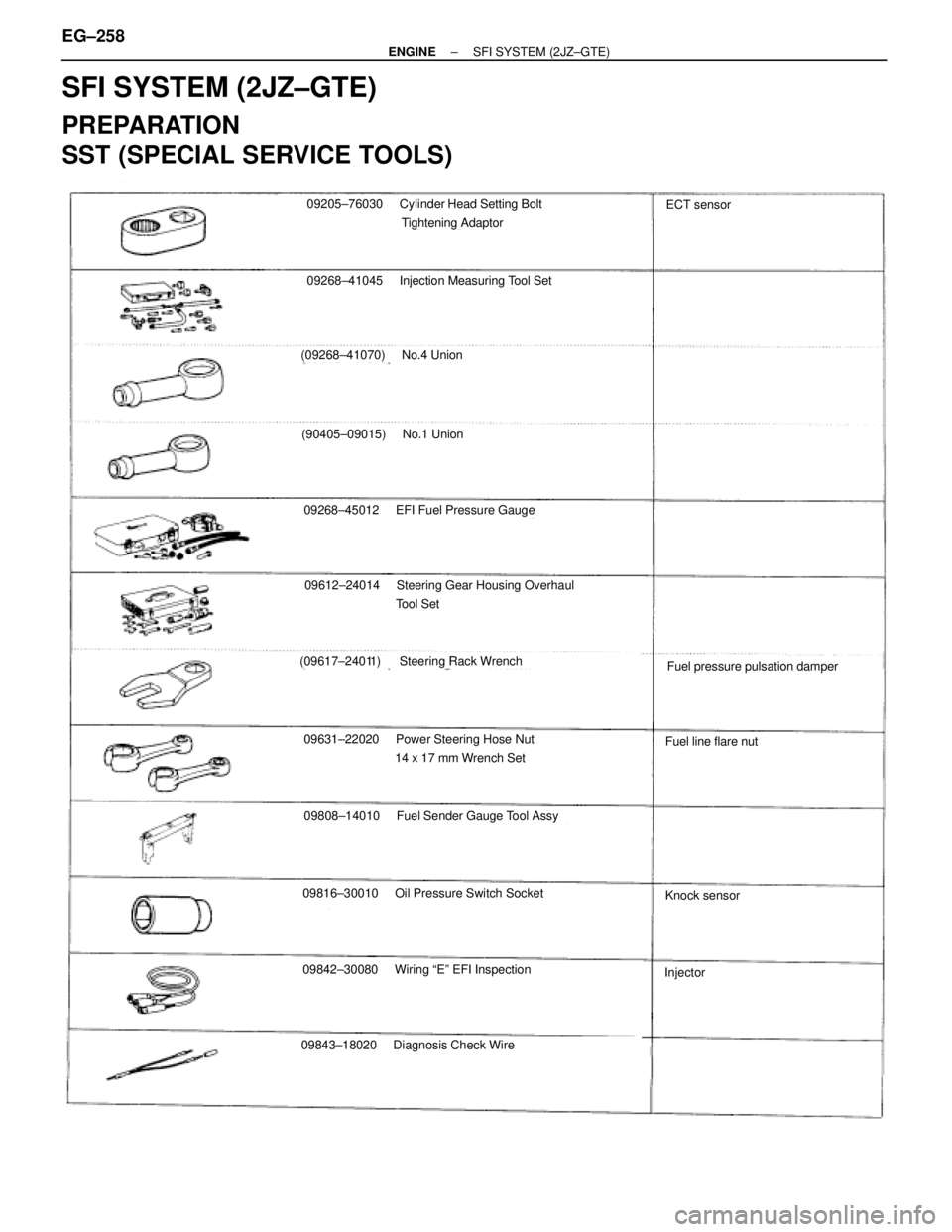
SFI SYSTEM (2JZ±GTE)
PREPARATION
SST (SPECIAL SERVICE TOOLS)
09205±76030 Cylinder Head Setting Bolt
Tightening Adaptor
09268±41045Injection Measuring Tool Set
(09268±41070)No.4 Union
(90405±09015)No.1 Union
09268±45012 EFI Fuel Pressure Gauge
ECT sensor
09612±24014 Steering Gear Housing Overhaul
Tool Set
(09617±24011) Steering Rack Wrench
09631±22020 Power Steering Hose Nut
14 x 17 mm Wrench Set
09808±14010Fuel Sender Gauge Tool Assy
09816±30010 Oil Pressure Switch Socket
09842±30080 Wiring ªEº EFI Inspection
Knock sensor
Fuel pressure pulsation damper
09843±18020 Diagnosis Check Wire
Injector
Fuel line flare nut
EG±258± ENGINESFI SYSTEM (2JZ±GTE)
Page 243 of 878
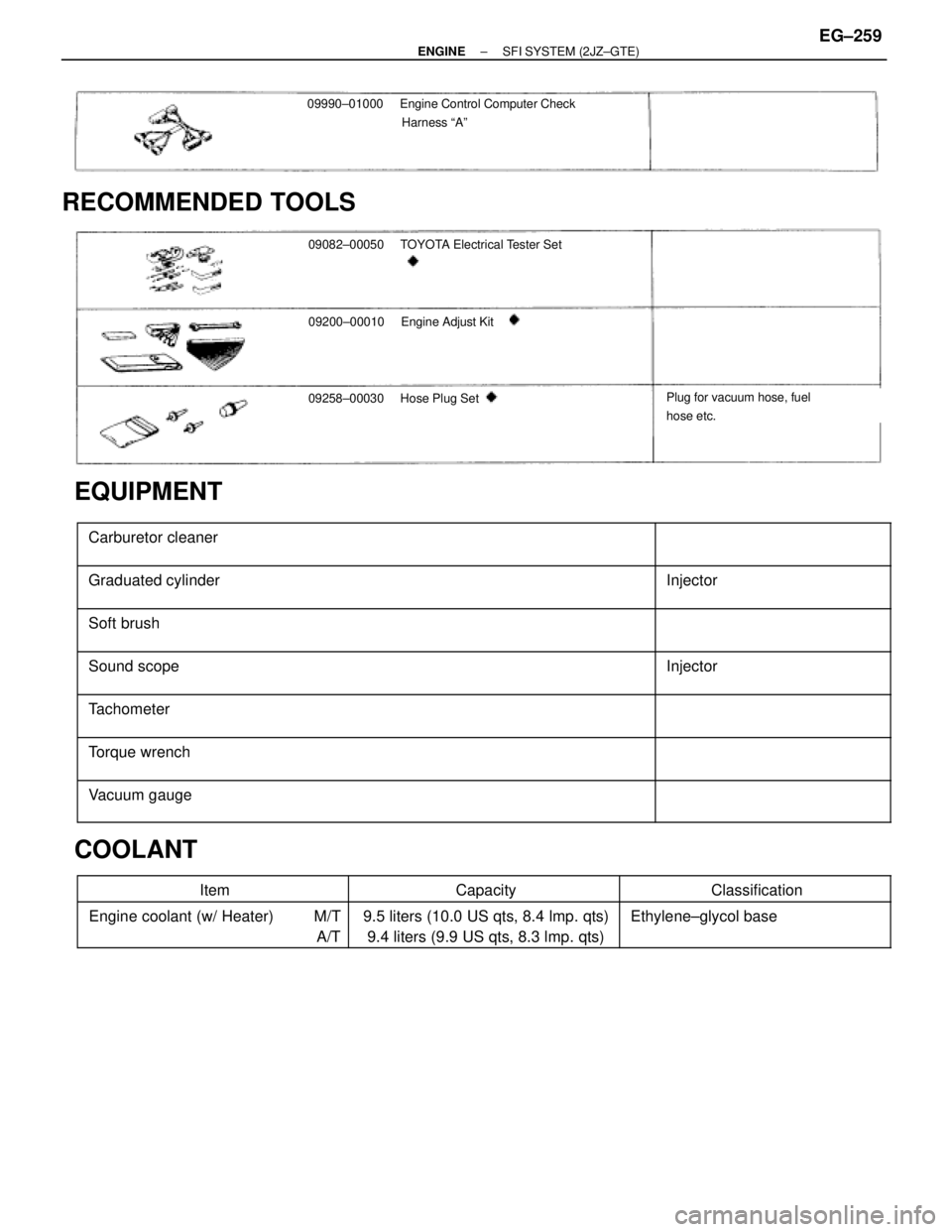
09990±01000Engine Control Computer Check
Harness ªAº
RECOMMENDED TOOLS
09082±00050 TOYOTA Electrical Tester Set
09200±00010Engine Adjust Kit
09258±00030 Hose Plug SetPlug for vacuum hose, fuel
hose etc.
EQUIPMENT
Carburetor cleaner
Graduated cylinder
Injector
Soft brush
Sound scope
Injector
Tachometer
Torque wrench
Vacuum gauge
COOLANT
Item Capacity Classification
Engine coolant (w/ Heater) M/T
A/T
9.5 liters (10.0 US qts, 8.4 lmp. qts)
9.4 liters (9.9 US qts, 8.3 lmp. qts)
Ethylene±glycol base
± ENGINESFI SYSTEM (2JZ±GTE)EG±259
Page 244 of 878
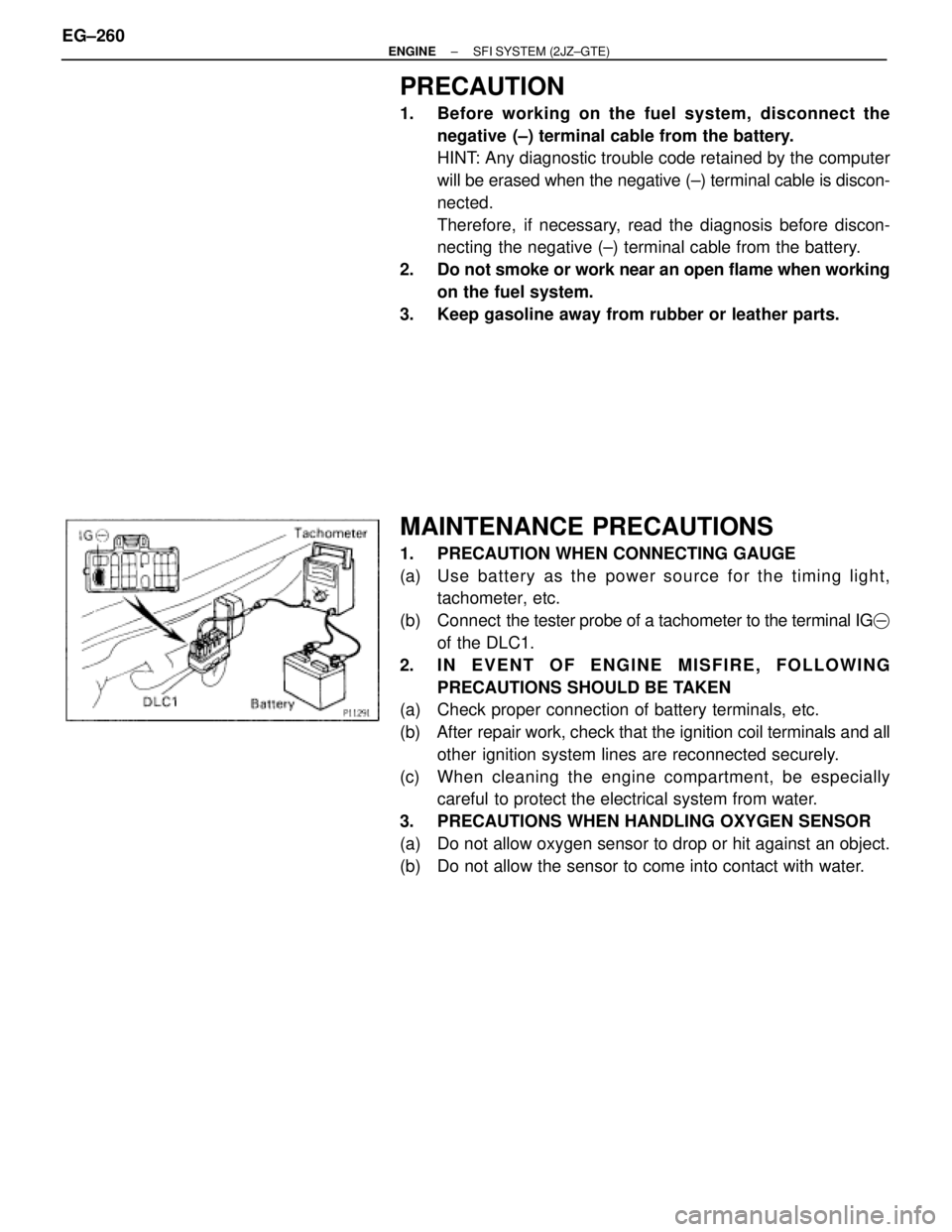
PRECAUTION
1. Before working on the fuel system, disconnect the
negative (±) terminal cable from the battery.
HINT: Any diagnostic trouble code retained by the computer
will be erased when the negative (±) terminal cable is discon-
nected.
Therefore, if necessary, read the diagnosis before discon-
necting the negative (±) terminal cable from the battery.
2. Do not smoke or work near an open flame when working
on the fuel system.
3. Keep gasoline away from rubber or leather parts.
MAINTENANCE PRECAUTIONS
1. PRECAUTION WHEN CONNECTING GAUGE
(a) Use ba tte ry as th e po we r so u rce fo r th e timin g lig h t,
tachometer, etc.
(b) Connect the tester probe of a tachometer to the terminal IG
of the DLC1.
2. IN EVENT OF ENGINE MISFIRE, FOLLOWING
PRECAUTIONS SHOULD BE TAKEN
(a) Check proper connection of battery terminals, etc.
(b) After repair work, check that the ignition coil terminals and all
other ignition system lines are reconnected securely.
(c) When cleaning the engine compartment, be especially
careful to protect the electrical system from water.
3. PRECAUTIONS WHEN HANDLING OXYGEN SENSOR
(a) Do not allow oxygen sensor to drop or hit against an object.
(b) Do not allow the sensor to come into contact with water. EG±260
± ENGINESFI SYSTEM (2JZ±GTE)
Page 245 of 878
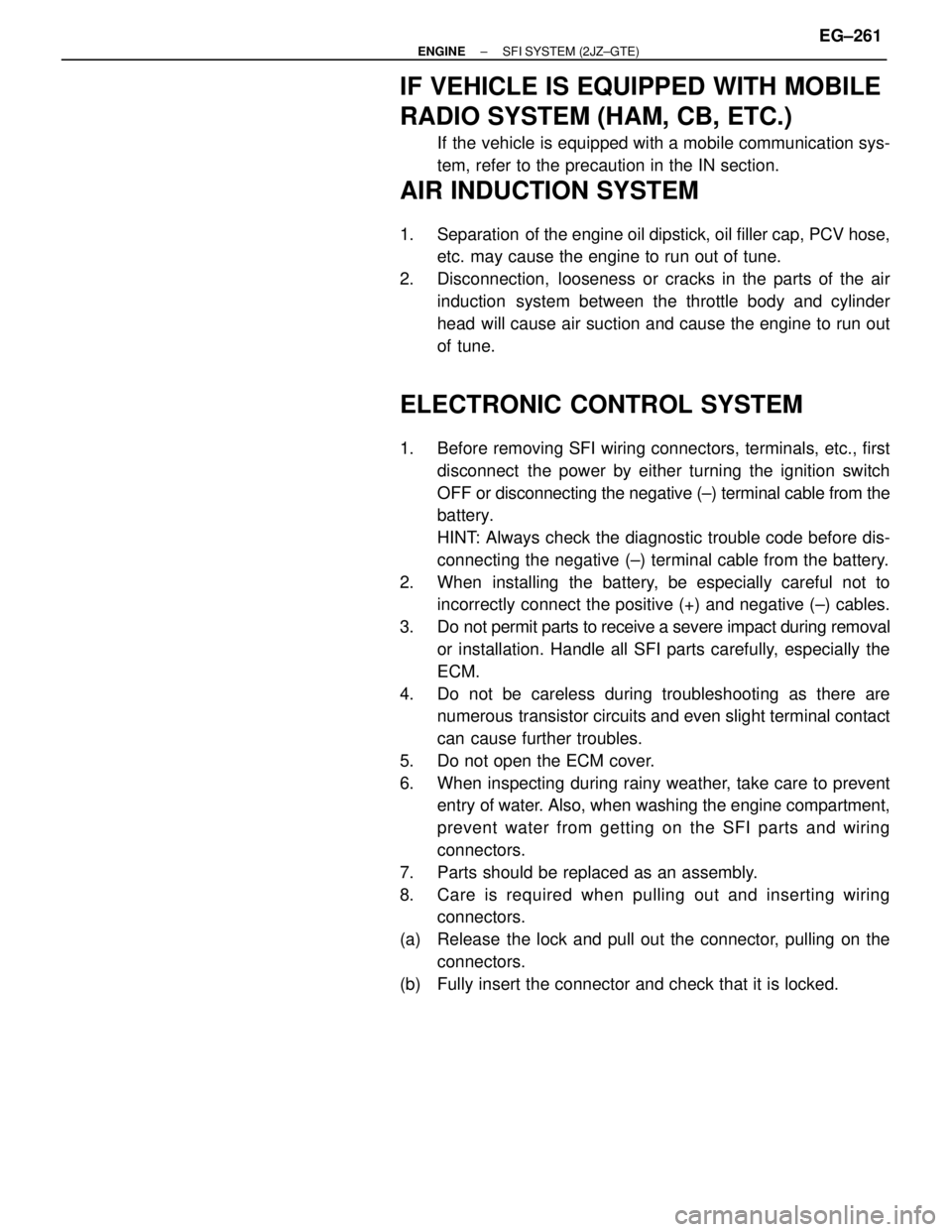
IF VEHICLE IS EQUIPPED WITH MOBILE
RADIO SYSTEM (HAM, CB, ETC.)
If the vehicle is equipped with a mobile communication sys-
tem, refer to the precaution in the IN section.
AIR INDUCTION SYSTEM
1. Separation of the engine oil dipstick, oil filler cap, PCV hose,
etc. may cause the engine to run out of tune.
2. Disconnection, looseness or cracks in the parts of the air
induction system between the throttle body and cylinder
head will cause air suction and cause the engine to run out
of tune.
ELECTRONIC CONTROL SYSTEM
1. Before removing SFI wiring connectors, terminals, etc., first
disconnect the power by either turning the ignition switch
OFF or disconnecting the negative (±) terminal cable from the
battery.
HINT: Always check the diagnostic trouble code before dis-
connecting the negative (±) terminal cable from the battery.
2. When installing the battery, be especially careful not to
incorrectly connect the positive (+) and negative (±) cables.
3. Do not permit parts to receive a severe impact during removal
or installation. Handle all SFI parts carefully, especially the
ECM.
4. Do not be careless during troubleshooting as there are
numerous transistor circuits and even slight terminal contact
can cause further troubles.
5. Do not open the ECM cover.
6. When inspecting during rainy weather, take care to prevent
entry of water. Also, when washing the engine compartment,
prevent water from getting on the SFI parts and wiring
connectors.
7. Parts should be replaced as an assembly.
8. Care is required when pulling out and inserting wiring
connectors.
(a) Release the lock and pull out the connector, pulling on the
connectors.
(b) Fully insert the connector and check that it is locked.
± ENGINESFI SYSTEM (2JZ±GTE)EG±261
Page 246 of 878
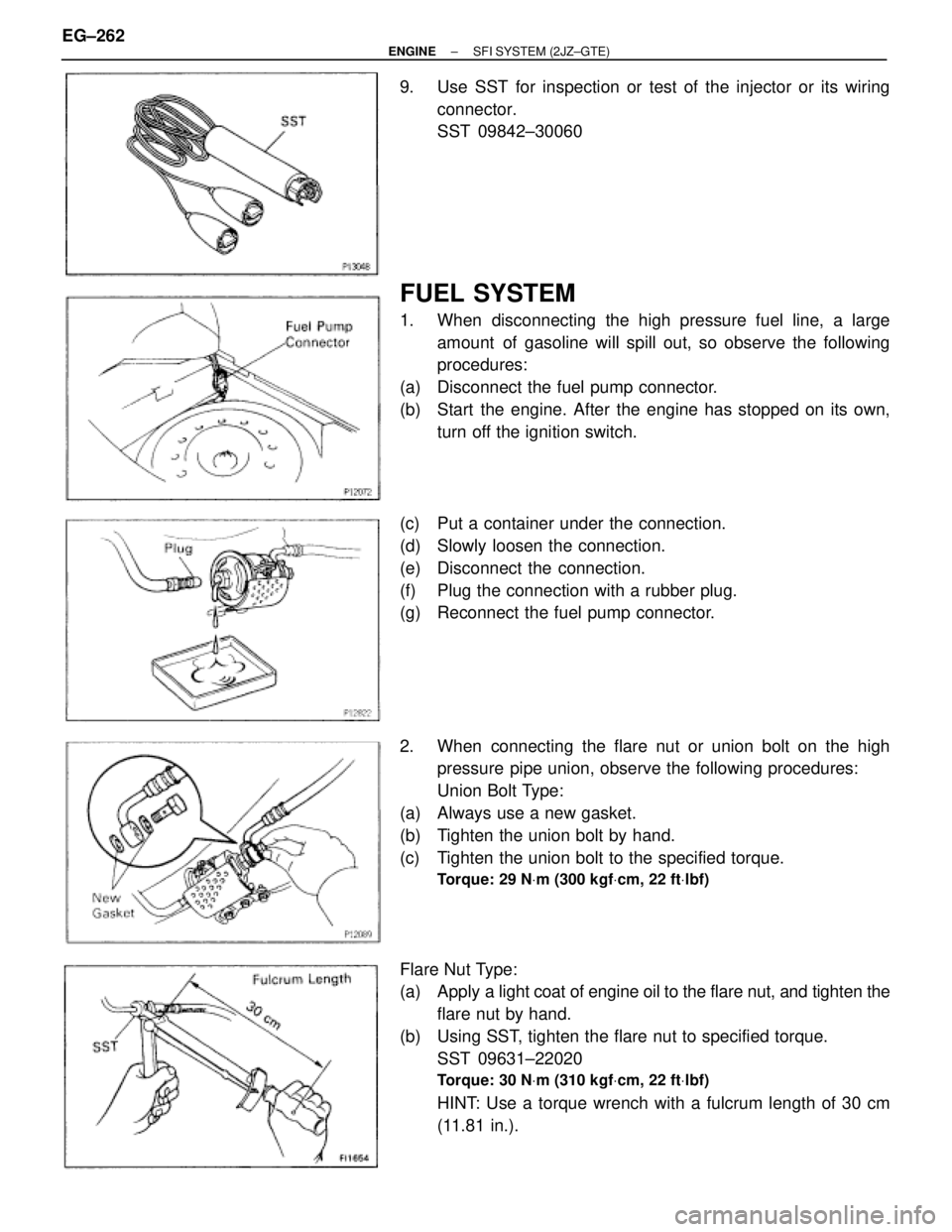
9. Use SST for inspection or test of the injector or its wiring
connector.
SST 09842±30060
FUEL SYSTEM
1. When disconnecting the high pressure fuel line, a large
amount of gasoline will spill out, so observe the following
procedures:
(a) Disconnect the fuel pump connector.
(b) Start the engine. After the engine has stopped on its own,
turn off the ignition switch.
(c) Put a container under the connection.
(d) Slowly loosen the connection.
(e) Disconnect the connection.
(f) Plug the connection with a rubber plug.
(g) Reconnect the fuel pump connector.
2. When connecting the flare nut or union bolt on the high
pressure pipe union, observe the following procedures:
Union Bolt Type:
(a) Always use a new gasket.
(b) Tighten the union bolt by hand.
(c) Tighten the union bolt to the specified torque.
Torque: 29 NVm (300 kgfVcm, 22 ftVlbf)
Flare Nut Type:
(a) Apply a light coat of engine oil to the flare nut, and tighten the
flare nut by hand.
(b) Using SST, tighten the flare nut to specified torque.
SST 09631±22020
Torque: 30 NVm (310 kgfVcm, 22 ftVlbf)
HINT: Use a torque wrench with a fulcrum length of 30 cm
(11.81 in.). EG±262
± ENGINESFI SYSTEM (2JZ±GTE)
Page 247 of 878
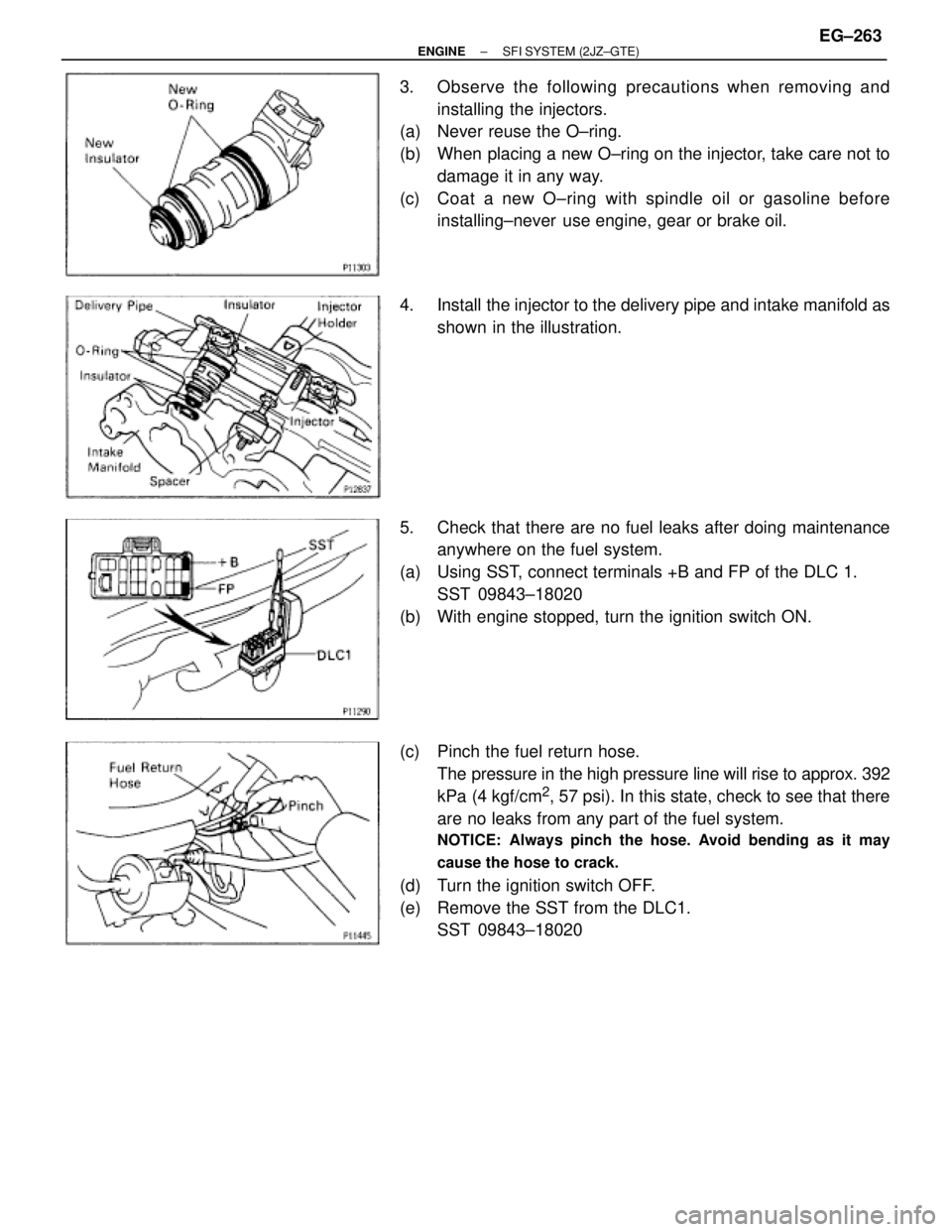
3. Observe the following precautions when removing and
installing the injectors.
(a) Never reuse the O±ring.
(b) When placing a new O±ring on the injector, take care not to
damage it in any way.
(c) Coat a new O±ring with spindle oil or gasoline before
installing±never use engine, gear or brake oil.
4. Install the injector to the delivery pipe and intake manifold as
shown in the illustration.
5. Check that there are no fuel leaks after doing maintenance
anywhere on the fuel system.
(a) Using SST, connect terminals +B and FP of the DLC 1.
SST 09843±18020
(b) With engine stopped, turn the ignition switch ON.
(c) Pinch the fuel return hose.
The pressure in the high pressure line will rise to approx. 392
kPa (4 kgf/cm
2, 57 psi). In this state, check to see that there
are no leaks from any part of the fuel system.
NOTICE: Always pinch the hose. Avoid bending as it may
cause the hose to crack.
(d) Turn the ignition switch OFF.
(e) Remove the SST from the DLC1.
SST 09843±18020
± ENGINESFI SYSTEM (2JZ±GTE)EG±263
Page 248 of 878
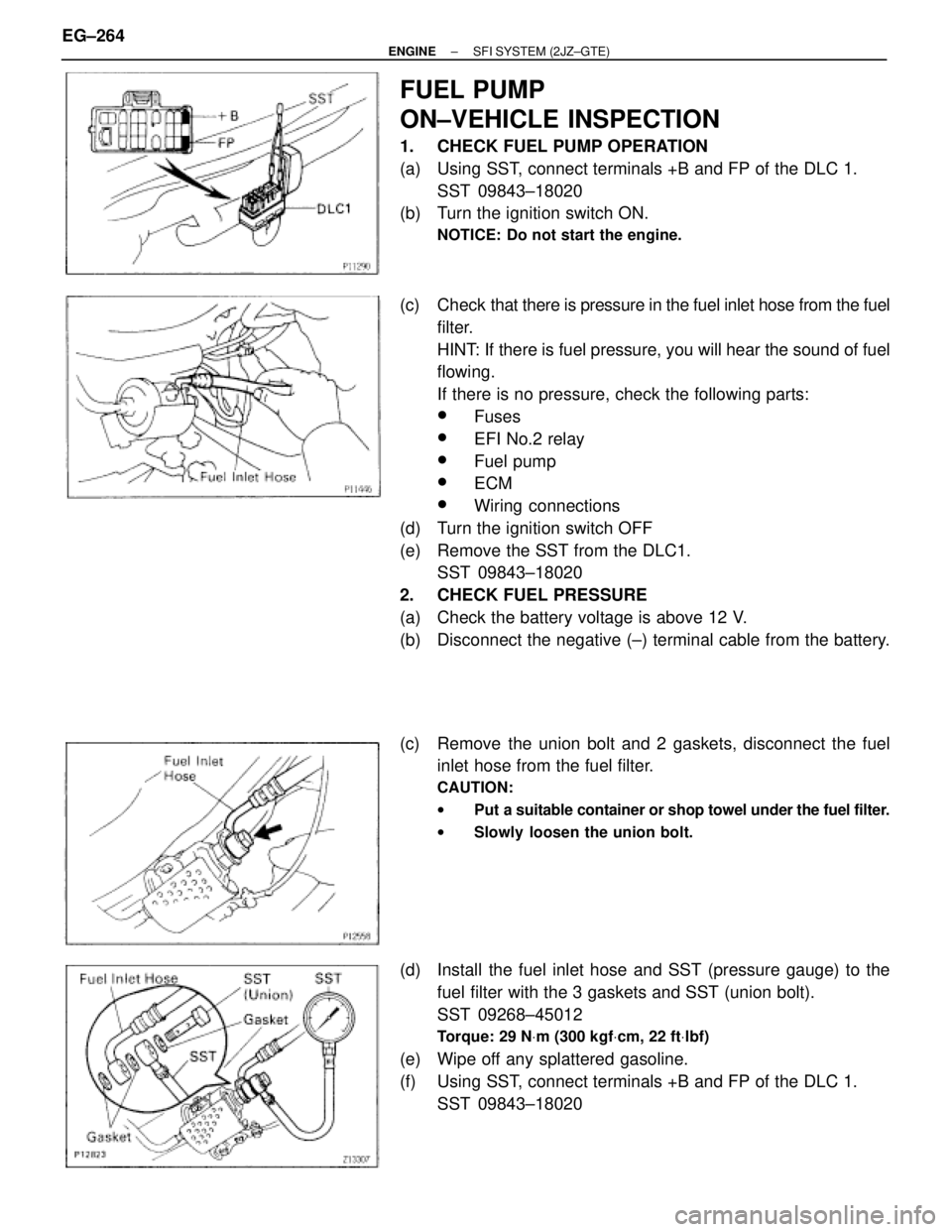
FUEL PUMP
ON±VEHICLE INSPECTION
1. CHECK FUEL PUMP OPERATION
(a) Using SST, connect terminals +B and FP of the DLC 1.
SST 09843±18020
(b) Turn the ignition switch ON.
NOTICE: Do not start the engine.
(c) Check that there is pressure in the fuel inlet hose from the fuel
filter.
HINT: If there is fuel pressure, you will hear the sound of fuel
flowing.
If there is no pressure, check the following parts:
wFuses
wEFI No.2 relay
wFuel pump
wECM
wWiring connections
(d) Turn the ignition switch OFF
(e) Remove the SST from the DLC1.
SST 09843±18020
2. CHECK FUEL PRESSURE
(a) Check the battery voltage is above 12 V.
(b) Disconnect the negative (±) terminal cable from the battery.
(c) Remove the union bolt and 2 gaskets, disconnect the fuel
inlet hose from the fuel filter.
CAUTION:
wPut a suitable container or shop towel under the fuel filter.
wSlowly loosen the union bolt.
(d) Install the fuel inlet hose and SST (pressure gauge) to the
fuel filter with the 3 gaskets and SST (union bolt).
SST 09268±45012
Torque: 29 NVm (300 kgfVcm, 22 ftVlbf)
(e) Wipe off any splattered gasoline.
(f) Using SST, connect terminals +B and FP of the DLC 1.
SST 09843±18020 EG±264
± ENGINESFI SYSTEM (2JZ±GTE)
Page 249 of 878
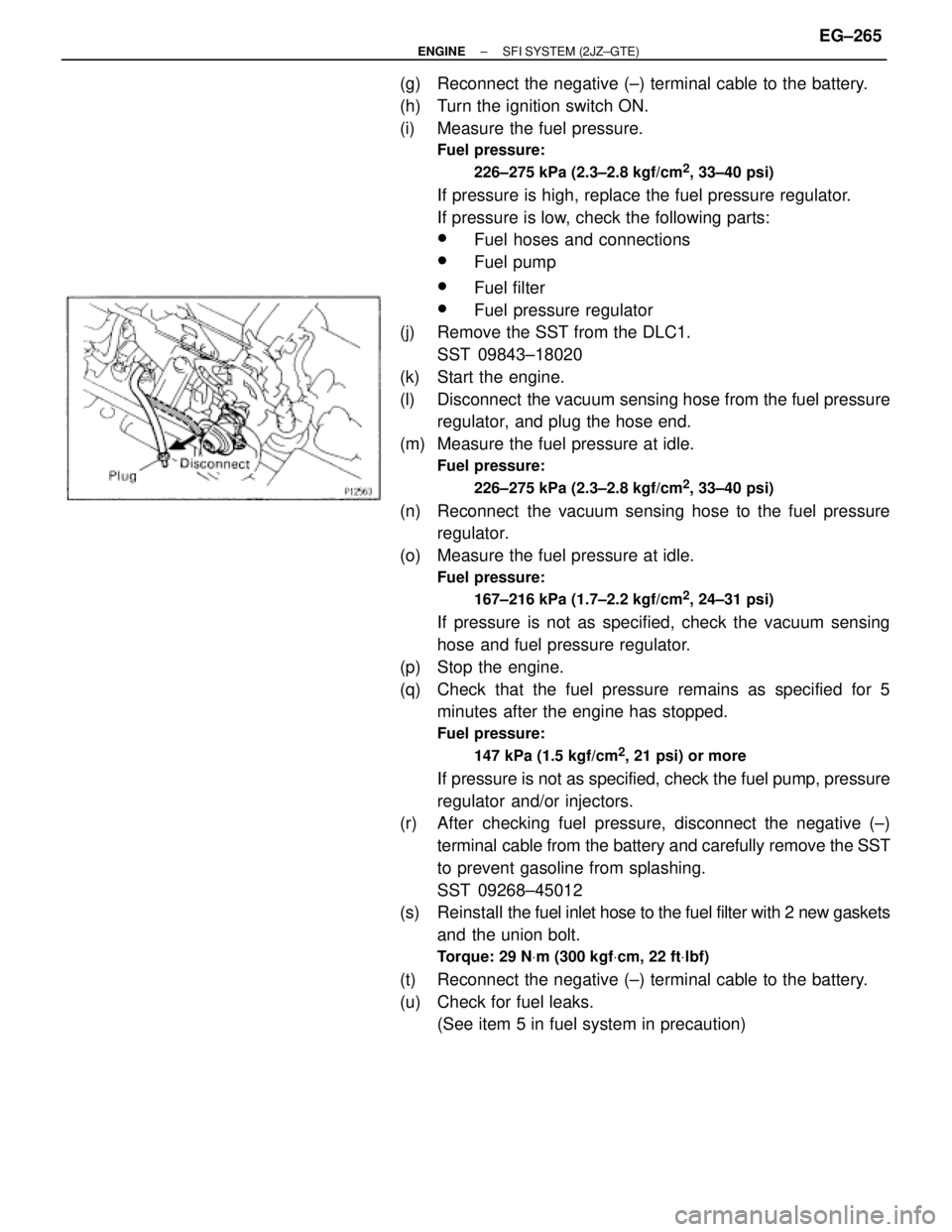
(g) Reconnect the negative (±) terminal cable to the battery.
(h) Turn the ignition switch ON.
(i) Measure the fuel pressure.
Fuel pressure:
226±275 kPa (2.3±2.8 kgf/cm
2, 33±40 psi)
If pressure is high, replace the fuel pressure regulator.
If pressure is low, check the following parts:
wFuel hoses and connections
wFuel pump
wFuel filter
wFuel pressure regulator
(j) Remove the SST from the DLC1.
SST 09843±18020
(k) Start the engine.
(l) Disconnect the vacuum sensing hose from the fuel pressure
regulator, and plug the hose end.
(m) Measure the fuel pressure at idle.
Fuel pressure:
226±275 kPa (2.3±2.8 kgf/cm
2, 33±40 psi)
(n) Reconnect the vacuum sensing hose to the fuel pressure
regulator.
(o) Measure the fuel pressure at idle.
Fuel pressure:
167±216 kPa (1.7±2.2 kgf/cm
2, 24±31 psi)
If pressure is not as specified, check the vacuum sensing
hose and fuel pressure regulator.
(p) Stop the engine.
(q) Check that the fuel pressure remains as specified for 5
minutes after the engine has stopped.
Fuel pressure:
147 kPa (1.5 kgf/cm
2, 21 psi) or more
If pressure is not as specified, check the fuel pump, pressure
regulator and/or injectors.
(r) After checking fuel pressure, disconnect the negative (±)
terminal cable from the battery and carefully remove the SST
to prevent gasoline from splashing.
SST 09268±45012
(s) Reinstall the fuel inlet hose to the fuel filter with 2 new gaskets
and the union bolt.
Torque: 29 NVm (300 kgfVcm, 22 ftVlbf)
(t) Reconnect the negative (±) terminal cable to the battery.
(u) Check for fuel leaks.
(See item 5 in fuel system in precaution)
± ENGINESFI SYSTEM (2JZ±GTE)EG±265
Page 250 of 878
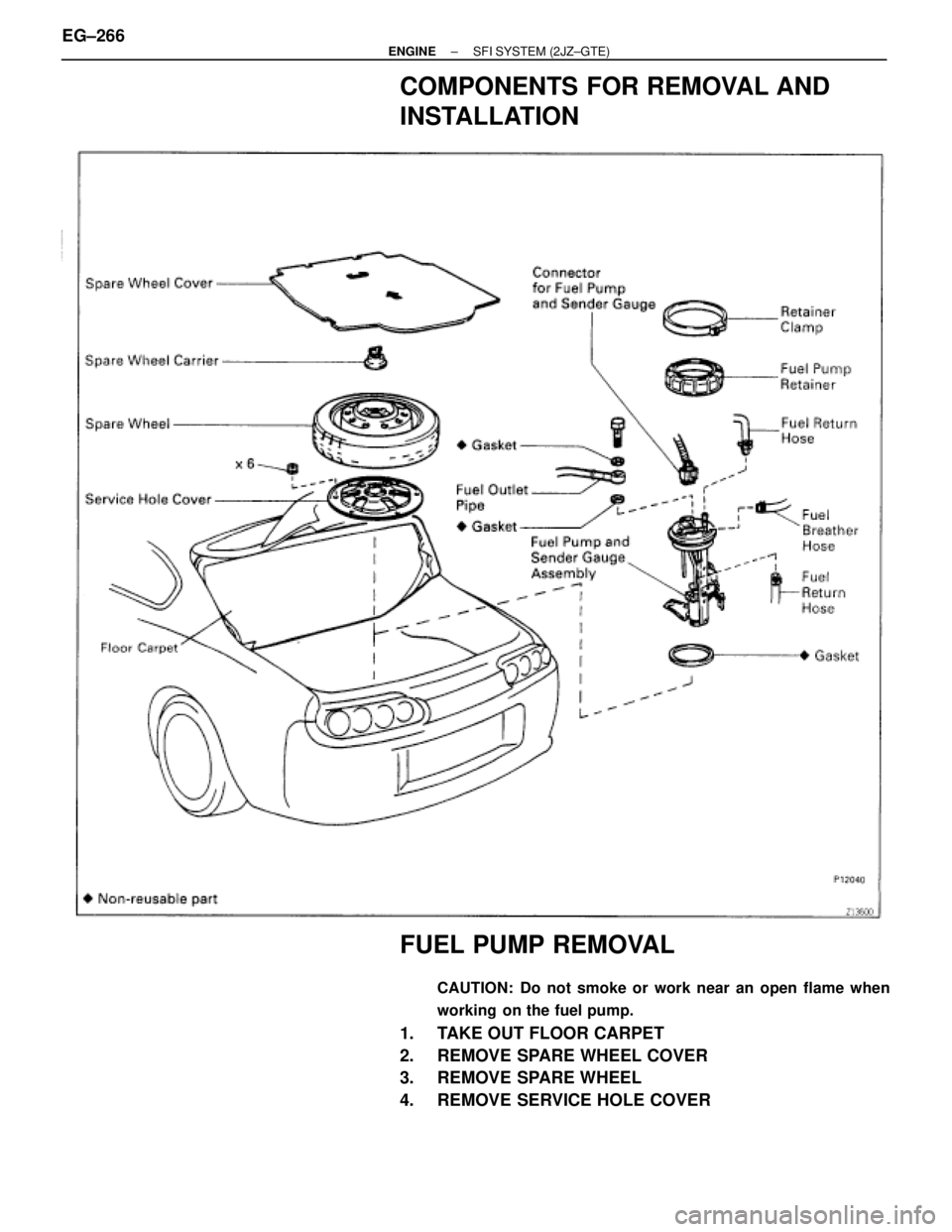
COMPONENTS FOR REMOVAL AND
INSTALLATION
FUEL PUMP REMOVAL
CAUTION: Do not smoke or work near an open flame when
working on the fuel pump.
1. TAKE OUT FLOOR CARPET
2. REMOVE SPARE WHEEL COVER
3. REMOVE SPARE WHEEL
4. REMOVE SERVICE HOLE COVER EG±266
± ENGINESFI SYSTEM (2JZ±GTE)