YAMAHA WR 250F 2014 Betriebsanleitungen (in German)
Manufacturer: YAMAHA, Model Year: 2014, Model line: WR 250F, Model: YAMAHA WR 250F 2014Pages: 236, PDF-Größe: 13.2 MB
Page 121 of 236
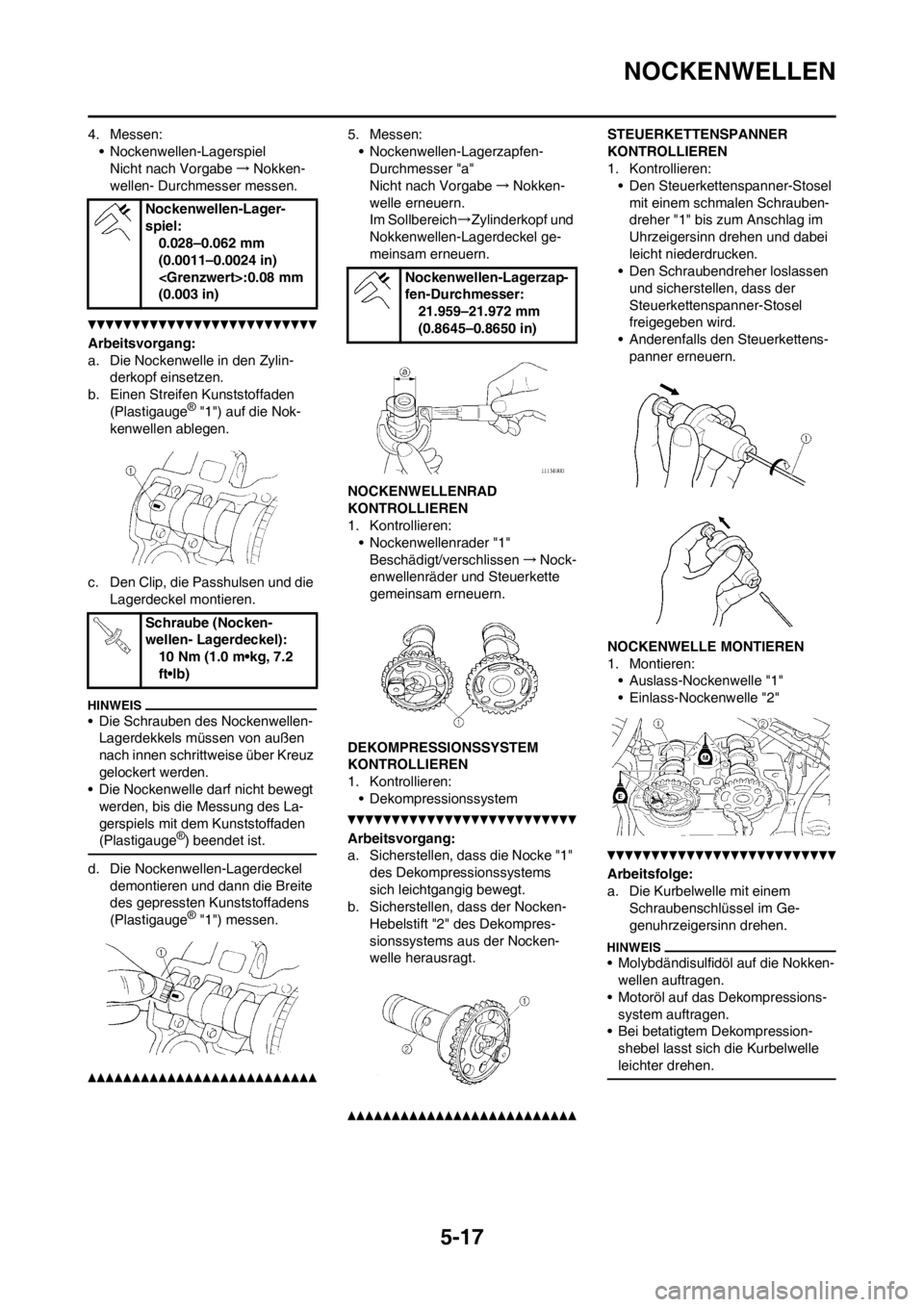
5-17
NOCKENWELLEN
4. Messen:
• Nockenwellen-Lagerspiel
Nicht nach Vorgabe→Nokken-
wellen- Durchmesser messen.
Arbeitsvorgang:
a. Die Nockenwelle in den Zylin-
derkopf einsetzen.
b. Einen Streifen Kunststoffaden
(Plastigauge
® "1") auf die Nok-
kenwellen ablegen.
c. Den Clip, die Passhulsen und die
Lagerdeckel montieren.
• Die Schrauben des Nockenwellen-
Lagerdekkels müssen von außen
nach innen schrittweise über Kreuz
gelockert werden.
• Die Nockenwelle darf nicht bewegt
werden, bis die Messung des La-
gerspiels mit dem Kunststoffaden
(Plastigauge
®) beendet ist.
d. Die Nockenwellen-Lagerdeckel
demontieren und dann die Breite
des gepressten Kunststoffadens
(Plastigauge
® "1") messen.
5. Messen:
• Nockenwellen-Lagerzapfen-
Durchmesser "a"
Nicht nach Vorgabe→Nokken-
welle erneuern.
Im Sollbereich→Zylinderkopf und
Nokkenwellen-Lagerdeckel ge-
meinsam erneuern.
NOCKENWELLENRAD
KONTROLLIEREN
1. Kontrollieren:
• Nockenwellenrader "1"
Beschädigt/verschlissen→Nock-
enwellenräder und Steuerkette
gemeinsam erneuern.
DEKOMPRESSIONSSYSTEM
KONTROLLIEREN
1. Kontrollieren:
• Dekompressionssystem
Arbeitsvorgang:
a. Sicherstellen, dass die Nocke "1"
des Dekompressionssystems
sich leichtgangig bewegt.
b. Sicherstellen, dass der Nocken-
Hebelstift "2" des Dekompres-
sionssystems aus der Nocken-
welle herausragt.
STEUERKETTENSPANNER
KONTROLLIEREN
1. Kontrollieren:
• Den Steuerkettenspanner-Stosel
mit einem schmalen Schrauben-
dreher "1" bis zum Anschlag im
Uhrzeigersinn drehen und dabei
leicht niederdrucken.
• Den Schraubendreher loslassen
und sicherstellen, dass der
Steuerkettenspanner-Stosel
freigegeben wird.
• Anderenfalls den Steuerkettens-
panner erneuern.
NOCKENWELLE MONTIEREN
1. Montieren:
• Auslass-Nockenwelle "1"
• Einlass-Nockenwelle "2"
Arbeitsfolge:
a. Die Kurbelwelle mit einem
Schraubenschlüssel im Ge-
genuhrzeigersinn drehen.
• Molybdändisulfidöl auf die Nokken-
wellen auftragen.
• Motoröl auf das Dekompressions-
system auftragen.
• Bei betatigtem Dekompression-
shebel lasst sich die Kurbelwelle
leichter drehen.
Nockenwellen-Lager-
spiel:
0.028–0.062 mm
(0.0011–0.0024 in)
(0.003 in)
Schraube (Nocken-
wellen- Lagerdeckel):
10 Nm (1.0 m•kg, 7.2
ft•lb)
Nockenwellen-Lagerzap-
fen-Durchmesser:
21.959–21.972 mm
(0.8645–0.8650 in)
Page 122 of 236
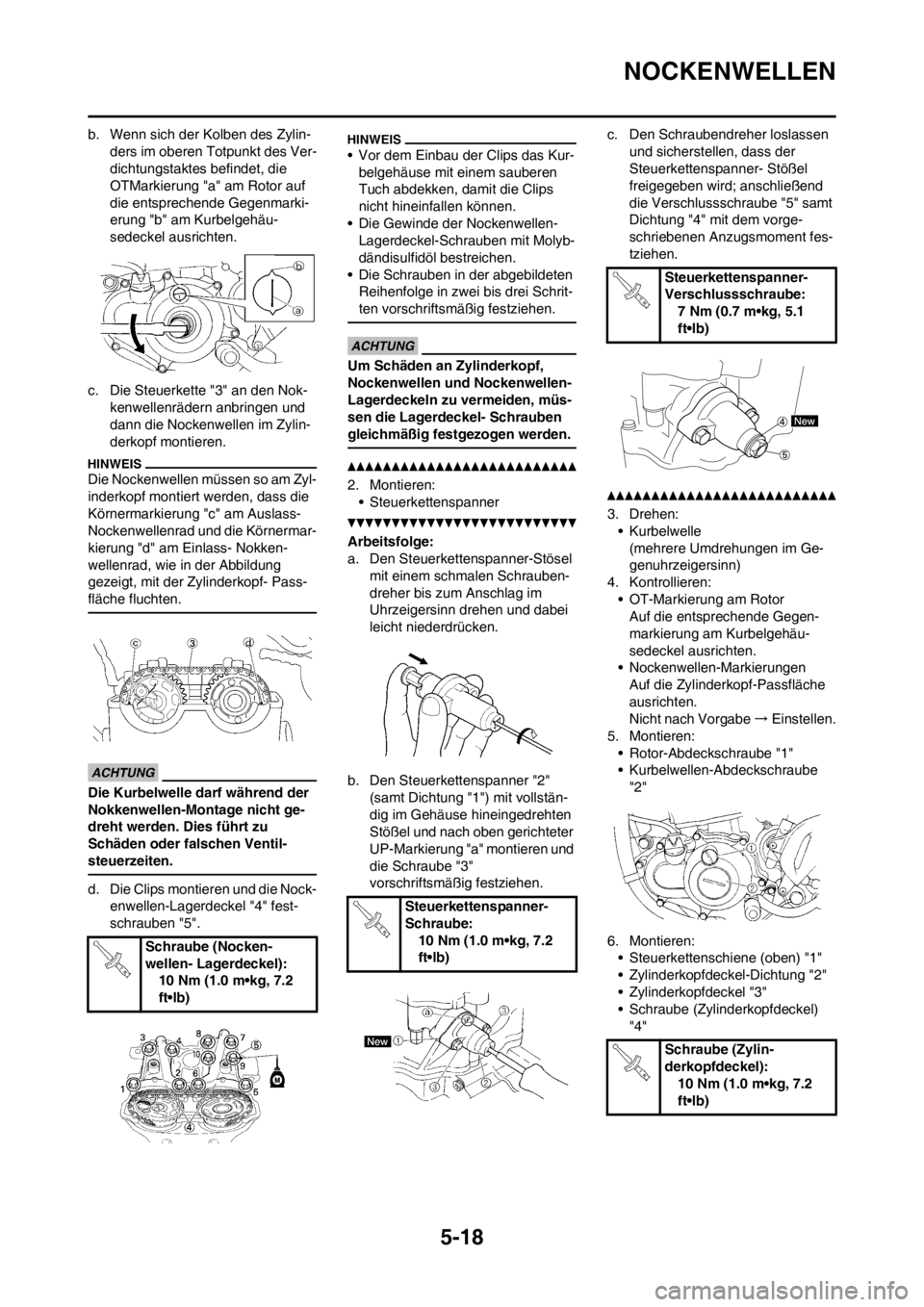
5-18
NOCKENWELLEN
b. Wenn sich der Kolben des Zylin-
ders im oberen Totpunkt des Ver-
dichtungstaktes befindet, die
OTMarkierung "a" am Rotor auf
die entsprechende Gegenmarki-
erung "b" am Kurbelgehäu-
sedeckel ausrichten.
c. Die Steuerkette "3" an den Nok-
kenwellenrädern anbringen und
dann die Nockenwellen im Zylin-
derkopf montieren.
Die Nockenwellen müssen so am Zyl-
inderkopf montiert werden, dass die
Körnermarkierung "c" am Auslass-
Nockenwellenrad und die Körnermar-
kierung "d" am Einlass- Nokken-
wellenrad, wie in der Abbildung
gezeigt, mit der Zylinderkopf- Pass-
fläche fluchten.
Die Kurbelwelle darf während der
Nokkenwellen-Montage nicht ge-
dreht werden. Dies führt zu
Schäden oder falschen Ventil-
steuerzeiten.
d. Die Clips montieren und die Nock-
enwellen-Lagerdeckel "4" fest-
schrauben "5".
• Vor dem Einbau der Clips das Kur-
belgehäuse mit einem sauberen
Tuch abdekken, damit die Clips
nicht hineinfallen können.
• Die Gewinde der Nockenwellen-
Lagerdeckel-Schrauben mit Molyb-
dändisulfidöl bestreichen.
• Die Schrauben in der abgebildeten
Reihenfolge in zwei bis drei Schrit-
ten vorschriftsmäßig festziehen.
Um Schäden an Zylinderkopf,
Nockenwellen und Nockenwellen-
Lagerdeckeln zu vermeiden, müs-
sen die Lagerdeckel- Schrauben
gleichmäßig festgezogen werden.
2. Montieren:
• Steuerkettenspanner
Arbeitsfolge:
a. Den Steuerkettenspanner-Stösel
mit einem schmalen Schrauben-
dreher bis zum Anschlag im
Uhrzeigersinn drehen und dabei
leicht niederdrücken.
b. Den Steuerkettenspanner "2"
(samt Dichtung "1") mit vollstän-
dig im Gehäuse hineingedrehten
Stößel und nach oben gerichteter
UP-Markierung "a" montieren und
die Schraube "3"
vorschriftsmäßig festziehen.c. Den Schraubendreher loslassen
und sicherstellen, dass der
Steuerkettenspanner- Stößel
freigegeben wird; anschließend
die Verschlussschraube "5" samt
Dichtung "4" mit dem vorge-
schriebenen Anzugsmoment fes-
tziehen.
3. Drehen:
• Kurbelwelle
(mehrere Umdrehungen im Ge-
genuhrzeigersinn)
4. Kontrollieren:
• OT-Markierung am Rotor
Auf die entsprechende Gegen-
markierung am Kurbelgehäu-
sedeckel ausrichten.
• Nockenwellen-Markierungen
Auf die Zylinderkopf-Passfläche
ausrichten.
Nicht nach Vorgabe→Einstellen.
5. Montieren:
• Rotor-Abdeckschraube "1"
• Kurbelwellen-Abdeckschraube
"2"
6. Montieren:
• Steuerkettenschiene (oben) "1"
• Zylinderkopfdeckel-Dichtung "2"
• Zylinderkopfdeckel "3"
• Schraube (Zylinderkopfdeckel)
"4" Schraube (Nocken-
wellen- Lagerdeckel):
10 Nm (1.0 m•kg, 7.2
ft•lb)
Steuerkettenspanner-
Schraube:
10 Nm (1.0 m•kg, 7.2
ft•lb)
Steuerkettenspanner-
Verschlussschraube:
7 Nm (0.7 m•kg, 5.1
ft•lb)
Schraube (Zylin-
derkopfdeckel):
10 Nm (1.0 m•kg, 7.2
ft•lb)
Page 123 of 236
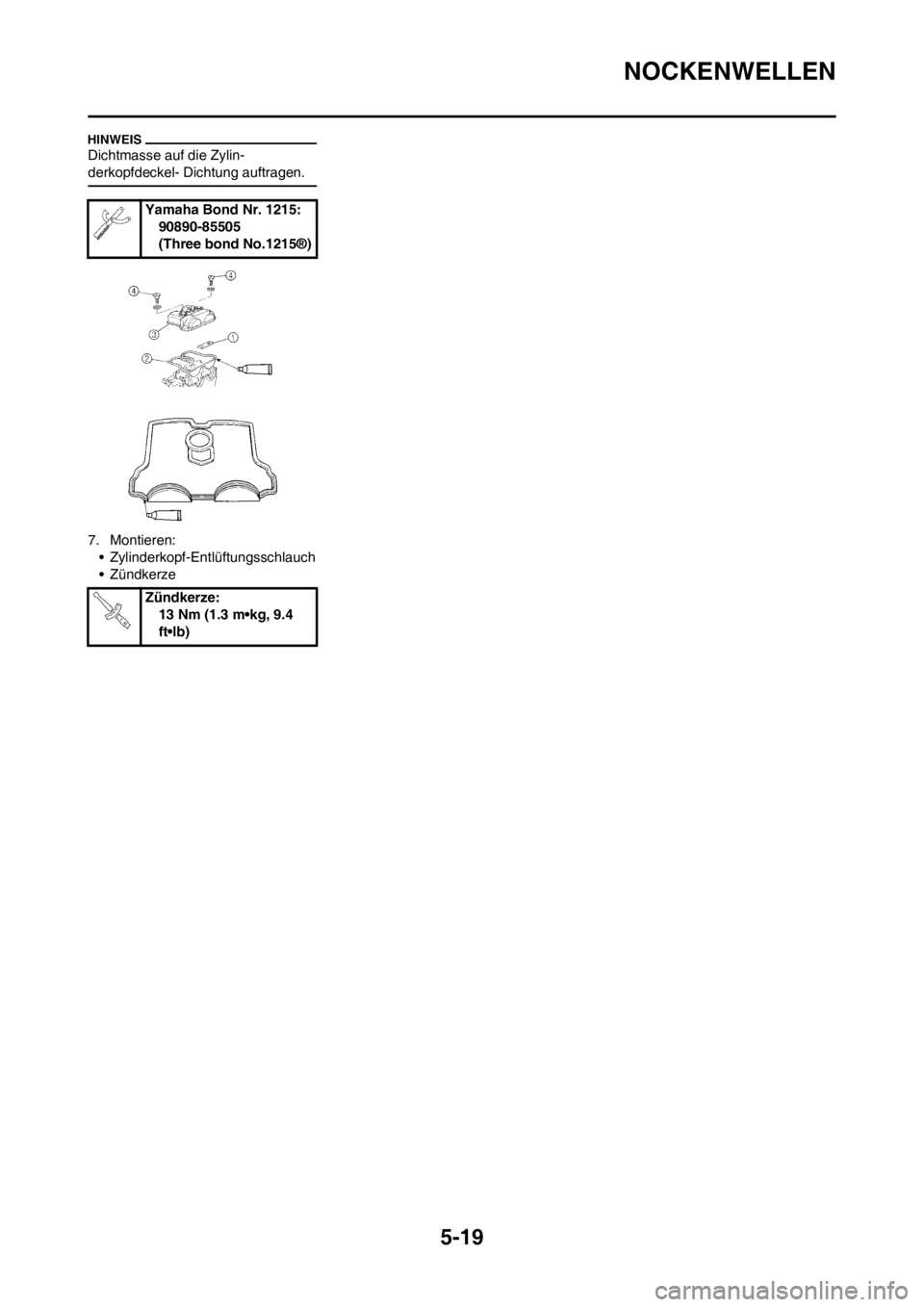
5-19
NOCKENWELLEN
Dichtmasse auf die Zylin-
derkopfdeckel- Dichtung auftragen.
7. Montieren:
• Zylinderkopf-Entlüftungsschlauch
• ZündkerzeYamaha Bond Nr. 1215:
90890-85505
(Three bond No.1215®)
Zündkerze:
13 Nm (1.3 m•kg, 9.4
ft•lb)
Page 124 of 236
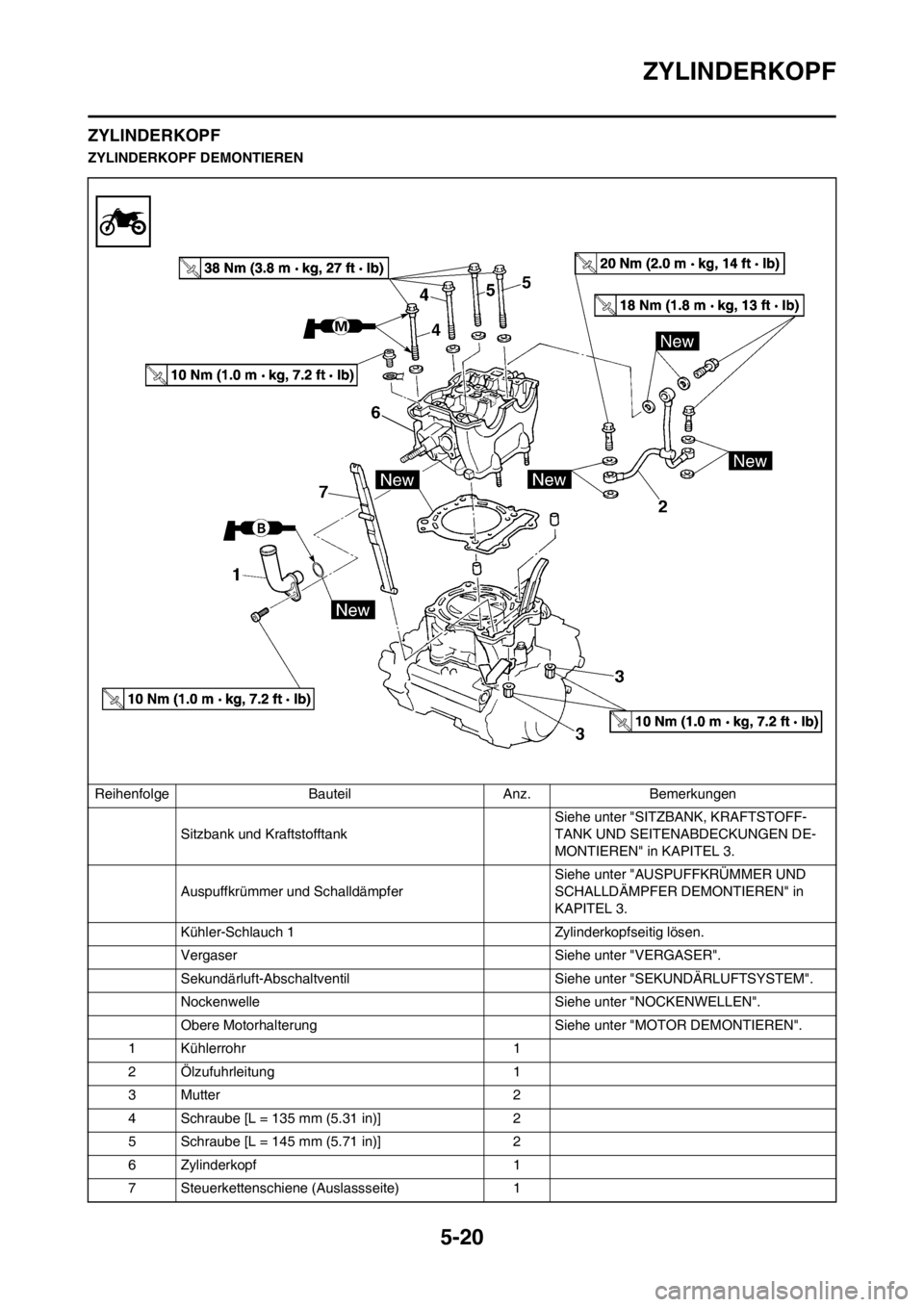
5-20
ZYLINDERKOPF
ZYLINDERKOPF
ZYLINDERKOPF DEMONTIEREN
Reihenfolge Bauteil Anz. Bemerkungen
Sitzbank und Kraftstofftank Siehe unter "SITZBANK, KRAFTSTOFF-
TANK UND SEITENABDECKUNGEN DE-
MONTIEREN" in KAPITEL 3.
Auspuffkrümmer und SchalldämpferSiehe unter "AUSPUFFKRÜMMER UND
SCHALLDÄMPFER DEMONTIEREN" in
KAPITEL 3.
Kühler-Schlauch 1 Zylinderkopfseitig lösen.
Vergaser Siehe unter "VERGASER".
Sekundärluft-Abschaltventil Siehe unter "SEKUNDÄRLUFTSYSTEM".
Nockenwelle Siehe unter "NOCKENWELLEN".
Obere Motorhalterung Siehe unter "MOTOR DEMONTIEREN".
1 Kühlerrohr 1
2 Ölzufuhrleitung 1
3Mutter 2
4 Schraube [L = 135 mm (5.31 in)] 2
5 Schraube [L = 145 mm (5.71 in)] 2
6 Zylinderkopf 1
7 Steuerkettenschiene (Auslassseite) 1
Page 125 of 236
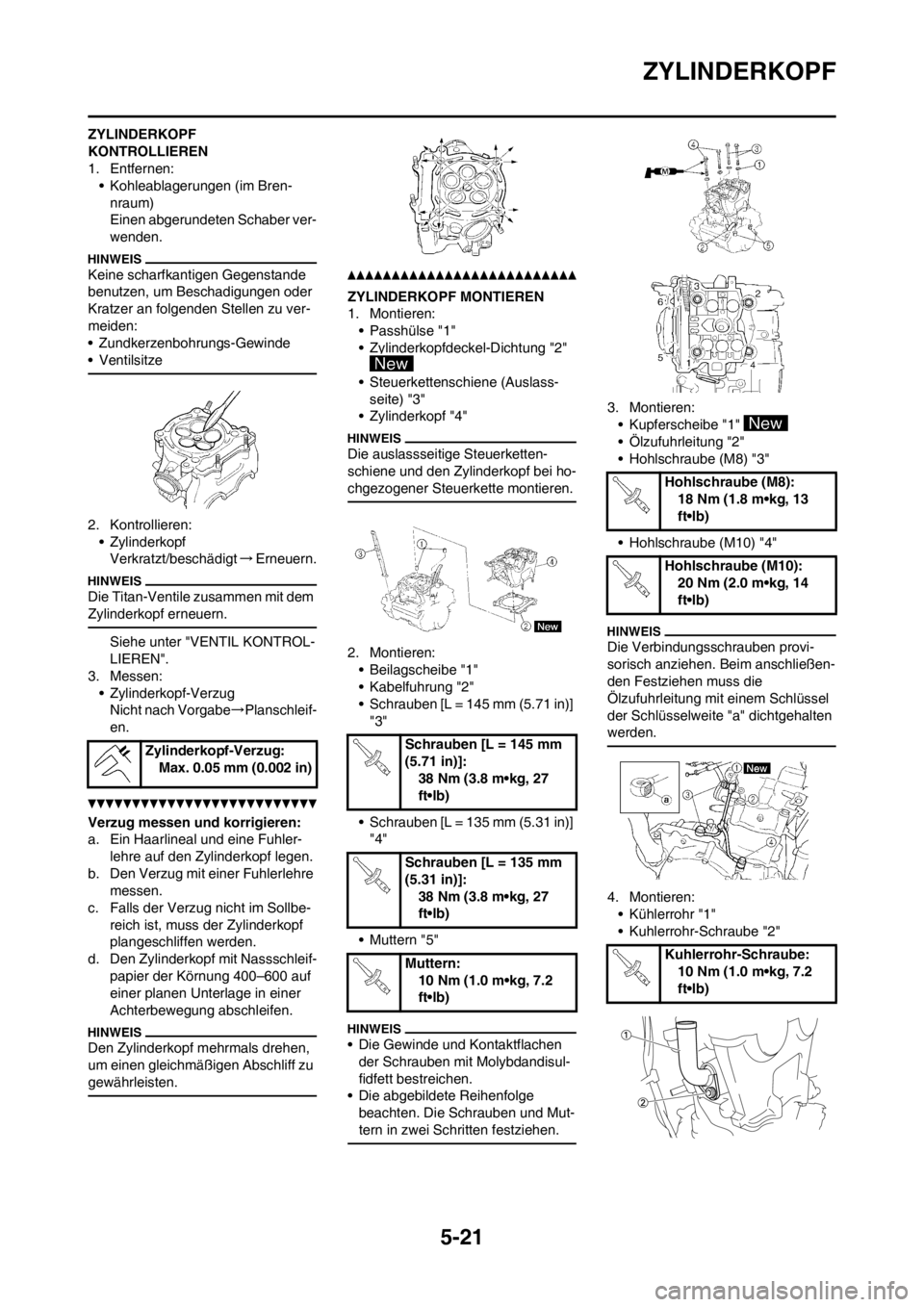
5-21
ZYLINDERKOPF
ZYLINDERKOPF
KONTROLLIEREN
1. Entfernen:
• Kohleablagerungen (im Bren-
nraum)
Einen abgerundeten Schaber ver-
wenden.
Keine scharfkantigen Gegenstande
benutzen, um Beschadigungen oder
Kratzer an folgenden Stellen zu ver-
meiden:
• Zundkerzenbohrungs-Gewinde
• Ventilsitze
2. Kontrollieren:
• Zylinderkopf
Verkratzt/beschädigt→Erneuern.
Die Titan-Ventile zusammen mit dem
Zylinderkopf erneuern.
Siehe unter "VENTIL KONTROL-
LIEREN".
3. Messen:
• Zylinderkopf-Verzug
Nicht nach Vorgabe→Planschleif-
en.
Verzug messen und korrigieren:
a. Ein Haarlineal und eine Fuhler-
lehre auf den Zylinderkopf legen.
b. Den Verzug mit einer Fuhlerlehre
messen.
c. Falls der Verzug nicht im Sollbe-
reich ist, muss der Zylinderkopf
plangeschliffen werden.
d. Den Zylinderkopf mit Nassschleif-
papier der Körnung 400–600 auf
einer planen Unterlage in einer
Achterbewegung abschleifen.
Den Zylinderkopf mehrmals drehen,
um einen gleichmäßigen Abschliff zu
gewährleisten.
ZYLINDERKOPF MONTIEREN
1. Montieren:
• Passhülse "1"
• Zylinderkopfdeckel-Dichtung "2"
• Steuerkettenschiene (Auslass-
seite) "3"
• Zylinderkopf "4"
Die auslassseitige Steuerketten-
schiene und den Zylinderkopf bei ho-
chgezogener Steuerkette montieren.
2. Montieren:
• Beilagscheibe "1"
• Kabelfuhrung "2"
• Schrauben [L = 145 mm (5.71 in)]
"3"
• Schrauben [L = 135 mm (5.31 in)]
"4"
• Muttern "5"
• Die Gewinde und Kontaktflachen
der Schrauben mit Molybdandisul-
fidfett bestreichen.
• Die abgebildete Reihenfolge
beachten. Die Schrauben und Mut-
tern in zwei Schritten festziehen.
3. Montieren:
• Kupferscheibe "1"
• Ölzufuhrleitung "2"
• Hohlschraube (M8) "3"
• Hohlschraube (M10) "4"
Die Verbindungsschrauben provi-
sorisch anziehen. Beim anschließen-
den Festziehen muss die
Ölzufuhrleitung mit einem Schlüssel
der Schlüsselweite "a" dichtgehalten
werden.
4. Montieren:
• Kühlerrohr "1"
• Kuhlerrohr-Schraube "2" Zylinderkopf-Verzug:
Max. 0.05 mm (0.002 in)
Schrauben [L = 145 mm
(5.71 in)]:
38 Nm (3.8 m•kg, 27
ft•lb)
Schrauben [L = 135 mm
(5.31 in)]:
38 Nm (3.8 m•kg, 27
ft•lb)
Muttern:
10 Nm (1.0 m•kg, 7.2
ft•lb)
Hohlschraube (M8):
18 Nm (1.8 m•kg, 13
ft•lb)
Hohlschraube (M10):
20 Nm (2.0 m•kg, 14
ft•lb)
Kuhlerrohr-Schraube:
10 Nm (1.0 m•kg, 7.2
ft•lb)
Page 126 of 236
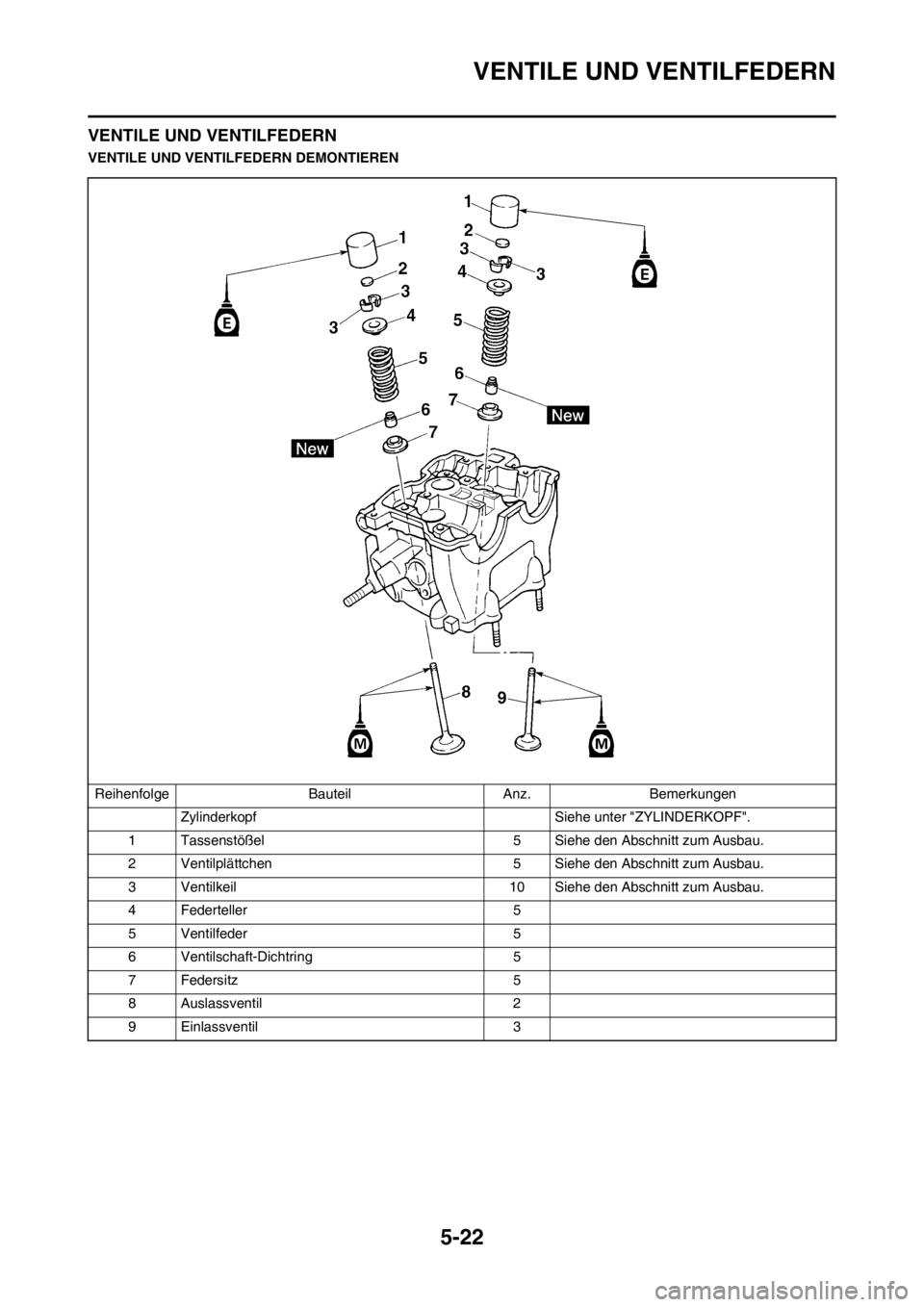
5-22
VENTILE UND VENTILFEDERN
VENTILE UND VENTILFEDERN
VENTILE UND VENTILFEDERN DEMONTIEREN
Reihenfolge Bauteil Anz. Bemerkungen
Zylinderkopf Siehe unter "ZYLINDERKOPF".
1 Tassenstößel 5 Siehe den Abschnitt zum Ausbau.
2 Ventilplättchen 5 Siehe den Abschnitt zum Ausbau.
3 Ventilkeil 10 Siehe den Abschnitt zum Ausbau.
4 Federteller 5
5 Ventilfeder 5
6 Ventilschaft-Dichtring 5
7 Federsitz 5
8 Auslassventil 2
9 Einlassventil 3
Page 127 of 236
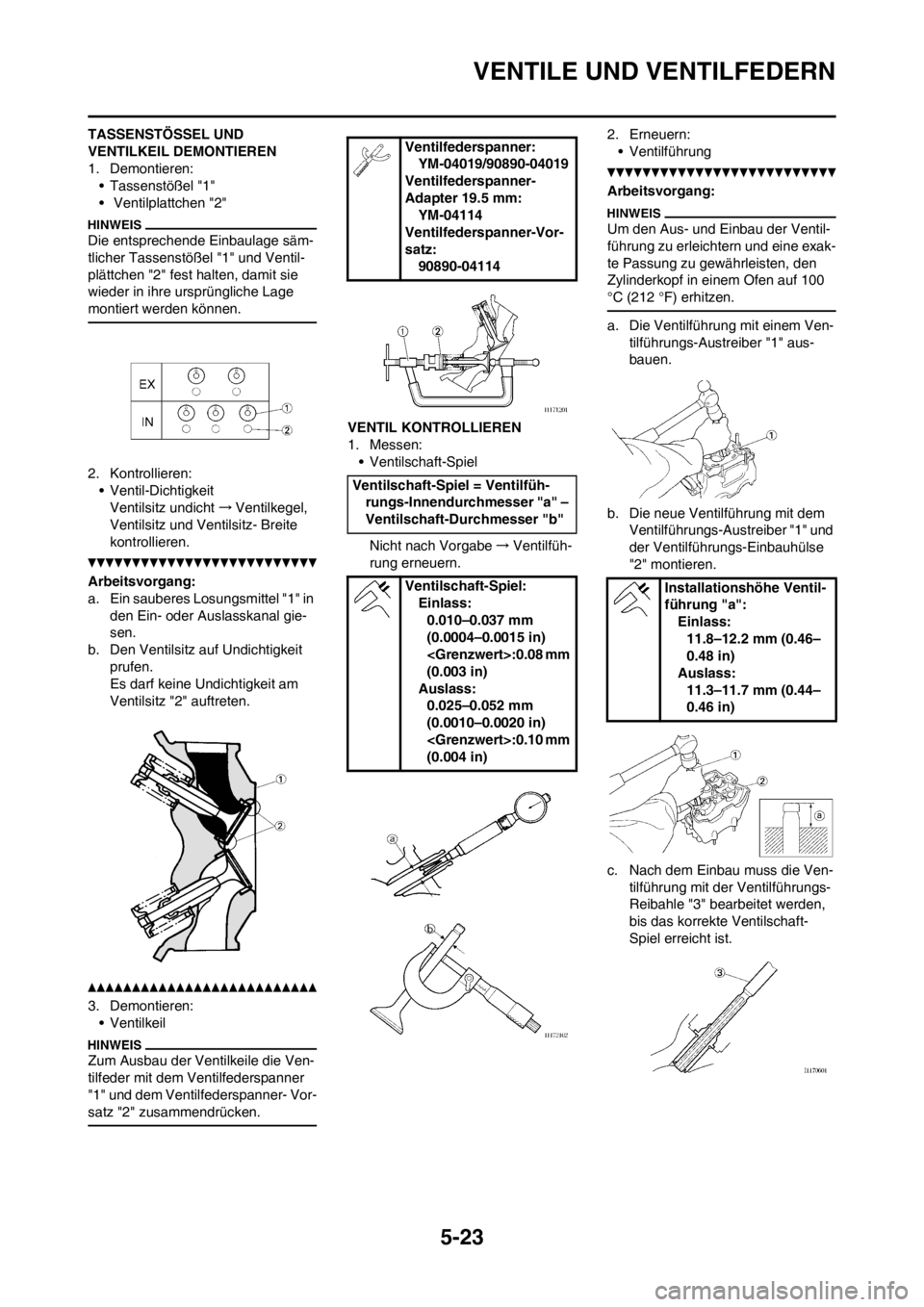
5-23
VENTILE UND VENTILFEDERN
TASSENSTÖSSEL UND
VENTILKEIL DEMONTIEREN
1. Demontieren:
• Tassenstößel "1"
• Ventilplattchen "2"
Die entsprechende Einbaulage säm-
tlicher Tassenstößel "1" und Ventil-
plättchen "2" fest halten, damit sie
wieder in ihre ursprüngliche Lage
montiert werden können.
2. Kontrollieren:
• Ventil-Dichtigkeit
Ventilsitz undicht→Ventilkegel,
Ventilsitz und Ventilsitz- Breite
kontrollieren.
Arbeitsvorgang:
a. Ein sauberes Losungsmittel "1" in
den Ein- oder Auslasskanal gie-
sen.
b. Den Ventilsitz auf Undichtigkeit
prufen.
Es darf keine Undichtigkeit am
Ventilsitz "2" auftreten.
3. Demontieren:
• Ventilkeil
Zum Ausbau der Ventilkeile die Ven-
tilfeder mit dem Ventilfederspanner
"1" und dem Ventilfederspanner- Vor-
satz "2" zusammendrücken.
VENTIL KONTROLLIEREN
1. Messen:
• Ventilschaft-Spiel
Nicht nach Vorgabe→Ventilfüh-
rung erneuern.2. Erneuern:
• Ventilführung
Arbeitsvorgang:
Um den Aus- und Einbau der Ventil-
führung zu erleichtern und eine exak-
te Passung zu gewährleisten, den
Zylinderkopf in einem Ofen auf 100
°C (212 °F) erhitzen.
a. Die Ventilführung mit einem Ven-
tilführungs-Austreiber "1" aus-
bauen.
b. Die neue Ventilführung mit dem
Ventilführungs-Austreiber "1" und
der Ventilführungs-Einbauhülse
"2" montieren.
c. Nach dem Einbau muss die Ven-
tilführung mit der Ventilführungs-
Reibahle "3" bearbeitet werden,
bis das korrekte Ventilschaft-
Spiel erreicht ist.
Ventilfederspanner:
YM-04019/90890-04019
Ventilfederspanner-
Adapter 19.5 mm:
YM-04114
Ventilfederspanner-Vor-
satz:
90890-04114
Ventilschaft-Spiel = Ventilfüh-
rungs-Innendurchmesser "a" –
Ventilschaft-Durchmesser "b"
Ventilschaft-Spiel:
Einlass:
0.010–0.037 mm
(0.0004–0.0015 in)
(0.003 in)
Auslass:
0.025–0.052 mm
(0.0010–0.0020 in)
(0.004 in)
Installationshöhe Ventil-
führung "a":
Einlass:
11.8–12.2 mm (0.46–
0.48 in)
Auslass:
11.3–11.7 mm (0.44–
0.46 in)
Page 128 of 236
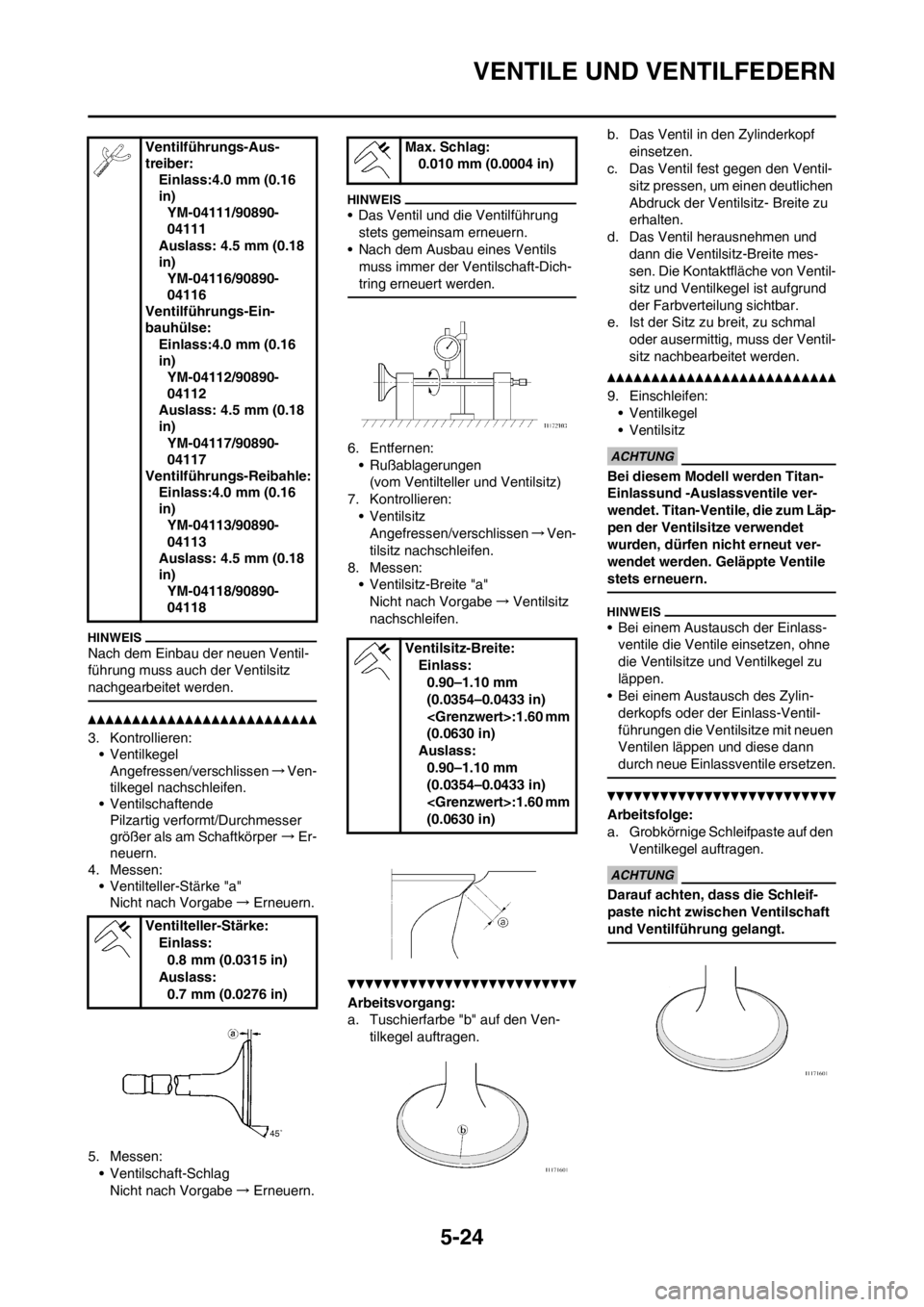
5-24
VENTILE UND VENTILFEDERN
Nach dem Einbau der neuen Ventil-
führung muss auch der Ventilsitz
nachgearbeitet werden.
3. Kontrollieren:
• Ventilkegel
Angefressen/verschlissen→Ven-
tilkegel nachschleifen.
• Ventilschaftende
Pilzartig verformt/Durchmesser
größer als am Schaftkörper→Er-
neuern.
4. Messen:
• Ventilteller-Stärke "a"
Nicht nach Vorgabe→Erneuern.
5. Messen:
• Ventilschaft-Schlag
Nicht nach Vorgabe→Erneuern.
• Das Ventil und die Ventilführung
stets gemeinsam erneuern.
• Nach dem Ausbau eines Ventils
muss immer der Ventilschaft-Dich-
tring erneuert werden.
6. Entfernen:
• Rußablagerungen
(vom Ventilteller und Ventilsitz)
7. Kontrollieren:
• Ventilsitz
Angefressen/verschlissen→Ven-
tilsitz nachschleifen.
8. Messen:
• Ventilsitz-Breite "a"
Nicht nach Vorgabe→Ventilsitz
nachschleifen.
Arbeitsvorgang:
a. Tuschierfarbe "b" auf den Ven-
tilkegel auftragen.b. Das Ventil in den Zylinderkopf
einsetzen.
c. Das Ventil fest gegen den Ventil-
sitz pressen, um einen deutlichen
Abdruck der Ventilsitz- Breite zu
erhalten.
d. Das Ventil herausnehmen und
dann die Ventilsitz-Breite mes-
sen. Die Kontaktfläche von Ventil-
sitz und Ventilkegel ist aufgrund
der Farbverteilung sichtbar.
e. Ist der Sitz zu breit, zu schmal
oder ausermittig, muss der Ventil-
sitz nachbearbeitet werden.
9. Einschleifen:
• Ventilkegel
• Ventilsitz
Bei diesem Modell werden Titan-
Einlassund -Auslassventile ver-
wendet. Titan-Ventile, die zum Läp-
pen der Ventilsitze verwendet
wurden, dürfen nicht erneut ver-
wendet werden. Geläppte Ventile
stets erneuern.
• Bei einem Austausch der Einlass-
ventile die Ventile einsetzen, ohne
die Ventilsitze und Ventilkegel zu
läppen.
• Bei einem Austausch des Zylin-
derkopfs oder der Einlass-Ventil-
führungen die Ventilsitze mit neuen
Ventilen läppen und diese dann
durch neue Einlassventile ersetzen.
Arbeitsfolge:
a. Grobkörnige Schleifpaste auf den
Ventilkegel auftragen.
Darauf achten, dass die Schleif-
paste nicht zwischen Ventilschaft
und Ventilführung gelangt.
Ventilführungs-Aus-
treiber:
Einlass:4.0 mm (0.16
in)
YM-04111/90890-
04111
Auslass: 4.5 mm (0.18
in)
YM-04116/90890-
04116
Ventilführungs-Ein-
bauhülse:
Einlass:4.0 mm (0.16
in)
YM-04112/90890-
04112
Auslass: 4.5 mm (0.18
in)
YM-04117/90890-
04117
Ventilführungs-Reibahle:
Einlass:4.0 mm (0.16
in)
YM-04113/90890-
04113
Auslass: 4.5 mm (0.18
in)
YM-04118/90890-
04118
Ventilteller-Stärke:
Einlass:
0.8 mm (0.0315 in)
Auslass:
0.7 mm (0.0276 in)Max. Schlag:
0.010 mm (0.0004 in)
Ventilsitz-Breite:
Einlass:
0.90–1.10 mm
(0.0354–0.0433 in)
(0.0630 in)
Auslass:
0.90–1.10 mm
(0.0354–0.0433 in)
(0.0630 in)
Page 129 of 236
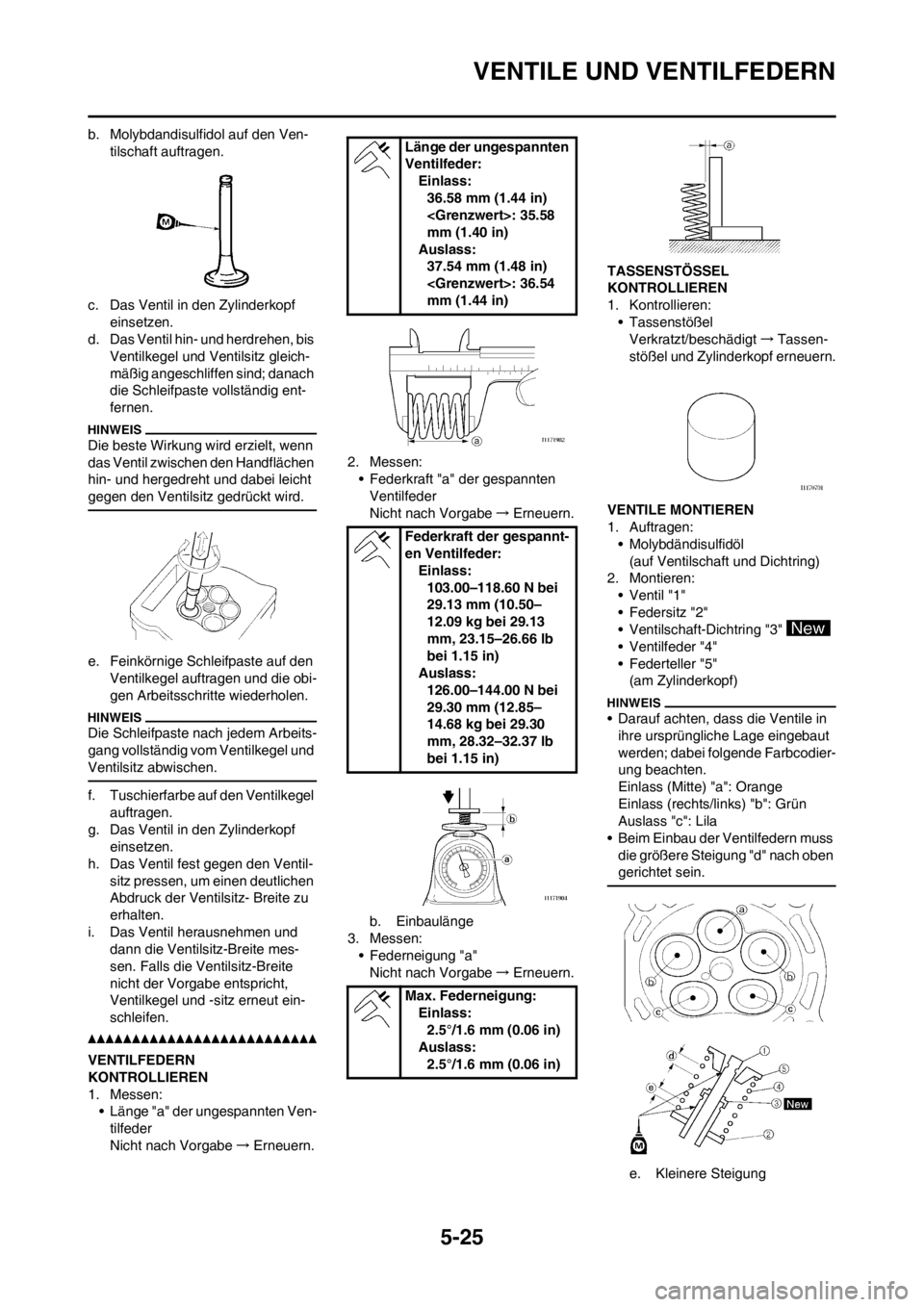
5-25
VENTILE UND VENTILFEDERN
b. Molybdandisulfidol auf den Ven-
tilschaft auftragen.
c. Das Ventil in den Zylinderkopf
einsetzen.
d. Das Ventil hin- und herdrehen, bis
Ventilkegel und Ventilsitz gleich-
mäßig angeschliffen sind; danach
die Schleifpaste vollständig ent-
fernen.
Die beste Wirkung wird erzielt, wenn
das Ventil zwischen den Handflächen
hin- und hergedreht und dabei leicht
gegen den Ventilsitz gedrückt wird.
e. Feinkörnige Schleifpaste auf den
Ventilkegel auftragen und die obi-
gen Arbeitsschritte wiederholen.
Die Schleifpaste nach jedem Arbeits-
gang vollständig vom Ventilkegel und
Ventilsitz abwischen.
f. Tuschierfarbe auf den Ventilkegel
auftragen.
g. Das Ventil in den Zylinderkopf
einsetzen.
h. Das Ventil fest gegen den Ventil-
sitz pressen, um einen deutlichen
Abdruck der Ventilsitz- Breite zu
erhalten.
i. Das Ventil herausnehmen und
dann die Ventilsitz-Breite mes-
sen. Falls die Ventilsitz-Breite
nicht der Vorgabe entspricht,
Ventilkegel und -sitz erneut ein-
schleifen.
VENTILFEDERN
KONTROLLIEREN
1. Messen:
• Länge "a" der ungespannten Ven-
tilfeder
Nicht nach Vorgabe→Erneuern.2. Messen:
• Federkraft "a" der gespannten
Ventilfeder
Nicht nach Vorgabe→Erneuern.
b. Einbaulänge
3. Messen:
• Federneigung "a"
Nicht nach Vorgabe→Erneuern.TASSENSTÖSSEL
KONTROLLIEREN
1. Kontrollieren:
• Tassenstößel
Verkratzt/beschädigt→Tassen-
stößel und Zylinderkopf erneuern.
VENTILE MONTIEREN
1. Auftragen:
• Molybdändisulfidöl
(auf Ventilschaft und Dichtring)
2. Montieren:
• Ventil "1"
• Federsitz "2"
• Ventilschaft-Dichtring "3"
• Ventilfeder "4"
• Federteller "5"
(am Zylinderkopf)
• Darauf achten, dass die Ventile in
ihre ursprüngliche Lage eingebaut
werden; dabei folgende Farbcodier-
ung beachten.
Einlass (Mitte) "a": Orange
Einlass (rechts/links) "b": Grün
Auslass "c": Lila
• Beim Einbau der Ventilfedern muss
die größere Steigung "d" nach oben
gerichtet sein.
e. Kleinere Steigung
Länge der ungespannten
Ventilfeder:
Einlass:
36.58 mm (1.44 in)
mm (1.40 in)
Auslass:
37.54 mm (1.48 in)
mm (1.44 in)
Federkraft der gespannt-
en Ventilfeder:
Einlass:
103.00–118.60 N bei
29.13 mm (10.50–
12.09 kg bei 29.13
mm, 23.15–26.66 lb
bei 1.15 in)
Auslass:
126.00–144.00 N bei
29.30 mm (12.85–
14.68 kg bei 29.30
mm, 28.32–32.37 lb
bei 1.15 in)
Max. Federneigung:
Einlass:
2.5°/1.6 mm (0.06 in)
Auslass:
2.5°/1.6 mm (0.06 in)
Page 130 of 236
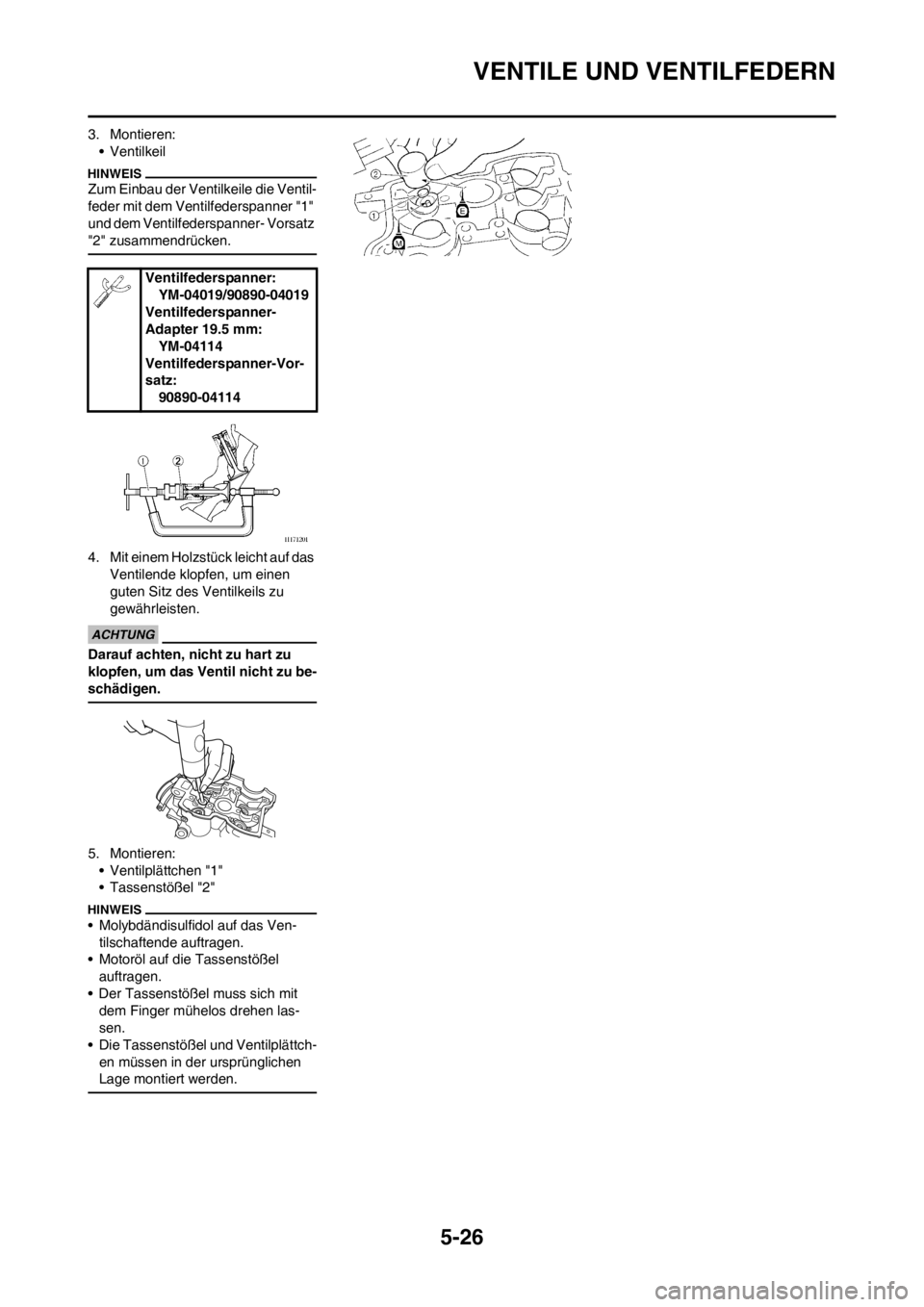
5-26
VENTILE UND VENTILFEDERN
3. Montieren:
• Ventilkeil
Zum Einbau der Ventilkeile die Ventil-
feder mit dem Ventilfederspanner "1"
und dem Ventilfederspanner- Vorsatz
"2" zusammendrücken.
4. Mit einem Holzstück leicht auf das
Ventilende klopfen, um einen
guten Sitz des Ventilkeils zu
gewährleisten.
Darauf achten, nicht zu hart zu
klopfen, um das Ventil nicht zu be-
schädigen.
5. Montieren:
• Ventilplättchen "1"
• Tassenstößel "2"
• Molybdändisulfidol auf das Ven-
tilschaftende auftragen.
• Motoröl auf die Tassenstößel
auftragen.
• Der Tassenstößel muss sich mit
dem Finger mühelos drehen las-
sen.
• Die Tassenstößel und Ventilplättch-
en müssen in der ursprünglichen
Lage montiert werden.
Ventilfederspanner:
YM-04019/90890-04019
Ventilfederspanner-
Adapter 19.5 mm:
YM-04114
Ventilfederspanner-Vor-
satz:
90890-04114