ECU ASTON MARTIN DB7 1997 Manual Online
[x] Cancel search | Manufacturer: ASTON MARTIN, Model Year: 1997, Model line: DB7, Model: ASTON MARTIN DB7 1997Pages: 421, PDF Size: 9.31 MB
Page 374 of 421
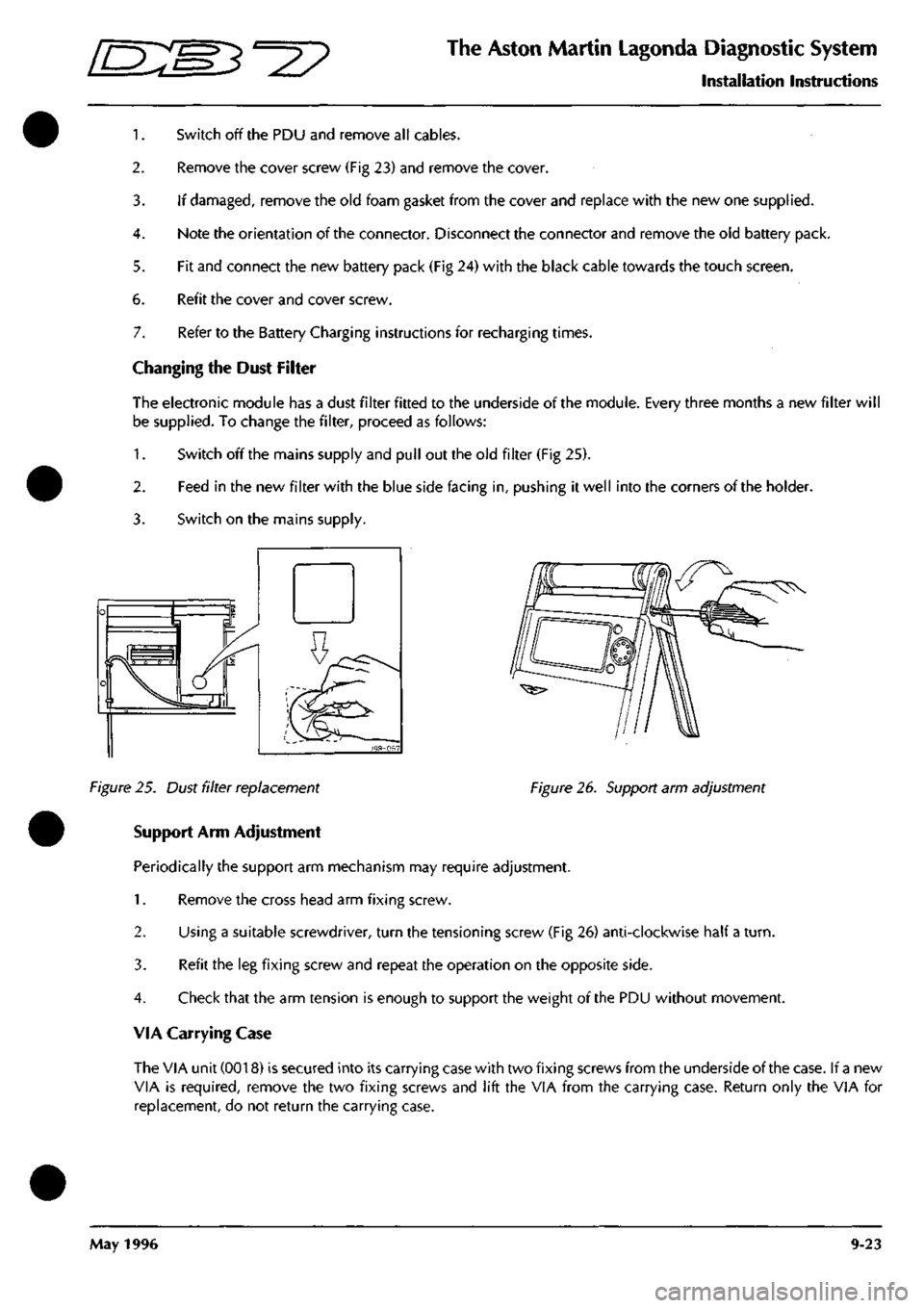
^?
The Aston Martin Lagonda Diagnostic System
Installation Instructions
1.
Switch off the PDU and remove all cables.
2.
Remove the cover screw (Fig 23) and remove the cover.
3. If damaged, remove the old foam gasket from the cover and replace with the new one supplied.
4.
Note the orientation of the connector. Disconnect the connector and remove the old battery pack.
5. Fit and connect the new battery pack (Fig 24) with the black cable towards the touch screen.
6. Refit the cover and cover screw.
7. Refer to the Battery Charging instructions for recharging times.
Changing the Dust Filter
The electronic module has a dust filter fitted to the underside of the module. Every three months a new filter wil
be supplied. To change the filter, proceed as follows:
1.
Switch off the mains supply and pull out the old filter (Fig 25).
2.
Feed in the new filter with the blue side facing in, pushing it well into the corners of the holder.
3. Switch on the mains supply.
Figure 25. Dust filter replacement Figure 26. Support arm adjustment
Support Arm Adjustment
Periodically the support arm mechanism may require adjustment.
1.
Remove the cross head arm fixing screw.
2.
Using a suitable screwdriver, turn the tensioning screw (Fig 26) anti-clockwise half a
turn.
3. Refit the leg fixing screw and repeat the operation on the opposite side.
4.
Check that the arm tension is enough to support the weight of the PDU without movement.
VIA Carrying Case
The VIA unit (0018) is secured into its carrying case with two fixing screws from the underside of the case. If a new
VIA is required, remove the two fixing screws and lift the VIA from the carrying case. Return only the VIA for
replacement, do not return the carrying case.
May 1996 9-23
Page 379 of 421
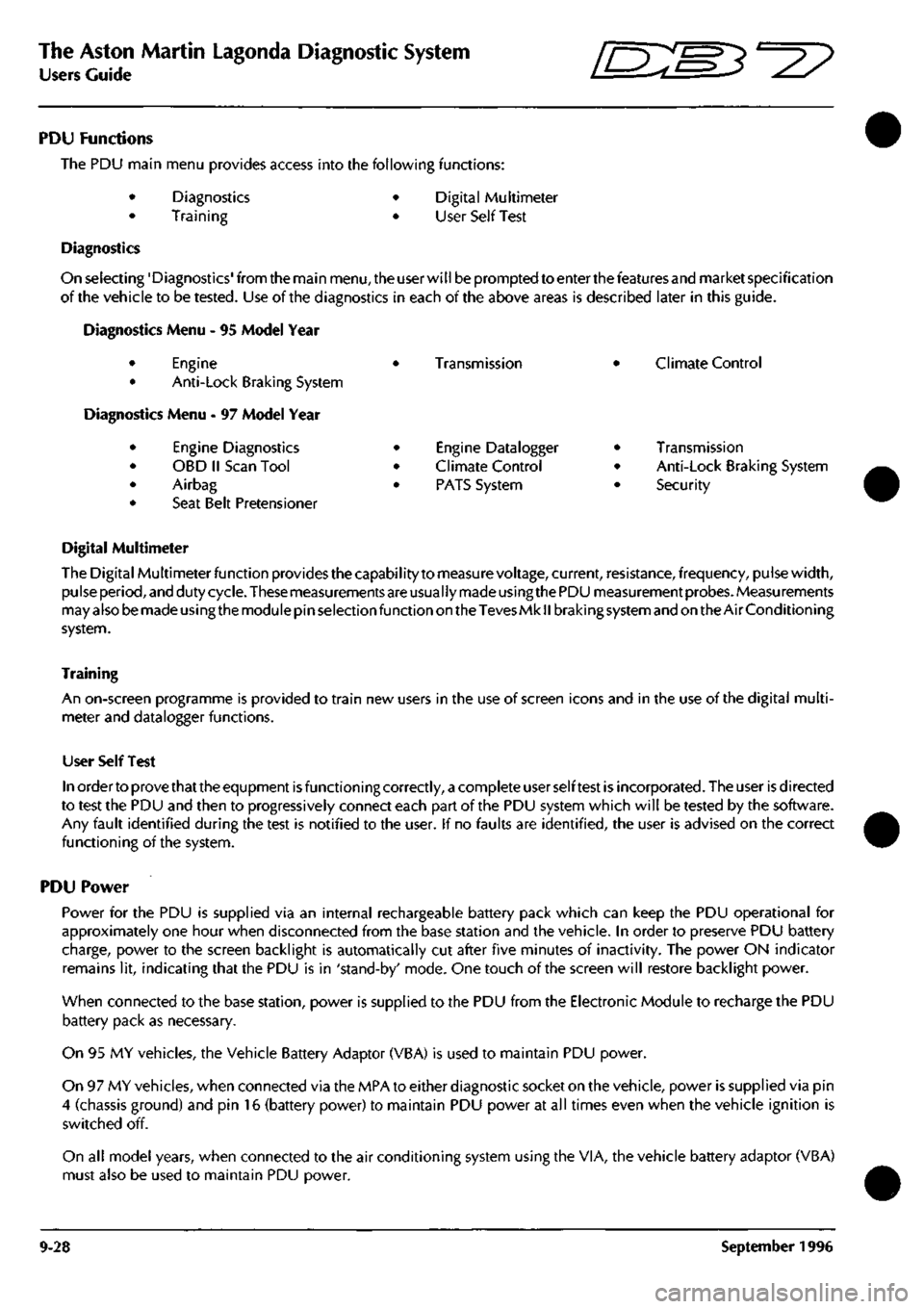
The Aston Martin Lagonda Diagnostic System
Users Guide o: "3^^?
PDU Functions
The PDU main menu provides access into the following functions:
Diagnostics
Training
Digital Multimeter
User Self Test
Diagnostics
On selecting'Diagnostics'from the main
menu,
the user will be prompted to enter the features and market specification
of the vehicle to be tested. Use of the diagnostics in each of the above areas is described later in this guide.
Diagnostics Menu - 95 Model Year
Engine
Anti-Lock Braking System
Vlenu - 97 Model Year
Engine Diagnostics
OBD II Scan Tool
Airbag
Seat Belt Pretensioner
•
•
•
•
Transmission
Engine Datalogger
Climate Control
PATS System
Climate Control
Transmission
Anti-Lock Braking System
Security
Digital Multimeter
The Digital Multimeter function provides the capabilityto measure voltage, current, resistance, frequency, pulse width,
pulse period, and duty cycle. These measurements are usually made using the PDU measurement probes. Measurements
may also be made using the module pin selection function on the Teves Mk
II
braking system and on the Air Conditioning
system.
Training
An on-screen programme is provided to train new users in the use of screen icons and in the use of the digital multi
meter and datalogger functions.
User Self Test
In order to prove that the equpment is functioning correctly, a complete user self test is incorporated. The user is directed
to test the PDU and then to progressively connect each part of the PDU system which will be tested by the software.
Any fault identified during the test is notified to the user. If no faults are identified, the user is advised on the correct
functioning of the system.
PDU Power
Power for the PDU is supplied via an internal rechargeable battery pack which can keep the PDU operational for
approximately one hour when disconnected from the base station and the vehicle. In order to preserve PDU battery
charge, power to the screen backlight is automatically cut after five minutes of inactivity. The power ON indicator
remains lit, indicating that the PDU is in 'stand-by' mode. One touch of the screen will restore backlight power.
When connected to the base station, power is supplied to the PDU from the Electronic Module to recharge the PDU
battery pack as necessary.
On 95 MY vehicles, the Vehicle Battery Adaptor (VBA) is used to maintain PDU power.
On 97 MY vehicles, when connected via the MPA to either diagnostic socket on the vehicle, power is supplied via pin
4 (chassis ground) and pin 16 (battery power) to maintain PDU power at all times even when the vehicle ignition is
switched off.
On all model years, when connected to the air conditioning system using the VIA, the vehicle battery adaptor (VBA)
must also be used to maintain PDU power.
9-28 September 1996
Page 380 of 421
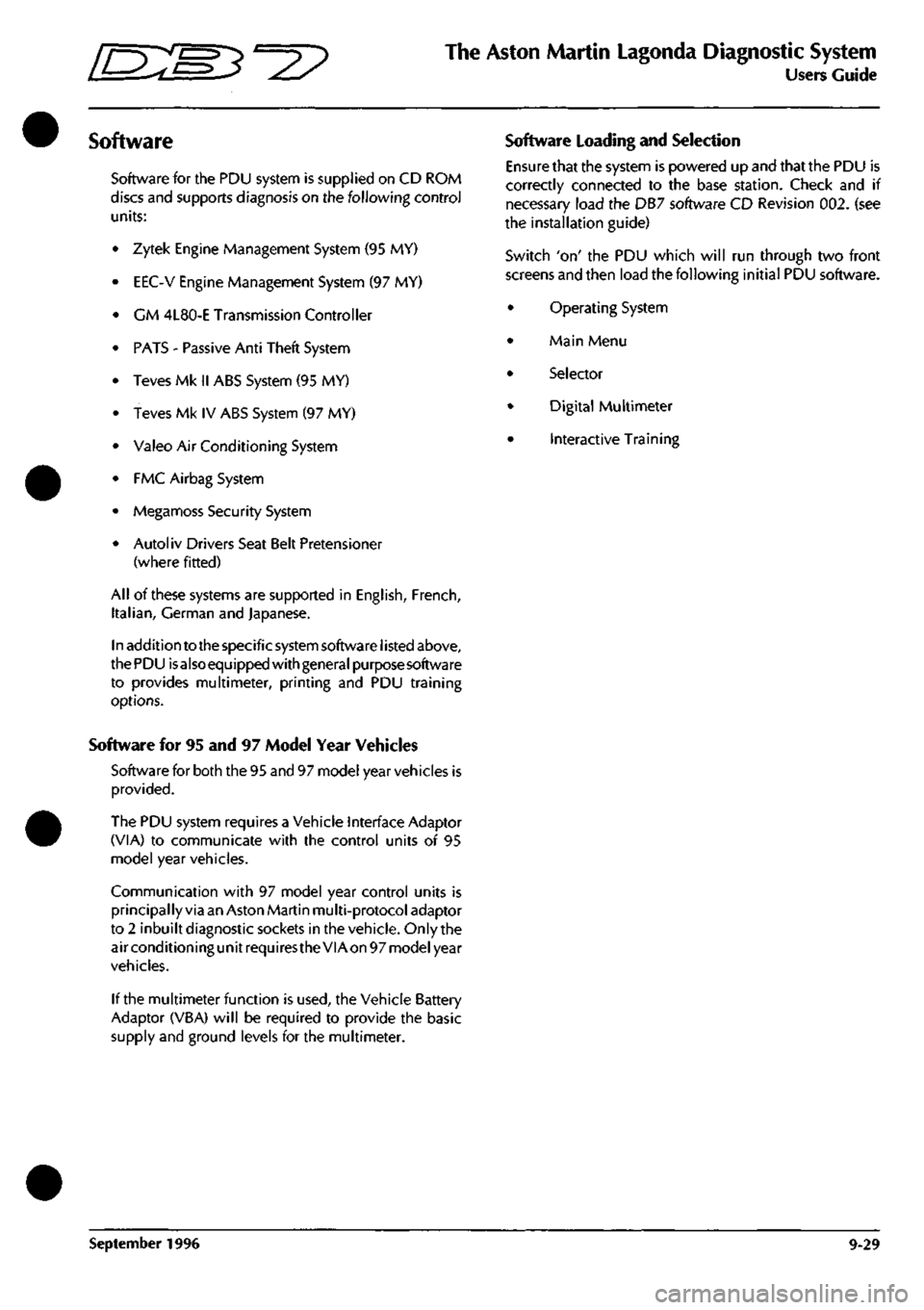
^=2?
The Aston Martin Lagonda Diagnostic System
Users Guide
Software
Software for the PDU system is supplied on CD ROM
discs and supports diagnosis on the following control
units:
Zytek Engine Management System (95 MY)
EEC-V Engine Management System (97 MY)
CM 4L80-E Transmission Controller
PATS - Passive Anti Theft System
Teves Mk II ABS System (95 MY)
Teves Mk IV ABS System (97 MY)
Valeo Air Conditioning System
PMC Airbag System
Megamoss Security System
Autoliv Drivers Seat Belt Pretensioner
(where fitted)
All of these systems are supported in English, French,
Italian,
German and Japanese.
In addition to the specific system software listed above,
thePDU isalsoequipped with general purpose software
to provides multimeter, printing and PDU training
options.
Software for 95 and 97 Model Year Vehicles
Software for both the 95 and 97 model year vehicles is
provided.
The PDU system requires a Vehicle Interface Adaptor
(VIA) to communicate with the control units of 95
model year vehicles.
Communication with 97 model year control units is
principally via an Aston Martin multi-protocol adaptor
to 2 inbuilt diagnostic sockets in the vehicle. Only the
air conditioning unit requires the VIA on 97 model year
vehicles.
If the multimeter function is used, the Vehicle Battery
Adaptor (VBA) will be required to provide the basic
supply and ground levels for the multimeter.
Software Loading and Selection
Ensure that the system is powered up and that the PDU is
correctly connected to the base station. Check and if
necessary load the DB7 software CD Revision 002. (see
the installation guide)
Switch 'on' the PDU which will run through two front
screens and then load the following initial PDU software.
Operating System
Main Menu
Selector
Digital Multimeter
Interactive Training
September 1996 9-29
Page 381 of 421
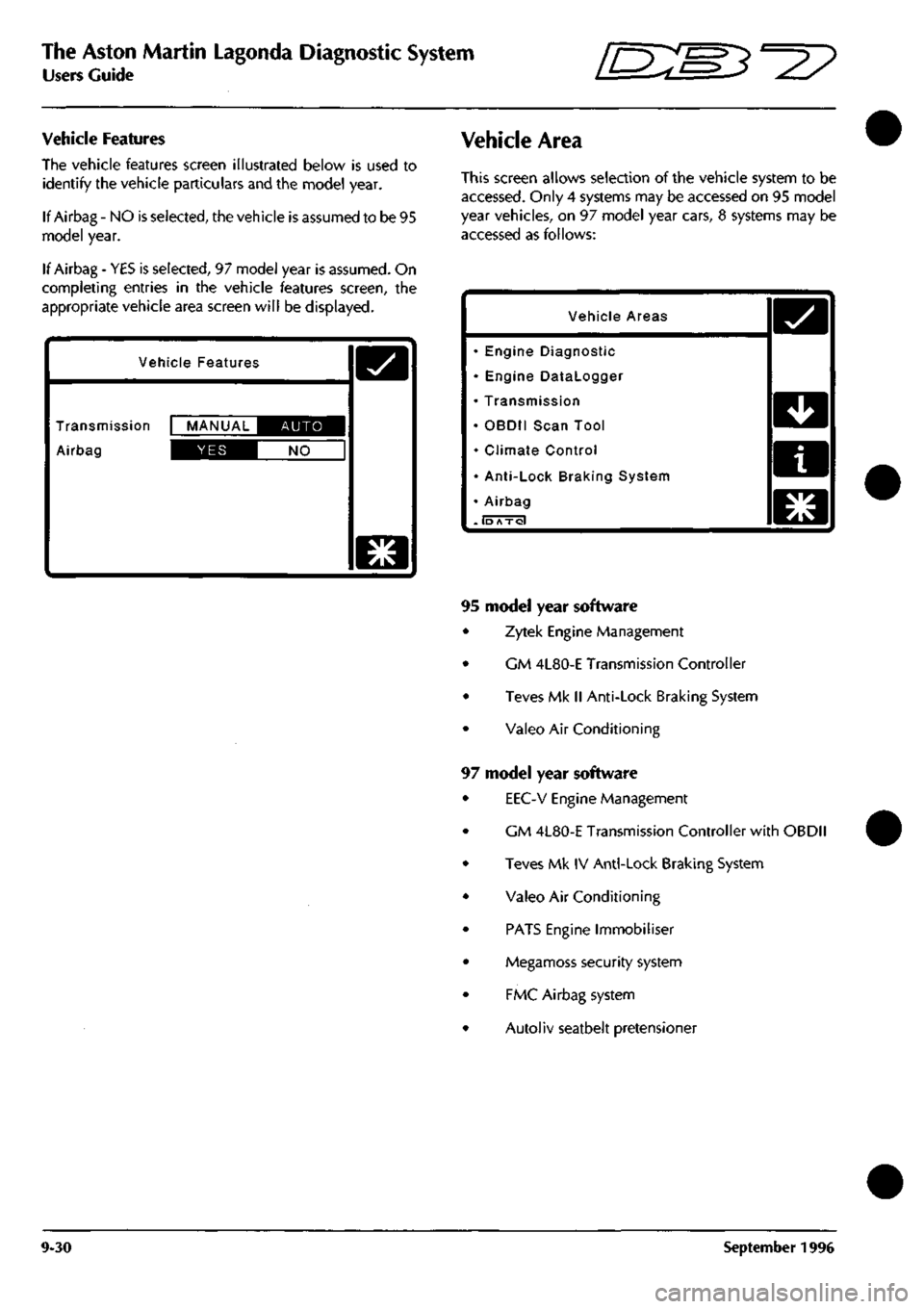
The Aston Martin Lagonda Diagnostic System
Users Guide D-^?
Vehicle Features
The vehicle features screen illustrated below is used to
identify the vehicle particulars and the model year.
If Airbag - NO is selected, the vehicle is assumed to be 95
model year.
If Airbag - YES is selected, 97 model year is assumed. On
completing entries in the vehicle features screen, the
appropriate vehicle area screen will be displayed.
Vehicle Features
Transmission MANUAL IIBIE^^I
Airbag IDS^I NO
D
Vehicle Area
This screen allows selection of the vehicle system to be
accessed.
Only 4 systems may be accessed on 95 model
year vehicles, on 97 model year cars, 8 systems may be
accessed as follows:
Vehicle Areas
• Engine Diagnostic
• Engine Datalogger
• Transmission
• OBDII Scan Tool
• Climate Control
• Anti-Lock Braking System
• Airbag
. lb Axol
o
PI
mLM
n
WLM
El
Ku^
95 model year software
Zytek Engine Management
GM 4L80-E Transmission Controller
Teves Mk II Anti-Lock Braking System
Valeo Air Conditioning
97 model year software
EEC-V Engine Management
CM 4L80-E Transmission Controller with OBDII
Teves Mk IV Anti-Lock Braking System
Valeo Air Conditioning
PATS Engine Immobiliser
Megamoss security system
FMC Airbag system
Autoliv seatbelt pretensioner
9-30 September 1996
Page 382 of 421
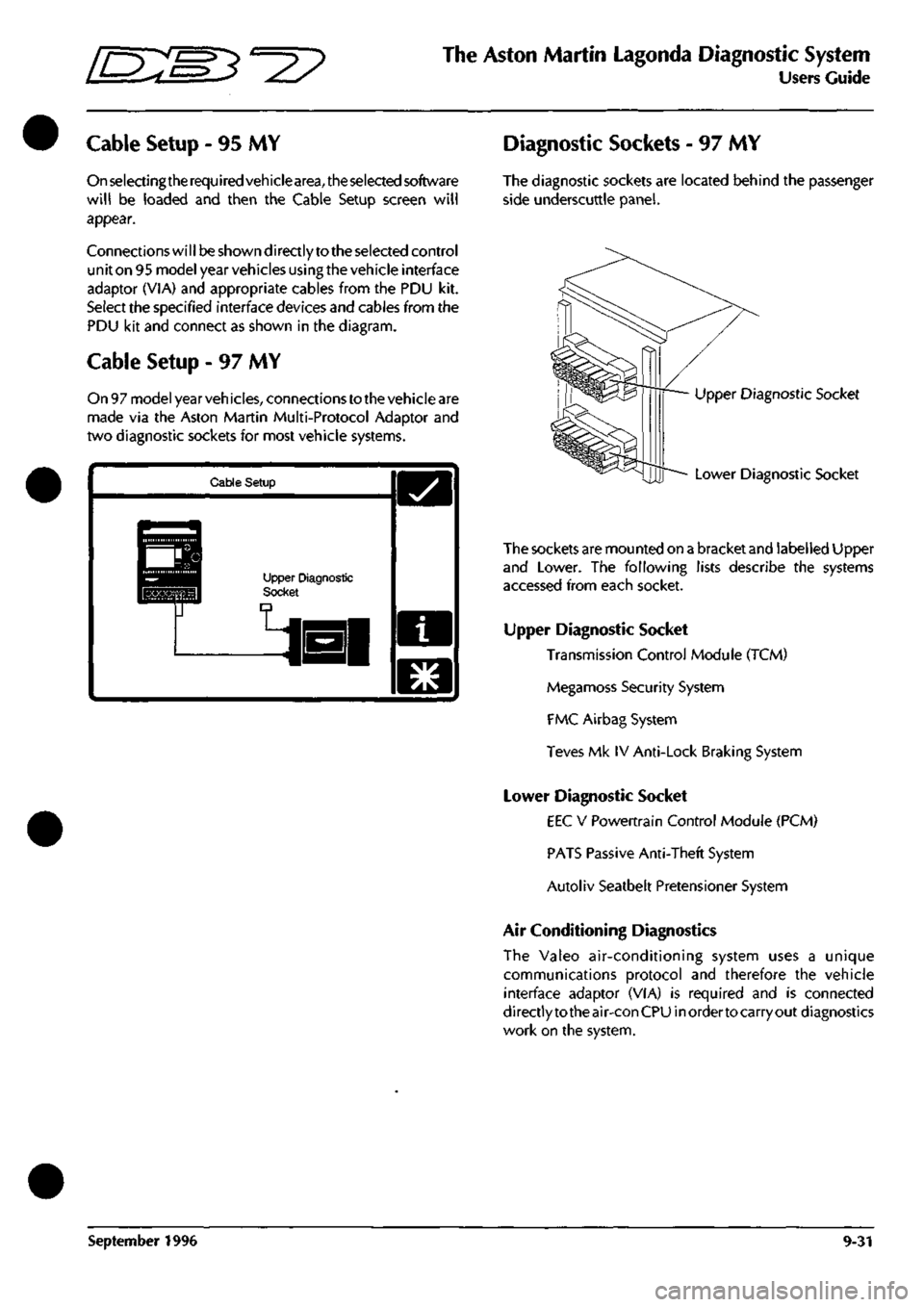
^?
The Aston Martin Lagonda Diagnostic System
Users Guide
Cable Setup - 95 MY
On
selectingthe
required
vehiclearea,
the selected
software
will be loaded and then the Cable Setup screen will
appear.
Connections will
be
shown directly
to the selected
control
unit
on
95 nnodel year vehicles
using
the vehicle interface
adaptor (VIA) and appropriate cables from the PDU kit.
Select the specified interface devices and cables from the
PDU kit and connect as shown in the diagram.
Cable Setup - 97 MY
On 97 model year
vehicles,
connections
to the
vehicle are
made via the Aston Martin Multi-Protocol Adaptor and
two diagnostic sockets for most vehicle systems.
Cable Setup
Upper Diagnostic Socket
o
Diagnostic Sockets - 97 MY
The diagnostic sockets are located behind the passenger
side underscuttle panel.
Upper Diagnostic Socket
Lower Diagnostic Socket
The
sockets are
mounted on
a
bracket
and
labelled Upper
and Lower. The following lists describe the systems
accessed from each socket.
Upper Diagnostic Socket
Transmission Control Module (TCM)
Megamoss Security System
FMC Airbag System
Teves Mk IV Anti-Lock Braking System
Lower Diagnostic Socket
EEC V Powertrain Control Module (PCM)
PATS Passive Anti-Theft System
Autoliv Seatbelt Pretensioner System
Air Conditioning Diagnostics
The Valeo air-conditioning system uses a unique
communications protocol and therefore the vehicle
interface adaptor (VIA) is required and is connected
directlytotheair-conCPU inordertocarryout diagnostics
work on the system.
September 1996 9-31
Page 383 of 421
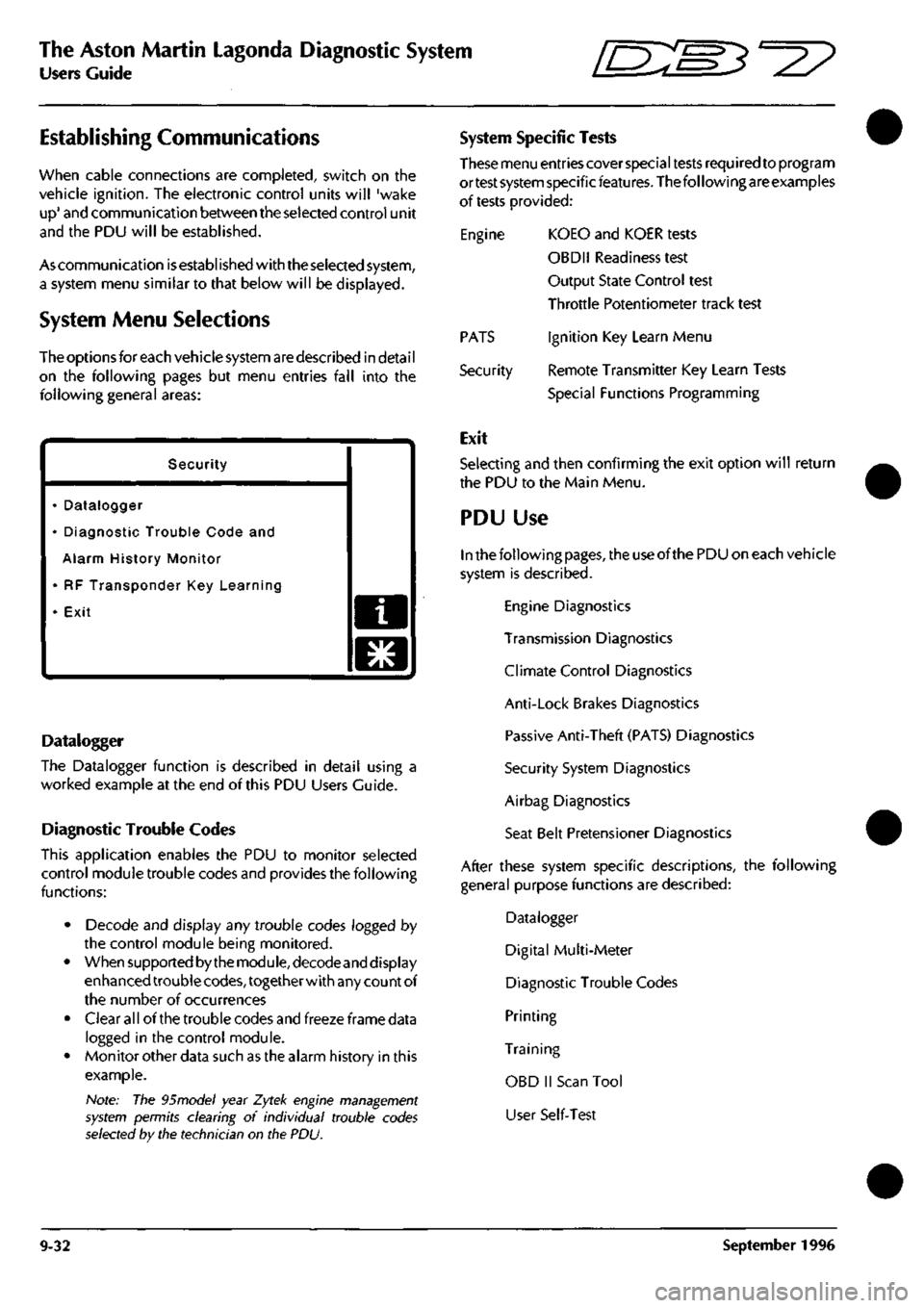
The Aston Martin Lagonda Diagnostic System
Users Guide "^7
Establishing Communications
when cable connections are completed, switch on the
vehicle ignition. The electronic control units will 'wake
up'
and communication between the selected control unit
and the PDU will be established.
As communication
is
established with the selected system,
a system menu similar to that below will be displayed.
System Menu Selections
The options for each vehicle system are described in detai
I
on the following pages but menu entries fall into the
following general areas:
Security
• Datalogger
• Diagnostic Trouble Code and
Alarm History Monitor
• RF Transponder Key Learning
• Exit a
o
Datalogger
The Datalogger function is described in detail using a
worked example at the end of this PDU Users Guide.
Diagnostic Trouble Codes
This application enables the PDU to monitor selected
control module trouble codes and provides the following
functions:
• Decode and display any trouble codes logged by
the control module being monitored.
• When supported by the module, decodeand display
enhanced trouble
codes,
together with any count of
the number of occurrences
• Clear all of the trouble codes and freeze frame data
logged in the control module.
• Monitor other data such as the alarm history in this
example.
Note: The 95model year Zytek engine management
system permits clearing of individual trouble codes
selected by the technician on the PDU.
System Specific Tests
These menu entries cover special tests required to program
ortest system specificfeatures. The following are examples
of tests provided:
Engine KOEO and KOER tests
OBDII Readiness test
Output State Control test
Throttle Potentiometer track test
Ignition Key Learn Menu
Remote Transmitter Key Learn Tests
Special Functions Programming
PATS
Security
Exit
Selecting and then confirming the exit option will return
the PDU to the Main Menu.
PDU Use
In the following
pages,
the use of the PDU on each vehicle
system is described.
Engine Diagnostics
Transmission Diagnostics
Climate Control Diagnostics
Anti-Lock Brakes Diagnostics
Passive Anti-Theft (PATS) Diagnostics
Security System Diagnostics
Airbag Diagnostics
Seat Belt Pretensioner Diagnostics
After these system specific descriptions, the following
general purpose functions are described:
Datalogger
Digital Multi-Meter
Diagnostic Trouble Codes
Printing
Training
OBD II Scan Tool
User Self-Test
9-32 September 1996
Page 387 of 421
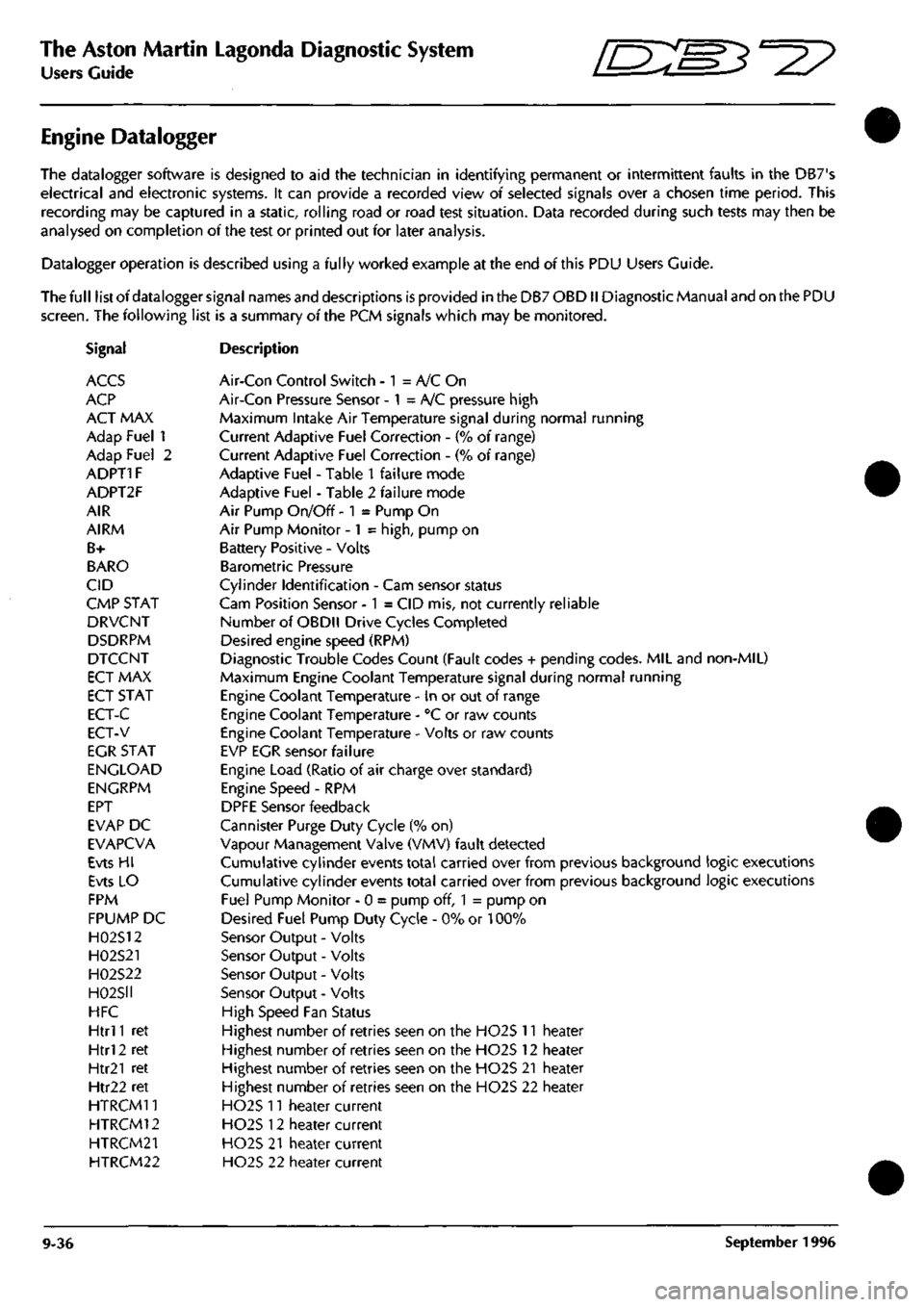
The Aston Martin Lagonda Diagnostic System
Users Guide ffi:S5'=2?
Engine Datalogger
The datalogger software is designed to aid the technician in identifying permanent or intermittent faults in the DB7's
electrical and electronic systems. It can provide a recorded view of selected signals over a chosen time period. This
recording may be captured in a static, rolling road or road test situation. Data recorded during such tests may then be
analysed on completion of the test or printed out for later analysis.
Datalogger operation is described using a fully worked example at the end of this PDU Users Guide.
The full list of datalogger signal names and descriptions is provided in the DB7 OBDII Diagnostic Manual and on the PDU
screen.
The following list is a summary of the PCM signals which may be monitored.
Signal Description
ACCS Air-Con Control Switch - 1 = A/C On
ACP Air-Con Pressure Sensor - 1 = A/C pressure high
ACT MAX Maximum Intake Air Temperature signal during normal running
Adap Fuel 1 Current Adaptive Fuel Correction - (% of range)
Adap Fuel 2 Current Adaptive Fuel Correction - (% of range)
ADPT1F Adaptive Fuel - Table 1 failure mode
ADPT2F Adaptive Fuel - Table 2 failure mode
AIR Air Pump On/Off - 1 = Pump On
AIRM Air Pump Monitor -1 =
high,
pump on
B+ Battery Positive - Volts
BARO Barometric Pressure
CID Cylinder Identification - Cam sensor status
CMP STAT Cam Position Sensor -1 = CID mis, not currently reliable
DRVCNT Number of OBDll Drive Cycles Completed
DSDRPM Desired engine speed (RPM)
DTCCNT Diagnostic Trouiale Codes Count (Fault codes + pending codes. MIL and non-MIL)
ECT MAX Maximum Engine Coolant Temperature signal during normal running
ECT STAT Engine Coolant Temperature - in or out of range
ECT-C Engine Coolant Temperature - "C or raw counts
ECT-V Engine Coolant Temperature - Volts or raw counts
EGR STAT EVP EGR sensor failure
ENGLOAD Engine Load (Ratio of air charge over standard)
ENGRPM Engine Speed - RPM
EPT DPFE Sensor feedback
EVAP DC Cannister Purge Duty Cycle (% on)
EVAPCVA Vapour Management Valve (VMV) fault detected
Evts HI Cumulative cylinder events total carried over from previous background logic executions
Evts LO Cumulative cylinder events total carried over from previous background logic executions
FPM Fuel Pump Monitor - 0 = pump off, 1 = pump on
FPUMP DC Desired Fuel Pump Duty Cycle - 0% or 100%
H02S12 Sensor Output - Volts
H02S21 Sensor Output - Volts
H02S22 Sensor Output - Volts
H02S1I Sensor Output - Volts
HFC High Speed Fan Status
Htrl
1
ret Highest number of retries seen on the H02S 11 heater
Htrl 2 ret Highest number of retries seen on the H02S 12 heater
Htr21 ret Highest number of retries seen on the H02S 21 heater
Htr22 ret Highest number of retries seen on the H02S 22 heater
HTRCM11 H02S n heater current
HTRCM12 H02S 12 heater current
HTRCM21 H02S 21 heater current
HTRCM22 H02S 22 heater current
9-36 September 1996
Page 395 of 421
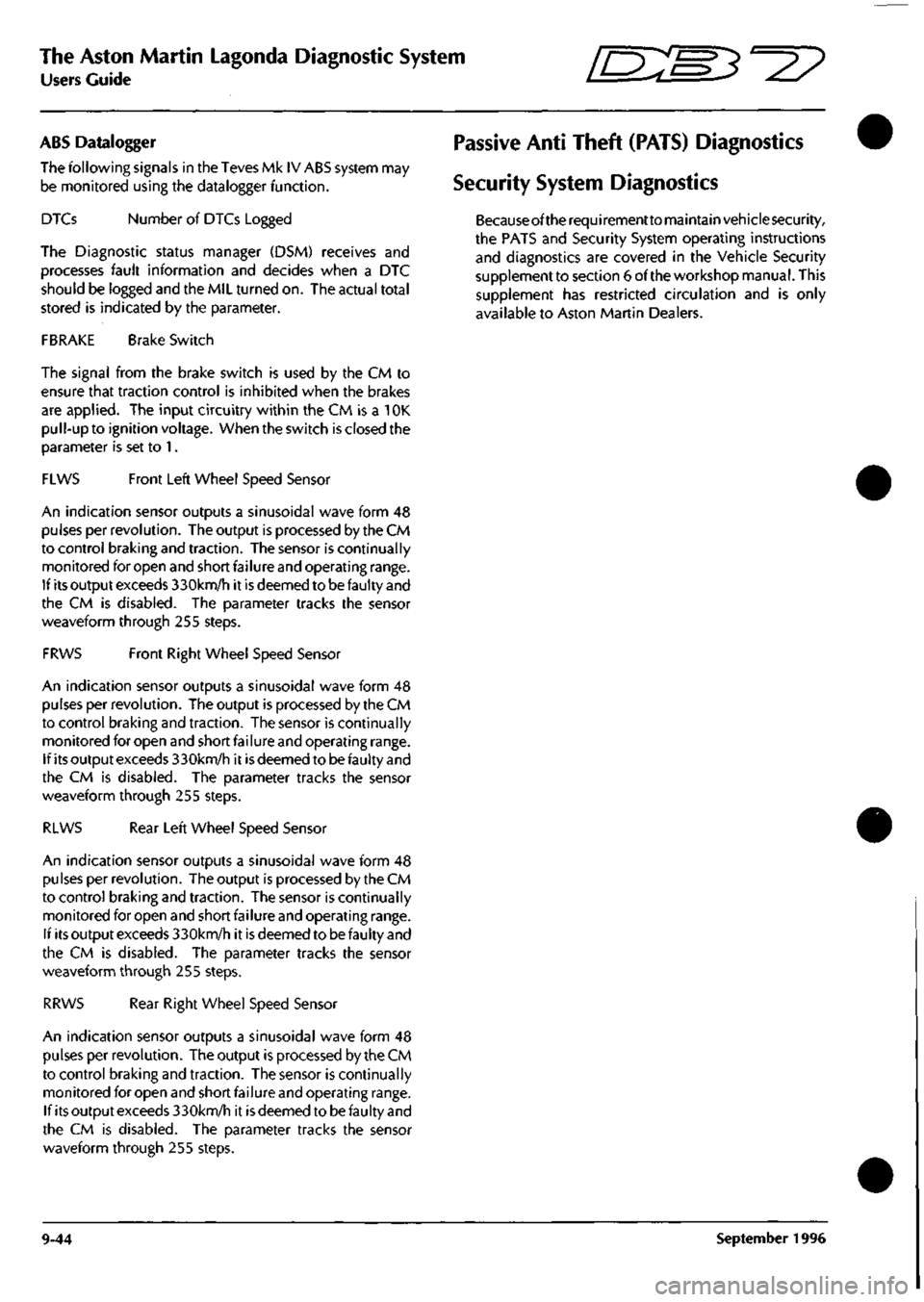
The Aston Martin Lagonda Diagnostic System
Users Guide
Em^'^?
ABS Datalogger
The following signals in the Teves Mk IV ABS system may
be monitored using the datalogger function.
DTCs Number of DTCs Logged
The Diagnostic status manager (DSM) receives and
processes fault information and decides when a DTC
should be logged and the MIL turned on. The actual total
stored is indicated by the parameter.
FBRAKE Brake Switch
The signal from the brake switch is used by the CM to
ensure that traction control is inhibited when the brakes
are applied. The input circuitry within the CM is a
1
OK
pull-up to ignition voltage. When the switch is closed the
parameter is set to 1.
FLWS Front Left Wheel Speed Sensor
An indication sensor outputs a sinusoidal wave form 48
pulses per revolution. The output is processed by the CM
to control braking and traction. The sensor is continually
monitored for open and short failure and operating range.
If its output exceeds 330km/h it is deemed to be faulty and
the CM is disabled. The parameter tracks the sensor
weaveform through 255 steps.
FRWS Front Right Wheel Speed Sensor
An indication sensor outputs a sinusoidal wave form 48
pulses per revolution. The output is processed by the CM
to control braking and traction. The sensor is continually
monitored for open and short failure and operating range.
If its output exceeds 330km/h it
is
deemed to be faulty and
the CM is disabled. The parameter tracks the sensor
weaveform through 255 steps.
RLWS Rear Left Wheel Speed Sensor
An indication sensor outputs a sinusoidal wave form 48
pulses per revolution. The output is processed by the CM
to control braking and traction. The sensor is continually
monitored for open and short failure and operating range.
If its output exceeds 330km/h it
is
deemed to be faulty and
the CM is disabled. The parameter tracks the sensor
weaveform through 255 steps.
RRWS Rear Right Wheel Speed Sensor
An indication sensor outputs a sinusoidal wave form 48
pulses per revolution. The output is processed by the CM
to control braking and traction. The sensor is continually
monitored for open and short failure and operating range.
If its output exceeds 330km/h it is deemed to be faulty and
the CM is disabled. The parameter tracks the sensor
waveform through 255 steps.
Passive Anti Theft (PATS) Diagnostics
Security System Diagnostics
Becauseof the requirementto maintain vehicle security,
the PATS and Security System operating instructions
and diagnostics are covered in the Vehicle Security
supplement to section 6 of the workshop manual. This
supplement has restricted circulation and is only
available to Aston Martin Dealers.
9-44 September 1996
Page 398 of 421
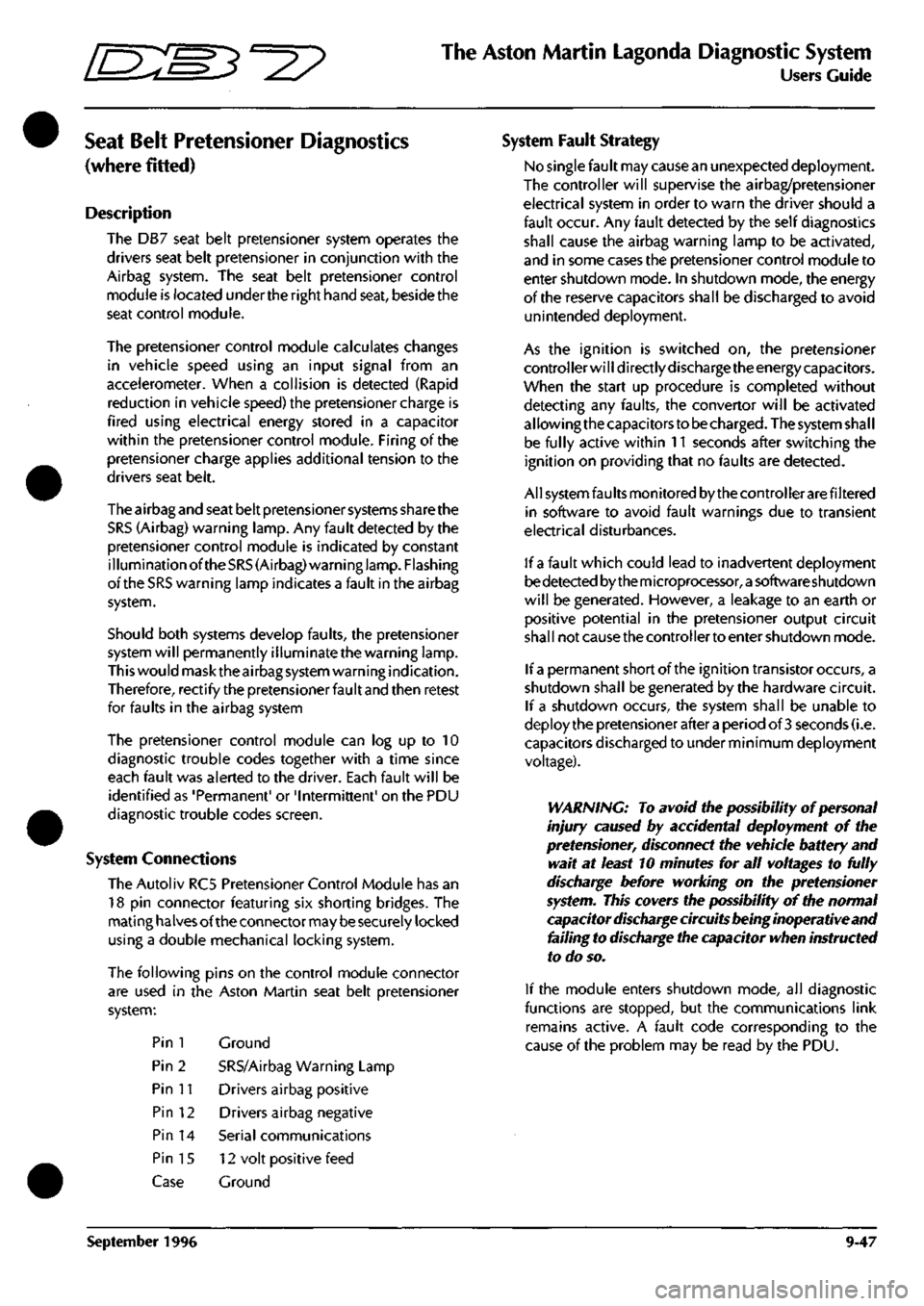
^^?
The Aston Martin Lagonda Diagnostic System
Users Guide
Seat Belt Pretensioner Diagnostics
(where fitted)
Description
The DB7 seat belt pretensioner system operates the
drivers seat belt pretensioner in conjunction with the
Airbag system. The seat belt pretensioner control
module is located underthe right hand seat, beside the
seat control module.
The pretensioner control module calculates changes
in vehicle speed using an input signal from an
accelerometer. When a collision is detected (Rapid
reduction in vehicle speed) the pretensioner charge is
fired using electrical energy stored in a capacitor
within the pretensioner control module. Firing of the
pretensioner charge applies additional tension to the
drivers seat belt.
The airbag and seat belt pretensioner systems share the
SRS (Airbag) warning lamp. Any fault detected by the
pretensioner control module is indicated by constant
illumination ofthe
SRS
(Airbag) warning
lamp.
Flashing
of the SRS warning lamp indicates a fault in the airbag
system.
Should both systems develop faults, the pretensioner
system will permanently illuminate the warning lamp.
This would mask the airbag system warning indication.
Therefore, rectify the pretensioner fault and then retest
for faults in the airbag system
The pretensioner control module can log up to 10
diagnostic trouble codes together with a time since
each fault was alerted to the driver. Each fault will be
identified as 'Permanent' or 'Intermittent' on the PDU
diagnostic trouble codes screen.
System Connections
The Autoliv RC5 Pretensioner Control Module has an
18 pin connector featuring six shorting bridges. The
mating halves ofthe connector may be securely locked
using a double mechanical locking system.
The following pins on the control module connector
are used in the Aston Martin seat belt pretensioner
system:
Pin 1
Pin 2
Pin n
Pin 12
Pin 14
Pin 15
Case
September 1996
Ground
SRS/Airbag Warning Lamp
Drivers airbag positive
Drivers airbag negative
Serial communications
12 volt positive feed
Ground
System Fault Strategy
No single fault may cause an unexpected deployment.
The controller will supervise the airbag/pretensioner
electrical system in order to warn the driver should a
fault occur. Any fault detected by the self diagnostics
shall cause the airbag warning lamp to be activated,
and in some cases the pretensioner control module to
enter shutdown mode. In shutdown mode, the energy
ofthe reserve capacitors shall be discharged to avoid
unintended deployment.
As the ignition is switched on, the pretensioner
controller will directly discharge theenergy capacitors.
When the start up procedure is completed without
detecting any faults, the converter will be activated
allowing the capacitors to be
charged.
The system shall
be fully active within 11 seconds after switching the
ignition on providing that no faults are detected.
All system faults monitored by the controller are filtered
in software to avoid fault warnings due to transient
electrical disturbances.
If a fault which could lead to inadvertent deployment
bedetectedbythemicroprocessor,asoftwareshutdown
will be generated. However, a leakage to an earth or
positive potential in the pretensioner output circuit
shall not cause the controller to enter shutdown mode.
If
a
permanent short of the ignition transistor occurs, a
shutdown shall be generated by the hardware circuit.
If a shutdown occurs, the system shall be unable to
deploy the pretensioner after a period of
3
seconds (i.e.
capacitors discharged to under minimum deployment
voltage).
WARNING: To avoid the possibility of personal
injury caused by accidental deployment of the
pretensioner, disconnect the vehicle battery and
wait at least 10 minutes for all voltages to fully
discharge before working on the pretensioner
system. This covers the possibility of the normal
capacitor discharge circuits being inopera tive and
failing to discharge the capacitor when instructed
to do so.
If the module enters shutdown mode, all diagnostic
functions are stopped, but the communications link
remains active. A fault code corresponding to the
cause of the problem may be read by the PDU.
9-47
Page 401 of 421
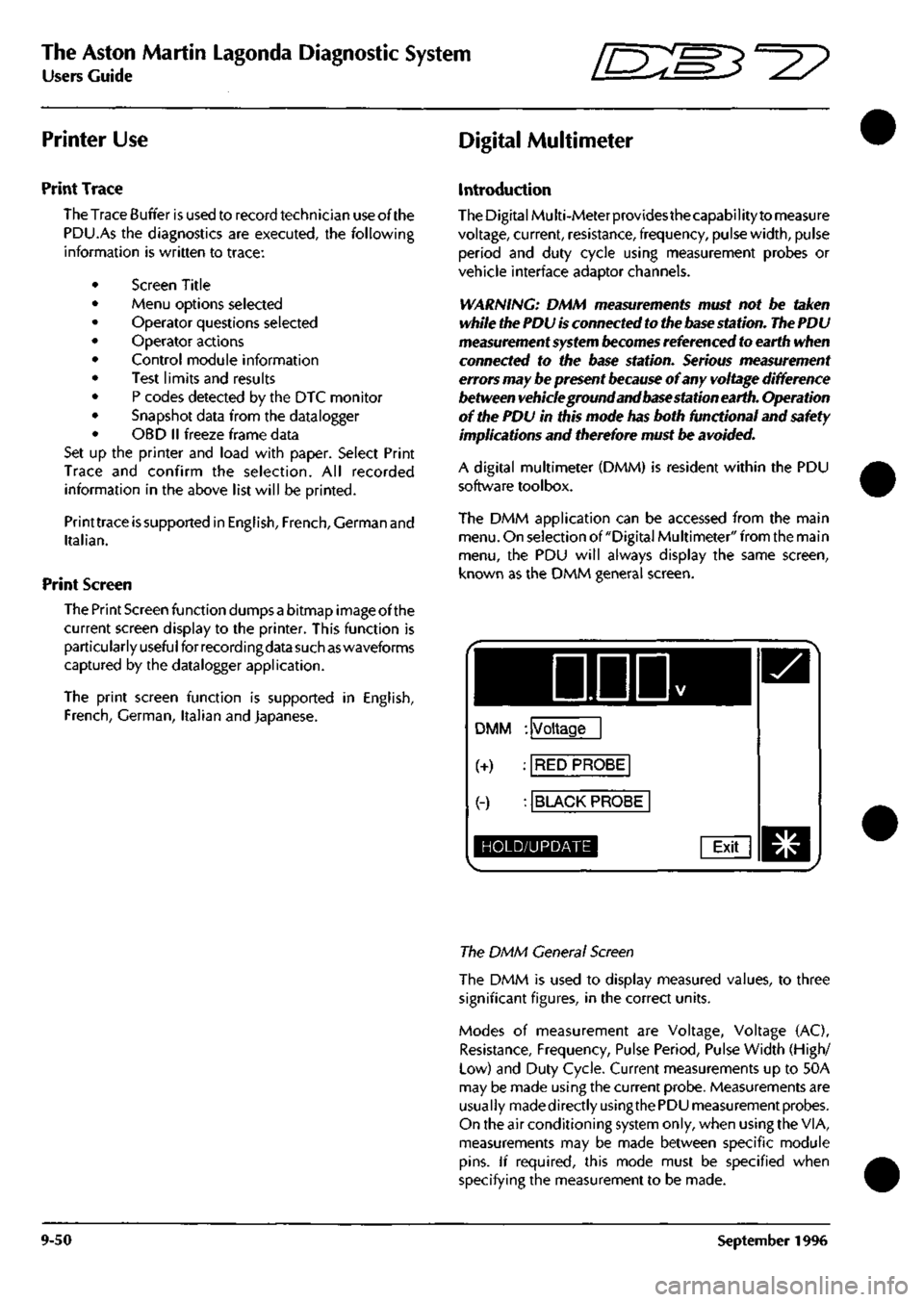
The Aston Martin Lagonda Diagnostic System
Users Guide ^=2?
Printer Use Digital Multimeter
Print Trace
The Trace Buffer is used to record technician use of the
PDU.As the diagnostics are executed, the following
information is written to trace:
Screen Title
Menu options selected
Operator questions selected
Operator actions
Control module information
Test limits and results
P codes detected by the DTC monitor
Snapshot data from the datalogger
OBD II freeze frame data
Set up the printer and load with paper. Select Print
Trace and confirm the selection. All recorded
information in the above list will be printed.
Printtrace is supported in English, French, German and
Italian.
Print Screen
The Print Screen function dumps a bitmap image of the
current screen display to the printer. This function is
particularly useful for recordingdata such as waveforms
captured by the datalogger application.
The print screen function is supported in English,
French,
German, Italian and Japanese.
Introduction
The Digital Multi-Meterprovidesthecapability to measure
voltage, current, resistance, frequency, pulse width, pulse
period and duty cycle using measurement probes or
vehicle interface adaptor channels.
WARNING: DMM measurements must not be taken
while the PDU
is
connected to the
base
station. The PDU
measurement system
becomes
referenced to earth when
connected to the base station. Serious measurement
errors may be present
because
of any voltage difference
between vehicle ground and base station earth. Operation
of the PDU in this mode has both functional and safety
implications and therefore must be
avoided.
A digital multimeter (DMM) is resident within the PDU
software toolbox.
The DMM application can be accessed from the main
menu.
On selection of "Digital Multimeter" from the main
menu,
the PDU will always display the same screen,
known as the DMM general screen.
DDD
DMM : Voltage
(+) : RED PROBE
(-) : BLACK PROBE
HOLD/UPDATE Exit
The DMM General Screen
The DMM is used to display measured values, to three
significant figures, in the correct units.
Modes of measurement are Voltage, Voltage (AC),
Resistance, Frequency, Pulse Period, Pulse Width (High/
Low) and Duty Cycle. Current measurements up to 50A
may be made using the current probe. Measurements are
usually madedirectlyusingthe PDU measurement probes.
On the air conditioning system only, when using the VIA,
measurements may be made between specific module
pins.
If required, this mode must be specified when
specifying the measurement to be made.
9-50 September 1996