sensor ASTON MARTIN V8 VANTAGE 2010 User Guide
[x] Cancel search | Manufacturer: ASTON MARTIN, Model Year: 2010, Model line: V8 VANTAGE, Model: ASTON MARTIN V8 VANTAGE 2010Pages: 947, PDF Size: 43.21 MB
Page 148 of 947
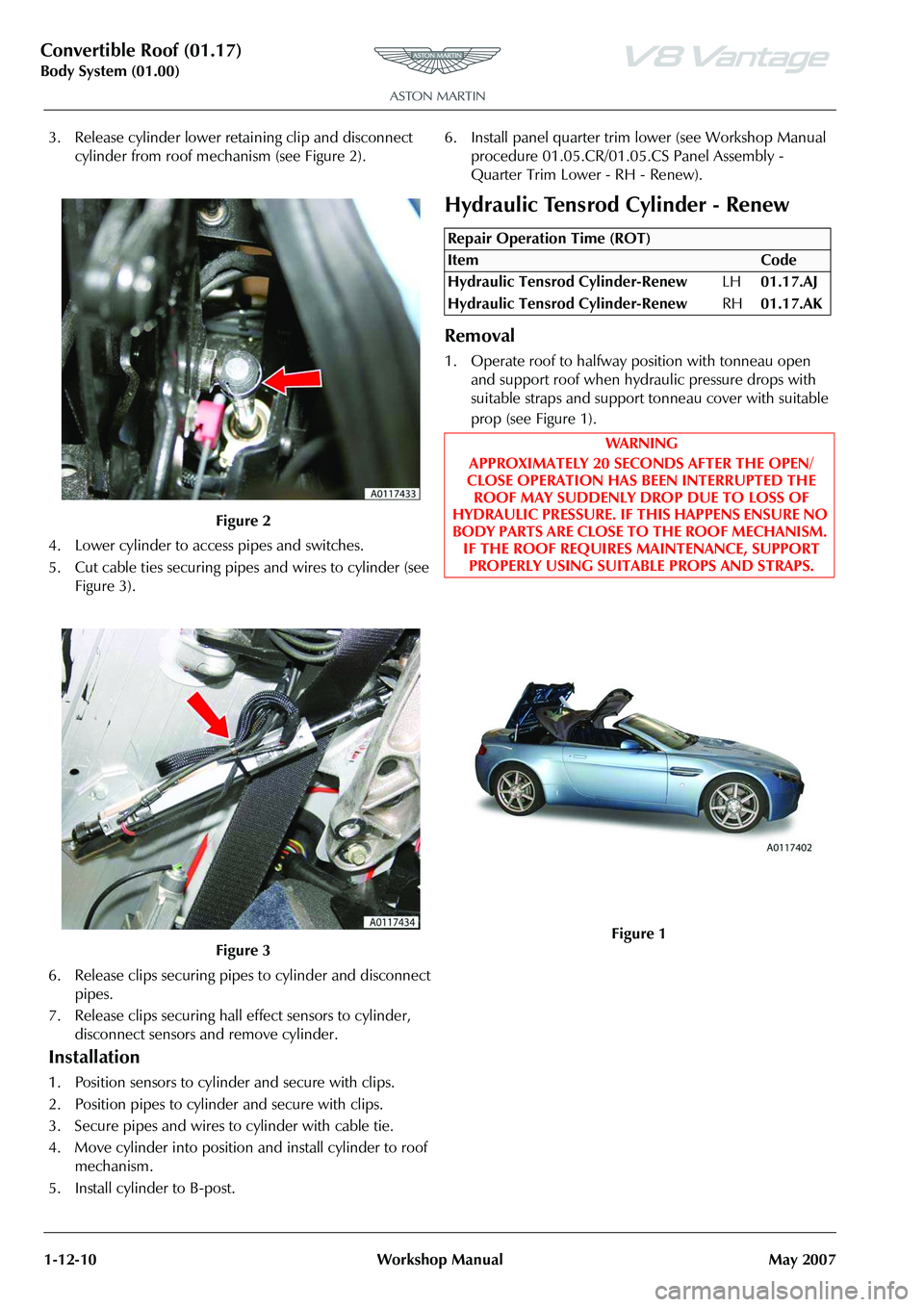
Convertible Roof (01.17)
Body System (01.00)1-12-10 Workshop Manual May 2007
3. Release cylinder lower retaining clip and disconnect cylinder from roof mechanism (see Figure 2).
4. Lower cylinder to access pipes and switches.
5. Cut cable ties securing pipes and wires to cylinder (see Figure 3).
6. Release clips securing pipes to cylinder and disconnect pipes.
7. Release clips securing hall effect sensors to cylinder,
disconnect sensors and remove cylinder.
Installation
1. Position sensors to cylind er and secure with clips.
2. Position pipes to cylinder and secure with clips.
3. Secure pipes and wires to cylinder with cable tie.
4. Move cylinder into position and install cylinder to roof
mechanism.
5. Install cylinder to B-post. 6. Install panel quarter trim lower (see Workshop Manual
procedure 01.05.CR/01.05.CS Panel Assembly -
Quarter Trim Lower - RH - Renew).
Hydraulic Tensrod Cylinder - Renew
Removal
1. Operate roof to halfway position with tonneau open and support roof when hydraulic pressure drops with
suitable straps and support tonneau cover with suitable
prop (see Figure 1).
Figure 2
Figure 3
Repair Operation Time (ROT)
ItemCode
Hydraulic Tensrod Cylinder-Renew LH01.17.AJ
Hydraulic Tensrod Cylinder-Renew RH01.17.AK
WAR NI NG
APPROXIMATELY 20 SECONDS AFTER THE OPEN/
CLOSE OPERATION HAS BEEN INTERRUPTED THE
ROOF MAY SUDDENLY DROP DUE TO LOSS OF
HYDRAULIC PRESSURE. IF THIS HAPPENS ENSURE NO
BODY PARTS ARE CLOSE TO THE ROOF MECHANISM.
IF THE ROOF REQUIRES MAINTENANCE, SUPPORT
PROPERLY USING SUITABLE PROPS AND STRAPS.
Figure 1
Page 150 of 947
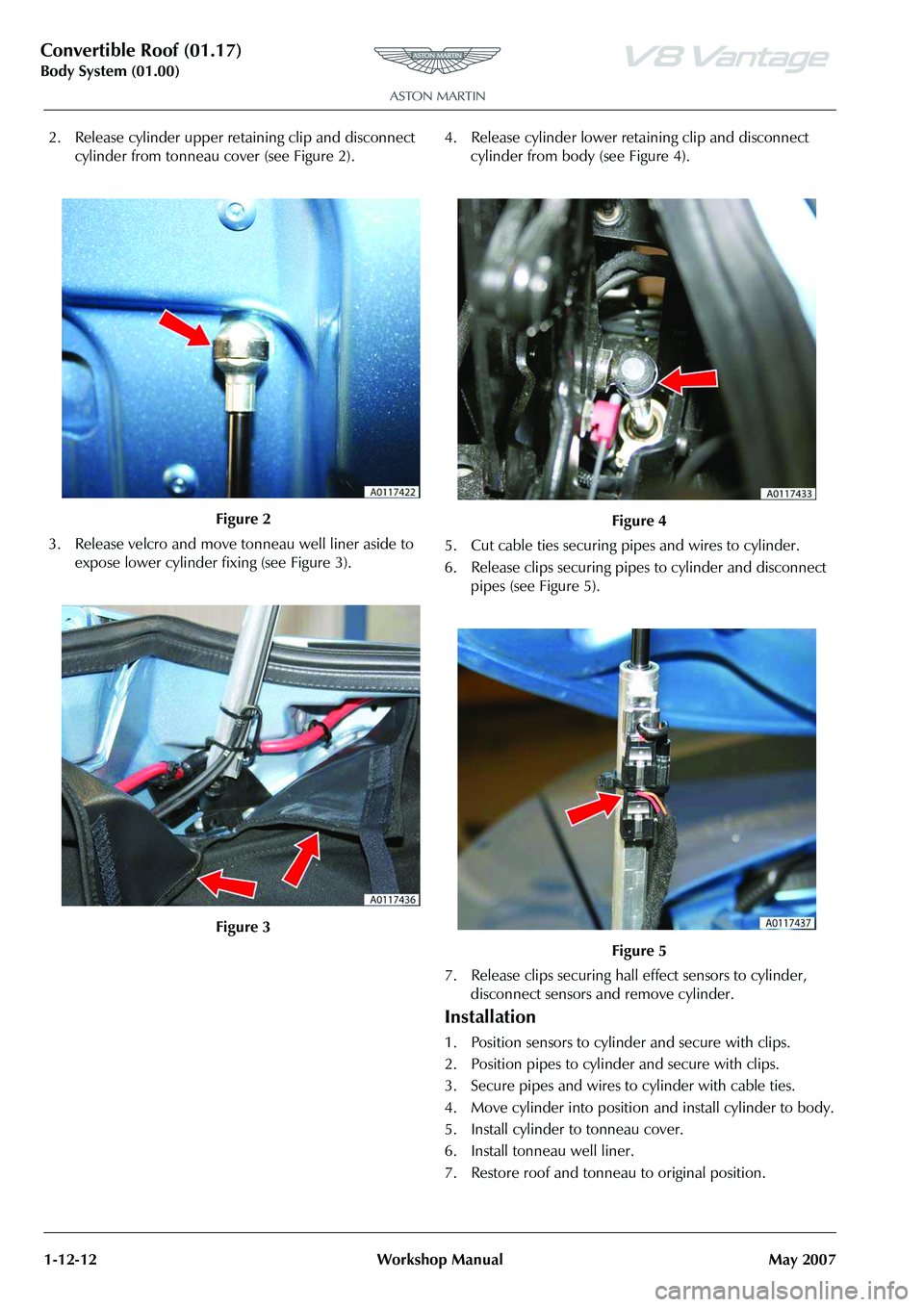
Convertible Roof (01.17)
Body System (01.00)1-12-12 Workshop Manual May 2007
2. Release cylinder upper retaining clip and disconnect cylinder from tonneau cover (see Figure 2).
3. Release velcro and move tonneau well liner aside to expose lower cylinder fixing (see Figure 3). 4. Release cylinder lower retaining clip and disconnect
cylinder from body (see Figure 4).
5. Cut cable ties securing pipes and wires to cylinder.
6. Release clips securing pipes to cylinder and disconnect pipes (see Figure 5).
7. Release clips securing hall effect sensors to cylinder, disconnect sensors and remove cylinder.
Installation
1. Position sensors to cylind er and secure with clips.
2. Position pipes to cylinder and secure with clips.
3. Secure pipes and wires to cylinder with cable ties.
4. Move cylinder into position and install cylinder to body.
5. Install cylinder to tonneau cover.
6. Install tonneau well liner.
7. Restore roof and tonneau to original position.
Figure 2
Figure 3
Figure 4
Figure 5
Page 160 of 947
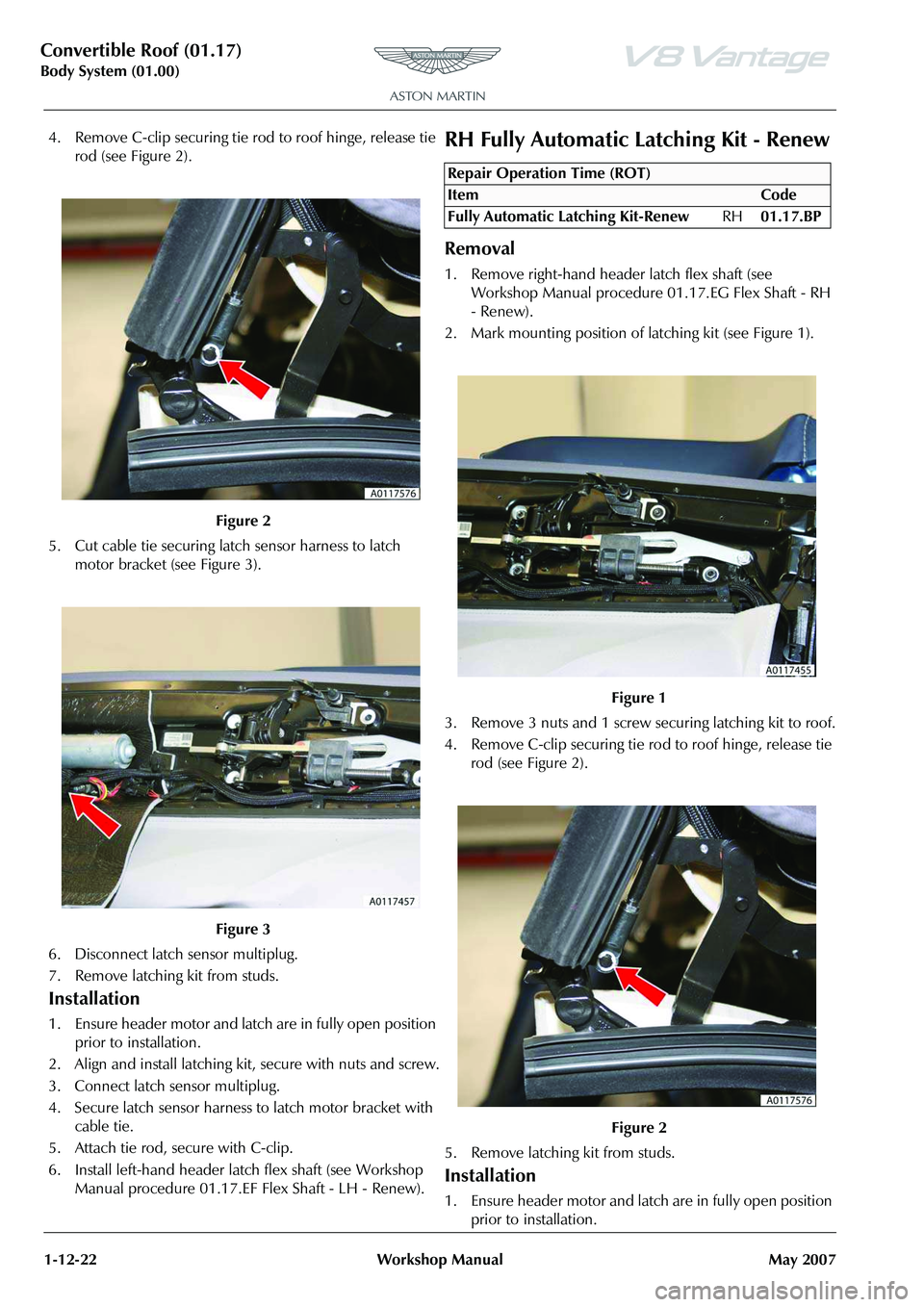
Convertible Roof (01.17)
Body System (01.00)1-12-22 Workshop Manual May 2007
4. Remove C-clip securing tie rod to roof hinge, release tie rod (see Figure 2).
5. Cut cable tie securing latch sensor harness to latch motor bracket (see Figure 3).
6. Disconnect latch sensor multiplug.
7. Remove latching kit from studs.
Installation
1. Ensure header motor and latch are in fully open position prior to installation.
2. Align and install latching kit, secure with nuts and screw.
3. Connect latch sensor multiplug.
4. Secure latch sensor harness to latch motor bracket with
cable tie.
5. Attach tie rod, secure with C-clip.
6. Install left-hand header latch flex shaft (see Workshop Manual procedure 01.17.EF Flex Shaft - LH - Renew).
RH Fully Automatic Latching Kit - Renew
Removal
1. Remove right-hand header latch flex shaft (see Workshop Manual procedure 01.17.EG Flex Shaft - RH
- Renew).
2. Mark mounting position of latching kit (see Figure 1).
3. Remove 3 nuts and 1 screw securing latching kit to roof.
4. Remove C-clip securing tie ro d to roof hinge, release tie
rod (see Figure 2).
5. Remove latching kit from studs.
Installation
1. Ensure header motor and latc h are in fully open position
prior to installation.
Figure 2
Figure 3
Repair Operation Time (ROT)
ItemCode
Fully Automatic Latching Kit-Renew RH01.17.BP
Figure 1
Figure 2
Page 211 of 947
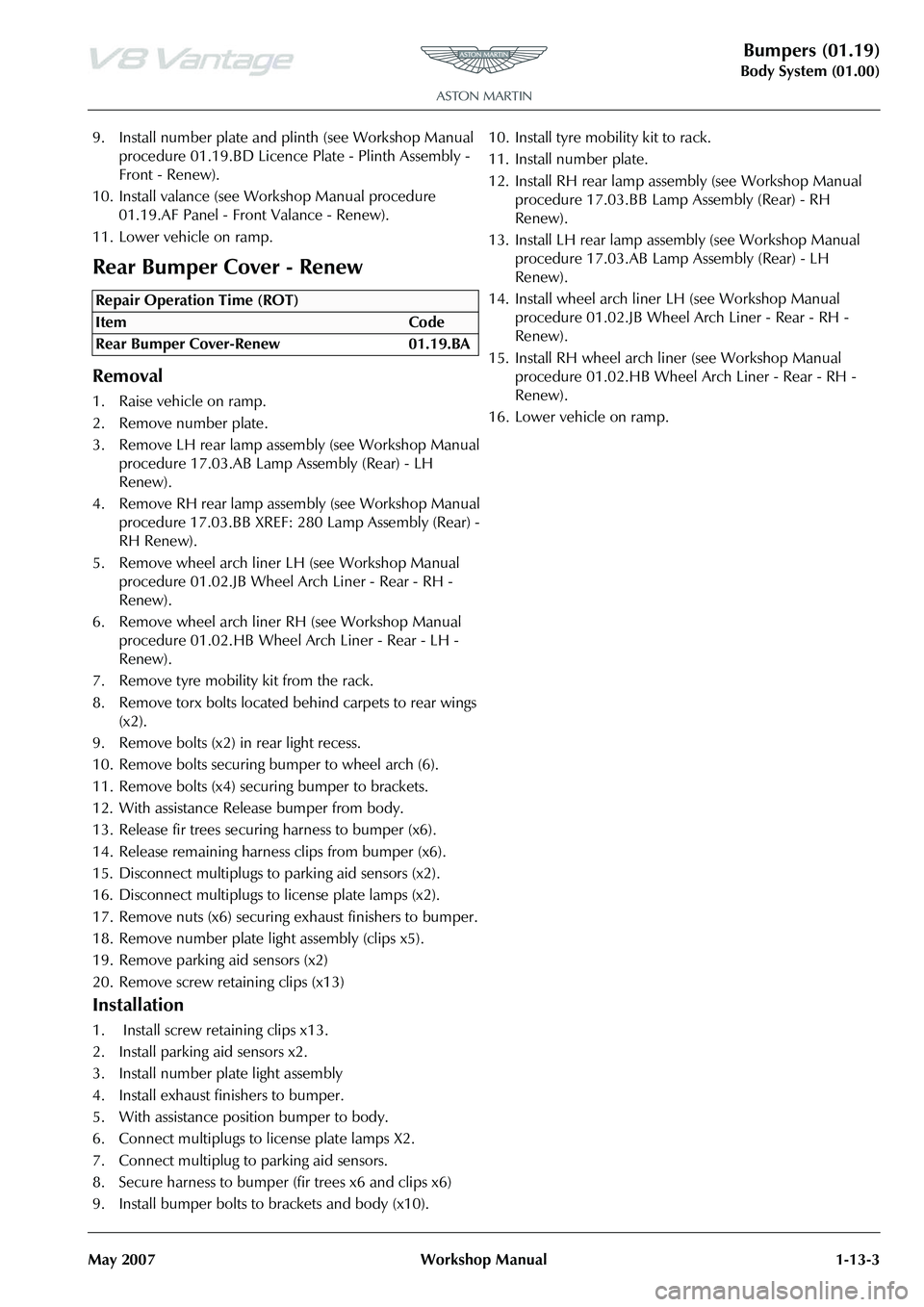
Bumpers (01.19)
Body System (01.00)
May 2007 Workshop Manual 1-13-3
9. Install number plate and plinth (see Workshop Manual procedure 01.19.BD Licence Plate - Plinth Assembly -
Front - Renew).
10. Install valance (see Workshop Manual procedure 01.19.AF Panel - Front Valance - Renew).
11. Lower vehicle on ramp.
Rear Bumper Cover - Renew
Removal
1. Raise vehicle on ramp.
2. Remove number plate.
3. Remove LH rear lamp assembly (see Workshop Manual procedure 17.03.AB Lamp Assembly (Rear) - LH
Renew).
4. Remove RH rear lamp assembly (see Workshop Manual procedure 17.03.BB XREF: 280 Lamp Assembly (Rear) -
RH Renew).
5. Remove wheel arch liner LH (see Workshop Manual procedure 01.02.JB Wheel Arch Liner - Rear - RH -
Renew).
6. Remove wheel arch liner RH (see Workshop Manual procedure 01.02.HB Wheel Arch Liner - Rear - LH -
Renew).
7. Remove tyre mobility kit from the rack.
8. Remove torx bolts located behind carpets to rear wings (x2).
9. Remove bolts (x2) in rear light recess.
10. Remove bolts securing bumper to wheel arch (6).
11. Remove bolts (x4) securing bumper to brackets.
12. With assistance Release bumper from body.
13. Release fir trees securing harness to bumper (x6).
14. Release remaining harness clips from bumper (x6).
15. Disconnect multiplugs to parking aid sensors (x2).
16. Disconnect multiplugs to license plate lamps (x2).
17. Remove nuts (x6) securing exhaust finishers to bumper.
18. Remove number plate light assembly (clips x5).
19. Remove parking aid sensors (x2)
20. Remove screw retaining clips (x13)
Installation
1. Install screw retaining clips x13.
2. Install parking aid sensors x2.
3. Install number pl ate light assembly
4. Install exhaust finishers to bumper.
5. With assistance position bumper to body.
6. Connect multiplugs to license plate lamps X2.
7. Connect multiplug to parking aid sensors.
8. Secure harness to bumper (f ir trees x6 and clips x6)
9. Install bumper bolts to brackets and body (x10). 10. Install tyre mobility kit to rack.
11. Install number plate.
12. Install RH rear lamp asse
mbly (see Workshop Manual
procedure 17.03.BB Lamp Assembly (Rear) - RH
Renew).
13. Install LH rear lamp assembly (see Workshop Manual procedure 17.03.AB Lamp Assembly (Rear) - LH
Renew).
14. Install wheel arch liner LH (see Workshop Manual procedure 01.02.JB Wheel Arch Liner - Rear - RH -
Renew).
15. Install RH wheel arch li ner (see Workshop Manual
procedure 01.02.HB Wheel Arch Liner - Rear - RH -
Renew).
16. Lower vehicle on ramp.
Repair Operation Time (ROT)
Page 214 of 947
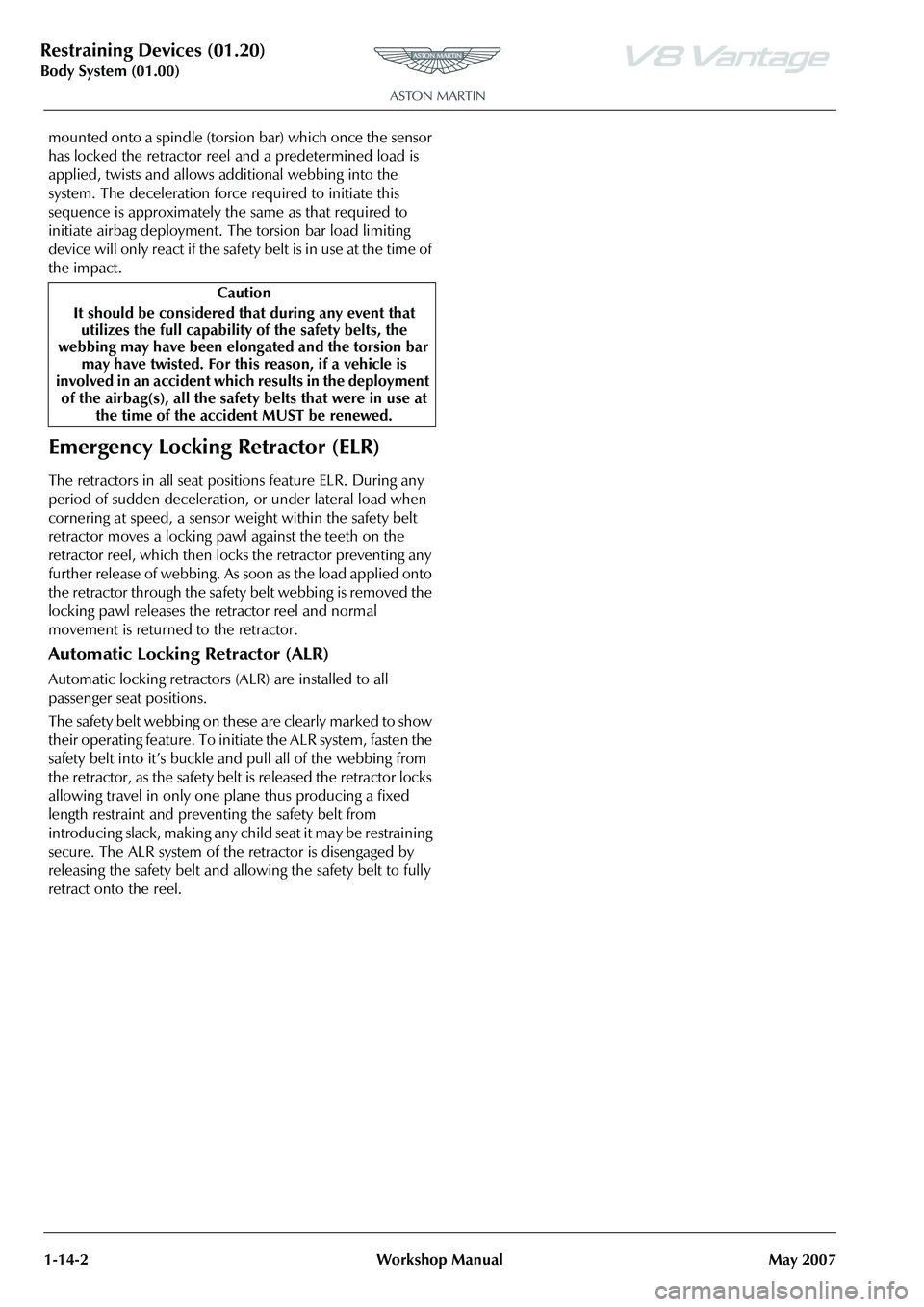
Restraining Devices (01.20)
Body System (01.00)1-14-2 Workshop Manual May 2007
mounted onto a spindle (torsion bar) which once the sensor
has locked the retractor reel and a predetermined load is
applied, twists and allows additional webbing into the
system. The deceleration force required to initiate this
sequence is approximately th e same as that required to
initiate airbag deployment. The torsion bar load limiting
device will only react if the safety belt is in use at the time of
the impact.
Emergency Locking Retractor (ELR)
The retractors in all seat posi tions feature ELR. During any
period of sudden deceleration, or under lateral load when
cornering at speed, a sensor weight within the safety belt
retractor moves a locking pawl against the teeth on the
retractor reel, which then locks the retractor preventing any
further release of webbing. As soon as the load applied onto
the retractor through the safety belt webbing is removed the
locking pawl releases the retractor reel and normal
movement is returned to the retractor.
Automatic Locking Retractor (ALR)
Automatic locking retractors (ALR) are installed to all
passenger seat positions.
The safety belt webbing on these are clearly marked to show
their operating feature. To initiate the ALR system, fasten the
safety belt into it’s buckle and pull all of the webbing from
the retractor, as the safety belt is released the retractor locks
allowing travel in only one plane thus producing a fixed
length restraint and preventing the safety belt from
introducing slack, making any child seat it may be restraining
secure. The ALR system of the retractor is disengaged by
releasing the safety belt and allowing the safety belt to fully
retract onto the reel. Caution
It should be considered th at during any event that
utilizes the full capability of the safety belts, the
webbing may have been elongated and the torsion bar may have twisted. For this reason, if a vehicle is
involved in an accident which results in the deployment of the airbag(s), all the safety belts that were in use at
the time of the accident MUST be renewed.
Page 215 of 947
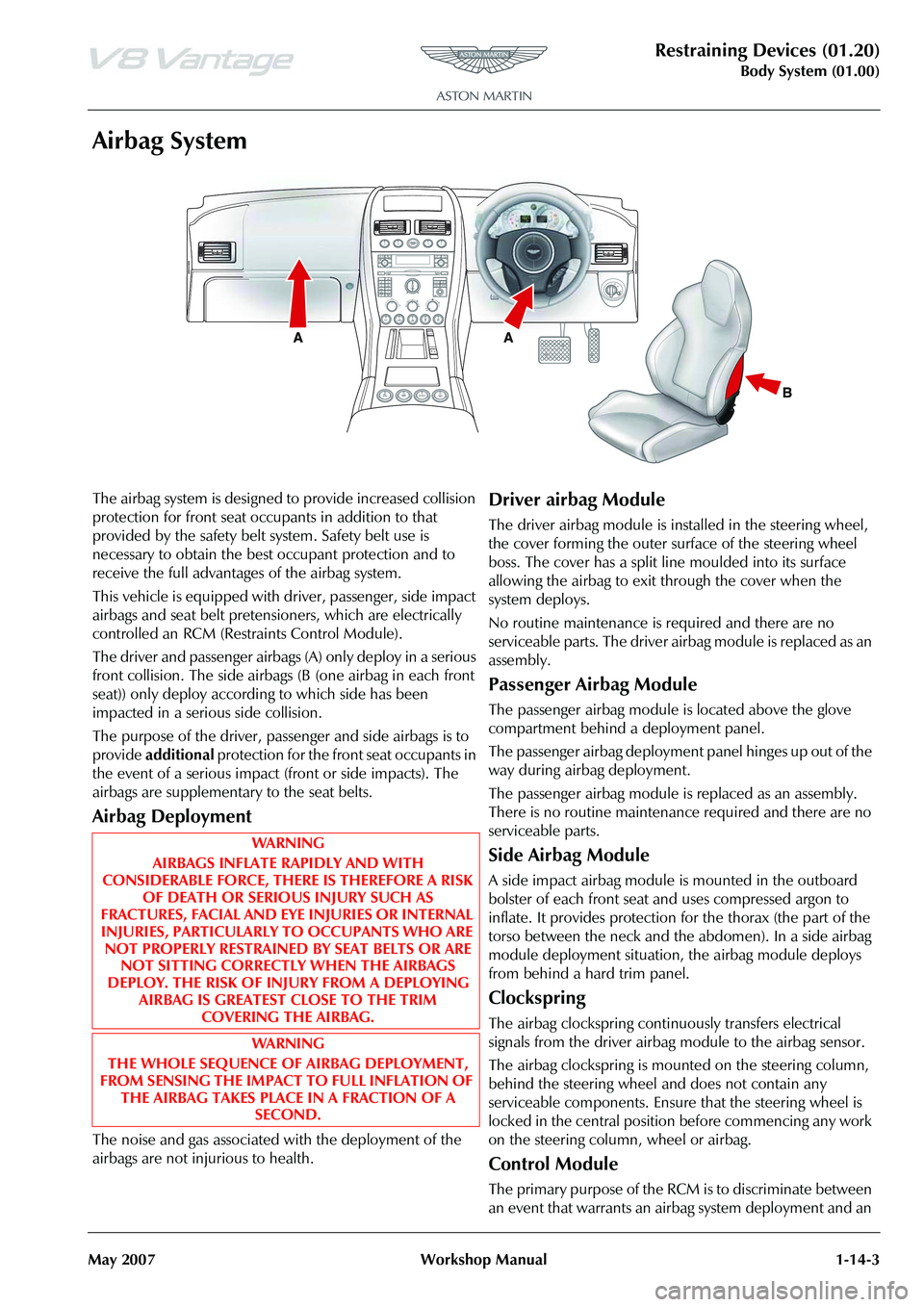
Restraining Devices (01.20)
Body System (01.00)
May 2007 Workshop Manual 1-14-3
Airbag System
The airbag system is designed to provide increased collision
protection for front seat occu pants in addition to that
provided by the safety belt system. Safety belt use is
necessary to obtain the best occupant protection and to
receive the full advantages of the airbag system.
This vehicle is equipped with dr iver, passenger, side impact
airbags and seat belt pretensioners, which are electrically
controlled an RCM (Restraints Control Module).
The driver and passenger airbags (A) only deploy in a serious
front collision. The side airbags (B (one airbag in each front
seat)) only deploy according to which side has been
impacted in a serious side collision.
The purpose of the driver, passenger and side airbags is to
provide additional protection for the front seat occupants in
the event of a serious impact (front or side impacts). The
airbags are supplementary to the seat belts.
Airbag Deployment
The noise and gas associated with the deployment of the
airbags are not injurious to health.
Driver airbag Module
The driver airbag module is installed in the steering wheel,
the cover forming the outer surface of the steering wheel
boss. The cover has a split line moulded into its surface
allowing the airbag to exit through the cover when the
system deploys.
No routine maintenance is required and there are no
serviceable parts. The driver airbag module is replaced as an
assembly.
Passenger Airbag Module
The passenger airbag module is located above the glove
compartment behind a deployment panel.
The passenger airbag deployment panel hinges up out of the
way during airbag deployment.
The passenger airbag module is replaced as an assembly.
There is no routine maintenance required and there are no
serviceable parts.
Side Airbag Module
A side impact airbag module is mounted in the outboard
bolster of each front seat and uses compressed argon to
inflate. It provides protection for the thorax (the part of the
torso between the neck and the abdomen). In a side airbag
module deployment situation, the airbag module deploys
from behind a hard trim panel.
Clockspring
The airbag clockspring continuously transfers electrical
signals from the driver airbag module to the airbag sensor.
The airbag clockspring is mounted on the steering column,
behind the steering wheel and does not contain any
serviceable components. Ensure that the steering wheel is
locked in the central position before commencing any work
on the steering column, wheel or airbag.
Control Module
The primary purpose of the RCM is to discriminate between
an event that warrants an airbag system deployment and an
R P
N
D
WAR NI N G
AIRBAGS INFLATE RAPIDLY AND WITH
CONSIDERABLE FORCE, THERE IS THEREFORE A RISK OF DEATH OR SERIOUS INJURY SUCH AS
FRACTURES, FACIAL AND EY E INJURIES OR INTERNAL
INJURIES, PARTICULARLY TO OCCUPANTS WHO ARE NOT PROPERLY RESTRAINED BY SEAT BELTS OR ARE NOT SITTING CORRECTLY WHEN THE AIRBAGS
DEPLOY. THE RISK OF IN JURY FROM A DEPLOYING
AIRBAG IS GREATEST CLOSE TO THE TRIM COVERING THE AIRBAG.
WAR NI N G
THE WHOLE SEQUENCE OF AIRBAG DEPLOYMENT,
FROM SENSING THE IMPACT TO FULL INFLATION OF THE AIRBAG TAKES PLACE IN A FRACTION OF A SECOND.
Page 216 of 947
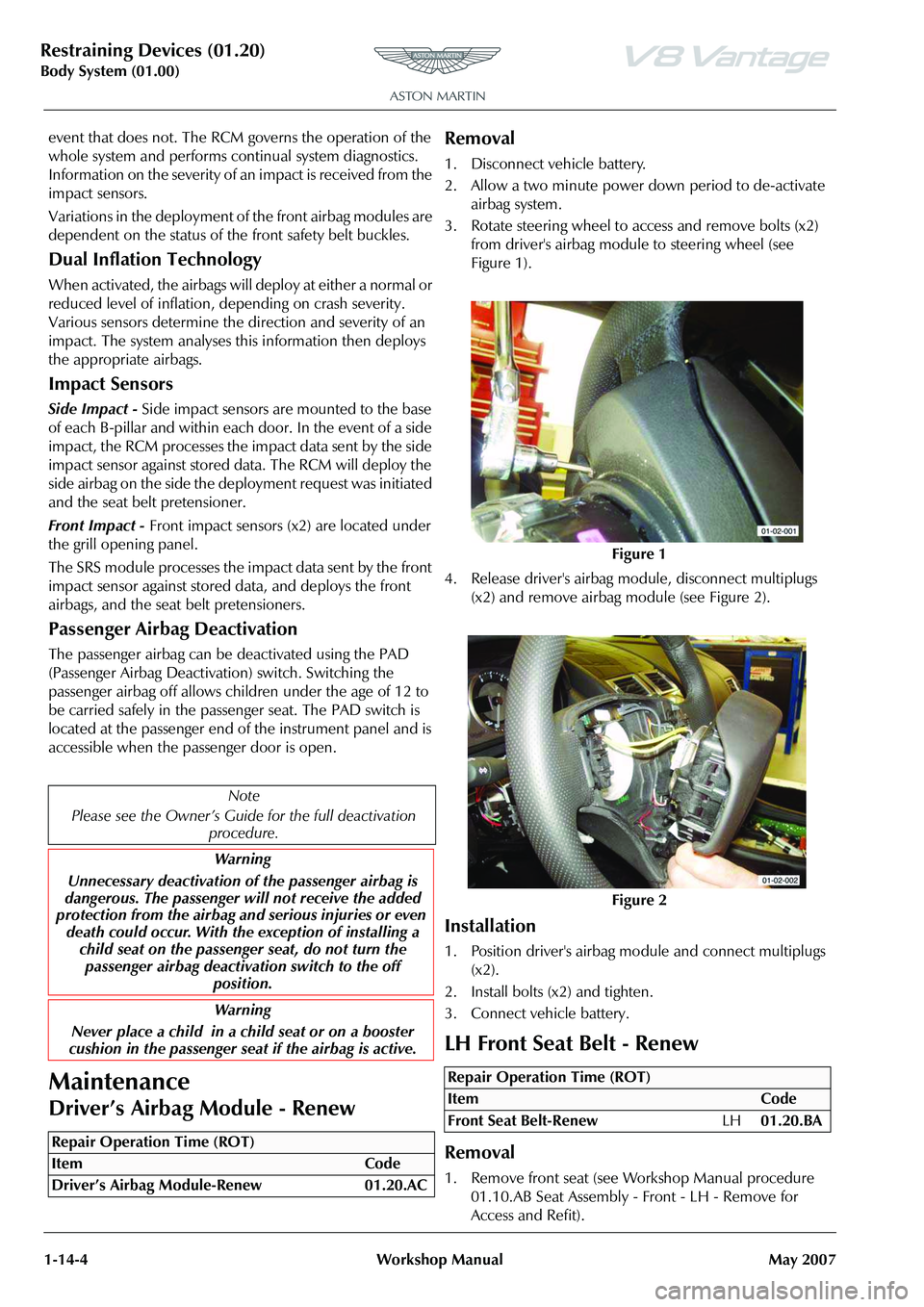
Restraining Devices (01.20)
Body System (01.00)1-14-4 Workshop Manual May 2007
event that does not. The RCM governs the operation of the
whole system and performs continual system diagnostics.
Information on the severity of an impact is received from the
impact sensors.
Variations in the deployment of the front airbag modules are
dependent on the status of the front safety belt buckles.
Dual Inflation Technology
When activated, the airbags will deploy at either a normal or
reduced level of inflation, depending on crash severity.
Various sensors determine the direction and severity of an
impact. The system analyses this information then deploys
the appropriate airbags.
Impact Sensors
Side Impact - Side impact sensors are mounted to the base
of each B-pillar and within each door. In the event of a side
impact, the RCM processes the impact data sent by the side
impact sensor against stored data. The RCM will deploy the
side airbag on the side the deployment request was initiated
and the seat belt pretensioner.
Front Impact - Front impact sensors (x2) are located under
the grill opening panel.
The SRS module processes the impact data sent by the front
impact sensor against stored data, and deploys the front
airbags, and the seat belt pretensioners.
Passenger Airbag Deactivation
The passenger airbag can be deactivated using the PAD
(Passenger Airbag Deactivation) switch. Switching the
passenger airbag off allows children under the age of 12 to
be carried safely in the passenger seat. The PAD switch is
located at the passenger end of the instrument panel and is
accessible when the pa ssenger door is open.
Maintenance
Driver’s Airbag Module - Renew
Removal
1. Disconnect vehicle battery.
2. Allow a two minute power down period to de-activate
airbag system.
3. Rotate steering wheel to access and remove bolts (x2) from driver's airbag module to steering wheel (see
Figure 1).
4. Release driver's airbag mo dule, disconnect multiplugs
(x2) and remove airbag module (see Figure 2).
Installation
1. Position driver's airbag mo dule and connect multiplugs
(x2).
2. Install bolts (x2) and tighten.
3. Connect vehicle battery.
LH Front Seat Belt - Renew
Removal
1. Remove front seat (see Workshop Manual procedure 01.10.AB Seat Assembly - Front - LH - Remove for
Access and Refit).
Note
Please see the Owner’s Guid e for the full deactivation
procedure.
Warning
Unnecessary deactivation of the passenger airbag is
dangerous. The passenger will not receive the added
protection from the airbag and serious injuries or even
death could occur. With the exception of installing a child seat on the passenge r seat, do not turn the
passenger airbag deactiva tion switch to the off
position.
Warning
Never place a child in a child seat or on a booster
cushion in the passenger seat if the airbag is active.
Repair Operation Time (ROT)
Figure 1
Figure 2
Repair Operation Time (ROT)
ItemCode
Front Seat Belt-Renew LH01.20.BA
Page 218 of 947
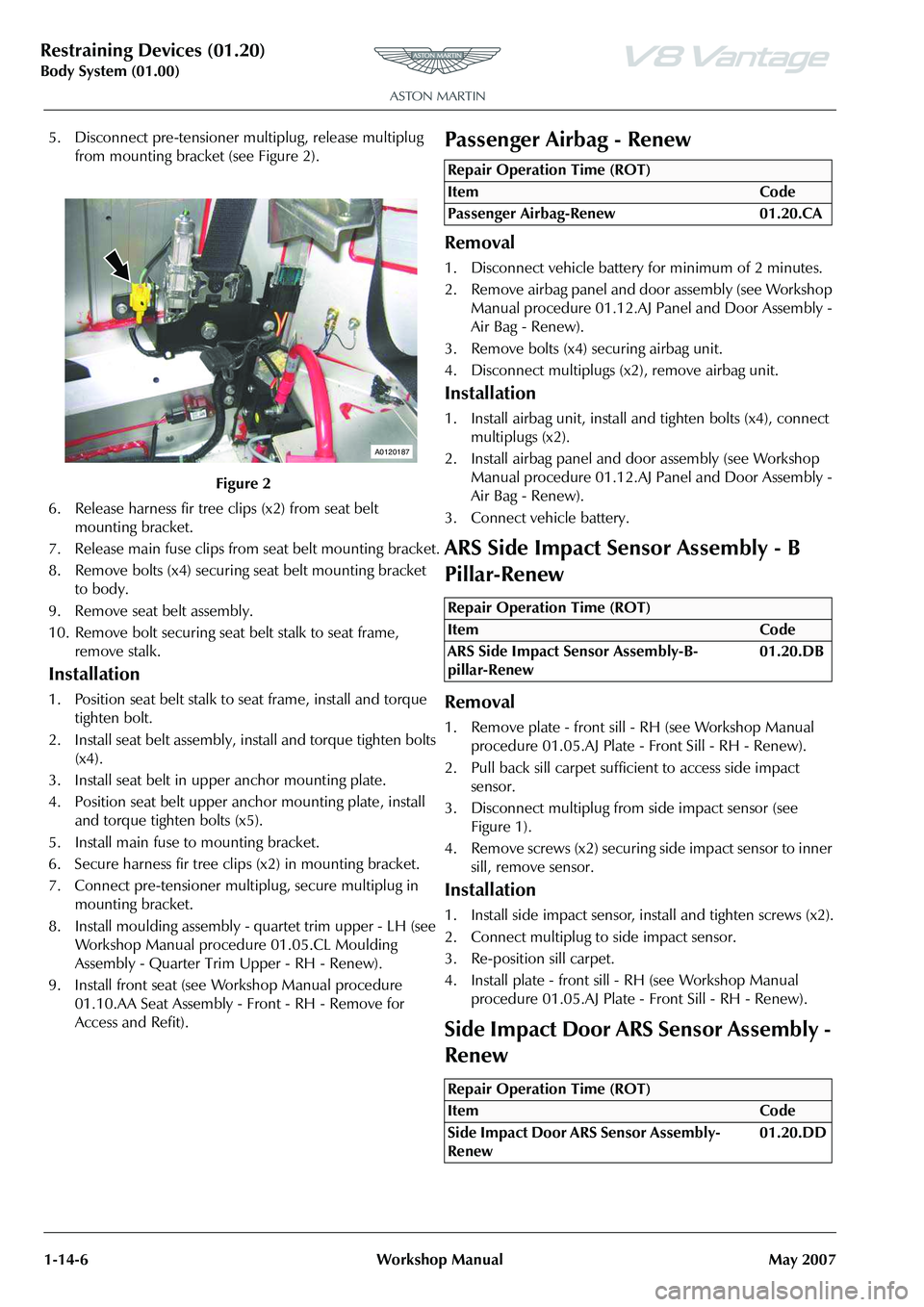
Restraining Devices (01.20)
Body System (01.00)1-14-6 Workshop Manual May 2007
5. Disconnect pre-tensioner mu ltiplug, release multiplug
from mounting bracket (see Figure 2).
6. Release harness fir tree clips (x2) from seat belt mounting bracket.
7. Release main fuse clips from seat belt mounting bracket.
8. Remove bolts (x4) securing seat belt mounting bracket to body.
9. Remove seat belt assembly.
10. Remove bolt securing seat belt stalk to seat frame, remove stalk.
Installation
1. Position seat belt stalk to seat frame, install and torque tighten bolt.
2. Install seat belt assembly, in stall and torque tighten bolts
(x4).
3. Install seat belt in upper anchor mounting plate.
4. Position seat belt upper anchor mounting plate, install and torque tighten bolts (x5).
5. Install main fuse to mounting bracket.
6. Secure harness fir tree clips (x2) in mounting bracket.
7. Connect pre-tensioner multip lug, secure multiplug in
mounting bracket.
8. Install moulding assembly - quartet trim upper - LH (see Workshop Manual procedure 01.05.CL Moulding
Assembly - Quarter Trim Upper - RH - Renew).
9. Install front seat (see Workshop Manual procedure 01.10.AA Seat Assembly - Front - RH - Remove for
Access and Refit).
Passenger Airbag - Renew
Removal
1. Disconnect vehicle battery for minimum of 2 minutes.
2. Remove airbag panel and door assembly (see Workshop Manual procedure 01.12.AJ Panel and Door Assembly -
Air Bag - Renew).
3. Remove bolts (x4) securing airbag unit.
4. Disconnect multiplugs (x2), remove airbag unit.
Installation
1. Install airbag unit, install and tighten bolts (x4), connect multiplugs (x2).
2. Install airbag panel and d oor assembly (see Workshop
Manual procedure 01.12.AJ Panel and Door Assembly -
Air Bag - Renew).
3. Connect vehicle battery.
ARS Side Impact Sensor Assembly - B
Pillar-Renew
Removal
1. Remove plate - front sill - RH (see Workshop Manual procedure 01.05.AJ Plate - Front Sill - RH - Renew).
2. Pull back sill carpet sufficient to access side impact sensor.
3. Disconnect multiplug from side impact sensor (see Figure 1).
4. Remove screws (x2) securing side impact sensor to inner
sill, remove sensor.
Installation
1. Install side impact sensor, install and tighten screws (x2).
2. Connect multiplug to side impact sensor.
3. Re-position sill carpet.
4. Install plate - front sill - RH (see Workshop Manual procedure 01.05.AJ Plate - Front Sill - RH - Renew).
Side Impact Door ARS Sensor Assembly -
Renew
Figure 2
A0120187
Repair Operation Time (ROT)
ItemCode
Passenger Airbag -Renew 01.20.CA
Repair Operation Time (ROT)
ItemCode
ARS Side Impact Sensor Assembly-B-
pillar-Renew 01.20.DB
Repair Operation Time (ROT)
ItemCode
Side Impact Door ARS Sensor Assembly-
Renew 01.20.DD
Page 219 of 947
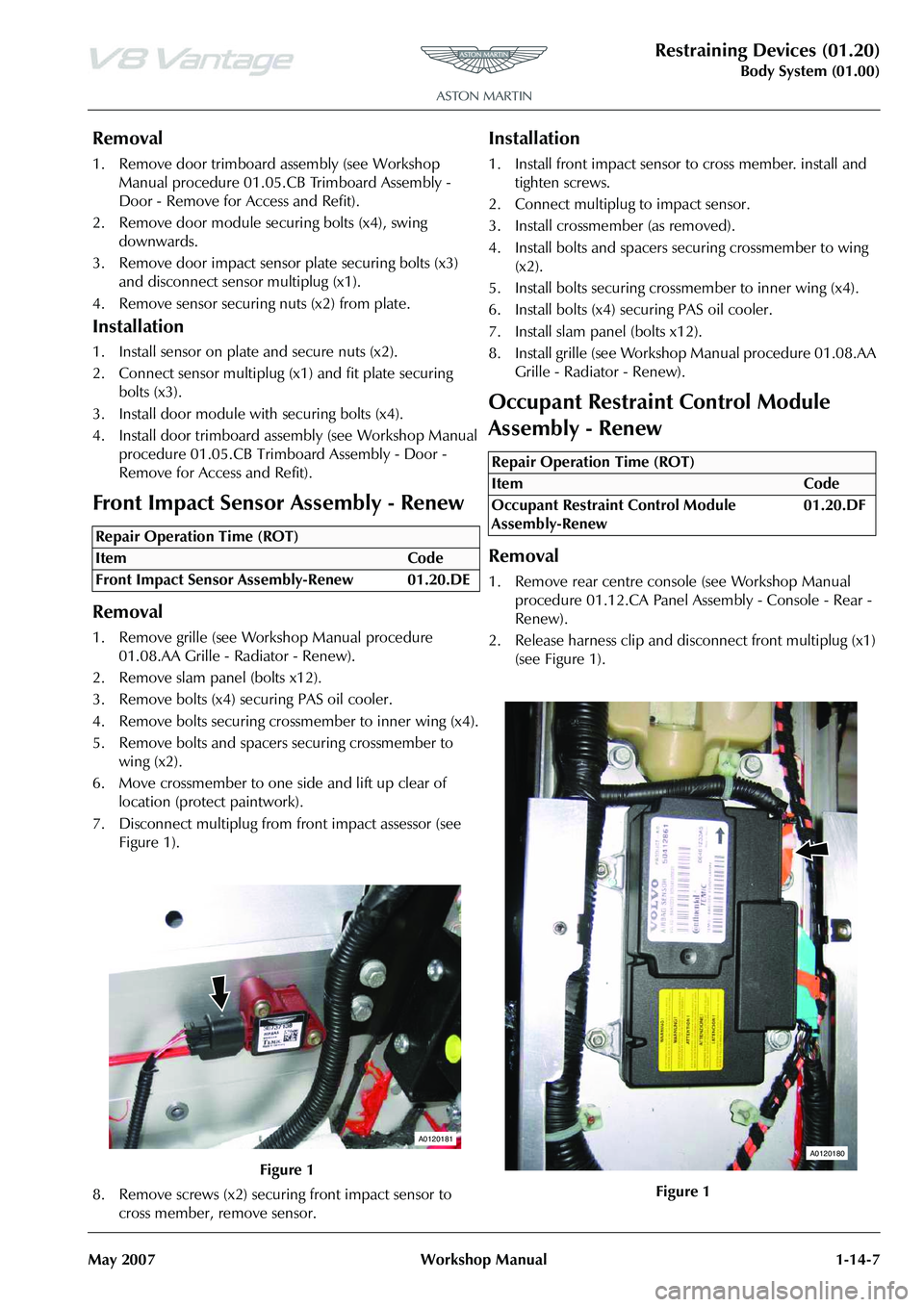
Restraining Devices (01.20)
Body System (01.00)
May 2007 Workshop Manual 1-14-7
Removal
1. Remove door trimboard assembly (see Workshop Manual procedure 01.05.CB Trimboard Assembly -
Door - Remove for Access and Refit).
2. Remove door module securing bolts (x4), swing downwards.
3. Remove door impact sensor plate securing bolts (x3) and disconnect sensor multiplug (x1).
4. Remove sensor securing nuts (x2) from plate.
Installation
1. Install sensor on plate and secure nuts (x2).
2. Connect sensor multiplug (x1) and fit plate securing bolts (x3).
3. Install door module wi th securing bolts (x4).
4. Install door trimboard asse mbly (see Workshop Manual
procedure 01.05.CB Trimboard Assembly - Door -
Remove for Access and Refit).
Front Impact Sensor Assembly - Renew
Removal
1. Remove grille (see Workshop Manual procedure 01.08.AA Grille - Radiator - Renew).
2. Remove slam panel (bolts x12).
3. Remove bolts (x4) securing PAS oil cooler.
4. Remove bolts securing crossmember to inner wing (x4).
5. Remove bolts and spacers securing crossmember to wing (x2).
6. Move crossmember to one side and lift up clear of location (protect paintwork).
7. Disconnect multiplug from front impact assessor (see
Figure 1).
8. Remove screws (x2) securi ng front impact sensor to
cross member, remove sensor.
Installation
1. Install front impact sensor to cross member. install and tighten screws.
2. Connect multiplug to impact sensor.
3. Install crossmember (as removed).
4. Install bolts and spacers securing crossmember to wing (x2).
5. Install bolts securing cros smember to inner wing (x4).
6. Install bolts (x4) securing PAS oil cooler.
7. Install slam panel (bolts x12).
8. Install grille (see Workshop Manual procedure 01.08.AA
Grille - Radiator - Renew).
Occupant Restraint Control Module
Assembly - Renew
Removal
1. Remove rear centre console (see Workshop Manual procedure 01.12.CA Panel Assembly - Console - Rear -
Renew).
2. Release harness clip and disconnect front multiplug (x1) (see Figure 1).
Repair Operation Time (ROT)
A0120181
Repair Operation Time (ROT)
A0120180
Page 224 of 947
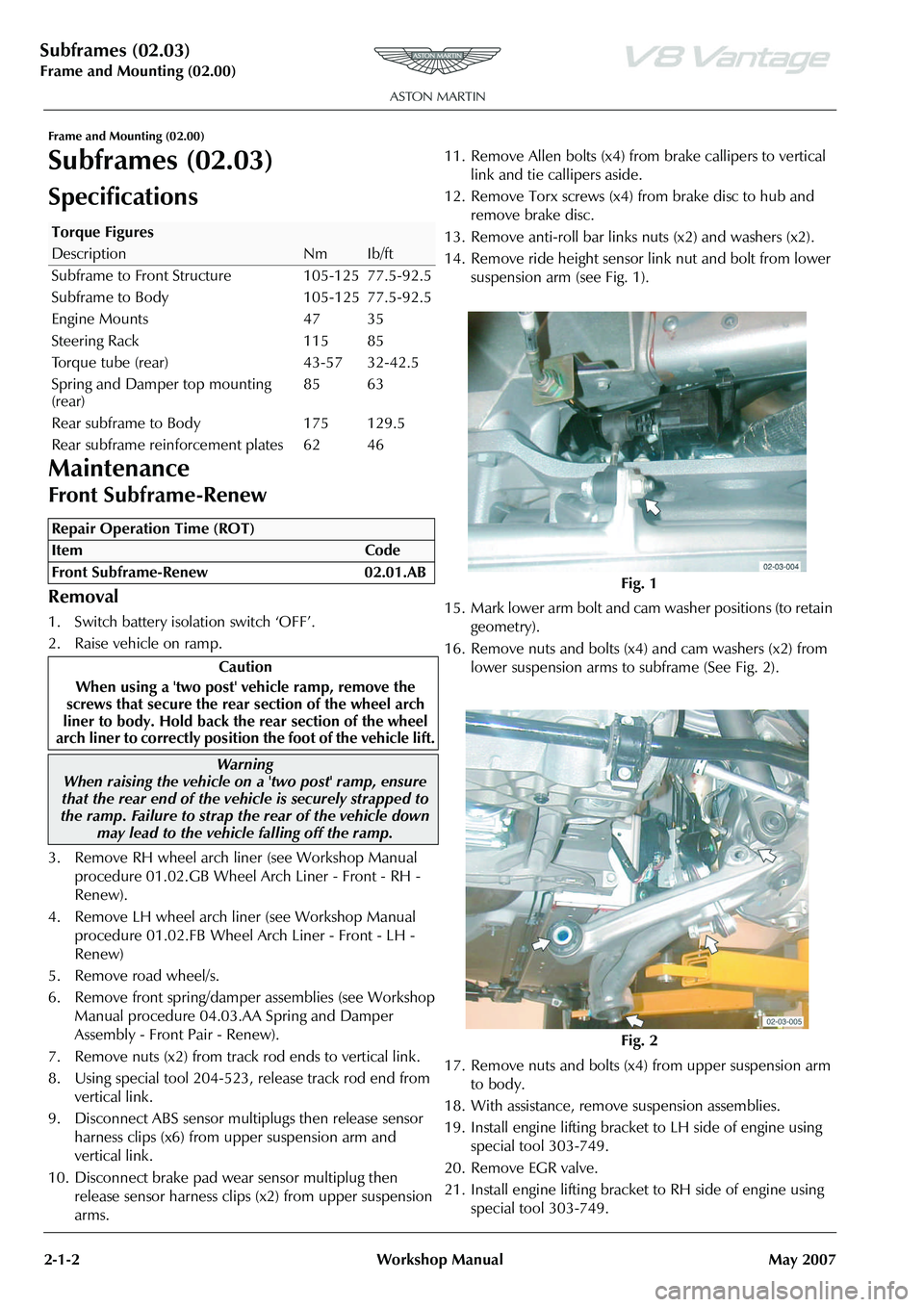
Subframes (02.03)
Frame and Mounting (02.00)
2-1-2 Workshop Manual May 2007
Frame and Mounting (02.00)
Subframes (02.03)
Specifications
Maintenance
Front Subframe-Renew
Removal
1. Switch battery isolation switch ‘OFF’.
2. Raise vehicle on ramp.
3. Remove RH wheel arch liner (see Workshop Manual procedure 01.02.GB Wheel Arch Liner - Front - RH -
Renew).
4. Remove LH wheel arch liner (see Workshop Manual procedure 01.02.FB Wheel Arch Liner - Front - LH -
Renew)
5. Remove road wheel/s.
6. Remove front spring/damper assemblies (see Workshop Manual procedure 04.03.AA Spring and Damper
Assembly - Front Pair - Renew).
7. Remove nuts (x2) from track rod ends to vertical link.
8. Using special tool 204-523, release track rod end from vertical link.
9. Disconnect ABS sensor multiplugs then release sensor harness clips (x6) from upper suspension arm and
vertical link.
10. Disconnect brake pad wear sensor multiplug then release sensor harness clips (x2) from upper suspension
arms. 11. Remove Allen bolts (x4) from brake callipers to vertical
link and tie callipers aside.
12. Remove Torx screws (x4) from brake disc to hub and remove brake disc.
13. Remove anti-roll bar links nuts (x2) and washers (x2).
14. Remove ride height sensor link nut and bolt from lower
suspension arm (see Fig. 1).
15. Mark lower arm bolt and cam washer positions (to retain
geometry).
16. Remove nuts and bolts (x4) and cam washers (x2) from lower suspension arms to subframe (See Fig. 2).
17. Remove nuts and bolts (x4) from upper suspension arm to body.
18. With assistance, remove suspension assemblies.
19. Install engine lifting bracket to LH side of engine using special tool 303-749.
20. Remove EGR valve.
21. Install engine lifting bracket to RH side of engine using special tool 303-749.
Torque Figures
DescriptionNmIb/ft
Subframe to Front Structure 105-125 77.5-92.5
Subframe to Body 105-125 77.5-92.5
Engine Mounts 47 35
Steering Rack 115 85
Torque tube (rear) 43-57 32-42.5
Spring and Damper top mounting
(rear) 85 63
Rear subframe to Body 175 129.5
Rear subframe reinforcement plates 62 46
Repair Operation Time (ROT)
Warning
When raising the vehicle on a 'two post' ramp, ensure
that the rear end of the vehi cle is securely strapped to
the ramp. Failure to strap th e rear of the vehicle down
may lead to the vehicl e falling off the ramp.
Fig. 1
Fig. 2