steering wheel ASTON MARTIN V8 VANTAGE 2010 Owner's Manual
[x] Cancel search | Manufacturer: ASTON MARTIN, Model Year: 2010, Model line: V8 VANTAGE, Model: ASTON MARTIN V8 VANTAGE 2010Pages: 947, PDF Size: 43.21 MB
Page 507 of 947
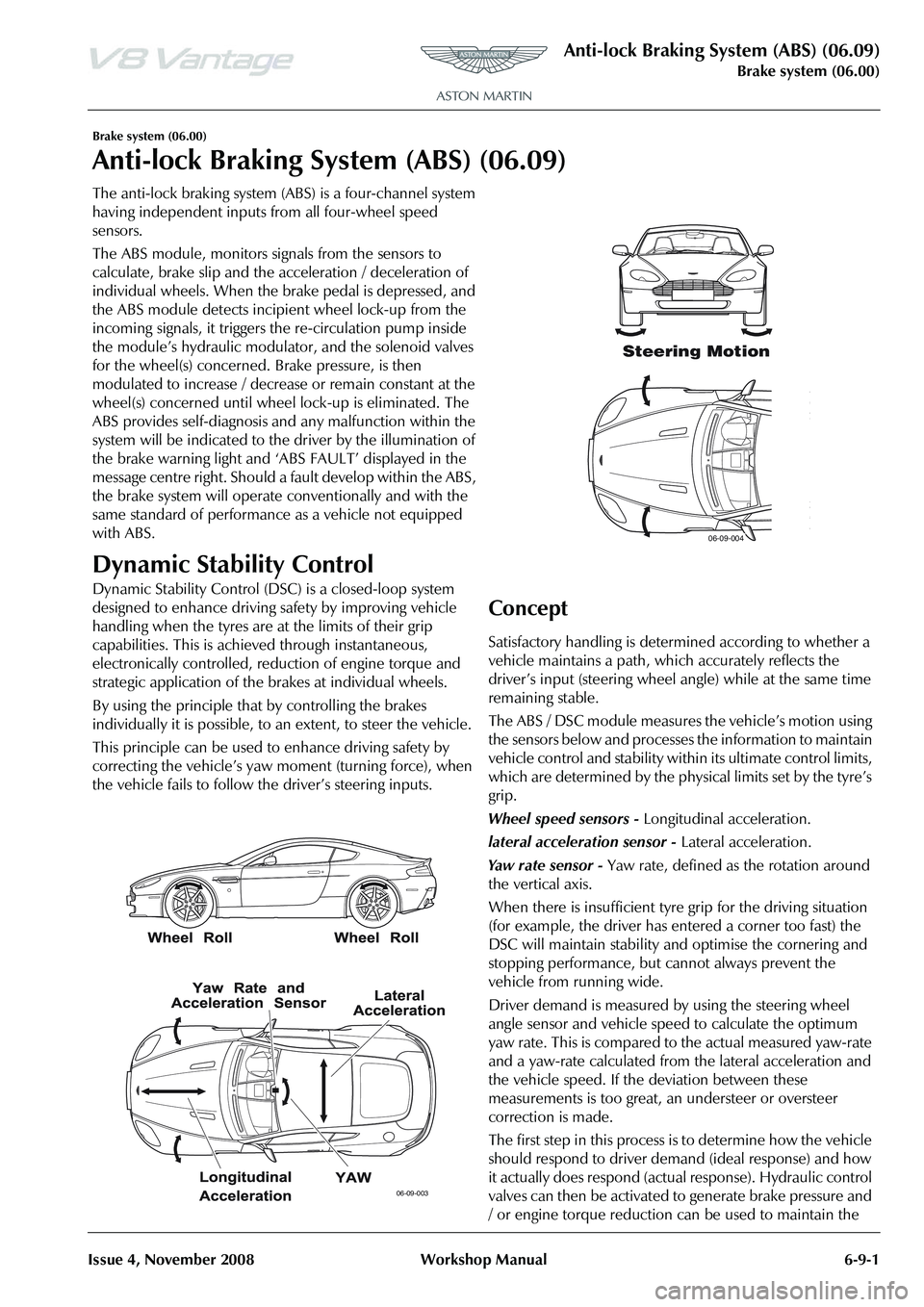
Anti-lock Braking System (ABS) (06.09)
Brake system (06.00)
Issue 4, November 2008 Workshop Manual 6-9-1
Brake system (06.00)
Anti-lock Braking System (ABS) (06.09)
The anti-lock braking system (ABS) is a four-channel system
having independent inputs from all four-wheel speed
sensors.
The ABS module, monitors signals from the sensors to
calculate, brake slip and the acceleration / deceleration of
individual wheels. When the brake pedal is depressed, and
the ABS module detects incipient wheel lock-up from the
incoming signals, it triggers the re-circulation pump inside
the module’s hydraulic modulator, and the solenoid valves
for the wheel(s) concerned. Brake pressure, is then
modulated to increase / decrease or remain constant at the
wheel(s) concerned until whee l lock-up is eliminated. The
ABS provides self-diagnosis and any malfunction within the
system will be indicated to the dr iver by the illumination of
the brake warning light and ‘ABS FAULT’ displayed in the
message centre right. Should a fault develop within the ABS,
the brake system will operate conventionally and with the
same standard of performanc e as a vehicle not equipped
with ABS.
Dynamic Stability Control
Dynamic Stability Control (DSC ) is a closed-loop system
designed to enhance driving safety by improving vehicle
handling when the tyres are at the limits of their grip
capabilities. This is achieved through instantaneous,
electronically controlled, reduction of engine torque and
strategic application of the brakes at individual wheels.
By using the principle that by controlling the brakes
individually it is possible, to an extent, to steer the vehicle.
This principle can be used to enhance driving safety by
correcting the vehicle’s yaw moment (turning force), when
the vehicle fails to follow th e driver’s steering inputs.
Concept
Satisfactory handling is determined according to whether a
vehicle maintains a path, wh ich accurately reflects the
driver
Page 508 of 947
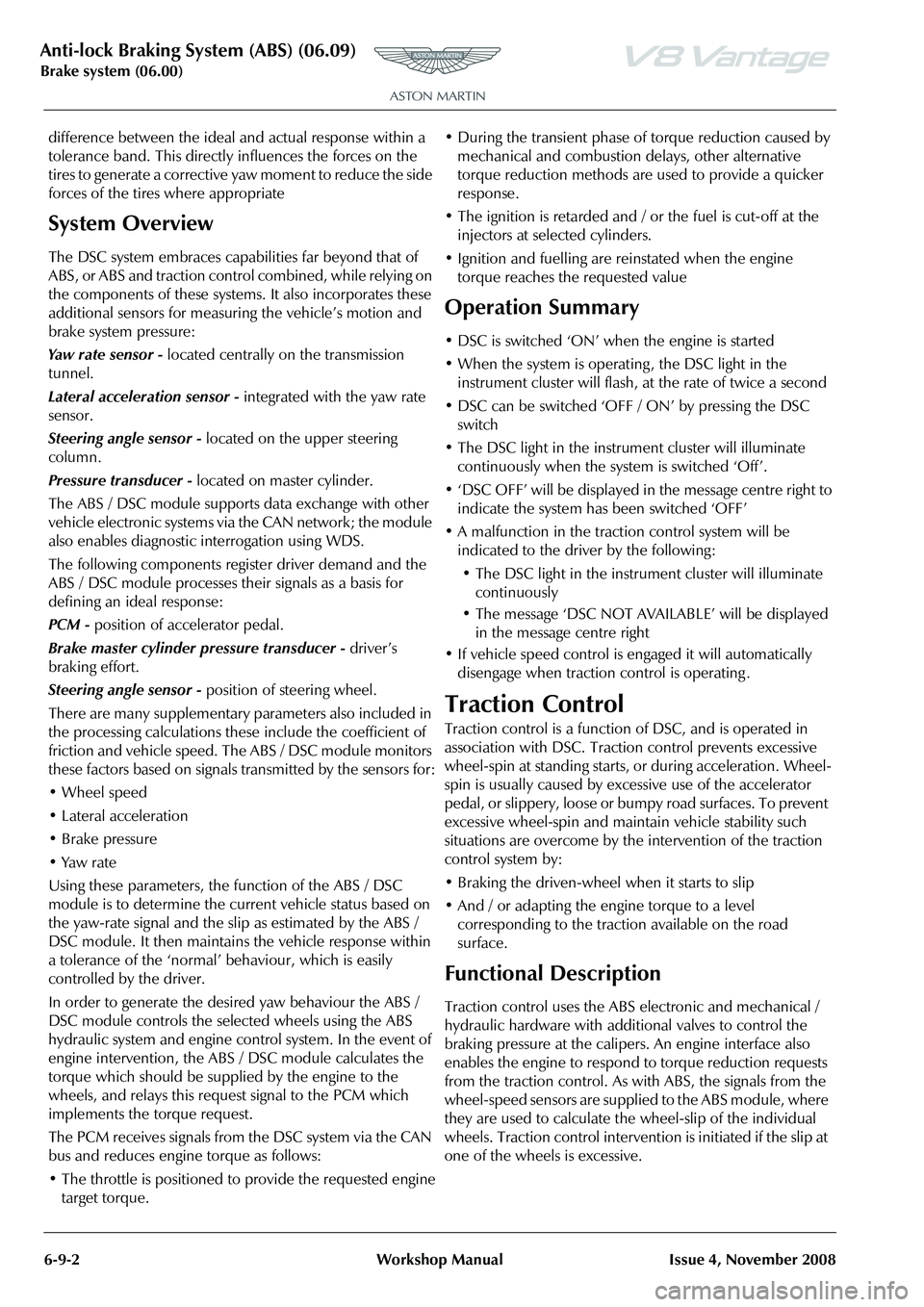
Anti-lock Braking System (ABS) (06.09)
Brake system (06.00)
6-9-2 Workshop Manual Issue 4, November 2008
difference between the ideal and actual response within a
tolerance band. This directly influences the forces on the
tires to generate a corrective yaw moment to reduce the side
forces of the tires where appropriate
System Overview
The DSC system embraces capabilities far beyond that of
ABS, or ABS and traction control combined, while relying on
the components of these systems. It also incorporates these
additional sensors for measur ing the vehicle’s motion and
brake system pressure:
Ya w r a t e s e n s o r - located centrally on the transmission
tunnel.
Lateral acceleration sensor - integrated with the yaw rate
sensor.
Steering angle sensor - located on the upper steering
column.
Pressure transducer - located on master cylinder.
The ABS / DSC module supports data exchange with other
vehicle electronic systems via the CAN network; the module
also enables diagnostic interrogation using WDS.
The following components register driver demand and the
ABS / DSC module processes their signals as a basis for
defining an ideal response:
PCM - position of accelerator pedal.
Brake master cylinder pressure transducer - driver’s
braking effort.
Steering angle sensor - position of steering wheel.
There are many supplementary parameters also included in
the processing calculations these include the coefficient of
friction and vehicle speed. The ABS / DSC module monitors
these factors based on signals transmitted by the sensors for:
• Wheel speed
• Lateral acceleration
• Brake pressure
• Yaw rate
Using these parameters, the function of the ABS / DSC
module is to determine the current vehicle status based on
the yaw-rate signal and the slip as estimated by the ABS /
DSC module. It then maintains the vehicle response within
a tolerance of the ‘normal’ behaviour, which is easily
controlled by the driver.
In order to generate the desired yaw behaviour the ABS /
DSC module controls the selected wheels using the ABS
hydraulic system and engine control system. In the event of
engine intervention, the ABS / DSC module calculates the
torque which should be supplied by the engine to the
wheels, and relays this request signal to the PCM which
implements the torque request.
The PCM receives signals from the DSC system via the CAN
bus and reduces engine torque as follows:
• The throttle is positioned to provide the requested engine target torque. • During the transient phase of torque reduction caused by
mechanical and combustion delays, other alternative
torque reduction methods are used to provide a quicker
response.
• The ignition is retarded and / or the fuel is cut-off at the injectors at selected cylinders.
• Ignition and fuelling are reinstated when the engine torque reaches the requested value
Operation Summary
• DSC is switched ‘ON’ when the engine is started
• When the system is operating , the DSC light in the instrument cluster will flash, at the rate of twice a second
• DSC can be switched ‘OFF / ON’ by pressing the DSC switch
• The DSC light in the instru ment cluster will illuminate
continuously when the system is switched ‘Off’.
• ‘DSC OFF’ will be displayed in the message centre right to indicate the system has been switched ‘OFF’
• A malfunction in the traction control system will be indicated to the driver by the following:
• The DSC light in the instru ment cluster will illuminate
continuously
• The message ‘DSC NOT AVAILABLE’ will be displayed in the message centre right
• If vehicle speed control is engaged it will automatically disengage when traction control is operating .
Traction Control
Traction control is a function of DSC, and is operated in
association with DSC. Traction control prevents excessive
wheel-spin at standing starts, or during acceleration. Wheel-
spin is usually caused by ex cessive use of the accelerator
pedal, or slippery, loose or bumpy road surfaces. To prevent
excessive wheel-spin and mainta in vehicle stability such
situations are overcome by the intervention of the traction
control system by:
• Braking the driven-wheel when it starts to slip
• And / or adapting the engine torque to a level corresponding to the traction available on the road
surface.
Functional Description
Traction control uses the ABS electronic and mechanical /
hydraulic hardware with additional valves to control the
braking pressure at the calipe rs. An engine interface also
enables the engine to respond to torque reduction requests
from the traction control. As with ABS, the signals from the
wheel-speed sensors are supplied to the ABS module, where
they are used to calculate the wheel-slip of the individual
wheels. Traction control intervention is initiated if the slip at
one of the wheels is excessive.
Page 509 of 947
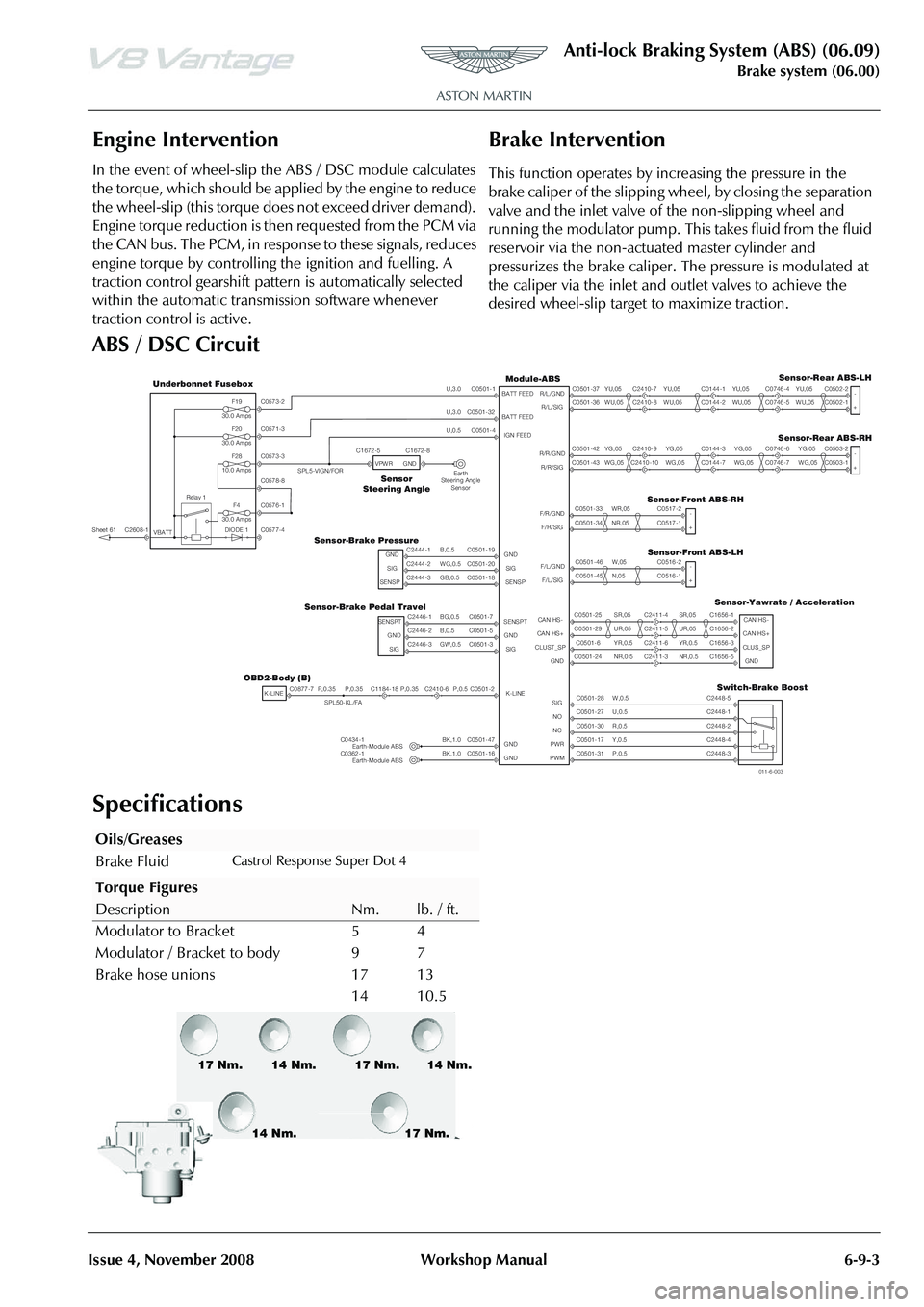
Anti-lock Braking System (ABS) (06.09)
Brake system (06.00)
Issue 4, November 2008 Workshop Manual 6-9-3
Engine Intervention
In the event of wheel-slip the ABS / DSC module calculates
the torque, which should be applied by the engine to reduce
the wheel-slip (this torque does not exceed driver demand).
Engine torque reduction is then requested from the PCM via
the CAN bus. The PCM, in response to these signals, reduces
engine torque by controlling the ignition and fuelling. A
traction control gearshift pattern is automatically selected
within the automatic transmission software whenever
traction control is active.
Brake Intervention
This function operates by increasing the pressure in the
brake caliper of the slipping wheel, by closing the separation
valve and the inlet valve of the non-slipping wheel and
running the modulator pump. This takes fluid from the fluid
reservoir via the non-actuated master cylinder and
pressurizes the brake caliper. The pressure is modulated at
the caliper via the inlet and outlet valves to achieve the
desired wheel-slip target to maximize traction.
ABS / DSC Circuit
Specifications
SR,05UR,05YR,0.5NR,0.5
WR,05NR,05
YG,05WG,05
YU,05WU,05
W,05N,05
W,0.5U,0.5R,0.5
P,0.5Y,0.5
B,0.5WG,0.5GB,0.5
B,0.5BG,0.5
GW,0.5
P,0.5
U,0.5
U,3.0
BK,1.0BK,1.0
P,0.35P,0.35P,0.35 U,3.0
WG,05YG,05
WU,05
SR,05UR,05YR,0.5NR,0.5
WG,05YG,05
WU,05
WG,05YG,05
WU,05YU,05YU,05YU,05Module-ABS
OBD2-Body (B)
Earth-Module ABSEarth-Module ABS
C1184-18C2410-6
Sensor-Brake Pressure
Sensor-Brake Pedal Travel
Sensor-Rear ABS-LH
C0746-7C0746-6
C0746-5
Switch-Brake Boost
Sensor-Yawrate / Acceleration
C2411-6C2411-5C2411-4
C2411-3
C0144-7C0144-3
C0144-2
Sensor-Front ABS-LH
Sensor-Front ABS-RH
C2410-10C2410-9
C2410-8
Sensor-Rear ABS-RH
C0746-4C0144-1C2410-7
C0877-7
K-LINESPL50-KL/FA
C0362-1C0434-1
C2444-2
SIGC2444-1
GND
C2444-3
SENSP
C2446-2
GNDC2446-1
SENSPT
C2446-3
SIG
C0501-47
GNDC0501-16
GND
C0501-2K-LINE
C0501-24
GND
C0501-31
PWM
C0501-30
NC
C0501-25
CAN HS-
C0501-28
SIGC0501-27
NO
C0501-29
CAN HS+C0501-6
CLUST_SP
C0501-17
PWR
C0501-5
GND
C0501-32BATT FEED
C0501-7
SENSPT
C0501-3 SIG
C0501-20 SIGC0501-19
GND
C0501-18 SENSP
C0501-4IGN FEED
C0501-46
F/L/GNDC0501-45
F/L/SIG
C0501-42
R/R/GNDC0501-43
R/R/SIG
C0501-36
R/L/SIG
C0501-34
F/R/SIGC0501-33
F/R/GND
C0501-1
BATT FEEDC0501-37
R/L/GND
C2448-5
C2448-3
C2448-2C2448-1
C2448-4
C1656-3 CLUS_SPC1656-2
CAN HS+C1656-1 CAN HS-
C1656-5
GND
C0516-2-C0516-1+
C0517-2
-C0517-1+
C0502-1
+
C0503-2 -C0503-1+
C0502-2 -
Sensor
Steering Angle
Sheet 61
F4
30.0 AmpsRelay 1
Underbonnet Fusebox
DIODE 1
F28
10.0 Amps
F20
30.0 Amps
F19
30.0 Amps
Earth
Steering Angle
Sensor
C0576-1
C0577-4C2608-1 VBATT
C0573-2
C0571-3
C0573-3
C0578-8SPL5-VIGN/FOR
C1672-5
VPWRC1672-8
GND
011-6-003
Oils/Greases
Brake FluidCastrol Response Super Dot 4
Torque Figures
DescriptionNm.lb. / ft.
Modulator to Bracket 5 4
Modulator / Bracket to body 9 7
Brake hose unions 17 1413
10.5
17 Nm. 17 Nm.
17 Nm.
14 Nm.
14 Nm. 14 Nm.
Page 600 of 947
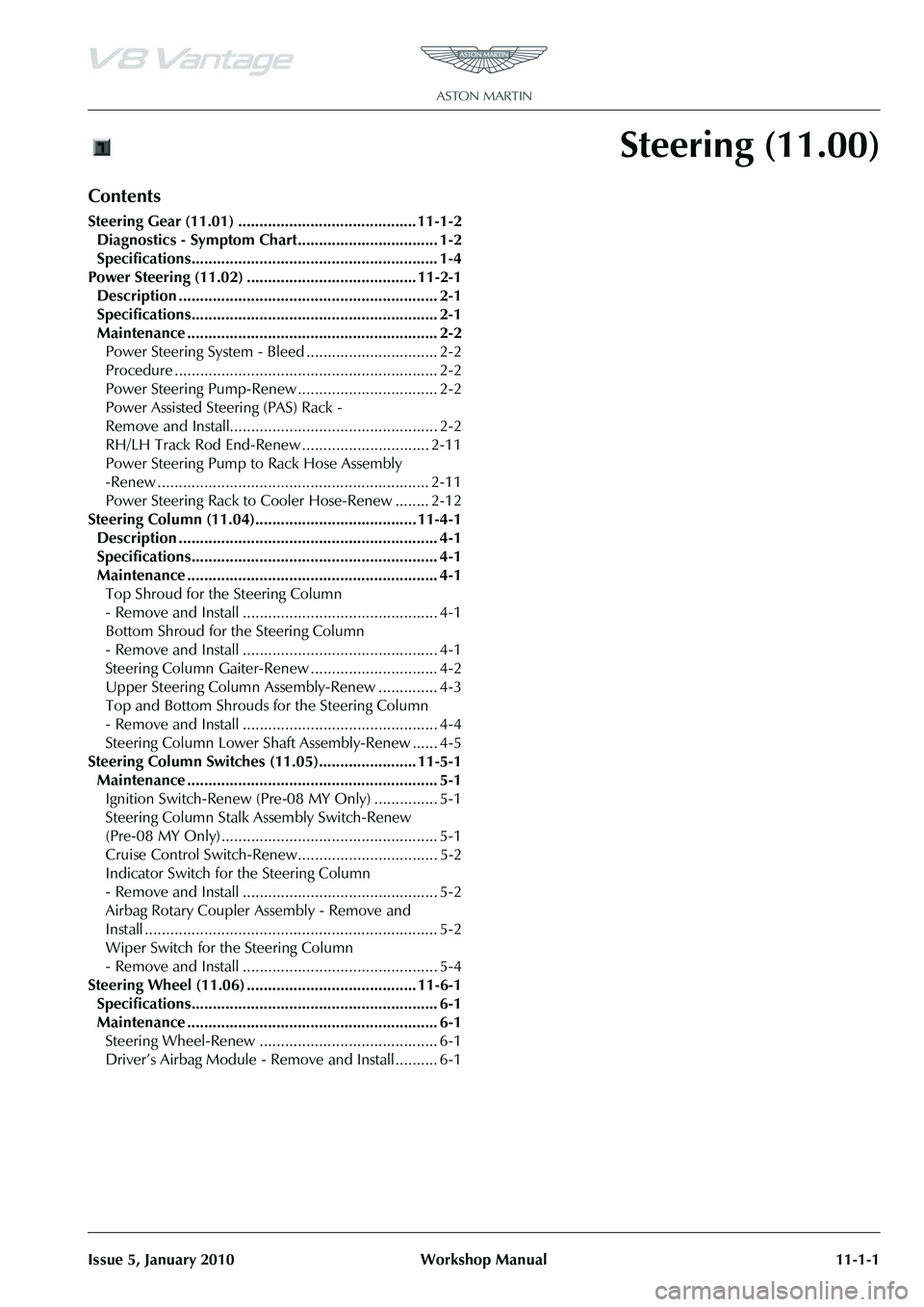
Issue 5, January 2010 Workshop Manual 11-1-1
Steering (11.00)
Contents
Steering Gear (11.01) .......................................... 11-1-2Diagnostics - Symptom Chart................................. 1-2
Specifications.......................................................... 1-4
Power Steering (11.02) ........................................ 11-2-1 Description ............................................................. 2-1
Specifications.......................................................... 2-1
Maintenance ........................................................... 2-2Power Steering System - Bleed ............................... 2-2
Procedure .............................................................. 2-2
Power Steering Pump-Renew ................................. 2-2
Power Assisted Steering (PAS) Rack -
Remove and Install................................................. 2-2
RH/LH Track Rod End-Renew .............................. 2-11
Power Steering Pump to Rack Hose Assembly
-Renew ................................................................ 2-11
Power Steering Rack to Cooler Hose-Renew ........ 2-12
Steering Column (11.04)...................................... 11-4-1 Description ............................................................. 4-1
Specifications.......................................................... 4-1
Maintenance ........................................................... 4-1Top Shroud for the Steering Column
- Remove and Install .............................................. 4-1
Bottom Shroud for the Steering Column
- Remove and Install .............................................. 4-1
Steering Column Gaiter-Renew .............................. 4-2
Upper Steering Column Assembly-Renew .............. 4-3
Top and Bottom Shrouds for the Steering Column
- Remove and Install .............................................. 4-4
Steering Column Lower Shaft Assembly-Renew ...... 4-5
Steering Column Switches (11.05)....................... 11-5-1 Maintenance ........................................................... 5-1Ignition Switch-Renew (Pre-08 MY Only) ............... 5-1
Steering Column Stalk Assembly Switch-Renew
(Pre-08 MY Only) ................................................... 5-1
Cruise Control Switch-Renew................................. 5-2
Indicator Switch for the Steering Column
- Remove and Install .............................................. 5-2
Airbag Rotary Coupler Assembly - Remove and
Install ..................................................................... 5-2
Wiper Switch for the Steering Column
- Remove and Install .............................................. 5-4
Steering Wheel (11.06) ........................................ 11-6-1 Specifications.......................................................... 6-1
Maintenance ........................................................... 6-1Steering Wheel-Renew .......................................... 6-1
Driver’s Airbag Module - Remove and Install .......... 6-1
Page 601 of 947
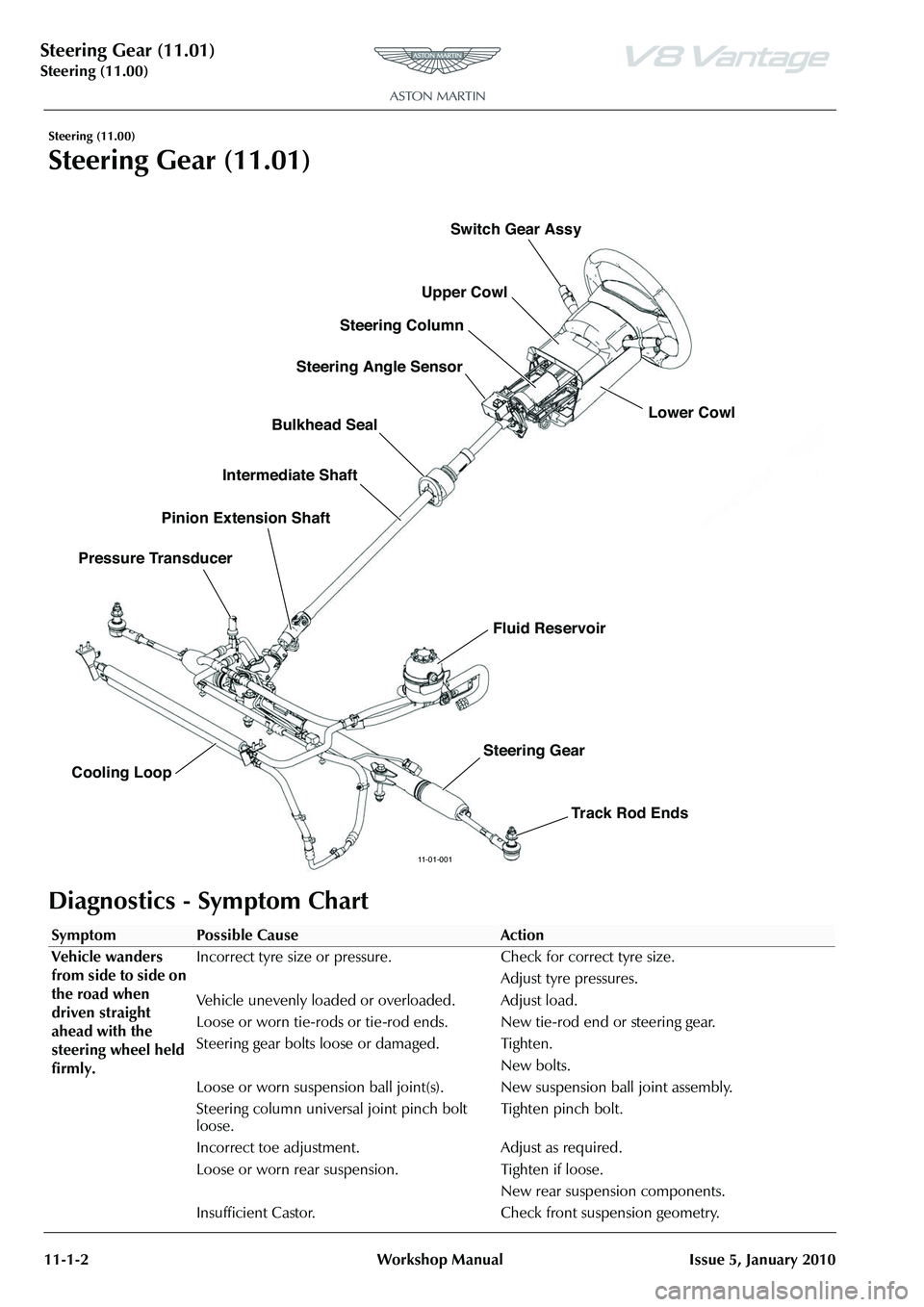
Steering Gear (11.01)
Steering (11.00)11-1-2 Workshop Manual Issue 5, January 2010
Steering (11.00)
Steering Gear (11.01)
Diagnostics - Symptom Chart
11-01-001
Upper Cowl Lower Cowl
Steering Column
Steering Angle Sensor
Bulkhead Seal
Intermediate Shaft
Pressure Transducer Pinion Extension Shaft
Cooling Loop Switch Gear Assy
Fluid Reservoir
Steering Gear Track Rod Ends
SymptomPossible CauseAction
Vehicle wanders
from side to side on
the road when
driven straight
ahead with the
steering wheel held
firmly. Incorrect tyre size or pressure. Check for correct tyre size.
Adjust tyre pressures.
Vehicle unevenly loaded or overloaded. Adjust load.
Loose or worn tie-rods or tie-rod ends. New tie-rod end or steering gear.
Steering gear bolts loose or damaged. Tighten. New bolts.
Loose or worn suspension ball joint(s). New suspension ball joint assembly.
Steering column universal joint pinch bolt
loose. Tighten pinch bolt.
Incorrect toe adjustment. Adjust as required.
Loose or worn rear suspension. Tighten if loose. New rear suspension components.
Insufficient Castor. Check fr ont suspension geometry.
Page 602 of 947
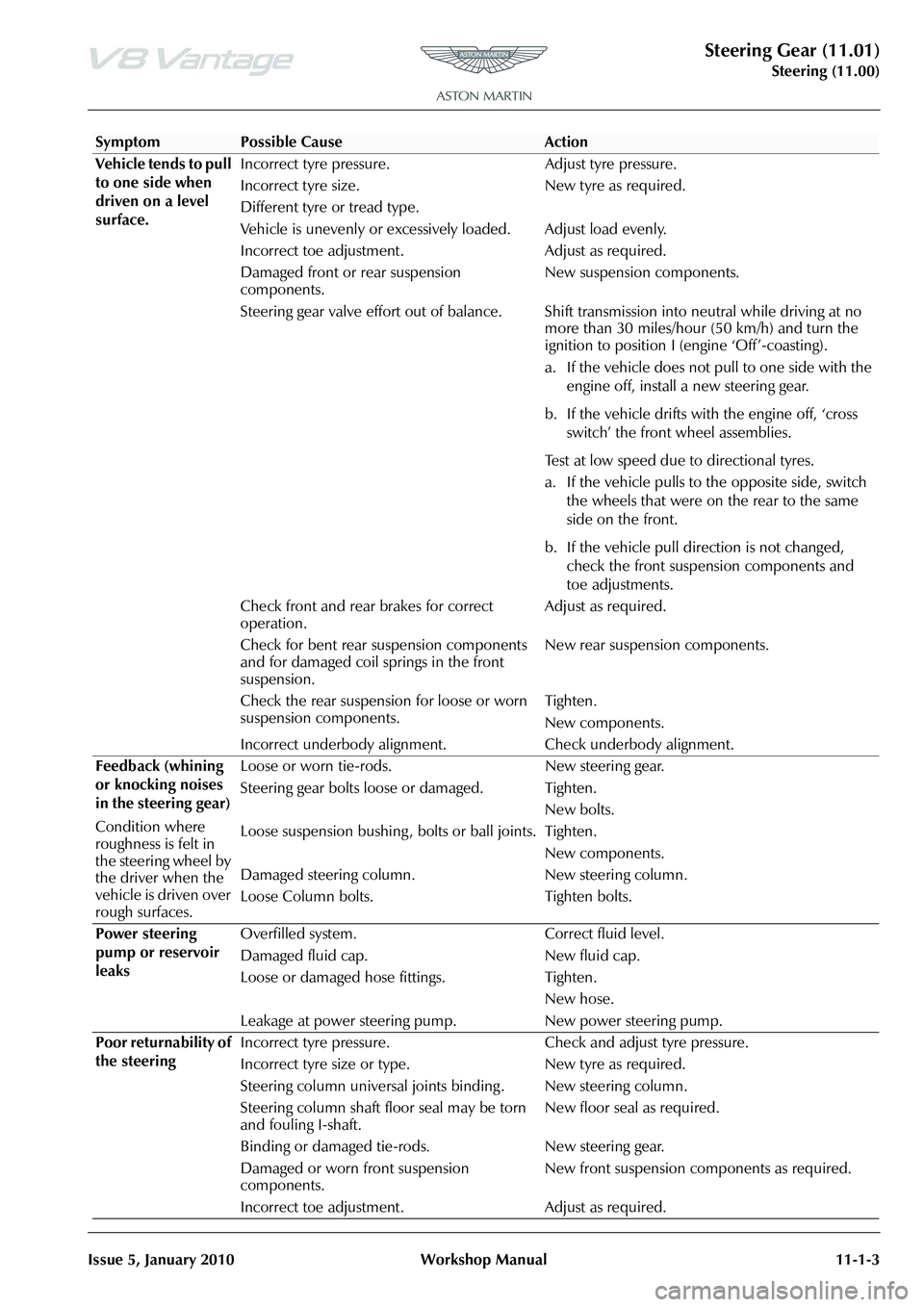
Steering Gear (11.01)
Steering (11.00)
Issue 5, January 2010 Workshop Manual 11-1-3
Vehicle tends to pull
to one side when
driven on a level
surface. Incorrect tyre pressure. Adjust tyre pressure.
Incorrect tyre size.
Different tyre or tread type.
New tyre as required.
Vehicle is unevenly or excessively loaded. Adjust load evenly.
Incorrect toe adjustment. Adjust as required.
Damaged front or rear suspension
components. New suspension components.
Steering gear valve effort out of balance. Shift transmission into neutral while driving at no more than 30 miles/hour (50 km/h) and turn the
ignition to position I (engine ‘Off’-coasting).
a. If the vehicle does not pull to one side with the
engine off, install a new steering gear.
b. If the vehicle drifts with the engine off, ‘cross switch’ the front wheel assemblies.
Test at low speed due to directional tyres.
a. If the vehicle pulls to the opposite side, switch the wheels that were on the rear to the same
side on the front.
b. If the vehicle pull direction is not changed, check the front suspension components and
toe adjustments.
Check front and rear brakes for correct
operation. Adjust as required.
Check for bent rear suspension components
and for damaged coil springs in the front
suspension. New rear suspension components.
Check the rear suspension for loose or worn
suspension components. Tighten.
New components.
Incorrect underbody alignment. Check underbody alignment.
Feedback (whining
or knocking noises
in the steering gear)
Condition where
roughness is felt in
the steering wheel by
the driver when the
vehicle is driven over
rough surfaces. Loose or worn tie-rods. New steering gear.
Steering gear bolts loose or damaged. Tighten.
New bolts.
Loose suspension bushing , bolts or ball joints. Tighten.
New components.
Damaged steering column.
Loose Column bolts. New steering column.
Tighten bolts.
Power steering
pump or reservoir
leaks Overfilled system. Correct fluid level.
Damaged fluid cap. New fluid cap.
Loose or damaged hose fittings. Tighten.
New hose.
Leakage at power steering pump. New power steering pump.
Poor returnability of
the steering Incorrect tyre pressure. Check
and adjust tyre pressure.
Incorrect tyre size or ty pe. New tyre as required.
Steering column universal joints binding . New steering column.
Steering column shaft floor seal may be torn
and fouling I-shaft. New floor seal as required.
Binding or damaged tie-rods. New steering gear.
Damaged or worn front suspension
components. New front suspension components as required.
Incorrect toe adjustment. Adjust as required.
SymptomPossible CauseAction
Page 603 of 947
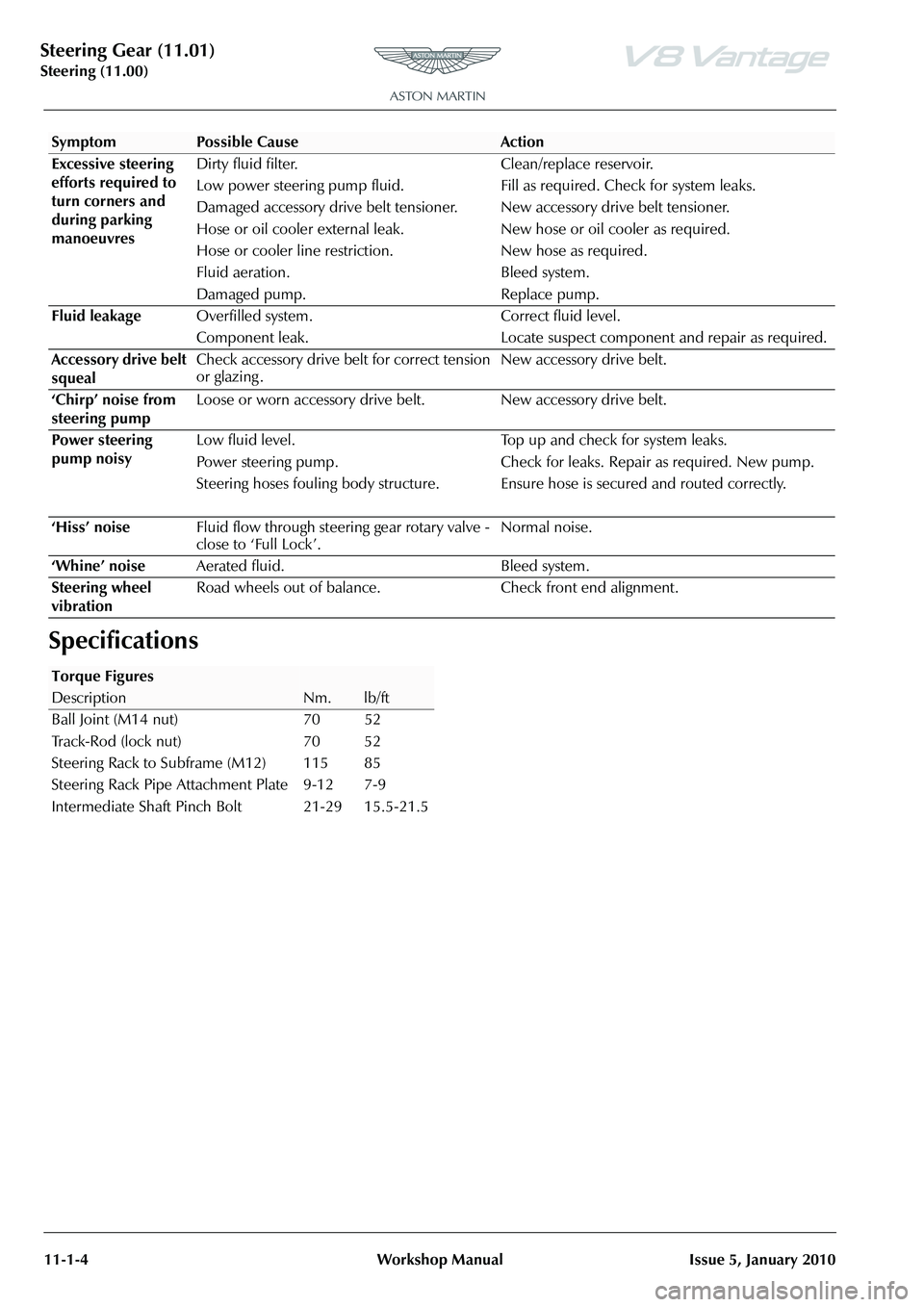
Steering Gear (11.01)
Steering (11.00)11-1-4 Workshop Manual Issue 5, January 2010
Specifications
Excessive steering
efforts required to
turn corners and
during parking
manoeuvres Dirty fluid filter.
Low power steering pump fluid.
Clean/replace reservoir.
Fill as required. Check for system leaks.
Damaged accessory drive belt tensioner. New accessory drive belt tensioner.
Hose or oil cooler external leak. New hose or oil cooler as required.
Hose or cooler line restriction. New hose as required.
Fluid aeration.
Damaged pump. Bleed system.
Replace pump.
Fluid leakage Overfilled system. Correct fluid level.
Component leak. Locate suspect component and repair as required.
Accessory drive belt
squeal Check accessory drive belt for correct tension
or glazing .
New accessory drive belt.
‘Chirp’ noise from
steering pump Loose or worn accessory drive belt. New accessory drive belt.
Power steering
pump noisy Low fluid level. Top up and check for system leaks.
Power steering pump.
Steering hoses fouling body structure. Check for leaks. Repair
as required. New pump.
Ensure hose is secured and routed correctly.
‘Hiss’ noise Fluid flow through steering gear rotary valve -
close to ‘Full Lock’. Normal noise.
‘Whine’ noise Aerated fluid. Bleed system.
Steering wheel
vibration Road wheels out of balance. Check front end alignment.
SymptomPossible CauseAction
Torque Figures
DescriptionNm.lb/ft
Ball Joint (M14 nut) 70 52
Track-Rod (lock nut) 70 52
Steering Rack to Subframe (M12) 115 85
Steering Rack Pipe Attachment Plate 9-12 7-9
Intermediate Shaft Pinch Bolt 21-29 15.5-21.5
Page 604 of 947
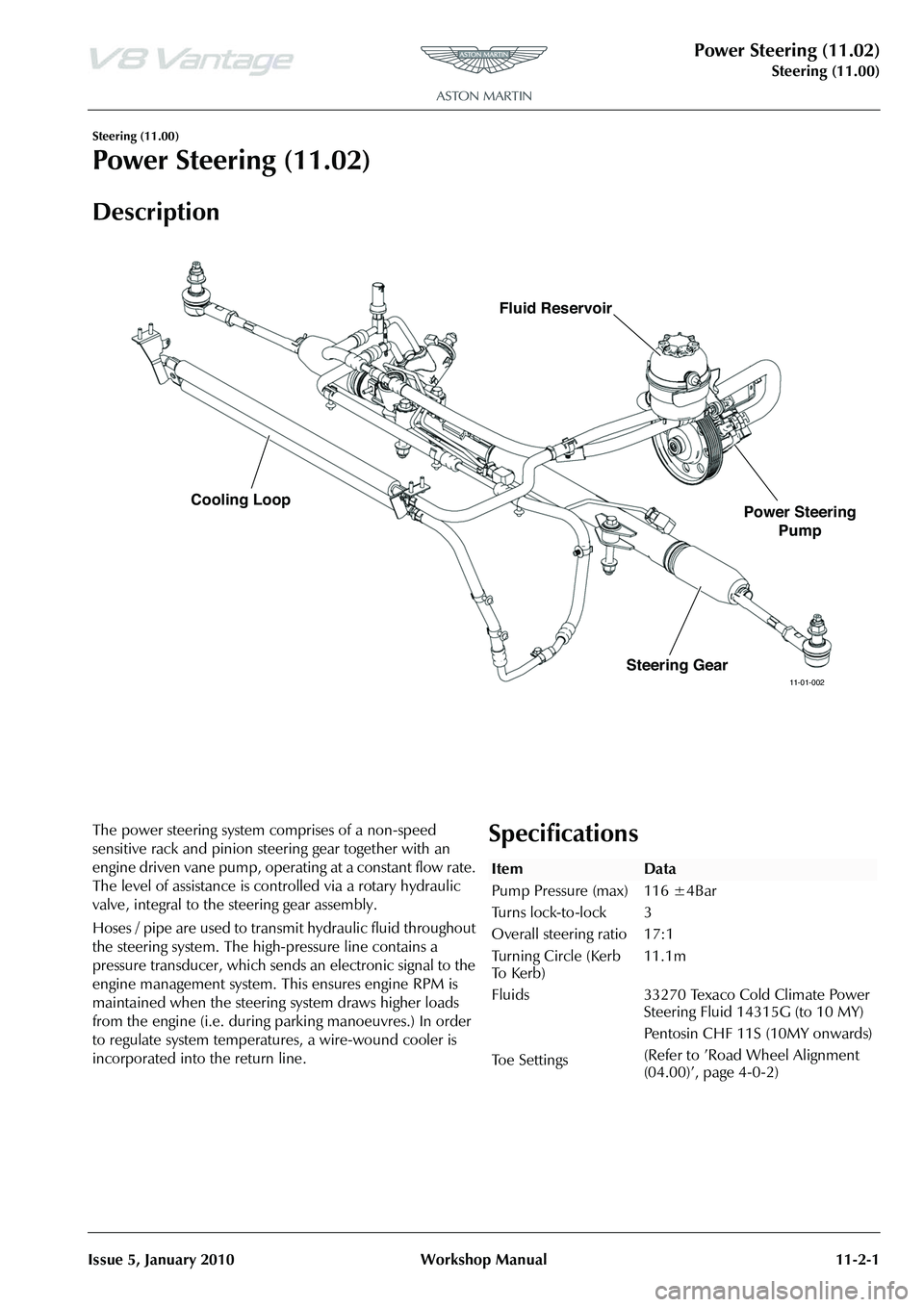
Power Steering (11.02)
Steering (11.00)
Issue 5, January 2010 Workshop Manual 11-2-1
Steering (11.00)
Power Steering (11.02)
Description
The power steering system comprises of a non-speed
sensitive rack and pinion steering gear together with an
engine driven vane pump, operating at a constant flow rate.
The level of assistance is co ntrolled via a rotary hydraulic
valve, integral to the steering gear assembly.
Hoses / pipe are used to transm it hydraulic fluid throughout
the steering system. The high -pressure line contains a
pressure transducer, which sends an electronic signal to the
engine management system. This ensures engine RPM is
maintained when the steering system draws higher loads
from the engine (i.e. during parking manoeuvres.) In order
to regulate system temperatures, a wire-wound cooler is
incorporated into the return line.Specifications
11-01-002Steering Gear
Cooling Loop
Power Steering
Pump
Fluid Reservoir
ItemData
Pump Pressure (max)
Turns lock-to-lock
Overall steering ratio
Turning Circle (Kerb
To K e r b )
Fluids
Toe Settings 116 ±4Bar
3
17:1
11.1m
33270 Texaco Cold Climate Power
Steering Fluid 14315G (to 10 MY)
Pentosin CHF 11S (10MY onwards)
(Refer to ’Road Wheel Alignment
(04.00)
Page 605 of 947
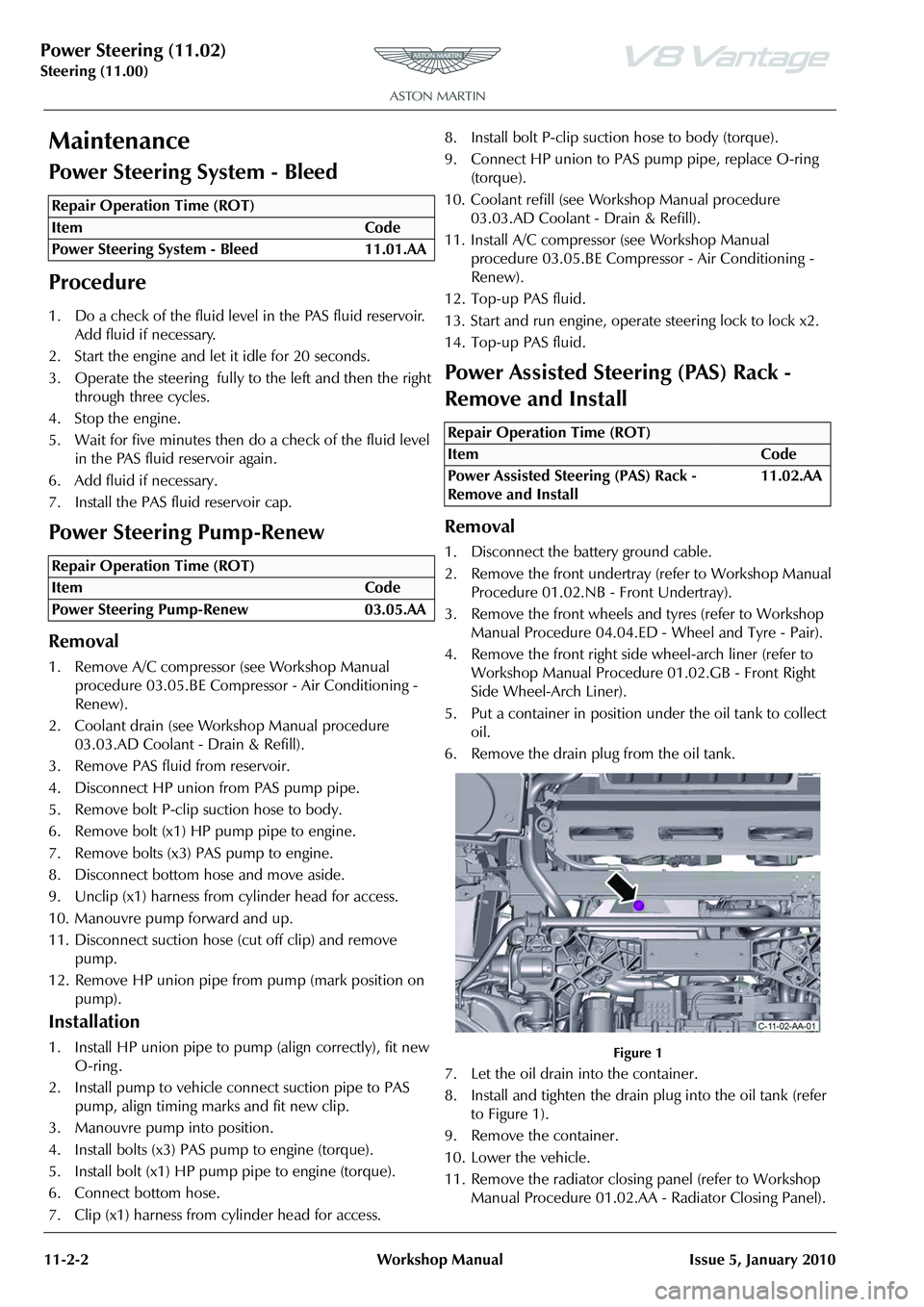
Power Steering (11.02)
Steering (11.00)11-2-2 Workshop Manual Issue 5, January 2010
Maintenance
Power Steering System - Bleed
Procedure
1. Do a check of the fluid level in the PAS fluid reservoir. Add fluid if necessary.
2. Start the engine and let it idle for 20 seconds.
3. Operate the steering fully to the left and then the right through three cycles.
4. Stop the engine.
5. Wait for five minutes then do a check of the fluid level in the PAS fluid reservoir again.
6. Add fluid if necessary.
7. Install the PAS fluid reservoir cap.
Power Steering Pump-Renew
Removal
1. Remove A/C compressor (see Workshop Manual procedure 03.05.BE Compre ssor - Air Conditioning -
Renew).
2. Coolant drain (see Workshop Manual procedure 03.03.AD Coolant - Drain & Refill).
3. Remove PAS fluid from reservoir.
4. Disconnect HP union from PAS pump pipe.
5. Remove bolt P-clip suction hose to body.
6. Remove bolt (x1) HP pump pipe to engine.
7. Remove bolts (x3) PAS pump to engine.
8. Disconnect bottom hose and move aside.
9. Unclip (x1) harness from cylinder head for access.
10. Manouvre pump forward and up.
11. Disconnect suction hose (cut off clip) and remove pump.
12. Remove HP union pipe from pump (mark position on
pump).
Installation
1. Install HP union pipe to pump (align correctly), fit new O-ring.
2. Install pump to vehicle connect suction pipe to PAS pump, align timing marks and fit new clip.
3. Manouvre pump into position.
4. Install bolts (x3) PAS pump to engine (torque).
5. Install bolt (x1) HP pump pipe to engine (torque).
6. Connect bottom hose.
7. Clip (x1) harness from cylinder head for access. 8. Install bolt P-clip suction hose to body (torque).
9. Connect HP union to PAS pump pipe, replace O-ring
(torque).
10. Coolant refill (see Workshop Manual procedure 03.03.AD Coolant - Drain & Refill).
11. Install A/C compressor (see Workshop Manual procedure 03.05.BE Compre ssor - Air Conditioning -
Renew).
12. Top-up PAS fluid.
13. Start and run engine, operate steering lock to lock x2.
14. Top-up PAS fluid.
Power Assisted Steering (PAS) Rack -
Remove and Install
Removal
1. Disconnect the battery ground cable.
2. Remove the front undertray (refer to Workshop Manual Procedure 01.02.NB - Front Undertray).
3. Remove the front wheels and tyres (refer to Workshop Manual Procedure 04.04.ED - Wheel and Tyre - Pair).
4. Remove the front right side wheel-arch liner (refer to Workshop Manual Procedure 01.02.GB - Front Right
Side Wheel-Arch Liner).
5. Put a container in position under the oil tank to collect oil.
6. Remove the drain plug from the oil tank.
Figure 1
7. Let the oil drain into the container.
8. Install and tighten the drain plug into the oil tank (refer to Figure 1).
9. Remove the container.
10. Lower the vehicle.
11. Remove the radiator closing panel (refer to Workshop Manual Procedure 01.02.AA - Radiator Closing Panel).
Repair Operation Time (ROT)
Repair Operation Time (ROT)
Repair Operation Time (ROT)
ItemCode
Power Assisted Steering (PAS) Rack -
Remove and Install 11.02.AA
Page 608 of 947
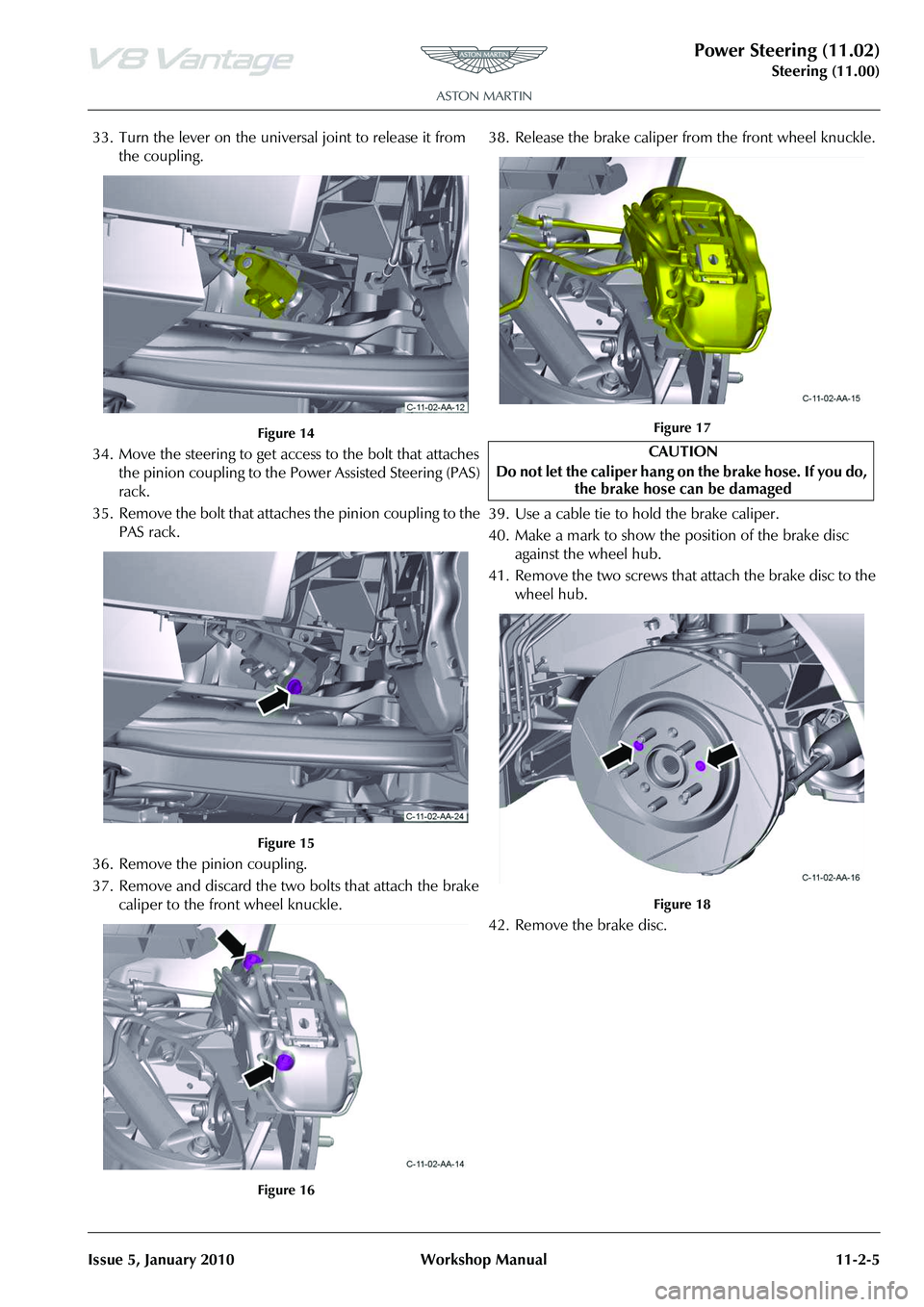
Power Steering (11.02)
Steering (11.00)
Issue 5, January 2010 Workshop Manual 11-2-5
33. Turn the lever on the universal joint to release it from the coupling.
Figure 14
34. Move the steering to get access to the bolt that attaches the pinion coupling to the Po wer Assisted Steering (PAS)
rack.
35. Remove the bolt that attaches the pinion coupling to the PAS rack.
Figure 15
36. Remove the pinion coupling.
37. Remove and discard the two bolts that attach the brake caliper to the front wheel knuckle.
Figure 16
38. Release the brake caliper from the front wheel knuckle.
Figure 17
39. Use a cable tie to hold the brake caliper.
40. Make a mark to show the position of the brake disc
against the wheel hub.
41. Remove the two screws that attach the brake disc to the wheel hub.
Figure 18
42. Remove the brake disc.
CAUTION
Do not let the caliper hang on the brake hose. If you do, the brake hose can be damaged