engine AUDI S4 1998 B5 / 1.G Engine Manual
[x] Cancel search | Manufacturer: AUDI, Model Year: 1998, Model line: S4, Model: AUDI S4 1998 B5 / 1.GPages: 72, PDF Size: 3.25 MB
Page 48 of 72
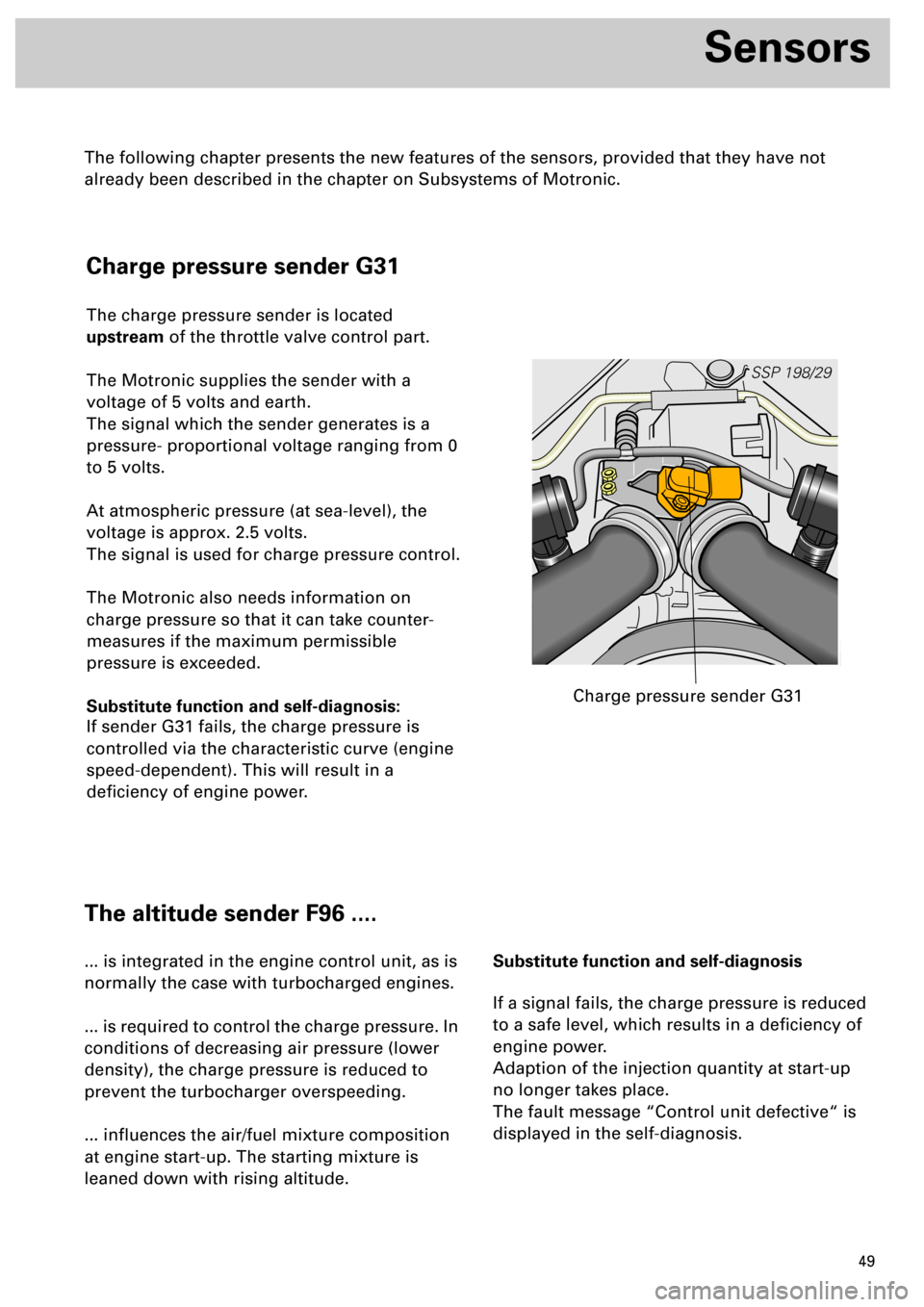
49
Sensors
Charge pressure sender G31
The charge pressure sender is located
upstream of the throttle valve control part.
The Motronic supplies the sender with a
voltage of 5 volts and earth.
The signal which the sender generates is a
pressure- proportional voltage ranging from 0
to 5 volts.
At atmospheric pressure (at sea-level), the
voltage is approx. 2.5 volts.
The signal is used for charge pressure control.
The Motronic also needs information on
charge pressure so that it can take counter-
measures if the maximum permissible
pressure is exceeded.
Substitute function and self-diagnosis:
If sender G31 fails, the charge pressure is
controlled via the characteristic curve (engine
speed-dependent). This will result in a
deficiency of engine power.
SSP 198/29
Charge pressure sender G31
The altitude sender F96 ....
... is integrated in the engine control unit, as is
normally the case with turbocharged engines.
... is required to control the charge pressure. In
conditions of decreasing air pressure (lower
density), the charge pressure is reduced to
prevent the turbocharger overspeeding.
... influences the air/fuel mixture composition
at engine start-up. The starting mixture is
leaned down with rising altitude.Substitute function and self-diagnosis
If a signal fails, the charge pressure is reduced
to a safe level, which results in a deficiency of
engine power.
Adaption of the injection quantity at start-up
no longer takes place.
The fault message “Control unit defective“ is
displayed in the self-diagnosis.
The following chapter presents the new features of the sensors, provided that they have not
already been described in the chapter on Subsystems of Motronic.
Page 49 of 72
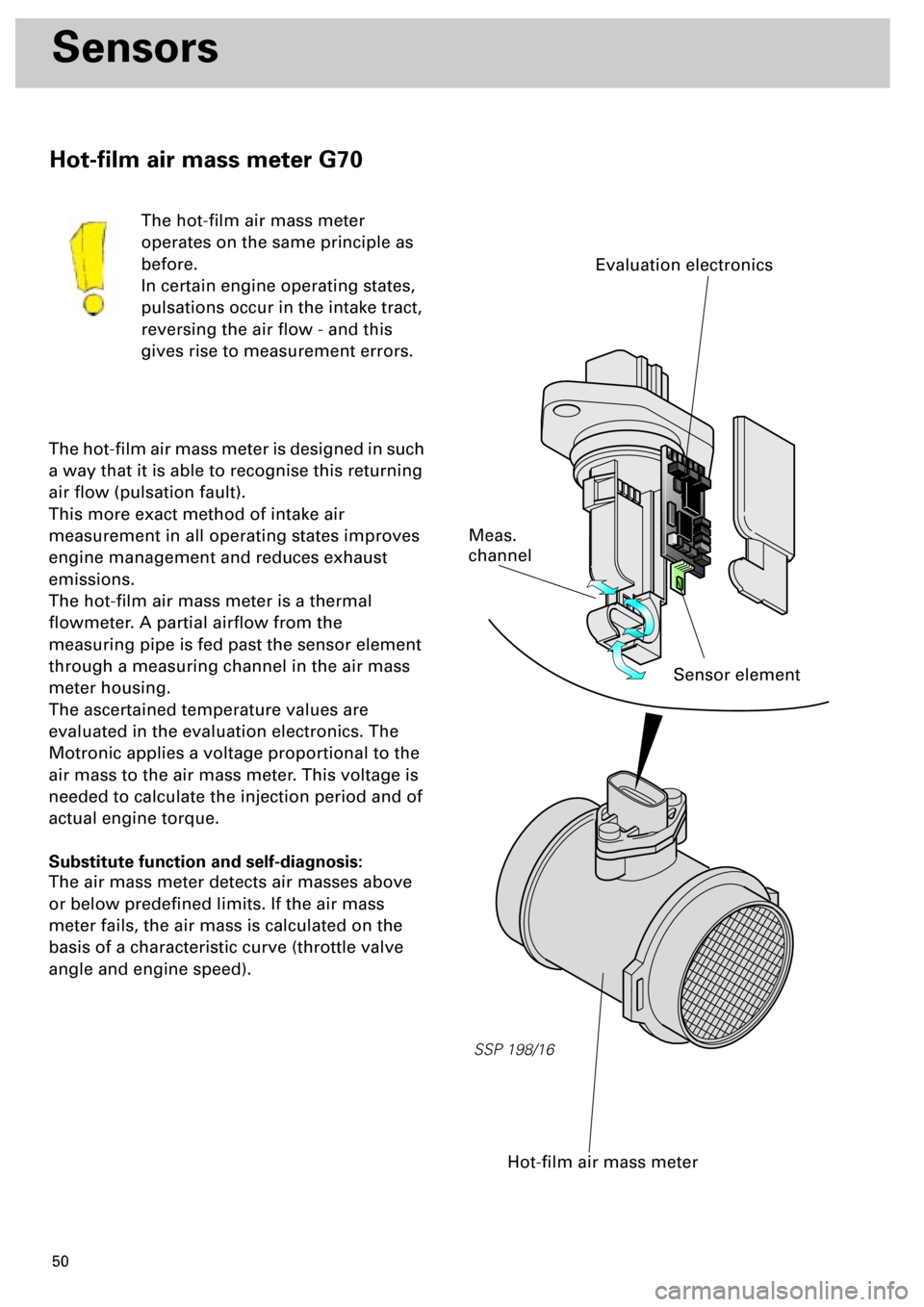
50
SSP 198/16
Sensors
The hot-film air mass meter
operates on the same principle as
before.
In certain engine operating states,
pulsations occur in the intake tract,
reversing the air flow - and this
gives rise to measurement errors.
The hot-film air mass meter is designed in such
a way that it is able to recognise this returning
air flow (pulsation fault).
This more exact method of intake air
measurement in all operating states improves
engine management and reduces exhaust
emissions.
The hot-film air mass meter is a thermal
flowmeter. A partial airflow from the
measuring pipe is fed past the sensor element
through a measuring channel in the air mass
meter housing.
The ascertained temperature values are
evaluated in the evaluation electronics. The
Motronic applies a voltage proportional to the
air mass to the air mass meter. This voltage is
needed to calculate the injection period and of
actual engine torque.
Substitute function and self-diagnosis:
The air mass meter detects air masses above
or below predefined limits. If the air mass
meter fails, the air mass is calculated on the
basis of a characteristic curve (throttle valve
angle and engine speed).
Hot-film air mass meter
Sensor element
Meas.
channel
Evaluation electronics
Hot-film air mass meter G70
Page 51 of 72
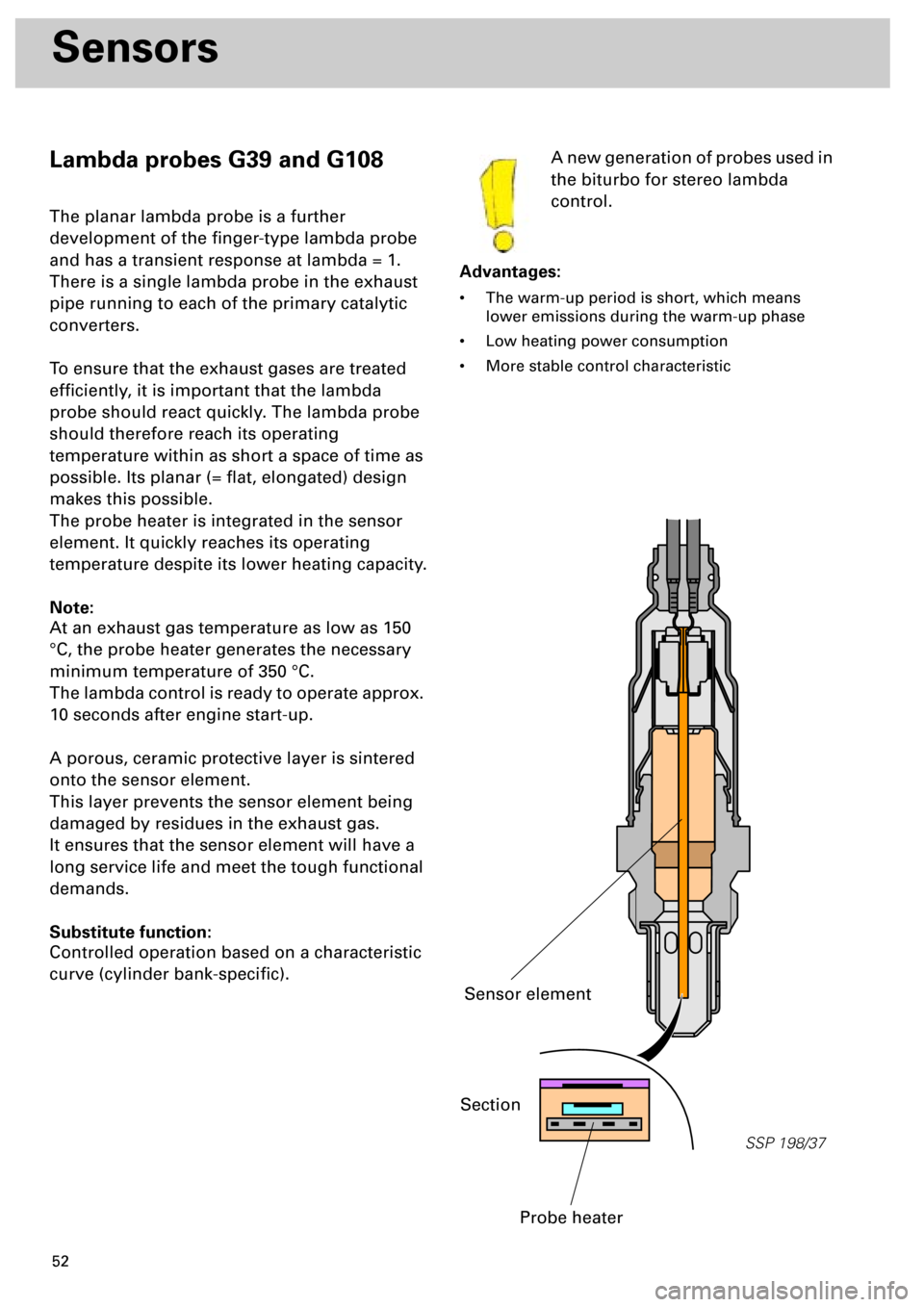
52
Sensors
Lambda probes G39 and G108
The planar lambda probe is a further
development of the finger-type lambda probe
and has a transient response at lambda = 1.
There is a single lambda probe in the exhaust
pipe running to each of the primary catalytic
converters.
To ensure that the exhaust gases are treated
efficiently, it is important that the lambda
probe should react quickly. The lambda probe
should therefore reach its operating
temperature within as short a space of time as
possible. Its planar (= flat, elongated) design
makes this possible.
The probe heater is integrated in the sensor
element. It quickly reaches its operating
temperature despite its lower heating capacity.
Note:
At an exhaust gas temperature as low as 150
°C, the probe heater generates the necessary
minimum temperature of 350 °C.
The lambda control is ready to operate approx.
10 seconds after engine start-up.
A porous, ceramic protective layer is sintered
onto the sensor element.
This layer prevents the sensor element being
damaged by residues in the exhaust gas.
It ensures that the sensor element will have a
long service life and meet the tough functional
demands.
Substitute function:
Controlled operation based on a characteristic
curve (cylinder bank-specific).A new generation of probes used in
the biturbo for stereo lambda
control.
Advantages:
• The warm-up period is short, which means
lower emissions during the warm-up phase
• Low heating power consumption
• More stable control characteristic
SSP 198/37
Section
Probe heater
Sensor element
Page 52 of 72
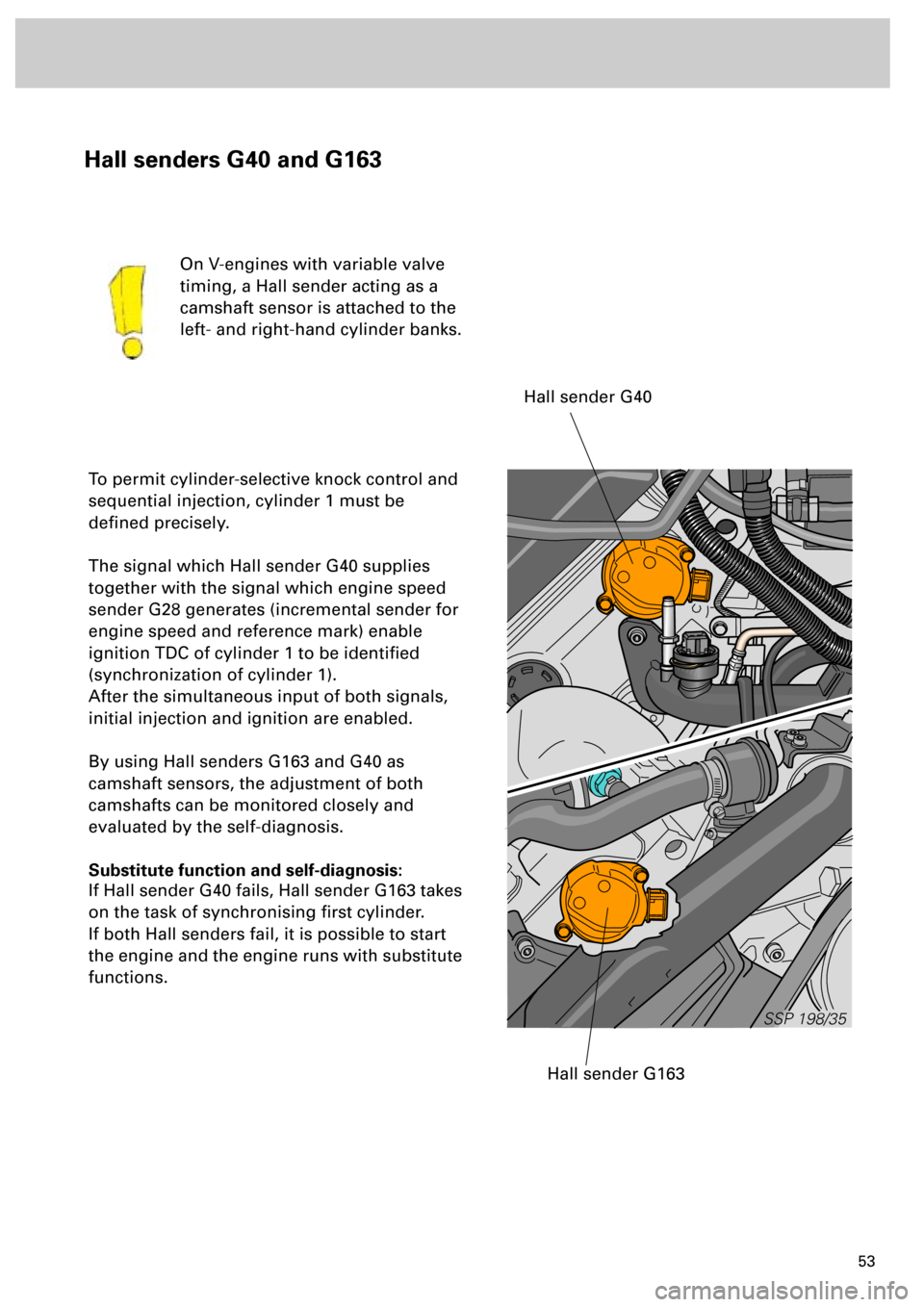
53
Hall senders G40 and G163
To permit cylinder-selective knock control and
sequential injection, cylinder 1 must be
defined precisely.
The signal which Hall sender G40 supplies
together with the signal which engine speed
sender G28 generates (incremental sender for
engine speed and reference mark) enable
ignition TDC of cylinder 1 to be identified
(synchronization of cylinder 1).
After the simultaneous input of both signals,
initial injection and ignition are enabled.
By using Hall senders G163 and G40 as
camshaft sensors, the adjustment of both
camshafts can be monitored closely and
evaluated by the self-diagnosis.
Substitute function and self-diagnosis:
If Hall sender G40 fails, Hall sender G163 takes
on the task of synchronising first cylinder.
If both Hall senders fail, it is possible to start
the engine and the engine runs with substitute
functions.On V-engines with variable valve
timing, a Hall sender acting as a
camshaft sensor is attached to the
left- and right-hand cylinder banks.
SSP 198/35
Hall sender G40
Hall sender G163
Page 53 of 72
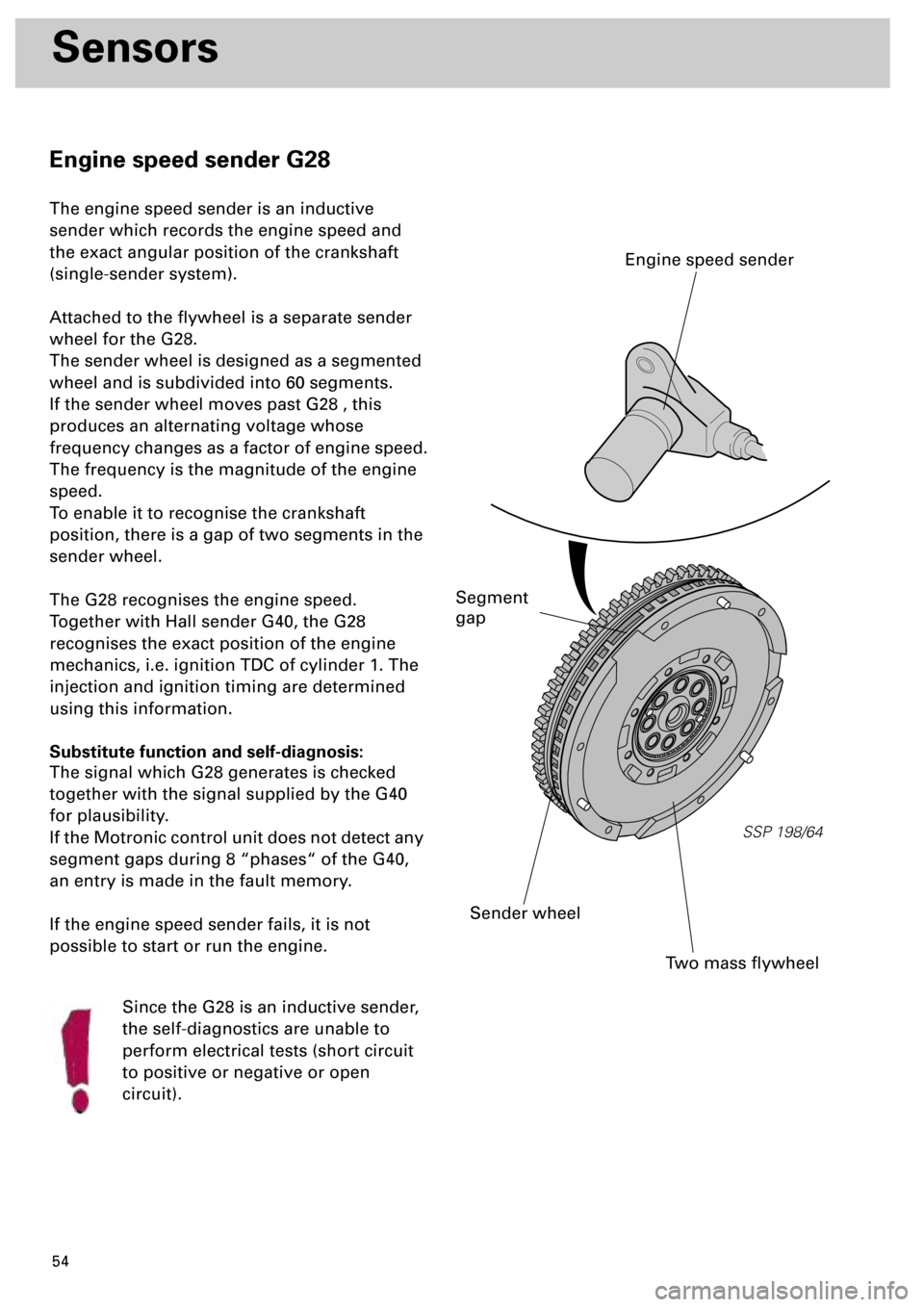
54
Sensors
Engine speed sender G28
The engine speed sender is an inductive
sender which records the engine speed and
the exact angular position of the crankshaft
(single-sender system).
Attached to the flywheel is a separate sender
wheel for the G28.
The sender wheel is designed as a segmented
wheel and is subdivided into 60 segments.
If the sender wheel moves past G28 , this
produces an alternating voltage whose
frequency changes as a factor of engine speed.
The frequency is the magnitude of the engine
speed.
To enable it to recognise the crankshaft
position, there is a gap of two segments in the
sender wheel.
The G28 recognises the engine speed.
Together with Hall sender G40, the G28
recognises the exact position of the engine
mechanics, i.e. ignition TDC of cylinder 1. The
injection and ignition timing are determined
using this information.
Substitute function and self-diagnosis:
The signal which G28 generates is checked
together with the signal supplied by the G40
for plausibility.
If the Motronic control unit does not detect any
segment gaps during 8 “phases“ of the G40,
an entry is made in the fault memory.
If the engine speed sender fails, it is not
possible to start or run the engine.
Since the G28 is an inductive sender,
the self-diagnostics are unable to
perform electrical tests (short circuit
to positive or negative or open
circuit).
SSP 198/64
Two mass flywheel
Sender wheel
Engine speed sender
Segment
gap
Page 54 of 72
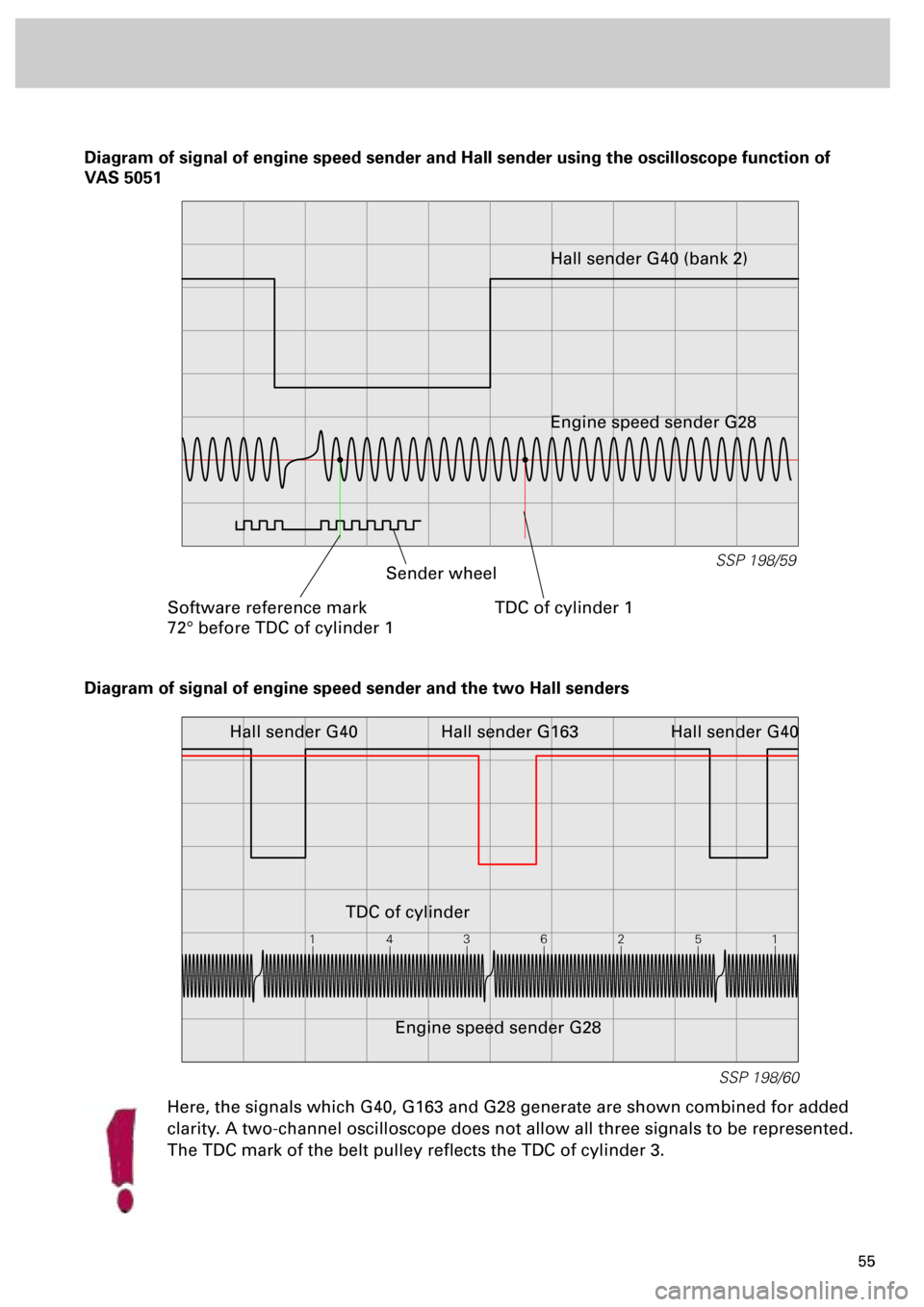
55
SSP 198/60
1436251
Diagram of signal of engine speed sender and Hall sender using the oscilloscope function of
VAS 5051
SSP 198/59
Software reference mark
72° before TDC of cylinder 1TDC of cylinder 1
Sender wheelHall sender G40 (bank 2)
Engine speed sender G28
Diagram of signal of engine speed sender and the two Hall senders
Hall sender G163 Hall sender G40
TDC of cylinder
Engine speed sender G28 Hall sender G40
Here, the signals which G40, G163 and G28 generate are shown combined for added
clarity. A two-channel oscilloscope does not allow all three signals to be represented.
The TDC mark of the belt pulley reflects the TDC of cylinder 3.
Page 55 of 72
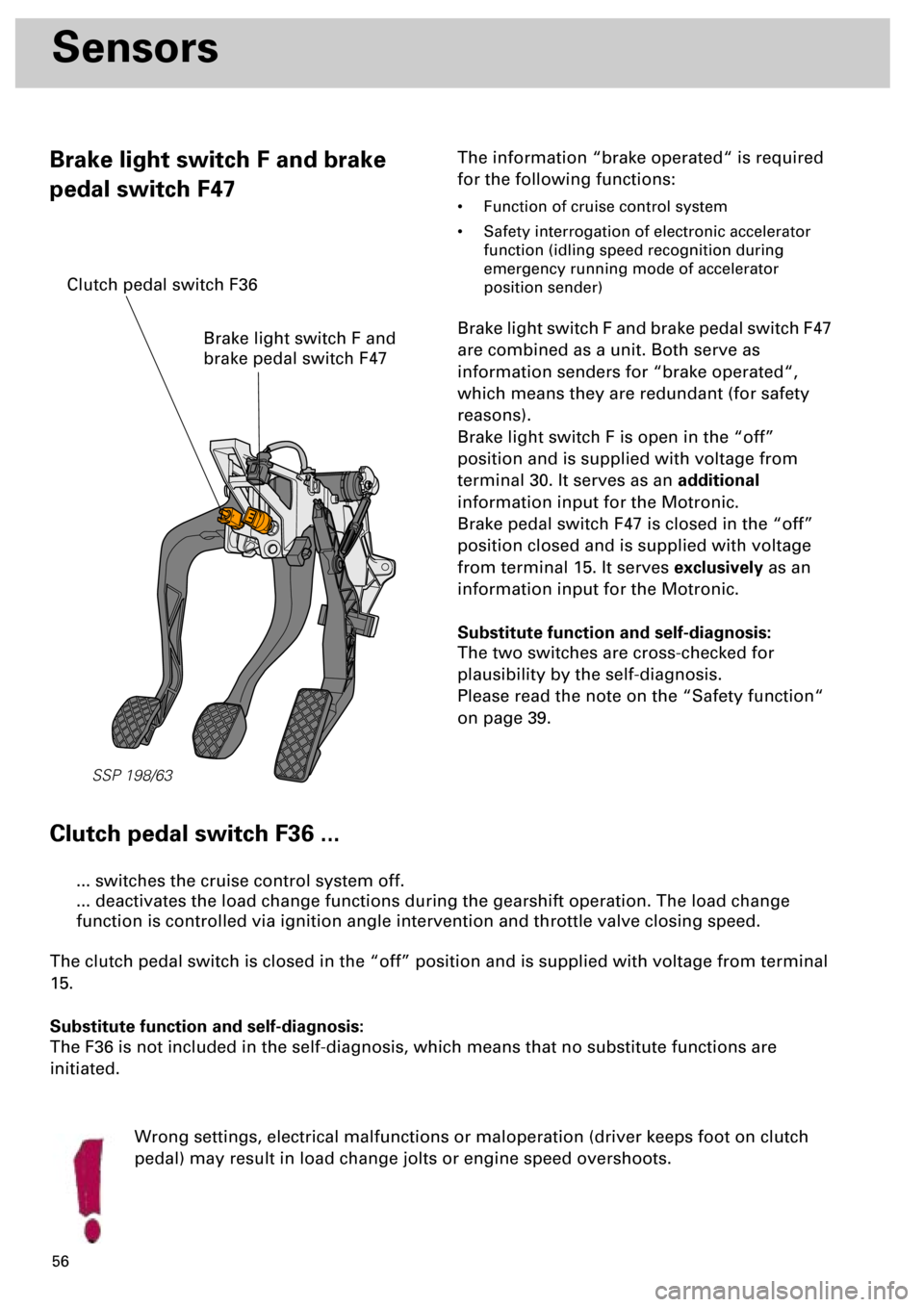
56
Sensors
Brake light switch F and brake
pedal switch F47The information “brake operated“ is required
for the following functions:
• Function of cruise control system
• Safety interrogation of electronic accelerator
function (idling speed recognition during
emergency running mode of accelerator
position sender)
Brake light switch F and brake pedal switch F47
are combined as a unit. Both serve as
information senders for “brake operated“,
which means they are redundant (for safety
reasons).
Brake light switch F is open in the “off”
position and is supplied with voltage from
terminal 30. It serves as an additional
information input for the Motronic.
Brake pedal switch F47 is closed in the “off”
position closed and is supplied with voltage
from terminal 15. It serves exclusively as an
information input for the Motronic.
Substitute function and self-diagnosis:
The two switches are cross-checked for
plausibility by the self-diagnosis.
Please read the note on the “Safety function“
on page 39.
Clutch pedal switch F36 ...
Wrong settings, electrical malfunctions or maloperation (driver keeps foot on clutch
pedal) may result in load change jolts or engine speed overshoots.
... switches the cruise control system off.
... deactivates the load change functions during the gearshift operation. The load change
function is controlled via ignition angle intervention and throttle valve closing speed.
The clutch pedal switch is closed in the “off” position and is supplied with voltage from terminal
15.
Substitute function and self-diagnosis:
The F36 is not included in the self-diagnosis, which means that no substitute functions are
initiated.
SSP 198/63
Brake light switch F and
brake pedal switch F47
Clutch pedal switch F36
Page 56 of 72
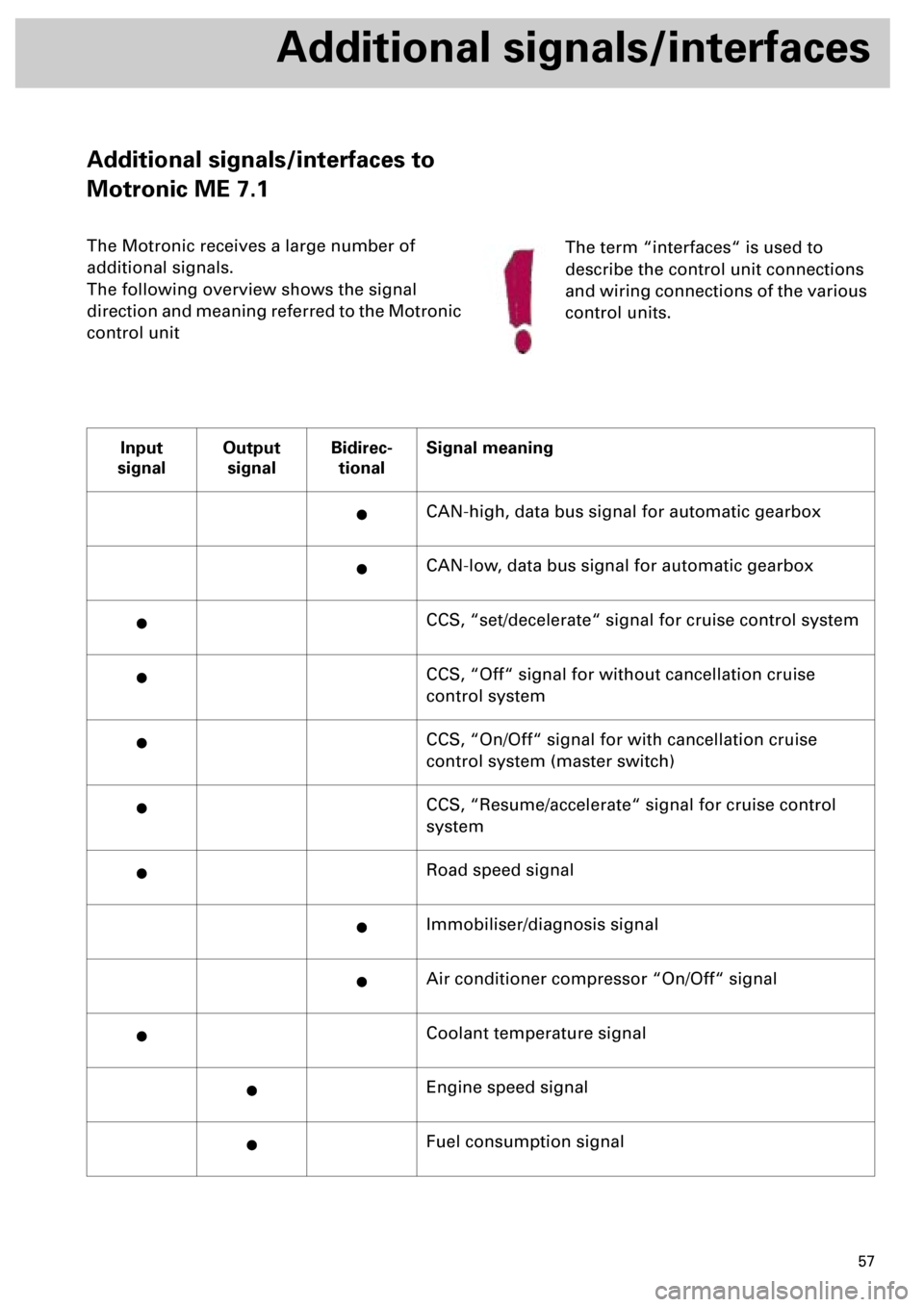
57
Additional signals/interfaces
Additional signals/interfaces to
Motronic ME 7.1
The Motronic receives a large number of
additional signals.
The following overview shows the signal
direction and meaning referred to the Motronic
control unit
Input
signalOutput
signalBidirec-
tionalSignal meaning
·CAN-high, data bus signal for automatic gearbox
·CAN-low, data bus signal for automatic gearbox
·CCS, “set/decelerate“ signal for cruise control system
·CCS, “Off“ signal for without cancellation cruise
control system
·CCS, “On/Off“ signal for with cancellation cruise
control system (master switch)
·CCS, “Resume/accelerate“ signal for cruise control
system
·Road speed signal
·Immobiliser/diagnosis signal
·Air conditioner compressor “On/Off“ signal
·Coolant temperature signal
·Engine speed signal
·Fuel consumption signal
The term “interfaces“ is used to
describe the control unit connections
and wiring connections of the various
control units.
Page 57 of 72
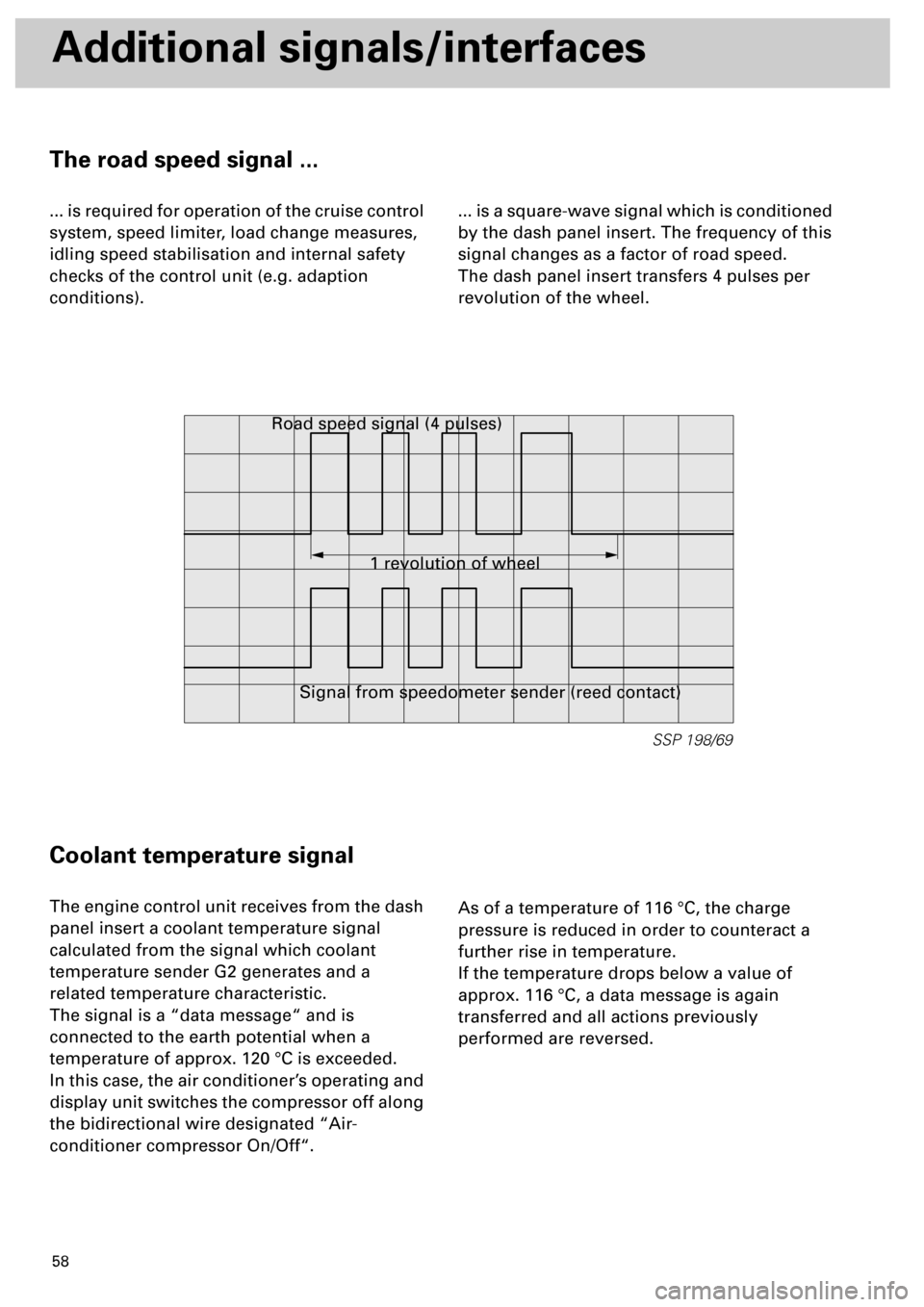
58
Additional signals/interfaces
The road speed signal ...
... is required for operation of the cruise control
system, speed limiter, load change measures,
idling speed stabilisation and internal safety
checks of the control unit (e.g. adaption
conditions).... is a square-wave signal which is conditioned
by the dash panel insert. The frequency of this
signal changes as a factor of road speed.
The dash panel insert transfers 4 pulses per
revolution of the wheel.
Coolant temperature signal
The engine control unit receives from the dash
panel insert a coolant temperature signal
calculated from the signal which coolant
temperature sender G2 generates and a
related temperature characteristic.
The signal is a “data message“ and is
connected to the earth potential when a
temperature of approx. 120 °C is exceeded.
In this case, the air conditioner’s operating and
display unit switches the compressor off along
the bidirectional wire designated “Air-
conditioner compressor On/Off“.As of a temperature of 116 °C, the charge
pressure is reduced in order to counteract a
further rise in temperature.
If the temperature drops below a value of
approx. 116 °C, a data message is again
transferred and all actions previously
performed are reversed.
SSP 198/69
1 revolution of wheel Road speed signal (4 pulses)
Signal from speedometer sender (reed contact)
Page 58 of 72
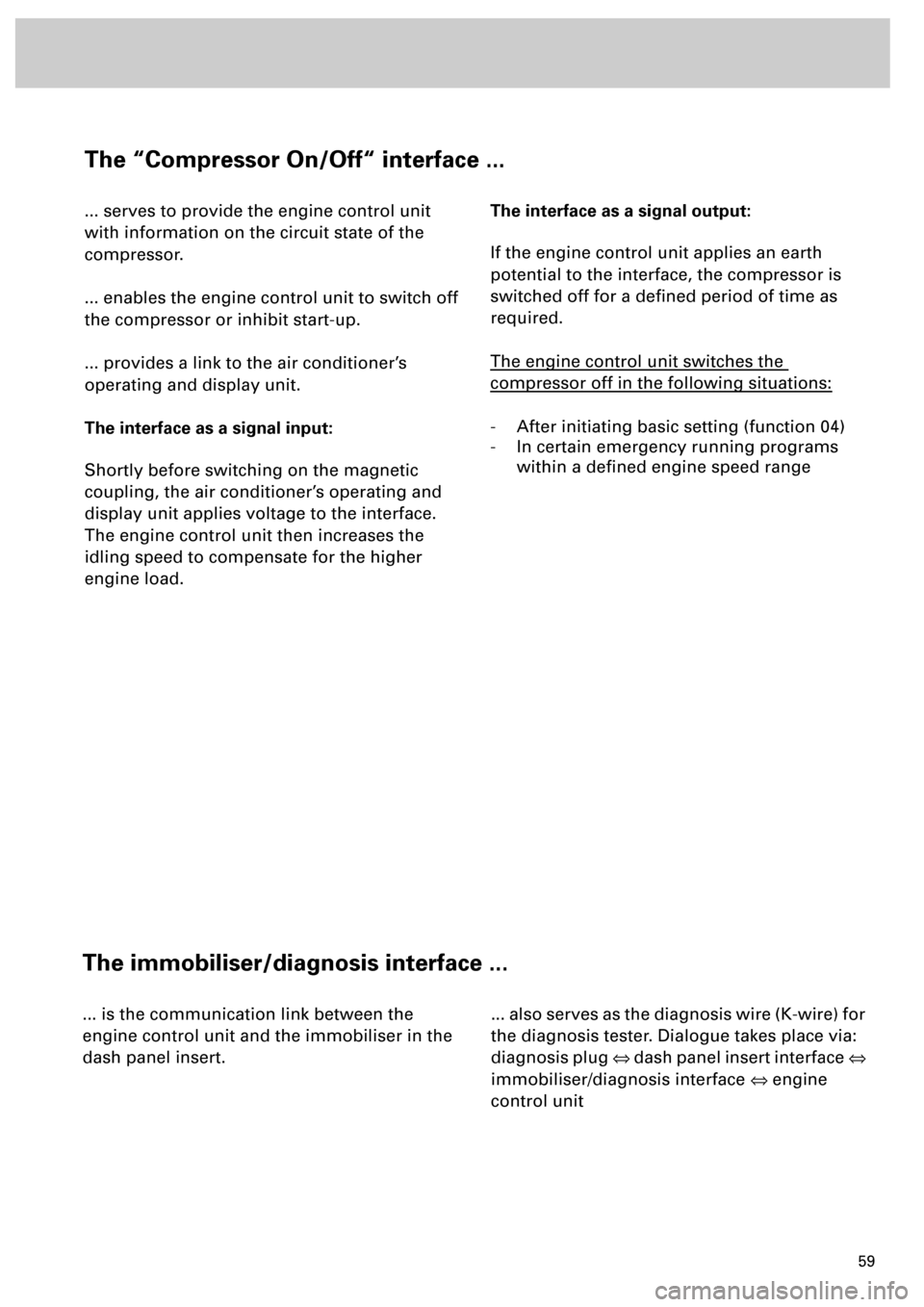
59
The “Compressor On/Off“ interface ...
... serves to provide the engine control unit
with information on the circuit state of the
compressor.
... enables the engine control unit to switch off
the compressor or inhibit start-up.
... provides a link to the air conditioner’s
operating and display unit.
The interface as a signal input:
Shortly before switching on the magnetic
coupling, the air conditioner’s operating and
display unit applies voltage to the interface.
The engine control unit then increases the
idling speed to compensate for the higher
engine load.The interface as a signal output:
If the engine control unit applies an earth
potential to the interface, the compressor is
switched off for a defined period of time as
required.
The engine control unit switches the
compressor off in the following situations:
- After initiating basic setting (function 04)
- In certain emergency running programs
within a defined engine speed range
The immobiliser/diagnosis interface ...
... is the communication link between the
engine control unit and the immobiliser in the
dash panel insert.... also serves as the diagnosis wire (K-wire) for
the diagnosis tester. Dialogue takes place via:
diagnosis plug Û dash panel insert interface Û
immobiliser/diagnosis interface Û engine
control unit