check engine BMW 528i 1998 E39 Workshop Manual
[x] Cancel search | Manufacturer: BMW, Model Year: 1998, Model line: 528i, Model: BMW 528i 1998 E39Pages: 1002
Page 482 of 1002
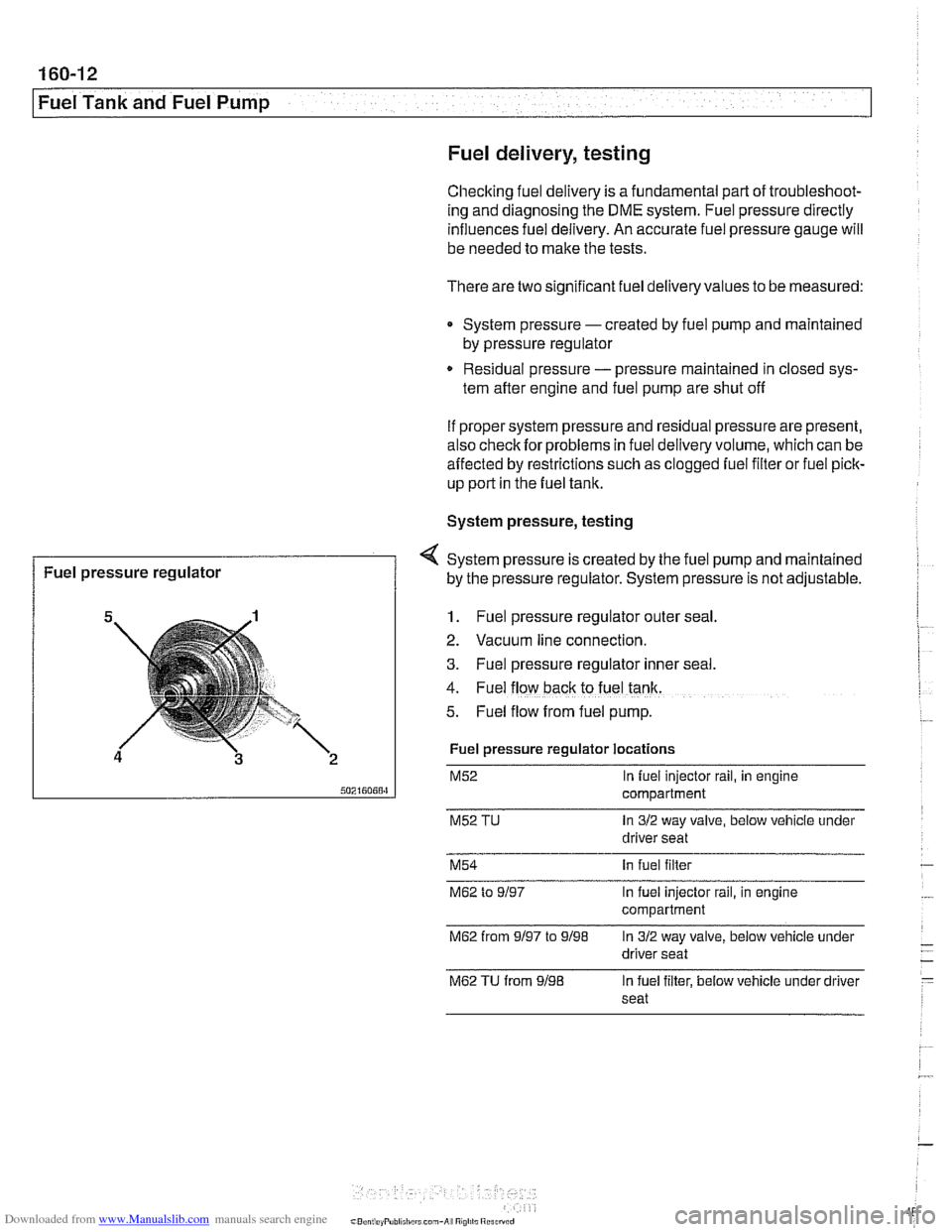
Downloaded from www.Manualslib.com manuals search engine
Fuel Tank and Fuel Pump
Fuel delivery,
testing
Checitino fuel delive~ is a fundamental oart of troubleshoot- .. ing and diagnosing thk DME system. ~ukl pressure directly
influences
fuel delivery. An accurate fuel pressure gauge will
be needed to make the tests.
There are two significant fuel deliveryvalues to be measured:
* System pressure - created by fuel pump and maintained
by pressure regulator
Residual pressure
- pressure maintained in closed sys-
tem after engine and fuel pump are shut off
if proper system pressure and residual pressure are present,
also check for problems in fuel delivery volume, which can be
affected by restrictions such as clogged fuel filter or fuel pick-
up port in the fuel tank.
System pressure, testing
1. Fuel pressure regulator outer seal
4 System pressure is created by the fuel pump and maintained
2. Vacuum line connection.
3. Fuel pressure regulator Inner seal.
4. Fuel flow back to fuel tank.
5. Fuel flow from fuel pump.
Fuel pressure
regulator
Fuel pressure regulator locations
M52 In fuel injector rail, in engine
compartment
M52 TU In 312 way valve, below vehicle under
driver seat
by the pressure
regulator. System pressure is not adjustable.
M54 In fuel filter
M62 to 9/97 In fuel injector rail, in engine
compartment
M62 from 9/97 to 9/98 In 312 way valve, below vehicle under
driver seat
M62 TU from 9/98 In fuel filter, below vehicle under driver
seat
Page 483 of 1002
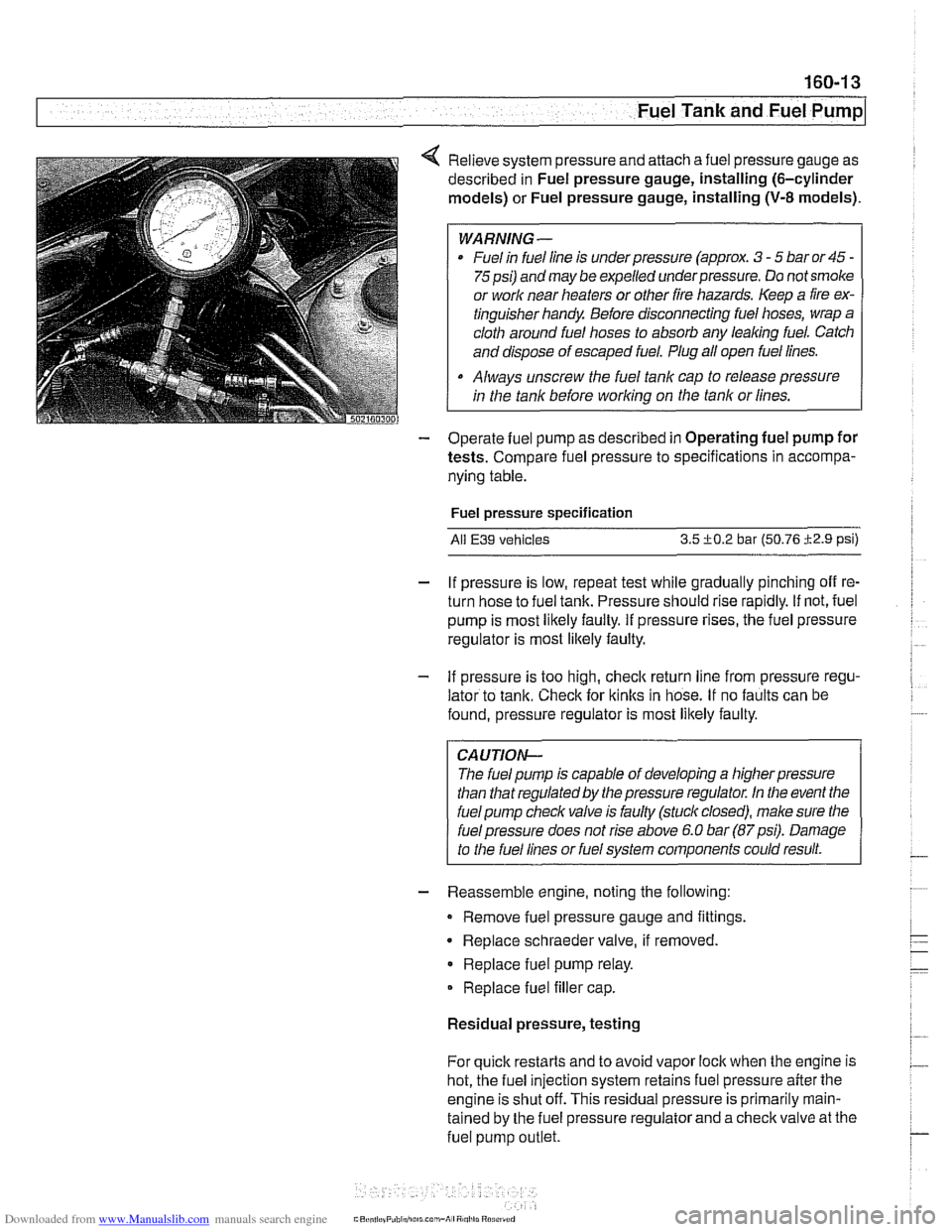
Downloaded from www.Manualslib.com manuals search engine
Fuel Tank and Fuel Pump
4 Relieve system pressure and attach a fuel pressure gauge as
described in Fuel pressure gauge, installing (6-cylinder
models) or Fuel pressure gauge, installing
(V-8 models).
WARNING-
Fuel in fuel line is under pressure (approx. 3 - 5 bar or 45 -
75psi) and may be expelled underpressure. Do not smoke
or
worlc near heaters or other fire hazards. Keep a fire ex-
tinguisher handy Before disconnecting fuel hoses, wrap a
cloth around fuel hoses to absorb any
leaking fuel. Catch
and dispose of escaped fuel. Plug all open fuel lines.
Always unscrew the fuel tank cap to release pressure
in the tank before
working on the tank or lines.
- Operate fuel pump as described in Operating fuel pump for
tests. Compare fuel pressure to specifications in accompa-
nying table.
Fuel pressure specification
All E39 vehicles 3.5 +0.2 bar (50.76 i2.9 psi)
- If pressure is low, repeat test while gradually pinching off re-
turn hose to fuel tank. Pressure should rise rapidly. If not, fuel
pump is most likely faulty. If pressure rises, the fuel pressure
regulator is most
likely faulty.
- If pressure is too high, checlc return line from pressure regu-
lator to tank. Check for
ltinks in hose. If no faults can be
found, pressure regulator is most likely faulty.
CAUTION-
The fuel pump is capable of developing a higher pressure
than that regulated by the pressure regulator. In the event the
fuel pump checlc valve is faulty (stuck closed), male sure the
I fuel pressure does not rise above 6.0 bar (87psi). Damage
to the fuel lines or fuel system components could result.
- Reassemble engine, noting the following:
Remove fuel pressure gauge and fittings.
Replace schraeder valve, if removed
Replace fuel pump relay.
Replace fuel filler cap.
Residual pressure, testing
For quick restarts and to avoid vapor lock when the engine is
hot, the fuel injection system retains fuel pressure after the
engine is shut off. This residual pressure is primarily
rnain-
tained by the fuel pressure regulator and a checlc valve at the
fuel pump
outlet.
Page 484 of 1002
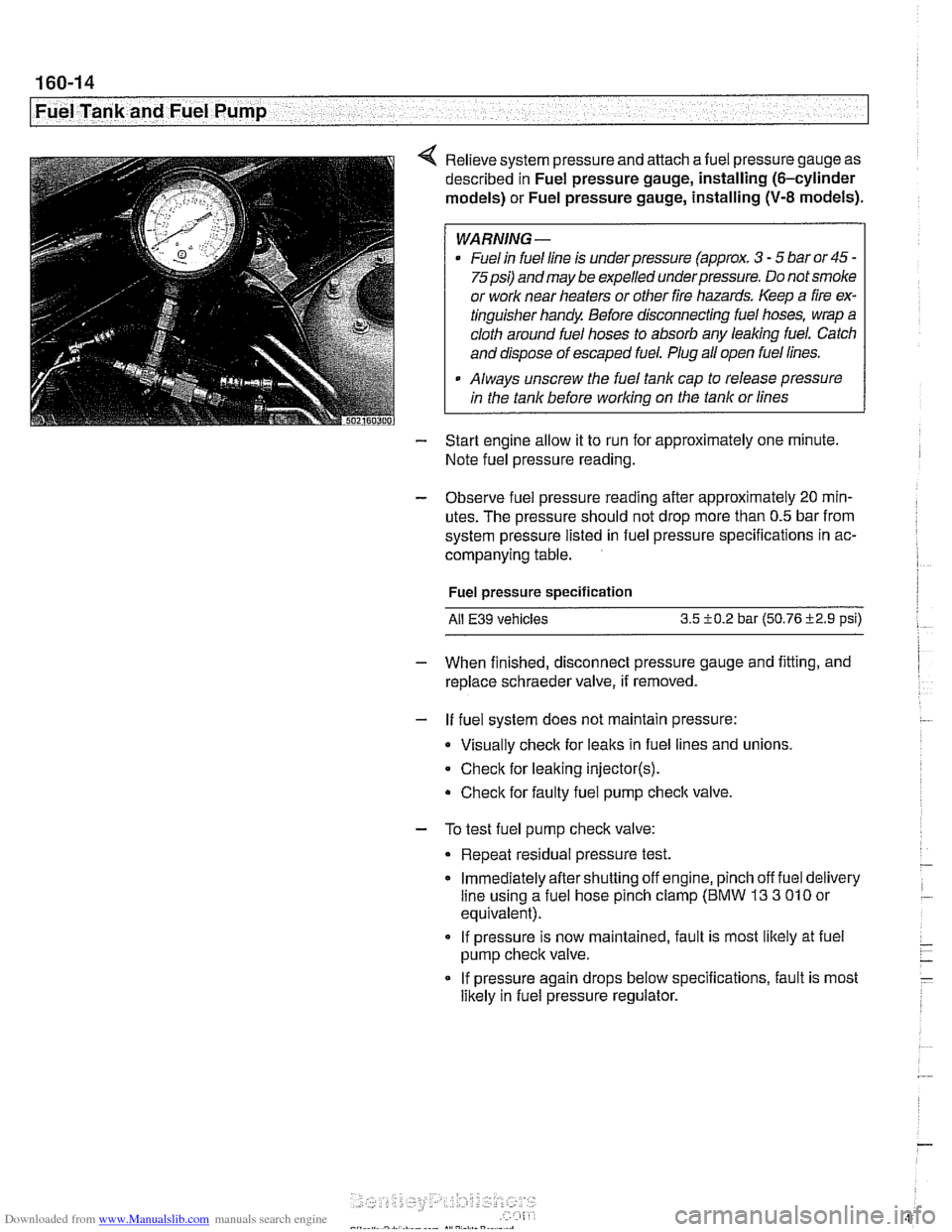
Downloaded from www.Manualslib.com manuals search engine
. .
I Fuel Tank and Fuel Pump I
4 Relieve system pressure and attach afuel pressure gauge as
described in Fuel pressure gauge, installing (6-cylinder
models) or Fuel pressure gauge, installing
(V-8 models).
WARNING -
Fuel in fuel line is underpressure (approx. 3 - 5 bar or45 -
75psi) and may be expelled underpressure. Do not smoke
or work near heaters or other fire hazards. Keep a fire ex-
tinguisher handy. Before disconnecting fuel hoses, wrap a
cloth around fuel hoses to absorb any leaking fuel. Catch
and dispose of escaped fuel. Plug all open fuel lines.
. Always unscrew the fuel tank cap to release pressure
in the tank before working on the tank or lines
- Start engine allow it to run for approximately one minute.
Note fuel pressure reading.
- Observe fuel pressure reading after approximately 20 mln-
utes. The pressure should not drop more than 0.5 bar from
system pressure listed in fuel pressure specifications in ac-
companying table.
Fuel pressure specification
Ail
E39 vehicles 3.5 i-0.2 bar (50.76 i2.9 psi)
- When finished, disconnect pressure gauge and fitting, and
replace schraeder valve, if removed.
- If fuel system does not maintain pressure:
Visually check for leaks in fuel lines and unions,
Check for leaking
injector(s).
Check for faulty fuel pump check valve.
- To test fuel pump check valve:
Repeat residual pressure test.
Immediately aftershutting off engine, pinch off fuel delivery
line using a fuel hose pinch clamp (BMW
13 3 010 or
equivalent).
If pressure is now maintained, fault is most likely at fuel
pump check valve.
If pressure again drops below specifications, fault is most
likely in fuel pressure regulator.
Page 485 of 1002
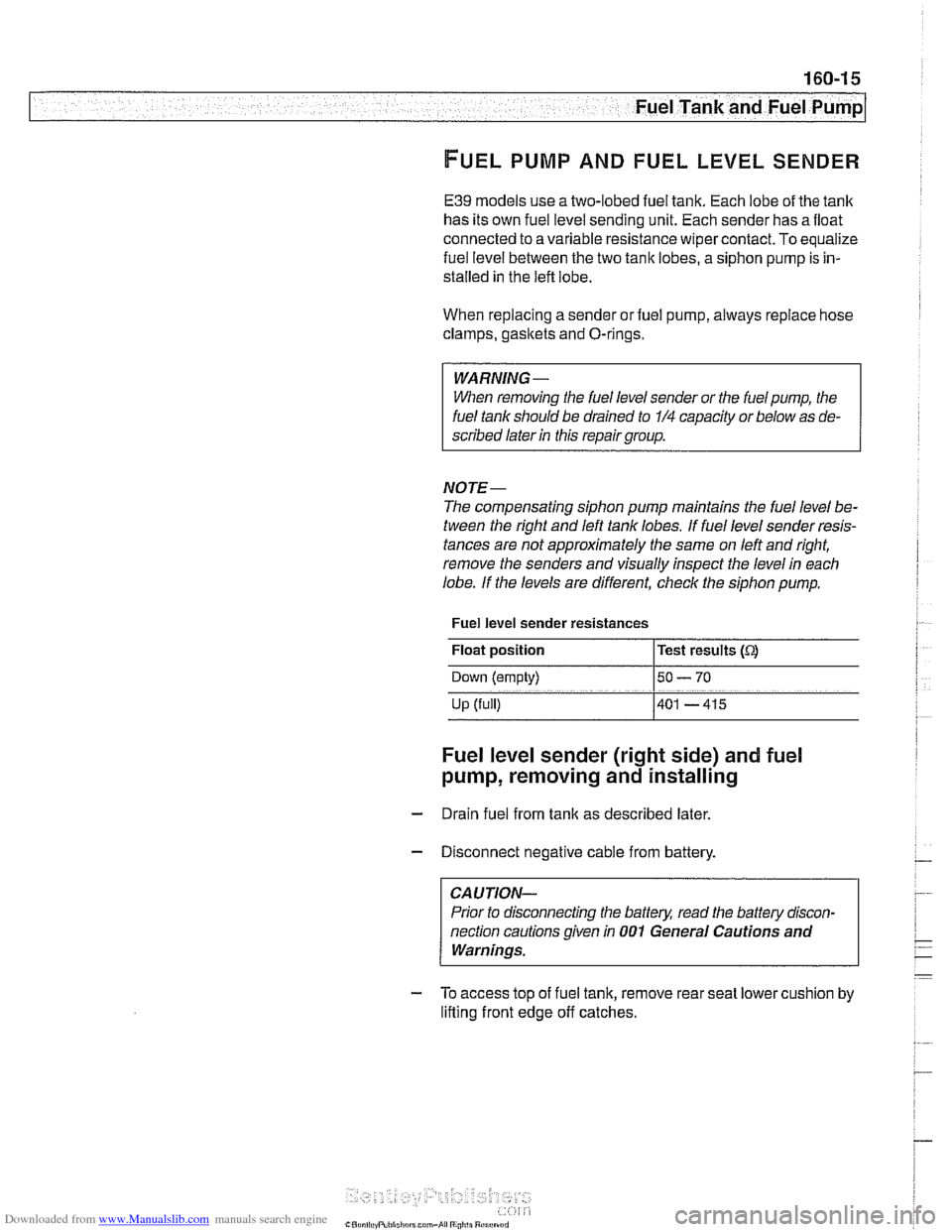
Downloaded from www.Manualslib.com manuals search engine
.-
err- .- Fuel Tank and Fuel Pump
FUELPUMP AND FUELLEVELSENDER
E39 models use a two-lobed fuel tank. Each lobe of the tank
has its own fuel level sending unit. Each sender has a float
connected to a variable resistance wipercontact. To equalize
fuel level between the two
tank lobes, a siphon pump is in-
stalled in the left lobe.
When replacing asender or fuel pump, always replace hose
clamps,
gasltets and O-rings.
WARNING
-
When removing the fuel level sender or the fuel pump, the
fuel tank should be drained to
1/4 capacity or below as de-
scribed later in this repair group.
NOTE-
The compensating siphon pump maintains the fuel level be-
tween the right and left tank lobes. If fuel level sender resis-
tances are not approximately the same on left and right,
remove the senders and visually inspect the level in each
lobe. If the levels are different, check the siphon pump.
Fuel level sender resistances
Float position
l~est results (Q
Down (empty) 150- 70
Up (full) 1401 -415
Fuel level sender (right side) and fuel
pump, removing
and installing
- Drain fuel from tank as described later.
- Disconnect negative cable from battery.
CAUTION-
Prior to disconnecting the battery, read the battery discon-
nection cautions given in
001 General Cautions and
Warnings.
- To access top of fuel tank, remove rear seat lower cushion by
lifting front edge
off catches.
Page 487 of 1002
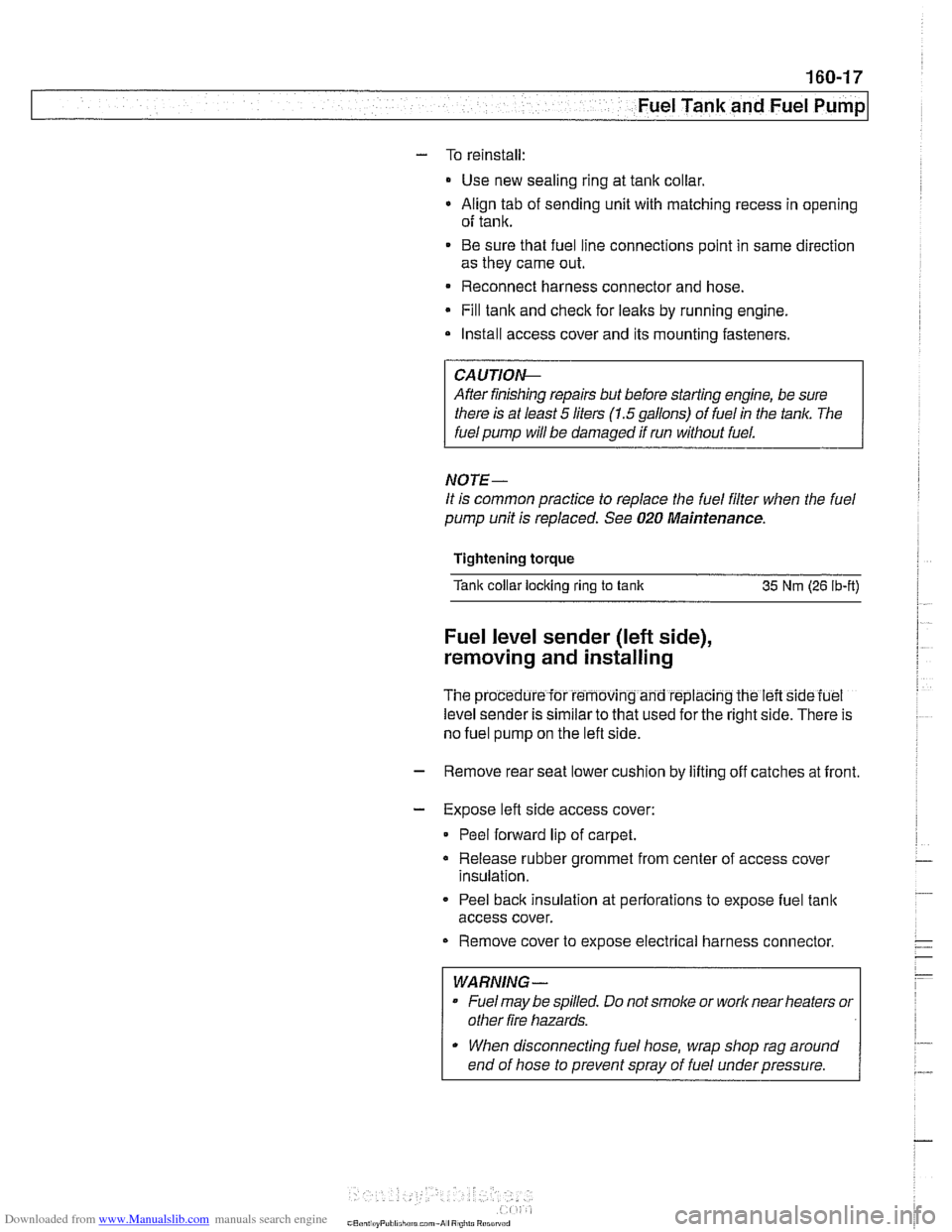
Downloaded from www.Manualslib.com manuals search engine
.- .
Fuel Tank and Fuel Pump
- To reinstall:
Use new sealing ring at tank collar.
* Align tab of sending unit with matching recess in opening
of tank.
Be sure that fuel line connections point in same direction
as they came out.
Reconnect harness connector and hose.
Fill tank and check for leaks by running engine.
Install access cover and its mounting fasteners.
CAUTIOI\C
After finishing repairs but before starting engine, be sure
there is at least
5 liters (1.5 gallons) of fuel in the tank. The
NOTE-
It is common practice to replace the fuel filter when the fuel
pump
unit is replaced. See 020 Maintenance.
Tightening torque
Tank collar locking ring to tank 35 Nm (26 lb-ft)
Fuel level sender (left side),
removing and installing
The procedure for removing and replacing the left side fuel
level sender is
simllar to that used for the r~ght side. There is
no fuel pump on the left side.
- Remove rear seat lower cushion by lifting off catches at front.
- Expose left side access cover:
- Peel forward lip of carpet.
Release rubber grommet from center of access cover
insulation.
Peel back insulation at
perforations to expose fuel tank
access cover.
Remove cover to expose electrical harness connector.
WARNING-
Fuel may be spilled. Do not smoke or work near heaters or
other fire hazards.
When disconnecting fuel hose, wrap shop rag around
end of hose to prevent spray of fuel under pressure.
Page 488 of 1002
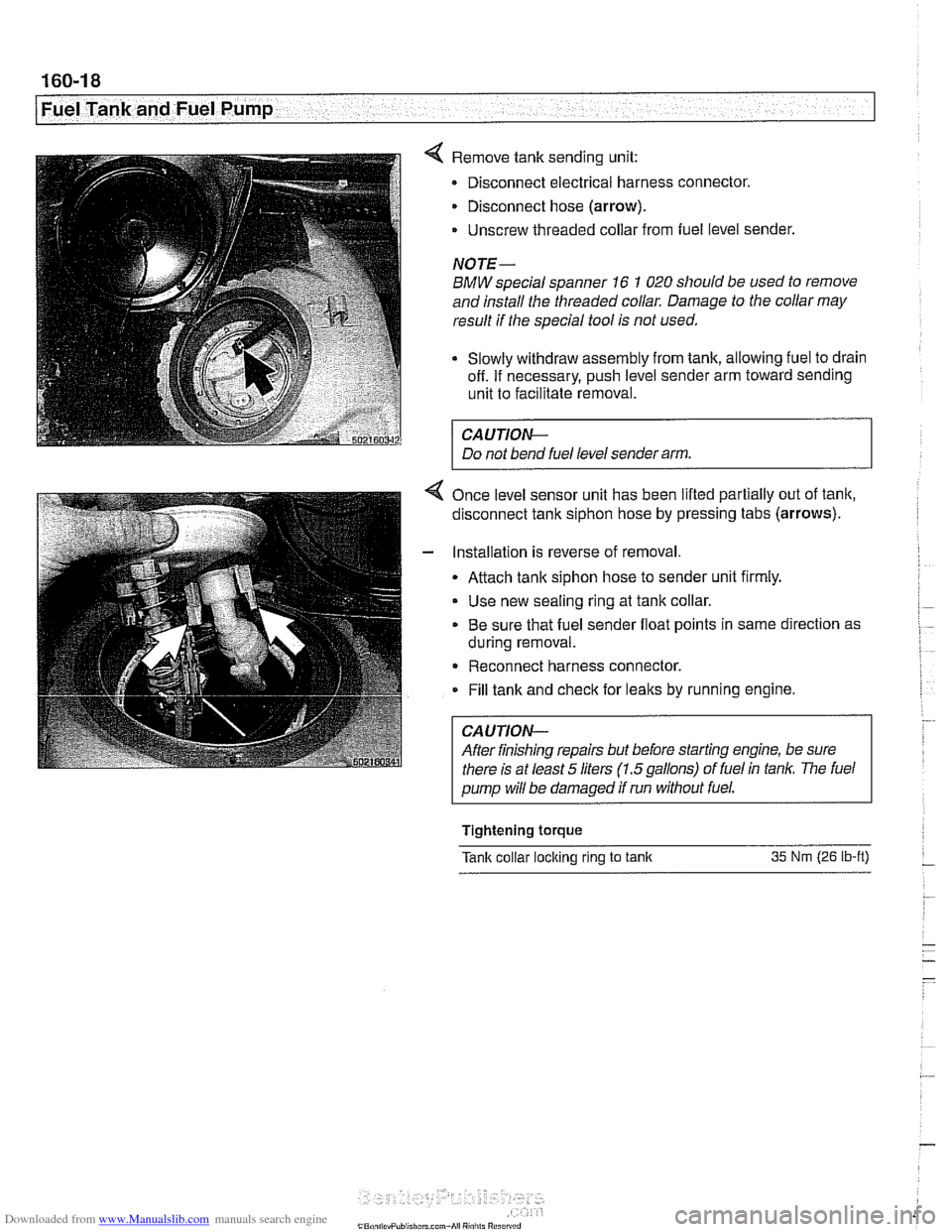
Downloaded from www.Manualslib.com manuals search engine
/ ~uel Tank and Fuel Pump
4 Remove tank sending unit:
Disconnect electrical harness connector.
Disconnect hose (arrow).
- Unscrew threaded collar from fuel level sender.
NOTE-
BMW special spanner 16 1 020 should be used to remove
and install the threaded collar. Damage to the collar may
result if the special tool is not used.
Slowly withdraw assembly from tank, allowing fuel to drain
off. If necessary, push level sender arm toward sending
unit to facilitate removal.
CA UTIOW-
Do not bend fuel level sender arm.
4 Once level sensor unit has been lifted partially out of tank,
disconnect tank siphon hose by pressing tabs (arrows).
- Installation is reverse of removal
Attach tank siphon hose to sender unit firmly.
Use new sealing ring at tank collar.
. Be sure that fuel sender float points in same direction as
during removal.
- Reconnect harness connector.
Fill tank and
check for leaks by running engine.
CAUTION-
After finishing repairs but before starting engine, be sure
there is at least
5 liters (1.5gallons) of fuel in tan/(. The fuel
pump will be damaged if run without fuel.
Tightening
torque
Tank collar loclting rlng to tanlt 35 Nm (26 lb-ft) -
Page 489 of 1002
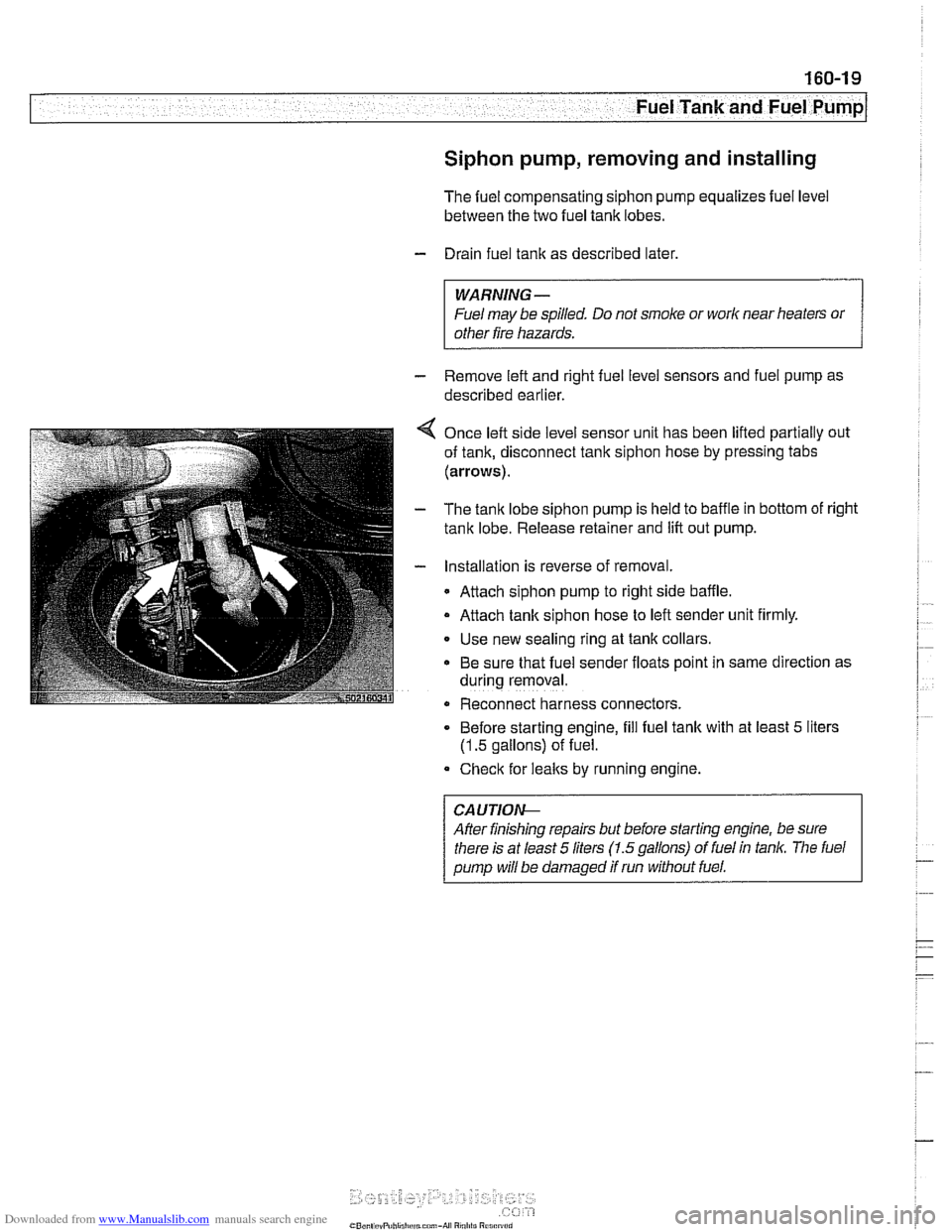
Downloaded from www.Manualslib.com manuals search engine
7 .- A Fuel Tank and Fuel Pump
Siphon pump, removing and installing
The fuel compensating siphon pump equalizes fuel level
between the two fuel tank lobes.
- Drain fuel tank as described later,
WARNING -
Fuel may be spilled. Do not smoke or work near heaters or
other fire hazards.
- Remove left and right fuel level sensors and fuel pump as
described earlier.
4 Once left side level sensor unit has been lifted partially out
of tank, disconnect tank siphon hose by pressing tabs
(arrows).
- The tank lobe siphon pump is held to baffle in bottom of right
tank lobe. Release retainer and lift out pump.
- Installation is reverse of removal.
Attach siphon pump to right side baffle.
Attach tank siphon hose to left sender unit firmly.
Use new sealing ring at tank collars
Be sure that fuel sender floats point in same direction as
during removal.
Reconnect harness connectors.
. Before starting engine, fill fuel tank with at least 5 liters
(1.5 gallons) of fuel.
Check for
leaks by running engine.
Afler finishing repairs but before starting engine, be sure
Page 492 of 1002
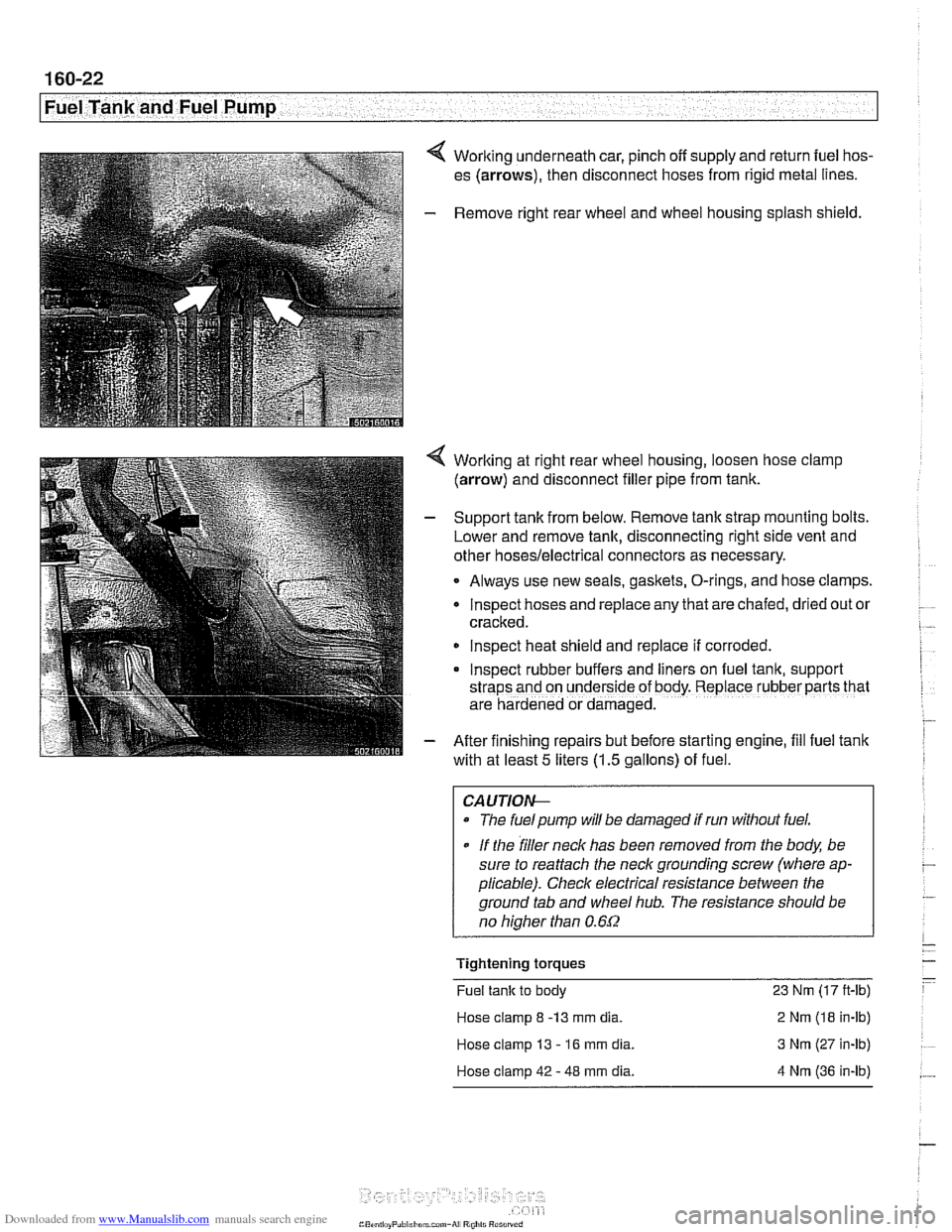
Downloaded from www.Manualslib.com manuals search engine
160-22
Fuel Tank and Fuel Pump
4 Working underneath car, pinch off supply and return fuel hos-
es (arrows), then disconnect hoses from rigid metal lines.
- Remove right rear wheel and wheel housing splash shield.
4 Worlting at right rear wheel housing, loosen hose clamp
(arrow) and disconnect filler pipe from tank.
- Support tank from below. Remove tank strap mounting bolts.
Lower and remove tank, disconnecting right side vent and
other
hoses/electrical connectors as necessary.
Always use new seals, gaskets, O-rings, and hose clamps.
lnspect hoses and replace any that are chafed,
dr~ed out or
cracked.
lnspect heat shield and replace if corroded.
Inspect rubber buffers and
hers on fuel tank, support
straps and on underside of body. Replace rubber parts that
are hardened or damaged.
- After finishing repairs but before starting engine, fill fuel tank
with at least
5 liters (1.5 gallons) of fuel.
CAUTlOI+
The fuelpump will be damaged if run without fuel.
* If the filler neck has been removed from the body, be
sure to reattach the
neck grounding screw (where ap-
plicable). Check electrical resistance between the
ground tab and wheel
hub. The resistance should be
no
hiaher than 0.6f2
Tightening torques
Fuel tank to body 23 Nm (17 ft-lb)
Hose clamp
8 -13 mm dia. 2 Nm (18 in-lb)
Hose clamp 13
- 16 mm dia. 3 Nm (27 in-lb)
Hose clamp 42
- 48 mm dia. 4 Nm (36 in-lb)
Page 501 of 1002
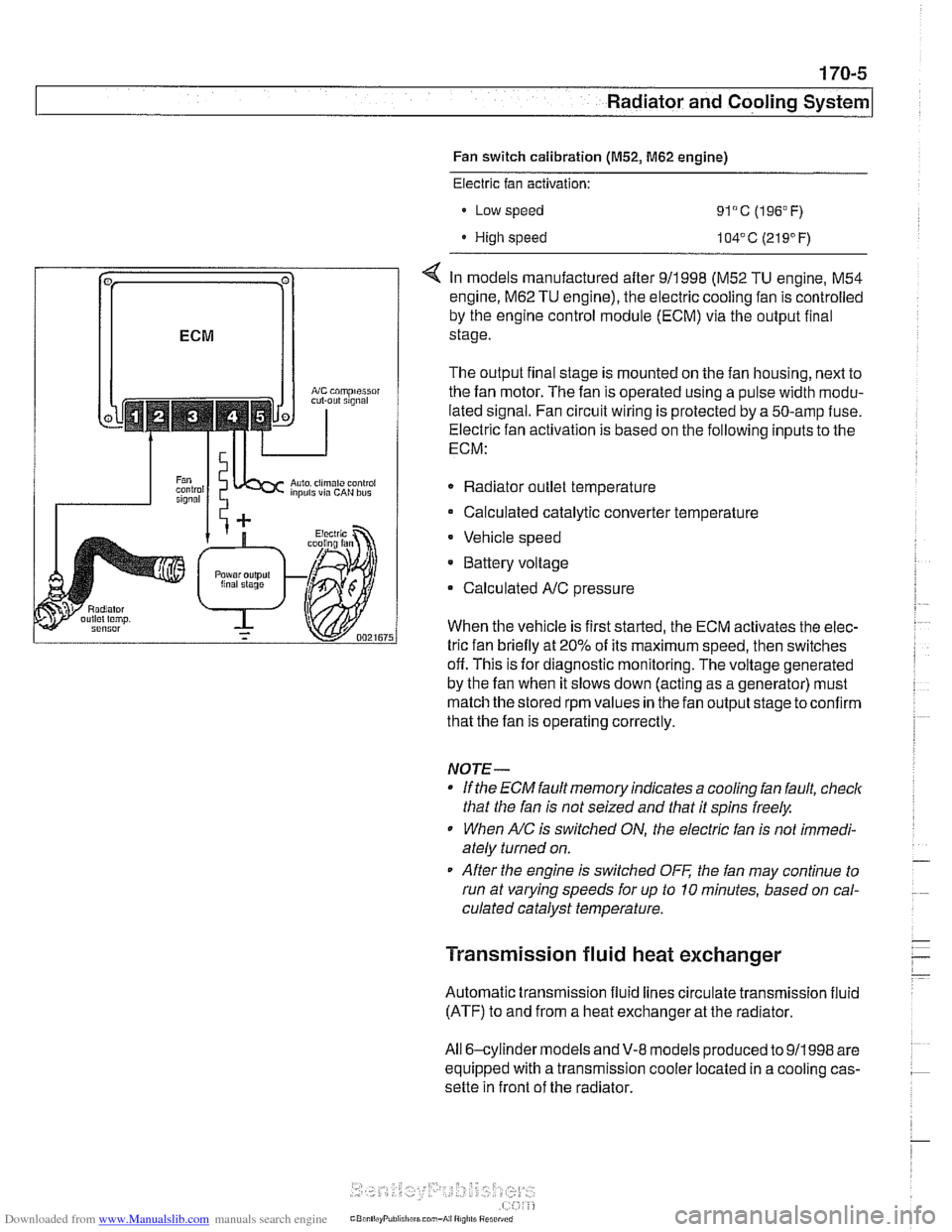
Downloaded from www.Manualslib.com manuals search engine
170-5
Radiator and Cooling System
Fan switch calibration (M52, M62 engine)
coniprairoi OUt rlgnal
Auto. ciimilte ~ontioi inpuls via CAN bus
Electric fan activation:
Low speed
91°C (196°F)
High speed 104' C (21 9' F)
< In models manufactured after 911998 (M52 TU engine, M54
engine.
M62 TU engine), the electric cooling fan is controlled
by the engine control module (ECM) via the output final
stage.
The output final stage is mounted on the fan housing, next to
the fan motor. The fan is operated using a pulse width modu-
lated signal. Fan circuit wiring is protected by a 50-amp fuse.
Electric fan activation is based on the following inputs to the
ECM:
Radiator outlet temperature
Calculated catalytic converter temperature
Vehicle speed
* Battery voltage
Calculated
A/C pressure
When the vehicle is first started, the ECM activates the elec-
tric fan briefly at 20% of its maximum speed, then switches
off. This is for diagnostic monitoring. The voltage generated
by the fan when it slows down (acting as a generator) must
match the stored rpm values in the fan output stage toconfirm
that the fan is operating correctly.
NOTE-
If the ECM fault memory indicates a cooling fan fault, check
that the fan is not seized and that it spins freely.
When
A/C is switched ON, the electric fan is not immedi-
ately turned on.
After the engine is switched
OFF the fan may continue to
run at varying speeds for up to 10 minutes, based on cal-
culated catalyst temperature.
Transmission fluid heat exchanger
Automatic transmission fluid lines circulate transmission fluid
(ATF) to and from a heat exchanger at the radiator.
All 6-cylinder
models andV-8 models produced to 911998 are
equipped with a transmission cooler located in a cooling cas-
sette in front of the radiator.
Page 503 of 1002
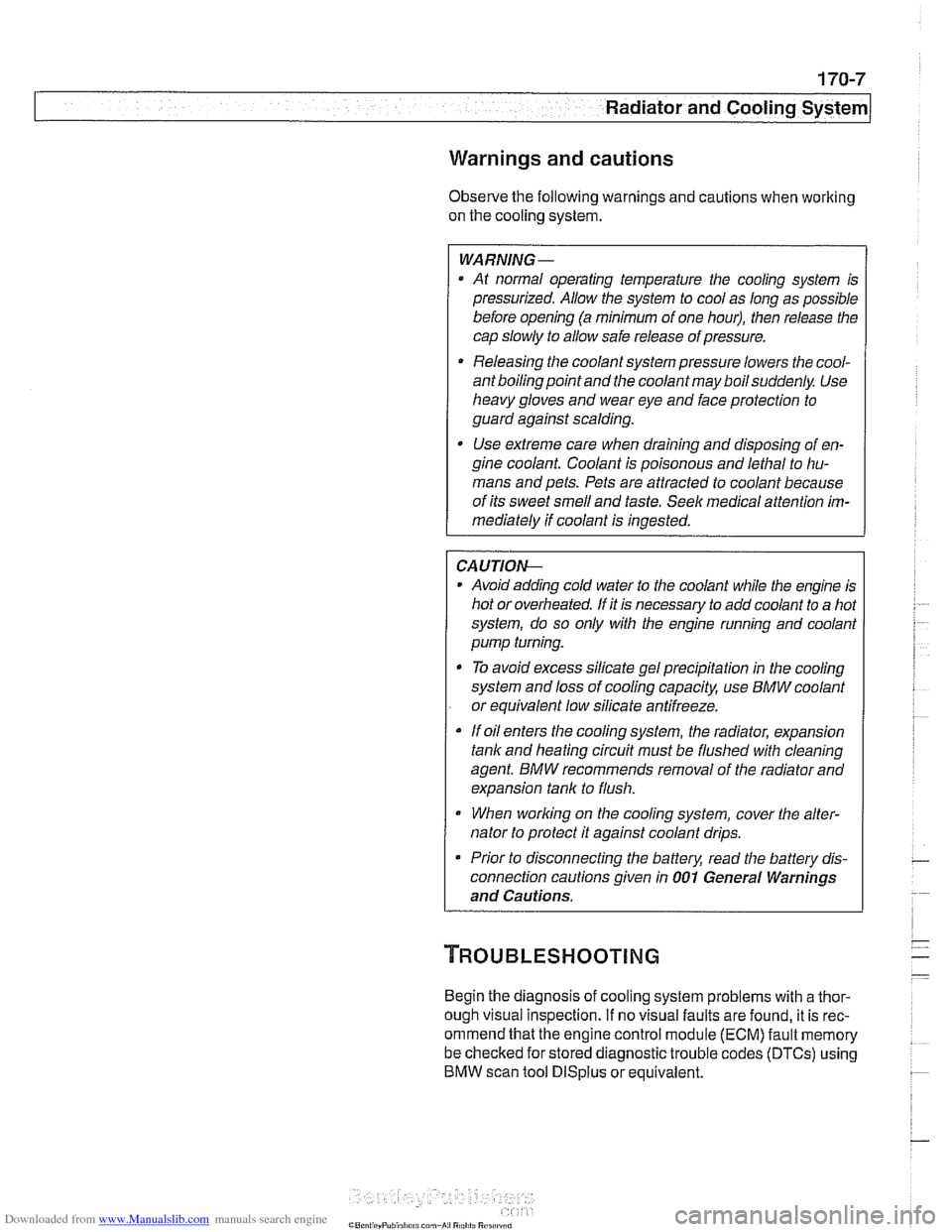
Downloaded from www.Manualslib.com manuals search engine
Warnings and cautions
Obse~e the following warnings and cautions when worlting
on the cooling system.
WARNING -
. At normal operating temperature the cooling system is
pressurized. Allow the system to cool as long as possible
before opening (a minimum of one hour), then release the
cap slowly to allow safe release ofpressure.
a Releasing the coolant system pressure lowers the cool-
ant boilingpoint and the coolant may boil suddenly. Use
1 heavy and wear eye and face protection to
guard against scalding.
Use extreme care when draining and disposing of en-
gine coolant. Coolant is poisonous and lethal to hu-
mans andpets. Pets are attracted to coolant because
of its sweet smell and taste. Seek medical attention im-
mediately if coolant is ingested.
CAUTIOG
Avoid adding cold water to the coolant while the engine is
hot or overheated. If it is necessary to add coolant to a
hol
system, do so only with the engine running and coolanl
pump turning.
To avoid excess silicate gel precipitation in the cooling
system and loss of cooling capacity, use BMW coolant
or equivalent low silicate antifreeze.
a If oil enters the cooling system, the radiator, expansion
tank and heating circuit must be flushed with cleaning
agent. BMW recommends removal of the radiator and
expansion
tank to flush.
When
worlcing on the cooling system, cover the alter-
nator to protect it against coolant drips.
Prior to disconnecting the battery, read the battery dis-
connection cautions given in
001 General Warnings
and Cautions.
Begin the diagnosis of cooling system problems with a thor-
ough visual inspection.
If no visual faults are found, it is rec-
ommend that the engine control module (ECM) fault memory
be checked for stored diagnostic trouble codes
(DTCs) using
BMW scan tool
DlSplus or equivalent.