check engine BMW 528i 1998 E39 Workshop Manual
[x] Cancel search | Manufacturer: BMW, Model Year: 1998, Model line: 528i, Model: BMW 528i 1998 E39Pages: 1002
Page 610 of 1002
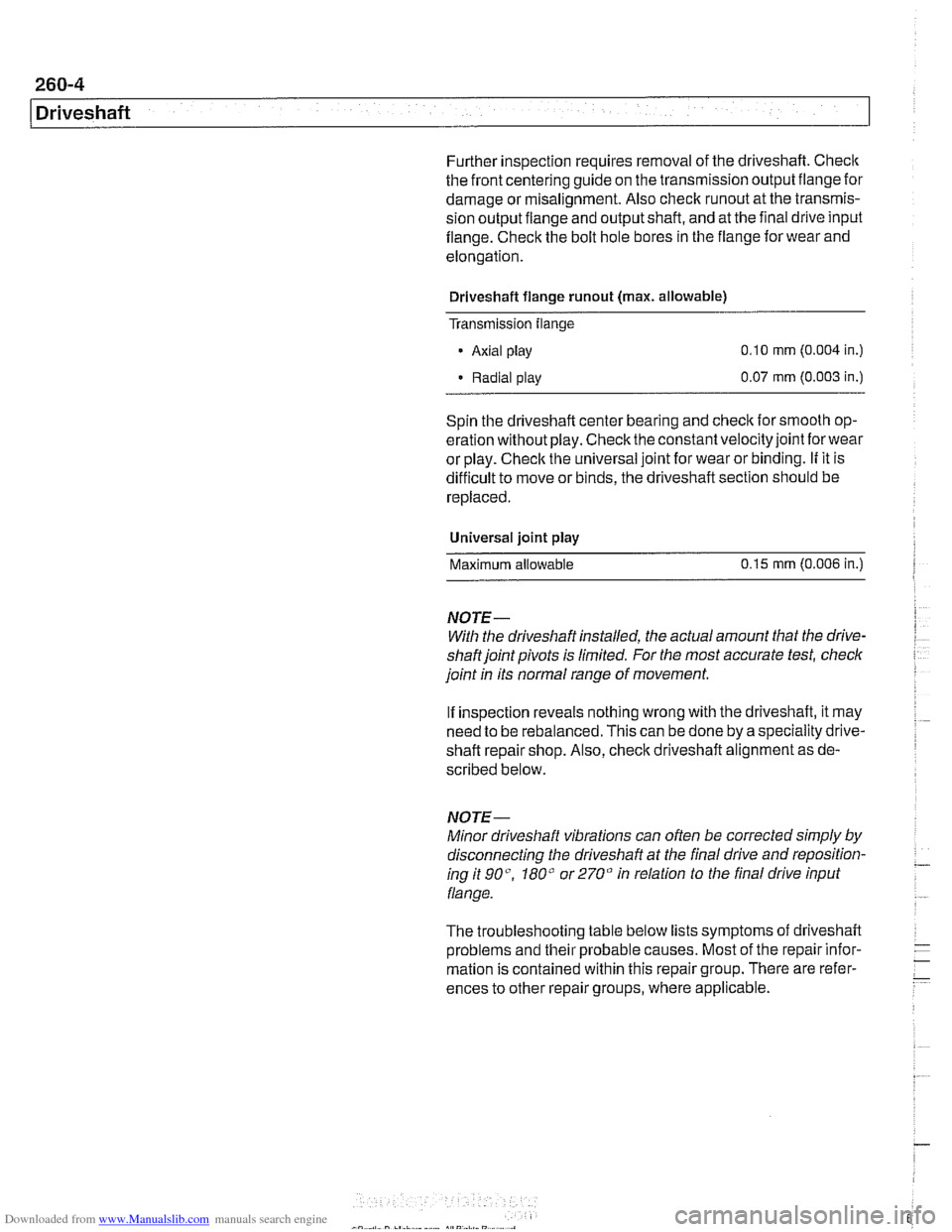
Downloaded from www.Manualslib.com manuals search engine
1 Driveshaft
Further inspection requires removal of the driveshaft. Checlc
the front centering guide on the transmission output flange for
damage or
misalignment. Also check runout at the transmis-
sion output fiange and output shaft, and at the final drive input
fiange. Check the bolt hole bores in the flange for wear and
elongation.
Driveshaft flange
runout (max. allowable)
Transmission
flange
- Axial play 0.10 mm (0.004 in.)
Radial play 0.07
mm (0.003 in.)
Spin the driveshaft center bearing and
check ior smooth op-
eration without play. Check the constant velocity joint
forwear
or play. Checlc the universal joint for wear or binding. If it is
difficult to move or binds, the driveshaft section should be
replaced.
Universal joint
play
Maximum allowable 0.15
mm (0.006 in.)
NOTE-
With the driveshaft installed, the actual amount that the drive-
shaftjoint pivots is limited. For the most accurate test, check
joint
in its normal range of movement.
If inspection reveals nothing wrong with the driveshaft, it may
need to be rebalanced. This can be done by a speciality drive-
shaft repair shop. Also,
checlc driveshaft alignment as de-
scribed below.
NOTE-
Minor driveshaft vibrations can often be corrected simply by
disconnecting the driveshaft at the final drive and reposition-
ing it go", 180" or 270" in relation to the final drive input
flange.
The troubleshooting table below lists symptoms
oi driveshaft
problems and their probable causes. Most of the repair infor-
mation is contained within this repair group. There are refer-
ences to other repair groups, where applicable.
Page 611 of 1002
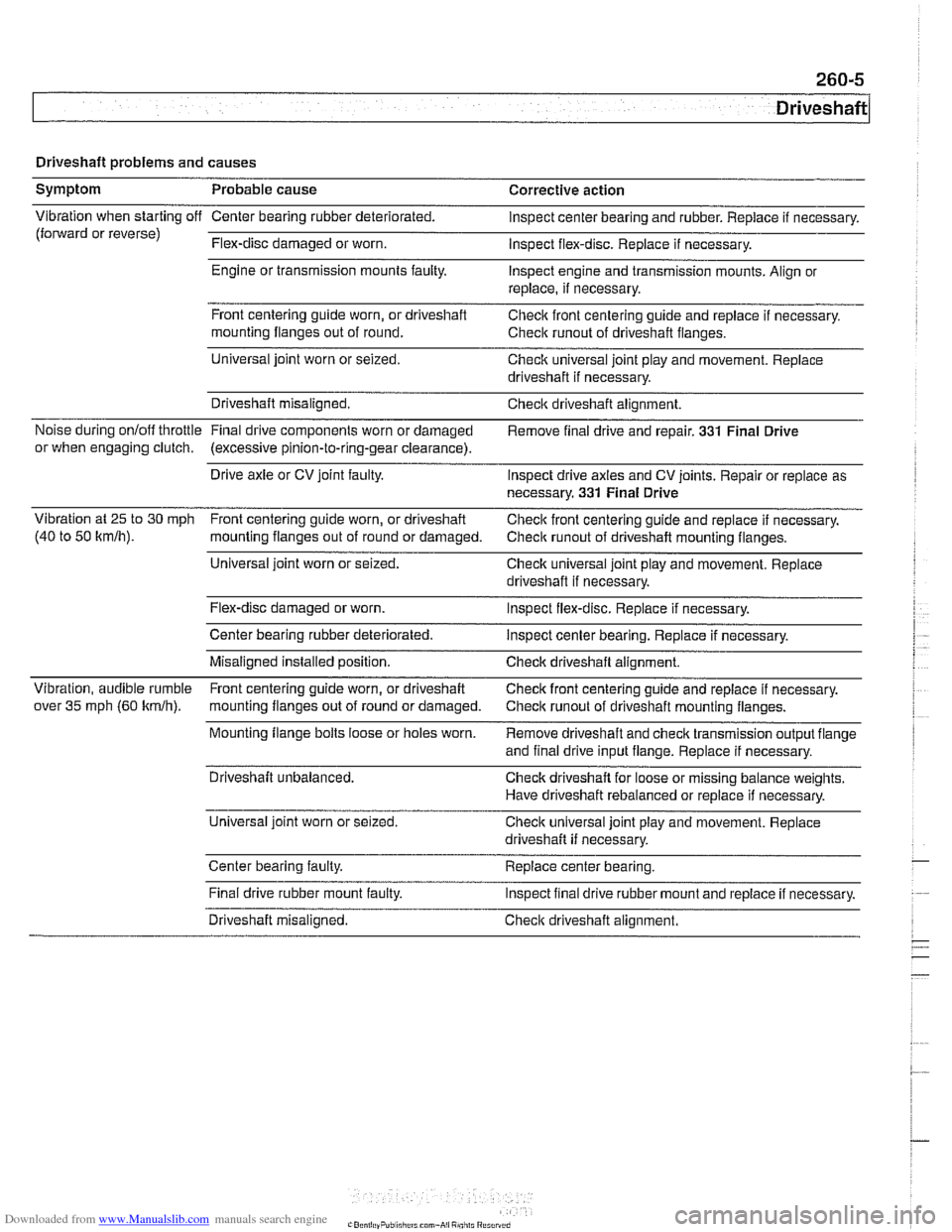
Downloaded from www.Manualslib.com manuals search engine
Driveshaft
Driveshaft problems and causes
Symptom Probable cause Corrective action
Vibration when starting off Center bearing rubber deteriorated. Inspect center bearing and rubber. Replace if necessary.
(forward or reverse)
Flex-disc damaged or worn.
Inspect flex-disc. Replace
if necessary.
Engine or transmission mounts
faulty. Inspect engine and transmission mounts. Align or
replace, if necessary.
Front centering guide worn, or driveshaft
Checic front centering guide and replace
if necessary.
mounting flanges out of round.
Check
runout of driveshaft flanges.
Universal joint worn or seized.
Check universal joint play and movement. Replace
driveshaft if necessary.
Driveshaft misaligned. Check driveshaft alignment.
Noise during onloff throttle Final
drive components worn or damaged
Remove final drive and repair. 331 Final Drive
or when engaging clutch. (excessive pinion-to-ring-gear clearance).
Drive axle or CV joint faulty.
Inspect drive axles and CV joints. Repair or replace as
necessary.
331 Final Drive
Vibration at 25 to
30 mph
Front centering guide worn, or driveshaft
Check front centering guide and replace if necessary.
(40 to 50
kmlh). mounting flanges out of round or damaged.
Check runout of driveshaft mounting flanges.
Universal joint worn or seized.
Check universal joint play and movement. Replace
driveshaft if necessary.
Flex-disc damaged or worn.
Inspect flex-disc. Replace if necessary.
Center bearing rubber deteriorated.
Inspect center bearing. Replace if necessary.
Misaligned installed position. Check driveshaft alignment.
Vibration, audible rumble Front centering guide worn, or driveshaft
Check front centering guide and replace
if necessary.
over
35 mph (60 kmlh). mounting flanges out of rouncl or damaged.
Check runout of driveshaft mounting flanges. - -
Mounting flange bolts loose or holes worn.
Remove driveshaft and check transmission output flange
and final drive input flange. Replace if necessary.
Driveshaft unbalanced. Check driveshaft for loose or missing balance weights.
Have driveshaft rebalanced or replace if necessary.
Universal ioint worn or seized.
Check universal ioint
~lav and movement. Reolace ' .. driveshaft if necessary.
Center bearing faulty.
Replace center bearing.
.
Final drive rubber mount faulty.
Inspect final drive rubber mount and repiace if necessary.
Driveshaft misaligned.
Check driveshaft alignment.
Page 613 of 1002
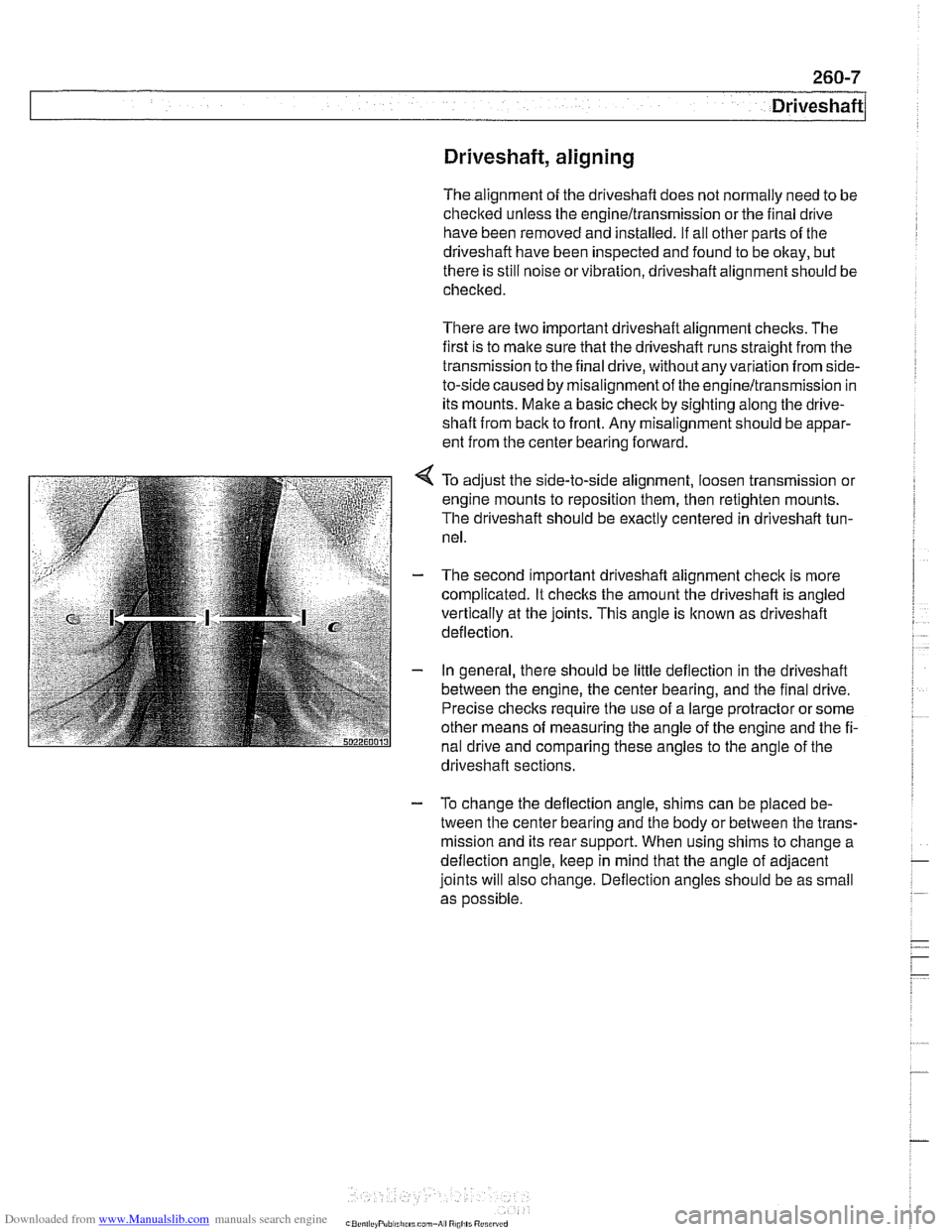
Downloaded from www.Manualslib.com manuals search engine
Driveshaft, aligning
The alignment of the driveshaft does not normally need to be
checked unless the engineltransmission or the final drive
have been removed and installed. if ail other parts of the
driveshaft have been inspected and found to be okay, but
there is still noise or vibration, driveshaft alignment should be
checked.
There are two important driveshaft alignment checks. The
first is to make sure that the driveshaft runs straight from the
transmission to the final drive, without any variation from
side-
to-side caused by misalignment of the engineltransmission in
its mounts. Make a basic check by sighting along the
drive-
shaft from back to front. Any misalignment should be appar-
ent from the center bearing forward.
To adjust the side-to-side alignment, loosen transmission or
engine mounts to reposition them, then retighten mounts.
The driveshaft should be exactly centered in driveshaft tun-
nel.
The second important driveshaft alignment check is more
complicated. It checlts the amount the driveshaft is angled
vertically at the joints. This angle is
lknown as driveshaft
deflection.
In general, there should be little deflection in the driveshaft
between the engine, the center bearing, and the final drive.
Precise checks require the use of a large protractor or some
other means of measuring the angle of the engine and the fi-
nal drive and comparing these angles to the angle of the
. . driveshaft sections.
- To change the deflection angle, shims can be placed be-
tween the center bearing and the body or between the trans-
mission and its rear support. When using shims to change a
deflection angle, keep in mind that the angle of adjacent
joints will also change. Deflection angles should be as small
as
oossible.
Page 617 of 1002
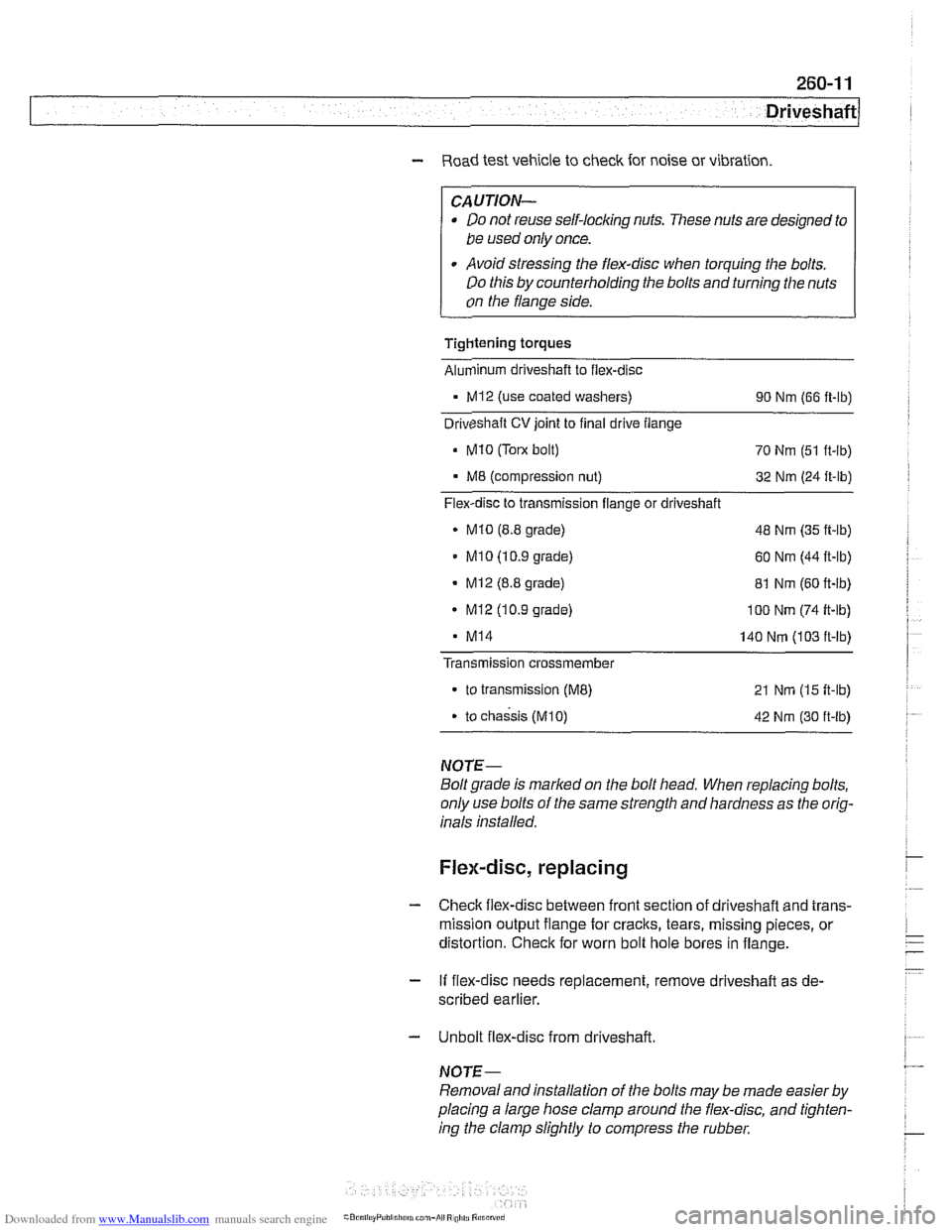
Downloaded from www.Manualslib.com manuals search engine
Driveshaft
- Road test vehicle to check for noise or vibration
CAUTION-
Do not reuse self-locking nuts. These nuts are designed to
be used only once.
Avoid stressing the flex-disc when torquing the bolts.
Do this by counterholding the bolts and turning the nuts
on the flange side.
Tightening torques
Alunlinum driveshaft to flex-disc
- MI2 (use coated washers)
90 Nm (66 ft-lb)
Driveshaft
CV joint to final drive flange
Mi0 (Tom bolt)
70 Nm (51 ft-lb)
M8 (compression nut) 32 Nm (24 ft-lb)
Flex-disc to transmission flange or driveshaft
MI0 (8.8 grade) 48 Nm (35 ft-lb)
MI 0 (1 0.9 grade) 60 Nm (44 ft-lb)
- Mi2 (8.8 grade)
81 Nm (60 ft-lb)
- MI2 (10.9 grade) I00 Nm (74 ft-lb)
MI4 140 Nm (103 ft-lb)
Transmission
crossmember
to transmission (ME) 21 Nm (15 ft-lb)
. to chassis (M10) 42 Nm (30 ft-lb)
NOTE-
Boltgrade is marked on the bolt head. When replacing bolts,
only use bolts of the same strength and hardness as the orig-
inals installed.
Flex-disc, replacing
- Checlc flex-disc between front section of driveshafl and trans-
mission output flange for craclts, tears, missing pieces, or
distortion. Check for worn bolt hole bores in flange.
- If flex-disc needs replacement, remove driveshafl as de-
scribed earlier.
- Unbolt flex-disc from driveshaft.
NOTE-
Removal andinstallation of the bolts may be made easier by
placing a large hose clamp around the flex-disc, and tighten-
ing the clamp slightly to compress the rubber.
Page 620 of 1002
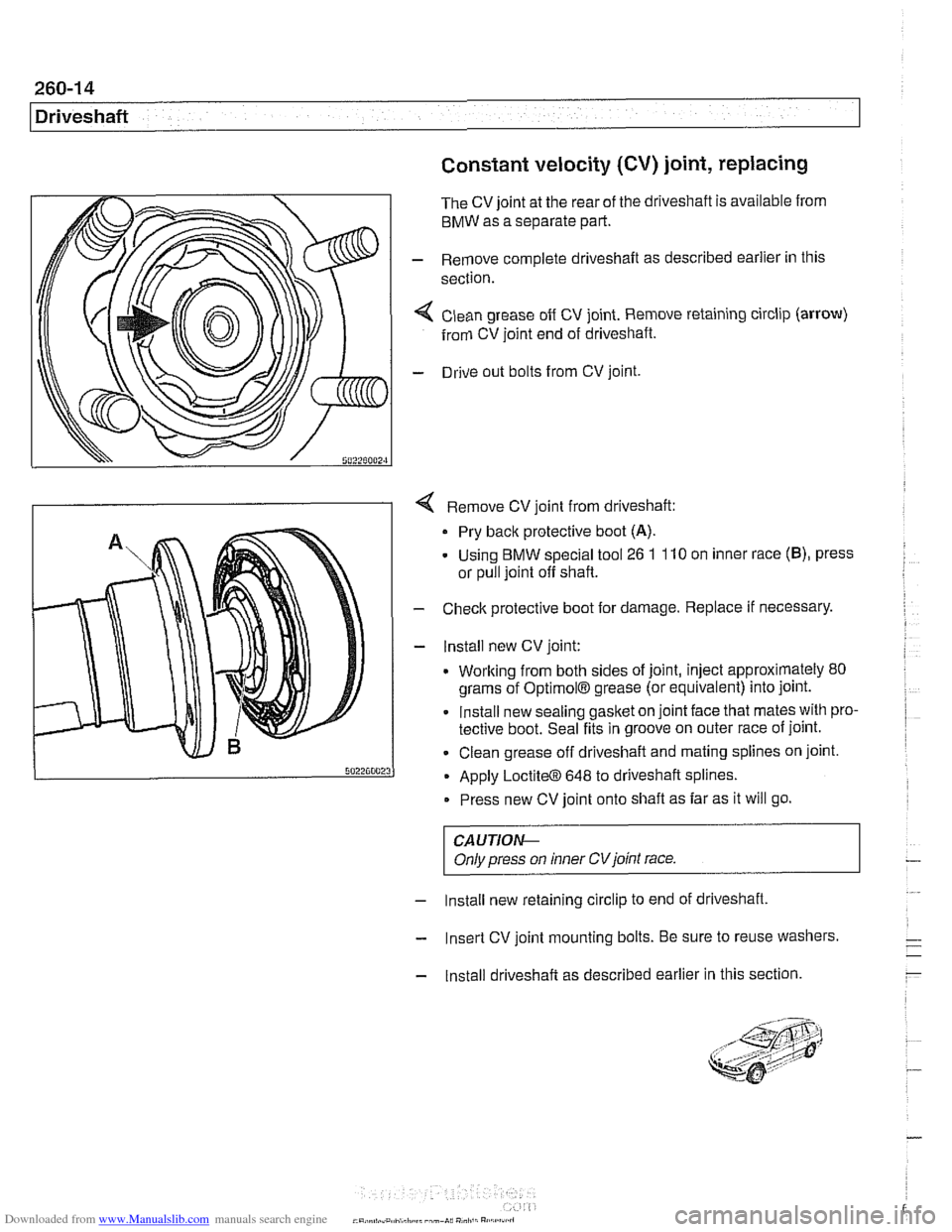
Downloaded from www.Manualslib.com manuals search engine
260-14
Driveshaft
Constant velocity (CV) joint, replacing
The CV joint at the rear of the driveshaft is available from
BMW as a separate part.
- Remove complete driveshaft as described earlier in this
section.
< Clean grease off CV joint. Remove retaining circlip (arrow)
from CV joint end of driveshaft.
- Drive out bolts from CV joint.
4 Remove CV joint from driveshaft:
Pry back protective boot
(A).
- Using BMW special tool 26 1 110 on inner race (B), press
or pull joint off shaft.
- Check protective boot for damage. Replace if necessary.
- lnstall new CV joint:
. Working from both sides of joint, inject approximately 80
grams of
OptimolB grease (or equivalent) into joint.
Install new sealing gasket on joint face that mates with pro-
tective boot. Seal fits in groove on outer race of joint.
Clean grease off driveshaft and mating splines on joint.
Apply
LoctiteO 648 to driveshaft splines.
Press new CV joint onto shaft as far as it will go.
CAUTIOI\C
Only press on inner CVjoint race.
- Install new retaining circlip to end of driveshaft,
- Insert CV joint mounting bolts. Be sure to reuse washers.
- Install driveshaft as described earlier in this section.
Page 646 of 1002
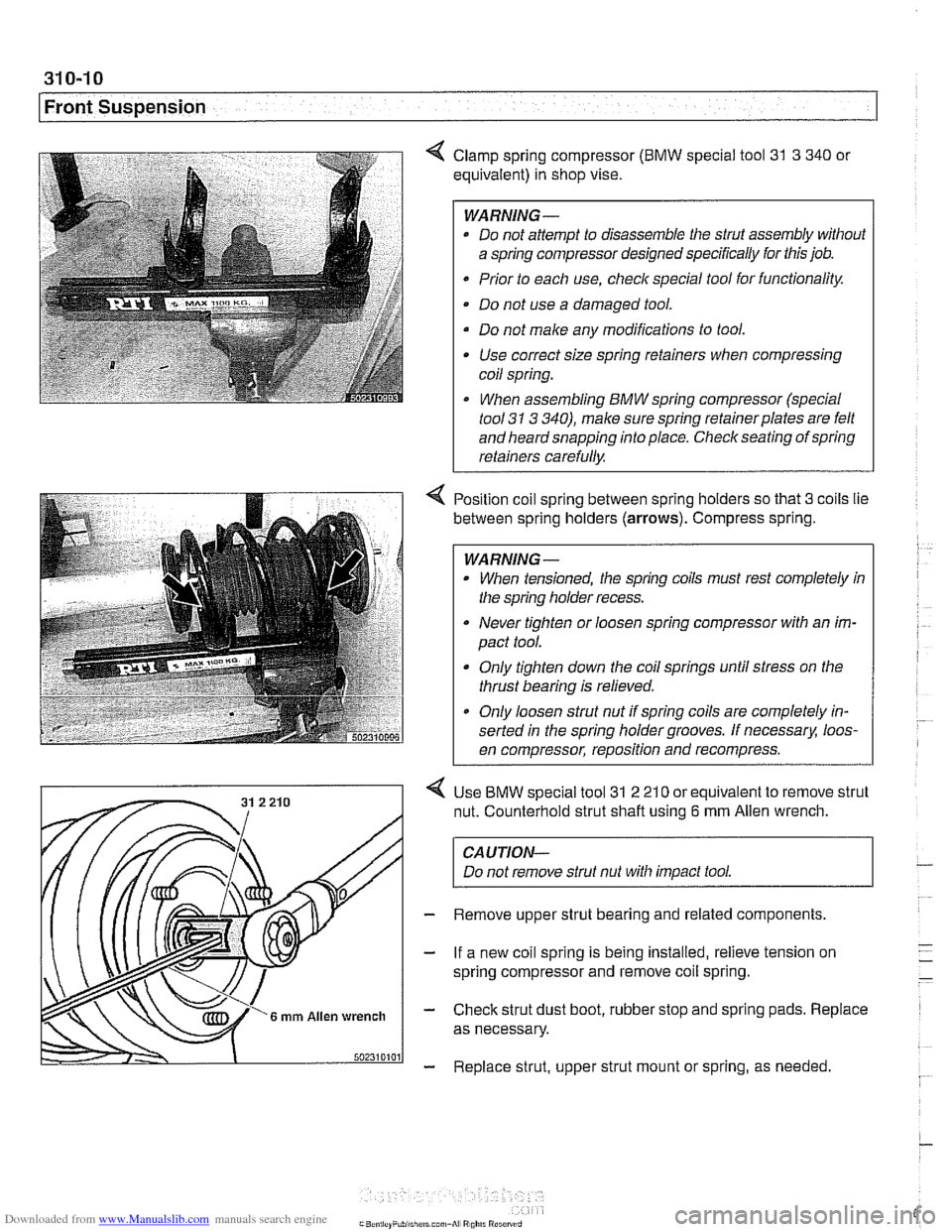
Downloaded from www.Manualslib.com manuals search engine
31 0-1 0
Front Suspension
4 Clamp spring compressor (BMW special tool 31 3 340 or
equivalent) in shop vise.
WARNING-
* Do not attempt to disassemble the strut assembly without
a spring compressor designed specifically for this job.
Prior to each use,
checlc special tool for functionality.
Do not use a damaged tool.
Do not make any modifications to tool. Use correct size spring retainers when compressing
coil spring.
I When assembling BMW spring compressor (special
tool
31 3 340), make sure spring retainerplates are felt
and heard snapping into place. Check seating of spring
retainers carefully.
Position coil spring between spring holders so that
3 coils lie
between spring holders
(arrows). Compress spring.
WARNING -
When tensioned, the spring coils must rest completely in
the spring holder recess.
Never tighten or loosen spring compressor with an im-
pact tool.
Only tighten down the coil springs until stress on the
thrust bearing is relieved.
a Only loosen strut nut if spring coils are completely in-
serted in the spring holder grooves. If
necessarx loos-
en compressor, reposition and recompress.
Use
BMW special tool 31 2 21 0 or equivalent to remove strut
nut. Counterhold strut shaft using
6 mm Allen wrench.
CAUTION-
Do not remove strut nut with impact tool.
Remove upper strut bearing and related components.
If a new coil spring is being installed, relieve tension on
spring compressor and remove coil spring.
Check strut dust boot, rubber stop and spring pads. Replace
as necessary.
Replace strut, upper strut mount or spring, as needed
Page 667 of 1002
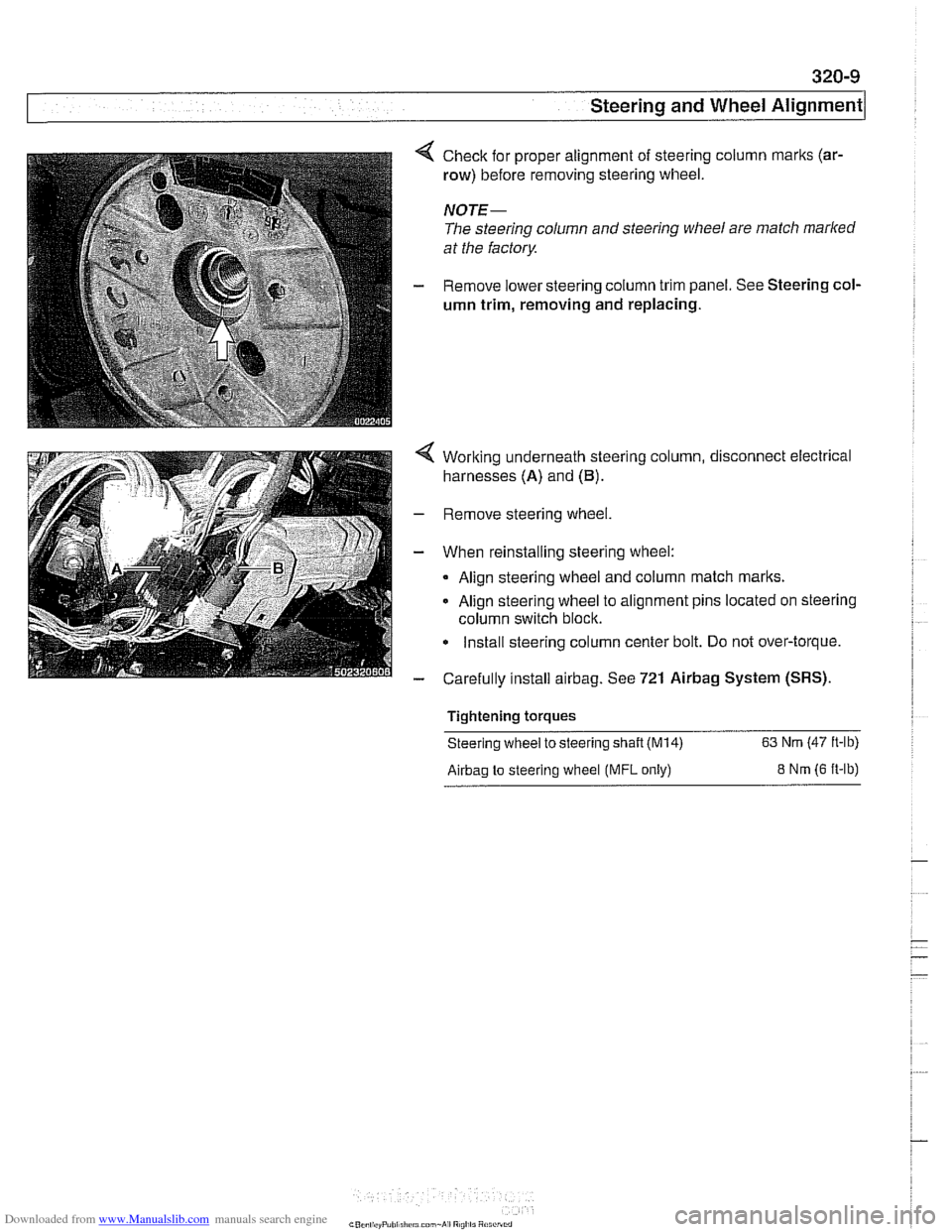
Downloaded from www.Manualslib.com manuals search engine
Check for proper alignment of steering column marks (ar-
row) before removing steering wheel.
NOTE-
The steering column and steering wheel are match marked
at the factory
Remove lower steering column trim panel. See Steering col-
umn trim, removing
and replacing.
Working underneath steering column, disconnect electrical
harnesses (A) and
(B).
Remove steering wheel.
When reinstalling steering wheel:
Align steering wheel and column match
marks.
Align steering wheel to alignment pins located on steering
column switch block.
Install steering column center bolt. Do not over-torque.
Carefully install
airbag. See 721 Airbag System (SRS).
Tightening torques
Steering wheel to steering
shaft (M14) 63 Nm (47 ft-lb)
Airbag to steering wheel (MFL only) 8 Nm (6 ft-lb)
Page 674 of 1002
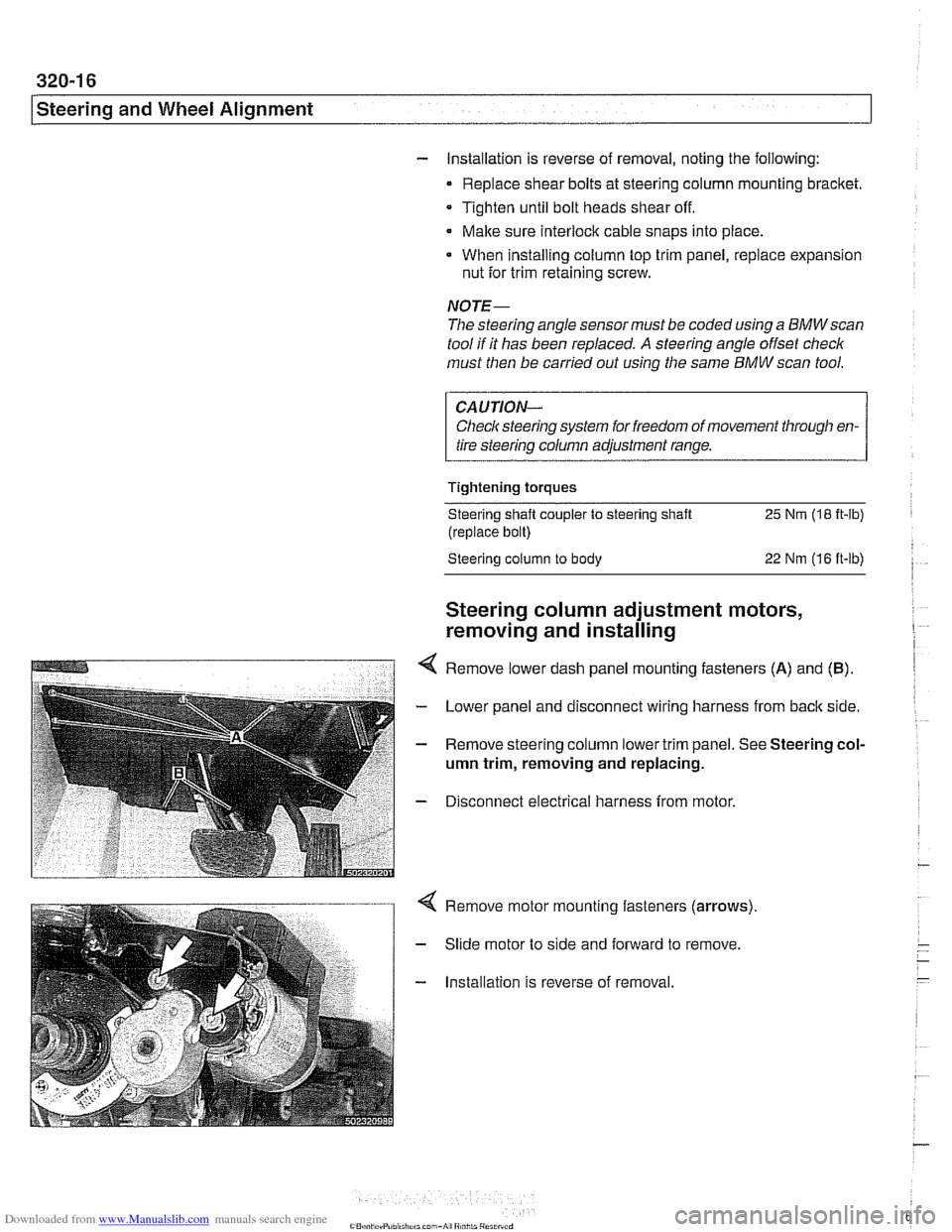
Downloaded from www.Manualslib.com manuals search engine
I Steering and Wheel Alignment
- Installation is reverse of removal, noting the following:
Replace shear bolts at steering column mounting bracket.
Tighten until bolt heads shear off.
Make sure
interlock cable snaps into place.
When installing column top trim panel, replace expansion
nut for trim retaining screw.
NOTE-
The steering angle sensor must be coded using a BMW scan
tool if it has been replaced.
A steering angle offset check
must then be carried out using the same
BMW scan tool.
CAUTION-
Check steering system for freedom of movement through en-
tire steering column
adiustment range.
Tightening torques Steering shaft coupler
to steering shaft 25 Nm (18 ft-lb)
(replace bolt)
Steering column to body
22 Nm (16 ft-lb)
Steering column adjustment motors,
removing and installing
Remove lower dash panel mounting fasteners (A) and (B).
- Lower panel and disconnect wiring harness from back side.
- Remove steering column lower trim panel. See Steering col-
umn trim, removing and replacing.
- Disconnect electrical harness from motor.
Remove motor mounting fasteners (arrows)
Slide motor to side and forward to remove.
Installation is reverse of removal.
Page 676 of 1002
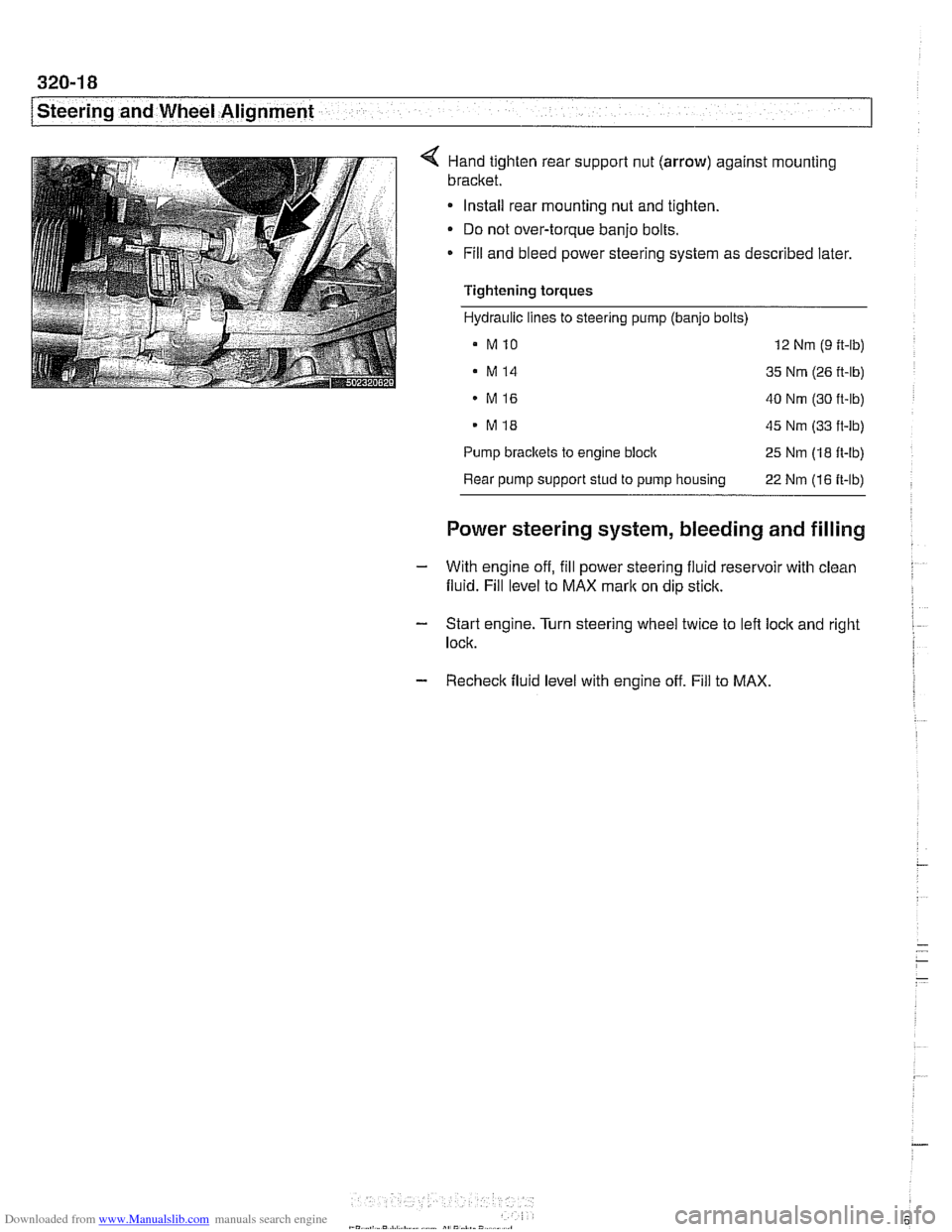
Downloaded from www.Manualslib.com manuals search engine
-
-steering and wheel -. Alignment I
< Hand tighten rear suppoll nut (arrow) against mounting
bracket.
Install rear mounting nut and tighten.
Do not over-torque banjo bolts.
* Fill and bleed power steering system as described later.
Tightening torques
Hydraulic lines to steering pump (banjo bolts)
a MlO 12 Nm (9 ft-lb)
. M14 35 Nm (26 ft-lb)
MI6 40 Nm (30 ft-lb)
. MI8 45 Nm (33 ft-lb)
Pump
brackets to engine block 25 Nm (18 ft-lb)
Rear pump support stud to pump housing
22 Nm (16 ft-lb)
Power steering system, bleeding and filling
- With engine off, fill power steering fluid reservoir with clean
fluid. Fill level to MAX
mark on dip stick.
- Start engine. Turn steering wheel twice to left lock and right I
lock.
- Recheck fluid level with engine off. Fill to MAX.
Page 690 of 1002
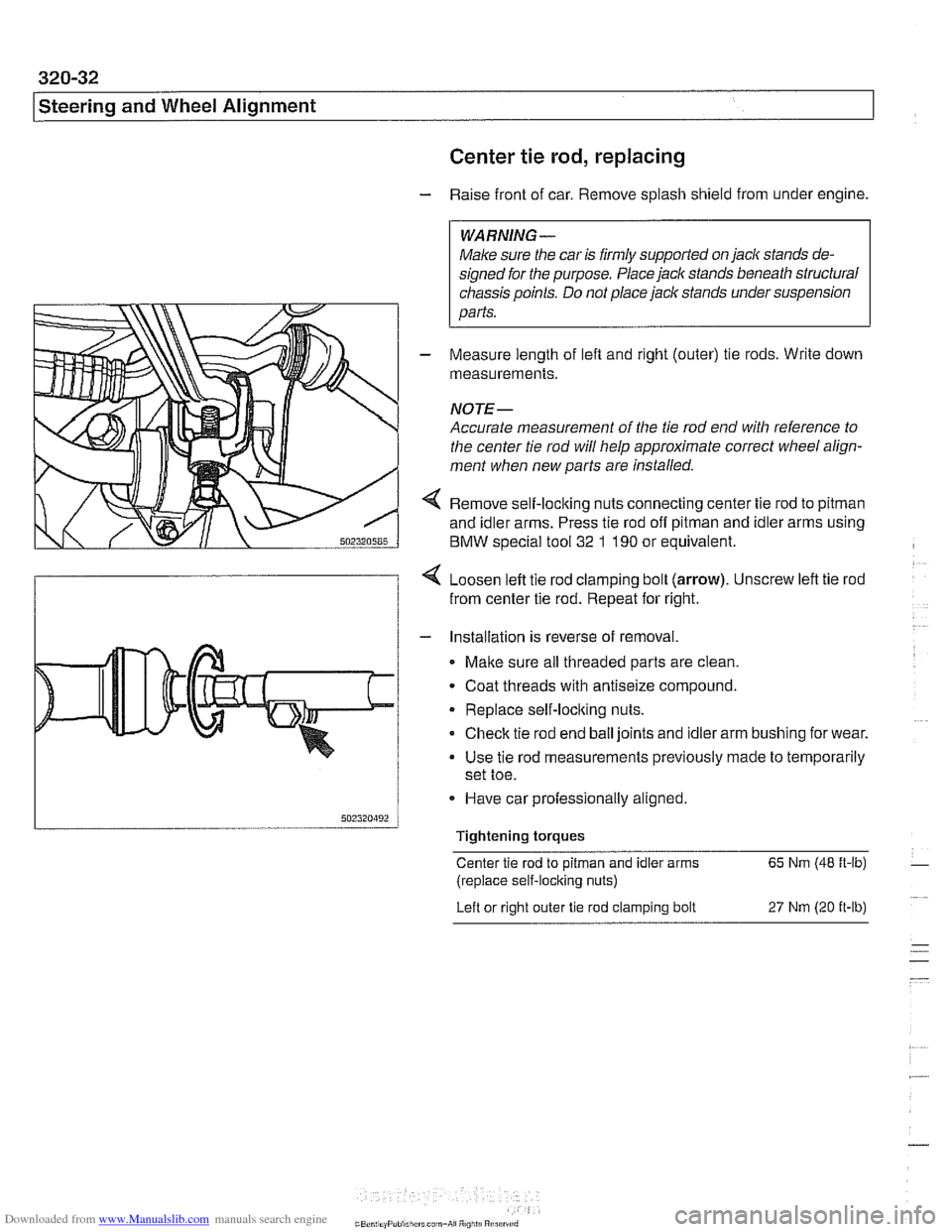
Downloaded from www.Manualslib.com manuals search engine
320-32
Steering and Wheel Alignment
Center tie
rod, replacing
- Raise front of car. Remove splash shield from under engine.
WARNING-
Make sure tlie car is firmly supported on jack stands de-
signed for the purpose. Place jack stands beneath structural
cliassis points. Do not place jack stands under suspension
parts.
- Measure length of left and right (outer) tie rods. Write down
measurements.
NOTE-
Accurate measurement of the tie rod end with reference to
the center tie rod will help approximate correct wheel align-
ment when new parts are installed.
4 Remove self-loclting nuts connecting center tie rod to pitman
and idler arms. Press tie rod off pitman and idler arms using
BMW special tool
32 1 190 or equivalent.
4 Loosen left tie rod clamping bolt (arrow). Unscrew left tie rod
from center tie rod. Repeat for right.
- Installation is reverse of removal.
Malte sure all threaded parts are clean.
. Coat threads with antiseize compound.
Replace self-loclting nuts.
Check tie rod end ball joints and idler arm bushing for wear.
Use tie rod measurements previously made to temporarily
set toe.
- Have car professionally aligned.
Tightening torques
Center tie rod to
pitman and idler arms 65 Nm (48 ft-lb)
(replace self-locking nuts)
Left or right outer
tie rod clamping bolt 27 Nm (20 it-lb)