BMW X5 2001 E53 M62TU Engine User Guide
Manufacturer: BMW, Model Year: 2001, Model line: X5, Model: BMW X5 2001 E53Pages: 37, PDF Size: 3.87 MB
Page 11 of 37
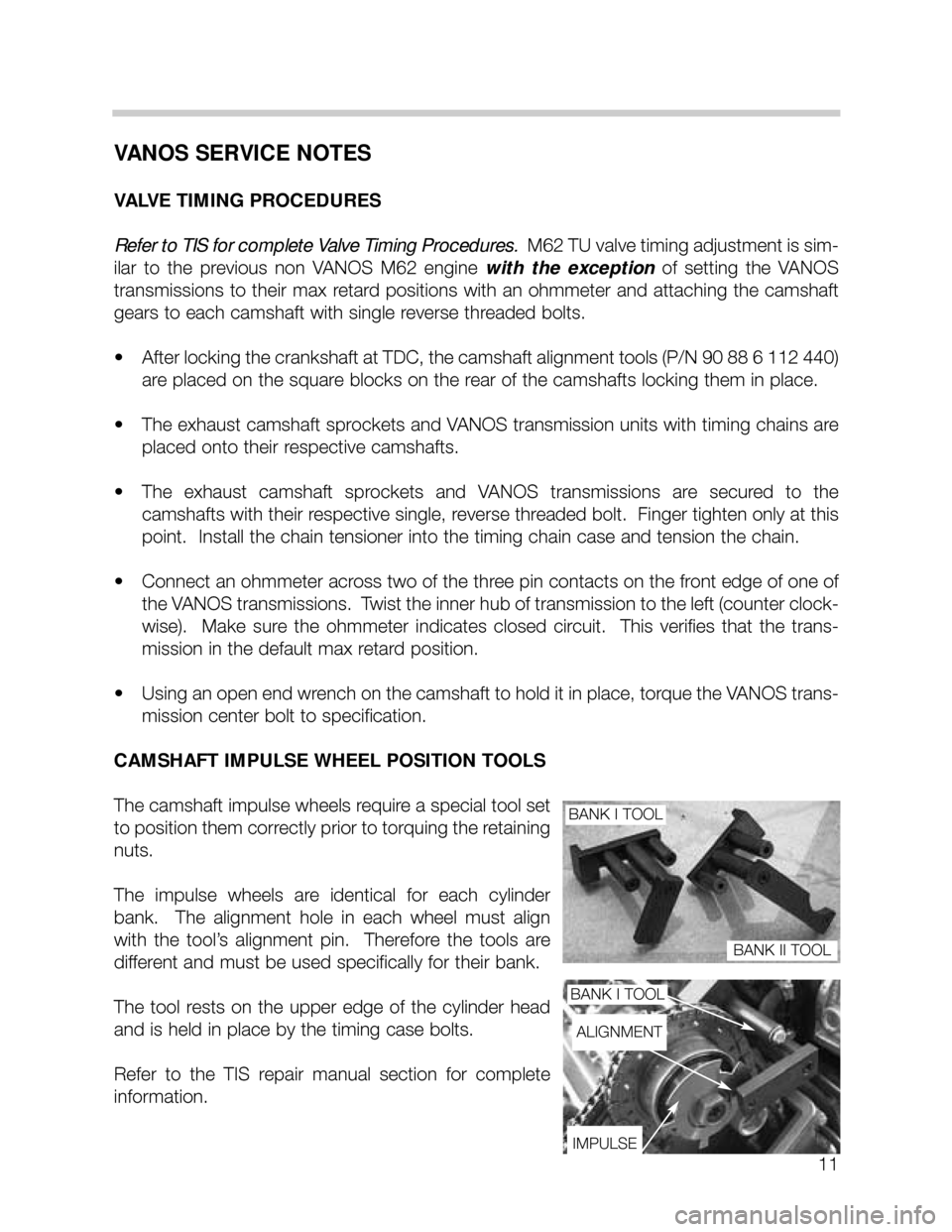
11
VANOS SERVICE NOTES
VALVE TIMING PROCEDURES
Refer to TIS for complete Valve Timing Procedures.M62 TU valve timing adjustment is sim-
ilar to the previous non VANOS M62 engine with the exceptionof setting the VANOS
transmissions to their max retard positions with an ohmmeter and attaching the camshaft
gears to each camshaft with single reverse threaded bolts.
• After locking the crankshaft at TDC, the camshaft alignment tools (P/N 90 88 6 112 440)
are placed on the square blocks on the rear of the camshafts locking them in place.
• The exhaust camshaft sprockets and VANOS transmission units with timing chains are
placed onto their respective camshafts.
• The exhaust camshaft sprockets and VANOS transmissions are secured to the
camshafts with their respective single, reverse threaded bolt. Finger tighten only at this
point. Install the chain tensioner into the timing chain case and tension the chain.
• Connect an ohmmeter across two of the three pin contacts on the front edge of one of
the VANOS transmissions. Twist the inner hub of transmission to the left (counter clock-
wise). Make sure the ohmmeter indicates closed circuit. This verifies that the trans-
mission in the default max retard position.
• Using an open end wrench on the camshaft to hold it in place, torque the VANOS trans-
mission center bolt to specification.
CAMSHAFT IMPULSE WHEEL POSITION TOOLS
The camshaft impulse wheels require a special tool set
to position them correctly prior to torquing the retaining
nuts.
The impulse wheels are identical for each cylinder
bank. The alignment hole in each wheel must align
with the tool’s alignment pin. Therefore the tools are
different and must be used specifically for their bank.
The tool rests on the upper edge of the cylinder head
and is held in place by the timing case bolts.
Refer to the TIS repair manual section for complete
information.
BANK I TOOL
BANK I TOOL
BANK II TOOL
ALIGNMENT
IMPULSE
Page 12 of 37
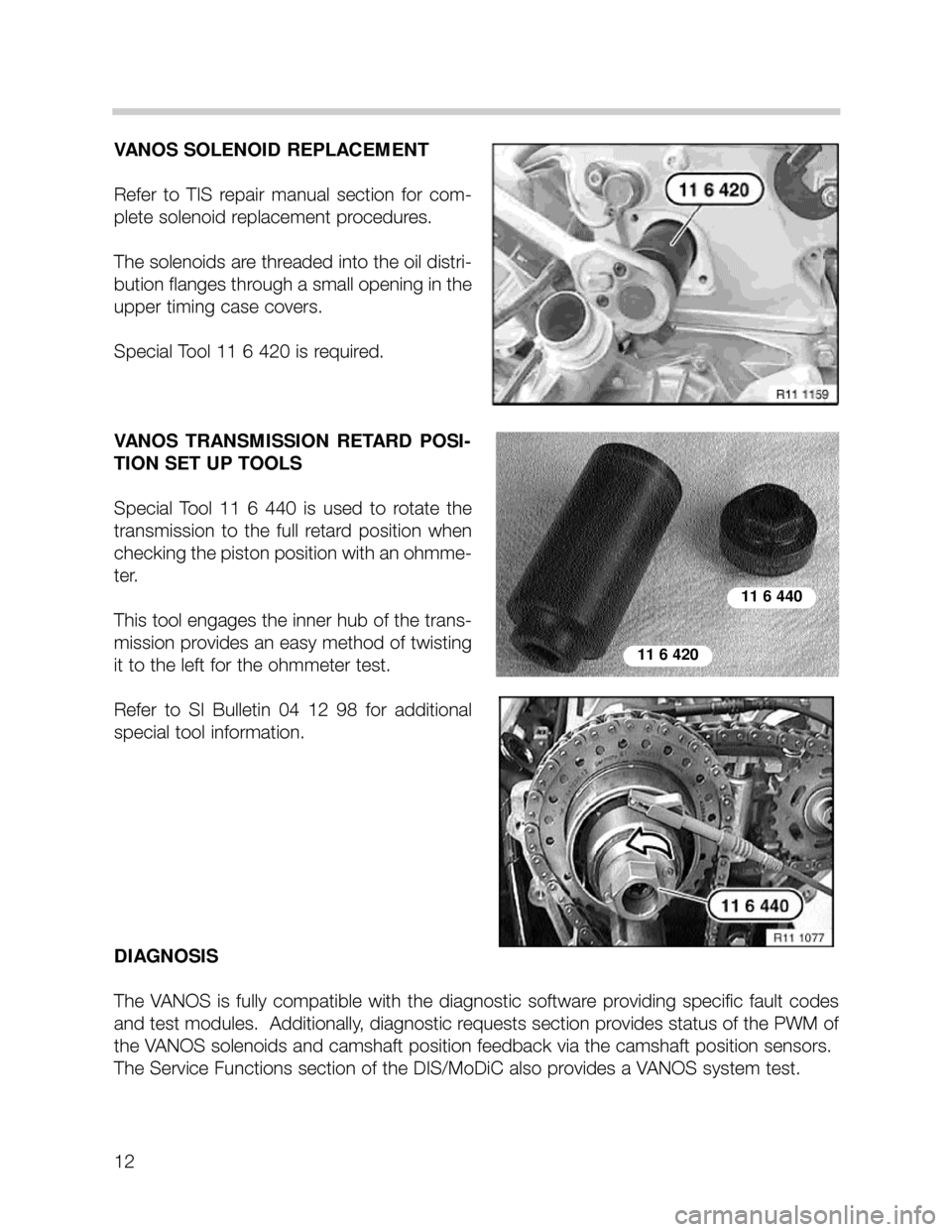
12
VANOS SOLENOID REPLACEMENT
Refer to TIS repair manual section for com-
plete solenoid replacement procedures.
The solenoids are threaded into the oil distri-
bution flanges through a small opening in the
upper timing case covers.
Special Tool 11 6 420 is required.
VANOS TRANSMISSION RETARD POSI-
TION SET UP TOOLS
Special Tool 11 6 440 is used to rotate the
transmission to the full retard position when
checking the piston position with an ohmme-
ter.
This tool engages the inner hub of the trans-
mission provides an easy method of twisting
it to the left for the ohmmeter test.
Refer to SI Bulletin 04 12 98 for additional
special tool information.
DIAGNOSIS
The VANOS is fully compatible with the diagnostic software providing specific fault codes
and test modules. Additionally, diagnostic requests section provides status of the PWM of
the VANOS solenoids and camshaft position feedback via the camshaft position sensors.
The Service Functions section of the DIS/MoDiC also provides a VANOS system test.
11 6 440
11 6 420
Page 13 of 37
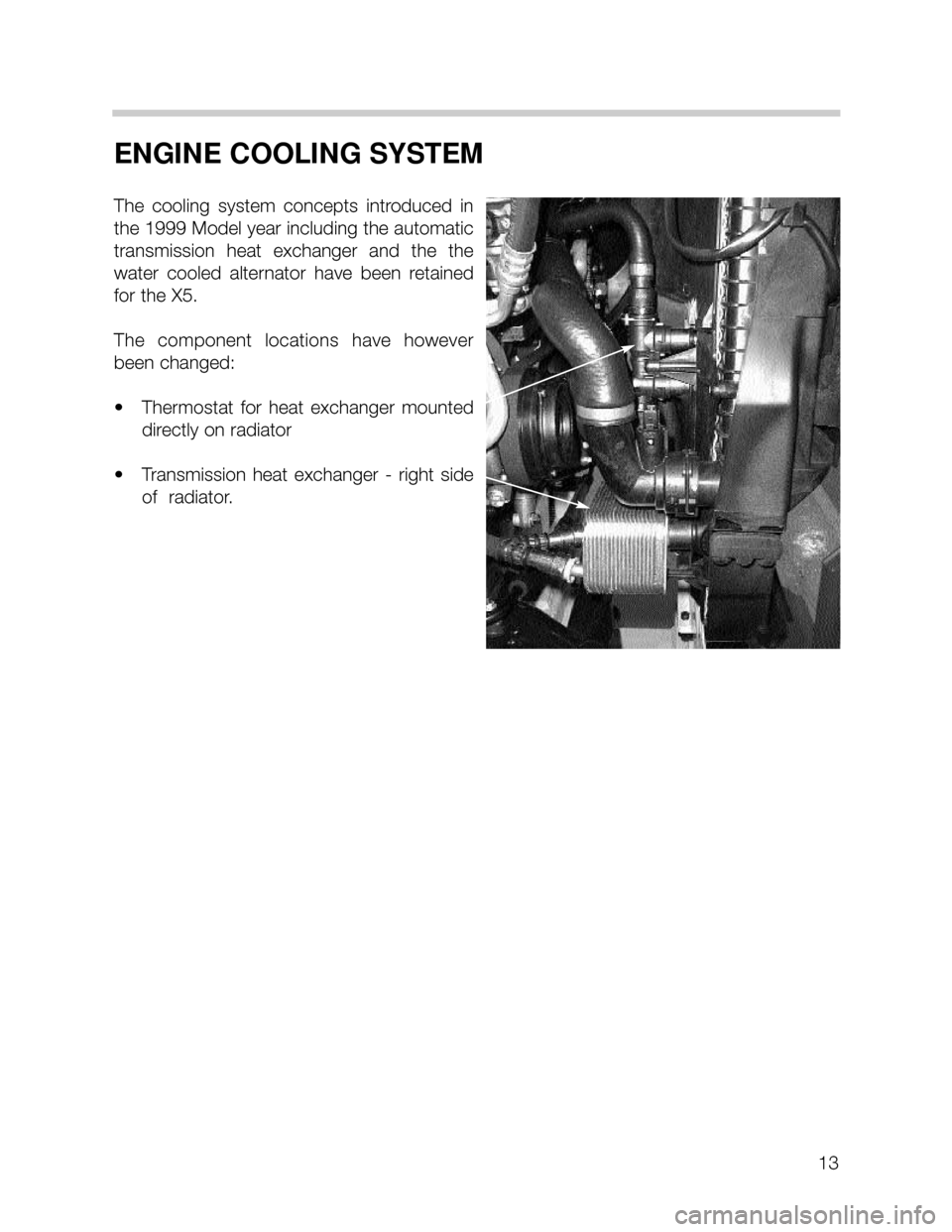
13
ENGINE COOLING SYSTEM
The cooling system concepts introduced in
the 1999 Model year including the automatic
transmission heat exchanger and the the
water cooled alternator have been retained
for the X5.
The component locations have however
been changed:
• Thermostat for heat exchanger mounted
directly on radiator
• Transmission heat exchanger - right side
of radiator.
Page 14 of 37
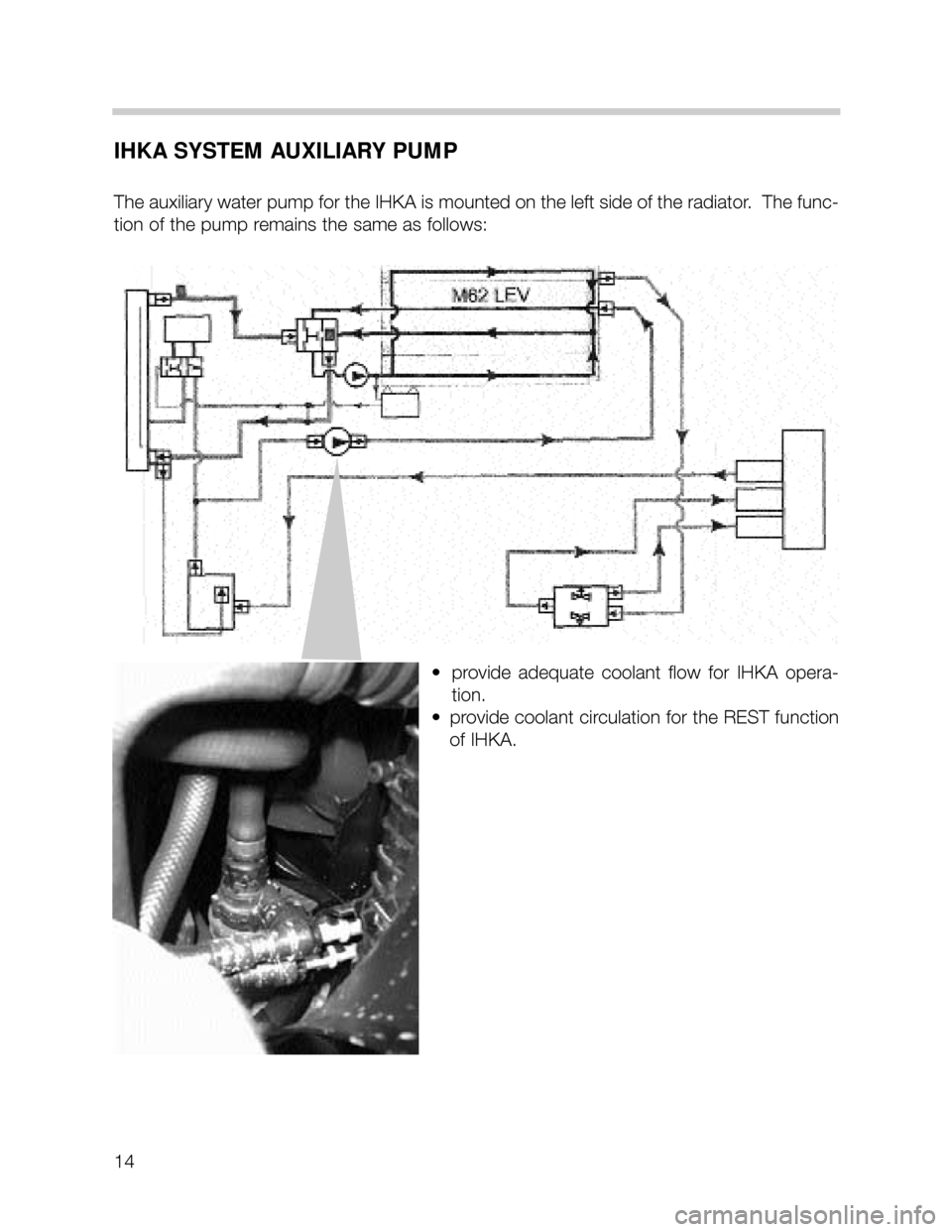
14
IHKA SYSTEM AUXILIARY PUMP
The auxiliary water pump for the IHKA is mounted on the left side of the radiator. The func-
tion of the pump remains the same as follows:
• provide adequate coolant flow for IHKA opera-
tion.
• provide coolant circulation for the REST function
of IHKA.
Page 15 of 37
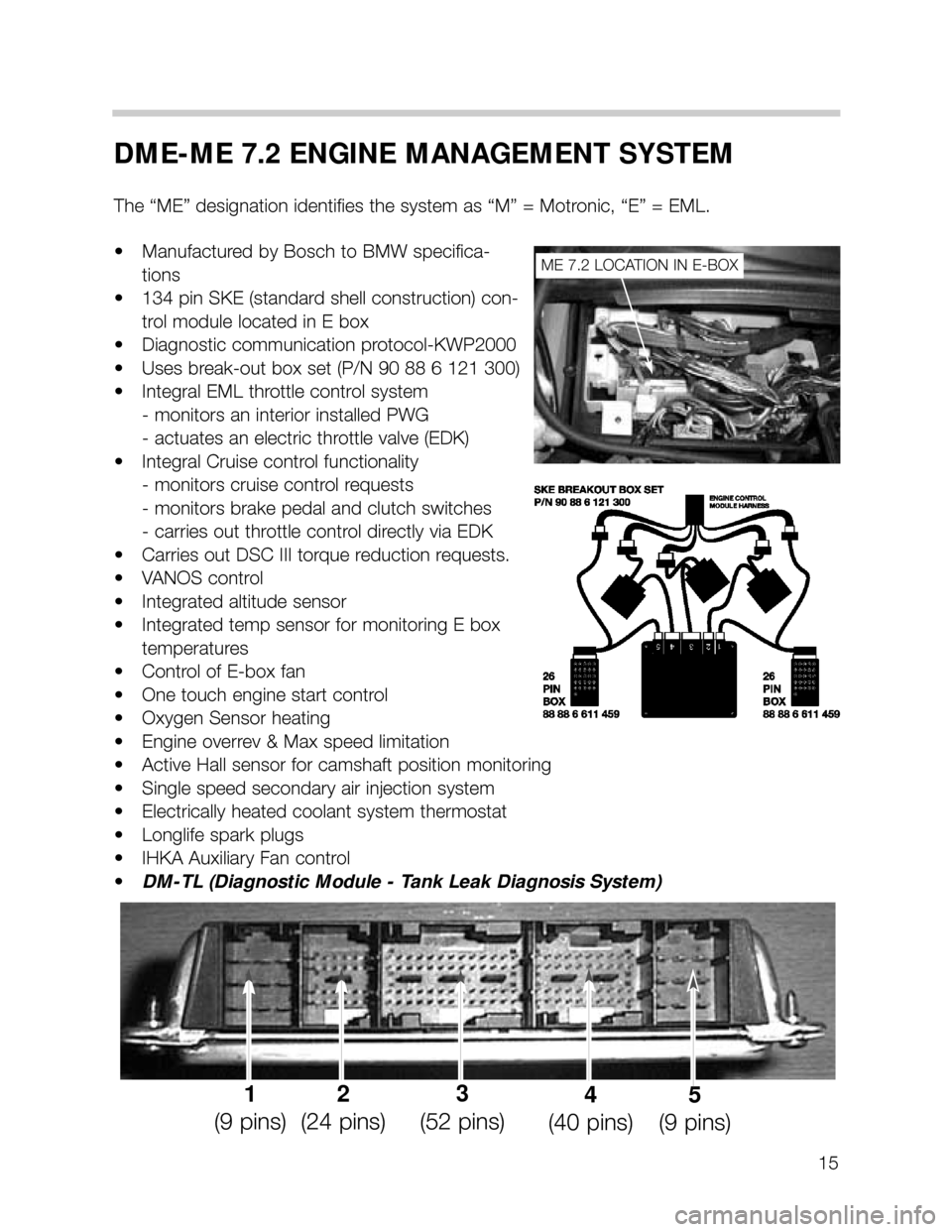
15
DME-ME 7.2 ENGINE MANAGEMENT SYSTEM
The “ME” designation identifies the system as “M” = Motronic, “E” = EML.
• Manufactured by Bosch to BMW specifica-
tions
• 134 pin SKE (standard shell construction) con-
trol module located in E box
• Diagnostic communication protocol-KWP2000
• Uses break-out box set (P/N 90 88 6 121 300)
• Integral EML throttle control system
- monitors an interior installed PWG
- actuates an electric throttle valve (EDK)
• Integral Cruise control functionality
- monitors cruise control requests
- monitors brake pedal and clutch switches
- carries out throttle control directly via EDK
• Carries out DSC III torque reduction requests.
• VANOS control
• Integrated altitude sensor
• Integrated temp sensor for monitoring E box
temperatures
• Control of E-box fan
• One touch engine start control
• Oxygen Sensor heating
• Engine overrev & Max speed limitation
• Active Hall sensor for camshaft position monitoring
• Single speed secondary air injection system
• Electrically heated coolant system thermostat
• Longlife spark plugs
• IHKA Auxiliary Fan control
•DM-TL (Diagnostic Module - Tank Leak Diagnosis System)
ME 7.2 LOCATION IN E-BOX
1
(9 pins)2
(24 pins)3
(52 pins)4
(40 pins)5
(9 pins)
Page 16 of 37
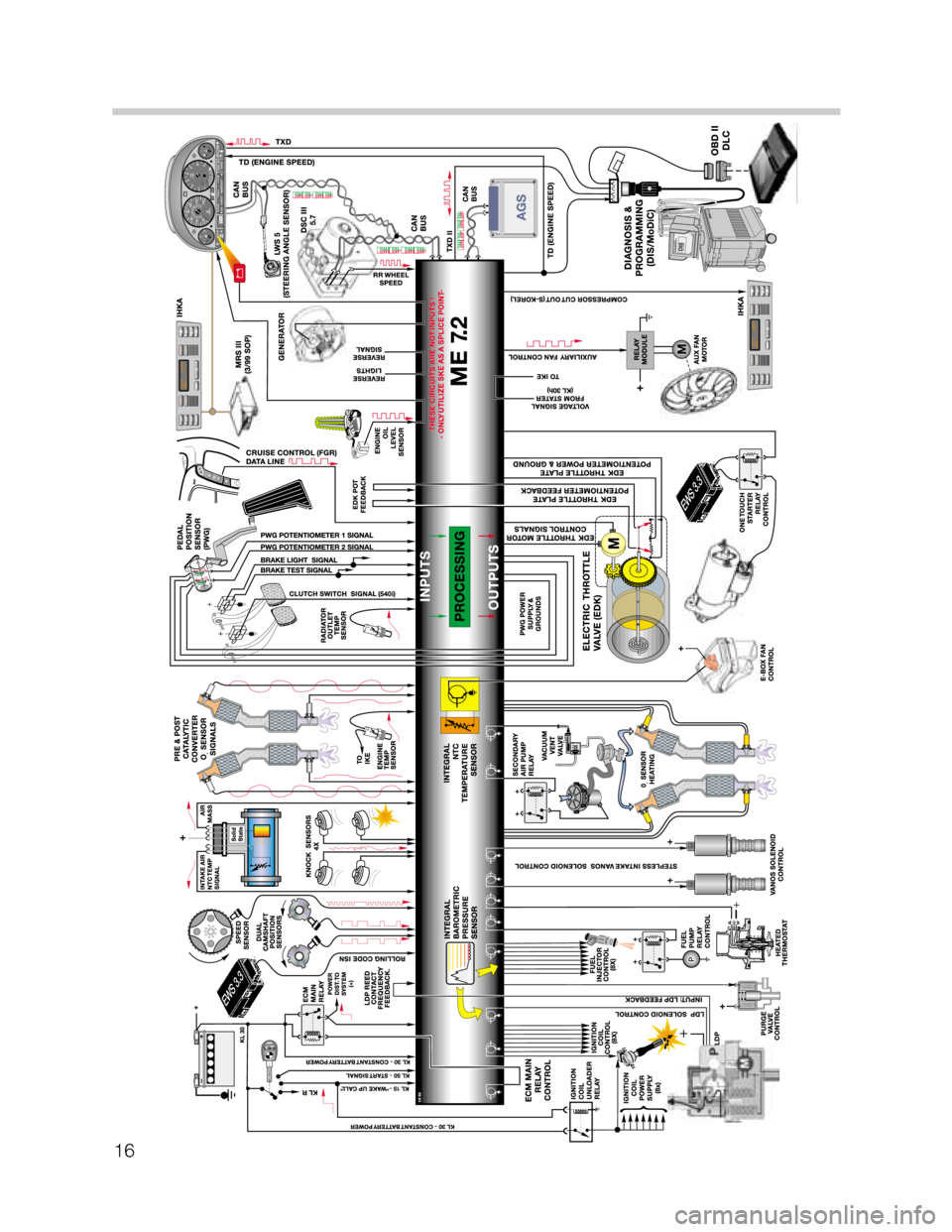
16
Page 17 of 37
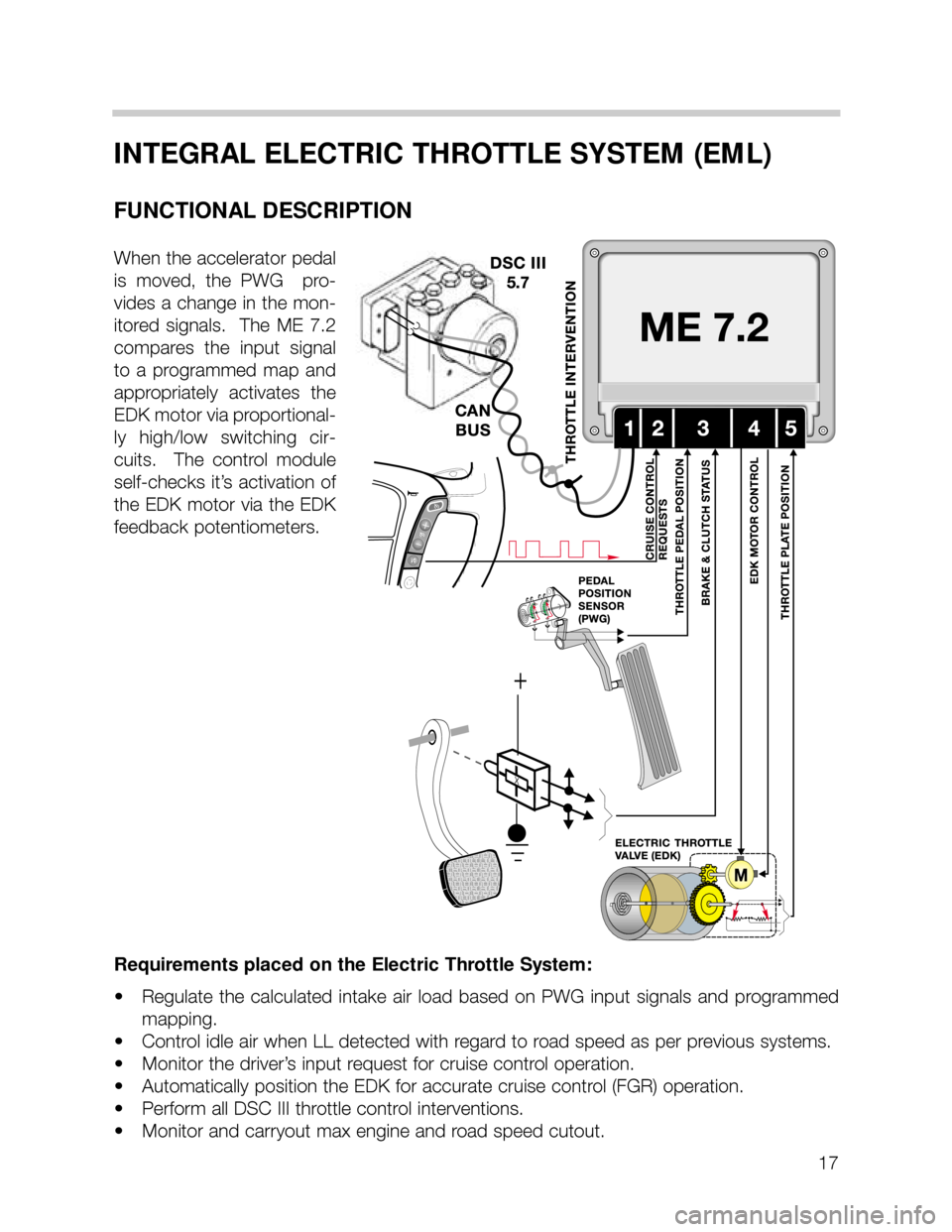
17
INTEGRAL ELECTRIC THROTTLE SYSTEM (EML)
FUNCTIONAL DESCRIPTION
When the accelerator pedal
is moved, the PWG pro-
vides a change in the mon-
itored signals. The ME 7.2
compares the input signal
to a programmed map and
appropriately activates the
EDK motor via proportional-
ly high/low switching cir-
cuits. The control module
self-checks it’s activation of
the EDK motor via the EDK
feedback potentiometers.
Requirements placed on the Electric Throttle System:
• Regulate the calculated intake air load based on PWG input signals and programmed
mapping.
• Control idle air when LL detected with regard to road speed as per previous systems.
• Monitor the driver’s input request for cruise control operation.
• Automatically position the EDK for accurate cruise control (FGR) operation.
• Perform all DSC III throttle control interventions.
• Monitor and carryout max engine and road speed cutout.
Page 18 of 37
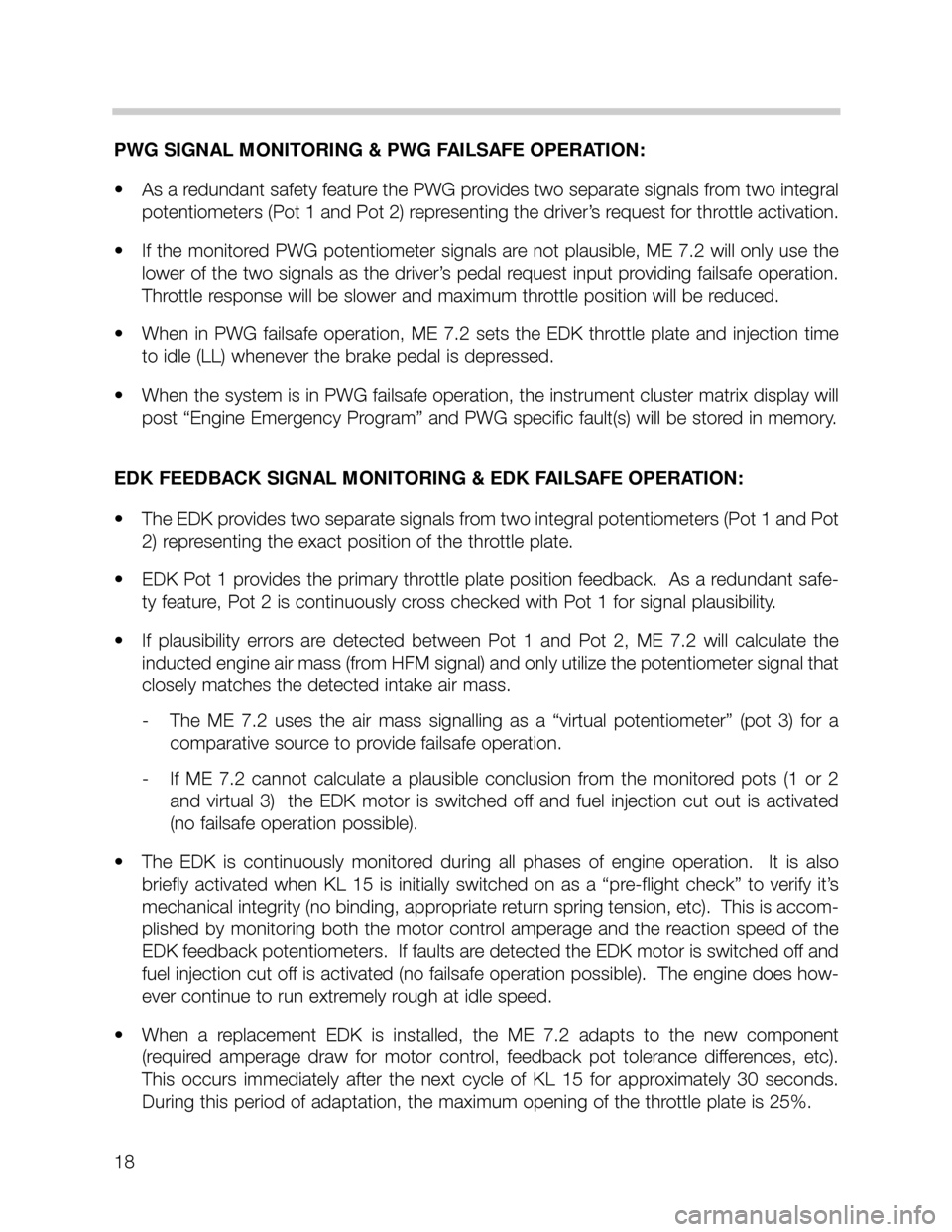
18
PWG SIGNAL MONITORING & PWG FAILSAFE OPERATION:
• As a redundant safety feature the PWG provides two separate signals from two integral
potentiometers (Pot 1 and Pot 2) representing the driver’s request for throttle activation.
• If the monitored PWG potentiometer signals are not plausible, ME 7.2 will only use the
lower of the two signals as the driver’s pedal request input providing failsafe operation.
Throttle response will be slower and maximum throttle position will be reduced.
• When in PWG failsafe operation, ME 7.2 sets the EDK throttle plate and injection time
to idle (LL) whenever the brake pedal is depressed.
• When the system is in PWG failsafe operation, the instrument cluster matrix display will
post “Engine Emergency Program” and PWG specific fault(s) will be stored in memory.
EDK FEEDBACK SIGNAL MONITORING & EDK FAILSAFE OPERATION:
• The EDK provides two separate signals from two integral potentiometers (Pot 1 and Pot
2) representing the exact position of the throttle plate.
• EDK Pot 1 provides the primary throttle plate position feedback. As a redundant safe-
ty feature, Pot 2 is continuously cross checked with Pot 1 for signal plausibility.
• If plausibility errors are detected between Pot 1 and Pot 2, ME 7.2 will calculate the
inducted engine air mass (from HFM signal) and only utilize the potentiometer signal that
closely matches the detected intake air mass.
- The ME 7.2 uses the air mass signalling as a “virtual potentiometer” (pot 3) for a
comparative source to provide failsafe operation.
- If ME 7.2 cannot calculate a plausible conclusion from the monitored pots (1 or 2
and virtual 3) the EDK motor is switched off and fuel injection cut out is activated
(no failsafe operation possible).
• The EDK is continuously monitored during all phases of engine operation. It is also
briefly activated when KL 15 is initially switched on as a “pre-flight check” to verify it’s
mechanical integrity (no binding, appropriate return spring tension, etc). This is accom-
plished by monitoring both the motor control amperage and the reaction speed of the
EDK feedback potentiometers. If faults are detected the EDK motor is switched off and
fuel injection cut off is activated (no failsafe operation possible). The engine does how-
ever continue to run extremely rough at idle speed.
• When a replacement EDK is installed, the ME 7.2 adapts to the new component
(required amperage draw for motor control, feedback pot tolerance differences, etc).
This occurs immediately after the next cycle of KL 15 for approximately 30 seconds.
During this period of adaptation, the maximum opening of the throttle plate is 25%.
Page 19 of 37
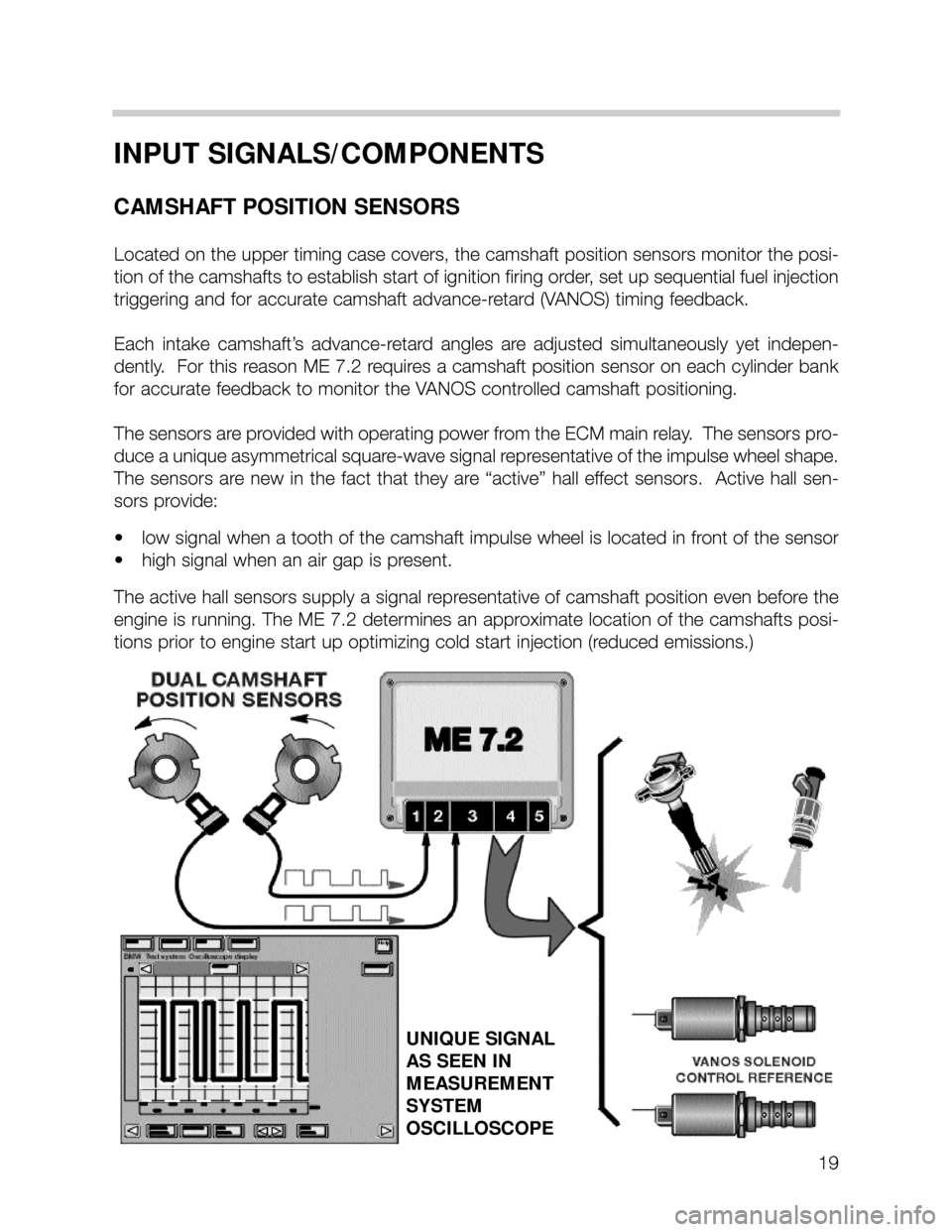
19
INPUT SIGNALS/COMPONENTS
CAMSHAFT POSITION SENSORS
Located on the upper timing case covers, the camshaft position sensors monitor the posi-
tion of the camshafts to establish start of ignition firing order, set up sequential fuel injection
triggering and for accurate camshaft advance-retard (VANOS) timing feedback.
Each intake camshaft’s advance-retard angles are adjusted simultaneously yet indepen-
dently. For this reason ME 7.2 requires a camshaft position sensor on each cy linder bank
for accurate feedback to monitor the VANOS controlled camshaft positioning.
The sensors are provided with operating power from the ECM main relay. The sensors pro-
duce a unique asymmetrical square-wave signal representative of the impulse wheel shape.
The sensors are new in the fact that they are “active” hall effect sensors. Active hall sen-
sors provide:
• low signal when a tooth of the camshaft impulse wheel is located in front of the sensor
• high signal when an air gap is present.
The active hall sensors supply a signal representative of camshaft position even before the
engine is running. The ME 7.2 determines an approximate location of the camshafts posi-
tions prior to engine start up optimizing cold start injection (reduced emissions.)
UNIQUE SIGNAL
AS SEEN IN
MEASUREMENT
SYSTEM
OSCILLOSCOPE
Page 20 of 37
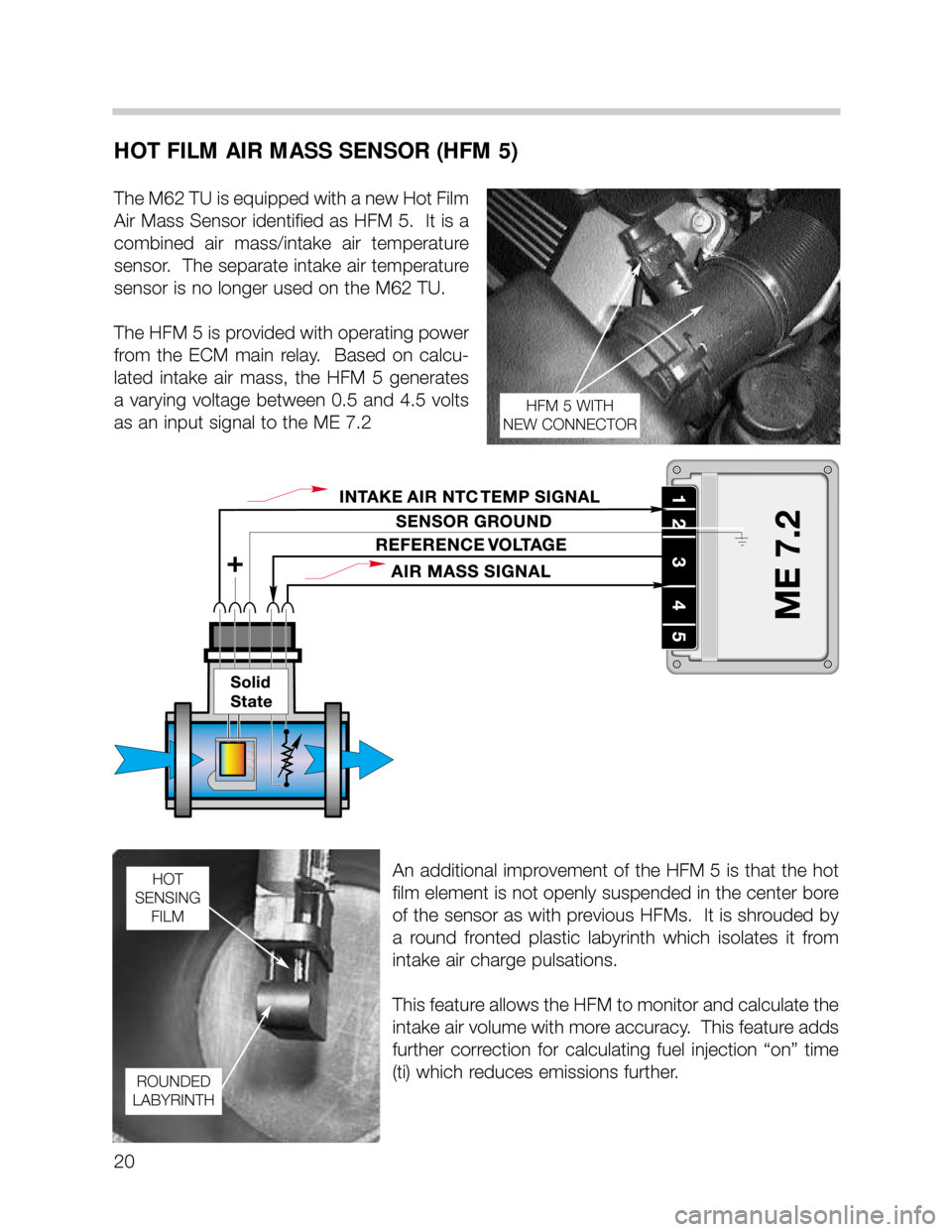
20
HOT FILM AIR MASS SENSOR (HFM 5)
The M62 TU is equipped with a new Hot Film
Air Mass Sensor identified as HFM 5. It is a
combined air mass/intake air temperature
sensor. The separate intake air temperature
sensor is no longer used on the M62 TU.
The HFM 5 is provided with operating power
from the ECM main relay. Based on calcu-
lated intake air mass, the HFM 5 generates
a varying voltage between 0.5 and 4.5 volts
as an input signal to the ME 7.2
An additional improvement of the HFM 5 is that the hot
film element is not openly suspended in the center bore
of the sensor as with previous HFMs. It is shrouded by
a round fronted plastic labyrinth which isolates it from
intake air charge pulsations.
This feature allows the HFM to monitor and calculate the
intake air volume with more accuracy. This feature adds
further correction for calculating fuel injection “on” time
(ti) which reduces emissions further.
HFM 5 WITH
NEW CONNECTOR
HOT
SENSING
FILM
ROUNDED
LABYRINTH