CHERY TIGGO 2009 Service Repair Manual
Manufacturer: CHERY, Model Year: 2009, Model line: TIGGO, Model: CHERY TIGGO 2009Pages: 1903, PDF Size: 33.38 MB
Page 1191 of 1903
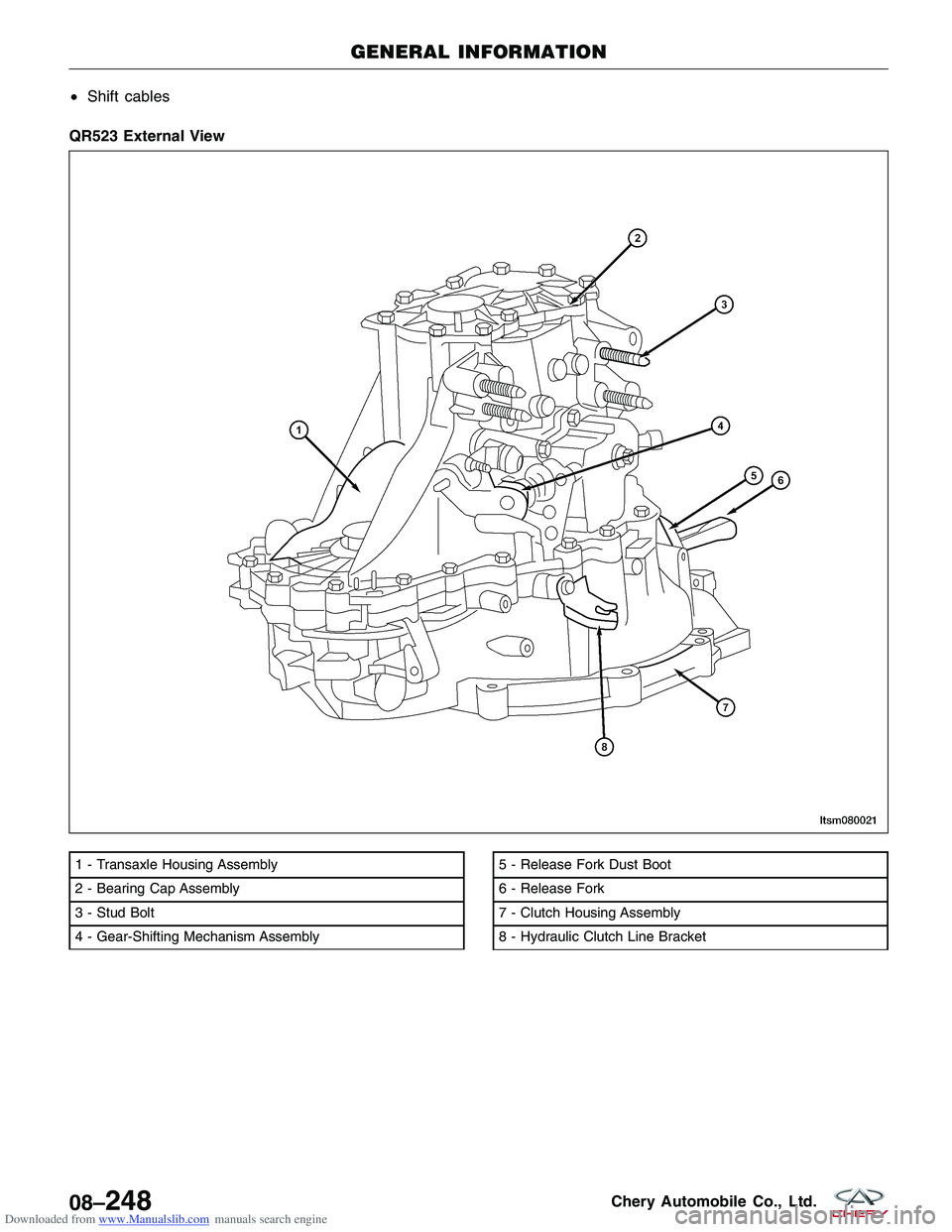
Downloaded from www.Manualslib.com manuals search engine •Shift cables
QR523 External View
1 - Transaxle Housing Assembly
2 - Bearing Cap Assembly
3 - Stud Bolt
4 - Gear-Shifting Mechanism Assembly5 - Release Fork Dust Boot
6 - Release Fork
7 - Clutch Housing Assembly
8 - Hydraulic Clutch Line Bracket
GENERAL INFORMATION
LTSM080021
08–248Chery Automobile Co., Ltd.
Page 1192 of 1903
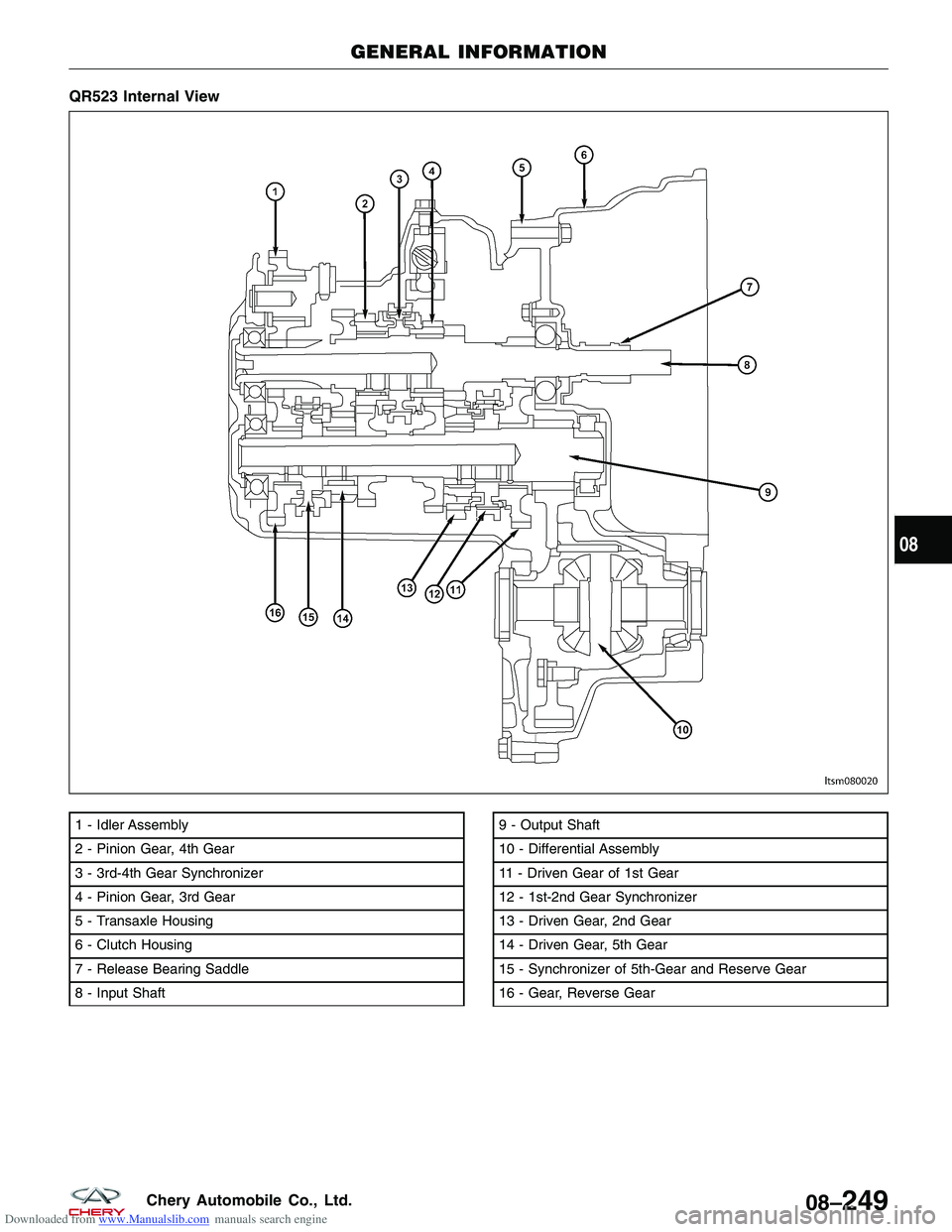
Downloaded from www.Manualslib.com manuals search engine QR523 Internal View
1 - Idler Assembly
2 - Pinion Gear, 4th Gear
3 - 3rd-4th Gear Synchronizer
4 - Pinion Gear, 3rd Gear
5 - Transaxle Housing
6 - Clutch Housing
7 - Release Bearing Saddle
8 - Input Shaft9 - Output Shaft
10 - Differential Assembly
11 - Driven Gear of 1st Gear
12 - 1st-2nd Gear Synchronizer
13 - Driven Gear, 2nd Gear
14 - Driven Gear, 5th Gear
15 - Synchronizer of 5th-Gear and Reserve Gear
16 - Gear, Reverse Gear
GENERAL INFORMATION
LTSM080020
08
08–249Chery Automobile Co., Ltd.
Page 1193 of 1903
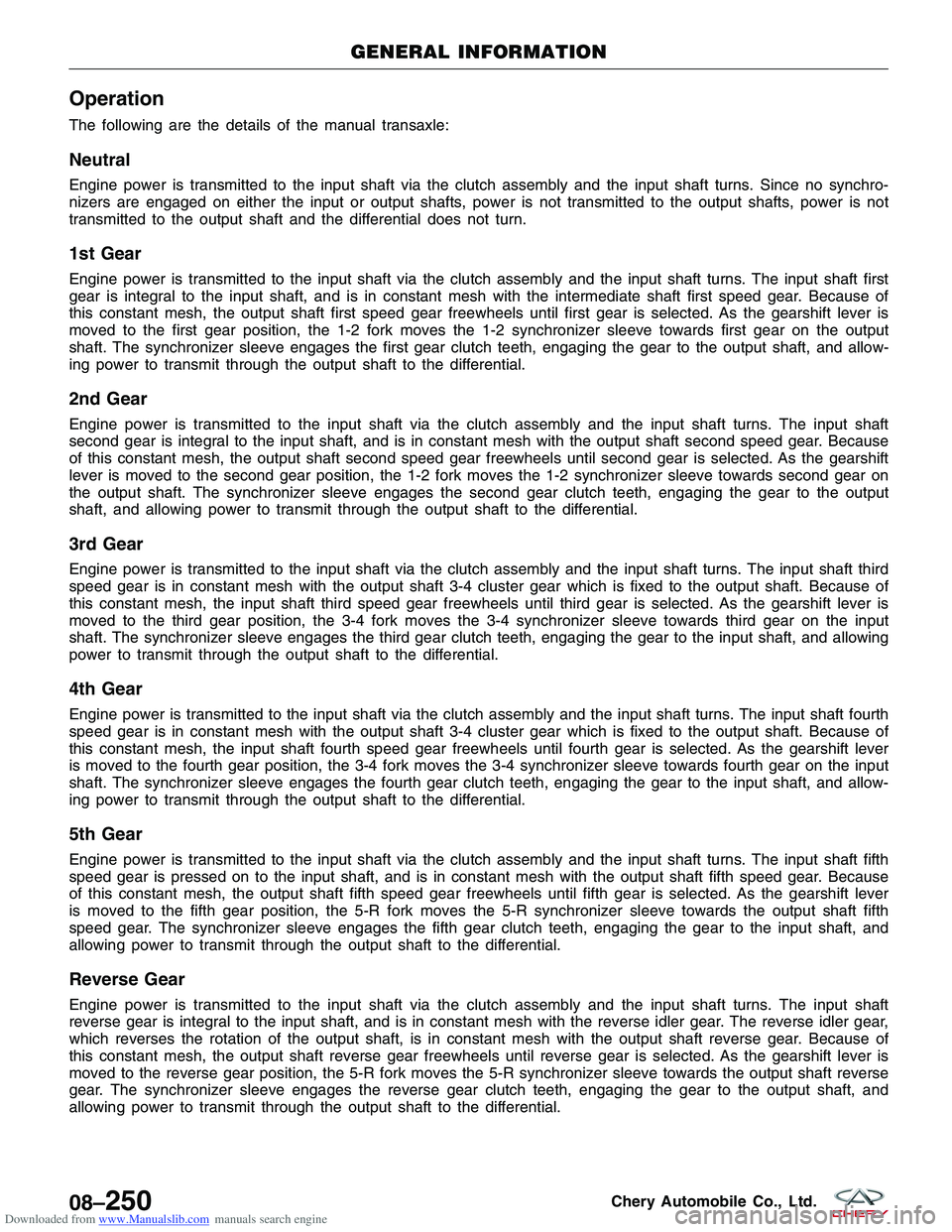
Downloaded from www.Manualslib.com manuals search engine Operation
The following are the details of the manual transaxle:
Neutral
Engine power is transmitted to the input shaft via the clutch assembly and the input shaft turns. Since no synchro-
nizers are engaged on either the input or output shafts, power is not transmitted to the output shafts, power is not
transmitted to the output shaft and the differential does not turn.
1st Gear
Engine power is transmitted to the input shaft via the clutch assembly and the input shaft turns. The input shaft first
gear is integral to the input shaft, and is in constant mesh with the intermediate shaft first speed gear. Because of
this constant mesh, the output shaft first speed gear freewheels until first gear is selected. As the gearshift lever is
moved to the first gear position, the 1-2 fork moves the 1-2 synchronizer sleeve towards first gear on the output
shaft. The synchronizer sleeve engages the first gear clutch teeth, engaging the gear to the output shaft, and allow-
ing power to transmit through the output shaft to the differential.
2nd Gear
Engine power is transmitted to the input shaft via the clutch assembly and the input shaft turns. The input shaft
second gear is integral to the input shaft, and is in constant mesh with the output shaft second speed gear. Because
of this constant mesh, the output shaft second speed gear freewheels until second gear is selected. As the gearshift
lever is moved to the second gear position, the 1-2 fork moves the 1-2 synchronizer sleeve towards second gear on
the output shaft. The synchronizer sleeve engages the second gear clutch teeth, engaging the gear to the output
shaft, and allowing power to transmit through the output shaft to the differential.
3rd Gear
Engine power is transmitted to the input shaft via the clutch assembly and the input shaft turns. The input shaft third
speed gear is in constant mesh with the output shaft 3-4 cluster gear which is fixed to the output shaft. Because of
this constant mesh, the input shaft third speed gear freewheels until third gear is selected. As the gearshift lever is
moved to the third gear position, the 3-4 fork moves the 3-4 synchronizer sleeve towards third gear on the input
shaft. The synchronizer sleeve engages the third gear clutch teeth, engaging the gear to the input shaft, and allowing
power to transmit through the output shaft to the differential.
4th Gear
Engine power is transmitted to the input shaft via the clutch assembly and the input shaft turns. The input shaft fourth
speed gear is in constant mesh with the output shaft 3-4 cluster gear which is fixed to the output shaft. Because of
this constant mesh, the input shaft fourth speed gear freewheels until fourth gear is selected. As the gearshift lever
is moved to the fourth gear position, the 3-4 fork moves the 3-4 synchronizer sleeve towards fourth gear on the input
shaft. The synchronizer sleeve engages the fourth gear clutch teeth, engaging the gear to the input shaft, and allow-
ing power to transmit through the output shaft to the differential.
5th Gear
Engine power is transmitted to the input shaft via the clutch assembly and the input shaft turns. The input shaft fifth
speed gear is pressed on to the input shaft, and is in constant mesh with the output shaft fifth speed gear. Because
of this constant mesh, the output shaft fifth speed gear freewheels until fifth gear is selected. As the gearshift lever
is moved to the fifth gear position, the 5-R fork moves the 5-R synchronizer sleeve towards the output shaft fifth
speed gear. The synchronizer sleeve engages the fifth gear clutch teeth, engaging the gear to the input shaft, and
allowing power to transmit through the output shaft to the differential.
Reverse Gear
Engine power is transmitted to the input shaft via the clutch assembly and the input shaft turns. The input shaft
reverse gear is integral to the input shaft, and is in constant mesh with the reverse idler gear. The reverse idler gear,
which reverses the rotation of the output shaft, is in constant mesh with the output shaft reverse gear. Because of
this constant mesh, the output shaft reverse gear freewheels until reverse gear is selected. As the gearshift lever is
moved to the reverse gear position, the 5-R fork moves the 5-R synchronizer sleeve towards the output shaft reverse
gear. The synchronizer sleeve engages the reverse gear clutch teeth, engaging the gear to the output shaft, and
allowing power to transmit through the output shaft to the differential.
GENERAL INFORMATION
08–250Chery Automobile Co., Ltd.
Page 1194 of 1903

Downloaded from www.Manualslib.com manuals search engine Transaxle Identification Number
The transaxle serial number can be found on a metal
tag (1) fastened to the transaxle case on the clutch
housing. The third row data is the transaxle serial
number.
Specifications
Maintenance Specifications
DESCRIPTIONALLOWABLE RANGE (mm) LIMIT VALUE (mm)
Axial Clearance Of Input Shaft Front
Bearing -0.01 - 0.21
-
Axial Clearance Of Input Shaft Rear
Bearing -0.01 - 0.12
-
Axial Clearance Of Input Shaft Fifth
Gear -0.01 - 0.09
-
Axial Clearance Of Output Shaft
Front Bearing -0.01 - 0.12
-
Axial Clearance Of Output Shaft
Rear Bearing -0.01 - 0.09
-
Axial Clearance Of Output Shaft
Third Gear -0.01 - 0.09
-
Back Clearance Of Differential Case
Planetary Gear 0.025 - 0.150
-
Clearance Between The Gear And
The Back Of Synchronizer Ring -
0.05
Pretension Of Differential Case 0.05 - 0.11-
GENERAL INFORMATION
LTSM020209
08
08–251Chery Automobile Co., Ltd.
Page 1195 of 1903
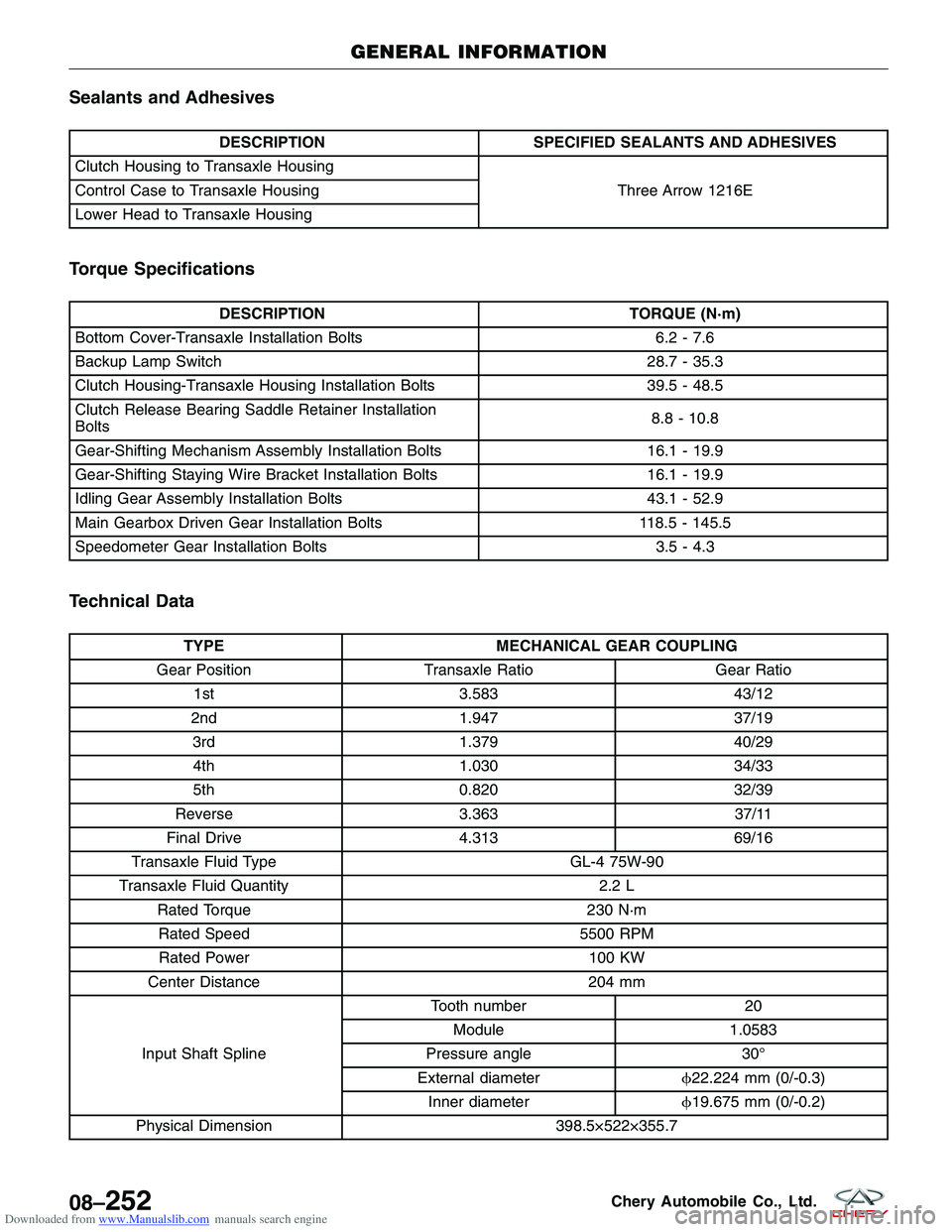
Downloaded from www.Manualslib.com manuals search engine Sealants and Adhesives
DESCRIPTIONSPECIFIED SEALANTS AND ADHESIVES
Clutch Housing to Transaxle Housing Three Arrow 1216E
Control Case to Transaxle Housing
Lower Head to Transaxle Housing
Torque Specifications
DESCRIPTION TORQUE (N·m)
Bottom Cover-Transaxle Installation Bolts 6.2 - 7.6
Backup Lamp Switch 28.7 - 35.3
Clutch Housing-Transaxle Housing Installation Bolts 39.5 - 48.5
Clutch Release Bearing Saddle Retainer Installation
Bolts 8.8 - 10.8
Gear-Shifting Mechanism Assembly Installation Bolts 16.1 - 19.9
Gear-Shifting Staying Wire Bracket Installation Bolts 16.1 - 19.9
Idling Gear Assembly Installation Bolts 43.1 - 52.9
Main Gearbox Driven Gear Installation Bolts 118.5 - 145.5
Speedometer Gear Installation Bolts 3.5 - 4.3
Technical Data
TYPEMECHANICAL GEAR COUPLING
Gear Position Transaxle Ratio Gear Ratio
1st 3.583 43/12
2nd 1.947 37/19
3rd 1.379 40/29
4th 1.030 34/33
5th 0.820 32/39
Reverse 3.36337/11
Final Drive 4.31369/16
Transaxle Fluid Type GL-4 75W-90
Transaxle Fluid Quantity 2.2 L
Rated Torque 230 N·m
Rated Speed 5500 RPM
Rated Power 100 KW
Center Distance 204 mm
Input Shaft Spline Tooth number
20
Module 1.0583
Pressure angle 30°
External diameter 22.224 mm (0/-0.3)
Inner diameter 19.675 mm (0/-0.2)
Physical Dimension 398.5×522×355.7
GENERAL INFORMATION
08–252Chery Automobile Co., Ltd.
Page 1196 of 1903
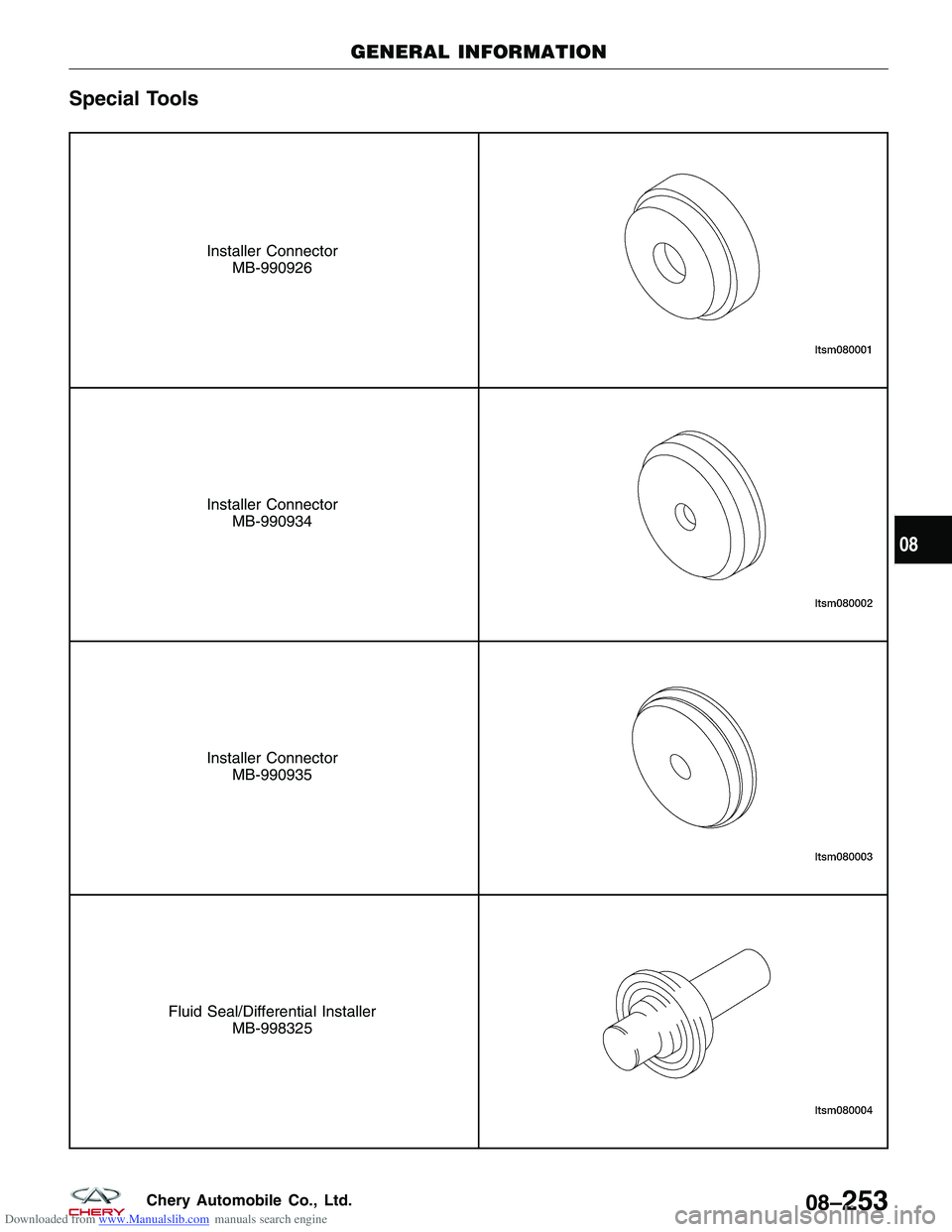
Downloaded from www.Manualslib.com manuals search engine Special Tools
Installer ConnectorMB-990926
Installer ConnectorMB-990934
Installer ConnectorMB-990935
Fluid Seal/Differential Installer MB-998325
GENERAL INFORMATION
08
08–253Chery Automobile Co., Ltd.
Page 1197 of 1903
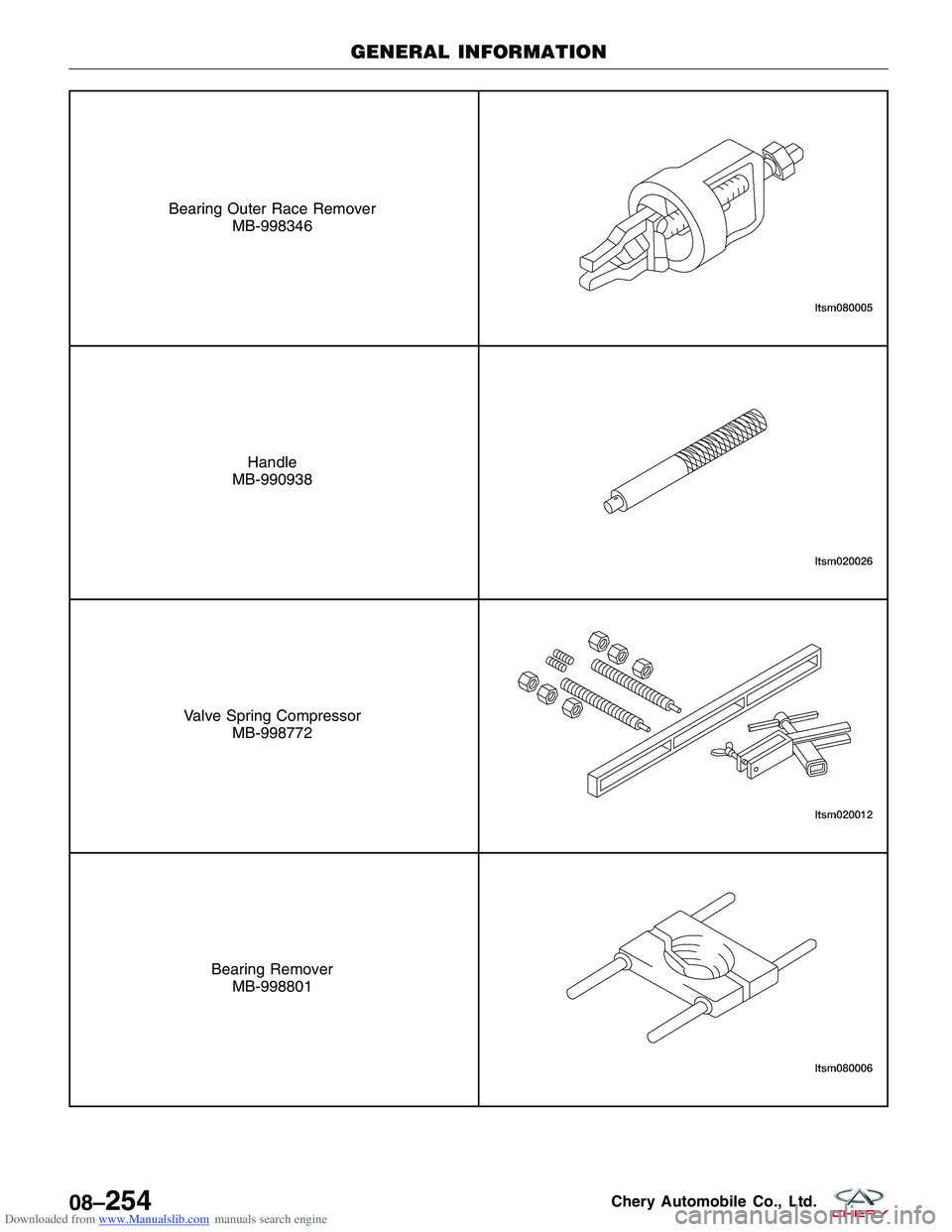
Downloaded from www.Manualslib.com manuals search engine Bearing Outer Race RemoverMB-998346
Handle
MB-990938
Valve Spring Compressor MB-998772
Bearing RemoverMB-998801
GENERAL INFORMATION
08–254Chery Automobile Co., Ltd.
Page 1198 of 1903
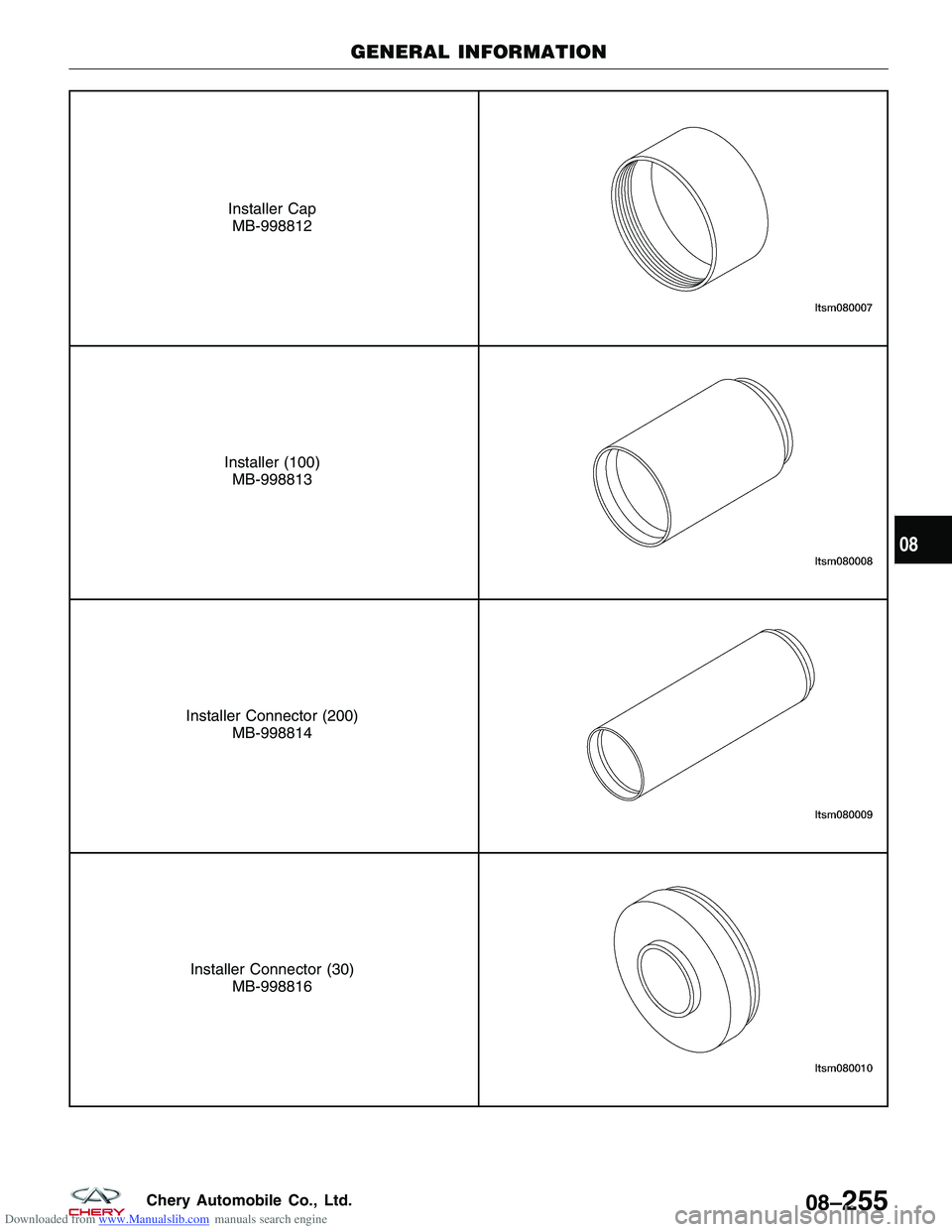
Downloaded from www.Manualslib.com manuals search engine Installer CapMB-998812
Installer (100) MB-998813
Installer Connector (200) MB-998814
Installer Connector (30)MB-998816
GENERAL INFORMATION
08
08–255Chery Automobile Co., Ltd.
Page 1199 of 1903
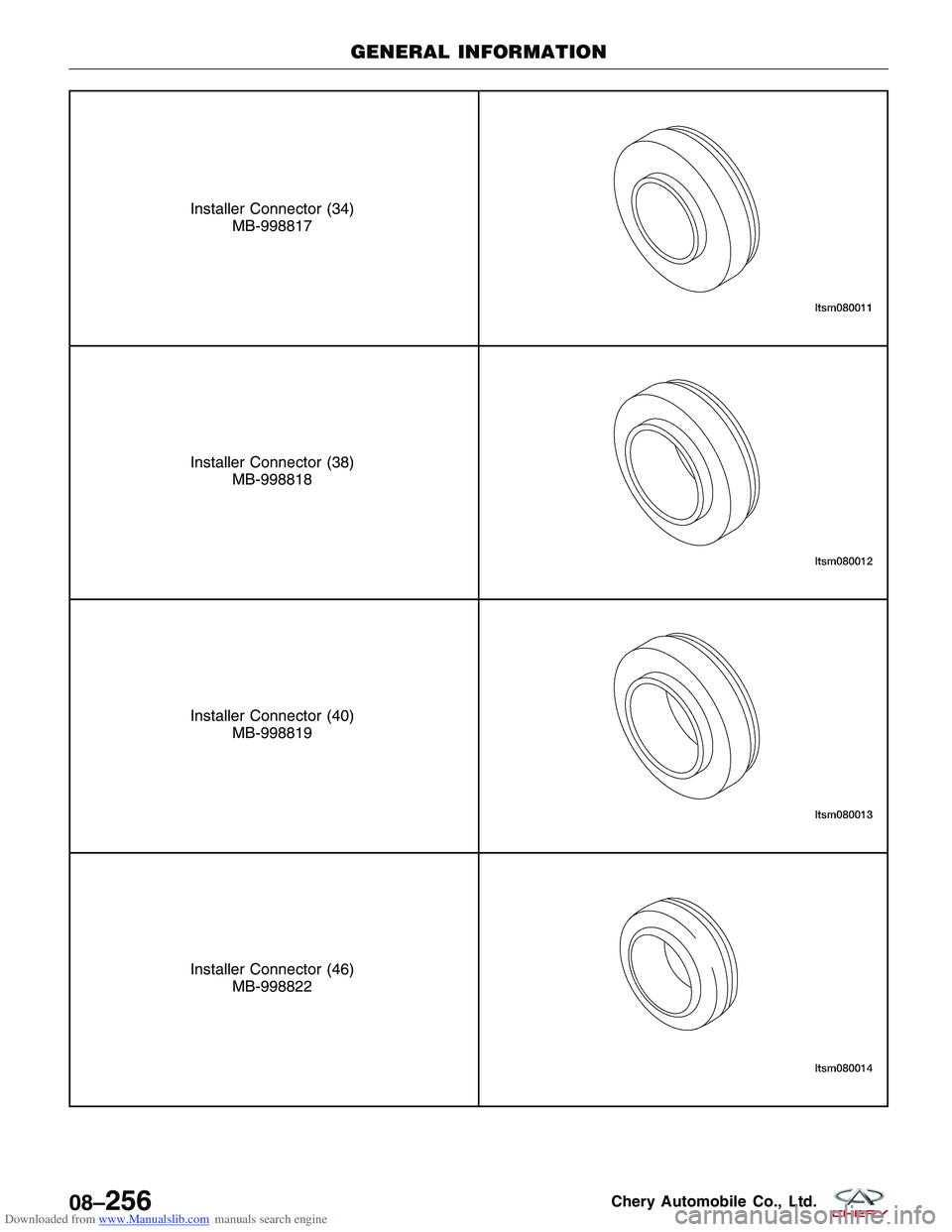
Downloaded from www.Manualslib.com manuals search engine Installer Connector (34)MB-998817
Installer Connector (38)MB-998818
Installer Connector (40)MB-998819
Installer Connector (46)MB-998822
GENERAL INFORMATION
08–256Chery Automobile Co., Ltd.
Page 1200 of 1903
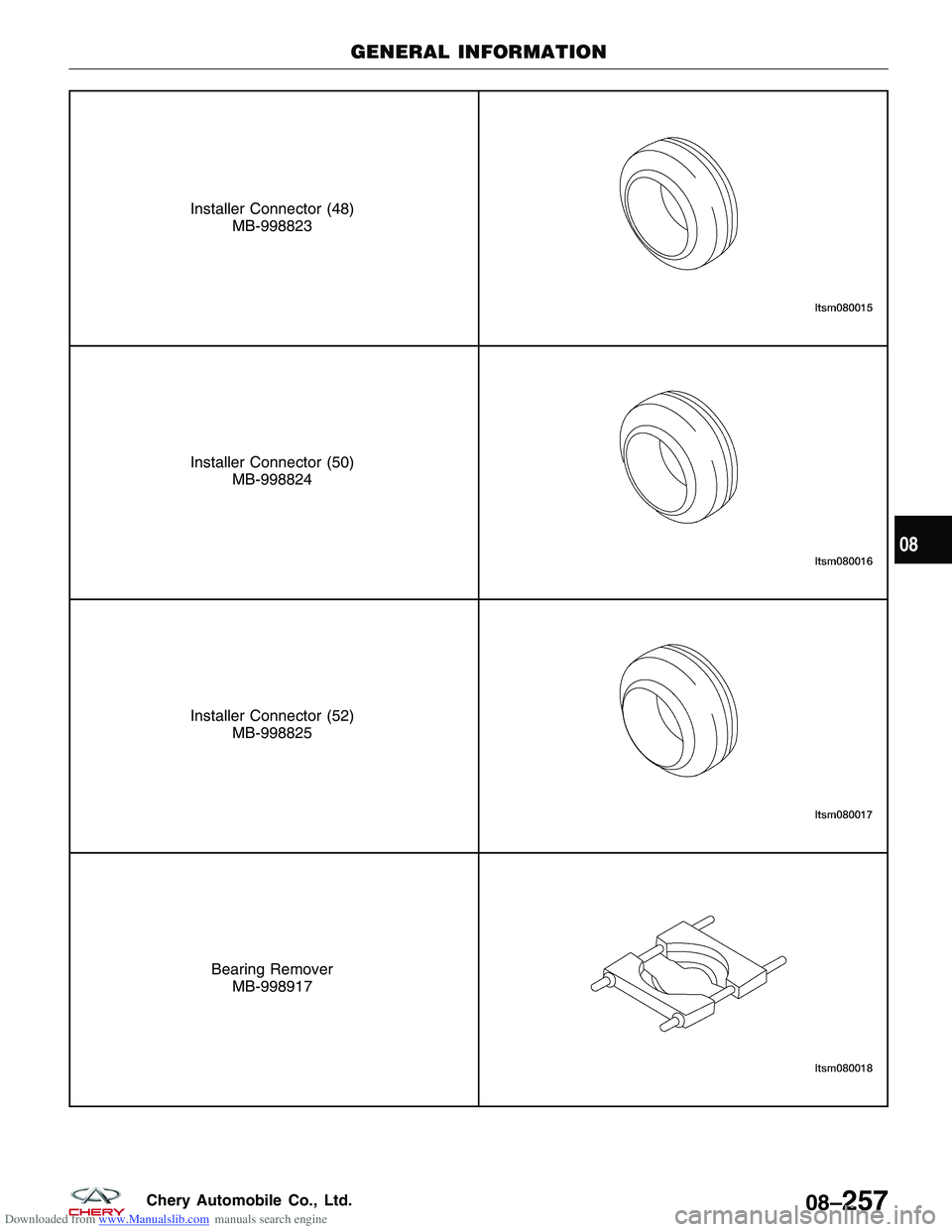
Downloaded from www.Manualslib.com manuals search engine Installer Connector (48)MB-998823
Installer Connector (50)MB-998824
Installer Connector (52)MB-998825
Bearing RemoverMB-998917
GENERAL INFORMATION
08
08–257Chery Automobile Co., Ltd.