CHEVROLET PLYMOUTH ACCLAIM 1993 Service Manual
Manufacturer: CHEVROLET, Model Year: 1993, Model line: PLYMOUTH ACCLAIM, Model: CHEVROLET PLYMOUTH ACCLAIM 1993Pages: 2438, PDF Size: 74.98 MB
Page 551 of 2438
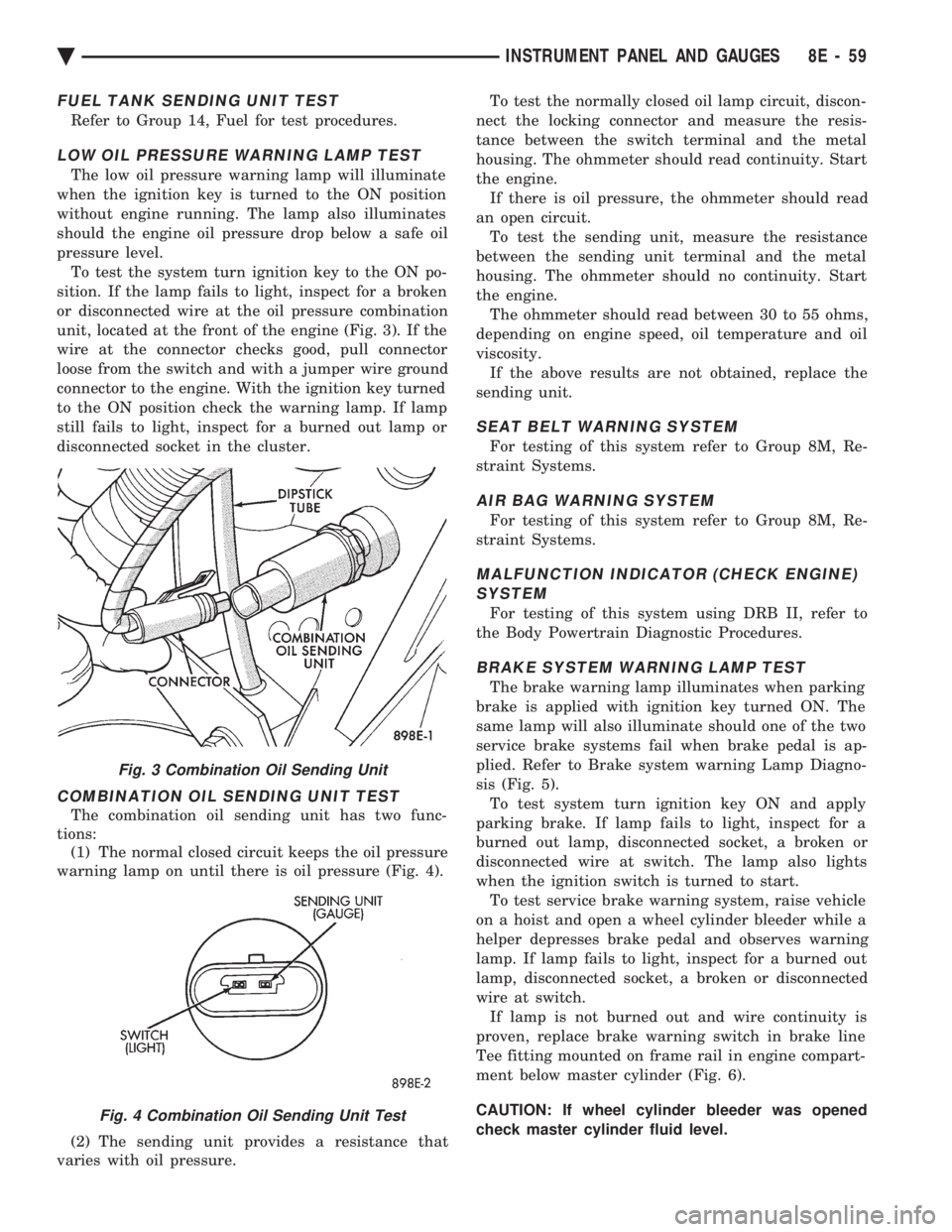
FUEL TANK SENDING UNIT TEST
Refer to Group 14, Fuel for test procedures.
LOW OIL PRESSURE WARNING LAMP TEST
The low oil pressure warning lamp will illuminate
when the ignition key is turned to the ON position
without engine running. The lamp also illuminates
should the engine oil pressure drop below a safe oil
pressure level. To test the system turn ignition key to the ON po-
sition. If the lamp fails to light, inspect for a broken
or disconnected wire at the oil pressure combination
unit, located at the front of the engine (Fig. 3). If the
wire at the connector checks good, pull connector
loose from the switch and with a jumper wire ground
connector to the engine. With the ignition key turned
to the ON position check the warning lamp. If lamp
still fails to light, inspect for a burned out lamp or
disconnected socket in the cluster.
COMBINATION OIL SENDING UNIT TEST
The combination oil sending unit has two func-
tions: (1) The normal closed circuit keeps the oil pressure
warning lamp on until there is oil pressure (Fig. 4).
(2) The sending unit provides a resistance that
varies with oil pressure. To test the normally closed oil lamp circuit, discon-
nect the locking connector and measure the resis-
tance between the switch terminal and the metal
housing. The ohmmeter should read continuity. Start
the engine. If there is oil pressure, the ohmmeter should read
an open circuit. To test the sending unit, measure the resistance
between the sending unit terminal and the metal
housing. The ohmmeter should no continuity. Start
the engine. The ohmmeter should read between 30 to 55 ohms,
depending on engine speed, oil temperature and oil
viscosity. If the above results are not obtained, replace the
sending unit.
SEAT BELT WARNING SYSTEM
For testing of this system refer to Group 8M, Re-
straint Systems.
AIR BAG WARNING SYSTEM
For testing of this system refer to Group 8M, Re-
straint Systems.
MALFUNCTION INDICATOR (CHECK ENGINE) SYSTEM
For testing of this system using DRB II, refer to
the Body Powertrain Diagnostic Procedures.
BRAKE SYSTEM WARNING LAMP TEST
The brake warning lamp illuminates when parking
brake is applied with ignition key turned ON. The
same lamp will also illuminate should one of the two
service brake systems fail when brake pedal is ap-
plied. Refer to Brake system warning Lamp Diagno-
sis (Fig. 5). To test system turn ignition key ON and apply
parking brake. If lamp fails to light, inspect for a
burned out lamp, disconnected socket, a broken or
disconnected wire at switch. The lamp also lights
when the ignition switch is turned to start. To test service brake warning system, raise vehicle
on a hoist and open a wheel cylinder bleeder while a
helper depresses brake pedal and observes warning
lamp. If lamp fails to light, inspect for a burned out
lamp, disconnected socket, a broken or disconnected
wire at switch. If lamp is not burned out and wire continuity is
proven, replace brake warning switch in brake line
Tee fitting mounted on frame rail in engine compart-
ment below master cylinder (Fig. 6).
CAUTION: If wheel cylinder bleeder was opened
check master cylinder fluid level.
Fig. 3 Combination Oil Sending Unit
Fig. 4 Combination Oil Sending Unit Test
Ä INSTRUMENT PANEL AND GAUGES 8E - 59
Page 552 of 2438
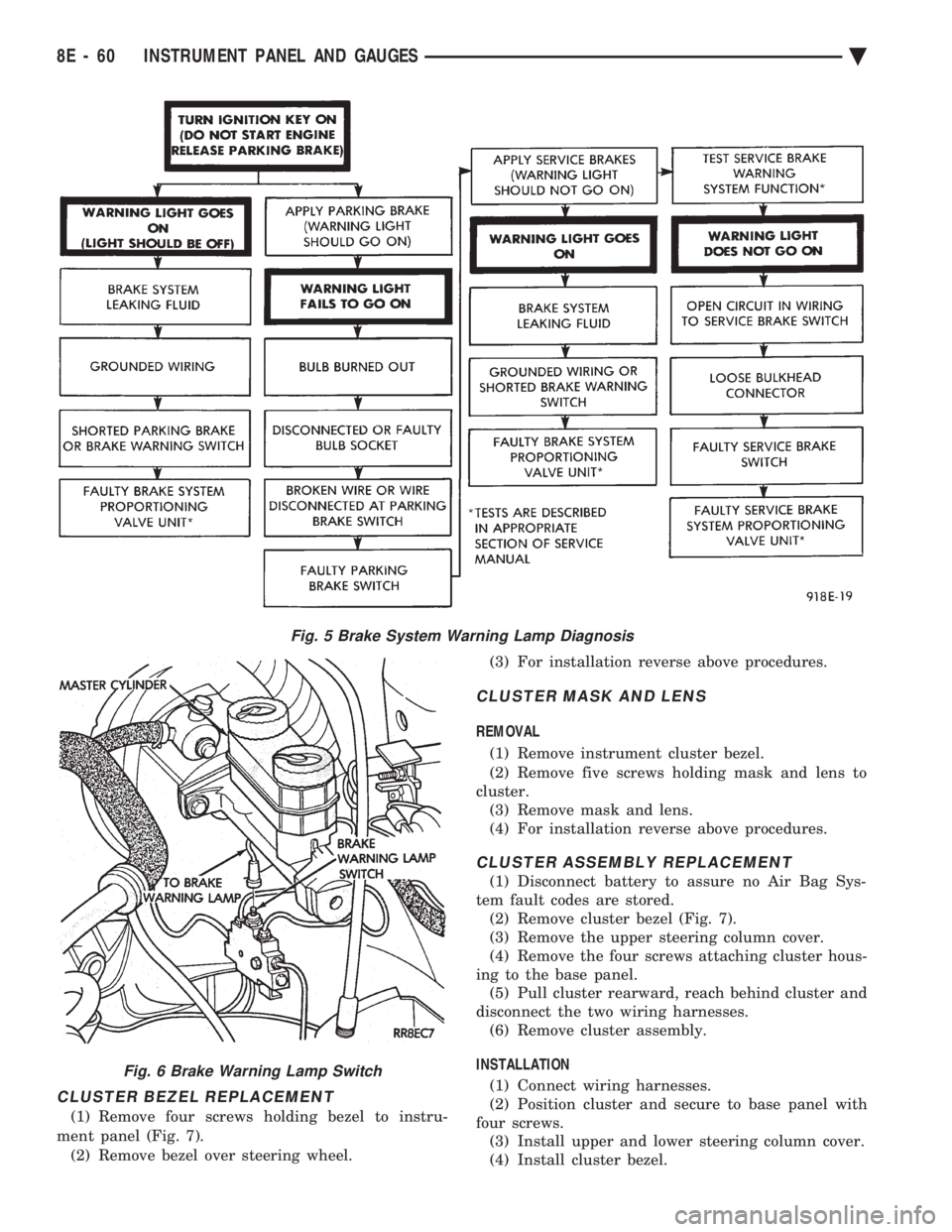
CLUSTER BEZEL REPLACEMENT
(1) Remove four screws holding bezel to instru-
ment panel (Fig. 7). (2) Remove bezel over steering wheel. (3) For installation reverse above procedures.
CLUSTER MASK AND LENS
REMOVAL
(1) Remove instrument cluster bezel.
(2) Remove five screws holding mask and lens to
cluster. (3) Remove mask and lens.
(4) For installation reverse above procedures.
CLUSTER ASSEMBLY REPLACEMENT
(1) Disconnect battery to assure no Air Bag Sys-
tem fault codes are stored. (2) Remove cluster bezel (Fig. 7).
(3) Remove the upper steering column cover.
(4) Remove the four screws attaching cluster hous-
ing to the base panel. (5) Pull cluster rearward, reach behind cluster and
disconnect the two wiring harnesses. (6) Remove cluster assembly.
INSTALLATION (1) Connect wiring harnesses.
(2) Position cluster and secure to base panel with
four screws. (3) Install upper and lower steering column cover.
(4) Install cluster bezel.
Fig. 5 Brake System Warning Lamp Diagnosis
Fig. 6 Brake Warning Lamp Switch
8E - 60 INSTRUMENT PANEL AND GAUGES Ä
Page 553 of 2438
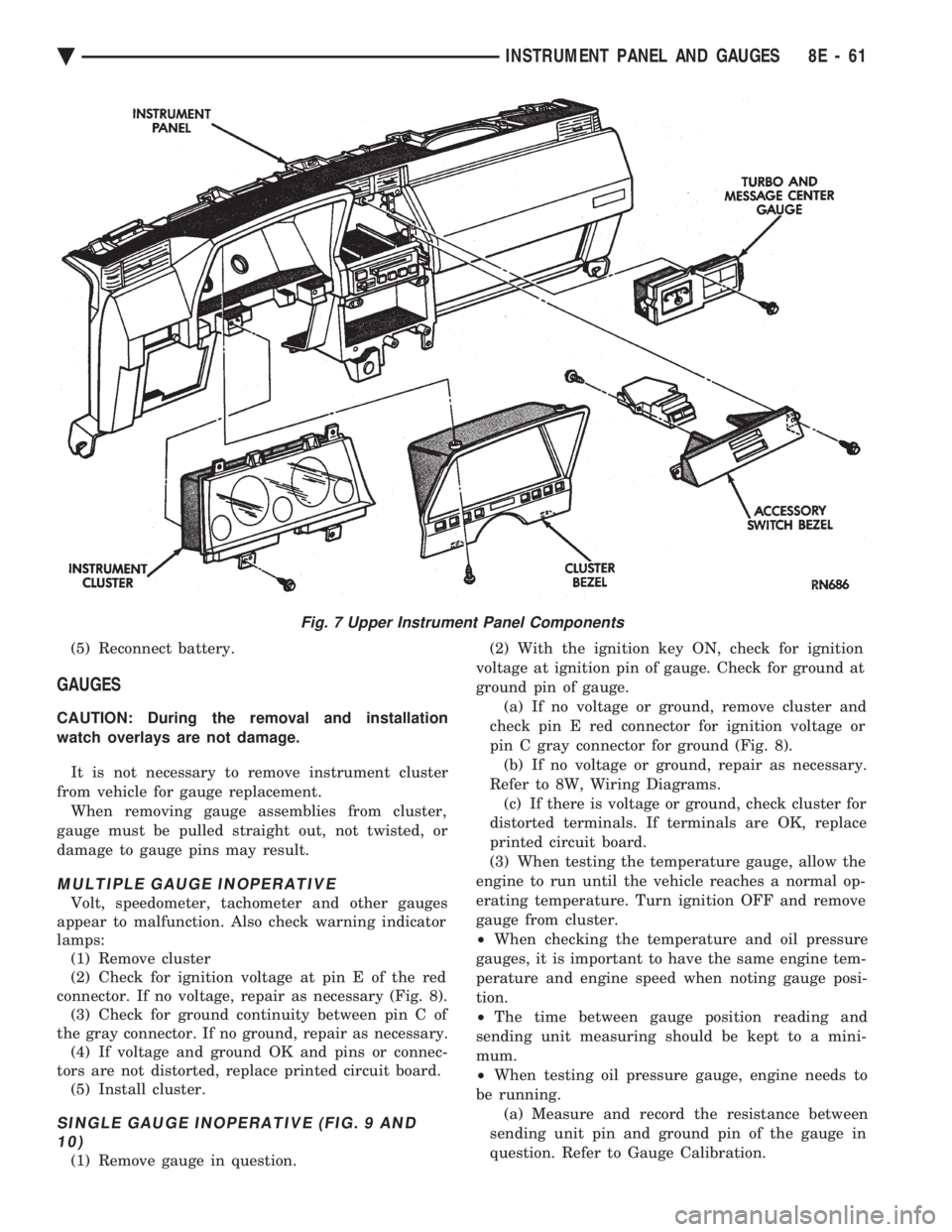
(5) Reconnect battery.
GAUGES
CAUTION: During the removal and installation
watch overlays are not damage.
It is not necessary to remove instrument cluster
from vehicle for gauge replacement. When removing gauge assemblies from cluster,
gauge must be pulled straight out, not twisted, or
damage to gauge pins may result.
MULTIPLE GAUGE INOPERATIVE
Volt, speedometer, tachometer and other gauges
appear to malfunction. Also check warning indicator
lamps: (1) Remove cluster
(2) Check for ignition voltage at pin E of the red
connector. If no voltage, repair as necessary (Fig. 8). (3) Check for ground continuity between pin C of
the gray connector. If no ground, repair as necessary. (4) If voltage and ground OK and pins or connec-
tors are not distorted, replace printed circuit board. (5) Install cluster.
SINGLE GAUGE INOPERATIVE (FIG. 9 AND10)
(1) Remove gauge in question. (2) With the ignition key ON, check for ignition
voltage at ignition pin of gauge. Check for ground at
ground pin of gauge. (a) If no voltage or ground, remove cluster and
check pin E red connector for ignition voltage or
pin C gray connector for ground (Fig. 8). (b) If no voltage or ground, repair as necessary.
Refer to 8W, Wiring Diagrams. (c) If there is voltage or ground, check cluster for
distorted terminals. If terminals are OK, replace
printed circuit board.
(3) When testing the temperature gauge, allow the
engine to run until the vehicle reaches a normal op-
erating temperature. Turn ignition OFF and remove
gauge from cluster.
² When checking the temperature and oil pressure
gauges, it is important to have the same engine tem-
perature and engine speed when noting gauge posi-
tion.
² The time between gauge position reading and
sending unit measuring should be kept to a mini-
mum.
² When testing oil pressure gauge, engine needs to
be running. (a) Measure and record the resistance between
sending unit pin and ground pin of the gauge in
question. Refer to Gauge Calibration.
Fig. 7 Upper Instrument Panel Components
Ä INSTRUMENT PANEL AND GAUGES 8E - 61
Page 554 of 2438
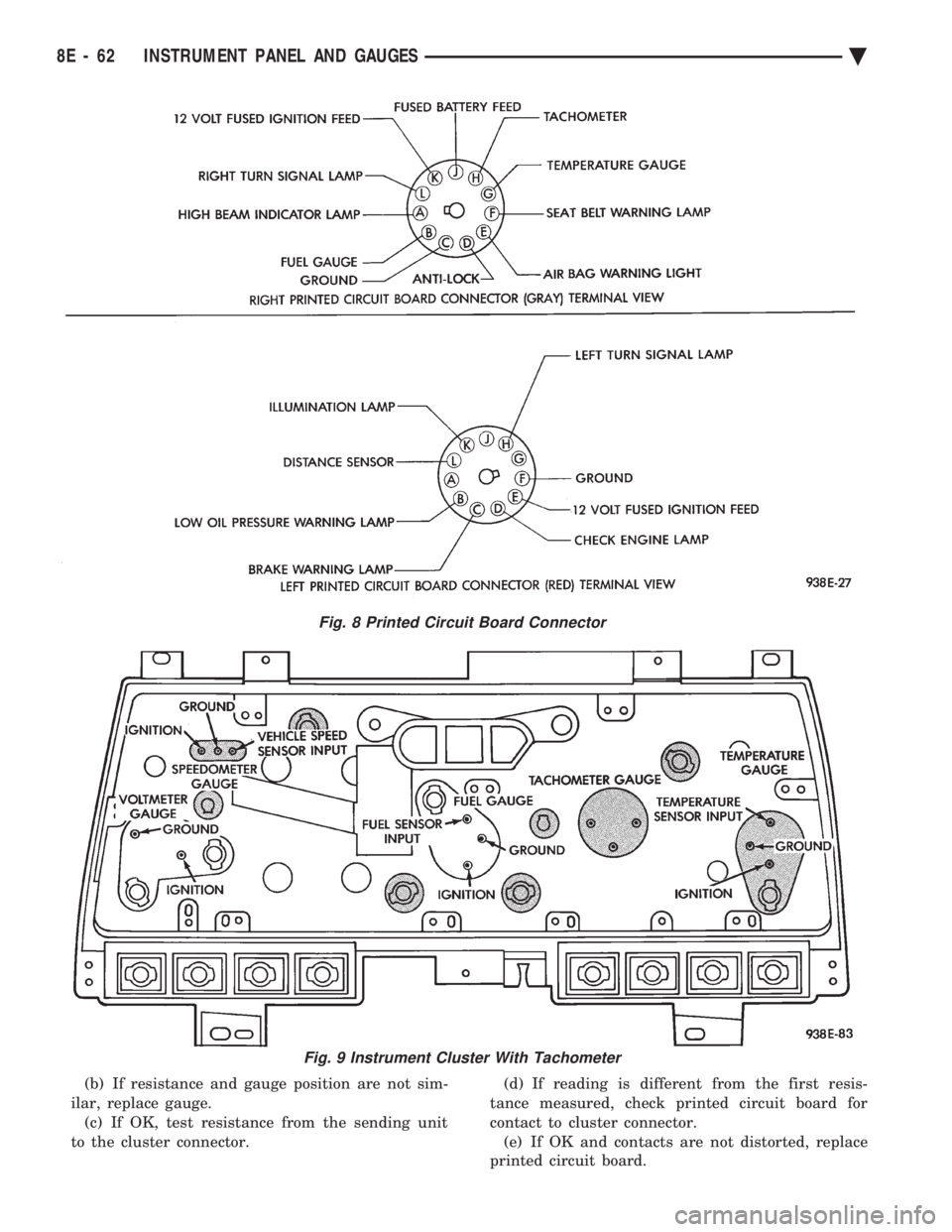
(b) If resistance and gauge position are not sim-
ilar, replace gauge. (c) If OK, test resistance from the sending unit
to the cluster connector. (d) If reading is different from the first resis-
tance measured, check printed circuit board for
contact to cluster connector. (e) If OK and contacts are not distorted, replace
printed circuit board.
Fig. 8 Printed Circuit Board Connector
Fig. 9 Instrument Cluster With Tachometer
8E - 62 INSTRUMENT PANEL AND GAUGES Ä
Page 555 of 2438
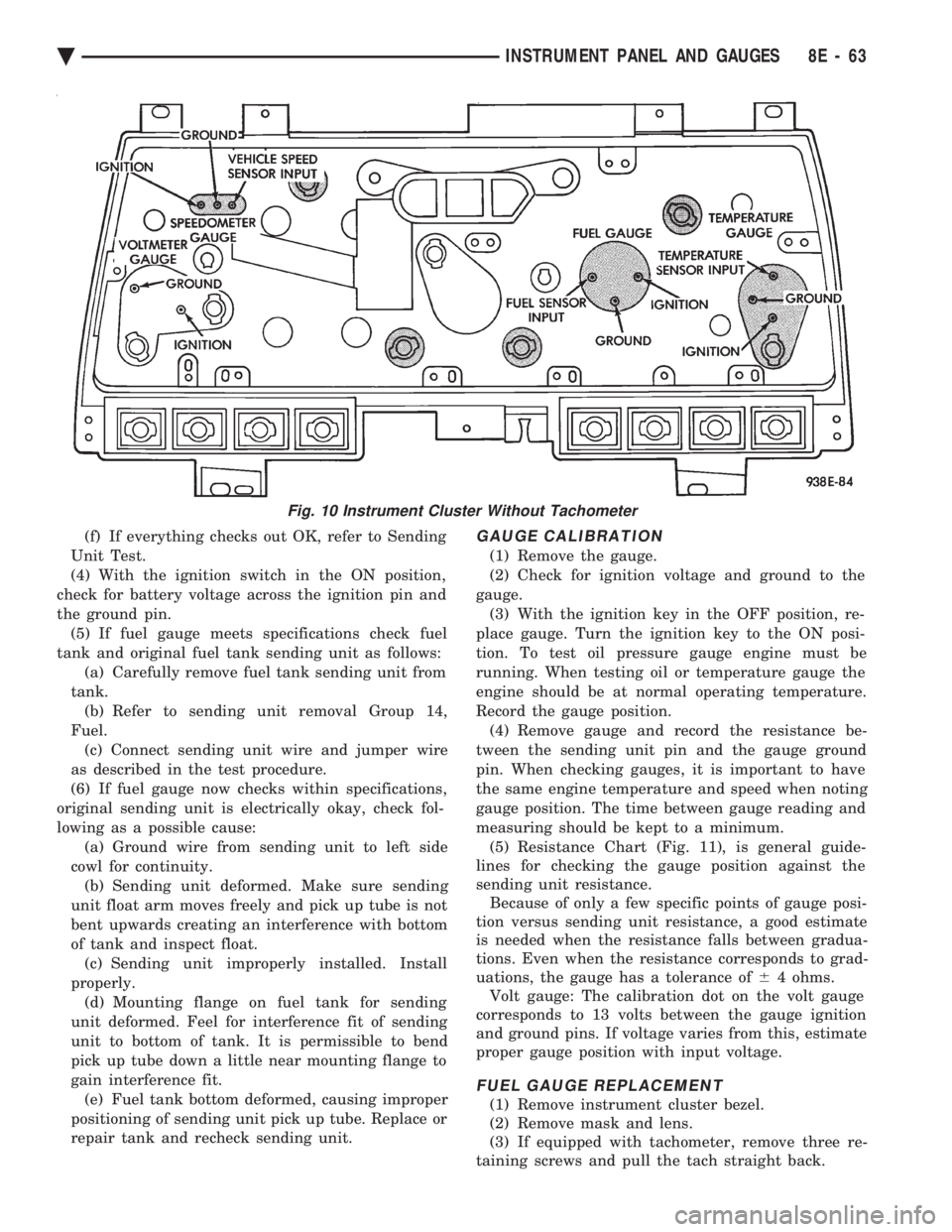
(f) If everything checks out OK, refer to Sending
Unit Test.
(4) With the ignition switch in the ON position,
check for battery voltage across the ignition pin and
the ground pin. (5) If fuel gauge meets specifications check fuel
tank and original fuel tank sending unit as follows: (a) Carefully remove fuel tank sending unit from
tank. (b) Refer to sending unit removal Group 14,
Fuel. (c) Connect sending unit wire and jumper wire
as described in the test procedure.
(6) If fuel gauge now checks within specifications,
original sending unit is electrically okay, check fol-
lowing as a possible cause: (a) Ground wire from sending unit to left side
cowl for continuity. (b) Sending unit deformed. Make sure sending
unit float arm moves freely and pick up tube is not
bent upwards creating an interference with bottom
of tank and inspect float. (c) Sending unit improperly installed. Install
properly. (d) Mounting flange on fuel tank for sending
unit deformed. Feel for interference fit of sending
unit to bottom of tank. It is permissible to bend
pick up tube down a little near mounting flange to
gain interference fit. (e) Fuel tank bottom deformed, causing improper
positioning of sending unit pick up tube. Replace or
repair tank and recheck sending unit.GAUGE CALIBRATION
(1) Remove the gauge.
(2) Check for ignition voltage and ground to the
gauge. (3) With the ignition key in the OFF position, re-
place gauge. Turn the ignition key to the ON posi-
tion. To test oil pressure gauge engine must be
running. When testing oil or temperature gauge the
engine should be at normal operating temperature.
Record the gauge position. (4) Remove gauge and record the resistance be-
tween the sending unit pin and the gauge ground
pin. When checking gauges, it is important to have
the same engine temperature and speed when noting
gauge position. The time between gauge reading and
measuring should be kept to a minimum. (5) Resistance Chart (Fig. 11), is general guide-
lines for checking the gauge position against the
sending unit resistance. Because of only a few specific points of gauge posi-
tion versus sending unit resistance, a good estimate
is needed when the resistance falls between gradua-
tions. Even when the resistance corresponds to grad-
uations, the gauge has a tolerance of 64 ohms.
Volt gauge: The calibration dot on the volt gauge
corresponds to 13 volts between the gauge ignition
and ground pins. If voltage varies from this, estimate
proper gauge position with input voltage.
FUEL GAUGE REPLACEMENT
(1) Remove instrument cluster bezel.
(2) Remove mask and lens.
(3) If equipped with tachometer, remove three re-
taining screws and pull the tach straight back.
Fig. 10 Instrument Cluster Without Tachometer
Ä INSTRUMENT PANEL AND GAUGES 8E - 63
Page 556 of 2438
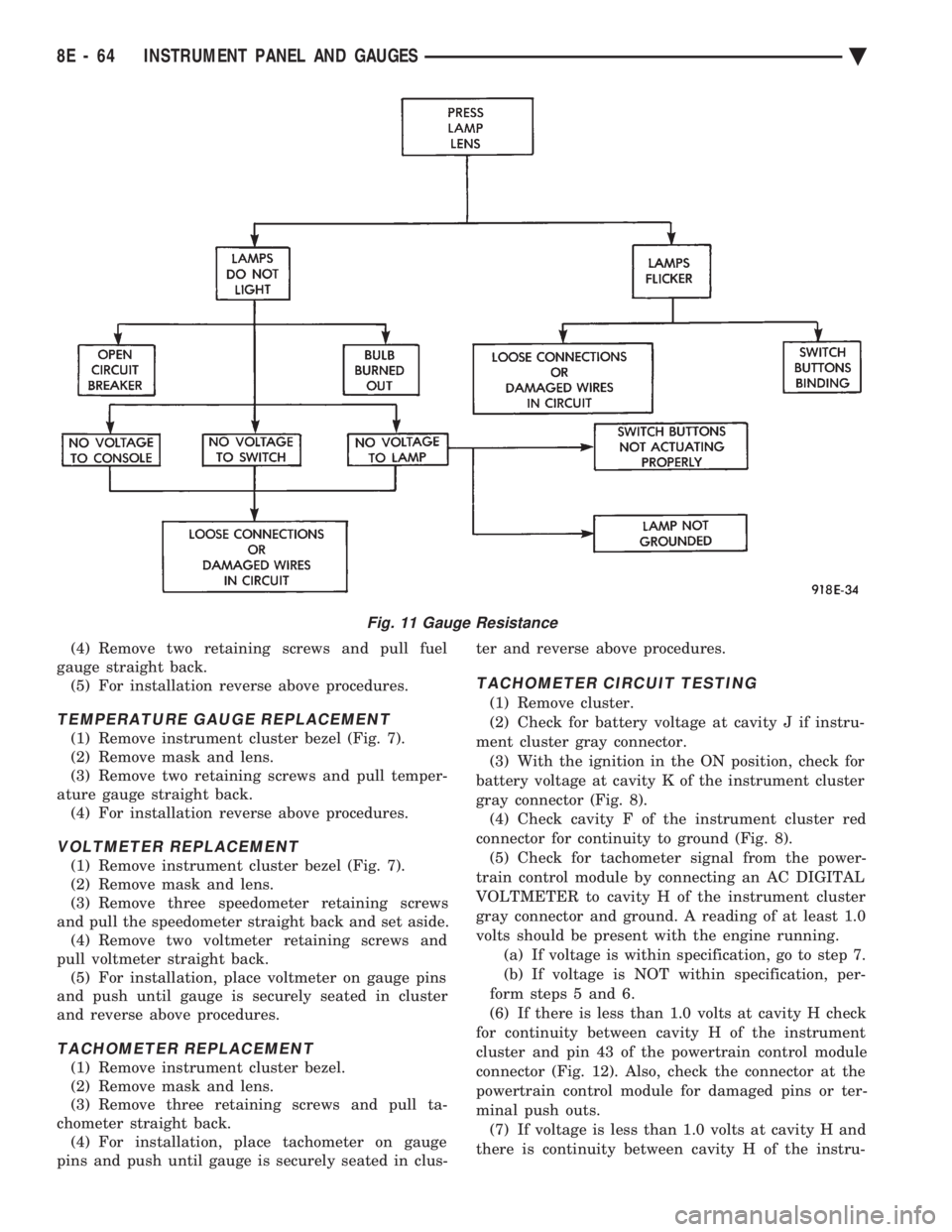
(4) Remove two retaining screws and pull fuel
gauge straight back. (5) For installation reverse above procedures.
TEMPERATURE GAUGE REPLACEMENT
(1) Remove instrument cluster bezel (Fig. 7).
(2) Remove mask and lens.
(3) Remove two retaining screws and pull temper-
ature gauge straight back. (4) For installation reverse above procedures.
VOLTMETER REPLACEMENT
(1) Remove instrument cluster bezel (Fig. 7).
(2) Remove mask and lens.
(3) Remove three speedometer retaining screws
and pull the speedometer straight back and set aside. (4) Remove two voltmeter retaining screws and
pull voltmeter straight back. (5) For installation, place voltmeter on gauge pins
and push until gauge is securely seated in cluster
and reverse above procedures.
TACHOMETER REPLACEMENT
(1) Remove instrument cluster bezel.
(2) Remove mask and lens.
(3) Remove three retaining screws and pull ta-
chometer straight back. (4) For installation, place tachometer on gauge
pins and push until gauge is securely seated in clus- ter and reverse above procedures.
TACHOMETER CIRCUIT TESTING
(1) Remove cluster.
(2) Check for battery voltage at cavity J if instru-
ment cluster gray connector. (3) With the ignition in the ON position, check for
battery voltage at cavity K of the instrument cluster
gray connector (Fig. 8). (4) Check cavity F of the instrument cluster red
connector for continuity to ground (Fig. 8). (5) Check for tachometer signal from the power-
train control module by connecting an AC DIGITAL
VOLTMETER to cavity H of the instrument cluster
gray connector and ground. A reading of at least 1.0
volts should be present with the engine running. (a) If voltage is within specification, go to step 7.
(b) If voltage is NOT within specification, per-
form steps 5 and 6.
(6) If there is less than 1.0 volts at cavity H check
for continuity between cavity H of the instrument
cluster and pin 43 of the powertrain control module
connector (Fig. 12). Also, check the connector at the
powertrain control module for damaged pins or ter-
minal push outs. (7) If voltage is less than 1.0 volts at cavity H and
there is continuity between cavity H of the instru-
Fig. 11 Gauge Resistance
8E - 64 INSTRUMENT PANEL AND GAUGES Ä
Page 557 of 2438
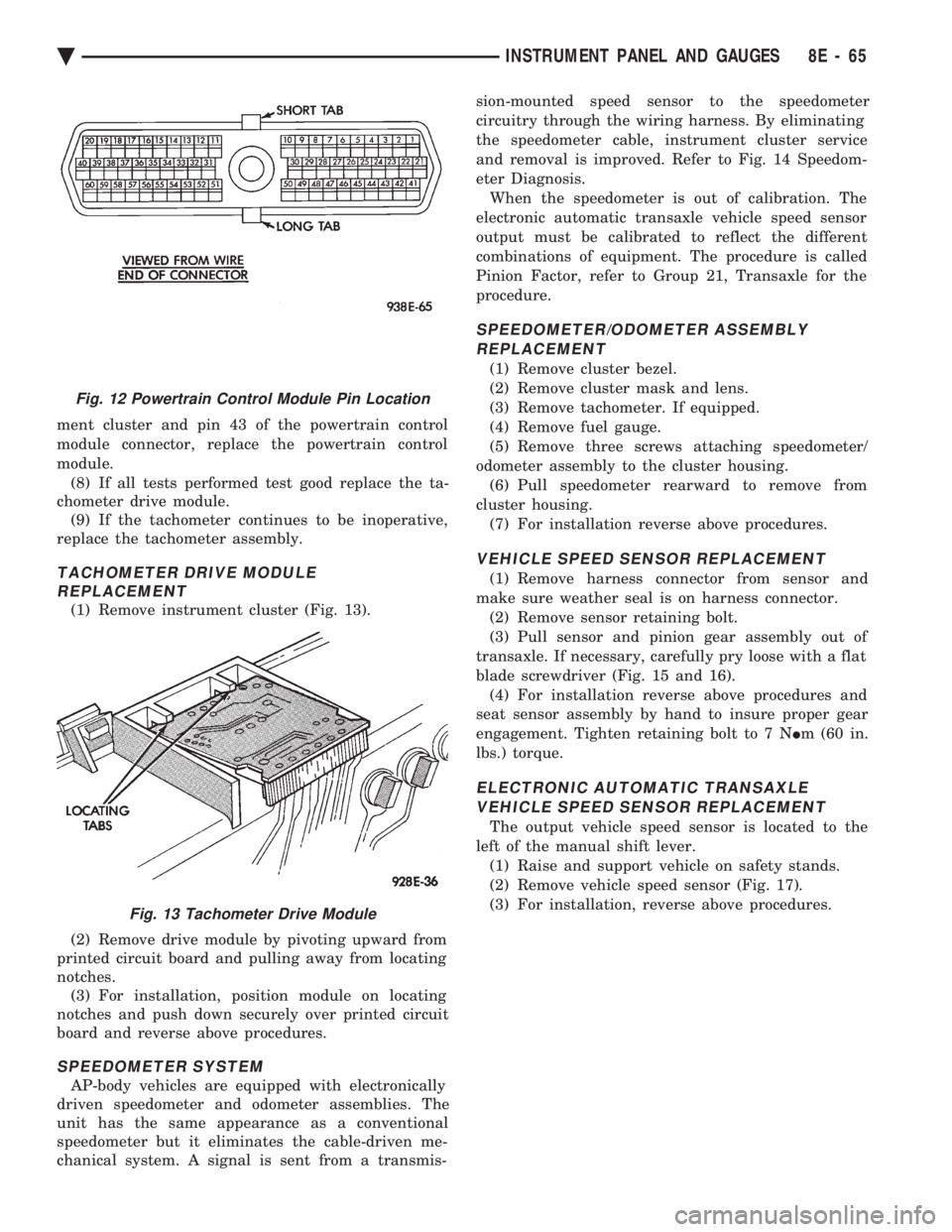
ment cluster and pin 43 of the powertrain control
module connector, replace the powertrain control
module. (8) If all tests performed test good replace the ta-
chometer drive module. (9) If the tachometer continues to be inoperative,
replace the tachometer assembly.
TACHOMETER DRIVE MODULE REPLACEMENT
(1) Remove instrument cluster (Fig. 13).
(2) Remove drive module by pivoting upward from
printed circuit board and pulling away from locating
notches. (3) For installation, position module on locating
notches and push down securely over printed circuit
board and reverse above procedures.
SPEEDOMETER SYSTEM
AP-body vehicles are equipped with electronically
driven speedometer and odometer assemblies. The
unit has the same appearance as a conventional
speedometer but it eliminates the cable-driven me-
chanical system. A signal is sent from a transmis- sion-mounted speed sensor to the speedometer
circuitry through the wiring harness. By eliminating
the speedometer cable, instrument cluster service
and removal is improved. Refer to Fig. 14 Speedom-
eter Diagnosis.
When the speedometer is out of calibration. The
electronic automatic transaxle vehicle speed sensor
output must be calibrated to reflect the different
combinations of equipment. The procedure is called
Pinion Factor, refer to Group 21, Transaxle for the
procedure.
SPEEDOMETER/ODOMETER ASSEMBLY REPLACEMENT
(1) Remove cluster bezel.
(2) Remove cluster mask and lens.
(3) Remove tachometer. If equipped.
(4) Remove fuel gauge.
(5) Remove three screws attaching speedometer/
odometer assembly to the cluster housing. (6) Pull speedometer rearward to remove from
cluster housing. (7) For installation reverse above procedures.
VEHICLE SPEED SENSOR REPLACEMENT
(1) Remove harness connector from sensor and
make sure weather seal is on harness connector. (2) Remove sensor retaining bolt.
(3) Pull sensor and pinion gear assembly out of
transaxle. If necessary, carefully pry loose with a flat
blade screwdriver (Fig. 15 and 16). (4) For installation reverse above procedures and
seat sensor assembly by hand to insure proper gear
engagement. Tighten retaining bolt to 7 N Im (60 in.
lbs.) torque.
ELECTRONIC AUTOMATIC TRANSAXLE VEHICLE SPEED SENSOR REPLACEMENT
The output vehicle speed sensor is located to the
left of the manual shift lever. (1) Raise and support vehicle on safety stands.
(2) Remove vehicle speed sensor (Fig. 17).
(3) For installation, reverse above procedures.
Fig. 12 Powertrain Control Module Pin Location
Fig. 13 Tachometer Drive Module
Ä INSTRUMENT PANEL AND GAUGES 8E - 65
Page 558 of 2438
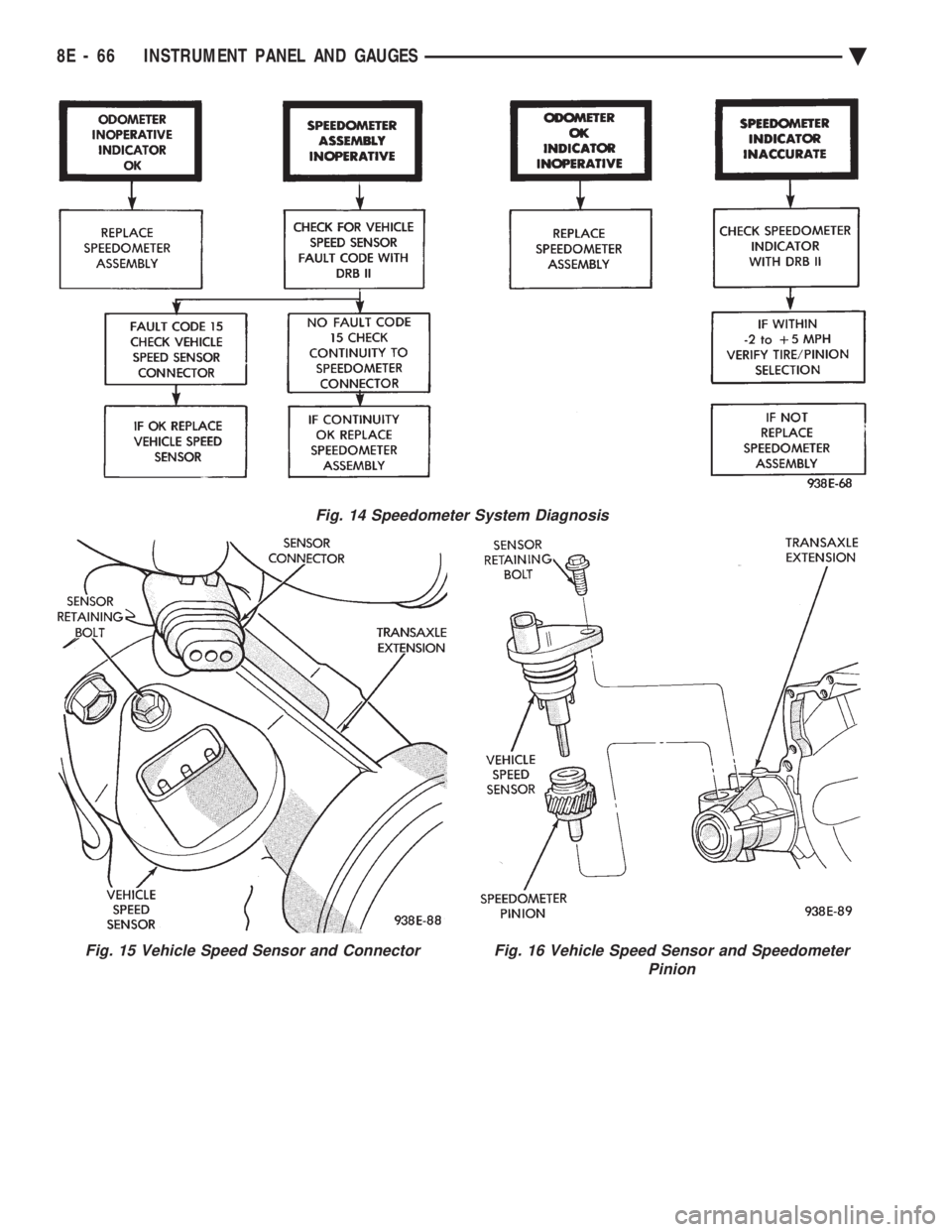
Fig. 14 Speedometer System Diagnosis
Fig. 15 Vehicle Speed Sensor and ConnectorFig. 16 Vehicle Speed Sensor and Speedometer Pinion
8E - 66 INSTRUMENT PANEL AND GAUGES Ä
Page 559 of 2438
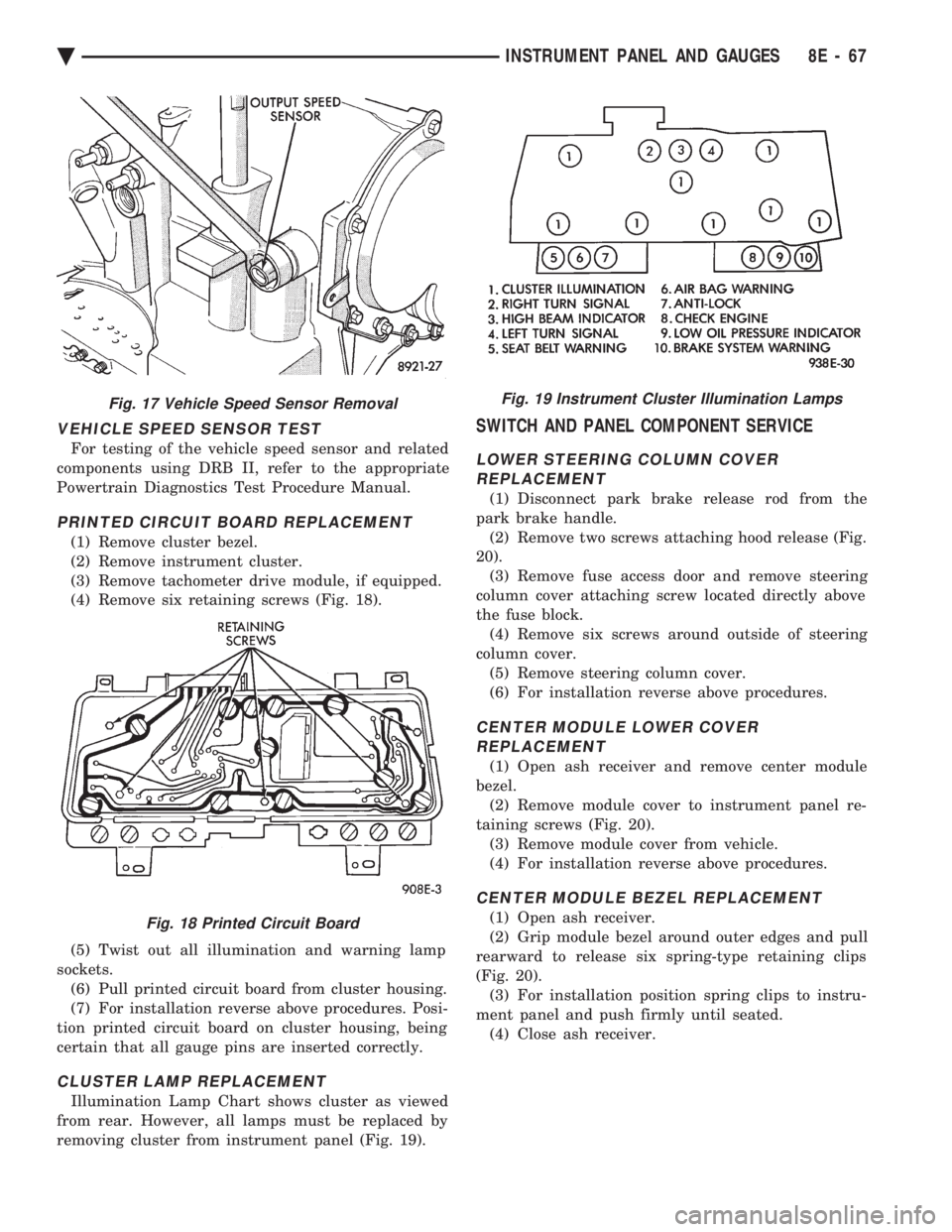
VEHICLE SPEED SENSOR TEST
For testing of the vehicle speed sensor and related
components using DRB II, refer to the appropriate
Powertrain Diagnostics Test Procedure Manual.
PRINTED CIRCUIT BOARD REPLACEMENT
(1) Remove cluster bezel.
(2) Remove instrument cluster.
(3) Remove tachometer drive module, if equipped.
(4) Remove six retaining screws (Fig. 18).
(5) Twist out all illumination and warning lamp
sockets. (6) Pull printed circuit board from cluster housing.
(7) For installation reverse above procedures. Posi-
tion printed circuit board on cluster housing, being
certain that all gauge pins are inserted correctly.
CLUSTER LAMP REPLACEMENT
Illumination Lamp Chart shows cluster as viewed
from rear. However, all lamps must be replaced by
removing cluster from instrument panel (Fig. 19).
SWITCH AND PANEL COMPONENT SERVICE
LOWER STEERING COLUMN COVER REPLACEMENT
(1) Disconnect park brake release rod from the
park brake handle. (2) Remove two screws attaching hood release (Fig.
20). (3) Remove fuse access door and remove steering
column cover attaching screw located directly above
the fuse block. (4) Remove six screws around outside of steering
column cover. (5) Remove steering column cover.
(6) For installation reverse above procedures.
CENTER MODULE LOWER COVER REPLACEMENT
(1) Open ash receiver and remove center module
bezel. (2) Remove module cover to instrument panel re-
taining screws (Fig. 20). (3) Remove module cover from vehicle.
(4) For installation reverse above procedures.
CENTER MODULE BEZEL REPLACEMENT
(1) Open ash receiver.
(2) Grip module bezel around outer edges and pull
rearward to release six spring-type retaining clips
(Fig. 20). (3) For installation position spring clips to instru-
ment panel and push firmly until seated. (4) Close ash receiver.
Fig. 17 Vehicle Speed Sensor Removal
Fig. 18 Printed Circuit Board
Fig. 19 Instrument Cluster Illumination Lamps
Ä INSTRUMENT PANEL AND GAUGES 8E - 67
Page 560 of 2438
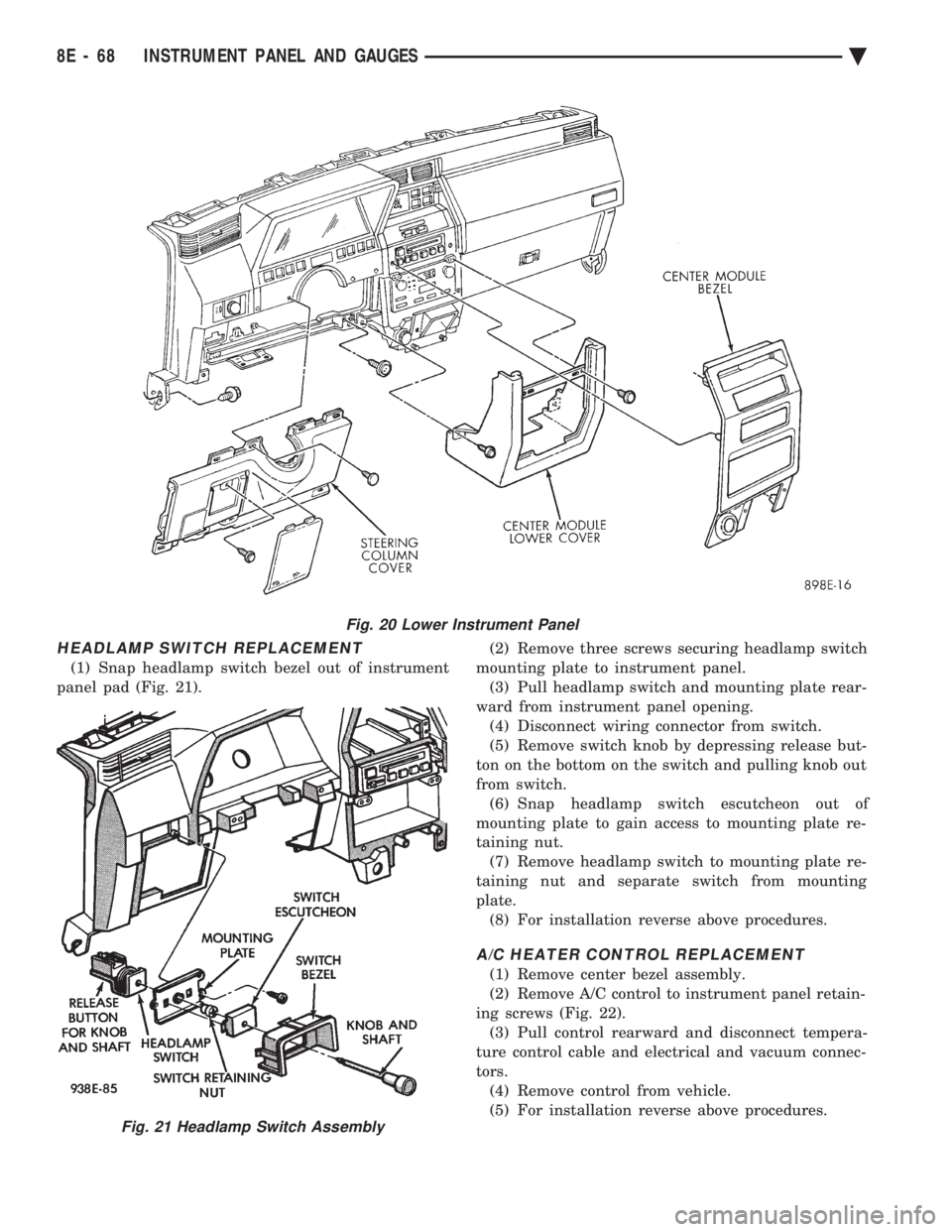
HEADLAMP SWITCH REPLACEMENT
(1) Snap headlamp switch bezel out of instrument
panel pad (Fig. 21). (2) Remove three screws securing headlamp switch
mounting plate to instrument panel. (3) Pull headlamp switch and mounting plate rear-
ward from instrument panel opening. (4) Disconnect wiring connector from switch.
(5) Remove switch knob by depressing release but-
ton on the bottom on the switch and pulling knob out
from switch. (6) Snap headlamp switch escutcheon out of
mounting plate to gain access to mounting plate re-
taining nut. (7) Remove headlamp switch to mounting plate re-
taining nut and separate switch from mounting
plate. (8) For installation reverse above procedures.
A/C HEATER CONTROL REPLACEMENT
(1) Remove center bezel assembly.
(2) Remove A/C control to instrument panel retain-
ing screws (Fig. 22). (3) Pull control rearward and disconnect tempera-
ture control cable and electrical and vacuum connec-
tors. (4) Remove control from vehicle.
(5) For installation reverse above procedures.
Fig. 20 Lower Instrument Panel
Fig. 21 Headlamp Switch Assembly
8E - 68 INSTRUMENT PANEL AND GAUGES Ä