DATSUN 210 1979 Service Manual
Manufacturer: DATSUN, Model Year: 1979, Model line: 210, Model: DATSUN 210 1979Pages: 548, PDF Size: 28.66 MB
Page 121 of 548
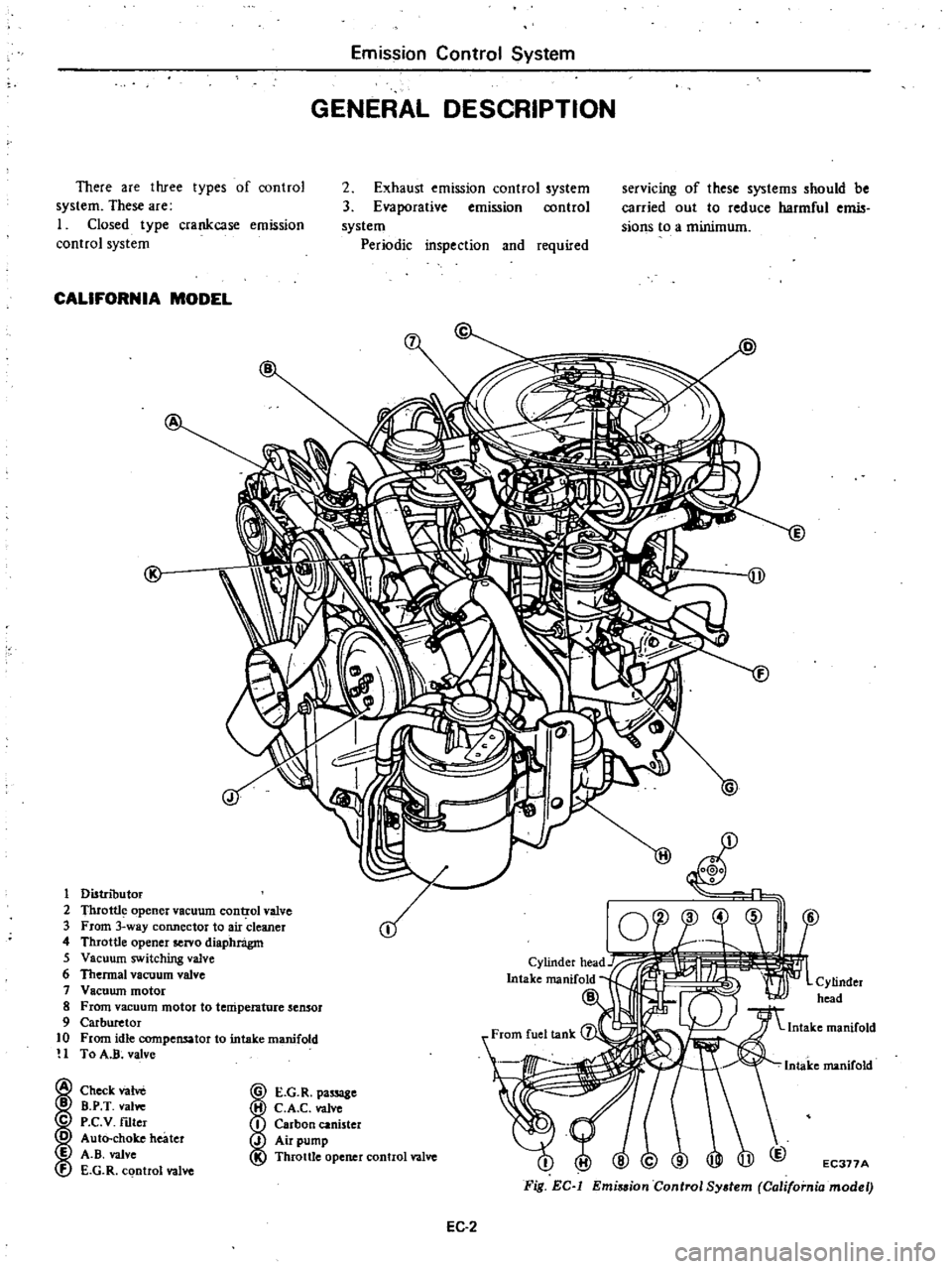
Emission
Control
System
GENERAL
DESCRIPTION
There
are
three
types
of
control
system
These
are
I
Closed
type
crankcase
emission
control
system
2
Exhaust
emISSIon
control
system
3
Evaporative
emission
control
system
Periodic
inspection
and
required
sefVIcmg
of
these
systems
should
be
carried
out
to
reduce
harmful
emis
sions
to
a
minimum
CALIFORNIA
MODEL
1
Distributor
2
Thrott1
opener
vacuum
cont
rol
valve
3
From
3
way
connector
to
air
cleaner
4
Throttle
opener
servo
diaphnigm
5
Vacuum
switching
valve
6
Thermal
vacuum
valve
7
Vacuwn
motor
8
From
vacuum
motor
to
temperature
sensor
9
Carburetor
10
From
idle
compensator
to
intake
manifold
H
To
A
R
valve
Check
vane
B
B
P
T
vallie
C
P
c
V
nIter
o
Auto
choke
heater
E
A
B
valve
f
E
G
R
control
valve
A
E
D
j
L
I
E
G
R
pa
8e
H
C
A
C
valve
I
Carbon
canister
J
Air
pump
Throttle
opener
control
valve
EC377A
Fig
EC
l
Emi
sion
Control
System
California
model
EC
2
Page 122 of 548
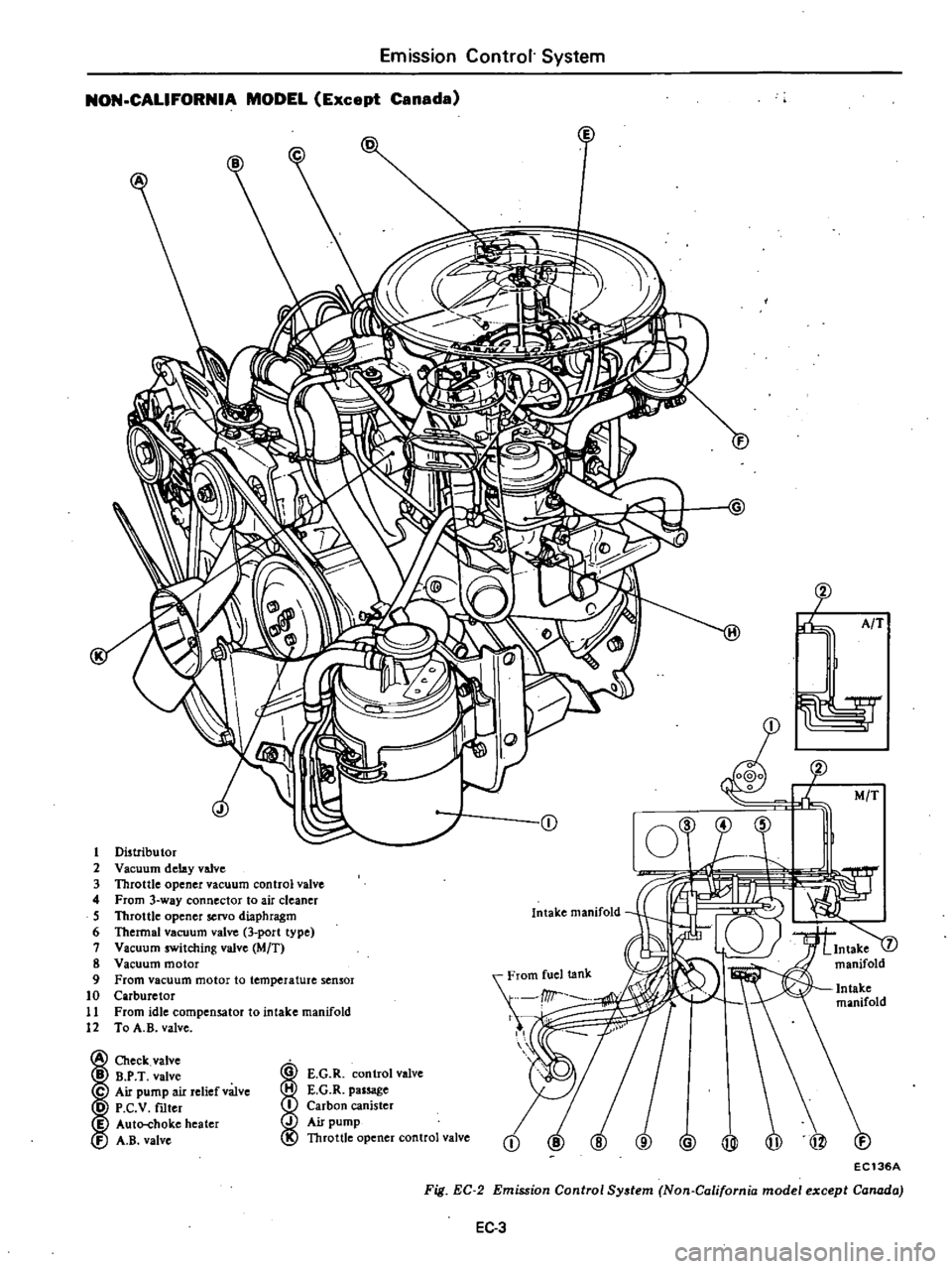
Emission
Control
System
NON
CALIFORNIA
MODEL
Except
Canada
5
CD
O@
j
l
t
AfT
M
T
1
Distributor
2
Vaellum
delay
valve
3
Throttle
opener
vacuum
control
valve
4
From
3
way
connector
to
air
cleaner
5
Throttle
opener
servo
diaphragm
6
Thermal
vacuum
valve
3
port
type
7
Vacuum
switching
valve
eMIT
8
Vacuum
motor
9
From
vacuum
motor
to
temperature
sensor
10
Carburetor
11
From
idle
compensator
to
intake
manifold
12
To
A
B
valve
rom
I
It
Intake
manifold
Check
valve
B
P
T
valve
C
Air
pump
air
relief
valve
D
P
C
V
mter
I
Auto
choke
heater
A
B
valve
I
E
G
R
control
valve
E
G
R
passage
Carbon
canister
Air
pump
Throttle
opener
control
valve
@
@
to
EC136A
Fig
EC
2
Emission
Control
System
Non
Californin
model
except
Canada
EC
3
Page 123 of 548
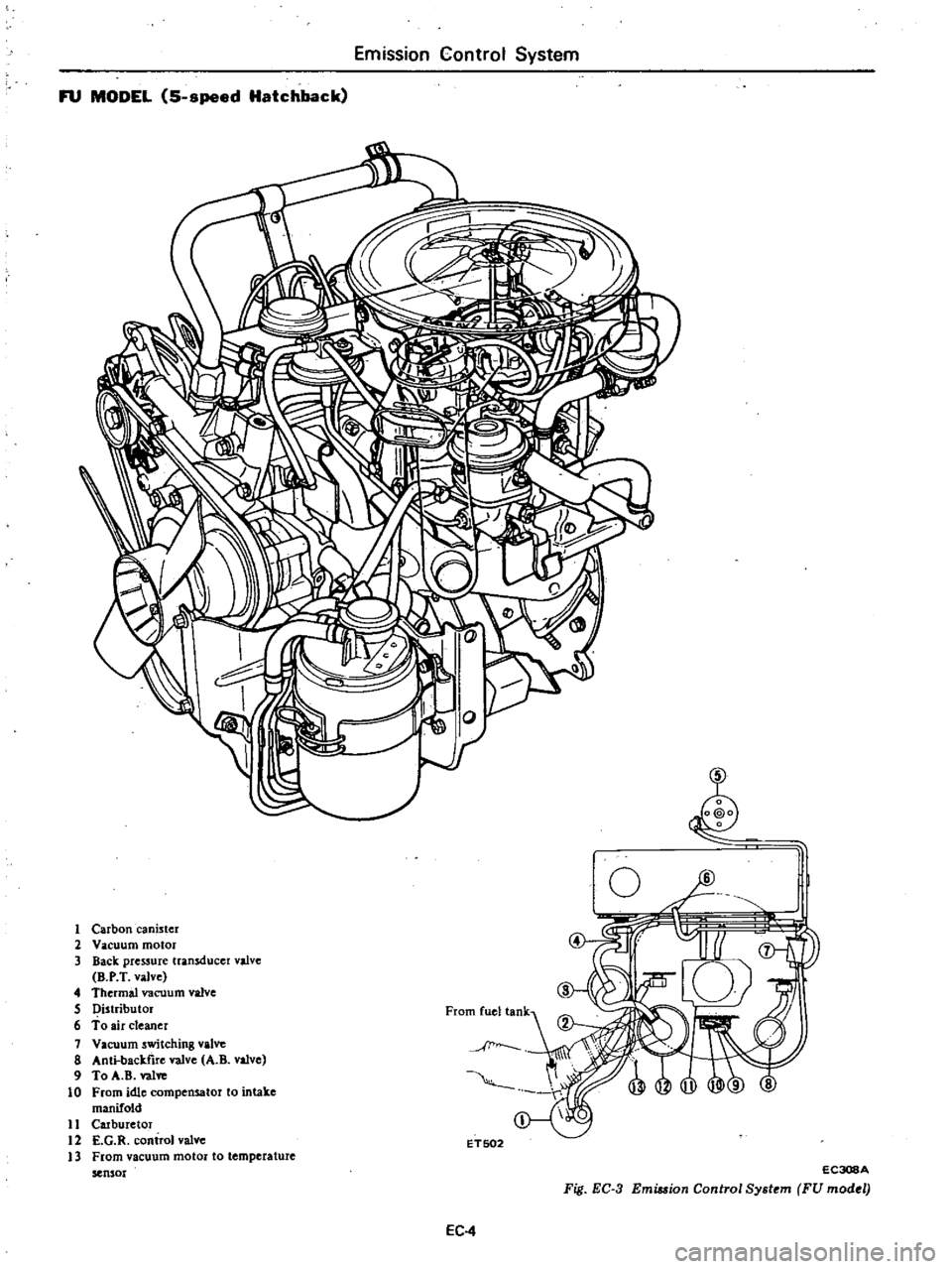
Emission
Control
System
FU
MODEL
S
speed
Hatchback
1
Carbon
canister
2
Vacuum
motor
3
Back
pressure
transducer
valve
B
P
T
valve
4
Thermal
vacuum
valve
S
I
istributor
6
To
air
cleaner
1
Vacuum
switching
valve
8
Anti
backfire
valve
A
B
valve
9
To
A
B
valve
10
From
idle
compensator
to
intake
manifold
11
Carburetor
12
E
G
R
control
valve
13
From
vacuum
motol
to
temperature
sensoI
ET502
EC308A
Fig
EC
3
Emission
Control
System
FU
model
EC
4
Page 124 of 548
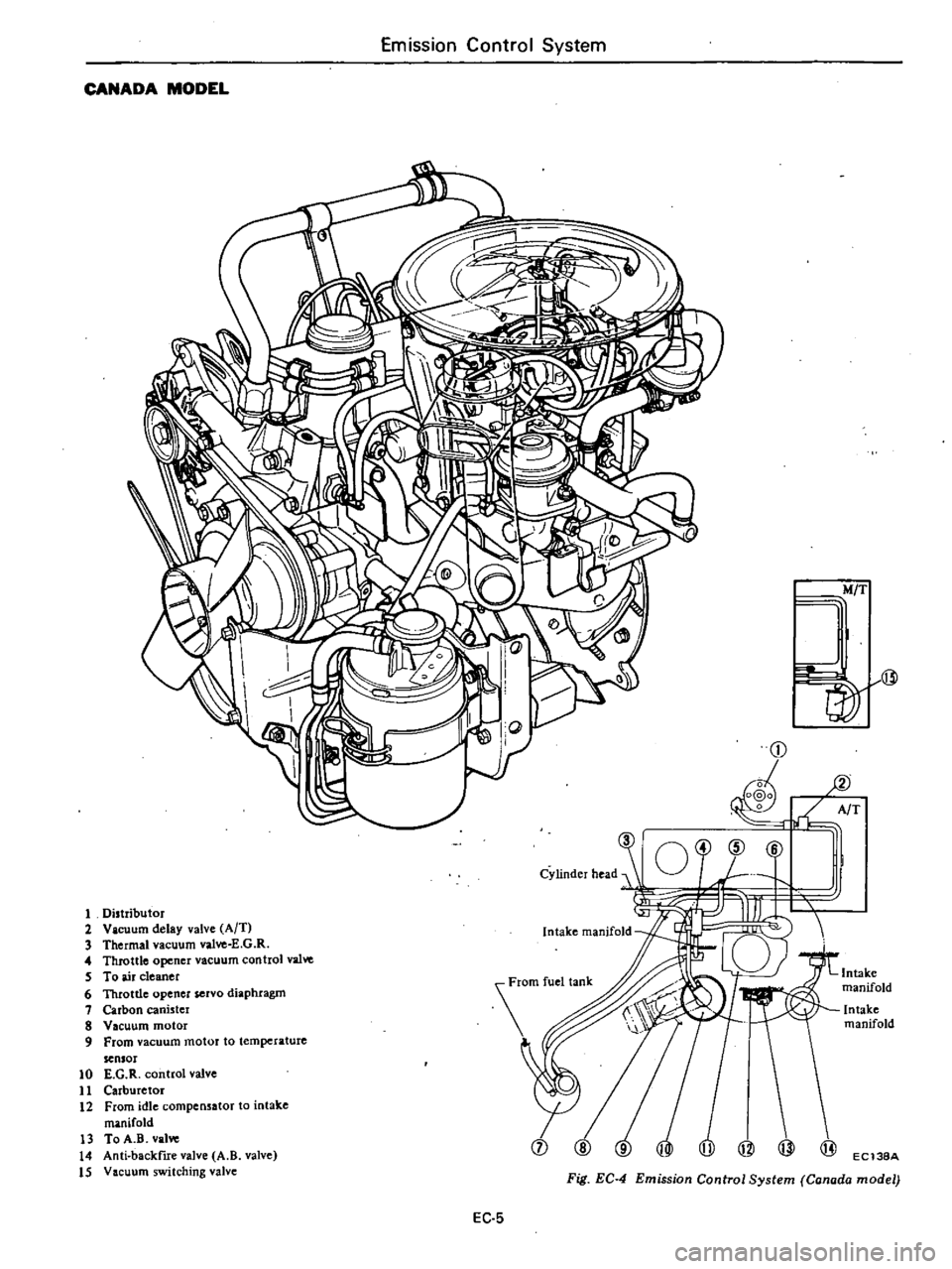
Emission
Control
System
CANADA
MODEL
1
Distributor
2
Vacuum
delay
valve
AfT
3
Thermal
vacuum
valve
E
G
R
4
Throttle
opener
vacuum
control
valve
S
To
air
cleaner
6
Throttle
opener
servo
diaphragm
7
Carbon
canister
8
Vacuum
motor
9
From
vacuum
motor
to
temperature
sensor
10
E
G
R
control
valve
11
Carburetor
12
From
idle
compensator
to
intake
manifold
13
To
A
B
valve
14
Anti
backltre
valve
A
B
valve
15
Vacuum
switching
valve
M
T
@
CD
ft
o@o
0
LA
T
CID
om
fuel
tank
Intake
manifold
Intake
manifold
@
It
Il
9
EC138A
Fig
EC
4
Emission
Control
System
Canada
model
EC
5
Page 125 of 548
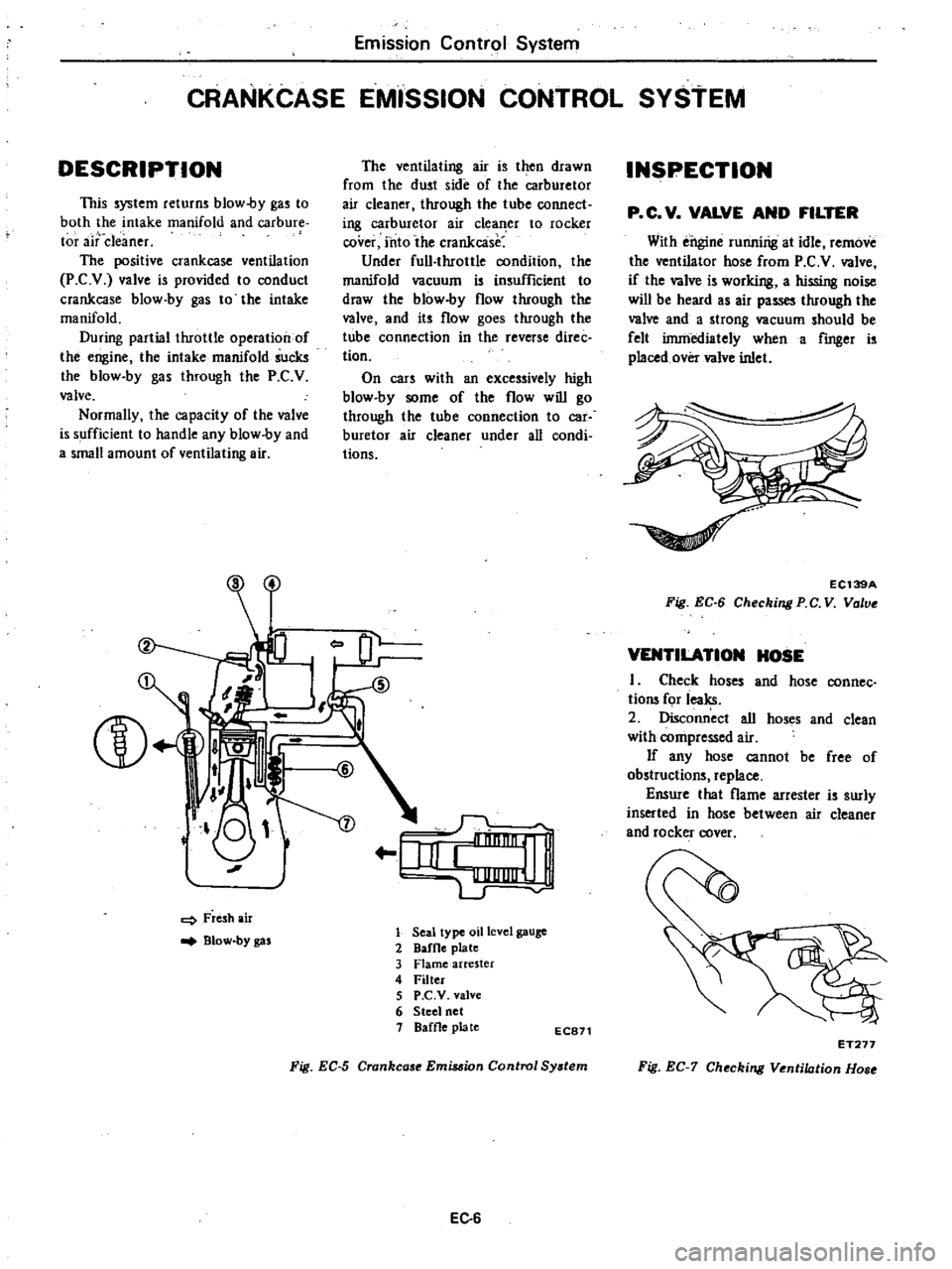
Emission
Control
System
CRANKCASE
EMISSION
CONTROL
SYSTEM
DESCRIPTION
This
system
returns
blow
by
gas
to
both
the
intake
manifold
and
carbure
tor
aitdeaner
The
positive
crankcase
ventilation
P
C
v
valve
is
provided
to
conduct
crankcase
blow
by
gas
to
the
intake
manifold
During
partial
throttle
operation
of
the
engine
the
intake
manifold
sucks
the
blow
by
gas
through
the
P
C
V
valve
Normally
the
capacity
of
the
valve
is
sufficient
to
handle
any
blow
by
and
a
small
amount
of
ventilating
air
L
J
J
o
I
Fresh
air
Blow
by
gas
The
ventilating
air
is
then
drawn
from
the
dust
side
of
the
carburetor
air
cleaner
through
the
tube
connect
ing
carburetor
air
cle
er
to
rocker
cover
into
the
crankcase
Under
full
throttle
condition
the
manifold
vacuum
is
insufficient
to
draw
the
blow
by
flow
through
the
valve
and
its
flow
goes
through
the
tube
connection
in
the
reverse
direc
tion
On
cars
with
an
excessively
high
blow
by
some
of
the
flow
will
go
through
the
tube
connection
to
car
buretor
air
cleaner
under
all
condi
tions
r
IiI
e
1
LJ
1
Seal
type
oil
level
gauge
2
DafOe
plate
3
Flame
arrester
4
Filter
5
P
C
V
valve
6
Steel
net
1
Baffle
plate
EC871
Fig
EC
5
Crankcase
Emis
ion
Control
Sy
tem
EC
6
INSPECTION
p
C
V
VALVE
AND
FILTER
With
ei
gine
runnirig
at
idle
remove
the
ventilator
hose
from
P
C
V
valve
if
the
valve
is
working
a
hissing
noise
wiD
be
heard
as
air
passes
through
the
valve
and
a
strong
vacuum
should
be
felt
irnniediately
when
a
fmger
is
placed
over
valve
inlet
EC139A
Fig
EC
6
Checking
PC
V
Vo
ve
VENTILATION
HOSE
I
Check
hoses
and
hose
connec
tions
for
ieaks
2
oisconn
ct
all
hoses
and
clean
with
compressed
air
If
any
hose
cannot
be
free
of
obstructions
replace
Ensure
that
flame
arrester
is
surly
inserted
in
hose
between
air
cleaner
and
rocker
rover
ET277
Fig
EC
7
Checking
Ventilation
Hose
Page 126 of 548
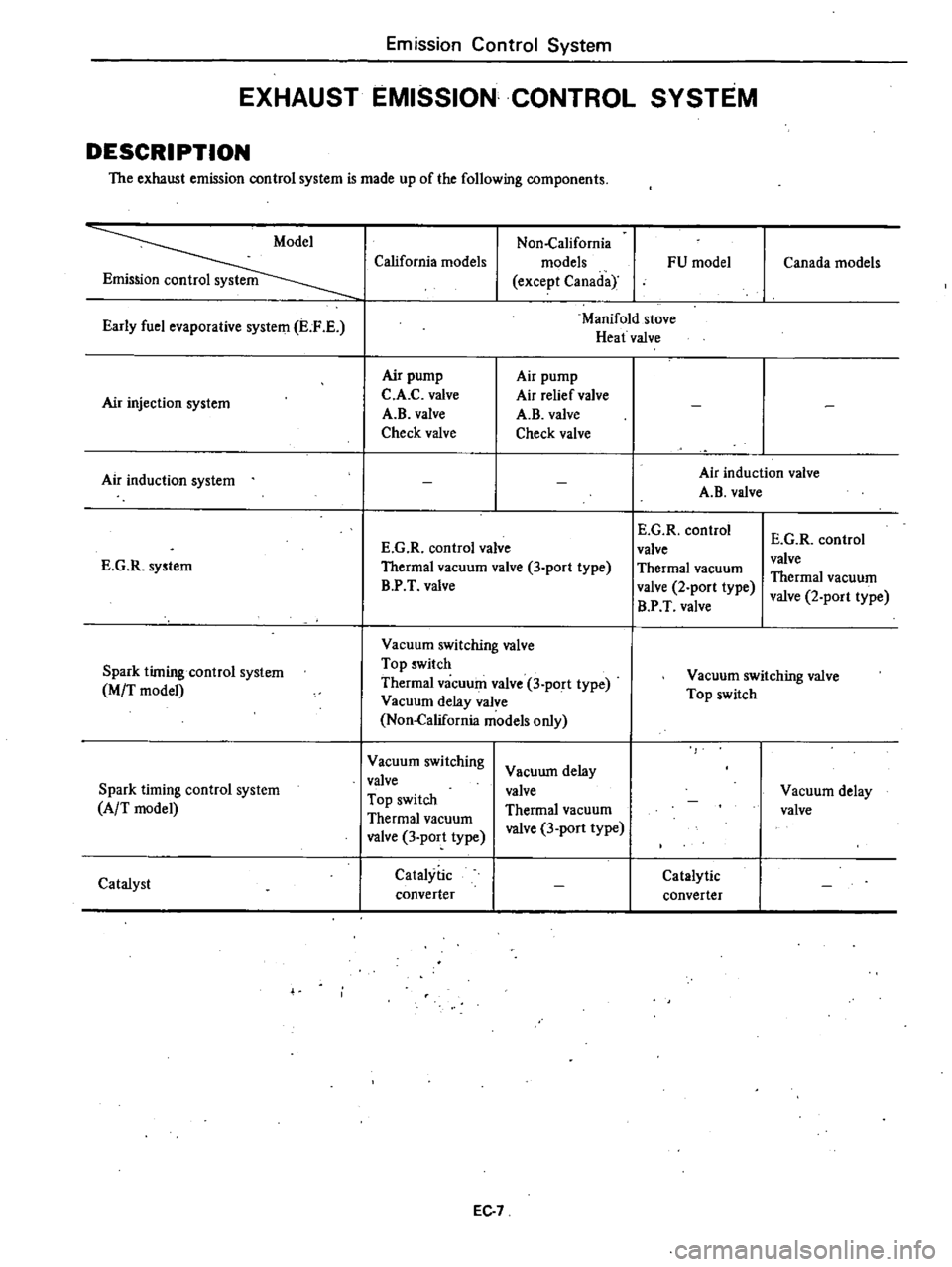
Emission
Control
System
EXHAUST
EMISSION
CONTROL
SYSTEM
DESCRIPTION
The
exhaust
emission
control
system
is
made
up
of
the
following
components
Early
fuel
evaporative
system
E
F
E
Air
injection
system
Air
induction
system
E
G
R
system
Spark
tirningcontrol
system
M
T
model
Spark
timing
control
system
A
T
model
Catalyst
Non
California
California
models
models
except
CanadaY
FU
model
Manifold
stove
Heat
valve
Air
pump
C
A
C
valve
A
B
valve
Check
valve
Air
pump
Air
relief
valve
A
B
valve
Check
valve
E
G
R
control
valve
Thermal
vacuum
valve
3
port
type
B
P
T
valve
Vacuum
switching
valve
Top
switch
Thermal
vacuum
valve
3
port
type
Vacuum
delay
valve
Non
California
models
only
Vacuum
switching
valve
Top
switch
Thermal
vacuum
valve
3
port
type
Vacuum
delay
valve
Thermal
vacuum
valve
3
port
type
Catalytic
converter
EC
7
Canada
models
Air
induction
valve
A
B
valve
E
G
R
control
valve
Thermal
vacuum
valve
2
port
type
B
P
T
valve
E
G
R
control
valve
Thermal
vacuum
valve
2
port
type
Vacuum
switching
valve
Top
switch
Catalytic
converter
Vacuum
delay
valve
Page 127 of 548
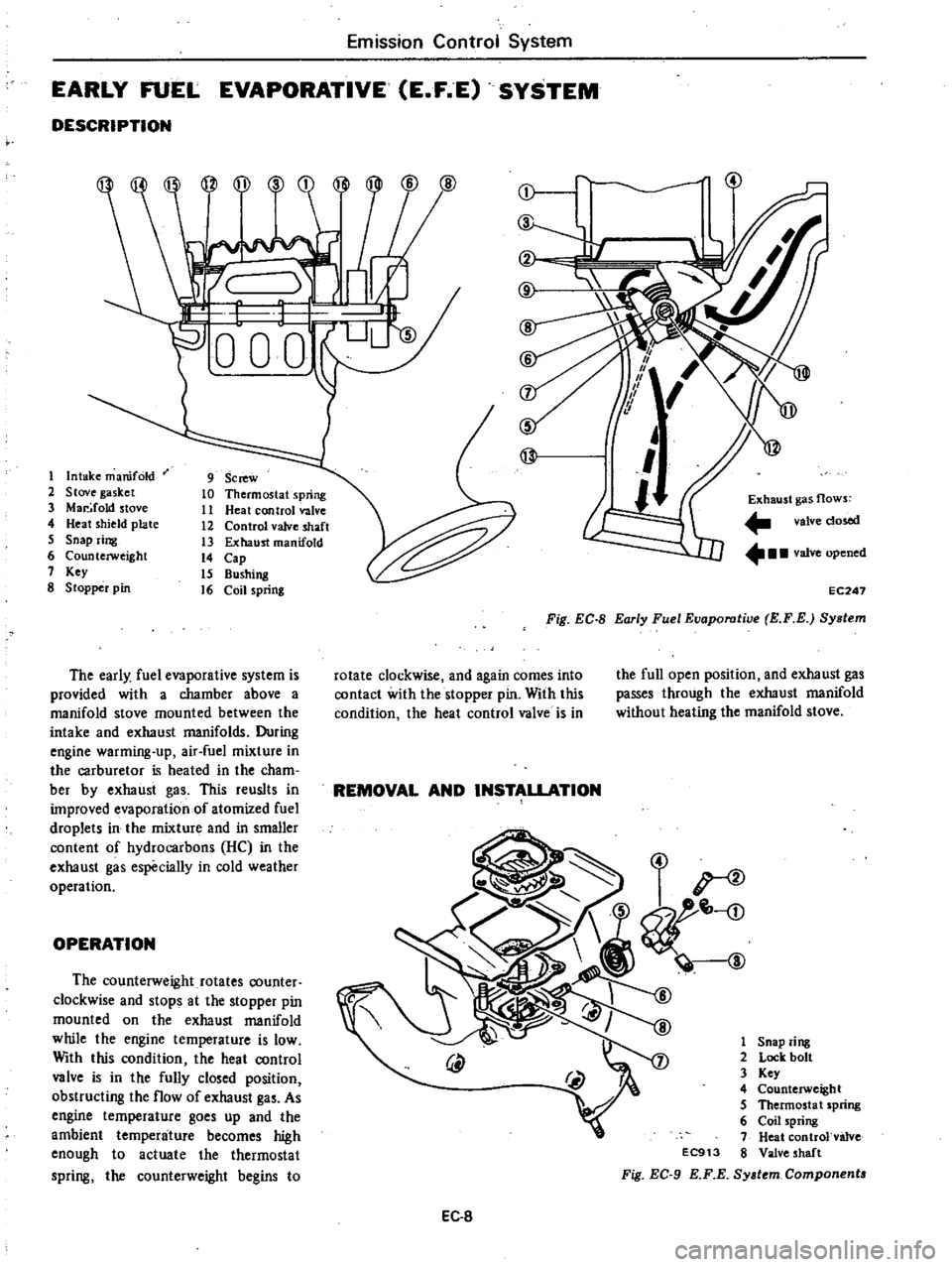
Emission
Control
System
EARLY
FUEL
EVAPORATIVE
E
FE
SYSTEM
DESCRIPTION
@
jl
D
W
o
0
0
UL
@
1
Intake
manifold
9
Screw
2
Stove
gasket
10
Thermostat
spring
3
Mar
fold
stove
11
Heat
control
valve
4
Heat
shield
plate
12
Control
valve
shaft
5
Snap
ring
13
Exhaust
manifold
6
Countczwcight
14
Cap
7
Key
15
Bushing
8
Stopper
pin
16
Coil
spring
The
early
fuel
evaporative
system
is
provided
with
a
chamber
above
a
manifold
stove
mounted
between
the
intake
and
exhaust
manifolds
During
engine
warming
up
air
fuel
mixture
in
the
carburetor
is
heated
in
the
cham
ber
by
exhaust
gas
This
reuslts
in
improved
evaporation
of
atomized
fuel
droplets
in
the
mixture
and
in
smaller
content
of
hydrocarbons
HC
in
the
exhaust
gas
especially
in
cold
weather
operation
OPERATION
The
counterweight
rotates
counter
clockwise
and
stops
at
the
stopper
pin
mounted
on
the
exhaust
manifold
while
the
engine
temperature
is
low
With
this
condition
the
heat
control
valve
is
in
the
fully
closed
position
obstructing
the
flow
of
exhaust
gas
As
engine
temperature
goes
up
and
the
ambient
temperature
becomes
high
enough
to
actuate
the
thermostat
spring
the
counterweight
begins
to
j
@
l
7
1
1
5
If
@
I
Exhaust
gas
flows
valve
dosed
valve
opened
EC247
Fig
EC
8
Early
Fuel
Eaaporatiae
E
F
E
System
rotate
clockwise
and
again
comes
into
contact
with
the
stopper
pin
With
this
condition
the
heat
control
valve
is
in
the
full
open
position
and
exhaust
gas
passes
through
the
exhaust
manifold
without
heating
the
manifold
stove
REMOVAL
AND
INSTALLATION
1
Snap
ring
2
Lock
bolt
3
Key
4
Counterweight
5
Thermosta
t
spring
6
Coil
spring
7
Heat
controlvalve
EC913
8
Valve
shaft
Fig
EC
9
KF
E
Sy
tem
Component
EC
8
Page 128 of 548
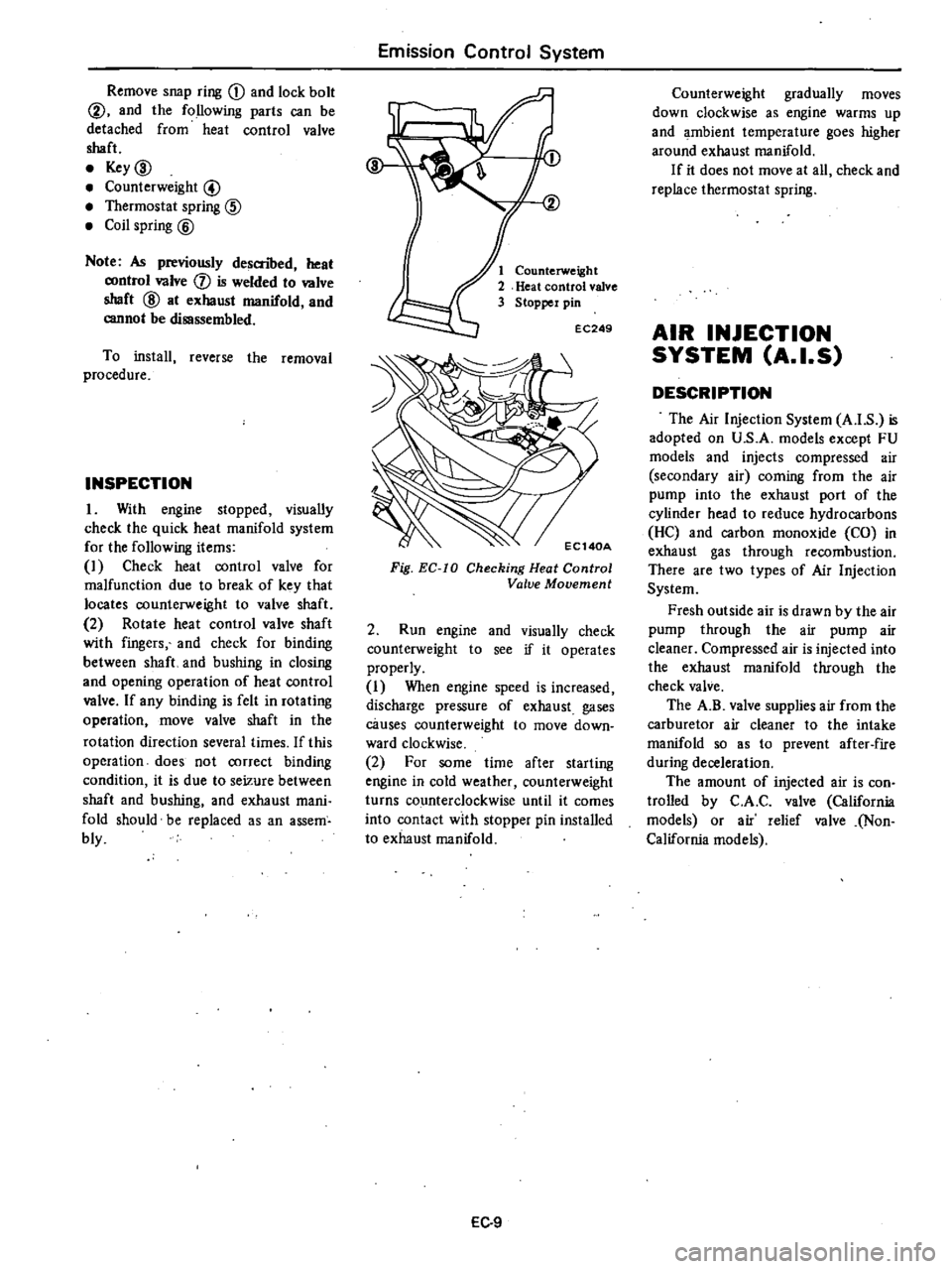
Remove
snap
ring
CD
and
lock
bolt
@
and
the
following
parts
can
be
detached
from
heat
control
valve
shaft
Key
ID
Counterweight
@
Thermostat
spring
@
Coil
spring
@
Note
As
previously
descnbed
heat
control
valve
j
is
welded
to
valve
shaft
@
at
exhaust
manifold
and
cannot
be
disassembled
To
install
reverse
the
removal
procedure
INSPECTION
1
With
engine
stopped
visually
check
the
quick
heat
manifold
system
for
the
following
items
I
Check
heat
control
valve
for
malfunction
due
to
break
of
key
that
locates
counterweight
to
valve
shaft
2
Rotate
heat
control
valve
shaft
with
fingers
and
check
for
binding
between
shaft
and
bushing
in
closing
and
opening
operation
of
heat
control
valve
If
any
binding
is
felt
in
rotating
operation
move
valve
shaft
in
the
rotation
direction
several
times
If
this
operation
does
not
correct
binding
condition
it
is
due
to
seizure
between
shaft
and
bushing
and
exhaust
mani
fold
should
be
replaced
as
an
assem
bly
Emission
Control
System
Counterweight
Heat
control
valve
Stopper
pin
EC249
Fig
EC
IO
Checking
Heat
Control
Valve
Movement
2
Run
engine
and
visually
check
counterweight
to
see
if
it
operates
properly
I
When
engine
speed
is
increased
discharge
pressure
of
exhaust
gases
causes
counterweight
to
move
down
ward
clockwise
2
For
some
time
after
starting
engine
in
cold
weather
counterweight
turns
counterclockwise
until
it
comes
into
contact
with
stopper
pin
installed
to
exhaust
manifold
EC
9
Counterweight
gradually
moves
down
clockwise
as
engine
warms
up
and
ambient
temperature
goes
higher
around
exhaust
manifold
If
it
does
not
move
at
all
check
and
replace
thermostat
spring
AIR
INJECTION
SYSTEM
A
I
S
DESCRIPTION
The
Air
Injection
System
A
I
S
is
adopted
on
U
S
A
models
except
FU
models
and
injects
compressed
air
secondary
air
coming
from
the
air
pump
into
the
exhaust
port
of
the
cylinder
head
to
reduce
hydrocarbons
He
and
carbon
monoxide
CO
in
exhaust
gas
through
recombustion
There
are
two
types
of
Air
Injection
System
Fresh
outside
air
is
drawn
by
the
air
pump
through
the
air
pump
air
cleaner
Compressed
air
is
injected
into
the
exhaust
manifold
through
the
check
valve
The
A
B
valve
supplies
air
from
the
carburetor
air
cleaner
to
the
intake
manifold
so
as
to
prevent
after
fire
during
deceleration
The
amount
of
injected
air
is
con
trolled
by
C
A
C
valve
California
models
or
air
relief
valve
Non
California
models
Page 129 of 548
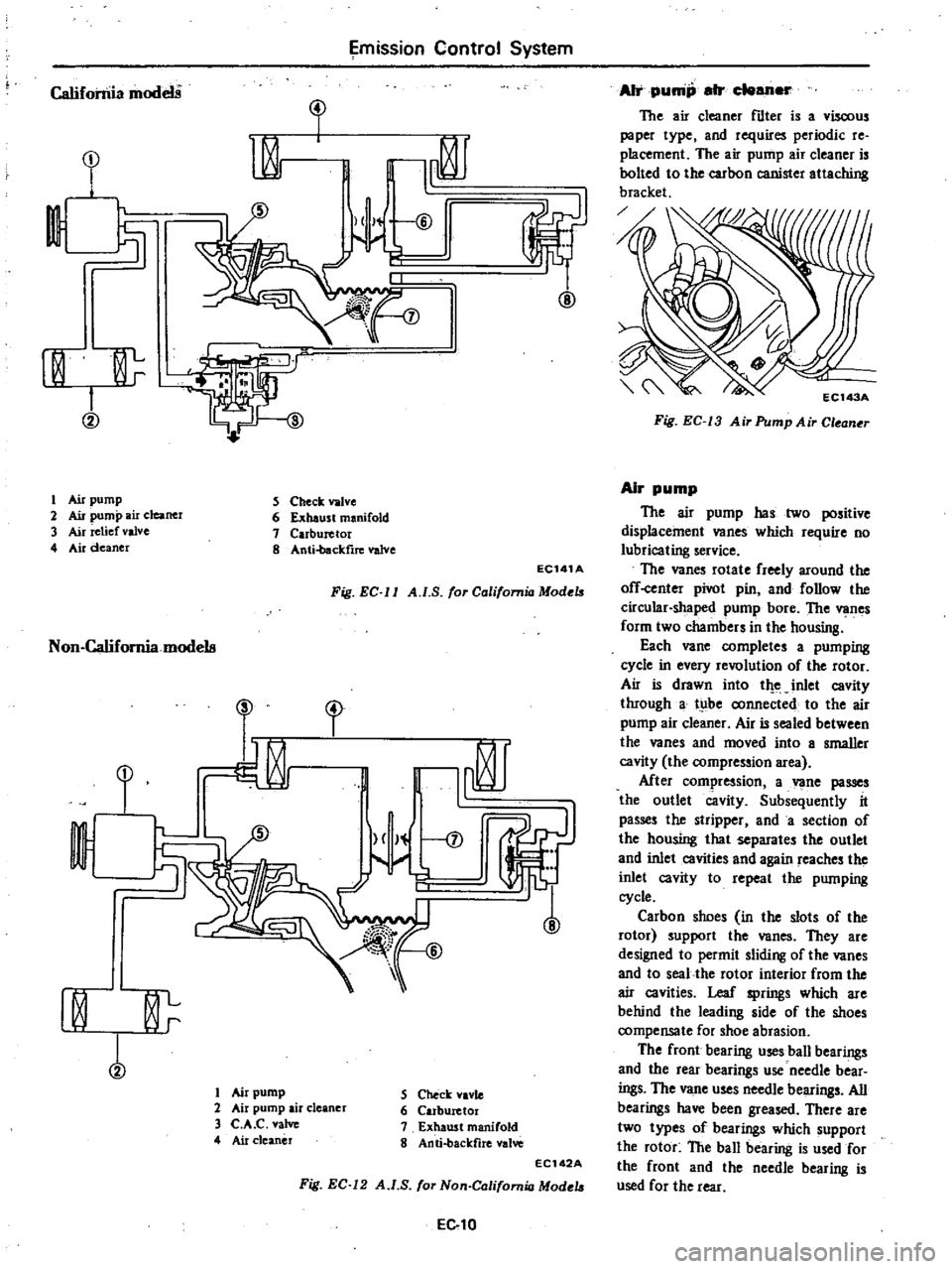
California
modelS
D
I
n
rn
lrr
I
00
1
Air
pump
2
Air
pump
air
cleaner
3
Air
relief
valve
4
Air
deaner
Non
Califomiamodels
I
I
mission
Control
System
hi
T1rID
j
I
S
Check
valve
6
Exhaust
manifold
7
Carburetor
8
Anti
backfire
valve
EC141A
Fig
EC
ll
A
l
S
for
CalifomitJ
Mod
1s
9
f
I
I
Ira
Pt
p
i
I
Air
pump
2
Air
pump
air
deaner
3
C
A
C
valve
4
Air
cleaner
SCheck
vav1e
6
Carburetor
7
Exhaust
manirold
8
Anti
backfire
valve
EC142A
Fig
EC
12
A
I
S
for
Non
CalifomitJ
Models
EC10
AJrpunip
air
cleaner
The
air
cleaner
ftlter
is
a
viscous
paper
type
and
requires
periodic
re
placement
The
air
pump
air
cleaner
i
bolted
to
the
carbon
canister
attaching
bracket
Fig
EC
13
AirPumpAirCl
an
r
Air
pump
The
air
pump
has
two
po
itive
displacement
vanes
which
require
no
lubricating
service
The
vane
rotate
freely
around
the
off
enter
pivot
pin
and
follow
the
circular
shaped
pump
bore
The
vanes
form
two
chambers
in
the
housing
Each
vane
complete
a
pumping
cycle
in
every
revolution
of
the
rotor
Air
is
drawn
into
tile
inlet
cavity
through
a
tllbe
connected
to
the
air
pump
air
cleaner
Air
is
sealed
between
the
vanes
and
moved
into
a
maller
cavity
the
compression
area
After
compression
a
yane
passes
the
outlet
cavity
Subsequently
it
passe
the
stripper
and
a
section
of
the
housing
that
parate
the
outlet
and
inlet
cavilies
and
again
reaches
the
inlet
cavity
to
repeat
the
pumping
cycle
Carbon
shoes
in
the
slots
of
the
rotor
upport
the
vanes
They
are
designed
to
permit
sliding
of
the
vanes
and
to
sealthe
rotor
interior
from
the
air
cavities
Leaf
springs
which
are
behind
the
leading
side
of
the
shoes
compensate
for
shoe
abrasion
The
front
bearing
uses
ball
bearing
and
the
rear
bearings
use
needle
bear
ings
The
vane
uses
needle
bearing
AU
bearings
have
been
greased
There
are
two
types
of
bearings
which
support
the
rotor
The
ball
bearing
is
used
for
the
front
and
the
needle
bearing
is
used
for
the
rear
Page 130 of 548
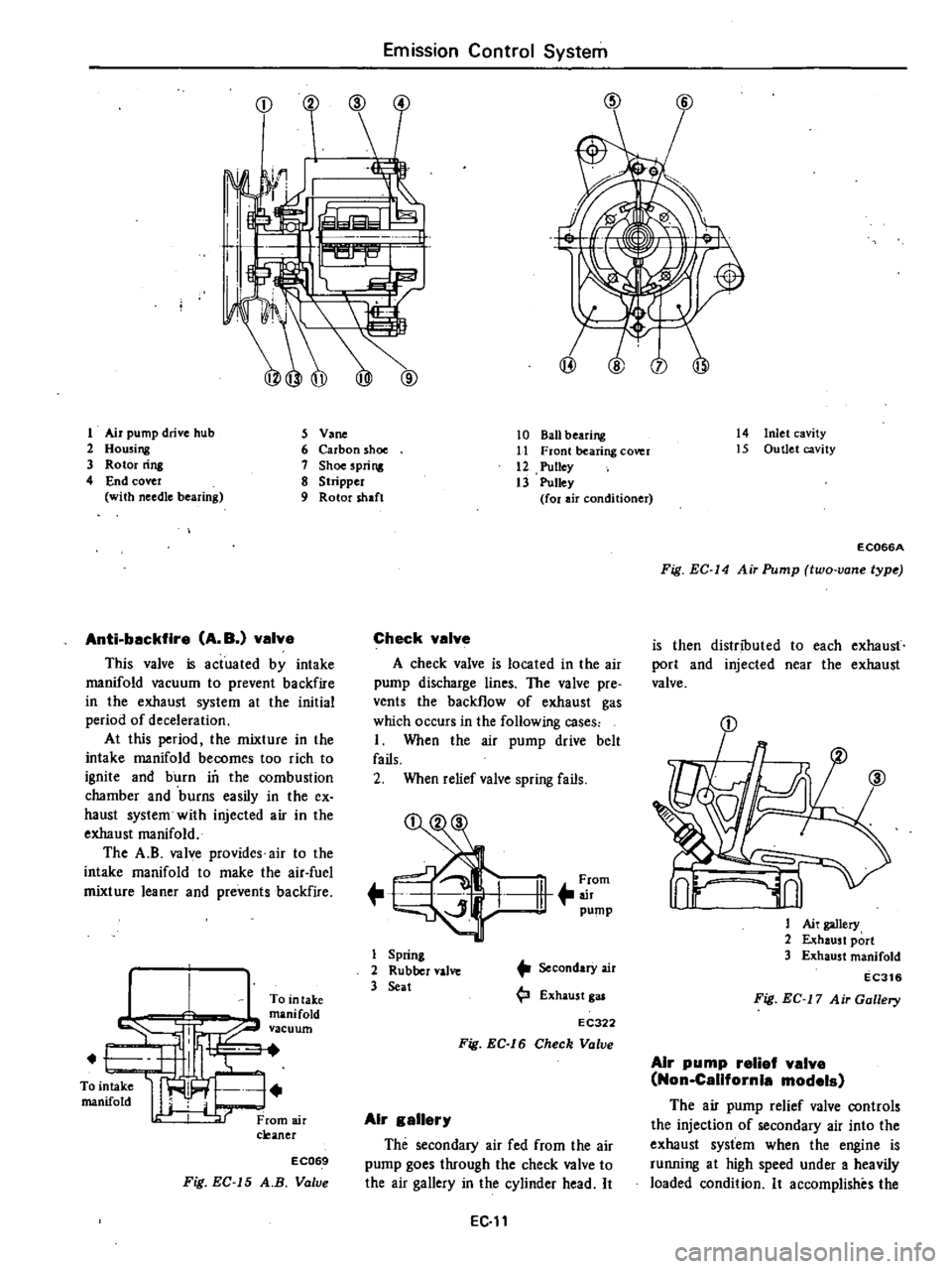
Emission
Control
System
r
@
@
CD
L
I
1
Air
pump
drive
hub
5
V
ne
2
Housing
6
Carbon
shoe
3
Rotor
rins
7
Shoe
spri
ng
4
End
cover
8
Stripper
with
needle
bearing
9
Rotor
shaft
Anti
backfire
A
B
valve
This
valve
is
actuated
by
intake
manifold
vacuum
to
prevent
backfire
in
the
exhaust
system
at
the
initial
period
of
deceleration
At
this
period
the
mixture
in
the
intake
manifold
becomes
too
rich
to
ignite
and
burn
in
the
combustion
chamber
and
burns
easily
in
the
ex
haust
system
with
injected
air
in
the
exhaust
manifold
The
A
B
valve
provides
air
to
the
intake
manifold
to
make
the
air
fuel
mixture
leaner
and
prevents
backfire
To
in
take
manifold
vacuum
EC069
Fig
EC
15
A
B
Valve
10
Ball
bearing
11
Front
bearing
cOYer
12
Pulley
13
Pulley
for
air
conditioner
Check
valve
A
check
valve
is
located
in
the
air
pump
discharge
lines
The
valve
pre
vents
the
backflow
of
exhaust
gas
which
occurs
in
the
following
cases
I
When
the
air
pump
drive
belt
fails
2
When
relief
valve
spring
fails
1
11
rom
pump
1
Spring
2
Rubber
valve
3
Seat
SecondarY
air
4
J
Exhaust
gas
EC322
Fig
EC
16
Check
Valve
Air
gallery
The
secondary
air
fed
from
the
air
pump
goes
through
the
check
valve
to
the
air
gallery
in
the
cylinder
head
It
EC
lt
14
Inlet
cavity
15
Outlet
cavity
EC066A
Fig
EC
14
Air
Pump
two
vane
lype
is
then
distributed
to
each
exhaust
port
and
injected
near
the
exhaust
valve
0
iJl
Ai
gallery
2
Exhaust
port
3
Exhaust
manifold
EC316
Fig
EC
17
Air
Gallery
Air
pump
relief
valve
Non
California
models
The
air
pump
relief
valve
controls
the
injection
of
secondary
air
into
the
exhaust
system
when
the
engine
is
running
at
high
speed
under
a
heavily
loaded
condition
It
accomplishes
the