engine DATSUN PICK-UP 1977 Service Manual
[x] Cancel search | Manufacturer: DATSUN, Model Year: 1977, Model line: PICK-UP, Model: DATSUN PICK-UP 1977Pages: 537, PDF Size: 35.48 MB
Page 219 of 537
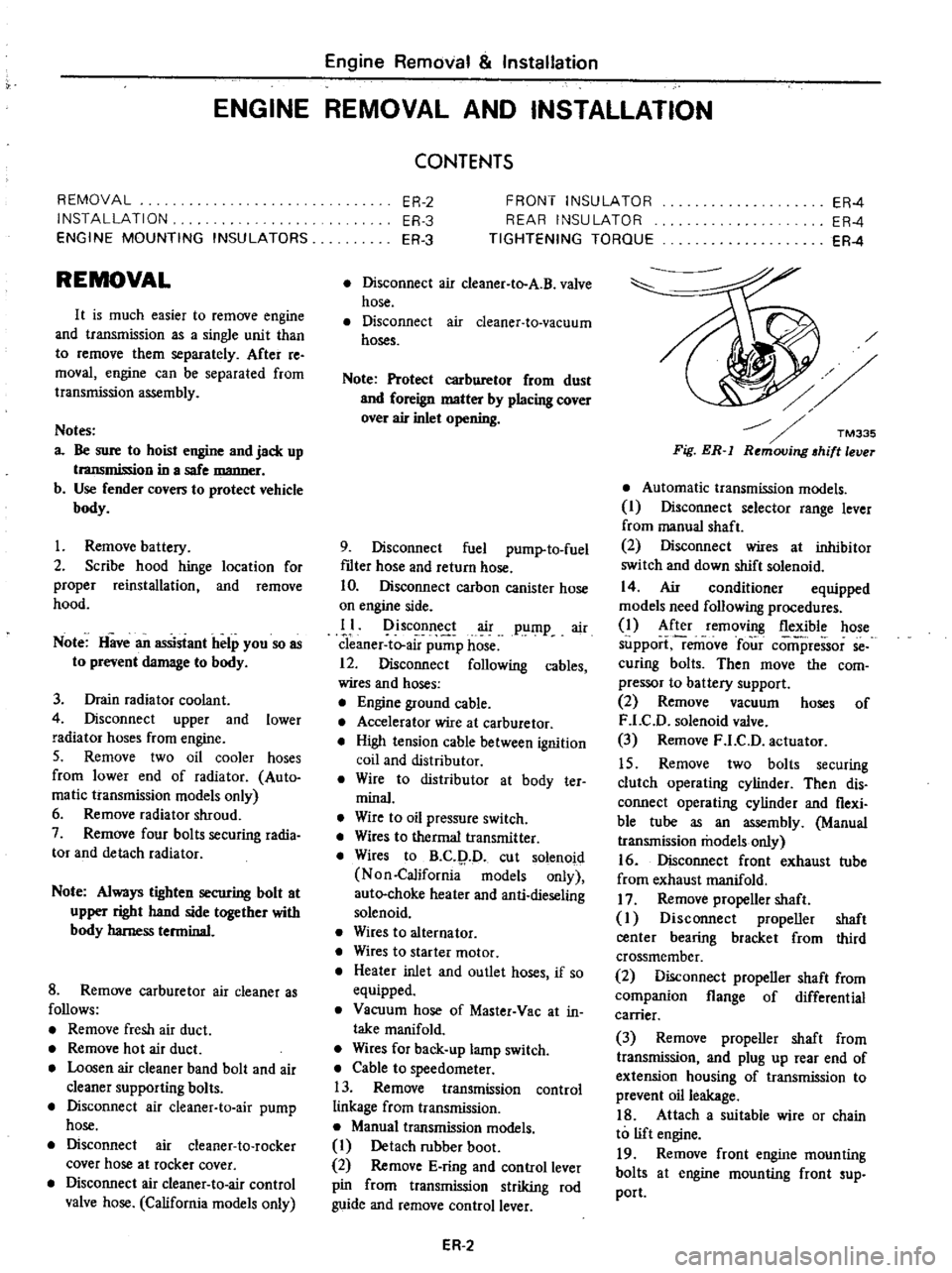
Engine
Removal
Installation
ENGINE
REMOVAL
AND
INSTAllATION
REMOVAL
INSTALLATION
ENGINE
MOUNTING
INSULATORS
REMOVAL
It
is
much
easier
to
remove
engine
and
transmission
as
a
single
unit
than
to
remove
them
separately
After
re
moval
engine
can
be
separated
from
transntission
assembly
Notes
a
Be
sure
to
hoist
engine
and
jack
up
transmission
in
a
safe
manner
b
Use
fender
cove
to
protect
vehicle
body
1
Remove
battery
2
Scribe
hood
hinge
location
for
proper
reinstallation
and
remove
hood
Note
Have
an
assistant
help
you
so
as
to
prevent
damage
to
body
3
Drain
radiator
coolant
4
Disconnect
upper
and
lower
radiator
hoses
from
engine
5
Remove
two
oil
cooler
hoses
from
lower
end
of
radiator
Auto
ma
tic
transmission
models
only
6
Remove
radiator
shroud
7
Remove
four
bolts
securing
radia
tor
and
detach
radiator
Note
Always
tighten
securing
bolt
at
upper
right
hand
side
together
with
body
harness
terminal
8
Remove
carburetor
air
cleaner
as
follows
Remove
fresh
air
duct
Remove
hot
air
duct
Loosen
air
cleaner
band
bolt
and
air
cleaner
supporting
bolts
Disconnect
air
cleaner
ta
air
pump
hose
Disconnect
air
cleaner
to
rocker
cover
hose
at
rocker
cover
Disconnect
air
cleaner
to
air
control
valve
hose
California
models
only
CONTENTS
ER
2
ER
3
ER
3
FRONT
INSULATOR
REAR
INSULATOR
TIGHTENING
TORQUE
ER
4
ER
4
ER
4
Disconnect
air
deaner
to
A
B
valve
hose
Disconnect
air
cleaner
ta
vacuum
hoses
Note
Protect
carburetor
from
dust
and
foreign
matter
by
placing
cover
over
air
inlet
opening
9
Disconnect
fuel
pump
to
fuel
fdter
hose
and
return
hose
10
Disconnect
carbon
canister
hose
on
engine
side
II
Disconnect
air
pump
air
C1eaner
to
al
p
p
hose
12
Disconnect
following
cables
wires
and
hoses
Engine
ground
cable
Accelerator
wire
at
carburetor
High
tension
cable
between
ignition
coil
and
distributor
Wire
to
distributor
at
body
ter
minal
Wire
to
oil
pressure
switch
Wires
to
thermal
transmitter
Wires
to
B
C
p
D
cut
solenoid
Non
California
models
only
auto
choke
heater
and
anti
dieseling
solenoid
Wires
to
alternator
Wires
to
starter
motor
Heater
inlet
and
outlet
hoses
if
so
equipped
Vacuum
hose
of
Master
Vac
at
in
taJce
manifold
Wires
for
back
up
lamp
switch
Cable
to
speedometer
13
Remove
transmission
control
linkage
from
transmission
Manual
transmission
models
I
Detach
rubber
boot
2
Remove
E
ring
and
control
lever
pin
from
transmission
striking
rod
guide
and
remove
control
lever
ER
2
Fig
ER
l
Automatic
transmission
models
I
Disconnect
selector
range
lever
from
manual
shaft
2
Disconnect
wires
at
inhibitor
switch
and
down
shift
solenoid
14
Air
conditioner
equipped
models
need
following
procedures
1
After
removing
flexible
hose
support
remove
four
comi
ressor
se
curing
bolts
Then
move
the
com
pressor
to
battery
support
2
Remove
vacuum
hoses
of
F
LC
D
solenoid
valve
3
Remove
F
LC
D
actuator
15
Remove
two
bolts
securing
clutch
operating
cylinder
Then
dis
connect
operating
cylinder
and
flexi
ble
tube
as
an
assembly
Manual
transmission
models
only
16
Disconnect
front
exhaust
tube
from
exhaust
manifold
17
Remove
propeller
shaft
I
Disconnect
propeller
shaft
center
bearing
bracket
from
third
crossmember
2
Disconnect
propeller
shaft
from
companion
flange
of
differential
carrier
3
Remove
propeller
shaft
from
transmission
and
plug
up
rear
end
of
extension
housing
of
transmission
to
prevent
oil
leakage
18
Attach
a
suitable
wire
or
chain
to
lift
engine
19
Remove
front
engine
mounting
bolts
at
engine
mounting
front
sup
port
Page 220 of 537
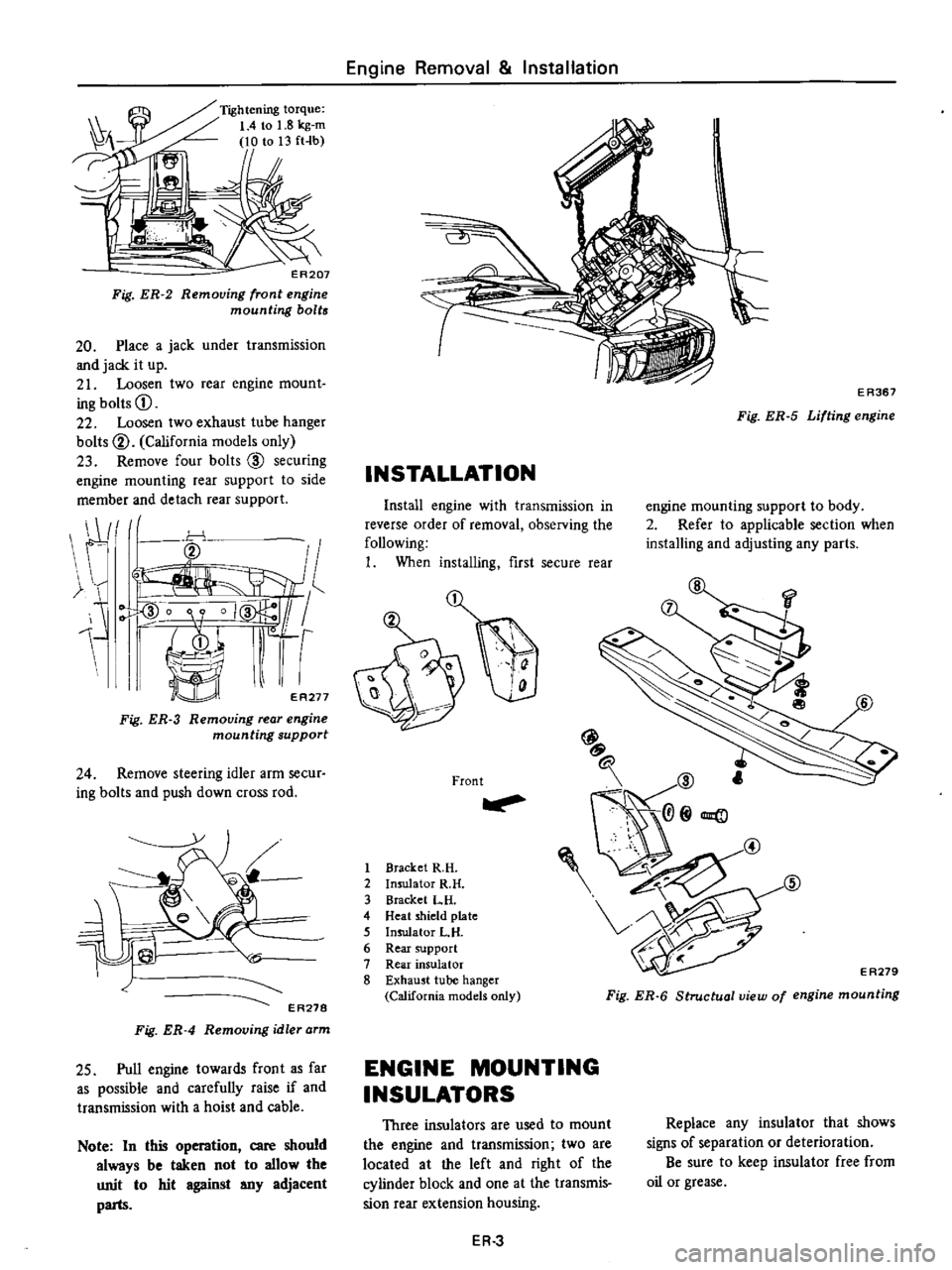
Fig
ER
2
ER207
Removing
front
engine
mounting
bolts
20
Place
a
jack
under
transmission
and
jack
it
up
21
Loosen
two
rear
engine
mount
ing
bolts
CD
22
Loosen
two
exhaust
tube
hanger
bolts
V
California
models
only
23
Remove
four
bolts
CID
securing
engine
mounting
rear
support
to
side
member
and
detach
rear
support
j
r
O
1
ER271
Fig
ER
3
Removing
rear
engine
mounting
support
24
Remove
steering
idler
arm
secur
ing
bolts
and
push
down
cross
rod
iC
EA278
Fig
ER
4
Removing
idler
arm
25
Pull
engine
towards
front
as
far
as
possible
and
carefully
raise
if
and
transmission
with
a
hoist
and
cable
Note
In
this
r
an
care
should
always
be
taken
not
to
allow
the
unit
to
hit
against
any
adjacent
parts
Engine
Removal
Installation
INSTALLATION
E
R367
Fig
ER
5
Lifting
engine
Install
engine
with
transmission
in
reverse
order
of
removal
observing
the
following
I
When
installing
first
secure
rear
2
Front
1
Bracket
R
H
2
Insulator
R
H
3
Bracket
LH
4
Heat
shield
plate
5
Insulator
L
H
6
Rear
support
7
Rear
insulator
8
Exhaust
tube
hanger
California
models
only
engine
mounting
support
to
body
2
Refer
to
applicable
section
when
installing
and
adjusting
any
parts
@
E
A279
Fig
ER
6
Structual
view
of
engine
mounting
ENGINE
MOUNTING
INSULATORS
Three
insulators
are
used
to
mount
the
engine
and
transmission
two
are
located
at
the
left
and
right
of
the
cylinder
block
and
one
at
the
transmis
sion
rear
extension
housing
Replace
any
insulator
that
shows
signs
of
separation
or
deterioration
Be
sure
to
keep
insulator
free
from
oil
or
grease
ER
3
Page 221 of 537
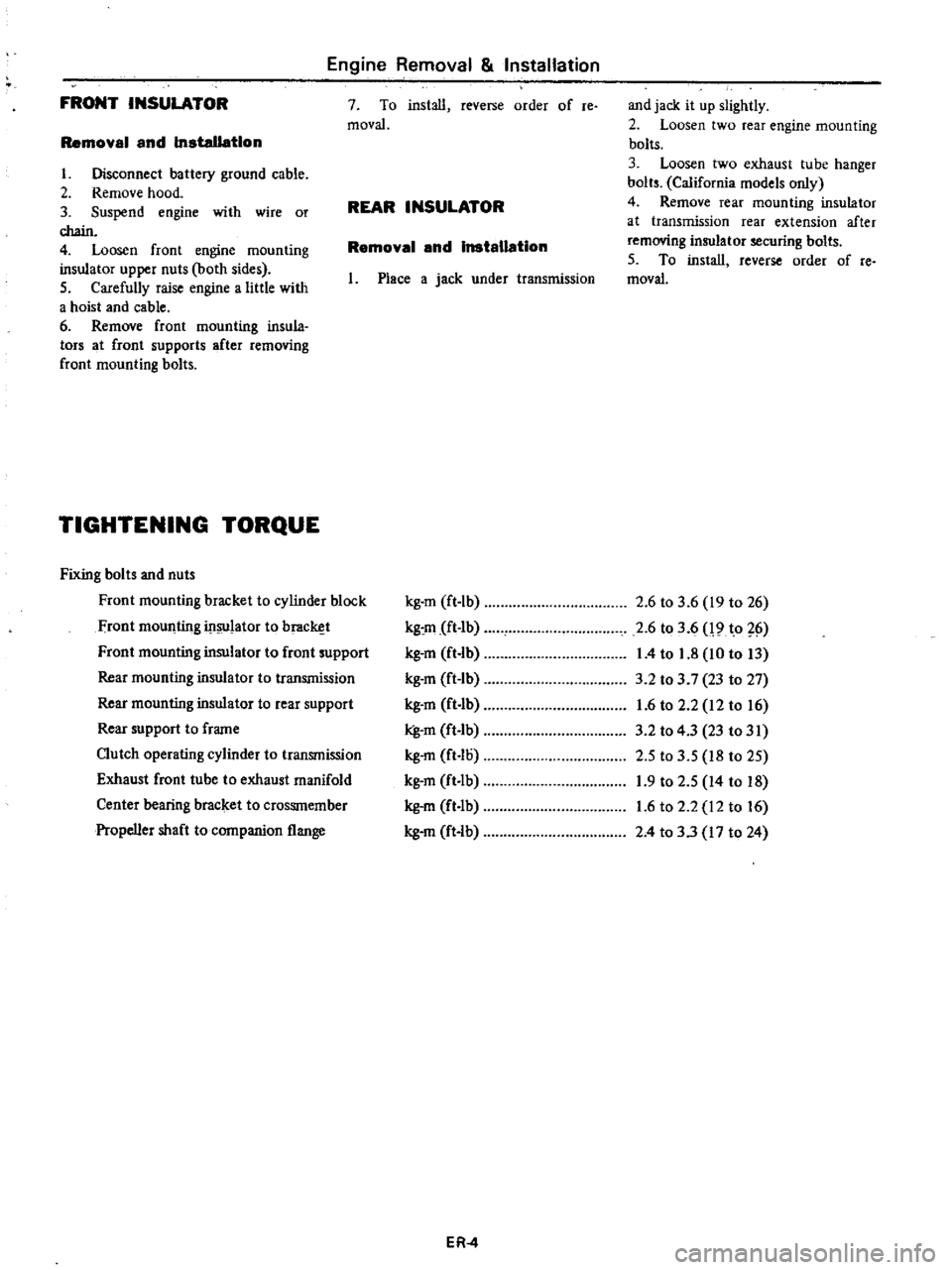
Engine
Removal
Installation
FRONT
INSULATOR
Removal
and
installation
7
To
install
reverse
order
of
re
moval
1
Disconnect
battery
ground
cable
2
Remove
hood
3
Suspend
engine
with
wire
or
chain
4
Loosen
front
engine
mounting
insulator
upper
nuts
both
sides
5
Carefully
raise
engine
a
little
with
a
hoist
and
cable
6
Remove
front
mounting
insula
tors
at
front
supports
after
removing
front
mounting
bolts
REAR
INSULATOR
Ramoval
and
Installation
1
Place
a
jack
under
transmission
TIGHTENING
TORQUE
Fixing
bolts
and
nuts
Front
mounting
bracket
to
cylinder
block
Front
mounting
in
lator
to
brac
t
Front
mounting
insulator
to
front
support
Rear
mounting
insulator
to
transmission
Rear
mounting
insulator
to
rear
support
Rear
support
to
frame
Clutch
operating
cylinder
to
transmission
Exhaust
front
tube
to
exhaust
manifold
Center
bearing
bracket
to
crossrnember
Propeller
shaft
to
companion
flange
kg
m
ft
lb
kg
m
ft
Ib
kg
m
ft
lb
kg
m
ft
lb
kg
m
ft
Ib
kg
m
ft
lb
kg
m
ft
Io
kg
m
ft
lb
kg
m
ft
lb
kg
m
ft
lb
ER
4
and
jack
it
up
slightly
2
Loosen
two
rear
engine
mounting
bolts
3
Loosen
two
exhaust
tube
hanger
bolts
California
models
only
4
Remove
rear
mounting
insulator
at
transmission
rear
extension
after
removing
insulator
securing
bolts
5
To
install
reverse
order
of
Ie
moval
2
6
to
3
6
19
to
26
2
6
to
3
6
19
t
o
76
1
4
to
1
8
10
to
13
3
2
to
3
7
23
to
27
1
6
to
2
2
12
to
16
3
2
to
4
3
23
to
31
2
5
to
3
5
18
to
25
1
9
to
2
5
14
to
18
1
6
to
2
2
12
to
16
2
4
to
3
3
17
to
24
Page 225 of 537
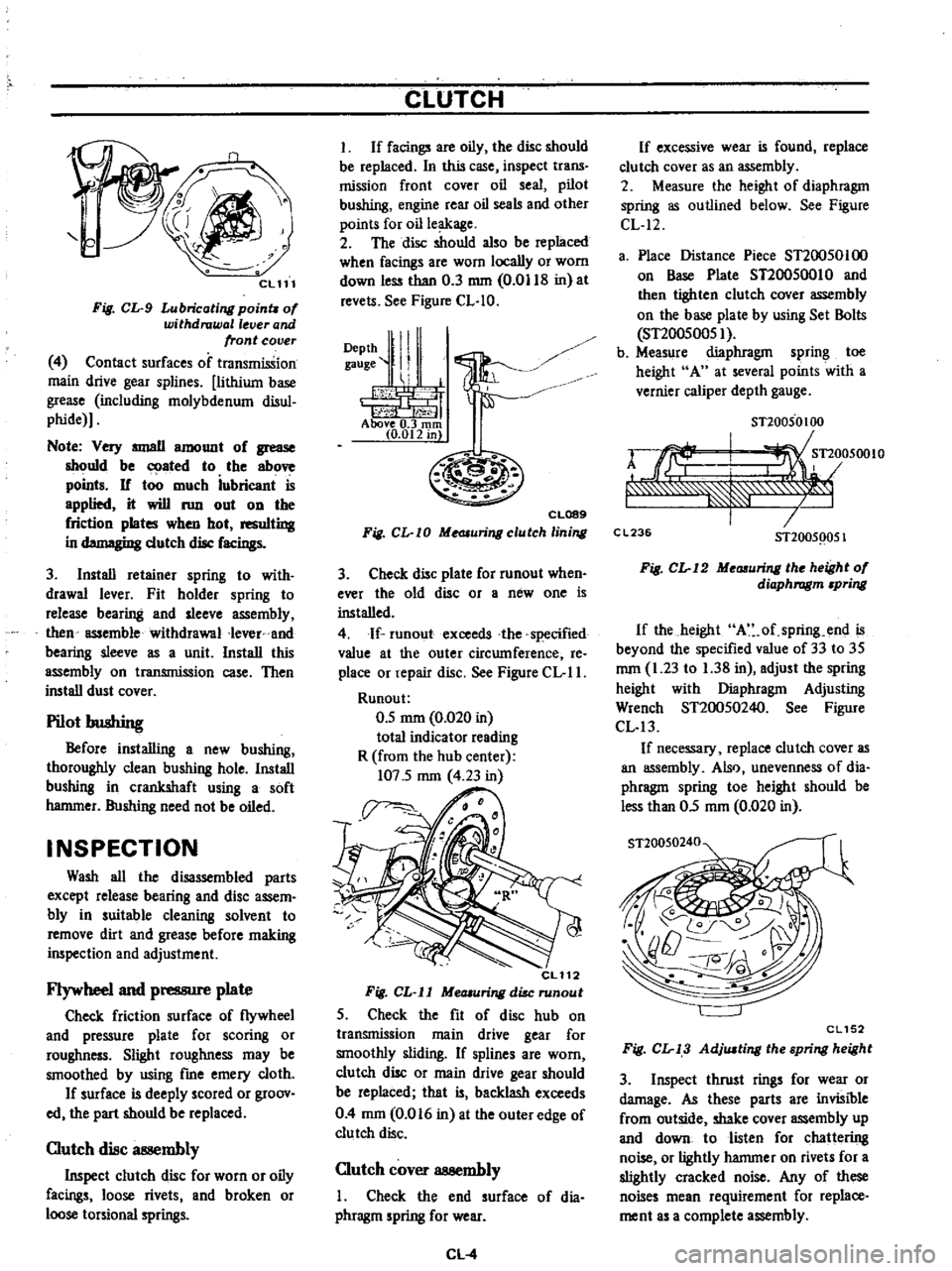
l
t
tJ
I
P
o
CUll
Fig
CL
9
Lubricating
poinu
of
withdrawal
lever
and
front
cover
4
Contact
surfaces
of
transmission
main
drive
gear
splines
lithium
base
grease
including
molybdenum
disul
phide
Note
Very
IIIIJllII
amount
of
grease
should
be
ated
to
the
above
points
If
too
much
iubricant
is
applied
it
will
run
out
on
the
friction
plates
when
hot
resulting
in
d
gi
dutch
disc
facings
3
Install
retainer
spring
to
with
drawal
lever
Fit
holder
spring
to
release
bearing
and
sleeve
assembly
then
assemble
withdrawal
Iever
and
bearing
sleeve
as
a
unit
Install
this
assembly
on
transmission
case
Then
install
dust
cover
Pilot
bushing
Before
installing
a
new
bushing
thoroughly
clean
bushing
hole
Install
bushing
in
crankshaft
using
a
soft
hammer
Bushing
need
not
be
oiled
INSPECTION
Wash
all
the
disassembled
parts
except
release
bearing
and
disc
assem
bly
in
suitable
cleaning
solvent
to
remove
dirt
and
grease
before
making
inspection
and
adjustment
Flywheel
and
pressure
plate
Check
friction
surface
of
flywheel
and
pressure
plate
for
scoring
or
roughness
Slight
roughness
may
be
smoothed
by
using
fme
emery
cloth
If
surface
is
deeply
scored
or
groov
ed
the
part
should
be
replaced
Clutch
disc
at
llembly
Inspect
clutch
disc
for
worn
or
oily
facings
loose
rivets
and
broken
or
loose
torsional
springs
CLUTCH
I
If
facings
are
oily
the
disc
should
be
replaced
In
this
case
inspect
trans
mission
front
cover
oil
seal
pilot
bushing
engine
rear
oil
seals
and
other
points
for
oil
leakage
2
The
disc
should
also
be
replaced
when
facings
are
worn
locally
or
worn
down
less
than
0
3
mm
0
0118
in
at
revels
See
Figure
CL
IO
DePth
ll
I
gauge
II
1
i
h
1
j1
t
f
Above
0
3
rom
10
012
in
CL089
Fig
CL
I0
Me
JIuringclutch
lining
3
Check
disc
plate
for
runout
when
ever
the
old
disc
or
a
new
one
is
installed
4
If
runoutexceeds
the
specified
value
at
the
outer
circumference
Ie
place
or
repair
disc
See
Figure
CL
II
Runou
t
0
5
mm
0
020
in
total
indicator
reading
R
from
the
hub
center
107
5
mm
4
23
in
CL112
Fig
CL
ll
MeOlUring
disc
runout
5
Check
the
fit
of
disc
hub
on
transmission
main
drive
gear
for
smoothly
sliding
If
splines
are
worn
clutch
disc
or
main
drive
gear
should
be
replaced
that
is
backlash
exceeds
0
4
mm
0
016
in
at
the
outer
edge
of
clutch
disc
Clutch
cover
assembly
I
Check
the
end
surface
of
dia
phragm
spring
for
wear
CL
4
If
excessive
wear
is
found
replace
clu
tch
cover
as
an
assembly
2
Measure
the
height
of
diaphragm
spring
as
outlined
below
See
Figure
CL
12
a
Place
Distance
Piece
ST20050100
on
Base
Plate
ST20050010
and
then
tighten
clutch
cover
assembly
on
the
base
plate
by
using
Set
Bolls
ST20050051
b
Measure
diaphragm
spring
toe
height
A
at
several
points
with
a
vernier
caliper
depth
gauge
STl0050100
rJrf
I
Tl
05001O
f
7
C
L23
STl005Q051
Fig
CL
12
Me
uring
the
height
of
diaphragm
pring
If
the
height
A
of
spring
end
is
beyond
the
specified
value
of
33
to
35
mm
1
23
to
1
38
in
adjust
the
spring
height
with
Diaphragm
Adjusting
Wrench
ST20050240
See
Figure
CL
13
If
necessary
replace
clutch
cover
as
an
assembly
Also
unevenness
of
dia
phragm
spring
toe
height
should
be
less
than
05
mm
0
020
in
ST20050240
CL152
Fig
CL
13
AdjlUting
the
spring
height
3
Inspect
thrust
rings
for
wear
or
damage
As
these
parts
are
invisible
from
outside
shake
cover
assembly
up
and
down
to
listen
for
chattering
noise
or
lightly
hammer
on
rivets
for
a
slightly
cracked
noise
Any
of
these
noises
mean
requirement
for
replace
ment
as
a
complete
assembly
Page 231 of 537
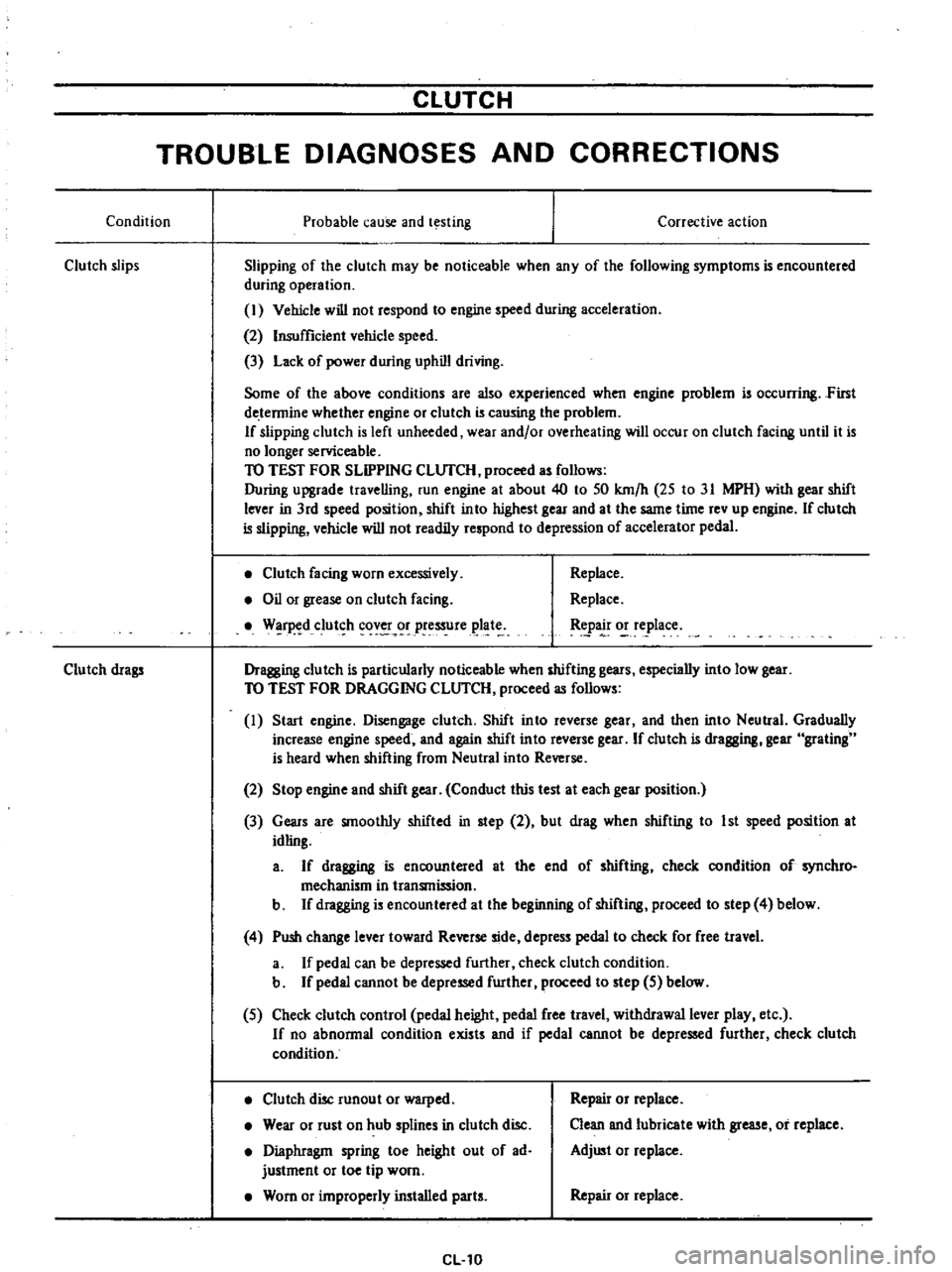
CLUTCH
TROUBLE
DIAGNOSES
AND
CORRECTIONS
Condition
Probable
cause
and
testing
Clutch
slips
Corrective
action
Slipping
of
the
clutch
may
be
noticeable
when
any
of
the
following
symptoms
is
encountered
during
operation
I
Vehicle
will
not
respond
to
engine
speed
during
acceleration
2
Insufficient
vehicle
speed
3
Lack
of
power
during
uphill
driving
Some
of
the
above
conditions
are
also
experienced
when
engine
problem
is
oc
urring
First
de
tennine
whether
engine
or
clutch
is
causing
the
problem
If
slipping
clutch
is
left
unheeded
wear
and
or
overheating
will
occur
on
clutch
facing
until
it
is
no
longer
serviceable
TO
TEST
FOR
SLIPPING
CLlJfCH
proceed
as
follows
During
upgrade
travelling
run
engine
at
about
40
to
50
km
h
25
to
31
MPH
with
gear
shift
lever
in
3rd
speed
position
shift
into
highest
gear
and
at
the
same
time
rev
up
engine
If
clutch
is
slipping
vehicle
will
not
readily
respond
to
depression
of
accelerator
pedal
Clutch
facing
worn
excessively
Oil
or
grease
on
clutch
facing
W
r
d
clut
h
cov
r
pressure
plat
Replace
Replace
tpa
o
e
lace
Dragging
clutch
is
particularly
noticeable
when
shifting
gears
especially
into
low
gear
TO
TEST
FOR
DRAGGING
CLlJfCH
proceed
as
follows
I
Start
engine
Disengage
clutch
Shift
into
reverse
gear
and
then
into
Neutral
Gradually
increase
engine
speed
and
again
shift
into
reverse
gear
If
clutch
is
dragging
gear
grating
is
heard
when
shifting
from
Neutral
into
Reverse
Clutch
drags
2
Stop
engine
and
shift
gear
Conduct
this
test
at
each
gear
position
3
Gears
are
smoothly
shifted
in
step
2
but
drag
when
shifting
to
1st
speed
position
at
idling
a
If
dragging
is
encountered
at
the
end
of
shifting
check
condition
of
synchro
mechanism
in
transmission
b
If
dragging
is
encountered
at
the
beginning
of
shifting
proceed
to
step
4
below
4
Push
change
lever
toward
Reverse
side
depress
pedal
to
check
for
free
travel
a
If
pedal
can
be
depressed
further
check
clutch
condition
b
If
pedal
cannot
be
depressed
further
proceed
to
step
5
below
5
Check
clutch
control
pedal
height
pedal
free
travel
withdrawal
lever
play
etc
If
no
abnonnal
condition
exists
and
if
pedal
cannot
be
depressed
further
check
clutch
condition
Clutch
disc
runout
or
warped
Wear
or
rust
on
hub
splines
in
clutch
disc
Diaphragm
spring
toe
height
out
of
ad
justment
or
toe
tip
worn
Worn
or
improperly
installed
parts
CL10
Repair
or
replace
Clean
and
lubricate
with
grease
or
replace
Adjust
or
replace
Repair
or
replace
Page 232 of 537
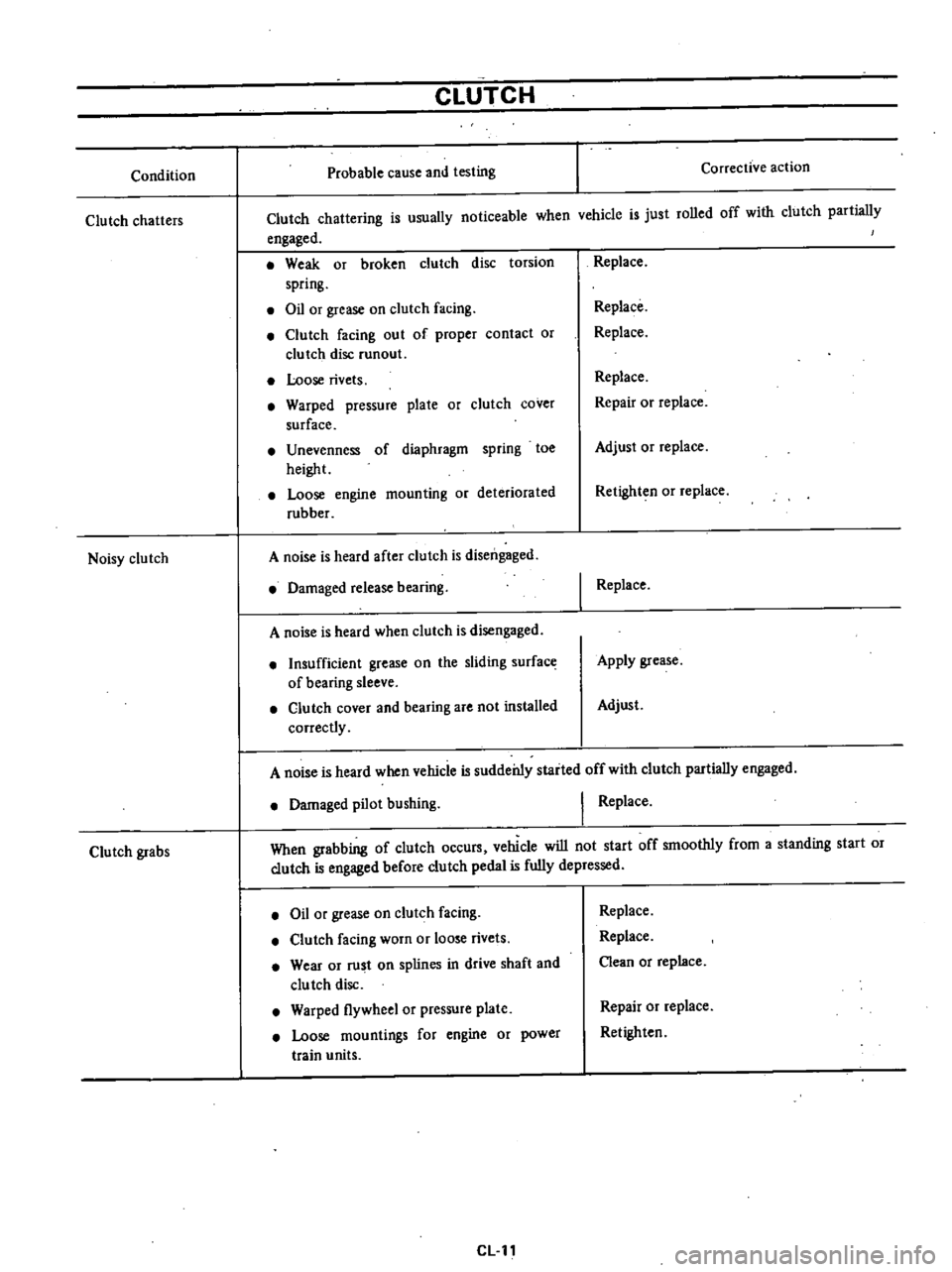
Condition
Clutch
chatters
Noisy
clutch
Clutch
grabs
CLUTCH
Probable
cause
and
testing
Corrective
action
Clutch
chattering
is
usually
noticeable
when
vchicle
is
just
rolled
off
with
clutch
partially
engaged
Weak
or
broken
clutch
disc
torsion
spring
Oil
or
grease
on
clutch
facing
Clutch
facing
out
of
proper
contact
or
clutch
disc
runout
Loose
rivets
Warped
pressure
plate
or
clutch
cover
surface
Unevenness
of
diaphragm
spring
toe
height
Loose
engine
mounting
or
deteriorated
rubber
A
noise
is
heard
after
clutch
is
disengaged
Damaged
release
bearing
A
noise
is
heard
when
clutch
is
disengaged
Insufficient
grease
on
the
sliding
surface
of
bearing
sleeve
Clutch
cover
and
bearing
are
not
installed
correctly
Replace
Replace
Replace
Replace
Repair
or
replace
Adjust
or
replace
Retighten
or
replace
I
Replace
Apply
grease
Adjust
A
noise
is
heard
when
vehicle
is
suddei11y
staited
off
with
clutch
partially
engaged
Damaged
pilot
bushing
I
Replace
When
grabbing
of
clutch
occurs
vehicle
will
not
start
off
smoothly
from
a
standing
start
or
clutch
is
engaged
before
clutch
pedal
is
fully
depressed
Oil
or
grease
on
clutch
facing
Clutch
facing
worn
or
loose
rivets
Wear
or
rust
on
splines
in
drive
shaft
and
clu
tch
disc
Warped
flywheel
or
pressure
plate
Loose
mountings
for
engine
or
power
train
units
CLll
Replace
Replace
Clean
or
replace
Repair
or
replace
Retighten
Page 238 of 537
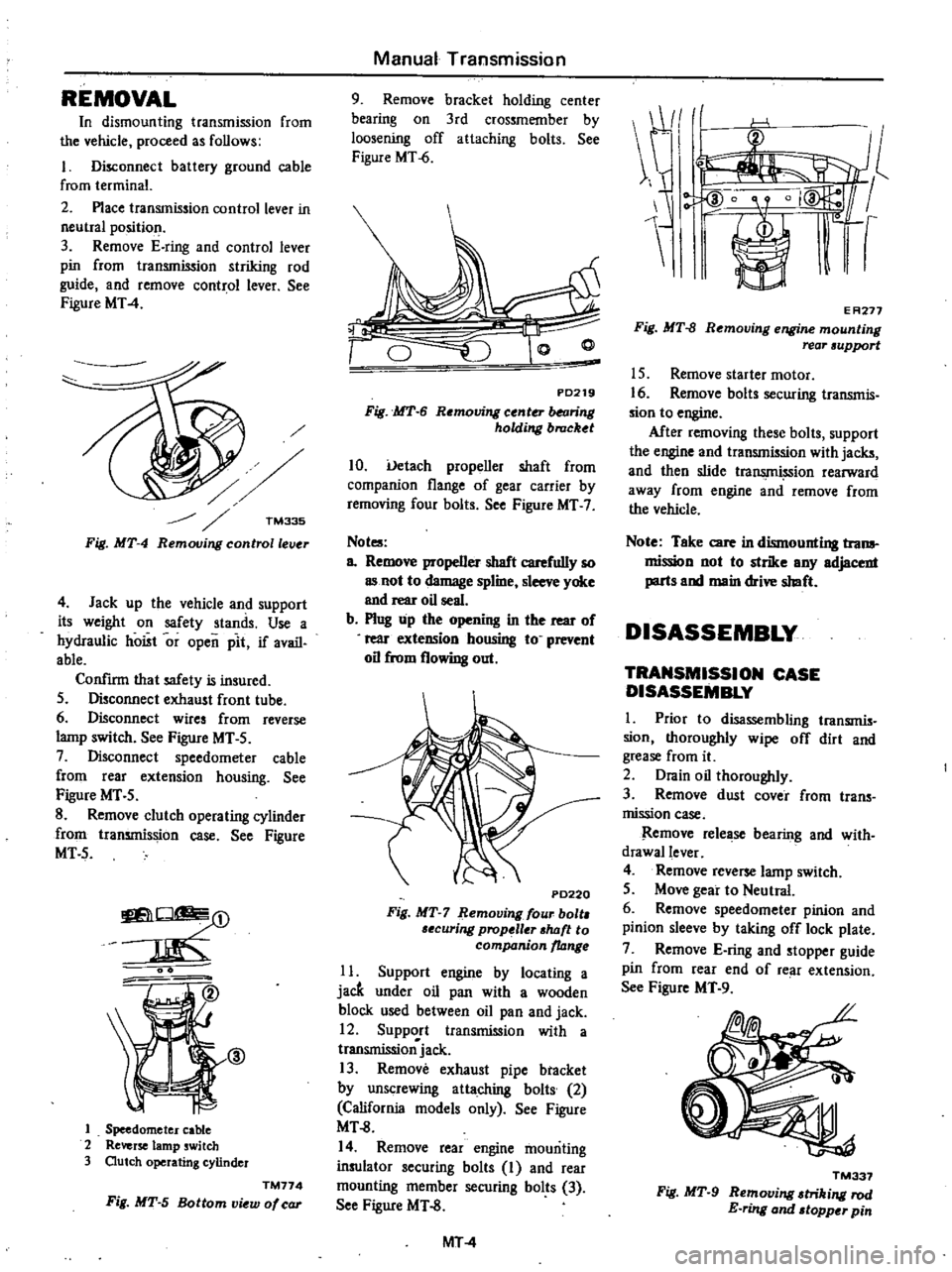
REMOVAL
In
dismounting
transmission
from
the
vehicle
proceed
as
follows
I
Disconnect
battery
ground
cable
from
terminal
2
Place
transmission
control
lever
in
neutIal
position
3
Remove
E
ring
and
control
lever
pin
from
transmission
striking
rod
guide
and
remove
control
lever
See
Figure
MT
4
TM335
Fig
MT
4
Remouing
controllelJ
r
4
Jack
up
the
vehicle
and
support
its
weight
on
safety
stands
Use
a
hydraulic
hoist
or
open
pit
if
avail
able
Confirm
that
safety
is
insured
5
Disconnect
exhaust
front
tube
6
Disconnect
wires
from
reverse
lamp
switch
See
Figure
MT
5
7
Disconnect
speedometer
cable
from
rear
extension
housing
See
Figure
MT
5
8
Remove
clutch
operating
cylinder
from
transmission
case
See
Figure
MT5
O
m
J
@
1
Speedometer
cable
2
Reverse
lamp
switch
3
Outch
operating
cylinder
TM774
Fig
MT
5
Bottom
view
of
car
Manual
Transmission
9
Remove
bracket
holding
center
bearing
on
3rd
crossmember
by
loosening
off
attaching
bolts
See
Figure
MT
6
PD219
Fig
MT
6
Removing
center
balring
holding
brucket
10
Uetach
propeller
shaft
from
companion
flange
of
gear
carrier
by
removing
four
bolts
See
Figure
MT
7
Not
a
Remove
propeller
shaft
carefully
so
as
not
to
damage
spline
sleeve
yoke
and
rear
oil
seal
b
Plug
up
the
opening
in
the
rear
of
rear
exteDSion
housing
to
prevent
oil
from
flowing
out
P0220
Fig
MT
7
Remouing
four
bolt
6ecuring
prop
ller
shtJft
to
companion
ltJnge
11
Support
engine
by
locating
a
jacft
under
oil
pan
with
a
wooden
block
used
between
oil
pan
and
jack
12
Support
transmission
with
a
transmissionjack
13
Remove
exhaust
pipe
btacket
by
unscrewing
attaching
bolts
2
California
models
only
See
Figure
MT
8
14
Remove
rear
engine
mounting
insulator
securing
bolts
I
and
rear
mounting
member
securing
bolts
3
See
Figure
MT
8
MT
4
E
A277
Fig
MT
8
Removing
engine
mounting
rear
support
15
Remove
starter
motor
16
Remove
bolt
securing
transmis
sion
to
engine
After
removing
these
bolts
support
the
engine
and
transmission
with
jacks
and
then
slide
tra
ion
rearward
away
from
engine
and
remove
from
the
vehicle
Note
Take
care
in
dismounting
trona
mission
not
to
strike
any
adjacent
parts
and
main
drive
shaft
DISASSEMBLY
TRANSMISSION
CASE
DISASSEMBLY
I
Prior
to
disassembling
transmis
sion
thoroughly
wipe
off
dirt
and
grease
from
it
2
Drain
oil
thoroughly
3
Remove
dust
cover
from
trans
mission
case
Remove
release
bearing
and
with
drawallever
4
Remove
reverse
lamp
switch
5
Move
gear
to
Neutral
6
Remove
speedometer
pinion
and
pinion
sleeve
by
taking
off
lock
plate
7
Remove
E
ring
and
stopper
guide
pin
from
rear
end
of
re
ll
extension
See
Figure
MT
9
TM337
Fig
MT
9
Removing
triking
rod
E
ring
and
topper
pin
Page 242 of 537
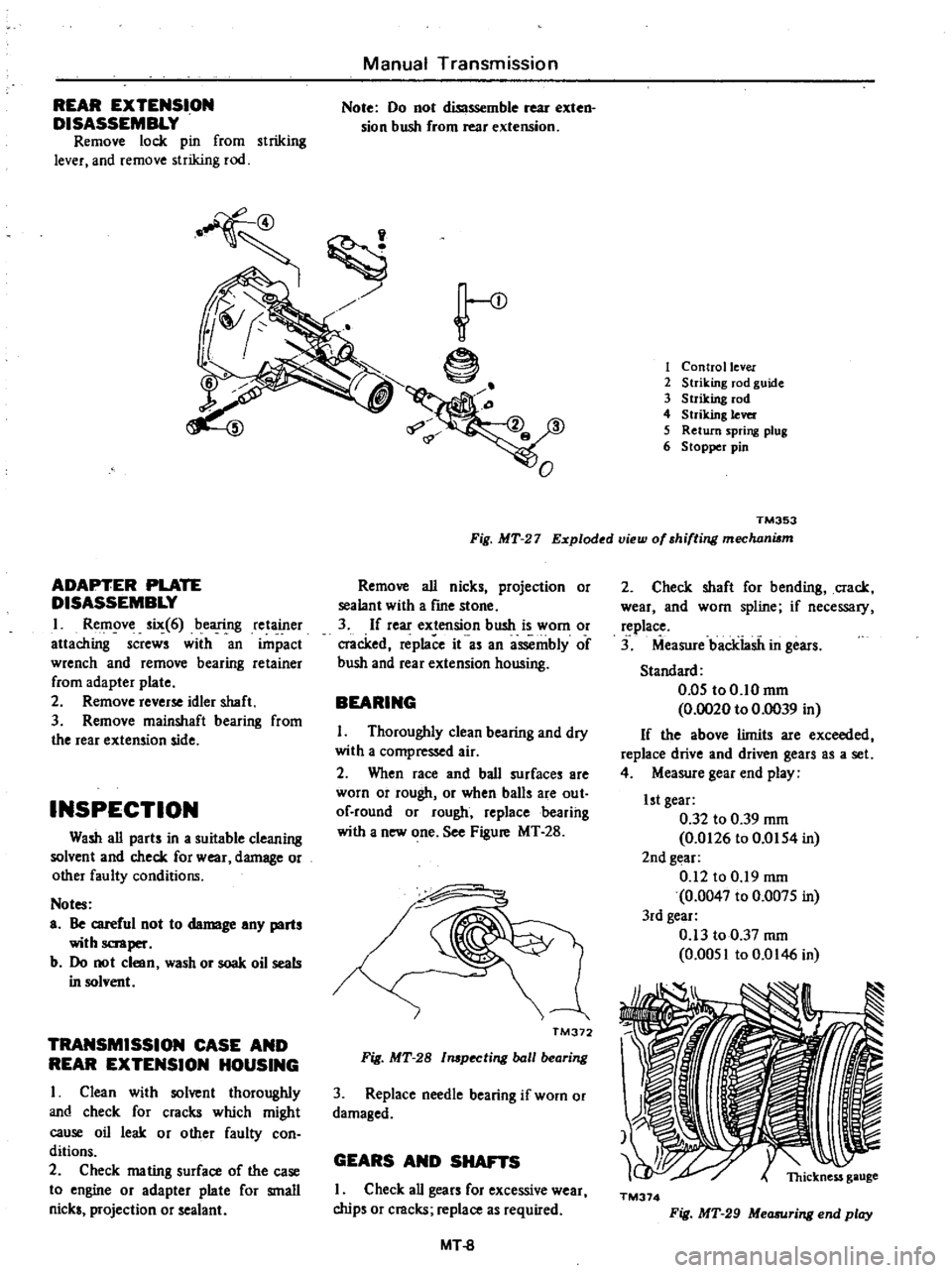
REAR
EXTENSION
DISASSEMBLY
Remove
lock
pin
from
striking
lever
and
remove
striking
rod
Manual
Transmission
Note
00
not
diSlssemble
rear
exten
sion
bush
from
rear
extension
ADAPTER
PLATE
DISASSEMBLY
I
Remove
six
6
bearing
retainer
attaching
screws
with
an
impact
wrench
and
remove
bearing
retainer
from
adapter
plate
2
Remove
reverse
idler
shaft
3
Remove
mainshaft
bearing
from
the
rear
extension
side
INSPECTION
Wash
all
parts
in
a
suitable
cleaning
solvent
and
check
for
wear
damage
or
other
faulty
conditions
Notes
a
Be
careful
not
to
damage
any
parts
with
scraper
b
00
not
clean
wash
or
soak
oil
seals
in
solvent
TRANSMISSION
CASE
AND
REAR
EXTENSION
HOUSING
I
Clean
with
solvent
thoroughly
and
check
for
cracks
which
might
cause
oil
leak
or
other
faulty
con
ditions
2
Check
mating
surface
of
the
case
to
engine
or
adapter
plate
for
small
nicks
projection
or
sealant
e
1
Control
lever
2
Striking
rod
guide
3
Striking
rod
4
Striking
lever
5
Return
spring
plug
6
Stopper
pin
TM353
Fig
MT
27
Exploded
view
of
shifting
mechani6m
Remove
all
nicks
projection
or
sealant
with
a
frne
stone
3
If
rear
extension
bush
is
worn
or
cracked
replace
it
as
an
assembly
of
bush
and
rear
extension
housing
BEARING
I
Thoroughly
clean
bearing
and
dry
with
a
compressed
air
2
When
race
and
ball
surfaces
are
worn
or
rough
or
when
balls
are
out
of
round
or
rough
replacebearihg
with
a
new
one
See
Figure
MT
28
I
TM372
Fig
MT
28
l
pecting
ball
bearing
3
Replace
needle
bearing
if
worn
or
damaged
GEARS
AND
SHAFTS
I
Check
all
gears
for
excessive
wear
chips
or
cracks
replace
as
required
MT
8
2
Check
shaft
for
bending
crack
wear
and
worn
spline
if
necessary
replace
3
Measure
backiasii
in
gears
Standard
0
05
to0
10mm
0
0020
to
0
0039
in
If
the
above
limits
are
exceeded
replace
drive
and
driven
gears
as
a
set
4
Measure
gear
end
play
1st
gear
0
32
to
0
39
mm
0
0126
to
0
0154
in
2nd
gear
0
12
to
0
19
mm
0
0047
to
0
0075
in
3rd
gear
0
13
to
0
37
mm
0
0051
to
0
0146
in
TM374
Fig
MT
29
Measuring
end
play
Page 248 of 537
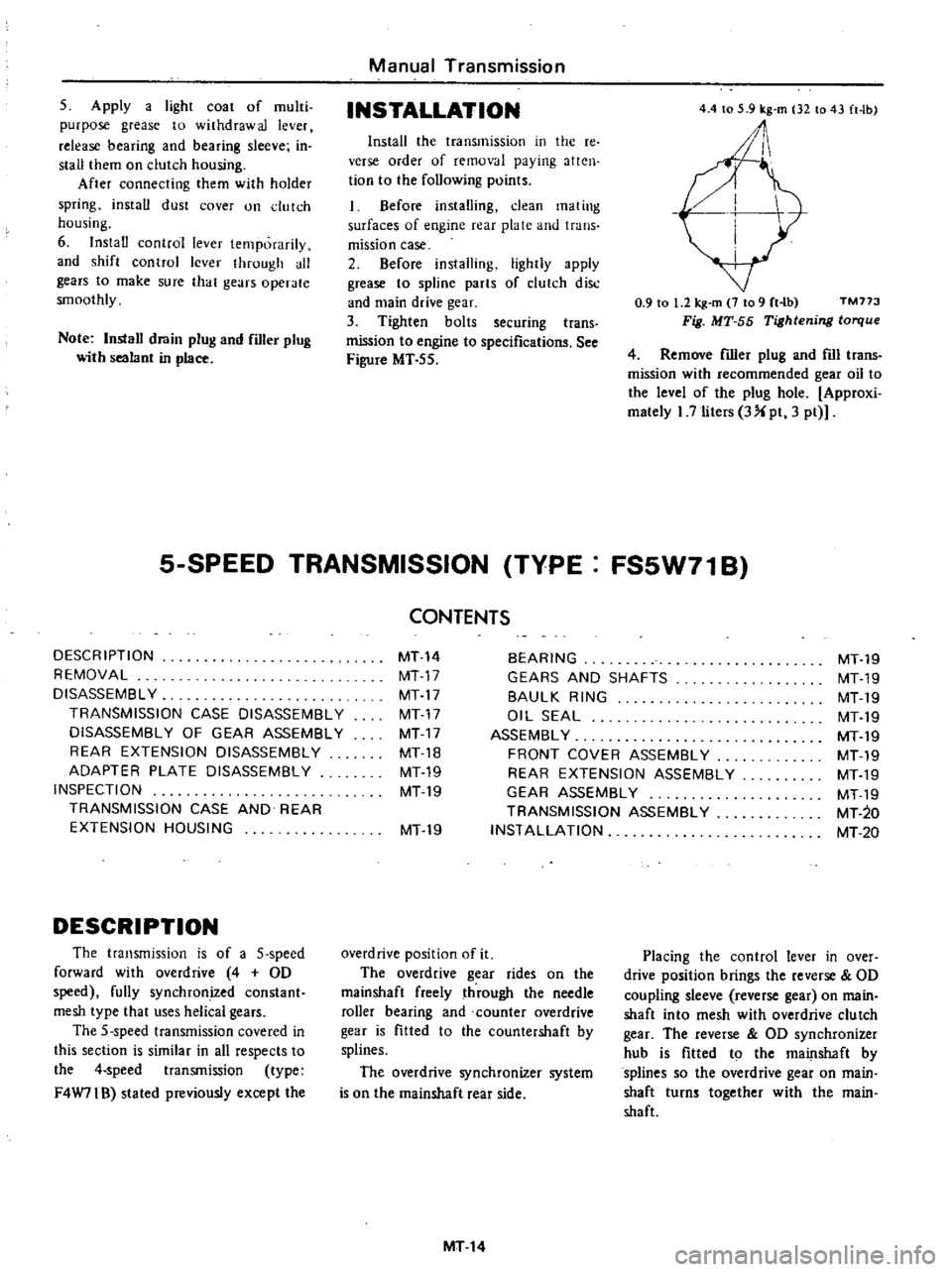
5
Apply
a
light
coat
of
multi
purpose
grease
to
withdrawal
lever
release
bearing
and
bearing
sleeve
in
stall
them
on
clutch
housing
After
connecting
them
with
holder
spring
instaU
dust
cover
on
clutch
housing
6
Install
control
lever
temporarily
and
shift
control
lever
through
all
gears
to
make
sure
that
gears
opera
Ie
smoothly
Note
Install
drain
plug
and
filler
plug
ith
sealant
in
place
Manual
Transmission
INSTALLATION
Install
the
transmission
in
the
reo
verse
order
uf
removal
paying
atten
tion
to
the
following
points
1
Before
installing
dean
mating
surfaces
of
engine
rear
plate
and
trans
mission
case
2
Before
installing
lightly
apply
grease
to
spline
parts
of
clutch
disc
and
main
drive
gear
3
Tighten
bolts
securing
trans
mission
to
engine
to
specifications
See
Figure
MT
55
5
SPEED
TRANSMISSION
TYPE
DESCRIPTION
REMOVAL
DISASSEMBL
Y
TRANSMISSION
CASE
DISASSEMBLY
DISASSEMBL
Y
OF
GEAR
ASSEMBLY
REAR
EXTENSION
DISASSEMBLY
ADAPTER
PLATE
DISASSEMBLY
INSPECTION
TRANSMISSION
CASE
AND
REAR
EXTENSION
HOUSING
DESCRIPTION
The
transmission
is
of
a
5
speed
forward
with
overdrive
4
OD
speed
fully
synchronized
constant
mesh
type
that
uses
helical
gears
The
5
speed
transmission
covered
in
this
section
is
similar
in
all
respects
to
the
4
speed
transmission
type
F4W71B
stated
previously
except
the
CONTENTS
MT14
MT17
MT17
MT17
MT17
MT18
MT19
MT19
4
4
to
5
9
kg
m
32
to
43
ft
Ib
1
0
9
to
1
2
kg
m
7
to
9
rt
lb
TM773
Fig
MT
55
Tightening
torque
4
Remove
filler
plug
and
fIll
trans
mission
with
recommended
gear
oil
to
the
level
of
the
plug
hole
Approxi
mately
I
7
liters
3
pt
3
pt
FS5W71B
BEARING
GEARS
AND
SHAFTS
BAULK
RING
OIL
SEAL
ASSEMBL
Y
FRONT
COVER
ASSEMBLY
REAR
EXTENSION
ASSEMBLY
GEAR
ASSEMBLY
TRANSMISSION
ASSEMBLY
INSTALLATION
MT19
overdrive
position
of
it
The
overdrive
gear
rides
on
the
mainshaft
freely
through
the
needle
roller
bearing
and
counter
overdrive
gear
is
fitted
to
the
countershaft
by
splines
The
overdrive
synchronizer
system
is
on
the
mainshaft
rear
side
MT14
MT19
MT19
MT19
MT19
MT19
MT19
MT19
MT19
MT
20
MT20
Placing
the
control
lever
in
over
drive
position
brings
the
reverse
OD
coupling
sleeve
reverse
gear
on
main
shaft
into
mesh
with
overdrive
clutch
gear
The
reverse
OD
synchronizer
hub
is
fItted
to
the
mainshaft
by
splines
so
the
overdrive
gear
on
main
shaft
turns
together
with
the
main
shaft
Page 256 of 537
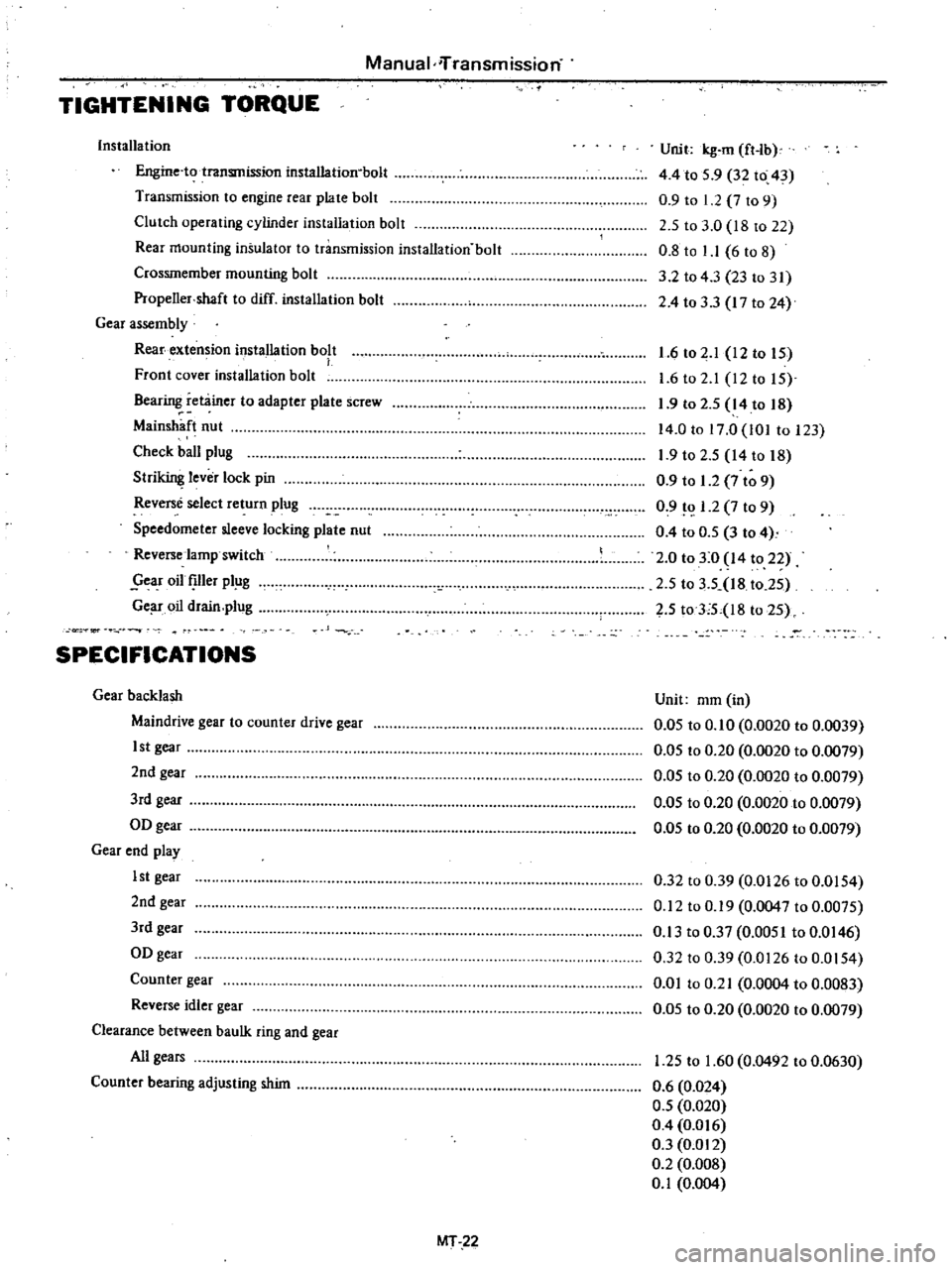
Manual
iTransmission
TIGHTENING
TORQUE
Installa
tion
Engine
to
transmission
installation
bolt
Transmission
to
engine
rear
plate
bolt
Clutch
operating
cylinder
installation
bolt
Rear
mounting
insulator
to
transmission
installation
bolt
Crossmember
mounting
bolt
Propeller
shaft
to
diff
installation
bolt
Gear
assembly
Rear
extension
installation
bolt
Front
cover
installation
bolt
Bearing
retainer
to
adapter
plate
screw
Main
haft
nut
Check
ball
plug
Stri
lever
lock
pin
Reverse
select
return
plug
Speedometer
sleeve
locking
plate
nut
Reverse
lamp
switch
year
oil
Ier
pl
g
Ge
r
oil
drain
plug
Unit
kg
m
ft
lb
4
4
to
5
9
32
to
43
0
9
to
1
2
7
to
9
2
5
to
3
0
18
to
22
0
8
to
1
1
6
to
8
3
2
to
43
23
to
31
2
4
to
33
17
to
24
1
6
to
2
1
12
to
IS
1
6
to
2
1
12to
IS
1
9
to
2
S
14
to
18
14
0
to
17
0
101
to
123
1
9
to
2
S
14
to
18
0
9
to
1
2
7
to
9
0
9
1
2
7
to
9
0
4
to
O
S
3
to
4
2
0
to
3
0
14
to
22
2
S
to
3
5
18
t02S
2
S
toTS
l8
to
2S
or
SPECIFICATIONS
Gear
backlash
Maindrive
gear
to
counter
drive
gear
1st
gear
2nd
gear
3rd
gear
OD
gear
Gear
end
play
1st
gear
2nd
gear
3rd
gear
OD
gear
Counter
gear
Reverse
idler
gear
Clearance
between
baulk
ring
and
gear
All
gears
Counter
bearing
adjusting
shim
Unit
mm
in
0
05
to
0
10
0
0020
to
0
0039
0
05
to
0
20
0
0020
to
0
0079
O
OS
to
0
20
0
0020
to
0
0079
0
05
to
0
20
0
0020
to
0
0079
0
05
to
0
20
0
0020
to
0
0079
0
32
to
0
39
0
0126
to
0
0154
0
12
to
0
19
0
0047
to
0
0075
0
13
to
0
37
0
0051
to
0
0146
0
32
to
0
39
0
0126
to
0
0154
0
01
to
0
21
0
0004
to
0
0083
0
05
to
0
20
0
0020
to
0
0079
1
25
to
1
60
0
0492
to
0
0630
0
6
0
024
0
5
0
020
0
4
0
016
0
3
0
012
0
2
0
008
0
1
0
004
MT
22