torque DATSUN PICK-UP 1977 Owner's Guide
[x] Cancel search | Manufacturer: DATSUN, Model Year: 1977, Model line: PICK-UP, Model: DATSUN PICK-UP 1977Pages: 537, PDF Size: 35.48 MB
Page 221 of 537
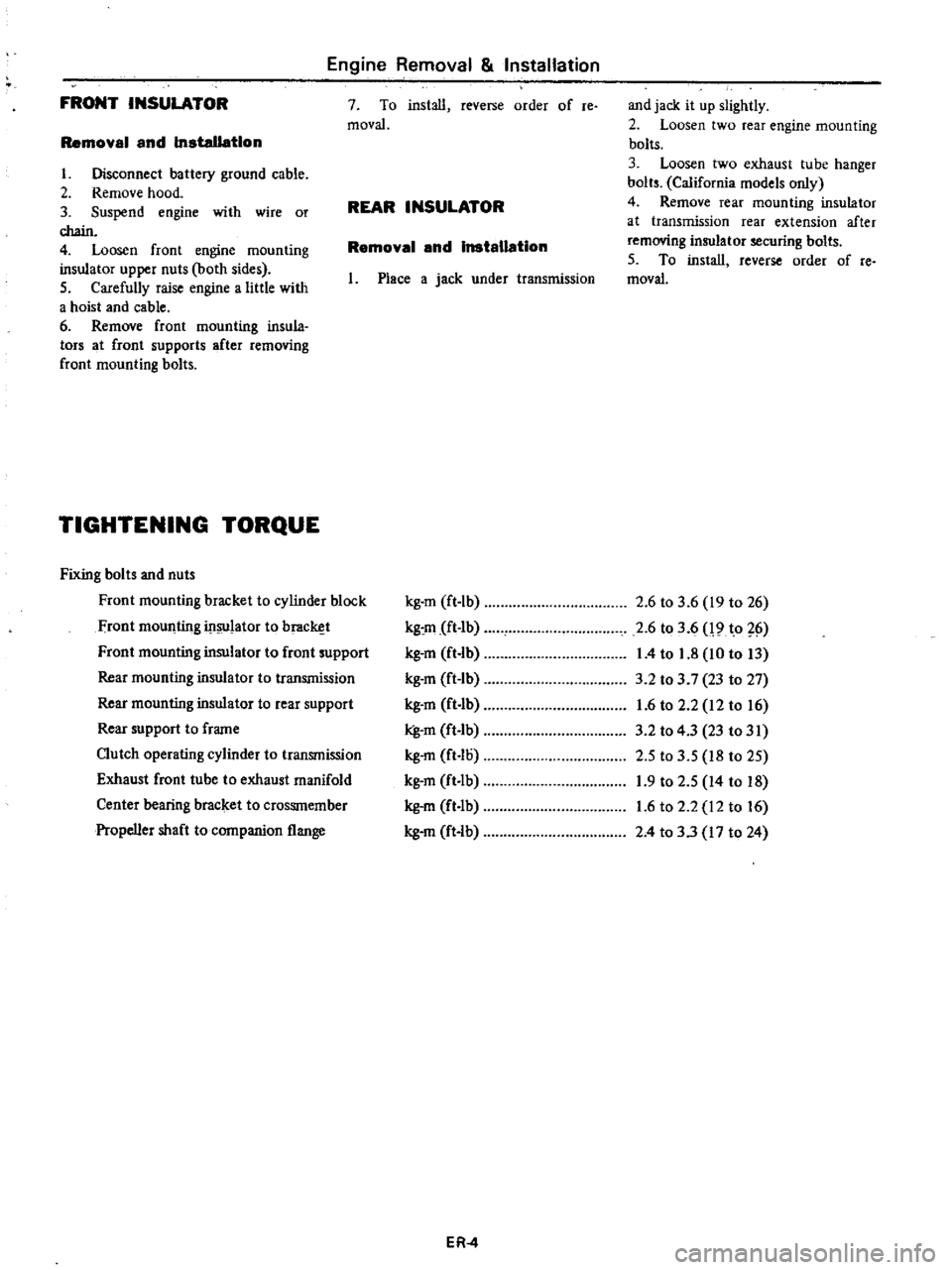
Engine
Removal
Installation
FRONT
INSULATOR
Removal
and
installation
7
To
install
reverse
order
of
re
moval
1
Disconnect
battery
ground
cable
2
Remove
hood
3
Suspend
engine
with
wire
or
chain
4
Loosen
front
engine
mounting
insulator
upper
nuts
both
sides
5
Carefully
raise
engine
a
little
with
a
hoist
and
cable
6
Remove
front
mounting
insula
tors
at
front
supports
after
removing
front
mounting
bolts
REAR
INSULATOR
Ramoval
and
Installation
1
Place
a
jack
under
transmission
TIGHTENING
TORQUE
Fixing
bolts
and
nuts
Front
mounting
bracket
to
cylinder
block
Front
mounting
in
lator
to
brac
t
Front
mounting
insulator
to
front
support
Rear
mounting
insulator
to
transmission
Rear
mounting
insulator
to
rear
support
Rear
support
to
frame
Clutch
operating
cylinder
to
transmission
Exhaust
front
tube
to
exhaust
manifold
Center
bearing
bracket
to
crossrnember
Propeller
shaft
to
companion
flange
kg
m
ft
lb
kg
m
ft
Ib
kg
m
ft
lb
kg
m
ft
lb
kg
m
ft
Ib
kg
m
ft
lb
kg
m
ft
Io
kg
m
ft
lb
kg
m
ft
lb
kg
m
ft
lb
ER
4
and
jack
it
up
slightly
2
Loosen
two
rear
engine
mounting
bolts
3
Loosen
two
exhaust
tube
hanger
bolts
California
models
only
4
Remove
rear
mounting
insulator
at
transmission
rear
extension
after
removing
insulator
securing
bolts
5
To
install
reverse
order
of
Ie
moval
2
6
to
3
6
19
to
26
2
6
to
3
6
19
t
o
76
1
4
to
1
8
10
to
13
3
2
to
3
7
23
to
27
1
6
to
2
2
12
to
16
3
2
to
4
3
23
to
31
2
5
to
3
5
18
to
25
1
9
to
2
5
14
to
18
1
6
to
2
2
12
to
16
2
4
to
3
3
17
to
24
Page 224 of 537

Installation
I
Apply
a
light
coat
of
lithium
base
grease
containing
molybdenum
disul
phide
on
transmission
main
drive
gear
splines
Slide
clutch
disc
on
main
drive
gear
several
times
Remove
clutch
disc
and
wipe
off
excess
lubricant
pushed
off
by
disc
hub
2
Install
clutch
disc
and
clutch
cover
assembly
on
flywheel
Support
two
assemblies
with
Clutch
Aligning
Bar
KV30100200
See
Figure
CL
3
Note
Be
sure
to
keep
disc
facings
flywheel
and
pressure
plate
clean
and
dry
7
00
R
rr
CL109
Fig
CL
3
l
talling
clutch
cover
assem
bly
3
Install
six
bolts
to
tighten
clutch
cover
assembly
to
flywheel
squarely
Each
bolt
should
be
tightened
one
turn
at
a
time
to
the
specified
torque
15
to
2
2
kg
m
II
to
16
ft
Ib
Note
Three
dowels
are
used
to
locate
clutch
cover
on
flywheel
properly
4
Remove
Clutch
Aligning
Bar
KV30100200
after
tightening
the
bolts
securely
5
Install
transmission
Note
Make
certain
that
withdrawal
lever
engages
lever
ball
pin
6
Connect
push
rod
of
clutch
op
erating
cylinder
to
withdrawal
lever
DISASSEMBLY
AND
ASSEMBLY
Disassembly
I
Clutch
cover
assembly
can
not
be
CLUTCH
disassembled
since
diaphragm
spring
is
securely
reveted
to
clutch
cover
and
clutch
cover
assembly
is
balanced
If
necessary
replace
clutch
cover
assembly
as
a
complete
unit
2
Remove
clutch
release
mechanism
as
follows
See
Figure
CL4
1
Remove
dust
cover
from
clutch
houisng
2
Remove
withdrawal
lever
from
clutch
housing
3
Remove
retainer
spring
from
withdrawal
lever
4
Remove
release
bearing
bearing
sleeve
and
holder
spring
from
clu
tch
housing
as
an
assembly
1
lo
1
Release
bearing
2
Release
bearing
sleeve
3
Holder
spring
4
Dust
cover
5
Withdrawal
lever
6
Retainer
spring
CL119
Fig
CL
4
Exploded
view
of
clutch
releaae
mechaniam
3
Take
out
clutch
release
bearing
from
bearing
sleeve
using
a
universal
puller
See
Figure
CL
5
C
L014
Fig
CL
5
D
embling
rele
e
b
aring
4
Remove
pilot
bushing
in
crank
shaft
by
Pilot
Bushing
Puller
ST16610001
if
necessary
See
Figure
CL
6
CL3
CLOSS
Fig
CL
6
Removing
pilot
bu
hing
Asse
bly
Release
mechaniam
1
When
assembling
release
bearing
on
sleeve
use
a
press
and
seat
bearing
squarely
on
sleeve
See
Figure
CL
7
l
J
I
CL215
I
1
J
1
Fig
CL
7
1
tailing
rele
e
bearing
2
Before
or
during
assembling
lu
bricate
the
following
points
with
a
light
coat
of
multi
purpose
grease
I
Inner
groove
of
release
bearing
sleeve
See
Figure
CL
8
Lf
I
n
JQt
CL216
Fig
CL
B
Lu
bricating
ee
of
bearing
slee
2
Contact
surfaces
of
withdrawal
lever
lever
ball
pin
and
bearing
sleeve
3
Contact
surfaces
of
transmission
front
cover
See
Figure
CL
9
Page 227 of 537
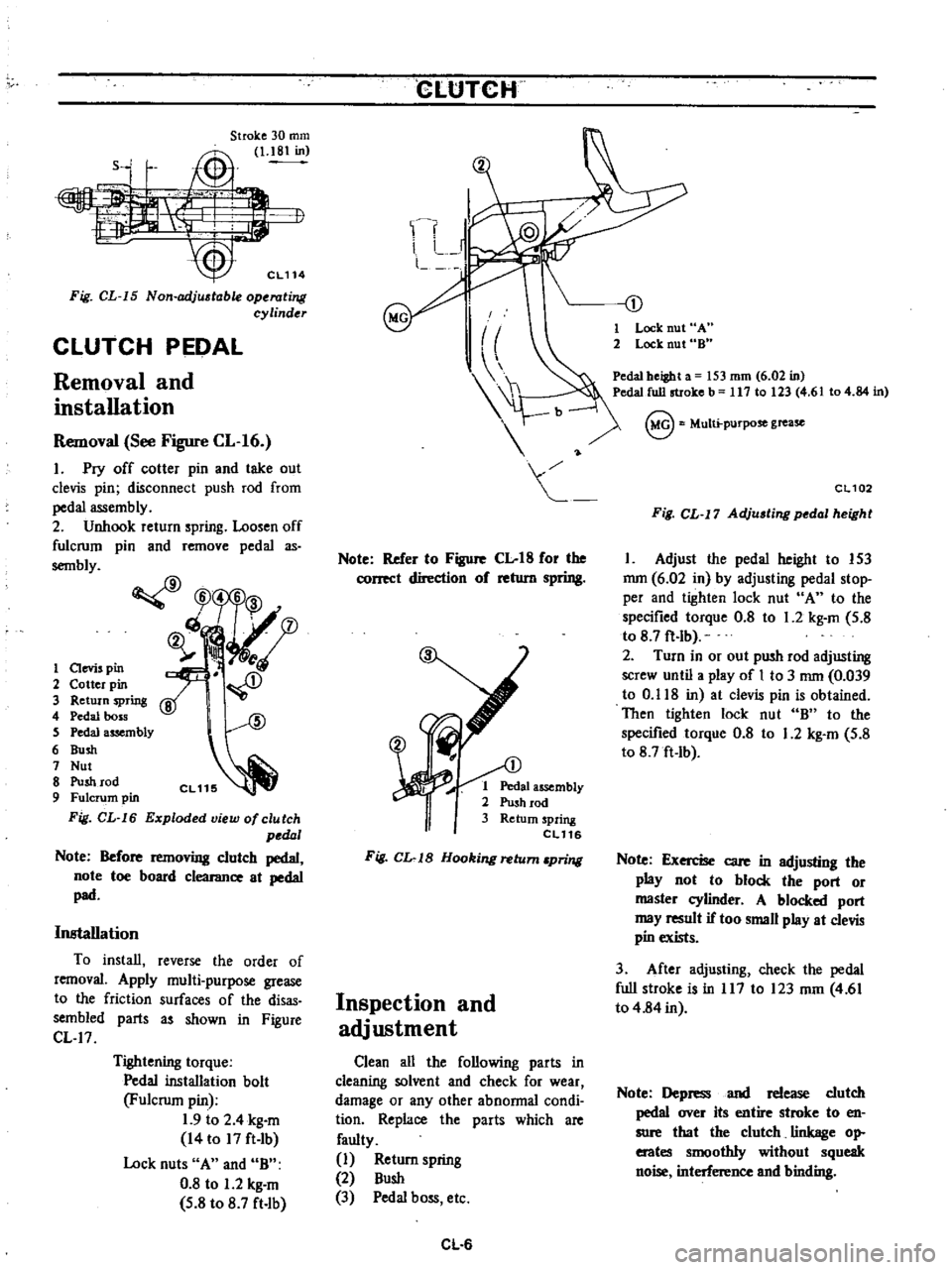
Stroke
30
mm
Jt
i
I
1
18
in
Sj
1
i
J
o
Fig
CL
15
Non
adj
table
operating
cylinder
CLUTCH
PEDAL
Removal
and
installation
Removal
See
Figure
CL
16
1
Pry
off
cotter
pin
and
take
out
clevis
pin
disconnect
push
rod
from
pedal
assembly
2
Unhook
return
spring
Loosen
off
fulcrum
pin
and
remove
pedal
as
sembly
CfJ
W5
6
3
ch
fD
ij
ll
i
A
1
aevis
pin
2
Cotter
pin
3
Return
spring
4
Pedal
boss
S
Pedal
assembly
6
Bush
7
Nut
8
Push
rod
9
Fulcrum
pin
Fig
CL
16
Exploded
view
of
clutch
pedal
Note
Before
removing
clutch
pedal
note
toe
board
clearance
at
pedal
pad
Installation
To
install
reverse
the
order
of
removal
Apply
multi
purpose
grease
to
the
friction
surfaces
of
the
disas
sembled
parts
as
shown
in
Figure
CL
17
Tightening
torque
Pedal
installation
bolt
Fulcrum
pin
1
9
to
2
4
kg
m
14
to
17
ft
Ib
Lock
nuts
A
and
B
0
8
to
1
2
kg
m
5
8
to
8
7
ft
lb
CLtJTCH
Note
Refer
to
Figure
Clot8
for
the
correct
direction
of
return
spring
1
Pedal
assembly
2
Push
rod
3
Return
spring
eL116
Fig
CL
1B
Hooking
return
pring
Inspection
and
adjustment
Clean
all
the
following
parts
in
cleaning
solvent
and
check
for
wear
damage
or
any
other
abnormal
condi
tion
Replace
the
parts
which
are
faulty
1
Return
spring
2
Bush
3
Pedal
boss
etc
CL
6
1
Lock
nut
A
2
Lock
nut
8
Pedal
beiBht
a
53
mm
6
02
in
Pedal
full
stroke
b
117
10
23
4
6
104
84
in
@
Multi
purpose
grease
CL102
Fig
CL
17
Adju
ting
pedal
height
1
Adjust
the
pedal
height
to
153
mm
6
02
in
by
adjusting
pedal
stop
per
and
tighten
lock
nut
A
to
the
specified
torque
0
8
to
1
2
kg
m
5
8
to
8
7
ft
lb
2
Turn
in
or
out
push
rod
adjusting
screw
until
a
play
of
I
to
3
mm
0
039
to
0
118
in
at
clevis
pin
is
obtained
Then
tighten
lock
nut
B
to
the
specified
torque
0
8
to
1
2
kg
m
5
8
to
8
7ft
Ib
Note
Exercise
care
in
adjusting
the
play
not
to
block
the
port
or
master
cylinder
A
blocked
port
may
result
if
too
small
play
at
clevis
pin
exists
3
After
adjusting
check
the
pedal
full
stroke
is
in
117
to
123
mm
4
61
to
4
84
in
Note
Depress
and
release
clutch
pedal
over
its
entire
stroke
to
en
sure
that
the
clutch
linkage
op
erates
smoothly
without
squeak
noise
interference
and
binding
Page 228 of 537
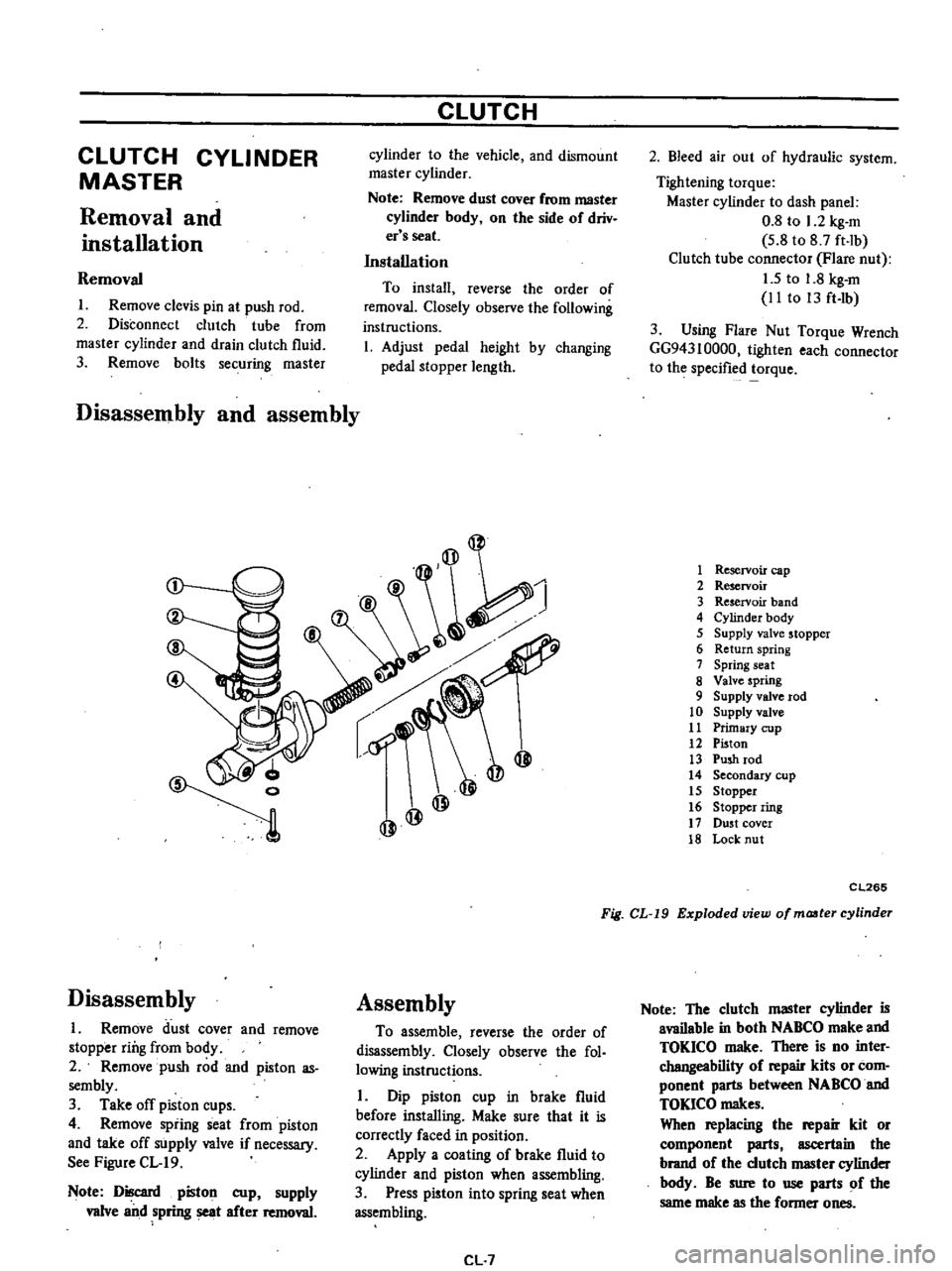
CLUTCH
CYLINDER
MASTER
Removal
and
installation
Removal
I
Remove
clcvis
pin
at
push
rod
2
Disconnect
clutch
tube
from
master
cylinder
and
drain
clutch
fluid
3
Remove
bolts
securing
master
Disassembly
and
assembly
CLUTCH
cylinder
to
the
vehicle
and
dismount
master
cylinder
Note
Remove
dust
cover
from
master
cylinder
body
on
the
side
of
driv
er
s
seat
Installation
To
install
reverse
the
order
of
removal
Closely
observe
the
following
instructions
1
Adjust
pedal
height
by
changing
pedal
stopper
length
Disassembly
1
Remove
dust
cover
and
remove
stopper
ring
from
body
2
Remove
push
rod
and
piston
as
sembly
3
Take
off
piston
cups
4
Remove
spiing
seat
from
piston
and
take
off
supply
valve
if
necessary
See
Figure
CL
19
Note
Discard
piston
cup
supply
valve
and
spring
seat
after
removal
Assembly
To
assemble
reverse
the
order
of
disassembly
Closely
observe
the
fol
lowing
instructions
I
Dip
piston
cup
in
brake
fluid
before
installing
Make
sure
that
it
is
correctly
faced
in
position
2
Apply
a
coating
of
brake
fluid
to
cylinder
and
piston
when
assembling
3
Press
piston
into
spring
seat
when
assembling
CL
7
2
Bleed
air
out
of
hydraulic
system
Tightening
torque
Master
cylinder
to
dash
panel
0
8
to
1
2
kg
m
5
8
to
8
7
ft
lb
Clutch
tube
connector
Flare
nut
1
5
to
1
8
kg
m
II
to
13
ft
lb
3
Using
Flare
Nut
Torque
Wrench
GG94310000
tighten
each
connector
to
the
specified
torque
1
Reservoir
cap
2
Reservoir
3
Reservoir
band
4
Cylinder
body
5
Supply
valve
stopper
6
Return
spring
7
Spring
seat
8
Valve
spring
9
Supply
valve
rod
10
Supply
valve
11
Primary
cup
12
Piston
13
Push
rod
14
Secondary
cup
15
Stopper
16
Stopper
ring
17
DU5t
cover
18
Lock
nut
CL265
Fig
CL
19
Exploded
view
of
maater
cylinder
Note
The
clutch
master
cylinder
is
available
in
both
NABCO
make
and
TOKICO
make
There
is
no
inter
changeability
of
repair
kits
or
com
ponent
parts
between
NABCO
and
TOKlCO
makes
When
replacing
the
repair
kit
or
component
parts
ascertain
the
brand
of
the
clutch
IIIBSter
cylinder
body
Be
sure
to
use
parts
of
the
same
make
as
the
former
ones
Page 229 of 537
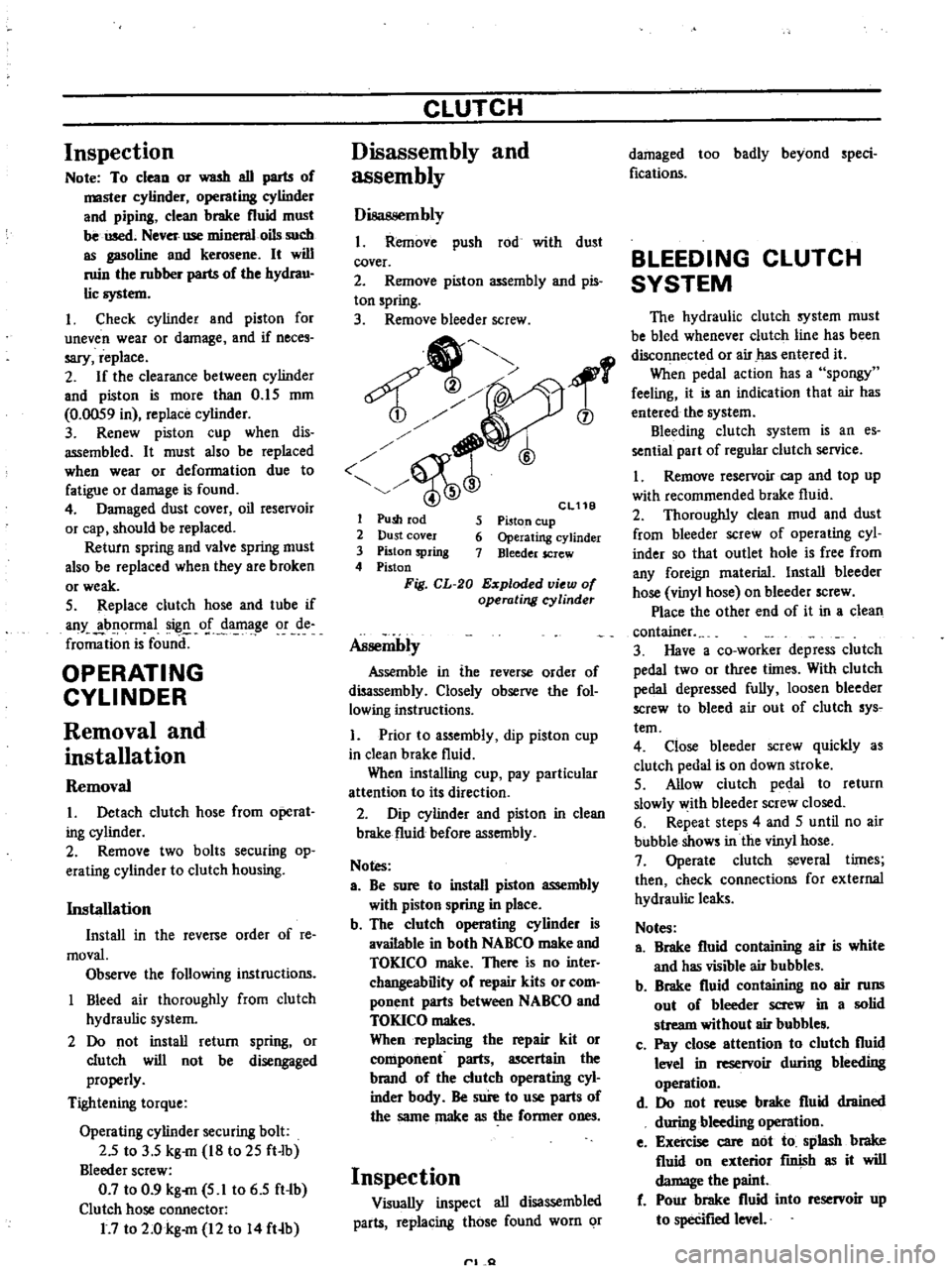
Inspection
Note
To
clean
or
wash
all
parts
of
master
cylinder
operating
cylinder
and
piping
clean
brake
fluid
must
be
used
Never
use
minera10ils
llUch
as
gasoline
and
kerosene
It
will
ruin
the
rubber
parts
of
the
hydrau
lic
system
I
Check
cylinder
and
piston
for
uneven
wear
or
damage
and
if
neces
sary
replace
2
If
the
clearance
between
cylinder
and
piston
is
more
than
0
15
mm
0
0059
in
replace
cylinder
3
Renew
piston
cup
when
dis
assembled
It
must
also
be
replaced
when
wear
or
deformation
due
to
fatigue
or
damage
is
found
4
Damaged
dust
cover
oil
reservoir
or
cap
should
be
replaced
Return
spring
and
valve
spring
must
also
be
replaced
when
they
are
broken
or
weak
5
Replace
clutch
hose
and
tube
if
any
abnormal
sign
of
damage
or
de
fro
ti
n
is
found
OPERATING
CYLINDER
Removal
and
installation
Removal
1
Detach
clutch
hose
from
operat
ing
cylinder
2
Remove
two
bolts
securing
op
erating
cylinder
to
clutch
housing
Installation
Install
in
the
reverse
order
of
re
moval
Observe
the
following
instructions
Bleed
air
thoroughly
from
clutch
hydraulic
system
2
Do
not
install
return
spring
or
clutch
will
not
be
disengaged
properly
Tightening
torque
Operating
cylinder
securing
bolt
2
5
to
3
5
kg
m
18
to
25
ft
lb
Bleeder
screw
0
7
to
0
9
kg
m
5
1
to
6
5
ft
Ib
Clutch
hose
connector
1
7
to
2
0
kg
m
12
to
14
ft
b
CLUTCH
Disassembly
and
assembly
Disassembly
1
Remove
push
rod
with
dust
cover
2
Remove
piston
assembly
and
pis
ton
spring
3
Remove
bleeder
screw
1
6
Cl11B
5
Piston
cup
6
Operating
cylinder
7
Bleeder
screw
1
Push
rod
2
Dust
cover
3
Piston
spring
4
Piston
Fig
CL
20
Exploded
view
of
operating
cyUnder
Assembly
Assemble
in
the
reverse
order
of
disassembly
Closely
observe
the
fol
lowing
instructions
1
Prior
to
assembly
dip
piston
cup
in
clean
brake
fluid
When
installing
cup
pay
particular
attention
to
its
direction
2
Dip
cylinder
and
piston
in
clean
brake
fluid
before
assembly
Notes
a
Be
sure
to
install
piston
assembly
with
piston
spring
in
place
b
The
clutch
operating
cylinder
is
available
in
both
NABCO
make
and
TOKICO
make
There
is
no
inter
changeability
of
repair
kits
or
com
ponent
parts
between
NABCO
and
TOKICO
makes
When
replacing
the
repair
kit
or
component
parts
ascertain
the
brand
of
the
clutch
operating
cyl
inder
bndy
Be
sure
to
use
parts
of
the
same
make
as
the
former
ones
Inspection
Visually
inspect
all
disassembled
parts
replacing
those
found
worn
or
rl
Q
damaged
too
badly
beyond
speci
fications
BLEEDING
CLUTCH
SYSTEM
The
hydraulic
clutch
system
must
be
bled
whenever
clutch
line
has
been
disconnected
or
air
has
entered
it
When
pedal
action
has
a
spongy
feeling
it
is
an
indication
that
air
has
entered
the
system
Bleeding
clutch
system
is
an
es
sential
part
of
regular
clutch
service
I
Remove
reservoir
cap
and
top
up
with
recommended
brake
fluid
2
Thoroughly
clean
mud
and
dust
from
bleeder
screw
of
operating
cyl
inder
so
that
outlet
hole
is
free
from
any
foreign
rnaterial
Install
bleeder
hose
vinyl
hose
on
bleeder
screw
Place
the
other
end
of
it
in
a
clean
container
3
Have
a
co
worker
depress
clutch
pedal
two
or
three
times
With
clu
tch
pedal
depressed
fully
loosen
bleeder
screw
to
bleed
air
out
of
clutch
sys
tern
4
Close
bleeder
screw
quickly
as
clutch
pedal
is
on
down
stroke
5
Allow
clutch
pedal
to
return
slowly
with
bleeder
screw
closed
6
Repeat
steps
4
and
5
until
no
air
bubble
shows
in
the
vinyl
hose
7
Operate
clutch
several
times
then
check
connections
for
external
hydraulic
leaks
Notes
a
Brake
fluid
containing
air
is
white
and
has
visible
air
bubbles
b
Brake
fluid
containing
no
air
runs
out
of
bleeder
screw
in
a
solid
stream
without
air
bubble
c
Pay
close
attention
to
clutch
fluid
level
in
reservoir
during
bleeding
operation
d
Do
not
reuse
brake
fluid
drained
during
bleeding
operation
e
Exercise
care
not
to
splash
brake
fluid
on
exterior
fInish
as
it
will
damage
the
paint
f
Pour
brake
fluid
into
reservoir
up
to
specifIed
level
Page 230 of 537
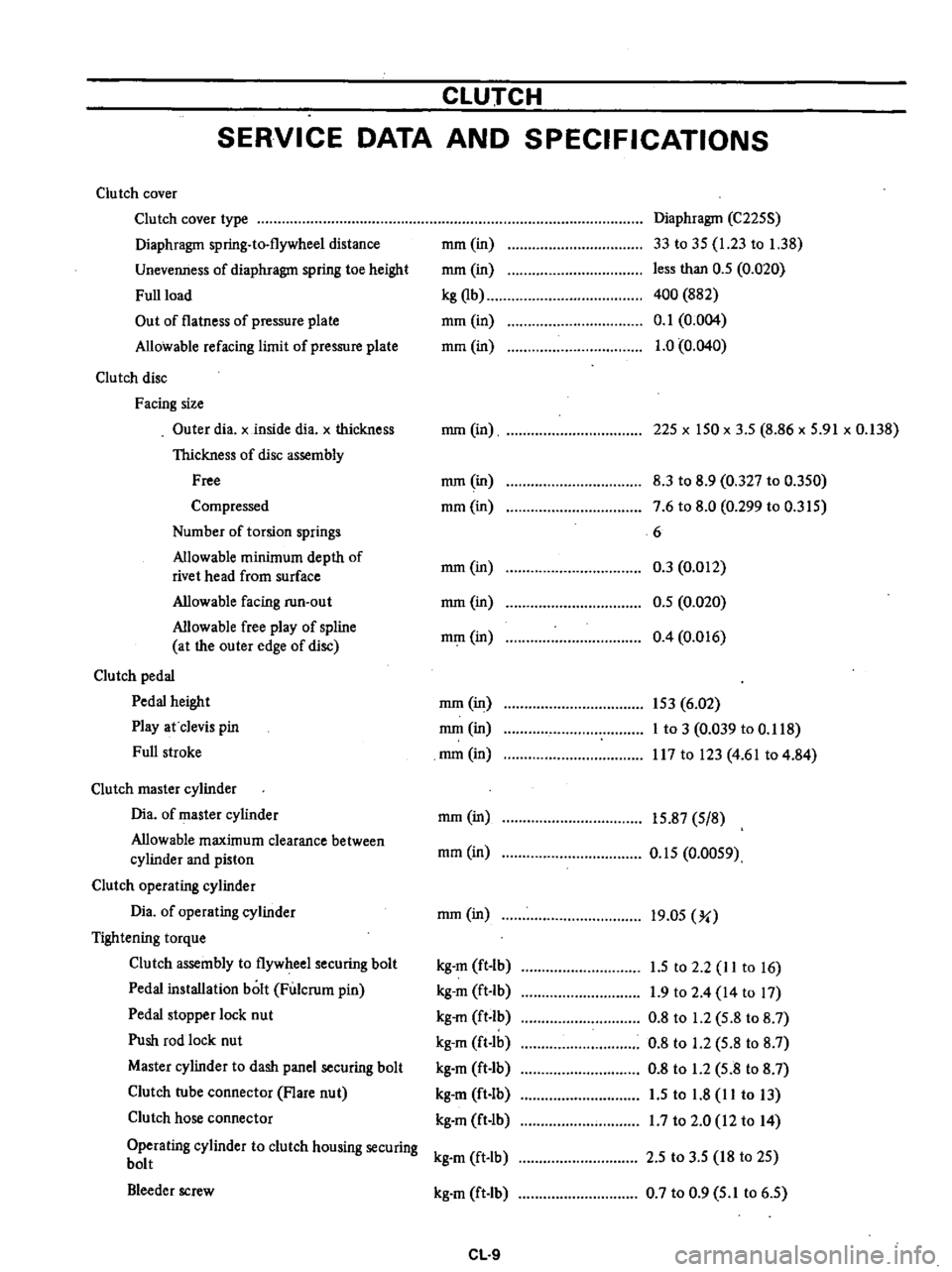
CLUTCH
SERVICE
DATA
AND
SPECIFICATIONS
Clutch
cover
Clu
tch
cover
type
Diaphragm
spring
to
flywheel
distance
Unevenness
of
diaphragm
spring
toe
height
Full
load
Out
of
flatness
of
pressure
plate
Allowable
refacing
limit
of
pressure
plate
Clutch
disc
Facing
size
Outer
dia
x
inside
dia
x
thickness
Thickness
of
disc
assembly
Free
Compressed
Number
of
torsion
springs
Allowable
minimum
depth
of
rivet
head
from
surface
Allowable
facing
run
out
Allowable
free
play
of
spline
at
the
outer
edge
of
disc
Clutch
pedal
Pedal
height
Play
at
clevis
pin
Full
stroke
Clutch
master
cylinder
Dia
of
master
cylinder
Allowable
maximum
clearance
between
cylinder
and
piston
Clutch
operating
cylinder
Dia
of
operating
cylinder
Tightening
torque
Clutch
assembly
to
flywheel
securing
bolt
Pedal
installation
bolt
Fulcrum
pin
Pedal
stopper
lock
nut
Push
rod
lock
nut
Master
cylinder
to
dash
panel
securing
bolt
Clutch
tube
connector
Flare
nut
Clutch
hose
connector
Operating
cylinder
to
clutch
housing
securing
bolt
Bleeder
screw
mm
in
mm
in
kg
Qb
mm
in
mm
in
Diaphragm
C225S
33
to
35
1
23
to
1
38
less
than
0
5
0
020
400
882
0
1
0
004
1
0
0
040
mm
in
225
x
150
x
3
5
8
86
x
5
91
x
0
138
mm
in
mm
in
8
3
to
8
9
0
327
to
0
350
7
6
to
8
0
0
299
to
0
315
6
0
3
0
012
0
5
0
020
0
4
0
016
mm
in
mm
in
mm
in
mm
in
153
6
02
mm
in
I
to
3
0
039
to
0
118
mm
in
117
to
123
4
61
to
4
84
mm
in
15
87
5
8
mm
in
0
15
0
0059
mm
in
19
05
Yo
kg
m
ft
lb
1
5
to
2
2
lito
16
kg
m
ft
Ib
1
9
to
2
4
14
to
17
kg
m
ft
b
0
8
to
1
2
5
8
to
8
7
kg
m
ft
lb
0
8
to
1
2
5
8
to
8
7
kg
m
ft
Ib
0
8
to
1
2
5
8
to
8
7
kg
m
ft
lb
1
5
to
1
8
11
to
13
kg
m
ft
lb
1
7
to
2
0
12
to
14
kg
m
ft
lb
2
5
to
3
5
18
to
25
kg
m
ft
Ib
0
7
to
0
9
5
1
to
6
5
CL
9
Page 234 of 537
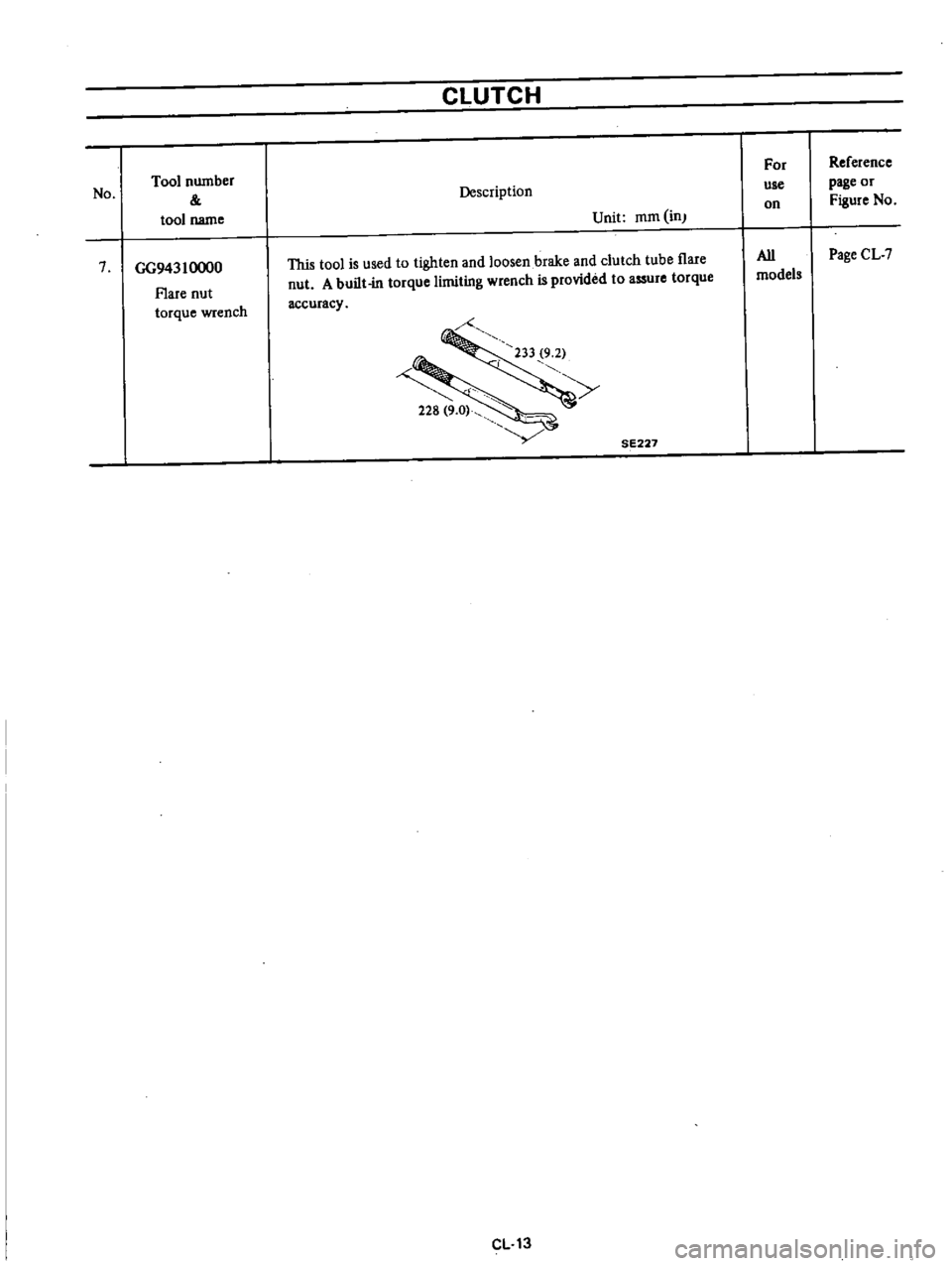
No
Tool
number
tool
name
7
GG94310000
Flare
nut
torque
wrench
CLUTCH
Description
Unit
mm
in
This
tool
is
used
to
tighten
and
loosen
brake
and
clutch
tube
flare
nut
A
built
in
torque
limiting
wrench
is
provided
to
assure
torque
accuracy
y
SE227
CL
13
For
use
on
All
models
Reference
page
or
Figure
No
Page
CL
7
Page 243 of 537
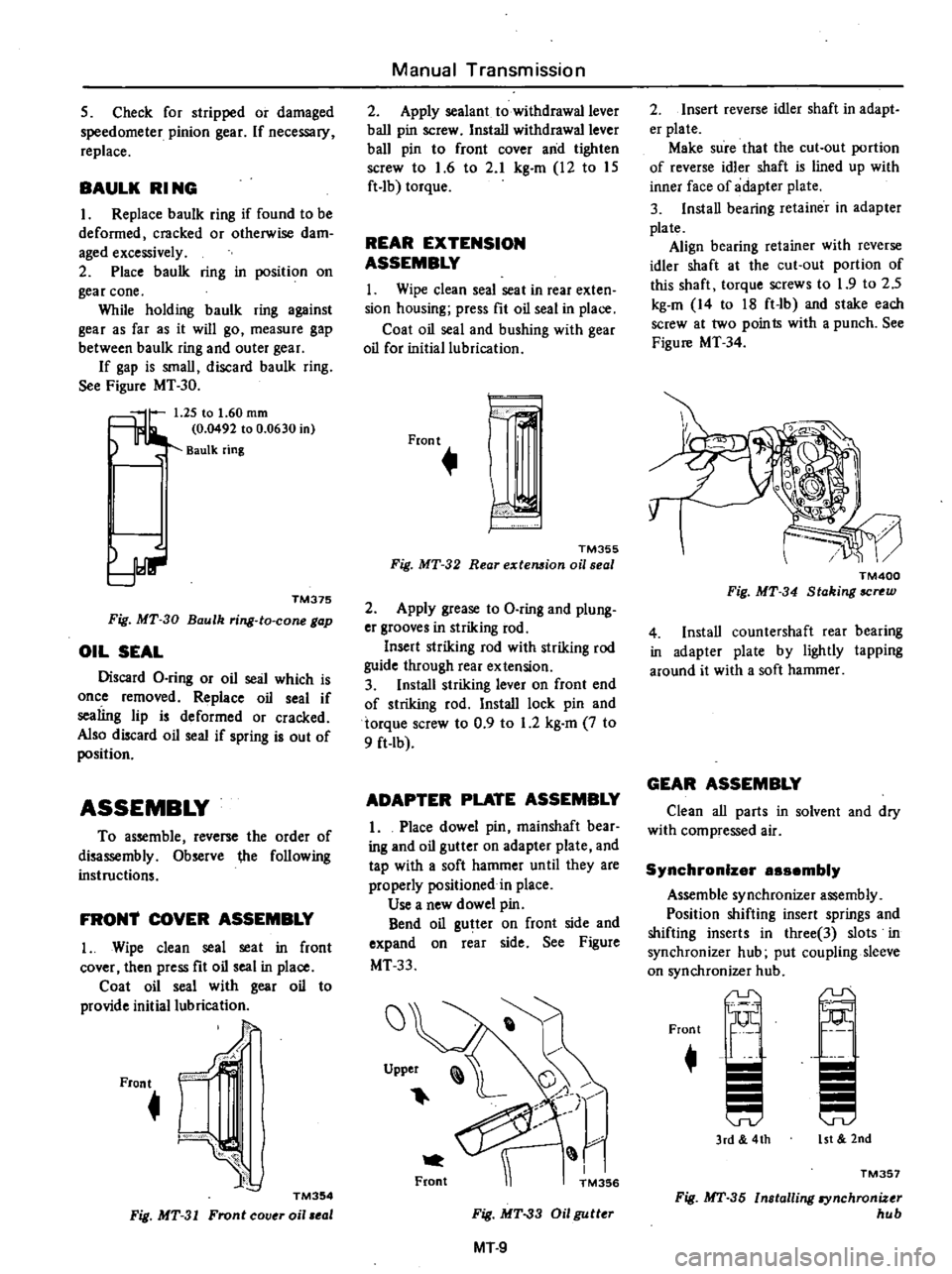
5
Check
for
stripped
or
damaged
speedometer
pinion
gear
If
necessary
replace
BAULK
RI
NG
I
Replace
baulk
ring
if
found
to
be
deformed
cracked
or
otherwise
dam
aged
excessively
2
Place
baulk
ring
in
position
on
gear
cone
While
holding
baulk
ring
against
gear
as
far
as
it
will
go
measure
gap
between
baulk
ring
and
outer
gear
If
gap
is
small
discard
baulk
ring
See
Figure
MT
30
5
lr
1
25
to
1
60
rom
0
0492
to
0
0630
in
Baulk
ring
TM375
Fig
MT
30
Baulk
ring
to
cone
gap
OIL
SEAL
Discard
O
ring
or
oil
seal
which
is
once
removed
Replace
oil
seal
if
sealing
lip
is
deformed
or
cracked
Also
discard
oil
seal
if
spring
is
out
of
position
ASSEMBLY
To
assemble
reverse
the
order
of
disassembly
Observe
ihe
following
instructions
FRON1
COVER
ASSEMBLY
I
Wipe
clean
seal
seat
in
front
cover
then
press
fit
oil
seal
in
place
Coat
oil
seal
with
gear
oil
to
provide
initial
lubrication
Front
J
f
C
J
TM354
Fig
MT
31
Front
cov
oil
eol
Manual
Transmission
2
Apply
sealant
to
withdrawal
lever
ball
pin
screw
Install
withdrawal
lever
ball
pin
to
front
cover
and
tighten
screw
to
1
6
to
2
1
kg
m
12
to
15
ft
lb
torque
REAR
EXTENSION
ASSEMBLY
1
Wipe
clean
seal
seat
in
rear
exten
sion
housing
press
fit
oil
seal
in
place
Coat
oil
seal
and
bushing
with
gear
oil
for
initial
lubrication
Front
h
TM355
Fig
MT
32
Rear
extemion
oil
seal
2
Apply
grease
to
O
ring
and
plung
er
grooves
in
striking
rod
Insert
striking
rod
with
striking
rod
guide
through
rear
extension
3
Install
striking
lever
on
front
end
of
striking
rod
Install
lock
pin
and
torque
screw
to
0
9
to
1
2
kg
m
7
to
9
ft
Ib
ADAPTER
PLATE
ASSEMBLY
1
Place
dowel
pin
mainshaft
bear
ing
and
oil
gutter
on
adapter
plate
and
tap
with
a
soft
hammer
until
they
are
properly
positioned
in
place
Use
a
new
dowel
pin
Bend
oil
gutter
on
front
side
and
expand
on
rear
side
See
Figure
MT33
J
7
r
M356
Upper
Front
Fig
MT
33
Oil
gutter
MT
9
2
Insert
reverse
idler
shaft
in
adapt
er
plate
Make
sure
that
the
cut
out
portion
of
reverse
idler
shaft
is
lined
up
with
inner
face
of
adapter
plate
3
Install
bearing
retainer
in
adapter
plate
Align
bearing
retainer
with
reverse
idler
shaft
at
the
cut
out
portion
of
this
shaft
torque
screws
to
1
9
to
2
5
kg
m
14
to
18
ft
lb
and
stake
each
screw
at
two
poin
Is
with
a
punch
See
Figure
MT
34
TM400
Fig
MT
34
Staking
SCN
W
4
Install
countershaft
rear
bearing
in
adapter
plate
by
lightly
tapping
around
it
with
a
soft
hammer
GEAR
ASSEMBLY
Clean
all
parts
in
solvent
and
dry
with
compressed
air
Synchronizer
888embly
Assemble
synchronizer
assembly
Position
shifting
insert
springs
and
shifting
inserts
in
three
3
slots
in
synchronizer
hub
put
coupling
sleeve
on
synchronizer
hub
r
Front
3rd
4th
15t
2nd
TM351
Fig
MT
35
Installing
synchronizer
hub
Page 245 of 537
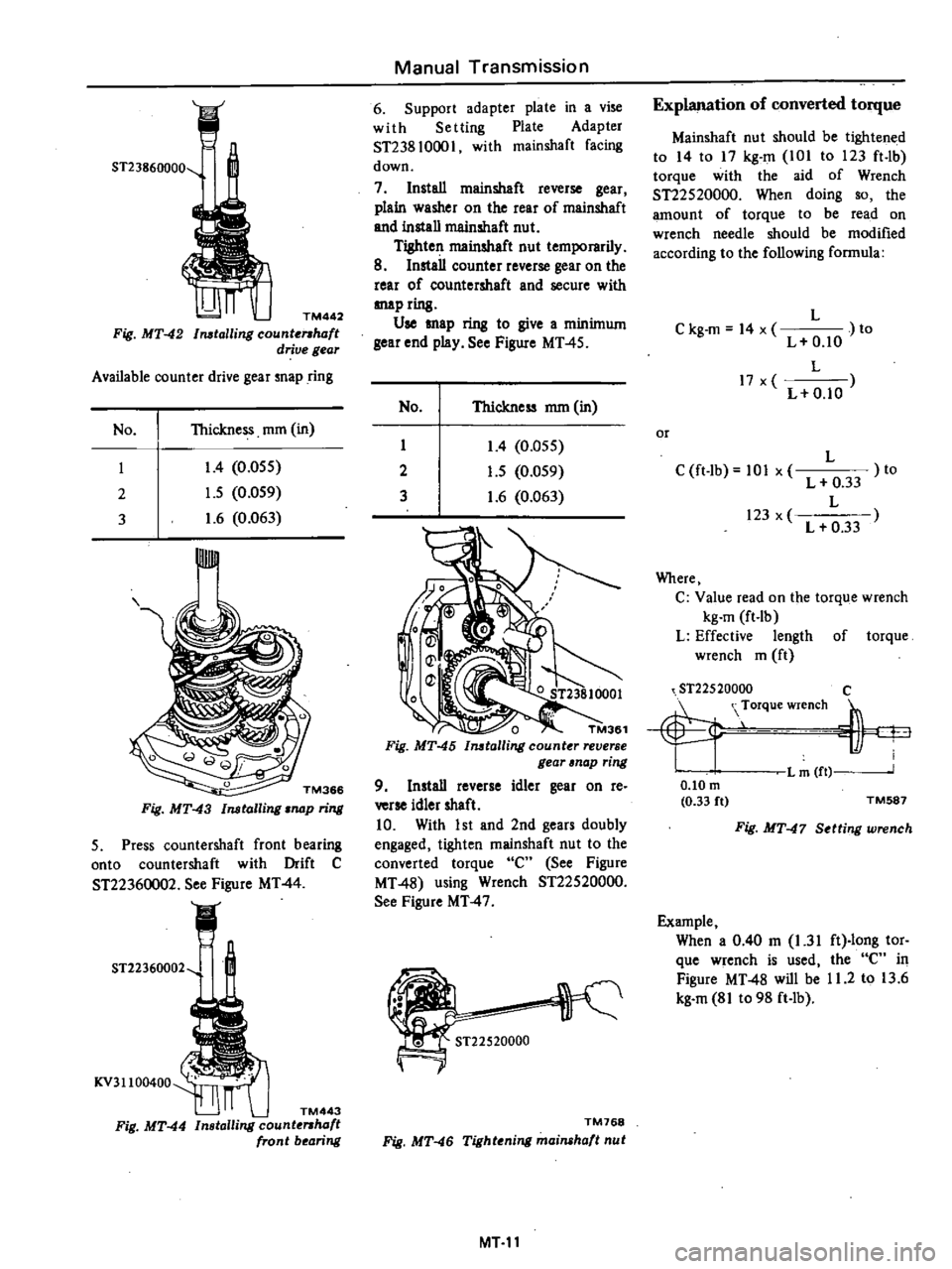
ST23860000
TM442
Fig
MT
42
l
talling
counte
haft
drive
gear
Available
counter
drive
gear
map
ring
No
Thickness
mm
in
I
2
3
1
4
0
055
1
5
0
059
1
6
0
063
II
TM366
Fig
MT
43
Installing
nap
ring
5
Press
countershaft
front
bearing
onto
countershaft
with
Drift
C
ST22360002
See
Figure
MT
44
ST22360002
KV3
II
00400
TM443
Fig
MT
44
Installing
counte
haft
front
bearing
Manual
Transmission
6
Support
adapter
plate
in
a
vise
with
Setting
Plate
Adapter
ST238
10001
with
mainshaft
facing
down
7
Install
mainshaft
reverse
gear
plain
washer
on
the
rear
of
mainshaft
and
install
mainshaft
nut
Tighten
mainshaft
nut
temporarily
8
Install
counter
reverse
gear
on
the
rear
of
countershaft
and
secure
with
map
ring
Use
snap
ring
to
give
a
minimum
gear
end
play
See
Figure
MT
45
No
Thickness
mm
in
I
2
3
1
4
0
055
1
5
0
059
1
6
0
063
o
TM361
Fig
MT
45
Imtalling
counter
reverse
gear
nap
ring
9
Install
reverse
idler
gear
on
re
verse
idler
shaft
10
With
1st
and
2nd
gears
doubly
engaged
tighten
mainshaft
nut
to
the
converted
torque
Cn
See
Figure
MT
48
using
Wrench
ST22520000
See
Figure
MT
4
7
ST22520000
TM768
Fig
MT
46
Tightening
mainshaft
nut
MTll
Explanation
of
converted
torque
Mainshaft
nut
should
be
tightened
to
14
to
17
kg
m
101
to
123
ft
lb
torque
with
the
aid
of
Wrench
ST22520000
When
doing
so
the
amount
of
torque
to
be
read
on
wrench
needle
should
be
modified
according
to
the
following
formula
L
C
kg
m
14
x
to
L
O
lO
L
17
x
L
0
10
or
L
C
ft
lb
101
x
L
0
33
to
L
123
x
L
0
33
Where
C
Value
read
on
the
torque
wrench
kg
m
ft
lb
L
Effective
length
of
torque
wrench
m
ft
ST22520000
Torque
wrench
Lm
ft
c
h
I
O
IOm
0
33
ft
TM587
Fig
MT
47
Setting
wrench
Example
When
a
0
40
m
1
31
ft
long
tor
que
wrench
is
used
the
Cn
in
Figure
MT
48
will
be
11
2
to
13
6
kg
m
81
to
98
ft
lb
Page 246 of 537
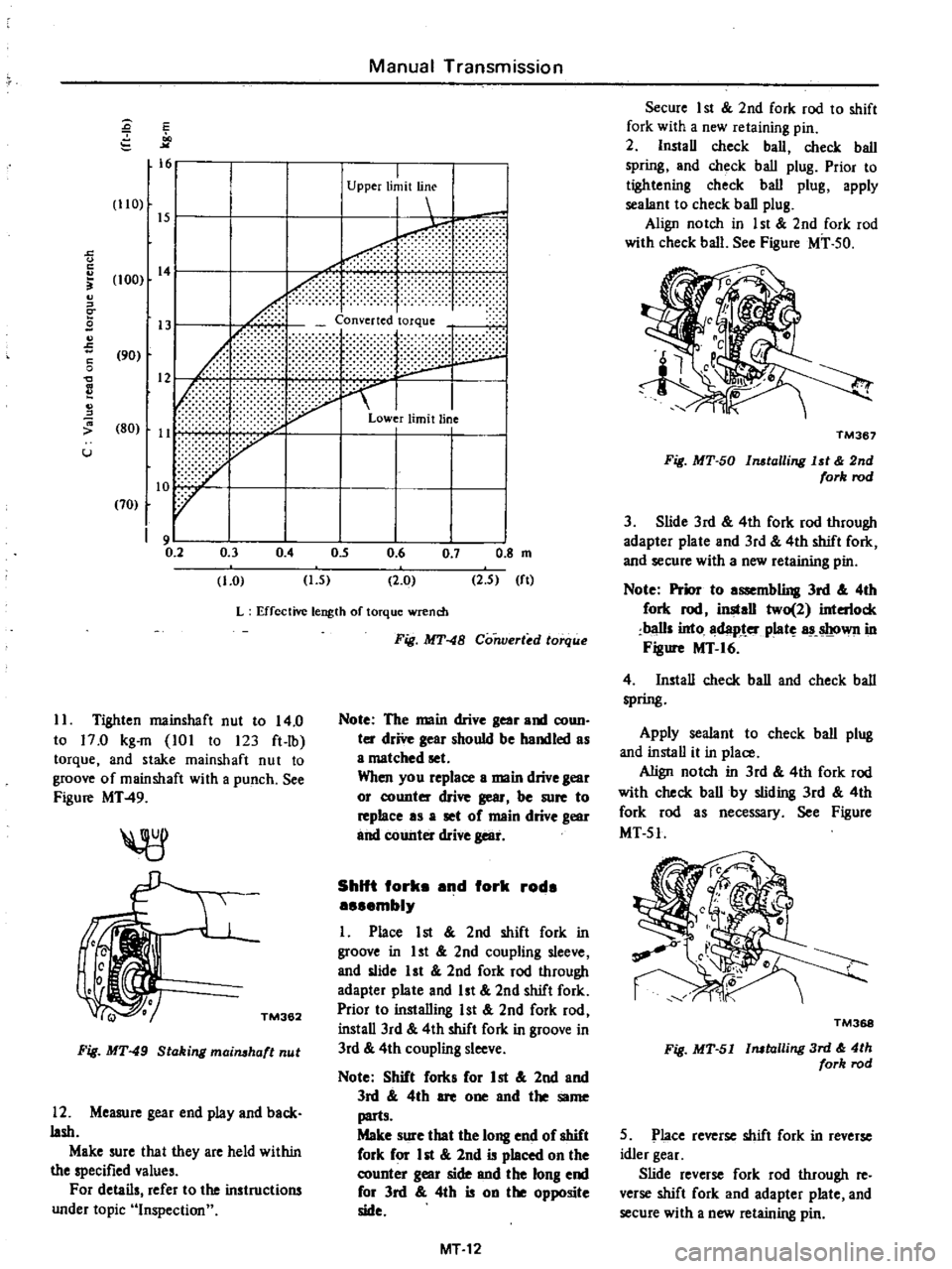
I
Upper
limit
line
I
r
6
1
f
fdl
13
Converted
torque
90
I
Lower
limit
line
80
11
70
10
V
S
s
15
110
15
c
u
c
c
9
S
c
o
C
U
100
14
9
0
2
0
3
1
0
0
4
Manual
Transmission
0
5
0
6
2
0
0
7
0
8
m
2
5
It
1
5
L
Effective
length
of
torque
wrench
Fig
MT
48
CO
1Vert
d
torque
11
Tighten
mainshaft
nut
to
14
0
to
17
0
kg
m
101
to
123
ft
lb
torque
and
stake
mainshaft
nut
to
groove
of
main
shaft
with
a
punch
See
Figure
MT49
TM362
Fig
MT
49
Staking
mai
haft
nut
12
Measure
gear
end
play
and
back
lash
Make
sure
that
they
are
held
within
the
specified
values
For
details
refer
to
the
instructions
under
topic
Inspection
Note
The
main
drive
gear
and
coun
ter
driVe
gear
should
be
handled
as
a
matched
set
When
you
replace
a
main
drive
gear
or
counter
drive
gear
be
sure
to
replace
as
a
set
of
main
drive
gear
and
counter
drive
gear
ShUt
fork
nd
fork
rod
mbly
I
Place
1st
2nd
shift
fork
in
groove
in
1st
2nd
coupling
sleeve
and
slide
1st
2nd
fork
rod
through
adapter
plate
and
1st
2nd
shift
fork
Prior
to
installing
1st
2nd
fork
rod
install
3rd
4th
shift
fork
in
groove
in
3rd
4th
coupling
sleeve
Note
Shift
forks
for
1st
2nd
and
3rd
4th
are
one
and
the
same
parts
Make
sure
that
the
long
end
of
shift
fork
for
lot
2nd
is
placed
on
the
counter
gear
side
and
the
long
end
for
3rd
4th
is
on
the
e
side
MT12
Secure
1st
2nd
fork
rod
to
shift
fork
with
a
new
retaining
pin
2
Install
check
ball
check
ball
spring
and
check
ball
plug
Prior
to
tightening
check
ball
plug
apply
sealant
to
check
ball
plug
Align
notch
in
1st
2nd
fork
rod
with
check
ball
See
Figure
MT
50
TM367
Fig
MT
50
l
talling
1st
2nd
fork
rod
3
Slide
3rd
4th
fork
rod
through
adapter
plate
and
3rd
4th
shift
fork
and
secure
with
a
new
retaining
pin
Note
Prior
to
a
mbling
3rd
4th
fork
rod
install
two
2
interlock
balls
into
dap
er
plat
own
in
Figure
MT
16
4
Install
check
ball
and
check
ball
spring
Apply
sealant
to
check
ball
plug
and
install
it
in
place
Align
notch
in
3rd
4th
fork
rod
with
check
ball
by
sliding
3rd
4th
fork
rod
as
necessary
See
Figure
MT51
TM368
Fig
MT
51
Installing
3rd
4th
fork
rod
5
Place
reverse
shift
fork
in
reverse
idler
gear
Slide
reverse
fork
rod
through
re
verse
shift
fork
and
adapter
plate
and
secure
with
a
new
retaining
pin