DODGE TRUCK 1993 Service Repair Manual
Manufacturer: DODGE, Model Year: 1993, Model line: TRUCK, Model: DODGE TRUCK 1993Pages: 1502, PDF Size: 80.97 MB
Page 291 of 1502
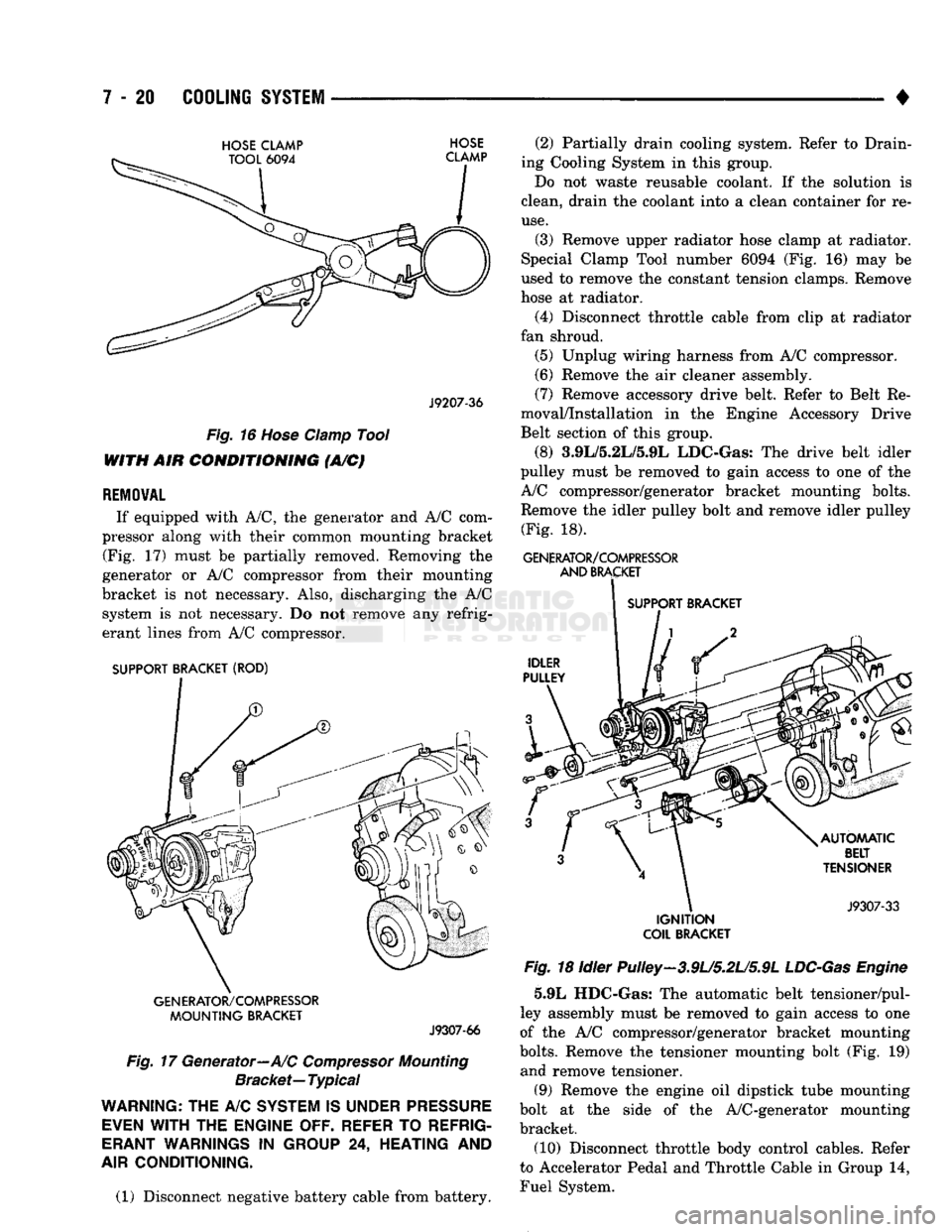
7 - 20
COOLING
SYSTEM
•
HOSE
CLAMP
HOSE
J9207-36
Fig.
16
Hose
Clamp
Tool
WITH AIR
CONDITIONING
(A/C)
REMOVAL
If equipped with A/C, the generator and A/C com
pressor along with their common mounting bracket (Fig. 17) must be partially removed. Removing the
generator or A/C compressor from their mounting
bracket is not necessary. Also, discharging the A/C system is not necessary. Do not remove any refrig
erant lines from A/C compressor.
SUPPORT BRACKET (ROD)
GENERATOR/COMPRESSOR
MOUNTING
BRACKET
J9307-66
Fig.
17 Generator—A/C
Compressor
Mounting
Bracket—
Typical
WARNING;
THE A/C
SYSTEM
IS
UNDER
PRESSURE
EVEN
WITH
THE
ENGINE OFF. REFER
TO
REFRIG
ERANT
WARNINGS
IN
GROUP
24,
HEATING
AND
AIR
CONDITIONING.
(1) Disconnect negative battery cable from battery. (2) Partially drain cooling system. Refer to Drain
ing Cooling System in this group.
Do not waste reusable coolant. If the solution is
clean, drain the coolant into a clean container for re
use.
(3) Remove upper radiator hose clamp at radiator.
Special Clamp Tool number 6094 (Fig. 16) may be
used to remove the constant tension clamps. Remove
hose at radiator.
(4) Disconnect throttle cable from clip at radiator
fan shroud. (5) Unplug wiring harness from A/C compressor.
(6) Remove the air cleaner assembly.
(7) Remove accessory drive belt. Refer to Belt Re
moval/Installation in the Engine Accessory Drive
Belt section of this group.
(8) 3.9L/5.2L/5.9L LDC-Gas: The drive belt idler
pulley must be removed to gain access to one of the
A/C compressor/generator bracket mounting bolts. Remove the idler pulley bolt and remove idler pulley (Fig. 18).
GENERATOR/COMPRESSOR
AND
BRACKET
SUPPORT BRACKET
IGNITION
COIL
BRACKET
Fig.
18 Idler Pulley-3.9U5.2U5.9L
LDC-Gas
Engine
5.9L HDC-Gas: The automatic belt tensioner/pul-
ley assembly must be removed to gain access to one
of the A/C compressor/generator bracket mounting
bolts.
Remove the tensioner mounting bolt (Fig. 19) and remove tensioner.
(9) Remove the engine oil dipstick tube mounting
bolt at the side of the A/C-generator mounting
bracket.
(10) Disconnect throttle body control cables. Refer
to Accelerator Pedal and Throttle Cable in Group 14,
Fuel System.
Page 292 of 1502
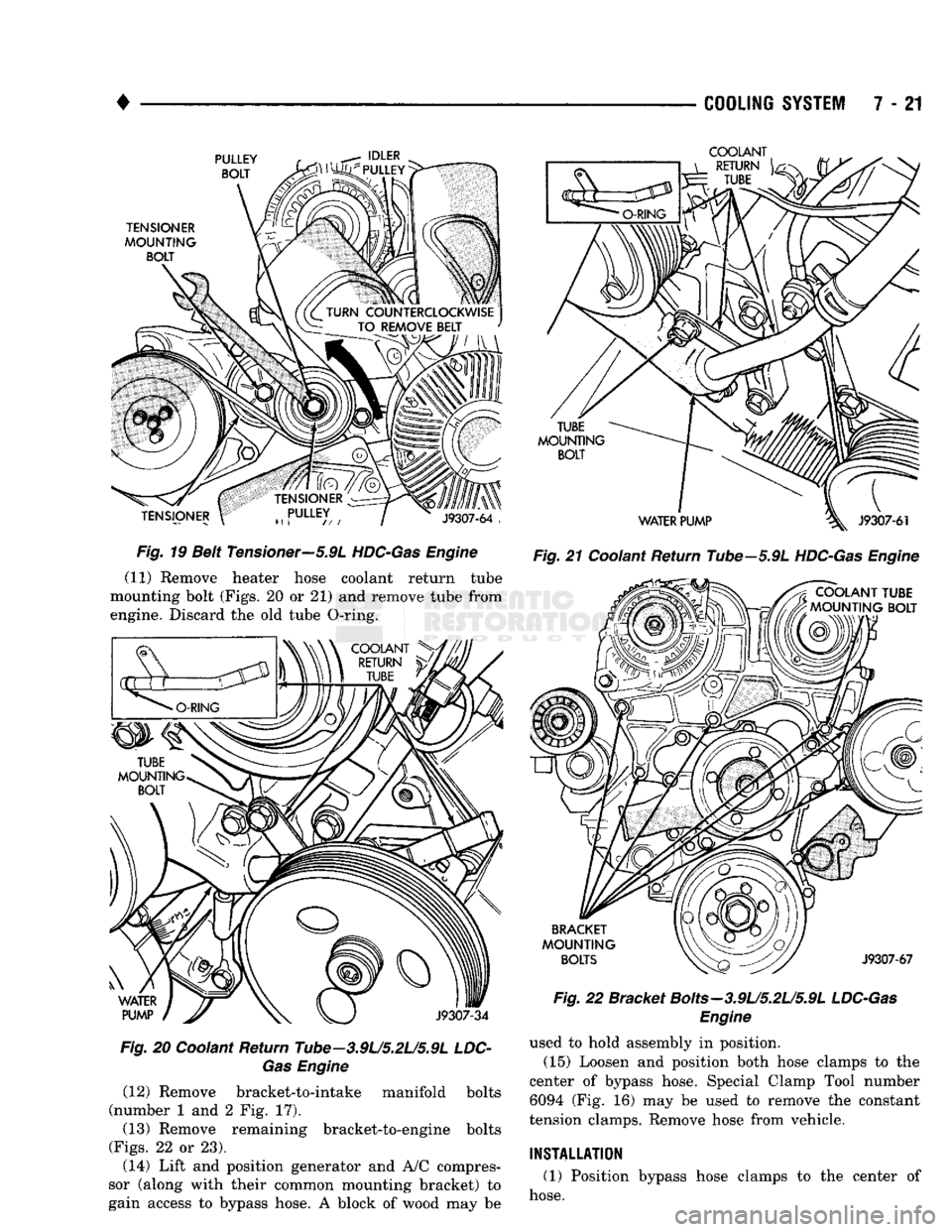
•
COOLING
SYSTEM
7 - 21
Fig.
19 Belt Tensioner—5.9L
HDC-Gas
Engine
(11) Remove heater hose coolant return tube
mounting bolt (Figs. 20 or 21) and remove tube from
engine. Discard the old tube O-ring,
Fig.
20 Coolant Return Tube-3.9U5.2U5.9L LDC-
Gas
Engine
(12) Remove bracket-to-intake manifold bolts
(number 1 and 2 Fig. 17).
(13) Remove remaining bracket-to-engine bolts
(Figs.
22 or 23). (14) Lift and position generator and A/C compres
sor (along with their common mounting bracket) to
gain access to bypass hose. A block of wood may be
Fig.
21 Coolant Return Tube—5.9L
HDC-Gas
Engine
Fig.
22 Bracket Bolts-3.9U5.2U5.9L
LDC-Gas
Engine
used to hold assembly in position.
(15) Loosen and position both hose clamps to the
center of bypass hose. Special Clamp Tool number
6094 (Fig. 16) may be used to remove the constant
tension clamps. Remove hose from vehicle.
INSTALLATION
(1) Position bypass hose clamps to the center of
hose.
Page 293 of 1502

7 - 22
COOLING
SYSTEM
•
Fig.
23 Bracket
Bolts—5.9L
HDC-Gas Engine
(2) Install bypass hose to engine.
(3) Secure both hose clamps.
(4) Install generator-A/C mounting bracket assem
bly to engine. Tighten bolts (number 1 and 2 Fig. 17)
to 54 Nnn (40 ft. lbs.) torque. Tighten bracket mount ing bolts (Figs. 22 or 23) to 40 N-m (30 ft. lbs.)
torque.
(5) Install a new O-ring to the heater hose coolant
return tube (Figs. 20 or 21). Coat the new O-ring
with antifreeze before installation. (6) Install coolant return tube and its mounting
bolt to engine (Figs. 20 or 21). (7) Connect throttle body control cables.
(8) Install oil dipstick mounting bolt.
(9) 3.9L/5.2L/5.9L LDC-Gas: Install idler pulley.
Tighten bolt to 54 Nnn (40 ft. lbs.) torque. 5.9L HDC-Gas: Install automatic belt tensioner
assembly to mounting bracket. A dowel pin is located
on back of tensioner (Fig. 24). Align this to dowel
hole (Fig. 25) in tensioner mounting bracket. Tighten
bolt to 41 N-m (30 ft. lbs.). (10) Install drive belt. Refer to Belt Removal/In
stallation in the Engine Accessory Drive Belt section
of this group.
CAUTION:
When installing
the
serpentine
accessory
drive belt,
the
belt must
be
routed correctly.
If not,
the engine
may
overheat
due to the
water pump
ro
tating
in the
wrong direction. Refer
to
Belt Schemat
ics
in the
Engine
Accessory
Drive Belt section
of
this
group
for
correct belt routing.
The
correct belt
with the
correct length must
be
used.
(11) Install air cleaner assembly.
BELT TENSIONER
DOWEL PIN
J9307-63
Fig.
24 Tensioner
Dowel
Pin—5.9L
HDC-Gas Engine Fig.
25 Tensioner
Mounting
Bracket
Dowel
Hote—5.9L
HDC-Gas Engine
(12) Install upper radiator hose to radiator.
(13) Connect throttle cable to clip at radiator fan
shroud.
(14) Connect wiring harness to A/C compressor. (15) Fill cooling system. Refer to Refilling Cooling
System in this group.
(16) Start and warm the engine. Check for leaks.
THERMOSTAT
GENERAL
INFORMATION
The thermostat on all gas powered engines is lo
cated beneath the thermostat housing at the front of
the intake manifold (Fig. 26). The thermostat has an air bleed notch.
The thermostat of the 5.9L diesel engine is located
in the thermostat housing at front of cylinder head.
This is on exhaust manifold side of engine (Fig. 27). The thermostat is a wax pellet driven, reverse pop
pet choke type. The wax pellet is located in a sealed container at the spring end of the thermostat. When
heated, the pellet expands, overcoming closing spring
Page 294 of 1502
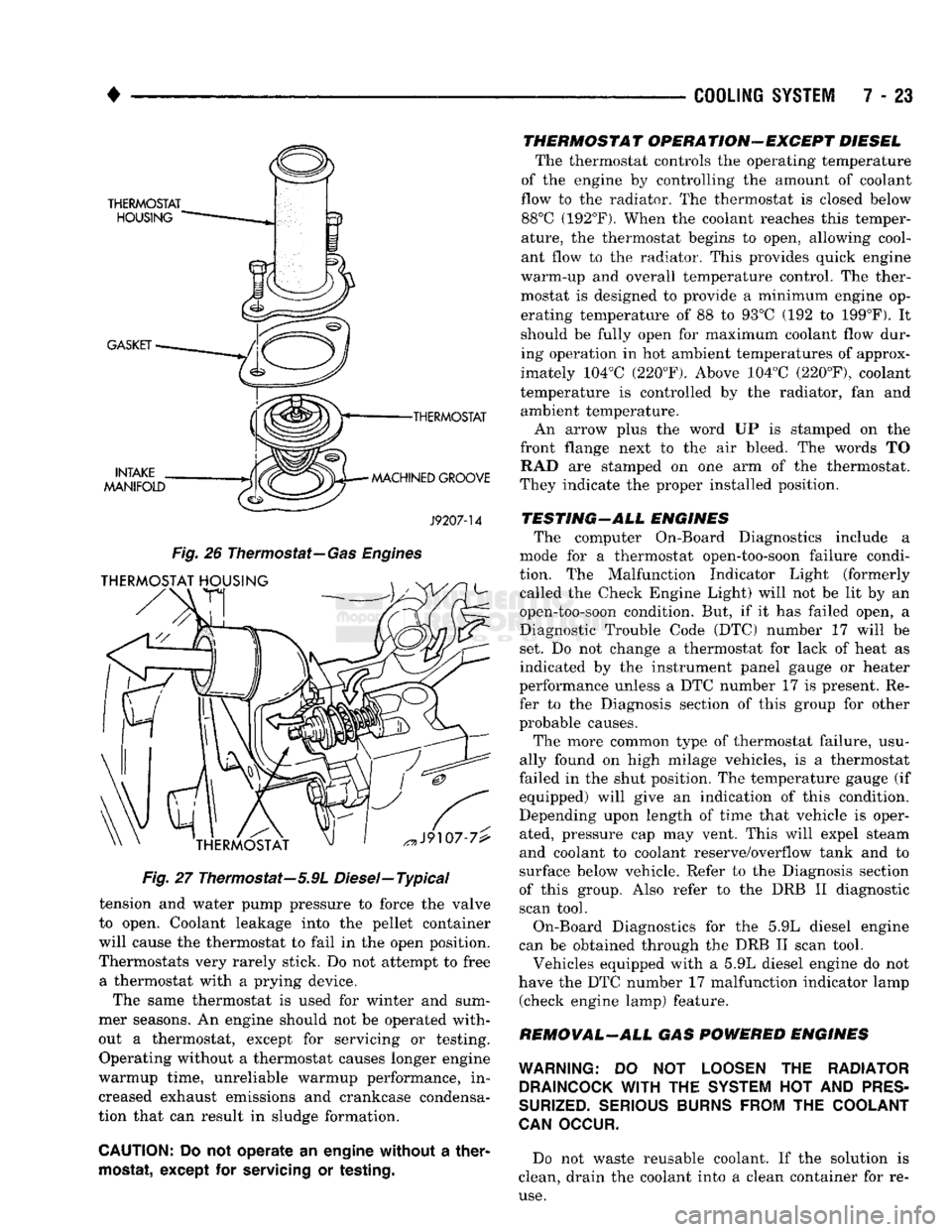
•
COOLING SYSTEM
7 - 23
•THERMOSTAT
MACHINED GROOVE
J9207-14
Fig.
26
Thermostat—
Gas Engines
Fig.
27 Thermostat—5.9L Diesel—Typical
tension and water pump pressure to force the valve
to open. Coolant leakage into the pellet container
will cause the thermostat to fail in the open position.
Thermostats very rarely stick. Do not attempt to free a thermostat with a prying device.
The same thermostat is used for winter and sum
mer seasons. An engine should not be operated with
out a thermostat, except for servicing or testing. Operating without a thermostat causes longer engine
warmup time, unreliable warmup performance, in
creased exhaust emissions and crankcase condensa
tion that can result in sludge formation.
CAUTION:
Do not operate an engine without a
ther
mostat,
except for
servicing
or
testing.
THERMOSTAT OPERATION-EXCEPT DIESEL
The thermostat controls the operating temperature
of the engine by controlling the amount of coolant
flow to the radiator. The thermostat is closed below 88°C (192°F). When the coolant reaches this temper
ature, the thermostat begins to open, allowing cool
ant flow to the radiator. This provides quick engine
warm-up and overall temperature control. The ther
mostat is designed to provide a minimum engine op erating temperature of 88 to 93°C (192 to 199°F). It
should be fully open for maximum coolant flow dur
ing operation in hot ambient temperatures of approx
imately 104°C (220°F). Above 104°C (220°F), coolant
temperature is controlled by the radiator, fan and ambient temperature.
An arrow plus the word UP is stamped on the
front flange next to the air bleed. The words TO RAD are stamped on one arm of the thermostat.
They indicate the proper installed position.
TESTING-ALL ENGINES The computer On-Board Diagnostics include a
mode for a thermostat open-too-soon failure condi
tion. The Malfunction Indicator Light (formerly called the Check Engine Light) will not be lit by an
open-too-soon condition. But, if it has failed open, a
Diagnostic Trouble Code (DTC) number 17 will be
set. Do not change a thermostat for lack of heat as
indicated by the instrument panel gauge or heater
performance unless a DTC number 17 is present. Re
fer to the Diagnosis section of this group for other
probable causes.
The more common type of thermostat failure, usu
ally found on high milage vehicles, is a thermostat
failed in the shut position. The temperature gauge (if equipped) will give an indication of this condition.
Depending upon length of time that vehicle is oper
ated, pressure cap may vent. This will expel steam
and coolant to coolant reserve/overflow tank and to
surface below vehicle. Refer to the Diagnosis section
of this group. Also refer to the DRB II diagnostic
scan tool.
On-Board Diagnostics for the 5.9L diesel engine
can be obtained through the DRB II scan tool.
Vehicles equipped with a 5.9L diesel engine do not
have the DTC number 17 malfunction indicator lamp (check engine lamp) feature.
REMOVAL-ALL GAS POWERED ENGINES
WARNING:
DO NOT
LOOSEN
THE
RADIATOR DRAINCOCK
WITH
THE
SYSTEM
HOT AND
PRES
SURIZED.
SERIOUS BURNS FROM
THE
COOLANT
CAN
OCCUR.
Do not waste reusable coolant. If the solution is
clean, drain the coolant into a clean container for re
use.
Page 295 of 1502
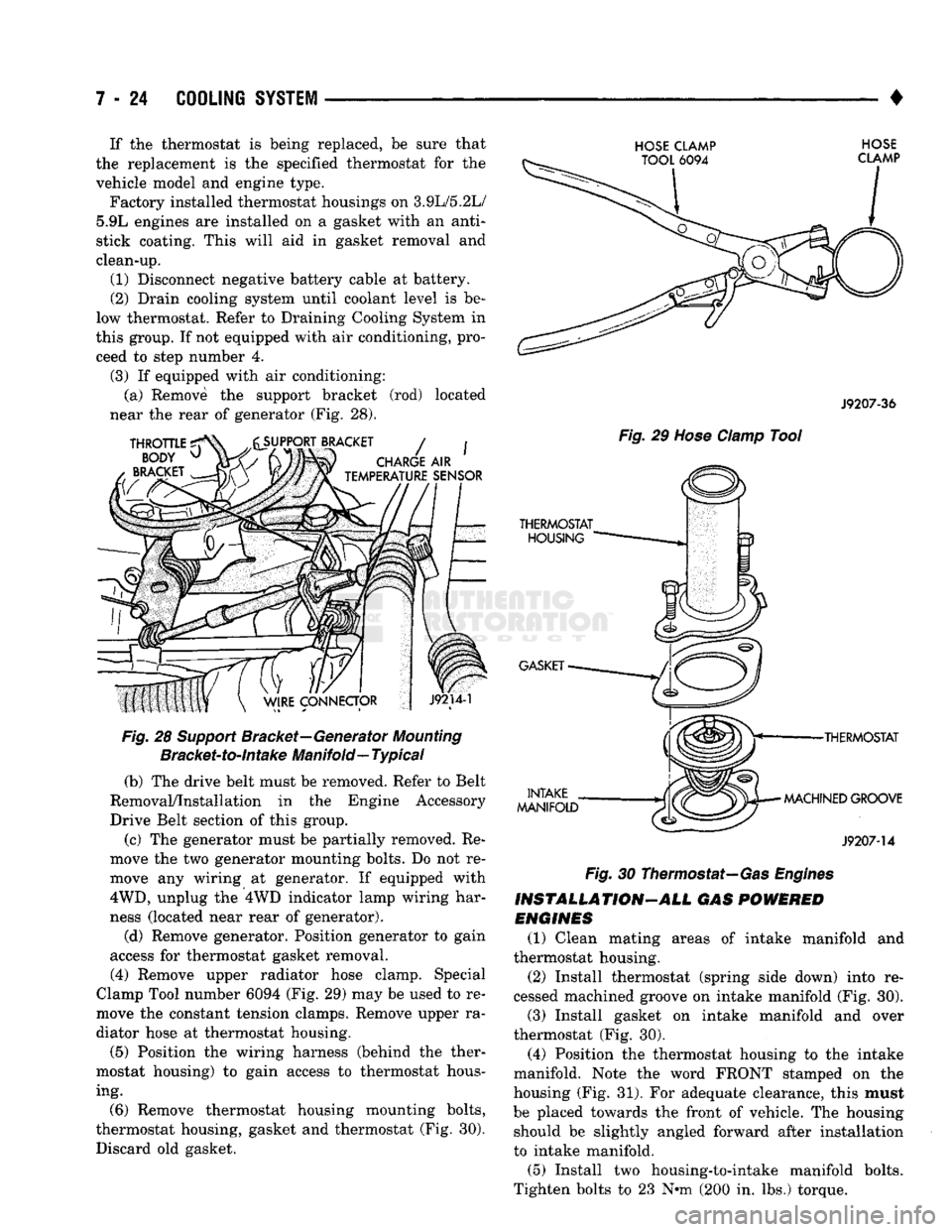
7 - 24
COOLING SYSTEM
• If the thermostat is being replaced, be sure that
the replacement is the specified thermostat for the vehicle model and engine type. Factory installed thermostat housings on 3.9L/5.2L/
5.9L engines are installed on a gasket with an anti-
stick coating. This will aid in gasket removal and
clean-up.
(1) Disconnect negative battery cable at battery.
(2) Drain cooling system until coolant level is be
low thermostat. Refer to Draining Cooling System in
this group. If not equipped with air conditioning, pro ceed to step number 4.
(3) If equipped with air conditioning: (a) Remove the support bracket (rod) located
near the rear of generator (Fig. 28).
Fig.
28
Support
Bracket—Generator
Mounting
Bracket-to-intake
Manifold—
Typical
(b) The drive belt must be removed. Refer to Belt
Removal/Installation in the Engine Accessory
Drive Belt section of this group.
(c) The generator must be partially removed. Re
move the two generator mounting bolts. Do not re
move any wiring at generator. If equipped with
4WD,
unplug the 4WD indicator lamp wiring har
ness (located near rear of generator).
(d) Remove generator. Position generator to gain
access for thermostat gasket removal.
(4) Remove upper radiator hose clamp. Special
Clamp Tool number 6094 (Fig. 29) may be used to re
move the constant tension clamps. Remove upper ra
diator hose at thermostat housing.
(5) Position the wiring harness (behind the ther
mostat housing) to gain access to thermostat hous ing.
(6) Remove thermostat housing mounting bolts,
thermostat housing, gasket and thermostat (Fig. 30). Discard old gasket.
HOSE CLAMP HOSE
J9207-36
Fig.
29
Hose
Clamp
Tool
•THERMOSTAT
MACHINED GROOVE
J9207-14
Fig.
30 Thermostat—Gas
Engines
INSTALLATION-ALL GAS
POWERED
ENGINES
(1) Clean mating areas of intake manifold and
thermostat housing. (2) Install thermostat (spring side down) into re
cessed machined groove on intake manifold (Fig. 30).
(3) Install gasket on intake manifold and over
thermostat (Fig. 30).
(4) Position the thermostat housing to the intake
manifold. Note the word FRONT stamped on the
housing (Fig. 31). For adequate clearance, this must
be placed towards the front of vehicle. The housing should be slightly angled forward after installation
to intake manifold.
(5) Install two housing-to-intake manifold bolts.
Tighten bolts to 23 N-m (200 in. lbs.) torque.
Page 296 of 1502
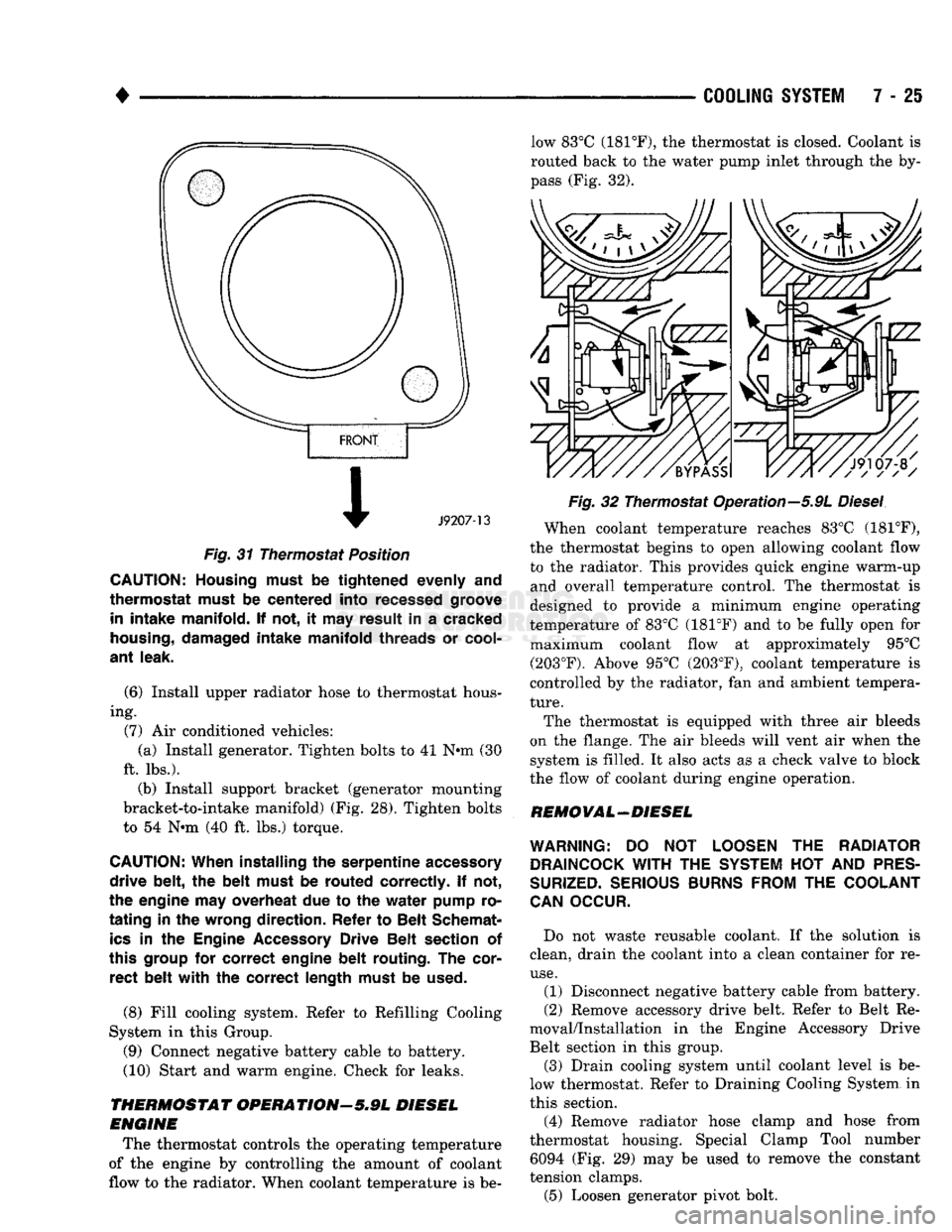
•
COOLING
SYSTEM
7 - 25
Fig.
31 Thermostat Position
CAUTION; Housing must
be
tightened
evenly and
thermostat must
be
centered into recessed groove in
intake manifold. If not, it may
result
in a
cracked
housing,
damaged intake manifold threads
or
cool
ant
leak.
(6) Install upper radiator hose to thermostat hous
ing. (7) Air conditioned vehicles: (a) Install generator. Tighten bolts to 41 N-m (30
ft. lbs.). (b) Install support bracket (generator mounting
bracket-to-intake manifold) (Fig. 28). Tighten bolts
to 54 N-m (40 ft. lbs.) torque.
CAUTION:
When installing
the
serpentine accessory
drive belt,
the
belt must
be
routed correctly.
If not,
the engine
may overheat due to the
water pump
ro
tating in the
wrong direction. Refer
to
Belt Schemat
ics
in the
Engine
Accessory
Drive Belt section
of
this group
for
correct engine belt routing.
The
cor rect belt with
the
correct length must
be
used.
(8) Fill cooling system. Refer to Refilling Cooling
System in this Group. (9) Connect negative battery cable to battery.
(10) Start and warm engine. Check for leaks.
THERMOSTAT OPERATIONr-5.9L DIESEL
ENGINE
The thermostat controls the operating temperature
of the engine by controlling the amount of coolant
flow to the radiator. When coolant temperature is be low 83°C (181°F), the thermostat is closed. Coolant is
routed back to the water pump inlet through the by
pass (Fig. 32).
Fig.
32 Thermostat Operation—5.9L
Diesel
When coolant temperature reaches 83°C (181°F),
the thermostat begins to open allowing coolant flow
to the radiator. This provides quick engine warm-up and overall temperature control. The thermostat is
designed to provide a minimum engine operating
temperature of 83°C (181°F) and to be fully open for maximum coolant flow at approximately 95°C (203°F). Above 95°C (203°F), coolant temperature is
controlled by the radiator, fan and ambient tempera
ture.
The thermostat is equipped with three air bleeds
on the flange. The air bleeds will vent air when the system is filled. It also acts as a check valve to block
the flow of coolant during engine operation.
REMOVAL-DIESEL
WARNING:
DO NOT
LOOSEN
THE
RADIATOR
DRAINCOCK
WITH
THE
SYSTEM
HOT
AND
PRES
SURIZED.
SERIOUS
BURNS
FROM
THE
COOLANT
CAN
OCCUR.
Do not waste reusable coolant. If the solution is
clean, drain the coolant into a clean container for re
use.
(1) Disconnect negative battery cable from battery.
(2) Remove accessory drive belt. Refer to Belt Re
moval/Installation in the Engine Accessory Drive
Belt section in this group.
(3) Drain cooling system until coolant level is be
low thermostat. Refer to Draining Cooling System in
this section.
(4) Remove radiator hose clamp and hose from
thermostat housing. Special Clamp Tool number 6094 (Fig. 29) may be used to remove the constant
tension clamps.
(5) Loosen generator pivot bolt.
Page 297 of 1502
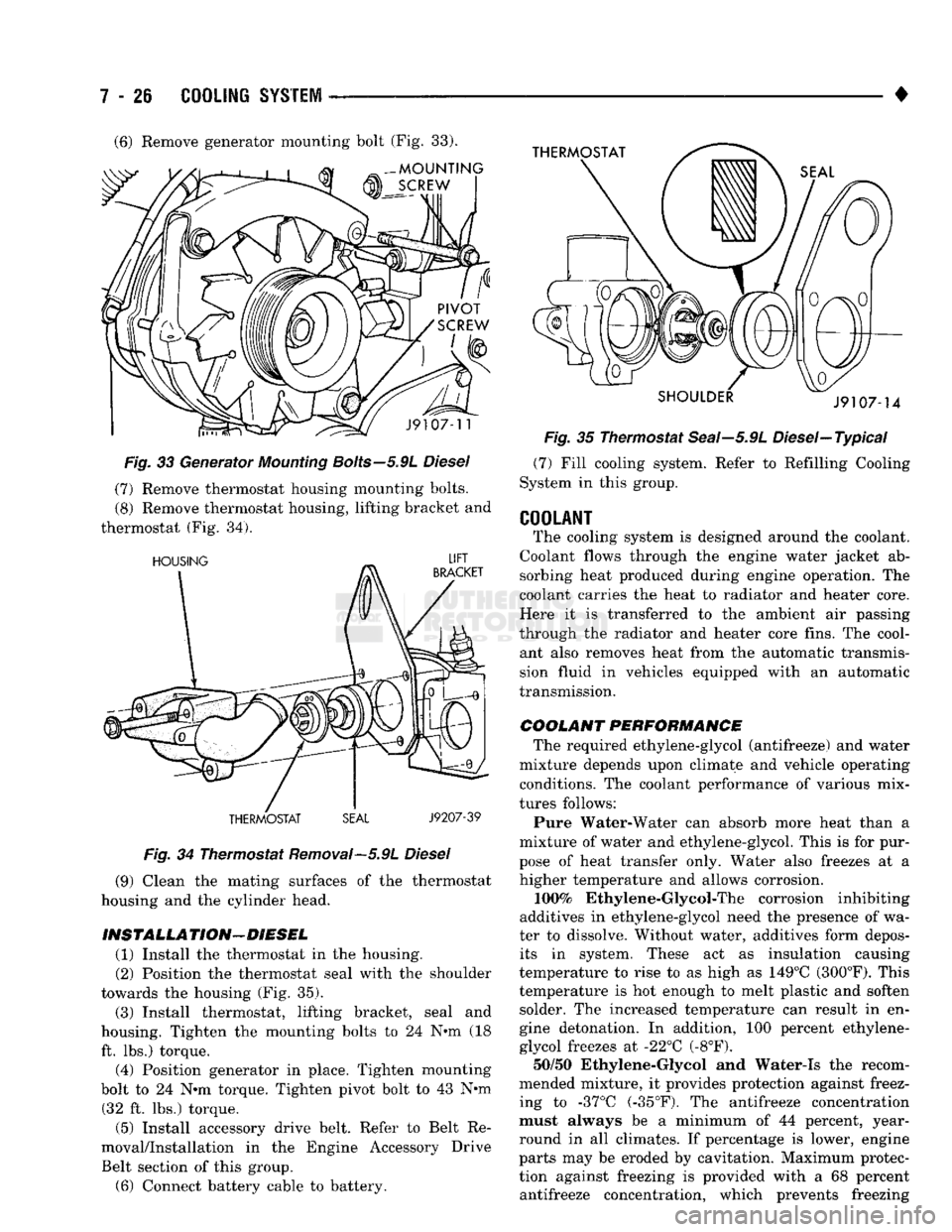
7 - 26
COOLING
SYSTEM
————
Fig. 33 Generator
Mounting
Bolts—5.9L
Diesel (7) Remove thermostat housing mounting bolts.
(8) Remove thermostat housing, lifting bracket and
thermostat (Fig. 34).
Fig.
34 Thermostat Removal—5.9L
Diesel
(9) Clean the mating surfaces of the thermostat
housing and the cylinder head.
INSTALLA TION—DIESEL (1) Install the thermostat in the housing.
(2) Position the thermostat seal with the shoulder
towards the housing (Fig. 35).
(3) Install thermostat, lifting bracket, seal and
housing. Tighten the mounting bolts to 24 N°m (18 ft. lbs.) torque. (4) Position generator in place. Tighten mounting
bolt to 24 N*m torque. Tighten pivot bolt to 43 N*m (32 ft. lbs.) torque.
(5) Install accessory drive belt. Refer to Belt Re
moval/Installation in the Engine Accessory Drive
Belt section of this group.
(6) Connect battery cable to battery. •
Fig.
35 Thermostat Seai—5.9L Diesel—Typical (7) Fill cooling system. Refer to Refilling Cooling
System in this group.
COOLANT
The cooling system is designed around the coolant.
Coolant flows through the engine water jacket ab sorbing heat produced during engine operation. The
coolant carries the heat to radiator and heater core.
Here it is transferred to the ambient air passing
through the radiator and heater core fins. The cool ant also removes heat from the automatic transmission fluid in vehicles equipped with an automatic
transmission.
COOLANT PERFORMANCE The required ethylene-glycol (antifreeze) and water
mixture depends upon climate and vehicle operating conditions. The coolant performance of various mix
tures follows:
Pure Water-Water can absorb more heat than a
mixture of water and ethylene-glycol. This is for pur
pose of heat transfer only. Water also freezes at a higher temperature and allows corrosion.
100%
Ethylene-Glycol-The corrosion inhibiting
additives in ethylene-glycol need the presence of wa
ter to dissolve. Without water, additives form depos its in system. These act as insulation causing
temperature to rise to as high as 149°C (300°F). This
temperature is hot enough to melt plastic and soften solder. The increased temperature can result in en
gine detonation. In addition, 100 percent ethylene-
glycol freezes at -22°C (-8°F). 50/50 Ethylene-Glycol and Water-Is the recom
mended mixture, it provides protection against freez
ing to -37°C (-35°F). The antifreeze concentration
must always be a minimum of 44 percent, year-
round in all climates. If percentage is lower, engine
parts may be eroded by cavitation. Maximum protec
tion against freezing is provided with a 68 percent antifreeze concentration, which prevents freezing (6) Remove generator mounting bolt (Fig. 33).
Page 298 of 1502
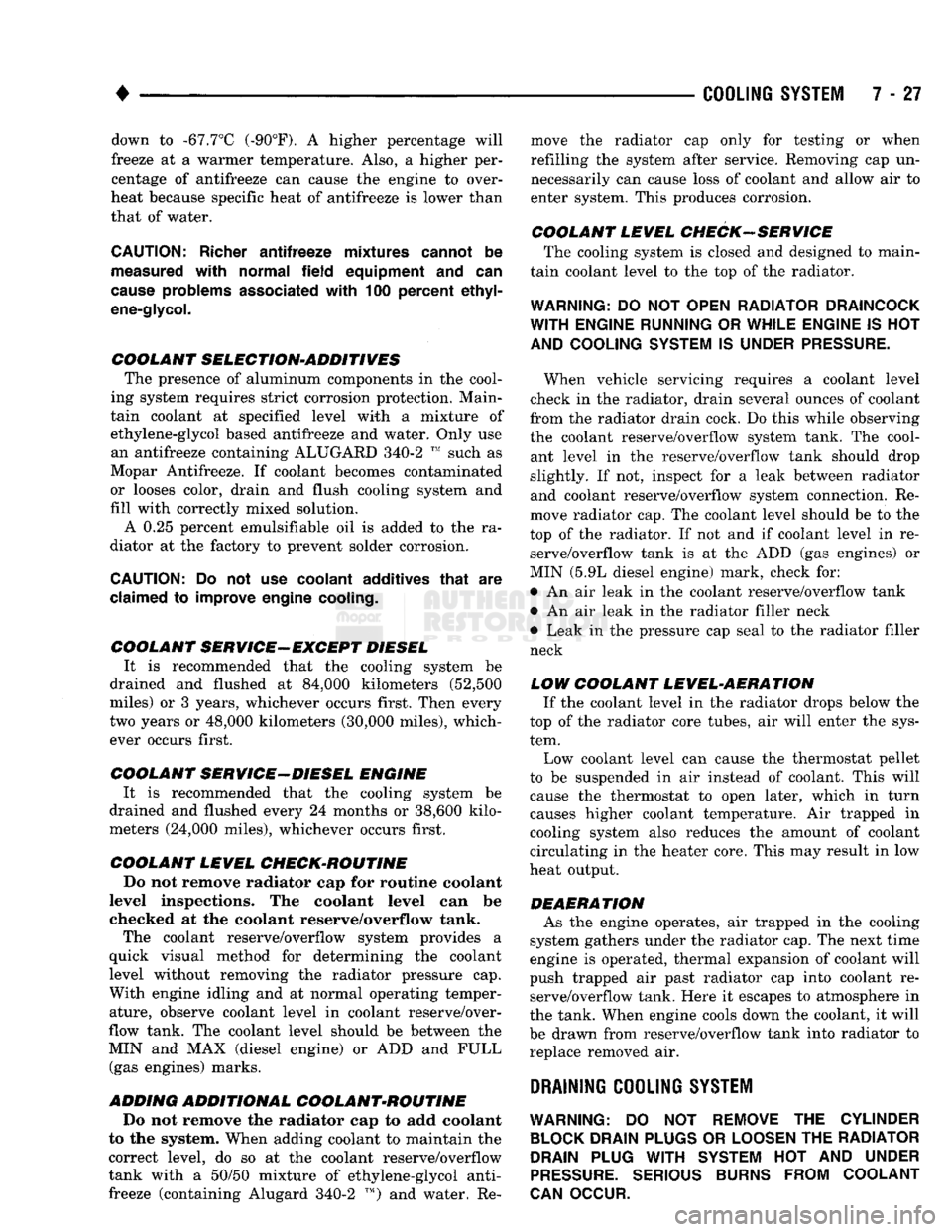
•
COOLING
SYSTEM
7 - 27 down to -67.7°C (-90°F). A higher percentage will
freeze at a warmer temperature. Also, a higher per centage of antifreeze can cause the engine to over
heat because specific heat of antifreeze is lower than
that of water.
CAUTION:
Richer
antifreeze
mixtures
cannot
be
measured
with
normal
field
equipment
and can
cause
problems
associated
with 100
percent
ethyl
ene-glycol.
COOLANT SELECTION-ADDITIVES The presence of aluminum components in the cool
ing system requires strict corrosion protection. Main
tain coolant at specified level with a mixture of ethylene-glycol based antifreeze and water. Only use an antifreeze containing ALUGARD 340-2
™
such as
Mopar Antifreeze. If coolant becomes contaminated
or looses color, drain and flush cooling system and
fill with correctly mixed solution.
A 0.25 percent emulsifiable oil is added to the ra
diator at the factory to prevent solder corrosion.
CAUTION:
Do not use
coolant
additives
that are
claimed
to
improve
engine
cooling.
COOLANT SERVICE-EXCEPT DIESEL It is recommended that the cooling system be
drained and flushed at 84,000 kilometers (52,500
miles) or 3 years, whichever occurs first. Then every
two years or 48,000 kilometers (30,000 miles), which ever occurs first.
COOLANT SERVICE-DIESEL ENGINE It is recommended that the cooling system be
drained and flushed every 24 months or 38,600 kilo meters (24,000 miles), whichever occurs first.
COOLANT LEVEL CHECK-ROUTINE Do not remove radiator cap for routine coolant
level inspections. The coolant level can be checked at the coolant reserve/overflow tank.
The coolant reserve/overflow system provides a
quick visual method for determining the coolant
level without removing the radiator pressure cap.
With engine idling and at normal operating temper ature, observe coolant level in coolant reserve/over
flow tank. The coolant level should be between the MIN and MAX (diesel engine) or ADD and FULL (gas engines) marks.
ADDING ADDITIONAL COOLANT-ROUTINE Do not remove the radiator cap to add coolant
to the system. When adding coolant to maintain the correct level, do so at the coolant reserve/overflow
tank with a 50/50 mixture of ethylene-glycol anti
freeze (containing Alugard 340-2 ™) and water. Re move the radiator cap only for testing or when
refilling the system after service. Removing cap un necessarily can cause loss of coolant and allow air to
enter system. This produces corrosion.
COOLANT LEVEL CHECK-SERVICE The cooling system is closed and designed to main
tain coolant level to the top of the radiator.
WARNING:
DO
NOT OPEN RADIATOR DRAINCOCK
WITH
ENGINE RUNNING
OR
WHILE ENGINE
IS HOT
AND COOLING
SYSTEM
IS
UNDER
PRESSURE.
When vehicle servicing requires a coolant level
check in the radiator, drain several ounces of coolant
from the radiator drain cock. Do this while observing
the coolant reserve/overflow system tank. The cool ant level in the reserve/overflow tank should drop
slightly. If not, inspect for a leak between radiator and coolant reserve/overflow system connection. Re
move radiator cap. The coolant level should be to the
top of the radiator. If not and if coolant level in re serve/overflow tank is at the ADD (gas engines) or
MIN (5.9L diesel engine) mark, check for:
• An air leak in the coolant reserve/overflow tank
• An air leak in the radiator filler neck
• Leak in the pressure cap seal to the radiator filler
neck
LOW COOLANT LEVEL-AERATION If the coolant level in the radiator drops below the
top of the radiator core tubes, air will enter the sys
tem. Low coolant level can cause the thermostat pellet
to be suspended in air instead of coolant. This will cause the thermostat to open later, which in turn causes higher coolant temperature. Air trapped in
cooling system also reduces the amount of coolant
circulating in the heater core. This may result in low
heat output.
DEAERATION As the engine operates, air trapped in the cooling
system gathers under the radiator cap. The next time
engine is operated, thermal expansion of coolant will
push trapped air past radiator cap into coolant re serve/overflow tank. Here it escapes to atmosphere in
the tank. When engine cools down the coolant, it will
be drawn from reserve/overflow tank into radiator to replace removed air.
DRAINING
COOLING
SYSTEM
WARNING:
DO NOT
REMOVE
THE
CYLINDER BLOCK DRAIN PLUGS
OR
LOOSEN THE RADIATOR
DRAIN PLUG
WITH
SYSTEM
HOT AND
UNDER
PRESSURE.
SERIOUS BURNS
FROM
COOLANT
CAN OCCUR.
Page 299 of 1502
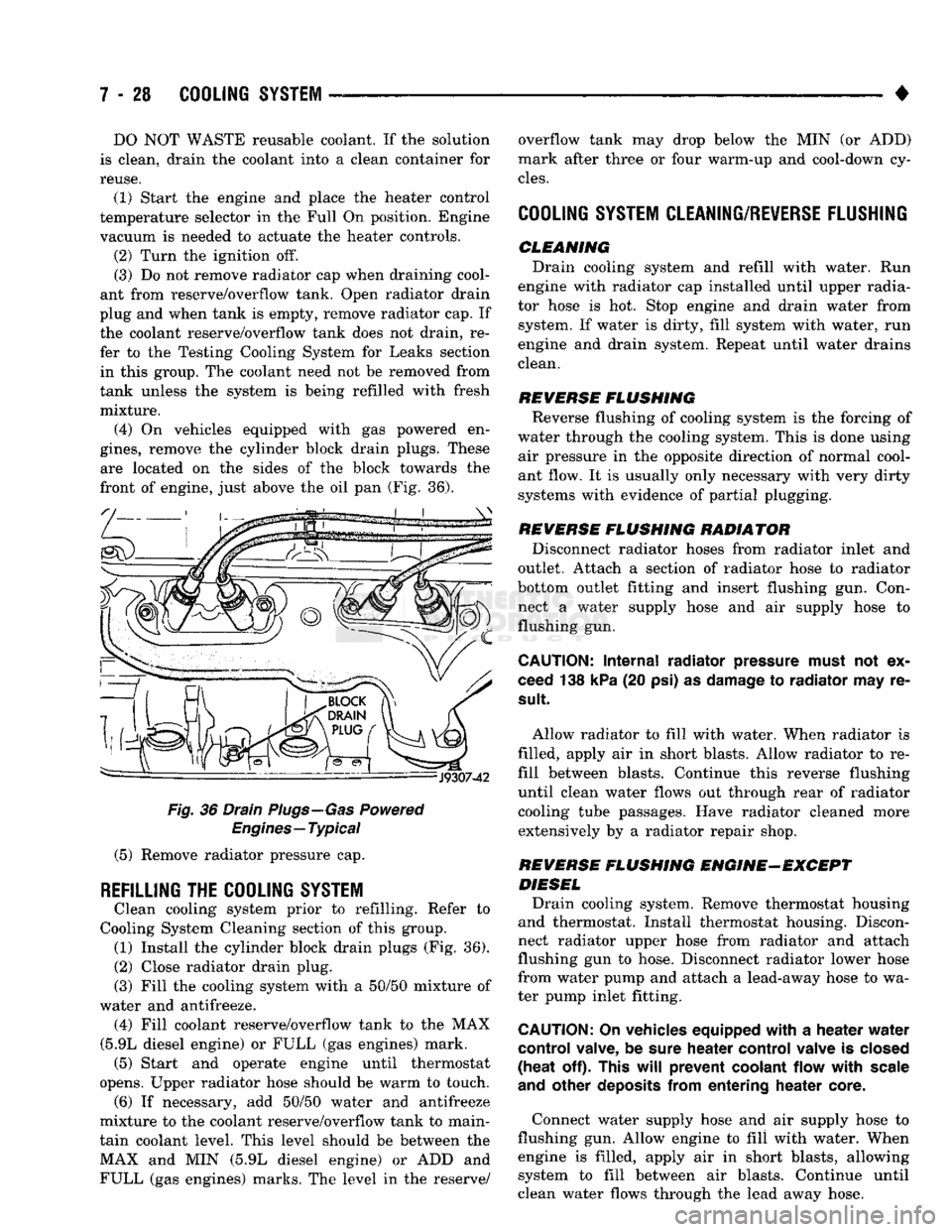
7 - 28
COOLING SYSTEM
DO NOT WASTE reusable coolant. If the solution
is clean, drain the coolant into a clean container for
reuse.
(1) Start the engine and place the heater control
temperature selector in the Full On position. Engine vacuum is needed to actuate the heater controls.
(2) Turn the ignition off. (3) Do not remove radiator cap when draining cool
ant from reserve/overflow tank. Open radiator drain
plug and when tank is empty, remove radiator cap. If
the coolant reserve/overflow tank does not drain, re fer to the Testing Cooling System for Leaks section
in this group. The coolant need not be removed from
tank unless the system is being refilled with fresh mixture.
(4) On vehicles equipped with gas powered en
gines,
remove the cylinder block drain plugs. These are located on the sides of the block towards the
front of engine, just above the oil pan (Fig. 36).
Fig.
36 Drain Plugs—Gas Powered
Engines—Typical
(5) Remove radiator pressure cap.
REFILLING
THE
COOLING SYSTEM
Clean cooling system prior to refilling. Refer to
Cooling System Cleaning section of this group. (1) Install the cylinder block drain plugs (Fig. 36).
(2)
Close radiator drain plug.
(3) Fill the cooling system with a 50/50 mixture of
water and antifreeze. (4) Fill coolant reserve/overflow tank to the MAX
(5.9L diesel engine) or FULL (gas engines) mark. (5) Start and operate engine until thermostat
opens. Upper radiator hose should be warm to touch. (6) If necessary, add 50/50 water and antifreeze
mixture to the coolant reserve/overflow tank to main
tain coolant level. This level should be between the MAX and MIN (5.9L diesel engine) or ADD and FULL (gas engines) marks. The level in the reserve/ overflow tank may drop below the MIN (or ADD)
mark after three or four warm-up and cool-down cy
cles.
COOLING SYSTEM CLEANING/REVERSE FLUSHING
CLEMMING Drain cooling system and refill with water. Run
engine with radiator cap installed until upper radia
tor hose is hot. Stop engine and drain water from system. If water is dirty, fill system with water, run
engine and drain system. Repeat until water drains
clean.
REVERSE
FLUSHING
Reverse flushing of cooling system is the forcing of
water through the cooling system. This is done using air pressure in the opposite direction of normal cool
ant flow. It is usually only necessary with very dirty
systems with evidence of partial plugging.
REVERSE
FLUSHING
RADIATOR Disconnect radiator hoses from radiator inlet and
outlet. Attach a section of radiator hose to radiator
bottom outlet fitting and insert flushing gun. Con
nect a water supply hose and air supply hose to flushing gun.
CAUTION:
Internal
radiator
pressure must
not'ex
ceed 138 kPa (20 psi) as damage to
radiator
may re
sult
Allow radiator to fill with water. When radiator is
filled, apply air in short blasts. Allow radiator to re
fill between blasts. Continue this reverse flushing
until clean water flows out through rear of radiator cooling tube passages. Have radiator cleaned more extensively by a radiator repair shop.
REVERSE
FLUSHING
ENGINE-EXCEPT DIESEL Drain cooling system. Remove thermostat housing
and thermostat. Install thermostat housing. Discon
nect radiator upper hose from radiator and attach
flushing gun to hose. Disconnect radiator lower hose
from water pump and attach a lead-away hose to wa
ter pump inlet fitting.
CAUTION;
On vehicles equipped
with
a
heater
water
control
valve, be sure
heater
control
valve is closed
(heat
off). This
will
prevent
coolant
flow
with
scale
and
other
deposits
from
entering
heater
core.
Connect water supply hose and air supply hose to
flushing gun. Allow engine to fill with water. When engine is filled, apply air in short blasts, allowing system to fill between air blasts. Continue until
clean water flows through the lead away hose.
Page 300 of 1502
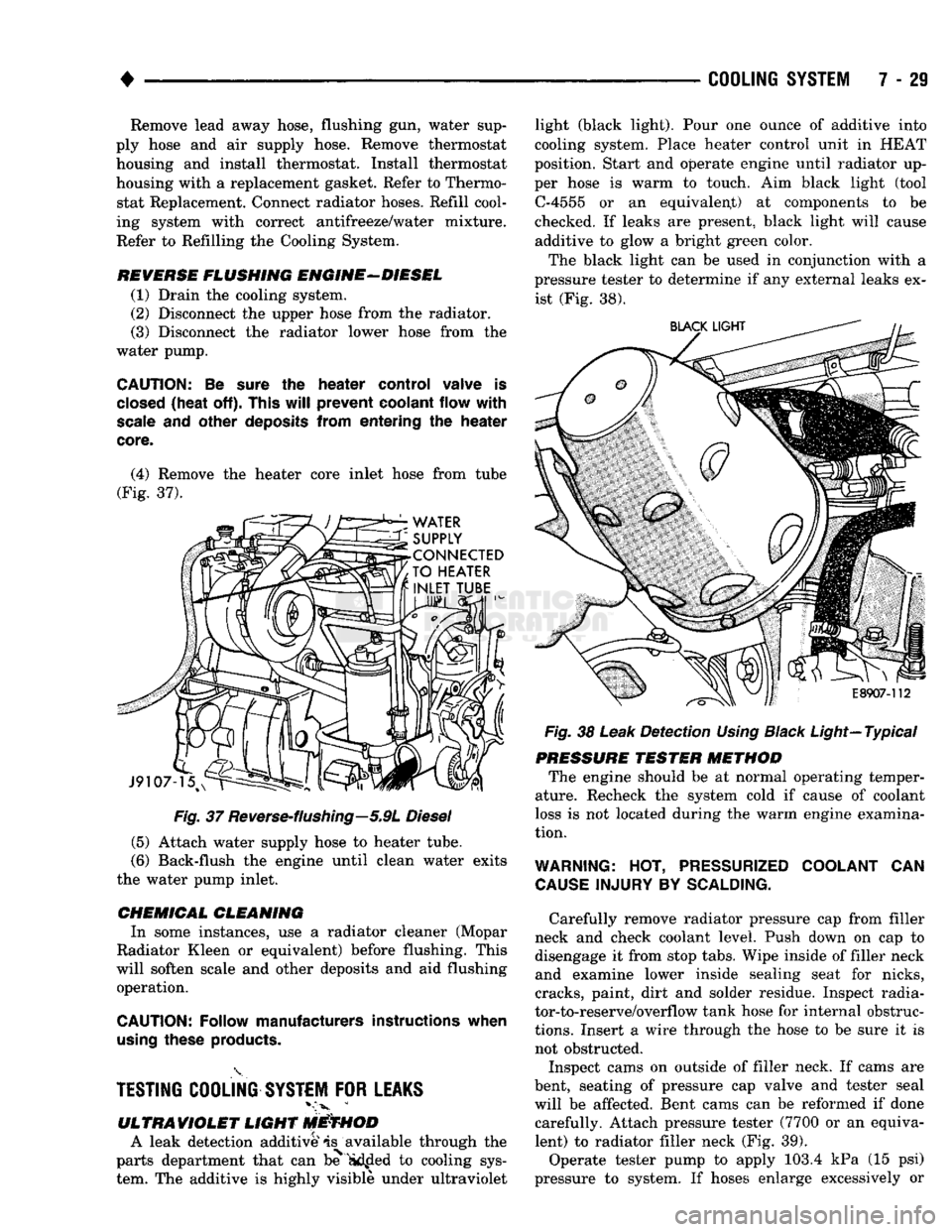
+
Fig.
37
Reverse-flushing—5.9L
Diesel
(5) Attach water supply hose to heater tube.
(6) Back-flush the engine until clean water exits
the water pump inlet.
CHEMICAL
CLEANING
In some instances, use a radiator cleaner (Mopar
Radiator Kleen or equivalent) before flushing. This
will soften scale and other deposits and aid flushing operation.
CAUTION;
Follow manufacturers instructions when
using
these
products.
TESTING
COOLING
SYSTEM
FOR
LEAKS
ULTRAVIOLET
LIGHT
METHOD
A leak detection additive is available through the
parts department that can be Sidfled to cooling sys
tem. The additive is highly visible under ultraviolet
COOLING
SYSTEM
7 - 29
Fig.
38
Leak
Detection
Using
Black
Light—Typical
PRESSURE
TESTER
METHOD
The engine should be at normal operating temper
ature. Recheck the system cold if cause of coolant
loss is not located during the warm engine examina
tion.
WARNING:
HOT,
PRESSURIZED
COOLANT
CAN
CAUSE
INJURY
BY
SCALDING.
Carefully remove radiator pressure cap from filler
neck and check coolant level. Push down on cap to
disengage it from stop tabs. Wipe inside of filler neck and examine lower inside sealing seat for nicks,
cracks, paint, dirt and solder residue. Inspect radia
tor-to-reserve/overflow tank hose for internal obstruc
tions.
Insert a wire through the hose to be sure it is
not obstructed.
Inspect cams on outside of filler neck. If cams are
bent, seating of pressure cap valve and tester seal
will be affected. Bent cams can be reformed if done carefully. Attach pressure tester (7700 or an equivalent) to radiator filler neck (Fig. 39).
Operate tester pump to apply 103.4 kPa (15 psi)
pressure to system. If hoses enlarge excessively or
Remove lead away hose, flushing gun, water sup
ply hose and air supply hose. Remove thermostat housing and install thermostat. Install thermostat
housing with a replacement gasket. Refer to Thermo stat Replacement. Connect radiator hoses. Refill cool
ing system with correct antifreeze/water mixture.
Refer to Refilling the Cooling System.
REVERSE
FLUSHING
ENGINE-DIESEL
(1) Drain the cooling system. (2) Disconnect the upper hose from the radiator.
(3) Disconnect the radiator lower hose from the
water pump.
CAUTION;
Be
sure
the
heater
control valve is
closed
(heat
off).
This
will
prevent coolant flow
with
scale
and other
deposits
from entering the
heater
core.
(4) Remove the heater core inlet hose from tube
(Fig. 37). light (black light). Pour one ounce of additive into
cooling system. Place heater control unit in HEAT
position. Start and operate engine until radiator up
per hose is warm to touch. Aim black light (tool C-4555 or an equivalent) at components to be
checked. If leaks are present, black light will cause additive to glow a bright green color.
The black light can be used in conjunction with a
pressure tester to determine if any external leaks ex ist (Fig. 38).