DODGE TRUCK 1993 Service Repair Manual
Manufacturer: DODGE, Model Year: 1993, Model line: TRUCK, Model: DODGE TRUCK 1993Pages: 1502, PDF Size: 80.97 MB
Page 301 of 1502
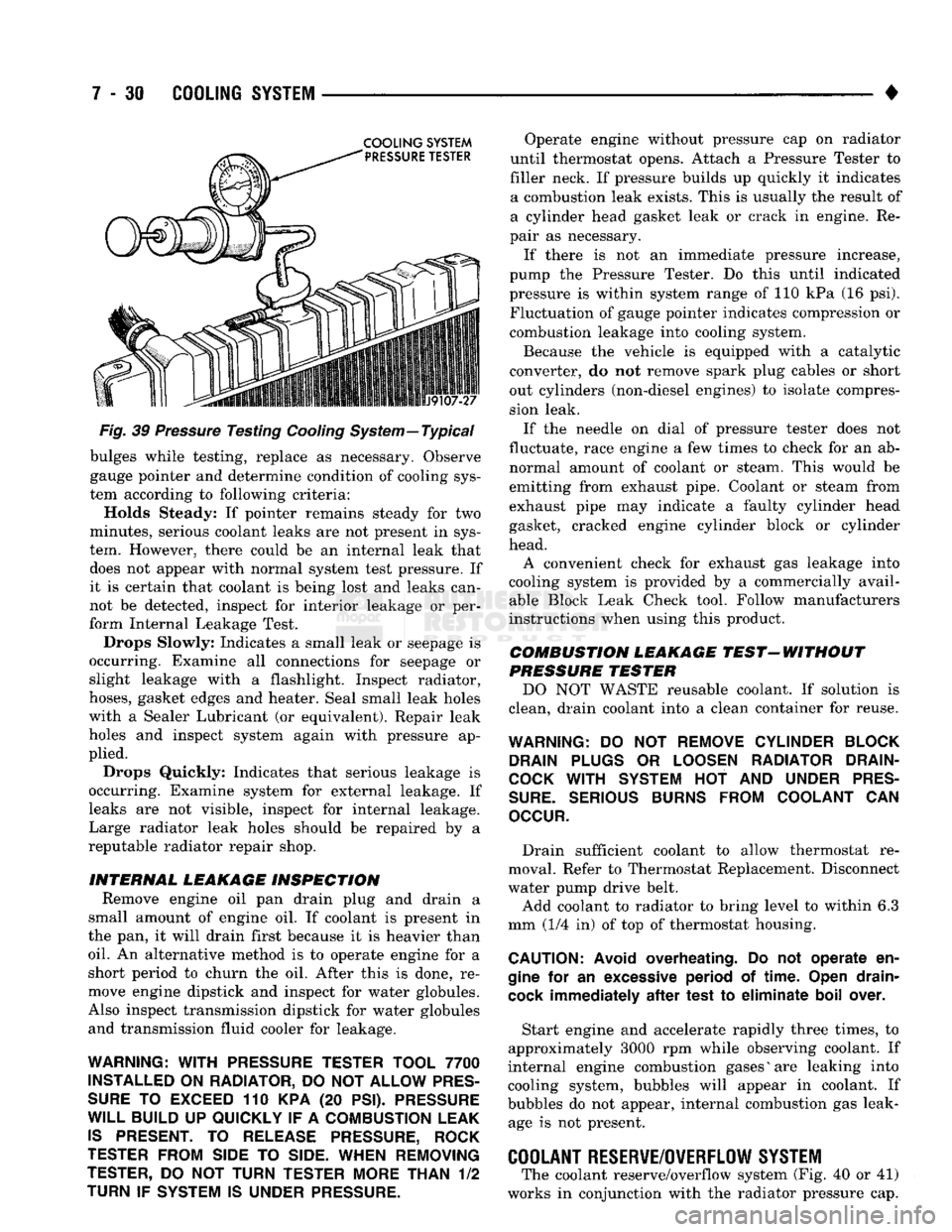
7 - 30
COOLING
SYSTEM
•
COOLING
SYSTEM
Fig.
39
Pressure
Testing
Cooling
System—Typical bulges while testing, replace as necessary. Observe
gauge pointer and determine condition of cooling sys
tem according to following criteria:
Holds Steady: If pointer remains steady for two
minutes, serious coolant leaks are not present in sys
tem. However, there could be an internal leak that does not appear with normal system test pressure. If
it is certain that coolant is being lost and leaks can
not be detected, inspect for interior leakage or per
form Internal Leakage Test.
Drops Slowly: Indicates a small leak or seepage is
occurring. Examine all connections for seepage or
slight leakage with a flashlight. Inspect radiator,
hoses,
gasket edges and heater. Seal small leak holes
with a Sealer Lubricant (or equivalent). Repair leak
holes and inspect system again with pressure ap
plied.
Drops Quickly: Indicates that serious leakage is
occurring. Examine system for external leakage. If
leaks are not visible, inspect for internal leakage.
Large radiator leak holes should be repaired by a
reputable radiator repair shop.
INTERNAL LEAKAGE INSPECTION Remove engine oil pan drain plug and drain a
small amount of engine oil. If coolant is present in
the pan, it will drain first because it is heavier than
oil.
An alternative method is to operate engine for a
short period to churn the oil. After this is done, re
move engine dipstick and inspect for water globules.
Also inspect transmission dipstick for water globules and transmission fluid cooler for leakage.
WARNING:
WITH
PRESSURE TESTER TOOL
7700
INSTALLED
ON
RADIATOR,
DO
NOT ALLOW
PRES
SURE
TO
EXCEED
110 KPA (20
PSI). PRESSURE
WILL
BUILD
UP
QUICKLY
IF A
COMBUSTION LEAK
IS
PRESENT.
TO
RELEASE
PRESSURE,
ROCK
TESTER
FROM SIDE
TO
SIDE. WHEN REMOVING
TESTER,
DO NOT
TURN TESTER MORE THAN
1/2
TURN
IF
SYSTEM
IS
UNDER
PRESSURE.
Operate engine without pressure cap on radiator
until thermostat opens. Attach a Pressure Tester to
filler neck. If pressure builds up quickly it indicates a combustion leak exists. This is usually the result of
a cylinder head gasket leak or crack in engine. Re
pair as necessary.
If there is not an immediate pressure increase,
pump the Pressure Tester. Do this until indicated
pressure is within system range of 110 kPa (16 psi). Fluctuation of gauge pointer indicates compression or
combustion leakage into cooling system.
Because the vehicle is equipped with a catalytic
converter, do not remove spark plug cables or short
out cylinders (non-diesel engines) to isolate compres
sion leak.
If the needle on dial of pressure tester does not
fluctuate, race engine a few times to check for an ab normal amount of coolant or steam. This would be
emitting from exhaust pipe. Coolant or steam from
exhaust pipe may indicate a faulty cylinder head
gasket, cracked engine cylinder block or cylinder
head. A convenient check for exhaust gas leakage into
cooling system is provided by a commercially avail able Block Leak Check tool. Follow manufacturers
instructions when using this product.
COMBUSTION LEAKAGE TEST-WITHOUT
PRESSURE TESTER DO NOT WASTE reusable coolant. If solution is
clean, drain coolant into a clean container for reuse.
WARNING:
DO NOT
REMOVE CYLINDER BLOCK DRAIN PLUGS
OR
LOOSEN RADIATOR DRAIN-
COCK
WITH
SYSTEM
HOT AND
UNDER PRES
SURE.
SERIOUS BURNS FROM COOLANT
CAN
OCCUR.
Drain sufficient coolant to allow thermostat re
moval. Refer to Thermostat Replacement. Disconnect
water pump drive belt. Add coolant to radiator to bring level to within 6.3
mm (1/4 in) of top of thermostat housing.
CAUTION:
Avoid
overheating.
Do not
operate
en
gine
for an
excessive
period
of
time.
Open
drain-
cock
immediately
after
test
to
eliminate
boil
over.
Start engine and accelerate rapidly three times, to
approximately 3000 rpm while observing coolant. If
internal engine combustion gases% are leaking into
cooling system, bubbles will appear in coolant. If
bubbles do not appear, internal combustion gas leak age is not present.
COOLANT
RESERVE/0WERFL0W
SYSTEM
The coolant reserve/overflow system (Fig. 40 or 41)
works in conjunction with the radiator pressure cap.
Page 302 of 1502
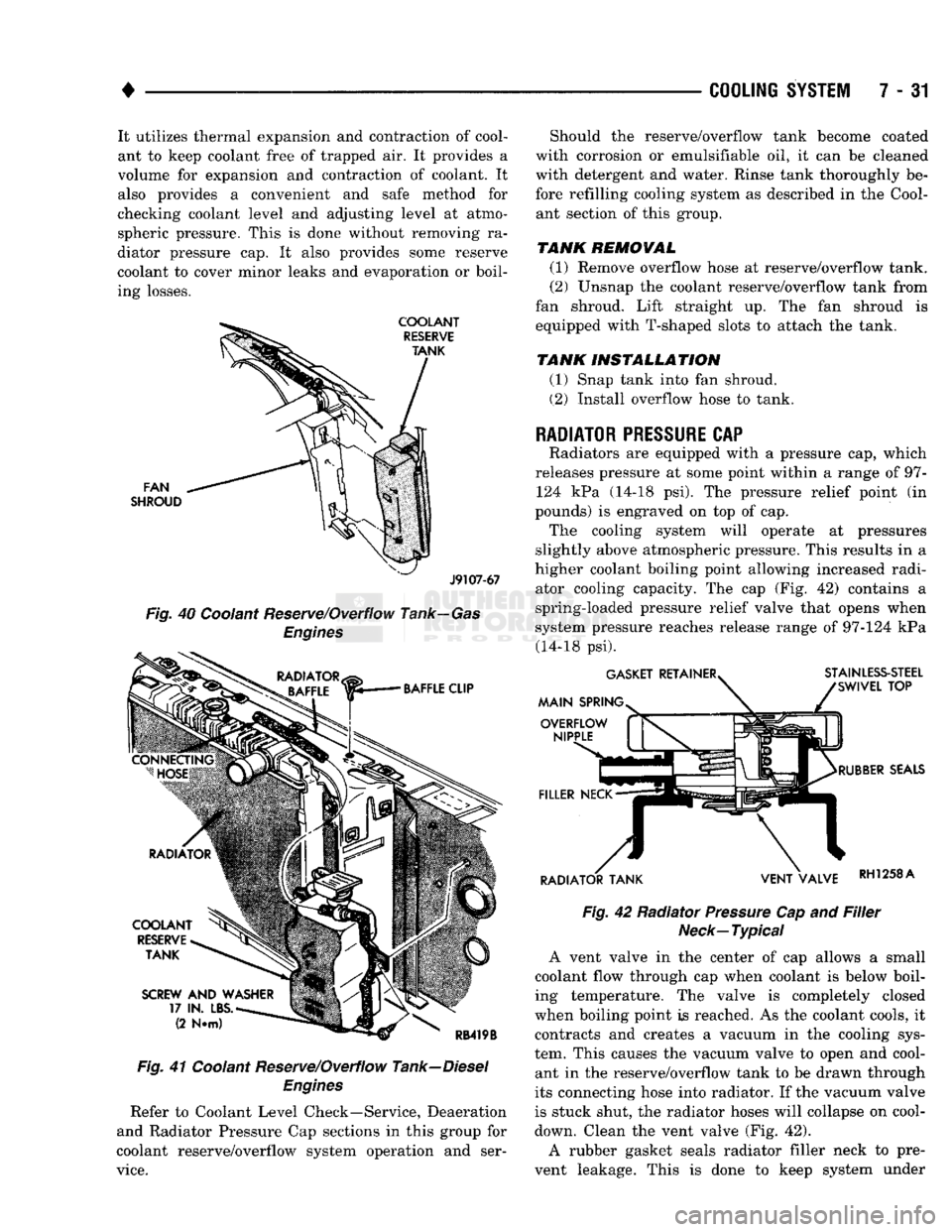
•
COOLING
SYSTEM
7 - 31 It utilizes thermal expansion and contraction of cool
ant to keep coolant free of trapped air. It provides a
volume for expansion and contraction of coolant. It
also provides a convenient and safe method for
checking coolant level and adjusting level at atmo
spheric pressure. This is done without removing ra
diator pressure cap. It also provides some reserve
coolant to cover minor leaks and evaporation or boil
ing losses.
FAN
SHROUD
J9107-67
Fig.
40 Coolant Reserve/Overflow Tank—Gas
Engines
Fig.
41 Coolant Reserve/Overflow Tank—Diesel
Engines
Refer to Coolant Level Check—Service, Deaeration
and Radiator Pressure Cap sections in this group for
coolant reserve/overflow system operation and ser
vice.
Should the reserve/overflow tank become coated
with corrosion or emulsifiable oil, it can be cleaned
with detergent and water. Rinse tank thoroughly be
fore refilling cooling system as described in the Cool ant section of this group.
TANK REMOVAL
(1) Remove overflow hose at reserve/overflow tank.
(2) Unsnap the coolant reserve/overflow tank from
fan shroud. Lift straight up. The fan shroud is
equipped with T-shaped slots to attach the tank.
TANK INSTALLATION
(1) Snap tank into fan shroud.
(2) Install overflow hose to tank.
RADIATOR
PRESSURE
CAP
Radiators are equipped with a pressure cap, which
releases pressure at some point within a range of 97- 124 kPa (14-18 psi). The pressure relief point (in
pounds) is engraved on top of cap. The cooling system will operate at pressures
slightly above atmospheric pressure. This results in a
higher coolant boiling point allowing increased radi ator cooling capacity. The cap (Fig. 42) contains a
spring-loaded pressure relief valve that opens when
system pressure reaches release range of 97-124 kPa (14-18 psi).
Fig.
42 Radiator
Pressure
Cap and
Filler
Neck—Typical
A vent valve in the center of cap allows a small
coolant flow through cap when coolant is below boil
ing temperature. The valve is completely closed
when boiling point is reached. As the coolant cools, it contracts and creates a vacuum in the cooling sys
tem. This causes the vacuum valve to open and cool ant in the reserve/overflow tank to be drawn through
its connecting hose into radiator. If the vacuum valve
is stuck shut, the radiator hoses will collapse on cool-
down. Clean the vent valve (Fig. 42).
A rubber gasket seals radiator filler neck to pre
vent leakage. This is done to keep system under
Page 303 of 1502
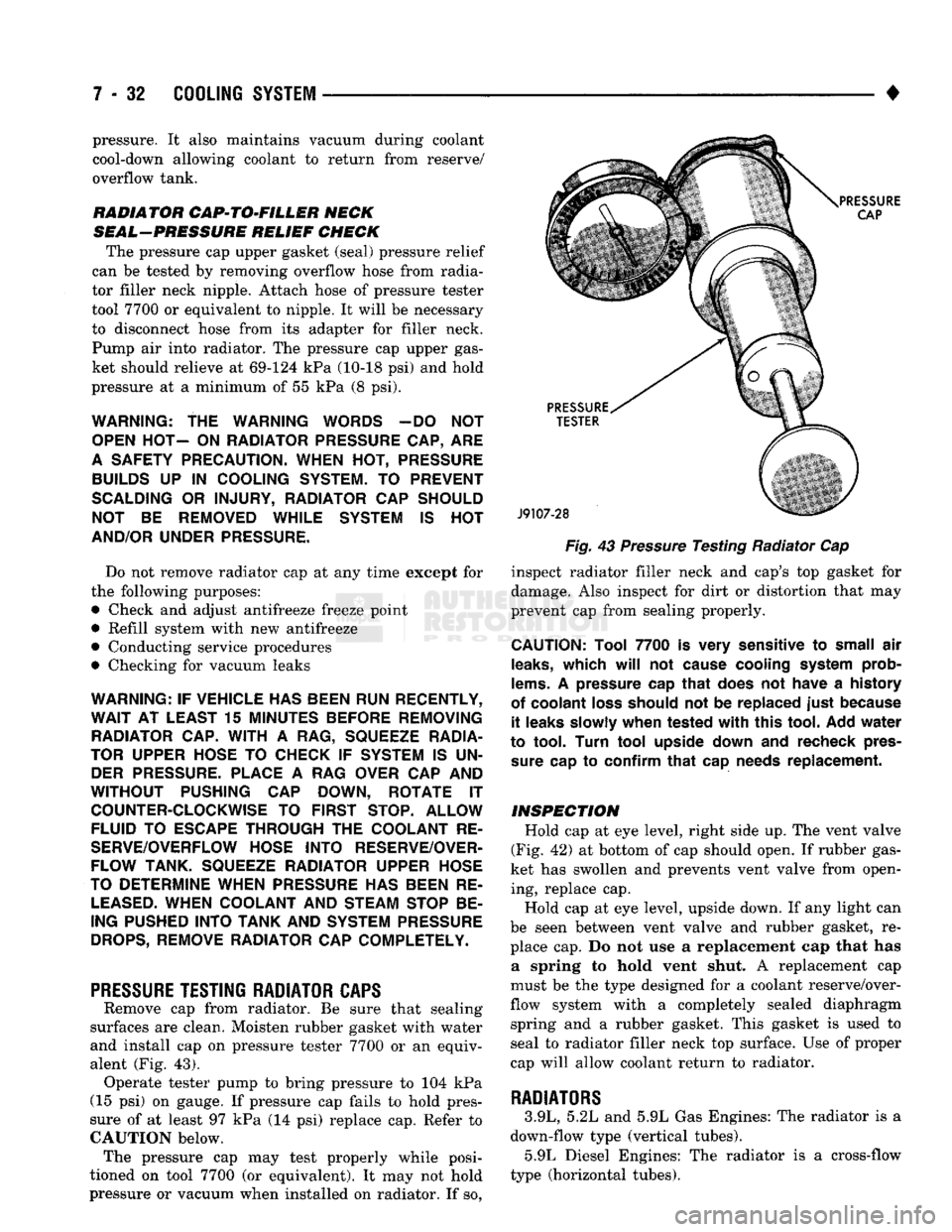
7 - 32
COOLING
SYSTEM
• pressure. It also maintains vacuum during coolant
cool-down allowing coolant to return from reserve/
overflow tank.
RADIATOR
CAP-TO-FILLER
NECK
SEAL-PRESSURE RELIEF CHECK The pressure cap upper gasket (seal) pressure relief
can be tested by removing overflow hose from radia
tor filler neck nipple. Attach hose of pressure tester
tool 7700 or equivalent to nipple. It will be necessary
to disconnect hose from its adapter for filler neck.
Pump air into radiator. The pressure cap upper gas
ket should relieve at 69-124 kPa (10-18 psi) and hold
pressure at a minimum of 55 kPa (8 psi).
WARNING;
THE
WARNING WORDS
-DO NOT
OPEN HOT—
ON
RADIATOR PRESSURE CAP, ARE
A SAFETY PRECAUTION. WHEN
HOT,
PRESSURE BUILDS
UP IN
COOLING SYSTEM.
TO
PREVENT
SCALDING
OR
INJURY, RADIATOR
CAP
SHOULD NOT
BE
REMOVED WHILE SYSTEM
IS HOT
AND/OR UNDER
PRESSURE.
Do not remove radiator cap at any time except for
the following purposes: • Check and adjust antifreeze freeze point
• Refill system with new antifreeze
• Conducting service procedures
• Checking for vacuum leaks
WARNING;
IF
VEHICLE HAS BEEN RUN RECENTLY,
WAIT
AT
LEAST
15
MINUTES BEFORE REMOVING
RADIATOR CAP.
WITH
A
RAG, SQUEEZE RADIA
TOR UPPER HOSE
TO
CHECK
IF
SYSTEM
IS UN
DER
PRESSURE.
PLACE
A RAG
OVER
CAP AND
WITHOUT
PUSHING
CAP
DOWN, ROTATE
IT
COUNTER-CLOCKWISE
TO
FIRST STOP. ALLOW FLUID
TO
ESCAPE THROUGH
THE
COOLANT RE
SERVE/OVERFLOW HOSE
INTO
RESERVE/OVER FLOW TANK. SQUEEZE RADIATOR UPPER HOSE
TO DETERMINE WHEN PRESSURE HAS BEEN RE
LEASED.
WHEN COOLANT AND STEAM STOP BE
ING PUSHED
INTO
TANK AND SYSTEM PRESSURE
DROPS,
REMOVE RADIATOR CAP COMPLETELY.
PRESSURE
TESTING
RADIATOR
CAPS
Remove cap from radiator. Be sure that sealing
surfaces are clean. Moisten rubber gasket with water
and install cap on pressure tester 7700 or an equiv
alent (Fig. 43). Operate tester pump to bring pressure to 104 kPa
(15 psi) on gauge. If pressure cap fails to hold pres
sure of at least 97 kPa (14 psi) replace cap. Refer to
CAUTION below. The pressure cap may test properly while posi
tioned on tool 7700 (or equivalent). It may not hold
pressure or vacuum when installed on radiator. If so,
Fig.
43
Pressure
Testing Radiator Cap
inspect radiator filler neck and cap's top gasket for
damage. Also inspect for dirt or distortion that may
prevent cap from sealing properly.
CAUTION:
Tool
7700
is
very
sensitive
to
small
air
leaks,
which
will
not
cause
cooling
system
prob
lems.
A
pressure
cap
that
does
not
have
a
history
of
coolant
loss
should
not be
replaced
just
because
it
leaks
slowly
when
tested
with
this
tool.
Add
water
to
tool.
Turn
tool
upside
down
and
recheck
pres
sure
cap to
confirm
that
cap
needs
replacement.
INSPECTION
Hold cap at eye level, right side up. The vent valve
(Fig. 42) at bottom of cap should open. If rubber gas
ket has swollen and prevents vent valve from open ing, replace cap.
Hold cap at eye level, upside down. If any light can
be seen between vent valve and rubber gasket, re place cap. Do not use a replacement cap that has a spring to hold vent shut. A replacement cap
must be the type designed for a coolant reserve/over
flow system with a completely sealed diaphragm spring and a rubber gasket. This gasket is used to
seal to radiator filler neck top surface. Use of proper
cap will allow coolant return to radiator.
RADIATORS
3.9L, 5.2L and 5.9L Gas Engines: The radiator is a
down-flow type (vertical tubes). 5.9L Diesel Engines: The radiator is a cross-flow
type (horizontal tubes).
Page 304 of 1502
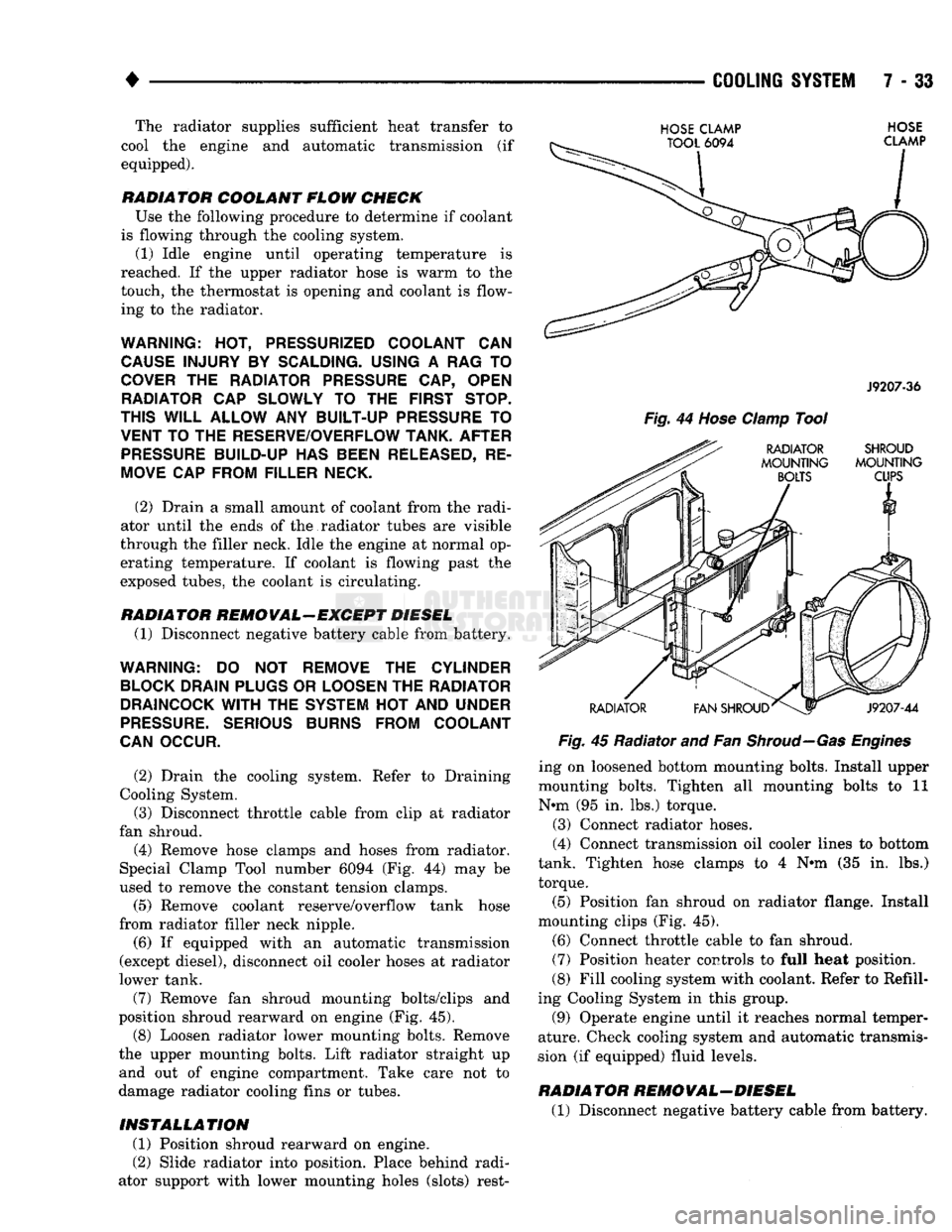
•
COOLING
SYSTEM
7 - 33 The radiator supplies sufficient heat transfer to
cool the engine and automatic transmission (if equipped).
RADIATOR COOLANT FLOW CHECK
Use the following procedure to determine if coolant
is flowing through the cooling system.
(1) Idle engine until operating temperature is
reached. If the upper radiator hose is warm to the
touch, the thermostat is opening and coolant is flow ing to the radiator.
WARNING:
HOT,
PRESSURIZED COOLANT
CAN
CAUSE
INJURY
BY
SCALDING. USING
A
RAG
TO
COVER
THE
RADIATOR
PRESSURE
CAP,
OPEN RADIATOR
CAP
SLOWLY
TO THE
FIRST STOP.
THIS
WILL
ALLOW
ANY
BUILT-UP
PRESSURE
TO
VENT
TO
THE
RESERVE/OVERFLOW TANK. AFTER
PRESSURE
BUILD-UP
HAS
BEEN RELEASED,
RE
MOVE
CAP
FROM FILLER NECK.
(2) Drain a small amount of coolant from the radi
ator until the ends of the radiator tubes are visible
through the filler neck. Idle the engine at normal op
erating temperature. If coolant is flowing past the
exposed tubes, the coolant is circulating.
RADIATOR REMOVAL-EXCEPT DIESEL
(1) Disconnect negative battery cable from battery.
WARNING;
DO NOT
REMOVE
THE
CYLINDER BLOCK DRAIN PLUGS
OR
LOOSEN
THE
RADIATOR
DRAINCOCK
WITH
THE
SYSTEM
HOT AND
UNDER
PRESSURE.
SERIOUS BURNS FROM COOLANT
CAN OCCUR.
(2) Drain the cooling system. Refer to Draining
Cooling System.
(3) Disconnect throttle cable from clip at radiator
fan shroud. (4) Remove hose clamps and hoses from radiator.
Special Clamp Tool number 6094 (Fig. 44) may be
used to remove the constant tension clamps.
(5) Remove coolant reserve/overflow tank hose
from radiator filler neck nipple.
(6) If equipped with an automatic transmission
(except diesel), disconnect oil cooler hoses at radiator
lower tank.
(7) Remove fan shroud mounting bolts/clips and
position shroud rearward on engine (Fig. 45). (8) Loosen radiator lower mounting bolts. Remove
the upper mounting bolts. Lift radiator straight up and out of engine compartment. Take care not to
damage radiator cooling fins or tubes.
INSTALLATION
(1) Position shroud rearward on engine.
(2) Slide radiator into position. Place behind radi
ator support with lower mounting holes (slots) rest-
HOSE
CLAMP
TOOL
6094
HOSE
CLAMP
J9207-36
Fig.
44
Hose
Clamp
Tool
RADIATOR SHROUD
MOUNTING MOUNTING
BOLTS
CUPS
RADIATOR
V1
FAN SHROUD^
J9207-44
Fig.
45 Radiator and Fan
Shroud—Gas Engines
ing on loosened bottom mounting bolts. Install upper
mounting bolts. Tighten all mounting bolts to 11
N*m (95 in. lbs.) torque.
(3) Connect radiator hoses.
(4) Connect transmission oil cooler lines to bottom
tank. Tighten hose clamps to 4 N#m (35 in. lbs.)
torque.
(5) Position fan shroud on radiator flange. Install
mounting clips (Fig. 45).
(6) Connect throttle cable to fan shroud.
(7) Position heater controls to full heat position.
(8) Fill cooling system with coolant. Refer to Refill
ing Cooling System in this group.
(9) Operate engine until it reaches normal temper
ature. Check cooling system and automatic transmis
sion (if equipped) fluid levels.
RADIATOR REMOVAL-DIESEL
(1) Disconnect negative battery cable from battery.
Page 305 of 1502
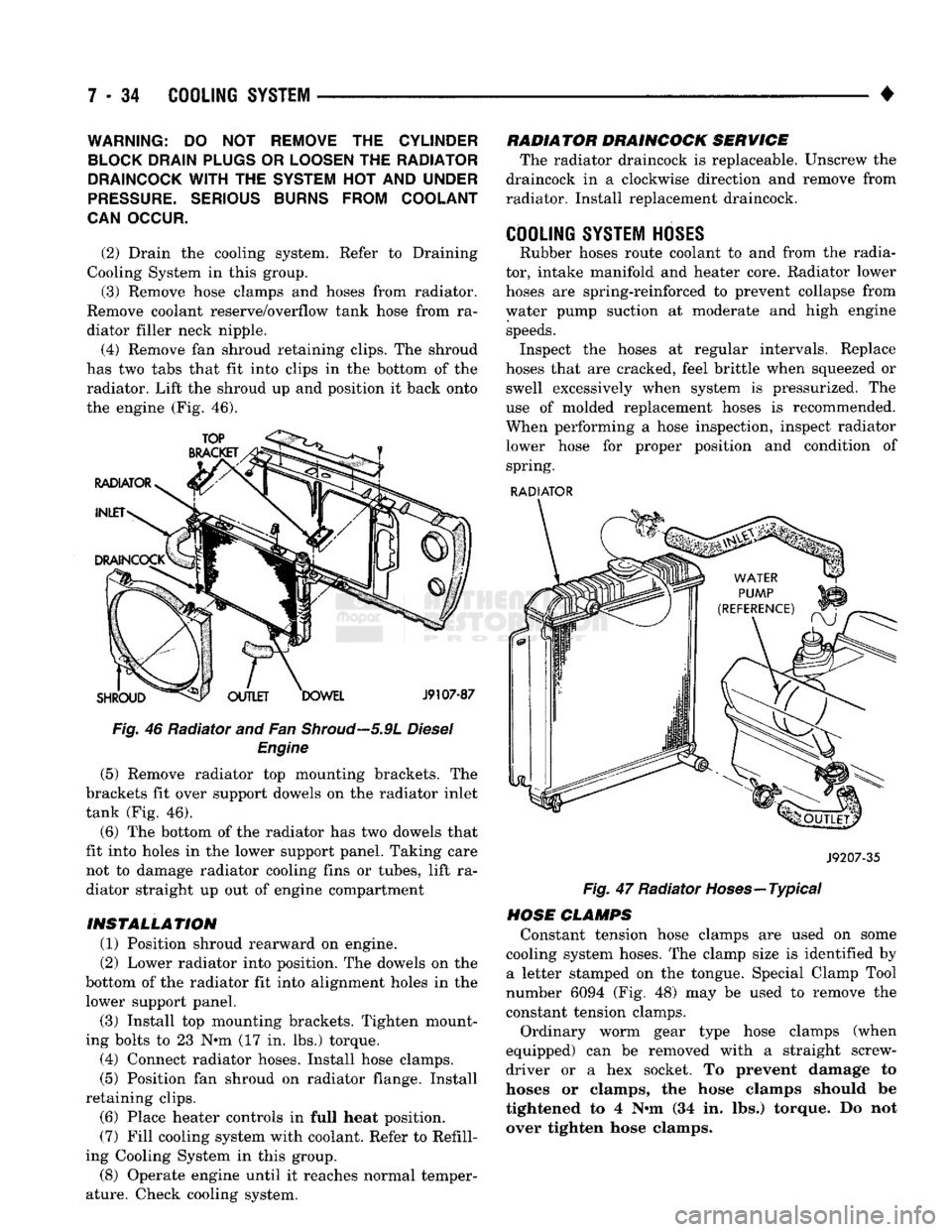
7 - 34
COOLING SYSTEM
•
WARNING;
DO NOT
REMOVE
THE
CYLINDER
BLOCK DRAIN PLUGS
OR
LOOSEN
THE
RADIATOR
DRAINCOCK
WITH
THE
SYSTEM
HOT AND
UNDER
PRESSURE.
SERIOUS BURNS FROM COOLANT
CAN OCCUR.
(2) Drain the cooling system. Refer to Draining
Cooling System in this group. (3) Remove hose clamps and hoses from radiator.
Remove coolant reserve/overflow tank hose from ra diator filler neck nipple.
(4) Remove fan shroud retaining clips. The shroud
has two tabs that fit into clips in the bottom of the radiator. Lift the shroud up and position it back onto
the engine (Fig. 46).
Fig. 46 Radiator and Fan
Shroud—5.9L
Diesel Engine
(5) Remove radiator top mounting brackets. The
brackets fit over support dowels on the radiator inlet
tank (Fig. 46).
(6) The bottom of the radiator has two dowels that
fit into holes in the lower support panel. Taking care not to damage radiator cooling fins or tubes, lift ra
diator straight up out of engine compartment
INSTALLATION (1) Position shroud rearward on engine.
(2) Lower radiator into position. The dowels on the
bottom of the radiator fit into alignment holes in the lower support panel.
(3) Install top mounting brackets. Tighten mount
ing bolts to 23 N*m (17 in. lbs.) torque. (4) Connect radiator hoses. Install hose clamps.
(5) Position fan shroud on radiator flange. Install
retaining clips. (6) Place heater controls in full heat position.
(7) Fill cooling system with coolant. Refer to Refill
ing Cooling System in this group.
(8) Operate engine until it reaches normal temper
ature. Check cooling system. RADIATOR DRAINCOCK SERVICE
The radiator draincock is replaceable. Unscrew the
draincock in a clockwise direction and remove from
radiator. Install replacement draincock.
COOLING SYSTEM HOSES
Rubber hoses route coolant to and from the radia
tor, intake manifold and heater core. Radiator lower
hoses are spring-reinforced to prevent collapse from
water pump suction at moderate and high engine speeds. Inspect the hoses at regular intervals. Replace
hoses that are cracked, feel brittle when squeezed or swell excessively when system is pressurized. The
use of molded replacement hoses is recommended.
When performing a hose inspection, inspect radiator lower hose for proper position and condition of spring.
RADIATOR
J9207-35
Fig. 47 Radiator Hoses—Typical
HOSE CLAMPS Constant tension hose clamps are used on some
cooling system hoses. The clamp size is identified by a letter stamped on the tongue. Special Clamp Tool
number 6094 (Fig. 48) may be used to remove the
constant tension clamps.
Ordinary worm gear type hose clamps (when
equipped) can be removed with a straight screw
driver or a hex socket. To prevent damage to
hoses or clamps, the hose clamps should be
tightened to 4 N«m (34 in. lbs.) torque. Do not
over tighten hose clamps.
Page 306 of 1502
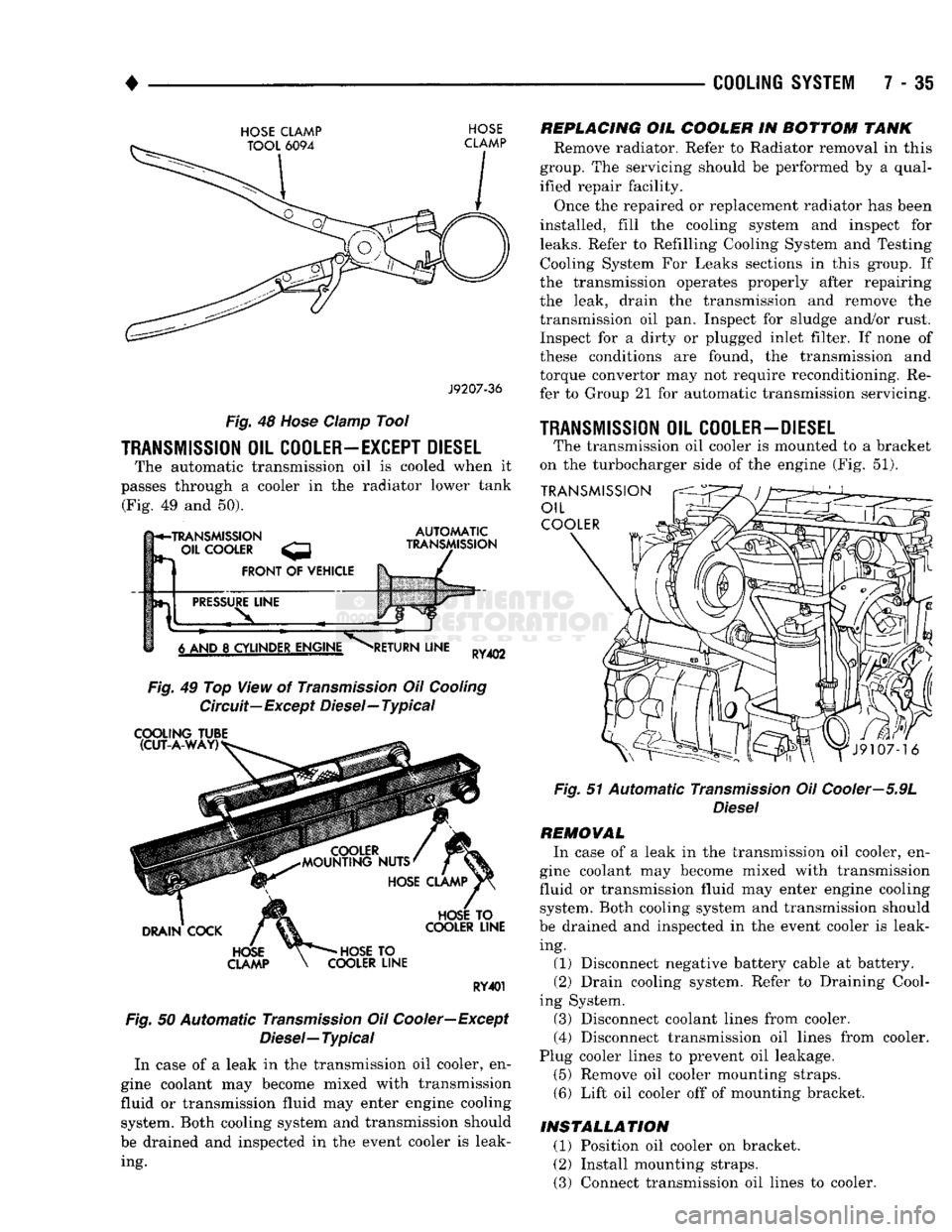
•
COOLING
SYSTEM
7 - 35
HOSE
CLAMP TOOL
6094
HOSE
CLAMP
J9207-36
Fig.
48
Hose
damp Tool
TRANSMISSION
OIL
COOLER—EXCEPT DIESEL
The automatic transmission oil is cooled when it
passes through a cooler in the radiator lower tank (Fig. 49 and 50).
h*-TRANSMISSION
- OIL
COOLER
FRONT
OF
VEHICLE
AUTOMATIC
TRANSMISSION
PRESSURE
LINE
6 AND
8
CYLINDER ENGINE
RETURN
LINE
RY402
Fig.
49 Top View of
Transmission
Oil
Cooling
Circuit—Except Diesel—Typical
COOLING
TUBE (CUT-A-WAY)
DRAIN
COCK
HOSE
CLAMP
HOSE
TO
COOLER
LINE
HOSE
TO
COOLER
LINE
RY401
Fig.
50 Automatic
Transmission
Oil Cooler—Except
Diesel—
Typical
In case of a leak in the transmission oil cooler, en
gine coolant may become mixed with transmission
fluid or transmission fluid may enter engine cooling system. Both cooling system and transmission should
be drained and inspected in the event cooler is leak ing.
REPLACING
OIL
COOLER
IN
BOTTOM
TANK
Remove radiator. Refer to Radiator removal in this
group. The servicing should be performed by a qual
ified repair facility.
Once the repaired or replacement radiator has been
installed, fill the cooling system and inspect for
leaks.
Refer to Refilling Cooling System and Testing Cooling System For Leaks sections in this group. If
the transmission operates properly after repairing
the leak, drain the transmission and remove the
transmission oil pan. Inspect for sludge and/or rust. Inspect for a dirty or plugged inlet filter. If none of
these conditions are found, the transmission and
torque convertor may not require reconditioning. Re
fer to Group 21 for automatic transmission servicing.
1RANSMISSI0N
OIL
COOLER-DIESEL
The transmission oil cooler is mounted to a bracket
on the turbocharger side of the engine (Fig. 51).
TRANSMISSION
OIL
COOLER
Fig.
51 Automatic
Transmission
Oil Cooler—5.9L
Diesel
REMOVAL
In case of a leak in the transmission oil cooler, en
gine coolant may become mixed with transmission
fluid or transmission fluid may enter engine cooling system. Both cooling system and transmission should
be drained and inspected in the event cooler is leak ing. (1) Disconnect negative battery cable at battery.
(2) Drain cooling system. Refer to Draining Cool
ing System. (3) Disconnect coolant lines from cooler.
(4) Disconnect transmission oil lines from cooler.
Plug cooler lines to prevent oil leakage. (5) Remove oil cooler mounting straps.
(6) Lift oil cooler off of mounting bracket.
INSTALLATION
(1) Position oil cooler on bracket.
(2) Install mounting straps.
(3) Connect transmission oil lines to cooler.
Page 307 of 1502
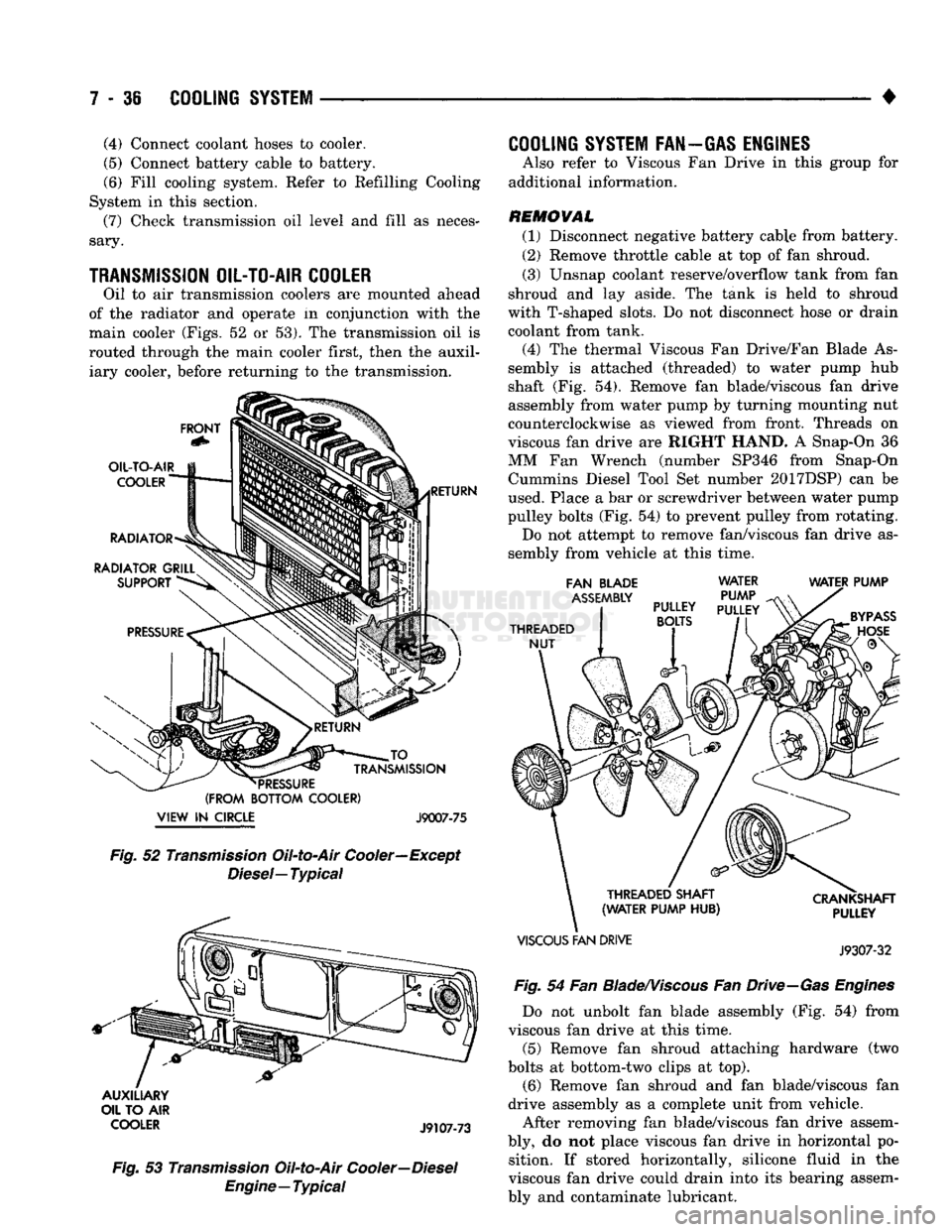
7 - 36
COOLING
SYSTEM
• (4) Connect coolant hoses to cooler.
(5)
Connect battery cable to battery.
(6)
Fill cooling system. Refer to Refilling Cooling
System in this section. (7) Check transmission oil level and fill as neces
sary.
TRANSMISSION
OIL/TO-AIR
COOLER
Oil to air transmission coolers are mounted ahead
of the radiator and operate in conjunction with the
main cooler (Figs, 52 or 53). The transmission oil is
routed through the main cooler first, then the auxil iary cooler, before returning to the transmission.
FRONT
OIL-TO-AIR
COOLER
RADIATOR
RADIATOR GRILL SUPPORT RETURN JO
_
TRANSMISSION
*
PRESSURE
(FROM BOTTOM COOLER)
VIEW
IN
CIRCLE J9007-75 Fig.
52
Transmission
Oil-to-Air Cooler—Except
Diesel—
Typical
AUXILIARY
OIL TO AIR
COOLER
J9107-73
Fig.
53
Transmission
Oil-to-Air
Cooler—Diesel
Engine—Typical
COOLING
SYSTEM FAN—GAS ENGINES
Also refer to Viscous Fan Drive in this group for
additional information.
REMOVAL (1) Disconnect negative battery cable from battery.
(2) Remove throttle cable at top of fan shroud.
(3) Unsnap coolant reserve/overflow tank from fan
shroud and lay aside. The tank is held to shroud
with T-shaped slots. Do not disconnect hose or drain
coolant from tank.
(4) The thermal Viscous Fan Drive/Fan Blade As
sembly is attached (threaded) to water pump hub
shaft (Fig. 54). Remove fan blade/viscous fan drive
assembly from water pump by turning mounting nut
counterclockwise as viewed from front. Threads on
viscous fan drive are RIGHT HAND. A Snap-On 36
MM Fan Wrench (number SP346 from Snap-On Cummins Diesel Tool Set number 2017DSP) can be
used. Place a bar or screwdriver between water pump
pulley bolts (Fig. 54) to prevent pulley from rotating. Do not attempt to remove fan/viscous fan drive as
sembly from vehicle at this time.
FAN BLADE
ASSEMBLY
THREADED NUT WATER
PUMP
PULLEY
PULLEY
BOLTS
WATER PUMP
THREADED SHAFT
(WATER PUMP HUB)
VISCOUS
FAN DRIVE CRANKSHAFT
PULLEY
J9307-32
Fig.
54 Fan
Blade/Viscous
Fan
Drive—Gas
Engines
Do not unbolt fan blade assembly (Fig. 54) from
viscous fan drive at this time.
(5) Remove fan shroud attaching hardware (two
bolts at bottom-two clips at top). (6) Remove fan shroud and fan blade/viscous fan
drive assembly as a complete unit from vehicle.
After removing fan blade/viscous fan drive assem
bly, do not place viscous fan drive in horizontal po sition. If stored horizontally, silicone fluid in the
viscous fan drive could drain into its bearing assem
bly and contaminate lubricant.
Page 308 of 1502
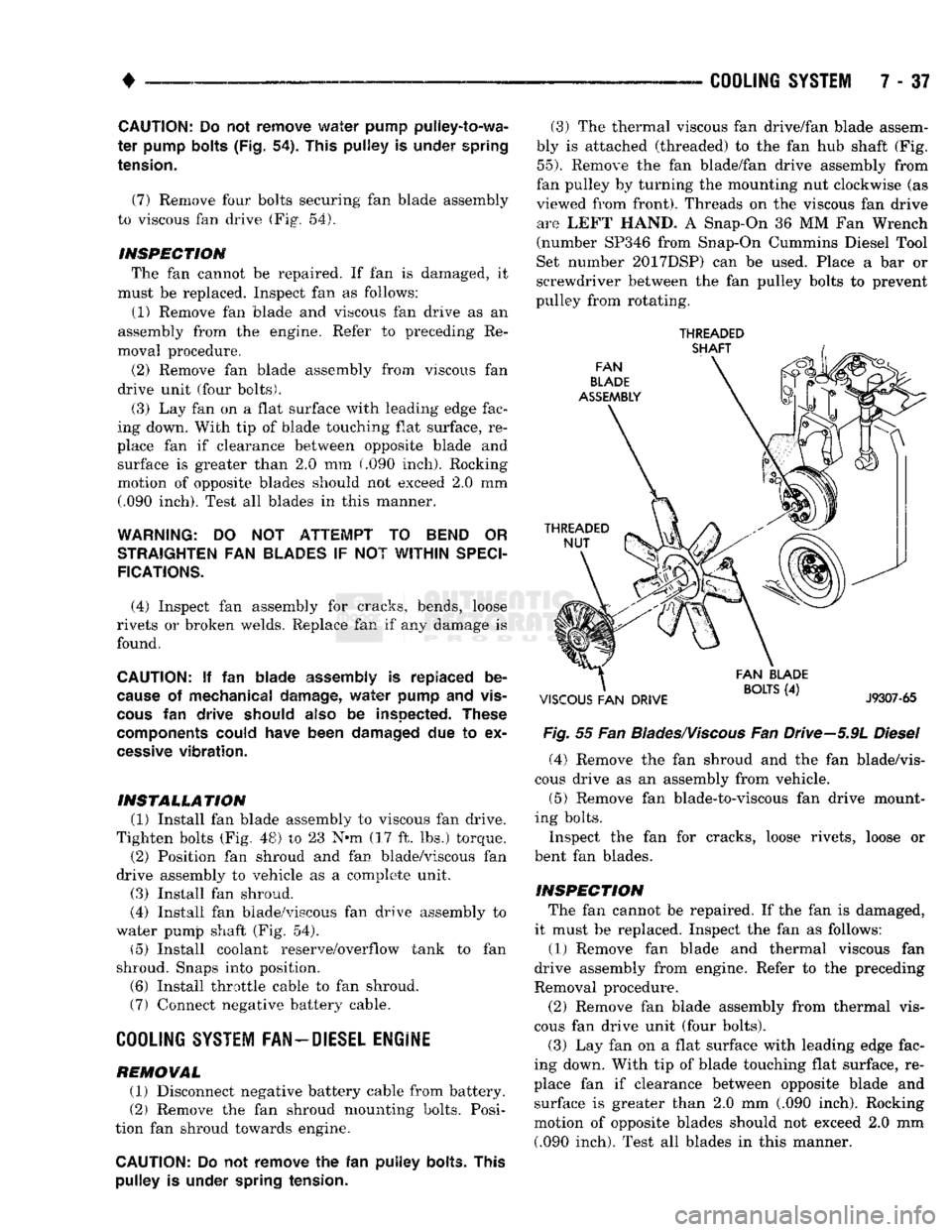
•
COOLING
SYSTEM
7 - 37
CAUTION:
Do not
remove
water
pump pulley-to-wa
ter
pump
bolts
(Fig. 54), This
pulley
is
under spring
tension.
(7) Remove four bolts securing fan blade assembly
to viscous fan drive (Fig. 54).
INSPECTION The fan cannot be repaired. If fan is damaged, it
must be replaced. Inspect fan as follows:
(1) Remove fan blade and viscous fan drive as an
assembly from the engine. Refer to preceding Re
moval procedure.
(2) Remove fan blade assembly from viscous fan
drive unit (four bolts).
(3) Lay fan on a flat surface with leading edge fac
ing down. With tip of blade touching flat surface, re
place fan if clearance between opposite blade and surface is greater than 2.0 mm (.090 inch). Rocking
motion of opposite blades should not exceed 2.0 mm (.090 inch). Test all blades in this manner.
WARNING:
DO NOT
ATTEMPT
TO
BEND
OR
STRAIGHTEN
FAN
BLADES
IF NOT
WITHIN
SPECI
FICATIONS.
(4) Inspect fan assembly for cracks, bends, loose
rivets or broken welds. Replace fan if any damage is
found,
CAUTION:
If fan
blade assembly
is
replaced
be
cause
of
mechanical damage,
water
pump
and
vis
cous
fan
drive should
also
be
inspected. These
components
could have been damaged
due to ex
cessive
vibration.
INSTALLATION (1) Install fan blade assembly to viscous fan drive.
Tighten bolts (Fig. 48) to 23 N*m (17 ft. lbs.) torque. (2) Position fan shroud and fan blade/viscous fan
drive assembly to vehicle as a complete unit.
(3) Install fan shroud.
(4) Install fan blade/viscous fan drive assembly to
water pump shaft (Fig. 54). (5) Install coolant reserve/overflow tank to fan
shroud. Snaps into position.
(6) Install throttle cable to fan shroud.
(7) Connect negative battery cable.
COOLING
SYSTEM
FAN-DIESEL ENGINE
REMOVAL (1) Disconnect negative battery cable from battery.
(2) Remove the fan shroud mounting bolts. Posi
tion fan shroud towards engine.
CAUTION:
Do not
remove
the fan
puHey bolts. This pulley
is
under spring tension.
(3) The thermal viscous fan drive/fan blade assem
bly is attached (threaded) to the fan hub shaft (Fig.
55).
Remove the fan blade/fan drive assembly from
fan pulley by turning the mounting nut clockwise (as
viewed from front). Threads on the viscous fan drive are LEFT HAND. A Snap-On 36 MM Fan Wrench
(number SP346 from Snap-On Cummins Diesel Tool
Set number 2017DSP) can be used. Place a bar or
screwdriver between the fan pulley bolts to prevent
pulley from rotating.
THREADED
Fig.
55 Fan
Blades/Viscous
Fan Drive-5.9L
Diesel
(4) Remove the fan shroud and the fan blade/vis
cous drive as an assembly from vehicle.
(5) Remove fan blade-to-viscous fan drive mount
ing bolts.
Inspect the fan for cracks, loose rivets, loose or
bent fan blades.
INSPECTION The fan cannot be repaired. If the fan is damaged,
it must be replaced. Inspect the fan as follows:
(1) Remove fan blade and thermal viscous fan
drive assembly from engine. Refer to the preceding
Removal procedure.
(2) Remove fan blade assembly from thermal vis
cous fan drive unit (four bolts). (3) Lay fan on a flat surface with leading edge fac
ing down. With tip of blade touching flat surface, re
place fan if clearance between opposite blade and surface is greater than 2.0 mm (.090 inch). Rocking
motion of opposite blades should not exceed 2.0 mm (.090 inch). Test all blades in this manner.
Page 309 of 1502
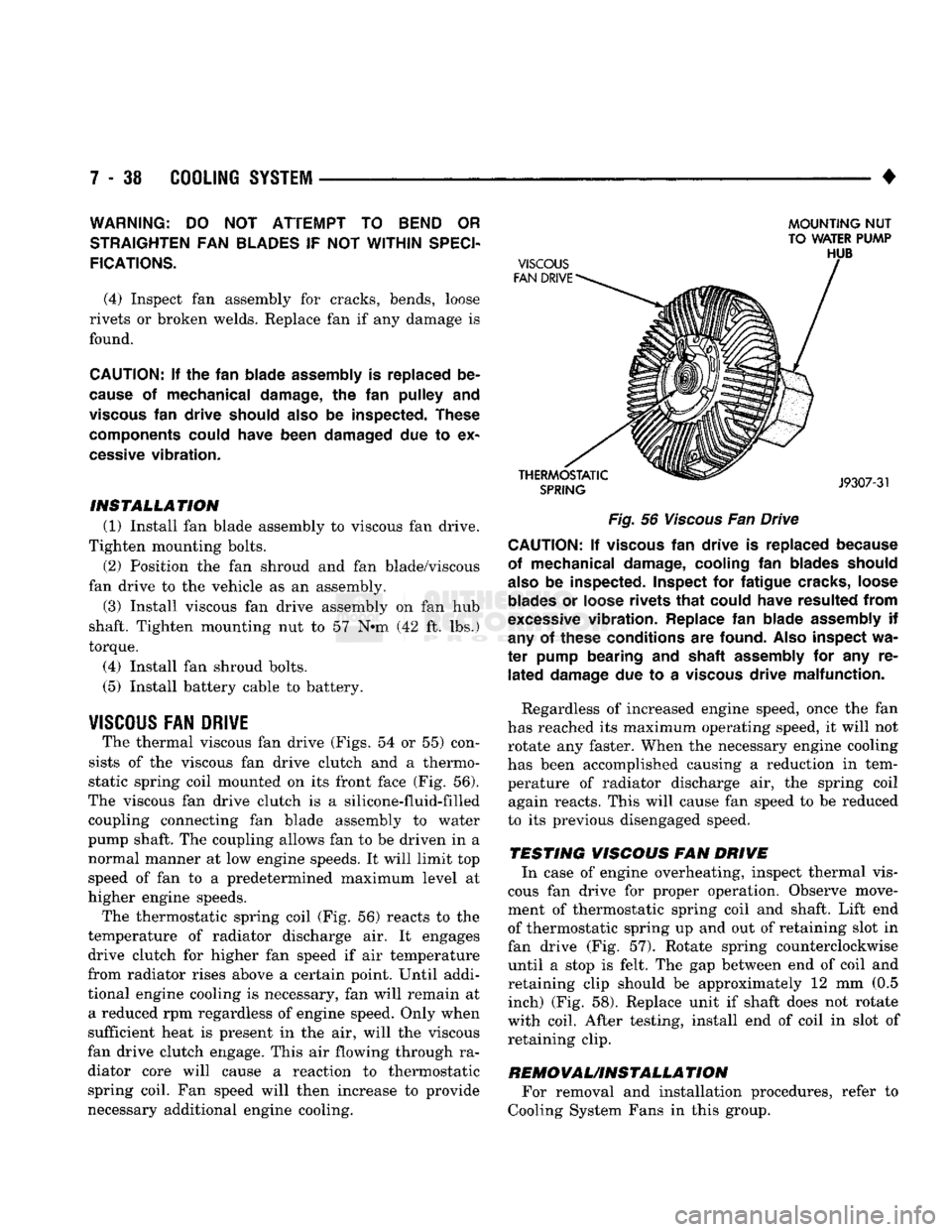
7 - 38
COOLING
SYSTEM
•
WARNING:
DO NOT
ATTEMPT
TO
BEND
OR
STRAIGHTEN
FAN
BLADES
IF
NOT WITHIN
SPECI
FICATIONS.
(4) Inspect fan assembly for cracks, bends, loose
rivets or broken welds. Replace fan if any damage is
found.
CAUTION; If the fan
blade assembly
is
replaced
be
cause
of
mechanical damage,
the fan
pulley
and
viscous
fan
drive should also
be
inspected.
These
components
could have been damaged
due to ex
cessive
vibration.
INSTALLATION
(1) Install fan blade assembly to viscous fan drive.
Tighten mounting bolts.
(2) Position the fan shroud and fan blade/viscous
fan drive to the vehicle as an assembly.
(3) Install viscous fan drive assembly on fan hub
shaft. Tighten mounting nut to 57 N*m (42 ft. lbs.)
torque.
(4) Install fan shroud bolts.
(5) Install battery cable to battery.
VISCOUS
FAN
DRIVE
The thermal viscous fan drive (Figs. 54 or 55) con
sists of the viscous fan drive clutch and a thermo
static spring coil mounted on its front face (Fig. 56).
The viscous fan drive clutch is a silicone-fluid-filled coupling connecting fan blade assembly to water
pump shaft. The coupling allows fan to be driven in a normal manner at low engine speeds. It will limit top
speed of fan to a predetermined maximum level at
higher engine speeds.
The thermostatic spring coil (Fig. 56) reacts to the
temperature of radiator discharge air. It engages drive clutch for higher fan speed if air temperature
from radiator rises above a certain point. Until addi
tional engine cooling is necessary, fan will remain at a reduced rpm regardless of engine speed. Only when
sufficient heat is present in the air, will the viscous
fan drive clutch engage. This air flowing through ra diator core will cause a reaction to thermostatic spring coil. Fan speed will then increase to provide
necessary additional engine cooling.
MOUNTING
NUT
TO WATER PUMP
Fig.
56
Viscous
Fan Drive CAUTION; If
viscous
fan
drive
is
replaced because
of mechanical damage, cooling
fan
blades should
also
be
inspected. Inspect
for
fatigue cracks, loose
blades
or
loose rivets
that
could have resulted
from
excessive
vibration. Replace
fan
blade assembly
if
any
of
these conditions
are
found.
Also
inspect
wa
ter
pump bearing
and
shaft assembly
for any re
lated
damage
due to a
viscous
drive malfunction.
Regardless of increased engine speed, once the fan
has reached its maximum operating speed, it will not
rotate any faster. When the necessary engine cooling
has been accomplished causing a reduction in tem perature of radiator discharge air, the spring coil again reacts. This will cause fan speed to be reduced
to its previous disengaged speed.
TESTING VISCOUS FAN DRIVE In case of engine overheating, inspect thermal vis
cous fan drive for proper operation. Observe move
ment of thermostatic spring coil and shaft. Lift end
of thermostatic spring up and out of retaining slot in
fan drive (Fig. 57). Rotate spring counterclockwise until a stop is felt. The gap between end of coil and
retaining clip should be approximately 12 mm (0.5 inch) (Fig. 58). Replace unit if shaft does not rotate
with coil. After testing, install end of coil in slot of retaining clip.
REMOVAUINSTALLA
TION For removal and installation procedures, refer to
Cooling System Fans in this group.
Page 310 of 1502
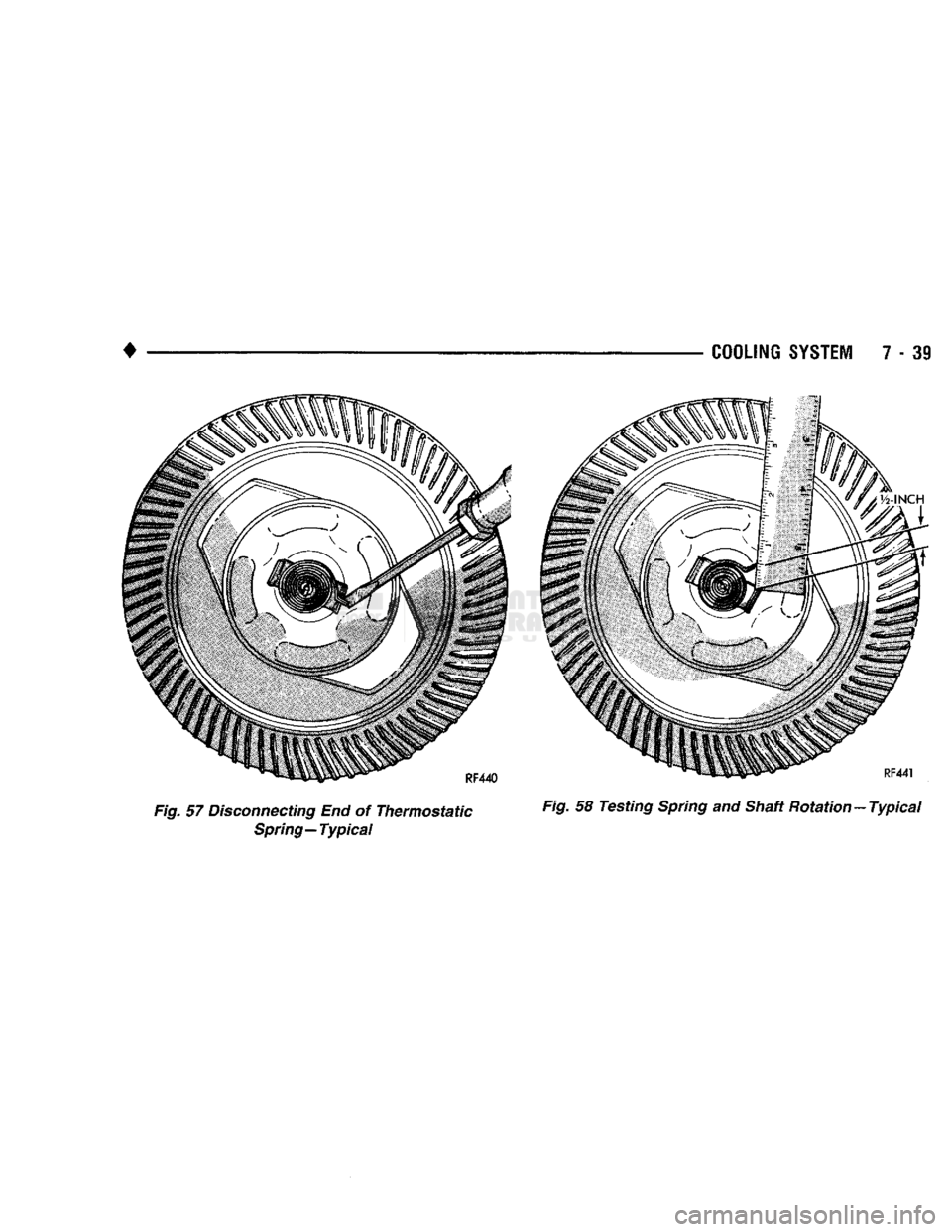
Fig.
57
Disconnecting
End of Thermostatic Fig. 58 Testing
Spring
and Shaft Rotation-Typical
Spring—Typical