FORD FIESTA 1989 Service Repair Manual
Manufacturer: FORD, Model Year: 1989, Model line: FIESTA, Model: FORD FIESTA 1989Pages: 296, PDF Size: 10.65 MB
Page 101 of 296
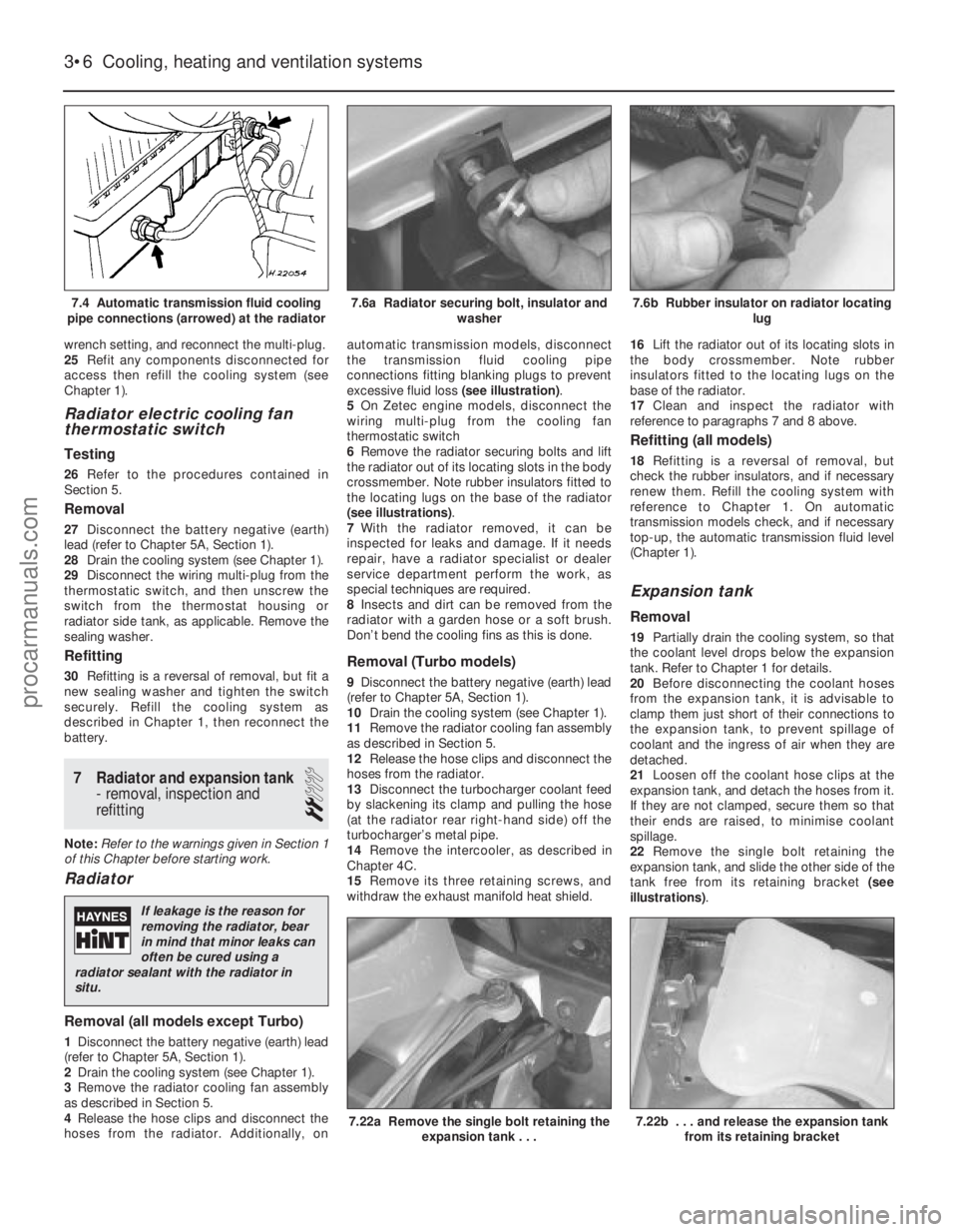
wrench setting, and reconnect the multi-plug.
25Refit any components disconnected for
access then refill the cooling system (see
Chapter 1).
Radiator electric cooling fan
thermostatic switch
Testing
26 Refer to the procedures contained in
Section 5.
Removal
27 Disconnect the battery negative (earth)
lead (refer to Chapter 5A, Section 1).
28 Drain the cooling system (see Chapter 1).
29 Disconnect the wiring multi-plug from the
thermostatic switch, and then unscrew the
switch from the thermostat housing or
radiator side tank, as applicable. Remove the
sealing washer.
Refitting
30 Refitting is a reversal of removal, but fit a
new sealing washer and tighten the switch
securely. Refill the cooling system as
described in Chapter 1, then reconnect the
battery.
7 Radiator and expansion tank
- removal, inspection and
refitting
2
Note: Refer to the warnings given in Section 1
of this Chapter before starting work.
Radiator
Removal (all models except Turbo)
1 Disconnect the battery negative (earth) lead
(refer to Chapter 5A, Section 1).
2 Drain the cooling system (see Chapter 1).
3 Remove the radiator cooling fan assembly
as described in Section 5.
4 Release the hose clips and disconnect the
hoses from the radiator. Additionally, on automatic transmission models, disconnect
the transmission fluid cooling pipe
connections fitting blanking plugs to prevent
excessive fluid loss
(see illustration).
5 On Zetec engine models, disconnect the
wiring multi-plug from the cooling fan
thermostatic switch
6 Remove the radiator securing bolts and lift
the radiator out of its locating slots in the body
crossmember. Note rubber insulators fitted to
the locating lugs on the base of the radiator
(see illustrations) .
7 With the radiator removed, it can be
inspected for leaks and damage. If it needs
repair, have a radiator specialist or dealer
service department perform the work, as
special techniques are required.
8 Insects and dirt can be removed from the
radiator with a garden hose or a soft brush.
Don’t bend the cooling fins as this is done.
Removal (Turbo models)
9 Disconnect the battery negative (earth) lead
(refer to Chapter 5A, Section 1).
10 Drain the cooling system (see Chapter 1).
11 Remove the radiator cooling fan assembly
as described in Section 5.
12 Release the hose clips and disconnect the
hoses from the radiator.
13 Disconnect the turbocharger coolant feed
by slackening its clamp and pulling the hose
(at the radiator rear right-hand side) off the
turbocharger’s metal pipe.
14 Remove the intercooler, as described in
Chapter 4C.
15 Remove its three retaining screws, and
withdraw the exhaust manifold heat shield. 16
Lift the radiator out of its locating slots in
the body crossmember. Note rubber
insulators fitted to the locating lugs on the
base of the radiator.
17 Clean and inspect the radiator with
reference to paragraphs 7 and 8 above.
Refitting (all models)
18 Refitting is a reversal of removal, but
check the rubber insulators, and if necessary
renew them. Refill the cooling system with
reference to Chapter 1. On automatic
transmission models check, and if necessary
top-up, the automatic transmission fluid level
(Chapter 1).
Expansion tank
Removal
19 Partially drain the cooling system, so that
the coolant level drops below the expansion
tank. Refer to Chapter 1 for details.
20 Before disconnecting the coolant hoses
from the expansion tank, it is advisable to
clamp them just short of their connections to
the expansion tank, to prevent spillage of
coolant and the ingress of air when they are
detached.
21 Loosen off the coolant hose clips at the
expansion tank, and detach the hoses from it.
If they are not clamped, secure them so that
their ends are raised, to minimise coolant
spillage.
22 Remove the single bolt retaining the
expansion tank, and slide the other side of the
tank free from its retaining bracket (see
illustrations) .
3•6Cooling, heating and ventilation systems
7.22b . . . and release the expansion tank
from its retaining bracket7.22a Remove the single bolt retaining the expansion tank . . .
7.6b Rubber insulator on radiator locating lug7.6a Radiator securing bolt, insulator andwasher7.4 Automatic transmission fluid cooling
pipe connections (arrowed) at the radiator
1595Ford Fiesta Remake
If leakage is the reason for
removing the radiator, bear
in mind that minor leaks can
often be cured using a
radiator sealant with the radiator in
situ.
procarmanuals.com
http://vnx.su
Page 102 of 296
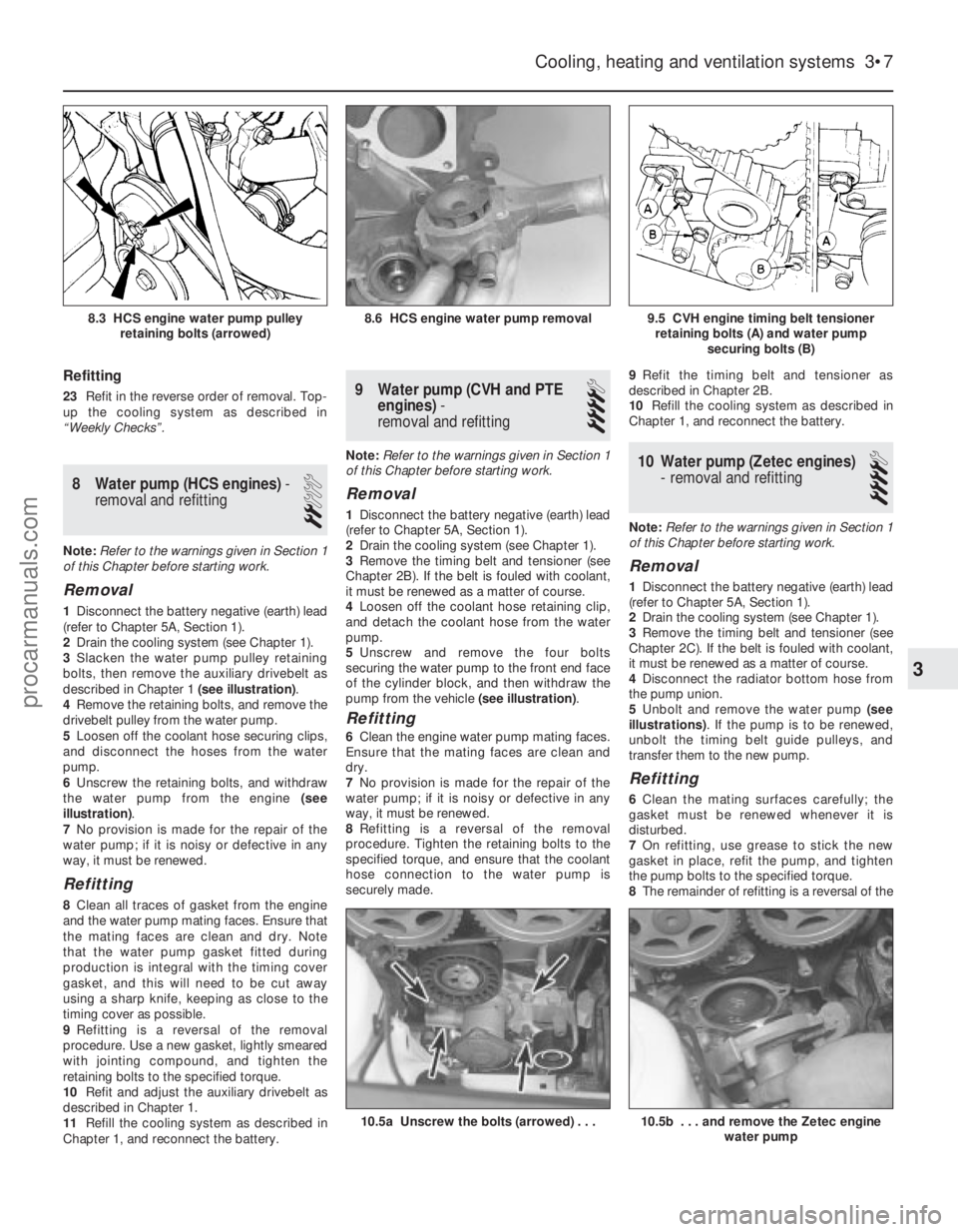
Refitting
23Refit in the reverse order of removal. Top-
up the cooling system as described in
“Weekly Checks”.
8 Water pump (HCS engines) -
removal and refitting
2
Note: Refer to the warnings given in Section 1
of this Chapter before starting work.
Removal
1 Disconnect the battery negative (earth) lead
(refer to Chapter 5A, Section 1).
2 Drain the cooling system (see Chapter 1).
3 Slacken the water pump pulley retaining
bolts, then remove the auxiliary drivebelt as
described in Chapter 1 (see illustration).
4 Remove the retaining bolts, and remove the
drivebelt pulley from the water pump.
5 Loosen off the coolant hose securing clips,
and disconnect the hoses from the water
pump.
6 Unscrew the retaining bolts, and withdraw
the water pump from the engine (see
illustration) .
7 No provision is made for the repair of the
water pump; if it is noisy or defective in any
way, it must be renewed.
Refitting
8 Clean all traces of gasket from the engine
and the water pump mating faces. Ensure that
the mating faces are clean and dry. Note
that the water pump gasket fitted during
production is integral with the timing cover
gasket, and this will need to be cut away
using a sharp knife, keeping as close to the
timing cover as possible.
9 Refitting is a reversal of the removal
procedure. Use a new gasket, lightly smeared
with jointing compound, and tighten the
retaining bolts to the specified torque.
10 Refit and adjust the auxiliary drivebelt as
described in Chapter 1.
11 Refill the cooling system as described in
Chapter 1, and reconnect the battery.
9 Water pump (CVH and PTE engines) -
removal and refitting
4
Note: Refer to the warnings given in Section 1
of this Chapter before starting work.
Removal
1 Disconnect the battery negative (earth) lead
(refer to Chapter 5A, Section 1).
2 Drain the cooling system (see Chapter 1).
3 Remove the timing belt and tensioner (see
Chapter 2B). If the belt is fouled with coolant,
it must be renewed as a matter of course.
4 Loosen off the coolant hose retaining clip,
and detach the coolant hose from the water
pump.
5 Unscrew and remove the four bolts
securing the water pump to the front end face
of the cylinder block, and then withdraw the
pump from the vehicle (see illustration).
Refitting
6Clean the engine water pump mating faces.
Ensure that the mating faces are clean and
dry.
7 No provision is made for the repair of the
water pump; if it is noisy or defective in any
way, it must be renewed.
8 Refitting is a reversal of the removal
procedure. Tighten the retaining bolts to the
specified torque, and ensure that the coolant
hose connection to the water pump is
securely made. 9
Refit the timing belt and tensioner as
described in Chapter 2B.
10 Refill the cooling system as described in
Chapter 1, and reconnect the battery.
10 Water pump (Zetec engines) - removal and refitting
4
Note: Refer to the warnings given in Section 1
of this Chapter before starting work.
Removal
1 Disconnect the battery negative (earth) lead
(refer to Chapter 5A, Section 1).
2 Drain the cooling system (see Chapter 1).
3 Remove the timing belt and tensioner (see
Chapter 2C). If the belt is fouled with coolant,
it must be renewed as a matter of course.
4 Disconnect the radiator bottom hose from
the pump union.
5 Unbolt and remove the water pump (see
illustrations) . If the pump is to be renewed,
unbolt the timing belt guide pulleys, and
transfer them to the new pump.
Refitting
6 Clean the mating surfaces carefully; the
gasket must be renewed whenever it is
disturbed.
7 On refitting, use grease to stick the new
gasket in place, refit the pump, and tighten
the pump bolts to the specified torque.
8 The remainder of refitting is a reversal of the
Cooling, heating and ventilation systems 3•7
9.5 CVH engine timing belt tensioner
retaining bolts (A) and water pump securing bolts (B)8.6 HCS engine water pump removal8.3 HCS engine water pump pulleyretaining bolts (arrowed)
10.5b . . . and remove the Zetec engine water pump10.5a Unscrew the bolts (arrowed) . . .
3
1595Ford Fiesta Remakeprocarmanuals.com
http://vnx.su
Page 103 of 296
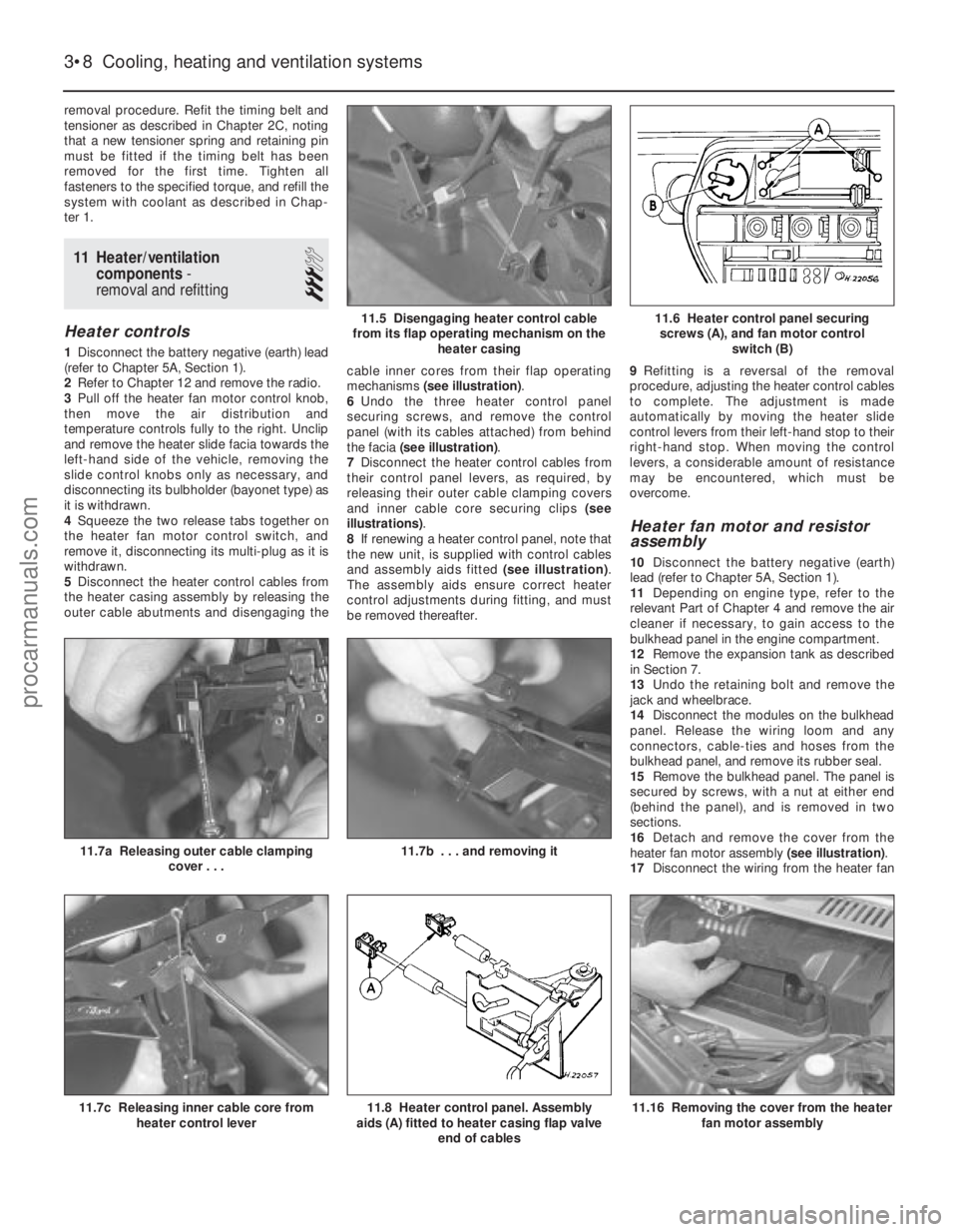
removal procedure. Refit the timing belt and
tensioner as described in Chapter 2C, noting
that a new tensioner spring and retaining pin
must be fitted if the timing belt has been
removed for the first time. Tighten all
fasteners to the specified torque, and refill the
system with coolant as described in Chap-
ter 1.
11 Heater/ventilationcomponents -
removal and refitting
3
Heater controls
1 Disconnect the battery negative (earth) lead
(refer to Chapter 5A, Section 1).
2 Refer to Chapter 12 and remove the radio.
3 Pull off the heater fan motor control knob,
then move the air distribution and
temperature controls fully to the right. Unclip
and remove the heater slide facia towards the
left-hand side of the vehicle, removing the
slide control knobs only as necessary, and
disconnecting its bulbholder (bayonet type) as
it is withdrawn.
4 Squeeze the two release tabs together on
the heater fan motor control switch, and
remove it, disconnecting its multi-plug as it is
withdrawn.
5 Disconnect the heater control cables from
the heater casing assembly by releasing the
outer cable abutments and disengaging the cable inner cores from their flap operating
mechanisms
(see illustration) .
6 Undo the three heater control panel
securing screws, and remove the control
panel (with its cables attached) from behind
the facia (see illustration) .
7 Disconnect the heater control cables from
their control panel levers, as required, by
releasing their outer cable clamping covers
and inner cable core securing clips (see
illustrations) .
8 If renewing a heater control panel, note that
the new unit, is supplied with control cables
and assembly aids fitted (see illustration).
The assembly aids ensure correct heater
control adjustments during fitting, and must
be removed thereafter. 9
Refitting is a reversal of the removal
procedure, adjusting the heater control cables
to complete. The adjustment is made
automatically by moving the heater slide
control levers from their left-hand stop to their
right-hand stop. When moving the control
levers, a considerable amount of resistance
may be encountered, which must be
overcome.
Heater fan motor and resistor
assembly
10 Disconnect the battery negative (earth)
lead (refer to Chapter 5A, Section 1).
11 Depending on engine type, refer to the
relevant Part of Chapter 4 and remove the air
cleaner if necessary, to gain access to the
bulkhead panel in the engine compartment.
12 Remove the expansion tank as described
in Section 7.
13 Undo the retaining bolt and remove the
jack and wheelbrace.
14 Disconnect the modules on the bulkhead
panel. Release the wiring loom and any
connectors, cable-ties and hoses from the
bulkhead panel, and remove its rubber seal.
15 Remove the bulkhead panel. The panel is
secured by screws, with a nut at either end
(behind the panel), and is removed in two
sections.
16 Detach and remove the cover from the
heater fan motor assembly (see illustration).
17 Disconnect the wiring from the heater fan
3•8 Cooling, heating and ventilation systems
11.16 Removing the cover from the heater
fan motor assembly11.8 Heater control panel. Assembly
aids (A) fitted to heater casing flap valve
end of cables11.7c Releasing inner cable core fromheater control lever
11.7b . . . and removing it11.7a Releasing outer cable clamping
cover . . .
11.6 Heater control panel securing screws (A), and fan motor control switch (B)11.5 Disengaging heater control cable
from its flap operating mechanism on the heater casing
1595Ford Fiesta Remakeprocarmanuals.com
http://vnx.su
Page 104 of 296
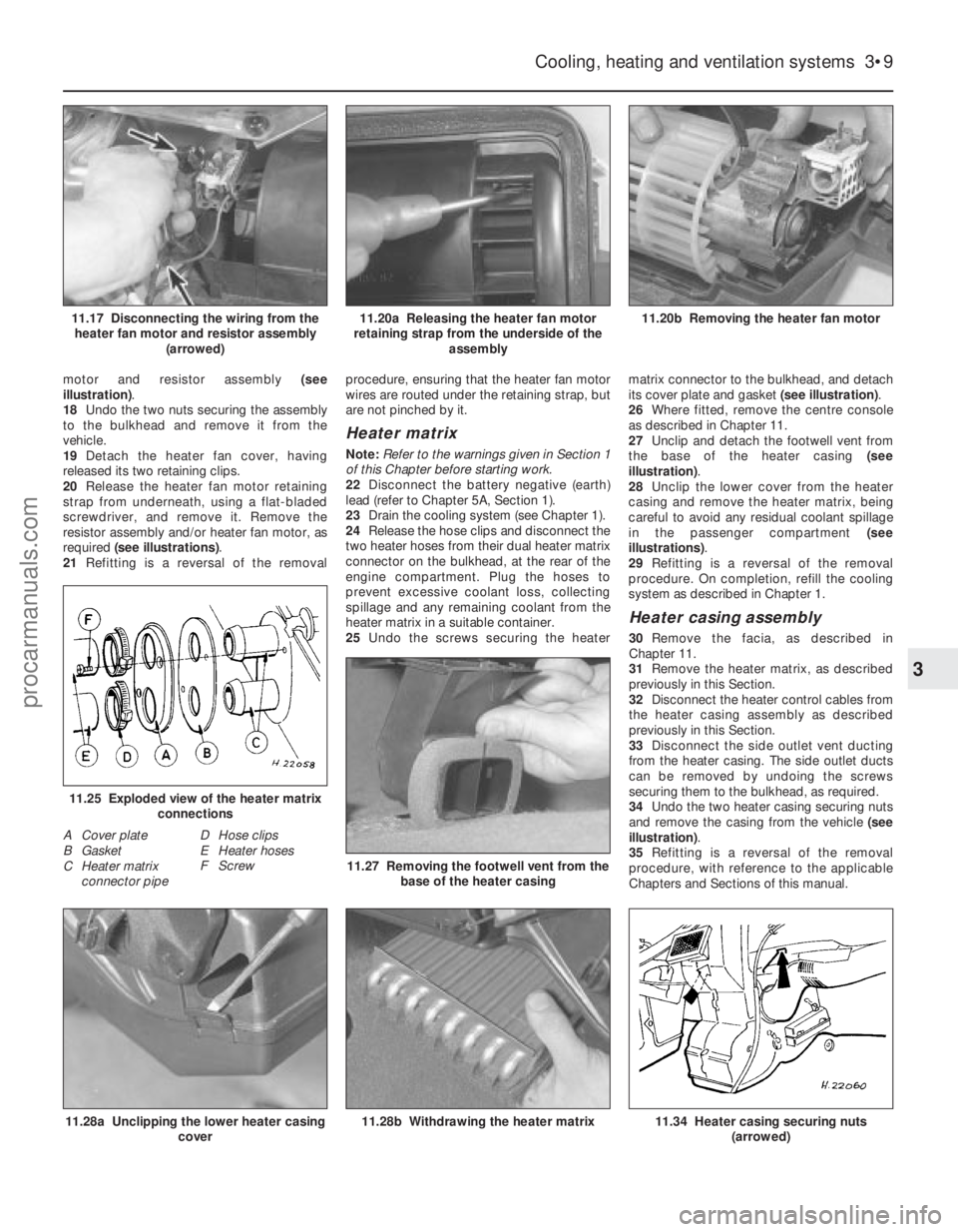
motor and resistor assembly (see
illustration) .
18 Undo the two nuts securing the assembly
to the bulkhead and remove it from the
vehicle.
19 Detach the heater fan cover, having
released its two retaining clips.
20 Release the heater fan motor retaining
strap from underneath, using a flat-bladed
screwdriver, and remove it. Remove the
resistor assembly and/or heater fan motor, as
required (see illustrations) .
21 Refitting is a reversal of the removal procedure, ensuring that the heater fan motor
wires are routed under the retaining strap, but
are not pinched by it.
Heater matrix
Note:
Refer to the warnings given in Section 1
of this Chapter before starting work.
22 Disconnect the battery negative (earth)
lead (refer to Chapter 5A, Section 1).
23 Drain the cooling system (see Chapter 1).
24 Release the hose clips and disconnect the
two heater hoses from their dual heater matrix
connector on the bulkhead, at the rear of the
engine compartment. Plug the hoses to
prevent excessive coolant loss, collecting
spillage and any remaining coolant from the
heater matrix in a suitable container.
25 Undo the screws securing the heater matrix connector to the bulkhead, and detach
its cover plate and gasket
(see illustration).
26 Where fitted, remove the centre console
as described in Chapter 11.
27 Unclip and detach the footwell vent from
the base of the heater casing (see
illustration) .
28 Unclip the lower cover from the heater
casing and remove the heater matrix, being
careful to avoid any residual coolant spillage
in the passenger compartment (see
illustrations) .
29 Refitting is a reversal of the removal
procedure. On completion, refill the cooling
system as described in Chapter 1.
Heater casing assembly
30 Remove the facia, as described in
Chapter 11.
31 Remove the heater matrix, as described
previously in this Section.
32 Disconnect the heater control cables from
the heater casing assembly as described
previously in this Section.
33 Disconnect the side outlet vent ducting
from the heater casing. The side outlet ducts
can be removed by undoing the screws
securing them to the bulkhead, as required.
34 Undo the two heater casing securing nuts
and remove the casing from the vehicle (see
illustration) .
35 Refitting is a reversal of the removal
procedure, with reference to the applicable
Chapters and Sections of this manual.
Cooling, heating and ventilation systems 3•9
11.20b Removing the heater fan motor11.20a Releasing the heater fan motor
retaining strap from the underside of the assembly11.17 Disconnecting the wiring from theheater fan motor and resistor assembly (arrowed)
11.34 Heater casing securing nuts(arrowed)11.28b Withdrawing the heater matrix
11.27 Removing the footwell vent from thebase of the heater casing
11.25 Exploded view of the heater matrix connections
A Cover plate
B Gasket
C Heater matrixconnector pipe D Hose clips
E Heater hoses
F Screw
11.28a Unclipping the lower heater casing
cover
3
1595Ford Fiesta Remakeprocarmanuals.com
http://vnx.su
Page 105 of 296
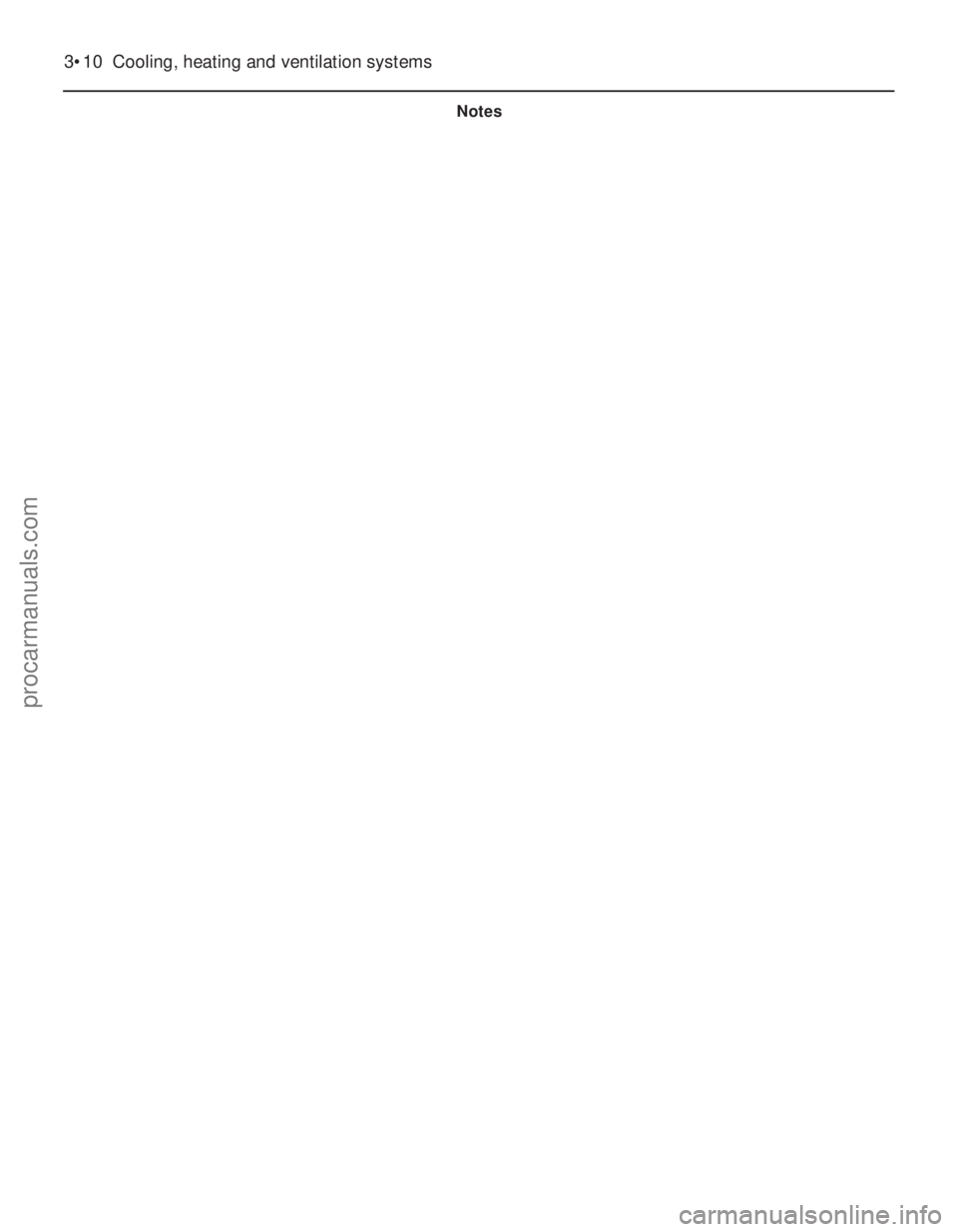
3•10 Cooling, heating and ventilation systems
1595Ford Fiesta Remake
Notes
procarmanuals.com
http://vnx.su
Page 106 of 296
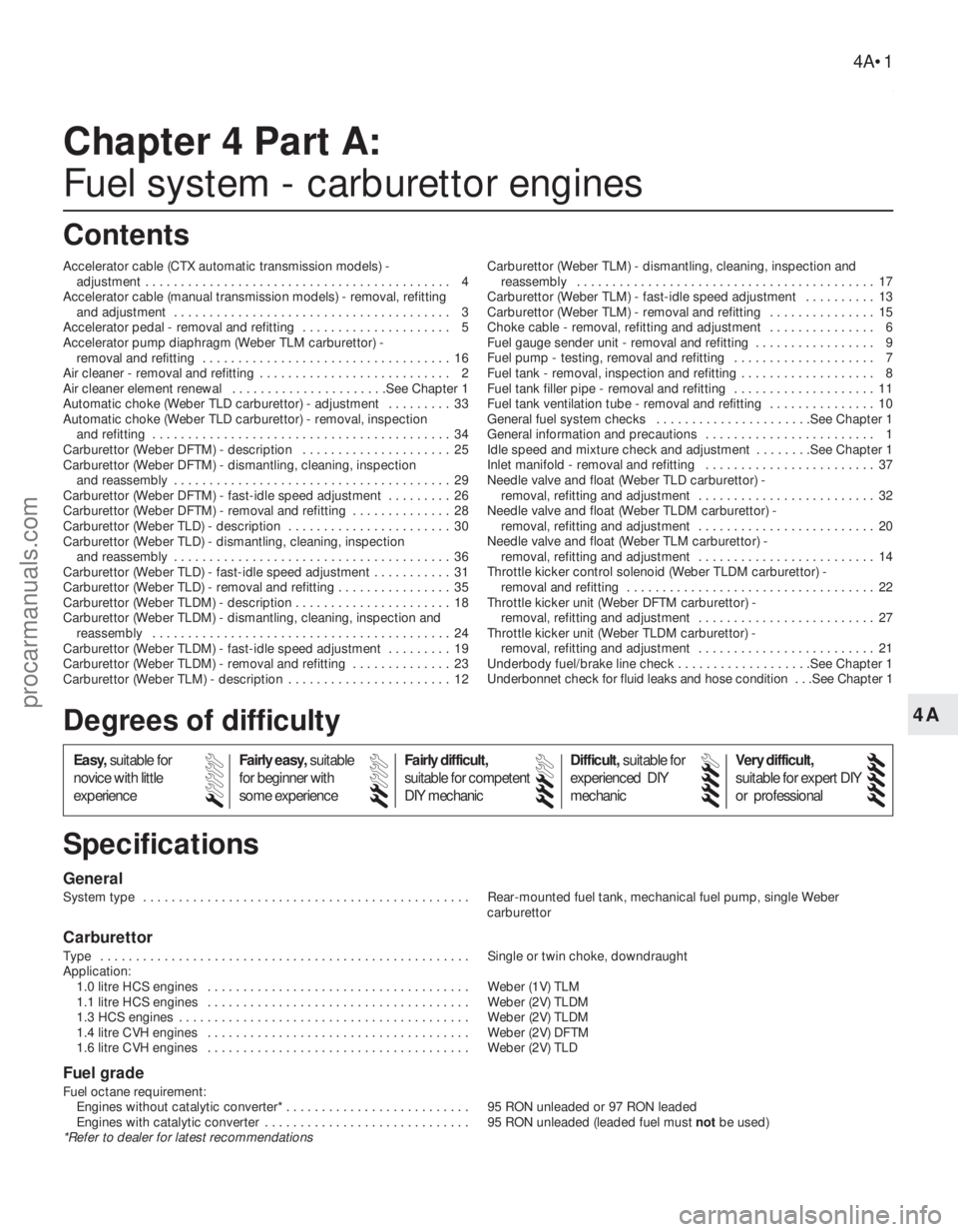
4A
1595Ford Fiesta Remake
General
System type . . . . . . . . . . . . . . . . . . . . . . . . . . . . . . . . . . . .\
. . . . . . . . . . Rear-mounted fuel tank, mechanical fuel pump, single Webercarburettor
Carburettor
Type . . . . . . . . . . . . . . . . . . . . . . . . . . . . . . . . . . . .\
. . . . . . . . . . . . . . . . Single or twin choke, downdraught
Application:1.0 litre HCS engines . . . . . . . . . . . . . . . . . . . . . . . . . . . . . . . . . . . .\
. Weber (1V) TLM
1.1 litre HCS engines . . . . . . . . . . . . . . . . . . . . . . . . . . . . . . . . . . . .\
. Weber (2V) TLDM
1.3 HCS engines . . . . . . . . . . . . . . . . . . . . . . . . . . . . . . . . . . . .\
. . . . . Weber (2V) TLDM
1.4 litre CVH engines . . . . . . . . . . . . . . . . . . . . . . . . . . . . . . . . . . . .\
. Weber (2V) DFTM
1.6 litre CVH engines . . . . . . . . . . . . . . . . . . . . . . . . . . . . . . . . . . . .\
. Weber (2V) TLD
Fuel grade
Fuel octane requirement:Engines without catalytic converter* . . . . . . . . . . . . . . . . . . . . . . . . . . 95 RON unleaded or 97 RON leaded
Engines with catalytic converter . . . . . . . . . . . . . . . . . . . . . . . . . . . . . 95 RON unleaded (leaded fuel must notbe used)
*Refer to dealer for latest recommendations
Chapter 4 Part A:
Fuel system - carburettor engines
Accelerator cable (CTX automatic transmission models) -
adjustment . . . . . . . . . . . . . . . . . . . . . . . . . . . . . . . . . . . .\
. . . . . . . 4
Accelerator cable (manual transmission models) - removal, refitting and adjustment . . . . . . . . . . . . . . . . . . . . . . . . . . . . . . . . . . . .\
. . . 3
Accelerator pedal - removal and refitting . . . . . . . . . . . . . . . . . . . . . 5
Accelerator pump diaphragm (Weber TLM carburettor) - removal and refitting . . . . . . . . . . . . . . . . . . . . . . . . . . . . . . . . . . . 16
Air cleaner - removal and refitting . . . . . . . . . . . . . . . . . . . . . . . . . . . 2
Air cleaner element renewal . . . . . . . . . . . . . . . . . . . . . .See Chapter 1
Automatic choke (Weber TLD carburettor) - adjustment . . . . . . . . . 33
Automatic choke (Weber TLD carburettor) - removal, inspection and refitting . . . . . . . . . . . . . . . . . . . . . . . . . . . . . . . . . . . .\
. . . . . . 34
Carburettor (Weber DFTM) - description . . . . . . . . . . . . . . . . . . . . . 25
Carburettor (Weber DFTM) - dismantling, cleaning, inspection and reassembly . . . . . . . . . . . . . . . . . . . . . . . . . . . . . . . . . . . .\
. . . 29
Carburettor (Weber DFTM) - fast-idle speed adjustment . . . . . . . . . 26
Carburettor (Weber DFTM) - removal and refitting . . . . . . . . . . . . . . 28
Carburettor (Weber TLD) - description . . . . . . . . . . . . . . . . . . . . . . . 30
Carburettor (Weber TLD) - dismantling, cleaning, inspection and reassembly . . . . . . . . . . . . . . . . . . . . . . . . . . . . . . . . . . . .\
. . . 36
Carburettor (Weber TLD) - fast-idle speed adjustment . . . . . . . . . . . 31
Carburettor (Weber TLD) - removal and refitting . . . . . . . . . . . . . . . . 35
Carburettor (Weber TLDM) - description . . . . . . . . . . . . . . . .\
. . . . . . 18
Carburettor (Weber TLDM) - dismantling, cleaning, inspection and
reassembly . . . . . . . . . . . . . . . . . . . . . . . . . . . . . . . . . . . .\
. . . . . . 24
Carburettor (Weber TLDM) - fast-idle speed adjustment . . . . . . . . . 19
Carburettor (Weber TLDM) - removal and refitting . . . . . . . . . . . . . . 23
Carburettor (Weber TLM) - description . . . . . . . . . . . . . . . . . . . . . . . 12 Carburettor (Weber TLM) - dismantling, cleaning, inspection and
reassembly . . . . . . . . . . . . . . . . . . . . . . . . . . . . . . . . . . . .\
. . . . . . 17
Carburettor (Weber TLM) - fast-idle speed adjustment . . . . . . . . . . 13
Carburettor (Weber TLM) - removal and refitting . . . . . . . . . . . . . . . 15
Choke cable - removal, refitting and adjustment . . . . . . . . . . . . . . . 6
Fuel gauge sender unit - removal and refitting . . . . . . . . . . . . . . . . . 9
Fuel pump - testing, removal and refitting . . . . . . . . . . . . . . . . . . . . 7
Fuel tank - removal, inspection and refitting . . . . . . . . . . . . . . . . . . . 8
Fuel tank filler pipe - removal and refitting . . . . . . . . . . . . . . . . . . . . 11
Fuel tank ventilation tube - removal and refitting . . . . . . . . . . . . . . . 10
General fuel system checks . . . . . . . . . . . . . . . . . . . . . .See Chapter 1
General information and precautions . . . . . . . . . . . . . . . . . . . . . . . . 1
Idle speed and mixture check and adjustment . . . . . . . .See Chapter 1
Inlet manifold - removal and refitting . . . . . . . . . . . . . . . . . . . . . . . . 37
Needle valve and float (Weber TLD carburettor) -
removal, refitting and adjustment . . . . . . . . . . . . . . . . . . . . . . . . . 32
Needle valve and float (Weber TLDM carburettor) - removal, refitting and adjustment . . . . . . . . . . . . . . . . . . . . . . . . . 20
Needle valve and float (Weber TLM carburettor) - removal, refitting and adjustment . . . . . . . . . . . . . . . . . . . . . . . . . 14
Throttle kicker control solenoid (Weber TLDM carburettor) -
removal and refitting . . . . . . . . . . . . . . . . . . . . . . . . . . . . . . . . . . . 22
Throttle kicker unit (Weber DFTM carburettor) - removal, refitting and adjustment . . . . . . . . . . . . . . . . . . . . . . . . . 27
Throttle kicker unit (Weber TLDM carburettor) - removal, refitting and adjustment . . . . . . . . . . . . . . . . . . . . . . . . . 21
Underbody fuel/brake line check . . . . . . . . . . . . . . . . . . .See\
Chapter 1
Underbonnet check for fluid leaks and hose condition . . .See Chapter 1
4A•1
Specifications Contents
Easy, suitable for
novice with little
experience Fairly easy,
suitable
for beginner with
some experience Fairly difficult,
suitable for competent
DIY mechanic
Difficult,
suitable for
experienced DIY
mechanic Very difficult,
suitable for expert DIY
or professional
Degrees of difficulty
54321
procarmanuals.com
http://vnx.su
Page 107 of 296
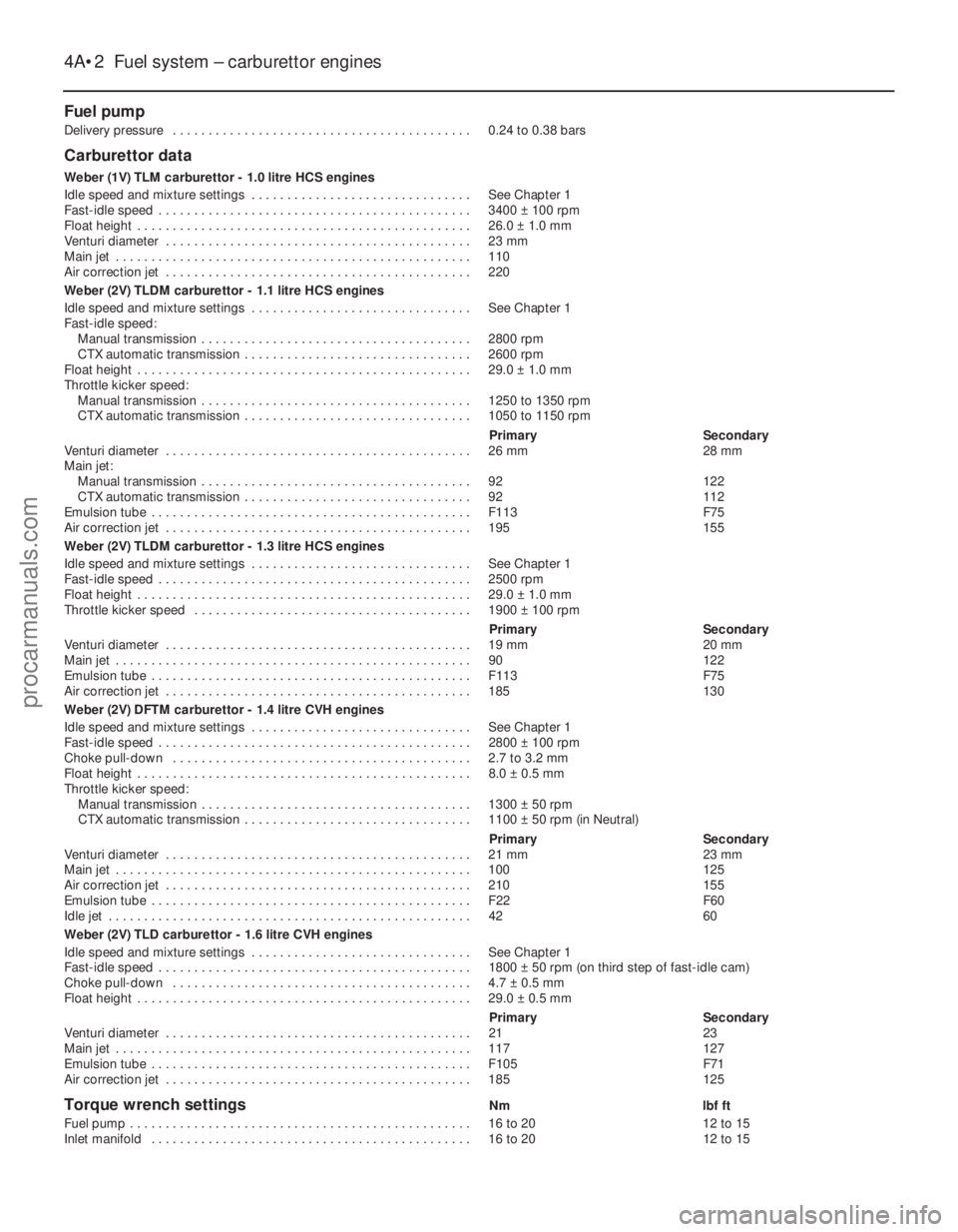
Fuel pump
Delivery pressure . . . . . . . . . . . . . . . . . . . . . . . . . . . . . . . . . . . .\
. . . . . . 0.24 to 0.38 bars
Carburettor data
Weber (1V) TLM carburettor - 1.0 litre HCS engines
Idle speed and mixture settings . . . . . . . . . . . . . . . . . . . . . . . . . . . . . . . See Chapter 1Fast-idle speed . . . . . . . . . . . . . . . . . . . . . . . . . . . . . . . . . . . .\
. . . . . . . . 3400 ± 100 rpm
Float height . . . . . . . . . . . . . . . . . . . . . . . . . . . . . . . . . . . .\
. . . . . . . . . . . 26.0 ± 1.0 mm
Venturi diameter . . . . . . . . . . . . . . . . . . . . . . . . . . . . . . . . . . . .\
. . . . . . . 23 mm
Main jet . . . . . . . . . . . . . . . . . . . . . . . . . . . . . . . . . . . .\
. . . . . . . . . . . . . . 110
Air correction jet . . . . . . . . . . . . . . . . . . . . . . . . . . . . . . . . . . . .\
. . . . . . . 220
Weber (2V) TLDM carburettor - 1.1 litre HCS engines
Idle speed and mixture settings . . . . . . . . . . . . . . . . . . . . . . . . . . . . . . . See Chapter 1Fast-idle speed:
Manual transmission . . . . . . . . . . . . . . . . . . . . . . . . . . . . . . . . . . . .\
. . 2800 rpm
CTX automatic transmission . . . . . . . . . . . . . . . . . . . . . . . . . . . . . . . . 2600 rpm
Float height . . . . . . . . . . . . . . . . . . . . . . . . . . . . . . . . . . . .\
. . . . . . . . . . . 29.0 ± 1.0 mm
Throttle kicker speed: Manual transmission . . . . . . . . . . . . . . . . . . . . . . . . . . . . . . . . . . . .\
. . 1250 to 1350 rpm
CTX automatic transmission . . . . . . . . . . . . . . . . . . . . . . . . . . . . . . . . 1050 to 1150 rpm
PrimarySecondary
Venturi diameter . . . . . . . . . . . . . . . . . . . . . . . . . . . . . . . . . . . .\
. . . . . . . 26 mm 28 mm
Main jet: Manual transmission . . . . . . . . . . . . . . . . . . . . . . . . . . . . . . . . . . . .\
. . 92122
CTX automatic transmission . . . . . . . . . . . . . . . . . . . . . . . . . . . . . . . . 92112
Emulsion tube . . . . . . . . . . . . . . . . . . . . . . . . . . . . . . . . . . . .\
. . . . . . . . . F113 F75
Air correction jet . . . . . . . . . . . . . . . . . . . . . . . . . . . . . . . . . . . .\
. . . . . . . 195 155
Weber (2V) TLDM carburettor - 1.3 litre HCS engines
Idle speed and mixture settings . . . . . . . . . . . . . . . . . . . . . . . . . . . . . . . See Chapter 1 Fast-idle speed . . . . . . . . . . . . . . . . . . . . . . . . . . . . . . . . . . . .\
. . . . . . . . 2500 rpmFloat height . . . . . . . . . . . . . . . . . . . . . . . . . . . . . . . . . . . .\
. . . . . . . . . . . 29.0 ± 1.0 mm
Throttle kicker speed . . . . . . . . . . . . . . . . . . . . . . . . . . . . . . . . . . . .\
. . . 1900 ± 100 rpm
PrimarySecondary
Venturi diameter . . . . . . . . . . . . . . . . . . . . . . . . . . . . . . . . . . . .\
. . . . . . . 19 mm 20 mm
Main jet . . . . . . . . . . . . . . . . . . . . . . . . . . . . . . . . . . . .\
. . . . . . . . . . . . . . 90122
Emulsion tube . . . . . . . . . . . . . . . . . . . . . . . . . . . . . . . . . . . .\
. . . . . . . . . F113 F75
Air correction jet . . . . . . . . . . . . . . . . . . . . . . . . . . . . . . . . . . . .\
. . . . . . . 185 130
Weber (2V) DFTM carburettor - 1.4 litre CVH engines
Idle speed and mixture settings . . . . . . . . . . . . . . . . . . . . . . . . . . . . . . . See Chapter 1 Fast-idle speed . . . . . . . . . . . . . . . . . . . . . . . . . . . . . . . . . . . .\
. . . . . . . . 2800 ± 100 rpm
Choke pull-down . . . . . . . . . . . . . . . . . . . . . . . . . . . . . . . . . . . .\
. . . . . . 2.7 to 3.2 mm
Float height . . . . . . . . . . . . . . . . . . . . . . . . . . . . . . . . . . . .\
. . . . . . . . . . . 8.0 ± 0.5 mm
Throttle kicker speed:
Manual transmission . . . . . . . . . . . . . . . . . . . . . . . . . . . . . . . . . . . .\
. . 1300 ± 50 rpm
CTX automatic transmission . . . . . . . . . . . . . . . . . . . . . . . . . . . . . . . . 1100 ± 50 rpm (in Neutral)
PrimarySecondary
Venturi diameter . . . . . . . . . . . . . . . . . . . . . . . . . . . . . . . . . . . .\
. . . . . . . 21 mm 23 mm
Main jet . . . . . . . . . . . . . . . . . . . . . . . . . . . . . . . . . . . .\
. . . . . . . . . . . . . . 100 125
Air correction jet . . . . . . . . . . . . . . . . . . . . . . . . . . . . . . . . . . . .\
. . . . . . . 210 155
Emulsion tube . . . . . . . . . . . . . . . . . . . . . . . . . . . . . . . . . . . .\
. . . . . . . . . F22 F60
Idle jet . . . . . . . . . . . . . . . . . . . . . . . . . . . . . . . . . . . .\
. . . . . . . . . . . . . . . 4260
Weber (2V) TLD carburettor - 1.6 litre CVH engines
Idle speed and mixture settings . . . . . . . . . . . . . . . . . . . . . . . . . . . . . . . See Chapter 1 Fast-idle speed . . . . . . . . . . . . . . . . . . . . . . . . . . . . . . . . . . . .\
. . . . . . . . 1800 ± 50 rpm (on third step of fast-idle cam)
Choke pull-down . . . . . . . . . . . . . . . . . . . . . . . . . . . . . . . . . . . .\
. . . . . . 4.7 ± 0.5 mm
Float height . . . . . . . . . . . . . . . . . . . . . . . . . . . . . . . . . . . .\
. . . . . . . . . . . 29.0 ± 0.5 mm
PrimarySecondary
Venturi diameter . . . . . . . . . . . . . . . . . . . . . . . . . . . . . . . . . . . .\
. . . . . . . 2123
Main jet . . . . . . . . . . . . . . . . . . . . . . . . . . . . . . . . . . . .\
. . . . . . . . . . . . . . 117 127
Emulsion tube . . . . . . . . . . . . . . . . . . . . . . . . . . . . . . . . . . . .\
. . . . . . . . . F105 F71
Air correction jet . . . . . . . . . . . . . . . . . . . . . . . . . . . . . . . . . . . .\
. . . . . . . 185 125
Torque wrench settingsNmlbf ft
Fuel pump . . . . . . . . . . . . . . . . . . . . . . . . . . . . . . . . . . . .\
. . . . . . . . . . . . 16 to 20 12 to 15
Inlet manifold . . . . . . . . . . . . . . . . . . . . . . . . . . . . . . . . . . . .\
. . . . . . . . . 16 to 20 12 to 15
4A•2 Fuel system – carburettor engines
1595Ford Fiesta Remakeprocarmanuals.com
http://vnx.su
Page 108 of 296
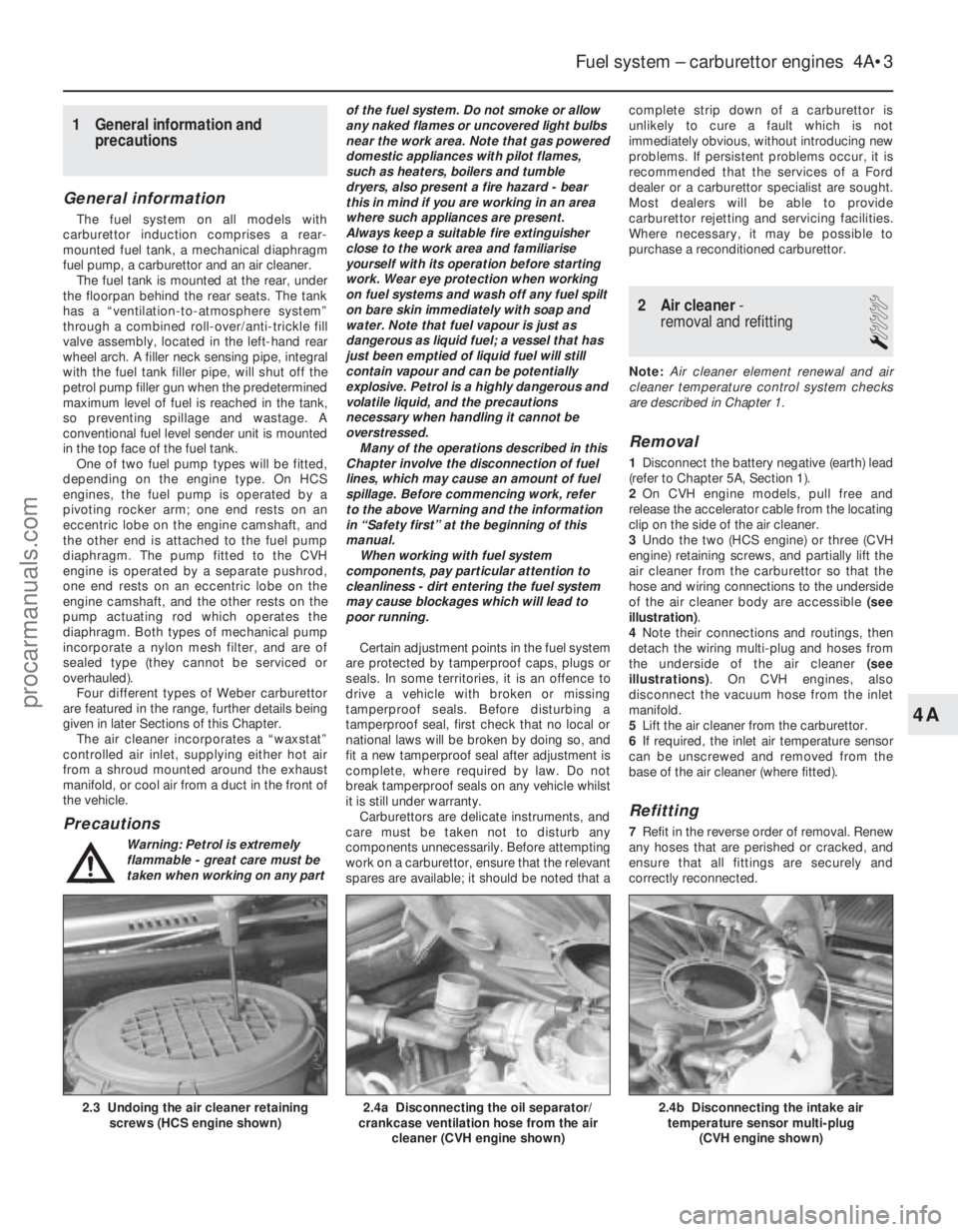
1 General information andprecautions
General information
The fuel system on all models with
carburettor induction comprises a rear-
mounted fuel tank, a mechanical diaphragm
fuel pump, a carburettor and an air cleaner. The fuel tank is mounted at the rear, under
the floorpan behind the rear seats. The tank
has a “ventilation-to-atmosphere system”
through a combined roll-over/anti-trickle fill
valve assembly, located in the left-hand rear
wheel arch. A filler neck sensing pipe, integral
with the fuel tank filler pipe, will shut off the
petrol pump filler gun when the predetermined
maximum level of fuel is reached in the tank,
so preventing spillage and wastage. A
conventional fuel level sender unit is mounted
in the top face of the fuel tank. One of two fuel pump types will be fitted,
depending on the engine type. On HCS
engines, the fuel pump is operated by a
pivoting rocker arm; one end rests on an
eccentric lobe on the engine camshaft, and
the other end is attached to the fuel pump
diaphragm. The pump fitted to the CVH
engine is operated by a separate pushrod,
one end rests on an eccentric lobe on the
engine camshaft, and the other rests on the
pump actuating rod which operates the
diaphragm. Both types of mechanical pump
incorporate a nylon mesh filter, and are of
sealed type (they cannot be serviced or
overhauled). Four different types of Weber carburettor
are featured in the range, further details being
given in later Sections of this Chapter. The air cleaner incorporates a “waxstat”
controlled air inlet, supplying either hot air
from a shroud mounted around the exhaust
manifold, or cool air from a duct in the front of
the vehicle.
Precautions
Warning: Petrol is extremely
flammable - great care must be
taken when working on any part of the fuel system. Do not smoke or allow
any naked flames or uncovered light bulbs
near the work area. Note that gas powered
domestic appliances with pilot flames,
such as heaters, boilers and tumble
dryers, also present a fire hazard - bear
this in mind if you are working in an area
where such appliances are present.
Always keep a suitable fire extinguisher
close to the work area and familiarise
yourself with its operation before starting
work. Wear eye protection when working
on fuel systems and wash off any fuel spilt
on bare skin immediately with soap and
water. Note that fuel vapour is just as
dangerous as liquid fuel; a vessel that has
just been emptied of liquid fuel will still
contain vapour and can be potentially
explosive. Petrol is a highly dangerous and
volatile liquid, and the precautions
necessary when handling it cannot be
overstressed.
Many of the operations described in this
Chapter involve the disconnection of fuel
lines, which may cause an amount of fuel
spillage. Before commencing work, refer
to the above Warning and the information
in “Safety first” at the beginning of this
manual.
When working with fuel system
components, pay particular attention to
cleanliness - dirt entering the fuel system
may cause blockages which will lead to
poor running.
Certain adjustment points in the fuel system
are protected by tamperproof caps, plugs or
seals. In some territories, it is an offence to
drive a vehicle with broken or missing
tamperproof seals. Before disturbing a
tamperproof seal, first check that no local or
national laws will be broken by doing so, and
fit a new tamperproof seal after adjustment is
complete, where required by law. Do not
break tamperproof seals on any vehicle whilst
it is still under warranty. Carburettors are delicate instruments, and
care must be taken not to disturb any
components unnecessarily. Before attempting
work on a carburettor, ensure that the relevant
spares are available; it should be noted that a complete strip down of a carburettor is
unlikely to cure a fault which is not
immediately obvious, without introducing new
problems. If persistent problems occur, it is
recommended that the services of a Ford
dealer or a carburettor specialist are sought.
Most dealers will be able to provide
carburettor rejetting and servicing facilities.
Where necessary, it may be possible to
purchase a reconditioned carburettor.
2 Air cleaner
-
removal and refitting
1
Note: Air cleaner element renewal and air
cleaner temperature control system checks
are described in Chapter 1.
Removal
1 Disconnect the battery negative (earth) lead
(refer to Chapter 5A, Section 1).
2 On CVH engine models, pull free and
release the accelerator cable from the locating
clip on the side of the air cleaner.
3 Undo the two (HCS engine) or three (CVH
engine) retaining screws, and partially lift the
air cleaner from the carburettor so that the
hose and wiring connections to the underside
of the air cleaner body are accessible (see
illustration) .
4 Note their connections and routings, then
detach the wiring multi-plug and hoses from
the underside of the air cleaner (see
illustrations) . On CVH engines, also
disconnect the vacuum hose from the inlet
manifold.
5 Lift the air cleaner from the carburettor.
6 If required, the inlet air temperature sensor
can be unscrewed and removed from the
base of the air cleaner (where fitted).
Refitting
7 Refit in the reverse order of removal. Renew
any hoses that are perished or cracked, and
ensure that all fittings are securely and
correctly reconnected.
Fuel system – carburettor engines 4A•3
2.4b Disconnecting the intake air temperature sensor multi-plug
(CVH engine shown)2.4a Disconnecting the oil separator/
crankcase ventilation hose from the air
cleaner (CVH engine shown)2.3 Undoing the air cleaner retainingscrews (HCS engine shown)
4A
1595Ford Fiesta Remakeprocarmanuals.com
http://vnx.su
Page 109 of 296
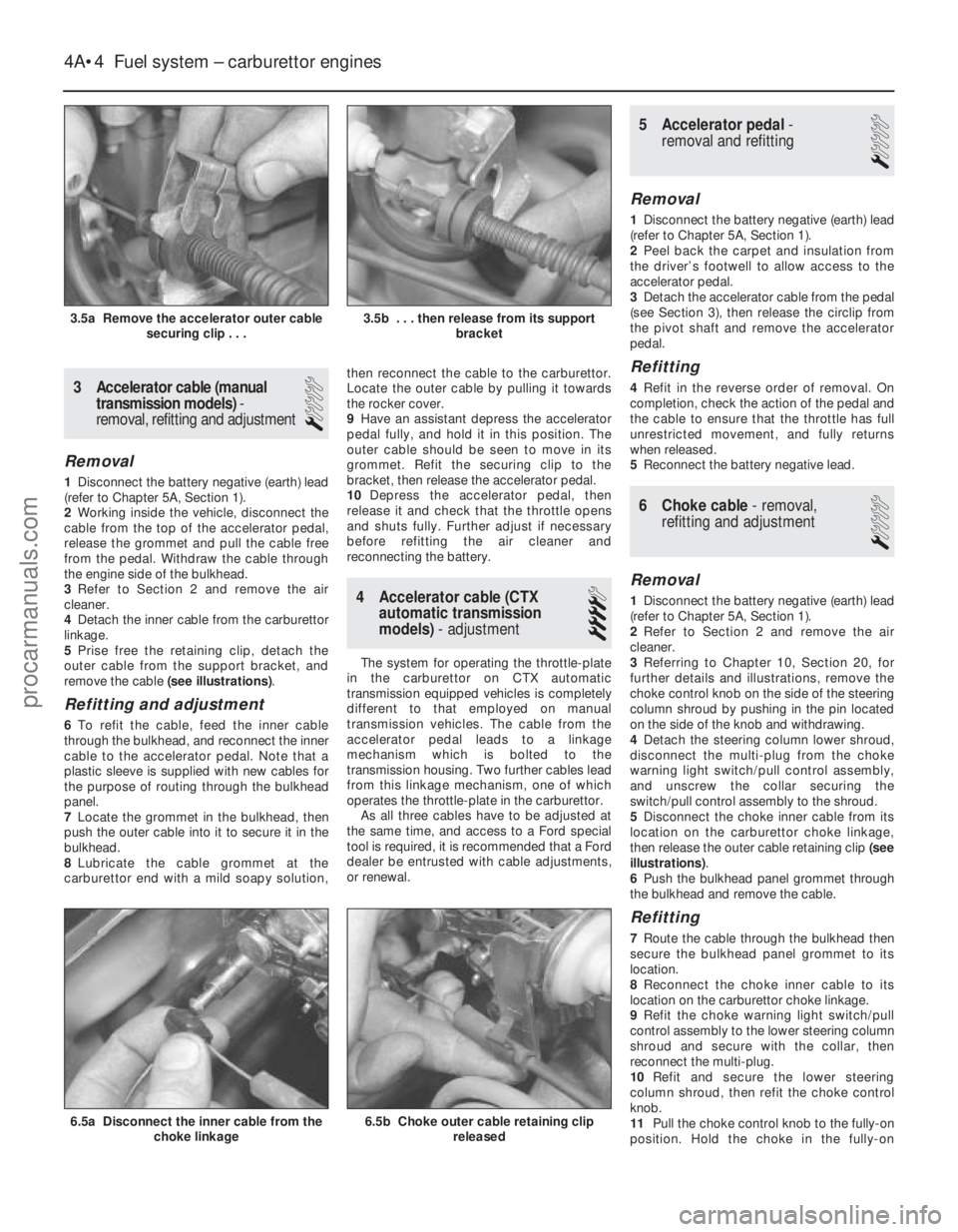
3Accelerator cable (manual
transmission models) -
removal, refitting and adjustment
1
Removal
1 Disconnect the battery negative (earth) lead
(refer to Chapter 5A, Section 1).
2 Working inside the vehicle, disconnect the
cable from the top of the accelerator pedal,
release the grommet and pull the cable free
from the pedal. Withdraw the cable through
the engine side of the bulkhead.
3 Refer to Section 2 and remove the air
cleaner.
4 Detach the inner cable from the carburettor
linkage.
5 Prise free the retaining clip, detach the
outer cable from the support bracket, and
remove the cable (see illustrations) .
Refitting and adjustment
6To refit the cable, feed the inner cable
through the bulkhead, and reconnect the inner
cable to the accelerator pedal. Note that a
plastic sleeve is supplied with new cables for
the purpose of routing through the bulkhead
panel.
7 Locate the grommet in the bulkhead, then
push the outer cable into it to secure it in the
bulkhead.
8 Lubricate the cable grommet at the
carburettor end with a mild soapy solution, then reconnect the cable to the carburettor.
Locate the outer cable by pulling it towards
the rocker cover.
9
Have an assistant depress the accelerator
pedal fully, and hold it in this position. The
outer cable should be seen to move in its
grommet. Refit the securing clip to the
bracket, then release the accelerator pedal.
10 Depress the accelerator pedal, then
release it and check that the throttle opens
and shuts fully. Further adjust if necessary
before refitting the air cleaner and
reconnecting the battery.
4 Accelerator cable (CTX automatic transmission
models) - adjustment
4
The system for operating the throttle-plate
in the carburettor on CTX automatic
transmission equipped vehicles is completely
different to that employed on manual
transmission vehicles. The cable from the
accelerator pedal leads to a linkage
mechanism which is bolted to the
transmission housing. Two further cables lead
from this linkage mechanism, one of which
operates the throttle-plate in the carburettor. As all three cables have to be adjusted at
the same time, and access to a Ford special
tool is required, it is recommended that a Ford
dealer be entrusted with cable adjustments,
or renewal.
5 Accelerator pedal -
removal and refitting
1
Removal
1 Disconnect the battery negative (earth) lead
(refer to Chapter 5A, Section 1).
2 Peel back the carpet and insulation from
the driver’s footwell to allow access to the
accelerator pedal.
3 Detach the accelerator cable from the pedal
(see Section 3), then release the circlip from
the pivot shaft and remove the accelerator
pedal.
Refitting
4 Refit in the reverse order of removal. On
completion, check the action of the pedal and
the cable to ensure that the throttle has full
unrestricted movement, and fully returns
when released.
5 Reconnect the battery negative lead.
6 Choke cable - removal,
refitting and adjustment
1
Removal
1 Disconnect the battery negative (earth) lead
(refer to Chapter 5A, Section 1).
2 Refer to Section 2 and remove the air
cleaner.
3 Referring to Chapter 10, Section 20, for
further details and illustrations, remove the
choke control knob on the side of the steering
column shroud by pushing in the pin located
on the side of the knob and withdrawing.
4 Detach the steering column lower shroud,
disconnect the multi-plug from the choke
warning light switch/pull control assembly,
and unscrew the collar securing the
switch/pull control assembly to the shroud.
5 Disconnect the choke inner cable from its
location on the carburettor choke linkage,
then release the outer cable retaining clip (see
illustrations) .
6 Push the bulkhead panel grommet through
the bulkhead and remove the cable.
Refitting
7 Route the cable through the bulkhead then
secure the bulkhead panel grommet to its
location.
8 Reconnect the choke inner cable to its
location on the carburettor choke linkage.
9 Refit the choke warning light switch/pull
control assembly to the lower steering column
shroud and secure with the collar, then
reconnect the multi-plug.
10 Refit and secure the lower steering
column shroud, then refit the choke control
knob.
11 Pull the choke control knob to the fully-on
position. Hold the choke in the fully-on
4A•4 Fuel system – carburettor engines
6.5b Choke outer cable retaining clip
released6.5a Disconnect the inner cable from thechoke linkage
3.5b . . . then release from its support bracket3.5a Remove the accelerator outer cablesecuring clip . . .
1595Ford Fiesta Remakeprocarmanuals.com
http://vnx.su
Page 110 of 296
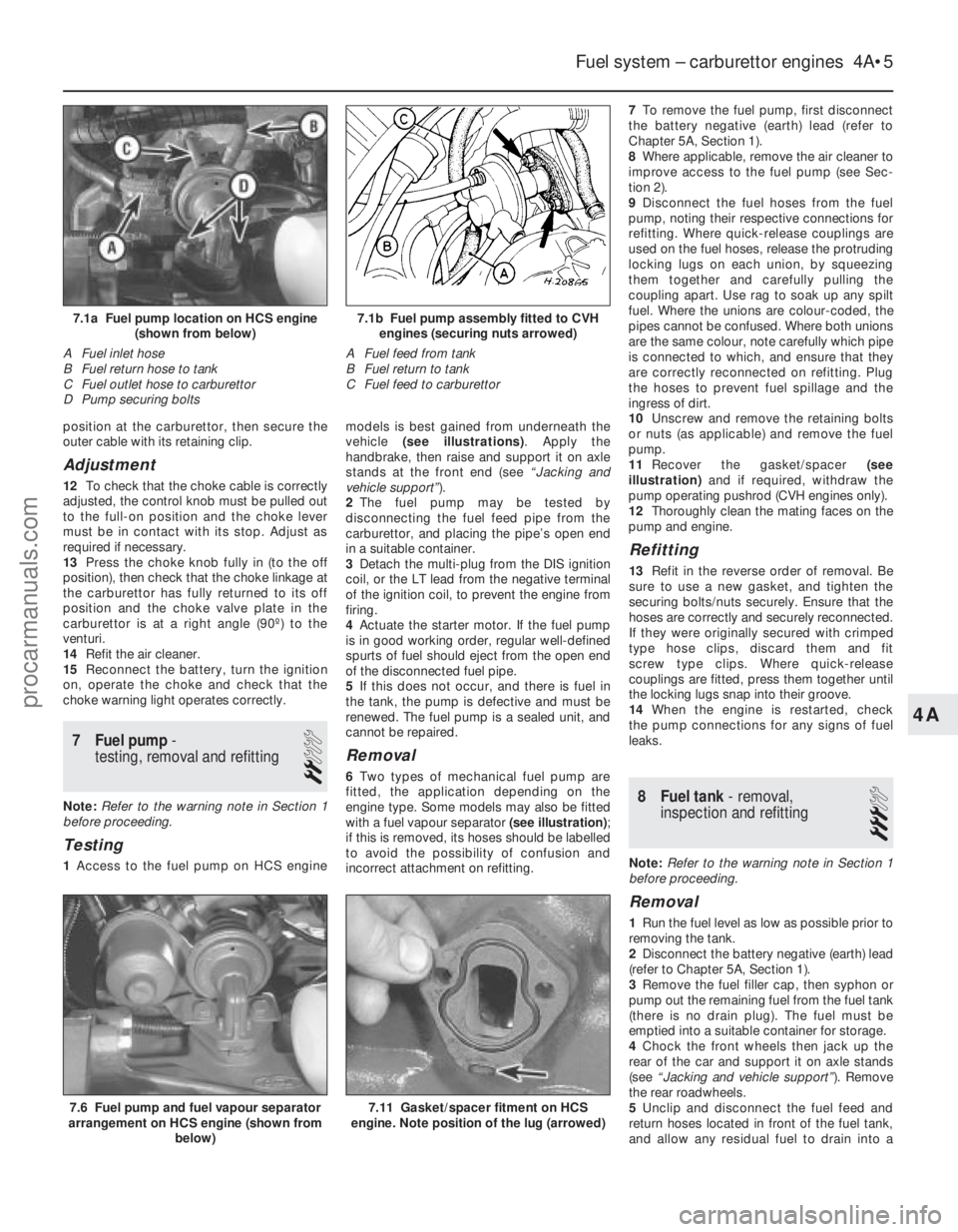
position at the carburettor, then secure the
outer cable with its retaining clip.
Adjustment
12To check that the choke cable is correctly
adjusted, the control knob must be pulled out
to the full-on position and the choke lever
must be in contact with its stop. Adjust as
required if necessary.
13 Press the choke knob fully in (to the off
position), then check that the choke linkage at
the carburettor has fully returned to its off
position and the choke valve plate in the
carburettor is at a right angle (90º) to the
venturi.
14 Refit the air cleaner.
15 Reconnect the battery, turn the ignition
on, operate the choke and check that the
choke warning light operates correctly.
7 Fuel pump -
testing, removal and refitting
2
Note: Refer to the warning note in Section 1
before proceeding.
Testing
1 Access to the fuel pump on HCS engine models is best gained from underneath the
vehicle
(see illustrations) . Apply the
handbrake, then raise and support it on axle
stands at the front end (see “Jacking and
vehicle support” ).
2 The fuel pump may be tested by
disconnecting the fuel feed pipe from the
carburettor, and placing the pipe’s open end
in a suitable container.
3 Detach the multi-plug from the DIS ignition
coil, or the LT lead from the negative terminal
of the ignition coil, to prevent the engine from
firing.
4 Actuate the starter motor. If the fuel pump
is in good working order, regular well-defined
spurts of fuel should eject from the open end
of the disconnected fuel pipe.
5 If this does not occur, and there is fuel in
the tank, the pump is defective and must be
renewed. The fuel pump is a sealed unit, and
cannot be repaired.
Removal
6 Two types of mechanical fuel pump are
fitted, the application depending on the
engine type. Some models may also be fitted
with a fuel vapour separator (see illustration) ;
if this is removed, its hoses should be labelled
to avoid the possibility of confusion and
incorrect attachment on refitting. 7
To remove the fuel pump, first disconnect
the battery negative (earth) lead (refer to
Chapter 5A, Section 1).
8 Where applicable, remove the air cleaner to
improve access to the fuel pump (see Sec-
tion 2).
9 Disconnect the fuel hoses from the fuel
pump, noting their respective connections for
refitting. Where quick-release couplings are
used on the fuel hoses, release the protruding
locking lugs on each union, by squeezing
them together and carefully pulling the
coupling apart. Use rag to soak up any spilt
fuel. Where the unions are colour-coded, the
pipes cannot be confused. Where both unions
are the same colour, note carefully which pipe
is connected to which, and ensure that they
are correctly reconnected on refitting. Plug
the hoses to prevent fuel spillage and the
ingress of dirt.
10 Unscrew and remove the retaining bolts
or nuts (as applicable) and remove the fuel
pump.
11 Recover the gasket/spacer (see
illustration) and if required, withdraw the
pump operating pushrod (CVH engines only).
12 Thoroughly clean the mating faces on the
pump and engine.
Refitting
13 Refit in the reverse order of removal. Be
sure to use a new gasket, and tighten the
securing bolts/nuts securely. Ensure that the
hoses are correctly and securely reconnected.
If they were originally secured with crimped
type hose clips, discard them and fit
screw type clips. Where quick-release
couplings are fitted, press them together until
the locking lugs snap into their groove.
14 When the engine is restarted, check
the pump connections for any signs of fuel
leaks.
8 Fuel tank - removal,
inspection and refitting
3
Note: Refer to the warning note in Section 1
before proceeding.
Removal
1 Run the fuel level as low as possible prior to
removing the tank.
2 Disconnect the battery negative (earth) lead
(refer to Chapter 5A, Section 1).
3 Remove the fuel filler cap, then syphon or
pump out the remaining fuel from the fuel tank
(there is no drain plug). The fuel must be
emptied into a suitable container for storage.
4 Chock the front wheels then jack up the
rear of the car and support it on axle stands
(see “Jacking and vehicle support” ). Remove
the rear roadwheels.
5 Unclip and disconnect the fuel feed and
return hoses located in front of the fuel tank,
and allow any residual fuel to drain into a
Fuel system – carburettor engines 4A•5
7.6 Fuel pump and fuel vapour separator
arrangement on HCS engine (shown from
below)
7.1b Fuel pump assembly fitted to CVHengines (securing nuts arrowed)
A Fuel feed from tank
B Fuel return to tank
C Fuel feed to carburettor7.1a Fuel pump location on HCS engine (shown from below)
A Fuel inlet hose
B Fuel return hose to tank
C Fuel outlet hose to carburettor
D Pump securing bolts
7.11 Gasket/spacer fitment on HCS
engine. Note position of the lug (arrowed)
4A
1595Ford Fiesta Remakeprocarmanuals.com
http://vnx.su