ECU GEELY CK 2008 User Guide
[x] Cancel search | Manufacturer: GEELY, Model Year: 2008, Model line: CK, Model: GEELY CK 2008Pages: 392, PDF Size: 38.86 MB
Page 88 of 392
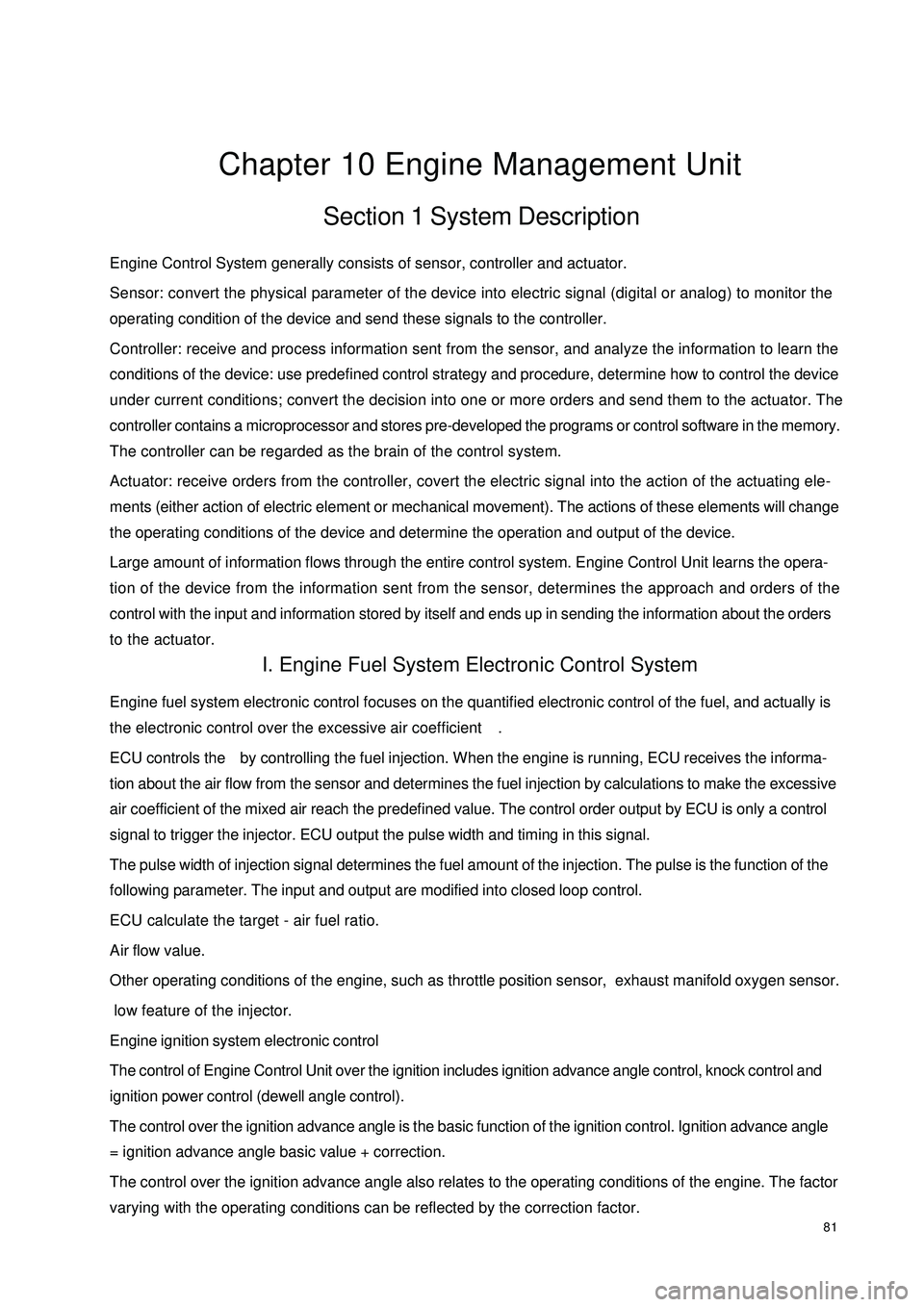
81Chapter 10 Engine Management UnitSection 1 System DescriptionEngine Control System generally consists of sensor, controller and actuator.
Sensor: convert the physical parameter of the device into electric signal (digital or analog) to monitor the
operating condition of the device and send these signals to the controller.
Controller: receive and process information sent from the sensor, and analyze the information to learn the
conditions of the device: use predefined control strategy and procedure, determine how to control the device
under current conditions; convert the decision into one or more orders and send them to the actuator. The
controller contains a microprocessor and stores pre-developed the programs or control software in the memory.
The controller can be regarded as the brain of the control system.
Actuator: receive orders from the controller, covert the electric signal into the action of the actuating ele-
ments (either action of electric element or mechanical movement). The actions of these elements will change
the operating conditions of the device and determine the operation and output of the device.
Large amount of information flows through the entire control system. Engine Control Unit learns the opera-
tion of the device from the information sent from the sensor, determines the approach and orders of the
control with the input and information stored by itself and ends up in sending the information about the orders
to the actuator.I. Engine Fuel System Electronic Control SystemEngine fuel system electronic control focuses on the quantified electronic control of the fuel, and actually is
the electronic control over the excessive air coefficient .
ECU controls the by controlling the fuel injection. When the engine is running, ECU receives the informa-
tion about the air flow from the sensor and determines the fuel injection by calculations to make the excessive
air coefficient of the mixed air reach the predefined value. The control order output by ECU is only a control
signal to trigger the injector. ECU output the pulse width and timing in this signal.
The pulse width of injection signal determines the fuel amount of the injection. The pulse is the function of the
following parameter. The input and output are modified into closed loop control.
ECU calculate the target - air fuel ratio.
Air flow value.
Other operating conditions of the engine, such as throttle position sensor, exhaust manifold oxygen sensor.
low feature of the injector.
Engine ignition system electronic control
The control of Engine Control Unit over the ignition includes ignition advance angle control, knock control and
ignition power control (dewell angle control).
The control over the ignition advance angle is the basic function of the ignition control. Ignition advance angle
= ignition advance angle basic value + correction.
The control over the ignition advance angle also relates to the operating conditions of the engine. The factor
varying with the operating conditions can be reflected by the correction factor.
Page 89 of 392
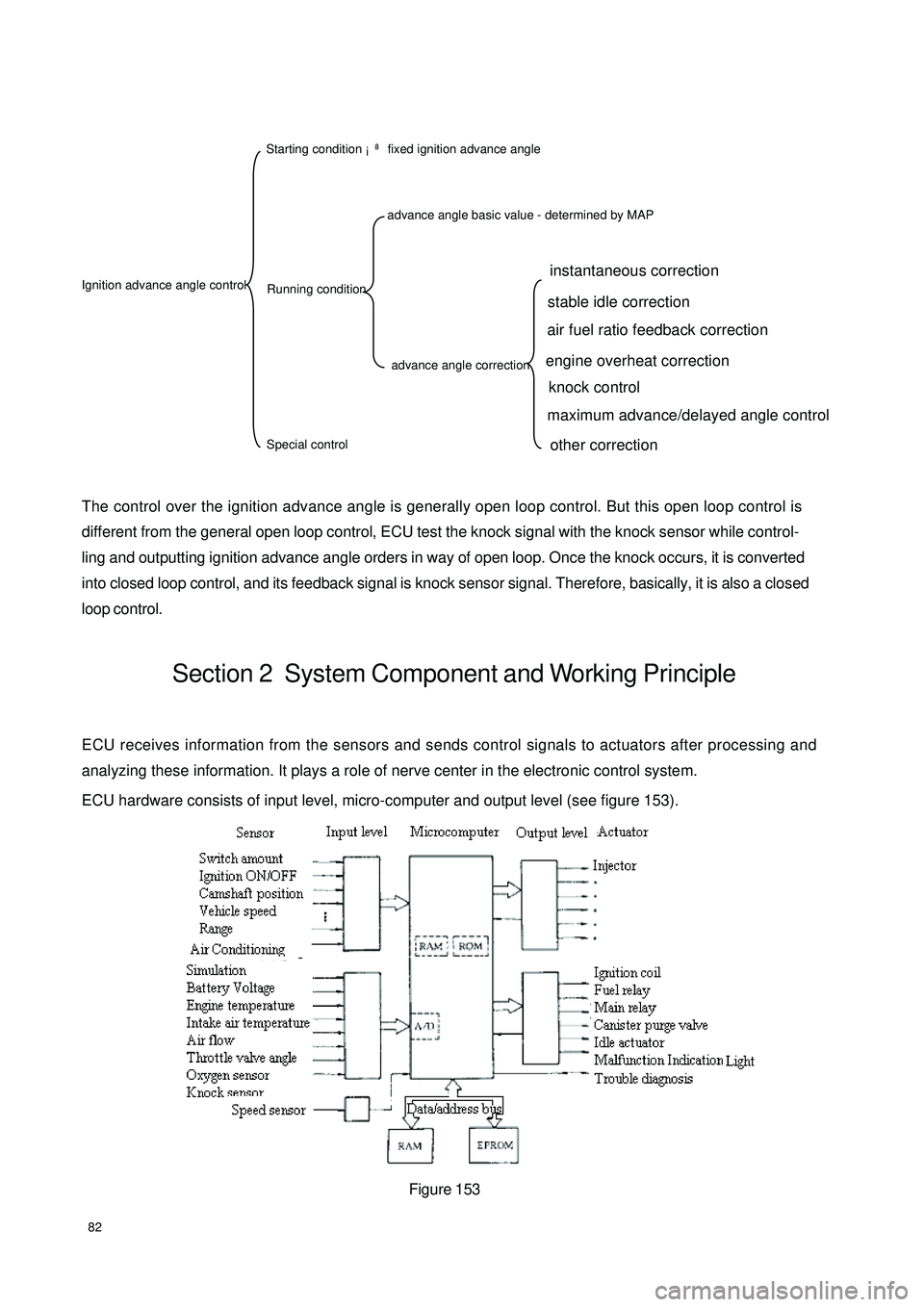
82The control over the ignition advance angle is generally open loop control. But this open loop control is
different from the general open loop control, ECU test the knock signal with the knock sensor while control-
ling and outputting ignition advance angle orders in way of open loop. Once the knock occurs, it is converted
into closed loop control, and its feedback signal is knock sensor signal. Therefore, basically, it is also a closed
loop control.Section 2 System Component and Working PrincipleECU receives information from the sensors and sends control signals to actuators after processing and
analyzing these information. It plays a role of nerve center in the electronic control system.
ECU hardware consists of input level, micro-computer and output level (see figure 153).
Figure 153Ignition advance angle control Starting condition ¡ª fixed ignition advance angle
Running conditionSpecial controladvance angle basic value - determined by MAPadvance angle correctioninstantaneous correction
stable idle correction
air fuel ratio feedback correction
engine overheat correction
knock control
maximum advance/delayed angle controlother correction
Page 90 of 392
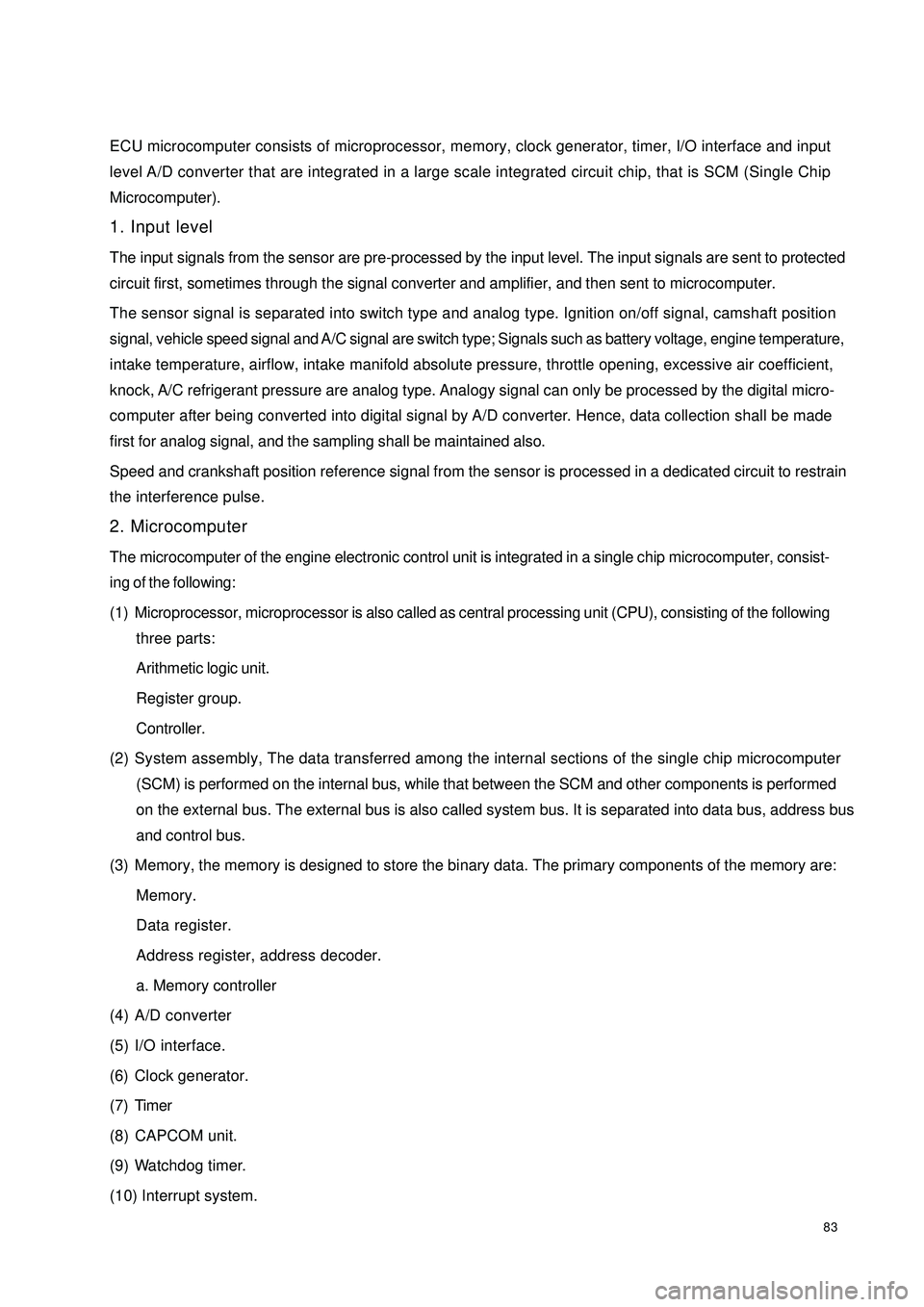
83ECU microcomputer consists of microprocessor, memory, clock generator, timer, I/O interface and input
level A/D converter that are integrated in a large scale integrated circuit chip, that is SCM (Single Chip
Microcomputer).
1. Input level
The input signals from the sensor are pre-processed by the input level. The input signals are sent to protected
circuit first, sometimes through the signal converter and amplifier, and then sent to microcomputer.
The sensor signal is separated into switch type and analog type. Ignition on/off signal, camshaft position
signal, vehicle speed signal and A/C signal are switch type; Signals such as battery voltage, engine temperature,
intake temperature, airflow, intake manifold absolute pressure, throttle opening, excessive air coefficient,
knock, A/C refrigerant pressure are analog type. Analogy signal can only be processed by the digital micro-
computer after being converted into digital signal by A/D converter. Hence, data collection shall be made
first for analog signal, and the sampling shall be maintained also.
Speed and crankshaft position reference signal from the sensor is processed in a dedicated circuit to restrain
the interference pulse.
2. Microcomputer
The microcomputer of the engine electronic control unit is integrated in a single chip microcomputer, consist-
ing of the following:
(1) Microprocessor, microprocessor is also called as central processing unit (CPU), consisting of the following
three parts:
Arithmetic logic unit.
Register group.
Controller.
(2) System assembly, The data transferred among the internal sections of the single chip microcomputer
(SCM) is performed on the internal bus, while that between the SCM and other components is performed
on the external bus. The external bus is also called system bus. It is separated into data bus, address bus
and control bus.
(3) Memory, the memory is designed to store the binary data. The primary components of the memory are:
Memory.
Data register.
Address register, address decoder.
a. Memory controller
(4) A/D converter
(5) I/O interface.
(6) Clock generator.
(7) Timer
(8) CAPCOM unit.
(9) Watchdog timer.
(10) Interrupt system.
Page 91 of 392
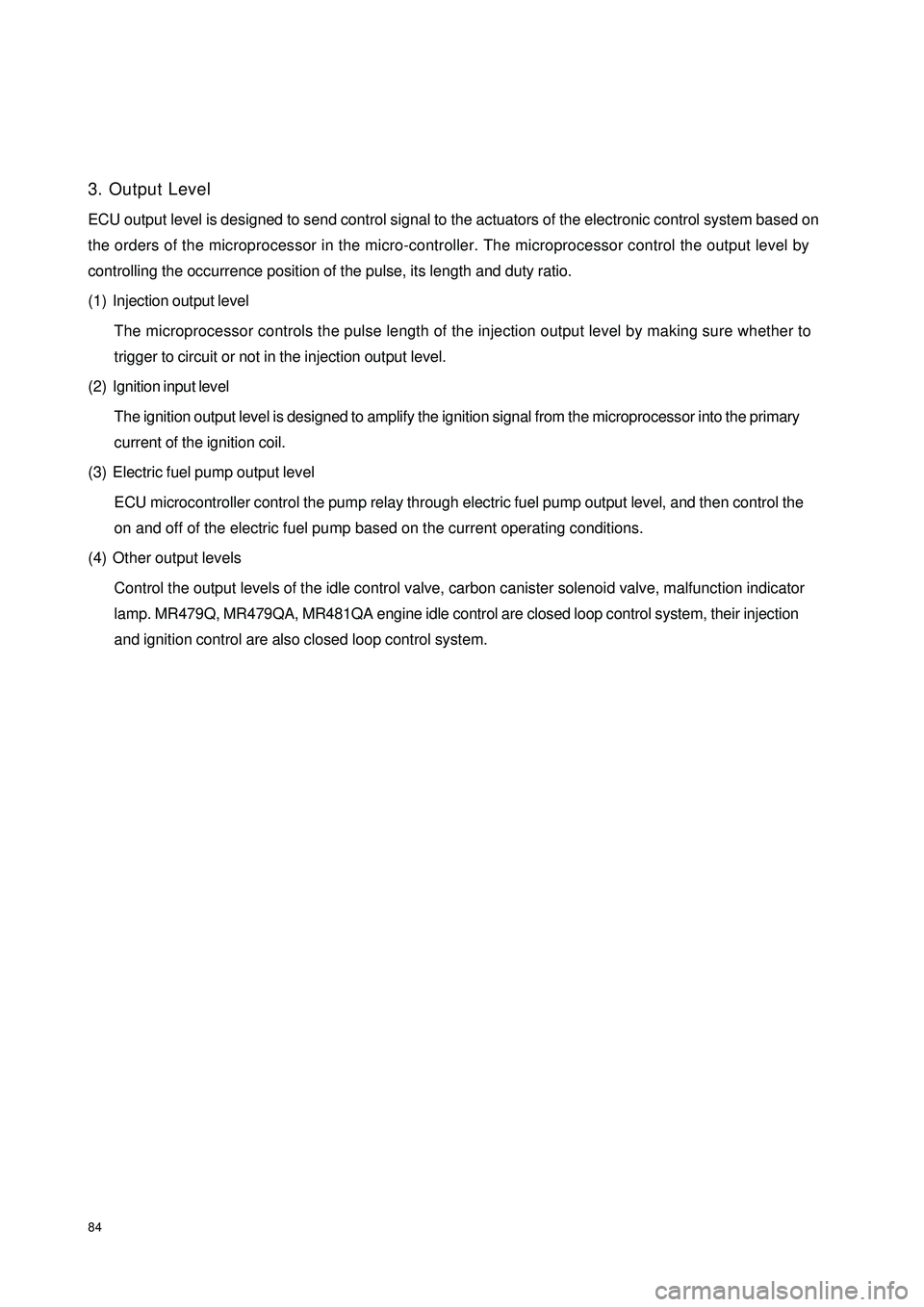
843. Output Level
ECU output level is designed to send control signal to the actuators of the electronic control system based on
the orders of the microprocessor in the micro-controller. The microprocessor control the output level by
controlling the occurrence position of the pulse, its length and duty ratio.
(1) Injection output level
The microprocessor controls the pulse length of the injection output level by making sure whether to
trigger to circuit or not in the injection output level.
(2) Ignition input level
The ignition output level is designed to amplify the ignition signal from the microprocessor into the primary
current of the ignition coil.
(3) Electric fuel pump output level
ECU microcontroller control the pump relay through electric fuel pump output level, and then control the
on and off of the electric fuel pump based on the current operating conditions.
(4) Other output levels
Control the output levels of the idle control valve, carbon canister solenoid valve, malfunction indicator
lamp. MR479Q, MR479QA, MR481QA engine idle control are closed loop control system, their injection
and ignition control are also closed loop control system.
Page 94 of 392
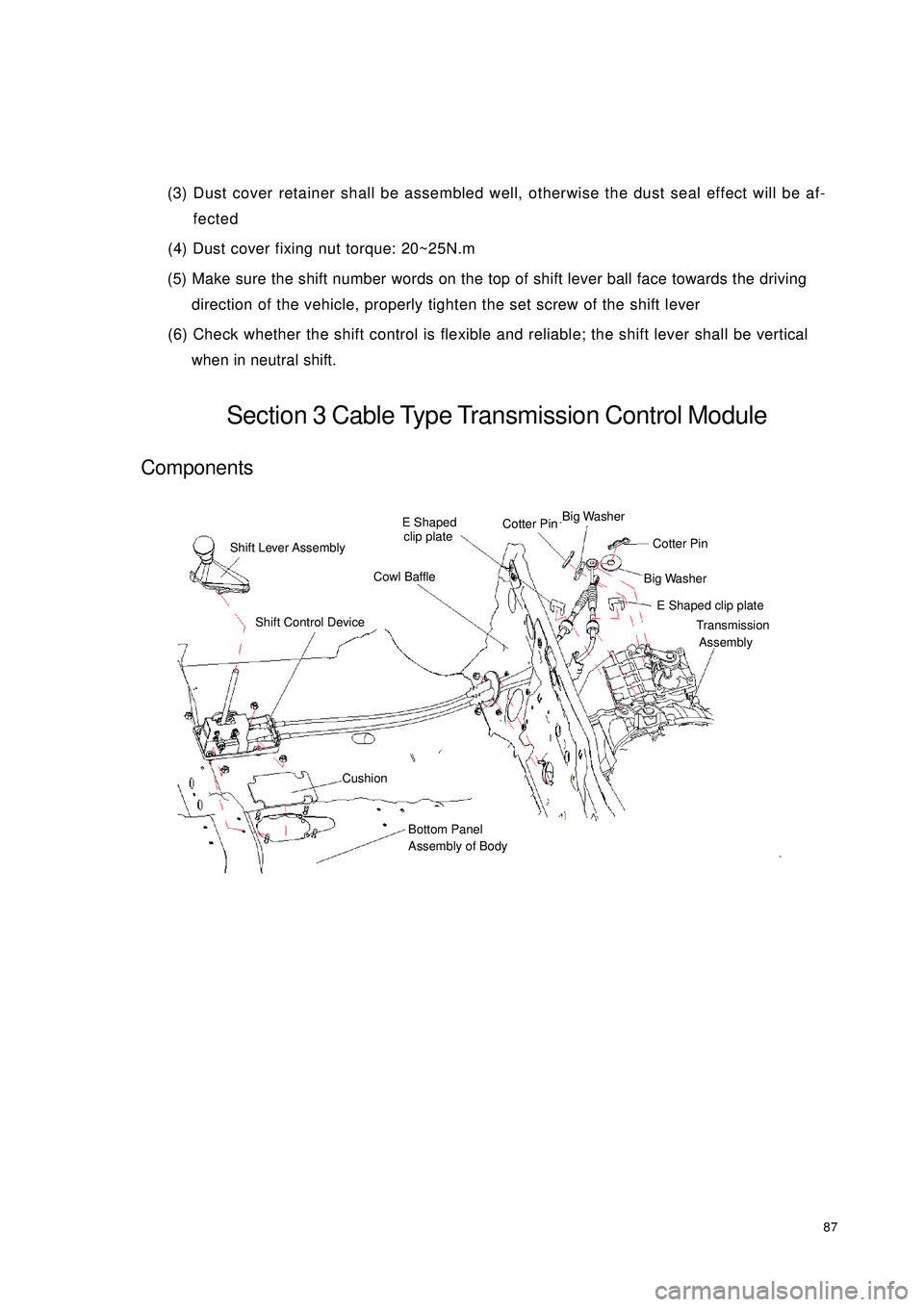
87(3) Dust cover retainer shall be assembled well, otherwise the dust seal effect will be af-
fected
(4) Dust cover fixing nut torque: 20~25N.m
(5) Make sure the shift number words on the top of shift lever ball face towards the driving
direction of the vehicle, properly tighten the set screw of the shift lever
(6) Check whether the shift control is flexible and reliable; the shift lever shall be vertical
when in neutral shift.Section 3 Cable Type Transmission Control ModuleComponentsShift Lever AssemblyE Shaped
clip plateCotter PinBig Washer Big Washer Cotter PinE Shaped clip plateTransmission
AssemblyCowl BaffleShift Control DeviceCushionBottom Panel
Assembly of Body
Page 110 of 392
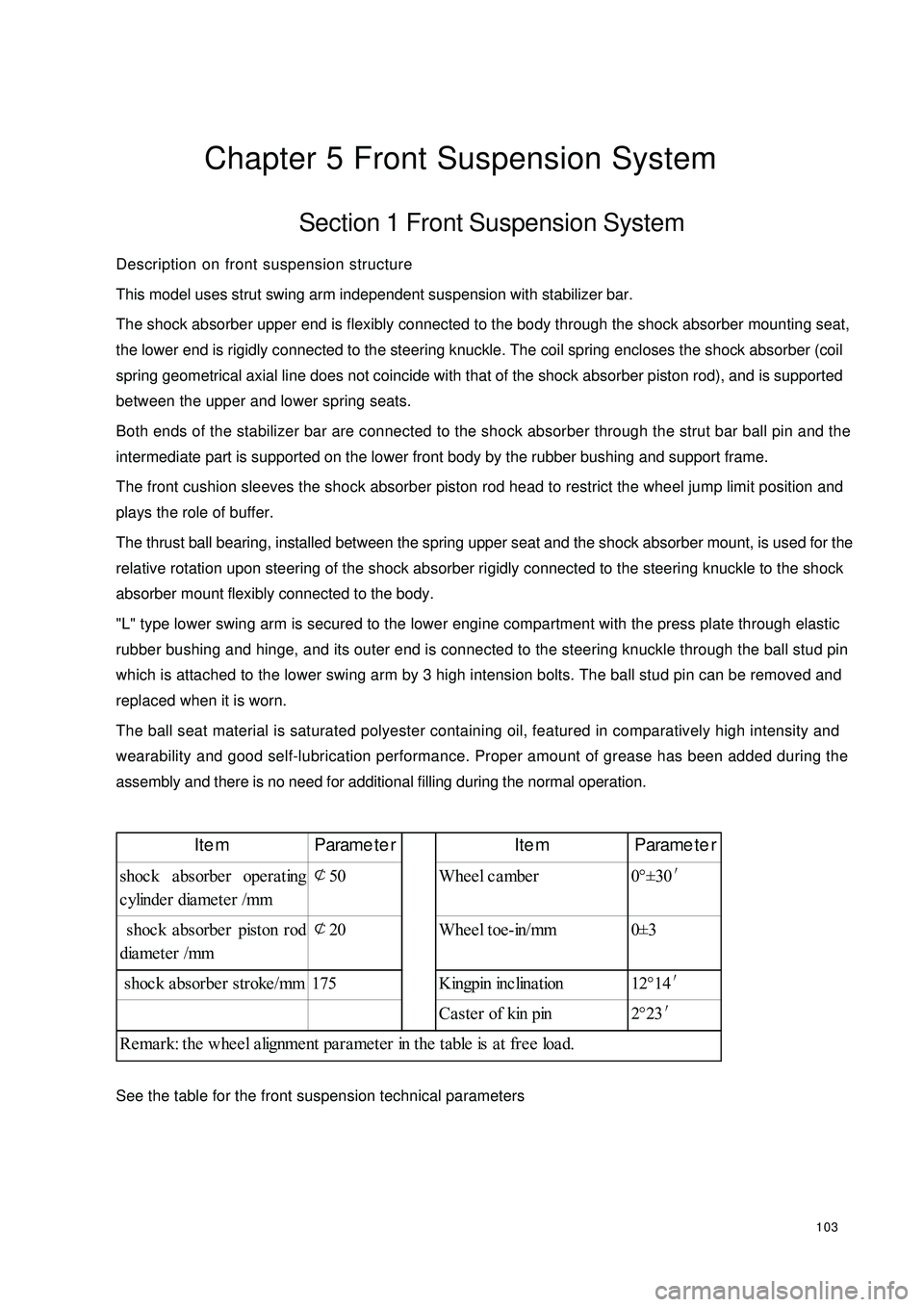
103Chapter 5 Front Suspension SystemSection 1 Front Suspension SystemDescription on front suspension structure
This model uses strut swing arm independent suspension with stabilizer bar.
The shock absorber upper end is flexibly connected to the body through the shock absorber mounting seat,
the lower end is rigidly connected to the steering knuckle. The coil spring encloses the shock absorber (coil
spring geometrical axial line does not coincide with that of the shock absorber piston rod), and is supported
between the upper and lower spring seats.
Both ends of the stabilizer bar are connected to the shock absorber through the strut bar ball pin and the
intermediate part is supported on the lower front body by the rubber bushing and support frame.
The front cushion sleeves the shock absorber piston rod head to restrict the wheel jump limit position and
plays the role of buffer.
The thrust ball bearing, installed between the spring upper seat and the shock absorber mount, is used for the
relative rotation upon steering of the shock absorber rigidly connected to the steering knuckle to the shock
absorber mount flexibly connected to the body.
"L" type lower swing arm is secured to the lower engine compartment with the press plate through elastic
rubber bushing and hinge, and its outer end is connected to the steering knuckle through the ball stud pin
which is attached to the lower swing arm by 3 high intension bolts. The ball stud pin can be removed and
replaced when it is worn.
The ball seat material is saturated polyester containing oil, featured in comparatively high intensity and
wearability and good self-lubrication performance. Proper amount of grease has been added during the
assembly and there is no need for additional filling during the normal operation.
See the table for the front suspension technical parametersItem Parameter Item Parameter
shoc k a bsorbe r ope ra ting
cylinder diameter /mm¢
50 Wheel camber 0°±30′
shoc k a bsorbe r piston rod
diameter /mm¢
20 Wheel toe-in/mm 0±3
shoc k a bsorbe r stroke /mm 175 Kingpin inc lina tion 12°14′
Ca ste r of kin pin 2°23′
Remark: the wheel alignment parameter in the table is at free load.
Page 116 of 392
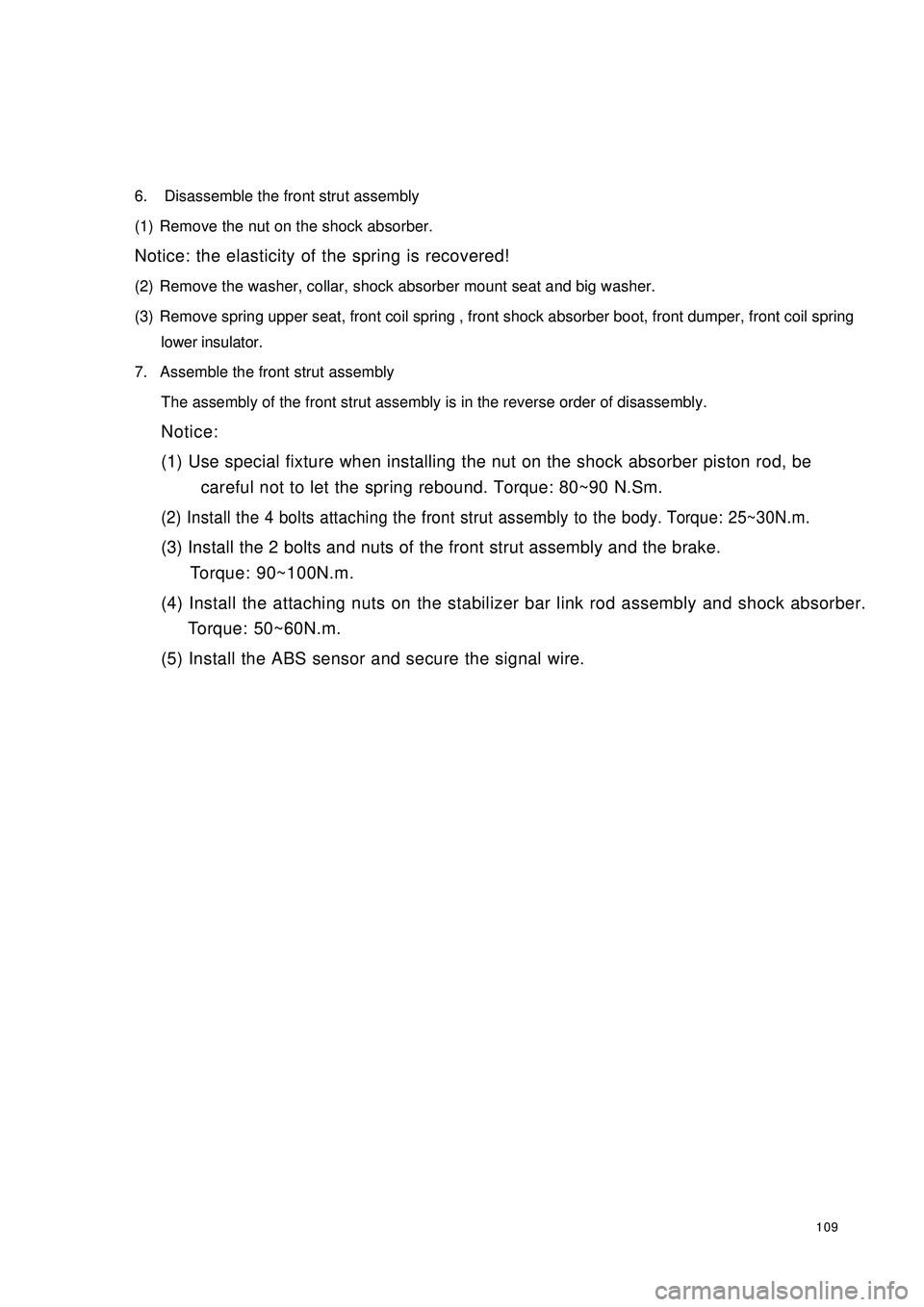
1096. Disassemble the front strut assembly
(1) Remove the nut on the shock absorber.
Notice: the elasticity of the spring is recovered!
(2) Remove the washer, collar, shock absorber mount seat and big washer.
(3) Remove spring upper seat, front coil spring , front shock absorber boot, front dumper, front coil spring
lower insulator.
7. Assemble the front strut assembly
The assembly of the front strut assembly is in the reverse order of disassembly.
Notice:
(1) Use special fixture when installing the nut on the shock absorber piston rod, be
careful not to let the spring rebound. Torque: 80~90 N.Sm.(2) Install the 4 bolts attaching the front strut assembly to the body. Torque: 25~30N.m.(3) Install the 2 bolts and nuts of the front strut assembly and the brake.
Torque: 90~100N.m.
(4) Install the attaching nuts on the stabilizer bar link rod assembly and shock absorber.
Torque: 50~60N.m.
(5) Install the ABS sensor and secure the signal wire.
Page 119 of 392
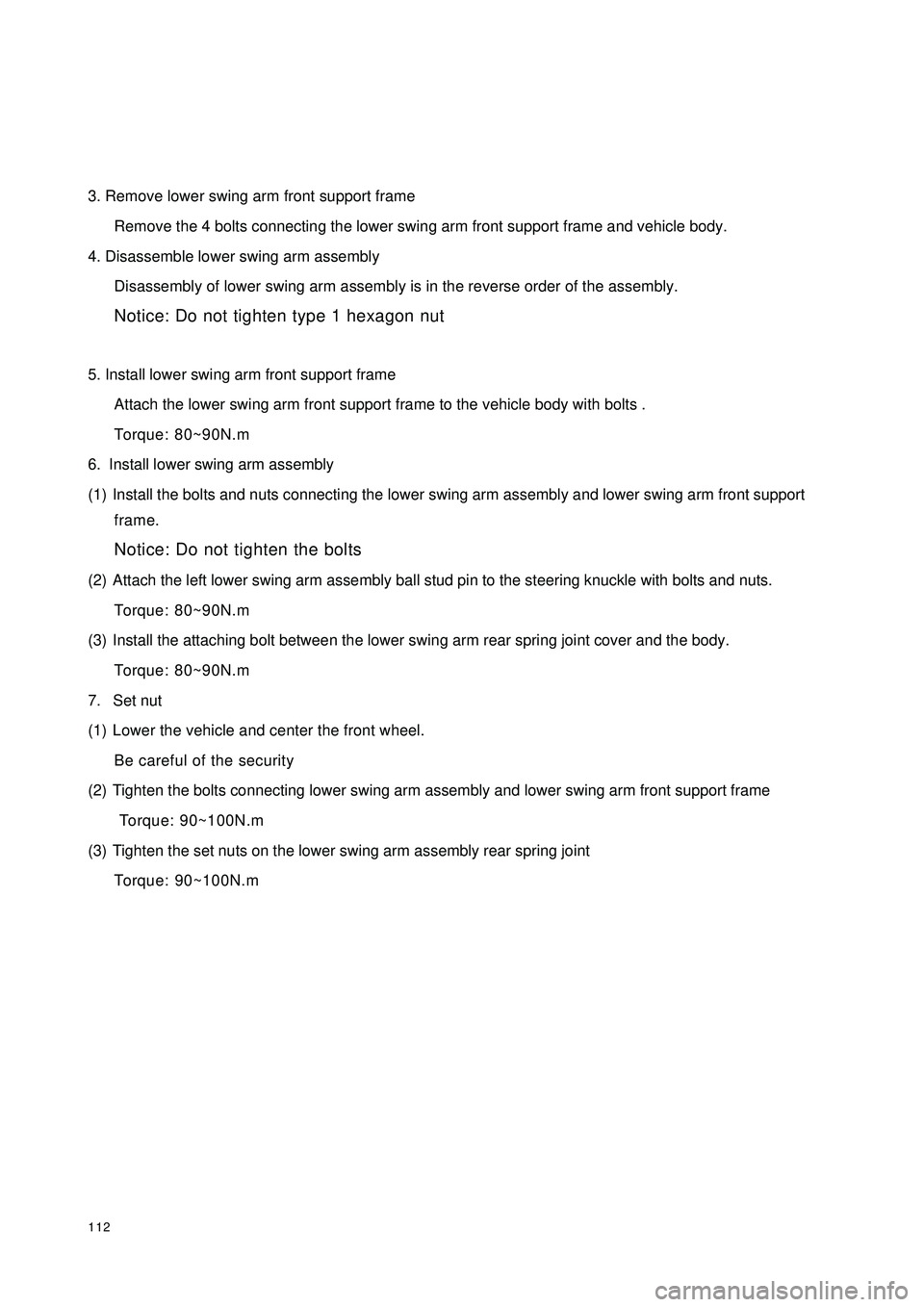
1123. Remove lower swing arm front support frame
Remove the 4 bolts connecting the lower swing arm front support frame and vehicle body.
4. Disassemble lower swing arm assembly
Disassembly of lower swing arm assembly is in the reverse order of the assembly.
Notice: Do not tighten type 1 hexagon nut
5. Install lower swing arm front support frame
Attach the lower swing arm front support frame to the vehicle body with bolts .
Torque: 80~90N.m
6. Install lower swing arm assembly
(1) Install the bolts and nuts connecting the lower swing arm assembly and lower swing arm front support
frame.
Notice: Do not tighten the bolts
(2) Attach the left lower swing arm assembly ball stud pin to the steering knuckle with bolts and nuts.
Torque: 80~90N.m
(3) Install the attaching bolt between the lower swing arm rear spring joint cover and the body.
Torque: 80~90N.m
7. Set nut
(1) Lower the vehicle and center the front wheel.
Be careful of the security
(2) Tighten the bolts connecting lower swing arm assembly and lower swing arm front support frame
Torque: 90~100N.m
(3) Tighten the set nuts on the lower swing arm assembly rear spring joint
Torque: 90~100N.m
Page 126 of 392
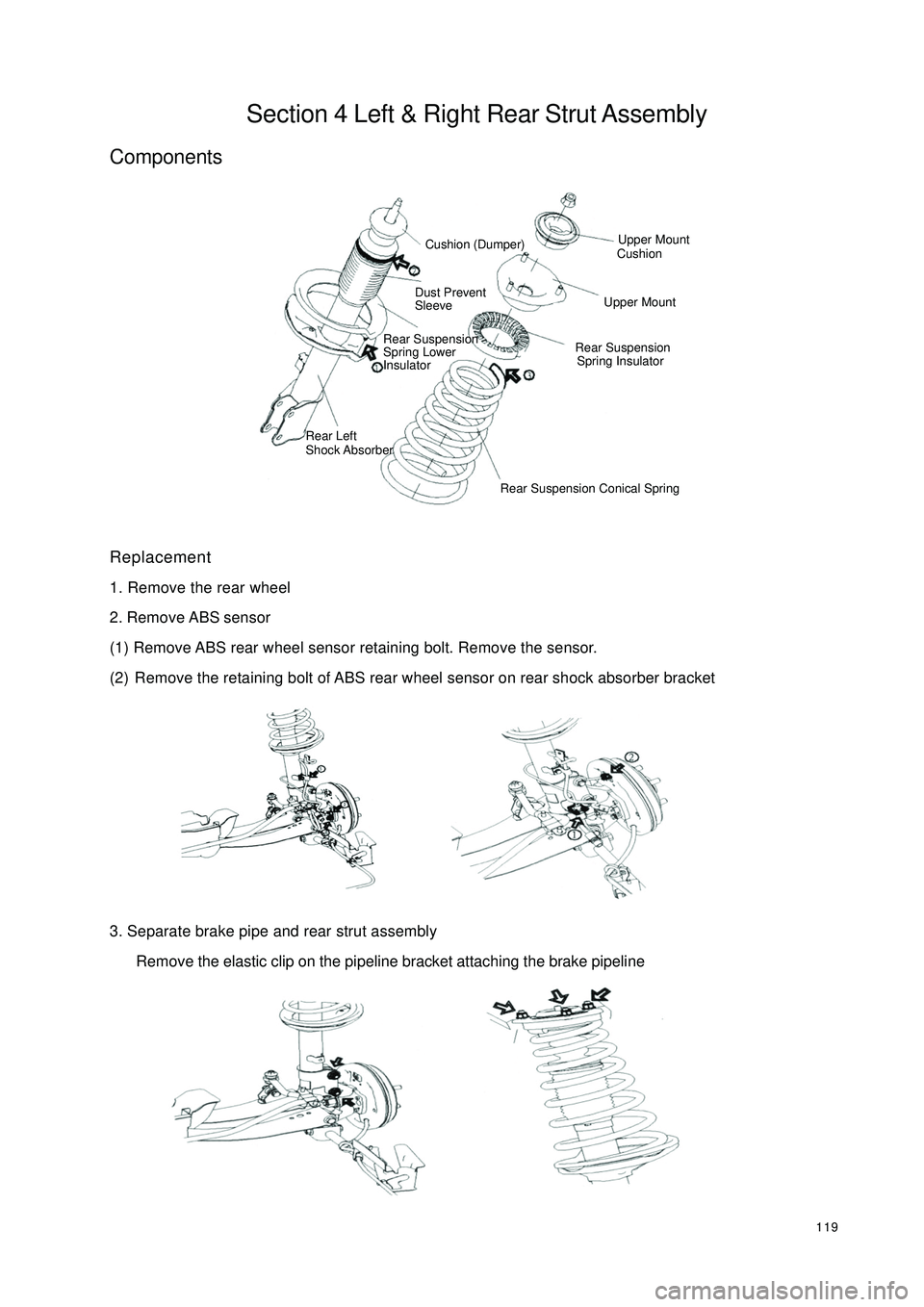
119Section 4 Left & Right Rear Strut AssemblyComponentsReplacement
1. Remove the rear wheel
2. Remove ABS sensor
(1) Remove ABS rear wheel sensor retaining bolt. Remove the sensor.
(2) Remove the retaining bolt of ABS rear wheel sensor on rear shock absorber bracket
3. Separate brake pipe and rear strut assembly
Remove the elastic clip on the pipeline bracket attaching the brake pipelineCushion (Dumper)Dust Prevent
SleeveRear Suspension
Spring Lower
InsulatorRear Left
Shock Absorber Upper Mount
CushionUpper MountRear Suspension
Spring Insulator
Rear Suspension Conical Spring
Page 127 of 392
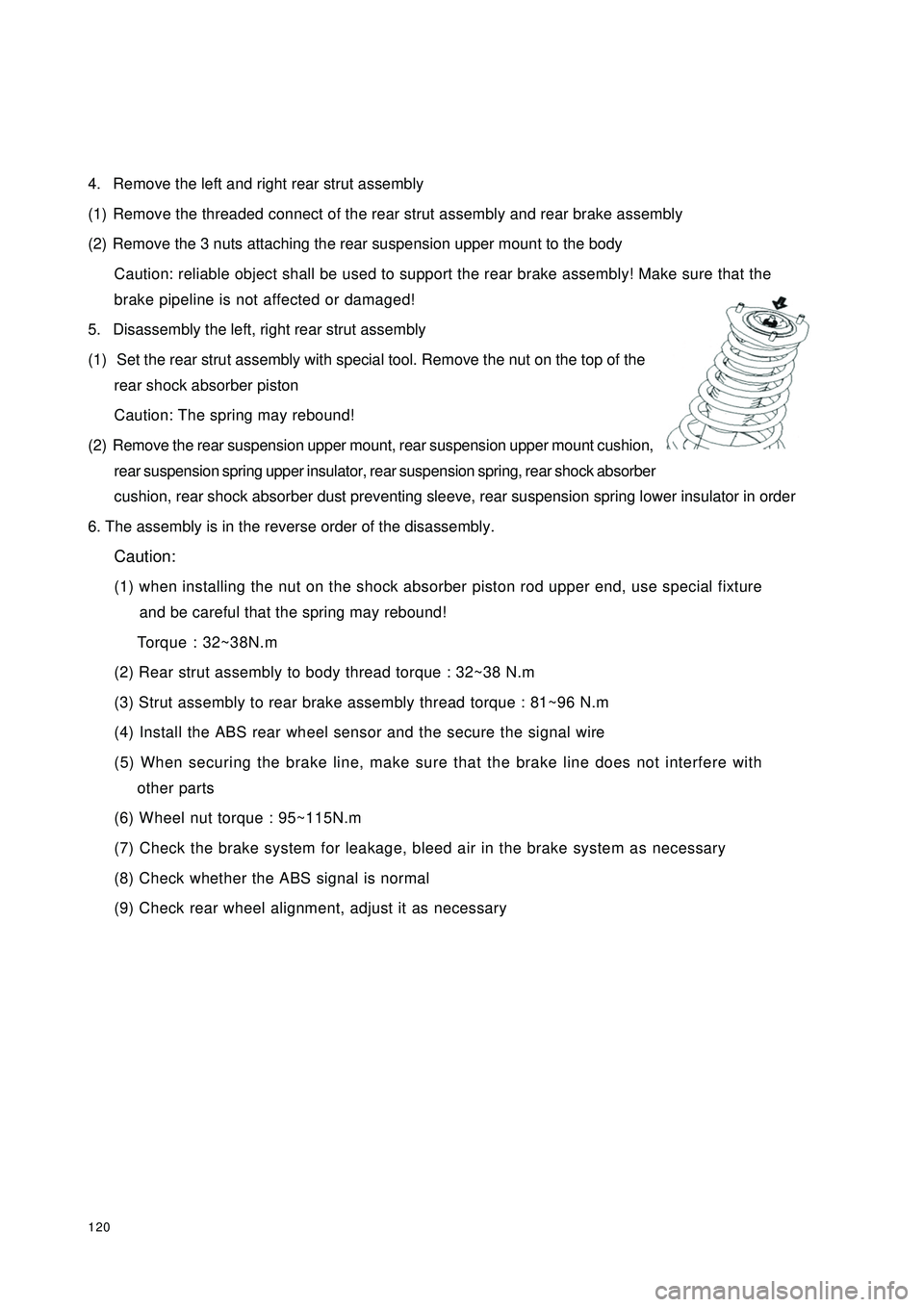
1204. Remove the left and right rear strut assembly
(1) Remove the threaded connect of the rear strut assembly and rear brake assembly
(2) Remove the 3 nuts attaching the rear suspension upper mount to the body
Caution: reliable object shall be used to support the rear brake assembly! Make sure that the
brake pipeline is not affected or damaged!
5. Disassembly the left, right rear strut assembly
(1) Set the rear strut assembly with special tool. Remove the nut on the top of the
rear shock absorber piston
Caution: The spring may rebound!
(2) Remove the rear suspension upper mount, rear suspension upper mount cushion,
rear suspension spring upper insulator, rear suspension spring, rear shock absorber
cushion, rear shock absorber dust preventing sleeve, rear suspension spring lower insulator in order
6. The assembly is in the reverse order of the disassembly.
Caution:
(1) when installing the nut on the shock absorber piston rod upper end, use special fixture
and be careful that the spring may rebound!
Torque : 32~38N.m
(2) Rear strut assembly to body thread torque : 32~38 N.m
(3) Strut assembly to rear brake assembly thread torque : 81~96 N.m
(4) Install the ABS rear wheel sensor and the secure the signal wire
(5) When securing the brake line, make sure that the brake line does not interfere with
other parts
(6) Wheel nut torque : 95~115N.m
(7) Check the brake system for leakage, bleed air in the brake system as necessary
(8) Check whether the ABS signal is normal
(9) Check rear wheel alignment, adjust it as necessary