HONDA CIVIC 2003 7.G Workshop Manual
Manufacturer: HONDA, Model Year: 2003, Model line: CIVIC, Model: HONDA CIVIC 2003 7.GPages: 1139, PDF Size: 28.19 MB
Page 561 of 1139
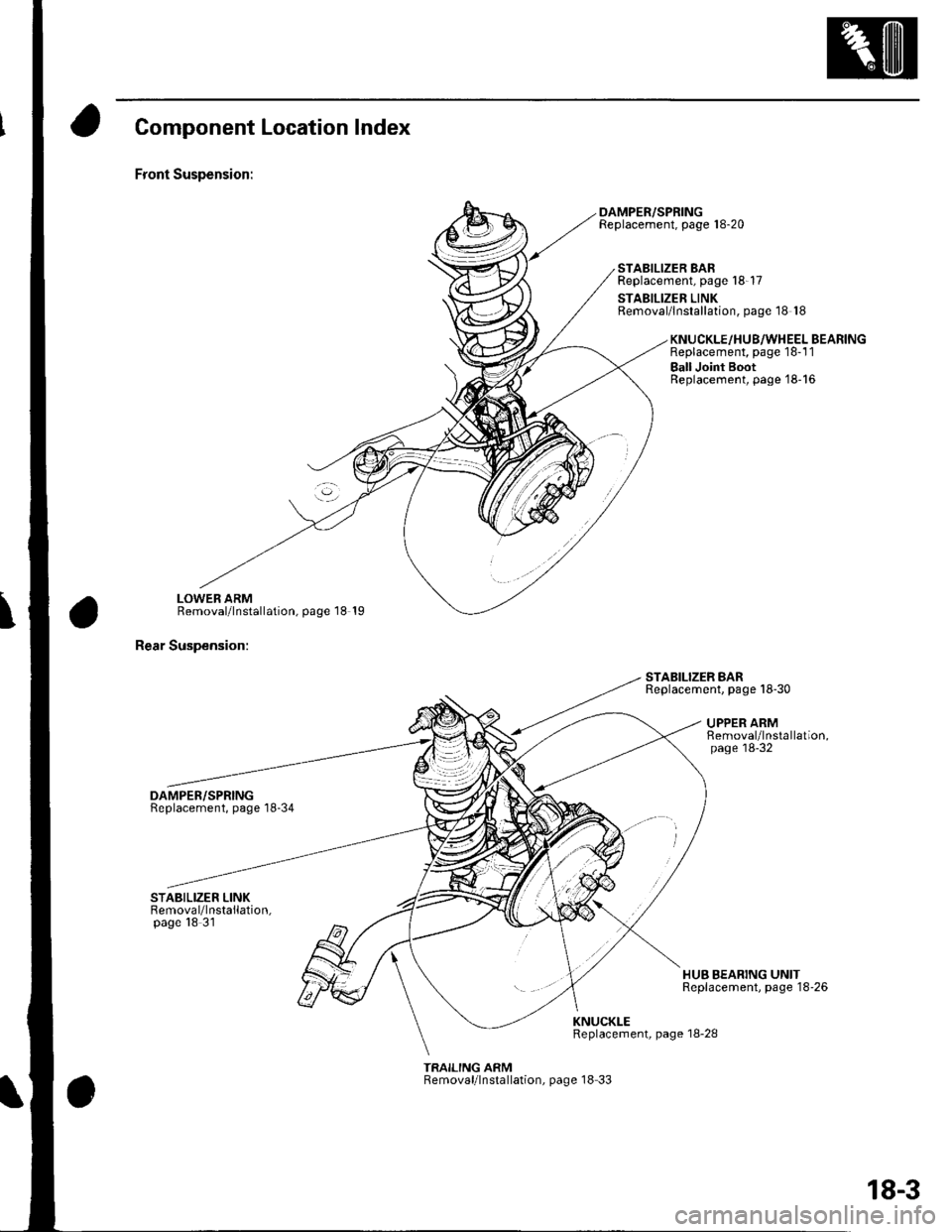
Component Location Index
Front Suspension:
LOWEB ARMRemoval/lnstallation, page 18 19
Rear Suspension:
DAMPER/SPRINGReplacement, page'18-34
DAMPER/SPRINGReplacement, page 18-20
STABILIZER BARReplacement, page 18-17
STABILIZER LINKRemoval/lnstallation, page 18 18
STABILIZER BARReplacement. page 18-30
KNUCKLE/HU8/WHEEL BEARINGReplacement, page 18-1 1
Ball Joint BootReplacement, page'18-16
UPPER ARMRemoval/lnstallation,page'18-32
HUB BEARING UNITReplacement, page 18'26
KNUCKLEReplacement, page 18-28
TRAILING ARMRemoval/lnstallation, page 18 33
18-3
Page 562 of 1139
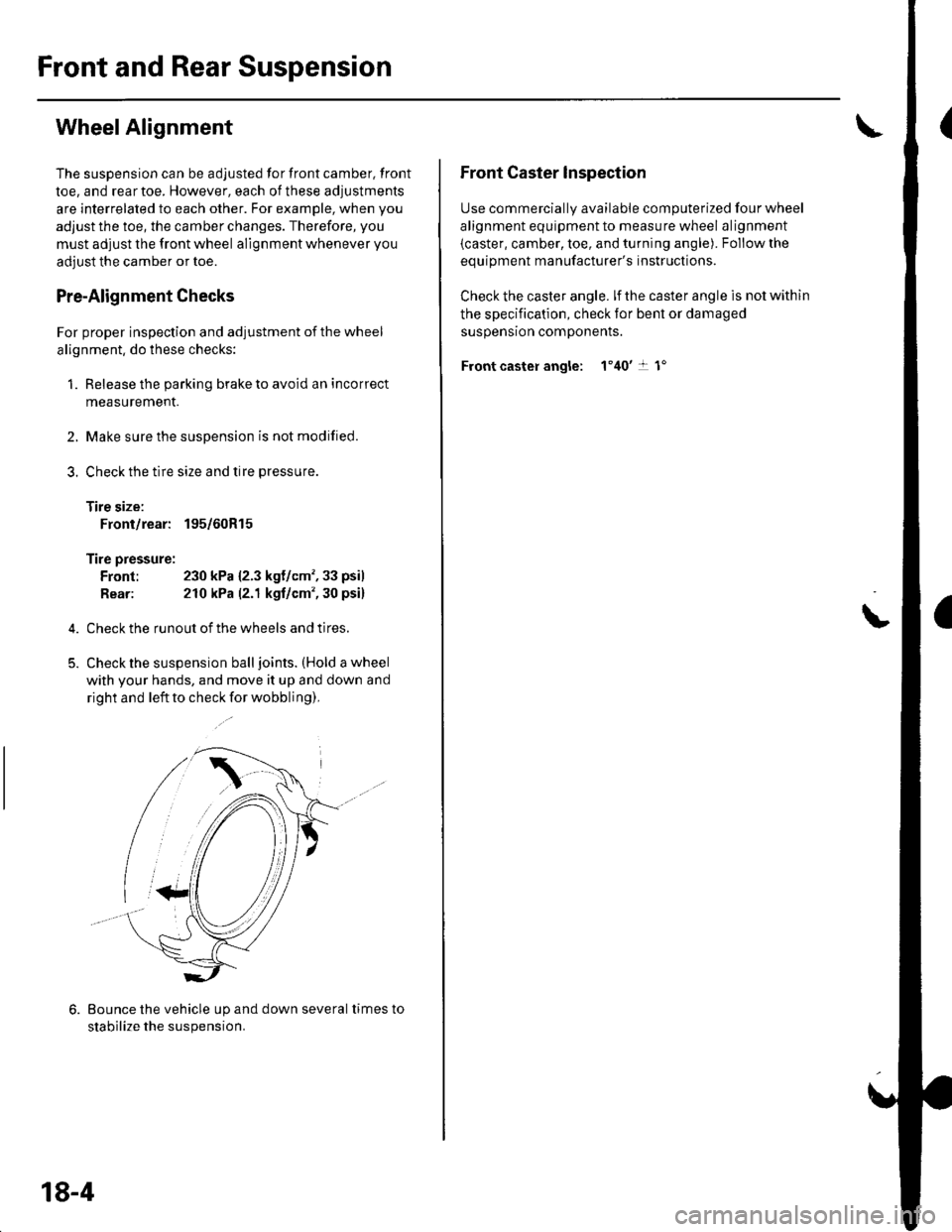
Front and Rear Suspension
WheelAlignment
The suspension can be adjusted for front camber, front
toe, and rear toe. However, each of these adjustments
are interrelated to each other. For example, when you
adjust the toe, the camber changes. Therefore, you
must adjust the front wheel alignment whenever you
adjust the camber or toe.
Pre-Alignment Checks
For proper inspection and adjustment of the wheel
alignment, do these checks:
1. Release the parking brake to avoid an incorrect
measurement.
Make sure the suspension is not modified.
Check the tire size and tire pressure
Tire size:
Front/rear: 195/60R15
Tire pressure:
Front: 230 kPa {2.3 kgf/cm',33 psil
Rear: 210 kPa |'2.1 kgf/cm', 30 psi)
Check the runout of the wheels and tires.
Check the suspension ball joints. (Hold a wheel
with your hands, and move it up and down and
right and left to check for wobbling),
2.
3.
Bounce the vehicle up and down several times to
stabilize the suspension.
18-4
Front Caster lnspection
Use commerciallv available comDuterized four wheel
alignment equipment to measure wheel alignment
(caster, camber, toe, and turning angle). Follow the
eouioment manufacturer's instructions.
Check the caster angle. lf the caster angle is not within
the specification, check for bent or damaged
susoensron comoonents.
Front caster angle: 1'40't 1"
\
Page 563 of 1139
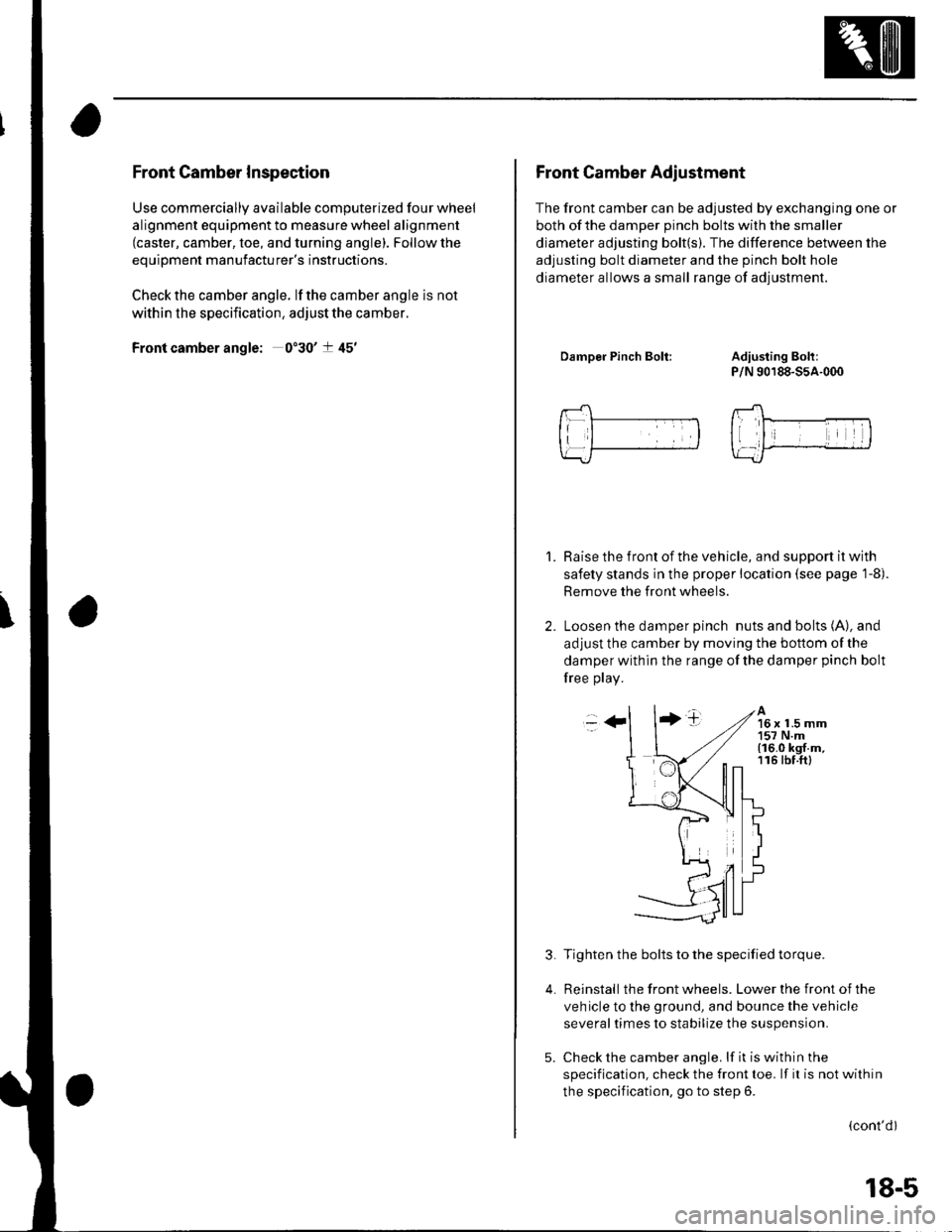
Front Camber Inspection
Use commercially available computerized four wheel
alignment equipment to measure wheel alignment(caster, camber, toe, and turning angle). Follow the
equipment manufacturer's instructions.
Check the camber angle. lf the camber angle is not
within the specification, adjust the camber.
Front camber angle: 0"30' t 45'
Front Camber Adjustment
The front camber can be adjusted by exchanging one or
both of the damDer Dinch bolts with the smaller
diameter adjusting bolt(s). The difference between the
adjusting bolt diameter and the pinch bolt hole
diameter allows a small range of adjustment.
DamDer Pinch Bolt:Adiusting Boh:
P/N 90188-55A-000
Raise the front of the vehicle, and support it with
safety stands in the proper location (see page 1-8).
Remove the front wheels.
Loosen the damper pinch nuts and bolts (A), and
adjust the camber by moving the bottom of the
damper within the range of the damper pinch bolt
free play.
1.
-++tA16 x 1.5 mm157 N.m(16.0 kgf.m,116 tbf.ftl
3.
4.
Tighten the bolts to the specified torque.
Reinstall the front wheels. Lower the front of the
veh icle to the ground, and bounce the vehicle
several times to stabilize the suspension.
Check the camber angle. lf it is within the
specification, check the front toe. lf it is not within
the specification, go to step 6.
(cont'dl
5.
18-5
Page 564 of 1139
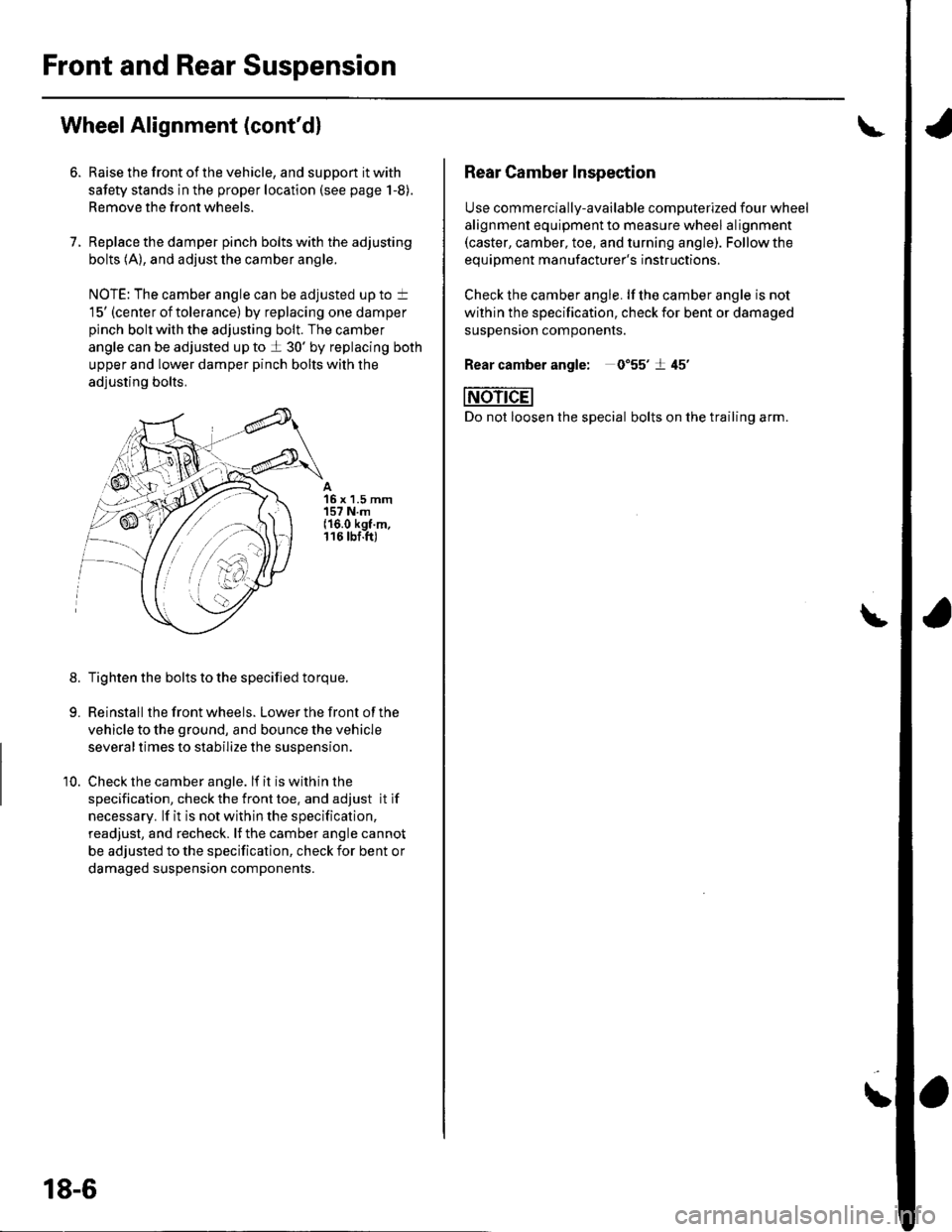
Front and Rear Suspension
Wheel Alignment (cont'd)
7.
Raise the front of the vehicle, and support it with
safety stands in the proper location (see page 1-8).
Remove the front wheels.
Replace the damper pinch bolts with the adjusting
bolts (A), and adjust the camber angle.
NOTE: The camber angle can be adjusted up to t
15' (center of tolerance) by replacing one damper
pinch bolt with the adjusting bolt. The camber
angle can be adjusted up to a 30' by replacing both
upper and lower damper pinch bolts with the
adjusting bolts.
15 x 1.5 mm157 N.m{16.0 kgt.m,116 tbf.ft)
8.Tighten the bolts to the specified torque.
Reinstall the front wheels. Lower the front of the
vehicle to the ground, and bounce the vehicle
several times to stabilize the suspension.
Check the camber angle. lf it is within the
specification, check the front toe. and adjust it if
necessary. lf it is not within the specification,
readjust, and recheck. lJ the camber angle cannot
be adjusted to the specification, check for bent or
damaged suspension components.
10.
'rntr
i,iY. a
.:r,//
18-6
Rear Camber Inspection
Use commercially-available computerized four wheel
alignment equipment to measure wheel alignment(caster, camber, toe, and turning angle). Follow the
eouiDment manufacturer's instructions.
Check the camber angle. lf lhe camber angle is not
within the specification, check for bent or damaged
susDenston comoonenrs.
0"55' t 45'
bolts on the trailing arm.
Rear camber angle: 0
NOn-dEl
Do not loosen the special
\
Page 565 of 1139
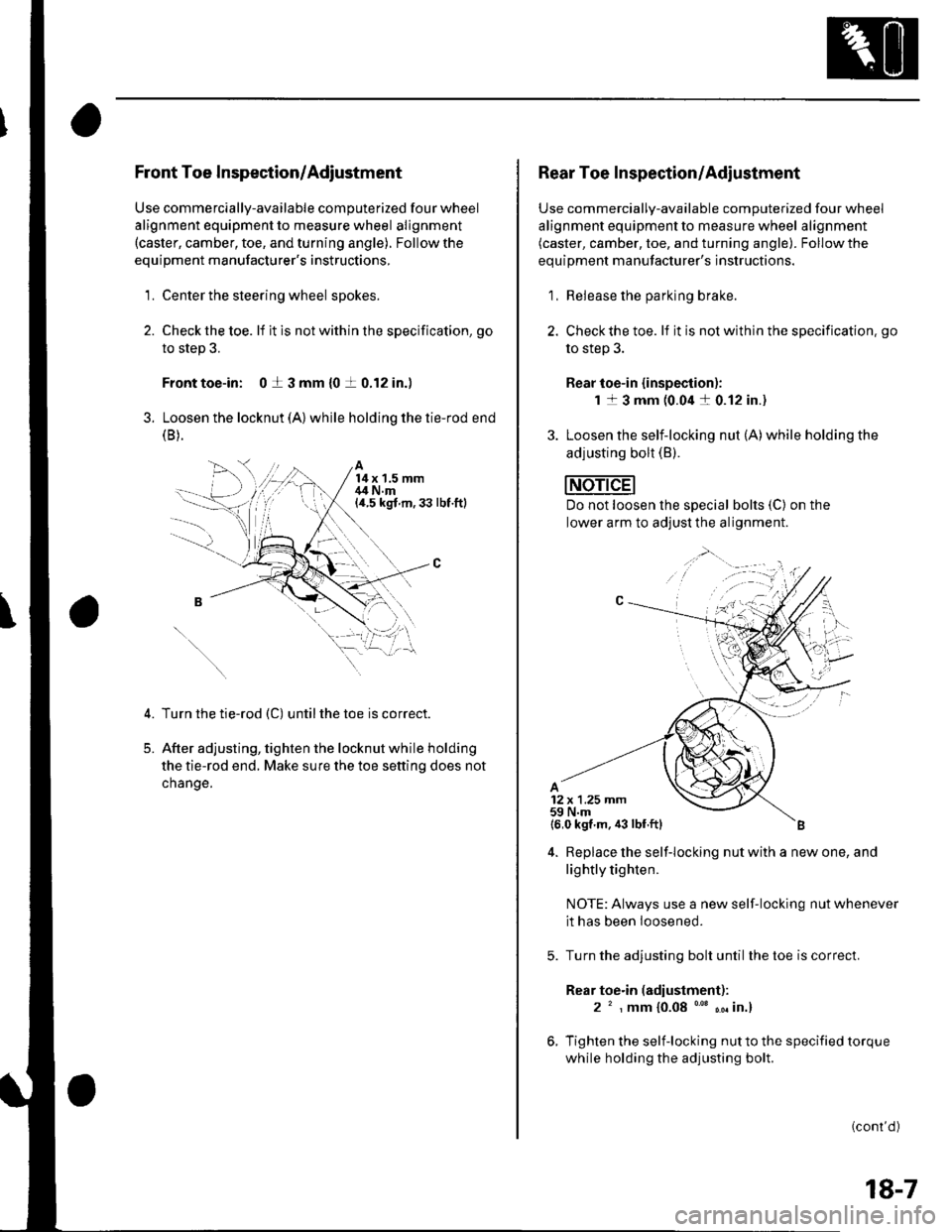
Front Toe Inspection/Adjustment
Use commercially-available computerized four wheel
alignment equipment to measure wheel alignment(caster, camber, toe, and turning angle). Follow the
equipment manufacturer's instructions,
1. Center the steering wheel spokes.
2. Checkthetoe. lf it is not with in the specif ication, go
to step 3.
Front toe-in: 0 t 3 mm {0 t 0.12 in.)
3. Loosen the locknut (A) while holding the tie-rod end(B ).
A14x 1.5 mm,14 N.m(a.5 kgt m,33 lbt.ftl
5.
Turn the tie-rod (C) untilthe toe is correct.
After adjusting, tighten the locknut while holding
the tie-rod end. Make sure the toe setting does not
change.
1,;
Rear Toe Inspection/Adiustment
Use commercially-available computerized four wheel
alignment equipment to measure wheel alignment(caster, camber, toe, and turning angle). Follow the
equipment manufacturer's instructions.
1, Release the parking brake.
2. Checkthe toe. lf it is not within the specification. go
to step 3.
Rear toe-in {inspection):
1 1 3 mm (0.04 a 0.12 in.)
3. Loosen the self-locking nut (A)while holding the
adjusting bolt (B).
Do not loosen lhe special bolts (C) on the
lower arm to adjust the alignment.
4. Replace the self-locking nut with a new one, and
lightly tighten.
NOTE: Always use a new self-locking nut whenever
it has been loosened.
Turn the adjusting bolt until the toe is correct.
Rear toe.in (adiustment):
2 ' , mm {0.08 "' ,. in.}
Tighten the self-locking nut to the specified torque
while holding the adjusting bolt.
(cont'd )
18-7
Page 566 of 1139
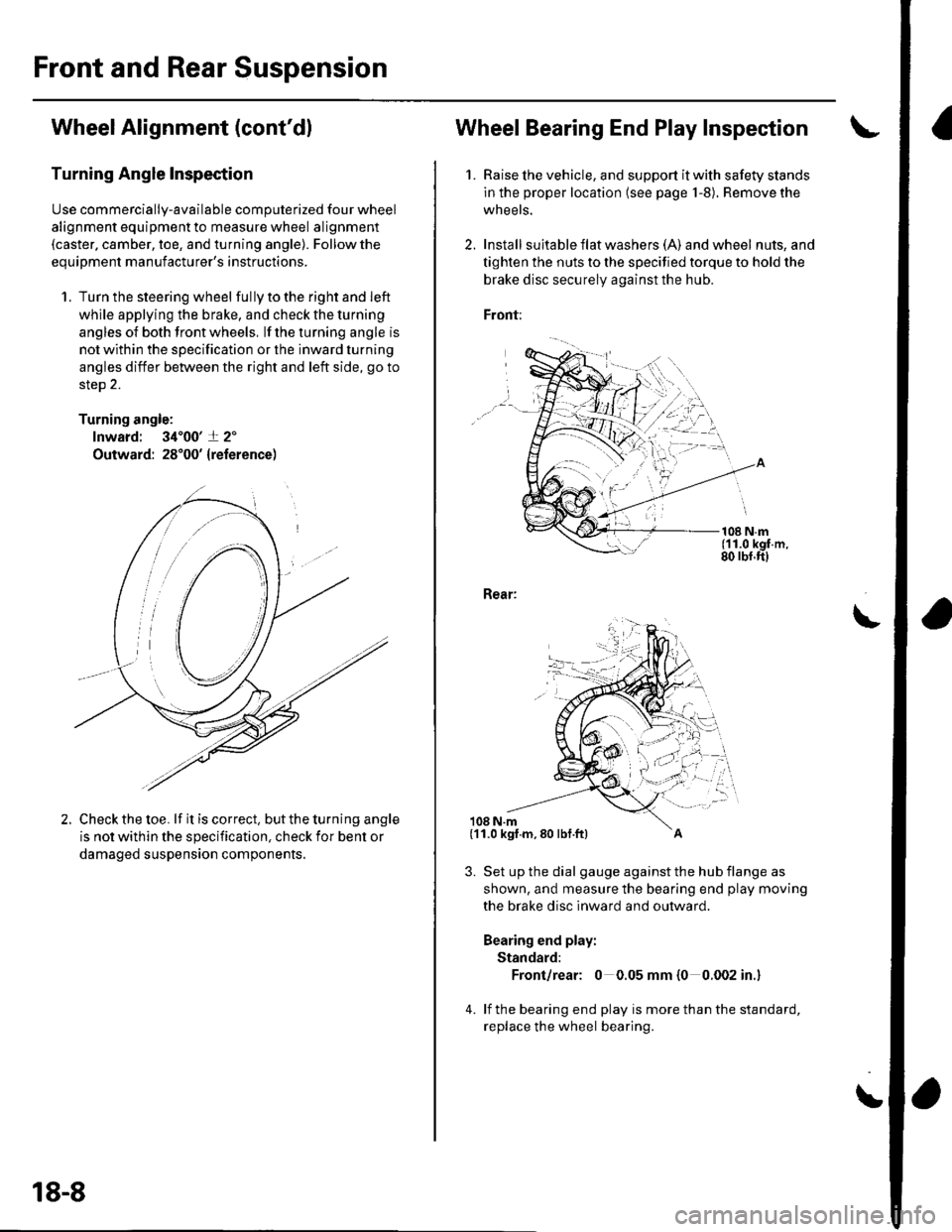
Front and Rear Suspension
Wheel Alignment (cont'dl
Turning Angle Inspection
Use commercially-available computerized four wheel
alignment equipment to measure wheel alignment(caster. camber, toe, and turning angle). Followthe
equiDment manufacturer's instructions.
1. Turn the steering wheel fullytotherightandleft
while applying the brake, and check the turning
angles of both front wheels, lf the turning angle is
not within the specification or the inward turning
angles differ between the right and left side, go to
steD 2.
Turning angle:
lnward: 34'00'+ 2'
Outward: 28'00' {reference)
Check the toe. lf it is correct, but the turning angle
is not within the specification, check ior bent or
damaged suspension components,
18-8
Wheel Bearing End Play Inspec'tion
1. Raise lhe vehicle, and support it with safety stands
in the proper location (see page 1-8). Remove the
wheels.
2. Install suita ble f lat washe rs (A) and wheel nuts, and
tighten the nuts to the specified torque to hold the
brake disc securely against the hub.
Front:
108 N.m(11.0 kgf.m,80 rbf.ft)
Rear:
108 N.m
3. Set up the dial gauge against the hub flange as
shown, and measure the bearing end play moving
the brake disc inward and outward.
Bearing end play:
Standard:
Front/rear: 0 0.05 mm {0 0.002 in.}
4. lf the bearing end play is more than the standard,
replace the wheel bearing.
\
(11.0 kgf.m,80 lbf.ft)
Page 567 of 1139
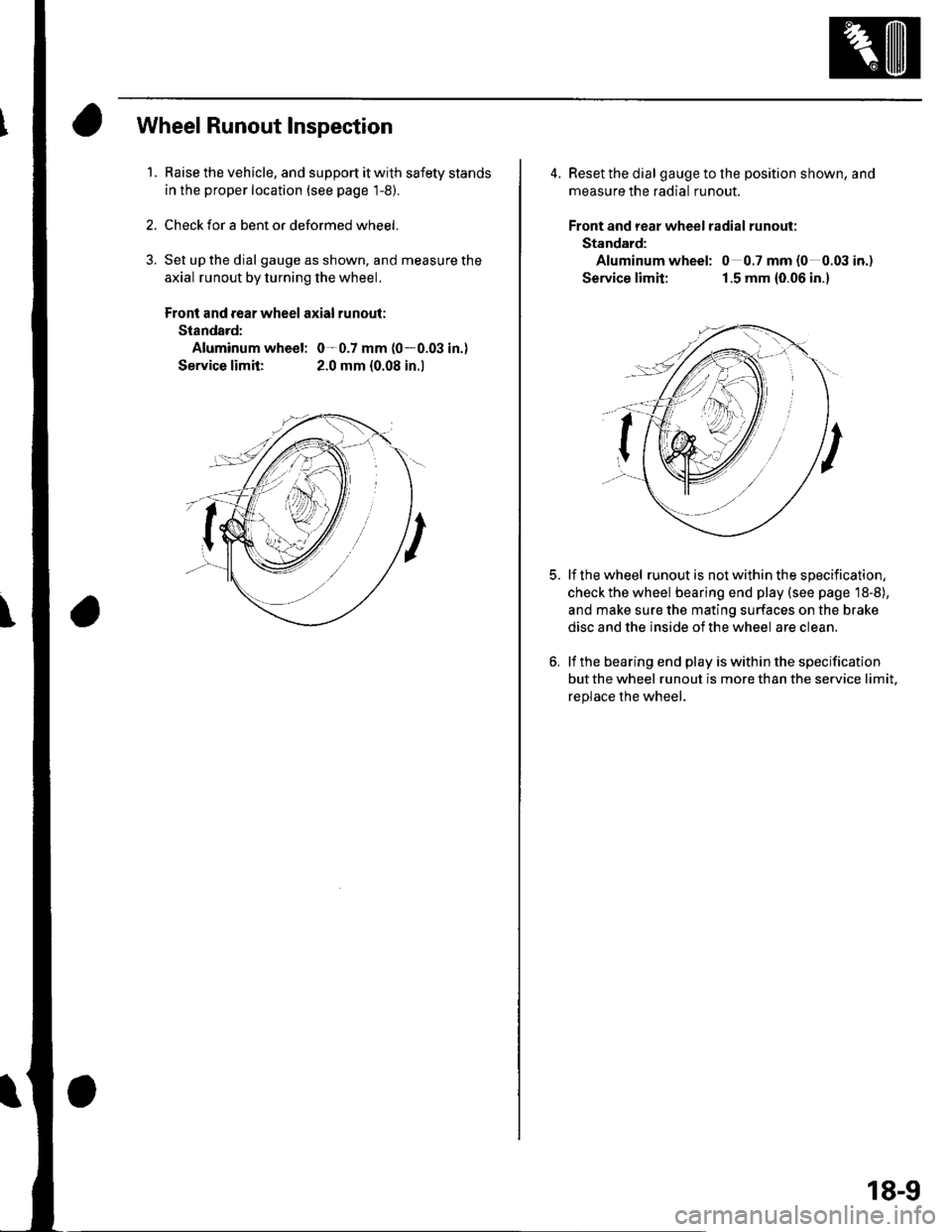
Wheel Runout Inspection
1.Raise the vehicle, and support it with safety stands
in the proper location (see page 1-5,.
Check for a bent or deformed wheel.
Set up the dial gauge as shown, and measure the
axial runout by turning the wheel.
Front and rear wheel axial runout:
Standard:
Aluminum wheel: 0-0.7 mm (0-0.03 in.)
Service limit: 2.0 mm {0.08 in.l
4. Reset the dial gaugetothe position shown, and
measure the radial runout.
Front and rear wheel radial runout:
Standard:
Aluminum wheel: 0 0.7 mm (0 0.03 io.)
Service limit: 1.5 mm {0.06 in.}
lf the wheel runout is not within the specification,
checkthe wheel bearing end play (see page 18-8),
and make sure the mating surfaces on the brake
disc and the inside of the wheel are clean.
lf the bearing end play is within the specification
but the wheel runout is more than the service limit.
replace the wheel.
18-9
Page 568 of 1139

Front and Rear Suspension
BallJoint Removal
Special Tools Required
Ball ioint remover.2S mm 07MAC-SL00200
Always use a ball joint remover to disconnect a ball
joint. Do not strike the housing or any other part of
the ball joint connection to disconnect it.
'1, Install a hex nut (A) ontothethreadsoftheballjoint
{B). Make sure the nut is flush with the balljoint pin
end to prevent damage to the threaded end of the
ball ioint oin.
Apply grease to the special tool on the areas shown(A). This will ease installation of the tool and
prevent damage to the pressure bolt {B) threads.
2.
18-10
3. Loosen the pressure bolt (A), and installthe special
tool as shown. Insen the jaws carefully, making
sure not to damage the ball joint boot. Adjust the
jaw spacing by turning the adjusting bolt (B).
10 mm HEX NUT
5.
07MAC-S100200
After adjusting the adjusting bolt, make sure the
head (C) of the adjusting bolt is in the position
shown to allow the jaw to pivot.
With a wrench, tighten the pressure bolt until the
ball ioint pin pops loose from the steering arm or
knuckle. lf necessary. apply penetrating type
lubricant to loosen the ball joint pin
NOTE: Do not use pneumatic or electric tools on
the pressure bolt.
Remove the tool, then remove the nut from the end
ofthe balljoint pin, and pullthe balljoint out ofthe
steering arm or knuckle. Inspectthe balljoint boot,
and replace it if damaged.
6.
Page 569 of 1139
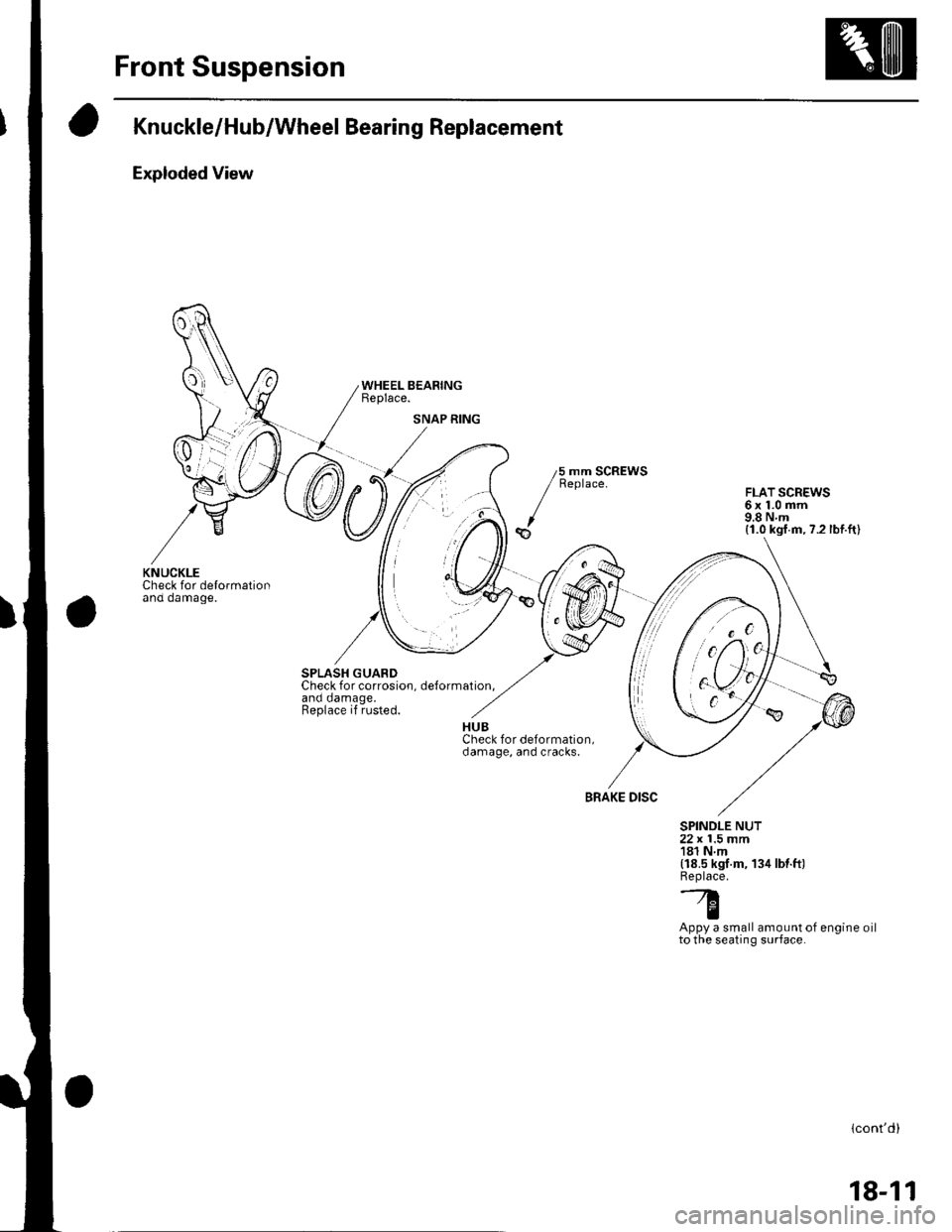
Front Suspension
Knuckle/Hub/Wheel Bearing Replacement
Exploded View
Check for delormationano oamage.
SPLASH GUARDCheck for corrosion. delormation.and damage.Replace if rusted.
WHEEL BEARINGReplace.
5 mm SCREWSReplace.FLAT SCREWS6x1.0mm9.8Nm(1.0 kgf.m,7.2 lbf.ft)
BRAKE DISC
SPINDLE NUT22 x 1.5 mm181 Nm(18.5 kgf.m, 134 lbt.ft)Replace.'--7.l'tq
IAppy a small amount of engine oilto the seating surface.
lcont'd)
SNAP RING
KNUCKLE
18-11
Page 570 of 1139
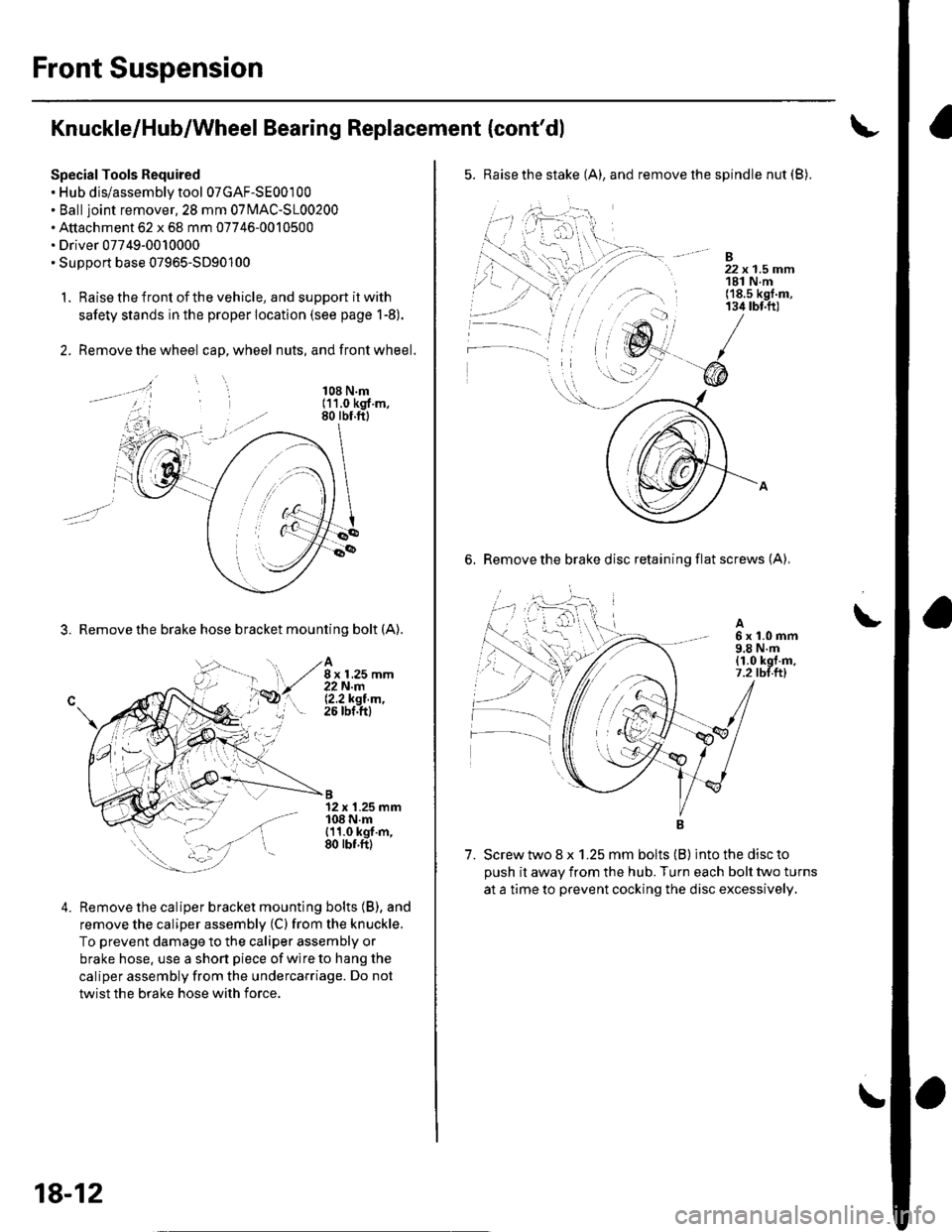
Front Suspension
Knuckle/Hub/Wheel Bearing Replacement {cont'dl
Special Tools Required. Hub dis/assembly tool 07GAF-SE00100. Balljoint remover,2S mm 0TlvlAC-S100200. Attachment 62 x 68 mm 07746-0010500. Driver 07749-0010000. SuDDort base 07965-5D90'100
1. Raise the front of the vehicle, and support it with
safety stands in the proper location (see page 1-8).
2. Remove the wheel cap, wheel nuts, and front wheel.
3. Remove the brake hose bracket mounting bolt (A).
108 N.m(11.0 kgf m,80 rbf.ftl
A8 x 1.25 mm22N.m12.2ksl.m,26 tbf.ftl
B12 x 1.25 mm108 N.m{11.0 kgf.m,80 rbf.ftl
4.Remove the caliper bracket mounting bolts (B), and
remove the caliper assembly (C) from the knuckle.
To prevent damage to the caliper assembly or
brake hose, use a short piece of wire to hang the
caliper assembly from the undercarriage. Do not
twist the brake hose with force.
18-12
5. Raise the stake (A), and remove the spindle nut (B).
-B
' 22x1.5mm, 181 N.m('18.s kgf.m,134 tbt.ft)
6. Remove the brake disc retaining flat screws (A).
A6x1.0mm9.8 N.m{1.0 kgt.m,7.2 tbl.ttl
7. Screw two 8 x 1.25 mm bolts (B) into the disc to
oush it awav from the hub. Turn each bolt two turns
at a time to prevent cocking the disc excessively,
\
\