Oil INFINITI M35 2006 Factory Service Manual
[x] Cancel search | Manufacturer: INFINITI, Model Year: 2006, Model line: M35, Model: INFINITI M35 2006Pages: 5621, PDF Size: 65.56 MB
Page 614 of 5621
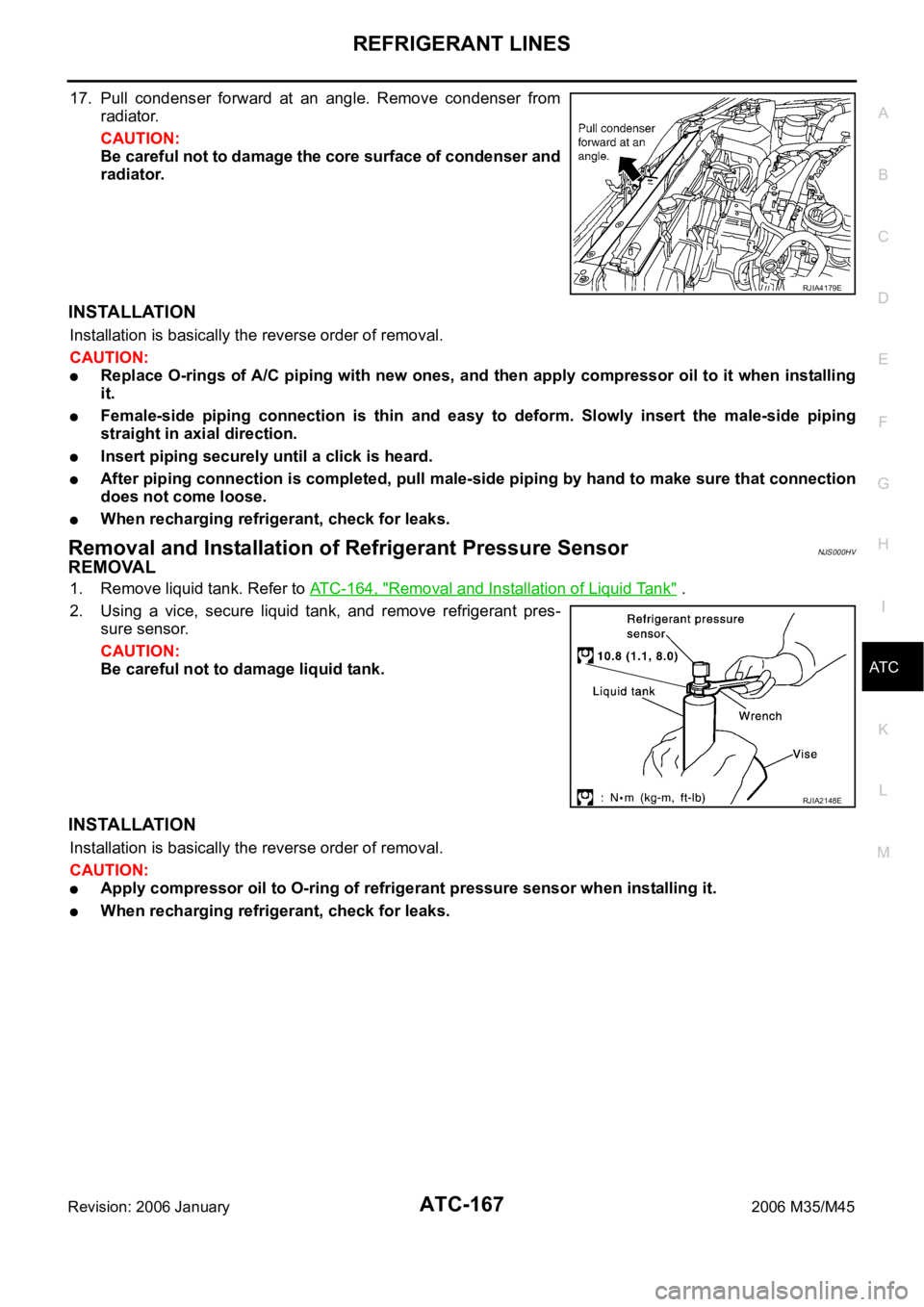
REFRIGERANT LINES
ATC-167
C
D
E
F
G
H
I
K
L
MA
B
AT C
Revision: 2006 January2006 M35/M45
17. Pull condenser forward at an angle. Remove condenser from
radiator.
CAUTION:
Be careful not to damage the core surface of condenser and
radiator.
INSTALLATION
Installation is basically the reverse order of removal.
CAUTION:
Replace O-rings of A/C piping with new ones, and then apply compressor oil to it when installing
it.
Female-side piping connection is thin and easy to deform. Slowly insert the male-side piping
straight in axial direction.
Insert piping securely until a click is heard.
After piping connection is completed, pull male-side piping by hand to make sure that connection
does not come loose.
When recharging refrigerant, check for leaks.
Removal and Installation of Refrigerant Pressure SensorNJS000HV
REMOVAL
1. Remove liquid tank. Refer to ATC-164, "Removal and Installation of Liquid Tank" .
2. Using a vice, secure liquid tank, and remove refrigerant pres-
sure sensor.
CAUTION:
Be careful not to damage liquid tank.
INSTALLATION
Installation is basically the reverse order of removal.
CAUTION:
Apply compressor oil to O-ring of refrigerant pressure sensor when installing it.
When recharging refrigerant, check for leaks.
RJIA4179E
RJIA2148E
Page 615 of 5621
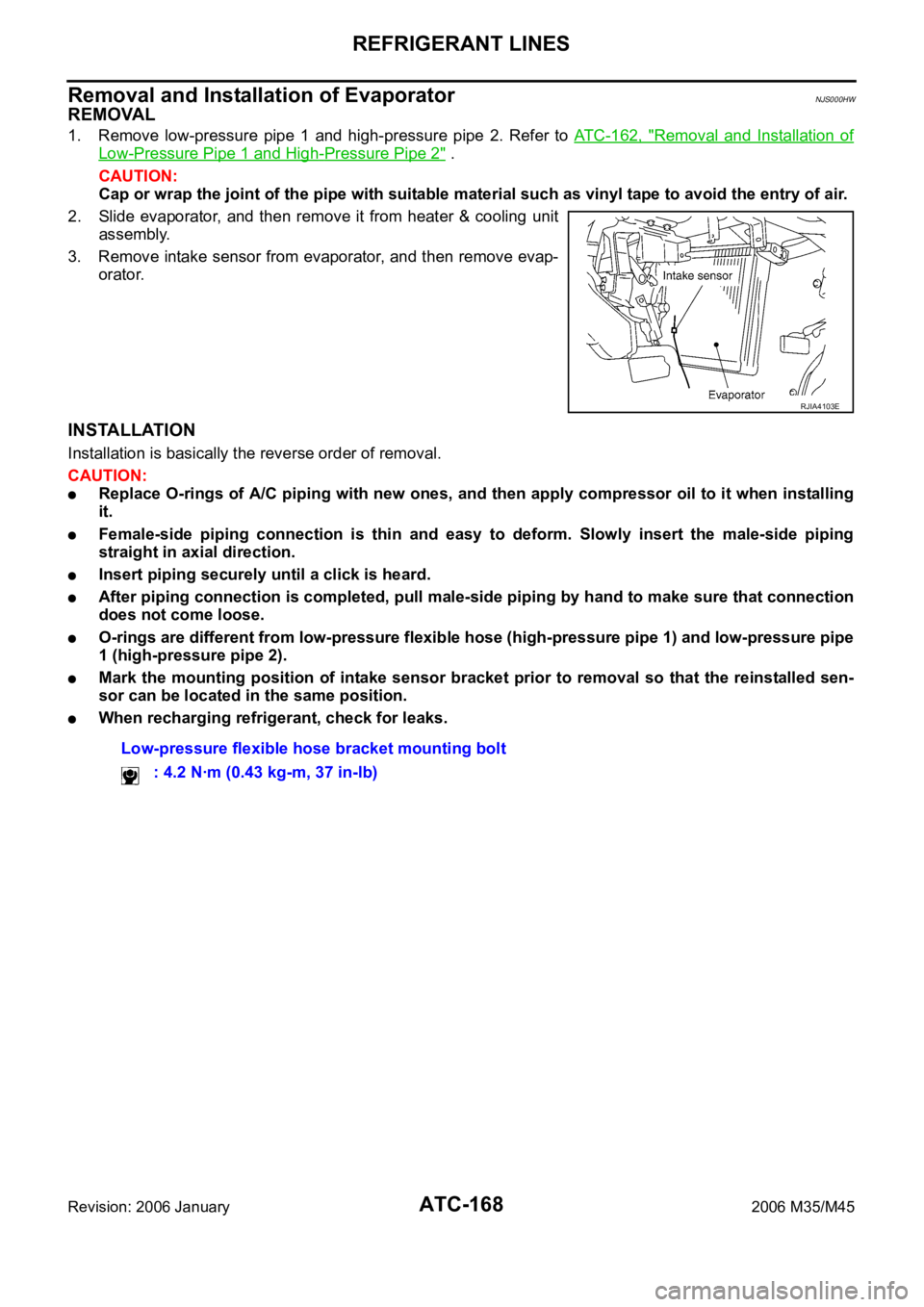
ATC-168
REFRIGERANT LINES
Revision: 2006 January2006 M35/M45
Removal and Installation of EvaporatorNJS000HW
REMOVAL
1. Remove low-pressure pipe 1 and high-pressure pipe 2. Refer to ATC-162, "Removal and Installation of
Low-Pressure Pipe 1 and High-Pressure Pipe 2" .
CAUTION:
Cap or wrap the joint of the pipe with suitable material such as vinyl tape to avoid the entry of air.
2. Slide evaporator, and then remove it from heater & cooling unit
assembly.
3. Remove intake sensor from evaporator, and then remove evap-
orator.
INSTALLATION
Installation is basically the reverse order of removal.
CAUTION:
Replace O-rings of A/C piping with new ones, and then apply compressor oil to it when installing
it.
Female-side piping connection is thin and easy to deform. Slowly insert the male-side piping
straight in axial direction.
Insert piping securely until a click is heard.
After piping connection is completed, pull male-side piping by hand to make sure that connection
does not come loose.
O-rings are different from low-pressure flexible hose (high-pressure pipe 1) and low-pressure pipe
1 (high-pressure pipe 2).
Mark the mounting position of intake sensor bracket prior to removal so that the reinstalled sen-
sor can be located in the same position.
When recharging refrigerant, check for leaks.
RJIA4103E
Low-pressure flexible hose bracket mounting bolt
: 4.2 Nꞏm (0.43 kg-m, 37 in-lb)
Page 616 of 5621
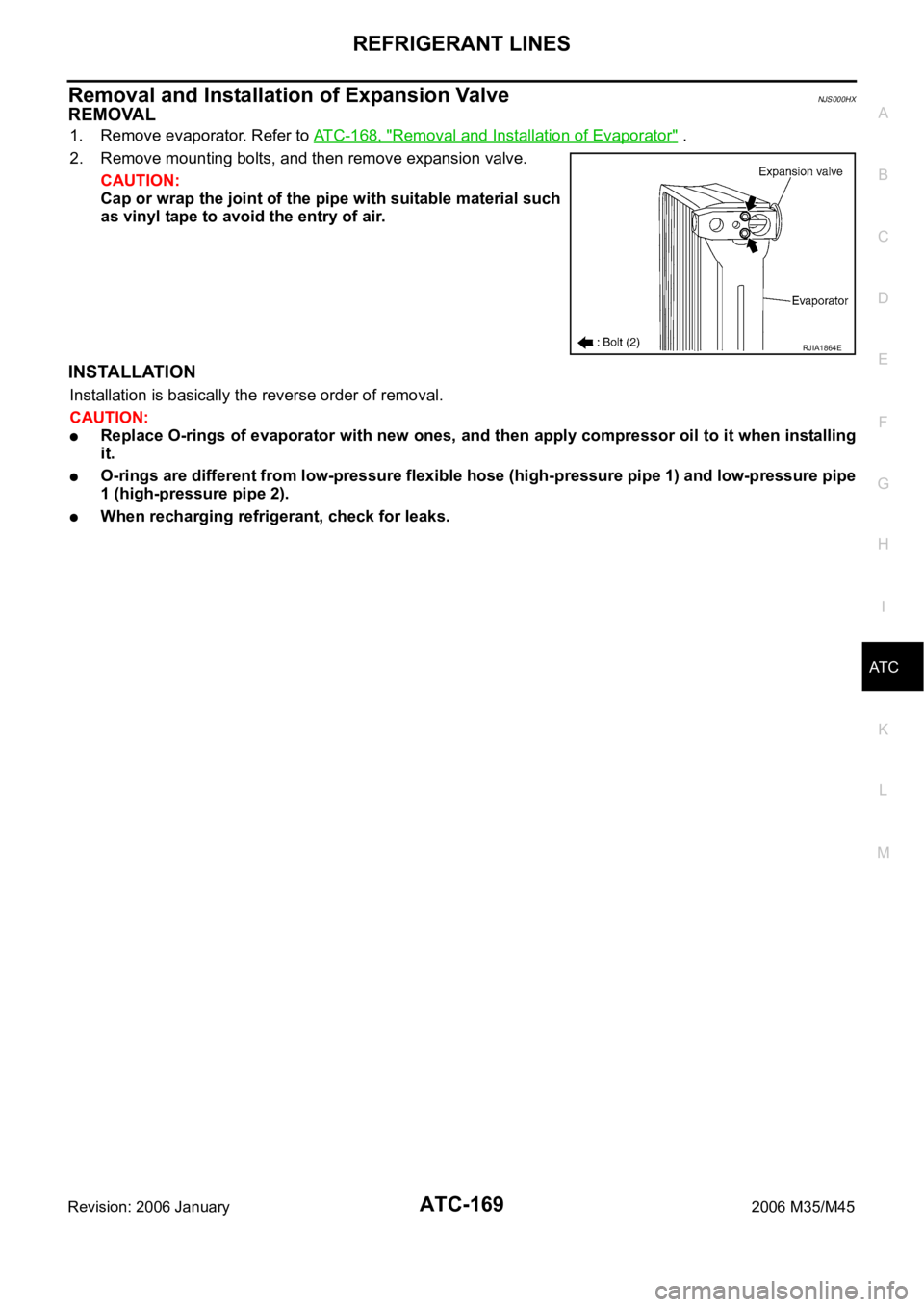
REFRIGERANT LINES
ATC-169
C
D
E
F
G
H
I
K
L
MA
B
AT C
Revision: 2006 January2006 M35/M45
Removal and Installation of Expansion ValveNJS000HX
REMOVAL
1. Remove evaporator. Refer to ATC-168, "Removal and Installation of Evaporator" .
2. Remove mounting bolts, and then remove expansion valve.
CAUTION:
Cap or wrap the joint of the pipe with suitable material such
as vinyl tape to avoid the entry of air.
INSTALLATION
Installation is basically the reverse order of removal.
CAUTION:
Replace O-rings of evaporator with new ones, and then apply compressor oil to it when installing
it.
O-rings are different from low-pressure flexible hose (high-pressure pipe 1) and low-pressure pipe
1 (high-pressure pipe 2).
When recharging refrigerant, check for leaks.
RJIA1864E
Page 617 of 5621
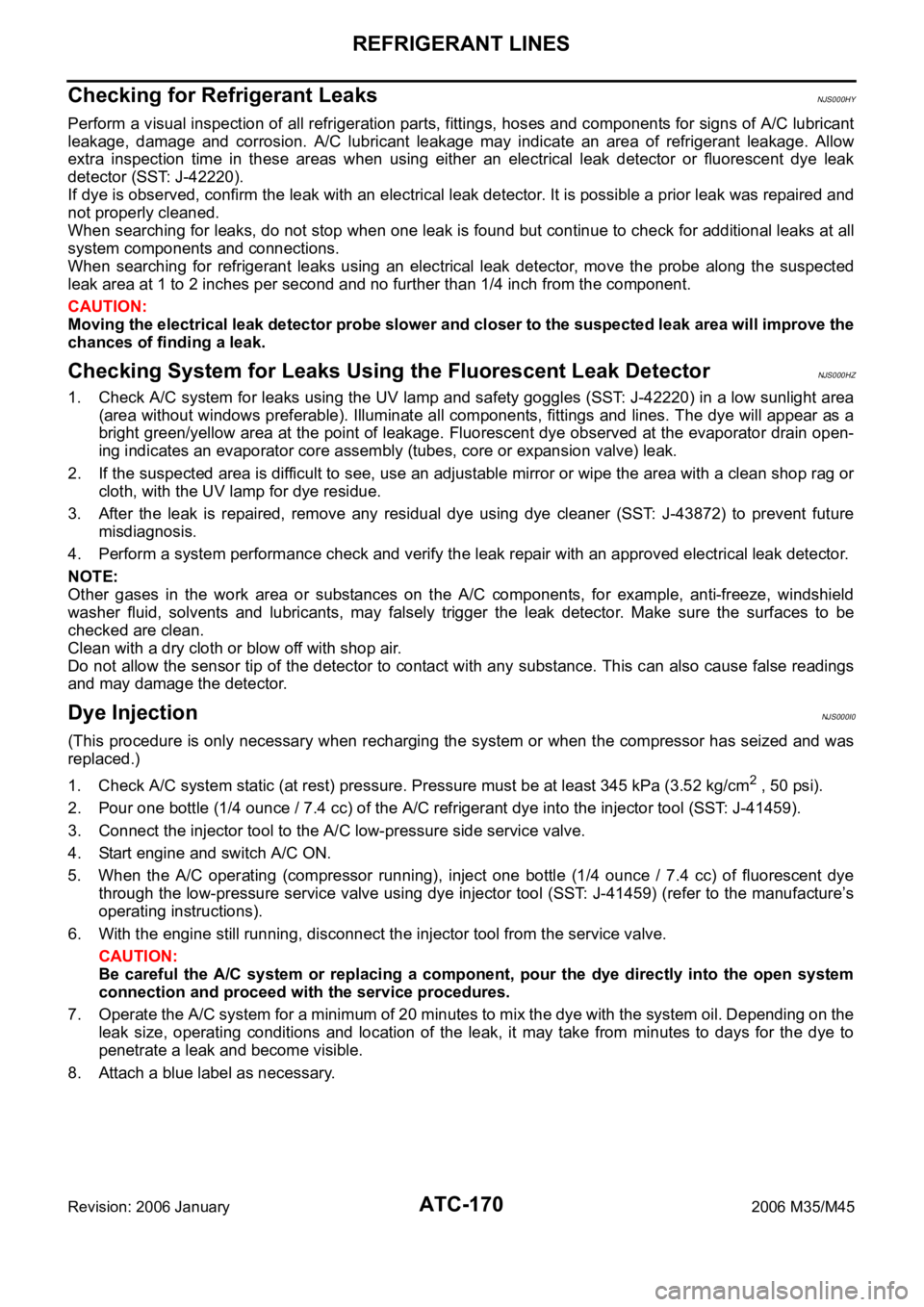
ATC-170
REFRIGERANT LINES
Revision: 2006 January2006 M35/M45
Checking for Refrigerant LeaksNJS000HY
Perform a visual inspection of all refrigeration parts, fittings, hoses and components for signs of A/C lubricant
leakage, damage and corrosion. A/C lubricant leakage may indicate an area of refrigerant leakage. Allow
extra inspection time in these areas when using either an electrical leak detector or fluorescent dye leak
detector (SST: J-42220).
If dye is observed, confirm the leak with an electrical leak detector. It is possible a prior leak was repaired and
not properly cleaned.
When searching for leaks, do not stop when one leak is found but continue to check for additional leaks at all
system components and connections.
When searching for refrigerant leaks using an electrical leak detector, move the probe along the suspected
leak area at 1 to 2 inches per second and no further than 1/4 inch from the component.
CAUTION:
Moving the electrical leak detector probe slower and closer to the suspected leak area will improve the
chances of finding a leak.
Checking System for Leaks Using the Fluorescent Leak DetectorNJS000HZ
1. Check A/C system for leaks using the UV lamp and safety goggles (SST: J-42220) in a low sunlight area
(area without windows preferable). Illuminate all components, fittings and lines. The dye will appear as a
bright green/yellow area at the point of leakage. Fluorescent dye observed at the evaporator drain open-
ing indicates an evaporator core assembly (tubes, core or expansion valve) leak.
2. If the suspected area is difficult to see, use an adjustable mirror or wipe the area with a clean shop rag or
cloth, with the UV lamp for dye residue.
3. After the leak is repaired, remove any residual dye using dye cleaner (SST: J-43872) to prevent future
misdiagnosis.
4. Perform a system performance check and verify the leak repair with an approved electrical leak detector.
NOTE:
Other gases in the work area or substances on the A/C components, for example, anti-freeze, windshield
washer fluid, solvents and lubricants, may falsely trigger the leak detector. Make sure the surfaces to be
checked are clean.
Clean with a dry cloth or blow off with shop air.
Do not allow the sensor tip of the detector to contact with any substance. This can also cause false readings
and may damage the detector.
Dye InjectionNJS000I0
(This procedure is only necessary when recharging the system or when the compressor has seized and was
replaced.)
1. Check A/C system static (at rest) pressure. Pressure must be at least 345 kPa (3.52 kg/cm
2 , 50 psi).
2. Pour one bottle (1/4 ounce / 7.4 cc) of the A/C refrigerant dye into the injector tool (SST: J-41459).
3. Connect the injector tool to the A/C low-pressure side service valve.
4. Start engine and switch A/C ON.
5. When the A/C operating (compressor running), inject one bottle (1/4 ounce / 7.4 cc) of fluorescent dye
through the low-pressure service valve using dye injector tool (SST: J-41459) (refer to the manufacture’s
operating instructions).
6. With the engine still running, disconnect the injector tool from the service valve.
CAUTION:
Be careful the A/C system or replacing a component, pour the dye directly into the open system
connection and proceed with the service procedures.
7. Operate the A/C system for a minimum of 20 minutes to mix the dye with the system oil. Depending on the
leak size, operating conditions and location of the leak, it may take from minutes to days for the dye to
penetrate a leak and become visible.
8. Attach a blue label as necessary.
Page 621 of 5621
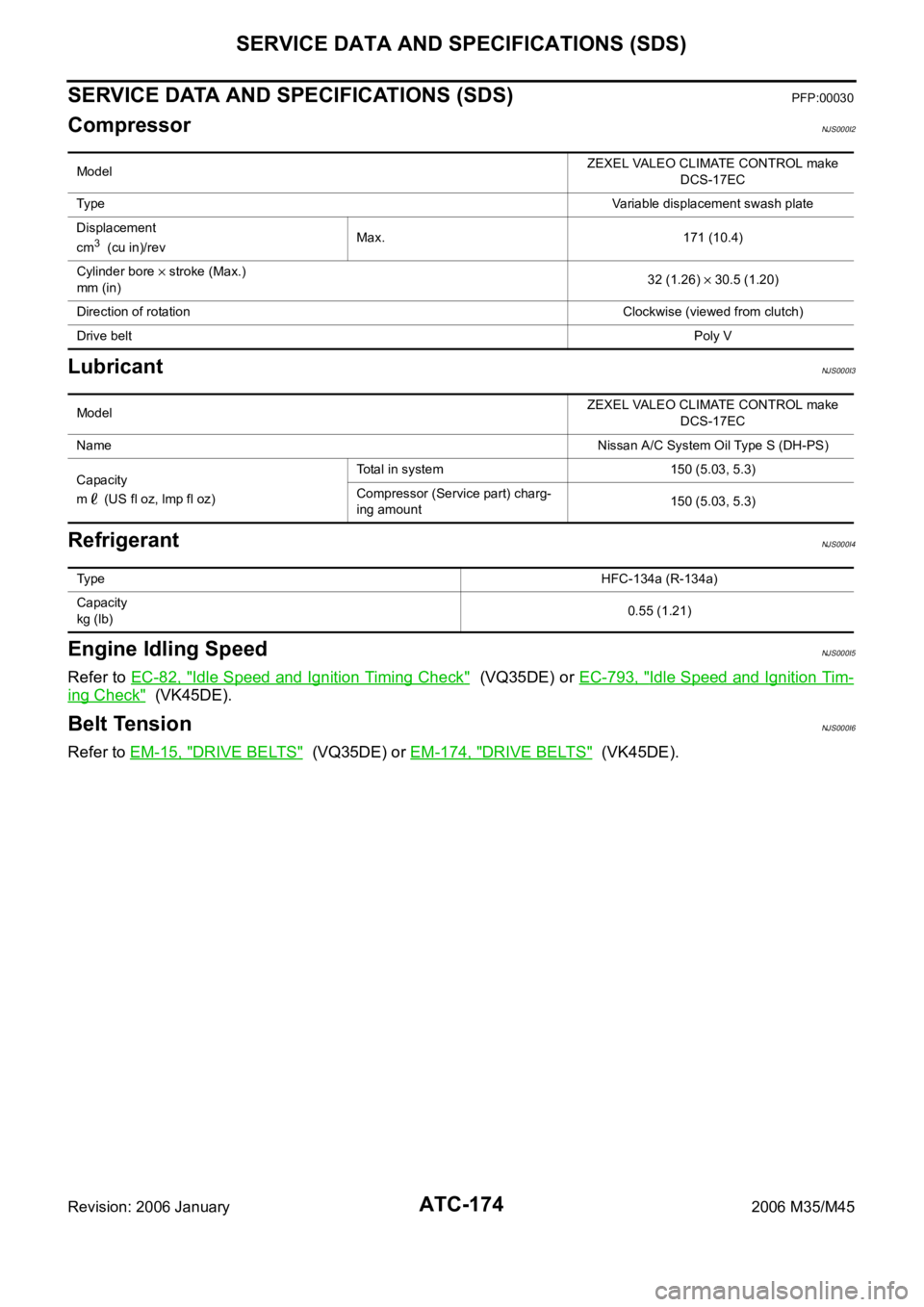
ATC-174
SERVICE DATA AND SPECIFICATIONS (SDS)
Revision: 2006 January2006 M35/M45
SERVICE DATA AND SPECIFICATIONS (SDS)PFP:00030
CompressorNJS000I2
LubricantNJS000I3
RefrigerantNJS000I4
Engine Idling SpeedNJS000I5
Refer to EC-82, "Idle Speed and Ignition Timing Check" (VQ35DE) or EC-793, "Idle Speed and Ignition Tim-
ing Check" (VK45DE).
Belt TensionNJS000I6
Refer to EM-15, "DRIVE BELTS" (VQ35DE) or EM-174, "DRIVE BELTS" (VK45DE).
ModelZEXEL VALEO CLIMATE CONTROL make
DCS-17EC
Ty p eVariable displacement swash plate
Displacement
cm
3 (cu in)/revMax. 171 (10.4)
Cylinder bore
stroke (Max.)
mm (in)32 (1.26) 30.5 (1.20)
Direction of rotationClockwise (viewed from clutch)
Drive beltPoly V
ModelZEXEL VALEO CLIMATE CONTROL make
DCS-17EC
NameNissan A/C System Oil Type S (DH-PS)
Capacity
m (US fl oz, lmp fl oz)Total in system 150 (5.03, 5.3)
Compressor (Service part) charg-
ing amount150 (5.03, 5.3)
Ty p eHFC-134a (R-134a)
Capacity
kg (lb)0.55 (1.21)
Page 929 of 5621
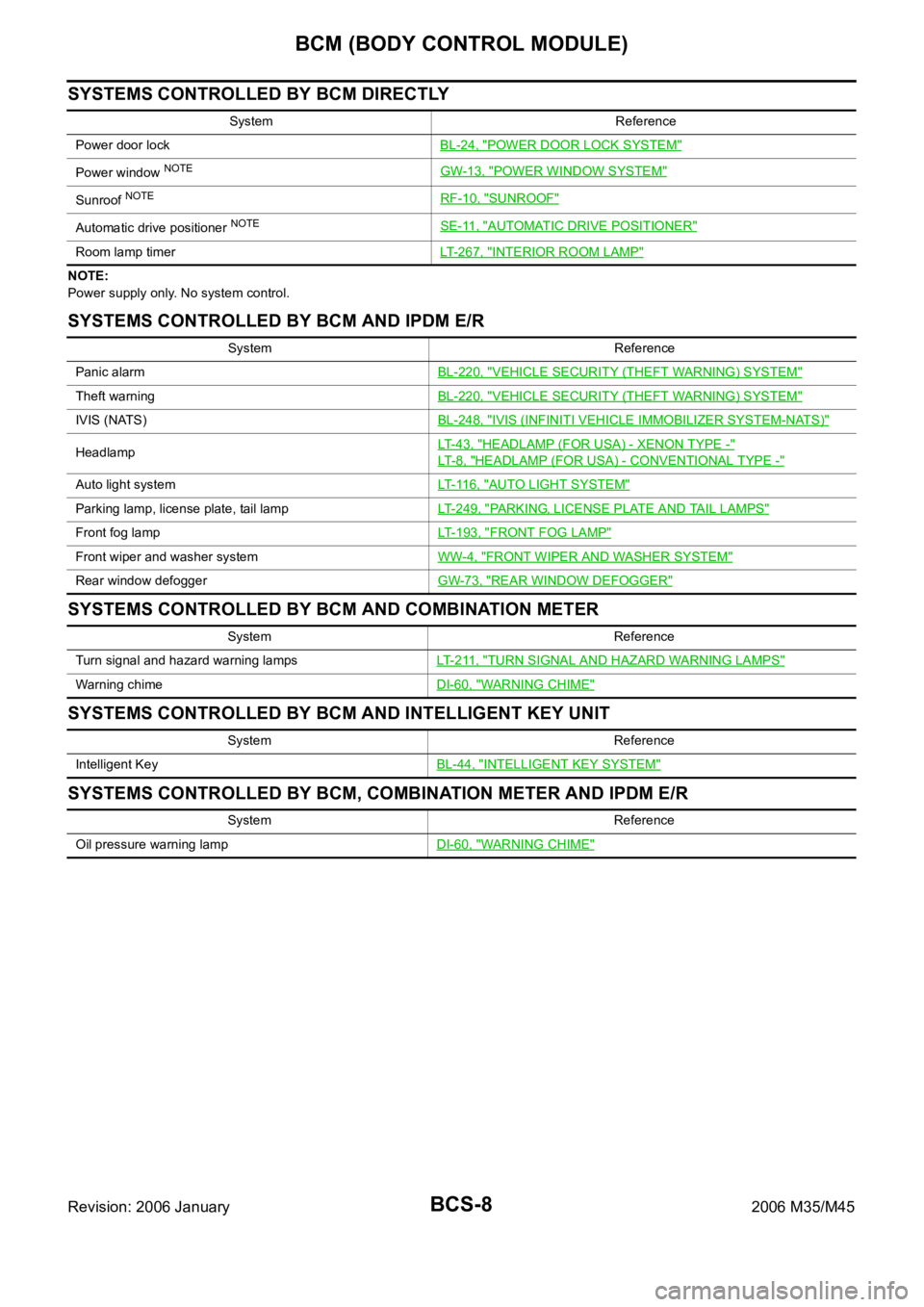
BCS-8
BCM (BODY CONTROL MODULE)
Revision: 2006 January2006 M35/M45
SYSTEMS CONTROLLED BY BCM DIRECTLY
NOTE:
Power supply only. No system control.
SYSTEMS CONTROLLED BY BCM AND IPDM E/R
SYSTEMS CONTROLLED BY BCM AND COMBINATION METER
SYSTEMS CONTROLLED BY BCM AND INTELLIGENT KEY UNIT
SYSTEMS CONTROLLED BY BCM, COMBINATION METER AND IPDM E/R
System Reference
Power door lockBL-24, "
POWER DOOR LOCK SYSTEM"
Power window NOTEGW-13, "POWER WINDOW SYSTEM"
Sunroof NOTERF-10, "SUNROOF"
Automatic drive positioner NOTESE-11, "AUTOMATIC DRIVE POSITIONER"
Room lamp timerLT-267, "INTERIOR ROOM LAMP"
System Reference
Panic alarmBL-220, "
VEHICLE SECURITY (THEFT WARNING) SYSTEM"
Theft warningBL-220, "VEHICLE SECURITY (THEFT WARNING) SYSTEM"
IVIS (NATS)BL-248, "IVIS (INFINITI VEHICLE IMMOBILIZER SYSTEM-NATS)"
HeadlampLT- 4 3 , "HEADLAMP (FOR USA) - XENON TYPE -"
LT- 8 , "HEADLAMP (FOR USA) - CONVENTIONAL TYPE -"
Auto light systemLT- 11 6 , "AUTO LIGHT SYSTEM"
Parking lamp, license plate, tail lampLT-249, "PARKING, LICENSE PLATE AND TAIL LAMPS"
Front fog lampLT-193, "FRONT FOG LAMP"
Front wiper and washer systemWW-4, "FRONT WIPER AND WASHER SYSTEM"
Rear window defoggerGW-73, "REAR WINDOW DEFOGGER"
System Reference
Turn signal and hazard warning lampsLT- 2 11 , "
TURN SIGNAL AND HAZARD WARNING LAMPS"
Warning chimeDI-60, "WARNING CHIME"
System Reference
Intelligent KeyBL-44, "
INTELLIGENT KEY SYSTEM"
System Reference
Oil pressure warning lampDI-60, "
WARNING CHIME"
Page 935 of 5621
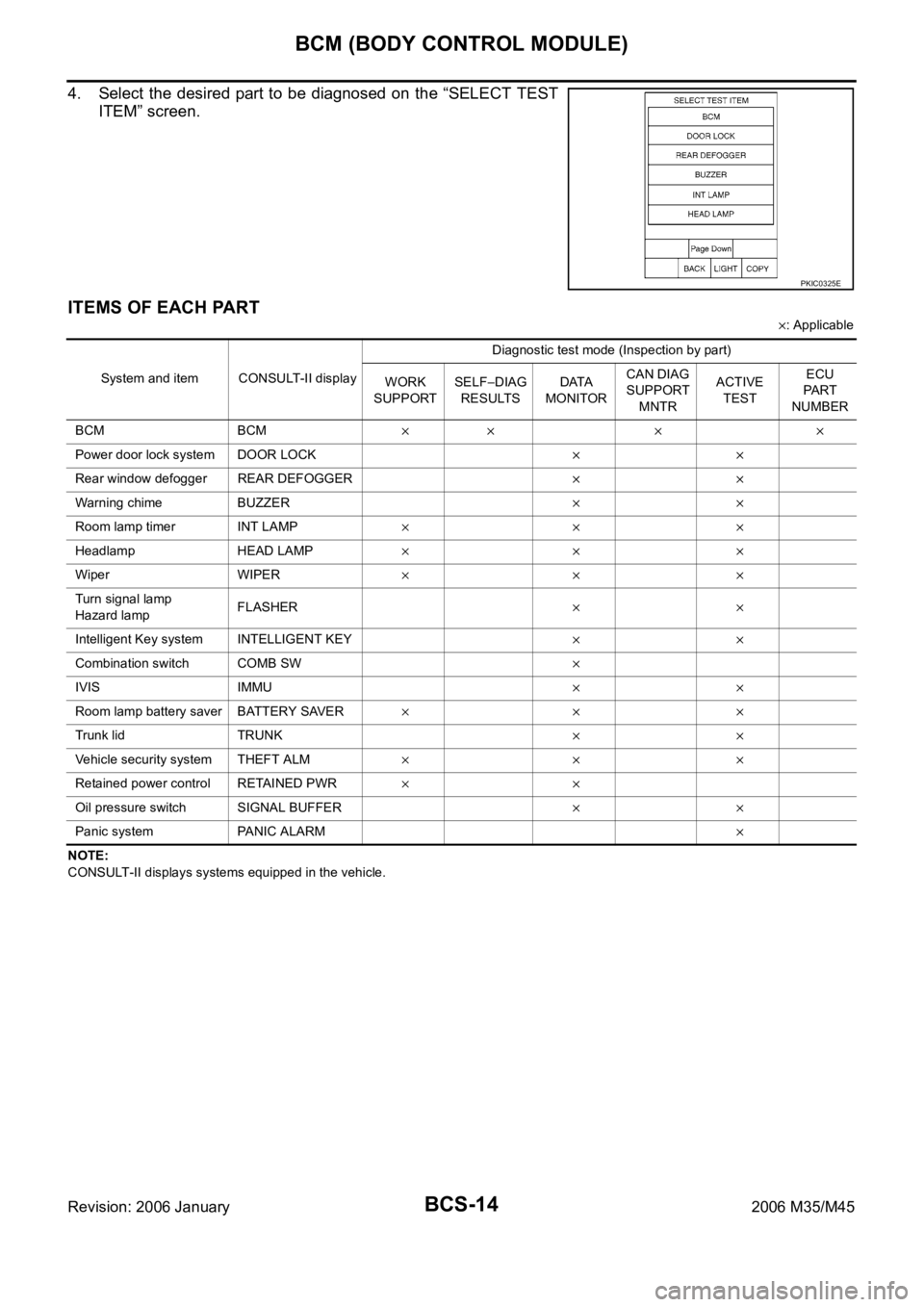
BCS-14
BCM (BODY CONTROL MODULE)
Revision: 2006 January2006 M35/M45
4. Select the desired part to be diagnosed on the “SELECT TEST
ITEM” screen.
ITEMS OF EACH PART
: Applicable
NOTE:
CONSULT-II displays systems equipped in the vehicle.
PKIC0325E
System and item CONSULT-II displayDiagnostic test mode (Inspection by part)
WORK
SUPPORTSELFDIAG
RESULTSDATA
MONITORCAN DIAG
SUPPORT
MNTRACTIVE
TESTECU
PA R T
NUMBER
BCM BCM
Power door lock system DOOR LOCK
Rear window defogger REAR DEFOGGER
Warning chime BUZZER
Room lamp timer INT LAMP
Headlamp HEAD LAMP
Wiper WIPER
Turn signal lamp
Hazard lampFLASHER
Intelligent Key system INTELLIGENT KEY
Combination switch COMB SW
IVIS IMMU
Room lamp battery saver BATTERY SAVER
Trunk lid TRUNK
Vehicle security system THEFT ALM
Retained power control RETAINED PWR
Oil pressure switch SIGNAL BUFFER
Panic system PANIC ALARM
Page 1278 of 5621
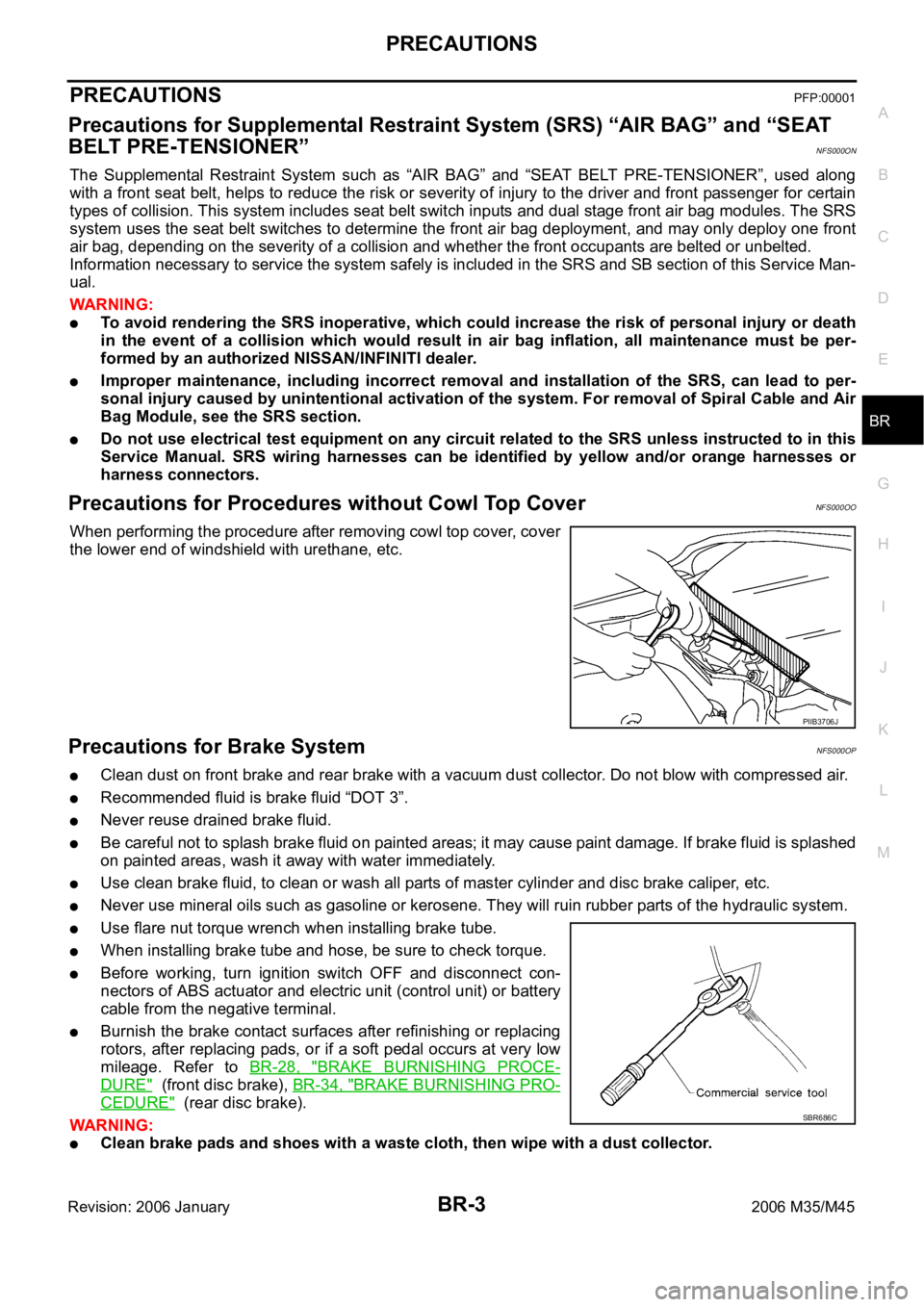
PRECAUTIONS
BR-3
C
D
E
G
H
I
J
K
L
MA
B
BR
Revision: 2006 January2006 M35/M45
PRECAUTIONSPFP:00001
Precautions for Supplemental Restraint System (SRS) “AIR BAG” and “SEAT
BELT PRE-TENSIONER”
NFS000ON
The Supplemental Restraint System such as “AIR BAG” and “SEAT BELT PRE-TENSIONER”, used along
with a front seat belt, helps to reduce the risk or severity of injury to the driver and front passenger for certain
types of collision. This system includes seat belt switch inputs and dual stage front air bag modules. The SRS
system uses the seat belt switches to determine the front air bag deployment, and may only deploy one front
air bag, depending on the severity of a collision and whether the front occupants are belted or unbelted.
Information necessary to service the system safely is included in the SRS and SB section of this Service Man-
ual.
WAR NING :
To avoid rendering the SRS inoperative, which could increase the risk of personal injury or death
in the event of a collision which would result in air bag inflation, all maintenance must be per-
formed by an authorized NISSAN/INFINITI dealer.
Improper maintenance, including incorrect removal and installation of the SRS, can lead to per-
sonal injury caused by unintentional activation of the system. For removal of Spiral Cable and Air
Bag Module, see the SRS section.
Do not use electrical test equipment on any circuit related to the SRS unless instructed to in this
Service Manual. SRS wiring harnesses can be identified by yellow and/or orange harnesses or
harness connectors.
Precautions for Procedures without Cowl Top CoverNFS000OO
When performing the procedure after removing cowl top cover, cover
the lower end of windshield with urethane, etc.
Precautions for Brake SystemNFS000OP
Clean dust on front brake and rear brake with a vacuum dust collector. Do not blow with compressed air.
Recommended fluid is brake fluid “DOT 3”.
Never reuse drained brake fluid.
Be careful not to splash brake fluid on painted areas; it may cause paint damage. If brake fluid is splashed
on painted areas, wash it away with water immediately.
Use clean brake fluid, to clean or wash all parts of master cylinder and disc brake caliper, etc.
Never use mineral oils such as gasoline or kerosene. They will ruin rubber parts of the hydraulic system.
Use flare nut torque wrench when installing brake tube.
When installing brake tube and hose, be sure to check torque.
Before working, turn ignition switch OFF and disconnect con-
nectors of ABS actuator and electric unit (control unit) or battery
cable from the negative terminal.
Burnish the brake contact surfaces after refinishing or replacing
rotors, after replacing pads, or if a soft pedal occurs at very low
mileage. Refer to BR-28, "
BRAKE BURNISHING PROCE-
DURE" (front disc brake), BR-34, "BRAKE BURNISHING PRO-
CEDURE" (rear disc brake).
WAR NING :
Clean brake pads and shoes with a waste cloth, then wipe with a dust collector.
PIIB3706J
SBR686C
Page 1285 of 5621
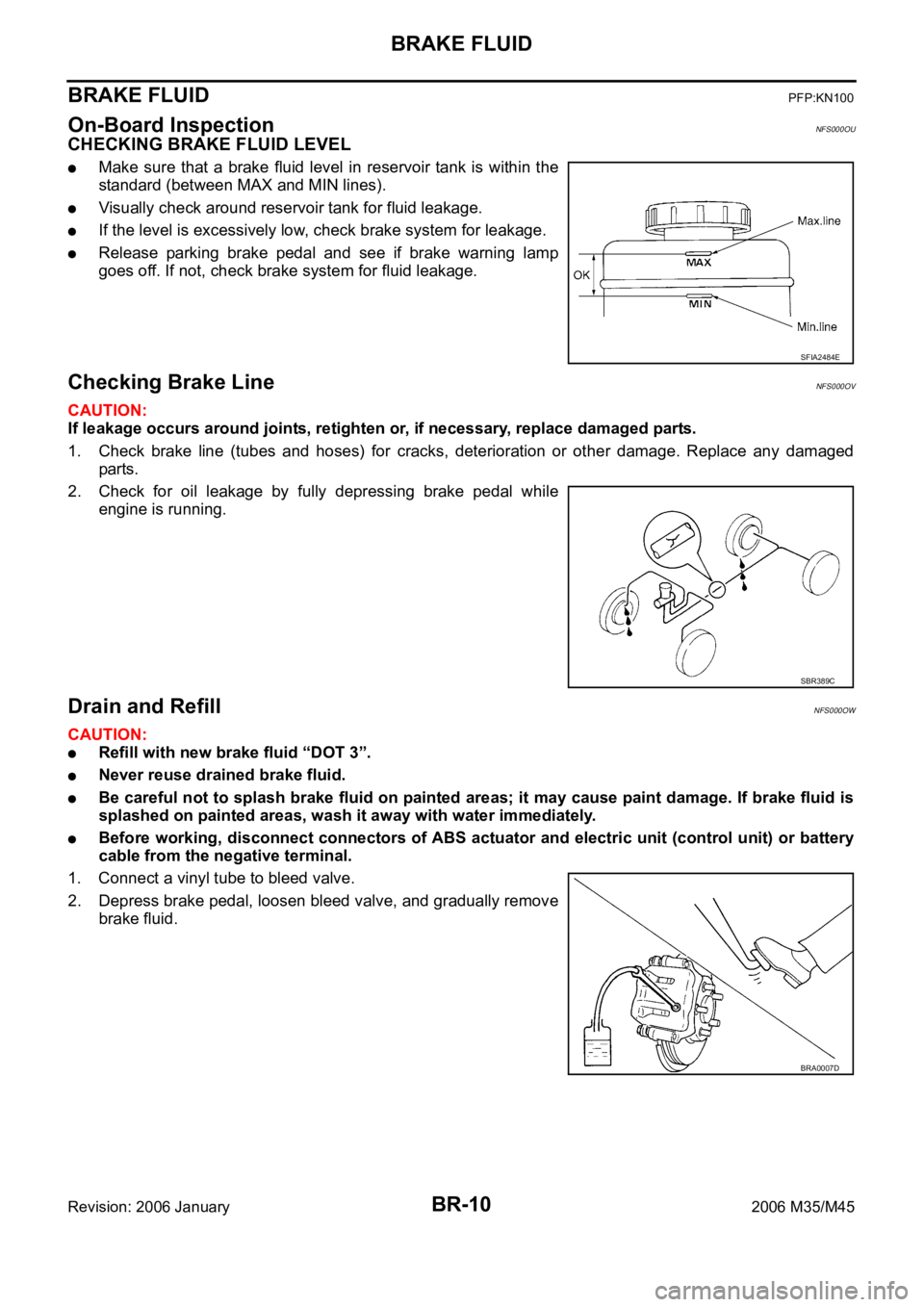
BR-10
BRAKE FLUID
Revision: 2006 January2006 M35/M45
BRAKE FLUIDPFP:KN100
On-Board Inspection NFS000OU
CHECKING BRAKE FLUID LEVEL
Make sure that a brake fluid level in reservoir tank is within the
standard (between MAX and MIN lines).
Visually check around reservoir tank for fluid leakage.
If the level is excessively low, check brake system for leakage.
Release parking brake pedal and see if brake warning lamp
goes off. If not, check brake system for fluid leakage.
Checking Brake LineNFS000OV
CAUTION:
If leakage occurs around joints, retighten or, if necessary, replace damaged parts.
1. Check brake line (tubes and hoses) for cracks, deterioration or other damage. Replace any damaged
parts.
2. Check for oil leakage by fully depressing brake pedal while
engine is running.
Drain and RefillNFS000OW
CAUTION:
Refill with new brake fluid “DOT 3”.
Never reuse drained brake fluid.
Be careful not to splash brake fluid on painted areas; it may cause paint damage. If brake fluid is
splashed on painted areas, wash it away with water immediately.
Before working, disconnect connectors of ABS actuator and electric unit (control unit) or battery
cable from the negative terminal.
1. Connect a vinyl tube to bleed valve.
2. Depress brake pedal, loosen bleed valve, and gradually remove
brake fluid.
SFIA2484E
SBR389C
BRA0007D
Page 1291 of 5621
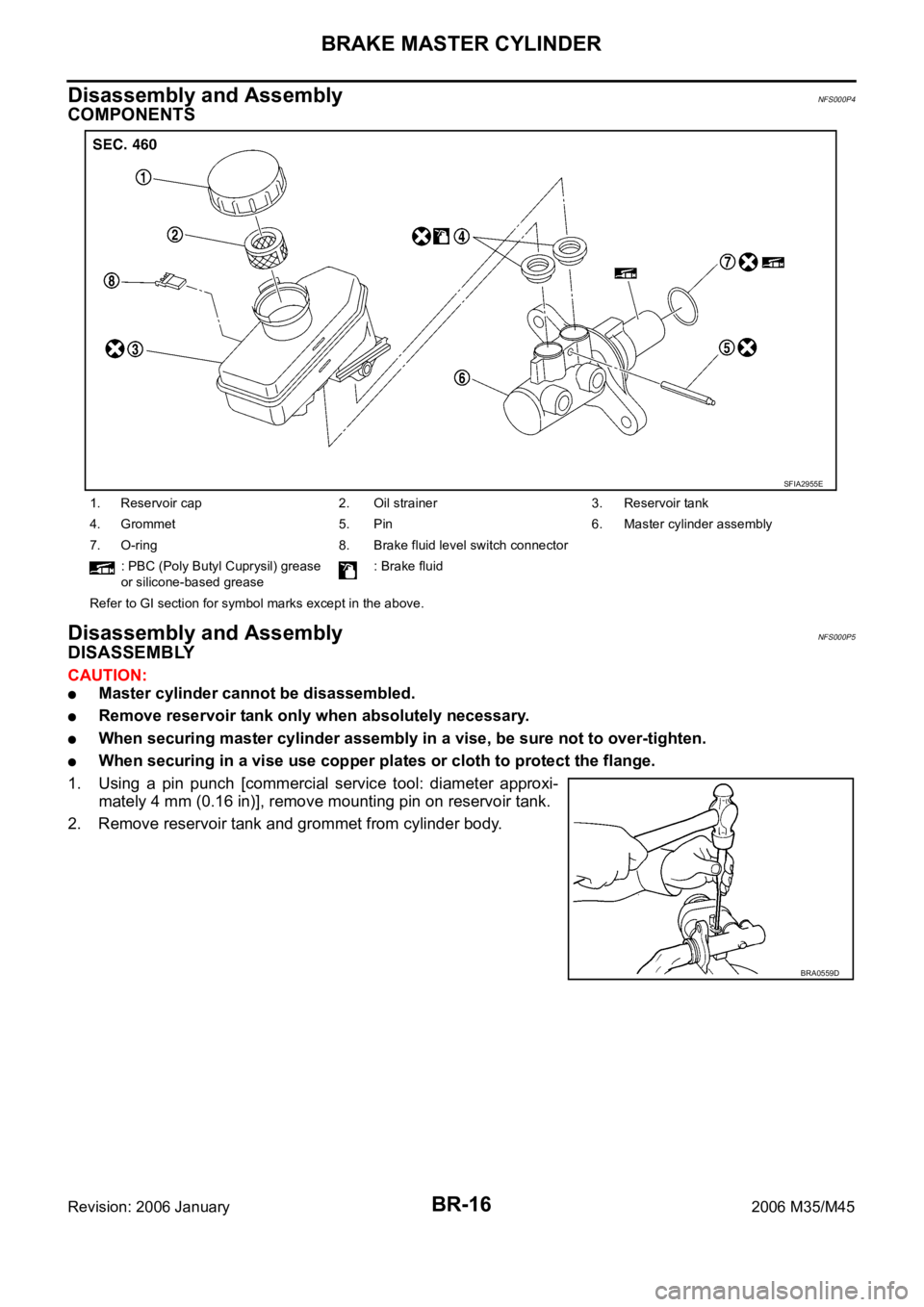
BR-16
BRAKE MASTER CYLINDER
Revision: 2006 January2006 M35/M45
Disassembly and AssemblyNFS000P4
COMPONENTS
Disassembly and AssemblyNFS000P5
DISASSEMBLY
CAUTION:
Master cylinder cannot be disassembled.
Remove reservoir tank only when absolutely necessary.
When securing master cylinder assembly in a vise, be sure not to over-tighten.
When securing in a vise use copper plates or cloth to protect the flange.
1. Using a pin punch [commercial service tool: diameter approxi-
mately 4 mm (0.16 in)], remove mounting pin on reservoir tank.
2. Remove reservoir tank and grommet from cylinder body.
1. Reservoir cap 2. Oil strainer 3. Reservoir tank
4. Grommet 5. Pin 6. Master cylinder assembly
7. O-ring 8. Brake fluid level switch connector
: PBC (Poly Butyl Cuprysil) grease
or silicone-based grease: Brake fluid
Refer to GI section for symbol marks except in the above.
SFIA2955E
BRA0559D