Oil INFINITI M35 2006 Factory Service Manual
[x] Cancel search | Manufacturer: INFINITI, Model Year: 2006, Model line: M35, Model: INFINITI M35 2006Pages: 5621, PDF Size: 65.56 MB
Page 1379 of 5621
![INFINITI M35 2006 Factory Service Manual CO-4
[VQ35DE]
PRECAUTIONS
Revision: 2006 January2006 M35/M45
3. Attach liquid gasket tube to the tube presser [SST: WS39930000
(—)].
Use Genuine RTV Silicone Sealant or equivalent. Refer to
INFINITI M35 2006 Factory Service Manual CO-4
[VQ35DE]
PRECAUTIONS
Revision: 2006 January2006 M35/M45
3. Attach liquid gasket tube to the tube presser [SST: WS39930000
(—)].
Use Genuine RTV Silicone Sealant or equivalent. Refer to](/img/42/57023/w960_57023-1378.png)
CO-4
[VQ35DE]
PRECAUTIONS
Revision: 2006 January2006 M35/M45
3. Attach liquid gasket tube to the tube presser [SST: WS39930000
(—)].
Use Genuine RTV Silicone Sealant or equivalent. Refer to
GI-48, "
RECOMMENDED CHEMICAL PRODUCTS AND
SEALANTS" .
4. Apply liquid gasket without breaks to the specified location with
the specified dimensions.
If there is a groove for the liquid gasket application, apply liq-
uid gasket to the groove.
As for the bolt holes, normally apply liquid gasket inside the
holes. Occasionally, it should be applied outside the holes.
Make sure to read the text of service manual.
Within five minutes of liquid gasket application, install the mat-
ing component.
If liquid gasket protrudes, wipe it off immediately.
Do not retighten after mounting bolts and nuts the installation.
After 30 minutes or more have passed from the installation, fill
engine oil and engine coolant.
CAUTION:
If there are specific instructions in this manual, observe them.
EMA0622D
SEM159F
Page 1391 of 5621
![INFINITI M35 2006 Factory Service Manual CO-16
[VQ35DE]
RADIATOR
Revision: 2006 January2006 M35/M45
Minimize the lift of A/C condenser to prevent load from being applied to A/C piping.
e. After removing the radiator, place the A/C con INFINITI M35 2006 Factory Service Manual CO-16
[VQ35DE]
RADIATOR
Revision: 2006 January2006 M35/M45
Minimize the lift of A/C condenser to prevent load from being applied to A/C piping.
e. After removing the radiator, place the A/C con](/img/42/57023/w960_57023-1390.png)
CO-16
[VQ35DE]
RADIATOR
Revision: 2006 January2006 M35/M45
Minimize the lift of A/C condenser to prevent load from being applied to A/C piping.
e. After removing the radiator, place the A/C condenser on the radiator core support to prevent load from
being applied to piping. And then, temporarily secure them using a rope to prevent them from being
dropped.
INSTALLATION
Installation is the reverse order of removal.
INSPECTION AFTER INSTALLATION
Check for leaks of engine coolant using the radiator cap tester adapter [SST: EG17650301 (J33984-A)]
and the radiator cap tester (commercial service tool). Refer to CO-11, "
LEAK CHECK" .
Start and warm up the engine. Visually make sure that there is no leaks of engine coolant and A/T fluid.
Checking Radiator CapNBS004QU
Check valve seat of radiator cap.
–Check if valve seat is swollen to the extent that the edge of the
plunger cannot be seen when watching it vertically from the top.
–Check if valve seat has no soil and damage.
Pull negative-pressure valve to open it, and make sure that it
close completely when released.
–Make sure that there is no dirt or damage on the valve seat of
radiator cap negative-pressure valve.
–Make sure that there are no unusualness in the opening and
closing conditions of negative-pressure valve.
Check radiator cap relief pressure.
–When connecting radiator cap to the radiator cap tester (com-
mercial service tool) and the radiator cap tester adapter (SST),
apply engine coolant to the cap seal surface.
Replace radiator cap if there is an unusualness related to the above three.
CAUTION:
When installing radiator cap, thoroughly wipe out the radiator filler neck to remove any waxy residue
or foreign material.
Checking RadiatorNBS004QV
Check radiator for mud or clogging. If necessary, clean radiator as follows.
Be careful not to bend or damage radiator fins.
PBIC2816E
SMA967B
Standard:
78 - 98 kPa (0.8 - 1.0 kg/cm
2 , 11 - 14 psi)
Limit:
59 kPa (0.6 kg/cm
2 , 9 psi)
SLC755A
Page 1401 of 5621
![INFINITI M35 2006 Factory Service Manual CO-26
[VQ35DE]
WATER PUMP
Revision: 2006 January2006 M35/M45
b. Screw M8 bolts [pitch: 1.25 mm (0.049 in) length: approx. 50
mm (1.97 in)] into water pumps upper and lower mounting b INFINITI M35 2006 Factory Service Manual CO-26
[VQ35DE]
WATER PUMP
Revision: 2006 January2006 M35/M45
b. Screw M8 bolts [pitch: 1.25 mm (0.049 in) length: approx. 50
mm (1.97 in)] into water pumps upper and lower mounting b](/img/42/57023/w960_57023-1400.png)
CO-26
[VQ35DE]
WATER PUMP
Revision: 2006 January2006 M35/M45
b. Screw M8 bolts [pitch: 1.25 mm (0.049 in) length: approx. 50
mm (1.97 in)] into water pumps upper and lower mounting bolt
holes until they reach timing chain case. Then, alternately
tighten each bolt for a half turn, and pull out water pump.
CAUTION:
Pull straight out while preventing vane from contacting
socket in installation area.
Remove water pump without causing sprocket to contact
timing chain.
c. Remove M8 bolts and O-rings from water pump.
CAUTION:
Do not disassemble water pump.
INSPECTION AFTER REMOVAL
Check for badly rusted or corroded water pump body assembly.
Check for rough operation due to excessive end play.
If anything is found, replace water pump.
INSTALLATION
1. Install new O-rings to water pump.
Apply engine oil and engine coolant to O-rings as shown in
the figure.
Locate O-ring with white paint mark to engine front side.
2. Install water pump.
CAUTION:
Do not allow cylinder block to nip O-rings when installing
water pump.
Make sure timing chain and water pump sprocket are
engaged.
Insert water pump by tightening mounting bolts alternately
and evenly.
3. Install timing chain tensioner (primary) as follows:
JLC357B
SLC943A
PBIC1397E
PBIC1058E
Page 1404 of 5621
![INFINITI M35 2006 Factory Service Manual WATER INLET AND THERMOSTAT ASSEMBLY
CO-29
[VQ35DE]
C
D
E
F
G
H
I
J
K
L
MA
CO
Revision: 2006 January2006 M35/M45
WATER INLET AND THERMOSTAT ASSEMBLYPFP:21200
ComponentsNBS004R3
Removal and Installation INFINITI M35 2006 Factory Service Manual WATER INLET AND THERMOSTAT ASSEMBLY
CO-29
[VQ35DE]
C
D
E
F
G
H
I
J
K
L
MA
CO
Revision: 2006 January2006 M35/M45
WATER INLET AND THERMOSTAT ASSEMBLYPFP:21200
ComponentsNBS004R3
Removal and Installation](/img/42/57023/w960_57023-1403.png)
WATER INLET AND THERMOSTAT ASSEMBLY
CO-29
[VQ35DE]
C
D
E
F
G
H
I
J
K
L
MA
CO
Revision: 2006 January2006 M35/M45
WATER INLET AND THERMOSTAT ASSEMBLYPFP:21200
ComponentsNBS004R3
Removal and InstallationNBS004R4
REMOVAL
1. Remove engine room cover (RH and LH). Refer to EM-14, "ENGINE ROOM COVER" .
2. Remove air duct (inlet). Refer to EM-17, "
AIR CLEANER AND AIR DUCT" .
3. Remove front engine undercover using power tool.
4. Drain engine coolant from radiator drain plug at the bottom of radiator, and from water drain plug at the
front of cylinder block. Refer to CO-11, "
Changing Engine Coolant" and CO-24, "WATER PUMP" .
CAUTION:
Perform this step when the engine is cold.
Do not spill engine coolant on drive belts.
5. Disconnect radiator hose (lower) and oil cooler water hose from water inlet and thermostat assembly.
6. Remove water inlet and thermostat assembly.
CAUTION:
Do not disassemble water inlet and thermostat assembly.
Replace them as a unit, if necessary.
1. Water inlet and thermostat assembly 2. Gasket
SBIA0483E
SLC962AB
Page 1420 of 5621
![INFINITI M35 2006 Factory Service Manual RADIATOR
CO-45
[VK45DE]
C
D
E
F
G
H
I
J
K
L
MA
CO
Revision: 2006 January2006 M35/M45
INSTALLATION
Installation is the reverse order of removal.
INSPECTION AFTER INSTALLATION
Check for leaks of eng INFINITI M35 2006 Factory Service Manual RADIATOR
CO-45
[VK45DE]
C
D
E
F
G
H
I
J
K
L
MA
CO
Revision: 2006 January2006 M35/M45
INSTALLATION
Installation is the reverse order of removal.
INSPECTION AFTER INSTALLATION
Check for leaks of eng](/img/42/57023/w960_57023-1419.png)
RADIATOR
CO-45
[VK45DE]
C
D
E
F
G
H
I
J
K
L
MA
CO
Revision: 2006 January2006 M35/M45
INSTALLATION
Installation is the reverse order of removal.
INSPECTION AFTER INSTALLATION
Check for leaks of engine coolant using radiator cap tester adapter [SST: EG17650301 (J33984-A)] and
radiator cap tester (commercial service tool). Refer to CO-40, "
LEAK CHECK" .
Start and warm up engine. Visually Check if there is no leaks of engine coolant and A/T fluid.
Checking Radiator CapNBS004RI
Check valve seat of radiator cap.
–Check if valve seat is swollen to the extent that the edge of the
plunger cannot be seen when watching it vertically from the top.
–Check if valve seat has no soil and damage.
Pull negative-pressure valve to open it, and make sure that it
close completely when released.
–Make sure that there is no dirt or damage on the valve seat of
radiator cap negative-pressure valve.
–Make sure that there are no unusualness in the opening and
closing conditions of negative-pressure valve.
Check radiator cap relief pressure.
–When connecting radiator cap to the radiator cap tester adapter
(SST) and the radiator cap tester (Commercial service tool),
apply engine coolant to the cap seal surface.
Replace radiator cap if there is an unusualness.
CAUTION:
When installing a radiator cap, thoroughly wipe out the radiator filler neck to remove any waxy residue
or foreign material.
Checking RadiatorNBS004RJ
Check radiator for mud or clogging. If necessary, clean radiator as follows:
Be careful not to bend or damage the radiator fins.
When radiator is cleaned without removal, remove all surrounding parts such as cooling fan, radiator
shroud and horns. Then tape the harness and electrical connectors to prevent water from entering.
1. Apply water by hose to the back side of the radiator core vertically downward.
2. Apply water again to all radiator core surface once per minute.
PBIC2816E
SMA967B
Standard : 78 - 98 kPa (0.8 - 1.0 kg/cm2 , 11 - 14 psi)
Limit : 59 kPa (0.6 kg/cm
2 , 9 psi)
SLC755A
Page 1434 of 5621
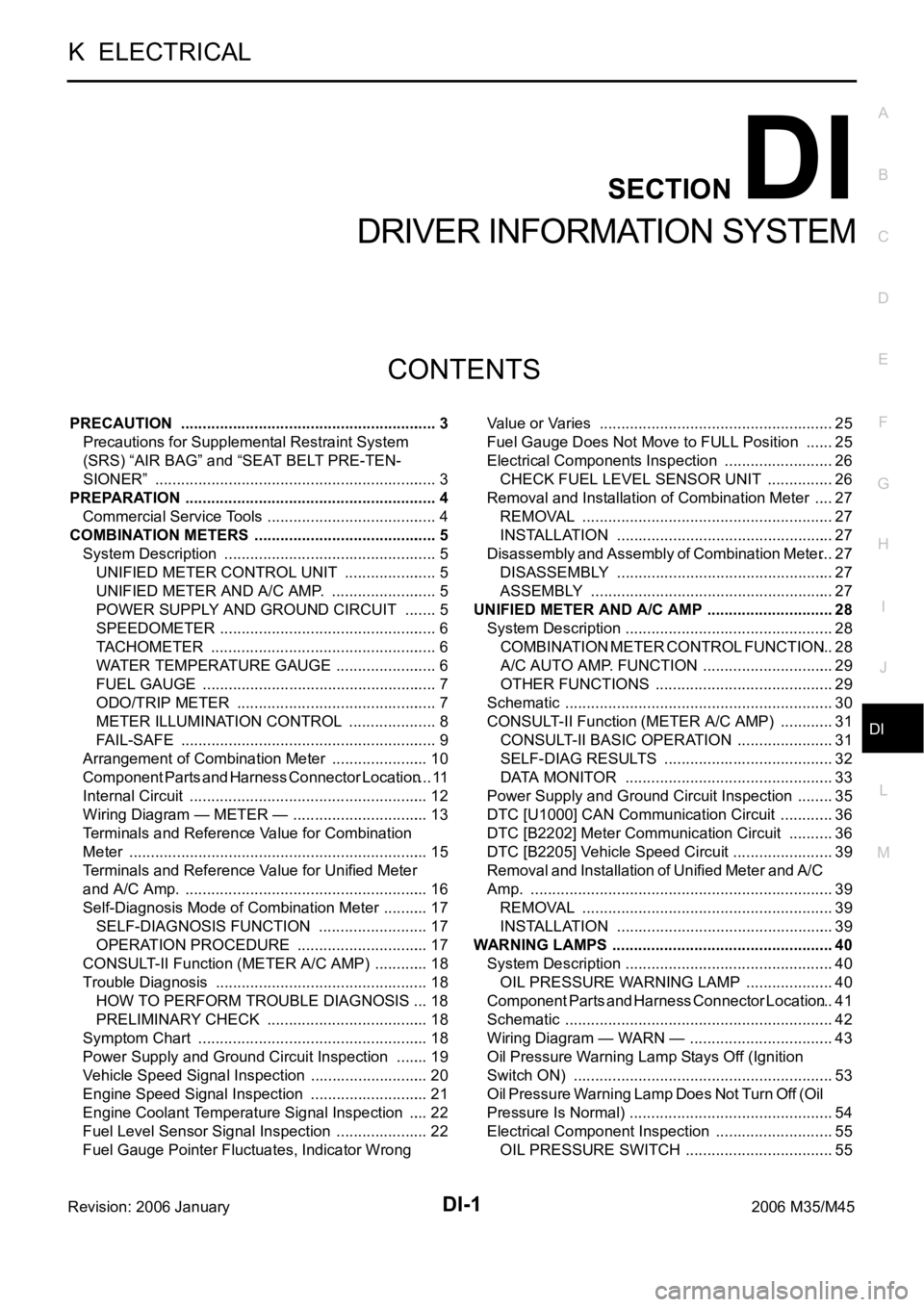
DI-1
DRIVER INFORMATION SYSTEM
K ELECTRICAL
CONTENTS
C
D
E
F
G
H
I
J
L
M
SECTION DI
A
B
DI
Revision: 2006 January2006 M35/M45
DRIVER INFORMATION SYSTEM
PRECAUTION ............................................................ 3
Precautions for Supplemental Restraint System
(SRS) “AIR BAG” and “SEAT BELT PRE-TEN-
SIONER” .................................................................. 3
PREPARATION ........................................................... 4
Commercial Service Tools ........................................ 4
COMBINATION METERS ........................................... 5
System Description .................................................. 5
UNIFIED METER CONTROL UNIT ...................... 5
UNIFIED METER AND A/C AMP. ......................... 5
POWER SUPPLY AND GROUND CIRCUIT ........ 5
SPEEDOMETER ................................................... 6
TACHOMETER ..................................................... 6
WATER TEMPERATURE GAUGE ........................ 6
FUEL GAUGE ....................................................... 7
ODO/TRIP METER ............................................... 7
METER ILLUMINATION CONTROL ..................... 8
FAIL-SAFE ............................................................ 9
Arrangement of Combination Meter ....................... 10
Component Parts and Harness Connector Location .... 11
Internal Circuit ........................................................ 12
Wiring Diagram — METER — ................................ 13
Terminals and Reference Value for Combination
Meter ...................................................................... 15
Terminals and Reference Value for Unified Meter
and A/C Amp. ......................................................... 16
Self-Diagnosis Mode of Combination Meter ........... 17
SELF-DIAGNOSIS FUNCTION .......................... 17
OPERATION PROCEDURE ............................... 17
CONSULT-II Function (METER A/C AMP) ............. 18
Trouble Diagnosis .................................................. 18
HOW TO PERFORM TROUBLE DIAGNOSIS ... 18
PRELIMINARY CHECK ...................................... 18
Symptom Chart ...................................................... 18
Power Supply and Ground Circuit Inspection ........ 19
Vehicle Speed Signal Inspection ............................ 20
Engine Speed Signal Inspection ............................ 21
Engine Coolant Temperature Signal Inspection ..... 22
Fuel Level Sensor Signal Inspection ...................... 22
Fuel Gauge Pointer Fluctuates, Indicator Wrong Value or Varies ....................................................... 25
Fuel Gauge Does Not Move to FULL Position ....... 25
Electrical Components Inspection .......................... 26
CHECK FUEL LEVEL SENSOR UNIT ................ 26
Removal and Installation of Combination Meter ..... 27
REMOVAL ........................................................
... 27
INSTALLATION ................................................... 27
Disassembly and Assembly of Combination Meter ... 27
DISASSEMBLY ................................................... 27
ASSEMBLY ......................................................... 27
UNIFIED METER AND A/C AMP ...........................
... 28
System Description ................................................. 28
COMBINATION METER CONTROL FUNCTION ... 28
A/C AUTO AMP. FUNCTION ............................... 29
OTHER FUNCTIONS .......................................... 29
Schematic ............................................................... 30
CONSULT-II Function (METER A/C AMP) ............. 31
CONSULT-II BASIC OPERATION ....................... 31
SELF-DIAG RESULTS ........................................ 32
DATA MONITOR ................................................. 33
Power Supply and Ground Circuit Inspection ......... 35
DTC [U1000] CAN Communication Circuit ............. 36
DTC [B2202] Meter Communication Circuit ........... 36
DTC [B2205] Vehicle Speed Circuit ........................ 39
Removal and Installation of Unified Meter and A/C
Amp. ....................................................................... 39
REMOVAL ........................................................
... 39
INSTALLATION ................................................... 39
WARNING LAMPS .................................................... 40
System Description ................................................. 40
OIL PRESSURE WARNING LAMP ..................... 40
Component Parts and Harness Connector Location ... 41
Schematic ............................................................... 42
Wiring Diagram — WARN — .................................. 43
Oil Pressure Warning Lamp Stays Off (Ignition
Switch ON) ............................................................. 53
Oil Pressure Warning Lamp Does Not Turn Off (Oil
Pressure Is Normal) ................................................ 54
Electrical Component Inspection ............................ 55
OIL PRESSURE SWITCH ................................... 55
Page 1442 of 5621
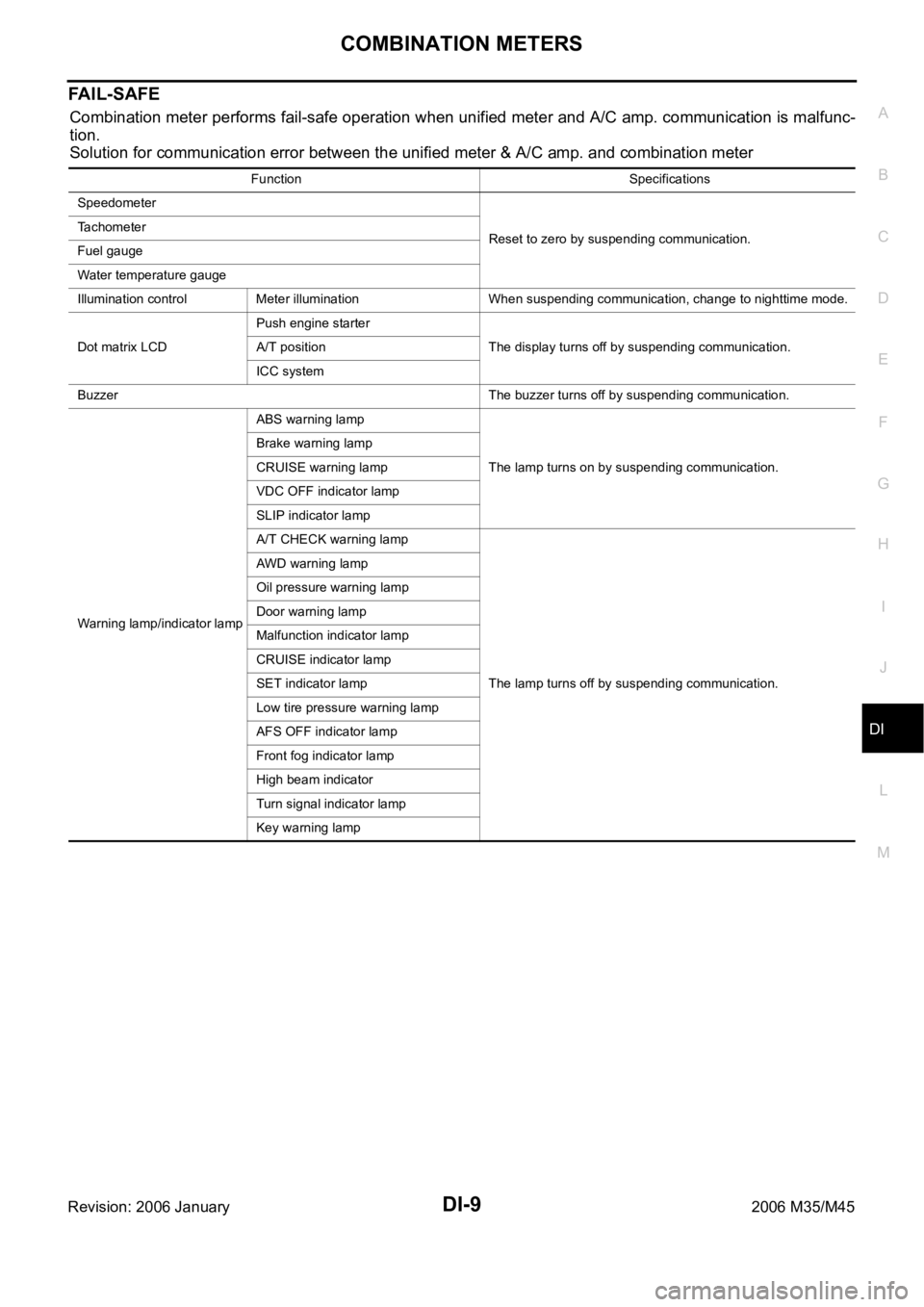
COMBINATION METERS
DI-9
C
D
E
F
G
H
I
J
L
MA
B
DI
Revision: 2006 January2006 M35/M45
FA I L - S A F E
Combination meter performs fail-safe operation when unified meter and A/C amp. communication is malfunc-
tion.
Solution for communication error between the unified meter & A/C amp. and combination meter
Function Specifications
Speedometer
Reset to zero by suspending communication. Tachometer
Fuel gauge
Water temperature gauge
Illumination control Meter illumination When suspending communication, change to nighttime mode.
Dot matrix LCDPush engine starter
The display turns off by suspending communication. A/T position
ICC system
Buzzer The buzzer turns off by suspending communication.
Warning lamp/indicator lampABS warning lamp
The lamp turns on by suspending communication. Brake warning lamp
CRUISE warning lamp
VDC OFF indicator lamp
SLIP indicator lamp
A/T CHECK warning lamp
The lamp turns off by suspending communication. AWD warning lamp
Oil pressure warning lamp
Door warning lamp
Malfunction indicator lamp
CRUISE indicator lamp
SET indicator lamp
Low tire pressure warning lamp
AFS OFF indicator lamp
Front fog indicator lamp
High beam indicator
Turn signal indicator lamp
Key warning lamp
Page 1461 of 5621
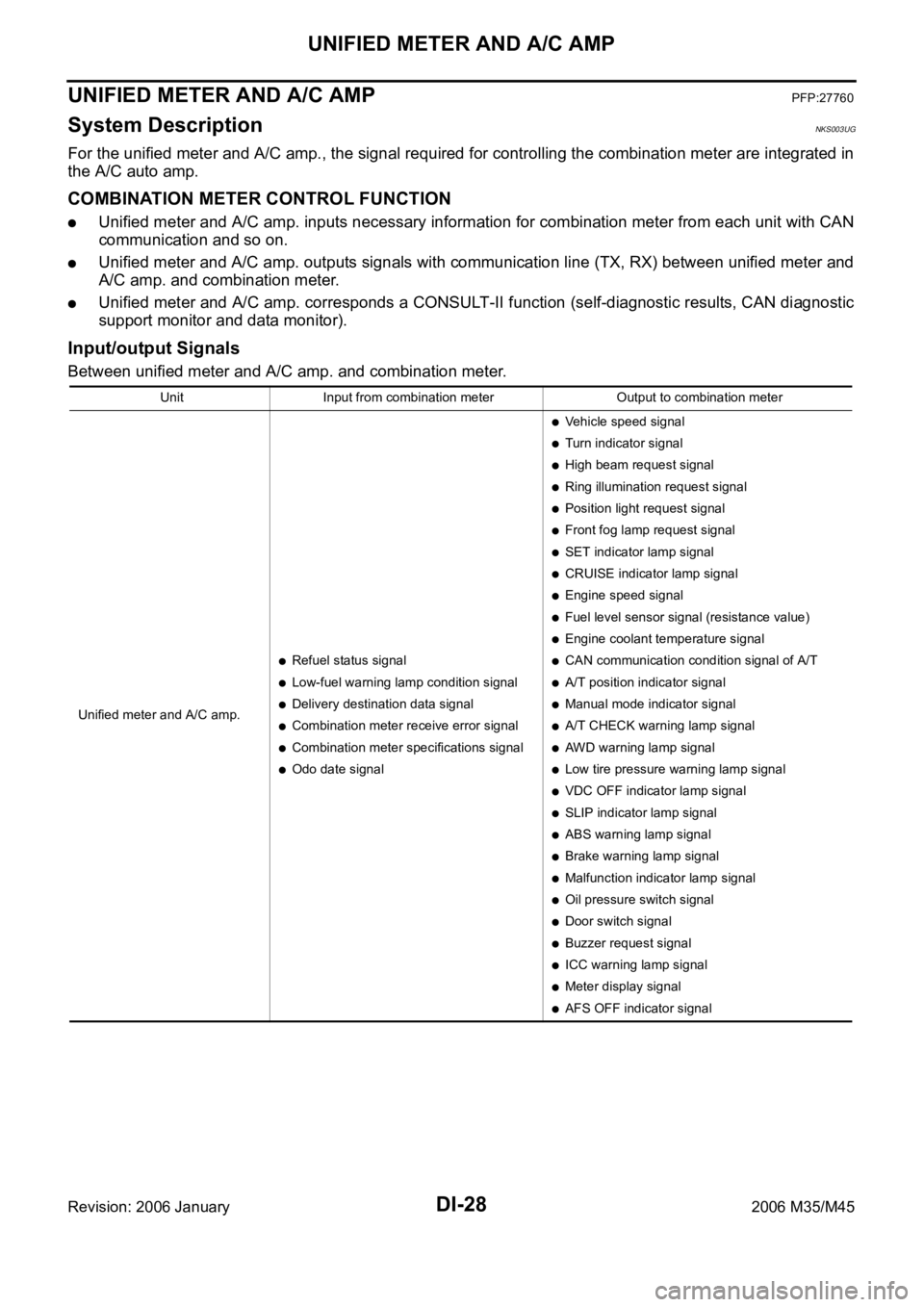
DI-28
UNIFIED METER AND A/C AMP
Revision: 2006 January2006 M35/M45
UNIFIED METER AND A/C AMPPFP:27760
System DescriptionNKS003UG
For the unified meter and A/C amp., the signal required for controlling the combination meter are integrated in
the A/C auto amp.
COMBINATION METER CONTROL FUNCTION
Unified meter and A/C amp. inputs necessary information for combination meter from each unit with CAN
communication and so on.
Unified meter and A/C amp. outputs signals with communication line (TX, RX) between unified meter and
A/C amp. and combination meter.
Unified meter and A/C amp. corresponds a CONSULT-II function (self-diagnostic results, CAN diagnostic
support monitor and data monitor).
Input/output Signals
Between unified meter and A/C amp. and combination meter.
Unit Input from combination meter Output to combination meter
Unified meter and A/C amp.
Refuel status signal
Low-fuel warning lamp condition signal
Delivery destination data signal
Combination meter receive error signal
Combination meter specifications signal
Odo date signal
Vehicle speed signal
Turn indicator signal
High beam request signal
Ring illumination request signal
Position light request signal
Front fog lamp request signal
SET indicator lamp signal
CRUISE indicator lamp signal
Engine speed signal
Fuel level sensor signal (resistance value)
Engine coolant temperature signal
CAN communication condition signal of A/T
A/T position indicator signal
Manual mode indicator signal
A/T CHECK warning lamp signal
AWD warning lamp signal
Low tire pressure warning lamp signal
VDC OFF indicator lamp signal
SLIP indicator lamp signal
ABS warning lamp signal
Brake warning lamp signal
Malfunction indicator lamp signal
Oil pressure switch signal
Door switch signal
Buzzer request signal
ICC warning lamp signal
Meter display signal
AFS OFF indicator signal
Page 1466 of 5621
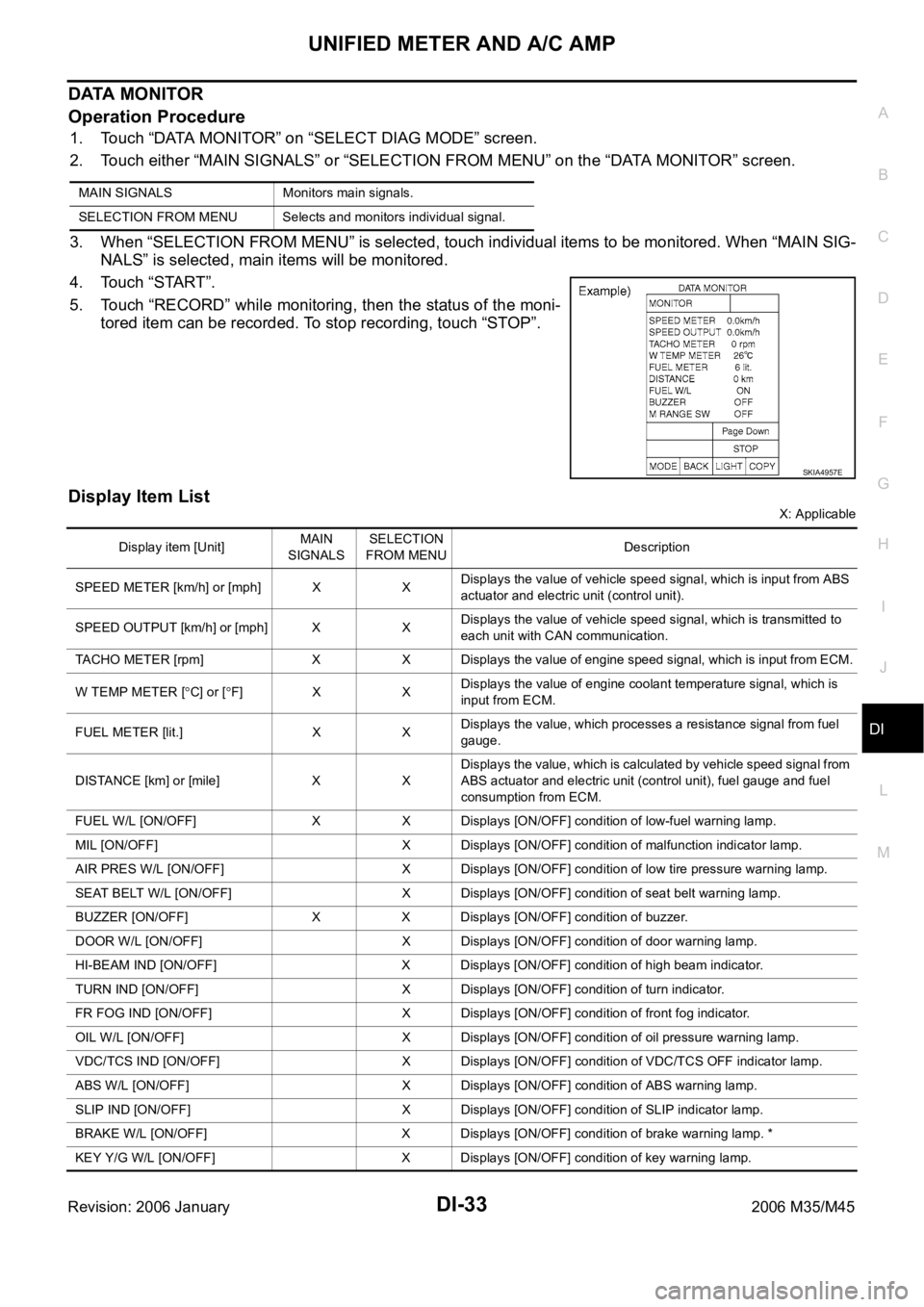
UNIFIED METER AND A/C AMP
DI-33
C
D
E
F
G
H
I
J
L
MA
B
DI
Revision: 2006 January2006 M35/M45
DATA MONITOR
Operation Procedure
1. Touch “DATA MONITOR” on “SELECT DIAG MODE” screen.
2. Touch either “MAIN SIGNALS” or “SELECTION FROM MENU” on the “DATA MONITOR” screen.
3. When “SELECTION FROM MENU” is selected, touch individual items to be monitored. When “MAIN SIG-
NALS” is selected, main items will be monitored.
4. Touch “START”.
5. Touch “RECORD” while monitoring, then the status of the moni-
tored item can be recorded. To stop recording, touch “STOP”.
Display Item List
X: Applicable MAIN SIGNALS Monitors main signals.
SELECTION FROM MENU Selects and monitors individual signal.
SKIA4957E
Display item [Unit]MAIN
SIGNALSSELECTION
FROM MENUDescription
SPEED METER [km/h] or [mph] X XDisplays the value of vehicle speed signal, which is input from ABS
actuator and electric unit (control unit).
SPEED OUTPUT [km/h] or [mph] X XDisplays the value of vehicle speed signal, which is transmitted to
each unit with CAN communication.
TACHO METER [rpm] X X Displays the value of engine speed signal, which is input from ECM.
W TEMP METER [
C] or [F] X XDisplays the value of engine coolant temperature signal, which is
input from ECM.
FUEL METER [lit.] X XDisplays the value, which processes a resistance signal from fuel
gauge.
DISTANCE [km] or [mile] X XDisplays the value, which is calculated by vehicle speed signal from
ABS actuator and electric unit (control unit), fuel gauge and fuel
consumption from ECM.
FUEL W/L [ON/OFF] X X Displays [ON/OFF] condition of low-fuel warning lamp.
MIL [ON/OFF] X Displays [ON/OFF] condition of malfunction indicator lamp.
AIR PRES W/L [ON/OFF] X Displays [ON/OFF] condition of low tire pressure warning lamp.
SEAT BELT W/L [ON/OFF] X Displays [ON/OFF] condition of seat belt warning lamp.
BUZZER [ON/OFF] X X Displays [ON/OFF] condition of buzzer.
DOOR W/L [ON/OFF] X Displays [ON/OFF] condition of door warning lamp.
HI-BEAM IND [ON/OFF] X Displays [ON/OFF] condition of high beam indicator.
TURN IND [ON/OFF] X Displays [ON/OFF] condition of turn indicator.
FR FOG IND [ON/OFF] X Displays [ON/OFF] condition of front fog indicator.
OIL W/L [ON/OFF] X Displays [ON/OFF] condition of oil pressure warning lamp.
VDC/TCS IND [ON/OFF] X Displays [ON/OFF] condition of VDC/TCS OFF indicator lamp.
ABS W/L [ON/OFF] X Displays [ON/OFF] condition of ABS warning lamp.
SLIP IND [ON/OFF] X Displays [ON/OFF] condition of SLIP indicator lamp.
BRAKE W/L [ON/OFF] X Displays [ON/OFF] condition of brake warning lamp. *
KEY Y/G W/L [ON/OFF] X Displays [ON/OFF] condition of key warning lamp.
Page 1473 of 5621
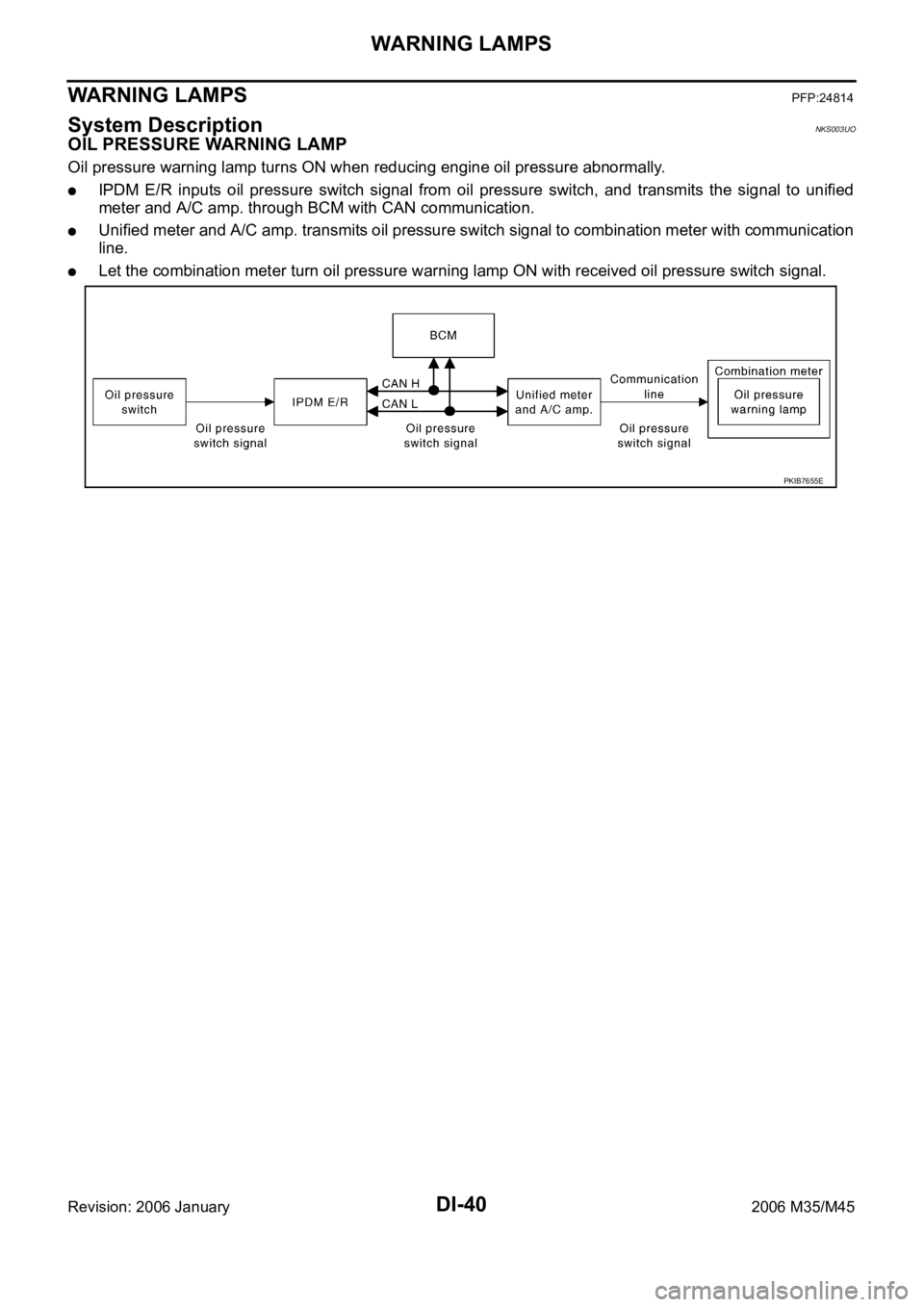
DI-40
WARNING LAMPS
Revision: 2006 January2006 M35/M45
WARNING LAMPSPFP:24814
System DescriptionNKS003UO
OIL PRESSURE WARNING LAMP
Oil pressure warning lamp turns ON when reducing engine oil pressure abnormally.
IPDM E/R inputs oil pressure switch signal from oil pressure switch, and transmits the signal to unified
meter and A/C amp. through BCM with CAN communication.
Unified meter and A/C amp. transmits oil pressure switch signal to combination meter with communication
line.
Let the combination meter turn oil pressure warning lamp ON with received oil pressure switch signal.
PKIB7655E