check INFINITI M35 2006 Factory Service Manual
[x] Cancel search | Manufacturer: INFINITI, Model Year: 2006, Model line: M35, Model: INFINITI M35 2006Pages: 5621, PDF Size: 65.56 MB
Page 4865 of 5621
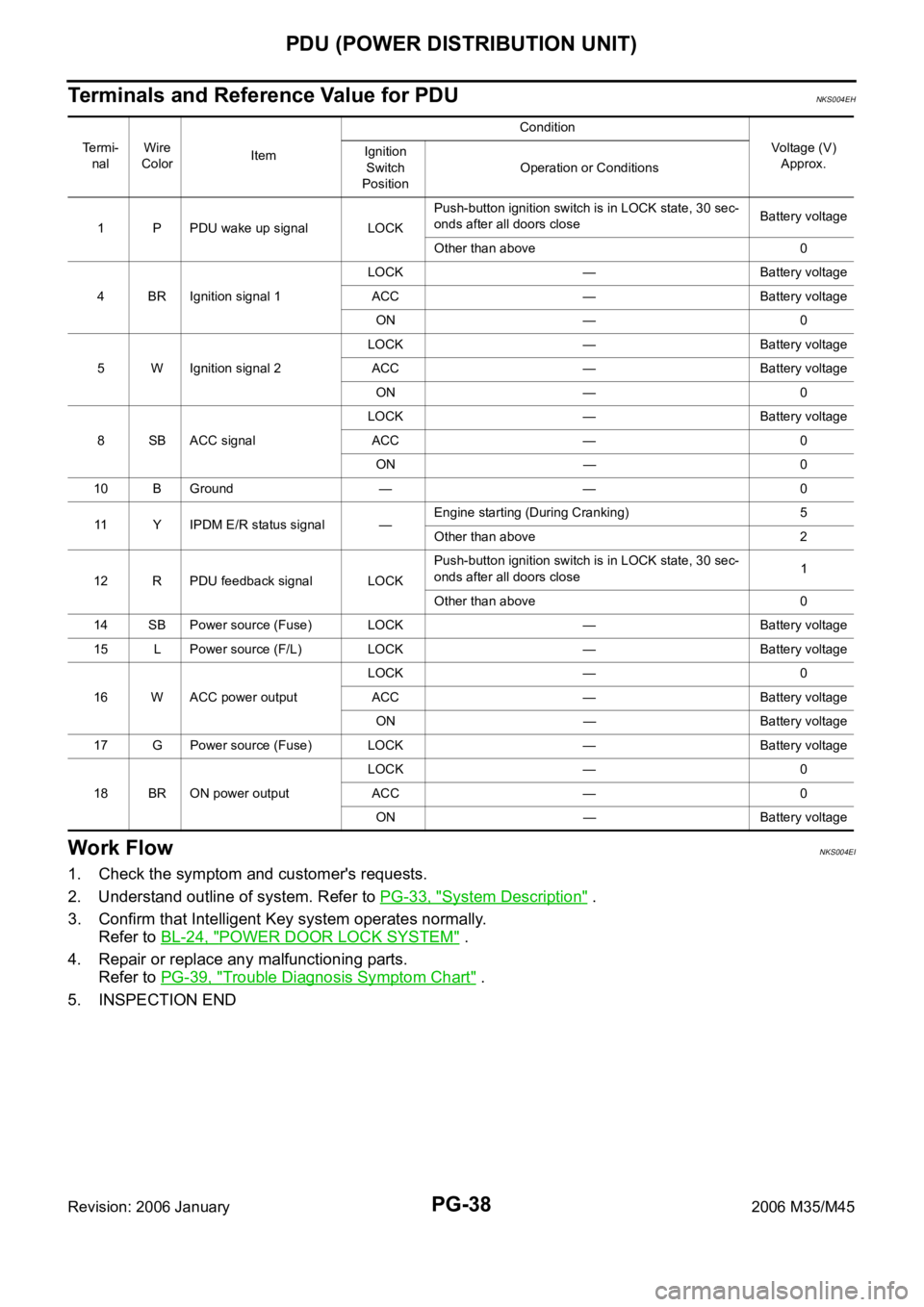
PG-38
PDU (POWER DISTRIBUTION UNIT)
Revision: 2006 January2006 M35/M45
Terminals and Reference Value for PDUNKS004EH
Work FlowNKS004EI
1. Check the symptom and customer's requests.
2. Understand outline of system. Refer to PG-33, "
System Description" .
3. Confirm that Intelligent Key system operates normally.
Refer to BL-24, "
POWER DOOR LOCK SYSTEM" .
4. Repair or replace any malfunctioning parts.
Refer to PG-39, "
Trouble Diagnosis Symptom Chart" .
5. INSPECTION END
Te r m i -
nalWire
ColorItemCondition
Voltage (V)
Approx. Ignition
Switch
PositionOperation or Conditions
1 P PDU wake up signal LOCKPush-button ignition switch is in LOCK state, 30 sec-
onds after all doors closeBattery voltage
Other than above 0
4 BR Ignition signal 1LOCK — Battery voltage
ACC — Battery voltage
ON — 0
5 W Ignition signal 2LOCK — Battery voltage
ACC — Battery voltage
ON — 0
8 SB ACC signalLOCK — Battery voltage
ACC — 0
ON — 0
10 B Ground — — 0
11 Y IPDM E/R status signal —Engine starting (During Cranking) 5
Other than above 2
12 R PDU feedback signal LOCKPush-button ignition switch is in LOCK state, 30 sec-
onds after all doors close1
Other than above 0
14 SB Power source (Fuse) LOCK — Battery voltage
15 L Power source (F/L) LOCK — Battery voltage
16 W ACC power outputLOCK — 0
ACC — Battery voltage
ON — Battery voltage
17 G Power source (Fuse) LOCK — Battery voltage
18 BR ON power outputLOCK — 0
ACC — 0
ON — Battery voltage
Page 4866 of 5621
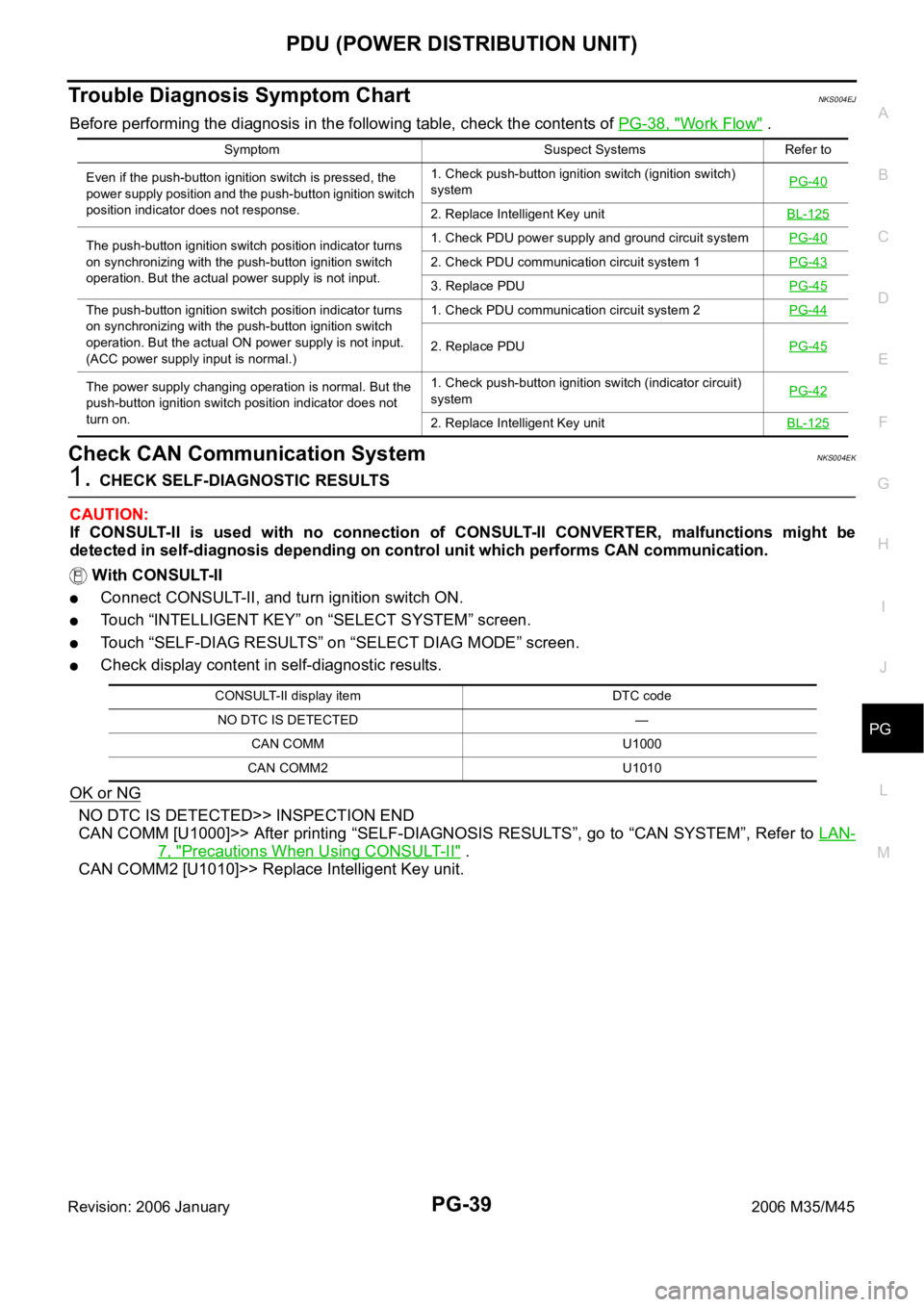
PDU (POWER DISTRIBUTION UNIT)
PG-39
C
D
E
F
G
H
I
J
L
MA
B
PG
Revision: 2006 January2006 M35/M45
Trouble Diagnosis Symptom ChartNKS004EJ
Before performing the diagnosis in the following table, check the contents of PG-38, "Work Flow" .
Check CAN Communication SystemNKS004EK
1. CHECK SELF-DIAGNOSTIC RESULTS
CAUTION:
If CONSULT-II is used with no connection of CONSULT-II CONVERTER, malfunctions might be
detected in self-diagnosis depending on control unit which performs CAN communication.
With CONSULT-II
Connect CONSULT-II, and turn ignition switch ON.
Touch “INTELLIGENT KEY” on “SELECT SYSTEM” screen.
Touch “SELF-DIAG RESULTS” on “SELECT DIAG MODE” screen.
Check display content in self-diagnostic results.
OK or NG
NO DTC IS DETECTED>> INSPECTION END
CAN COMM [U1000]>> After printing “SELF-DIAGNOSIS RESULTS”, go to “CAN SYSTEM”, Refer to LAN-
7, "Precautions When Using CONSULT-II" .
CAN COMM2 [U1010]>> Replace Intelligent Key unit.
Symptom Suspect Systems Refer to
Even if the push-button ignition switch is pressed, the
power supply position and the push-button ignition switch
position indicator does not response.1. Check push-button ignition switch (ignition switch)
systemPG-40
2. Replace Intelligent Key unitBL-125
The push-button ignition switch position indicator turns
on synchronizing with the push-button ignition switch
operation. But the actual power supply is not input.1. Check PDU power supply and ground circuit systemPG-40
2. Check PDU communication circuit system 1PG-43
3. Replace PDUPG-45
The push-button ignition switch position indicator turns
on synchronizing with the push-button ignition switch
operation. But the actual ON power supply is not input.
(ACC power supply input is normal.)1. Check PDU communication circuit system 2PG-44
2. Replace PDUPG-45
The power supply changing operation is normal. But the
push-button ignition switch position indicator does not
turn on.1. Check push-button ignition switch (indicator circuit)
systemPG-42
2. Replace Intelligent Key unitBL-125
CONSULT-II display item DTC code
NO DTC IS DETECTED —
CAN COMM U1000
CAN COMM2 U1010
Page 4867 of 5621
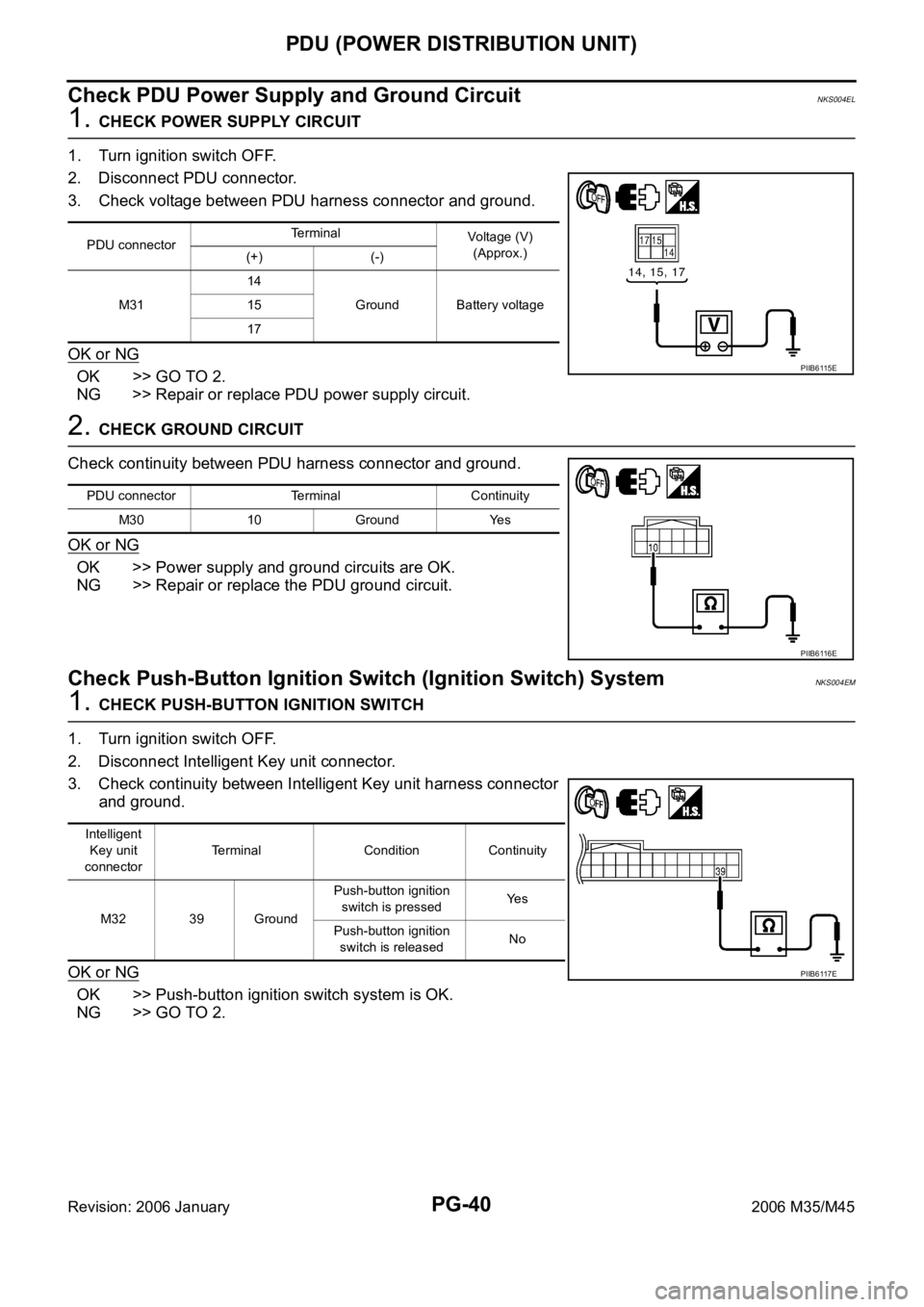
PG-40
PDU (POWER DISTRIBUTION UNIT)
Revision: 2006 January2006 M35/M45
Check PDU Power Supply and Ground CircuitNKS004EL
1. CHECK POWER SUPPLY CIRCUIT
1. Turn ignition switch OFF.
2. Disconnect PDU connector.
3. Check voltage between PDU harness connector and ground.
OK or NG
OK >> GO TO 2.
NG >> Repair or replace PDU power supply circuit.
2. CHECK GROUND CIRCUIT
Check continuity between PDU harness connector and ground.
OK or NG
OK >> Power supply and ground circuits are OK.
NG >> Repair or replace the PDU ground circuit.
Check Push-Button Ignition Switch (Ignition Switch) SystemNKS004EM
1. CHECK PUSH-BUTTON IGNITION SWITCH
1. Turn ignition switch OFF.
2. Disconnect Intelligent Key unit connector.
3. Check continuity between Intelligent Key unit harness connector
and ground.
OK or NG
OK >> Push-button ignition switch system is OK.
NG >> GO TO 2.
PDU connectorTerminal
Voltage (V)
(Approx.)
(+) (-)
M3114
Ground Battery voltage 15
17
PIIB6115E
PDU connector Terminal Continuity
M30 10 Ground Yes
PIIB6116E
Intelligent
Key unit
connectorTerminal Condition Continuity
M32 39 GroundPush-button ignition
switch is pressedYe s
Push-button ignition
switch is releasedNo
PIIB6117E
Page 4868 of 5621
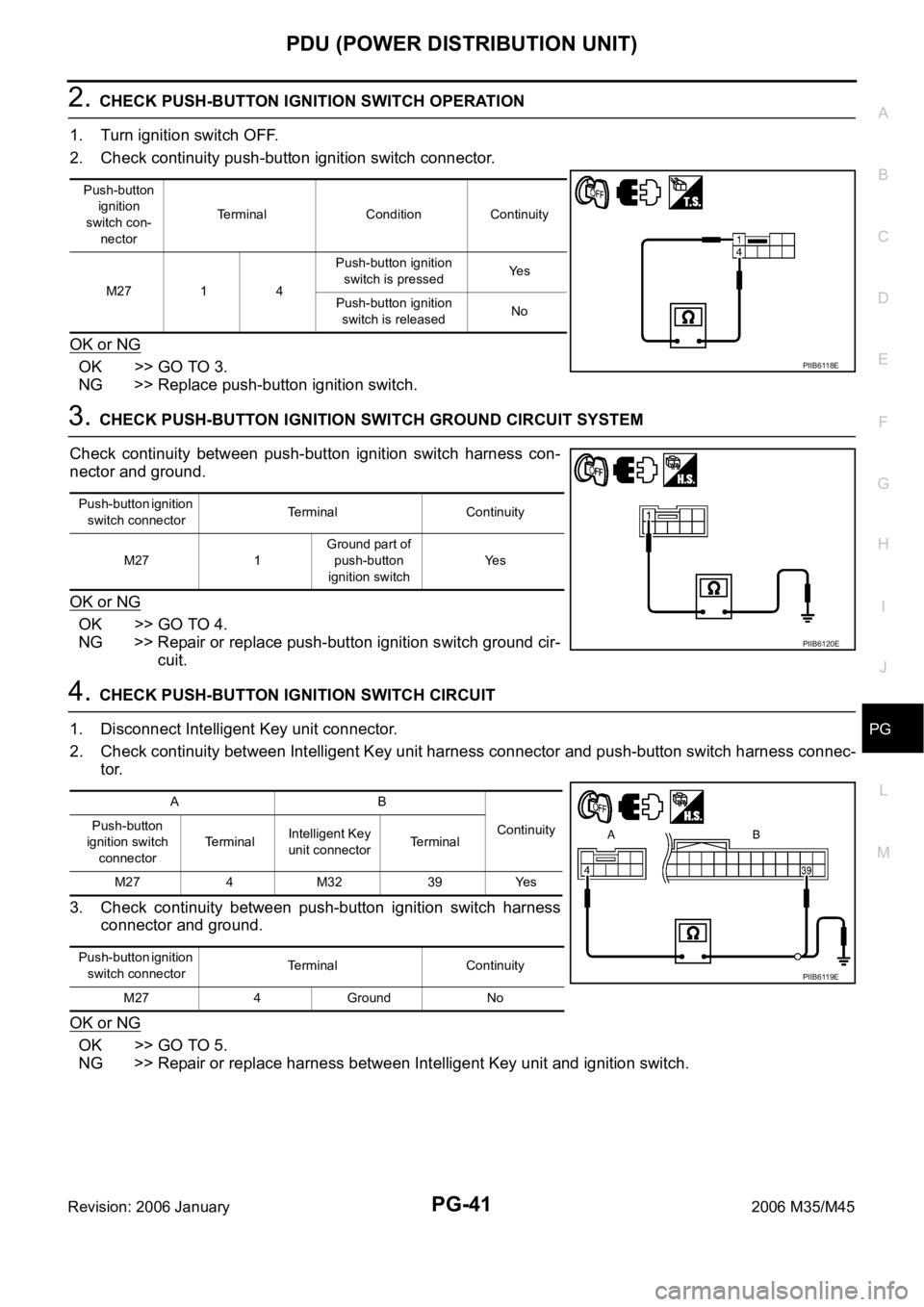
PDU (POWER DISTRIBUTION UNIT)
PG-41
C
D
E
F
G
H
I
J
L
MA
B
PG
Revision: 2006 January2006 M35/M45
2. CHECK PUSH-BUTTON IGNITION SWITCH OPERATION
1. Turn ignition switch OFF.
2. Check continuity push-button ignition switch connector.
OK or NG
OK >> GO TO 3.
NG >> Replace push-button ignition switch.
3. CHECK PUSH-BUTTON IGNITION SWITCH GROUND CIRCUIT SYSTEM
Check continuity between push-button ignition switch harness con-
nector and ground.
OK or NG
OK >> GO TO 4.
NG >> Repair or replace push-button ignition switch ground cir-
cuit.
4. CHECK PUSH-BUTTON IGNITION SWITCH CIRCUIT
1. Disconnect Intelligent Key unit connector.
2. Check continuity between Intelligent Key unit harness connector and push-button switch harness connec-
tor.
3. Check continuity between push-button ignition switch harness
connector and ground.
OK or NG
OK >> GO TO 5.
NG >> Repair or replace harness between Intelligent Key unit and ignition switch.
Push-button
ignition
switch con-
nectorTerminal Condition Continuity
M27 1 4Push-button ignition
switch is pressedYe s
Push-button ignition
switch is releasedNo
PIIB6118E
Push-button ignition
switch connectorTerminal Continuity
M27 1Ground part of
push-button
ignition switchYe s
PIIB6120E
AB
Continuity Push-button
ignition switch
connectorTerminalIntelligent Key
unit connectorTerminal
M27 4 M32 39 Yes
Push-button ignition
switch connectorTerminal Continuity
M27 4 Ground No
PIIB6119E
Page 4869 of 5621
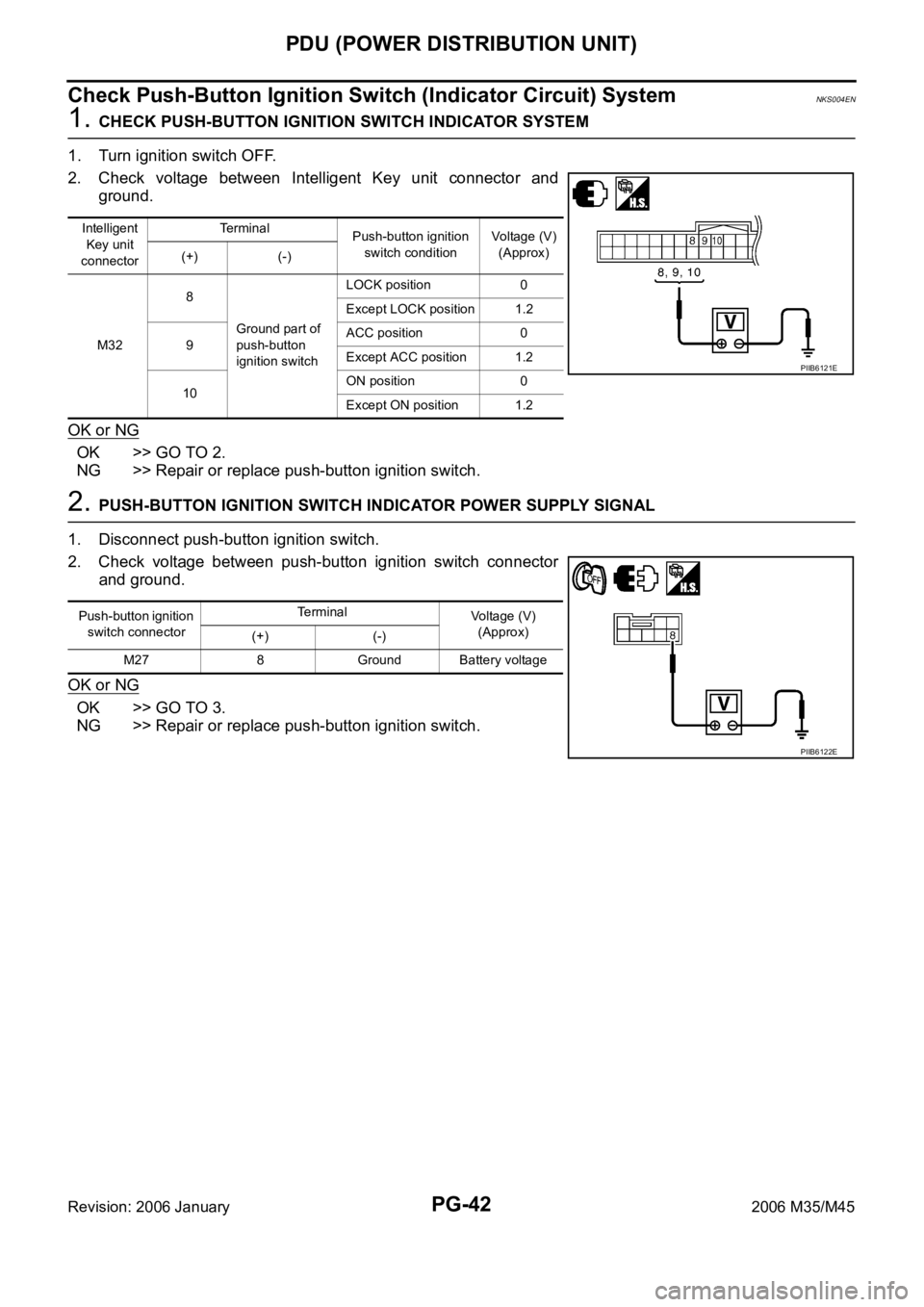
PG-42
PDU (POWER DISTRIBUTION UNIT)
Revision: 2006 January2006 M35/M45
Check Push-Button Ignition Switch (Indicator Circuit) SystemNKS004EN
1. CHECK PUSH-BUTTON IGNITION SWITCH INDICATOR SYSTEM
1. Turn ignition switch OFF.
2. Check voltage between Intelligent Key unit connector and
ground.
OK or NG
OK >> GO TO 2.
NG >> Repair or replace push-button ignition switch.
2. PUSH-BUTTON IGNITION SWITCH INDICATOR POWER SUPPLY SIGNAL
1. Disconnect push-button ignition switch.
2. Check voltage between push-button ignition switch connector
and ground.
OK or NG
OK >> GO TO 3.
NG >> Repair or replace push-button ignition switch.
Intelligent
Key unit
connectorTe r m i n a l
Push-button ignition
switch conditionVoltage (V)
(Approx)
(+) (-)
M328
Ground part of
push-button
ignition switchLOCK position 0
Except LOCK position 1.2
9ACC position 0
Except ACC position 1.2
10ON position 0
Except ON position 1.2
PIIB6121E
Push-button ignition
switch connectorTerminal
Voltage (V)
(Approx)
(+) (-)
M27 8 Ground Battery voltage
PIIB6122E
Page 4870 of 5621
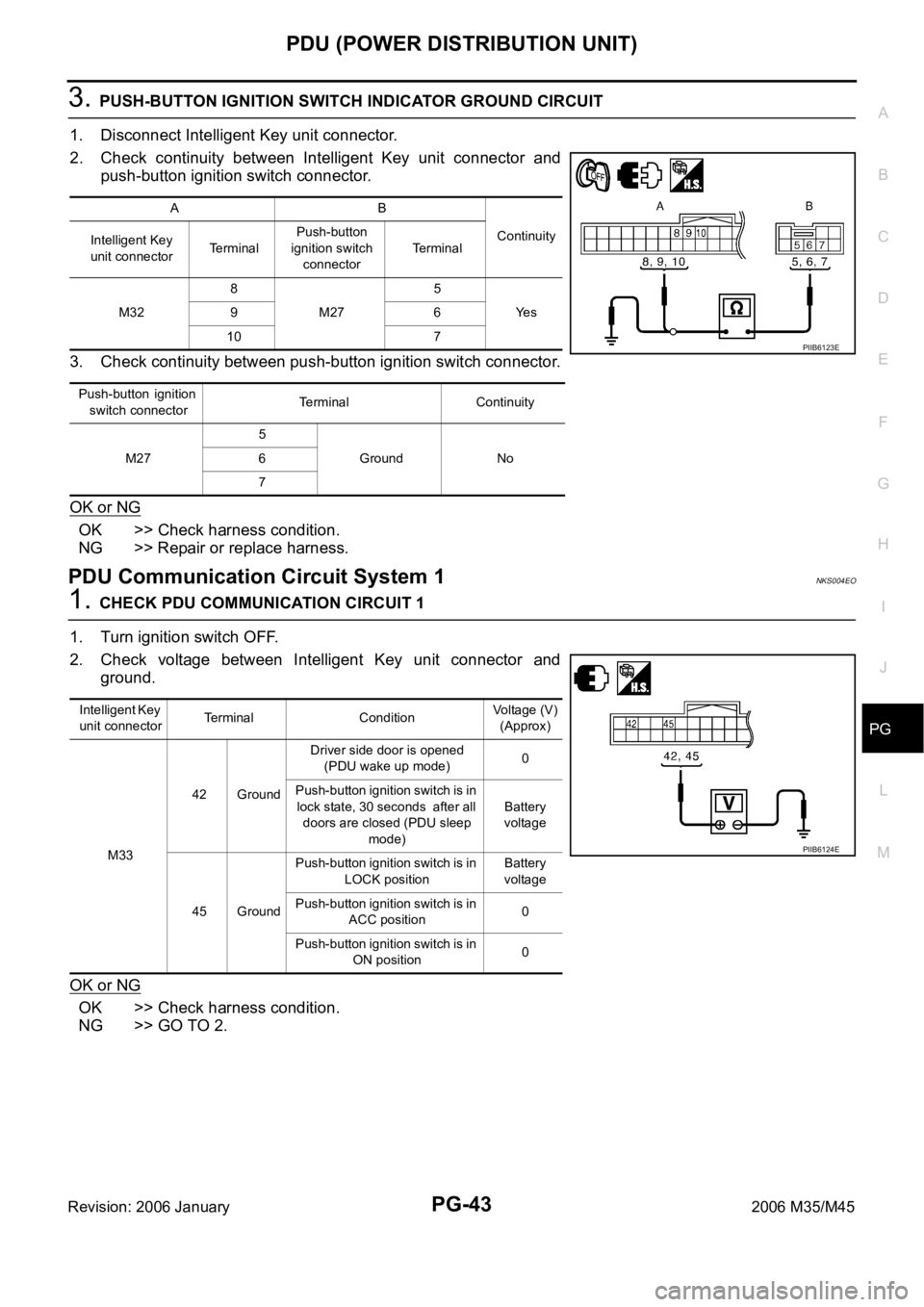
PDU (POWER DISTRIBUTION UNIT)
PG-43
C
D
E
F
G
H
I
J
L
MA
B
PG
Revision: 2006 January2006 M35/M45
3. PUSH-BUTTON IGNITION SWITCH INDICATOR GROUND CIRCUIT
1. Disconnect Intelligent Key unit connector.
2. Check continuity between Intelligent Key unit connector and
push-button ignition switch connector.
3. Check continuity between push-button ignition switch connector.
OK or NG
OK >> Check harness condition.
NG >> Repair or replace harness.
PDU Communication Circuit System 1NKS004EO
1. CHECK PDU COMMUNICATION CIRCUIT 1
1. Turn ignition switch OFF.
2. Check voltage between Intelligent Key unit connector and
ground.
OK or NG
OK >> Check harness condition.
NG >> GO TO 2.
AB
Continuity
Intelligent Key
unit connectorTerminalPush-button
ignition switch
connectorTe r m i n a l
M328
M275
Ye s 96
10 7
P u s h - b u t t o n i g n i t i o n
switch connectorTerminal Continuity
M275
Ground No 6
7
PIIB6123E
Intelligent Key
unit connectorTerminal ConditionVoltage (V)
(Approx)
M3342 GroundDriver side door is opened
(PDU wake up mode)0
Push-button ignition switch is in
lock state, 30 seconds after all
doors are closed (PDU sleep
mode)Battery
voltage
45 GroundPush-button ignition switch is in
LOCK positionBattery
voltage
Push-button ignition switch is in
ACC position0
Push-button ignition switch is in
ON position0
PIIB6124E
Page 4871 of 5621
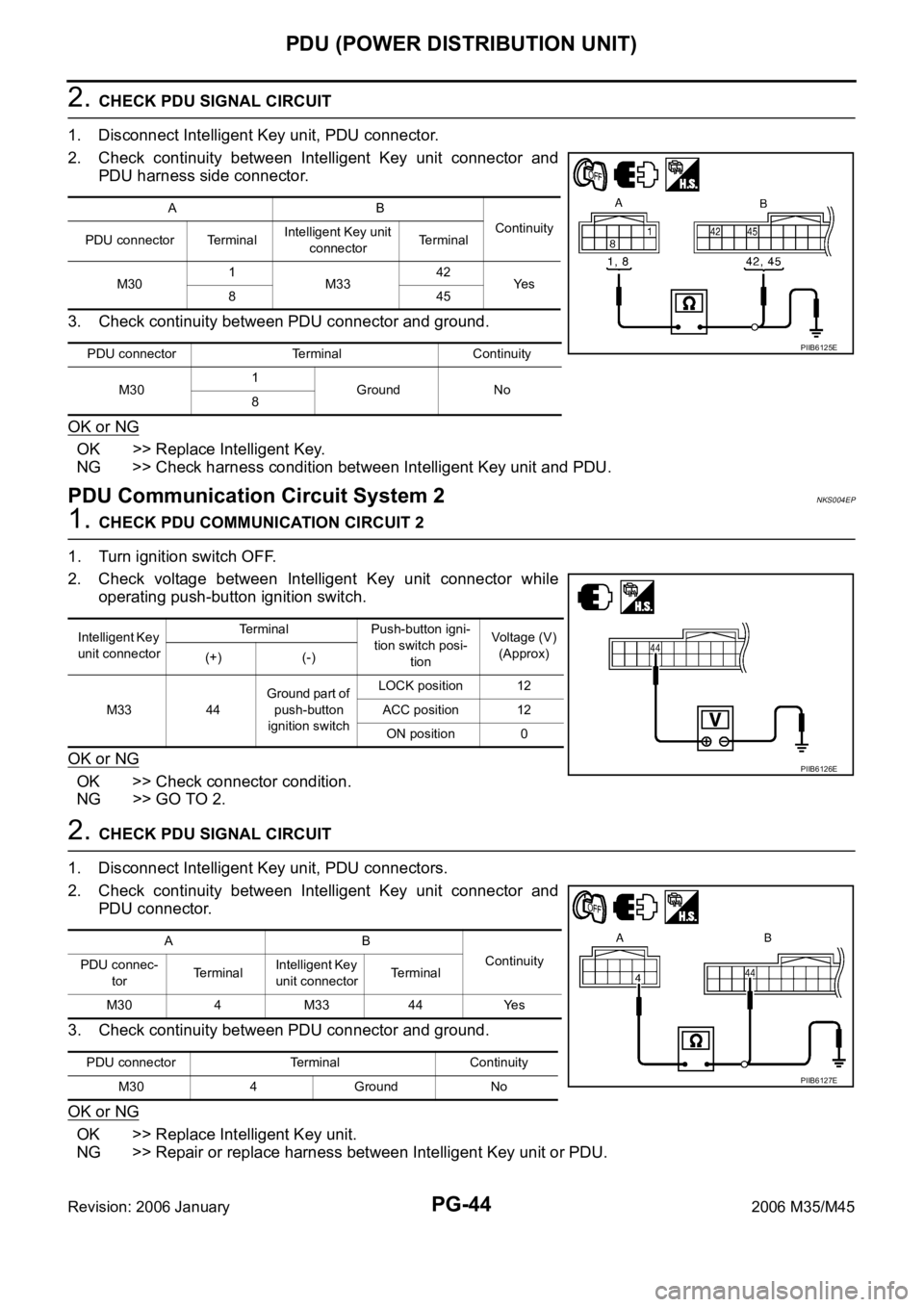
PG-44
PDU (POWER DISTRIBUTION UNIT)
Revision: 2006 January2006 M35/M45
2. CHECK PDU SIGNAL CIRCUIT
1. Disconnect Intelligent Key unit, PDU connector.
2. Check continuity between Intelligent Key unit connector and
PDU harness side connector.
3. Check continuity between PDU connector and ground.
OK or NG
OK >> Replace Intelligent Key.
NG >> Check harness condition between Intelligent Key unit and PDU.
PDU Communication Circuit System 2NKS004EP
1. CHECK PDU COMMUNICATION CIRCUIT 2
1. Turn ignition switch OFF.
2. Check voltage between Intelligent Key unit connector while
operating push-button ignition switch.
OK or NG
OK >> Check connector condition.
NG >> GO TO 2.
2. CHECK PDU SIGNAL CIRCUIT
1. Disconnect Intelligent Key unit, PDU connectors.
2. Check continuity between Intelligent Key unit connector and
PDU connector.
3. Check continuity between PDU connector and ground.
OK or NG
OK >> Replace Intelligent Key unit.
NG >> Repair or replace harness between Intelligent Key unit or PDU.
AB
Continuity
PDU connector TerminalIntelligent Key unit
connectorTerminal
M301
M3342
Ye s
845
PDU connector Terminal Continuity
M301
Ground No
8
PIIB6125E
Intelligent Key
unit connectorTerminal Push-button igni-
tion switch posi-
tionVoltage (V)
(Approx)
(+) (-)
M33 44Ground part of
push-button
ignition switchLOCK position 12
ACC position 12
ON position 0
PIIB6126E
AB
Continuity
PDU connec-
torTerminalIntelligent Key
unit connectorTerminal
M30 4 M33 44 Yes
PDU connector Terminal Continuity
M30 4 Ground No
PIIB6127E
Page 4943 of 5621
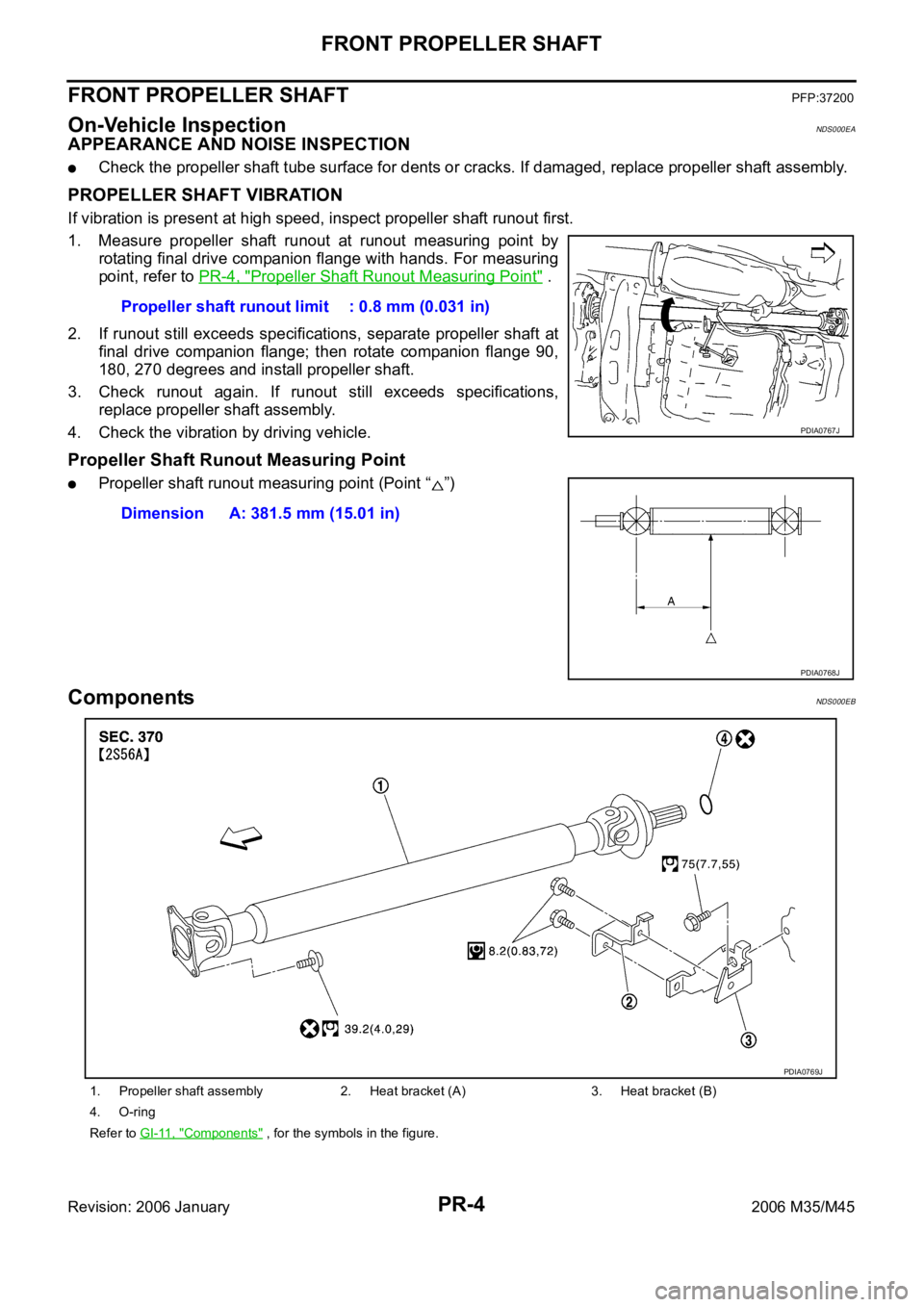
PR-4
FRONT PROPELLER SHAFT
Revision: 2006 January2006 M35/M45
FRONT PROPELLER SHAFTPFP:37200
On-Vehicle InspectionNDS000EA
APPEARANCE AND NOISE INSPECTION
Check the propeller shaft tube surface for dents or cracks. If damaged, replace propeller shaft assembly.
PROPELLER SHAFT VIBRATION
If vibration is present at high speed, inspect propeller shaft runout first.
1. Measure propeller shaft runout at runout measuring point by
rotating final drive companion flange with hands. For measuring
point, refer to PR-4, "
Propeller Shaft Runout Measuring Point" .
2. If runout still exceeds specifications, separate propeller shaft at
final drive companion flange; then rotate companion flange 90,
180, 270 degrees and install propeller shaft.
3. Check runout again. If runout still exceeds specifications,
replace propeller shaft assembly.
4. Check the vibration by driving vehicle.
Propeller Shaft Runout Measuring Point
Propeller shaft runout measuring point (Point “ ”)
ComponentsNDS000EB
Propeller shaft runout limit : 0.8 mm (0.031 in)
PDIA0767J
Dimension A: 381.5 mm (15.01 in)
PDIA0768J
1. Propeller shaft assembly 2. Heat bracket (A) 3. Heat bracket (B)
4. O-ring
Refer to GI-11, "
Components" , for the symbols in the figure.
PDIA0769J
Page 4944 of 5621
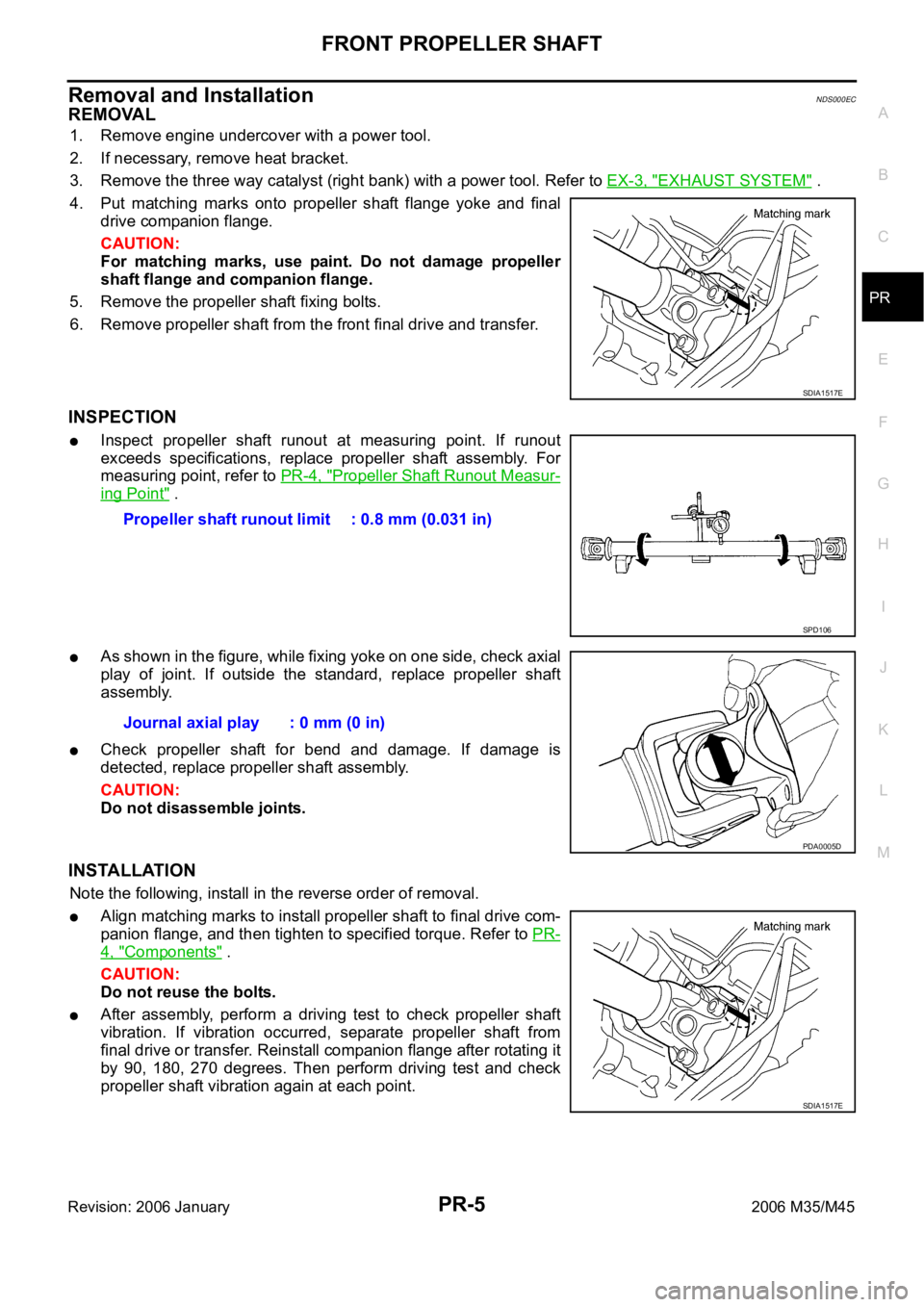
FRONT PROPELLER SHAFT
PR-5
C
E
F
G
H
I
J
K
L
MA
B
PR
Revision: 2006 January2006 M35/M45
Removal and InstallationNDS000EC
REMOVAL
1. Remove engine undercover with a power tool.
2. If necessary, remove heat bracket.
3. Remove the three way catalyst (right bank) with a power tool. Refer to EX-3, "
EXHAUST SYSTEM" .
4. Put matching marks onto propeller shaft flange yoke and final
drive companion flange.
CAUTION:
For matching marks, use paint. Do not damage propeller
shaft flange and companion flange.
5. Remove the propeller shaft fixing bolts.
6. Remove propeller shaft from the front final drive and transfer.
INSPECTION
Inspect propeller shaft runout at measuring point. If runout
exceeds specifications, replace propeller shaft assembly. For
measuring point, refer to PR-4, "
Propeller Shaft Runout Measur-
ing Point" .
As shown in the figure, while fixing yoke on one side, check axial
play of joint. If outside the standard, replace propeller shaft
assembly.
Check propeller shaft for bend and damage. If damage is
detected, replace propeller shaft assembly.
CAUTION:
Do not disassemble joints.
INSTALLATION
Note the following, install in the reverse order of removal.
Align matching marks to install propeller shaft to final drive com-
panion flange, and then tighten to specified torque. Refer to PR-
4, "Components" .
CAUTION:
Do not reuse the bolts.
After assembly, perform a driving test to check propeller shaft
vibration. If vibration occurred, separate propeller shaft from
final drive or transfer. Reinstall companion flange after rotating it
by 90, 180, 270 degrees. Then perform driving test and check
propeller shaft vibration again at each point.
SDIA1517E
Propeller shaft runout limit : 0.8 mm (0.031 in)
SPD106
Journal axial play : 0 mm (0 in)
PDA0005D
SDIA1517E
Page 4945 of 5621
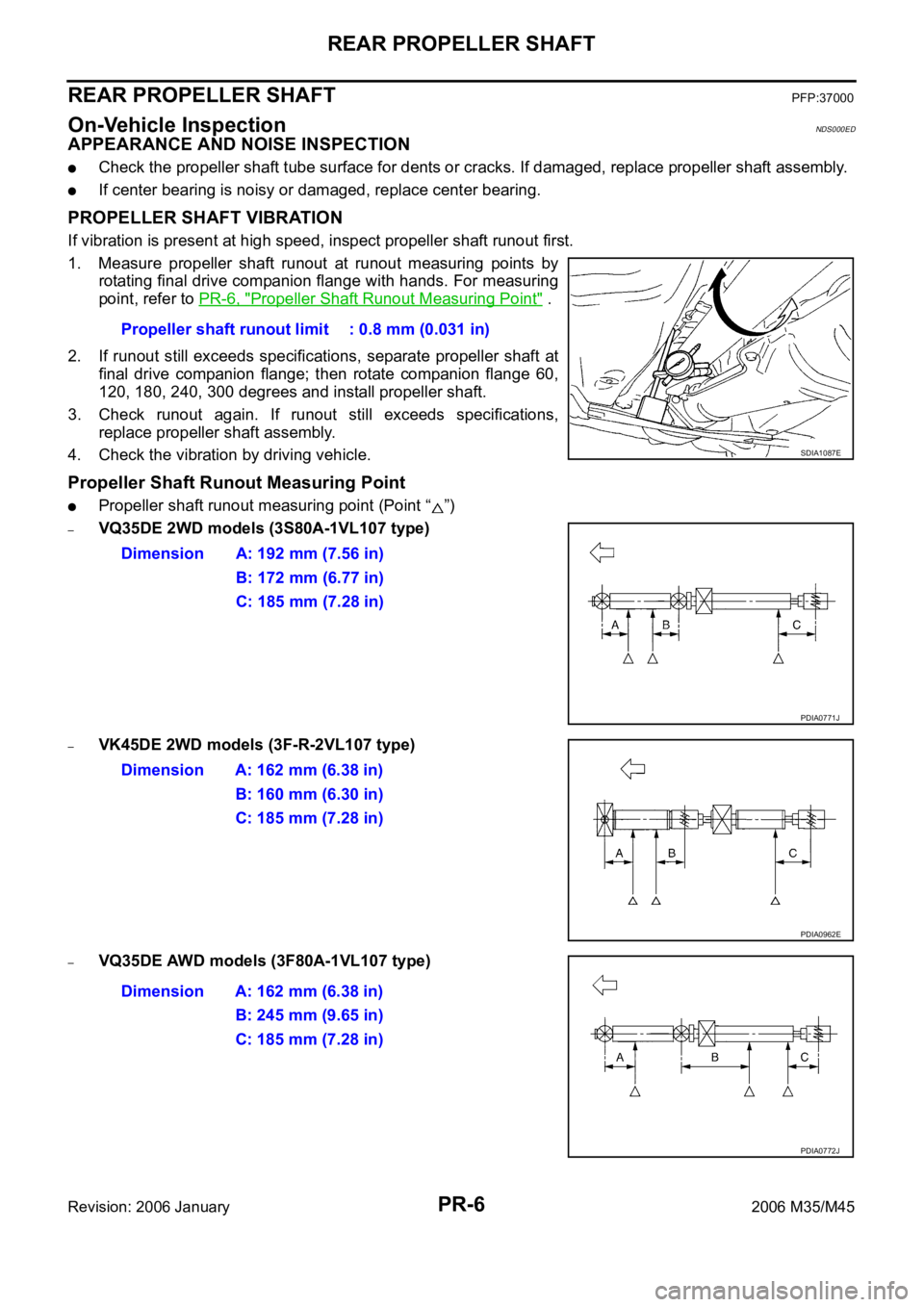
PR-6
REAR PROPELLER SHAFT
Revision: 2006 January2006 M35/M45
REAR PROPELLER SHAFTPFP:37000
On-Vehicle InspectionNDS000ED
APPEARANCE AND NOISE INSPECTION
Check the propeller shaft tube surface for dents or cracks. If damaged, replace propeller shaft assembly.
If center bearing is noisy or damaged, replace center bearing.
PROPELLER SHAFT VIBRATION
If vibration is present at high speed, inspect propeller shaft runout first.
1. Measure propeller shaft runout at runout measuring points by
rotating final drive companion flange with hands. For measuring
point, refer to PR-6, "
Propeller Shaft Runout Measuring Point" .
2. If runout still exceeds specifications, separate propeller shaft at
final drive companion flange; then rotate companion flange 60,
120, 180, 240, 300 degrees and install propeller shaft.
3. Check runout again. If runout still exceeds specifications,
replace propeller shaft assembly.
4. Check the vibration by driving vehicle.
Propeller Shaft Runout Measuring Point
Propeller shaft runout measuring point (Point “ ”)
–VQ35DE 2WD models (3S80A-1VL107 type)
–VK45DE 2WD models (3F-R-2VL107 type)
–VQ35DE AWD models (3F80A-1VL107 type)Propeller shaft runout limit : 0.8 mm (0.031 in)
SDIA1087E
Dimension A: 192 mm (7.56 in)
B: 172 mm (6.77 in)
C: 185 mm (7.28 in)
PDIA0771J
Dimension A: 162 mm (6.38 in)
B: 160 mm (6.30 in)
C: 185 mm (7.28 in)
PDIA0962E
Dimension A: 162 mm (6.38 in)
B: 245 mm (9.65 in)
C: 185 mm (7.28 in)
PDIA0772J