service INFINITI M35 2006 Factory Service Manual
[x] Cancel search | Manufacturer: INFINITI, Model Year: 2006, Model line: M35, Model: INFINITI M35 2006Pages: 5621, PDF Size: 65.56 MB
Page 5362 of 5621
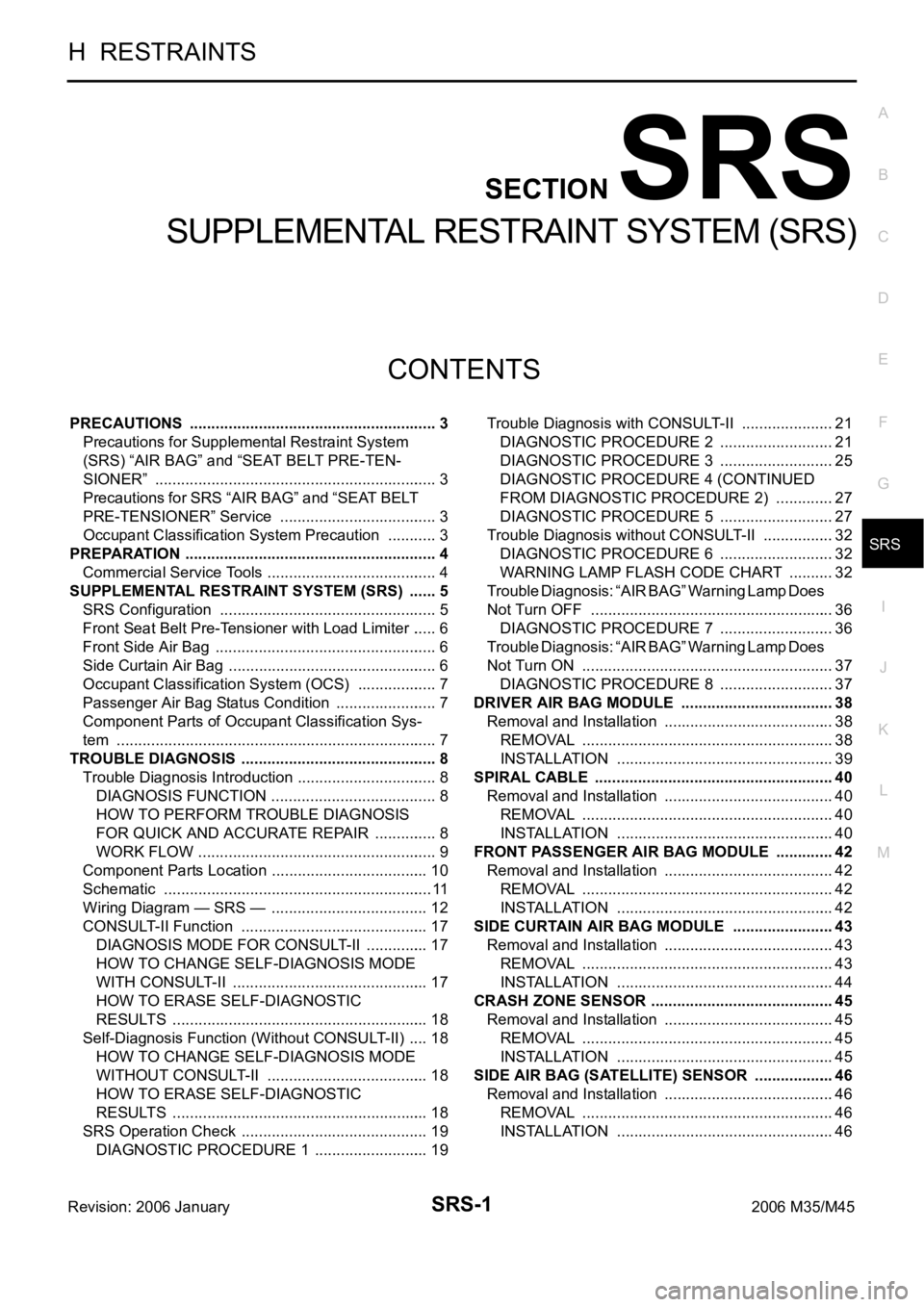
SRS-1
SUPPLEMENTAL RESTRAINT SYSTEM (SRS)
H RESTRAINTS
CONTENTS
C
D
E
F
G
I
J
K
L
M
SECTION SRS
A
B
SRS
Revision: 2006 January2006 M35/M45
SUPPLEMENTAL RESTRAINT SYSTEM (SRS)
PRECAUTIONS .......................................................... 3
Precautions for Supplemental Restraint System
(SRS) “AIR BAG” and “SEAT BELT PRE-TEN-
SIONER” .................................................................. 3
Precautions for SRS “AIR BAG” and “SEAT BELT
PRE-TENSIONER” Service ..................................... 3
Occupant Classification System Precaution ............ 3
PREPARATION ........................................................... 4
Commercial Service Tools ........................................ 4
SUPPLEMENTAL RESTRAINT SYSTEM (SRS) ....... 5
SRS Configuration ..............................................
..... 5
Front Seat Belt Pre-Tensioner with Load Limiter ...... 6
Front Side Air Bag .................................................... 6
Side Curtain Air Bag ................................................. 6
Occupant Classification System (OCS) ................... 7
Passenger Air Bag Status Condition ........................ 7
Component Parts of Occupant Classification Sys-
tem ........................................................................... 7
TROUBLE DIAGNOSIS .............................................. 8
Trouble Diagnosis Introduction ................................. 8
DIAGNOSIS FUNCTION ....................................... 8
HOW TO PERFORM TROUBLE DIAGNOSIS
FOR QUICK AND ACCURATE REPAIR ............... 8
WORK FLOW ........................................................ 9
Component Parts Location ..................................... 10
Schematic ............................................................... 11
Wiring Diagram — SRS — ..................................... 12
CONSULT-II Function ............................................ 17
DIAGNOSIS MODE FOR CONSULT-II ............... 17
HOW TO CHANGE SELF-DIAGNOSIS MODE
WITH CONSULT-II .............................................. 17
HOW TO ERASE SELF-DIAGNOSTIC
RESULTS ............................................................ 18
Self-Diagnosis Function (Without CONSULT-II) ..... 18
HOW TO CHANGE SELF-DIAGNOSIS MODE
WITHOUT CONSULT-II ...................................... 18
HOW TO ERASE SELF-DIAGNOSTIC
RESULTS ............................................................ 18
SRS Operation Check ............................................ 19
DIAGNOSTIC PROCEDURE 1 ........................... 19Trouble Diagnosis with CONSULT-II ...................... 21
DIAGNOSTIC PROCEDURE 2 ........................... 21
DIAGNOSTIC PROCEDURE 3 ........................... 25
DIAGNOSTIC PROCEDURE 4 (CONTINUED
FROM DIAGNOSTIC PROCEDURE 2) .............. 27
DIAGNOSTIC PROCEDURE 5 ........................... 27
Trouble Diagnosis without CONSULT-II ................. 32
DIAGNOSTIC PROCEDURE 6 ........................... 32
WARNING LAMP FLASH CODE CHART ........... 32
Trouble Diagnosis: “AIR BAG” Warning Lamp Does
Not Turn OFF ......................................................... 36
DIAGNOSTIC PROCEDURE 7 ........................... 36
Trouble Diagnosis: “AIR BAG” Warning Lamp Does
Not Turn ON ........................................................... 37
DIAGNOSTIC PROCEDURE 8 ........................... 37
DRIVER AIR BAG MODULE .................................... 38
Removal and Installation ........................................ 38
REMOVAL ........................................................
... 38
INSTALLATION ................................................... 39
SPIRAL CABLE ........................................................ 40
Removal and Installation ........................................ 40
REMOVAL ........................................................
... 40
INSTALLATION ................................................... 40
FRONT PASSENGER AIR BAG MODULE .............. 42
Removal and Installation ........................................ 42
REMOVAL ........................................................
... 42
INSTALLATION ................................................... 42
SIDE CURTAIN AIR BAG MODULE ........................ 43
Removal and Installation ........................................ 43
REMOVAL ........................................................
... 43
INSTALLATION ................................................... 44
CRASH ZONE SENSOR ........................................... 45
Removal and Installation ........................................ 45
REMOVAL ........................................................
... 45
INSTALLATION ................................................... 45
SIDE AIR BAG (SATELLITE) SENSOR ................... 46
Removal and Installation ........................................ 46
REMOVAL ........................................................
... 46
INSTALLATION ................................................... 46
Page 5364 of 5621
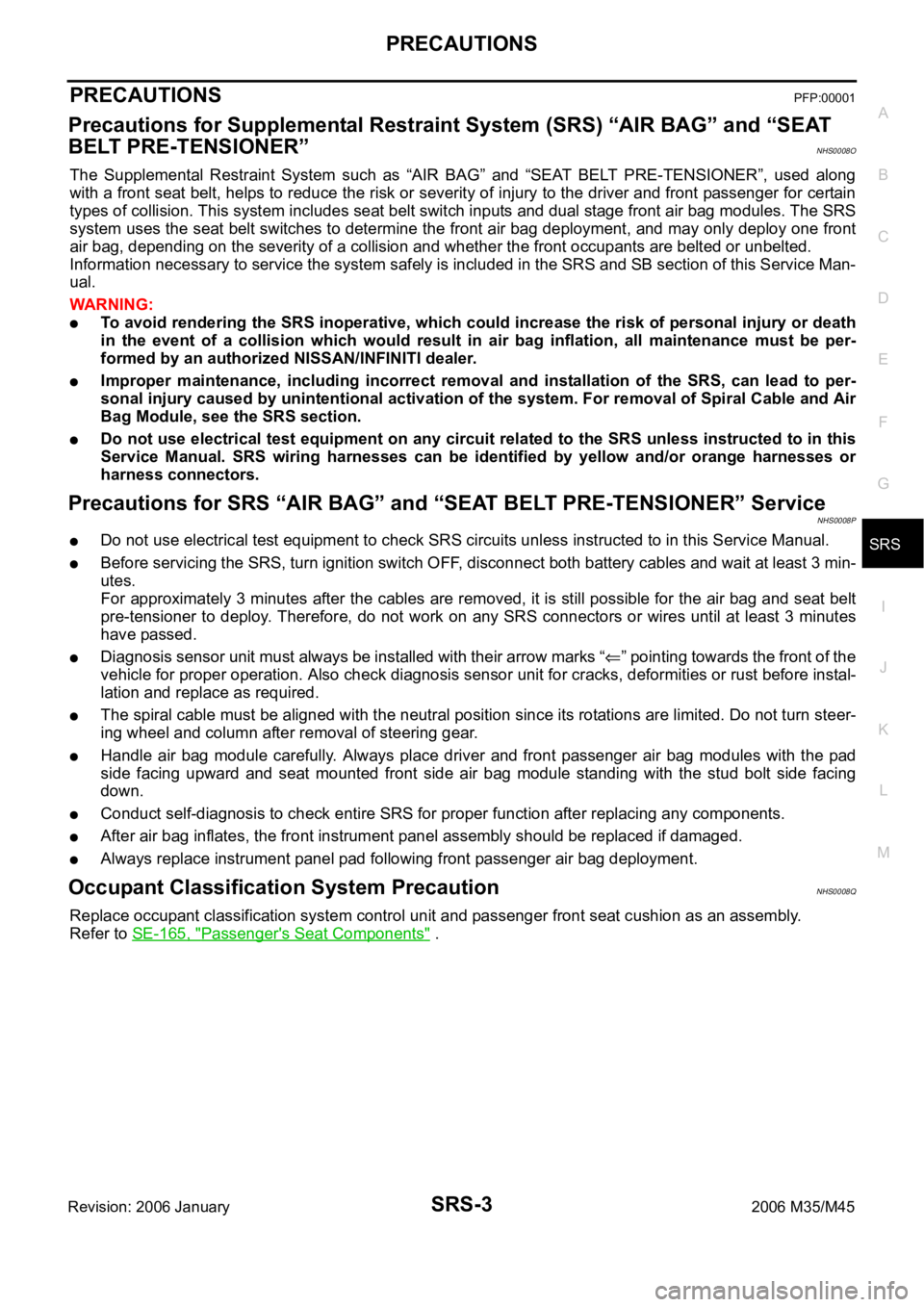
PRECAUTIONS
SRS-3
C
D
E
F
G
I
J
K
L
MA
B
SRS
Revision: 2006 January2006 M35/M45
PRECAUTIONSPFP:00001
Precautions for Supplemental Restraint System (SRS) “AIR BAG” and “SEAT
BELT PRE-TENSIONER”
NHS0008O
The Supplemental Restraint System such as “AIR BAG” and “SEAT BELT PRE-TENSIONER”, used along
with a front seat belt, helps to reduce the risk or severity of injury to the driver and front passenger for certain
types of collision. This system includes seat belt switch inputs and dual stage front air bag modules. The SRS
system uses the seat belt switches to determine the front air bag deployment, and may only deploy one front
air bag, depending on the severity of a collision and whether the front occupants are belted or unbelted.
Information necessary to service the system safely is included in the SRS and SB section of this Service Man-
ual.
WAR NING :
To avoid rendering the SRS inoperative, which could increase the risk of personal injury or death
in the event of a collision which would result in air bag inflation, all maintenance must be per-
formed by an authorized NISSAN/INFINITI dealer.
Improper maintenance, including incorrect removal and installation of the SRS, can lead to per-
sonal injury caused by unintentional activation of the system. For removal of Spiral Cable and Air
Bag Module, see the SRS section.
Do not use electrical test equipment on any circuit related to the SRS unless instructed to in this
Service Manual. SRS wiring harnesses can be identified by yellow and/or orange harnesses or
harness connectors.
Precautions for SRS “AIR BAG” and “SEAT BELT PRE-TENSIONER” ServiceNHS0008P
Do not use electrical test equipment to check SRS circuits unless instructed to in this Service Manual.
Before servicing the SRS, turn ignition switch OFF, disconnect both battery cables and wait at least 3 min-
utes.
For approximately 3 minutes after the cables are removed, it is still possible for the air bag and seat belt
pre-tensioner to deploy. Therefore, do not work on any SRS connectors or wires until at least 3 minutes
have passed.
Diagnosis sensor unit must always be installed with their arrow marks “” pointing towards the front of the
vehicle for proper operation. Also check diagnosis sensor unit for cracks, deformities or rust before instal-
lation and replace as required.
The spiral cable must be aligned with the neutral position since its rotations are limited. Do not turn steer-
ing wheel and column after removal of steering gear.
Handle air bag module carefully. Always place driver and front passenger air bag modules with the pad
side facing upward and seat mounted front side air bag module standing with the stud bolt side facing
down.
Conduct self-diagnosis to check entire SRS for proper function after replacing any components.
After air bag inflates, the front instrument panel assembly should be replaced if damaged.
Always replace instrument panel pad following front passenger air bag deployment.
Occupant Classification System PrecautionNHS0008Q
Replace occupant classification system control unit and passenger front seat cushion as an assembly.
Refer to SE-165, "
Passenger's Seat Components" .
Page 5365 of 5621
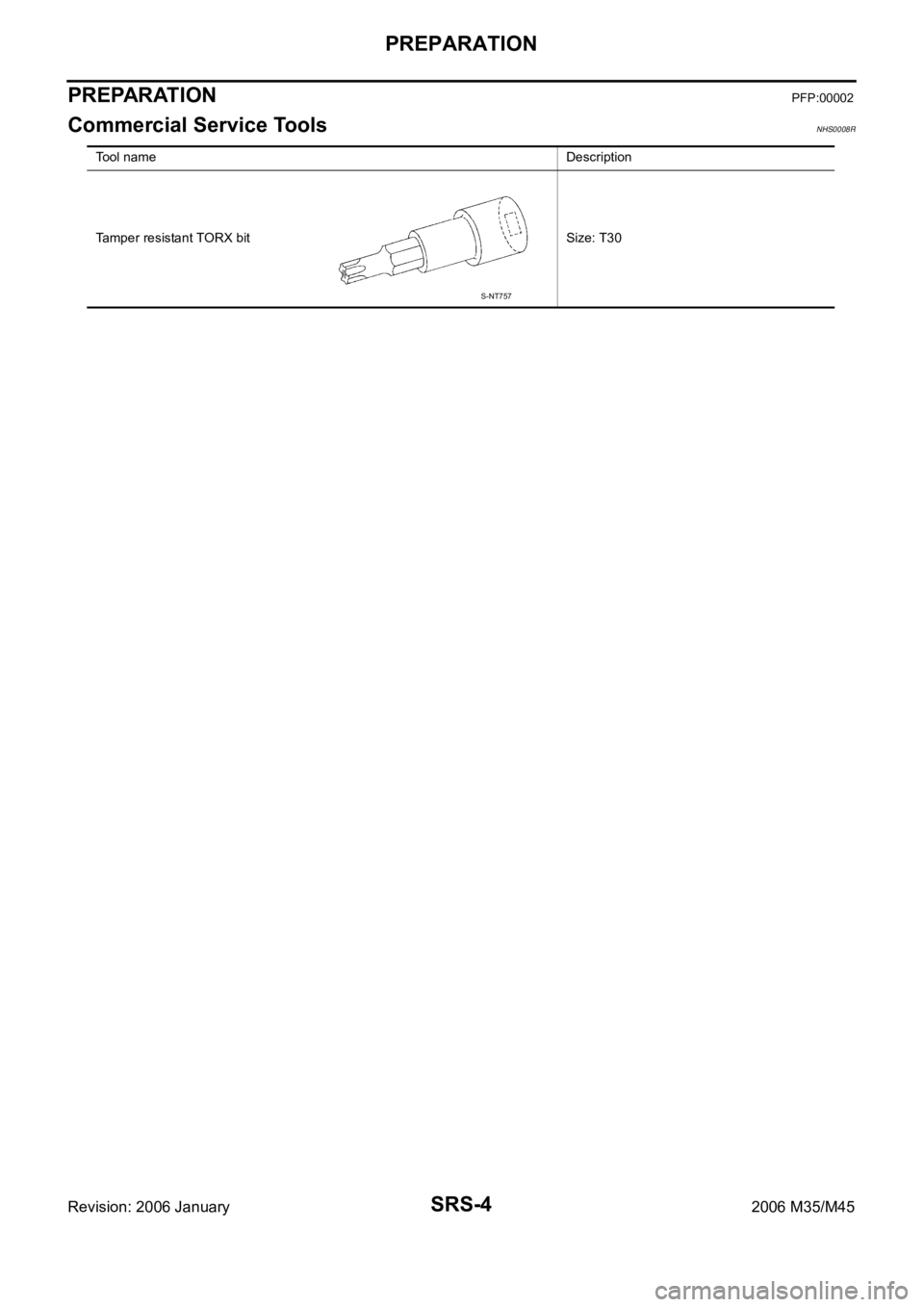
SRS-4
PREPARATION
Revision: 2006 January2006 M35/M45
PREPARATIONPFP:00002
Commercial Service ToolsNHS0008R
Tool name Description
Tamper resistant TORX bit Size: T30
S-NT757
Page 5402 of 5621
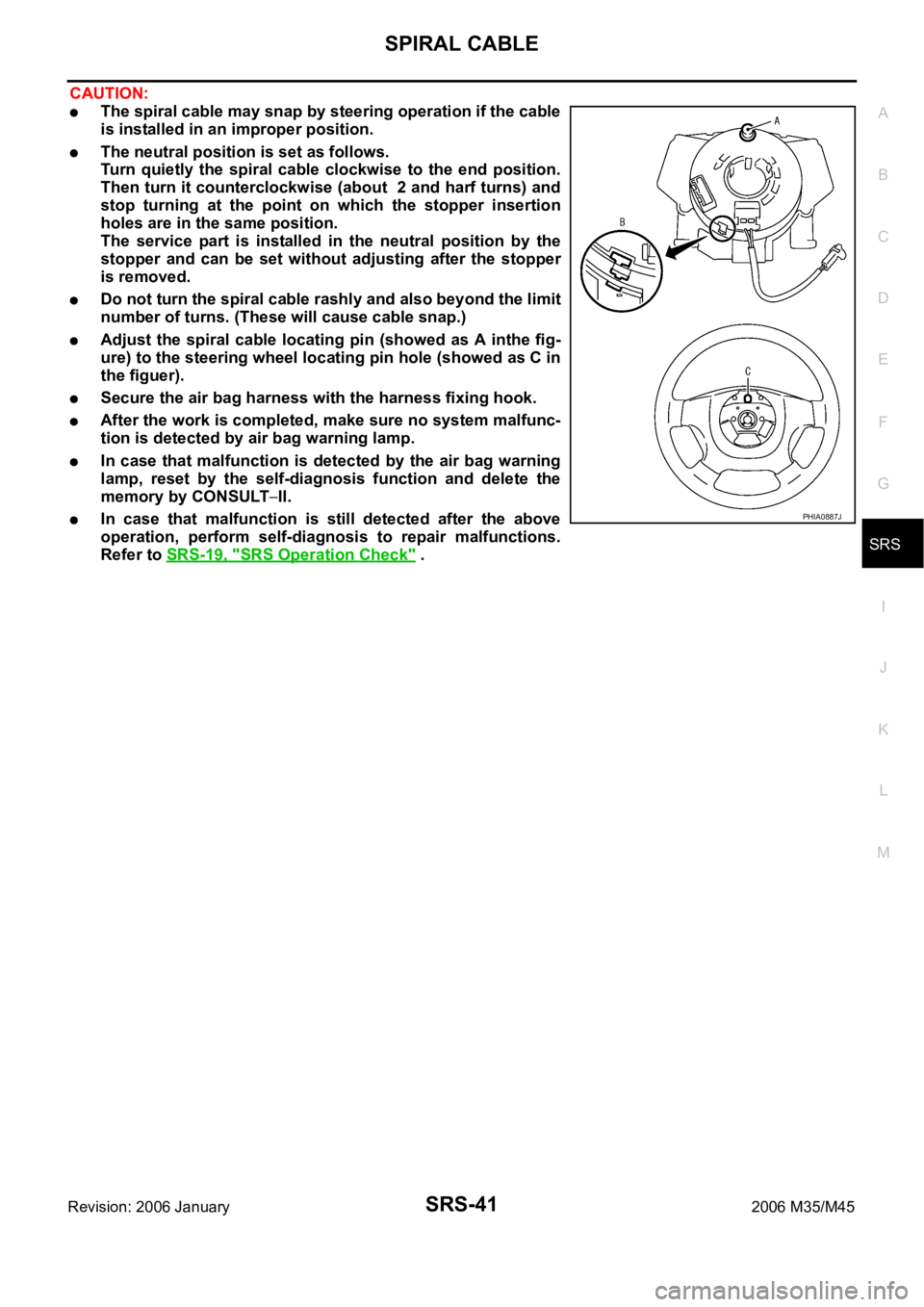
SPIRAL CABLE
SRS-41
C
D
E
F
G
I
J
K
L
MA
B
SRS
Revision: 2006 January2006 M35/M45
CAUTION:
The spiral cable may snap by steering operation if the cable
is installed in an improper position.
The neutral position is set as follows.
Turn quietly the spiral cable clockwise to the end position.
Then turn it counterclockwise (about 2 and harf turns) and
stop turning at the point on which the stopper insertion
holes are in the same position.
The service part is installed in the neutral position by the
stopper and can be set without adjusting after the stopper
is removed.
Do not turn the spiral cable rashly and also beyond the limit
number of turns. (These will cause cable snap.)
Adjust the spiral cable locating pin (showed as A inthe fig-
ure) to the steering wheel locating pin hole (showed as C in
the figuer).
Secure the air bag harness with the harness fixing hook.
After the work is completed, make sure no system malfunc-
tion is detected by air bag warning lamp.
In case that malfunction is detected by the air bag warning
lamp, reset by the self-diagnosis function and delete the
memory by CONSULT
II.
In case that malfunction is still detected after the above
operation, perform self-diagnosis to repair malfunctions.
Refer to SRS-19, "
SRS Operation Check" .
PHIA0887J
Page 5424 of 5621
![INFINITI M35 2006 Factory Service Manual TROUBLE DIAGNOSIS
STC-9
[EPS]
C
D
E
F
H
I
J
K
L
MA
B
STC
Revision: 2006 January2006 M35/M45
For Fast and Accurate Trouble DiagnosisNGS000E1
Check the following items with the vehicle stopped
Is air pr INFINITI M35 2006 Factory Service Manual TROUBLE DIAGNOSIS
STC-9
[EPS]
C
D
E
F
H
I
J
K
L
MA
B
STC
Revision: 2006 January2006 M35/M45
For Fast and Accurate Trouble DiagnosisNGS000E1
Check the following items with the vehicle stopped
Is air pr](/img/42/57023/w960_57023-5423.png)
TROUBLE DIAGNOSIS
STC-9
[EPS]
C
D
E
F
H
I
J
K
L
MA
B
STC
Revision: 2006 January2006 M35/M45
For Fast and Accurate Trouble DiagnosisNGS000E1
Check the following items with the vehicle stopped
Is air pressure and size of tires proper?
Is the specified part used for the steering wheel?
Is control unit a genuine part?
Are there any fluid leakage from steering gear assembly, power steering oil pump, and hydraulic pipes,
etc? Refer to PS-8, "
POWER STEERING FLUID" .
Is the fluid level proper? Refer to PS-8, "POWER STEERING FLUID" .
Is the wheel alignment adjusted properly? Refer to FSU-19, "SERVICE DATA AND SPECIFICATIONS
(SDS)" (2WD), FSU-36, "SERVICE DATA AND SPECIFICATIONS (SDS)" (AWD).
Are there any damage or modification to suspension or body resulting in increased weight or altered
ground clearance?
Check each link installation condition of suspension and axle.
Check each connector connection condition.
Check the following items while driving the vehicle
Check conditions when the malfunction occurred (5W 1H).
Is the engine condition normal?
Basic InspectionNGS000E2
POWER SUPPLY CIRCUIT TERMINAL LOOSENESS AND BATTERY
Check battery terminals for looseness on both positive and negative ones and ground connection. Also make
sure that battery voltage does not drop.
Inspection: Power Steering Control Unit Power Supply Circuit and GroundNGS000E3
1. CHECK POWER STEERING CONTROL UNIT CONNECTOR
Turn ignition switch OFF, disconnect power steering control unit harness connector, and check terminal for
deformation, disconnection, looseness, etc.
OK or NG
OK >> GO TO 2.
NG >> Connector terminal connection is loose, damaged, open, or shorted. Repair or replace the termi-
nal.
2. CHECK POWER STEERING CONTROL UNIT GROUND CIRCUIT
Disconnect power steering control unit harness connector M8, and
then check continuity between power steering control unit harness
connector M8 and ground.
OK or NG
OK >> GO TO 3.
NG >> Ground circuit open or shorted. Repair or replace any
inoperative parts. Terminal 2 – Ground : Continuity exist.
SGIA1231E
Page 5446 of 5621
![INFINITI M35 2006 Factory Service Manual TROUBLE DIAGNOSIS
STC-31
[RAS]
C
D
E
F
H
I
J
K
L
MA
B
STC
Revision: 2006 January2006 M35/M45
Diagnosis Procedure with Self-Diagnosis Function (Without CONSULT- I I )NGS000EL
DESCRIPTION
If a malfunc INFINITI M35 2006 Factory Service Manual TROUBLE DIAGNOSIS
STC-31
[RAS]
C
D
E
F
H
I
J
K
L
MA
B
STC
Revision: 2006 January2006 M35/M45
Diagnosis Procedure with Self-Diagnosis Function (Without CONSULT- I I )NGS000EL
DESCRIPTION
If a malfunc](/img/42/57023/w960_57023-5445.png)
TROUBLE DIAGNOSIS
STC-31
[RAS]
C
D
E
F
H
I
J
K
L
MA
B
STC
Revision: 2006 January2006 M35/M45
Diagnosis Procedure with Self-Diagnosis Function (Without CONSULT- I I )NGS000EL
DESCRIPTION
If a malfunction is detected in the system, the RAS warning lamp turns on and indicates the malfunction. At
that time, fail-safe activates, and then stops the function.
SELF-DIAGNOSIS PROCEDURE
1. Start engine.
2. Turn steering wheel left and right at 20
or more and 5 times or more within 10 seconds. And then depress
the service brake 5 times or more.
3. RAS warning lamp blinks (displays normal/malfunction).
SELF-DIAGNOSIS DISPLAY
RAS warning lamp blinks and displays the self-diagnostic results.
Only DTCs are displayed as the pattern shown in the figure, and
then repeat the display.
If all items are normal, RAS warning lamp blinks at 4 Hz cycle.
SELF-DIAGNOSIS DISPLAY ITEMS
HOW TO ERASE SELF-DIAGNOSIS
If there is the history data for when the fail-safe has activated in the past, erase the memory with CONSULT-II.
Refer to STC-29, "
How to Erase Self-Diagnostic Results" .
CAN CommunicationNGS000EM
SYSTEM DESCRIPTION
CAN (Controller Area Network) is a serial communication line for real time application. It is an on-vehicle mul-
tiplex communication line with high data communication speed and excellent error detection ability. Many elec-
tronic control units are equipped onto a vehicle, and each control unit shares information and links with other
control units during operation (not independent). In CAN communication, control units are connected with 2
communication lines (CAN H line, CAN L line) allowing a high rate of information transmission with less wiring.
Each control unit transmits/receives data but selectively reads required data only. Refer to LAN-34, "
CAN
Communication Unit" .
SGIA1243E
DTC (warning lamp blinks) Diagnosis item Inspection item
11 RAS control unitSTC-35, "
Inspection 1: RAS Control Unit Malfunction"
12 Motor power supplySTC-35, "Inspection 2: Motor Power Supply System"
13 Motor outputSTC-37, "Inspection 3: RAS Motor Output Malfunction"
21 Vehicle speed signalSTC-38, "Inspection 4: Vehicle Speed Signal"
22 Steering angle signalSTC-38, "Inspection 5: Steering Angle Signal Malfunction"
24 Rear wheel steering angle (main)STC-40, "Inspection 6: Rear Main Signal and Rear Sub Signal
Malfunction"
25 Rear wheel steering angle (sub)STC-40, "Inspection 6: Rear Main Signal and Rear Sub Signal
Malfunction"
26 VDCSTC-42, "Inspection 7: VDC Malfunction"
33 Engine speed signalSTC-43, "Inspection 8: Engine Speed Signal Malfunction"
Page 5447 of 5621
![INFINITI M35 2006 Factory Service Manual STC-32
[RAS]
TROUBLE DIAGNOSIS
Revision: 2006 January2006 M35/M45
For Fast and Accurate Trouble DiagnosisNGS000EN
Check the following items with the vehicle stopped
Is air pressure and size of tires p INFINITI M35 2006 Factory Service Manual STC-32
[RAS]
TROUBLE DIAGNOSIS
Revision: 2006 January2006 M35/M45
For Fast and Accurate Trouble DiagnosisNGS000EN
Check the following items with the vehicle stopped
Is air pressure and size of tires p](/img/42/57023/w960_57023-5446.png)
STC-32
[RAS]
TROUBLE DIAGNOSIS
Revision: 2006 January2006 M35/M45
For Fast and Accurate Trouble DiagnosisNGS000EN
Check the following items with the vehicle stopped
Is air pressure and size of tires proper?
Is the specified part used for the steering wheel?
Is control unit a genuine part?
Are there any fluid leakage from steering gear assembly, power steering oil pump, and hydraulic pipes,
etc? Refer to PS-8, "
POWER STEERING FLUID" .
Is the fluid level proper? Refer to PS-8, "POWER STEERING FLUID" .
Is the wheel alignment is adjusted properly? Refer to FSU-19, "SERVICE DATA AND SPECIFICATIONS
(SDS)" (2WD), FSU-36, "SERVICE DATA AND SPECIFICATIONS (SDS)" (AWD).
Are there any damage or modification to suspension or body resulting in increased weight or altered
ground clearance?
Check each link installation condition of suspension and axle.
Is the battery voltage proper?
Check each connector connection condition.
Check the following items while driving the vehicle
Conditions when the error occurred (5W 1H).
Is the engine is normal?
Basic InspectionNGS000EO
BASIC INSPECTION 1: POWER SUPPLY CIRCUIT TERMINAL LOOSENESS AND BATTERY
Check battery terminals for looseness on both positive and negative ones and ground connection. Also make
sure that battery voltage does not drop.
BASIC INSPECTION 2: RAS WARNING LAMP INSPECTION
1. Make sure RAS warning lamp turns on when ignition switch is turned ON.
If it does not turn on, refer to STC-33, "Trouble Diagnosis Chart" .
2. Make sure that RAS warning lamp turns off when the engine is started after ignition switch is turned ON. If
it does not turn off, perform self-diagnosis. Refer to STC-28, "
SELF-DIAG RESULT MODE" .
3. Always erase DTC memory after completing self-diagnosis. Refer to STC-29, "
How to Erase Self-Diag-
nostic Results" .
BASIC INSPECTION 3: RAS CONTROL UNIT POWER SUPPLY CIRCUIT AND GROUND CIR-
CUIT INSPECTION
1. CHECK RAS CONTROL UNIT CONNECTOR
Turn ignition switch OFF, disconnect RAS control unit harness connector, and check terminal for deformation,
disconnection, looseness, etc.
OK or NG
OK >> GO TO 2.
NG >> Poor connection of connector terminal. Repair or replace the terminal.
2. CHECK RAS CONTROL UNIT GROUND CIRCUIT
1. Disconnect RAS control unit harness connector B127, and then
check continuity between RAS control unit harness connector
B127 and ground.
OK or NG
OK >> GO TO 3.
NG >> Ground circuit open or shorted. Repair or replace any
inoperative parts. Terminal 34 – Ground : Continuity
SGIA1244E
Page 5466 of 5621
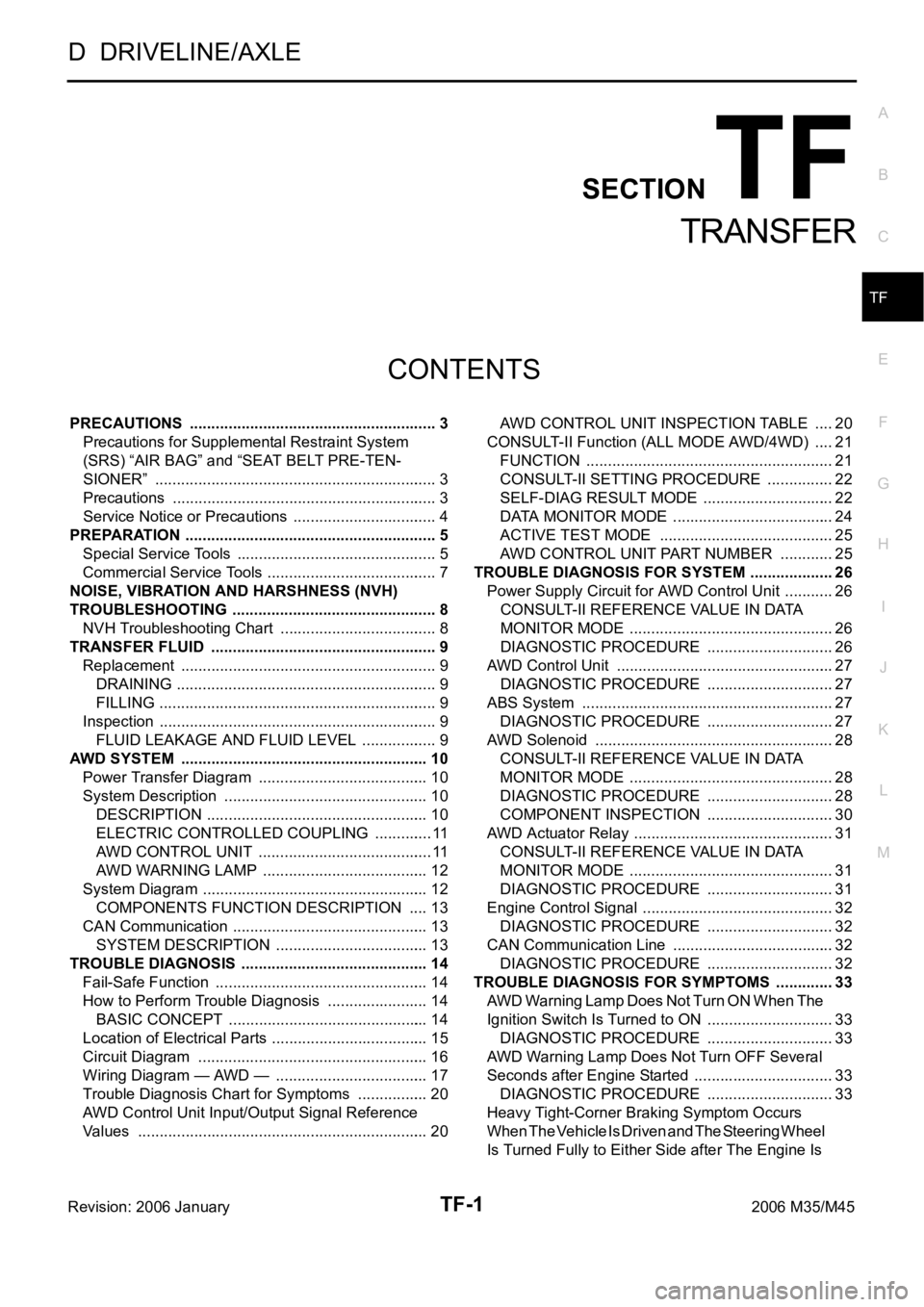
TF-1
TRANSFER
D DRIVELINE/AXLE
CONTENTS
C
E
F
G
H
I
J
K
L
M
SECTION TF
A
B
TF
Revision: 2006 January2006 M35/M45
TRANSFER
PRECAUTIONS .......................................................... 3
Precautions for Supplemental Restraint System
(SRS) “AIR BAG” and “SEAT BELT PRE-TEN-
SIONER” .................................................................. 3
Precautions .............................................................. 3
Service Notice or Precautions .................................. 4
PREPARATION ........................................................... 5
Special Service Tools ............................................... 5
Commercial Service Tools ........................................ 7
NOISE, VIBRATION AND HARSHNESS (NVH)
TROUBLESHOOTING ................................................ 8
NVH Troubleshooting Chart ..................................... 8
TRANSFER FLUID ..................................................... 9
Replacement ............................................................ 9
DRAINING ............................................................. 9
FILLING ................................................................. 9
Inspection ................................................................. 9
FLUID LEAKAGE AND FLUID LEVEL .................. 9
AWD SYSTEM .......................................................... 10
Power Transfer Diagram ........................................ 10
System Description ................................................ 10
DESCRIPTION .................................................... 10
ELECTRIC CONTROLLED COUPLING .............. 11
AWD CONTROL UNIT ......................................... 11
AWD WARNING LAMP ....................................... 12
System Diagram ..................................................... 12
COMPONENTS FUNCTION DESCRIPTION ..... 13
CAN Communication .............................................. 13
SYSTEM DESCRIPTION .................................... 13
TROUBLE DIAGNOSIS ............................................ 14
Fail-Safe Function .................................................. 14
How to Perform Trouble Diagnosis ........................ 14
BASIC CONCEPT ............................................... 14
Location of Electrical Parts ..................................... 15
Circuit Diagram ...................................................... 16
Wiring Diagram — AWD — .................................... 17
Trouble Diagnosis Chart for Symptoms ................. 20
AWD Control Unit Input/Output Signal Reference
Values .................................................................... 20AWD CONTROL UNIT INSPECTION TABLE ..... 20
CONSULT-II Function (ALL MODE AWD/4WD) ..... 21
FUNCTION .......................................................
... 21
CONSULT-II SETTING PROCEDURE ................ 22
SELF-DIAG RESULT MODE ............................... 22
DATA MONITOR MODE ...................................... 24
ACTIVE TEST MODE ......................................... 25
AWD CONTROL UNIT PART NUMBER ............. 25
TROUBLE DIAGNOSIS FOR SYSTEM .................... 26
Power Supply Circuit for AWD Control Unit ............ 26
CONSULT-II REFERENCE VALUE IN DATA
MONITOR MODE ................................................ 26
DIAGNOSTIC PROCEDURE .............................. 26
AWD Control Unit ................................................... 27
DIAGNOSTIC PROCEDURE .............................. 27
ABS System ........................................................... 27
DIAGNOSTIC PROCEDURE .............................. 27
AWD Solenoid ........................................................ 28
CONSULT-II REFERENCE VALUE IN DATA
MONITOR MODE ................................................ 28
DIAGNOSTIC PROCEDURE .............................. 28
COMPONENT INSPECTION .............................. 30
AWD Actuator Relay ............................................... 31
CONSULT-II REFERENCE VALUE IN DATA
MONITOR MODE ................................................ 31
DIAGNOSTIC PROCEDURE .............................. 31
Engine Control Signal ............................................. 32
DIAGNOSTIC PROCEDURE .............................. 32
CAN Communication Line ...................................... 32
DIAGNOSTIC PROCEDURE .............................. 32
TROUBLE DIAGNOSIS FOR SYMPTOMS .............. 33
AWD Warning Lamp Does Not Turn ON When The
Ignition Switch Is Turned to ON .............................. 33
DIAGNOSTIC PROCEDURE .............................. 33
AWD Warning Lamp Does Not Turn OFF Several
Seconds after Engine Started ................................. 33
DIAGNOSTIC PROCEDURE .............................. 33
Heavy Tight-Corner Braking Symptom Occurs
When The Vehicle Is Driven and The Steering Wheel
Is Turned Fully to Either Side after The Engine Is
Page 5467 of 5621
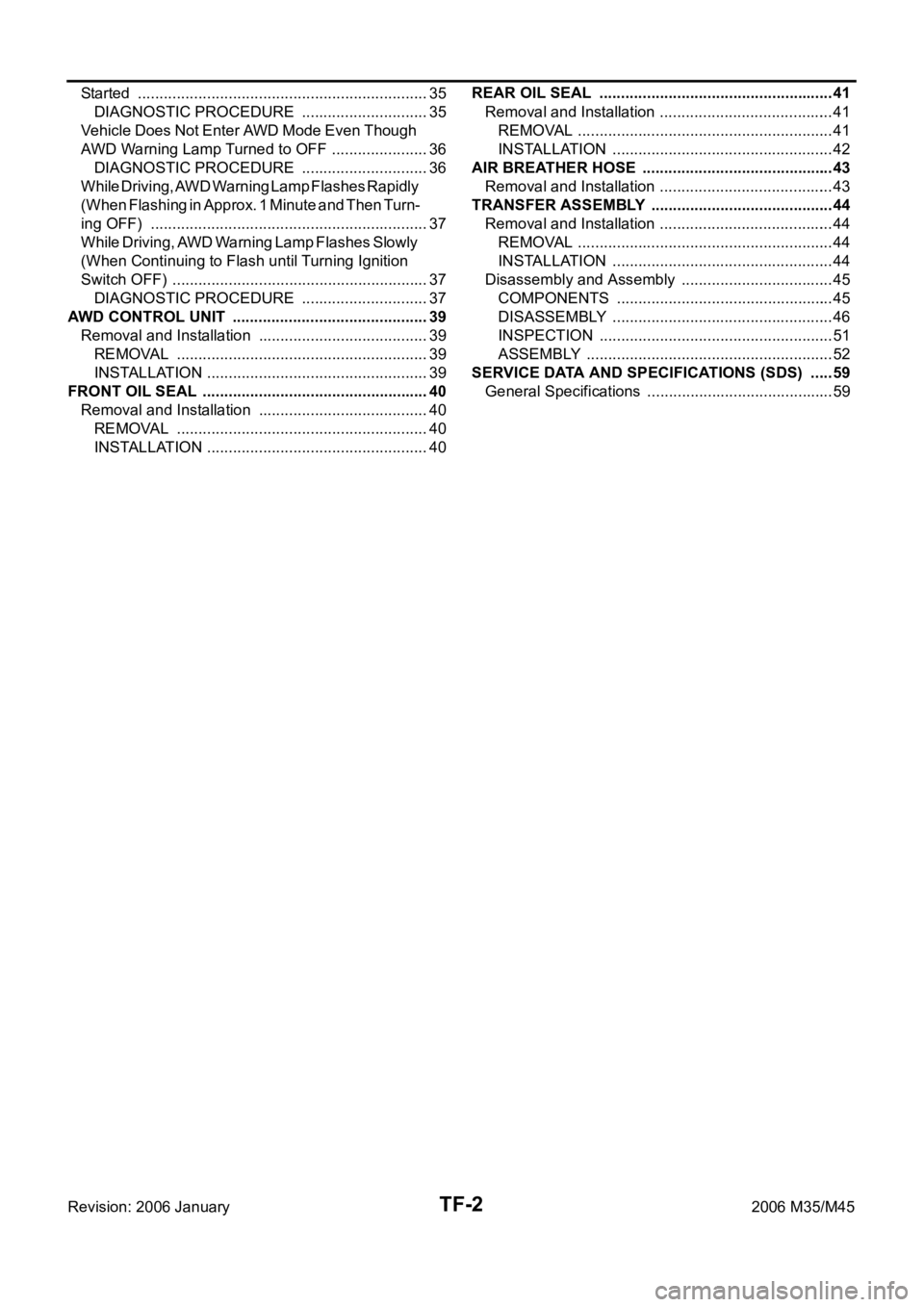
TF-2Revision: 2006 January2006 M35/M45 Started .................................................................... 35
DIAGNOSTIC PROCEDURE .............................. 35
Vehicle Does Not Enter AWD Mode Even Though
AWD Warning Lamp Turned to OFF ....................... 36
DIAGNOSTIC PROCEDURE .............................. 36
While Driving, AWD Warning Lamp Flashes Rapidly
(When Flashing in Approx. 1 Minute and Then Turn-
ing OFF) ................................................................. 37
While Driving, AWD Warning Lamp Flashes Slowly
(When Continuing to Flash until Turning Ignition
Switch OFF) ............................................................ 37
DIAGNOSTIC PROCEDURE .............................. 37
AWD CONTROL UNIT .............................................. 39
Removal and Installation ........................................ 39
REMOVAL ........................................................
... 39
INSTALLATION .................................................... 39
FRONT OIL SEAL ..................................................... 40
Removal and Installation ........................................ 40
REMOVAL ........................................................
... 40
INSTALLATION .................................................... 40REAR OIL SEAL ....................................................... 41
Removal and Installation ......................................... 41
REMOVAL ............................................................ 41
INSTALLATION .................................................... 42
AIR BREATHER HOSE ............................................. 43
Removal and Installation ......................................... 43
TRANSFER ASSEMBLY ........................................... 44
Removal and Installation ......................................... 44
REMOVAL ............................................................ 44
INSTALLATION .................................................... 44
Disassembly and Assembly .................................... 45
COMPONENTS ................................................... 45
DISASSEMBLY .................................................... 46
INSPECTION ....................................................... 51
ASSEMBLY .......................................................... 52
SERVICE DATA AND SPECIFICATIONS (SDS) ...... 59
General Specifications ......................................... ... 59
Page 5468 of 5621
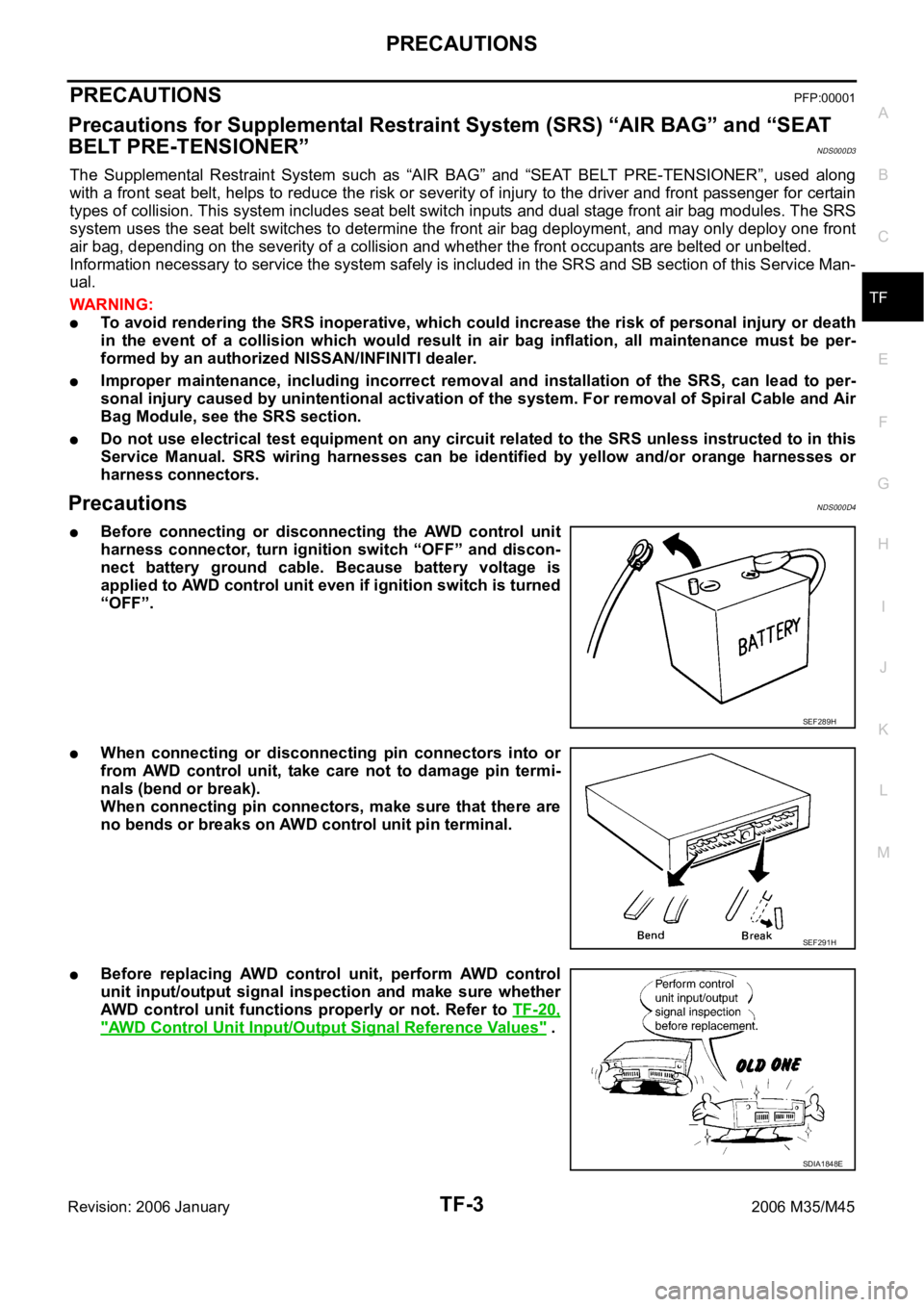
PRECAUTIONS
TF-3
C
E
F
G
H
I
J
K
L
MA
B
TF
Revision: 2006 January2006 M35/M45
PRECAUTIONSPFP:00001
Precautions for Supplemental Restraint System (SRS) “AIR BAG” and “SEAT
BELT PRE-TENSIONER”
NDS000D3
The Supplemental Restraint System such as “AIR BAG” and “SEAT BELT PRE-TENSIONER”, used along
with a front seat belt, helps to reduce the risk or severity of injury to the driver and front passenger for certain
types of collision. This system includes seat belt switch inputs and dual stage front air bag modules. The SRS
system uses the seat belt switches to determine the front air bag deployment, and may only deploy one front
air bag, depending on the severity of a collision and whether the front occupants are belted or unbelted.
Information necessary to service the system safely is included in the SRS and SB section of this Service Man-
ual.
WAR NING :
To avoid rendering the SRS inoperative, which could increase the risk of personal injury or death
in the event of a collision which would result in air bag inflation, all maintenance must be per-
formed by an authorized NISSAN/INFINITI dealer.
Improper maintenance, including incorrect removal and installation of the SRS, can lead to per-
sonal injury caused by unintentional activation of the system. For removal of Spiral Cable and Air
Bag Module, see the SRS section.
Do not use electrical test equipment on any circuit related to the SRS unless instructed to in this
Service Manual. SRS wiring harnesses can be identified by yellow and/or orange harnesses or
harness connectors.
PrecautionsNDS000D4
Before connecting or disconnecting the AWD control unit
harness connector, turn ignition switch “OFF” and discon-
nect battery ground cable. Because battery voltage is
applied to AWD control unit even if ignition switch is turned
“OFF”.
When connecting or disconnecting pin connectors into or
from AWD control unit, take care not to damage pin termi-
nals (bend or break).
When connecting pin connectors, make sure that there are
no bends or breaks on AWD control unit pin terminal.
Before replacing AWD control unit, perform AWD control
unit input/output signal inspection and make sure whether
AWD control unit functions properly or not. Refer to TF-20,
"AWD Control Unit Input/Output Signal Reference Values" .
SEF289H
SEF291H
SDIA1848E