Panel INFINITI M35 2006 Factory Repair Manual
[x] Cancel search | Manufacturer: INFINITI, Model Year: 2006, Model line: M35, Model: INFINITI M35 2006Pages: 5621, PDF Size: 65.56 MB
Page 1229 of 5621
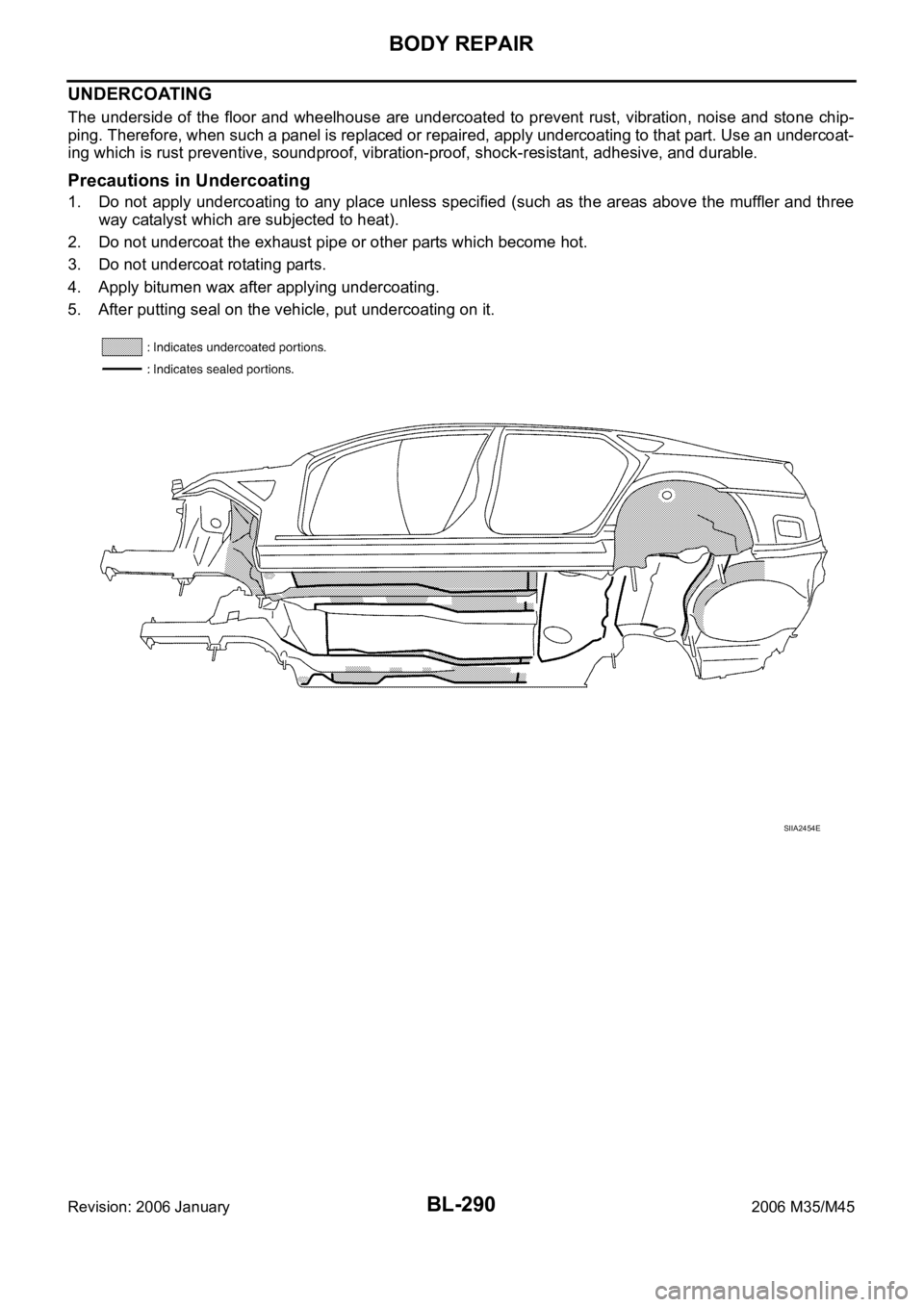
BL-290
BODY REPAIR
Revision: 2006 January2006 M35/M45
UNDERCOATING
The underside of the floor and wheelhouse are undercoated to prevent rust, vibration, noise and stone chip-
ping. Therefore, when such a panel is replaced or repaired, apply undercoating to that part. Use an undercoat-
ing which is rust preventive, soundproof, vibration-proof, shock-resistant, adhesive, and durable.
Precautions in Undercoating
1. Do not apply undercoating to any place unless specified (such as the areas above the muffler and three
way catalyst which are subjected to heat).
2. Do not undercoat the exhaust pipe or other parts which become hot.
3. Do not undercoat rotating parts.
4. Apply bitumen wax after applying undercoating.
5. After putting seal on the vehicle, put undercoating on it.
SIIA2454E
Page 1235 of 5621
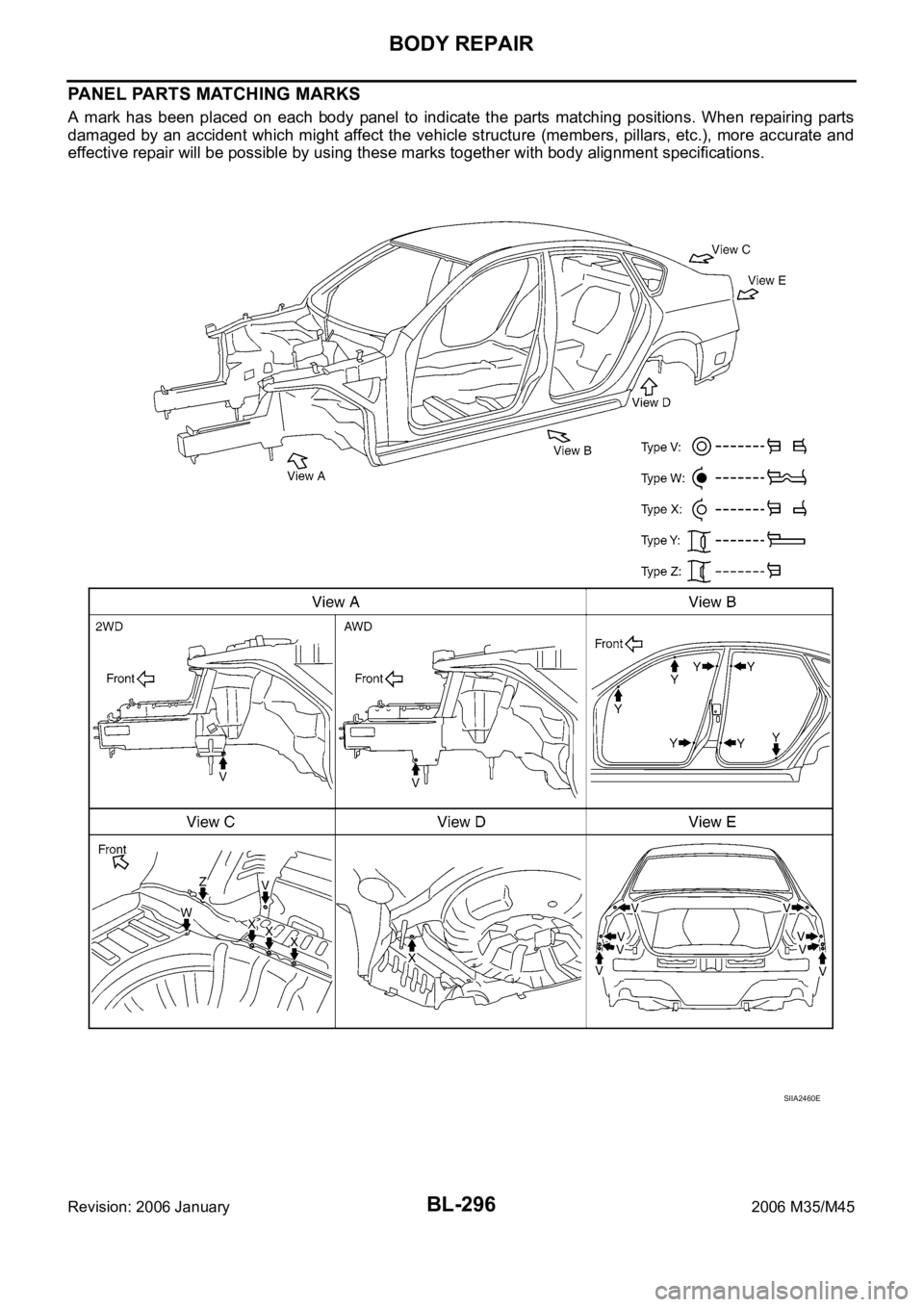
BL-296
BODY REPAIR
Revision: 2006 January2006 M35/M45
PANEL PARTS MATCHING MARKS
A mark has been placed on each body panel to indicate the parts matching positions. When repairing parts
damaged by an accident which might affect the vehicle structure (members, pillars, etc.), more accurate and
effective repair will be possible by using these marks together with body alignment specifications.
SIIA2460E
Page 1248 of 5621
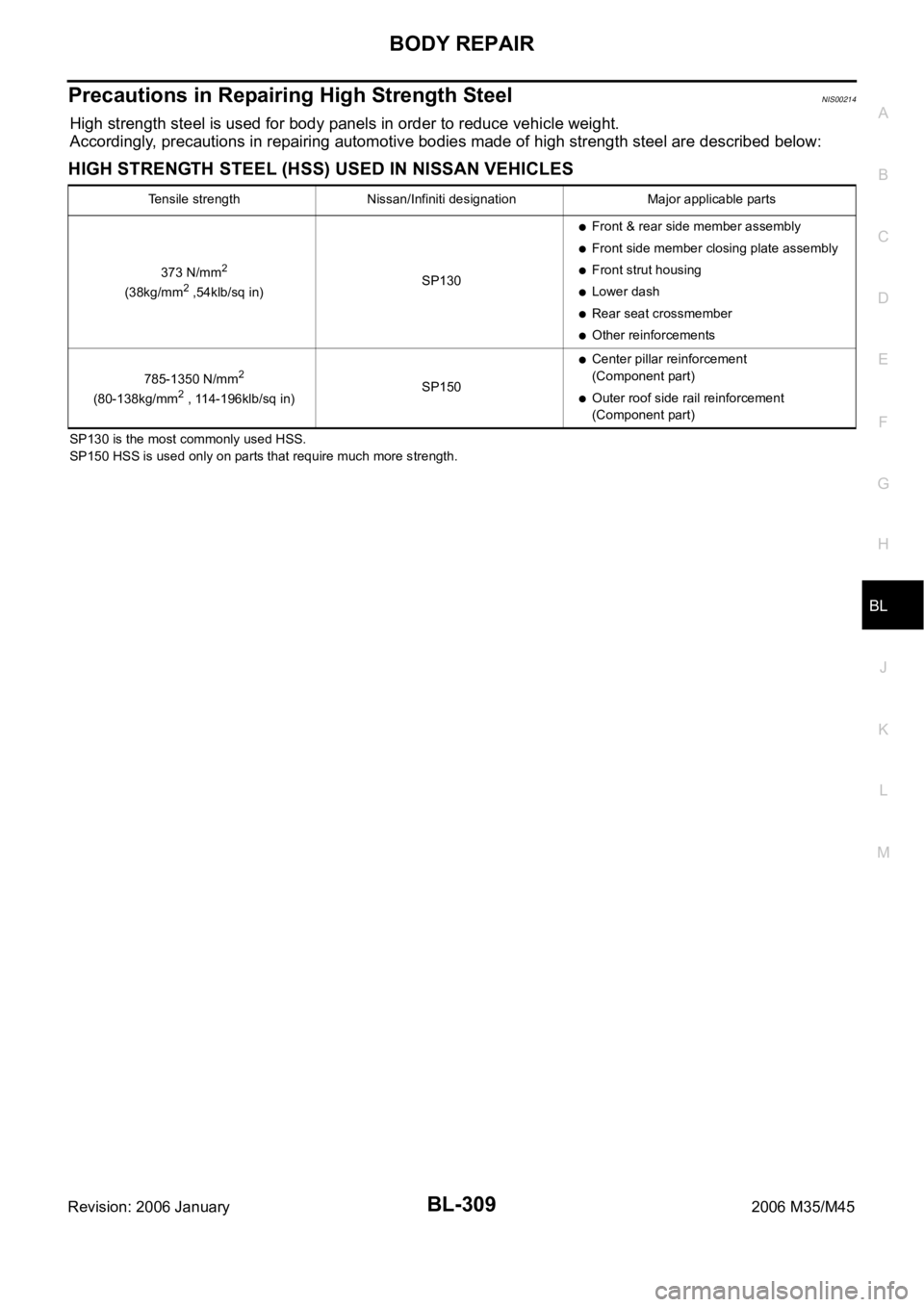
BODY REPAIR
BL-309
C
D
E
F
G
H
J
K
L
MA
B
BL
Revision: 2006 January2006 M35/M45
Precautions in Repairing High Strength SteelNIS00214
High strength steel is used for body panels in order to reduce vehicle weight.
Accordingly, precautions in repairing automotive bodies made of high strength steel are described below:
HIGH STRENGTH STEEL (HSS) USED IN NISSAN VEHICLES
SP130 is the most commonly used HSS.
SP150 HSS is used only on parts that require much more strength. Tensile strength Nissan/Infiniti designation Major applicable parts
373 N/mm
2
(38kg/mm2 ,54klb/sq in)SP130
Front & rear side member assembly
Front side member closing plate assembly
Front strut housing
Lower dash
Rear seat crossmember
Other reinforcements
785-1350 N/mm
2
(80-138kg/mm2 , 114-196klb/sq in)SP150
Center pillar reinforcement
(Component part)
Outer roof side rail reinforcement
(Component part)
Page 1249 of 5621
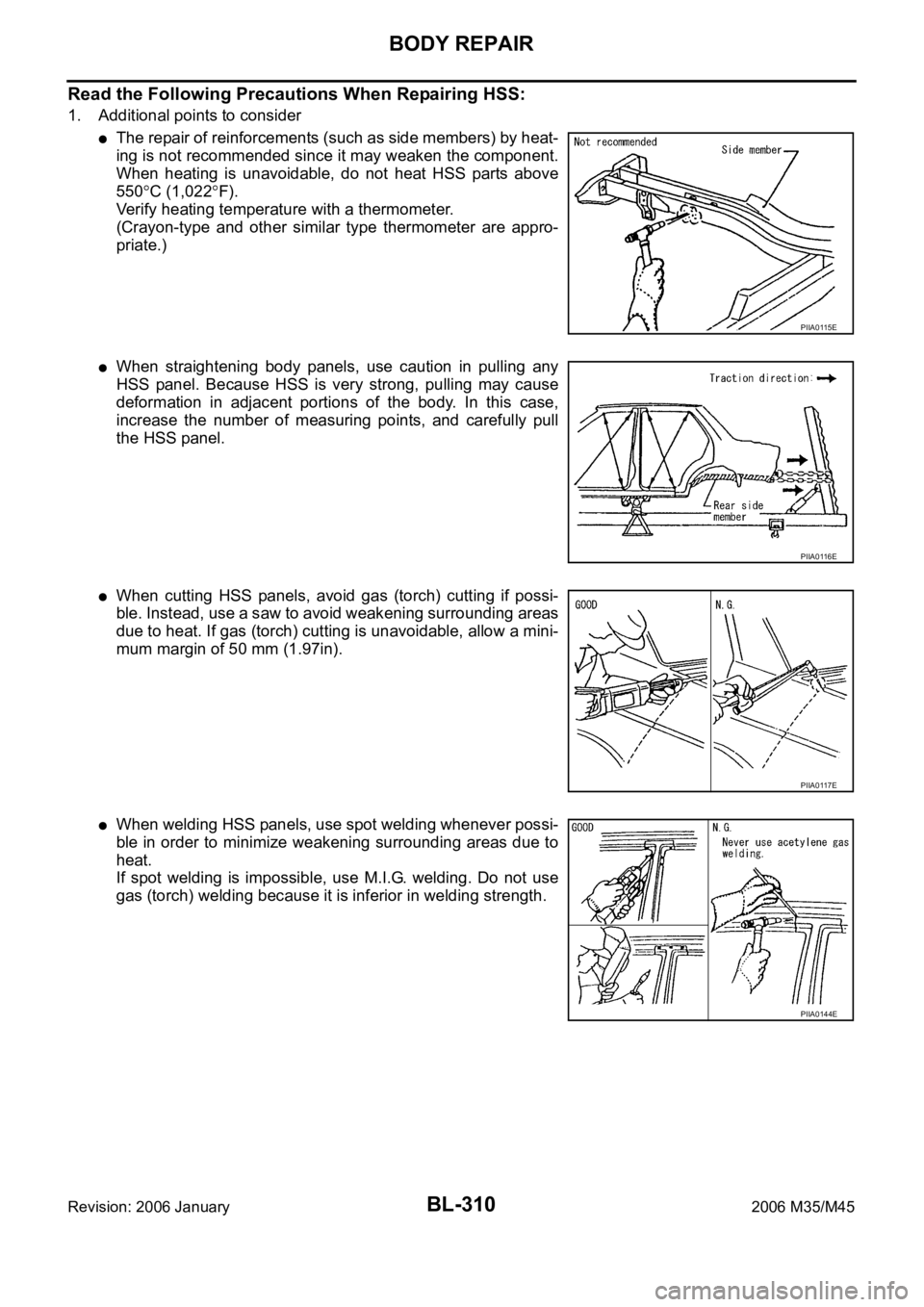
BL-310
BODY REPAIR
Revision: 2006 January2006 M35/M45
Read the Following Precautions When Repairing HSS:
1. Additional points to consider
The repair of reinforcements (such as side members) by heat-
ing is not recommended since it may weaken the component.
When heating is unavoidable, do not heat HSS parts above
550
C (1,022F).
Verify heating temperature with a thermometer.
(Crayon-type and other similar type thermometer are appro-
priate.)
When straightening body panels, use caution in pulling any
HSS panel. Because HSS is very strong, pulling may cause
deformation in adjacent portions of the body. In this case,
increase the number of measuring points, and carefully pull
the HSS panel.
When cutting HSS panels, avoid gas (torch) cutting if possi-
ble. Instead, use a saw to avoid weakening surrounding areas
due to heat. If gas (torch) cutting is unavoidable, allow a mini-
mum margin of 50 mm (1.97in).
When welding HSS panels, use spot welding whenever possi-
ble in order to minimize weakening surrounding areas due to
heat.
If spot welding is impossible, use M.I.G. welding. Do not use
gas (torch) welding because it is inferior in welding strength.
PIIA0115E
PIIA0116E
PIIA0117E
PIIA0144E
Page 1250 of 5621
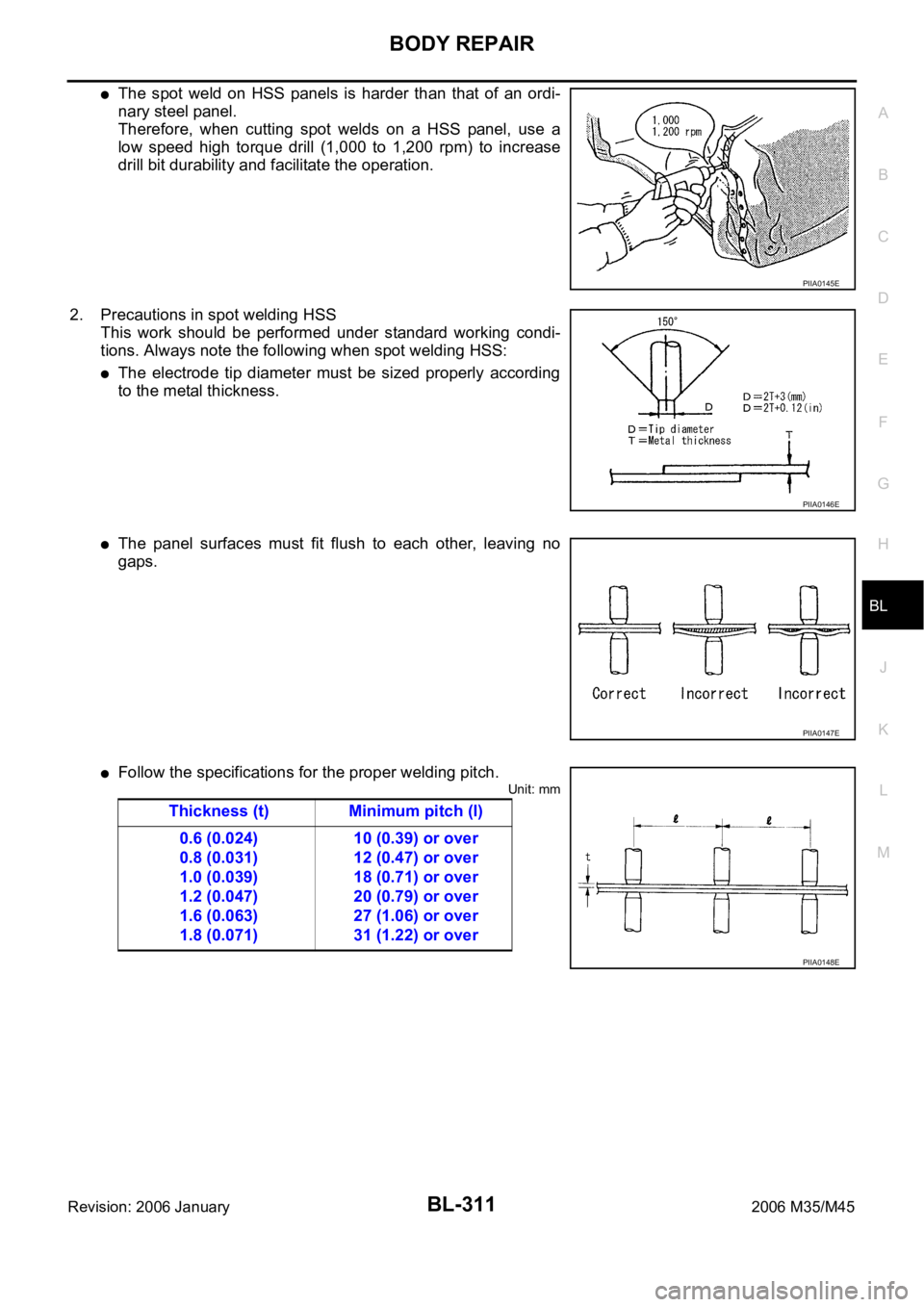
BODY REPAIR
BL-311
C
D
E
F
G
H
J
K
L
MA
B
BL
Revision: 2006 January2006 M35/M45
The spot weld on HSS panels is harder than that of an ordi-
nary steel panel.
Therefore, when cutting spot welds on a HSS panel, use a
low speed high torque drill (1,000 to 1,200 rpm) to increase
drill bit durability and facilitate the operation.
2. Precautions in spot welding HSS
This work should be performed under standard working condi-
tions. Always note the following when spot welding HSS:
The electrode tip diameter must be sized properly according
to the metal thickness.
The panel surfaces must fit flush to each other, leaving no
gaps.
Follow the specifications for the proper welding pitch.
Unit: mm
PIIA0145E
PIIA0146E
PIIA0147E
Thickness (t) Minimum pitch (l)
0.6 (0.024)
0.8 (0.031)
1.0 (0.039)
1.2 (0.047)
1.6 (0.063)
1.8 (0.071)10 (0.39) or over
12 (0.47) or over
18 (0.71) or over
20 (0.79) or over
27 (1.06) or over
31 (1.22) or over
PIIA0148E
Page 1251 of 5621
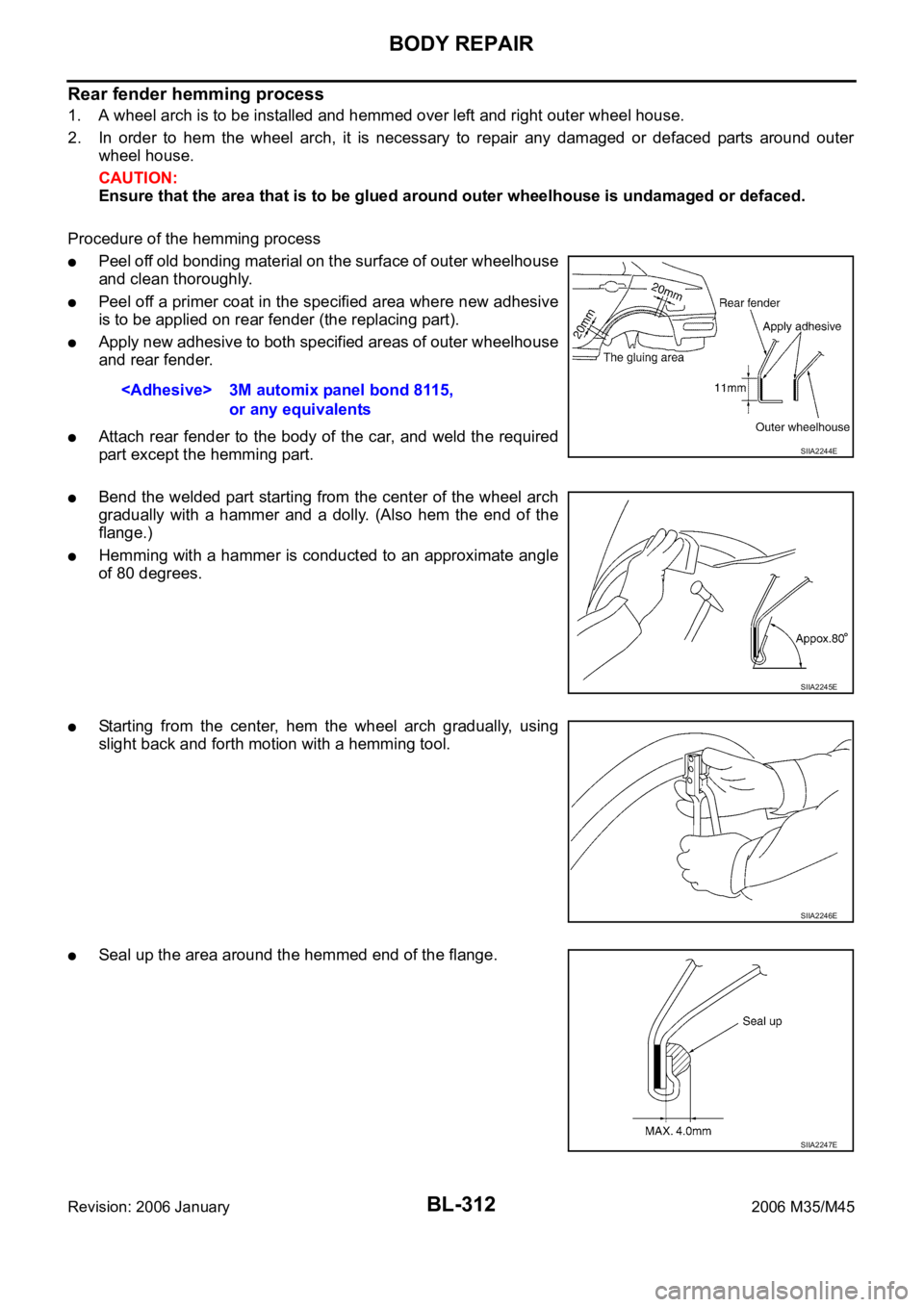
BL-312
BODY REPAIR
Revision: 2006 January2006 M35/M45
Rear fender hemming process
1. A wheel arch is to be installed and hemmed over left and right outer wheel house.
2. In order to hem the wheel arch, it is necessary to repair any damaged or defaced parts around outer
wheel house.
CAUTION:
Ensure that the area that is to be glued around outer wheelhouse is undamaged or defaced.
Procedure of the hemming process
Peel off old bonding material on the surface of outer wheelhouse
and clean thoroughly.
Peel off a primer coat in the specified area where new adhesive
is to be applied on rear fender (the replacing part).
Apply new adhesive to both specified areas of outer wheelhouse
and rear fender.
Attach rear fender to the body of the car, and weld the required
part except the hemming part.
Bend the welded part starting from the center of the wheel arch
gradually with a hammer and a dolly. (Also hem the end of the
flange.)
Hemming with a hammer is conducted to an approximate angle
of 80 degrees.
Starting from the center, hem the wheel arch gradually, using
slight back and forth motion with a hemming tool.
Seal up the area around the hemmed end of the flange.
or any equivalents
SIIA2244E
SIIA2245E
SIIA2246E
SIIA2247E
Page 1271 of 5621
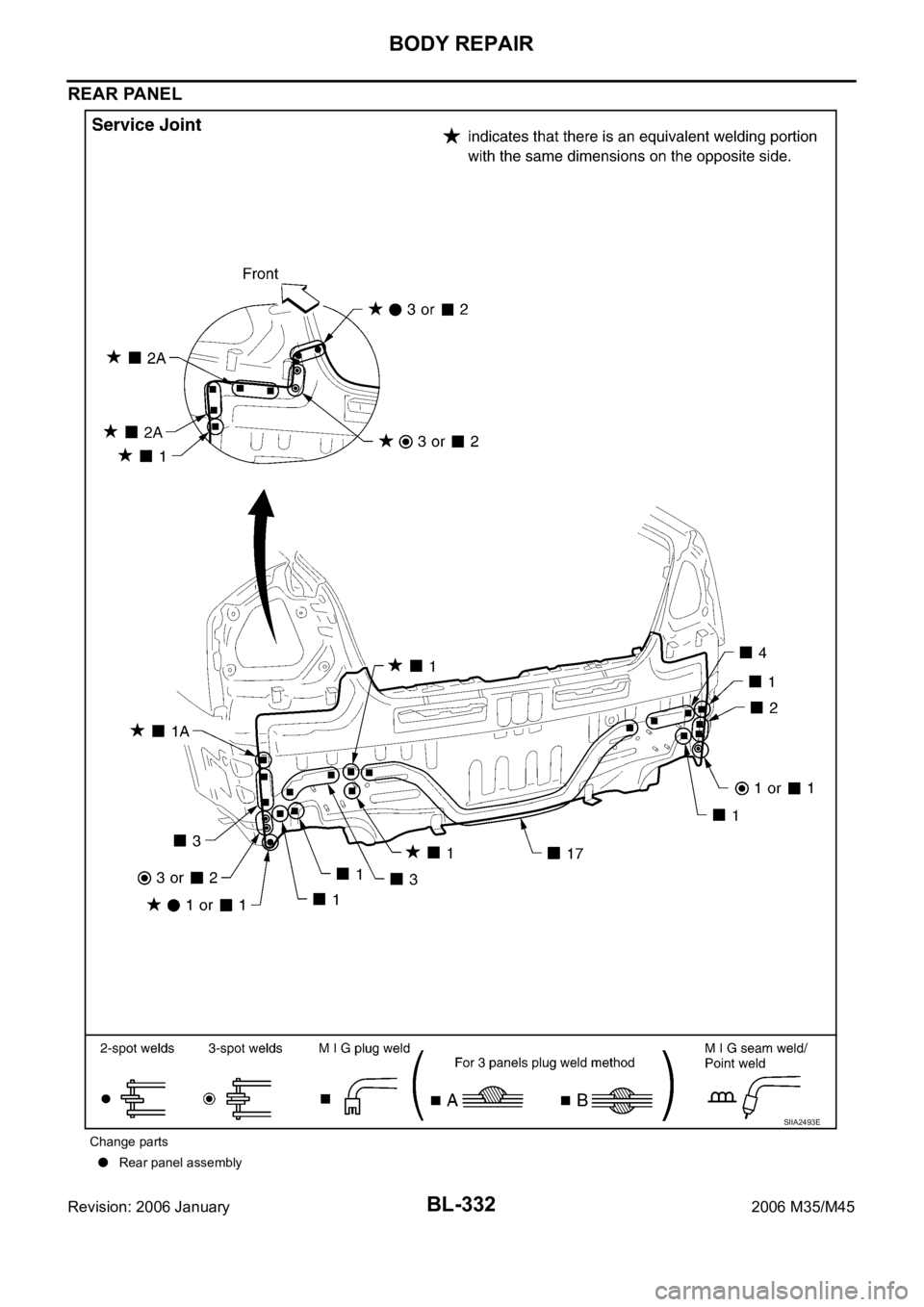
BL-332
BODY REPAIR
Revision: 2006 January2006 M35/M45
REAR PANEL
Change parts
Rear panel assembly
SIIA2493E
Page 1272 of 5621
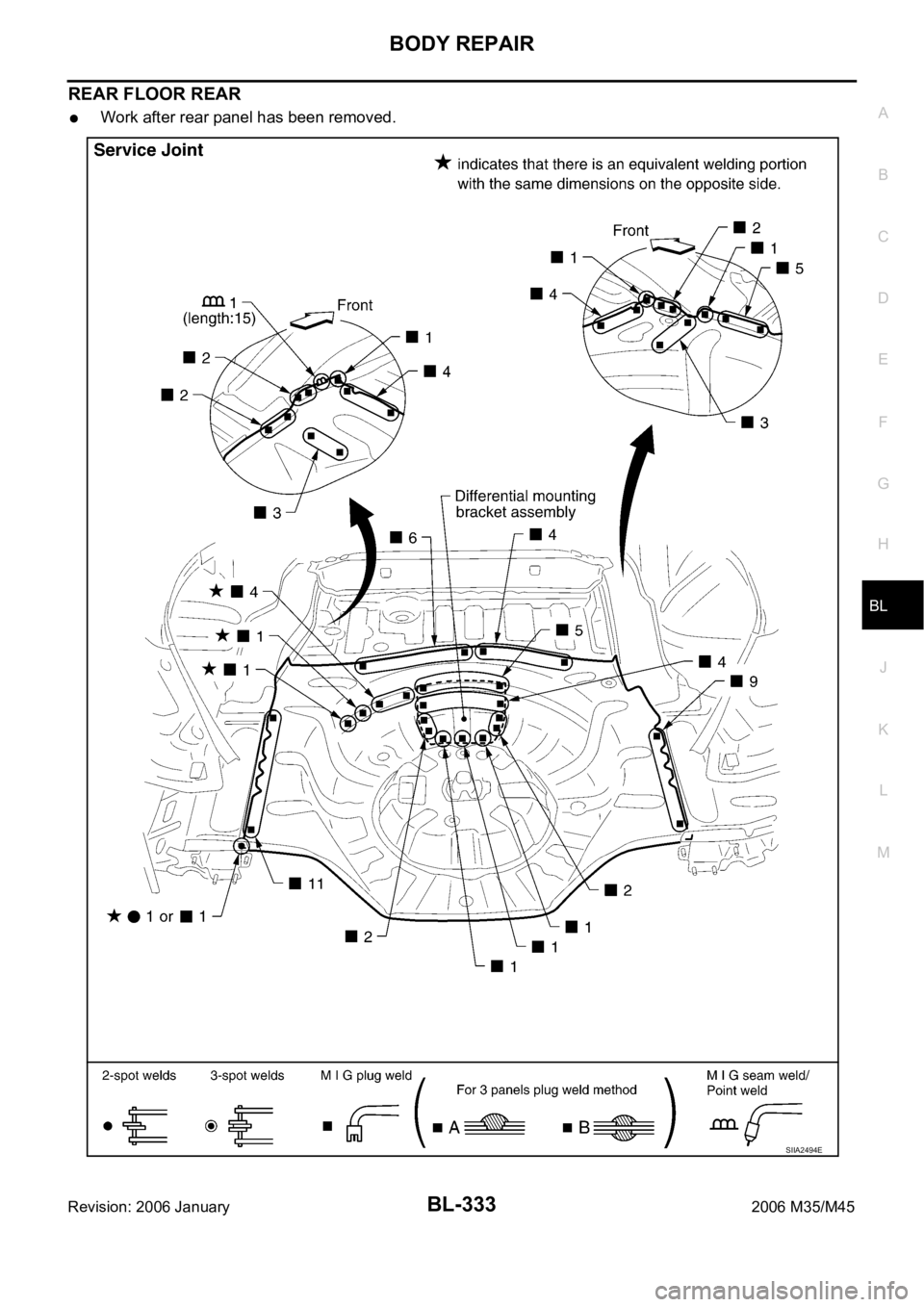
BODY REPAIR
BL-333
C
D
E
F
G
H
J
K
L
MA
B
BL
Revision: 2006 January2006 M35/M45
REAR FLOOR REAR
Work after rear panel has been removed.
SIIA2494E
Page 1274 of 5621
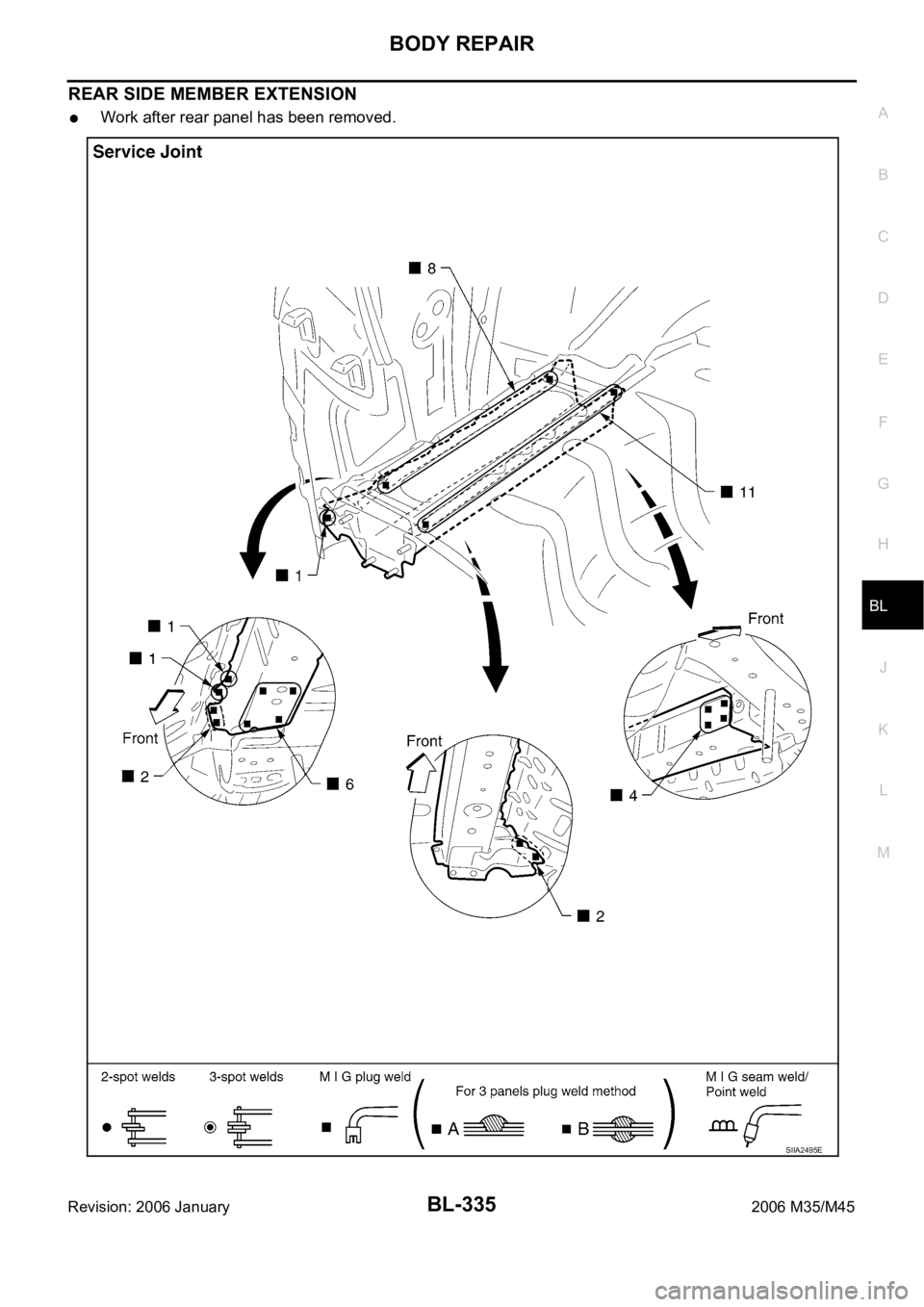
BODY REPAIR
BL-335
C
D
E
F
G
H
J
K
L
MA
B
BL
Revision: 2006 January2006 M35/M45
REAR SIDE MEMBER EXTENSION
Work after rear panel has been removed.
SIIA2495E
Page 1281 of 5621
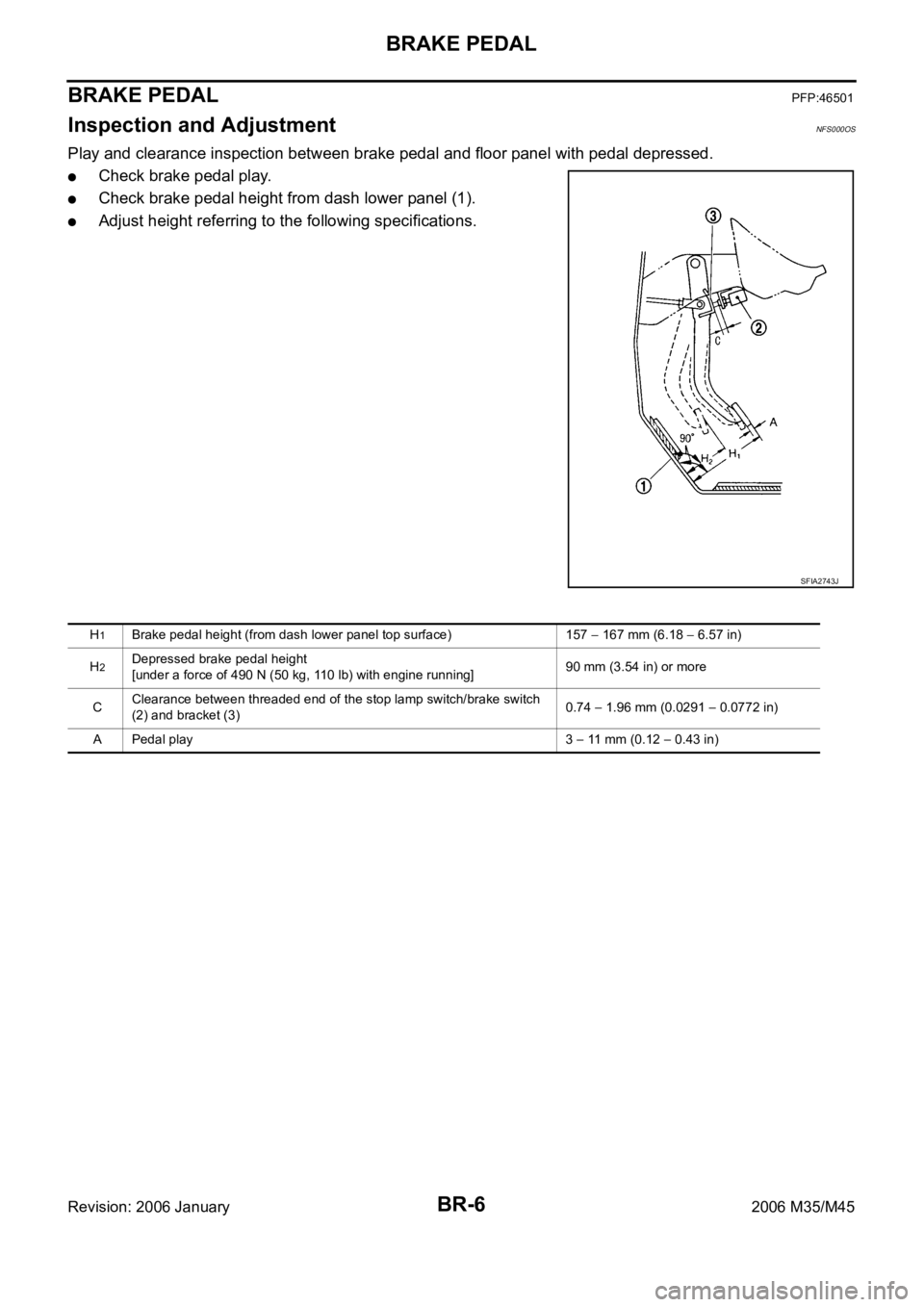
BR-6
BRAKE PEDAL
Revision: 2006 January2006 M35/M45
BRAKE PEDALPFP:46501
Inspection and AdjustmentNFS000OS
Play and clearance inspection between brake pedal and floor panel with pedal depressed.
Check brake pedal play.
Check brake pedal height from dash lower panel (1).
Adjust height referring to the following specifications.
SFIA2743J
H1Brake pedal height (from dash lower panel top surface) 157 167 mm (6.18 6.57 in)
H
2Depressed brake pedal height
[under a force of 490 N (50 kg, 110 lb) with engine running]90 mm (3.54 in) or more
CClearance between threaded end of the stop lamp switch/brake switch
(2) and bracket (3)0.74
1.96 mm (0.0291 0.0772 in)
A Pedal play 3
11 mm (0.12 0.43 in)