INFINITI QX56 2008 Factory Service Manual
Manufacturer: INFINITI, Model Year: 2008, Model line: QX56, Model: INFINITI QX56 2008Pages: 4083, PDF Size: 81.73 MB
Page 2731 of 4083
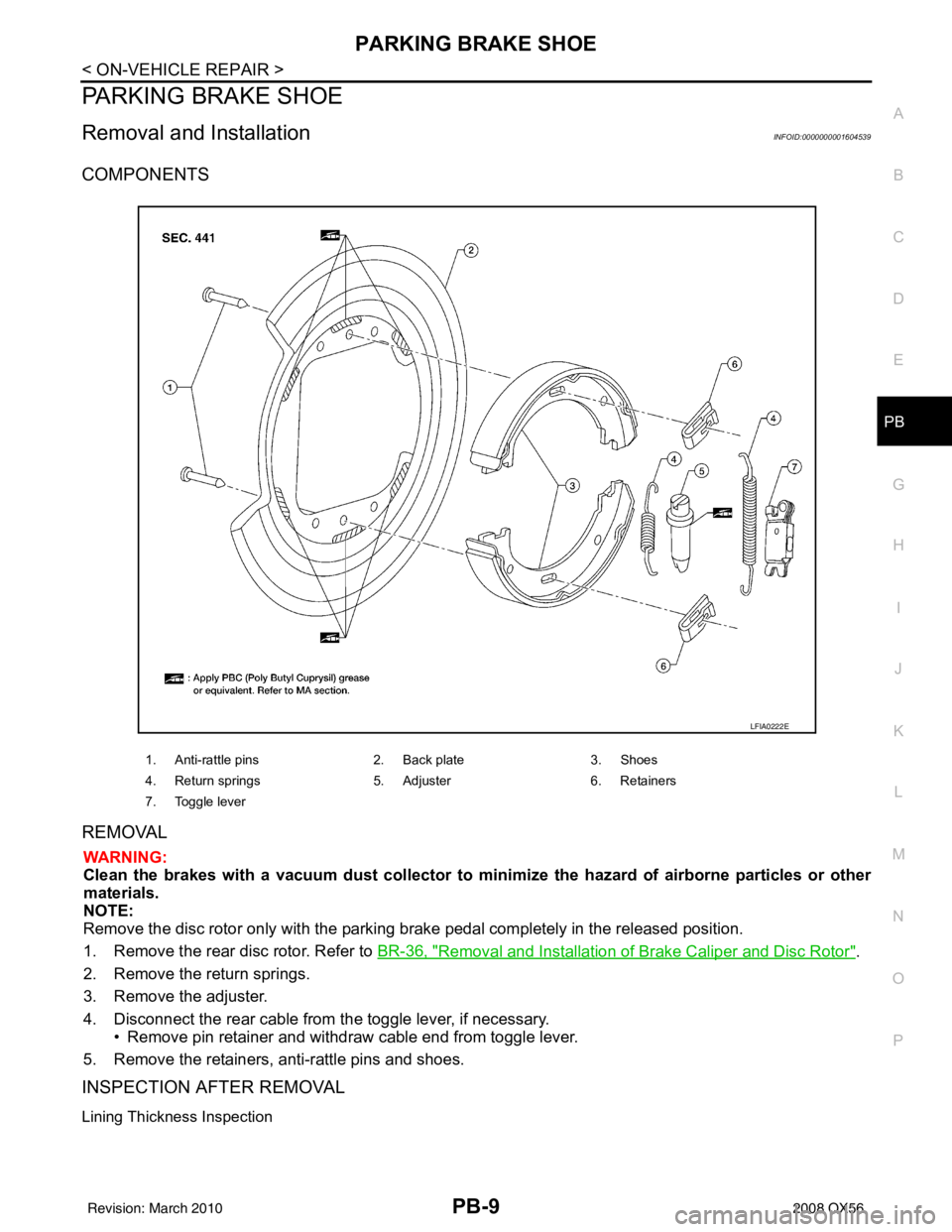
PARKING BRAKE SHOEPB-9
< ON-VEHICLE REPAIR >
C
DE
G H
I
J
K L
M A
B
PB
N
O P
PARKING BRAKE SHOE
Removal and InstallationINFOID:0000000001604539
COMPONENTS
REMOVAL
WARNING:
Clean the brakes with a vacuum dust co llector to minimize the hazard of airborne particles or other
materials.
NOTE:
Remove the disc rotor only with the parking brake pedal completely in the released position.
1. Remove the rear disc rotor. Refer to BR-36, "
Removal and Installation of Brake Caliper and Disc Rotor".
2. Remove the return springs.
3. Remove the adjuster.
4. Disconnect the rear cable from the toggle lever, if necessary.
• Remove pin retainer and withdraw cable end from toggle lever.
5. Remove the retainers, anti-rattle pins and shoes.
INSPECTION AFTER REMOVAL
Lining Thickness Inspection
1. Anti-rattle pins 2. Back plate3. Shoes
4. Return springs 5. Adjuster6. Retainers
7. Toggle lever
LFIA0222E
Revision: March 2010 2008 QX56
Page 2732 of 4083
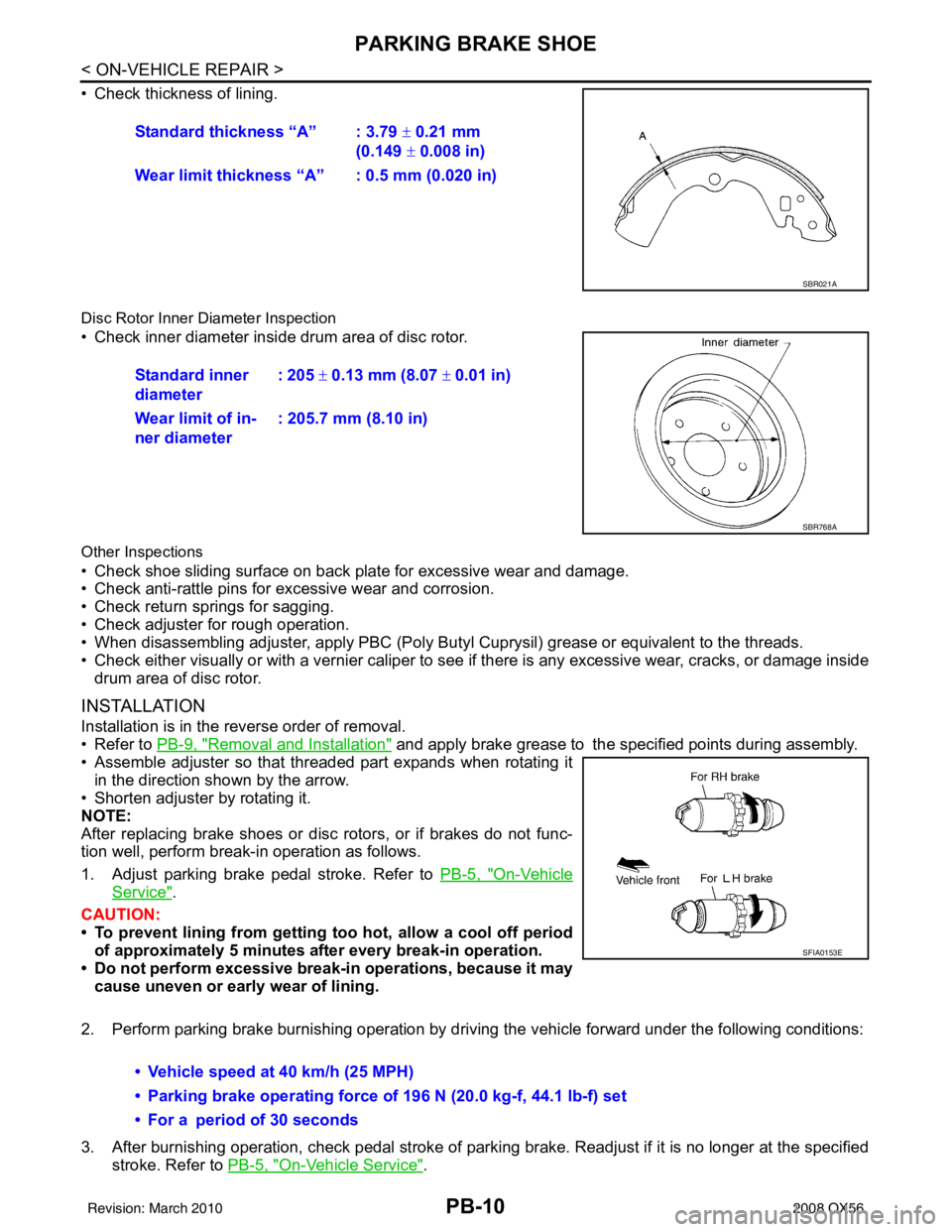
PB-10
< ON-VEHICLE REPAIR >
PARKING BRAKE SHOE
• Check thickness of lining.
Disc Rotor Inner Diameter Inspection
• Check inner diameter insi de drum area of disc rotor.
Other Inspections
• Check shoe sliding surface on back plate for excessive wear and damage.
• Check anti-rattle pins for excessive wear and corrosion.
• Check return springs for sagging.
• Check adjuster for rough operation.
• When disassembling adjuster, apply PBC (Poly Butyl Cuprysil) grease or equivalent to the threads.
• Check either visually or with a vernier caliper to see if there is any excessive wear, cracks, or damage inside
drum area of disc rotor.
INSTALLATION
Installation is in the reverse order of removal.
• Refer to PB-9, "
Removal and Installation" and apply brake grease to the specified points during assembly.
• Assemble adjuster so that threaded part expands when rotating it in the direction shown by the arrow.
• Shorten adjuster by rotating it.
NOTE:
After replacing brake shoes or disc rotors, or if brakes do not func-
tion well, perform break-in operation as follows.
1. Adjust parking brake pedal stroke. Refer to PB-5, "
On-Vehicle
Service".
CAUTION:
• To prevent lining from getting too hot, allow a cool off period
of approximately 5 minutes after every break-in operation.
• Do not perform excessive break-in operations, because it may
cause uneven or early wear of lining.
2. Perform parking brake burnishing operation by driving the vehicle forward under the following conditions:
3. After burnishing operation, check pedal stroke of parki ng brake. Readjust if it is no longer at the specified
stroke. Refer to PB-5, "
On-Vehicle Service".
Standard thickness “A” : 3.79
± 0.21 mm
(0.149 ± 0.008 in)
Wear limit thickness “A” : 0.5 mm (0.020 in)
SBR021A
Standard inner
diameter : 205
± 0.13 mm (8.07 ± 0.01 in)
Wear limit of in-
ner diameter : 205.7 mm (8.10 in)
SBR768A
SFIA0153E
• Vehicle speed at 40 km/h (25 MPH)
• Parking brake operating force of 196 N (20.0 kg-f, 44.1 lb-f) set
• For a period of 30 seconds
Revision: March 2010
2008 QX56
Page 2733 of 4083
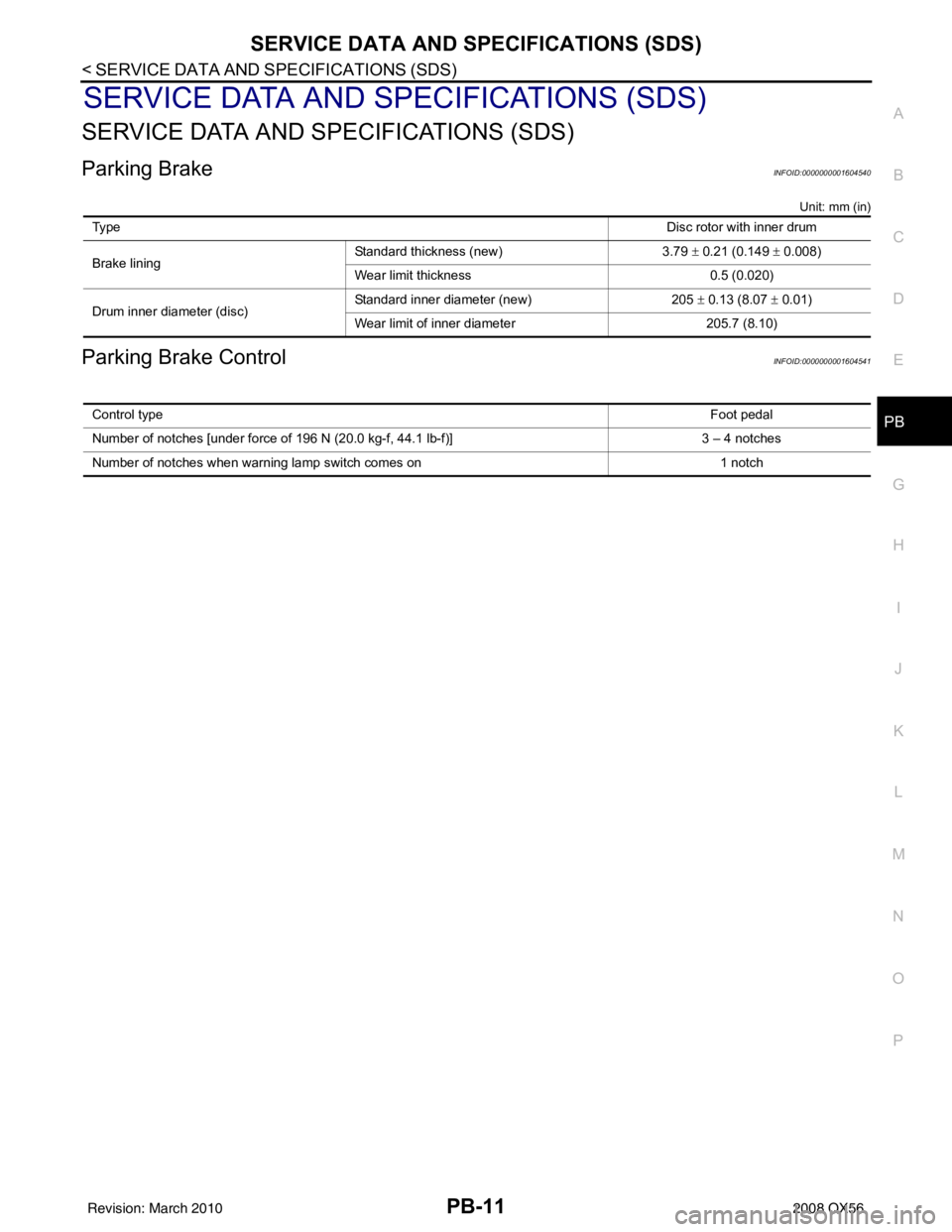
SERVICE DATA AND SPECIFICATIONS (SDS)PB-11
< SERVICE DATA AND SPECIFICATIONS (SDS)
C
DE
G H
I
J
K L
M A
B
PB
N
O P
SERVICE DATA AND SPECIFICATIONS (SDS)
SERVICE DATA AND SPECIFICATIONS (SDS)
Parking BrakeINFOID:0000000001604540
Unit: mm (in)
Parking Brake ControlINFOID:0000000001604541
Ty p e Disc rotor with inner drum
Brake lining Standard thickness (new)
3.79 ± 0.21 (0.149 ± 0.008)
Wear limit thickness 0.5 (0.020)
Drum inner diameter (disc) Standard inner diameter (new)
205 ± 0.13 (8.07 ± 0.01)
Wear limit of inner diameter 205.7 (8.10)
Control type Foot pedal
Number of notches [under force of 196 N (20.0 kg-f, 44.1 lb-f)] 3 – 4 notches
Number of notches when warning lamp switch comes on 1 notch
Revision: March 2010 2008 QX56
Page 2734 of 4083
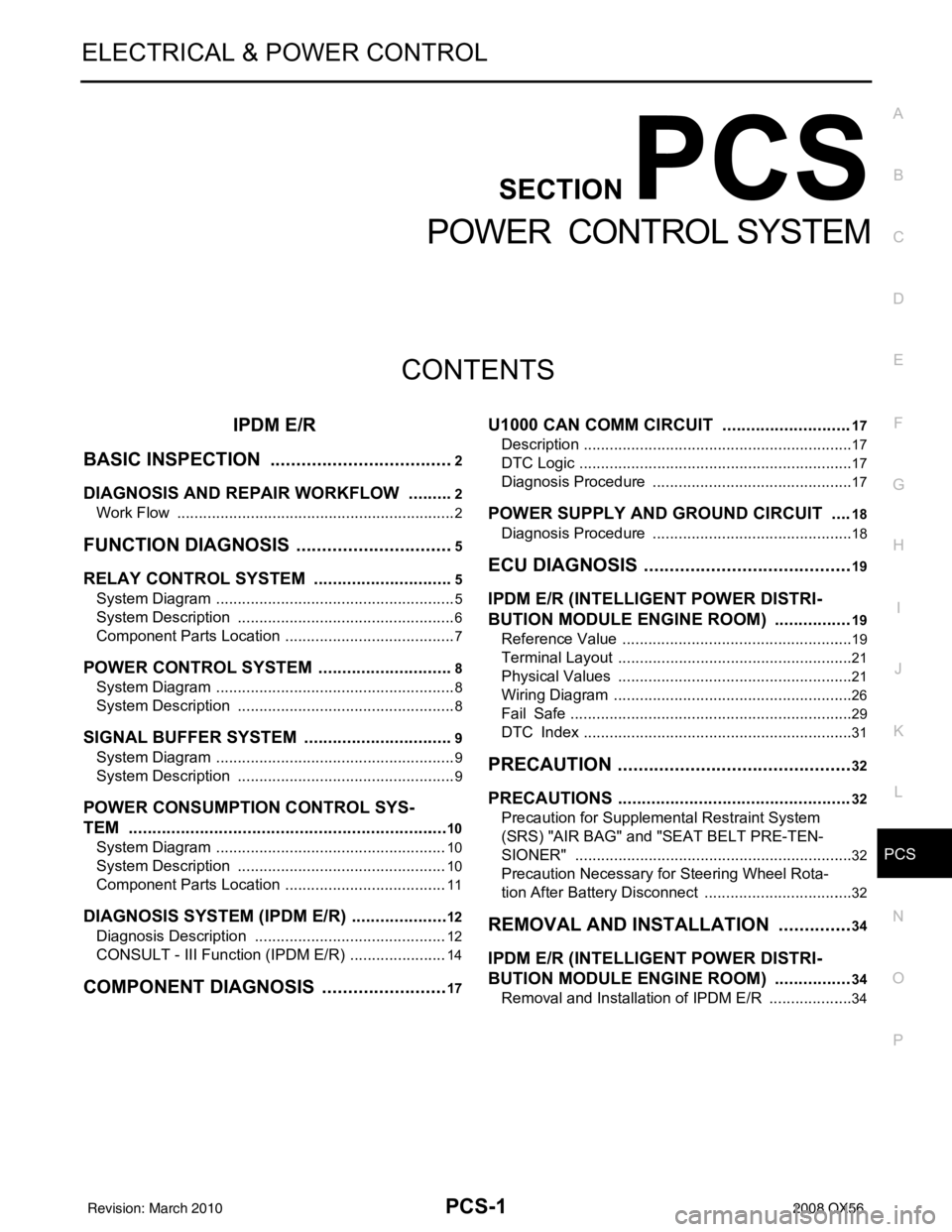
PCS
PCS-1
ELECTRICAL & POWER CONTROL
C
DE
F
G H
I
J
K L
B
SECTION PCS
A
O P
N
CONTENTS
POWER CONTROL SYSTEM
IPDM E/R
BASIC INSPECTION ....... .............................
2
DIAGNOSIS AND REPAIR WORKFLOW ..... .....2
Work Flow ........................................................... ......2
FUNCTION DIAGNOSIS ...............................5
RELAY CONTROL SYSTEM ......................... .....5
System Diagram .................................................. ......5
System Description ...................................................6
Component Parts Location ........................................7
POWER CONTROL SYSTEM .............................8
System Diagram .................................................. ......8
System Description ...................................................8
SIGNAL BUFFER SYSTEM ................................9
System Diagram .................................................. ......9
System Description ...................................................9
POWER CONSUMPTION CONTROL SYS-
TEM ....................................................................
10
System Diagram .................................................. ....10
System Description .................................................10
Component Parts Location ......................................11
DIAGNOSIS SYSTEM (IPDM E/R) .....................12
Diagnosis Description ......................................... ....12
CONSULT - III Function (IPDM E/R) .......................14
COMPONENT DIAGNOSIS .........................17
U1000 CAN COMM CIRCUIT ...........................17
Description ........................................................... ....17
DTC Logic ................................................................17
Diagnosis Procedure ...............................................17
POWER SUPPLY AND GROUND CIRCUIT ....18
Diagnosis Procedure ...............................................18
ECU DIAGNOSIS .........................................19
IPDM E/R (INTELLIGENT POWER DISTRI-
BUTION MODULE ENGINE ROOM) ................
19
Reference Value .................................................. ....19
Terminal Layout .......................................................21
Physical Values ................................................... ....21
Wiring Diagram ........................................................26
Fail Safe ..................................................................29
DTC Index ...............................................................31
PRECAUTION ..............................................32
PRECAUTIONS .................................................32
Precaution for Supplemental Restraint System
(SRS) "AIR BAG" and "SEAT BELT PRE-TEN-
SIONER" ............................................................. ....
32
Precaution Necessary for Steering Wheel Rota-
tion After Battery Disconnect ...................................
32
REMOVAL AND INSTALLATION ...............34
IPDM E/R (INTELLIGENT POWER DISTRI-
BUTION MODULE ENGINE ROOM) ................
34
Removal and Installation of IPDM E/R ................ ....34
Revision: March 2010 2008 QX56
Page 2735 of 4083
![INFINITI QX56 2008 Factory Service Manual PCS-2
< BASIC INSPECTION >[IPDM E/R]
DIAGNOSIS AND REPAIR WORKFLOW
BASIC INSPECTION
DIAGNOSIS AND REPAIR WORKFLOW
Work FlowINFOID:0000000004868608
OVERALL SEQUENCE
DETAILED FLOW
JMKIA0101GB
Revision: INFINITI QX56 2008 Factory Service Manual PCS-2
< BASIC INSPECTION >[IPDM E/R]
DIAGNOSIS AND REPAIR WORKFLOW
BASIC INSPECTION
DIAGNOSIS AND REPAIR WORKFLOW
Work FlowINFOID:0000000004868608
OVERALL SEQUENCE
DETAILED FLOW
JMKIA0101GB
Revision:](/img/42/57030/w960_57030-2734.png)
PCS-2
< BASIC INSPECTION >[IPDM E/R]
DIAGNOSIS AND REPAIR WORKFLOW
BASIC INSPECTION
DIAGNOSIS AND REPAIR WORKFLOW
Work FlowINFOID:0000000004868608
OVERALL SEQUENCE
DETAILED FLOW
JMKIA0101GB
Revision: March 2010
2008 QX56
Page 2736 of 4083
![INFINITI QX56 2008 Factory Service Manual PCS
DIAGNOSIS AND REPAIR WORKFLOWPCS-3
< BASIC INSPECTION > [IPDM E/R]
C
D
E
F
G H
I
J
K L
B A
O P
N
1. GET INFORMATION FOR SYMPTOM
Get the detailed information from the customer about the symptom (th INFINITI QX56 2008 Factory Service Manual PCS
DIAGNOSIS AND REPAIR WORKFLOWPCS-3
< BASIC INSPECTION > [IPDM E/R]
C
D
E
F
G H
I
J
K L
B A
O P
N
1. GET INFORMATION FOR SYMPTOM
Get the detailed information from the customer about the symptom (th](/img/42/57030/w960_57030-2735.png)
PCS
DIAGNOSIS AND REPAIR WORKFLOWPCS-3
< BASIC INSPECTION > [IPDM E/R]
C
D
E
F
G H
I
J
K L
B A
O P
N
1. GET INFORMATION FOR SYMPTOM
Get the detailed information from the customer about the symptom (the condition and the environment when
the incident/malfunction occurred).
>> GO TO 2
2. CHECK DTC
1. Check DTC.
2. Perform the following procedure if DTC is displayed.
- Record DTC and freeze frame data.
- Erase DTC.
- Study the relationship between the cause detected by DTC and the symptom described by the customer.
3. Check related service bulletins for information.
Is any symptom described and any DTC detected?
Symptom is described, DTC is displayed>>GO TO 3
Symptom is described, DTC is not displayed>>GO TO 4
Symptom is not described, DTC is displayed>>GO TO 5
3. CONFIRM THE SYMPTOM
Confirm the symptom described by the customer.
Connect CONSULT-III to the vehicle in “DATA MONI TOR” mode and check real time diagnosis results.
Verify relationship between the symptom and the condition when the symptom is detected.
>> GO TO 5
4. CONFIRM THE SYMPTOM
Confirm the symptom described by the customer.
Connect CONSULT-III to the vehicle in “DATA MONI TOR” mode and check real time diagnosis results.
Verify relationship between the symptom and the condition when the symptom is detected.
>> GO TO 6
5. PERFORM DTC CONFIRMATION PROCEDURE
Perform DTC Confirmation Procedure for the display ed DTC, and then check that DTC is detected again.
At this time, always connect CONSULT-III to the vehicle, and check diagnostic results in real time.
NOTE:
• Freeze frame data is useful if the DTC is not detected.
• Perform Component Function Check if DTC Confirmation Procedure is not included in Service Manual. This simplified check procedure is an effective alternat ive though DTC cannot be detected during this check.
If the result of Component Function Check is NG, it is the same as the detection of DTC by DTC Confirma-
tion Procedure.
Is DTC detected?
YES >> GO TO 8
NO >> Refer to GI-38, "
Intermittent Incident".
6. PERFORM BASIC INSPECTION
Perform a basic inspection of the IPDM E/R.
Inspection End>>GO TO 7
7. DETECT MALFUNCTIONING SYSTEM BY SYMPTOM
Detect malfunctioning system according to PCS-6, "
System Description" based on the confirmed symptom in
step 4, and determine the trouble diagnosis or der based on possible causes and symptom.
>> GO TO 8
8. DETECT MALFUNCTIONING PART BY DIAGNOSTIC PROCEDURE
Revision: March 2010 2008 QX56
Page 2737 of 4083
![INFINITI QX56 2008 Factory Service Manual PCS-4
< BASIC INSPECTION >[IPDM E/R]
DIAGNOSIS AND REPAIR WORKFLOW
Inspect according to Diagnostic Procedure of the system.
NOTE:
The Diagnostic Procedure described based on open circuit inspection. A INFINITI QX56 2008 Factory Service Manual PCS-4
< BASIC INSPECTION >[IPDM E/R]
DIAGNOSIS AND REPAIR WORKFLOW
Inspect according to Diagnostic Procedure of the system.
NOTE:
The Diagnostic Procedure described based on open circuit inspection. A](/img/42/57030/w960_57030-2736.png)
PCS-4
< BASIC INSPECTION >[IPDM E/R]
DIAGNOSIS AND REPAIR WORKFLOW
Inspect according to Diagnostic Procedure of the system.
NOTE:
The Diagnostic Procedure described based on open circuit inspection. A short circuit inspection is also
required for the circuit check in the Diagnostic Procedure.
Is malfunctioning part detected?
YES >> GO TO 9
NO >> Check voltage of related BCM terminals using CONSULT-III.
9. REPAIR OR REPLACE THE MALFUNCTIONING PART
1. Repair or replace the malfunctioning part.
2. Reconnect parts or connectors disconnected during Diagnostic Procedure again after repair and replace- ment.
3. Check DTC. If DTC is displayed, erase it.
>> GO TO 10
10. FINAL CHECK
When DTC was detected in step 2, perform DTC Confirmation Procedure or Component Function Check
again, and then check that the malfunction have been fully repaired.
When symptom was described from the customer, refer to confirmed symptom in step 3 or 4 and check that
the symptom is not detected.
Is the inspection result normal?
YES >> Inspection End.
NO (DTC is detected)>>GO TO 8
NO (Symptom remains)>>GO TO 6
Revision: March 2010 2008 QX56
Page 2738 of 4083
![INFINITI QX56 2008 Factory Service Manual PCS
RELAY CONTROL SYSTEMPCS-5
< FUNCTION DIAGNOSIS > [IPDM E/R]
C
D
E
F
G H
I
J
K L
B A
O P
N
FUNCTION DIAGNOSIS
RELAY CONTROL SYSTEM
System DiagramINFOID:0000000001696480
AWMIA1109GB
Revision: March INFINITI QX56 2008 Factory Service Manual PCS
RELAY CONTROL SYSTEMPCS-5
< FUNCTION DIAGNOSIS > [IPDM E/R]
C
D
E
F
G H
I
J
K L
B A
O P
N
FUNCTION DIAGNOSIS
RELAY CONTROL SYSTEM
System DiagramINFOID:0000000001696480
AWMIA1109GB
Revision: March](/img/42/57030/w960_57030-2737.png)
PCS
RELAY CONTROL SYSTEMPCS-5
< FUNCTION DIAGNOSIS > [IPDM E/R]
C
D
E
F
G H
I
J
K L
B A
O P
N
FUNCTION DIAGNOSIS
RELAY CONTROL SYSTEM
System DiagramINFOID:0000000001696480
AWMIA1109GB
Revision: March 2010
2008 QX56
Page 2739 of 4083
![INFINITI QX56 2008 Factory Service Manual PCS-6
< FUNCTION DIAGNOSIS >[IPDM E/R]
RELAY CONTROL SYSTEM
System Description
INFOID:0000000001696481
IPDM E/R activates the internal cont rol circuit to perform the relay ON-OFF control according to INFINITI QX56 2008 Factory Service Manual PCS-6
< FUNCTION DIAGNOSIS >[IPDM E/R]
RELAY CONTROL SYSTEM
System Description
INFOID:0000000001696481
IPDM E/R activates the internal cont rol circuit to perform the relay ON-OFF control according to](/img/42/57030/w960_57030-2738.png)
PCS-6
< FUNCTION DIAGNOSIS >[IPDM E/R]
RELAY CONTROL SYSTEM
System Description
INFOID:0000000001696481
IPDM E/R activates the internal cont rol circuit to perform the relay ON-OFF control according to the input sig-
nals from various sensors and the request signals received from control units via CAN communication.
CAUTION:
IPDM E/R integrated relays cannot be removed.
Control relay Input/outputTransmit unitControl partReference
page
Front fog lamp relay Front fog lamp request signal BCM (CAN) Front fog lampsEXL-15
• Headlamp high relay
• Headlamp low relay • High beam request signal
• Low beam request signal
BCM (CAN)• Headlamp high
• Headlamp lowEXL-7
EXL-7
Tail lamp relay
Position light request signal BCM (CAN) •Parking lamps
• License plate lamps
• Tail lamps
• Trailer tow relay
• Illumination systemEXL-18
• Front wiper relay
• Front wiper high relay
Front wiper request signal BCM (CAN)
Front wiper motorWW-4
Rear window defogger re-
lay Rear window defogger re-
quest signal
BCM (CAN)
Rear window defoggerWW-8
A/C relay A/C request signal •BCM (CAN)
•ECM (CAN)
A/C compressor
HAC-20
Starter relay Ignition switch START signal TCM Starter motorSTR-8
Cooling fan relay Cooling fan request signal ECM (CAN) Cooling fan relayEC-36
Heated mirror relay Heate d mirror request signal BCM (CAN) Door mirrors DEF-4
ECM relayECM relay control signal ECM (CAN) ECM relayEC-21
Throttle control motor relay Throttle control motor control
signal ECM (CAN)
Throttle contro
l motor re-
lay EC-28
Fuel pump relay
Fuel pump request signal ECM (CAN) Fuel pumpEC-28
Ignition relay Ignition switch ON signal Ignition switch Ignition relayEC-31
Revision: March 2010 2008 QX56
Page 2740 of 4083
![INFINITI QX56 2008 Factory Service Manual PCS
RELAY CONTROL SYSTEMPCS-7
< FUNCTION DIAGNOSIS > [IPDM E/R]
C
D
E
F
G H
I
J
K L
B A
O P
N
Component Parts LocationINFOID:0000000001696482
1. IPDM E/R E118, E119, E120, E121,
E122, E123, E124
ALMI INFINITI QX56 2008 Factory Service Manual PCS
RELAY CONTROL SYSTEMPCS-7
< FUNCTION DIAGNOSIS > [IPDM E/R]
C
D
E
F
G H
I
J
K L
B A
O P
N
Component Parts LocationINFOID:0000000001696482
1. IPDM E/R E118, E119, E120, E121,
E122, E123, E124
ALMI](/img/42/57030/w960_57030-2739.png)
PCS
RELAY CONTROL SYSTEMPCS-7
< FUNCTION DIAGNOSIS > [IPDM E/R]
C
D
E
F
G H
I
J
K L
B A
O P
N
Component Parts LocationINFOID:0000000001696482
1. IPDM E/R E118, E119, E120, E121,
E122, E123, E124
ALMIA0341ZZ
Revision: March 2010 2008 QX56