wheel INFINITI QX56 2009 Factory Service Manual
[x] Cancel search | Manufacturer: INFINITI, Model Year: 2009, Model line: QX56, Model: INFINITI QX56 2009Pages: 4171, PDF Size: 84.65 MB
Page 2142 of 4171
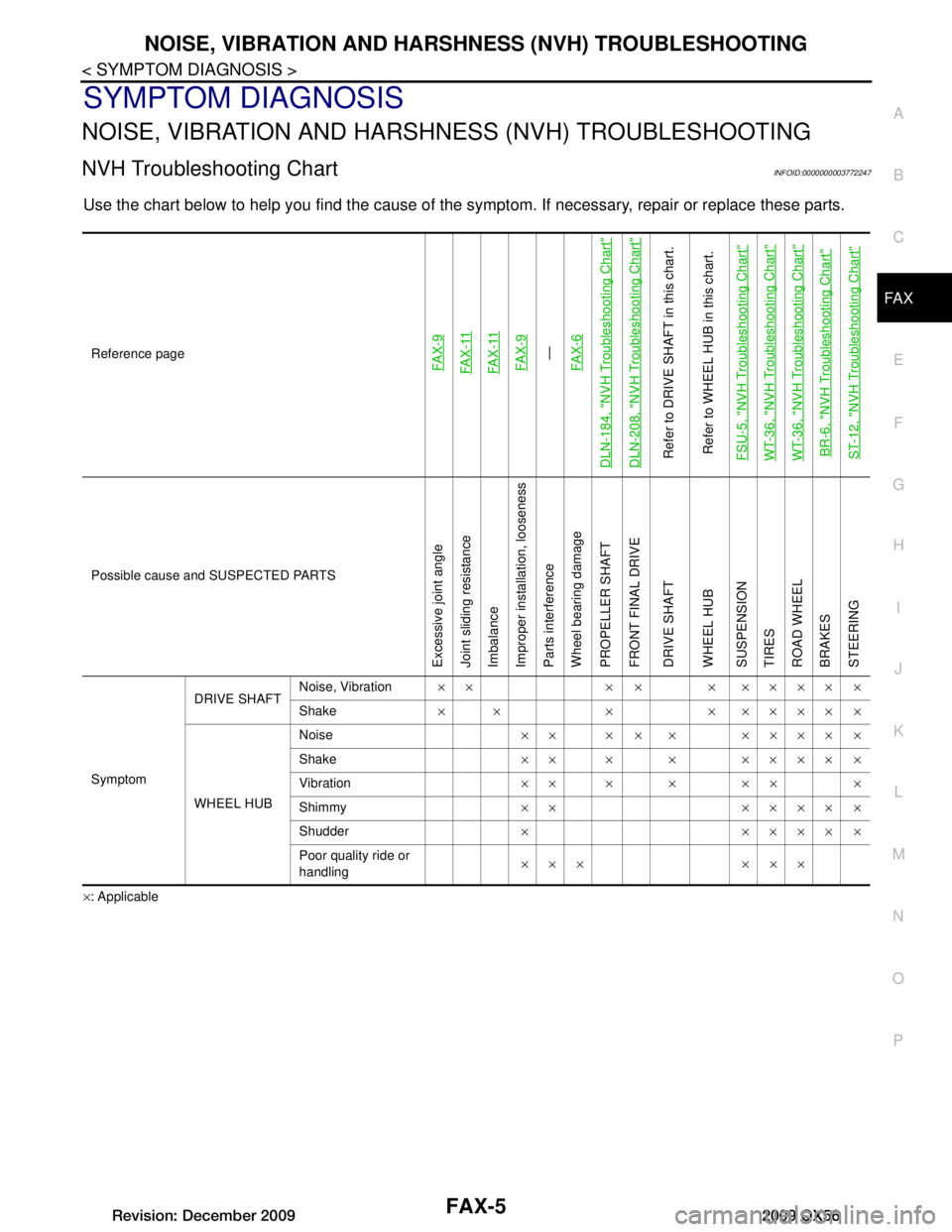
NOISE, VIBRATION AND HARSHNESS (NVH) TROUBLESHOOTINGFAX-5
< SYMPTOM DIAGNOSIS >
CEF
G H
I
J
K L
M A
B
FA X
N
O P
SYMPTOM DIAGNOSIS
NOISE, VIBRATION AND HARSHN ESS (NVH) TROUBLESHOOTING
NVH Troubleshooting ChartINFOID:0000000003772247
Use the chart below to help you find t he cause of the symptom. If necessary, repair or replace these parts.
×: ApplicableReference page
FA X - 9FA X - 11FA X - 11FA X - 9—
FA X - 6
DLN-184, "NVH Troubleshooting Chart"DLN-208, "NVH Troubleshooting Chart"Refer to DRIVE SHAFT in this chart.
Refer to WHEEL HUB in this chart.
FSU-5, "NVH Troubleshooting Chart"WT-36, "NVH Troubleshooting Chart"WT-36, "NVH Troubleshooting Chart"BR-6, "NVH Troubleshooting Chart"ST-12, "NVH Troubleshooting Chart"
Possible cause and SUSPECTED PARTS
Excessive joint angle
Joint sliding resistance
Imbalance
Improper installation, looseness
Parts interference
Wheel bearing damage
PROPELLER SHAFT
FRONT FINAL DRIVE
DRIVE SHAFT
WHEEL HUB
SUSPENSION
TIRES
ROAD WHEEL
BRAKES
STEERING
Symptom DRIVE SHAFT
Noise, Vibration
×× × × × ×××× ×
Shake × × × × ×××× ×
WHEEL HUB Noise
×× × × × ×××× ×
Shake ×× × × ×××× ×
Vibration ×× × × ×× ×
Shimmy ×× ×××× ×
Shudder ××××××
Poor quality ride or
handling ××× ×××
Revision: December 20092009 QX56
Page 2143 of 4171
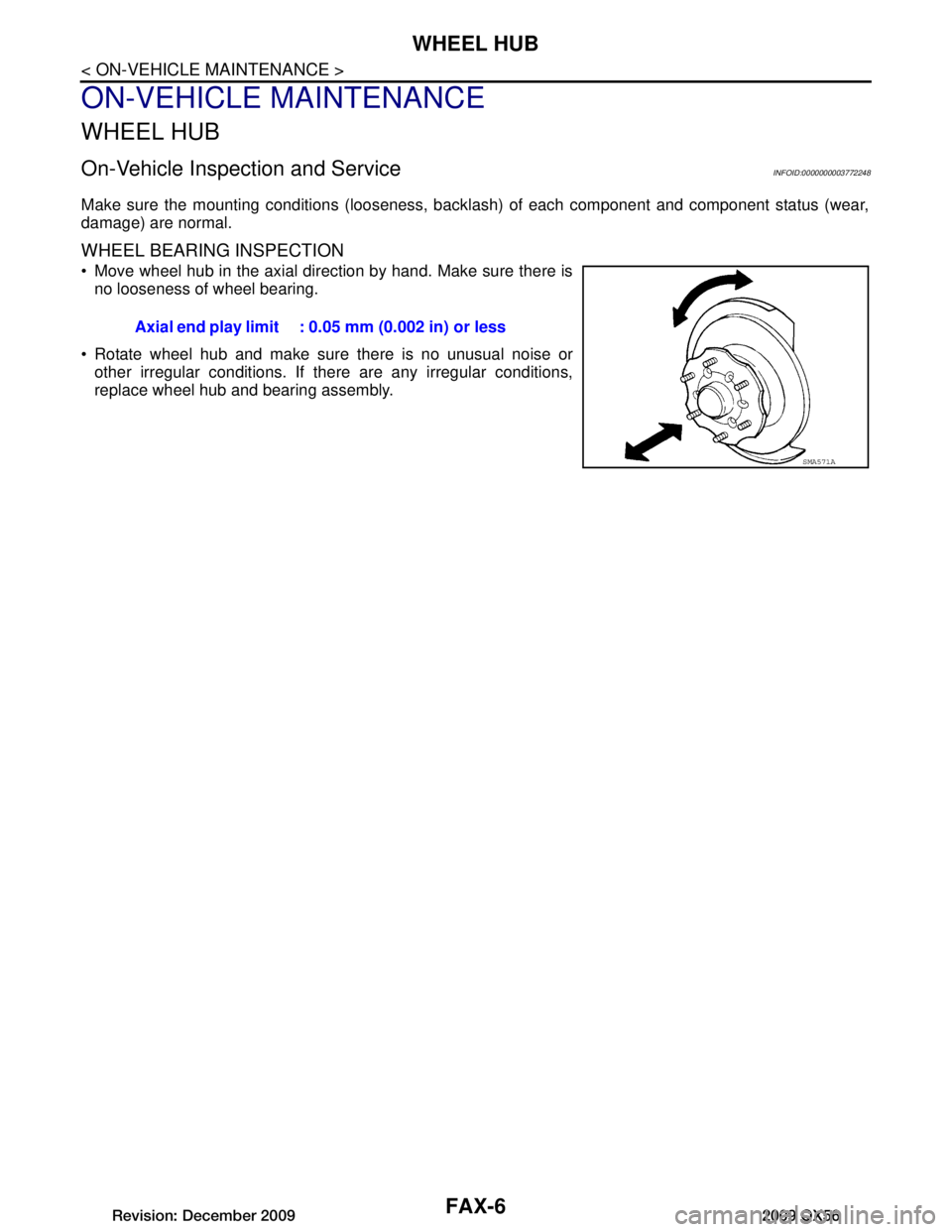
FAX-6
< ON-VEHICLE MAINTENANCE >
WHEEL HUB
ON-VEHICLE MAINTENANCE
WHEEL HUB
On-Vehicle Inspection and ServiceINFOID:0000000003772248
Make sure the mounting conditions (looseness, backlash) of each component and component status (wear,
damage) are normal.
WHEEL BEARING INSPECTION
Move wheel hub in the axial direction by hand. Make sure there is
no looseness of wheel bearing.
Rotate wheel hub and make sure there is no unusual noise or other irregular conditions. If there are any irregular conditions,
replace wheel hub and bearing assembly. Axial end play limit : 0.05 mm (0.002 in) or less
SMA571A
Revision: December 20092009 QX56
Page 2144 of 4171
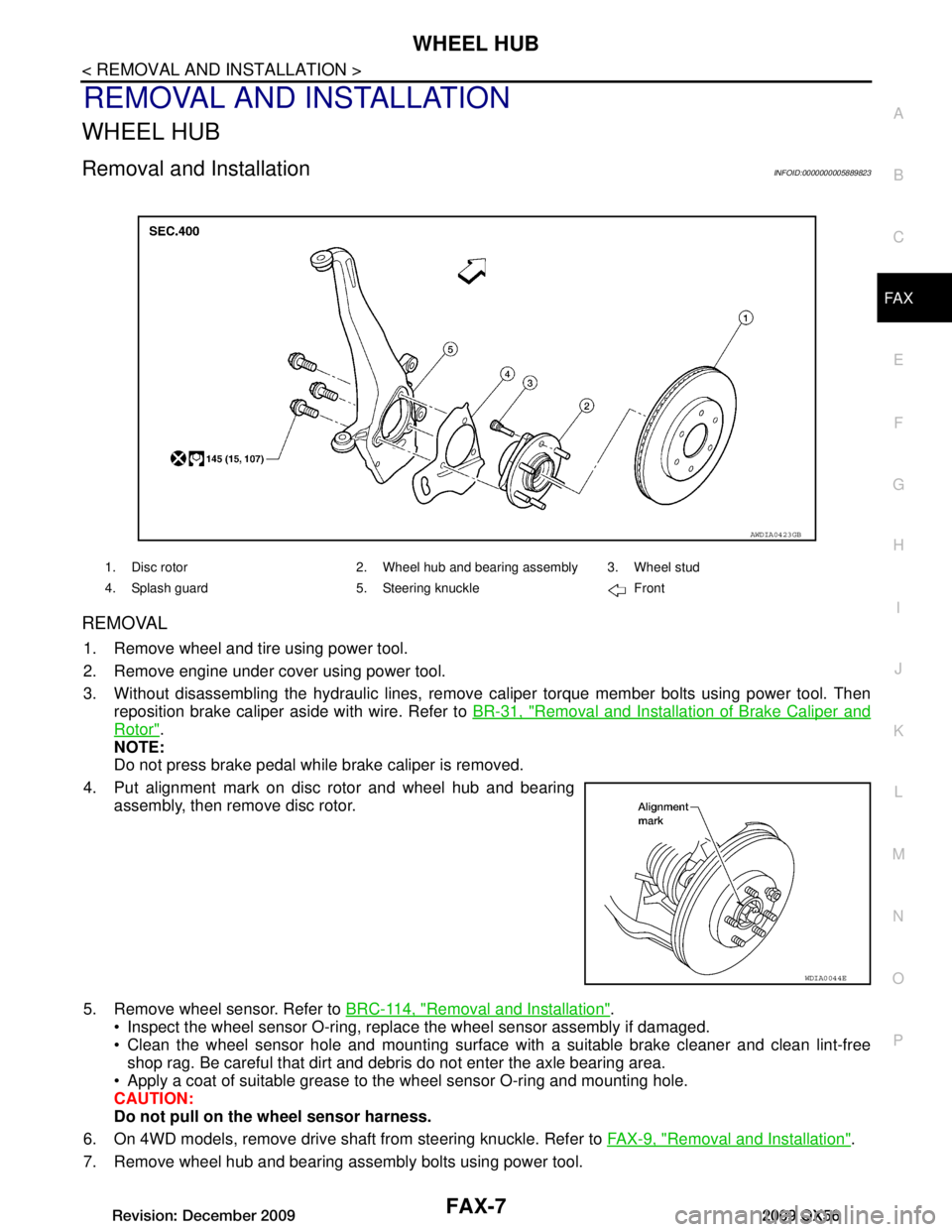
WHEEL HUBFAX-7
< REMOVAL AND INSTALLATION >
CEF
G H
I
J
K L
M A
B
FA X
N
O P
REMOVAL AND INSTALLATION
WHEEL HUB
Removal and InstallationINFOID:0000000005889823
REMOVAL
1. Remove wheel and tire using power tool.
2. Remove engine under cover using power tool.
3. Without disassembling the hydraulic lines, remove caliper torque member bolts using power tool. Then reposition brake caliper aside with wire. Refer to BR-31, "Removal and Installation of Brake Caliper and
Rotor".
NOTE:
Do not press brake pedal while brake caliper is removed.
4. Put alignment mark on disc rotor and wheel hub and bearing assembly, then remove disc rotor.
5. Remove wheel sensor. Refer to BRC-114, "Removal and Installation"
.
Inspect the wheel sensor O-ring, replac e the wheel sensor assembly if damaged.
Clean the wheel sensor hole and mounting surface with a suitable brake cleaner and clean lint-free shop rag. Be careful that dirt and debr is do not enter the axle bearing area.
Apply a coat of suitable grease to t he wheel sensor O-ring and mounting hole.
CAUTION:
Do not pull on th e wheel sensor harness.
6. On 4WD models, remove drive shaft from steering knuckle. Refer to FAX-9, "Removal and Installation"
.
7. Remove wheel hub and bearing assembly bolts using power tool.
1. Disc rotor 2. Wheel hub and bearing assembly 3. Wheel stud
4. Splash guard 5. Steering knuckle Front
AWDIA0423GB
WDIA0044E
Revision: December 20092009 QX56
Page 2145 of 4171

FAX-8
< REMOVAL AND INSTALLATION >
WHEEL HUB
8. Remove splash guard and wheel hub and bearing assembly from steering knuckle.
INSPECTION AFTER REMOVAL
Check for deformity, cracks and damage on each part, replace if necessary.
INSTALLATION
Installation is in the reverse order of removal.
Use new bolts when installing the wheel hub and bearing assembly.
Tighten drive shaft nut to specification. Refer to FAX-9, "Removal and Installation"
.
When installing disc rotor on wheel hub and bearing assembly, position the disc rotor according to alignment mark.
(When not using the alignment mark, refer to BR-7, "DISC ROTOR
: Inspection".)
When installing wheel and tire. Refer to WT-41, "Adjustment"
.
WDIA0044E
Revision: December 20092009 QX56
Page 2146 of 4171
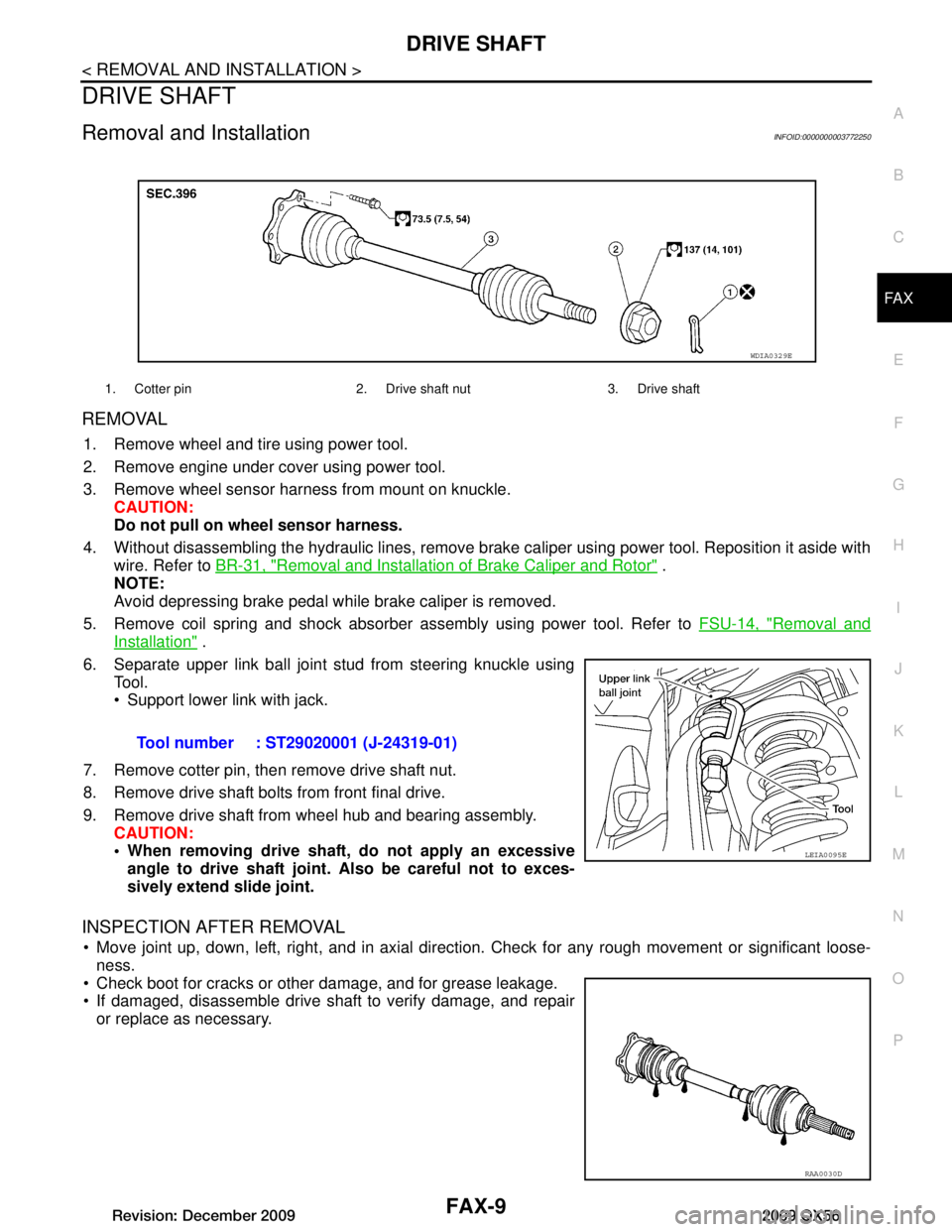
DRIVE SHAFTFAX-9
< REMOVAL AND INSTALLATION >
CEF
G H
I
J
K L
M A
B
FA X
N
O P
DRIVE SHAFT
Removal and InstallationINFOID:0000000003772250
REMOVAL
1. Remove wheel and tire using power tool.
2. Remove engine under cover using power tool.
3. Remove wheel sensor harness from mount on knuckle. CAUTION:
Do not pull on wheel sensor harness.
4. Without disassembling the hydraulic lines, remove brake caliper using power tool. Reposition it aside with wire. Refer to BR-31, "Removal and Installation of Brake Caliper and Rotor"
.
NOTE:
Avoid depressing brake pedal while brake caliper is removed.
5. Remove coil spring and shock absorber assembly using power tool. Refer to FSU-14, "Removal and
Installation" .
6. Separate upper link ball joint stud from steering knuckle using Tool.
Support lower link with jack.
7. Remove cotter pin, then remove drive shaft nut.
8. Remove drive shaft bolts from front final drive.
9. Remove drive shaft from wheel hub and bearing assembly. CAUTION:
When removing drive shaft, do not apply an excessiveangle to drive shaft joint. Also be careful not to exces-
sively extend slide joint.
INSPECTION AFTER REMOVAL
Move joint up, down, left, right, and in axial directi on. Check for any rough movement or significant loose-
ness.
Check boot for cracks or other damage, and for grease leakage.
If damaged, disassemble drive shaft to verify damage, and repair or replace as necessary.
1. Cotter pin 2. Drive shaft nut 3. Drive shaft
WDIA0329E
Tool number : ST29020001 (J-24319-01)
LEIA0095E
RAA0030D
Revision: December 20092009 QX56
Page 2147 of 4171
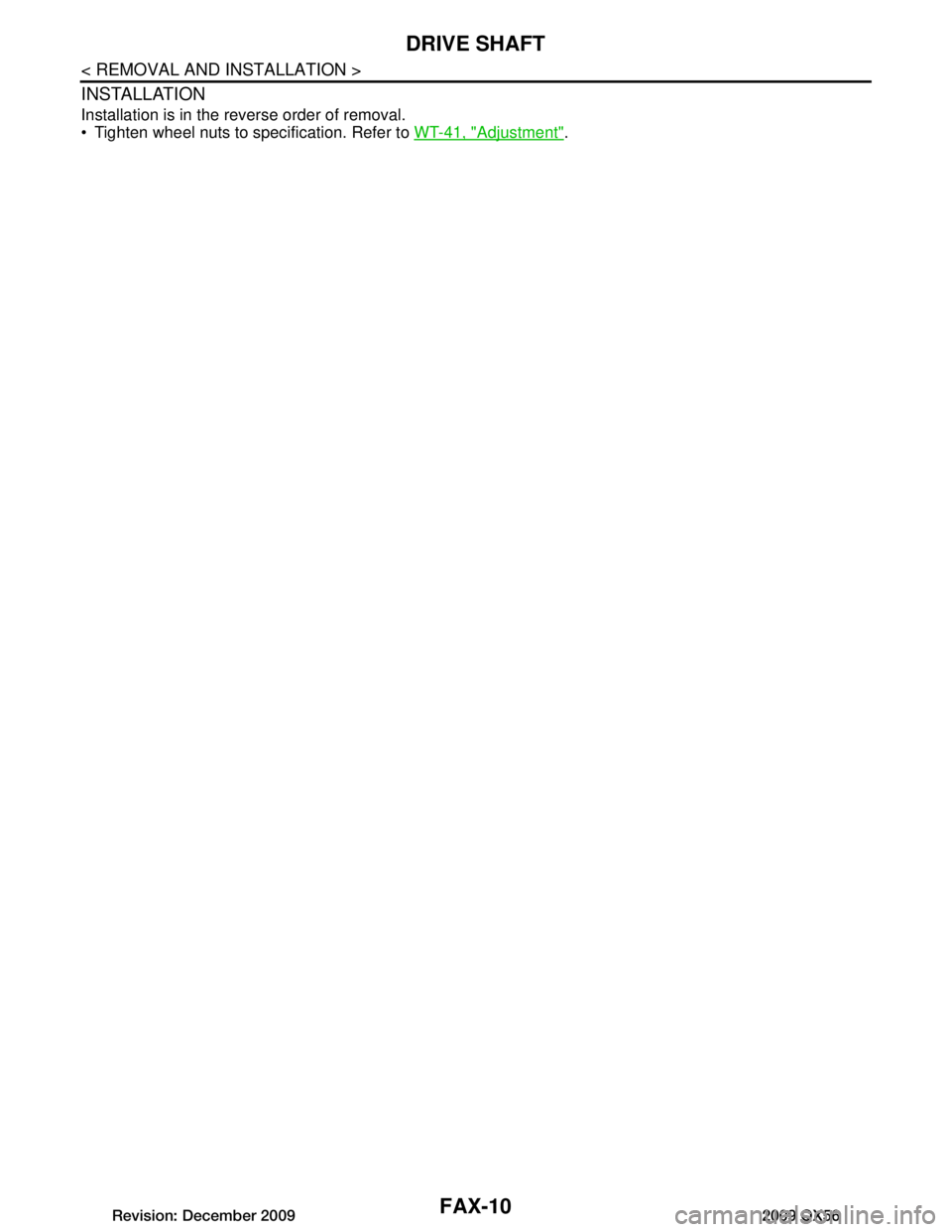
FAX-10
< REMOVAL AND INSTALLATION >
DRIVE SHAFT
INSTALLATION
Installation is in the reverse order of removal.
Tighten wheel nuts to specification. Refer to WT-41, "Adjustment"
.
Revision: December 20092009 QX56
Page 2149 of 4171
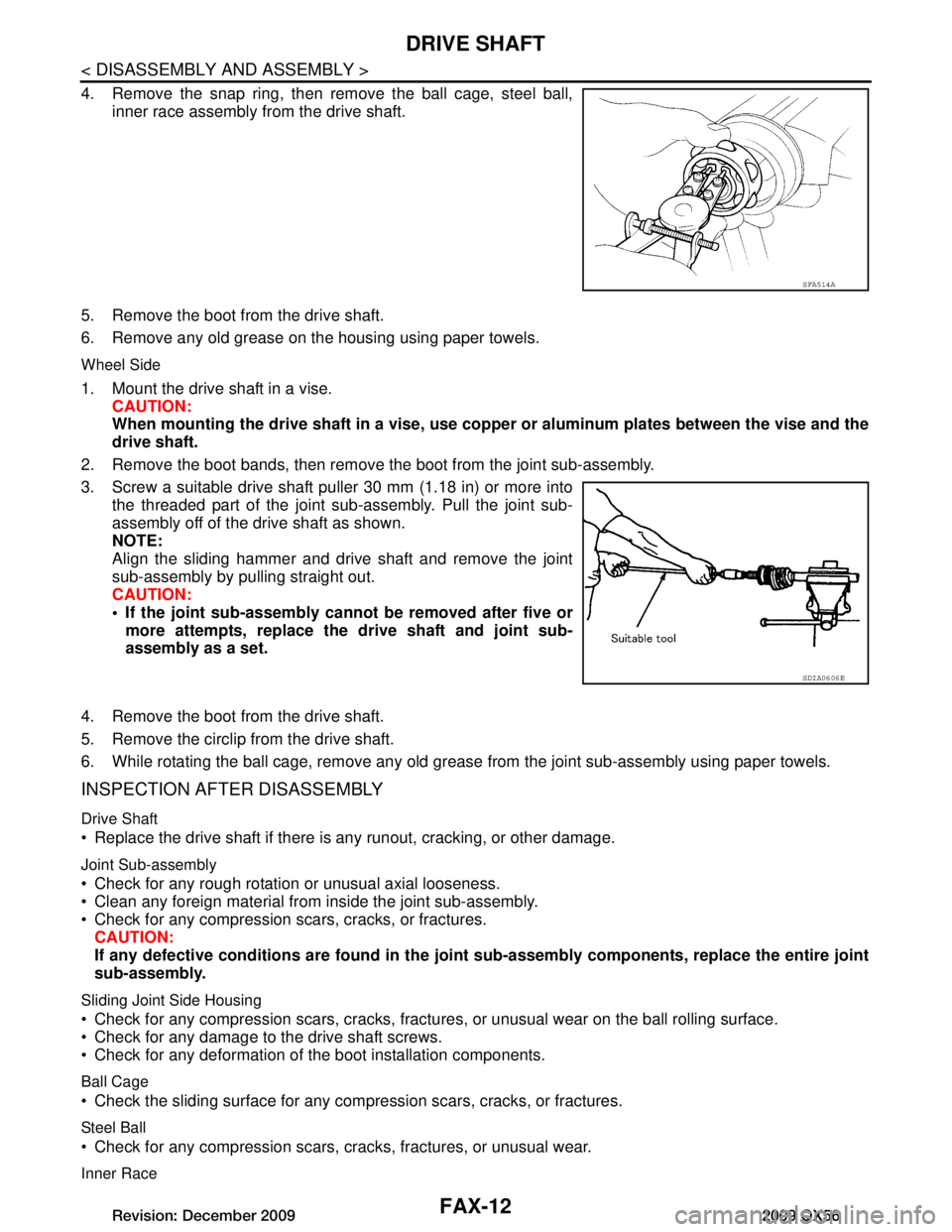
FAX-12
< DISASSEMBLY AND ASSEMBLY >
DRIVE SHAFT
4. Remove the snap ring, then remove the ball cage, steel ball,inner race assembly from the drive shaft.
5. Remove the boot from the drive shaft.
6. Remove any old grease on the housing using paper towels.
Wheel Side
1. Mount the drive shaft in a vise. CAUTION:
When mounting the drive shaft in a vise, use copp er or aluminum plates between the vise and the
drive shaft.
2. Remove the boot bands, then remove the boot from the joint sub-assembly.
3. Screw a suitable drive shaft puller 30 mm (1.18 in) or more into the threaded part of the joint sub-assembly. Pull the joint sub-
assembly off of the drive shaft as shown.
NOTE:
Align the sliding hammer and drive shaft and remove the joint
sub-assembly by pulling straight out.
CAUTION:
If the joint sub-assembly cannot be removed after five ormore attempts, replace the drive shaft and joint sub-
assembly as a set.
4. Remove the boot from the drive shaft.
5. Remove the circlip from the drive shaft.
6. While rotating the ball cage, remove any old grease from the joint sub-assembly using paper towels.
INSPECTION AFTER DISASSEMBLY
Drive Shaft
Replace the drive shaft if there is any runout, cracking, or other damage.
Joint Sub-assembly
Check for any rough rotation or unusual axial looseness.
Clean any foreign material from inside the joint sub-assembly.
Check for any compression scars, cracks, or fractures.
CAUTION:
If any defective conditions are found in the joint sub-assembly comp onents, replace the entire joint
sub-assembly.
Sliding Joint Side Housing
Check for any compression scars, cracks, fracture s, or unusual wear on the ball rolling surface.
Check for any damage to the drive shaft screws.
Check for any deformation of the boot installation components.
Ball Cage
Check the sliding surface for any compression scars, cracks, or fractures.
Steel Ball
Check for any compression scars, cr acks, fractures, or unusual wear.
Inner Race
SFA514A
SDIA0606E
Revision: December 20092009 QX56
Page 2151 of 4171
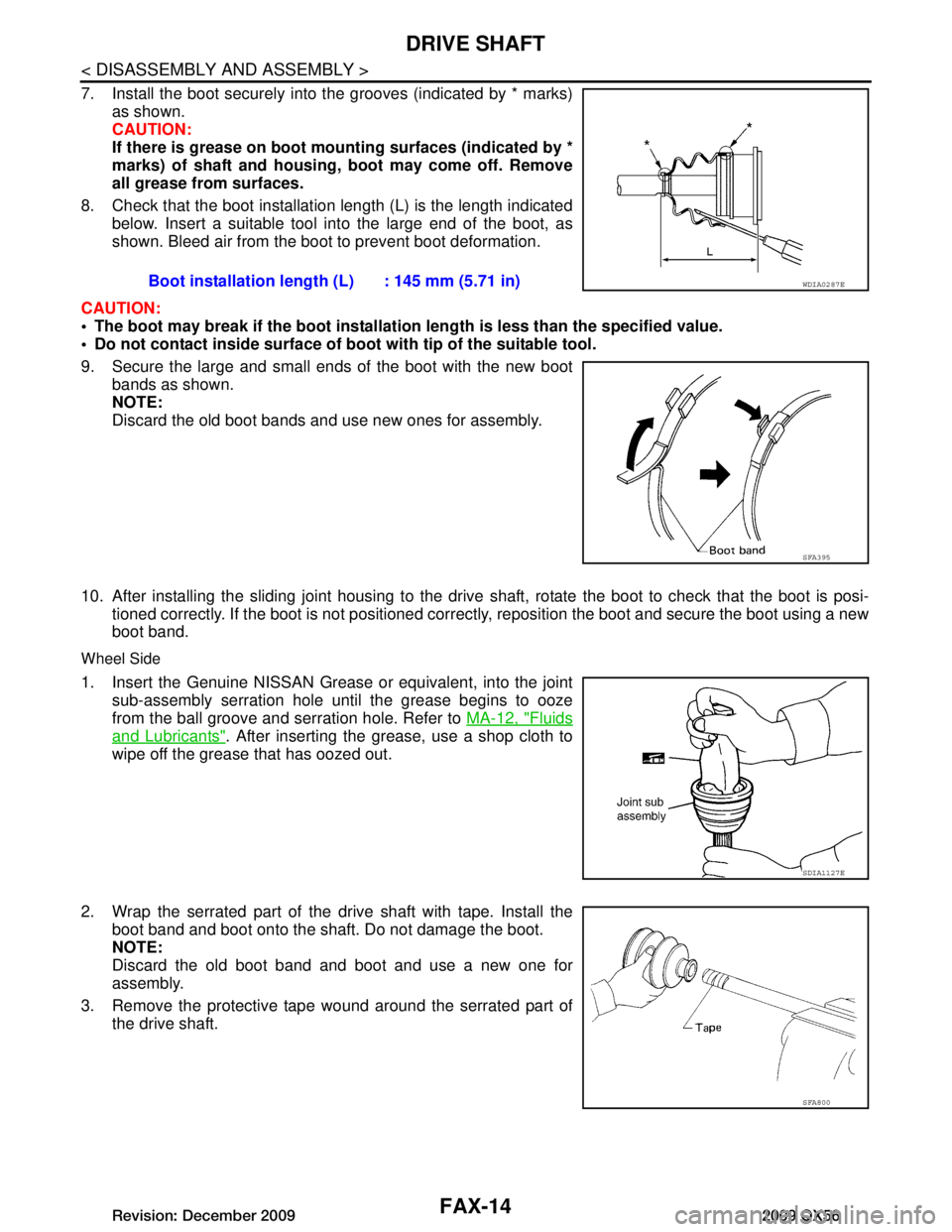
FAX-14
< DISASSEMBLY AND ASSEMBLY >
DRIVE SHAFT
7. Install the boot securely into the grooves (indicated by * marks)as shown.
CAUTION:
If there is grease on boot mounting surfaces (indicated by *
marks) of shaft and housing, boot may come off. Remove
all grease from surfaces.
8. Check that the boot installation length (L) is the length indicated below. Insert a suitable tool into the large end of the boot, as
shown. Bleed air from the boot to prevent boot deformation.
CAUTION:
The boot may break if the boot installati on length is less than the specified value.
Do not contact inside surface of boot with tip of the suitable tool.
9. Secure the large and small ends of the boot with the new boot bands as shown.
NOTE:
Discard the old boot bands and use new ones for assembly.
10. After installing the sliding joint housing to the drive shaft, rotate the boot to check that the boot is posi-
tioned correctly. If the boot is not positioned correctly , reposition the boot and secure the boot using a new
boot band.
Wheel Side
1. Insert the Genuine NISSAN Grease or equivalent, into the joint
sub-assembly serration hole until the grease begins to ooze
from the ball groove and serration hole. Refer to MA-12, "Fluids
and Lubricants". After inserting the grease, use a shop cloth to
wipe off the grease that has oozed out.
2. Wrap the serrated part of the drive shaft with tape. Install the boot band and boot onto the shaft. Do not damage the boot.
NOTE:
Discard the old boot band and boot and use a new one for
assembly.
3. Remove the protective tape wound around the serrated part of the drive shaft. Boot installation leng
th (L) : 145 mm (5.71 in)
WDIA0287E
SFA395
SDIA1127E
SFA800
Revision: December 20092009 QX56
Page 2153 of 4171
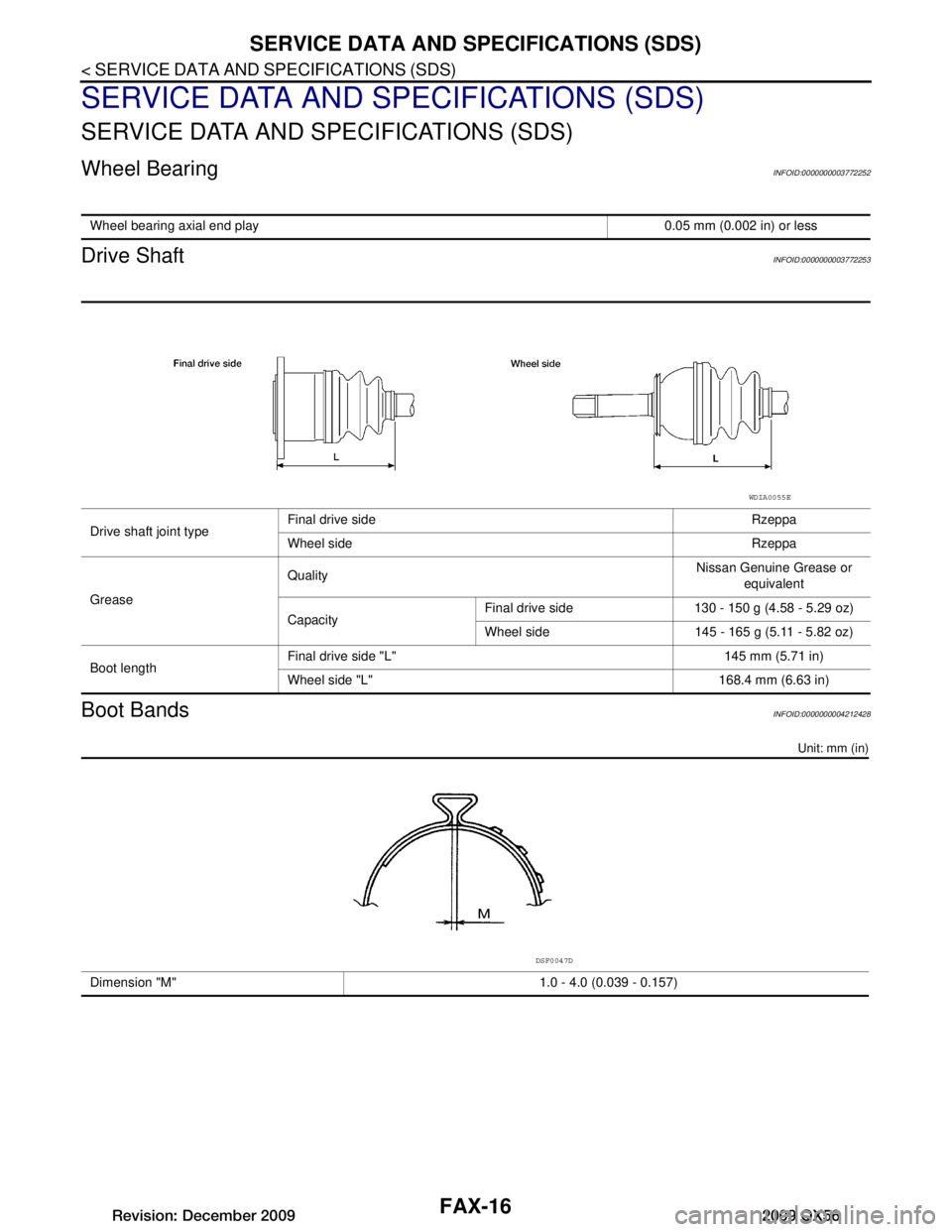
FAX-16
< SERVICE DATA AND SPECIFICATIONS (SDS)
SERVICE DATA AND SPECIFICATIONS (SDS)
SERVICE DATA AND SPECIFICATIONS (SDS)
SERVICE DATA AND SPECIFICATIONS (SDS)
Wheel BearingINFOID:0000000003772252
Drive ShaftINFOID:0000000003772253
Boot BandsINFOID:0000000004212428
Unit: mm (in)
Wheel bearing axial end play 0.05 mm (0.002 in) or less
Drive shaft joint typeFinal drive side Rzeppa
Wheel side Rzeppa
Grease Quality
Nissan Genuine Grease or
equivalent
Capacity Final drive side 130 - 150 g (4.58 - 5.29 oz)
Wheel side 145 - 165 g (5.11 - 5.82 oz)
Boot length Final drive side "L" 145 mm (5.71 in)
Wheel side "L" 168.4 mm (6.63 in)
WDIA0055E
Dimension "M" 1.0 - 4.0 (0.039 - 0.157)
DSF0047D
Revision: December 20092009 QX56
Page 2154 of 4171
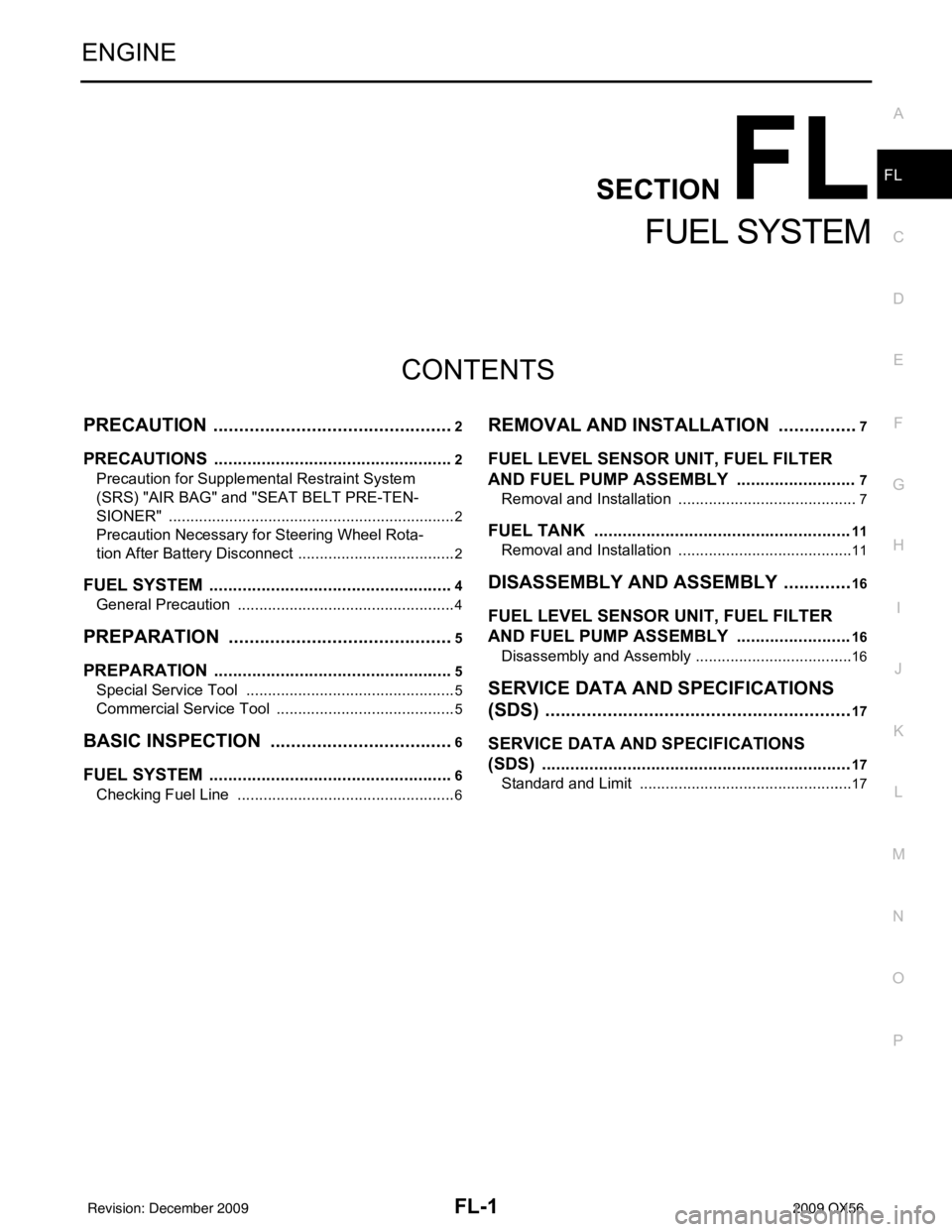
FL-1
ENGINE
C
DE
F
G H
I
J
K L
M
SECTION FL
A
FL
N
O P
CONTENTS
FUEL SYSTEM
PRECAUTION ....... ........................................2
PRECAUTIONS .............................................. .....2
Precaution for Supplemental Restraint System
(SRS) "AIR BAG" and "SEAT BELT PRE-TEN-
SIONER" ............................................................. ......
2
Precaution Necessary for Steering Wheel Rota-
tion After Battery Disconnect ............................... ......
2
FUEL SYSTEM ....................................................4
General Precaution ............................................. ......4
PREPARATION ............................................5
PREPARATION .............................................. .....5
Special Service Tool ........................................... ......5
Commercial Service Tool ..........................................5
BASIC INSPECTION ....................................6
FUEL SYSTEM ............................................... .....6
Checking Fuel Line ............................................. ......6
REMOVAL AND INSTALLATION ................7
FUEL LEVEL SENSOR UNIT, FUEL FILTER
AND FUEL PUMP ASSEMBLY .........................
7
Removal and Installation ..................................... .....7
FUEL TANK ......................................................11
Removal and Installation ..................................... ....11
DISASSEMBLY AND ASSEMBLY ..............16
FUEL LEVEL SENSOR UNIT, FUEL FILTER
AND FUEL PUMP ASSEMBLY ........................
16
Disassembly and Assembly ................................. ....16
SERVICE DATA AND SPECIFICATIONS
(SDS) ............... .......................................... ...
17
SERVICE DATA AND SPECIFICATIONS
(SDS) .................................................................
17
Standard and Limit .............................................. ....17
Revision: December 20092009 QX56