wheel INFINITI QX56 2009 Factory Workshop Manual
[x] Cancel search | Manufacturer: INFINITI, Model Year: 2009, Model line: QX56, Model: INFINITI QX56 2009Pages: 4171, PDF Size: 84.65 MB
Page 401 of 4171
![INFINITI QX56 2009 Factory Workshop Manual
BCS
DIAGNOSIS SYSTEM (BCM)BCS-27
< FUNCTION DIAGNOSIS > [BCM]
C
D
E
F
G H
I
J
K L
B A
O P
N
AIR PRESSURE MONITOR
AIR PRESSURE MONITOR : Diagnosis DescriptionINFOID:0000000003776404
DESCRIPTION
During INFINITI QX56 2009 Factory Workshop Manual
BCS
DIAGNOSIS SYSTEM (BCM)BCS-27
< FUNCTION DIAGNOSIS > [BCM]
C
D
E
F
G H
I
J
K L
B A
O P
N
AIR PRESSURE MONITOR
AIR PRESSURE MONITOR : Diagnosis DescriptionINFOID:0000000003776404
DESCRIPTION
During](/img/42/57031/w960_57031-400.png)
BCS
DIAGNOSIS SYSTEM (BCM)BCS-27
< FUNCTION DIAGNOSIS > [BCM]
C
D
E
F
G H
I
J
K L
B A
O P
N
AIR PRESSURE MONITOR
AIR PRESSURE MONITOR : Diagnosis DescriptionINFOID:0000000003776404
DESCRIPTION
During driving, the TPMS receives the signal transmitt
ed from the transmitter installed in each wheel, when
the tire pressure becomes low. The control unit (BC M) of this system has pressure judgment and trouble diag-
nosis functions.
When the TPMS detects low inflation pressure or anot her unusual symptom, the warning lamps in the combi-
nation meter comes on.
SELF DIAGNOSTIC PROCE DURE (WITH CONSULT-III)
With CONSULT-III
Touch “SELF-DIAG RESULTS” display to show malf unction experienced since the last erasing operation.
Refer to BCS-51, "DTC Index"
.
SELF DIAGNOSTIC PROCE DURE (WITHOUT CONSULT-III)
Without CONSULT-III
To start the self-diagnostic results mode, ground terminal of the tire pressure warning check connector. The
malfunction location is indicated by the warning lamp flashing.
NOTE:
When the low tire warning lamp flashes 5 Hz and continues repeating it, the system is normal.
Test Item Operation Description
OIL PRESSURE SW OFF OFF
ON
BCM transmits the oil pressure switch signal to the combination meter via CAN communica-
tion, which operates the oil pressure gauge in the combination meter.
SEIA0745E
Flickering
pattern Items Diagnostic items detected when··· Check item
15 Tire pressure value (Front LH) Front LH tire pressure drops to 181 kPa (1.8 kg/cm, 25.25 psi) or less.
–
16 Tire pressure value (Front RH) Front RH tire pressure drops to 181 kPa (1.8 kg/cm, 25.25 psi) or less.
17 Tire pressure value (Rear RH) Rear RH tire pressure drops to 181 kPa (1.8 kg/cm, 25.25 psi) or less.
18 Tire pressure value (Rear LH) Rear LH tire pressure drops to 181 kPa (1.8 kg/cm, 25.25 psi) or less.
21 Transmitter no data (Front LH) Data from front LH transmitter can not be received.
WT-27
22 Transmitter no data (Front RH) Data from front RH transmitter can not be received.
23 Transmitter no data (Rear RH) Data from Rear RH transmitter can not be received.
24 Transmitter no data (Rear LH) Data from Rear LH transmitter can not be received.
Revision: December 20092009 QX56
Page 428 of 4171
![INFINITI QX56 2009 Factory Workshop Manual
BCS-54
< PRECAUTION >[BCM]
PRECAUTIONS
PRECAUTION
PRECAUTIONS
Precaution for Supplemental Restraint S
ystem (SRS) "AIR BAG" and "SEAT BELT
PRE-TENSIONER"
INFOID:0000000005851887
The Supplemental Res INFINITI QX56 2009 Factory Workshop Manual
BCS-54
< PRECAUTION >[BCM]
PRECAUTIONS
PRECAUTION
PRECAUTIONS
Precaution for Supplemental Restraint S
ystem (SRS) "AIR BAG" and "SEAT BELT
PRE-TENSIONER"
INFOID:0000000005851887
The Supplemental Res](/img/42/57031/w960_57031-427.png)
BCS-54
< PRECAUTION >[BCM]
PRECAUTIONS
PRECAUTION
PRECAUTIONS
Precaution for Supplemental Restraint S
ystem (SRS) "AIR BAG" and "SEAT BELT
PRE-TENSIONER"
INFOID:0000000005851887
The Supplemental Restraint System such as “A IR BAG” and “SEAT BELT PRE-TENSIONER”, used along
with a front seat belt, helps to reduce the risk or severi ty of injury to the driver and front passenger for certain
types of collision. This system includes seat belt switch inputs and dual stage front air bag modules. The SRS
system uses the seat belt switches to determine the front air bag deployment, and may only deploy one front
air bag, depending on the severity of a collision and w hether the front occupants are belted or unbelted.
Information necessary to service the system safely is included in the SR and SB section of this Service Man-
ual.
WARNING:
To avoid rendering the SRS inopera tive, which could increase the risk of personal injury or death in
the event of a collision which would result in air bag inflation, all maintenance must be performed by
an authorized NISS AN/INFINITI dealer.
Improper maintenance, including in correct removal and installation of the SRS, can lead to personal
injury caused by unintent ional activation of the system. For re moval of Spiral Cable and Air Bag
Module, see the SR section.
Do not use electrical test equipmen t on any circuit related to the SRS unless instructed to in this
Service Manual. SRS wiring harnesses can be identi fied by yellow and/or orange harnesses or har-
ness connectors.
PRECAUTIONS WHEN USING POWER TOOLS (AIR OR ELECTRIC) AND HAMMERS
WARNING:
When working near the Airbag Diagnosis Sensor Unit or other Airbag System sensors with the Igni-
tion ON or engine running, DO NOT use air or electri c power tools or strike near the sensor(s) with a
hammer. Heavy vibration could activate the sensor( s) and deploy the air bag(s), possibly causing
serious injury.
When using air or electric power tools or hammers , always switch the Ignition OFF, disconnect the
battery, and wait at least 3 minu tes before performing any service.
Precaution Necessary for Steering W heel Rotation After Battery Disconnect
INFOID:0000000005851888
NOTE:
This Procedure is applied only to models with Intelli gent Key system and NATS (NISSAN ANTI-THEFT SYS-
TEM).
Remove and install all control units after disconnecting both battery cables with the ignition knob in the
″LOCK ″ position.
Always use CONSULT-III to perform self-diagnosis as a part of each function inspection after finishing work.
If DTC is detected, perform trouble diagnosis according to self-diagnostic results.
For models equipped with the Intelligent Key system and NATS, an electrically controlled steering lock mech-
anism is adopted on the key cylinder.
For this reason, if the battery is disconnected or if the battery is discharged, the steering wheel will lock and
steering wheel rotation will become impossible.
If steering wheel rotation is required when battery pow er is interrupted, follow the procedure below before
starting the repair operation.
OPERATION PROCEDURE
1. Connect both battery cables. NOTE:
Supply power using jumper cables if battery is discharged.
2. Use the Intelligent Key or mechanical key to turn the ignition switch to the ″ACC ″ position. At this time, the
steering lock will be released.
3. Disconnect both battery cables. The steering lock will remain released and the steering wheel can be
rotated.
4. Perform the necessary repair operation.
Revision: December 20092009 QX56
Page 431 of 4171
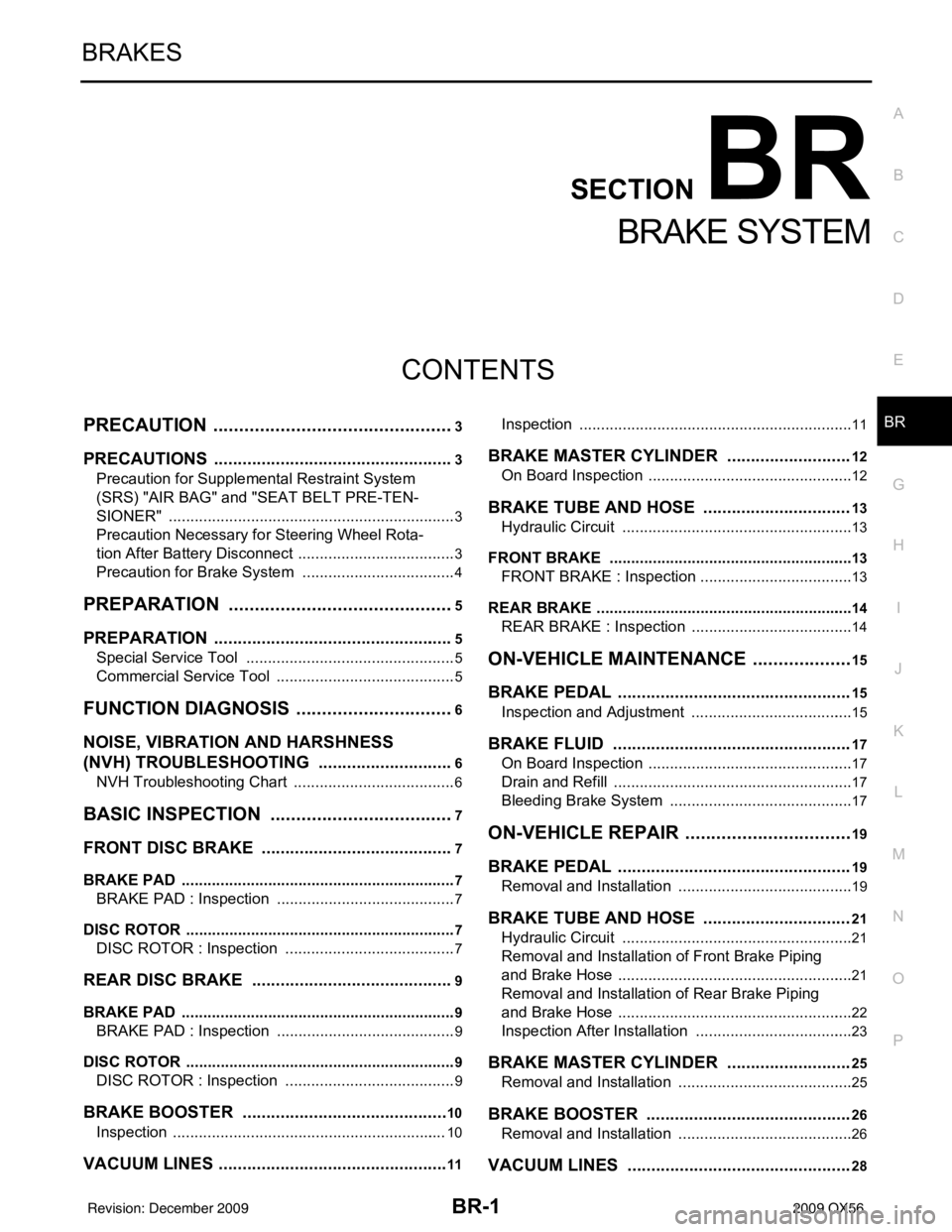
BR-1
BRAKES
C
DE
G H
I
J
K L
M
SECTION BR
A
B
BR
N
O P
CONTENTS
BRAKE SYSTEM
PRECAUTION ....... ........................................3
PRECAUTIONS .............................................. .....3
Precaution for Supplemental Restraint System
(SRS) "AIR BAG" and "SEAT BELT PRE-TEN-
SIONER" ............................................................. ......
3
Precaution Necessary for Steering Wheel Rota-
tion After Battery Disconnect ............................... ......
3
Precaution for Brake System ....................................4
PREPARATION ............................................5
PREPARATION .............................................. .....5
Special Service Tool ........................................... ......5
Commercial Service Tool ..........................................5
FUNCTION DIAGNOSIS ...............................6
NOISE, VIBRATION AND HARSHNESS
(NVH) TROUBLESHOOTING ........................ .....
6
NVH Troubleshooting Chart ................................ ......6
BASIC INSPECTION ....................................7
FRONT DISC B RAKE .................................... .....7
BRAKE PAD .......................................................... ......7
BRAKE PAD : Inspection ..........................................7
DISC ROTOR ......................................................... ......7
DISC ROTOR : Inspection ........................................7
REAR DISC BRAKE ...................................... .....9
BRAKE PAD .......................................................... ......9
BRAKE PAD : Inspection ..........................................9
DISC ROTOR ......................................................... ......9
DISC ROTOR : Inspection ........................................9
BRAKE BOOSTER ............................................10
Inspection ............................................................ ....10
VACUUM LINES ............................................. ....11
Inspection ............................................................ ....11
BRAKE MASTER CYLINDER ..........................12
On Board Inspection ................................................12
BRAKE TUBE AND HOSE ...............................13
Hydraulic Circuit ......................................................13
FRONT BRAKE ..................................................... ....13
FRONT BRAKE : Inspection ......................... ...........13
REAR BRAKE ........................................................ ....14
REAR BRAKE : Inspection ........................ ..............14
ON-VEHICLE MAINTEN ANCE ....................15
BRAKE PEDAL .................................................15
Inspection and Adjustment .................................. ....15
BRAKE FLUID ..................................................17
On Board Inspection ............................................ ....17
Drain and Refill ........................................................17
Bleeding Brake System ...........................................17
ON-VEHICLE REPAIR .................................19
BRAKE PEDAL .................................................19
Removal and Installation ..................................... ....19
BRAKE TUBE AND HOSE ...............................21
Hydraulic Circuit ......................................................21
Removal and Installation of Front Brake Piping
and Brake Hose .......................................................
21
Removal and Installation of Rear Brake Piping
and Brake Hose .......................................................
22
Inspection After Installation .....................................23
BRAKE MASTER CYLINDER ..........................25
Removal and Installation .........................................25
BRAKE BOOSTER ...........................................26
Removal and Installation ..................................... ....26
VACUUM LINES ...............................................28
Revision: December 20092009 QX56
Page 433 of 4171
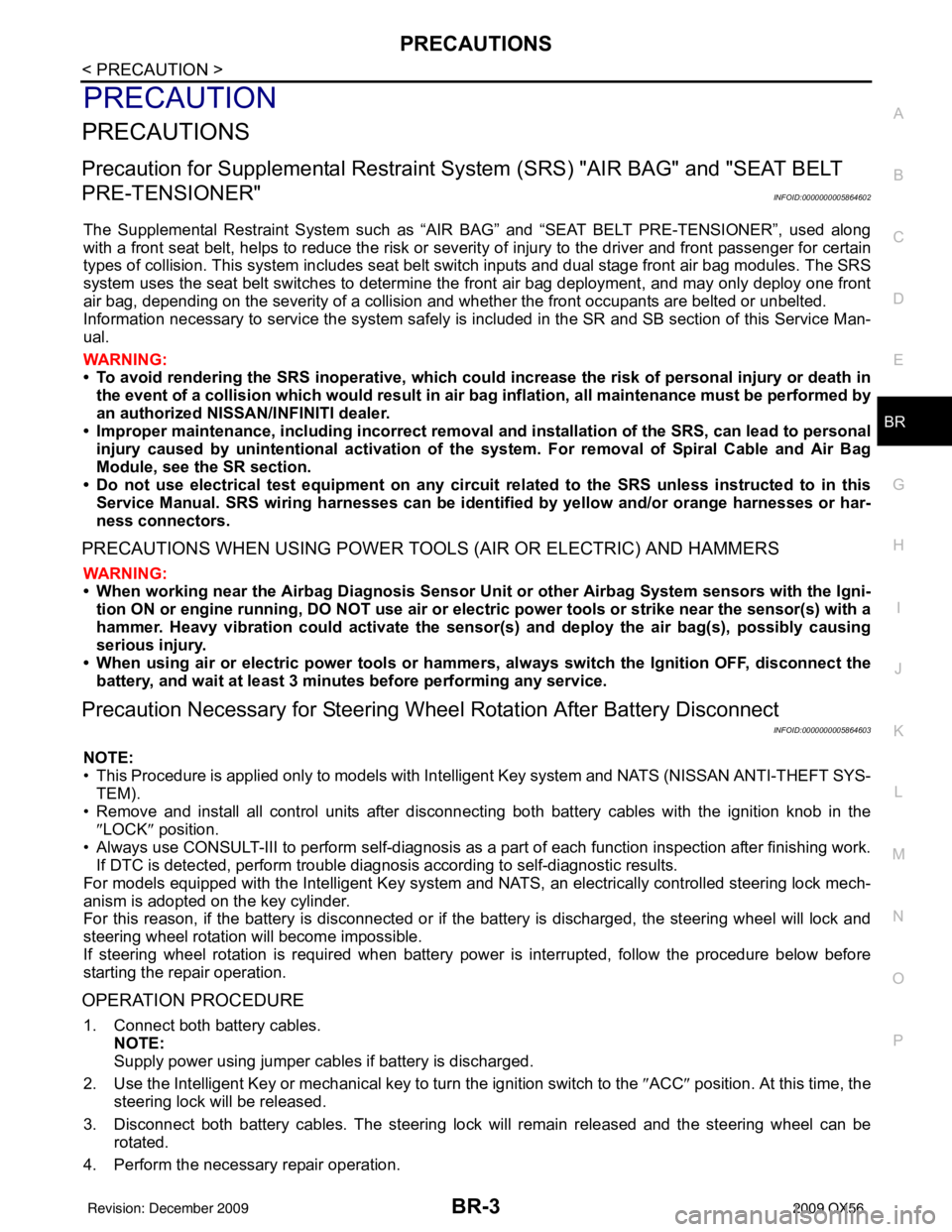
PRECAUTIONSBR-3
< PRECAUTION >
C
DE
G H
I
J
K L
M A
B
BR
N
O P
PRECAUTION
PRECAUTIONS
Precaution for Supplemental Restraint System (SRS) "AIR BAG" and "SEAT BELT
PRE-TENSIONER"
INFOID:0000000005864602
The Supplemental Restraint System such as “AIR BAG” and “SEAT BELT PRE-TENSIONER”, used along
with a front seat belt, helps to reduce the risk or severi ty of injury to the driver and front passenger for certain
types of collision. This system includes seat belt switch inputs and dual stage front air bag modules. The SRS
system uses the seat belt switches to determine the front air bag deployment, and may only deploy one front
air bag, depending on the severity of a collision and w hether the front occupants are belted or unbelted.
Information necessary to service the system safely is included in the SR and SB section of this Service Man-
ual.
WARNING:
• To avoid rendering the SRS inoper ative, which could increase the risk of personal injury or death in
the event of a collision which would result in air bag inflation, all maintenance must be performed by
an authorized NISSAN/INFINITI dealer.
• Improper maintenance, including in correct removal and installation of the SRS, can lead to personal
injury caused by unintentional act ivation of the system. For removal of Spiral Cable and Air Bag
Module, see the SR section.
• Do not use electrical test equipm ent on any circuit related to the SRS unless instructed to in this
Service Manual. SRS wiring harnesses can be identi fied by yellow and/or orange harnesses or har-
ness connectors.
PRECAUTIONS WHEN USING POWER TOOLS (AIR OR ELECTRIC) AND HAMMERS
WARNING:
• When working near the Airbag Diagnosis Sensor Un it or other Airbag System sensors with the Igni-
tion ON or engine running, DO NOT use air or el ectric power tools or strike near the sensor(s) with a
hammer. Heavy vibration could activate the sensor( s) and deploy the air bag(s), possibly causing
serious injury.
• When using air or electric power tools or hammers, always switch the Ignition OFF, disconnect the battery, and wait at least 3 minutes before performing any service.
Precaution Necessary for Steering Wheel Rotation After Battery Disconnect
INFOID:0000000005864603
NOTE:
• This Procedure is applied only to models with Intelligent Key system and NATS (NISSAN ANTI-THEFT SYS-
TEM).
• Remove and install all control units after disconnecti ng both battery cables with the ignition knob in the
″ LOCK ″ position.
• Always use CONSULT-III to perform self-diagnosis as a part of each function inspection after finishing work.
If DTC is detected, perform trouble diagnosis according to self-diagnostic results.
For models equipped with the Intelligent Key system and NATS , an electrically controlled steering lock mech-
anism is adopted on the key cylinder.
For this reason, if the battery is disconnected or if the battery is discharged, the steering wheel will lock and
steering wheel rotation will become impossible.
If steering wheel rotation is required when battery power is interrupted, follow the procedure below before
starting the repair operation.
OPERATION PROCEDURE
1. Connect both battery cables. NOTE:
Supply power using jumper cables if battery is discharged.
2. Use the Intelligent Key or mechanical key to turn the ignition switch to the ″ACC ″ position. At this time, the
steering lock will be released.
3. Disconnect both battery cables. The steering lock will remain released and the steering wheel can be
rotated.
4. Perform the necessary repair operation.
Revision: December 20092009 QX56
Page 434 of 4171
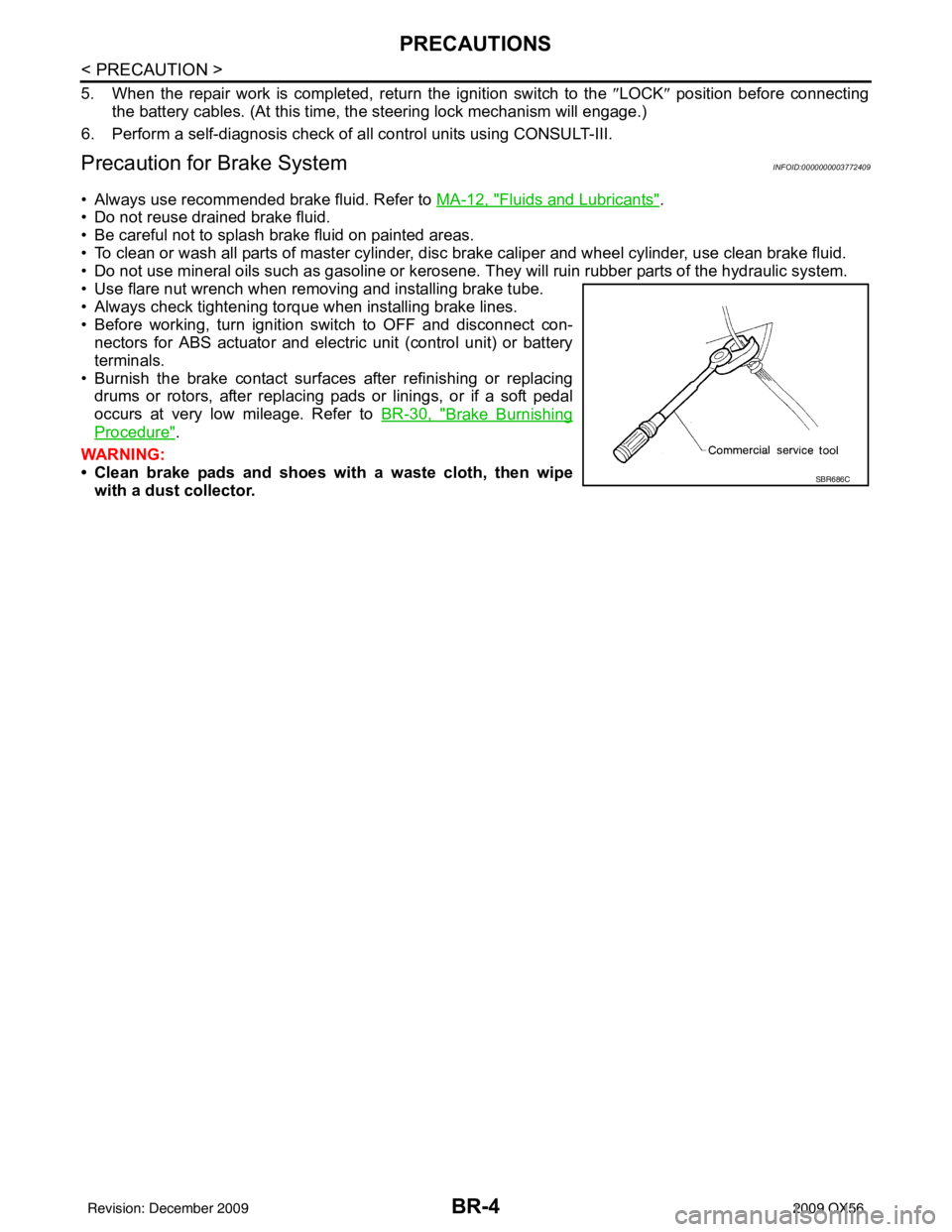
BR-4
< PRECAUTION >
PRECAUTIONS
5. When the repair work is completed, return the ignition switch to the ″LOCK ″ position before connecting
the battery cables. (At this time, the steering lock mechanism will engage.)
6. Perform a self-diagnosis check of a ll control units using CONSULT-III.
Precaution for Brake SystemINFOID:0000000003772409
• Always use recommended brake fluid. Refer to MA-12, "Fluids and Lubricants".
• Do not reuse drained brake fluid.
• Be careful not to splash brake fluid on painted areas.
• To clean or wash all parts of master cylinder, disc brake caliper and wheel cylinder, use clean brake fluid.
• Do not use mineral oils such as gasoline or kerosene. They will ruin rubber parts of the hydraulic system.
• Use flare nut wrench when removing and installing brake tube.
• Always check tightening torque when installing brake lines.
• Before working, turn ignition switch to OFF and disconnect con- nectors for ABS actuator and electric unit (control unit) or battery
terminals.
• Burnish the brake contact surfaces after refinishing or replacing drums or rotors, after replacing pads or linings, or if a soft pedal
occurs at very low mileage. Refer to BR-30, "
Brake Burnishing
Procedure".
WARNING:
• Clean brake pads and shoes wi th a waste cloth, then wipe
with a dust collector.
SBR686C
Revision: December 20092009 QX56
Page 436 of 4171
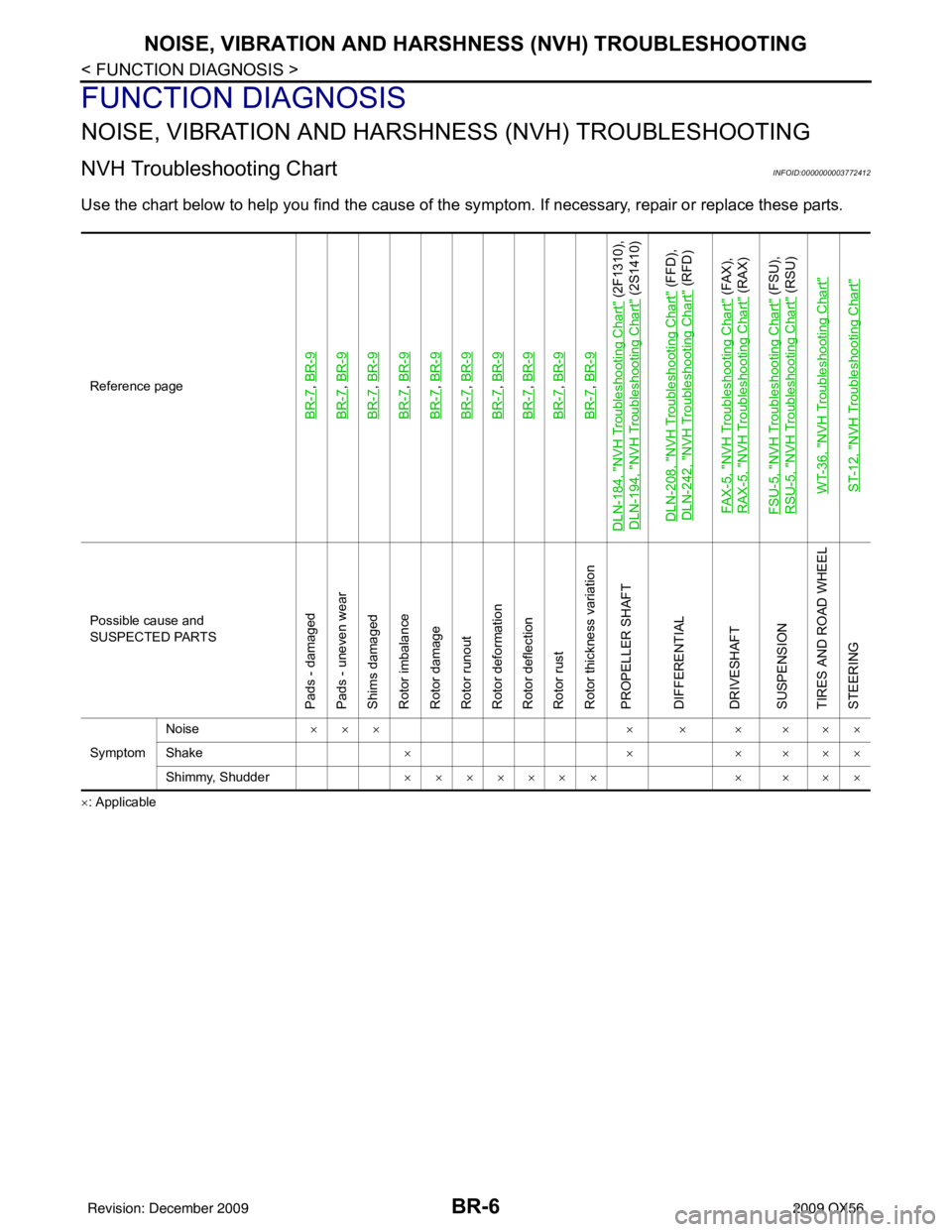
BR-6
< FUNCTION DIAGNOSIS >
NOISE, VIBRATION AND HARSHNESS (NVH) TROUBLESHOOTING
FUNCTION DIAGNOSIS
NOISE, VIBRATION AND HARSHNESS (NVH) TROUBLESHOOTING
NVH Troubleshooting ChartINFOID:0000000003772412
Use the chart below to help you find the cause of the sy mptom. If necessary, repair or replace these parts.
×: ApplicableReference page
BR-7
, BR-9
BR-7
, BR-9
BR-7
, BR-9
BR-7
, BR-9
BR-7
, BR-9
BR-7
, BR-9
BR-7
, BR-9
BR-7
, BR-9
BR-7
, BR-9
BR-7
, BR-9
DLN-184, "
NVH Troubleshooting Chart
" (2F1310),
DLN-194, "
NVH Troubleshooting Chart
" (2S1410)
DLN-208, "
NVH Troubleshooting Chart
" (FFD),
DLN-242, "
NVH Troubleshooting Chart
" (RFD)
FAX-5, "
NVH Troubleshooting Chart
" (FAX),
RAX-5, "
NVH Troubleshooting Chart
" (RAX)
FSU-5, "
NVH Troubleshooting Chart
" (FSU),
RSU-5, "
NVH Troubleshooting Chart
" (RSU)
WT-36, "
NVH Troubleshooting Chart
"
ST-12, "
NVH Troubleshooting Chart
"
Possible cause and
SUSPECTED PARTS
Pads - damaged
Pads - uneven wear
Shims damaged
Rotor imbalance
Rotor damage
Rotor runout
Rotor deformation
Rotor deflection
Rotor rust
Rotor thickness variation
PROPELLER SHAFT
DIFFERENTIAL
DRIVESHAFT
SUSPENSION
TIRES AND ROAD WHEEL
STEERING
Symptom Noise
××× × × × × ××
Shake ×× ××××
Shimmy, Shudder ××××××× × × ××
Revision: December 20092009 QX56
Page 437 of 4171
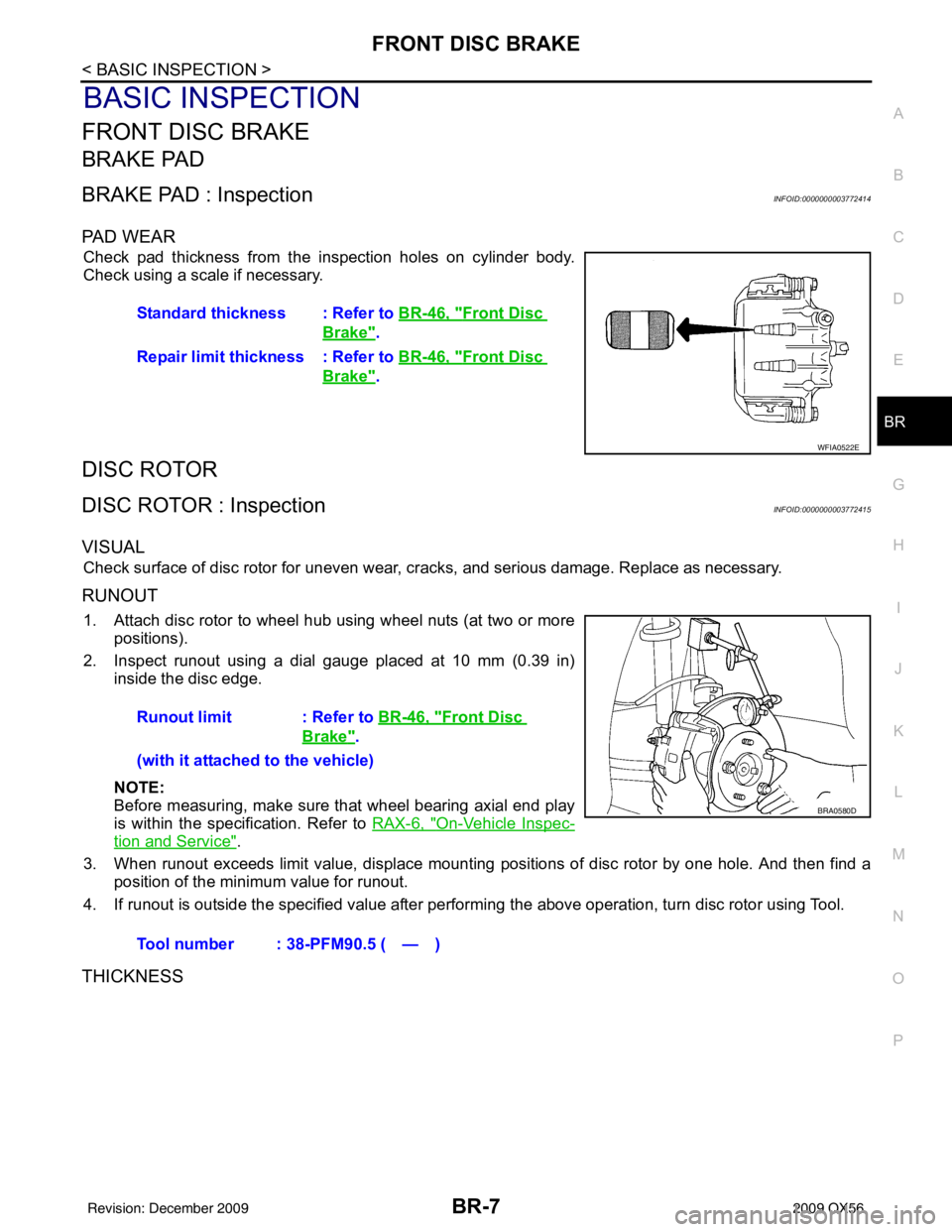
FRONT DISC BRAKEBR-7
< BASIC INSPECTION >
C
DE
G H
I
J
K L
M A
B
BR
N
O P
BASIC INSPECTION
FRONT DISC BRAKE
BRAKE PAD
BRAKE PAD : InspectionINFOID:0000000003772414
PA D W E A R
Check pad thickness from the inspection holes on cylinder body.
Check using a scale if necessary.
DISC ROTOR
DISC ROTOR : InspectionINFOID:0000000003772415
VISUAL
Check surface of disc rotor for uneven wear, cracks, and serious damage. Replace as necessary.
RUNOUT
1. Attach disc rotor to wheel hub using wheel nuts (at two or more positions).
2. Inspect runout using a dial gauge placed at 10 mm (0.39 in) inside the disc edge.
NOTE:
Before measuring, make sure that wheel bearing axial end play
is within the specification. Refer to RAX-6, "
On-Vehicle Inspec-
tion and Service".
3. When runout exceeds limit value, displace mounting positions of disc rotor by one hole. And then find a position of the minimum value for runout.
4. If runout is outside the specified value after performing the above operation, turn disc rotor using Tool.
THICKNESS
Standard thickness : Refer to BR-46, "Front Disc
Brake".
Repair limit thickness : Refer to BR-46, "
Front Disc
Brake".
WFIA0522E
Runout limit : Refer to BR-46, "Front Disc
Brake".
(with it attached to the vehicle)
Tool number : 38-PFM90.5 ( — )
BRA0580D
Revision: December 20092009 QX56
Page 439 of 4171
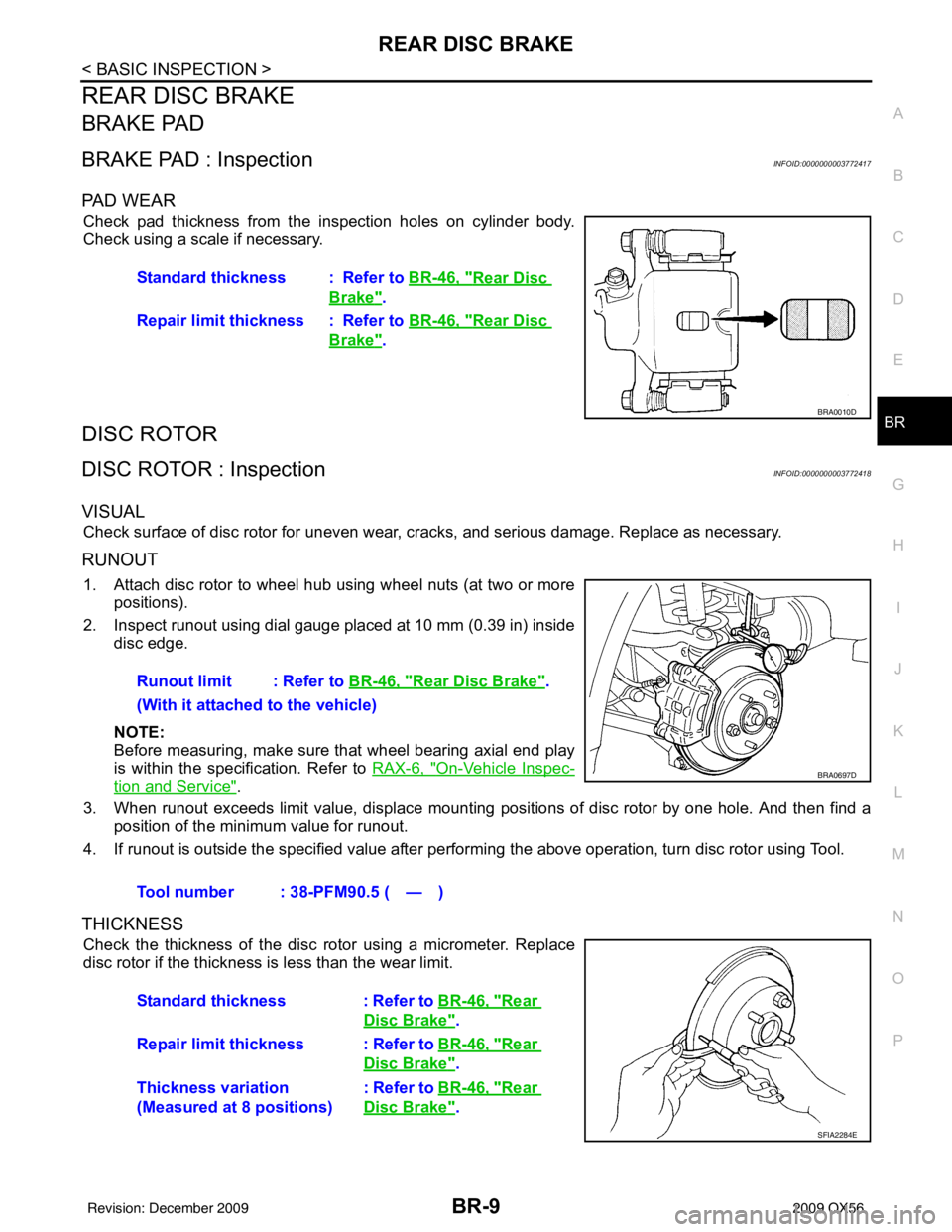
REAR DISC BRAKEBR-9
< BASIC INSPECTION >
C
DE
G H
I
J
K L
M A
B
BR
N
O P
REAR DISC BRAKE
BRAKE PAD
BRAKE PAD : InspectionINFOID:0000000003772417
PA D W E A R
Check pad thickness from the inspection holes on cylinder body.
Check using a scale if necessary.
DISC ROTOR
DISC ROTOR : InspectionINFOID:0000000003772418
VISUAL
Check surface of disc rotor for uneven wear, cracks, and serious damage. Replace as necessary.
RUNOUT
1. Attach disc rotor to wheel hub using wheel nuts (at two or more positions).
2. Inspect runout using dial gauge placed at 10 mm (0.39 in) inside disc edge.
NOTE:
Before measuring, make sure that wheel bearing axial end play
is within the specification. Refer to RAX-6, "
On-Vehicle Inspec-
tion and Service".
3. When runout exceeds limit value, displace mounting positions of disc rotor by one hole. And then find a position of the minimum value for runout.
4. If runout is outside the specified value after performing the above operation, turn disc rotor using Tool.
THICKNESS
Check the thickness of the disc rotor using a micrometer. Replace
disc rotor if the thickness is less than the wear limit. Standard thickness : Refer to
BR-46, "
Rear Disc
Brake".
Repair limit thickness : Refer to BR-46, "
Rear Disc
Brake".
BRA0010D
Runout limit : Refer to BR-46, "Rear Disc Brake".
(With it attached to the vehicle)
Tool number : 38-PFM90.5 ( — )
BRA0697D
Standard thickness : Refer to BR-46, "Rear
Disc Brake".
Repair limit thickness : Refer to BR-46, "
Rear
Disc Brake".
Thickness variation
(Measured at 8 positions) : Refer to
BR-46, "
Rear
Disc Brake".
SFIA2284E
Revision: December 20092009 QX56
Page 443 of 4171
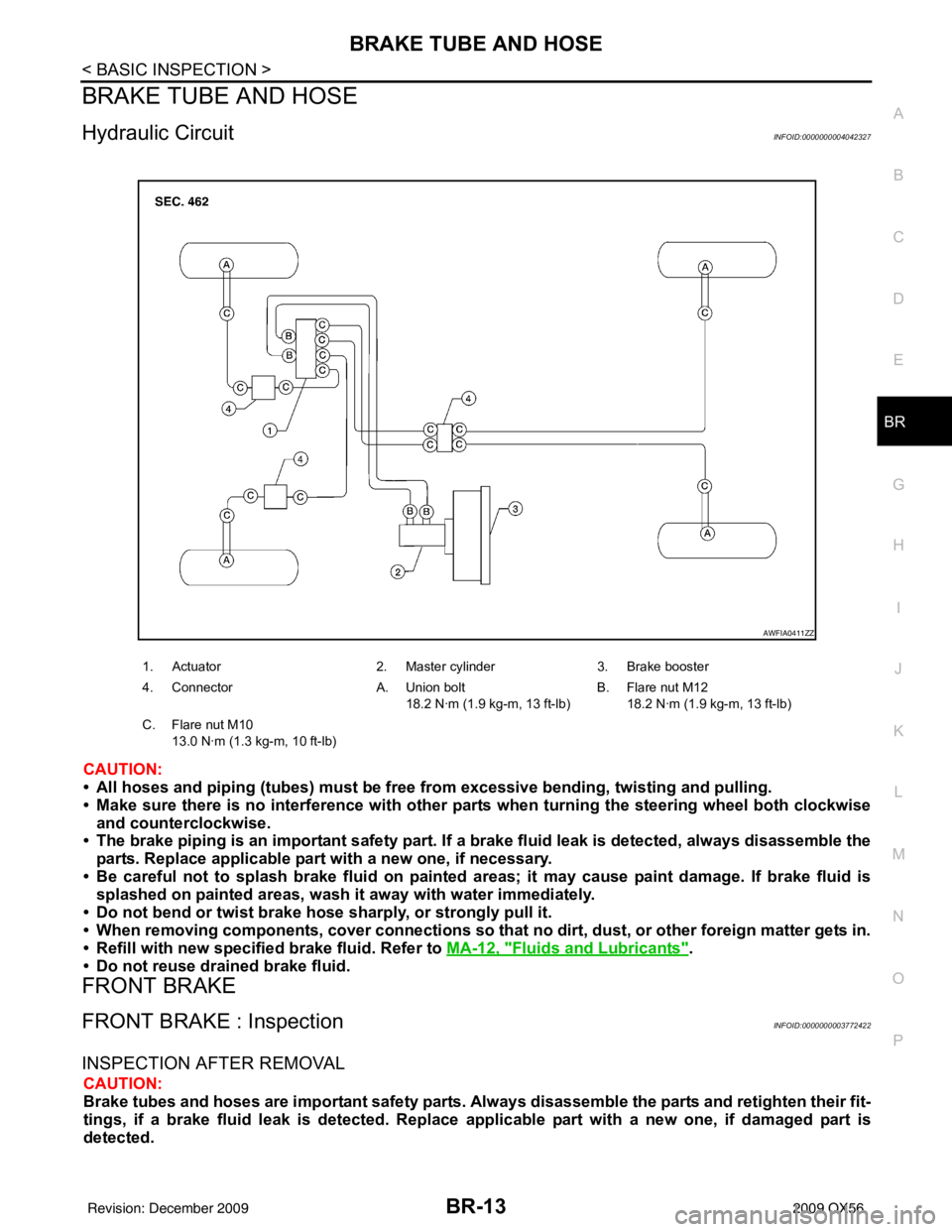
BRAKE TUBE AND HOSEBR-13
< BASIC INSPECTION >
C
DE
G H
I
J
K L
M A
B
BR
N
O P
BRAKE TUBE AND HOSE
Hydraulic CircuitINFOID:0000000004042327
CAUTION:
• All hoses and piping (tubes) must be fr ee from excessive bending, twisting and pulling.
• Make sure there is no interference with other parts when turning the steering wheel both clockwise
and counterclockwise.
• The brake piping is an important safety part. If a brake fluid leak is detected, always disassemble the
parts. Replace applicable part with a new one, if necessary.
• Be careful not to splash brake fluid on painted areas; it may cause paint damage. If brake fluid is
splashed on painted areas, wash it away with water immediately.
• Do not bend or twist brake hose sharply, or strongly pull it.
• When removing components, cover connections so that no dirt, dust, or other foreign matter gets in.
• Refill with new specified brake fluid. Refer to MA-12, "
Fluids and Lubricants".
• Do not reuse drained brake fluid.
FRONT BRAKE
FRONT BRAKE : InspectionINFOID:0000000003772422
INSPECTION AFTER REMOVAL
CAUTION:
Brake tubes and hoses are important safety parts. Always disassemble the parts and retighten their fit-
tings, if a brake fluid leak is det ected. Replace applicable part with a new one, if damaged part is
detected.
1. Actuator 2. Master cylinder3. Brake booster
4. Connector A. Union bolt
18.2 N·m (1.9 kg-m, 13 ft-lb) B. Flare nut M12
18.2 N·m (1.9 kg-m, 13 ft-lb)
C. Flare nut M10 13.0 N·m (1.3 kg-m, 10 ft-lb)
AWFIA0411ZZ
Revision: December 20092009 QX56
Page 448 of 4171
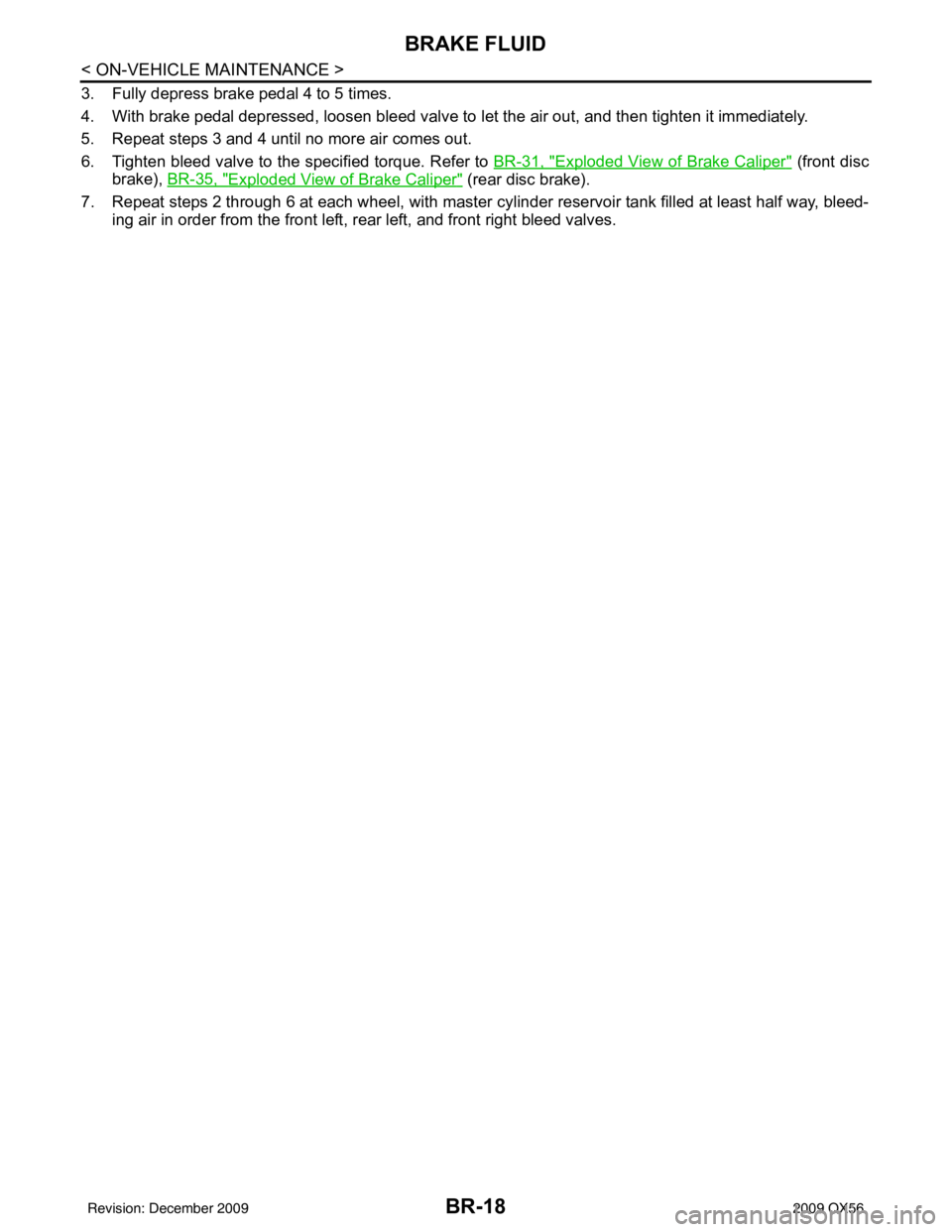
BR-18
< ON-VEHICLE MAINTENANCE >
BRAKE FLUID
3. Fully depress brake pedal 4 to 5 times.
4. With brake pedal depressed, loosen bleed valve to let the air out, and then tighten it immediately.
5. Repeat steps 3 and 4 until no more air comes out.
6. Tighten bleed valve to the specified torque. Refer to BR-31, "
Exploded View of Brake Caliper" (front disc
brake), BR-35, "
Exploded View of Brake Caliper" (rear disc brake).
7. Repeat steps 2 through 6 at each wheel, with master cylinder reservoir tank filled at least half way, bleed- ing air in order from the front left, rear left, and front right bleed valves.
Revision: December 20092009 QX56