torque INFINITI QX56 2010 Factory Manual PDF
[x] Cancel search | Manufacturer: INFINITI, Model Year: 2010, Model line: QX56, Model: INFINITI QX56 2010Pages: 4210, PDF Size: 81.91 MB
Page 1352 of 4210
![INFINITI QX56 2010 Factory Manual PDF DLN-270
< SERVICE DATA AND SPECIFICATIONS (SDS) [REAR FINAL DRIVE: R230]
SERVICE DATA AND SPECIFICATIONS (SDS)
SERVICE DATA AND SPECIFICATIONS (SDS)
SERVICE DATA AND SPECIFICATIONS (SDS)
General Speci INFINITI QX56 2010 Factory Manual PDF DLN-270
< SERVICE DATA AND SPECIFICATIONS (SDS) [REAR FINAL DRIVE: R230]
SERVICE DATA AND SPECIFICATIONS (SDS)
SERVICE DATA AND SPECIFICATIONS (SDS)
SERVICE DATA AND SPECIFICATIONS (SDS)
General Speci](/img/42/57032/w960_57032-1351.png)
DLN-270
< SERVICE DATA AND SPECIFICATIONS (SDS) [REAR FINAL DRIVE: R230]
SERVICE DATA AND SPECIFICATIONS (SDS)
SERVICE DATA AND SPECIFICATIONS (SDS)
SERVICE DATA AND SPECIFICATIONS (SDS)
General SpecificationINFOID:0000000005148937
Inspection and AdjustmentINFOID:0000000005148938
DRIVE GEAR RUNOUT
Unit: mm (in)
SIDE GEAR CLEARANCE
Unit: mm (in)
PRELOAD TORQUE
Unit: N·m (kg-m, in-lb)
BACKLASH
Unit: mm (in)
COMPANION FLANGE RUNOUT
Unit: mm (in)
SELECTIVE PARTS
Side Gear Thrust Washer
Applied model VK56DE
A/T
Final drive model R230
Gear ratio 3.357
Number of teeth (Drive gear/Drive pinion) 47/14
Oil capacity (Approx.) 1.75 (3 3/4 US pt, 3 1/8 Imp pt)
Number of pinion gears 2
Drive pinion adjustment spacer type Collapsible
ItemRunout limit
Drive gear back face 0.05 (0.0020) or less
ItemSpecification
Side gear back clearance
(Clearance limit between side gear and differential case for adjusting
side gear backlash) 0.20 (0.0079) or less
(Each gear should rotate smoothly without excessive resis- tance during differential motion.)
Item Specification
Drive pinion bearing preload torque 1.77 − 2.64 N·m (0.18 − 0.26 kg−m, 16 − 23 in-lb)
Side bearing preload torque (reference value determined by drive
gear bolt pulling force) 0.20
− 0.52 N·m (0.02 − 0.05 kg −m, 2 − 4 in-lb)
Drive gear bolt pulling force (by spring gauge) 34.2 − 39.2 N (3.5 − 4.0 kg, 7.7 − 8.8 lb)
Total preload torque
(Total preload torque = drive pinion bearing preload torque + Side
bearing preload torque) 2.05
− 4.11 N·m (0.21 − 0.42 kg−m, 19 − 36 in-lb)
Item Specification
Drive gear to drive pinion gear 0.13 − 0.18 (0.0051 − 0.0070)
Item Runout limit
Outer side of the companion flange 0.08 (0.0031) or less
Revision: April 20092010 QX56
Page 1393 of 4210
![INFINITI QX56 2010 Factory Manual PDF EC-40
< FUNCTION DIAGNOSIS >[VK56DE]
INTAKE VALVE TIMING CONTROL
INTAKE VALVE TIMING CONTROL
DescriptionINFOID:0000000005149073
SYSTEM DESCRIPTION
*: This signal is sent to the ECM through CAN communi INFINITI QX56 2010 Factory Manual PDF EC-40
< FUNCTION DIAGNOSIS >[VK56DE]
INTAKE VALVE TIMING CONTROL
INTAKE VALVE TIMING CONTROL
DescriptionINFOID:0000000005149073
SYSTEM DESCRIPTION
*: This signal is sent to the ECM through CAN communi](/img/42/57032/w960_57032-1392.png)
EC-40
< FUNCTION DIAGNOSIS >[VK56DE]
INTAKE VALVE TIMING CONTROL
INTAKE VALVE TIMING CONTROL
DescriptionINFOID:0000000005149073
SYSTEM DESCRIPTION
*: This signal is sent to the ECM through CAN communication line
This mechanism hydraulically controls cam phases c
ontinuously with the fixed operating angle of the intake
valve.
The ECM receives signals such as crankshaft posit ion, camshaft position, engine speed, and engine coolant
temperature. Then, the ECM sends ON/OFF pulse duty si gnals to the intake valve timing (IVT) control sole-
noid valve depending on driving status. This makes it po ssible to control the shut/open timing of the intake
valve to increase engine torque in low/mid speed range and output in high-speed range.
Sensor Input signal to ECM function ECMActuator
Crankshaft position sensor (POS)
Camshaft position sensor (PHASE) Engine speed
Intake valve
timing controlIntake valve timing control
solenoid valve
Intake valve timing control position sensor Intake valve timing signal
Engine coolant temperature sensor
Engine coolant temperature
Wheel sensor Vehicle speed*
PBIB3276E
Revision: April 20092010 QX56
Page 1504 of 4210
![INFINITI QX56 2010 Factory Manual PDF P0133, P0153 A/F SENSOR 1EC-151
< COMPONENT DIAGNOSIS > [VK56DE]
C
D
E
F
G H
I
J
K L
M A
EC
NP
O
Refer to
EC-85, "Ground Inspection".
OK or NG
OK >> GO TO 2.
NG >> Repair or replace ground connection INFINITI QX56 2010 Factory Manual PDF P0133, P0153 A/F SENSOR 1EC-151
< COMPONENT DIAGNOSIS > [VK56DE]
C
D
E
F
G H
I
J
K L
M A
EC
NP
O
Refer to
EC-85, "Ground Inspection".
OK or NG
OK >> GO TO 2.
NG >> Repair or replace ground connection](/img/42/57032/w960_57032-1503.png)
P0133, P0153 A/F SENSOR 1EC-151
< COMPONENT DIAGNOSIS > [VK56DE]
C
D
E
F
G H
I
J
K L
M A
EC
NP
O
Refer to
EC-85, "Ground Inspection".
OK or NG
OK >> GO TO 2.
NG >> Repair or replace ground connections.
2.RETIGHTEN A/F SENSOR 1
Loosen and retighten the A/F sensor 1.
>> GO TO 3.
3.CHECK EXHAUST GAS LEAK
1. Start engine and run it at idle.
2. Listen for an exhaust gas leak before three way catalyst (manifold).
OK or NG
OK >> GO TO 4.
NG >> Repair or replace.
4.CHECK FOR INTAKE AIR LEAK
Listen for an intake air leak after the mass air flow sensor.
OK or NG
OK >> GO TO 5.
NG >> Repair or replace.
5.CLEAR THE SELF-LEARNING DATA
With CONSULT-III
1. Start engine and warm it up to normal operating temperature.
BBIA0354E
Tightening torque: 50 N-m (5.1 kg-m, 37 ft-lb)
BBIA0375E
PBIB1216E
Revision: April 20092010 QX56
Page 1737 of 4210
![INFINITI QX56 2010 Factory Manual PDF EC-384
< COMPONENT DIAGNOSIS >[VK56DE]
P2A00, P2A03 A/F SENSOR 1
1. Loosen and retighten the A/F sensor 1.
>> GO TO 3.
3.CHECK FOR INTAKE AIR LEAK
1. Start engine and run it at idle.
2. Listen for an INFINITI QX56 2010 Factory Manual PDF EC-384
< COMPONENT DIAGNOSIS >[VK56DE]
P2A00, P2A03 A/F SENSOR 1
1. Loosen and retighten the A/F sensor 1.
>> GO TO 3.
3.CHECK FOR INTAKE AIR LEAK
1. Start engine and run it at idle.
2. Listen for an](/img/42/57032/w960_57032-1736.png)
EC-384
< COMPONENT DIAGNOSIS >[VK56DE]
P2A00, P2A03 A/F SENSOR 1
1. Loosen and retighten the A/F sensor 1.
>> GO TO 3.
3.CHECK FOR INTAKE AIR LEAK
1. Start engine and run it at idle.
2. Listen for an intake air leak after the mass air flow sensor.
OK or NG
OK >> GO TO 4.
NG >> Repair or replace.
4.CLEAR THE SELF-LEARNING DATA
With CONSULT-III
1. Start engine and warm it up to normal operating temperature.
2. Select “SELF-LEARNING CONT” in “WORK SUPPORT” mode with CONSULT-III.
3. Clear the self-learning control coefficient by touching “CLEAR”.
4. Run engine for at least 10 minutes at idle speed. Is the 1st trip DTC P0171, P0172, P0174 or P0175 detected?
Is it difficult to start engine?
Without CONSULT-III
1. Start engine and warm it up to normal operating temperature.
2. Turn ignition switch OFF.
3. Disconnect mass air flow sensor harness connector.
4. Restart engine and let it idle for at least 5 seconds.
5. Stop engine and reconnect mass air flow sensor harness con- nector.
6. Make sure DTC P0102 is displayed.
7. Erase the DTC memory. Refer to EC-459, "
DTC Index".
8. Make sure DTC P0000 is displayed.
9. Run engine for at least 10 minutes at idle speed.
Is the 1st trip DTC P0171, P0172, P0174 or P0175 detected?
Is it difficult to start engine?
Ye s o r N o
Yes >> Perform trouble diagnosis for DTC P0171, P0174 or P0172, P0175. Refer to EC-172
or EC-177.
No >> GO TO 5.
5.CHECK HARNESS CONNECTOR
1. Turn ignition switch OFF. Tightening torque: 50 N-m (5.1 kg-m, 37 ft-lb)
BBIA0375E
BBIA0368E
Revision: April 20092010 QX56
Page 1814 of 4210
![INFINITI QX56 2010 Factory Manual PDF ECM
EC-461
< ECU DIAGNOSIS > [VK56DE]
C
D
E
F
G H
I
J
K L
M A
EC
NP
OEVAP GROSS LEAK
P04550455—2×EC-254
EVAP VERY SML LEAK P04560456
×*42 ×EC-261
FUEL LEV SEN SLOSH P04600460—2×EC-269
FUEL LEV INFINITI QX56 2010 Factory Manual PDF ECM
EC-461
< ECU DIAGNOSIS > [VK56DE]
C
D
E
F
G H
I
J
K L
M A
EC
NP
OEVAP GROSS LEAK
P04550455—2×EC-254
EVAP VERY SML LEAK P04560456
×*42 ×EC-261
FUEL LEV SEN SLOSH P04600460—2×EC-269
FUEL LEV](/img/42/57032/w960_57032-1813.png)
ECM
EC-461
< ECU DIAGNOSIS > [VK56DE]
C
D
E
F
G H
I
J
K L
M A
EC
NP
OEVAP GROSS LEAK
P04550455—2×EC-254
EVAP VERY SML LEAK P04560456
×*42 ×EC-261
FUEL LEV SEN SLOSH P04600460—2×EC-269
FUEL LEVEL SENSOR P04610461—2×EC-271
FUEL LEVL SEN/CIRC P04620462—2×EC-273
FUEL LEVL SEN/CIRC P04630463—2×EC-273
VEH SPEED SEN/CIRC*6P0500 0500—2×EC-275
ISC SYSTEM P05060506—2×EC-277
ISC SYSTEM P05070507—2×EC-279
PW ST P SEN/CIRC P05500550—2—EC-281
ECM BACK UP/CIRC P06030603—2×EC-284
ECM P06050605—1 or 2 × or — EC-286
ECM P06070607—1×EC-288
SENSOR POWER/CIRC P06430643—1×EC-289
TRANSMISSION CONT P07000700—1×TM-44
T/M RANGE SENSOR A P07050705—2×TM-45
FLUID TEMP SENSOR A P07100710—2×TM-73
INPUT SPEED SENSOR A P07170717—2×TM-48
OUTPUT SPEED SENSOR*6P0720 0720—2×TM-50
1GR INCORRECT RATION P07310731—2×TM-55
2GR INCORRECT RATION P07320732—2×TM-57
3GR INCORRECT RATION P07330733—2×TM-59
4GR INCORRECT RATION P07340734—2×TM-61
5GR INCORRECT RATION P07350735—2×TM-63
TORQUE CONVERTER P07400740—2×TM-65
TORQUE CONVERTER P07440744—2×TM-67
PC SOLENOID A P07450745—2×TM-69
P-N POS SW/CIRCUIT P08500850—2×EC-292
INTK TIM S/CIRC-B1 P11401140—2×EC-295
INTK TIM S/CIRC-B2 P11451145—2×EC-295
CLOSED LOOP-B1 P11481148—1×EC-299
CLOSED LOOP-B2 P11681168—1×EC-299
TCS C/U FUNCTN P12111211—2—EC-300
TCS/CIRC P12121212—2—EC-301
ENG OVER TEMP P12171217—1×EC-36
CTP LEARNING-B1 P12251225—2—EC-306
CTP LEARNING-B1 P12261226—2—EC-308
COLD START CONTROL P14211421—2×EC-310
BAT CURRENT SENSOR P15501550—2—EC-312
BAT CURRENT SENSOR P15511551—2—EC-316
BAT CURRENT SENSOR P15521552—2—EC-316
BAT CURRENT SENSOR P15531553—2—EC-320
Items
(CONSULT-IIl screen terms) DTC*
1
SRT code Trip
MILReference
page
CONSULT-IIl
GST*
2ECM*3
Revision: April 20092010 QX56
Page 1838 of 4210
![INFINITI QX56 2010 Factory Manual PDF PRECAUTIONSEC-485
< PRECAUTION > [VK56DE]
C
D
E
F
G H
I
J
K L
M A
EC
NP
O
•
Do not operate fuel pump when there is no fuel in lines.
• Tighten fuel hose clamps to the specified torque.
• Do no INFINITI QX56 2010 Factory Manual PDF PRECAUTIONSEC-485
< PRECAUTION > [VK56DE]
C
D
E
F
G H
I
J
K L
M A
EC
NP
O
•
Do not operate fuel pump when there is no fuel in lines.
• Tighten fuel hose clamps to the specified torque.
• Do no](/img/42/57032/w960_57032-1837.png)
PRECAUTIONSEC-485
< PRECAUTION > [VK56DE]
C
D
E
F
G H
I
J
K L
M A
EC
NP
O
•
Do not operate fuel pump when there is no fuel in lines.
• Tighten fuel hose clamps to the specified torque.
• Do not depress accelerator pedal when starting.
• Immediately after starting, do not rev up engine unnecessar-
ily.
• Do not rev up engine ju st prior to shutdown.
• When installing C.B. ham radio or a mobile phone, be sure to
observe the following as it may adversely affect electronic
control systems depending on installation location.
- Keep the antenna as far as possible from the electronic con-
trol units.
- Keep the antenna feeder line more than 20 cm (8 in) away
from the harness of electronic controls.
Do not let them run para llel for a long distance.
- Adjust the antenna and feeder line so that the standing-wave
radio can be kept smaller.
- Be sure to ground the radio to vehicle body.
BBIA0402E
SEF709Y
SEF708Y
Revision: April 20092010 QX56
Page 1855 of 4210
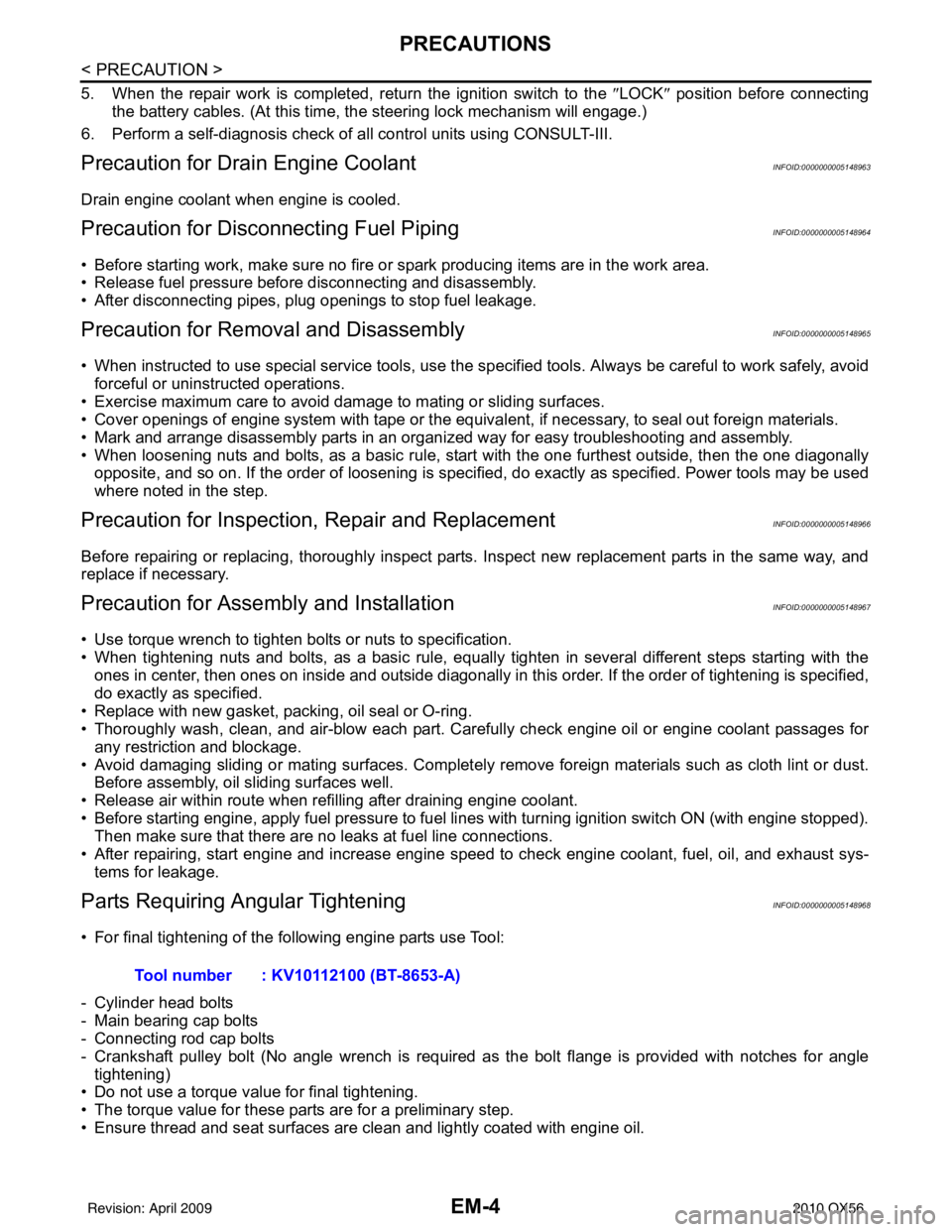
EM-4
< PRECAUTION >
PRECAUTIONS
5. When the repair work is completed, return the ignition switch to the ″LOCK ″ position before connecting
the battery cables. (At this time, the steering lock mechanism will engage.)
6. Perform a self-diagnosis check of a ll control units using CONSULT-III.
Precaution for Drain Engine CoolantINFOID:0000000005148963
Drain engine coolant when engine is cooled.
Precaution for Disconnecting Fuel PipingINFOID:0000000005148964
• Before starting work, make sure no fire or spark producing items are in the work area.
• Release fuel pressure before disconnecting and disassembly.
• After disconnecting pipes, plug openings to stop fuel leakage.
Precaution for Removal and DisassemblyINFOID:0000000005148965
• When instructed to use special service tools, use the s pecified tools. Always be careful to work safely, avoid
forceful or uninstructed operations.
• Exercise maximum care to avoid damage to mating or sliding surfaces.
• Cover openings of engine system with tape or the equivalent, if necessary, to seal out foreign materials.
• Mark and arrange disassembly parts in an organi zed way for easy troubleshooting and assembly.
• When loosening nuts and bolts, as a basic rule, start with the one furthest outside, then the one diagonally opposite, and so on. If the order of loosening is specified, do exactly as specified. Power tools may be used
where noted in the step.
Precaution for Inspection, Repair and ReplacementINFOID:0000000005148966
Before repairing or replacing, thoroughly inspect parts. Inspect new replacement parts in the same way, and
replace if necessary.
Precaution for Assembly and InstallationINFOID:0000000005148967
• Use torque wrench to tighten bolts or nuts to specification.
• When tightening nuts and bolts, as a basic rule, equally tighten in several different steps starting with theones in center, then ones on inside and outside diagonally in this order. If the order of tightening is specified,
do exactly as specified.
• Replace with new gasket, packing, oil seal or O-ring.
• Thoroughly wash, clean, and air-blow each part. Carefully check engine oil or engine coolant passages for any restriction and blockage.
• Avoid damaging sliding or mating surfaces. Completely remove foreign materials such as cloth lint or dust. Before assembly, oil sliding surfaces well.
• Release air within route when refilling after draining engine coolant.
• Before starting engine, apply fuel pressure to fuel lines with turning ignition switch ON (with engine stopped). Then make sure that there are no leaks at fuel line connections.
• After repairing, start engine and increase engine s peed to check engine coolant, fuel, oil, and exhaust sys-
tems for leakage.
Parts Requiring Angular TighteningINFOID:0000000005148968
• For final tightening of the following engine parts use Tool:
- Cylinder head bolts
- Main bearing cap bolts
- Connecting rod cap bolts
- Crankshaft pulley bolt (No angle wrench is required as the bolt flange is provided with notches for angle tightening)
• Do not use a torque value for final tightening.
• The torque value for these parts are for a preliminary step.
• Ensure thread and seat surfaces are clean and lightly coated with engine oil. Tool number : KV10112100 (BT-8653-A)
Revision: April 20092010 QX56
Page 1883 of 4210
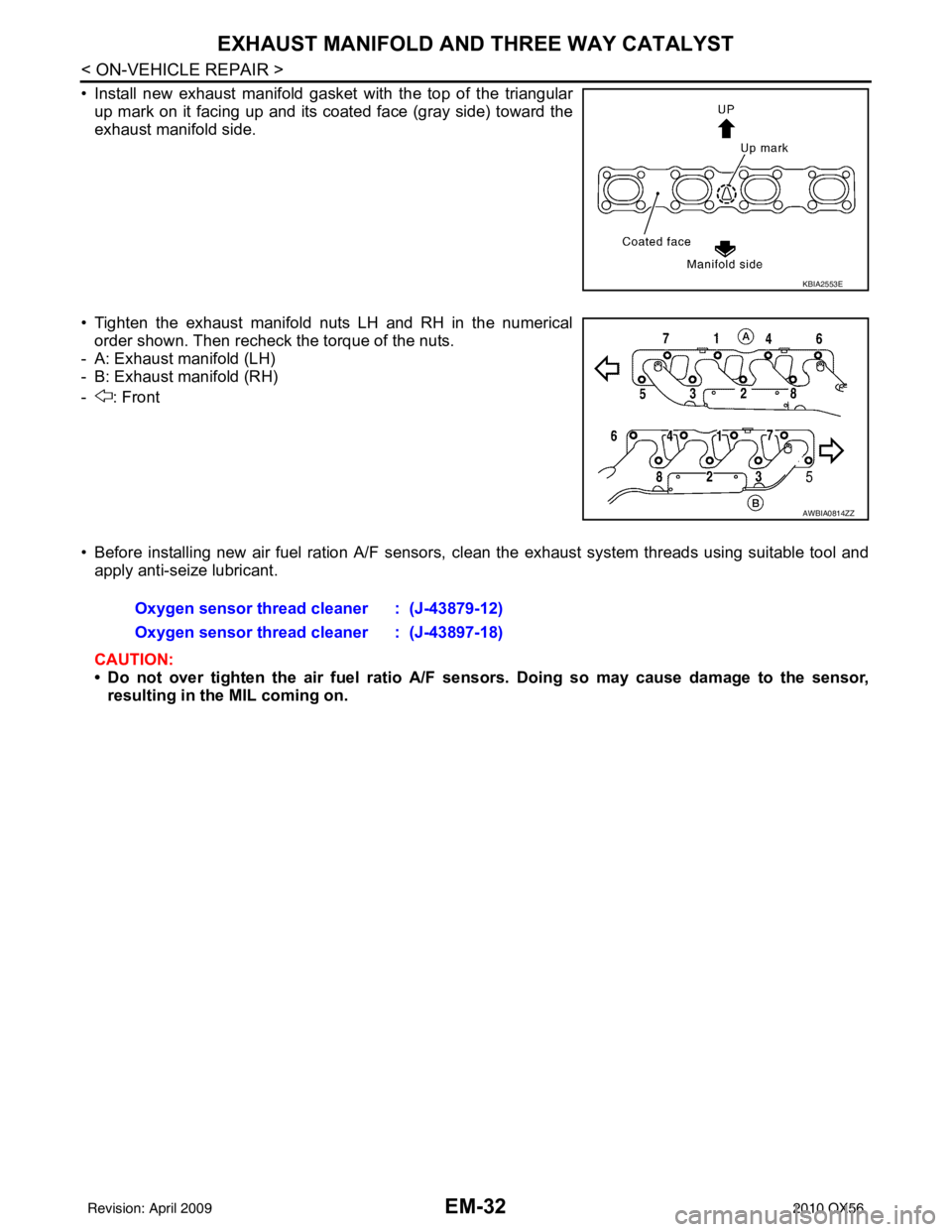
EM-32
< ON-VEHICLE REPAIR >
EXHAUST MANIFOLD AND THREE WAY CATALYST
• Install new exhaust manifold gasket with the top of the triangularup mark on it facing up and its coated face (gray side) toward the
exhaust manifold side.
• Tighten the exhaust manifold nuts LH and RH in the numerical order shown. Then recheck the torque of the nuts.
- A: Exhaust manifold (LH)
- B: Exhaust manifold (RH)
- : Front
• Before installing new air fuel ration A/F sensors, clean the exhaust system threads using suitable tool and
apply anti-seize lubricant.
CAUTION:
• Do not over tighten the air fuel ratio A/F se nsors. Doing so may cause damage to the sensor,
resulting in the MIL coming on.
KBIA2553E
AWBIA0814ZZ
Oxygen sensor thread cleaner : (J-43879-12)
Oxygen sensor thread cleaner : (J-43897-18)
Revision: April 20092010 QX56
Page 1902 of 4210
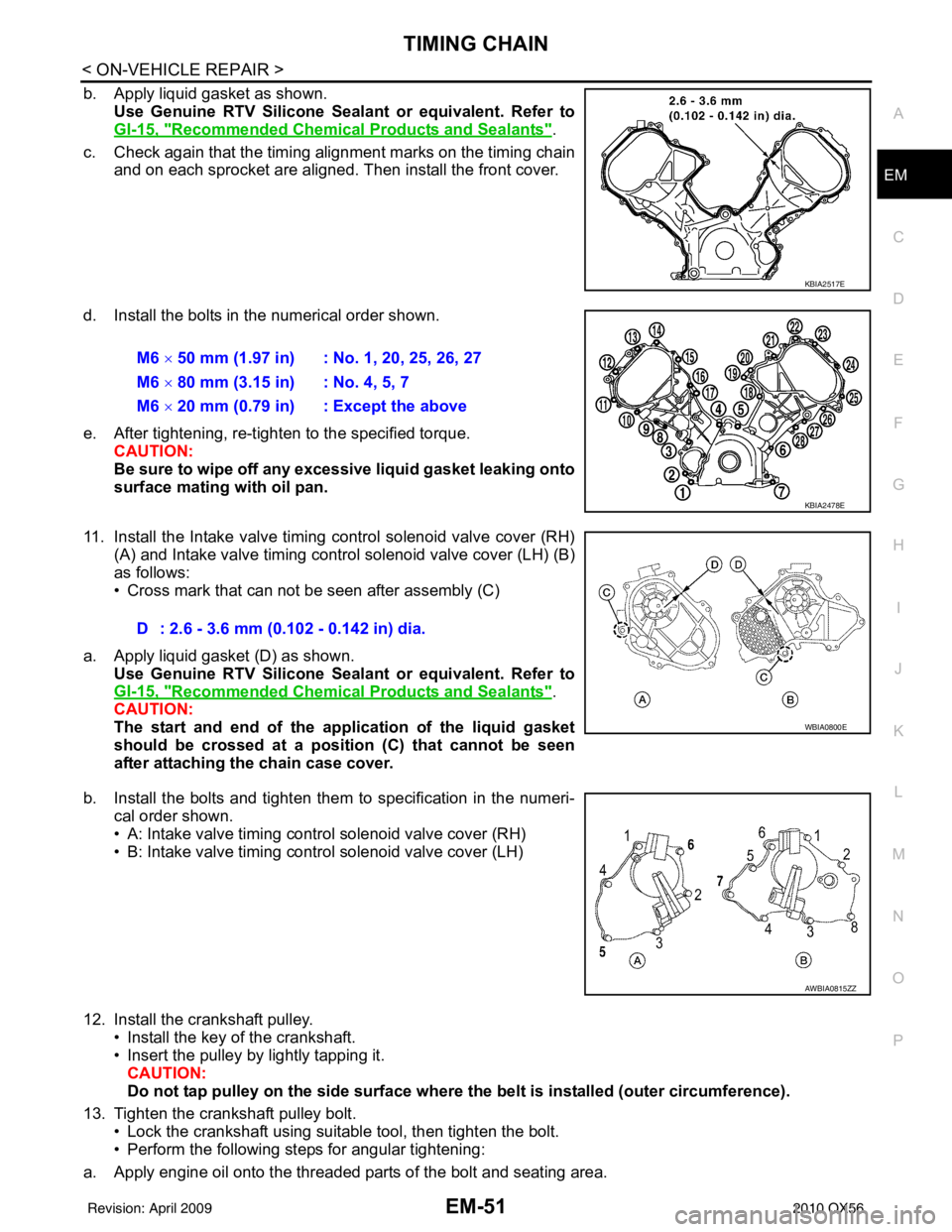
TIMING CHAINEM-51
< ON-VEHICLE REPAIR >
C
DE
F
G H
I
J
K L
M A
EM
NP
O
b. Apply liquid gasket as shown.
Use Genuine RTV Silicone Seal ant or equivalent. Refer to
GI-15, "
Recommended Chemical Products and Sealants".
c. Check again that the timing alignment marks on the timing chain and on each sprocket are aligned. Then install the front cover.
d. Install the bolts in the numerical order shown.
e. After tightening, re-tighten to the specified torque. CAUTION:
Be sure to wipe off any excessive liquid gasket leaking onto
surface mating with oil pan.
11. Install the Intake valve timing control solenoid valve cover (RH) (A) and Intake valve timing control solenoid valve cover (LH) (B)
as follows:
• Cross mark that can not be seen after assembly (C)
a. Apply liquid gasket (D) as shown. Use Genuine RTV Silicone Seal ant or equivalent. Refer to
GI-15, "
Recommended Chemical Products and Sealants".
CAUTION:
The start and end of the appl ication of the liquid gasket
should be crossed at a position (C) that cannot be seen
after attaching the chain case cover.
b. Install the bolts and tighten them to specification in the numeri- cal order shown.
• A: Intake valve timing control solenoid valve cover (RH)
• B: Intake valve timing control solenoid valve cover (LH)
12. Install the crankshaft pulley. • Install the key of the crankshaft.
• Insert the pulley by lightly tapping it.
CAUTION:
Do not tap pulley on the side surface where th e belt is installed (outer circumference).
13. Tighten the crankshaft pulley bolt. • Lock the crankshaft using suitable tool, then tighten the bolt.
• Perform the following steps for angular tightening:
a. Apply engine oil onto the threaded parts of the bolt and seating area.
KBIA2517E
M6 × 50 mm (1.97 in) : No. 1, 20, 25, 26, 27
M6 × 80 mm (3.15 in) : No. 4, 5, 7
M6 × 20 mm (0.79 in) : Except the above
KBIA2478E
D : 2.6 - 3.6 mm (0.102 - 0.142 in) dia.
WBIA0800E
AWBIA0815ZZ
Revision: April 20092010 QX56
Page 1903 of 4210

EM-52
< ON-VEHICLE REPAIR >
TIMING CHAIN
b. Select the one most visible notch of the four on the bolt flange.Corresponding to the selected notch, put a alignment mark
(such as paint) on the crankshaft pulley.
14. Rotate the crankshaft pulley in normal direction (clockwise when viewed from engine front) to check for parts interference.
15. Installation of the remaining components is in the reverse of order of removal.
INSPECTION AFTER INSTALLATION
• Before starting the engine, check oil/fluid levels in cluding engine coolant and engine oil. If the levels are
lower than required quantity, fill to the specified level. Refer to MA-13, "
Fluids and Lubricants".
• Use procedure below to check for fuel leakage.
• Turn ignition switch ON (with engine stopped). With fuel pressure applied to the fuel piping, check for fuel leakage at the connection points.
• Start engine. With engine speed increased, che ck again for fuel leakage at connection points.
• Run engine to check for unusual noise and vibration. NOTE:
If hydraulic pressure inside timing chain tensioner drops after removal and installation, slack in the guide
may generate a pounding noise during and just after engine start. However, this is normal. Noise will stop
after hydraulic pressure rises.
• Warm up engine thoroughly to make sure there is no leakage of fuel, exhaust gas, or any oils/fluids including engine oil and engine coolant.
• Bleed air from passages in lines and hoses, such as in cooling system.
• After cooling down the engine, again check oil/fluid levels including engine oil and engine coolant. Refill to
specified level if necessary.
• Summary of the inspection items:
*Transmission/transaxle/CVT fluid, power steering fluid, brake fluid, etc.
Crankshaft pulley bolt torque
Step 1 : 93.1 N·m (9.5 kg-m, 69 ft-lb)
Step 2 : additional 90 ° (angle tightening)
KBIA2519E
Item Before starting engine Engine runningAfter engine stopped
Engine coolant LevelLeakage Level
Engine oil LevelLeakage Level
Other oils and fluids* LevelLeakage Level
Fuel LeakageLeakageLeakage
Exhaust gas —Leakage —
Revision: April 20092010 QX56