light INFINITI QX56 2011 Factory Service Manual
[x] Cancel search | Manufacturer: INFINITI, Model Year: 2011, Model line: QX56, Model: INFINITI QX56 2011Pages: 5598, PDF Size: 94.53 MB
Page 1746 of 5598
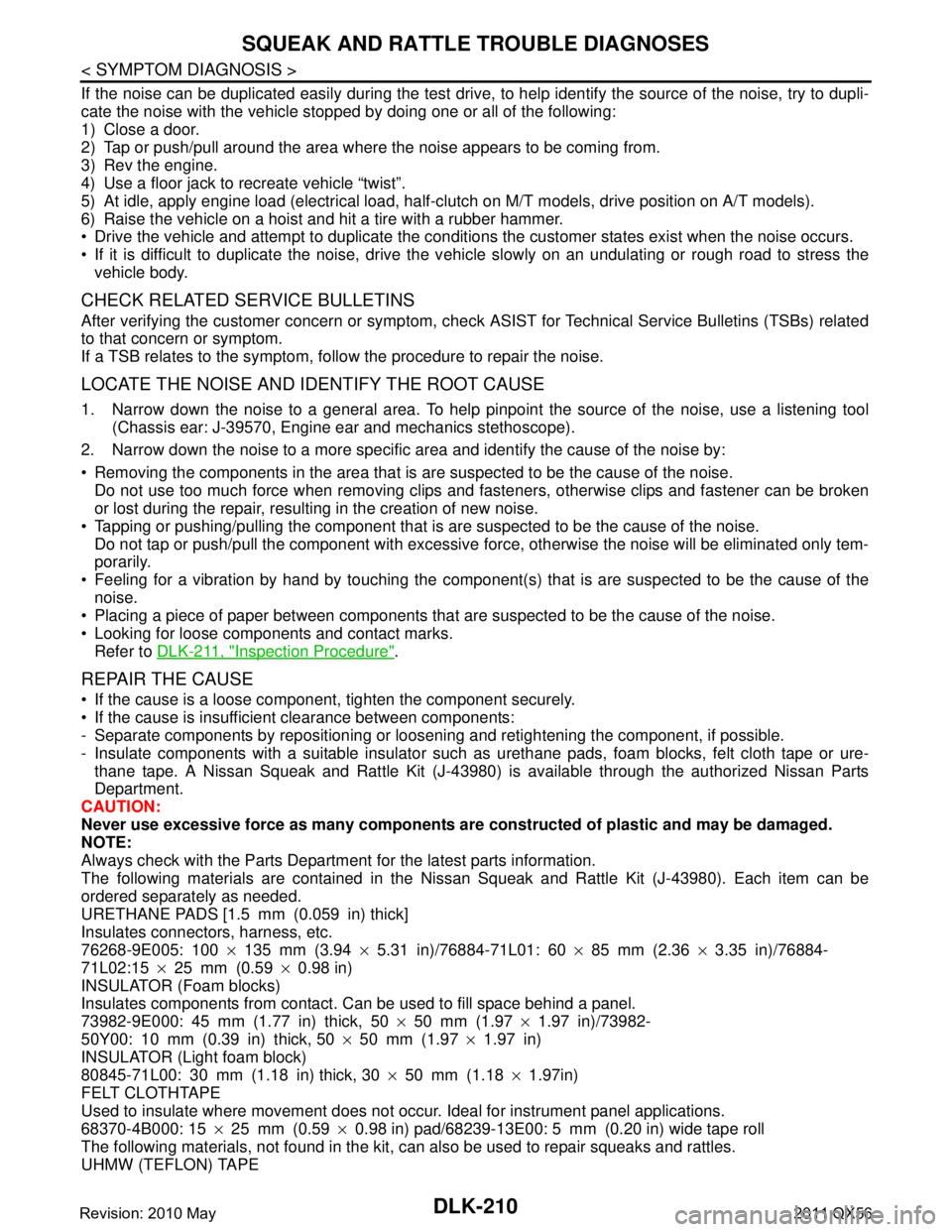
DLK-210
< SYMPTOM DIAGNOSIS >
SQUEAK AND RATTLE TROUBLE DIAGNOSES
If the noise can be duplicated easily during the test drive, to help identify the source of the noise, try to dupli-
cate the noise with the vehicle stopped by doing one or all of the following:
1) Close a door.
2) Tap or push/pull around the area where the noise appears to be coming from.
3) Rev the engine.
4) Use a floor jack to recreate vehicle “twist”.
5) At idle, apply engine load (electrical load, half-cl utch on M/T models, drive position on A/T models).
6) Raise the vehicle on a hoist and hit a tire with a rubber hammer.
Drive the vehicle and attempt to duplicate the conditions the customer states exist when the noise occurs.
If it is difficult to duplicate the noise, drive the v ehicle slowly on an undulating or rough road to stress the
vehicle body.
CHECK RELATED SERVICE BULLETINS
After verifying the customer concern or symptom, chec k ASIST for Technical Service Bulletins (TSBs) related
to that concern or symptom.
If a TSB relates to the symptom, follo w the procedure to repair the noise.
LOCATE THE NOISE AND IDENTIFY THE ROOT CAUSE
1. Narrow down the noise to a general area. To help pi npoint the source of the noise, use a listening tool
(Chassis ear: J-39570, Engine ear and mechanics stethoscope).
2. Narrow down the noise to a more specific area and identify the cause of the noise by:
Removing the components in the area that is are suspected to be the cause of the noise.
Do not use too much force when removing clips and fasteners, otherwise clips and fastener can be broken
or lost during the repair, resulting in the creation of new noise.
Tapping or pushing/pulling the component that is are suspected to be the cause of the noise.
Do not tap or push/pull the component with excessive force, otherwise the noise will be eliminated only tem-
porarily.
Feeling for a vibration by hand by touching the component (s) that is are suspected to be the cause of the
noise.
Placing a piece of paper between components that are suspected to be the cause of the noise.
Looking for loose components and contact marks. Refer to DLK-211, "
Inspection Procedure".
REPAIR THE CAUSE
If the cause is a loose component, tighten the component securely.
If the cause is insufficient clearance between components:
- Separate components by repositioning or loos ening and retightening the component, if possible.
- Insulate components with a suitable insulator such as urethane pads, foam blocks, felt cloth tape or ure-
thane tape. A Nissan Squeak and Rattle Kit (J-43980) is available through the authorized Nissan Parts
Department.
CAUTION:
Never use excessive force as many components are constructed of plastic and may be damaged.
NOTE:
Always check with the Parts Departm ent for the latest parts information.
The following materials are contained in the Nissan Squeak and Rattle Kit (J-43980). Each item can be
ordered separately as needed.
URETHANE PADS [1.5 mm (0.059 in) thick]
Insulates connectors, harness, etc.
76268-9E005: 100 ×135 mm (3.94 ×5.31 in)/76884-71L01: 60 ×85 mm (2.36 ×3.35 in)/76884-
71L02:15 ×25 mm (0.59 ×0.98 in)
INSULATOR (Foam blocks)
Insulates components from contact. Can be used to fill space behind a panel.
73982-9E000: 45 mm (1.77 in) thick, 50 ×50 mm (1.97 ×1.97 in)/73982-
50Y00: 10 mm (0.39 in) thick, 50 ×50 mm (1.97 ×1.97 in)
INSULATOR (Light foam block)
80845-71L00: 30 mm (1.18 in) thick, 30 ×50 mm (1.18 ×1.97in)
FELT CLOTHTAPE
Used to insulate where movement does not occu r. Ideal for instrument panel applications.
68370-4B000: 15 ×25 mm (0.59 ×0.98 in) pad/68239-13E00: 5 mm (0.20 in) wide tape roll
The following materials, not found in the kit, can also be used to repair squeaks and rattles.
UHMW (TEFLON) TAPE
Revision: 2010 May2011 QX56
Page 1747 of 5598
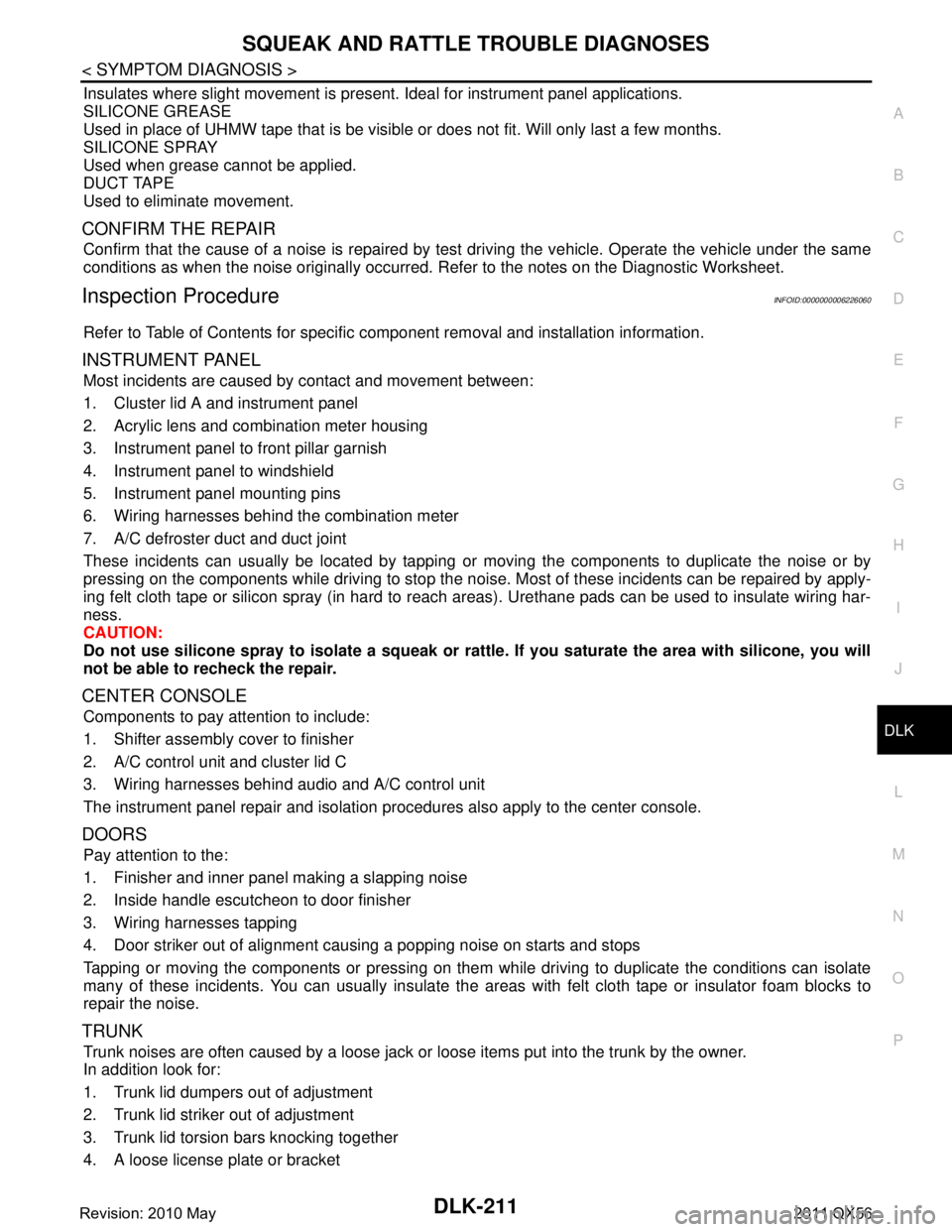
SQUEAK AND RATTLE TROUBLE DIAGNOSESDLK-211
< SYMPTOM DIAGNOSIS >
C
DE
F
G H
I
J
L
M A
B
DLK
N
O P
Insulates where slight movement is present. Ideal for instrument panel applications.
SILICONE GREASE
Used in place of UHMW tape that is be visible or does not fit. Will only last a few months.
SILICONE SPRAY
Used when grease cannot be applied.
DUCT TAPE
Used to eliminate movement.
CONFIRM THE REPAIR
Confirm that the cause of a noise is repaired by test driving the vehicle. Operate the vehicle under the same
conditions as when the noise originally occurred. Refer to the notes on the Diagnostic Worksheet.
Inspection ProcedureINFOID:0000000006226060
Refer to Table of Contents for specific component removal and installation information.
INSTRUMENT PANEL
Most incidents are caused by contact and movement between:
1. Cluster lid A and instrument panel
2. Acrylic lens and combination meter housing
3. Instrument panel to front pillar garnish
4. Instrument panel to windshield
5. Instrument panel mounting pins
6. Wiring harnesses behind the combination meter
7. A/C defroster duct and duct joint
These incidents can usually be located by tapping or moving the components to duplicate the noise or by
pressing on the components while driving to stop the noi se. Most of these incidents can be repaired by apply-
ing felt cloth tape or silicon spray (in hard to reach areas). Urethane pads can be used to insulate wiring har-
ness.
CAUTION:
Do not use silicone spray to isolate a squeak or ra ttle. If you saturate the area with silicone, you will
not be able to recheck the repair.
CENTER CONSOLE
Components to pay attention to include:
1. Shifter assembly cover to finisher
2. A/C control unit and cluster lid C
3. Wiring harnesses behind audio and A/C control unit
The instrument panel repair and isolation pr ocedures also apply to the center console.
DOORS
Pay attention to the:
1. Finisher and inner panel making a slapping noise
2. Inside handle escutcheon to door finisher
3. Wiring harnesses tapping
4. Door striker out of alignment causing a popping noise on starts and stops
Tapping or moving the components or pressing on them while driving to duplicate the conditions can isolate
many of these incidents. You can usually insulate the areas with felt cloth tape or insulator foam blocks to
repair the noise.
TRUNK
Trunk noises are often caused by a loose jack or loose items put into the trunk by the owner.
In addition look for:
1. Trunk lid dumpers out of adjustment
2. Trunk lid striker out of adjustment
3. Trunk lid torsion bars knocking together
4. A loose license plate or bracket
Revision: 2010 May2011 QX56
Page 1748 of 5598
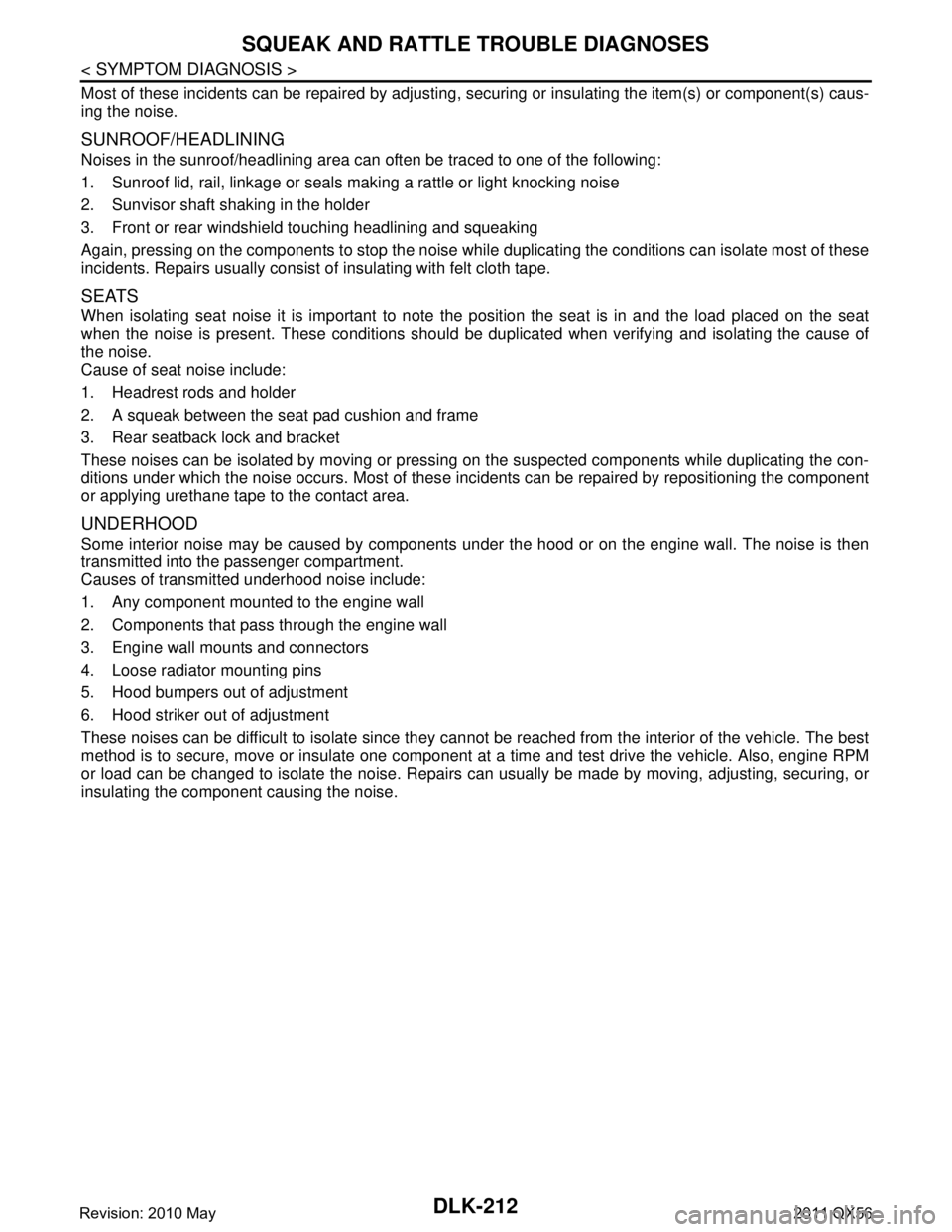
DLK-212
< SYMPTOM DIAGNOSIS >
SQUEAK AND RATTLE TROUBLE DIAGNOSES
Most of these incidents can be repaired by adjusting, securing or insulating the item(s) or component(s) caus-
ing the noise.
SUNROOF/HEADLINING
Noises in the sunroof/headlining area c an often be traced to one of the following:
1. Sunroof lid, rail, linkage or seals making a rattle or light knocking noise
2. Sunvisor shaft shaking in the holder
3. Front or rear windshield touching headlining and squeaking
Again, pressing on the components to stop the noise while duplicating the conditions can isolate most of these
incidents. Repairs usually consist of insulating with felt cloth tape.
SEATS
When isolating seat noise it is important to note t he position the seat is in and the load placed on the seat
when the noise is present. These conditions should be duplicated when verifying and isolating the cause of
the noise.
Cause of seat noise include:
1. Headrest rods and holder
2. A squeak between the seat pad cushion and frame
3. Rear seatback lock and bracket
These noises can be isolated by moving or pressing on the suspected components while duplicating the con-
ditions under which the noise occurs. Most of thes e incidents can be repaired by repositioning the component
or applying urethane tape to the contact area.
UNDERHOOD
Some interior noise may be caused by components under the hood or on the engine wall. The noise is then
transmitted into the passenger compartment.
Causes of transmitted underhood noise include:
1. Any component mounted to the engine wall
2. Components that pass through the engine wall
3. Engine wall mounts and connectors
4. Loose radiator mounting pins
5. Hood bumpers out of adjustment
6. Hood striker out of adjustment
These noises can be difficult to isolate since they cannot be reached from the interior of the vehicle. The best
method is to secure, move or insulate one component at a time and test drive the \
vehicle. Also, engine RPM
or load can be changed to isolate the noise. Repairs can usually be made by moving, adjusting, securing, or
insulating the component causing the noise.
Revision: 2010 May2011 QX56
Page 1753 of 5598
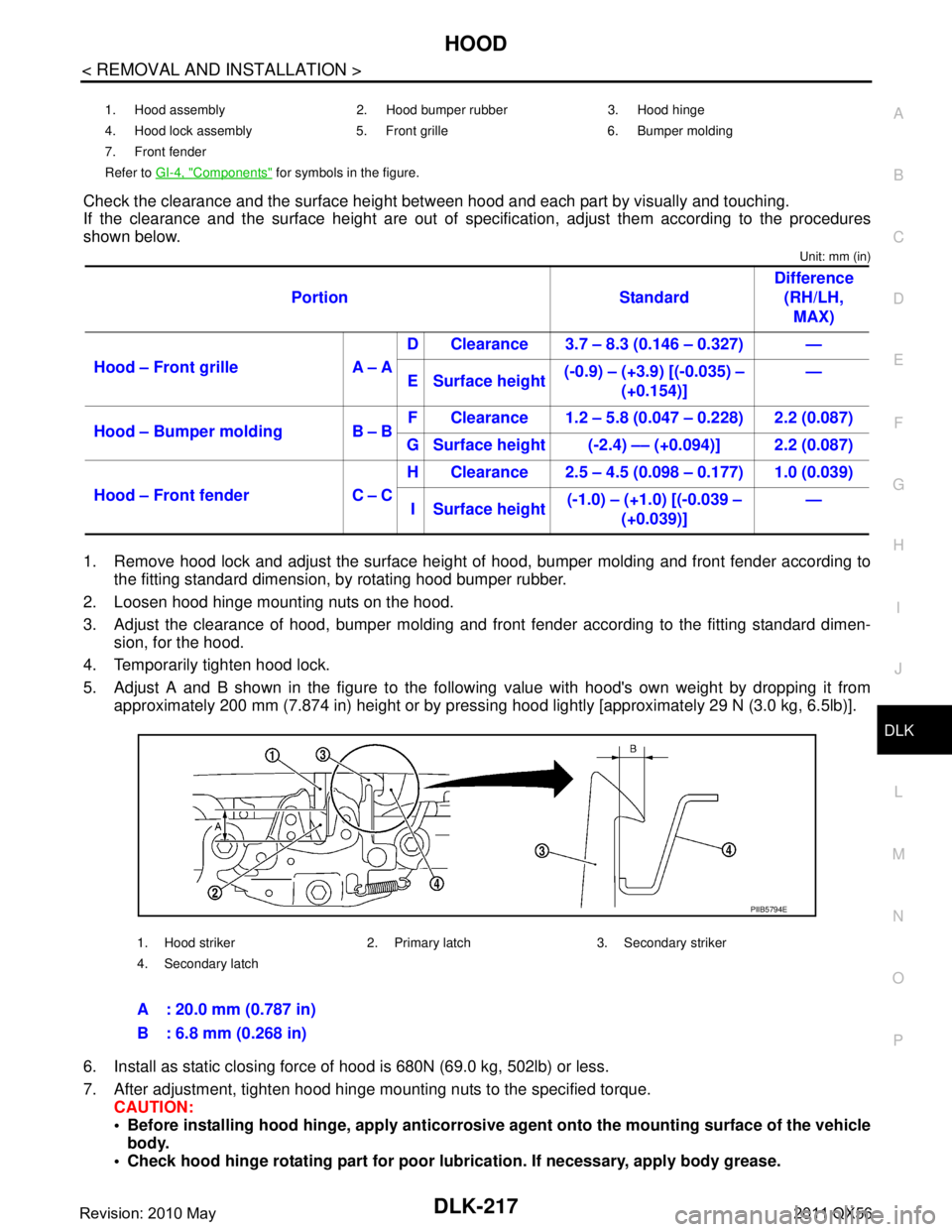
HOOD
DLK-217
< REMOVAL AND INSTALLATION >
C
D E
F
G H
I
J
L
M A
B
DLK
N
O P
Check the clearance and the surface height betw een hood and each part by visually and touching.
If the clearance and the surface height are out of spec ification, adjust them according to the procedures
shown below.
Unit: mm (in)
1. Remove hood lock and adjust the surface height of hood, bumper molding and front fender according to
the fitting standard dimension, by rotating hood bumper rubber.
2. Loosen hood hinge mounting nuts on the hood.
3. Adjust the clearance of hood, bumper molding and fr ont fender according to the fitting standard dimen-
sion, for the hood.
4. Temporarily tighten hood lock.
5. Adjust A and B shown in the figure to the following value with hood's own weight by dropping it from approximately 200 mm (7.874 in) height or by pressi ng hood lightly [approximately 29 N (3.0 kg, 6.5lb)].
6. Install as static closing force of hood is 680N (69.0 kg, 502lb) or less.
7. After adjustment, tighten hood hinge mounting nuts to the specified torque. CAUTION:
Before installing hood hinge, apply anticorrosive agent onto th e mounting surface of the vehicle
body.
Check hood hinge rotating pa rt for poor lubrication. If necessary, apply body grease.
1. Hood assembly 2. Hood bumper rubber 3. Hood hinge
4. Hood lock assembly 5. Front grille 6. Bumper molding
7. Front fender
Refer to GI-4, "
Components" for symbols in the figure.
Portion Standard Difference
(RH/LH, MAX)
Hood – Front grille A – A D Clearance 3.7 – 8.3 (0.146 – 0.327) —
E Surface height (-0.9) – (+3.9) [(-0.035) –
(+0.154)] —
Hood – Bumper molding B – B F Clearance 1.2 – 5.8 (0.047 – 0.228) 2.2 (0.087)
G Surface height (-2.4) –– (+0.094)] 2.2 (0.087)
Hood – Front fender C – C H Clearance 2.5 – 4.5 (0.098 – 0.177) 1.0 (0.039)
I Surface height (-1.0) – (+1.0) [(-0.039 –
(+0.039)] —
1. Hood striker 2. Primary latch 3. Secondary striker
4. Secondary latch
A : 20.0 mm (0.787 in)
B : 6.8 mm (0.268 in)
PIIB5794E
Revision: 2010 May2011 QX56
Page 1771 of 5598
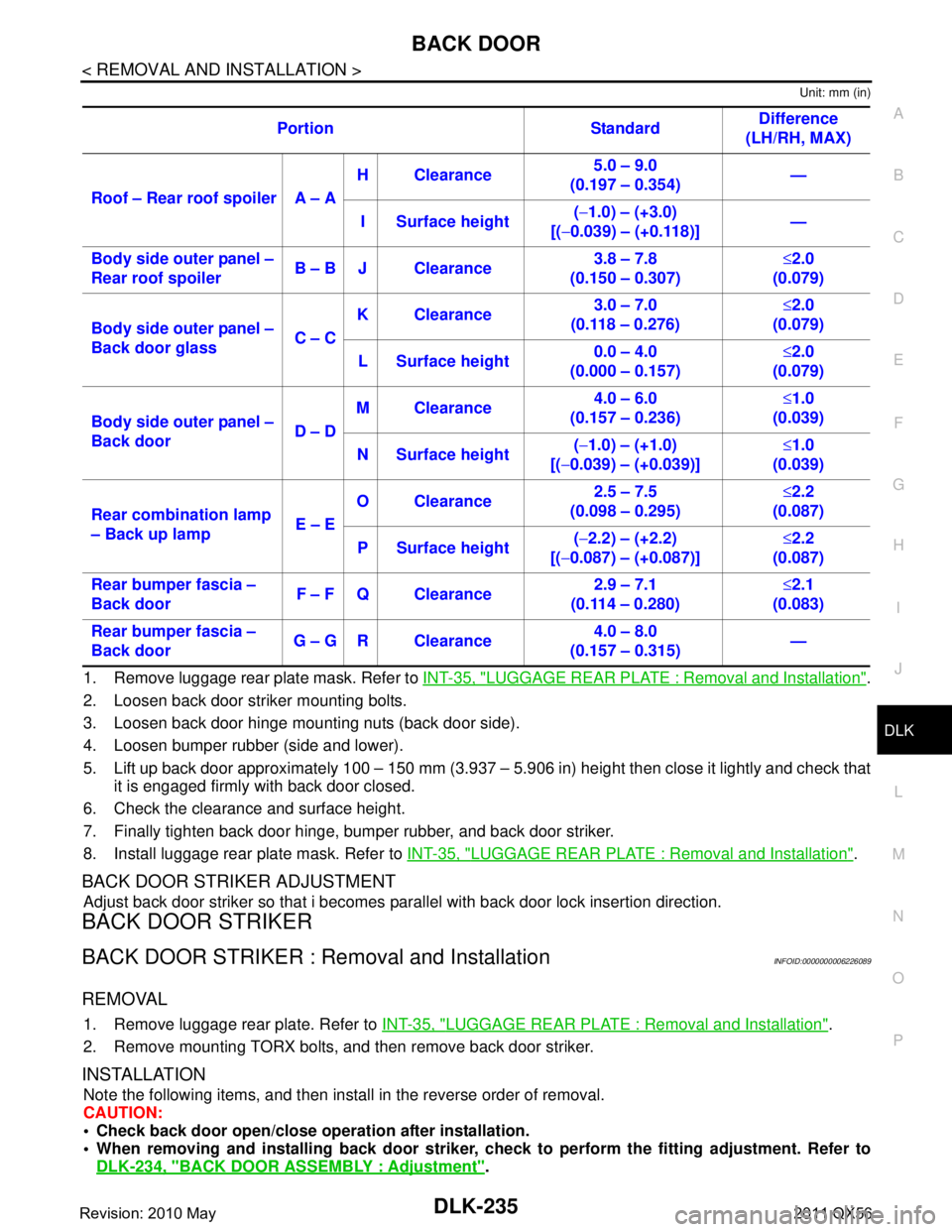
BACK DOORDLK-235
< REMOVAL AND INSTALLATION >
C
DE
F
G H
I
J
L
M A
B
DLK
N
O P
Unit: mm (in)
1. Remove luggage rear plate mask. Refer to INT-35, "LUGGAGE REAR PLATE : Removal and Installation".
2. Loosen back door striker mounting bolts.
3. Loosen back door hinge mounting nuts (back door side).
4. Loosen bumper rubber (side and lower).
5. Lift up back door approximately 100 – 150 mm (3.937 – 5.906 in) height then close it lightly and check that
it is engaged firmly with back door closed.
6. Check the clearance and surface height.
7. Finally tighten back door hinge, bumper rubber, and back door striker.
8. Install luggage rear plate mask. Refer to INT-35, "
LUGGAGE REAR PLATE : Removal and Installation".
BACK DOOR STRIKER ADJUSTMENT
Adjust back door striker so that i becomes parallel with back door lock insertion direction.
BACK DOOR STRIKER
BACK DOOR STRIKER : Removal and InstallationINFOID:0000000006226089
REMOVAL
1. Remove luggage rear plate. Refer to INT-35, "LUGGAGE REAR PLATE : Removal and Installation".
2. Remove mounting TORX bolts, and then remove back door striker.
INSTALLATION
Note the following items, and then install in the reverse order of removal.
CAUTION:
Check back door open/close ope ration after installation.
When removing and installing b ack door striker, check to perform th e fitting adjustment. Refer to
DLK-234, "
BACK DOOR ASSEMBLY : Adjustment".
Portion Standard
Difference
(LH/RH, MAX)
Roof – Rear roof spoiler A – A H Clearance
5.0 – 9.0
(0.197 – 0.354) —
I Surface height (
− 1.0) – (+3.0)
[( −0.039) – (+0.118)] —
Body side outer panel –
Rear roof spoiler B – B J Clearance 3.8 – 7.8
(0.150 – 0.307) ≤
2.0
(0.079)
Body side outer panel –
Back door glass C – CK Clearance
3.0 – 7.0
(0.118 – 0.276) ≤
2.0
(0.079)
L Surface height 0.0 – 4.0
(0.000 – 0.157) ≤
2.0
(0.079)
Body side outer panel –
Back door D – DM Clearance
4.0 – 6.0
(0.157 – 0.236) ≤
1.0
(0.039)
N Surface height (
− 1.0) – (+1.0)
[( −0.039) – (+0.039)] ≤
1.0
(0.039)
Rear combination lamp
– Back up lamp E – EO Clearance
2.5 – 7.5
(0.098 – 0.295) ≤
2.2
(0.087)
P Surface height (
− 2.2) – (+2.2)
[( −0.087) – (+0.087)] ≤
2.2
(0.087)
Rear bumper fascia –
Back door F – F Q Clearance 2.9 – 7.1
(0.114 – 0.280) ≤
2.1
(0.083)
Rear bumper fascia –
Back door G – G R Clearance 4.0 – 8.0
(0.157 – 0.315) —
Revision: 2010 May2011 QX56
Page 1899 of 5598
![INFINITI QX56 2011 Factory Service Manual
4WD WARNING LAMPDLN-97
< DTC/CIRCUIT DIAGNOSIS > [TRANSFER: ATX90A]
C
EF
G H
I
J
K L
M A
B
DLN
N
O P
4WD WARNING LAMP
Component Function CheckINFOID:0000000006222308
1.CHECK 4WD WARNING LAMP FUNCTION INFINITI QX56 2011 Factory Service Manual
4WD WARNING LAMPDLN-97
< DTC/CIRCUIT DIAGNOSIS > [TRANSFER: ATX90A]
C
EF
G H
I
J
K L
M A
B
DLN
N
O P
4WD WARNING LAMP
Component Function CheckINFOID:0000000006222308
1.CHECK 4WD WARNING LAMP FUNCTION](/img/42/57033/w960_57033-1898.png)
4WD WARNING LAMPDLN-97
< DTC/CIRCUIT DIAGNOSIS > [TRANSFER: ATX90A]
C
EF
G H
I
J
K L
M A
B
DLN
N
O P
4WD WARNING LAMP
Component Function CheckINFOID:0000000006222308
1.CHECK 4WD WARNING LAMP FUNCTION
1. Turn the ignition switch OFF to ON.
2. Check that 4WD warning lamp light up.
Is the inspection result normal?
YES >> INSPECTION END
NO >> Proceed diagnosis procedure. Refer to DLN-97, "
Diagnosis Procedure".
Diagnosis ProcedureINFOID:0000000006222309
1.CHECK POWER SUPPLY AND GROUND CIRCUIT
Perform the trouble diagnosis for power supply and ground circuit. Refer to DLN-64, "
Diagnosis Procedure".
Is the inspection result normal?
YES >> GO TO 2.
NO >> Repair or replace the error-detected parts.
2.PERFORM SELF-DIAGNOSIS
With CONSULT-III
Perform self-diagnosis for “ALL MODE AWD/4WD”.
Is any DTC detected?
YES >> Check the DTC.
NO >> GO TO 3.
3.CHECK 4WD WARNING LAMP SIGNAL
With CONSULT-III
1. Turn the ignition switch ON. CAUTION:
Never start the engine.
2. Check “4WD FAIL LAMP” of CONSULT-III “DATA MONITOR” for “ALL MODE AWD/4WD”.
Does the item on
“DATA MONITOR” indicate “On”?
YES >> Check combination meter. Refer to MWI-64, "COMBINATION METER : Diagnosis Procedure".
NO >> Replace transfer control unit. Refer to DLN-107, "
Removal and Installation".
Revision: 2010 May2011 QX56
Page 1901 of 5598
![INFINITI QX56 2011 Factory Service Manual
HEAVY TIGHT-CORNER BRAKING SYMPTOM OCCURS
DLN-99
< SYMPTOM DIAGNOSIS > [TRANSFER: ATX90A]
C
EF
G H
I
J
K L
M A
B
DLN
N
O P
SYMPTOM DIAGNOSIS
HEAVY TIGHT-CORNER BRAKING SYMPTOM OCCURS
DescriptionINFOI INFINITI QX56 2011 Factory Service Manual
HEAVY TIGHT-CORNER BRAKING SYMPTOM OCCURS
DLN-99
< SYMPTOM DIAGNOSIS > [TRANSFER: ATX90A]
C
EF
G H
I
J
K L
M A
B
DLN
N
O P
SYMPTOM DIAGNOSIS
HEAVY TIGHT-CORNER BRAKING SYMPTOM OCCURS
DescriptionINFOI](/img/42/57033/w960_57033-1900.png)
HEAVY TIGHT-CORNER BRAKING SYMPTOM OCCURS
DLN-99
< SYMPTOM DIAGNOSIS > [TRANSFER: ATX90A]
C
EF
G H
I
J
K L
M A
B
DLN
N
O P
SYMPTOM DIAGNOSIS
HEAVY TIGHT-CORNER BRAKING SYMPTOM OCCURS
DescriptionINFOID:0000000006222312
Heavy tight-corner braking symptom o ccurs when the vehicle is driven and the steering wheel is turned fully to
either side after the engine is started.
NOTE:
Light tight-corner braking symptom may occur dependi ng on driving conditions. This is not malfunction.
Diagnosis ProcedureINFOID:0000000006222313
1.PERFORM ECM SELF-DIAGNOSIS
With CONSULT-III
Perform self-diagnosis for “ECM”.
Is any DTC detected?
YES >> Check the DTC. Refer to EC-98, "DTC Index".
NO >> GO TO 2.
2.PERFORM SELF-DIAGNOSIS
With CONSULT-III
Perform self-diagnosis for “ALL MODE AWD/4WD”.
Is any DTC detected?
YES >> Check the DTC. Refer to DLN-29, "DTC Index".
NO >> GO TO 3.
3.CHECK TRANSFER INTERNAL FUNCTION
With CONSULT-III
1. Remove transfer control actuator. Refer to DLN-114, "
Removal and Installation".
2. Turn the actuator shaft. Refer to DLN-114, "
Inspection".
3. Check “ROTARY POSI SEN” of CONSULT-II I “DATA MONITOR” for “ALL MODE AWD/4WD”.
Is the inspection result normal?
YES >> INSPECTION END
NO >> Transfer assembly is mechanical malfunction. Replace transfer assembly. Refer to DLN-121,
"Removal and Installation".
Monitor item Condition Status
ROTARY POSI SEN Turn the actuator shaft. Value is changing
Revision: 2010 May2011 QX56
Page 1932 of 5598
![INFINITI QX56 2011 Factory Service Manual
DLN-130
< REMOVAL AND INSTALLATION >[FRONT PROPELLER SHAFT: 2F P15]
FRONT PROPELLER SHAFT
1. Put a matching mark (A) between propeller shaft and flange
yoke and remove snap rings (1).
CAUTION:
For ma INFINITI QX56 2011 Factory Service Manual
DLN-130
< REMOVAL AND INSTALLATION >[FRONT PROPELLER SHAFT: 2F P15]
FRONT PROPELLER SHAFT
1. Put a matching mark (A) between propeller shaft and flange
yoke and remove snap rings (1).
CAUTION:
For ma](/img/42/57033/w960_57033-1931.png)
DLN-130
< REMOVAL AND INSTALLATION >[FRONT PROPELLER SHAFT: 2F P15]
FRONT PROPELLER SHAFT
1. Put a matching mark (A) between propeller shaft and flange
yoke and remove snap rings (1).
CAUTION:
For matching mark, use paint. Never damage the surface.
2. Lightly tap bottom of yoke using a copper hammer and remove journal bearing.
CAUTION:
Never damage the yoke.
ASSEMBLY
1. Install journal bearing to journal.CAUTION:
Never reuse journal or journal bearing.
Always replace journal, journal b earing, and snap rings as a set.
Apply multi-purpose grease to journal bearing.
2. Install bearing (1) using a vise. CAUTION:
Never damage bearing or flange yoke.
3. Install journal to propeller shaft so that grease nipple (1) on jour- nal portion is in the same direction.
CAUTION:
Never reuse journal.
4. Measure journal axial play. If necessary, select the appropriate snap ring.
JPDID0375ZZ
PDA0034D
JSDIA0370ZZ
JPDID0327ZZ
Revision: 2010 May2011 QX56
Page 1940 of 5598
![INFINITI QX56 2011 Factory Service Manual
DLN-138
< REMOVAL AND INSTALLATION >[REAR PROPELLER SHAFT: 2F P26]
REAR PROPELLER SHAFT
1. Put a matching mark between propeller shaft and flange yoke
and remove snap rings (1).
CAUTION:
For matching INFINITI QX56 2011 Factory Service Manual
DLN-138
< REMOVAL AND INSTALLATION >[REAR PROPELLER SHAFT: 2F P26]
REAR PROPELLER SHAFT
1. Put a matching mark between propeller shaft and flange yoke
and remove snap rings (1).
CAUTION:
For matching](/img/42/57033/w960_57033-1939.png)
DLN-138
< REMOVAL AND INSTALLATION >[REAR PROPELLER SHAFT: 2F P26]
REAR PROPELLER SHAFT
1. Put a matching mark between propeller shaft and flange yoke
and remove snap rings (1).
CAUTION:
For matching mark, use paint. Never damage the surface.
2. Lightly tap bottom of yoke using a copper hammer and remove journal bearing.
CAUTION:
Never damage the yoke.
3. Remove grease nipple.
ASSEMBLY
1. Install journal bearing to journal. CAUTION:
Never reuse journal or journal bearing.
Always replace journal, journal b earing, and snap rings as a set.
Apply multi-purpose grease to journal bearing.
2. Install bearing (1) using a vise. CAUTION:
Never damage bearing or flange yoke.
3. Install journal to propeller shaft so that grease nipple (1) on jour- nal portion is in the same direction.
CAUTION:
Never reuse journal.
JSDIA0369ZZ
PDA0034D
JSDIA0370ZZ
JPDID0327ZZ
Revision: 2010 May2011 QX56
Page 1947 of 5598
![INFINITI QX56 2011 Factory Service Manual
REAR PROPELLER SHAFTDLN-145
< REMOVAL AND INSTALLATION > [REAR PROPELLER SHAFT: 2S1410]
C
EF
G H
I
J
K L
M A
B
DLN
N
O P
2. Remove snap ring.
3. Lightly tap bottom of yoke using a copper hammer and r INFINITI QX56 2011 Factory Service Manual
REAR PROPELLER SHAFTDLN-145
< REMOVAL AND INSTALLATION > [REAR PROPELLER SHAFT: 2S1410]
C
EF
G H
I
J
K L
M A
B
DLN
N
O P
2. Remove snap ring.
3. Lightly tap bottom of yoke using a copper hammer and r](/img/42/57033/w960_57033-1946.png)
REAR PROPELLER SHAFTDLN-145
< REMOVAL AND INSTALLATION > [REAR PROPELLER SHAFT: 2S1410]
C
EF
G H
I
J
K L
M A
B
DLN
N
O P
2. Remove snap ring.
3. Lightly tap bottom of yoke using a copper hammer and remove journal bearing.
CAUTION:
Never damage the yoke.
ASSEMBLY
1. Install journal bearing to journal.CAUTION:
Never reuse journal or journal bearing.
Always replace journal, journal b earing, and snap rings as a set.
Apply multi-purpose grease to journal bearing.
2. Install bearing (1) using a vise. CAUTION:
Never damage bearing or flange yoke.
3. Measure journal axial play. If necessary, select the appropriate snap ring.
a. While pushing to 98 N·m (10 kg-m, 72 ft-lb), check the clearance between snap ring (1) and needle bearing (2).
b. If journal axial play is outside the specification, use a thicker/ thinner snap ring to adjust.
CAUTION:
Never reuse snap ring.
Select snap rings so that thickness difference between LH
and RH is within 0.02 mm (0.0008 in).
APD011
PDA0034D
JSDIA0370ZZ
Journal axial play : Refer to DLN-147,
"Journal Axial Play"
JPDID0331ZZ
Revision: 2010 May2011 QX56