brakes ISUZU TFS SERIES 1997 Owner's Manual
[x] Cancel search | Manufacturer: ISUZU, Model Year: 1997, Model line: TFS SERIES, Model: ISUZU TFS SERIES 1997Pages: 1600, PDF Size: 40.98 MB
Page 344 of 1600
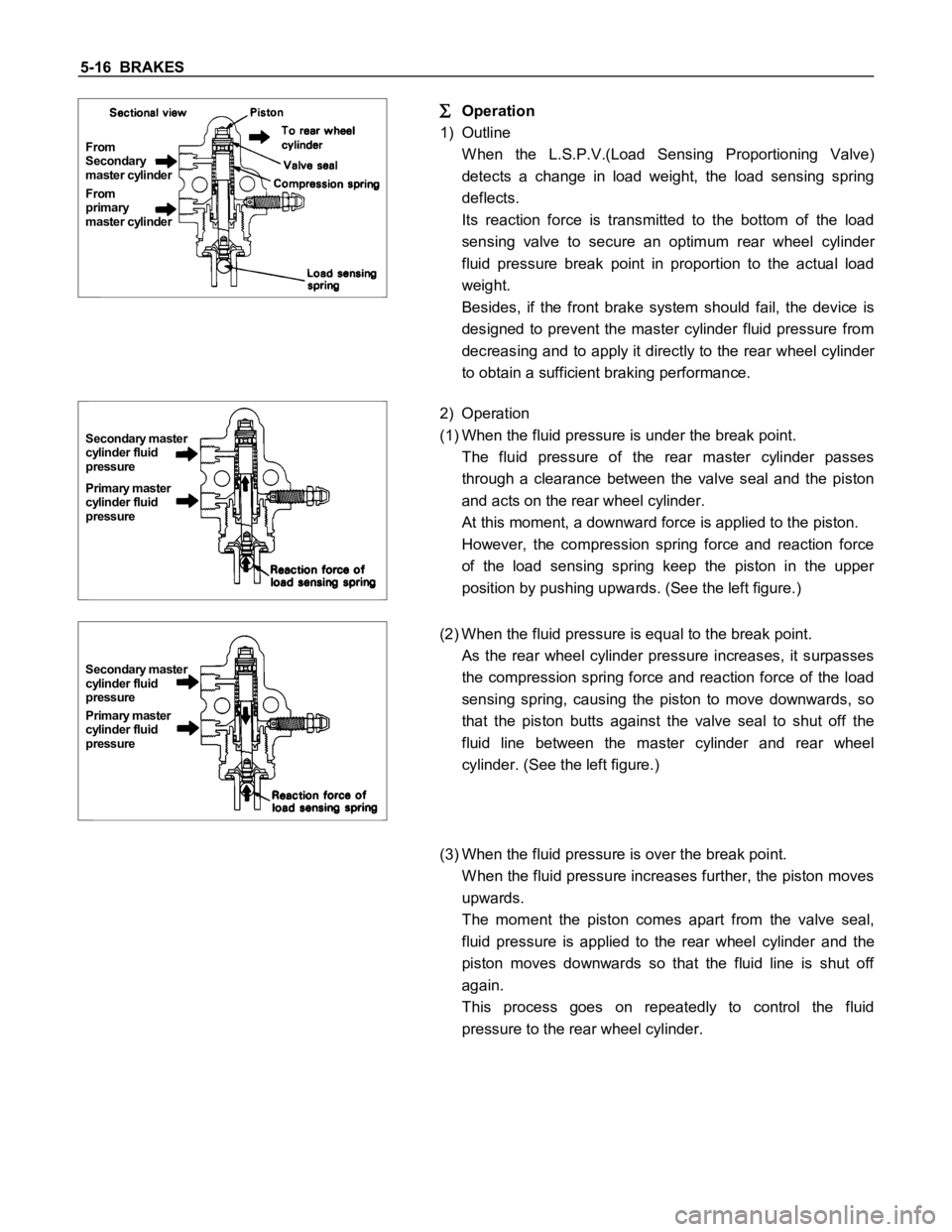
5-16 BRAKES
From
primary
master cylinder From
Secondary
master cylinder
Operation
1) Outline
W hen the L.S.P.V.(Load Sensing Proportioning Valve)
detects a change in load weight, the load sensing spring
deflects.
Its reaction force is transmitted to the bottom of the load
sensing valve to secure an optimum rear wheel cylinder
fluid pressure break point in proportion to the actual load
weight.
Besides, if the front brake system should fail, the device is
designed to prevent the master cylinder fluid pressure from
decreasing and to apply it directly to the rear wheel cylinder
to obtain a sufficient braking performance.
Primary master
cylinder fluid
pressure Secondary master
cylinder fluid
pressure
2) Operation
(1) When the fluid pressure is under the break point.
The fluid pressure of the rear master cylinder passes
through a clearance between the valve seal and the piston
and acts on the rear wheel cylinder.
At this moment, a downward force is applied to the piston.
However, the compression spring force and reaction force
of the load sensing spring keep the piston in the upper
position by pushing upwards. (See the left figure.)
Primary master
cylinder fluid
pressure Secondary master
cylinder fluid
pressure
(2) When the fluid pressure is equal to the break point.
As the rear wheel cylinder pressure increases, it surpasses
the compression spring force and reaction force of the load
sensing spring, causing the piston to move downwards, so
that the piston butts against the valve seal to shut off the
fluid line between the master cylinder and rear wheel
cylinder. (See the left figure.)
(3) When the fluid pressure is over the break point.
W hen the fluid pressure increases further, the piston moves
upwards.
The moment the piston comes apart from the valve seal,
fluid pressure is applied to the rear wheel cylinder and the
piston moves downwards so that the fluid line is shut off
again.
This process goes on repeatedly to control the fluid
pressure to the rear wheel cylinder.
Page 345 of 1600
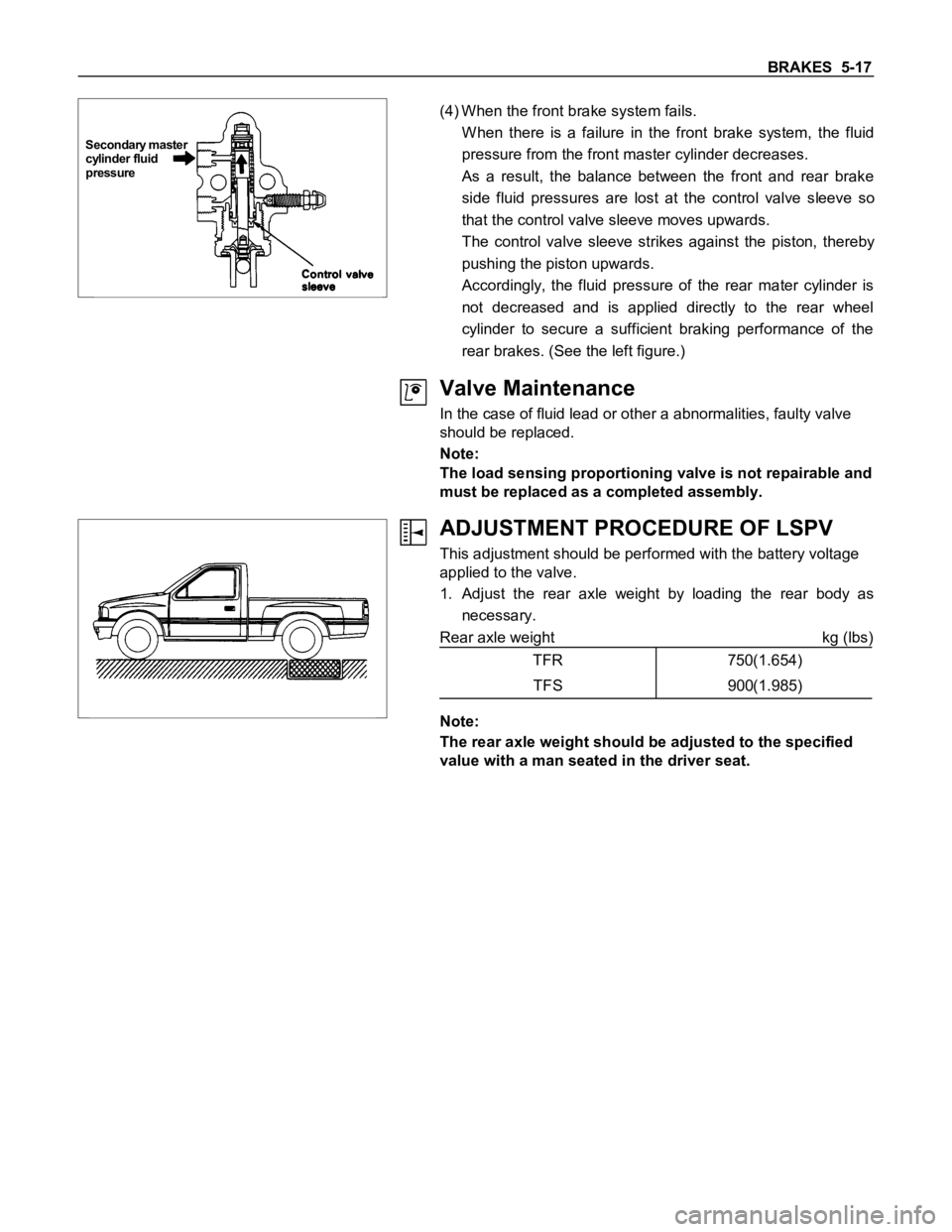
BRAKES 5-17
Secondary master
cylinder fluid
pressure
(4) When the front brake system fails.
W hen there is a failure in the front brake system, the fluid
pressure from the front master cylinder decreases.
As a result, the balance between the front and rear brake
side fluid pressures are lost at the control valve sleeve so
that the control valve sleeve moves upwards.
The control valve sleeve strikes against the piston, thereby
pushing the piston upwards.
Accordingly, the fluid pressure of the rear mater cylinder is
not decreased and is applied directly to the rear wheel
cylinder to secure a sufficient braking performance of the
rear brakes. (See the left figure.)
Valve Maintenance
In the case of fluid lead or other a abnormalities, faulty valve
should be replaced.
Note:
The load sensing proportioning valve is not repairable and
must be replaced as a completed assembly.
ADJUSTMENT PROCEDURE OF LSPV
This adjustment should be performed with the battery voltage
applied to the valve.
1. Adjust the rear axle weight by loading the rear body as
necessary.
Rear axle weight kg (lbs)
TFR 750(1.654)
TFS 900(1.985)
Note:
The rear axle weight should be adjusted to the specified
value with a man seated in the driver seat.
Page 346 of 1600
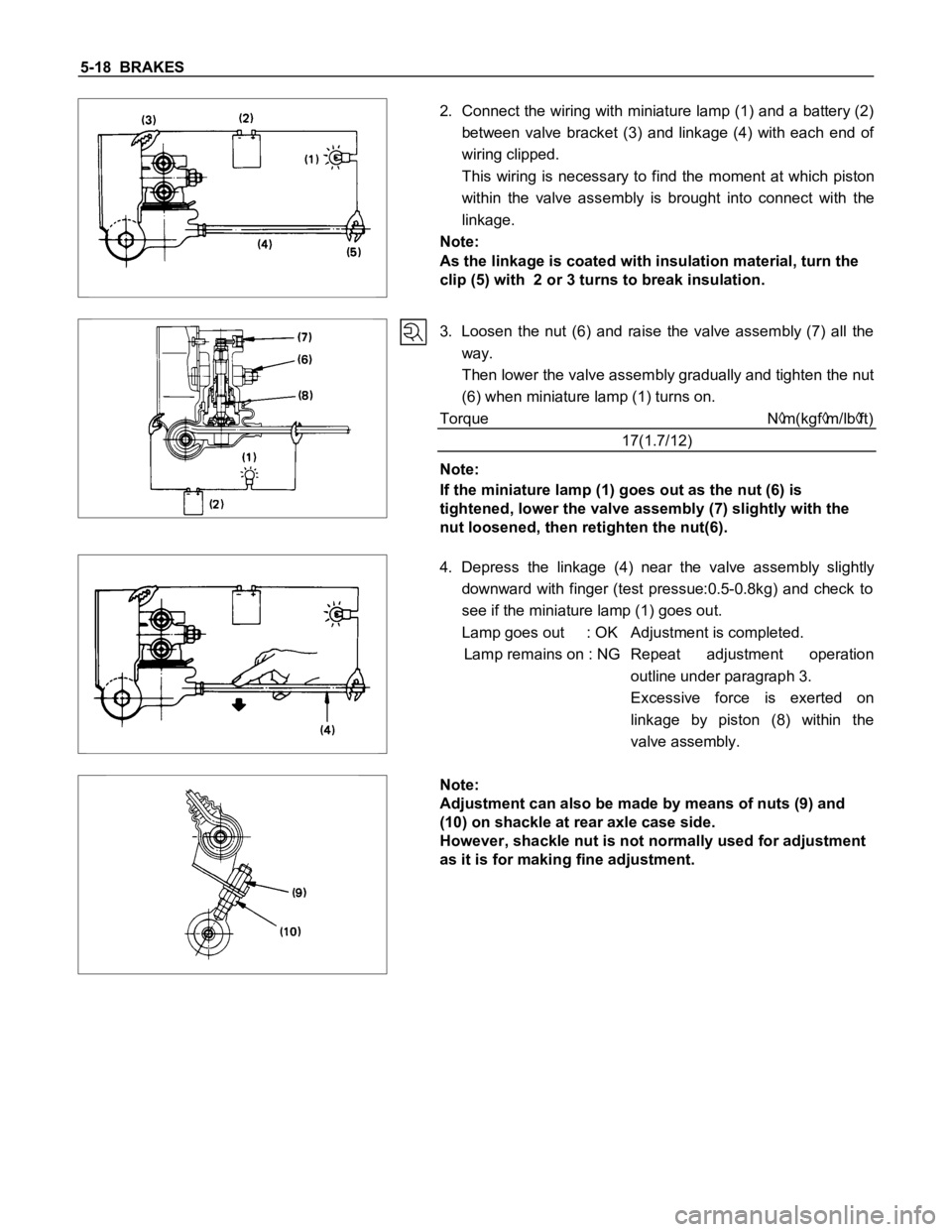
5-18 BRAKES
2. Connect the wiring with miniature lamp (1) and a battery (2)
between valve bracket (3) and linkage (4) with each end of
wiring clipped.
This wiring is necessary to find the moment at which piston
within the valve assembly is brought into connect with the
linkage.
Note:
As the linkage is coated with insulation material, turn the
clip (5) with 2 or 3 turns to break insulation.
3. Loosen the nut (6) and raise the valve assembly (7) all the
way.
Then lower the valve assembly gradually and tighten the nut
(6) when miniature lamp (1) turns on.
Torque N
m(kgfm/lbft)
17(1.7/12)
Note:
If the miniature lamp (1) goes out as the nut (6) is
tightened, lower the valve assembly (7) slightly with the
nut loosened, then retighten the nut(6).
4. Depress the linkage (4) near the valve assembly slightly
downward with finger (test pressue:0.5-0.8kg) and check to
see if the miniature lamp (1) goes out.
Lamp goes out : OK Adjustment is completed.
Lamp remains on : NG Repeat adjustment operation
outline under paragraph 3.
Excessive force is exerted on
linkage by piston (8) within the
valve assembly.
Note:
Adjustment can also be made by means of nuts (9) and
(10) on shackle at rear axle case side.
However, shackle nut is not normally used for adjustment
as it is for making fine adjustment.
Page 347 of 1600
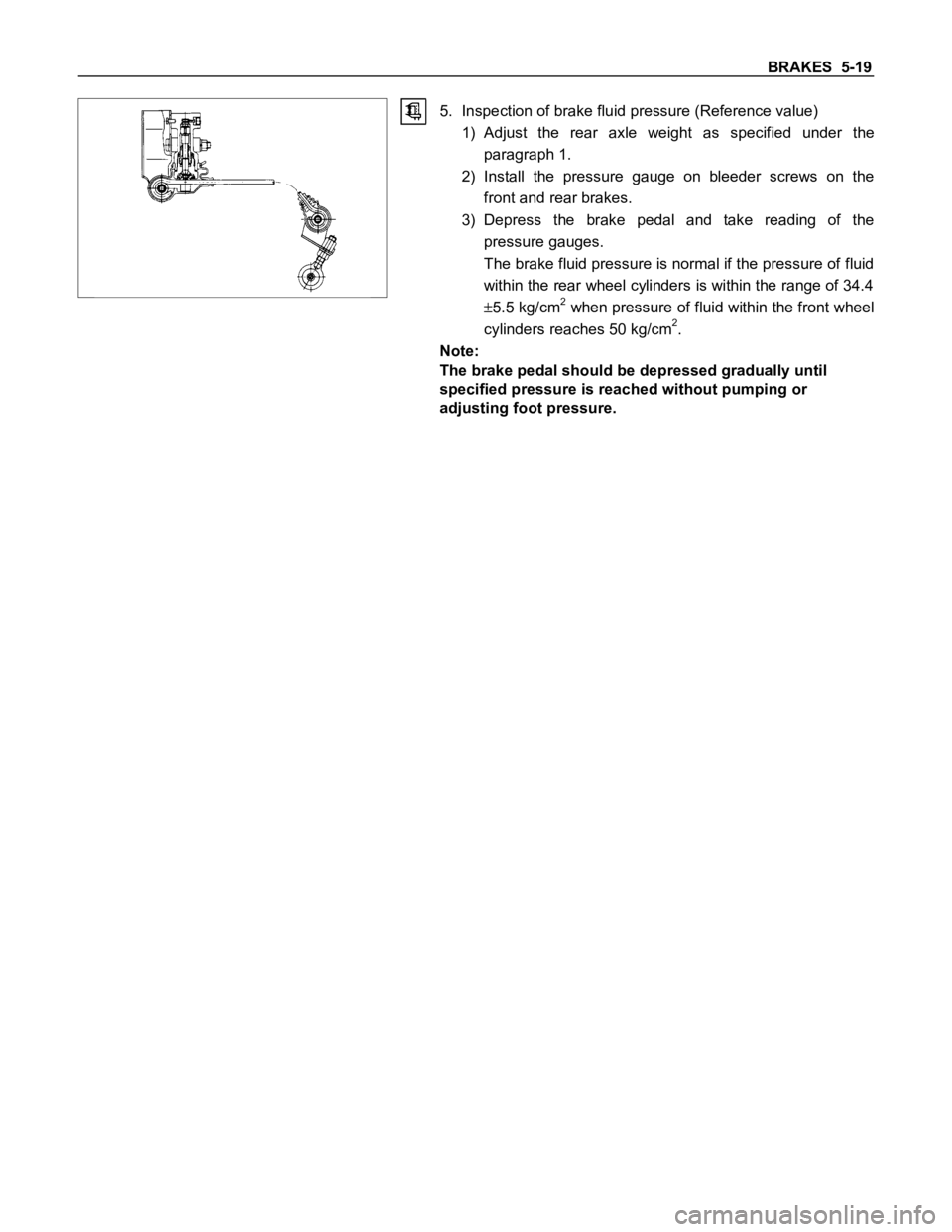
BRAKES 5-19
5. Inspection of brake fluid pressure (Reference value)
1) Adjust the rear axle weight as specified under the
paragraph 1.
2) Install the pressure gauge on bleeder screws on the
front and rear brakes.
3) Depress the brake pedal and take reading of the
pressure gauges.
The brake fluid pressure is normal if the pressure of fluid
within the rear wheel cylinders is within the range of 34.4
5.5 kg/cm2 when pressure of fluid within the front wheel
cylinders reaches 50 kg/cm2.
Note:
The brake pedal should be depressed gradually until
specified pressure is reached without pumping or
adjusting foot pressure.
Page 348 of 1600

5-20 BRAKES
BLEND PROPORTIONING VALVE (IF SO EQUIPPED)
Structure and Operation
Structure
Side
I shows P-valve ; side II shows bypass valve.
Bypass valve seals the routes
4 and 5 using the seal 2 at
the piston
1 end.
In addition, spring
3 presses against the piston 1, and in
order to seal out the route
4 and route 5 sufficiently, spring
3 presses seal 2 against cylinder end surface.
The left figure is a characteristic curve diagram.
Page 349 of 1600
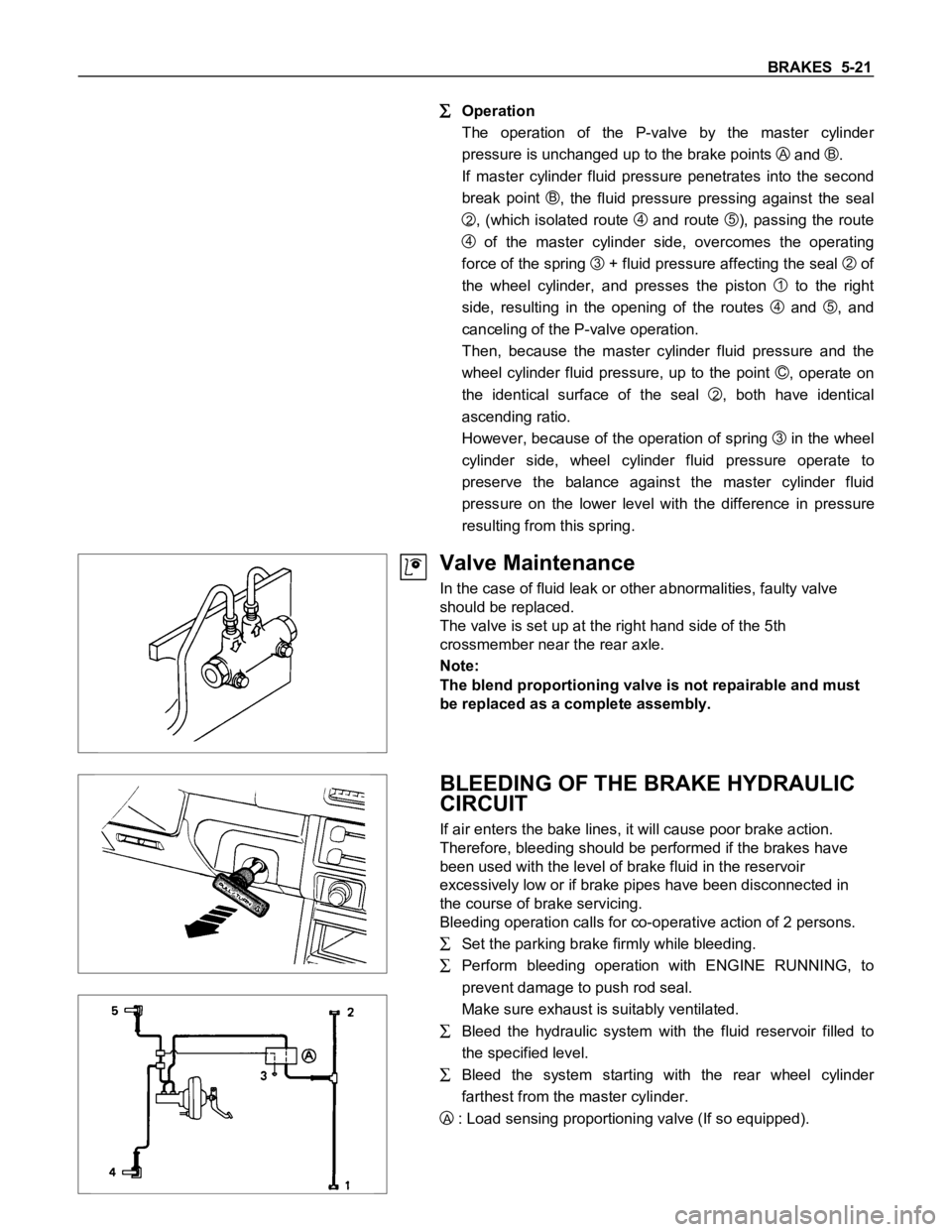
BRAKES 5-21
Operation
The operation of the P-valve by the master cylinder
pressure is unchanged up to the brake points
A and B.
If master cylinder fluid pressure penetrates into the second
break point
B, the fluid pressure pressing against the seal
2, (which isolated route 4 and route 5), passing the route
4 of the master cylinder side, overcomes the operating
force of the spring
3 + fluid pressure affecting the seal 2 of
the wheel cylinder, and presses the piston
1 to the right
side, resulting in the opening of the routes
4 and 5, and
canceling of the P-valve operation.
Then, because the master cylinder fluid pressure and the
wheel cylinder fluid pressure, up to the point
C, operate on
the identical surface of the seal
2, both have identical
ascending ratio.
However, because of the operation of spring
3 in the wheel
cylinder side, wheel cylinder fluid pressure operate to
preserve the balance against the master cylinder fluid
pressure on the lower level with the difference in pressure
resulting from this spring.
Valve Maintenance
In the case of fluid leak or other abnormalities, faulty valve
should be replaced.
The valve is set up at the right hand side of the 5th
crossmember near the rear axle.
Note:
The blend proportioning valve is not repairable and must
be replaced as a complete assembly.
BLEEDING OF THE BRAKE HYDRAULIC
CIRCUIT
If air enters the bake lines, it will cause poor brake action.
Therefore, bleeding should be performed if the brakes have
been used with the level of brake fluid in the reservoir
excessively low or if brake pipes have been disconnected in
the course of brake servicing.
Bleeding operation calls for co-operative action of 2 persons.
Set the parking brake firmly while bleeding.
Perform bleeding operation with ENGINE RUNNING, to
prevent damage to push rod seal.
Make sure exhaust is suitably ventilated.
Bleed the hydraulic system with the fluid reservoir filled to
the specified level.
Bleed the system starting with the rear wheel cylinder
farthest from the master cylinder.
A : Load sensing proportioning valve (If so equipped).
Page 350 of 1600
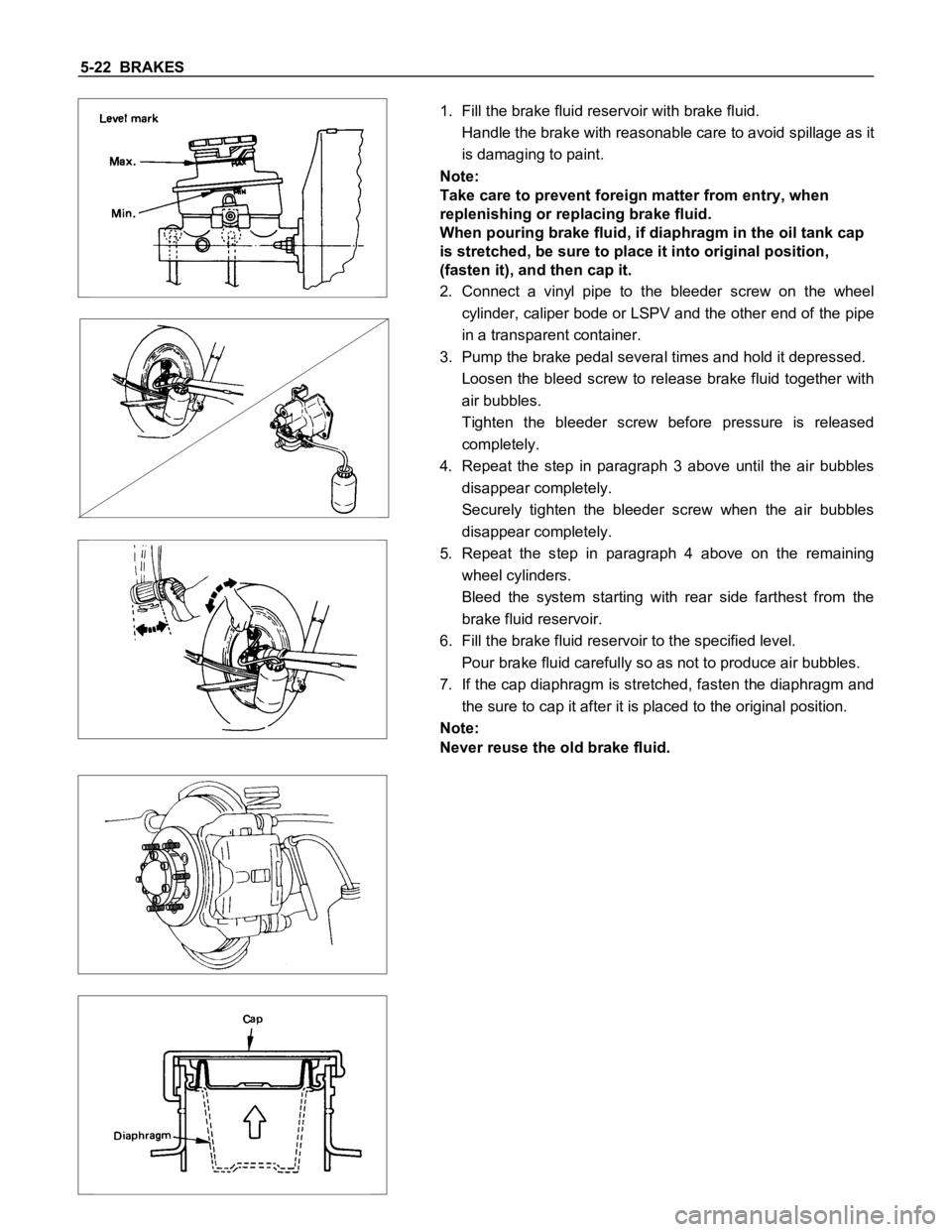
5-22 BRAKES
1. Fill the brake fluid reservoir with brake fluid.
Handle the brake with reasonable care to avoid spillage as it
is damaging to paint.
Note:
Take care to prevent foreign matter from entry, when
replenishing or replacing brake fluid.
When pouring brake fluid, if diaphragm in the oil tank cap
is stretched, be sure to place it into original position,
(fasten it), and then cap it.
2. Connect a vinyl pipe to the bleeder screw on the wheel
cylinder, caliper bode or LSPV and the other end of the pipe
in a transparent container.
3. Pump the brake pedal several times and hold it depressed.
Loosen the bleed screw to release brake fluid together with
air bubbles.
Tighten the bleeder screw before pressure is released
completely.
4. Repeat the step in paragraph 3 above until the air bubbles
disappear completely.
Securely tighten the bleeder screw when the air bubbles
disappear completely.
5. Repeat the step in paragraph 4 above on the remaining
wheel cylinders.
Bleed the system starting with rear side farthest from the
brake fluid reservoir.
6. Fill the brake fluid reservoir to the specified level.
Pour brake fluid carefully so as not to produce air bubbles.
7. If the cap diaphragm is stretched, fasten the diaphragm and
the sure to cap it after it is placed to the original position.
Note:
Never reuse the old brake fluid.
Page 351 of 1600
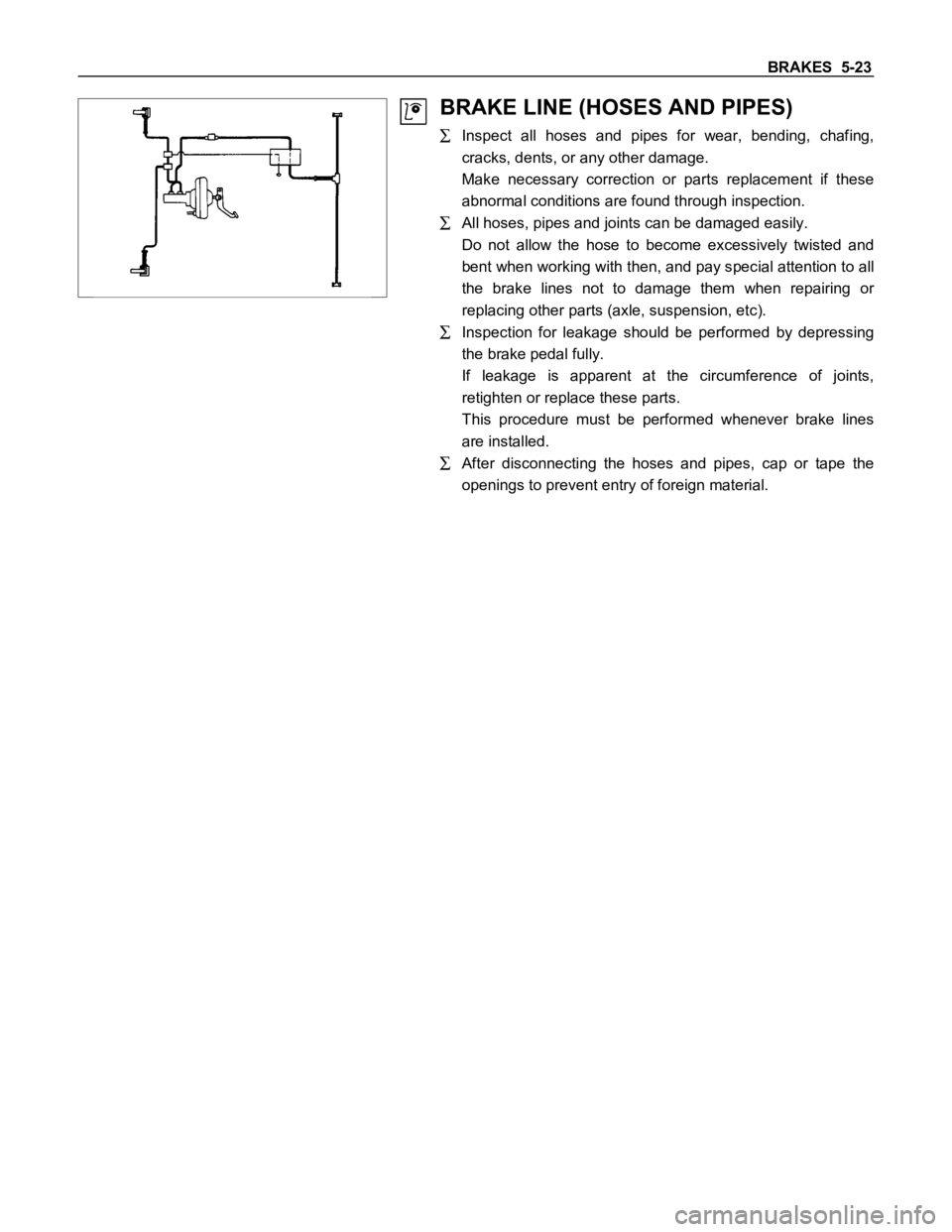
BRAKES 5-23
BRAKE LINE (HOSES AND PIPES)
Inspect all hoses and pipes for wear, bending, chafing,
cracks, dents, or any other damage.
Make necessary correction or parts replacement if these
abnormal conditions are found through inspection.
All hoses, pipes and joints can be damaged easily.
Do not allow the hose to become excessively twisted and
bent when working with then, and pay special attention to all
the brake lines not to damage them when repairing or
replacing other parts (axle, suspension, etc).
Inspection for leakage should be performed by depressing
the brake pedal fully.
If leakage is apparent at the circumference of joints,
retighten or replace these parts.
This procedure must be performed whenever brake lines
are installed.
After disconnecting the hoses and pipes, cap or tape the
openings to prevent entry of foreign material.
Page 352 of 1600
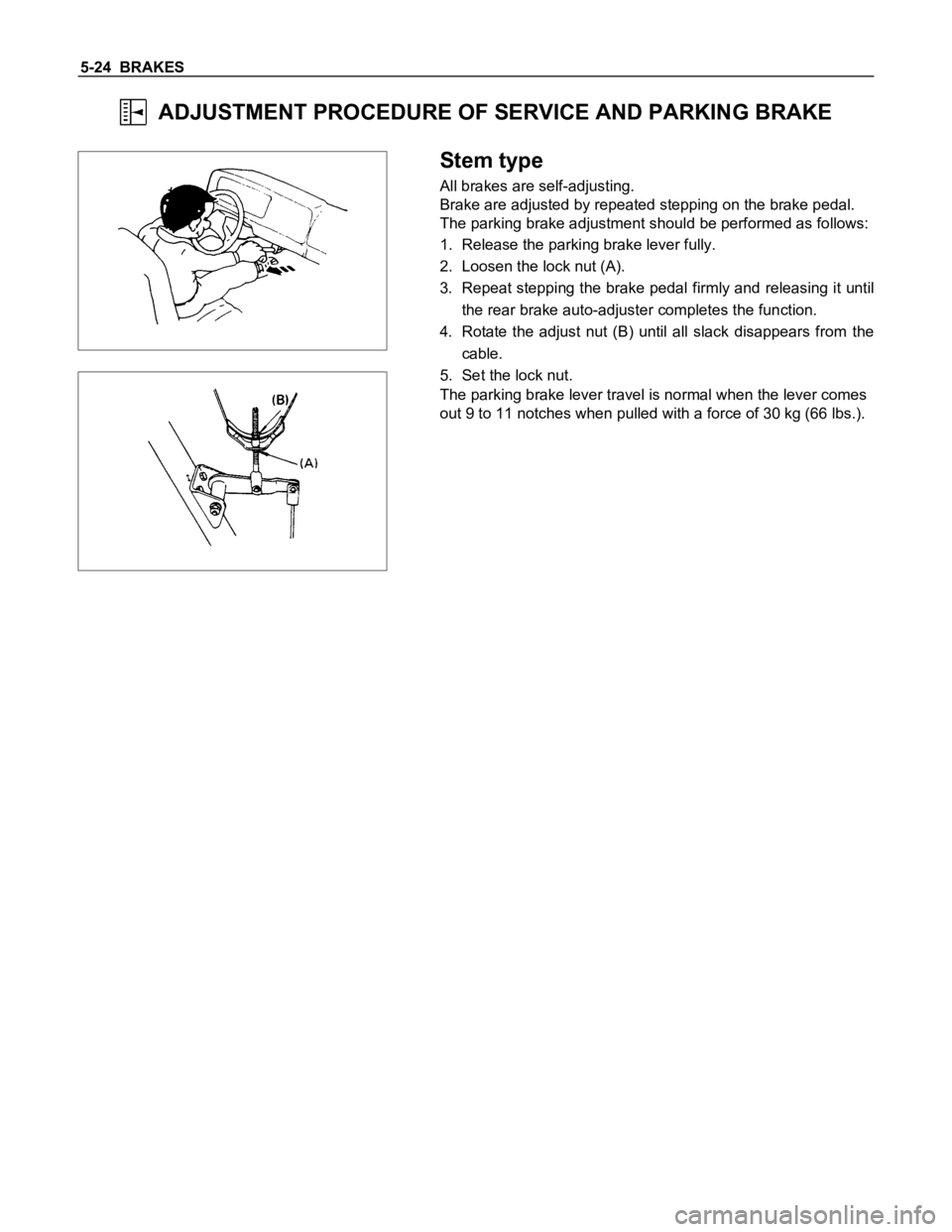
5-24 BRAKES
ADJUSTMENT PROCEDURE OF SERVICE AND PARKING BRAKE
Stem type
All brakes are self-adjusting.
Brake are adjusted by repeated stepping on the brake pedal.
The parking brake adjustment should be performed as follows:
1. Release the parking brake lever fully.
2. Loosen the lock nut (A).
3. Repeat stepping the brake pedal firmly and releasing it until
the rear brake auto-adjuster completes the function.
4. Rotate the adjust nut (B) until all slack disappears from the
cable.
5. Set the lock nut.
The parking brake lever travel is normal when the lever comes
out 9 to 11 notches when pulled with a force of 30 kg (66 lbs.).
Page 353 of 1600
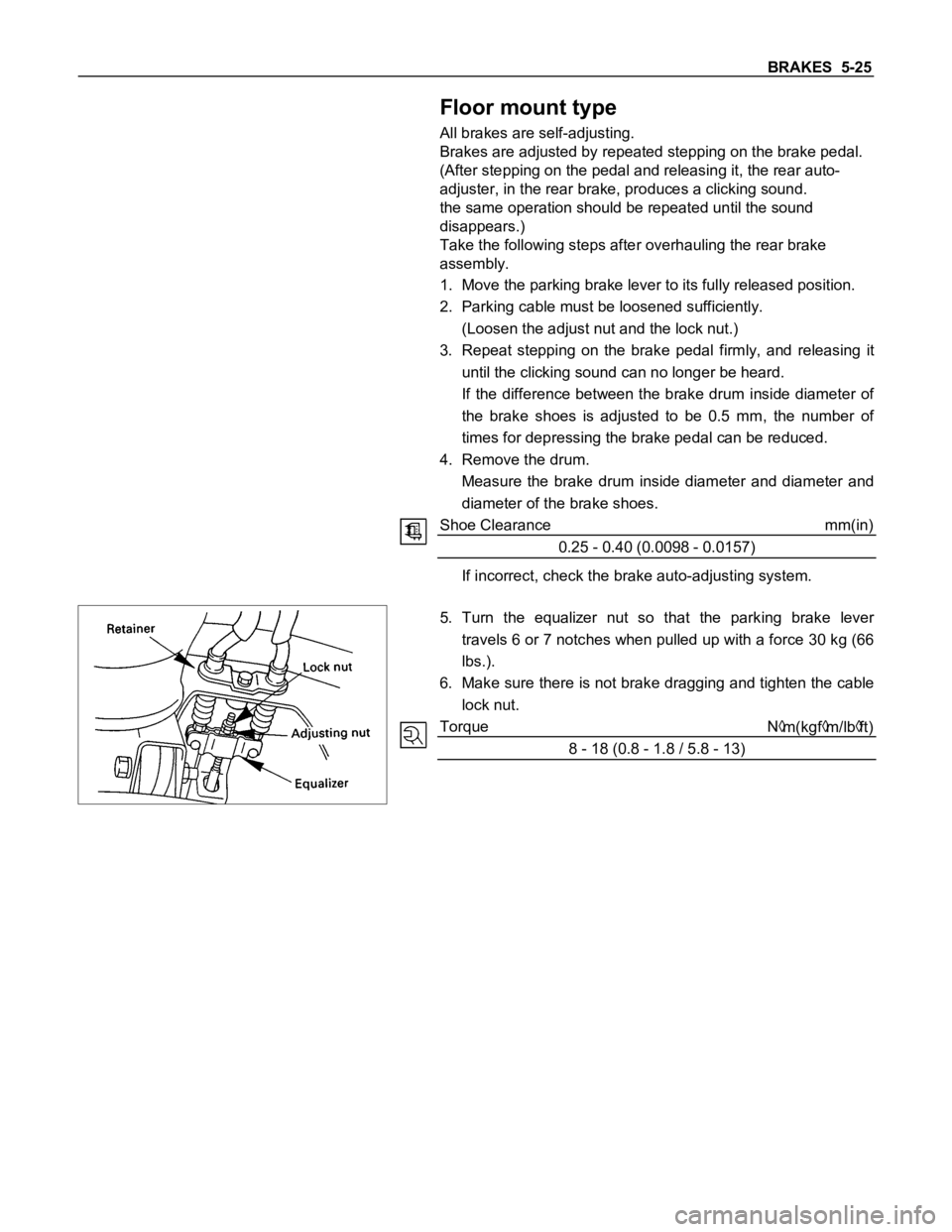
BRAKES 5-25
Floor mount type
All brakes are self-adjusting.
Brakes are adjusted by repeated stepping on the brake pedal.
(After stepping on the pedal and releasing it, the rear auto-
adjuster, in the rear brake, produces a clicking sound.
the same operation should be repeated until the sound
disappears.)
Take the following steps after overhauling the rear brake
assembly.
1. Move the parking brake lever to its fully released position.
2. Parking cable must be loosened sufficiently.
(Loosen the adjust nut and the lock nut.)
3. Repeat stepping on the brake pedal firmly, and releasing it
until the clicking sound can no longer be heard.
If the difference between the brake drum inside diameter of
the brake shoes is adjusted to be 0.5 mm, the number of
times for depressing the brake pedal can be reduced.
4. Remove the drum.
Measure the brake drum inside diameter and diameter and
diameter of the brake shoes.
Shoe Clearance mm(in)
0.25 - 0.40 (0.0098 - 0.0157)
If incorrect, check the brake auto-adjusting system.
5. Turn the equalizer nut so that the parking brake lever
travels 6 or 7 notches when pulled up with a force 30 kg (66
lbs.).
6. Make sure there is not brake dragging and tighten the cable
lock nut.
Torque N
m(kgfm/lbft)
8 - 18 (0.8 - 1.8 / 5.8 - 13)