JAGUAR XJ6 1994 2.G Electrical Diagnostic Manual
Manufacturer: JAGUAR, Model Year: 1994, Model line: XJ6, Model: JAGUAR XJ6 1994 2.GPages: 327, PDF Size: 13.73 MB
Page 181 of 327
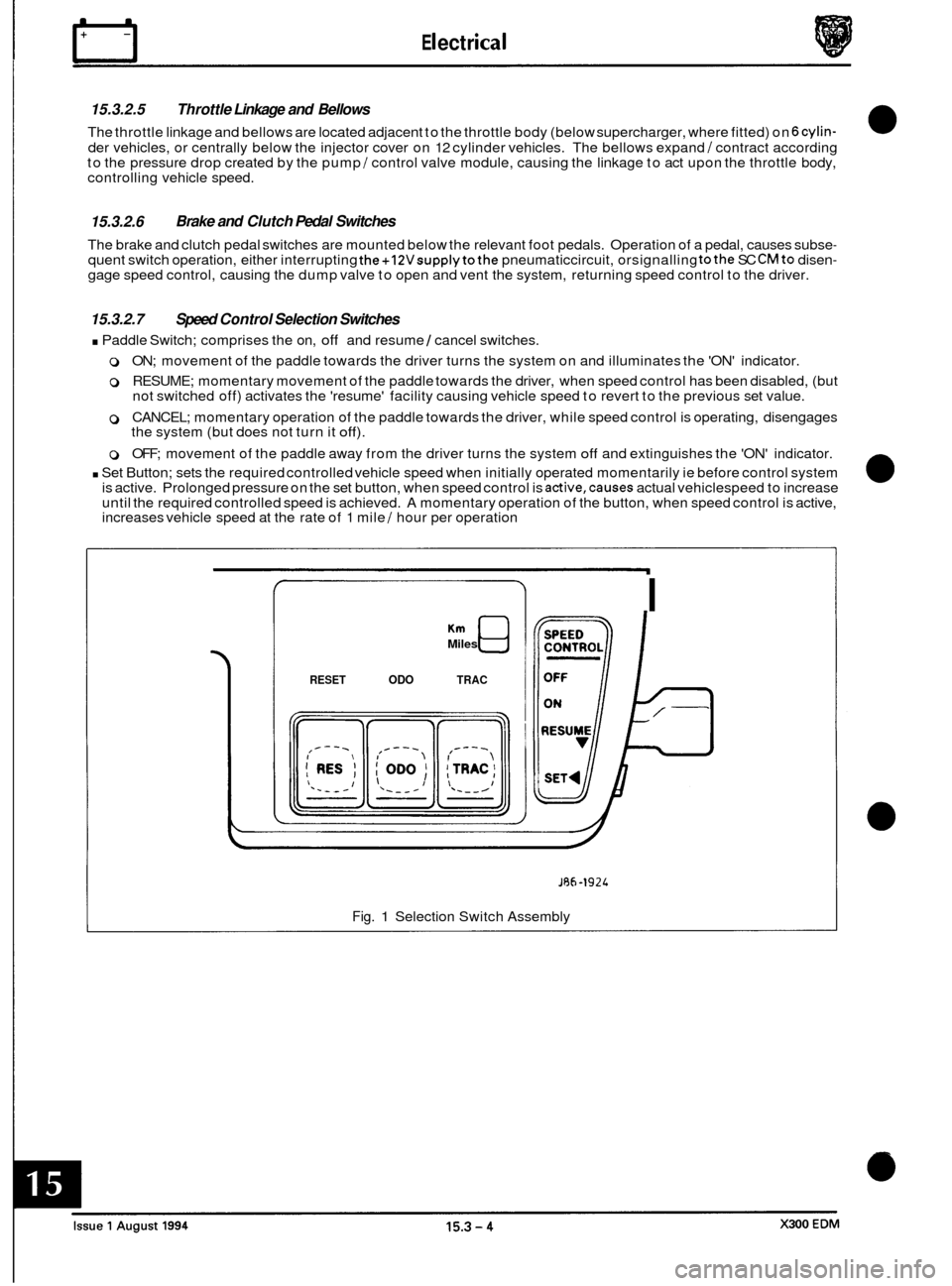
I3 E I ect r ical
15.3.2.5 Throttle Linkage and Bellows
The throttle linkage and bellows are located adjacent to the throttle body (below supercharger, where fitted) on 6cylin-
der vehicles, or centrally below the injector cover on 12 cylinder vehicles. The bellows expand I contract according
to the pressure drop created by the pump I control valve module, causing the linkage to act upon the throttle body,
controlling vehicle speed.
15.3.2.6
The brake and clutch pedal switches are mounted below the relevant foot pedals. Operation of a pedal, causes subse- quent switch operation, either interrupting the+12Vsupplytothe pneumaticcircuit, orsignalling tothe SC CMto disen- gage speed control, causing the dump valve to open and vent the system, returning speed control to the driver.
Brake and Clutch Pedal Switches
15.3.2.7 Speed Control Selection Switches
. Paddle Switch; comprises the on, off and resume 1 cancel switches.
0 ON; movement of the paddle towards the driver turns the system on and illuminates the 'ON' indicator.
0 RESUME; momentary movement of the paddle towards the driver, when speed control has been disabled, (but
not switched off) activates the 'resume' facility causing vehicle speed to revert to the previous set value.
0 CANCEL; momentary operation of the paddle towards the driver, while speed control is operating, disengages
the system (but does not turn it off).
0 OFF; movement of the paddle away from the driver turns the system off and extinguishes the 'ON' indicator.
. Set Button; sets the required controlled vehicle speed when initially operated momentarily ie before control system
is active. Prolonged pressure on the set button, when speed control is active,causes actual vehiclespeed to increase
until the required controlled speed is achieved. A momentary operation of the button, when speed control is active,
increases vehicle speed at the rate of 1 mile
/ hour per operation
Miles
RESET ODO TRAC
I
JRh-1924
Fig. 1 Selection Switch Assembly
Page 182 of 327
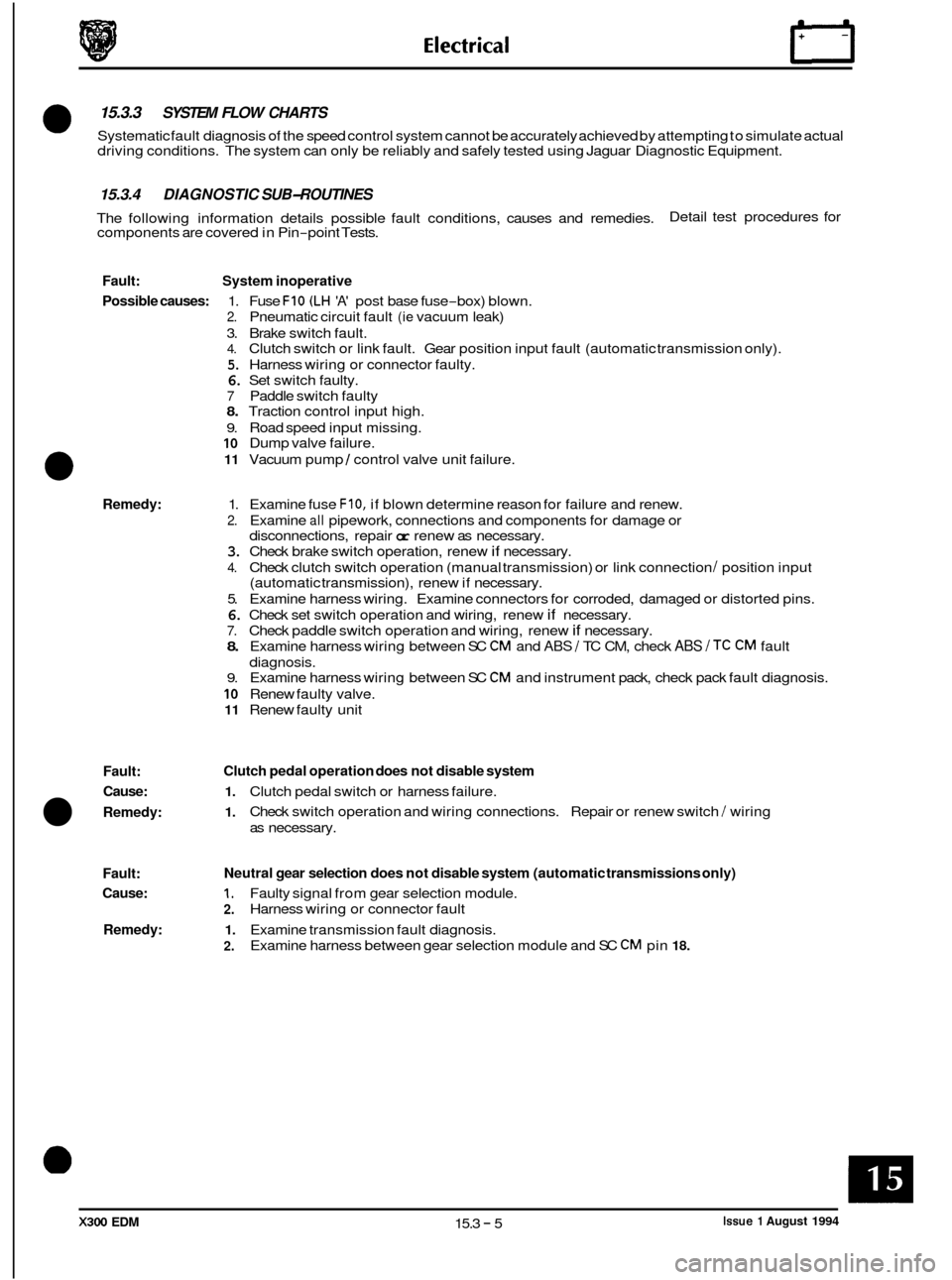
0 15.3.3 SYSTEM FLOW CHARTS
Systematic fault diagnosis of the speed control system cannot be accurately achieved by attempting to simulate actual
driving conditions. The system can only be reliably and safely tested using Jaguar Diagnostic Equipment.
15.3.4 DIAGNOSTIC SUB-ROUTINES
The following information details possible fault conditions, causes and remedies.
components are covered in Pin-point Tests. Detail test procedures
for
Fault: System inoperative
Possible causes:
1. Fuse FIO (LH 'A' post base fuse-box) blown.
2. Pneumatic circuit fault (ie vacuum leak)
3. Brake switch fault.
4. Clutch switch or link fault. Gear position input fault (automatic transmission only).
5. Harness wiring or connector faulty.
6. Set switch faulty.
7 Paddle switch faulty
8. Traction control input high.
9. Road speed input missing.
10 Dump valve failure.
11 Vacuum pump 1 control valve unit failure.
Remedy: 1. Examine fuse F10, if blown determine reason for failure and renew.
2. Examine all pipework, connections and components for damage or
disconnections, repair
or renew as necessary.
3. Check brake switch operation, renew if necessary.
4. Check clutch switch operation (manual transmission) or link connection I position input
(automatic transmission), renew if necessary.
5. Examine harness wiring. Examine connectors for corroded, damaged or distorted pins.
6. Check set switch operation and wiring, renew if necessary.
7. Check paddle switch operation and wiring, renew if necessary.
8. Examine harness wiring between SC CM and ABS / TC CM, check ABS /TC CM fault
diagnosis.
9. Examine harness wiring between SC CM and instrument pack, check pack fault diagnosis.
10 Renew faulty valve.
11 Renew faulty unit
0
Fault:
Cause:
1. Clutch pedal switch or harness failure.
Clutch pedal operation does not disable system
1. Remedy: Check switch operation and wiring connections. Repair or renew switch / wiring
as necessary.
Fault:
Cause:
1, Faulty signal from gear selection module.
Remedy: 1. Examine transmission fault diagnosis.
Neutral gear selection does not disable system (automatic transmissions only)
2.
2.
Harness wiring or connector fault
Examine harness between gear selection module and SC
CM pin 18.
X300 EDM 15.3 - 5 Issue 1 August 1994
Page 183 of 327
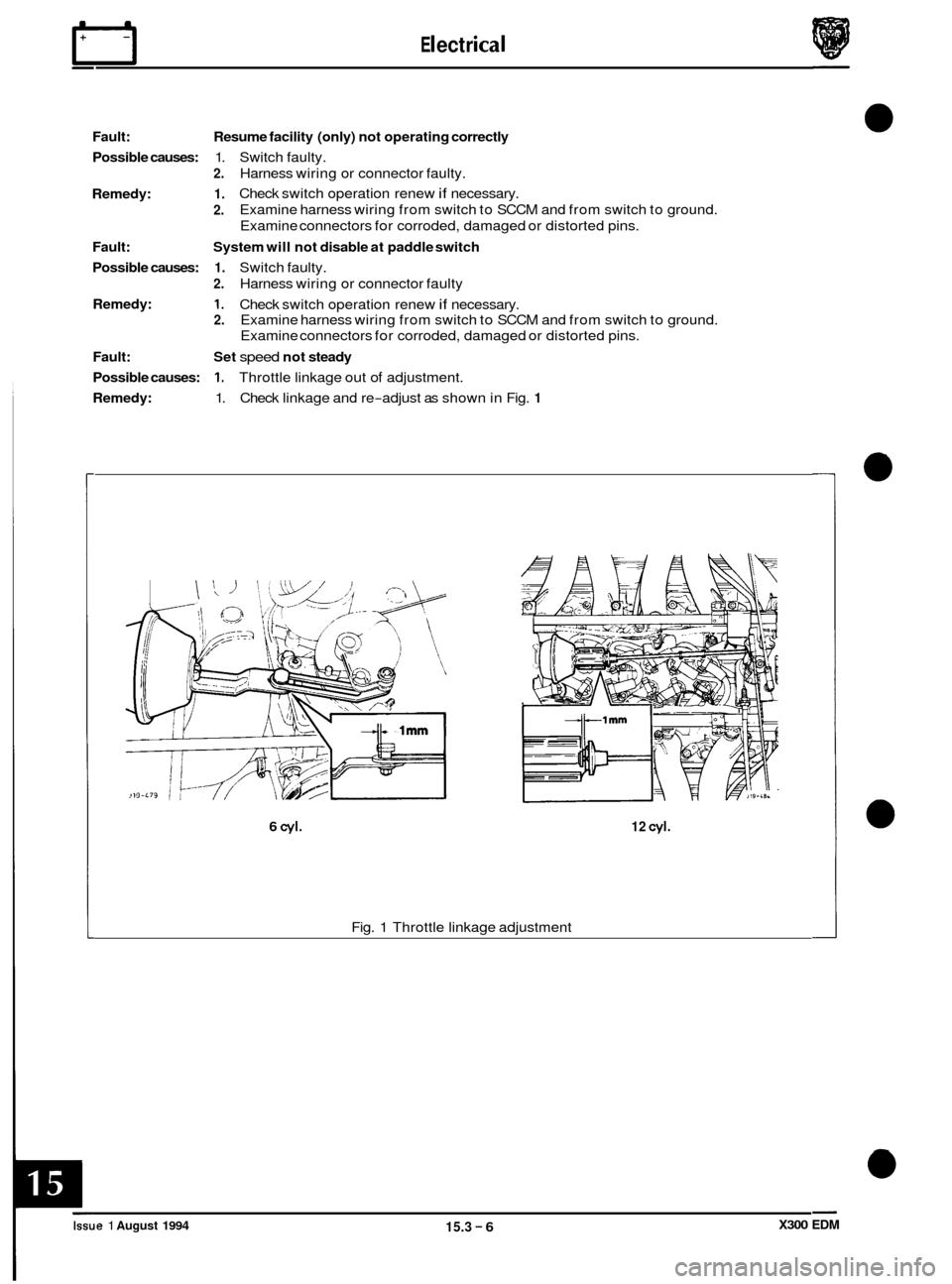
E I ect r ical rl
Fault:
Possible causes:
Remedy:
Fault:
Possible causes:
Remedy:
Fault:
Possible causes:
Remedy: Resume
facility (only) not operating correctly
1. Switch faulty.
2.
1.
2.
System will not disable at paddle switch
1. Switch faulty.
2. Harness wiring or connector faulty
1. Check switch operation renew if necessary.
2. Examine harness wiring from switch to SCCM and from switch to ground.
Examine connectors for corroded, damaged or distorted pins.
Set speed not steady
1. Throttle linkage out of adjustment.
1. Check linkage and re-adjust as shown in Fig. 1
Harness wiring or connector faulty.
Check switch operation renew
if necessary.
Examine harness wiring from switch to SCCM and from switch to ground.
Examine connectors for corroded, damaged or distorted pins.
6 cyl. 12 cyl.
Fig. 1 Throttle linkage adjustment
X300 EDM Issue 1 August 1994 15.3 - 6
Page 184 of 327
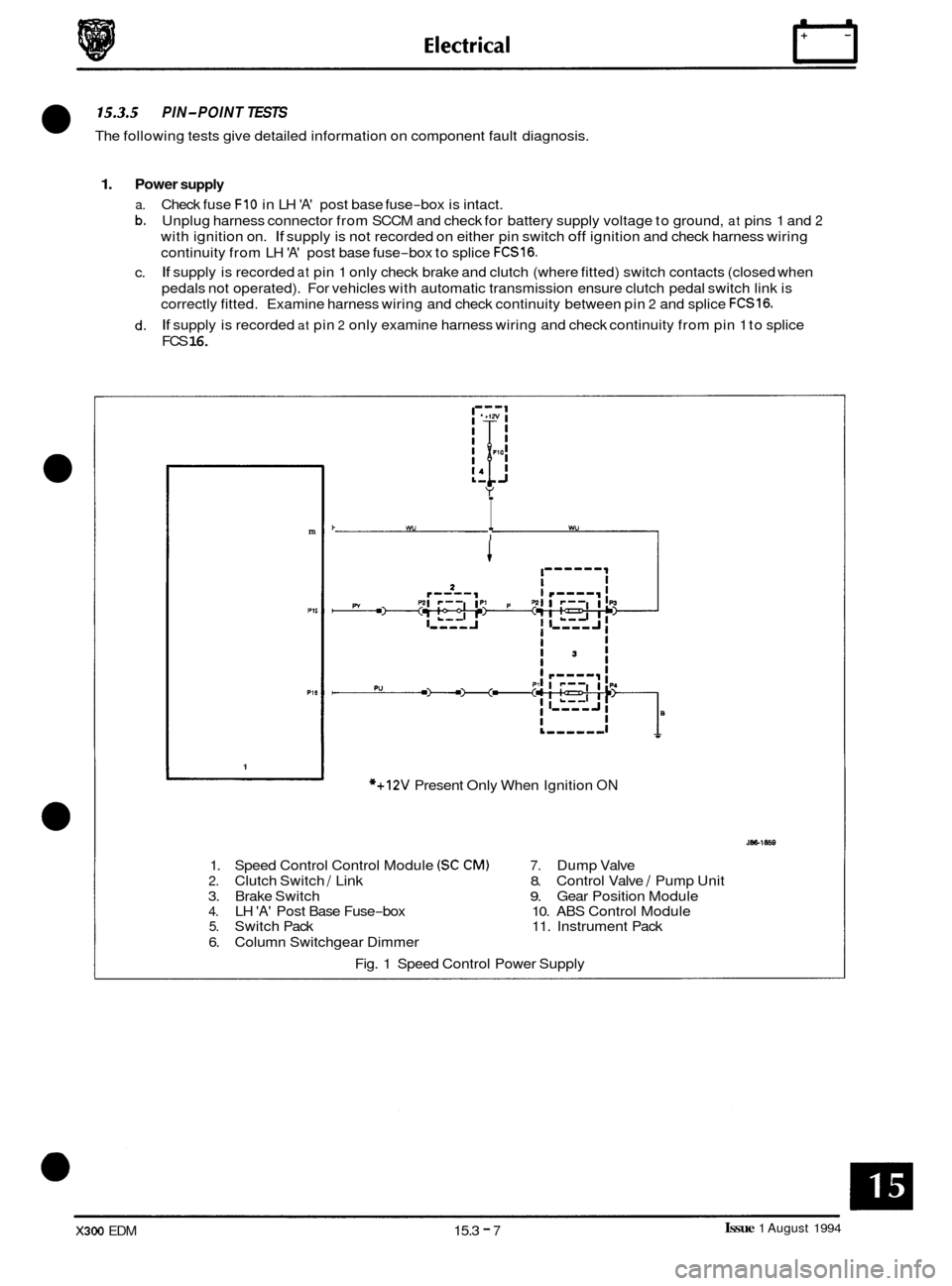
15.3.5 PIN-POINT TESTS
The following tests give detailed information on component fault diagnosis.
1. Power supply
a. Check fuse FIO in LH 'A' post base fuse-box is intact.
b. Unplug harness connector from SCCM and check for battery supply voltage to ground, at pins 1 and 2
with ignition on. If supply is not recorded on either pin switch off ignition and check harness wiring
continuity from LH
'A' post base fuse-box to splice FCS16.
If supply is recorded at pin 1 only check brake and clutch (where fitted) switch contacts (closed when
pedals not operated). For vehicles with automatic transmission ensure clutch pedal switch link is
correctly fitted. Examine harness wiring and check continuity between pin
2 and splice FCS16.
If supply is recorded at pin 2 only examine harness wiring and check continuity from pin 1 to splice
FCS
16.
c.
d.
m
P1I
1
k wv I wu I
I-------
*+12V Present Only When Ignition ON
1. Speed Control Control Module (SC CM) 7. Dump Valve
2. Clutch Switch / Link 8. Control Valve / Pump Unit
3. Brake Switch
9. Gear Position Module 4. LH 'A' Post Base Fuse-box 10. ABS Control Module 5. Switch Pack 11. Instrument Pack
6. Column Switchgear Dimmer
Fig. 1 Speed Control Power Supply
Issue 1 August 1994 X300 EDM 15.3 - 7
Page 185 of 327
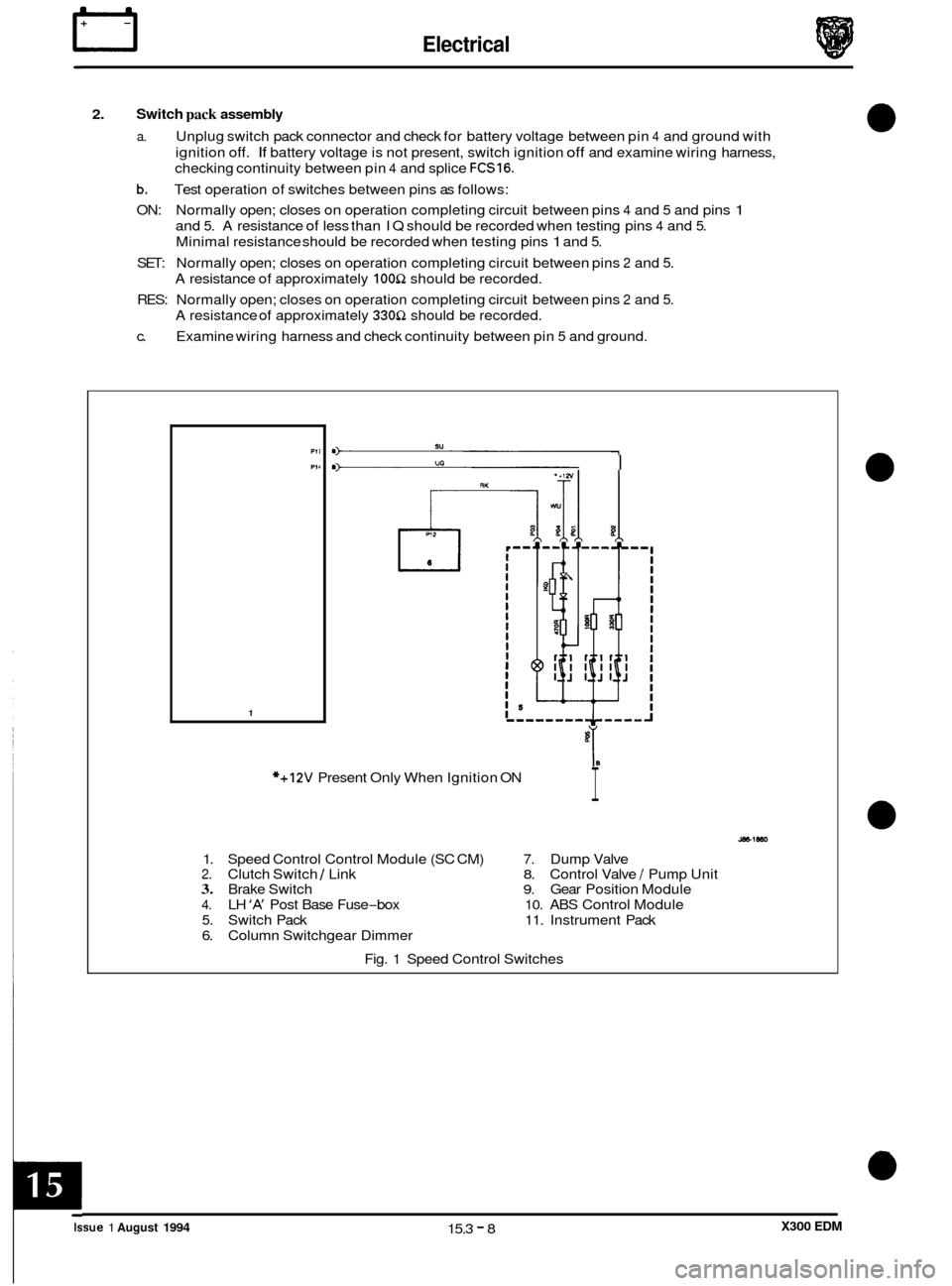
n Electrical
2. Switch pack assembly
a. Unplug switch pack connector and check for battery voltage between pin 4 and ground with
ignition
off. If battery voltage is not present, switch ignition off and examine wiring harness,
checking continuity between pin
4 and splice FCS16.
b. Test operation of switches between pins as follows:
ON: Normally open; closes on operation completing circuit between pins
4 and 5 and pins 1
and 5. A resistance of less than IQ should be recorded when testing pins 4 and 5.
Minimal resistance should be recorded when testing pins 1 and 5.
SET: Normally open; closes on operation completing circuit between pins 2 and 5.
A resistance of approximately 100Q should be recorded.
RES: Normally open; closes on operation completing circuit between pins
2 and 5.
A resistance of approximately 330Q should be recorded.
c. Examine wiring harness and check continuity between pin
5 and ground.
Ptl
PI1
1
m) su
I U0
I
*+12V Present Only When Ignition ON
1. Speed Control Control Module (SC CM)
7. Dump Valve 2. Clutch Switch I Link 8. Control Valve / Pump Unit 3. Brake Switch 9. Gear Position Module
4. LH ‘A’ Post Base Fuse-box 10. ABS Control Module
5. Switch Pack 11. Instrument Pack
6. Column Switchgear Dimmer
Fig. 1 Speed Control Switches
0
0
0
0
Issue 1 August 1994 15.3 - 8 X300 EDM
Page 186 of 327
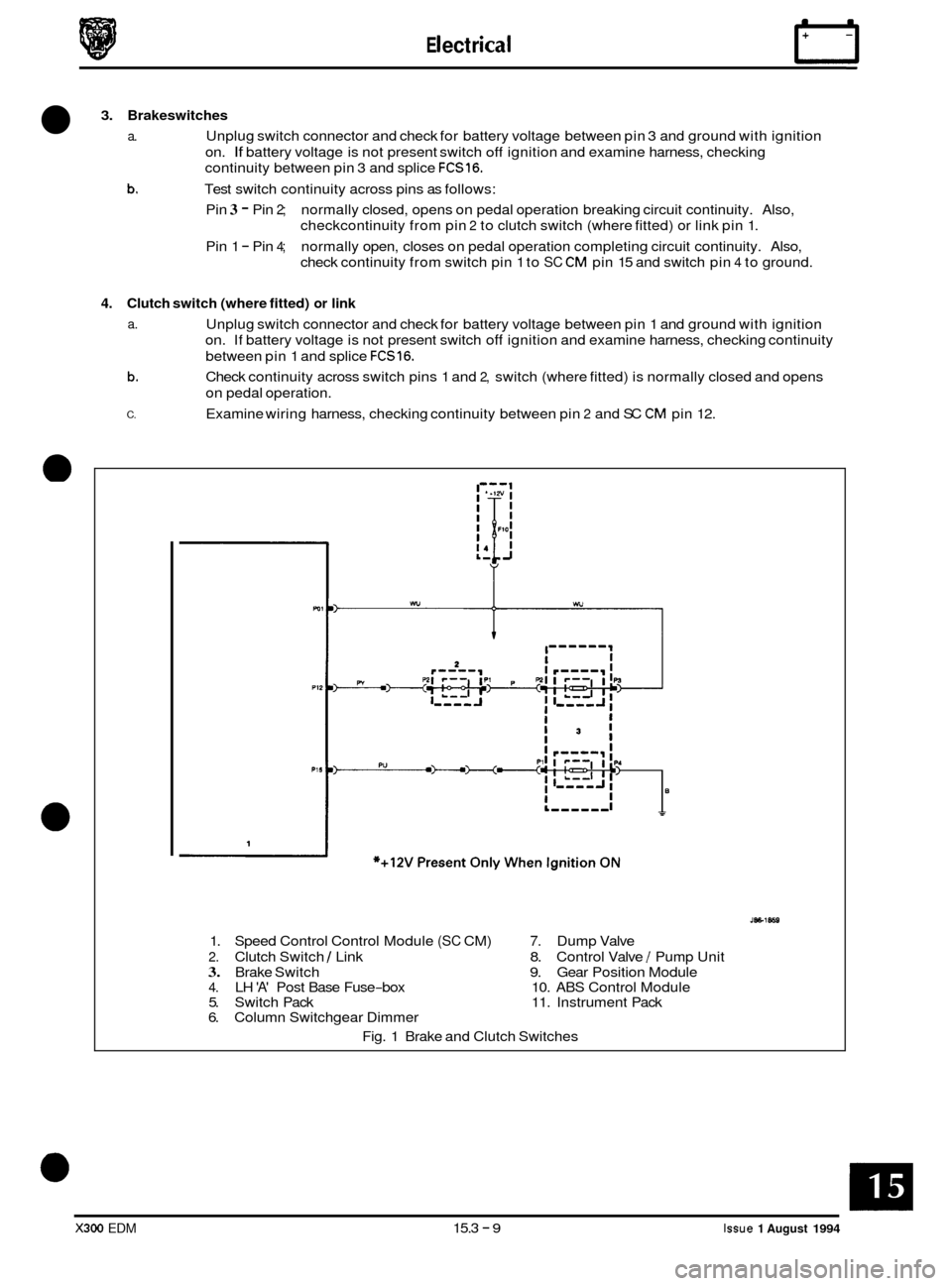
E I ect r ica I n
3. Brakeswitches
a. Unplug switch connector and check for battery voltage between pin 3 and ground with ignition
b.
on. If battery voltage is not present switch off ignition and examine harness, checking
continuity between pin 3 and splice
FCS16.
Test switch continuity across pins as follows:
Pin
3 - Pin 2; normally closed, opens on pedal operation breaking circuit continuity. Also,
checkcontinuity from pin
2 to clutch switch (where fitted) or link pin 1.
Pin 1
- Pin 4; normally open, closes on pedal operation completing circuit continuity. Also,
check continuity from switch pin 1 to
SC CM pin 15 and switch pin 4 to ground.
4. Clutch switch (where fitted) or link
a. Unplug switch connector and check for battery voltage between pin 1 and ground with ignition
on. If battery voltage is not present switch
off ignition and examine harness, checking continuity
between pin 1 and splice
FCS16.
Check continuity across switch pins 1 and 2, switch (where fitted) is normally closed and opens
on pedal operation.
Examine wiring harness, checking continuity between pin
2 and SC CM pin 12.
b.
C.
1
.---I
1. Speed Control Control Module (SC CM) 7. Dump Valve
2. Clutch Switch 1 Link 8. Control Valve / Pump Unit
3. Brake Switch 9. Gear Position Module 4. LH 'A' Post Base Fuse-box 10. ABS Control Module
5. Switch Pack 11. Instrument Pack
6. Column Switchgear Dimmer
Fig. 1 Brake and Clutch Switches
X300 EDM 15.3 - 9 Issue 1 August 1994
Page 187 of 327
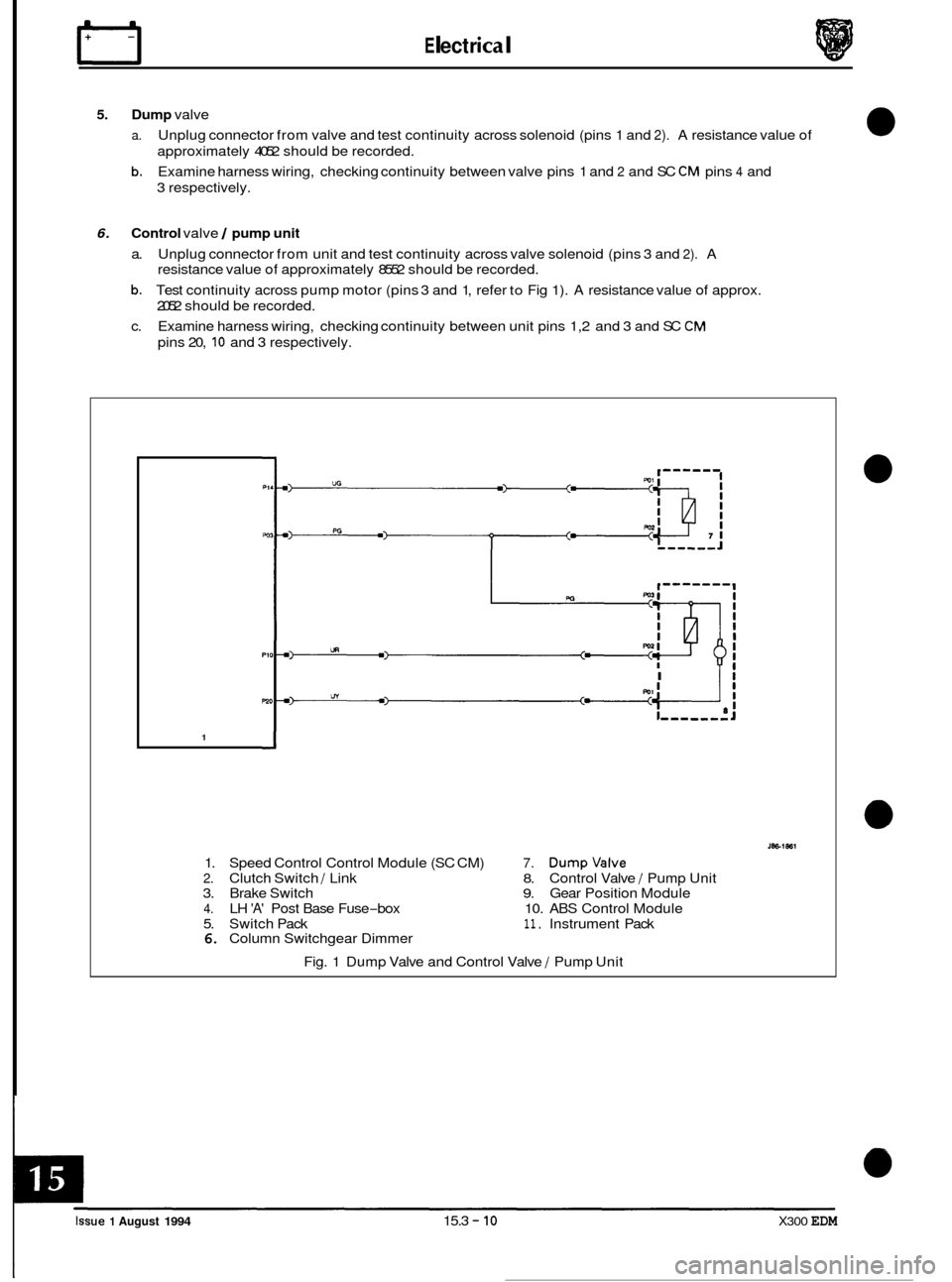
rl E I ect r ica I
5. Dump valve
a.
b.
Unplug connector from valve and test continuity across solenoid (pins 1 and 2). A resistance value of
approximately 4052 should be recorded.
Examine harness wiring, checking continuity between valve pins 1 and
2 and SC CM pins 4 and
3 respectively.
6. Control valve / pump unit
a. Unplug connector from unit and test continuity across valve solenoid (pins 3 and 2). A
resistance value of approximately 8552 should be recorded.
b. Test continuity across pump motor (pins 3 and 1, refer to Fig 1). A resistance value of approx.
2052 should be recorded.
c. Examine harness wiring, checking continuity between unit pins 1,2 and 3 and SC
CM
pins 20, 10 and 3 respectively.
I Ii
1
1. Speed Control Control Module (SC CM) 7. Dumpvalve
2. Clutch Switch / Link 8. Control Valve / Pump Unit
3. Brake Switch 9. Gear Position Module
4. LH 'A' Post Base Fuse-box 10. ABS Control Module
5. Switch Pack
11. Instrument Pack 6. Column Switchgear Dimmer
Fig. 1 Dump Valve and Control Valve
/ Pump Unit
0
0
0
0
Issue 1 August 1994 15.3 - 10 X300 EDM
Page 188 of 327
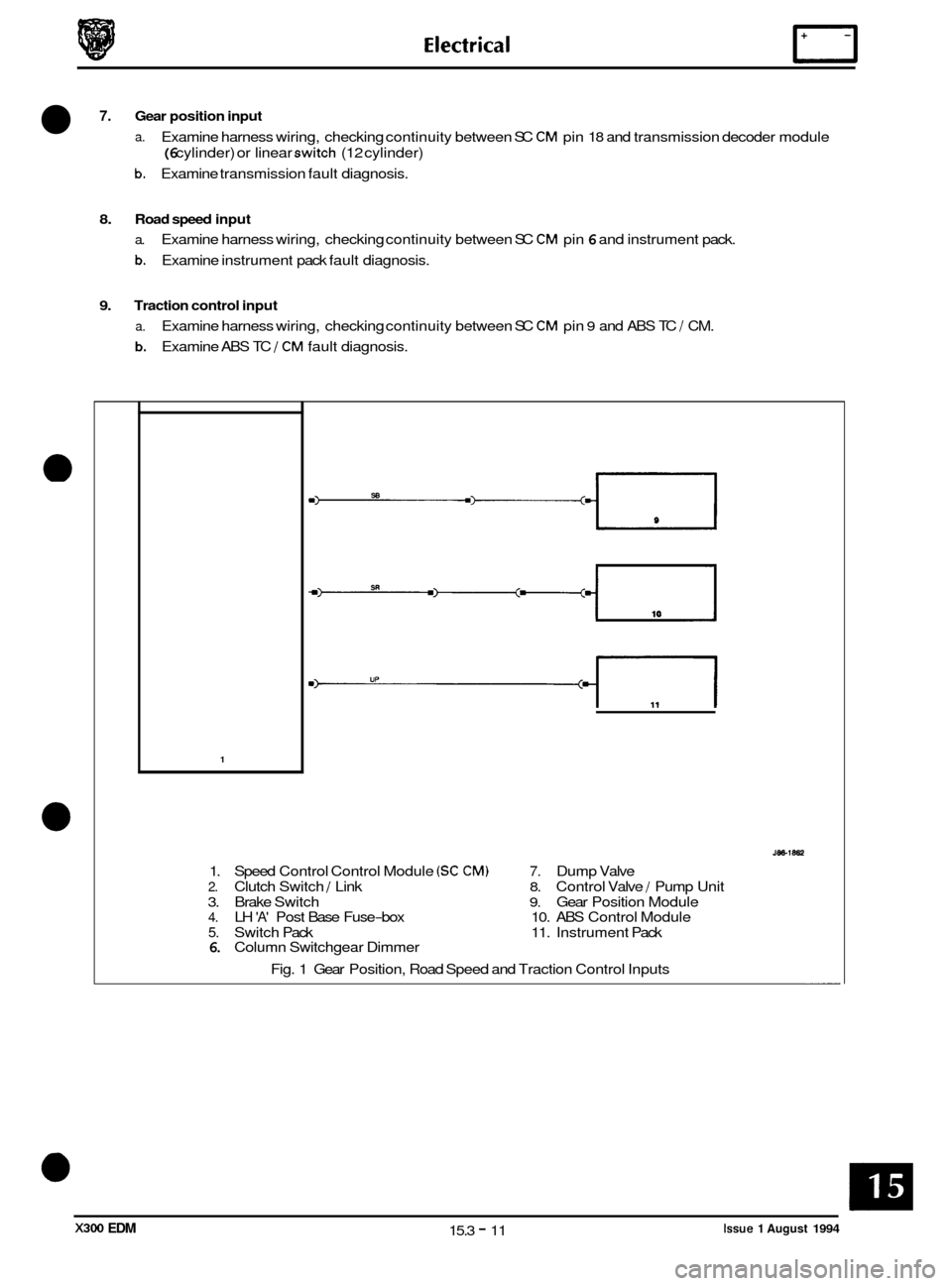
7. Gear position input
a. Examine harness wiring, checking continuity between SC CM pin 18 and transmission decoder module
(6 cylinder) or linear switch (12 cylinder)
b. Examine transmission fault diagnosis.
8. Road speed input
a. Examine harness wiring, checking continuity between SC CM pin 6 and instrument pack.
b. Examine instrument pack fault diagnosis.
9. Traction control input
a.
b.
Examine harness wiring, checking continuity between SC CM pin 9 and ABS TC J CM.
Examine ABS TC
J CM fault diagnosis.
1
1. Speed Control Control Module (SC CM) 7. Dump Valve
2. Clutch Switch J Link 8. Control Valve / Pump Unit
3. Brake Switch
9. Gear Position Module 4. LH 'A' Post Base Fuse-box 10. ABS Control Module
5. Switch Pack 11. Instrument Pack 6. Column Switchgear Dimmer
Fig. 1 Gear Position, Road Speed and Traction Control Inputs
Issue 1 August 1994 15.3 - 11 X300 EDM
Page 189 of 327
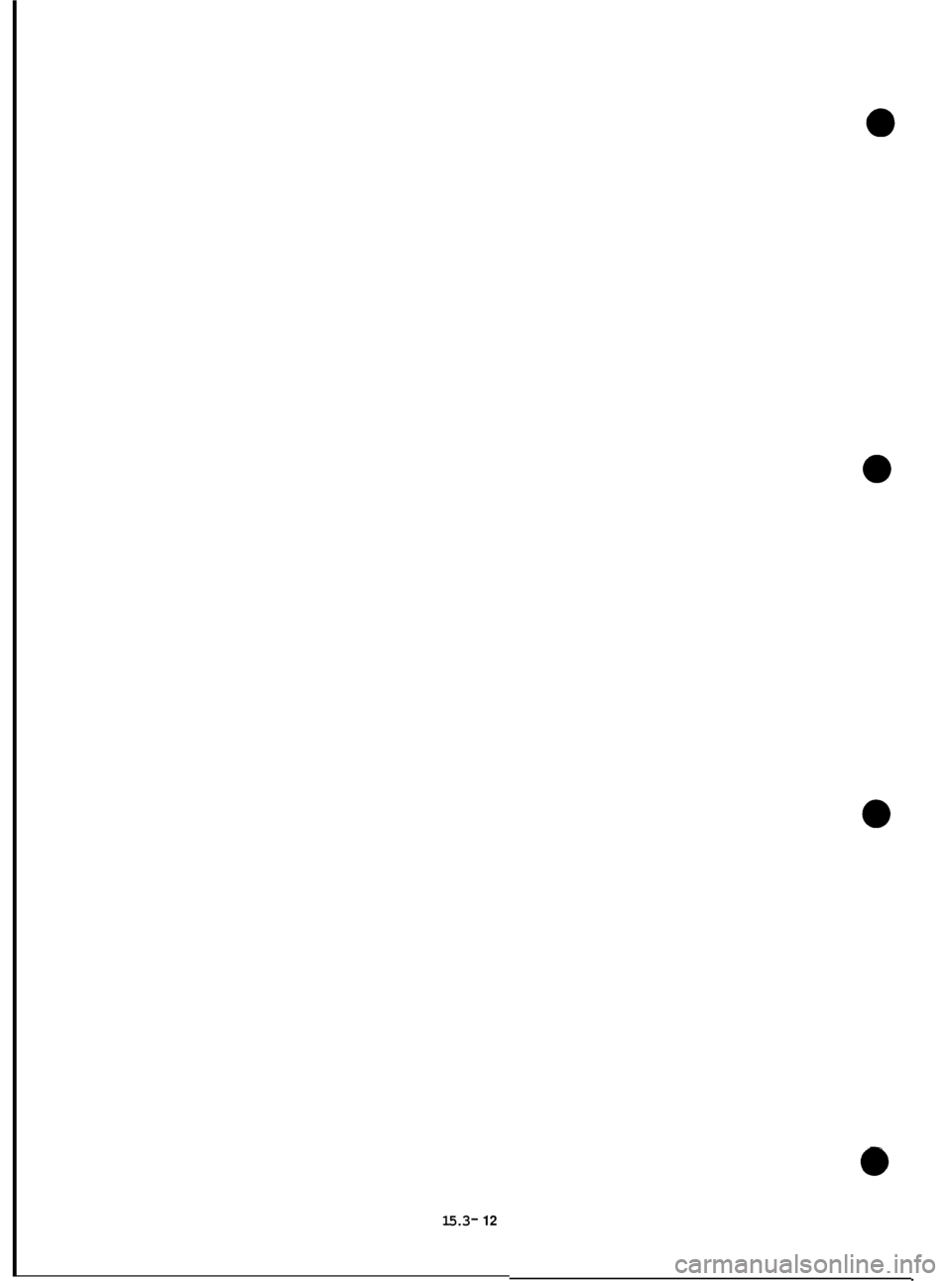
15.3 - 12
Page 190 of 327
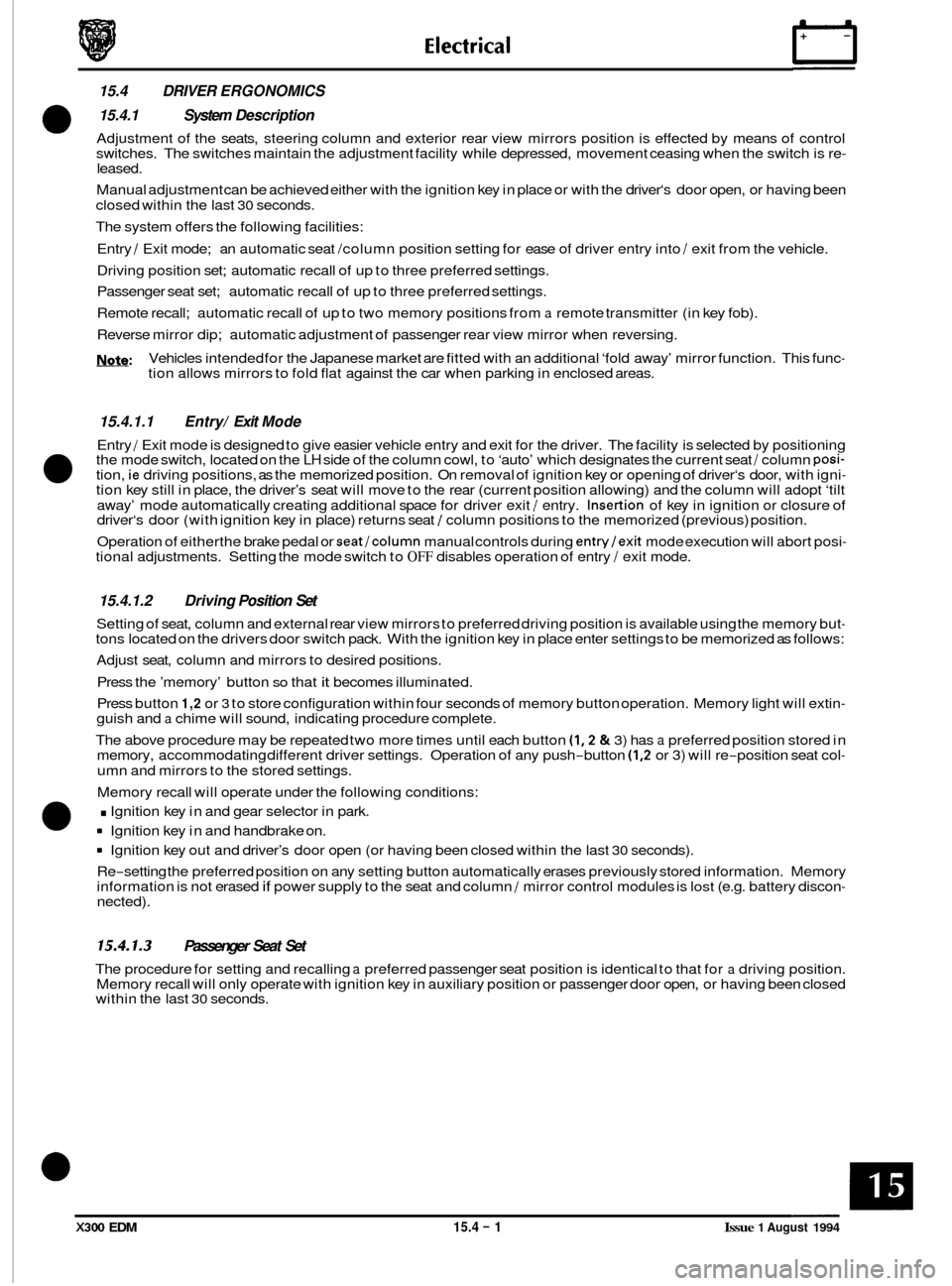
15.4 DRIVER ERGONOMICS
15.4.1 System Description
Adjustment of the seats, steering column and exterior rear view mirrors position is effected by means of control
switches. The switches maintain the adjustment facility while depressed, movement ceasing when the switch is re- leased.
Manual adjustment can be achieved either with the ignition key in place or with the driver‘s door open, or having been
closed within the last
30 seconds.
The system offers the following facilities:
Entry
/ Exit mode; an automatic seat /column position setting for ease of driver entry into / exit from the vehicle.
Driving position set; automatic recall of up to three preferred settings.
Passenger seat set; automatic recall of up to three preferred settings.
Remote recall; automatic recall of up to two memory positions from
a remote transmitter (in key fob).
Reverse mirror dip; automatic adjustment of passenger rear view mirror when reversing.
U: Vehicles intended for the Japanese market are fitted with an additional ‘fold away’ mirror function. This func- tion allows mirrors to fold flat against the car when parking in enclosed areas.
15.4.1.1 Entry/ Exit Mode
Entry / Exit mode is designed to give easier vehicle entry and exit for the driver. The facility is selected by positioning
the mode switch, located on the LH side of the column cowl, to ‘auto’ which designates the current seat / column posi- tion, ie driving positions, as the memorized position. On removal of ignition key or opening of driver‘s door, with igni- tion key still in place, the driver’s seat will move to the rear (current position allowing) and the column will adopt ‘tilt
away’ mode automatically creating additional space for driver exit
/ entry. Insertion of key in ignition or closure of
driver‘s door (with ignition key in place) returns seat / column positions to the memorized (previous) position.
Operation of eitherthe brake pedal or
seat/column manual controls during entry/exit mode execution will abort posi- tional adjustments. Setting the mode switch to OFF disables operation of entry / exit mode.
15.4.1.2 Driving Position Set
Setting of seat, column and external rear view mirrors to preferred driving position is available using the memory but- tons located on the drivers door switch pack. With the ignition key in place enter settings to be memorized as follows:
Adjust seat, column and mirrors to desired positions.
Press the ’memory’ button
so that it becomes illuminated.
Press button
1,2 or 3 to store configuration within four seconds of memory button operation. Memory light will extin- guish and a chime will sound, indicating procedure complete.
The above procedure may be repeated two more times until each button
(1,2 & 3) has a preferred position stored in
memory, accommodating different driver settings. Operation of any push-button (1,2 or 3) will re-position seat col-
umn and mirrors to the stored settings.
Memory recall will operate under the following conditions:
. Ignition key in and gear selector in park.
8 Ignition key in and handbrake on.
8 Ignition key out and driver’s door open (or having been closed within the last 30 seconds).
Re
-setting the preferred position on any setting button automatically erases previously stored information. Memory
information is not erased if power supply to the seat and column / mirror control modules is lost (e.g. battery discon- nected).
15.4.1.3 Passenger Seat Set
The procedure for setting and recalling a preferred passenger seat position is identical to that for a driving position.
Memory recall will only operate with ignition key in auxiliary position or passenger door open, or having been closed
within the last
30 seconds.
X300 EDM 15.4 - 1 Issue 1 August 1994