steering wheel JAGUAR XJ6 1994 2.G User Guide
[x] Cancel search | Manufacturer: JAGUAR, Model Year: 1994, Model line: XJ6, Model: JAGUAR XJ6 1994 2.GPages: 521, PDF Size: 17.35 MB
Page 206 of 521
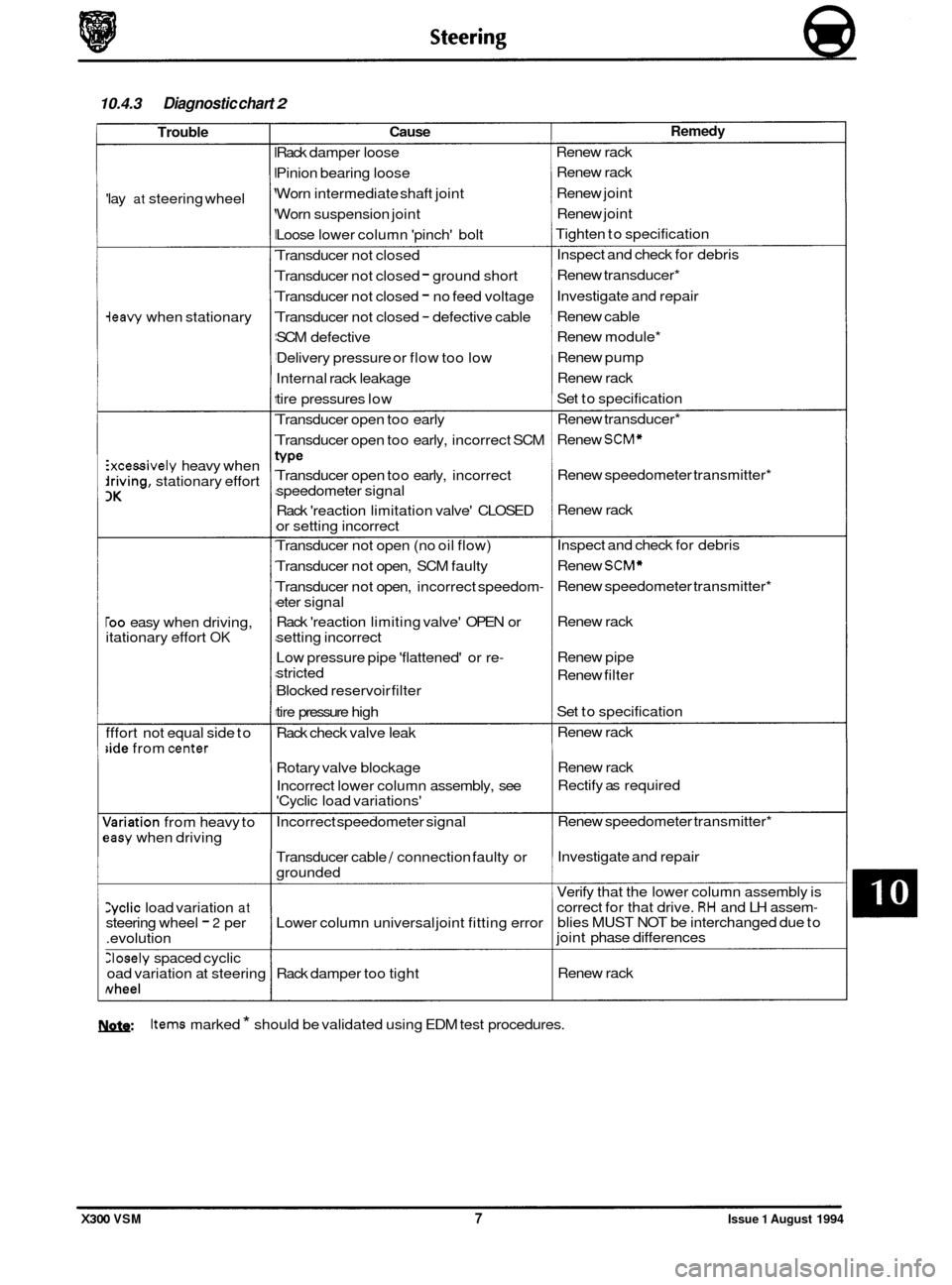
10.4.3 Diagnostic chart 2
0 Trouble
'lay at steering wheel
ieavy when stationary
Excessively heavy when
hiving, stationary effort
3K
Too easy when driving,
itationary effort OK
fffort not equal side to
;ide from center
dariation from heavy to
?asy when driving
:yclic load variation at steering wheel - 2 per
.evolution
:losely spaced cyclic
oad variation at steering
Nheel
Cause
Rack damper loose
Pinion bearing loose
Worn intermediate shaft joint
Worn suspension joint
Loose lower column 'pinch' bolt
Transducer not closed
Transducer not closed
- ground short
Transducer not closed
- no feed voltage
Transducer not closed
- defective cable
SCM defective
Delivery pressure or flow too low
Internal rack leakage
tire pressures low
Transducer open too early
Transducer open too early, incorrect SCM
h/Pe
Transducer open too early, incorrect
speedometer signal
Rack 'reaction limitation valve' CLOSED
or setting incorrect
Transducer not open (no oil flow)
Transducer not open, SCM faulty
Transducer not open, incorrect speedom
-
eter signal
Rack 'reaction limiting valve' OPEN or
setting incorrect
Low pressure pipe 'flattened' or re
-
stricted
Blocked reservoir filter
tire pressure high
Rack check valve leak
Rotary valve blockage Incorrect lower column assembly, see
'Cyclic load variations'
Incorrect speedometer signal
Transducer cable
/ connection faulty or
grounded
Lower column universal joint fitting error
Rack damper too tight
Remedy
Renew rack
Renew rack
Renew joint
Renew joint
Tighten to specification
Inspect and check for debris
Renew transducer*
Investigate and repair
Renew cable
Renew module*
Renew pump
Renew rack
Set to specification
Renew transducer*
Renew
SCM*
Renew speedometer transmitter*
Renew rack
Inspect and check for debris
Renew
SCM*
Renew speedometer transmitter*
Renew rack
Renew pipe
Renew filter
Set to specification
Renew rack
Renew rack
Rectify as required
Renew speedometer transmitter*
Investigate and repair
Verify that the lower column assembly is
correct for that drive.
RH and LH assem- blies MUST NOT be interchanged due to
joint phase differences
Renew rack
W: Items marked * should be validated using EDM test procedures.
X300 VSM 7 Issue 1 August 1994
Page 208 of 521
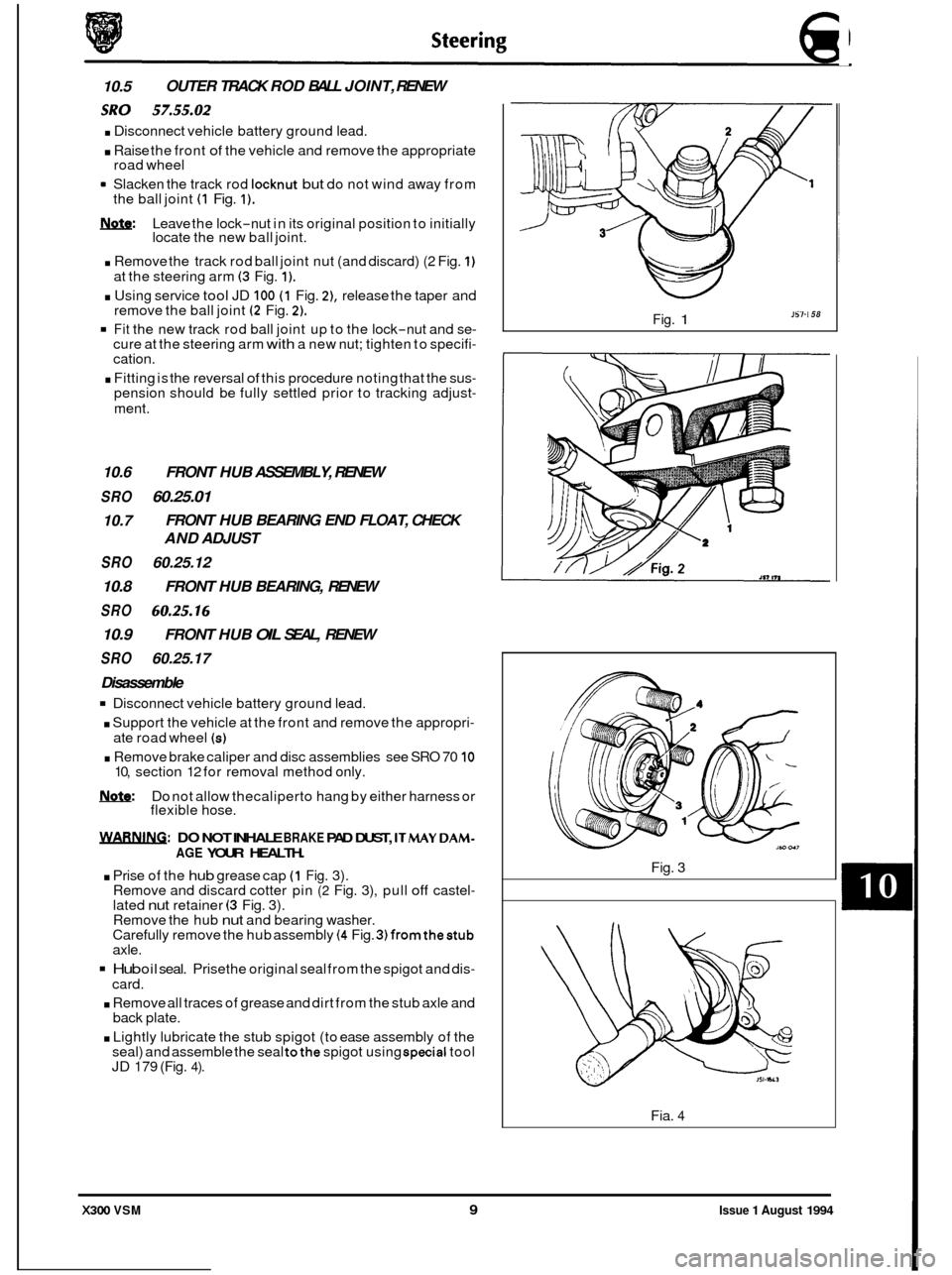
10.5 OUTER
TRACK ROD BALL JOINT, RENEW
sRo . Disconnect 57.55.02 vehicle battery ground lead.
. Raise the front of the vehicle and remove the appropriate
road wheel
Slacken the track rod
locknut but do not wind away from
the ball joint (1 Fig. 1).
m: Leave the lock-nut in its original position to initially
locate the new ball joint.
. Remove the track rod ball joint nut (and discard) (2 Fig. 1)
at the steering arm (3 Fig. 1).
. Using service tool JD 100 (1 Fig. 2), release the taper and
remove the ball joint (2 Fig. 2).
Fit the new track rod ball joint up to the lock-nut and se- cure at the steering arm with a new nut; tighten to specifi- cation.
. Fitting is the reversal of this procedure noting that the sus- pension should be fully settled prior to tracking adjust-
ment.
0 10.6 FRONT HUB ASSEMBLY, RENEW
SRO 60.25.01
10.7
SRO 60.25.12
10.8 FRONT HUB BEARING, RENEW
SRO 60.25.16
10.9
SRO 60.25.17
Disassemble
Disconnect vehicle battery ground lead.
. Support the vehicle at the front and remove the appropri-
. Remove brake caliper and disc assemblies see SRO 70 10
IWQ: Do not allow thecaliperto hang by either harness or
flexible hose.
FRONT HUB BEARING END FLOAT, CHECK
AND ADJUST
FRONT HUB
OIL SEAL, RENEW
ate road wheel (s)
10, section 12 for removal method only.
WARNIM: DO NOT INHALE BRAKE PAD DUST, ITMAY DAM-
0
AGE YOUR HEALTH.
. Prise of the hub grease cap (1 Fig. 3).
Remove and discard cotter pin (2 Fig. 3), pull off castel- lated nut retainer (3 Fig. 3).
Remove the hub nut and bearing washer.
Carefully remove the hub assembly (4 Fig. 3)fromthestub axle.
Hub oil seal. Prise the original seal from the spigot and dis-
card.
. Remove all traces of grease and dirt from the stub axle and
back plate.
. Lightly lubricate the stub spigot (to ease assembly of the
seal) and assemble the seal tothe spigot using special tool JD 179 (Fig. 4).
JS7-i 58 Fig. 1
Fig. 3
Fia.
4
X300 VSM 9 Issue 1 August 1994
Page 216 of 521
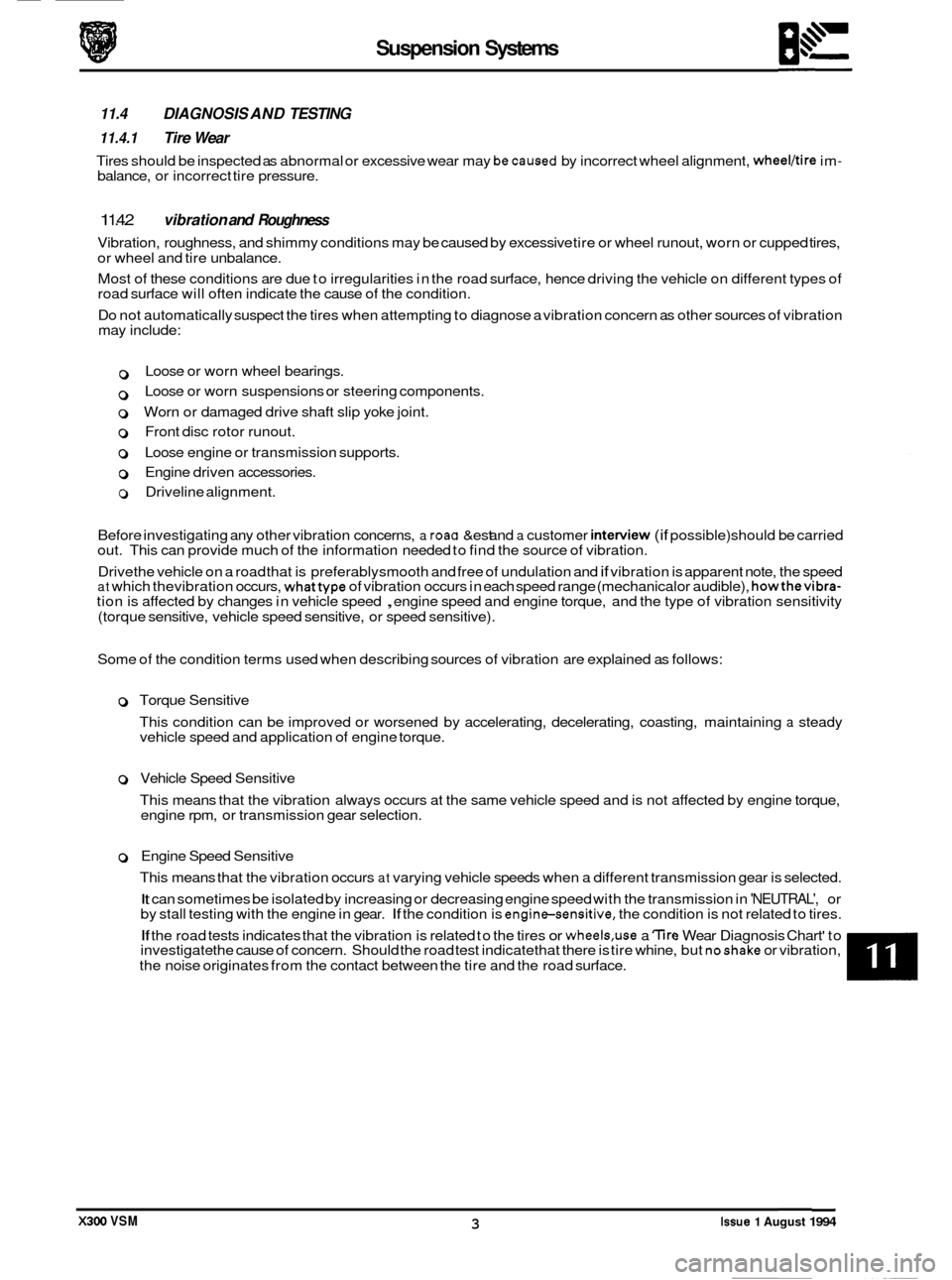
may include:
0
0
Loose or worn wheel bearings.
Loose or worn suspensions or steering components.
0 Worn or damaged drive shaft slip yoke joint.
0 Front disc rotor runout.
o Loose engine or transmission supports.
0 Driveline alignment.
0 Engine driven accessories.
Suspension Systems
11.4 DIAGNOSIS AND TESTING
' 11.4.1 Tire Wear
Tires should be inspected as abnormal or excessive wear may becaused by incorrect wheel alignment, wheelbire im- balance, or incorrect tire pressure.
1 1.4.2 vibration and Roughness
Vibration, roughness, and shimmy conditions may be caused by excessive tire or wheel runout, worn or cupped tires,
or wheel and tire unbalance.
Most of these conditions are due to irregularities in the road surface, hence driving the vehicle on different types of
road surface will often indicate the cause of the condition.
Do not automatically suspect the tires when attempting to diagnose a vibration concern as other sources of vibration
Before investigating any other vibration concerns,
a roaG &est and a customer inter\,.dw (if possible) should be carried
out. This can provide much of the information needed to find the source of vibration.
Drive the vehicle on a road that is preferably smooth and free of undulation and
if vibration is apparent note, the speed at which thevibration occurs, whattype of vibration occurs in each speed range (mechanical or audible), howthevibra- tion is affected by changes in vehicle speed , engine speed and engine torque, and the type of vibration sensitivity
(torque sensitive, vehicle speed sensitive, or speed sensitive).
Some of the condition terms used when describing sources of vibration are explained as follows:
0 Torque Sensitive
This condition can be improved or worsened by accelerating, decelerating, coasting, maintaining
a steady
vehicle speed and application of engine torque.
0 Vehicle Speed Sensitive
This means that the vibration always occurs at the same vehicle speed and is not affected by engine torque,
engine rpm, or transmission gear selection.
B
0 Engine Speed Sensitive
This means that the vibration occurs
at varying vehicle speeds when a different transmission gear is selected.
It can sometimes be isolated by increasing or decreasing engine speed with the transmission in 'NEUTRAL', or
by stall testing with the engine in gear. If the condition is enginesensitive, the condition is not related to tires.
If the road tests indicates that the vibration is related to the tires or wheels,use a 'lire Wear Diagnosis Chart' to
investigate the cause of concern. Should the road test indicate that there is tire whine, but noshake or vibration,
the noise originates from the contact between the tire and the road surface.
X300 VSM 3 Issue 1 August 1994
Page 217 of 521
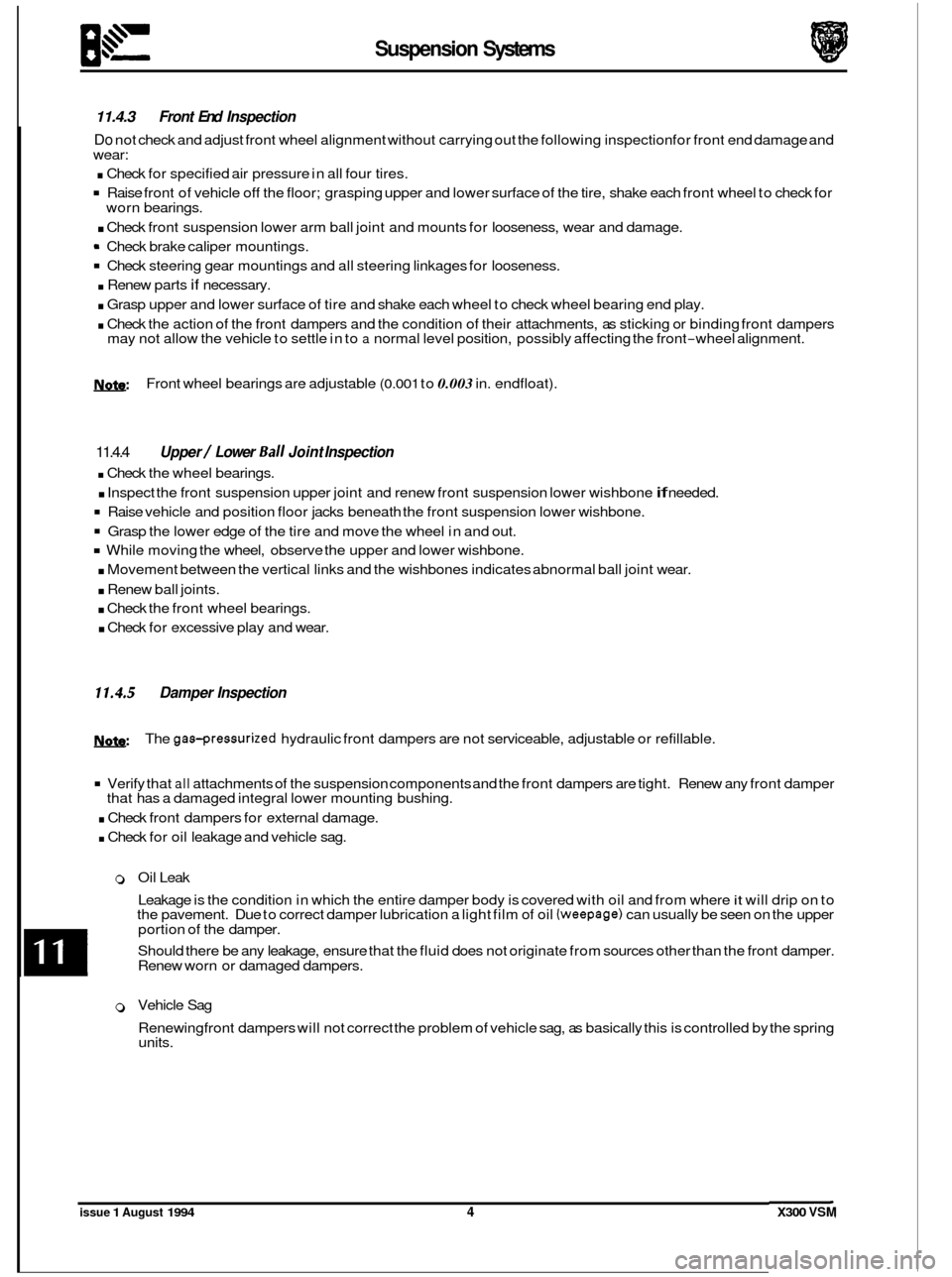
Suspension Systems
11.4.3 Front End Inspection
Do not check and adjust front wheel alignment without carrying out the following inspection for front end damage and
wear:
. Check for specified air pressure in all four tires.
Raise front of vehicle off the floor; grasping upper and lower surface of the tire, shake each front wheel to check for
. Check front suspension lower arm ball joint and mounts for looseness, wear and damage.
Check steering gear mountings and all steering linkages for looseness.
. Renew parts if necessary.
. Grasp upper and lower surface of tire and shake each wheel to check wheel bearing end play.
. Check the action of the front dampers and the condition of their attachments, as sticking or binding front dampers
worn
bearings.
Check brake caliper mountings.
may not allow the vehicle to settle in to a normal level position, possibly affecting the front-wheel alignment.
m: Front wheel bearings are adjustable (0.001 to 0.003 in. endfloat).
11.4.4
. Check the wheel bearings.
. Inspect the front suspension upper joint and renew front suspension lower wishbone if needed.
Raise vehicle and position floor jacks beneath the front suspension lower wishbone.
Grasp the lower edge of the tire and move the wheel in and out.
While moving the wheel, observe the upper and lower wishbone.
. Movement between the vertical links and the wishbones indicates abnormal ball joint wear.
. Renew ball joints.
. Check the front wheel bearings.
. Check for excessive play and wear.
Upper / Lower Ball Joint Inspection
11.4.5 Damper Inspection
m: The gas-pressurized hydraulic front dampers are not serviceable, adjustable or refillable.
Verify that all attachments of the suspension components and the front dampers are tight. Renew any front damper
. Check front dampers for external damage.
. Check for oil leakage and vehicle sag.
that
has a damaged integral lower mounting bushing.
0 Oil Leak
Leakage is the condition in which the entire damper body is covered with oil and from where
it will drip on to
the pavement. Due to correct damper lubrication a light film of oil (weepage) can usually be seen on the upper
portion of the damper.
Should there be any leakage, ensure that the fluid does not originate from sources other than the front damper.
Renew worn or damaged dampers.
0 Vehicle Sag
Renewing front dampers will not correct the problem of vehicle sag, as basically this is controlled by the spring
units.
issue 1 August 1994 4 X300 VSM
Page 219 of 521
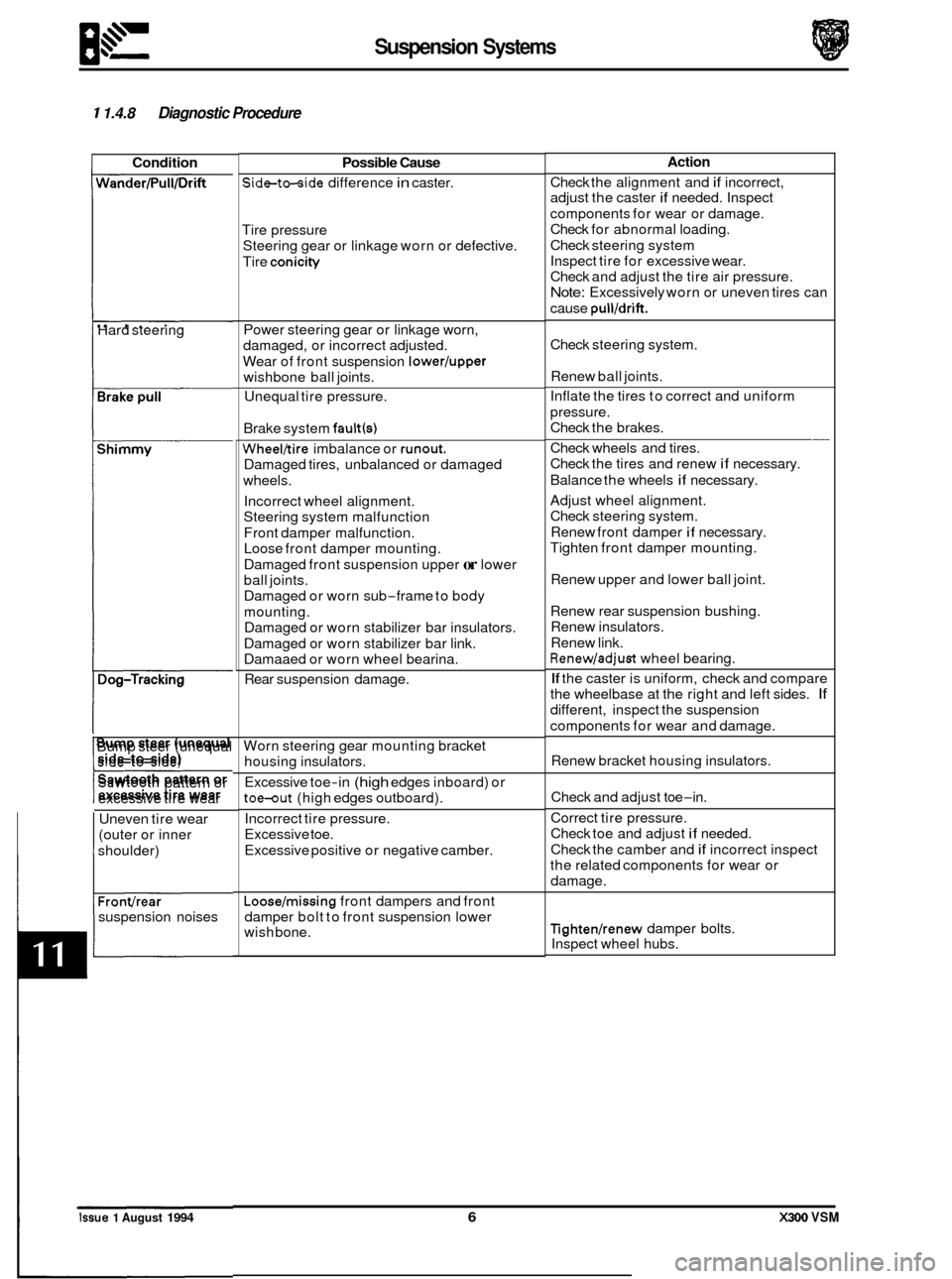
Suspension Systems
1 1.4.8 Diagnostic Procedure
Condition
Hard steering
Shimmy
I----
Bump steer (unequal
side-to-side)
Sawtooth pattern or
t excessive tire wear
Uneven tire wear
(outer or inner
shoulder)
Fronvrear
suspension noises
Possible Cause
Side-to-side difference in caster.
Tire pressure Steering gear or linkage worn or defective.
Tire
conicity
Power steering gear or linkage worn,
damaged, or incorrect adjusted.
Wear of front suspension
lower/upper
wishbone ball joints.
Unequal tire pressure.
Brake system
fault(s)
Wheel/tire imbalance or runout.
Damaged tires, unbalanced or damaged
wheels.
Incorrect wheel alignment.
Steering system malfunction
Front damper malfunction.
Loose front damper mounting.
Damaged front suspension upper
or lower
ball joints.
Damaged or worn sub
-frame to body
mounting. Damaged or worn stabilizer bar insulators.
Damaged or worn stabilizer bar link.
Damaaed or worn wheel bearina.
Rear suspension damage.
Worn steering gear mounting bracket
housing insulators.
Excessive toe
-in (high edges inboard) or
toe-out (high edges outboard).
Incorrect tire pressure.
Excessive toe.
Excessive positive or negative camber.
Loose/missing front dampers and front
damper bolt to front suspension lower
wish bone.
Action
Check the alignment and if incorrect,
adjust the caster
if needed. Inspect
components for wear or damage.
Check for abnormal loading.
Check steering system
Inspect tire for excessive wear.
Check and adjust the tire air pressure.
Note: Excessively worn or uneven tires can
cause
pull/drift.
Check steering system.
Renew ball joints.
Inflate the tires to correct and uniform
pressure.
Check the brakes.
Check wheels and tires.
Check the tires and renew
if necessary.
Balance the wheels
if necessary.
Adjust wheel alignment.
Check steering system.
Renew front damper
if necessary.
Tighten front damper mounting.
-
Renew upper and lower ball joint.
Renew rear suspension bushing.
Renew insulators.
Renew link.
Renew/adjust wheel bearing.
If the caster is uniform, check and compare
the wheelbase at the right and left sides.
If
different, inspect the suspension
components for wear and damage.
Renew bracket housing insulators.
Check and adjust toe
-in.
Correct tire pressure.
Check toe and adjust
if needed.
Check the camber and
if incorrect inspect
the related components for wear or
damage.
Tighten/renew damper bolts.
Inspect wheel hubs.
0
0
0
lssue 1 August 1994 6 X300 VSM
Page 220 of 521
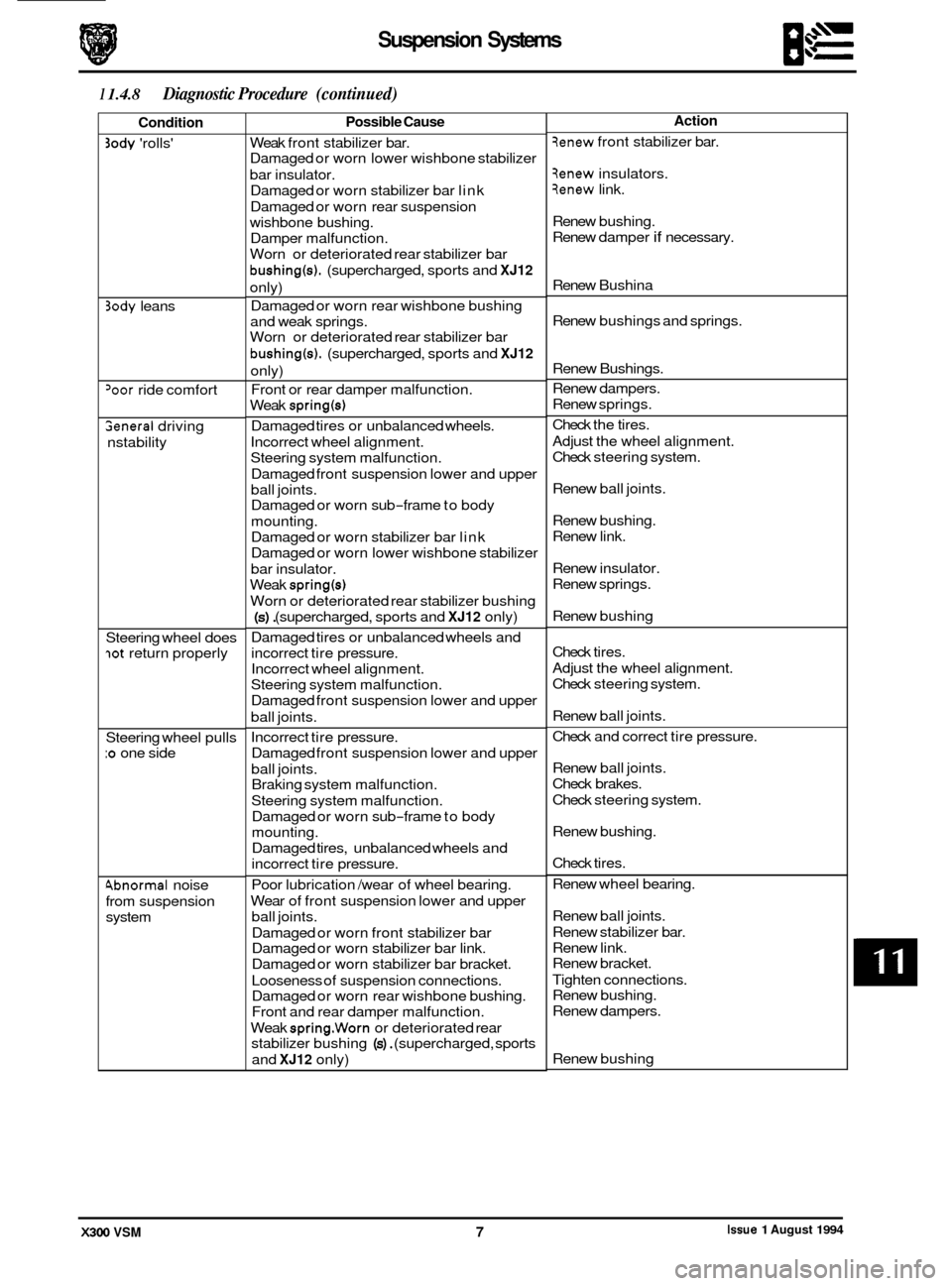
Suspension Systems I.\" b-
1 1.4.8 Diagnostic Procedure (continued)
Condition
30dy 'rolls'
3ody leans
'oor ride comfort
Seneral driving
nstability
Steering wheel does
lot return properly
Steering wheel pulls
:o one side
4bnormal noise
from suspension
system
Possible Cause
Weak front stabilizer bar.
Damaged or worn lower wishbone stabilizer
bar insulator. Damaged or worn stabilizer bar link
Damaged or worn rear suspension
wishbone bushing.
Damper malfunction.
Worn or deteriorated rear stabilizer bar
bushing(s). (supercharged, sports and XJ12
only)
Damaged or worn rear wishbone bushing
and weak springs.
Worn or deteriorated rear stabilizer bar
bushing(s). (supercharged, sports and XJ12
only)
Front or rear damper malfunction.
Weak
spring(s1
Damaged tires or unbalanced wheels.
Incorrect wheel alignment.
Steering system malfunction.
Damaged front suspension lower and upper
ball joints.
Damaged or worn sub
-frame to body
mounting.
Damaged or worn stabilizer bar link
Damaged or worn lower wishbone stabilizer
bar insulator.
Weak
spring(s)
Worn or deteriorated rear stabilizer bushing
(s). (supercharged, sports and XJ12 only)
Damaged tires or unbalanced wheels and
incorrect tire pressure.
Incorrect wheel alignment.
Steering system malfunction.
Damaged front suspension lower and upper
ball joints.
Incorrect tire pressure.
Damaged front suspension lower and upper
ball joints. Braking system malfunction.
Steering system malfunction.
Damaged or worn sub
-frame to body
mounting.
Damaged tires, unbalanced wheels and
incorrect tire pressure.
Poor lubrication /wear of wheel bearing.
Wear of front suspension lower and upper
ball joints.
Damaged or worn front stabilizer bar
Damaged or worn stabilizer bar link.
Damaged or worn stabilizer bar bracket.
Looseness of suspension connections.
Damaged or worn rear wishbone bushing.
Front and rear damper malfunction.
Weak
spring.Worn or deteriorated rear
stabilizer bushing
(s). (supercharged, sports
and
XJ12 only)
Action
3enew front stabilizer bar.
3enew insulators.
3enew link.
Renew bushing.
Renew damper
if necessary.
Renew Bushina
Renew bushings and springs.
Renew Bushings.
Renew dampers.
Renew springs.
Check the tires.
Adjust the wheel alignment.
Check steering system.
Renew ball joints.
Renew bushing.
Renew link.
Renew insulator.
Renew springs.
Renew bushing
Check tires.
Adjust the wheel alignment.
Check steering system.
Renew ball joints.
Check and correct tire pressure.
Renew ball joints.
Check brakes.
Check steering system.
Renew bushing.
Check tires.
Renew wheel bearing.
Renew ball joints.
Renew stabilizer bar.
Renew link.
Renew bracket.
Tighten connections.
Renew bushing.
Renew dampers.
Renew bushing
Issue 1 August 1994 X300 VSM 7
Page 246 of 521
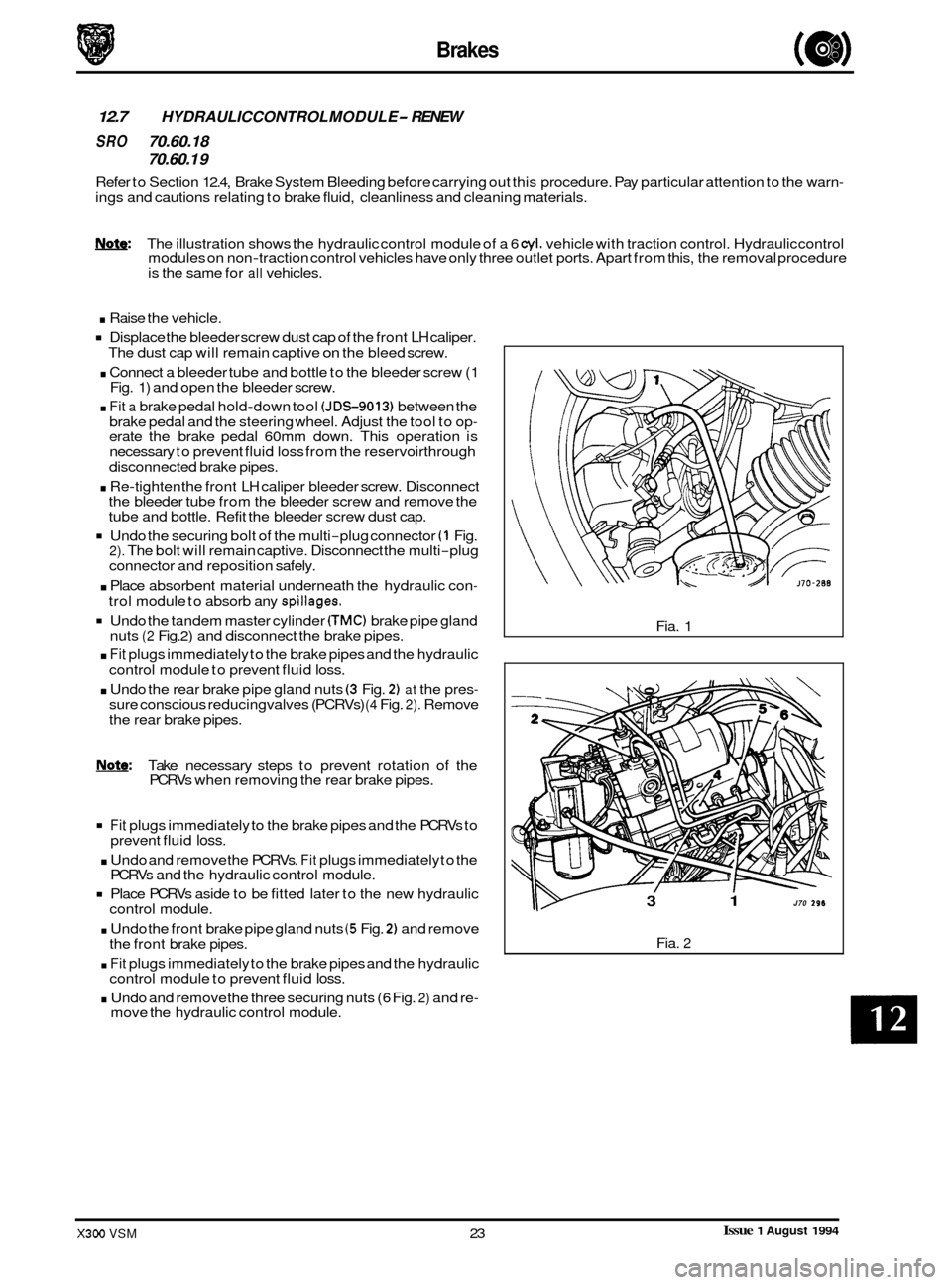
Brakes
12.7 HYDRAULICCONTROL MODULE- RENEW
SRO 70.60.18
70.60.1
9
Refer to Section 12.4, Brake System Bleeding before carrying out this procedure. Pay particular attention to the warn- ings and cautions relating to brake fluid, cleanliness and cleaning materials.
W: The illustration shows the hydraulic control module of a 6 cyl. vehicle with traction control. Hydraulic control
modules on non-traction control vehicles have only three outlet ports. Apart from this, the removal procedure
is the same for all vehicles.
. Raise the vehicle.
Displace the bleeder screw dust cap of the front LH caliper.
The dust cap will remain captive
on the bleed screw.
. Connect a bleeder tube and bottle to the bleeder screw (1
Fig. 1) and open the bleeder screw.
. Fit a brake pedal hold-down tool (JDS-9013) between the
brake pedal and the steering wheel. Adjust the tool to op
- erate the brake pedal 60mm down. This operation is
necessary to prevent fluid loss from the reservoirthrough
. Re-tighten the front LH caliper bleeder screw. Disconnect
the bleeder tube from the bleeder screw and remove the
tube and bottle. Refit the bleeder screw dust cap.
Undo the securing bolt of the multi-plug connector (1 Fig. 2). The bolt will remain captive. Disconnect the multi-plug
connector and reposition safely.
. Place absorbent material underneath the hydraulic con-
trol module to absorb any spillages.
Undo the tandem master cylinder CTMC) brake pipe gland
nuts (2 Fig.2) and disconnect the brake pipes.
. Fit plugs immediately to the brake pipes and the hydraulic
control module to prevent fluid
loss.
. Undo the rear brake pipe gland nuts (3 Fig. 2) at the pres- sure conscious reducing valves (PCRVs) (4 Fig. 2). Remove
the rear brake pipes.
disconnected brake pipes.
Note: Take necessary steps to prevent rotation of the
PCRVs when removing the rear brake pipes.
Fit plugs immediately to the brake pipes and the PCRVs to
. Undo and remove the PCRVs. Fit plugs immediately to the
Place PCRVs aside to be fitted later to the new hydraulic
. Undo the front brake pipe gland nuts (5 Fig. 2) and remove
. Fit plugs immediately to the brake pipes and the hydraulic
. Undo and remove the three securing nuts (6 Fig. 2) and re-
0 prevent fluid loss.
PCRVs and the hydraulic control module.
control module.
the front brake pipes.
control module to prevent fluid
loss.
move the hydraulic control module. Fia.
1
3 1 J70 296
Fia. 2
Issue 1 August 1994 X300 VSM 23
Page 248 of 521
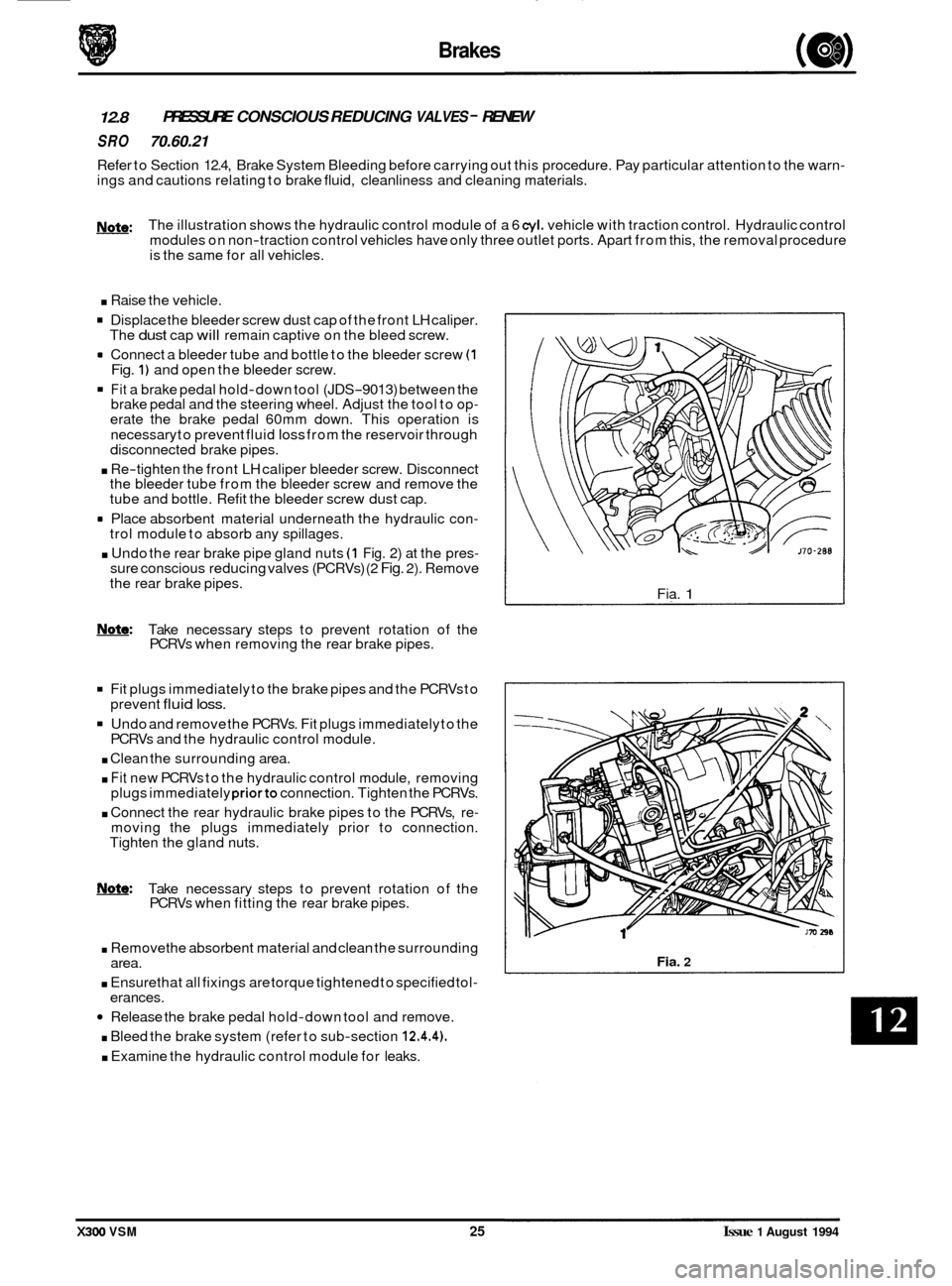
Brakes
12.8
SRO 70.60.21
PRESSURE CONSCIOUS REDUCING VALVES - RENEW
Refer to Section 12.4, Brake System Bleeding before carrying out this procedure. Pay particular attention to the warn- ings and cautions relating to brake fluid, cleanliness and cleaning materials.
Note: The illustration shows the hydraulic control module of a 6 cyl. vehicle with traction control. Hydraulic control
modules on non-traction control vehicles have only three outlet ports. Apart from this, the removal procedure
is the same for all vehicles.
. Raise the vehicle.
Displace the bleeder screw dust cap of the front LH caliper.
The dust cap will remain captive on the bleed screw.
rn Connect a bleeder tube and bottle to the bleeder screw (1 Fig. 1) and open the bleeder screw.
Fit a brake pedal hold-down tool (JDS-9013) between the
brake pedal and the steering wheel. Adjust the tool to op- erate the brake pedal 60mm down. This operation is
necessary to prevent fluid
loss from the reservoir through
disconnected brake pipes.
. Re-tighten the front LH caliper bleeder screw. Disconnect
the bleeder tube from the bleeder screw and remove the
tube and bottle. Refit the bleeder screw dust cap.
rn Place absorbent material underneath the hydraulic con- trol module to absorb any spillages.
. Undo the rear brake pipe gland nuts (1 Fig. 2) at the pres- sure conscious reducing valves (PCRVs) (2 Fig. 2). Remove
the rear brake pipes.
m: Take necessary steps to prevent rotation of the
PCRVs when removing the rear brake pipes.
Fit plugs immediately to the brake pipes and the PCRVs to
Undo and remove the PCRVs. Fit plugs immediately to the
. Clean the surrounding area.
. Fit new PCRVs to the hydraulic control module, removing
plugs immediately priorto connection. Tighten the PCRVs.
. Connect the rear hydraulic brake pipes to the PCRVs, re- moving the plugs immediately prior to connection.
Tighten the gland nuts.
prevent
fluid loss.
PCRVs
and the hydraulic control module.
0
Note: Take necessary steps to prevent rotation of the
PCRVs when fitting the rear brake pipes.
. Removethe absorbent material and clean the surrounding
. Ensure that all fixings are torque tightened to specified tol-
Release the brake pedal hold-down tool and remove.
. Bleed the brake system (refer to sub-section 12.4.4).
. Examine the hydraulic control module for leaks.
area.
erances. Fia.
1
Fia. 2
X300 VSM 25 Issue 1 August 1994
Page 276 of 521
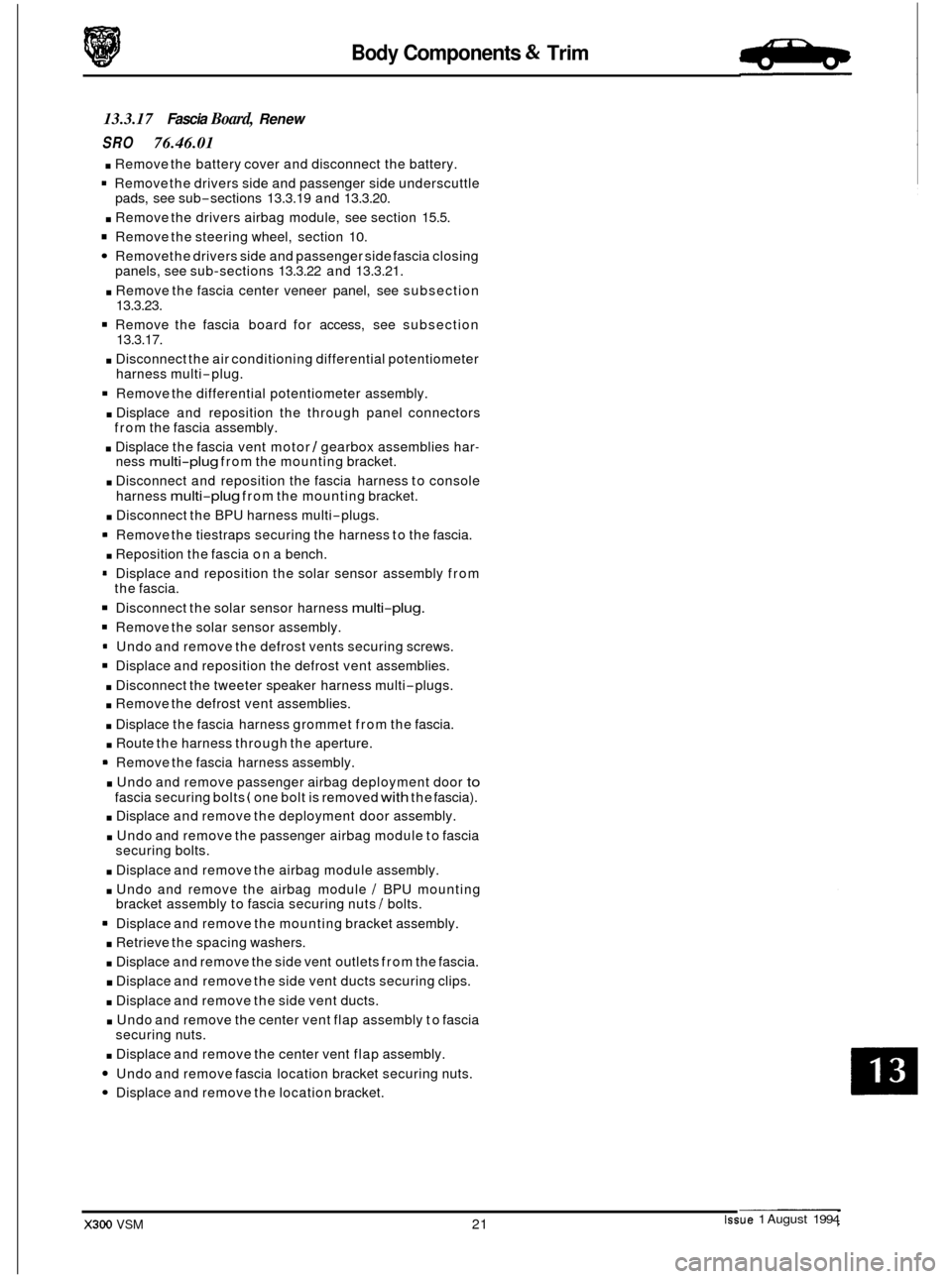
Body Components & Trim ~
issue 1 August 1994 X300 VSM 21
13.3.17 Fascia Board, Renew
SRO 76.46.01
. Remove
the battery cover and disconnect the battery.
Remove the drivers side and passenger side underscuttle
pads, see sub
-sections 13.3.19 and 13.3.20.
. Remove the drivers airbag module, see section 15.5.
Remove the steering wheel, section 10.
Remove the drivers side and passenger side fascia closing
. Remove the fascia center veneer panel, see subsection
Remove the fascia board for access, see subsection
. Disconnect the air conditioning differential potentiometer
Remove the differential potentiometer assembly.
. Displace and reposition the through panel connectors
from the fascia assembly.
. Displace the fascia vent motor / gearbox assemblies har- ness multi-plug from the mounting bracket.
. Disconnect and reposition the fascia harness to console
harness
multi-plug from the mounting bracket.
. Disconnect the BPU harness multi-plugs.
Remove the tiestraps securing the harness to the fascia.
. Reposition the fascia on a bench.
= Displace and reposition the solar sensor assembly from
Disconnect the solar sensor harness multi-plug.
Remove the solar sensor assembly.
= Undo and remove the defrost vents securing screws.
Displace and reposition the defrost vent assemblies.
. Disconnect the tweeter speaker harness multi-plugs.
. Remove the defrost vent assemblies.
. Displace the fascia harness grommet from the fascia.
. Route the harness through the aperture.
Remove the fascia harness assembly.
. Undo and remove passenger airbag deployment door to
fascia securing bolts ( one bolt is removed with the fascia).
. Displace and remove the deployment door assembly.
. Undo and remove the passenger airbag module to fascia
. Displace and remove the airbag module assembly.
. Undo and remove the airbag module I BPU mounting
bracket assembly to fascia securing nuts 1 bolts.
= Displace and remove the mounting bracket assembly.
. Retrieve the spacing washers.
. Displace and remove the side vent outlets from the fascia.
. Displace and remove the side vent ducts securing clips.
. Displace and remove the side vent ducts.
. Undo and remove the center vent flap assembly to fascia
. Displace and remove the center vent flap assembly.
Undo and remove fascia location bracket securing nuts.
Displace and remove the location bracket.
panels, see
sub
-sections 13.3.22 and 13.3.21.
13.3.23. 13.3.17.
harness multi
-plug.
the fascia.
securing bolts.
securing nuts.
Page 278 of 521
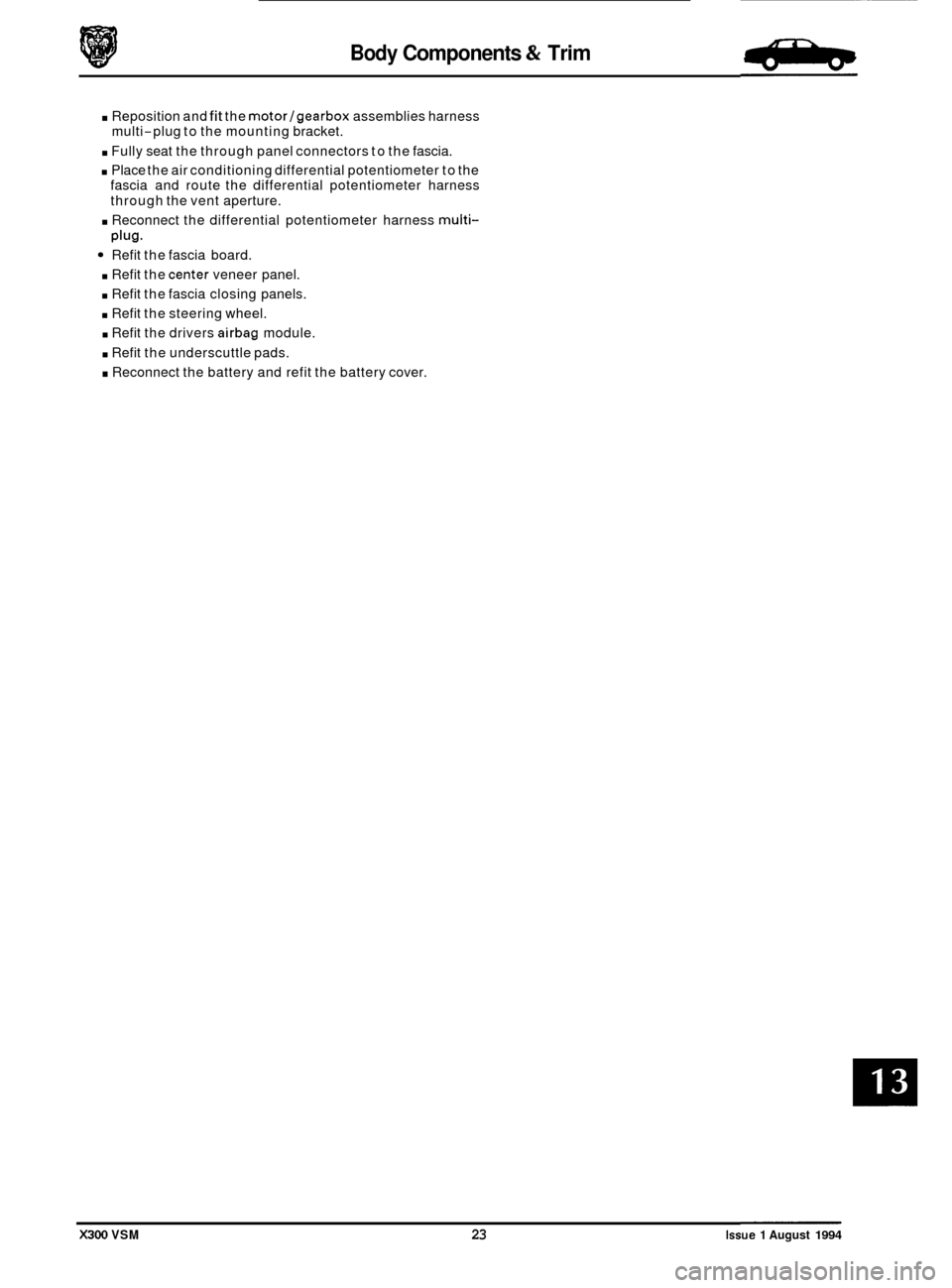
Body Components & Trim
. Reposition and fit the motor/gearbox assemblies harness
. Fully seat the through panel connectors to the fascia.
. Place the air conditioning differential potentiometer to the
fascia and route the differential potentiometer harness
through the vent aperture.
. Reconnect the differential potentiometer harness multi-
Plug.
Refit the fascia board.
. Refit the center veneer panel.
. Refit the fascia closing panels.
. Refit the steering wheel.
. Refit the drivers airbag module.
. Refit the underscuttle pads.
. Reconnect the battery and refit the battery cover.
multi
-plug
to the mounting bracket.
X300 VSM 23 Issue 1 August 1994