JEEP CHEROKEE 1995 Service Repair Manual
Manufacturer: JEEP, Model Year: 1995, Model line: CHEROKEE, Model: JEEP CHEROKEE 1995Pages: 2198, PDF Size: 82.83 MB
Page 111 of 2198
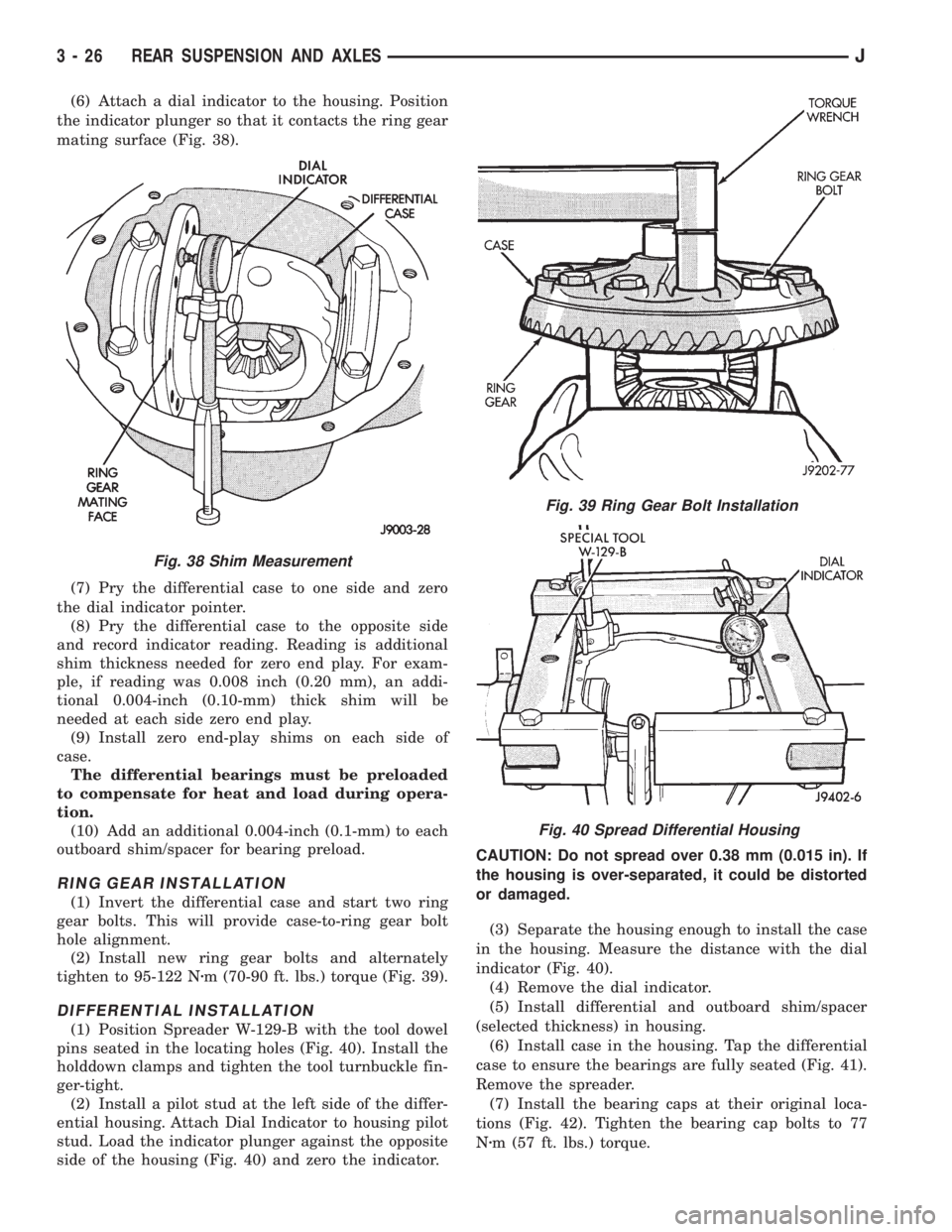
(6) Attach a dial indicator to the housing. Position
the indicator plunger so that it contacts the ring gear
mating surface (Fig. 38).
(7) Pry the differential case to one side and zero
the dial indicator pointer.
(8) Pry the differential case to the opposite side
and record indicator reading. Reading is additional
shim thickness needed for zero end play. For exam-
ple, if reading was 0.008 inch (0.20 mm), an addi-
tional 0.004-inch (0.10-mm) thick shim will be
needed at each side zero end play.
(9) Install zero end-play shims on each side of
case.
The differential bearings must be preloaded
to compensate for heat and load during opera-
tion.
(10) Add an additional 0.004-inch (0.1-mm) to each
outboard shim/spacer for bearing preload.
RING GEAR INSTALLATION
(1) Invert the differential case and start two ring
gear bolts. This will provide case-to-ring gear bolt
hole alignment.
(2) Install new ring gear bolts and alternately
tighten to 95-122 Nzm (70-90 ft. lbs.) torque (Fig. 39).
DIFFERENTIAL INSTALLATION
(1) Position Spreader W-129-B with the tool dowel
pins seated in the locating holes (Fig. 40). Install the
holddown clamps and tighten the tool turnbuckle fin-
ger-tight.
(2) Install a pilot stud at the left side of the differ-
ential housing. Attach Dial Indicator to housing pilot
stud. Load the indicator plunger against the opposite
side of the housing (Fig. 40) and zero the indicator.CAUTION: Do not spread over 0.38 mm (0.015 in). If
the housing is over-separated, it could be distorted
or damaged.
(3) Separate the housing enough to install the case
in the housing. Measure the distance with the dial
indicator (Fig. 40).
(4) Remove the dial indicator.
(5) Install differential and outboard shim/spacer
(selected thickness) in housing.
(6) Install case in the housing. Tap the differential
case to ensure the bearings are fully seated (Fig. 41).
Remove the spreader.
(7) Install the bearing caps at their original loca-
tions (Fig. 42). Tighten the bearing cap bolts to 77
Nzm (57 ft. lbs.) torque.
Fig. 38 Shim Measurement
Fig. 39 Ring Gear Bolt Installation
Fig. 40 Spread Differential Housing
3 - 26 REAR SUSPENSION AND AXLESJ
Page 112 of 2198
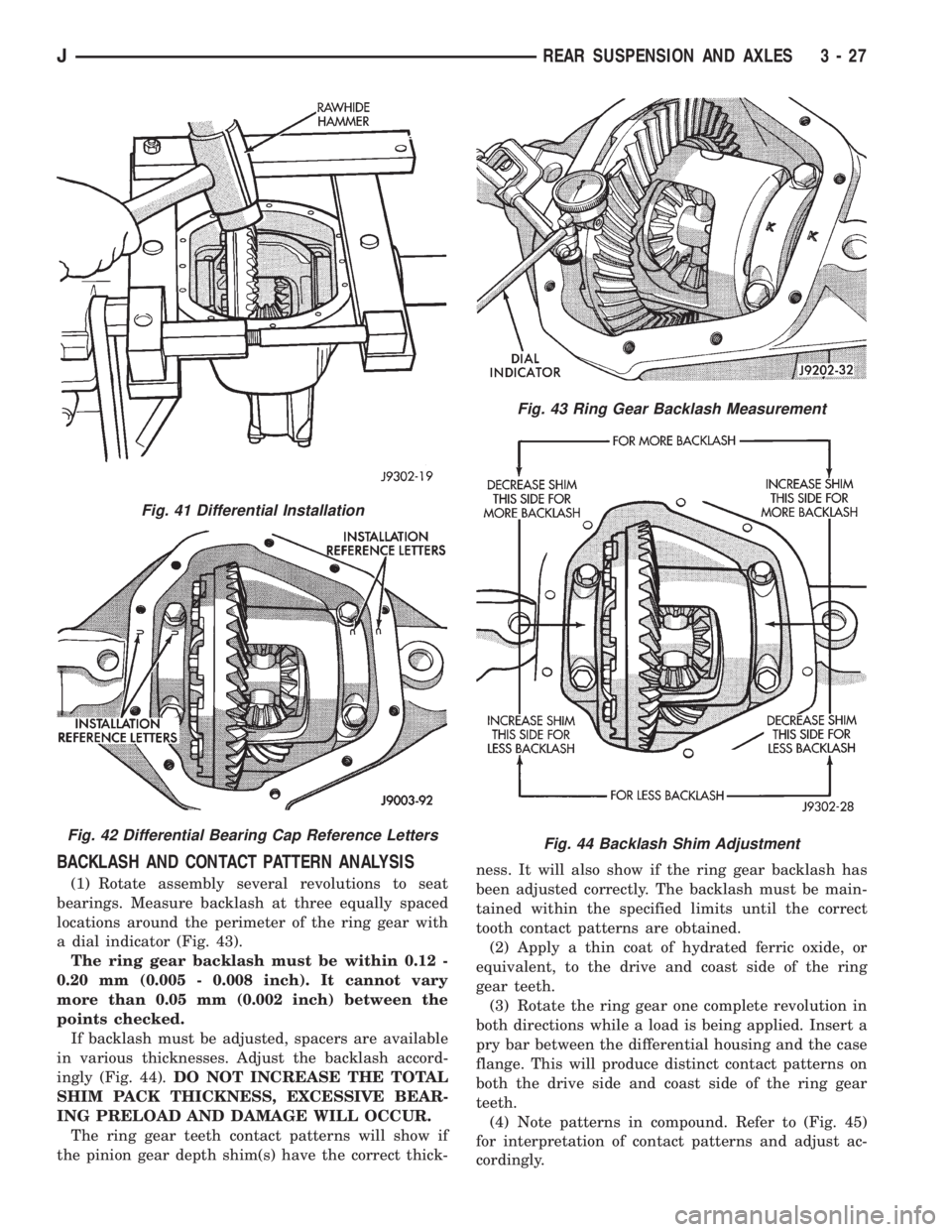
BACKLASH AND CONTACT PATTERN ANALYSIS
(1) Rotate assembly several revolutions to seat
bearings. Measure backlash at three equally spaced
locations around the perimeter of the ring gear with
a dial indicator (Fig. 43).
The ring gear backlash must be within 0.12 -
0.20 mm (0.005 - 0.008 inch). It cannot vary
more than 0.05 mm (0.002 inch) between the
points checked.
If backlash must be adjusted, spacers are available
in various thicknesses. Adjust the backlash accord-
ingly (Fig. 44).DO NOT INCREASE THE TOTAL
SHIM PACK THICKNESS, EXCESSIVE BEAR-
ING PRELOAD AND DAMAGE WILL OCCUR.
The ring gear teeth contact patterns will show if
the pinion gear depth shim(s) have the correct thick-ness. It will also show if the ring gear backlash has
been adjusted correctly. The backlash must be main-
tained within the specified limits until the correct
tooth contact patterns are obtained.
(2) Apply a thin coat of hydrated ferric oxide, or
equivalent, to the drive and coast side of the ring
gear teeth.
(3) Rotate the ring gear one complete revolution in
both directions while a load is being applied. Insert a
pry bar between the differential housing and the case
flange. This will produce distinct contact patterns on
both the drive side and coast side of the ring gear
teeth.
(4) Note patterns in compound. Refer to (Fig. 45)
for interpretation of contact patterns and adjust ac-
cordingly.
Fig. 41 Differential Installation
Fig. 42 Differential Bearing Cap Reference Letters
Fig. 43 Ring Gear Backlash Measurement
Fig. 44 Backlash Shim Adjustment
JREAR SUSPENSION AND AXLES 3 - 27
Page 113 of 2198
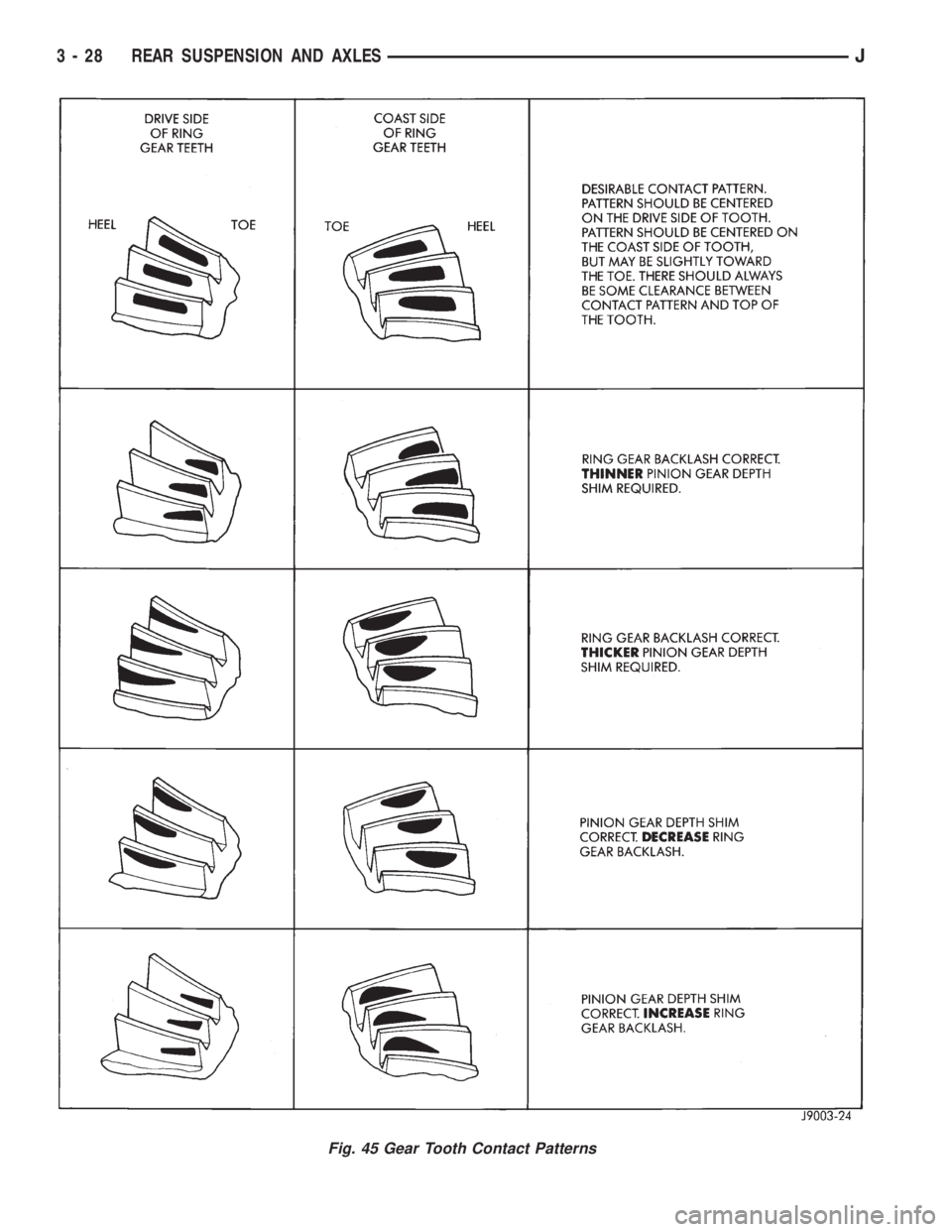
Fig. 45 Gear Tooth Contact Patterns
3 - 28 REAR SUSPENSION AND AXLESJ
Page 114 of 2198
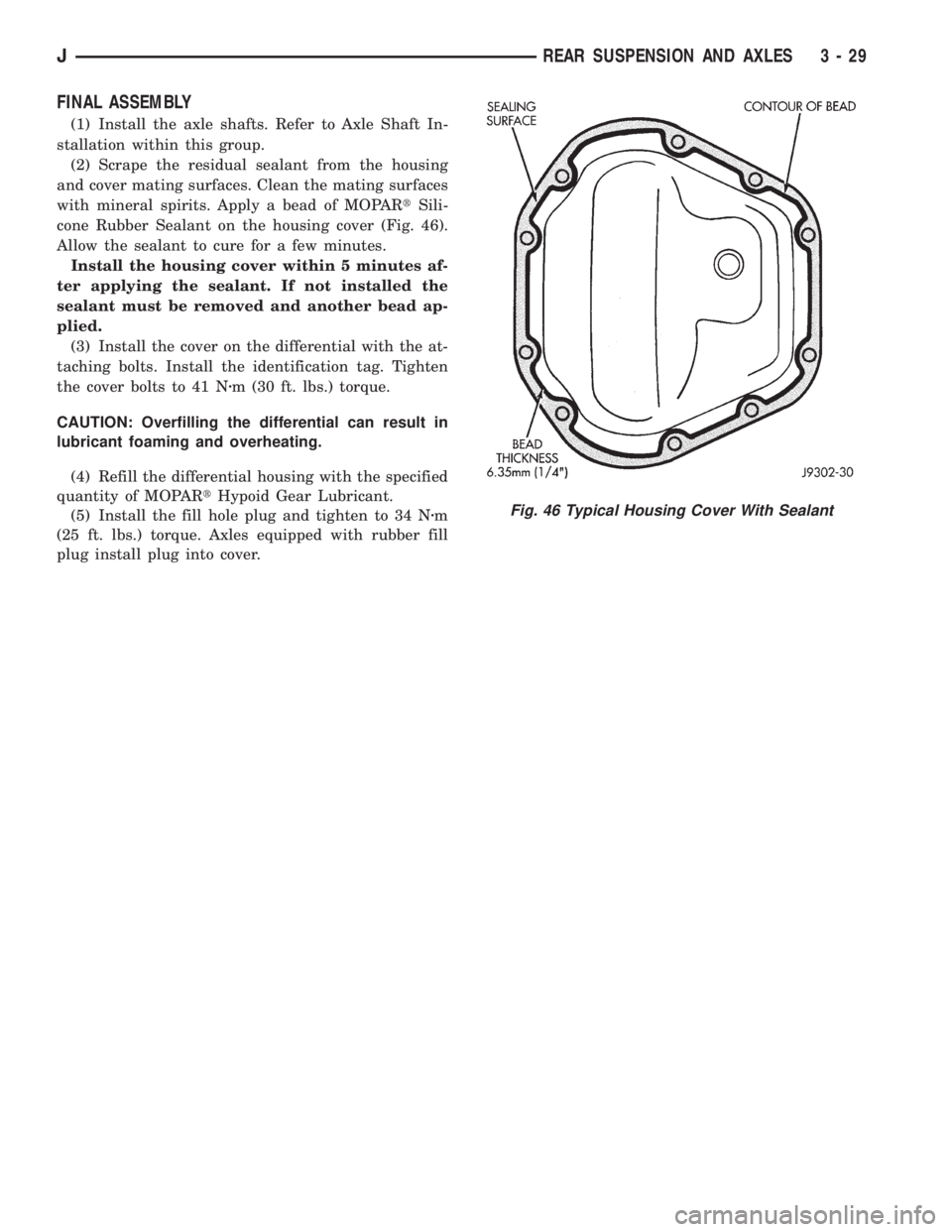
FINAL ASSEMBLY
(1) Install the axle shafts. Refer to Axle Shaft In-
stallation within this group.
(2) Scrape the residual sealant from the housing
and cover mating surfaces. Clean the mating surfaces
with mineral spirits. Apply a bead of MOPARtSili-
cone Rubber Sealant on the housing cover (Fig. 46).
Allow the sealant to cure for a few minutes.
Install the housing cover within 5 minutes af-
ter applying the sealant. If not installed the
sealant must be removed and another bead ap-
plied.
(3) Install the cover on the differential with the at-
taching bolts. Install the identification tag. Tighten
the cover bolts to 41 Nzm (30 ft. lbs.) torque.
CAUTION: Overfilling the differential can result in
lubricant foaming and overheating.
(4) Refill the differential housing with the specified
quantity of MOPARtHypoid Gear Lubricant.
(5) Install the fill hole plug and tighten to 34 Nzm
(25 ft. lbs.) torque. Axles equipped with rubber fill
plug install plug into cover.
Fig. 46 Typical Housing Cover With Sealant
JREAR SUSPENSION AND AXLES 3 - 29
Page 115 of 2198
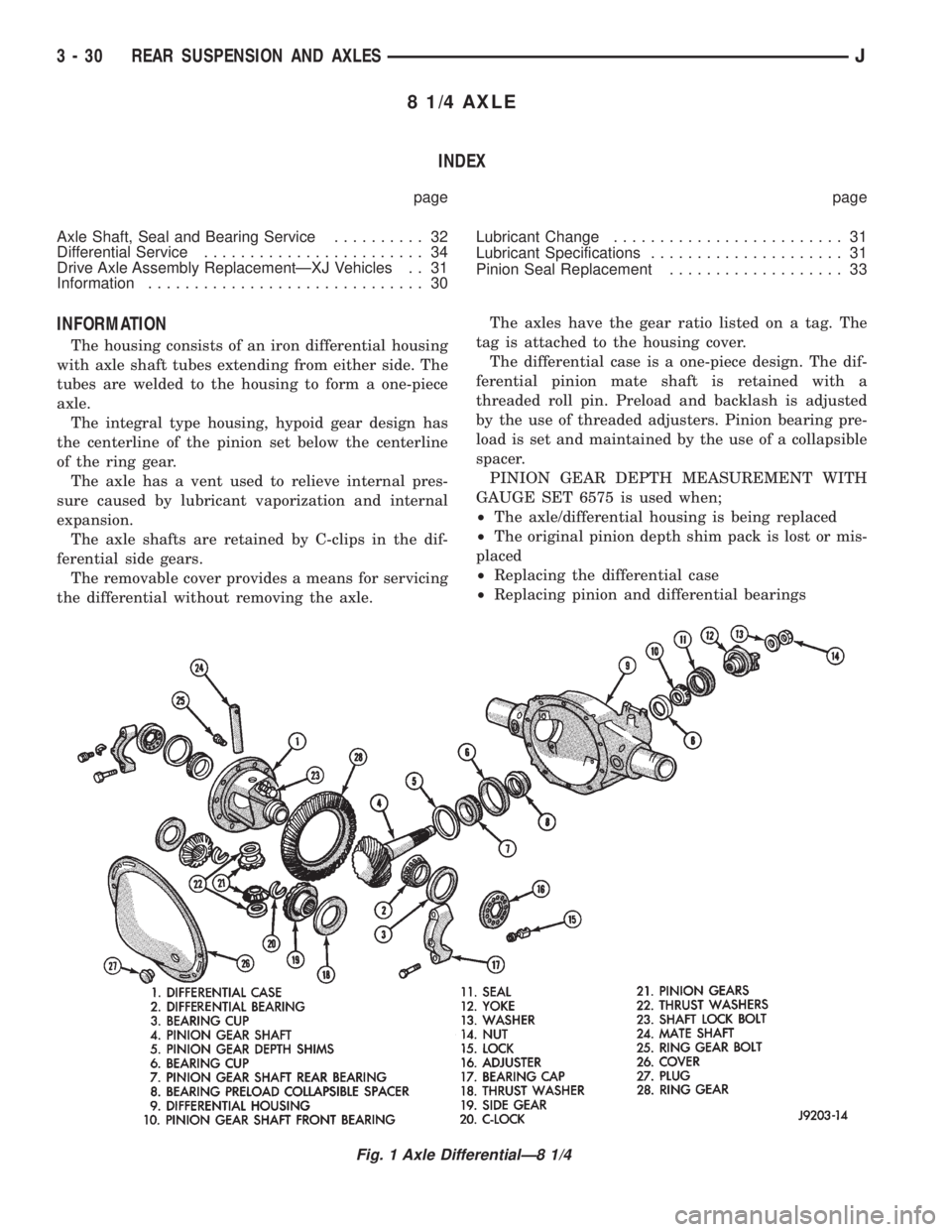
8 1/4 AXLE
INDEX
page page
Axle Shaft, Seal and Bearing Service.......... 32
Differential Service........................ 34
Drive Axle Assembly ReplacementÐXJ Vehicles . . 31
Information.............................. 30Lubricant Change......................... 31
Lubricant Specifications..................... 31
Pinion Seal Replacement................... 33
INFORMATION
The housing consists of an iron differential housing
with axle shaft tubes extending from either side. The
tubes are welded to the housing to form a one-piece
axle.
The integral type housing, hypoid gear design has
the centerline of the pinion set below the centerline
of the ring gear.
The axle has a vent used to relieve internal pres-
sure caused by lubricant vaporization and internal
expansion.
The axle shafts are retained by C-clips in the dif-
ferential side gears.
The removable cover provides a means for servicing
the differential without removing the axle.The axles have the gear ratio listed on a tag. The
tag is attached to the housing cover.
The differential case is a one-piece design. The dif-
ferential pinion mate shaft is retained with a
threaded roll pin. Preload and backlash is adjusted
by the use of threaded adjusters. Pinion bearing pre-
load is set and maintained by the use of a collapsible
spacer.
PINION GEAR DEPTH MEASUREMENT WITH
GAUGE SET 6575 is used when;
²The axle/differential housing is being replaced
²The original pinion depth shim pack is lost or mis-
placed
²Replacing the differential case
²Replacing pinion and differential bearings
Fig. 1 Axle DifferentialÐ8 1/4
3 - 30 REAR SUSPENSION AND AXLESJ
Page 116 of 2198
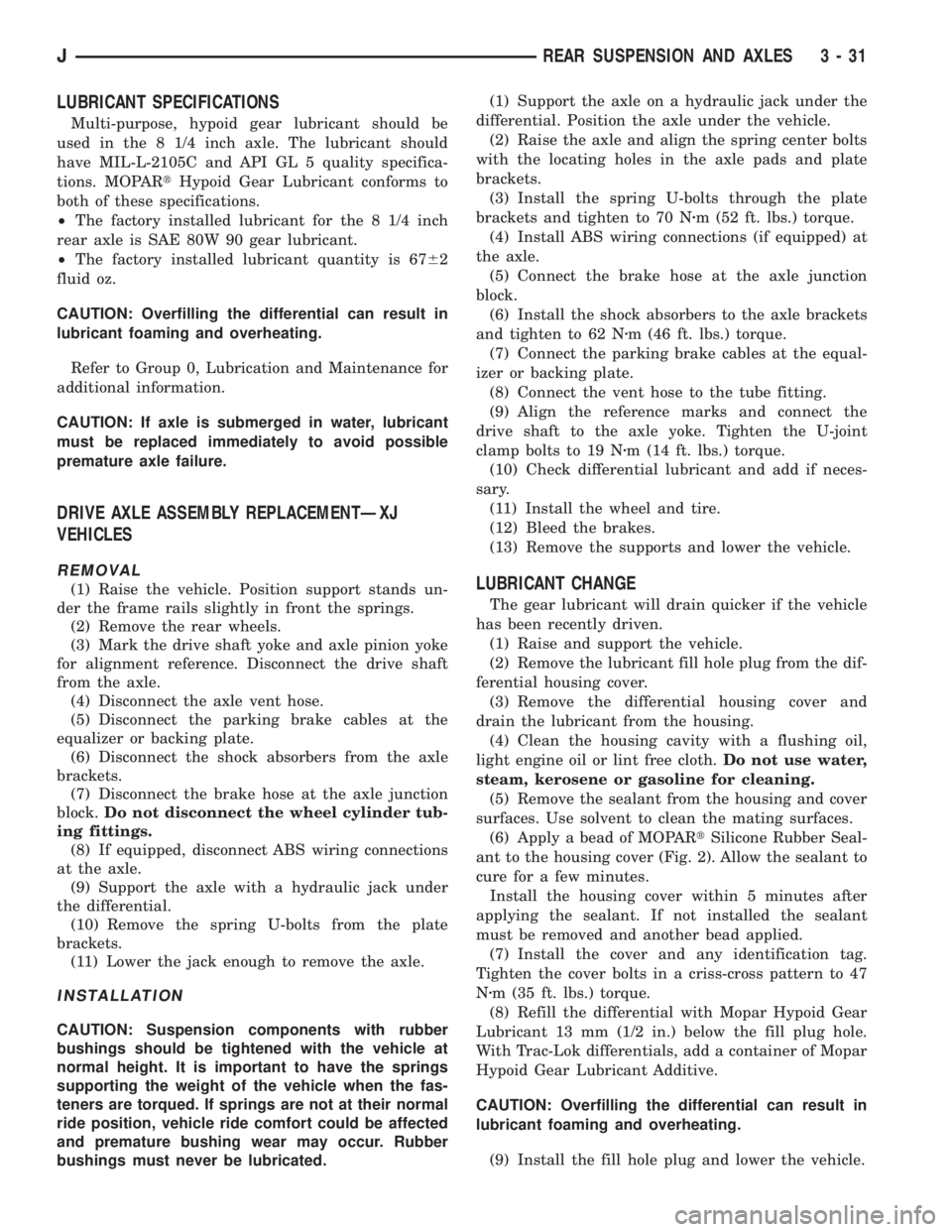
LUBRICANT SPECIFICATIONS
Multi-purpose, hypoid gear lubricant should be
used in the 8 1/4 inch axle. The lubricant should
have MIL-L-2105C and API GL 5 quality specifica-
tions. MOPARtHypoid Gear Lubricant conforms to
both of these specifications.
²The factory installed lubricant for the 8 1/4 inch
rear axle is SAE 80W 90 gear lubricant.
²The factory installed lubricant quantity is 6762
fluid oz.
CAUTION: Overfilling the differential can result in
lubricant foaming and overheating.
Refer to Group 0, Lubrication and Maintenance for
additional information.
CAUTION: If axle is submerged in water, lubricant
must be replaced immediately to avoid possible
premature axle failure.
DRIVE AXLE ASSEMBLY REPLACEMENTÐXJ
VEHICLES
REMOVAL
(1) Raise the vehicle. Position support stands un-
der the frame rails slightly in front the springs.
(2) Remove the rear wheels.
(3) Mark the drive shaft yoke and axle pinion yoke
for alignment reference. Disconnect the drive shaft
from the axle.
(4) Disconnect the axle vent hose.
(5) Disconnect the parking brake cables at the
equalizer or backing plate.
(6) Disconnect the shock absorbers from the axle
brackets.
(7) Disconnect the brake hose at the axle junction
block.Do not disconnect the wheel cylinder tub-
ing fittings.
(8) If equipped, disconnect ABS wiring connections
at the axle.
(9) Support the axle with a hydraulic jack under
the differential.
(10) Remove the spring U-bolts from the plate
brackets.
(11) Lower the jack enough to remove the axle.
INSTALLATION
CAUTION: Suspension components with rubber
bushings should be tightened with the vehicle at
normal height. It is important to have the springs
supporting the weight of the vehicle when the fas-
teners are torqued. If springs are not at their normal
ride position, vehicle ride comfort could be affected
and premature bushing wear may occur. Rubber
bushings must never be lubricated.(1) Support the axle on a hydraulic jack under the
differential. Position the axle under the vehicle.
(2) Raise the axle and align the spring center bolts
with the locating holes in the axle pads and plate
brackets.
(3) Install the spring U-bolts through the plate
brackets and tighten to 70 Nzm (52 ft. lbs.) torque.
(4) Install ABS wiring connections (if equipped) at
the axle.
(5) Connect the brake hose at the axle junction
block.
(6) Install the shock absorbers to the axle brackets
and tighten to 62 Nzm (46 ft. lbs.) torque.
(7) Connect the parking brake cables at the equal-
izer or backing plate.
(8) Connect the vent hose to the tube fitting.
(9) Align the reference marks and connect the
drive shaft to the axle yoke. Tighten the U-joint
clamp bolts to 19 Nzm (14 ft. lbs.) torque.
(10) Check differential lubricant and add if neces-
sary.
(11) Install the wheel and tire.
(12) Bleed the brakes.
(13) Remove the supports and lower the vehicle.
LUBRICANT CHANGE
The gear lubricant will drain quicker if the vehicle
has been recently driven.
(1) Raise and support the vehicle.
(2) Remove the lubricant fill hole plug from the dif-
ferential housing cover.
(3) Remove the differential housing cover and
drain the lubricant from the housing.
(4) Clean the housing cavity with a flushing oil,
light engine oil or lint free cloth.Do not use water,
steam, kerosene or gasoline for cleaning.
(5) Remove the sealant from the housing and cover
surfaces. Use solvent to clean the mating surfaces.
(6) Apply a bead of MOPARtSilicone Rubber Seal-
ant to the housing cover (Fig. 2). Allow the sealant to
cure for a few minutes.
Install the housing cover within 5 minutes after
applying the sealant. If not installed the sealant
must be removed and another bead applied.
(7) Install the cover and any identification tag.
Tighten the cover bolts in a criss-cross pattern to 47
Nzm (35 ft. lbs.) torque.
(8) Refill the differential with Mopar Hypoid Gear
Lubricant 13 mm (1/2 in.) below the fill plug hole.
With Trac-Lok differentials, add a container of Mopar
Hypoid Gear Lubricant Additive.
CAUTION: Overfilling the differential can result in
lubricant foaming and overheating.
(9) Install the fill hole plug and lower the vehicle.
JREAR SUSPENSION AND AXLES 3 - 31
Page 117 of 2198
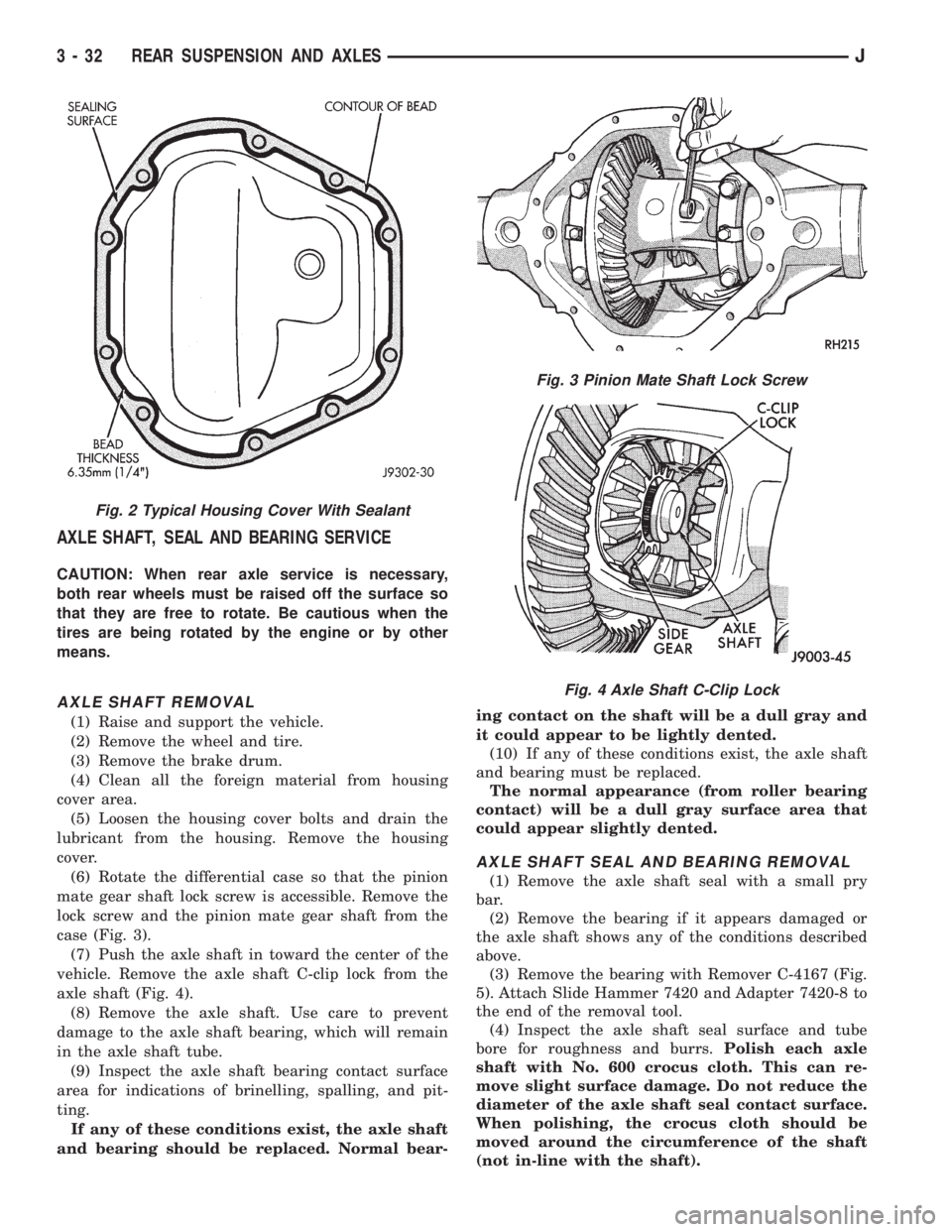
AXLE SHAFT, SEAL AND BEARING SERVICE
CAUTION: When rear axle service is necessary,
both rear wheels must be raised off the surface so
that they are free to rotate. Be cautious when the
tires are being rotated by the engine or by other
means.
AXLE SHAFT REMOVAL
(1) Raise and support the vehicle.
(2) Remove the wheel and tire.
(3) Remove the brake drum.
(4) Clean all the foreign material from housing
cover area.
(5) Loosen the housing cover bolts and drain the
lubricant from the housing. Remove the housing
cover.
(6) Rotate the differential case so that the pinion
mate gear shaft lock screw is accessible. Remove the
lock screw and the pinion mate gear shaft from the
case (Fig. 3).
(7) Push the axle shaft in toward the center of the
vehicle. Remove the axle shaft C-clip lock from the
axle shaft (Fig. 4).
(8) Remove the axle shaft. Use care to prevent
damage to the axle shaft bearing, which will remain
in the axle shaft tube.
(9) Inspect the axle shaft bearing contact surface
area for indications of brinelling, spalling, and pit-
ting.
If any of these conditions exist, the axle shaft
and bearing should be replaced. Normal bear-ing contact on the shaft will be a dull gray and
it could appear to be lightly dented.
(10) If any of these conditions exist, the axle shaft
and bearing must be replaced.
The normal appearance (from roller bearing
contact) will be a dull gray surface area that
could appear slightly dented.
AXLE SHAFT SEAL AND BEARING REMOVAL
(1) Remove the axle shaft seal with a small pry
bar.
(2) Remove the bearing if it appears damaged or
the axle shaft shows any of the conditions described
above.
(3) Remove the bearing with Remover C-4167 (Fig.
5). Attach Slide Hammer 7420 and Adapter 7420-8 to
the end of the removal tool.
(4) Inspect the axle shaft seal surface and tube
bore for roughness and burrs.Polish each axle
shaft with No. 600 crocus cloth. This can re-
move slight surface damage. Do not reduce the
diameter of the axle shaft seal contact surface.
When polishing, the crocus cloth should be
moved around the circumference of the shaft
(not in-line with the shaft).
Fig. 2 Typical Housing Cover With Sealant
Fig. 3 Pinion Mate Shaft Lock Screw
Fig. 4 Axle Shaft C-Clip Lock
3 - 32 REAR SUSPENSION AND AXLESJ
Page 118 of 2198
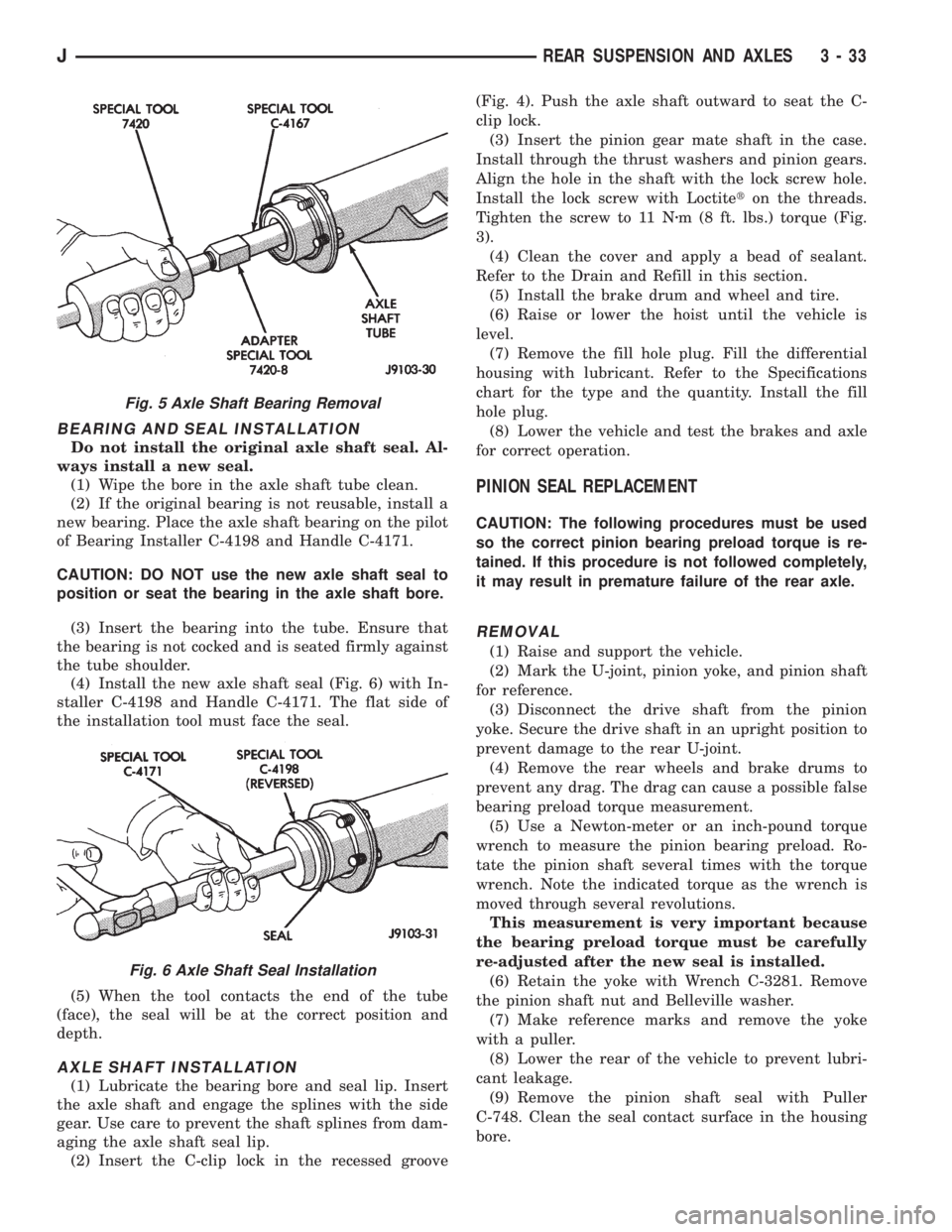
BEARING AND SEAL INSTALLATION
Do not install the original axle shaft seal. Al-
ways install a new seal.
(1) Wipe the bore in the axle shaft tube clean.
(2) If the original bearing is not reusable, install a
new bearing. Place the axle shaft bearing on the pilot
of Bearing Installer C-4198 and Handle C-4171.
CAUTION: DO NOT use the new axle shaft seal to
position or seat the bearing in the axle shaft bore.
(3) Insert the bearing into the tube. Ensure that
the bearing is not cocked and is seated firmly against
the tube shoulder.
(4) Install the new axle shaft seal (Fig. 6) with In-
staller C-4198 and Handle C-4171. The flat side of
the installation tool must face the seal.
(5) When the tool contacts the end of the tube
(face), the seal will be at the correct position and
depth.
AXLE SHAFT INSTALLATION
(1) Lubricate the bearing bore and seal lip. Insert
the axle shaft and engage the splines with the side
gear. Use care to prevent the shaft splines from dam-
aging the axle shaft seal lip.
(2) Insert the C-clip lock in the recessed groove(Fig. 4). Push the axle shaft outward to seat the C-
clip lock.
(3) Insert the pinion gear mate shaft in the case.
Install through the thrust washers and pinion gears.
Align the hole in the shaft with the lock screw hole.
Install the lock screw with Loctiteton the threads.
Tighten the screw to 11 Nzm (8 ft. lbs.) torque (Fig.
3).
(4) Clean the cover and apply a bead of sealant.
Refer to the Drain and Refill in this section.
(5) Install the brake drum and wheel and tire.
(6) Raise or lower the hoist until the vehicle is
level.
(7) Remove the fill hole plug. Fill the differential
housing with lubricant. Refer to the Specifications
chart for the type and the quantity. Install the fill
hole plug.
(8) Lower the vehicle and test the brakes and axle
for correct operation.
PINION SEAL REPLACEMENT
CAUTION: The following procedures must be used
so the correct pinion bearing preload torque is re-
tained. If this procedure is not followed completely,
it may result in premature failure of the rear axle.
REMOVAL
(1) Raise and support the vehicle.
(2) Mark the U-joint, pinion yoke, and pinion shaft
for reference.
(3) Disconnect the drive shaft from the pinion
yoke. Secure the drive shaft in an upright position to
prevent damage to the rear U-joint.
(4) Remove the rear wheels and brake drums to
prevent any drag. The drag can cause a possible false
bearing preload torque measurement.
(5) Use a Newton-meter or an inch-pound torque
wrench to measure the pinion bearing preload. Ro-
tate the pinion shaft several times with the torque
wrench. Note the indicated torque as the wrench is
moved through several revolutions.
This measurement is very important because
the bearing preload torque must be carefully
re-adjusted after the new seal is installed.
(6) Retain the yoke with Wrench C-3281. Remove
the pinion shaft nut and Belleville washer.
(7) Make reference marks and remove the yoke
with a puller.
(8) Lower the rear of the vehicle to prevent lubri-
cant leakage.
(9) Remove the pinion shaft seal with Puller
C-748. Clean the seal contact surface in the housing
bore.
Fig. 5 Axle Shaft Bearing Removal
Fig. 6 Axle Shaft Seal Installation
JREAR SUSPENSION AND AXLES 3 - 33
Page 119 of 2198
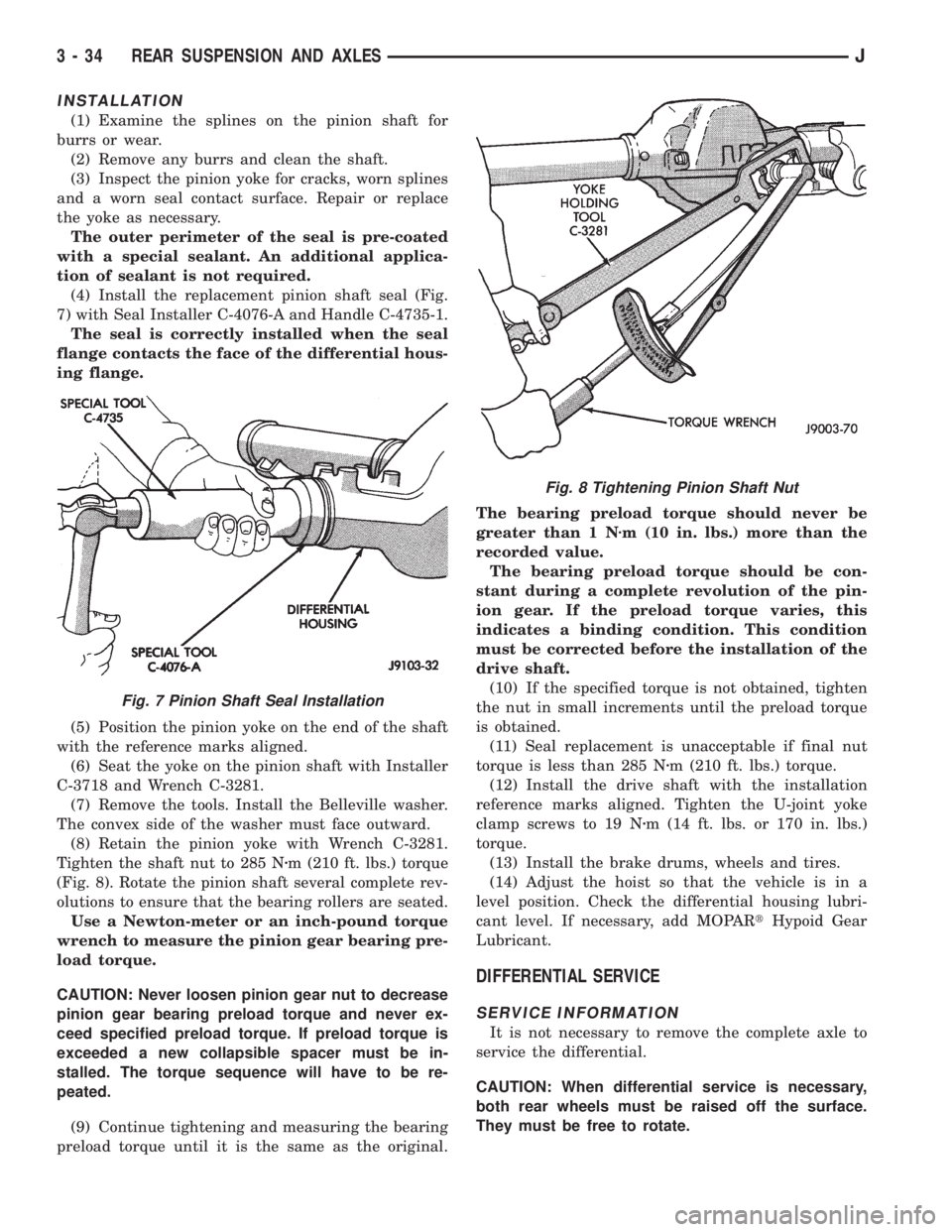
INSTALLATION
(1) Examine the splines on the pinion shaft for
burrs or wear.
(2) Remove any burrs and clean the shaft.
(3) Inspect the pinion yoke for cracks, worn splines
and a worn seal contact surface. Repair or replace
the yoke as necessary.
The outer perimeter of the seal is pre-coated
with a special sealant. An additional applica-
tion of sealant is not required.
(4) Install the replacement pinion shaft seal (Fig.
7) with Seal Installer C-4076-A and Handle C-4735-1.
The seal is correctly installed when the seal
flange contacts the face of the differential hous-
ing flange.
(5) Position the pinion yoke on the end of the shaft
with the reference marks aligned.
(6) Seat the yoke on the pinion shaft with Installer
C-3718 and Wrench C-3281.
(7) Remove the tools. Install the Belleville washer.
The convex side of the washer must face outward.
(8) Retain the pinion yoke with Wrench C-3281.
Tighten the shaft nut to 285 Nzm (210 ft. lbs.) torque
(Fig. 8). Rotate the pinion shaft several complete rev-
olutions to ensure that the bearing rollers are seated.
Use a Newton-meter or an inch-pound torque
wrench to measure the pinion gear bearing pre-
load torque.
CAUTION: Never loosen pinion gear nut to decrease
pinion gear bearing preload torque and never ex-
ceed specified preload torque. If preload torque is
exceeded a new collapsible spacer must be in-
stalled. The torque sequence will have to be re-
peated.
(9) Continue tightening and measuring the bearing
preload torque until it is the same as the original.The bearing preload torque should never be
greater than 1 Nzm (10 in. lbs.) more than the
recorded value.
The bearing preload torque should be con-
stant during a complete revolution of the pin-
ion gear. If the preload torque varies, this
indicates a binding condition. This condition
must be corrected before the installation of the
drive shaft.
(10) If the specified torque is not obtained, tighten
the nut in small increments until the preload torque
is obtained.
(11) Seal replacement is unacceptable if final nut
torque is less than 285 Nzm (210 ft. lbs.) torque.
(12) Install the drive shaft with the installation
reference marks aligned. Tighten the U-joint yoke
clamp screws to 19 Nzm (14 ft. lbs. or 170 in. lbs.)
torque.
(13) Install the brake drums, wheels and tires.
(14) Adjust the hoist so that the vehicle is in a
level position. Check the differential housing lubri-
cant level. If necessary, add MOPARtHypoid Gear
Lubricant.
DIFFERENTIAL SERVICE
SERVICE INFORMATION
It is not necessary to remove the complete axle to
service the differential.
CAUTION: When differential service is necessary,
both rear wheels must be raised off the surface.
They must be free to rotate.
Fig. 7 Pinion Shaft Seal Installation
Fig. 8 Tightening Pinion Shaft Nut
3 - 34 REAR SUSPENSION AND AXLESJ
Page 120 of 2198
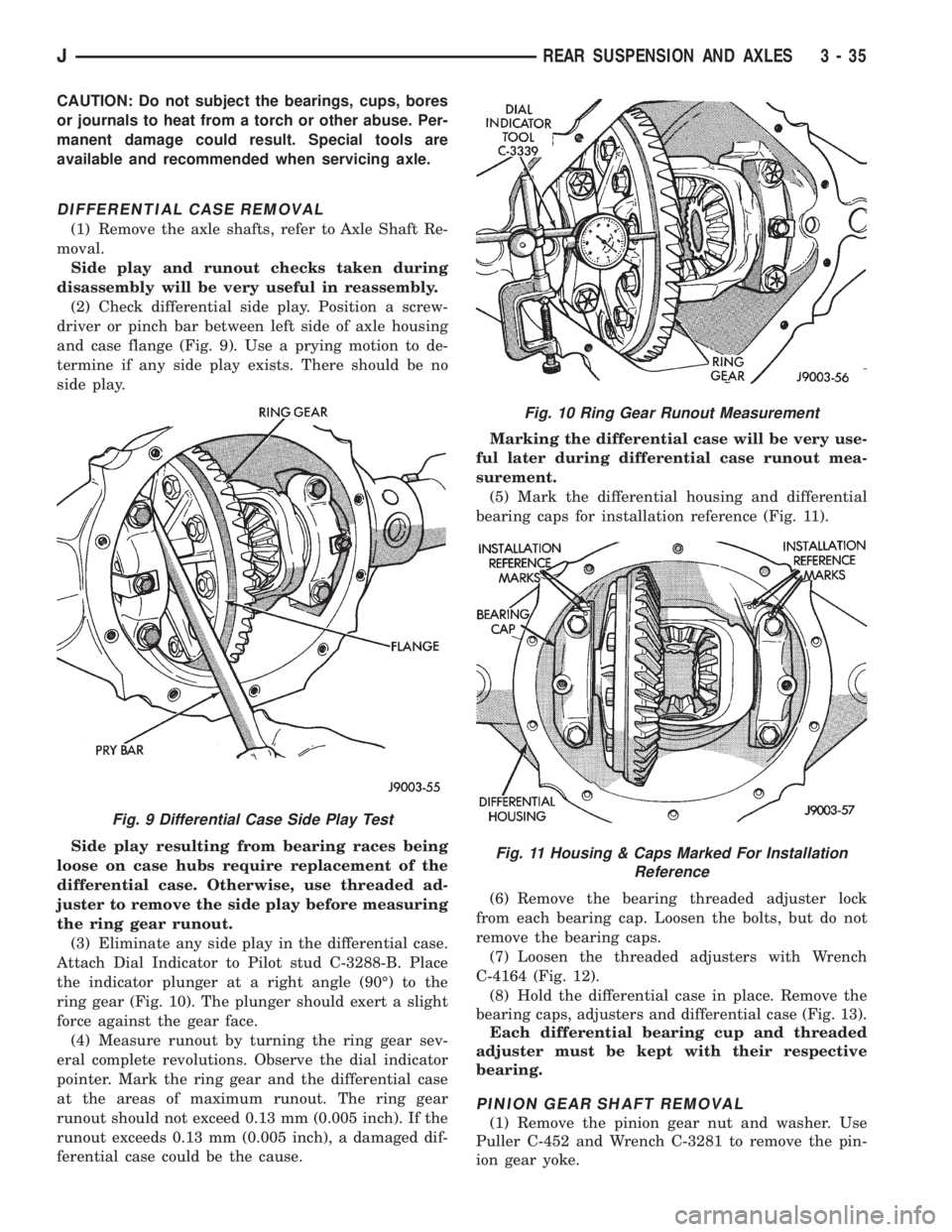
CAUTION: Do not subject the bearings, cups, bores
or journals to heat from a torch or other abuse. Per-
manent damage could result. Special tools are
available and recommended when servicing axle.
DIFFERENTIAL CASE REMOVAL
(1) Remove the axle shafts, refer to Axle Shaft Re-
moval.
Side play and runout checks taken during
disassembly will be very useful in reassembly.
(2) Check differential side play. Position a screw-
driver or pinch bar between left side of axle housing
and case flange (Fig. 9). Use a prying motion to de-
termine if any side play exists. There should be no
side play.
Side play resulting from bearing races being
loose on case hubs require replacement of the
differential case. Otherwise, use threaded ad-
juster to remove the side play before measuring
the ring gear runout.
(3) Eliminate any side play in the differential case.
Attach Dial Indicator to Pilot stud C-3288-B. Place
the indicator plunger at a right angle (90É) to the
ring gear (Fig. 10). The plunger should exert a slight
force against the gear face.
(4) Measure runout by turning the ring gear sev-
eral complete revolutions. Observe the dial indicator
pointer. Mark the ring gear and the differential case
at the areas of maximum runout. The ring gear
runout should not exceed 0.13 mm (0.005 inch). If the
runout exceeds 0.13 mm (0.005 inch), a damaged dif-
ferential case could be the cause.Marking the differential case will be very use-
ful later during differential case runout mea-
surement.
(5) Mark the differential housing and differential
bearing caps for installation reference (Fig. 11).
(6) Remove the bearing threaded adjuster lock
from each bearing cap. Loosen the bolts, but do not
remove the bearing caps.
(7) Loosen the threaded adjusters with Wrench
C-4164 (Fig. 12).
(8) Hold the differential case in place. Remove the
bearing caps, adjusters and differential case (Fig. 13).
Each differential bearing cup and threaded
adjuster must be kept with their respective
bearing.
PINION GEAR SHAFT REMOVAL
(1) Remove the pinion gear nut and washer. Use
Puller C-452 and Wrench C-3281 to remove the pin-
ion gear yoke.
Fig. 9 Differential Case Side Play Test
Fig. 10 Ring Gear Runout Measurement
Fig. 11 Housing & Caps Marked For Installation
Reference
JREAR SUSPENSION AND AXLES 3 - 35